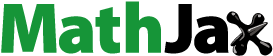
ABSTRACT
This study studied the tribological properties of PVD AISI 4140 low – alloy TiN coated and reported. The morphologies before testing are assessed with a laser confocal microscope and XRD. Three tests are conducted per sample: the rotating, scratch, and reciprocation tests. The contour of counter bodies and wear scares are studied and reported. The wear scares are also further studied using the SEM-EDS chemical analysis to study the amount of wear that has occurred. The results showed a change in roughness and waviness after coating. In the reciprocating tests showed a high degree of spalling on the TiN sample is observed with a higher wear volume compared to the substrate. However, a lower coefficient of friction is observed. This is similar to the rest of the tests.
KEYWORDS:
1. Introduction
Developing new technologies in various industries has brought about demands for versatile materials. For engineers and researchers to accurately design systems and machinery, it is very critical for them to understand the behaviour of new and existing materials. It is essential in predicting mechanical systems’ life cycle and energy consumption. Friction and other facts have been shown to contribute to more than 20% of factors of energy losses in mechanical systems annually [Citation1–3]. To overcome these challenges, researchers have explored and developed surface modification methods such as coating. A coating method that has existed for over a hundred years is Titanium Nitride (TiN) physical vapour deposition (PVD) coating. The advantages of this method include its low-cost maintenance, low environmental impact, functionality over various applications, and many more [Citation4]. In a recent tribology study, monolayer titanium-based coating has shown excellent resistance to wear when coated on alloy steel, with a 71,73 % reduction in the coefficient of friction [Citation5]. It is, therefore, essential to study the reaction of these systems to various surfaces; such studies are generally referred to as tribological research. This area offers great and interesting research opportunities [Citation6]. The use of nitrides and carbides has been shown to improve the tool wear and efficiency during machining processes. Badiger et al. [Citation5] proposed novel monolayer aluminium and iron-based coatings on a WC-CO substrate for machining applications. A reduction of 22% and 18% in surface roughness and cutting forces, respectively, was reported compared to a WC-CO tool. While the tool wear was reduced by 3,63 and 1,63 times the uncoated tool using the aluminium and iron-based coatings in that order.
EN 19 (AISI 4140) typical applications include gears, shafts, load-bearing tie rods, and other applications requiring high tensile strength and hardness. It has recently gained popularity in the oil and gas industry [Citation7]. And quite often, these applications involve surface-to-surface contact with dynamic or static loading. Therefore, selecting the most effective materials efficiently and effectively for designing mechanical systems is critical. This has led to the development of various surface enhancement methods adding increased research opportunities in investigating tribological and other properties caused by these enhancements.
To further enhance the tribological properties of this alloy, it is commonly coated with TiN using physical vapour deposition (PVD). The PVD technique works with different topological modifications, such as ion plating, evaporation, and sputtering. The main focus of these coating methods is initiated by vaporising the coating material and then allowing it to condense on the substrate’s surface [Citation8,Citation9]. The performance of the coating greatly depends on the adhesion strength of the coating to the substrate [Citation10]. The adhesion properties are affected by the type of substrate and surface morphology, thermal expansion coefficient, hardness, and crystal lattice of the substrate and coating [Citation11–13].
In this study, the adhesion and wear properties of AISI 4140 coated with TiN are experimentally studied. The instrumentation used for the study allows for a detailed topological study of both the sample’s wear track and topological wear on the testing counter body. Based on the literature survey conducted, to our knowledge, there are currently no studies sharing such details. The presented results are useful for the design of both tooling and mechanical parts.
2. Experimentation methodology
2.1. Sample preparation
or this work, two round 25 Ø and 25 mm high AISI 4140 steel samples were precision ground to obtain an almost mirror-shine finish and cleaned. The chemical composition of AISI 4140 is shown in [Citation14]. To assess the effect of the coating on the steel, one sample is PVD coated with TiN and one is left uncoated, as illustrated in . The layer has an average thickness of 5 µm as shown in , and the average surface roughness and topology is 0.91 µm. The coating was done at a commercial facility at TD Coating Centre (Pty) Ltd Johannesburg, South Africa. Two tests were conducted, the reciprocating, rotating, and scratch test, using the Rtec MFT-5000. The testing facility allows for a live test recording and direct measurement of the wear tracks and testing probe or ball.
Figure 2. (a) SEM micrograph of cross-section showing coating thickness, (b) - (c) EDS analysis of coating and substrate respectively and (d) chemical spectrum of cross-section.
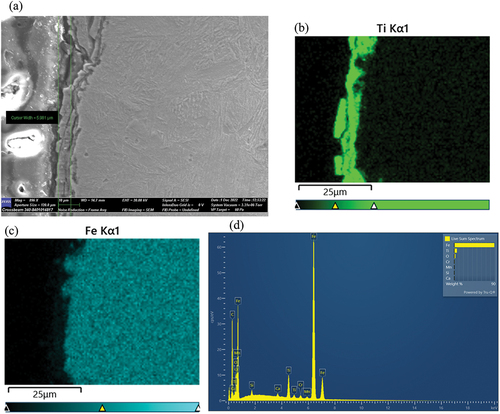
Table 1. AISI 4140 chemical composition.
2.2. Morphological characterisation of coating and uncoated surfaces
The surface topology of the samples was measured and characterised with a laser confocal microscope, Carl Zeiss LSM 900, XRD analysis of the coated and uncoated surfaces, and the EDS chemical composition of the test track or scratch with the SEM. Therefore, the samples are evaluated before and after the tests.
The effect of surface roughness on wear is an important factor to take into account when studying the wear rate of a material [Citation15]. For that reason, a study of the measured surface topologies was conducted. This is useful information for researchers developing models for wear rate predictions, of machine elements, machining processes, and other applications [Citation16–18]. It is recommended to use noncontact methods for topography measurements; noncontact methods are both non-invasive and convenient, with the capability to measure a variety of materials with high accuracy and reliability [Citation19]. In this study, the measurements are taken using laser confocal microscopy. The measured data is processed and analysed based on ISO 25,178.
From the surface measurements of the base material before coating and after coating there is a clear change in the surface roughness and waviness as shown by . There is more than 10% change in the surface roughness and waviness. summarises the measured surface properties, roughness, and waviness, respectively, of the base and coating.
Table 2. ISO 25,178 - Roughness (S-L).
The X-ray diffraction patterns of EN19 coated with TiN and uncoated EN19 are shown in . The diffraction peaks show high intensity at (111), (200), (220) and (311) planes of FCC [Citation20], as shown in . There is a slight shift in the peaks and this is because of the processing parameters used during the PVD coating. PVD TiN coatings have been shown previously exhibit special magnitudes of orientation. To determine these the Harris texture index, equation 1 is used to illustrate this [Citation21]. The texture coefficients are shown in .
There is a direct relation between the grain size and the hardness of metallic coatings, to analyse this relationship the Williamson-Hall (W-H) analysis method is used [Citation22,Citation23]. The general approach is to determine the size of the average nanocrystalline from the Debye-Scherrer formula in equation 2.
Where is the shape factor (0,9),
is the wavelength and
is the instrument broadening. The estimated strain is also given by the following equation 3:
The sum of equation 2 and 3 is assumed to contribute to the line broadening and that each equation is independent to each other with a Cauchy profile, giving equation 4 [Citation24].
The results of the W-H analysis are shown in . Where the average crystallite size was determined by the intercept of the fitted line. The W-H analysis indicates a decrease in crystallite size after coating [Citation10]. This is caused by oxygen contamination that occurred on the grain boundaries causing low merging earlier than anticipated [Citation25].
The pin-on-disc rotatory test based on ASTM G99 was followed to test the coating wear rate. To measure the reciprocation wear test standard ASTM G133 was followed. , summarises the test parameters used for the study.
Table 3. ISO 25,178 - waviness (S-F).
Table 4. Summary of test parameters.
3. Results and discussion
3.1. Reciprocating test
Shown in are the results of the coefficient of friction of the coated samples and substrate tested over 5 hours using the Al2O3 ball. The slight sudden friction coefficient fluctuations are attributed to the plastic deformation and particles fall off the surface. The friction coefficient of the substrate is significantly higher than the coated sample. This is due to the significant decrease in the surface roughness observed in and after coating [Citation26]. This is also evident in the micrographs of the scratched surfaces and the counter bodies in . (c) shows the wear scare cross-sectional volume of the TiN coated surface. The measured depth was close to 2 µm. In comparison, that of the substrate shown in (a) was close to 1 µm with more spalling than the TiN coated surface indicating plastic deformation, showing significant improvement to wear resistance. (d) shows the measured roughness and surface contour of the counter body used to test the TiN coated surface; from the measured roughness there is a clear deformation of the counter body due to the surface’s resistance to wear, compared to (b) where there was almost no deformation on the surface of the counter body.
3.2. Rotating test
(a) and (b) show the friction coefficient results of the rotating test on the substrate and coated material. A constant normal force of 5 N on the coated sample and 8 N on the substrate material, at an 8 mm radius with a 6 mm diameter WC ball was applied. The TiN coated sample exhibited a lower friction coefficient at 0.55 while the substrate is as high as 0.7.
The surface of the counter bodies and wear track were also measured for this test, and this is shown in , where (a) is the wear track of the TiN coated sample (b) the counter body used and (c) the wear of the substrate lastly the counter body in (d). In (a) the TiN coating showed a great degree of spalling and plastic deformation and in (b) the counter body was worn greatly leaving a plateau on the contact surface. This is opposed to what was observed for the substrate in (c) and (d). As expected, the size of the spalling debris of the TiN coating is larger than those of the substrate, while the degree of plastic deformation in the substrate track is higher than that of the TiN coated sample.
3.3. Scratch test
The scratch tests were conducted based on ISO 20,507; shows the scratch test wear results of the TiN coated sample and the micrographs of the test per failure mode. Three tests were conducted and further summarised in . The average critical load LC1 is the first cracking of the coating at 4.42 N, partial delamination occurs at LC2 at an average critical load of 6.58 and lastly full delamination is recorded at LC3 which was an average critical load of 9.22 N as shown in to (b). The average wear results of the coating are shown in .
shows the scratch wear test results of the substrate. The three tests are summarised in ; an average critical load of 4,98 N at the start of the scratch and an average final critical load of 10.48 was observed. These are slightly higher than those of the TiN coated sample. However, their maximum depth for the TiN coated sample is lower than that of the substrate. Therefore, there was good adhesion between the substrate and TiN and this aided in improving its COF.
Further analysis of the wear scares was conducted on the SEM using EDS, and results are shown in . This was done to chemically analyse the amount of material removed during the TiN coating tests. Based on the micrographs, it is clear that some of the coatings remained intact, or the adhesion seemed better than in other areas of the substrate. On the EDS analysis of the tests, a great amount of Nitrogen was observed still intact in the wear scares of all tests. Some amount of fretting wear is observed in all the tests, this is, however, more prominent in the rotating test.
4. Conclusion
The present study performed the scratch, rotational, and reciprocation wear tests on AISI 4140 low – alloy steel PVD coated with TiN. A 10% change after coating in morphology was reported, a clear indication of the effect of surface roughness on wear resistance. Concerning the tribological tests, the following conclusions can be made:
In the reciprocating wear test, slight fluctuations in friction coefficient were observed, with those of the untreated sample being higher than those of the coated sample, showing an improvement in wear due to coating. Due to this result, the counter body used on the substrate showed signs of plastic deformation, while that used for the coated sample showed no signs of degradation or deformation.
A similar observation with the rotating wear test was reported. However, the counter body used on the coated sample was deformed or almost flattened with a high degree of spalling along the wear track. While the substrate showed a higher degree of plastic deformation in the wear, the track of the counter body remained intact.
During the scratch test, an average cracking load of 4.42 N on the coated sample was observed, followed by an average partial delamination load of 6.58 N and full delamination at 9.22 N. The average critical load of 4.98 N was recorded for the substrate.
TiN coating application on AISI 4140 increased its wear performance, showing excellent adhesion properties. Future work should look into the optimisation of preprocessing parameters and post processing procedures; and their effects on the tribological properties of TiN coated AISI 4140.
Acknowledgements
The authors acknowledge the contributions by Rtech instruments Switzerland and thank the financial support from the University of South Africa and the National Research Council of South Africa (NRF).
Disclosure statement
No potential conflict of interest was reported by the authors.
Additional information
Funding
References
- Holmberg K, Erdemir A. Influence of tribology on global energy consumption, costs and emissions. Friction. 2017;5:263–284. DOI:10.1007/s40544-017-0183-5.
- Zhang S, Ma T, Erdemir A, et al. Tribology of two-dimensional materials: from mechanisms to modulating strategies. Materials Today Elsevier. 2019;26:67–86. DOI:10.1016/j.mattod.2018.12.002.
- Bozkurt YB, Kovacı H, Yetim AF, et al. Tribocorrosion properties and mechanism of a shot peened AISI 4140 low-alloy steel. Surf Coat Technol. 2022;440:128444.
- Baptista A, Silva F, Porteiro J, et al. sputtering physical vapour deposition (PVD) coatings: a critical review on process improvement and market trend demands. Coatings 2018;8:402. https://www.mdpi.com/2079-6412/8/11/402/htm InternetAvailable from: [cited 2022 Dec 5].
- Badiger PV, Desai V, Ramesh MR, et al. Effect of cutting parameters on tool wear, cutting force and surface roughness in machining of MDN431 alloy using Al and Fe coated tools. Mater Res Express. [cited 2022 Dec 6]. 2018;6:016401. InternetAvailable from. 1. https://iopscience.iop.org/article/10.1088/2053-1591/aae2a3
- Walia RS, Singh RP, Butola R, et al. Wear behaviour on a Pin-on-Disc setup for thermal spray of coating using ABAQUS: study and computational analysis. 10.1080/2374068X.2022.2126926. 2022
- Gurumurthy, Sharma SS, Gowrishankar, et al. Study of mechanical properties of dual phase EN19 steel (AISI4140). Indian J Sci Technol. 2016;9(37).
- Baptista A, Silva F, Porteiro J, et al. Sputtering physical vapour deposition (PVD) coatings: a critical review on process improvement and market trend demands. Coatings 2018;8:402 InternetAvailable from: [cited 2021 Dec 6] 10.3390/coatings8110402.
- Hussain M, Askari Rizvi SH, Abbas N, et al. Recent developments in coatings for orthopedic metallic implants. Coatings 2021;11:791. https://www.mdpi.com/2079-6412/11/7/791/htm InternetAvailable from: [cited 2021 Dec 6].
- Xian G, Xiong J, Fan H, et al. Investigations on microstructure, mechanical and tribological properties of TiN coatings deposited on three different tool materials. Int J Refract Metals Hard Mater. 2022;102:105700.
- Daniel M, Friedemann M, Jöhrmann N, et al. Influence of the substrate thermal expansion coefficient on the morphology and elastic stress of CoSb3 thin films. Phys Status Solidi (A) Appl Mater Sci. 2013;210:140–146.
- Sprute T, Tillmann W, Grisales D, et al. Influence of substrate pre-treatments on residual stresses and tribo-mechanical properties of TiAlN-based PVD coatings. Surf Coat Technol. 2014;260:369–379.
- Wang YX, Zhang S, Lee JW, et al. Influence of bias voltage on the hardness and toughness of CrAlN coatings via magnetron sputtering. Surf Coat Technol. 2012;206(24):5103–5107. DOI:10.1016/j.surfcoat.2012.06.041
- Şimşir M, Selçuk B, Aslan N Investigating the effect of testing parameters on adhesive wear using Taguchi method. [Internet]. 2016 [cited 2022 Dec 12];1:493–507.Available from: https://www.tandfonline.com/doi/abs/10.1080/2374068X.2016.1143209.
- Hanief M, Wani MF. Effect of surface roughness on wear rate during running-in of En31-steel: model and experimental validation. Mater Lett. 2016;176:91–93.
- Pereira K, Yue T, Abdel Wahab M. Multiscale analysis of the effect of roughness on fretting wear. Tribol Int. 2017;110:222–231.
- Li B, Li P, Zhou R, et al. Contact mechanics in tribological and contact damage-related problems: a review. Tribol Int 2022;171:107534. https://linkinghub.elsevier.com/retrieve/pii/S0301679X22001074 InternetAvailable from: [cited 2022 Apr 6].
- Alexandrov S, Jeng Y-R, Kuo C-Y, et al. Towards the theoretical/experimental description of the evolution of material properties at frictional interfaces in metal forming processes. Tribol Int 2022;171:107518. https://linkinghub.elsevier.com/retrieve/pii/S0301679X22000913 InternetAvailable from: [cited 2022 Apr 6].
- Badiger PV, Desai V, Ramesh MR, Development and characterization of Ti/TiC/TiN coatings by cathodic arc evaporation technique. Trans Indian Inst Met 2017;70:2459–2464. https://link.springer.com/article/10.1007/s12666-017-1107-9 InternetAvailable from: [cited 2022 Dec 9].
- Jones MI, McColl IR, Grant DM. Effect of substrate preparation and deposition conditions on the preferred orientation of TiN coatings deposited by RF reactive sputtering. Surf Coat Technol. 2000;132(2–3):143–151.
- Chen YM, Yu GP, Huang JH. Characterizing the effects of multiprocess parameters on the preferred orientation of TiN coating using a combined index. Vacuum. 2002;66:19–25.
- Lin CH, Tsai YZ, Duh JG. Effect of grain size on mechanical properties in CrAlN/SiNx multilayer coatings. Thin Solid Films. 2010;518(24):7312–7315.
- Rebouta L, Tavares CJ, Aimo R, et al. Hard nanocomposite Ti–Si–N coatings prepared by DC reactive magnetron sputtering. Surf Coat Technol. 2000;133–134:234–239.
- Mote VD, Purushotham Y, Dole BN Williamson-Hall analysis in estimation of lattice strain in nanometer-sized ZnO particles. 2012 [cited 2022 Aug 10]; Available from: http://www.jtaphys.com/content/2251-7235/6/1/6.
- Zhang L, Yang H, Pang X, et al. Microstructure, residual stress, and fracture of sputtered TiN films. Surf Coat Technol. 2013;224:120–125.
- Chang K, Dong Y, Zheng G, et al. Friction and wear properties of TiAlN coated tools with different levels of surface integrity. Ceram Int. 2022;48(4):4433–4443. DOI:10.1016/j.ceramint.2021.10.105