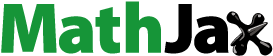
ABSTRACT
This paper investigates the use of marble dust waste, fly ash, and silica fume as raw materials for manufacturing geopolymer pastes. The chemical composition of each raw material is established using chemical analysis (X-ray fluorescence XRF) and mineralogical analysis, X-ray diffraction (XRD) pattern of raw materials. The experimental work was divided into three groups (A, B, C) according to the water to binder ratio (w/b) (A =28%, B = 30%, C = 33%). Each group is further divided into five subgroups according to the percentage of marble dust, fly ash, and silica fume. The samples are cured at 60°C for three days. The properties of the geopolymer pastes are determined by performing the following tests: compressive, tensile, and flexural strength and water absorption. The highest mechanical properties were obtained from mixes containing 70% fly ash and 30% marble dust at w/b = 0.28. It was 40% more than those obtained from control mixes containing 50% fly ash and 50% marble dust. It is worth mentioning that the best amount of marble dust was 30% as the resistance of the geopolymer paste reached values up to 237.8 kg/cm2. The results were confirmed by SEM imaging.
Introduction
The traditional methods of eliminating conventional waste have negative side effects on the surrounding environment. These effects result in many types of pollution besides the high cost in the transfer and burial of such wastes. Environmentally friendly and cost-effective ways include the use of waste material in construction industry such as blast furnace slag and fly ash (Pappu, Saxena, & Asolekar, Citation2007), (Safiuddin, Jumaat, Salam, Islam, & Hashim, Citation2010) and (Horpibulsuk, Munsrakest, Udomchai, Chinkulkijniwat, & Arulrajah, Citation2014). On the other hand, as a part of the development in industrial human activities, the cement industry in particular recorded a significant increase (Turner & Collins, Citation2013). This increase caused an increase in the carbon dioxide emitted from the industries. The production of one ton of cement met about one ton of carbon dioxide to the atmosphere (Radlinski & Moncarz, Citation2011). Due to the great problems related to the OPC industry, it is necessary to find solutions and search for alternatives. One of the alternatives to OPC is geopolymer concrete (Davidovits, Citation2002). On the other hand, the use of industrial waste products in GPC industry contributed to solving many problems, including solving the problem of how to get rid of industry waste products by using them as source materials in the production of the GPC and thus maintain the integrity of the environment (Turner & Collins, Citation2013). The GPC industry is also the ideal solution for greenhouse emissions related to the OPC industry by reducing emissions (Habert, Lacaillerie, & Roussel, Citation2011). There is a significant decrease in carbon dioxide emission in the new method (GPC), estimated to be 80% compared to the old methods (OPC) (Turner & Collins, Citation2013). geopolymer is defined as an inorganic polymer, like a ceramic, produced at low temperatures (Wang, Li Yan, & Yan, Citation2005). The geopolymer is formed as a result of chemical reaction of the alkaline activator with the alumina and silicate found in the pozzolanic material (source material) (Jaarsveld, Deventer, & Lukey, Citation2002) and (Gourley, Citation2014). In addition, this reaction was described as a rapid reaction resulting in a three-dimensional polymer and ring structure consisting of SI-O-AL-0 bonds (Gourley, Citation2014).
There are many pozzolanic raw materials for geopolymer such as fly ash from coal combustion (Andini et al., Citation2008) and (Boke, Birch, Nyale, & Petrik, Citation2015), metakaolin (Zhang, Zhu, Zhou, & Wang, Citation2016), slag waste from metallurgical industries (Alex et al., Citation2013), glass wastes (Novais, Ascensao, Seabra, & Labrincha, Citation2016), and bagasse (Amin, Gul, Gul, & gul, Citation2016). Recent scientific research has proven a wide range of geopolymer applications such as fire retardants, concrete, thermal insulation, cement, arts and other applications (Davidovits, Citation2011). There are many scientific studies that have concluded that the most important factors affecting the compressive strength of the geopolymer are the curing time and temperature (Arioz, Arioz, & Kockar, Citation2013). When the fly ash-based geopolymer was treated at 60°C for 48 hours a very high compressive strength was gained (Swanepoel & Strydom, Citation2002). Both alkaline activator (types and concentration) (Xin, Jin-Yu, Weimin, & Erlei, Citation2014) and calcination temperature (Elimbi, Tchakoute, & Jopwouo, Citation2011) directly affect the properties of the geopolymer concrete. Geopolymer concrete was influenced by the time of mixing. Mixing of fly ash-based geopolymer for up to 16 minutes increased compressive strength (Hardjito, Citation2005). The setting time of blast furnace slag and metakaolin based geopolymer concrete ranges between 15 and 45 minutes at 60°c (Cheng & Chiu, Citation2003). It was also confirmed that the setting time of fresh geopolymer concrete up to 120 minutes (Cheng & Chiu, Citation2003). The partial replacement of marble dust in different proportions of cement results in a clear distinction between ordinary cement and pozzolanic-containing cement. And through the scanning electron microscope (SEM) diagram it is also shown that the continuous formation of marble dust is increasing the morphological structure of the space between cement and marble dust (Shukla, Gupta, & Gupta, Citation2020). The workability of marble-based geopolymer concrete can meet the requirements of first-stage self-compacting concrete. The slump and slump flow can achieve 520 and 640 mm, respectively. The large-scale test for marble-based geopolymer mortar in a ready-mixed plant was successful, and the fresh properties were good for making several cubic meter blocks (Lee, Lin, Chang, Ding, & Cheng, Citation2020). By using marble powder as the fine aggregate the compressive strength of the concrete is being increased. Also with the increase in percentage of marble powder the cube tends to set quickly than other geopolymer and conventional cubes (Raja, Rajalakshmi, Valliappan, & Dhivya, Citation2018). Since marble dust (MD) poses a serious hazard to environment and is usually dumped in rural areas causing a lot of environment damage, the main objective in this study is to investigate whether marble dust-based geopolymer possesses suitable mechanical characteristics to serve as a construction material or not.
Experimental work
Materials
To achieve the research objectives, an intensive experimental program was planned and conducted. The experimental work investigates Egyptian marble dust as a suitable base for a new geopolymer implementing a mixture of marble dust with different percentages of fly ash (FA) and/or silica fume (SF). These three materials which are composed of mainly silicon (Si) and aluminum (AL) were added to react with alkaline activator (sodium hydroxide (NaoH) and sodium silicate (Na2Sio3) to obtain the geopolymer paste.
Characteristics of different materials
Basic chemical compositions of raw materials marble dust (MD), fly ash (FA), and silica fume (SF) were examined with X-ray fluorescence (XRF), . In addition, X-ray diffraction (XRD) implementation was to verify the mineralogical pattern of these materials, . The pattern of marble dust, fly ash, and silica fume revealed that it consists mainly of calcite, quartz, and moganite respectively. shows that silica fume consists mainly of amorphous silica.
Table 1. Chemical analysis of all raw materials.
Mix proportions
Fifteen mixes were prepared with three different w/b ratios (0.28, 0.30, and 0.33) as shown in . Each mix contains alkaline activators substances, an activation solution of 1% NaoH as a dissolver in a 1:1 solution of Na2O3Si and H2O. The control mix was prepared with using 50% fly ash and 50% marble dust.
Table 2. Details of mix proportions.
Casting, curing, and testing of geopolymer paste
The alkaline activator solution was prepared and left for one day before use. The materials were then mixed with ready-made solutions for full homogeneity before casting in molds. The samples were left for one day in molds. All specimens were continuously cured at (60 °C) in furnace at age of 3 days. Compressive strength test was carried out according to the Egyptian Code of Practice (Egyptian Code of Practice (ECP), Citation2020) at 3 days after casting. At testing age, three specimens (cubes of 50x50x50mm) were tested in compression. Indirect tensile strength test was conducted on samples of cylinders (5 cm diameter, 10 cm length) according to (ASTM C496, Citation2002) at age 3 days. Flexural strength test was conducted on prisms (4 x 4 × 16 cm) according to (ASTM C496, Citation2002) at age 3 days. The water absorption test was conducted according to (ES 5324, 2006). Six samples (M-A1, M-B1, M-C1, M-A5, M-B4, and M-C5) were selected from the different subgroup .The samples were immersed in a basin of water at room temperature for 24 hours and then placed into the oven at 105° c for 24 hours. Eq. (1) was used to calculate the absorption percentage. Scanning electron microscope (SEM) test was performed according to ASTM C1723.
Where:
Wd = dry weight of the specimen, Ws = saturated weight of the specimen after submersion in water.
Results and discussion
Compressive strength (Fc)
The average compressive strength at 3 days curing for the investigated w/b ratios with different ratios of waste materials (marble dust, fly ash and silica fume) is shown in . It can be noticed that the increase in the w/b ratio led to a decrease in the compressive strength with using a different percentage of MD and FA. shows the percentage of increase and decrease in the compressive strength when using different ratios of MD, FA and SF. The control mixture contains 50% marble dust and 50% fly ash.
Table 3. Test results of compressive strength of FA/MD /SF geopolymer mixes.
There is a significant increase (additional 41.5%) in the compressive strength in mix (M-A2) which contains 30% marble dust. It was 1.5 and 1.2 times the mixes containing 50% and 10% marble dust respectively. This means that the use of w/b ratio 0.28 and marble dust ratio 30% gives the highest value of compressive strength. The ideal ratio of marble dust was 30% and fly ash was 70%. For all w/b ratios, the compressive strength values decreased when fly ash ratio increased beyond 70%. Adding silica fume to the geopolymer mixtures led to the deterioration of the compressive strength results with the presence of (fly ash and marble dust), . This may be due to that formation of bubbles was observed when adding silica fume to the mixture containing alkaline activator. Also, large pores were observed on whole surface samples with an increase in volume. These voids and pores, in turn, led to weakness of the samples during compressive strength test.
It can be concluded from that the highest compressive strength recorded at w/b ratio 0.28 is 237.8 Kg/cm2 (M-A2). The compressive strength decreases by 26.8% and 38.4% at w/b ratio 0.30 and 0.33 respectively. The above compressive strength ratios indicate the inverse relationship between w/b ratio and compressive strength values of geopolymer mixes used in this research, similar to ordinary cement paste. It can be also noticed from that the paste containing 40% fly ash, 40% marble dust, and 20% silica fume is the worst paste giving the lowest values of compressive strength at all w/b ratios. At w/b ratio 0.33, the lowest compressive strength is 6.65 Kg/cm2 (M-C4).
Flexural load
The average flexural load at 3 days curing for the investigated three percentage of w/b ratio with different ratios of waste materials (marble dust, fly ash, and silica fume) is shown in . It can be noticed that the highest value of the ultimate flexural load obtained of geopolymer paste contains 90% fly ash and 10% marble powder at w/b ratio 0.28 (M-A3). Whereas using w/b ratio 0.30 and 0.33 results in lowest FL value in the same paste. shows the percentage of increase and decrease in the flexural load at different ratios of FA, MD, and SF.
Table 4. Test results of flexural load of FA/MD /SF geopolymer mixes.
There is a significant increase (36%) in the flexural load at mix (M-A3) containing 10% marble dust and 90% fly ash with respect to the mix contains 50% marble dust and 50% fly ash. During the test there is no clear reason for that the optimum compressive strength was found at 30% addition of marble dust and the optimum flexural strength was at 10% adding of marble dust. This may be attributed to the fact that it is a new concrete and its behavior was different from traditional concrete. It can be also noticed that increasing the percentage of silica fume beyond 10% to the geopolymer mixture led to a significant decrease in the flexural load, . Moreover, during the preparation of geopolymer paste the formation of bubbles was observed. Large pores were observed on the whole surface samples with an increase in volume. These pores, in turn, led to the weakness of the samples during the fracture.
From , it can be concluded that the geopolymer paste containing 90% fly ash and 10% marble dust with w/b ratio of 0.28 is considered the best one giving the highest values of ultimate flexural load (M-A3).
Indirect tensile strength
The average indirect tensile strength at 3 days curing is shown in and . It can be concluded that the highest value of the splitting tensile strength obtained without silica fume is that of 90% fly ash and 10% marble dust at w/b ratio 0.28 (M-A3) and the highest with silica fume is that of 45/45/10 mix at w/b ratio 0.33 (M-C4). The addition of silica fume led to a significant increase in the splitting tensile strength. Although adding silica fume reduces compressive and flexural strength, adding 10% SF in mix (M-C4) contributed to the highest value of splitting tensile strength 14.9 Kg/cm2. This may be attributed to the chemical composition of geopolymer paste making it different in behavior than traditional paste ().
Figure 9. Effect of addition % silica fume on splitting. %marble dust on splitting tensile strength.
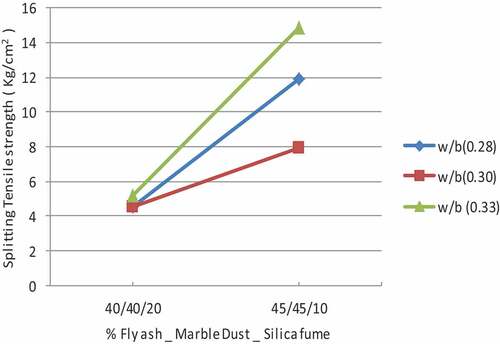
Table 5. Test results of indirect tensile strength of FA/MD /SF geopolymer mixes.
Water absorption
The water absorption is shown in . It can be concluded that the highest water absorption was recorded at w/b ratio = 0.33 at different proportions of the geopolymer paste. It was 19.5% and 26% for mixes (M-C1) and (M-C5), respectively. The lowest water absorption (8%) was at w/b ratio = 0.28 in (M-A1). For mix containing 20% silica fume (M-B5) the lowest water absorption (6%) was found at w/b ratio = 0.30.
Scanning Electron Microscope (SEM) behavior
Illustrates the SEM microscopic images that were captured for some samples of the geopolymer paste after 3 days curing in order to ascertain the studied characteristics. Large spaces and voids were observed, which in turn indicate a weakness in the sample and lack of cohesion. This complies with the very week compressive strength results of this sample obtained previously. In addition to the white spots, which are mostly calcareous materials (silica fume). This sample (M-C4) contains 45% marble dust, 45% fly ash, and 10% silica fume at w/b ratio (0.33). For more details, shows the X-ray spectrum of surface specimen. It can be noted that the main elements for interface surface are Ca and Si for the shown windows. The presence of Ca and Si elements is representative of the Ca(OH)2 and C-S-H present in the specimen.
As shown in the SEM image shows a decrease in the void and gaps size which has a good effect on improving the mechanical properties. shows the X-ray spectrum of surface specimen. It can be noticed that the main element for the interface surface is silicon that means more leaching of Ca(OH)2 and more generation of CSH which is responsible for improving mechanical and durability properties. This sample (M-A2) contains 30% marble dust and 70% fly ash at w/b ratio (0.28).
Conclusions and recommendations
This paper presented experimental results and discussions for the mechanical properties of geopolymer concrete incorporating different types and ratios of waste materials. Many experimental tests, which included compressive strength, tensile strength, flexural strength, water absorption, and scanning electron microscope (SEM), were performed.
It can be concluded that marble dust has been characterized to be a good supplementary material. Using marble dust has resulted in an increase in the mechanical properties. The results obtained and the observations made in the current study indicate that the highest increment in compressive strength compared to the control mix was at mix containing 30% marble dust and 70% fly ash, in which compressive strength was 237.8 kg /cm2. It was 40% more than those obtained from mixes containing fly ash and marble dust by (50%) equally. The highest value of splitting tensile strength (14.9 kg/cm2) is at 45% fly ash, 45% marble dust, and 10% silica fume for mix (M-C4), and flexural load (245 kg) is at 90% fly ash and 10% marble dust for mix (M-A3). So the optimum value of marble dust is 30% for compressive strength, 10% for splitting strength, and 45% for flexural strength.
Adding silica fume reduces the value of compressive strength more than (50%) with respect to control mix.
Examination of SEM photos and images confirms that fly ash and marble dust play an important role in improving the whole geopolymer properties through its ability to fill voids and pores and also confirms evidence of mechanical and physical properties. Moreover, SEM photos confirm that adding silica fume has a negative effect on mechanical properties through the appearance of cracks, voids, and pores.
For construction purposes that need pastes with high compressive strength a mix containing 30% marble dust can be used. For construction purposes that need pastes with high splitting strength and flexural strength only mixes containing 10% marble dust can be used.
Using marble dust in construction applications would lead to considerable environmental benefits and at the same time strength properties are increased.
In further work there is a need to study the behavior of these mixes in long term at different curing time ages and conditions.
Disclosure statement
No potential conflict of interest was reported by the author(s).
References
- Alex, T. C., Kalinkin, A. M., Nath, S. K., Gurevich, B. I., Kalinkina, E. V., Tyukavkina, V. V., & Kumar, S. (2013). Utilization of zinc slag through geopolymerization: Influence of milling atmosphere. International Journal of Mineral Processing, 123, 102–107. doi:10.1016/j.minpro.2013.06.001
- Amin, N., Gul, S., Gul, S., & gul, S. (2016). Synthesis and characterization of geopolymer from bagasse bottom ash, waste of sugar industries and naturally available China clay. Journal of Cleaner Production, 129, 491–495. doi:10.1016/j.jclepro.2016.04.024
- Andini, S., Cioffi, R., Colangelo, F., Grieco, T., Montagnaro, F., & Santoro, L. (2008). Coal fly ash as raw material for the manufacture of geopolymer based products. Waste Management, 28(2), 416–423. doi:10.1016/j.wasman.2007.02.001
- Arioz, E., Arioz, O., & Kockar, O. M. (2013). The effect of curing conditions on the properties of geopolymer samples. International Journal of Chemical Engineering and Applications, 4, 423–426.
- ASTM C496. (2002). Standard test method for splitting strength ASTM International. USA: American Society of Testing Materials.
- Boke, N., Birch, G. D., Nyale, S. M., & Petrik, L. F. (2015). New synthesis method for the production of coal fly ash based foamed geopolymers. Construction and Building Materials, 75, 189–199. doi:10.1016/j.conbuildmat.2014.07.041
- Cheng, T. W., & Chiu, J. P. (2003). Fire-resistant geopolymer produced by granulated blast furnace slag. Minerals Engineering, 16(3), 203–210. doi:10.1016/S0892-6875(03)00008-6
- Davidovits, J., 2002. 30 years of successes and failures in geopolymer applications. Market trends and potential breakthroughs. In: Proceedings of international conference, Melbourne, Australia. 1–16.
- Davidovits, J. (2011). Geopolymer Chemistry and Applications (3rd ed.). Geopolymer institute, Saint-Quentin France.
- Egyptian Code of Practice (ECP). (2020). Design and Execution of Reinforced Concrete Structures. HRBC, Egypt: Guide for Laboratory Tests of Concrete Materials.
- Elimbi, A., Tchakoute, H. K., & Jopwouo, D. N. (2011). Effects of calcination temperature of kaolinite clays on the properties of geopolymer cements. Construction and Building Materials, 25(6), 2805–2812. doi:10.1016/j.conbuildmat.2010.12.055
- ES 5324/2006. (2006). Standard test methods for sampling and testing of building brick masonry units made from clay. Cairo, Egypt: Egyptian Organization for Standardization and Quality.
- Gourley, J. T. (2014). Geopolymers in Australia. Journal of the Australian Ceramics Society, 50, 102–110.
- Habert, D. G., Lacaillerie, J. B., & Roussel, N. (2011). An environmental evaluation of geopolymer based concrete production. Journal of Cleaner Production, 19(11), 1229–1238. doi:10.1016/j.jclepro.2011.03.012
- Hardjito, D., 2005. Studies on fly ash based geopolymer concrete. Curtin University of Technology, Faculty of Engineering and computing, Ph.D. thesis.
- Horpibulsuk, S., Munsrakest, V., Udomchai, A., Chinkulkijniwat, A., & Arulrajah, A. (2014). Strength of sustainable non-bearing masonry units manufactured from calcium carbide residue and fly ash. Construction and Building Materials, 71, 210–215. doi:10.1016/j.conbuildmat.2014.08.033
- Jaarsveld, J. G. S., Deventer, J. S. J., & Lukey, G. C. (2002). The effect of composition and temperature on the properties of fly ash and kaolinite based geopolymers. Construction and Building Materials, 89(1–3), 63–73. doi:10.1016/S1385-8947(02)00025-6
- Lee, W.-H., Lin, K.-L., Chang, T.-H., Ding, Y.-C., & Cheng, T.-W. (2020). Sustainable development and performance evaluation of marble-waste-based geopolymer concrete. Polymers, 12(9), 1924. doi:10.3390/polym12091924
- Novais, R., Ascensao, G., Seabra, M., & Labrincha, J. (2016). Waste glass from end of life fluorescent lamps as raw material in geopolymers. Waste Management, 52, 245–255. doi:10.1016/j.wasman.2016.04.003
- Pappu, A., Saxena, M. S., & Asolekar, R. (2007). Solid wastes generation in India and their recycling potential in building materials. Building and Environment, 42(6), 2311–2320. doi:10.1016/j.buildenv.2006.04.015
- Radlinski, M. H., & Moncarz, N. (2011). Sustainable concrete: Impacts of existing and emerging materials and technologies on the construction industry.
- Raja, M. A., Rajalakshmi, S., Valliappan, S., & Dhivya, K. S. (2018). Utilization of granulated marble geopolymer concrete. International Research Journal of Engineering and Technology (IRJET), 4, 12.
- Safiuddin, M. D., Jumaat, M. Z., Salam, M. A., Islam, M. S., & Hashim, R. (2010). Utilization of solid wastes in construction materials. International Journal of Physical Sciences, 13, 1952–1963.
- Shukla, A., Gupta, N., & Gupta, A. (2020). Development of green concrete using waste marble dust. Mathura 281406, India: Department of Civil Engineering, GLA University.
- Swanepoel, J. C., & Strydom, C. A. (2002). Utilization of fly ash in a geopolymeric material, Appl. Geochem, 17, 1143–1148.
- Turner, L. K., & Collins, F. G. (2013). Carbon dioxide equivalent (CO2) emissions: A comparison between geopolymer and OPC cement concrete. Construction and Building Materials, 43, 125 130. doi:10.1016/j.conbuildmat.2013.01.023
- Wang, H., Li Yan, H., & Yan, F. (2005). Synthesis and mechanical properties of meta-kaolinite based geopolymer. Colloids and Surfaces A: Physicochemical and Engineering Aspects, 268(1–3), 1–6. doi:10.1016/j.colsurfa.2005.01.016
- Xin, L., Jin-Yu, X., Weimin, L., & Erlei, B. (2014). Effect of alkali-activator types on the dynamic compressive deformation behavior of geopolymer concrete. Materials Letters, 124, 310–312. doi:10.1016/j.matlet.2014.03.102
- Zhang, Z. H., Zhu, H. J., Zhou, C. H., & Wang, H. (2016). Geopolymer from kaolin in China: An overview. Applied Clay Science, 119, 31–41. doi:10.1016/j.clay.2015.04.023