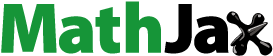
ABSTRACT
Fly ash, a by-product of coal combustion consisting of particulates and flue gases expelled from coal-fired furnaces, has found application as a substitute for organic fillers in the composites industry. In this study, the focus lies on assessing the vibrational and acoustic performance of composites composed of epoxy-based basalt combined with fly ash. Experimental investigations were carried out on specimens containing different weight percentages of fly ash (0%, 10%, 15% and 20% of the epoxy weight) to evaluate free vibration and acoustic impedance. Additionally, the impact of moisture on the vibrational and acoustic properties of Basalt/Fly ash-Epoxy composites was examined by subjecting the specimens to 3 months of ageing in distiled water. The results revealed that increasing the filler content up to 15% led to an increase in natural frequencies (8.5 Hz) and stiffness (3.8 N/mm) of the material, although the damping ratio (0.219) has decreased. Notably, as the specimens aged, the damping ratio is improved by 9%, while the natural frequency and stiffness decline by 9.67% and 12.5%, respectively. The material density emerged as a critical factor influencing the sound absorption capability of the specimens. The inclusion of fly ash in the epoxy matrix has enhanced the acoustic properties of the tested specimens.
1. Introduction
Fibre-reinforced composites (FRC), widely utilised in aerospace, automotive, civil, medical, and sports sectors, represent a rapidly growing segment within the materials industry. FRC are being created in increasing numbers to replace metals and meet the market demand for a high strength-to-weight ratio. While composites have several technical advantages, there are ample of challenges when it comes to recycling them. Although different composite recycling methods are being explored, none of them are cost-effective. As a result, natural fibres are being used more frequently to increase the sustainability. However, natural fibres cannot be regarded as a long-term replacement, because of their hydrophilic nature and inferior performance when compared to synthetic FRCs [Citation1–3].
Basalt Fibre (BF) has gained popularity as a promising and long-term solution to these issues in recent years. Basalt fibre is a high-performance inorganic silicate with outstanding mechanical and thermal qualities that is produced naturally from igneous (volcanic) rock. It has good resistance to chemicals and does not endanger the environment or is not carcinogenic. Moreover, basalt has minimal water absorption behaviour and good acoustic absorption qualities. Basalt fibres’ strong heat resistance makes them ideal for use as insulation in the transportation of hot fluids [Citation1,Citation4–6]. Silicon dioxide (45%), aluminium oxide (12%), calcium oxide (11%), magnesium oxide (10%), and a few other metallic oxides in trace amounts make up the majority of basalt’s perfect composition [Citation7].
Despite having a similar composition to glass fibre (GF), basalt fibre has superior chemical, thermal, and mechanical capabilities, according to studies by Adesina A [Citation8], Monaldo et al. [Citation9], and Dhand et al. [Citation10]. As there are no additives used in the sole process for making basalt, basalt fibres are more affordable than synthetic fibres [Citation11]. Moreover, basalt fibre has demonstrated greater resilience in strong alkalis than GF. The composition of basalt changes at substantially higher temperatures because its operating range is between −200°C and 800°C [Citation12]. In comparison to carbon fibre, basalt fibre has demonstrated a higher strain-to-failure ratio. Due to basalt’s increased chemical resistance, it has found use in a variety of industrial applications, including the chemical industry, construction reinforcement, and even the automotive sector for anti-friction purposes. Basalt fibre provides a better performance-to-cost ratio than the majority of the FRCs already in use, drawing numerous new applications to the sector. The hybridisation of basalt fibre with natural fibre enhanced the vibration and damping factor of the composites. The materials consisting of basalt as skin and natural fibre as core improved the damping factor by 117% as compared to neat basalt fibre reinforced composites. The addition of carbon fibre and silicon carbide enhanced the sound absorption and thermal insulation properties of the basalt fibre reinforced composites [Citation13].
In order to improve the mechanical, thermal, and chemical properties while minimising changes to weight and cost of polymer matrixes, fillers are increasingly being used in conjunction with matrices in polymer composites. Some of the most popular fillers in the composites sector include carbon nanotubes, sawdust, kaolin, rice husk, and fly ash [Citation14–16]. It was shown that adding filler to the matrix significantly decreased the sound transmissibility of composite materials. When fillers are added to the matrix, consistent cavities emerge, which enhances friction within the material and improves the material’s acoustic qualities. The effect of increasing the density and thickness of fibre-boards has been demonstrated in the study by Nandanwar et al. [Citation17] The findings revealed that the sound absorption has a direct correlation with the thickness and inverse relationship with the density of the material.
The structural integrity, damping factor and natural frequency of the basalt fibre reinforced composites were enhanced by the addition of various percentage of Nano clay in epoxy matrix material. An addition of 2% of Nano clay into the epoxy matrix enhanced the natural frequency and damping factor by 4.93% and 10.88% as compared to the specimens containing 0, 0.5,1 and 3% of Nano Clay [Citation18].
Fly ash’s increasing use has been primarily driven by the presence of silanol, aluminol, and other hydroxy groups that modify the filler’s surface polarity. A variety of metal oxides, including silicon oxide (60–70%), aluminium oxide (20–25%), and ferric oxide (2–3%) make up the fly ash [Citation19]. Fly ash also includes cenospheric particles, which contribute to the low overall density of composites [Citation20]. The interface bond between a fibre and the matrix weakens with the exposure to ambient conditions, which will impair the composite’s properties. Moisture intrusion into a composite can result in an unintended increase in mass, material swelling, and unequal stress distribution. These elements also lessen the material’s stiffness, which diminishes the damping behaviour. Hence, to ensure that composites are suitable for cutting-edge applications such as marine and glacial atmospheres, it is necessary to test, analyse, and model the effect of moisture on composites [Citation21]. Chemical modification of fly ash with ultrasonic wave method will enhance the porosity and the sound absorption characteristics. Qi et al. [Citation22] optimised the surface modification process of the fly ash and obtained an average porosity of about 60%. The sound absorption coefficient of the porous fly ash-based materials was found to be 0.353 at low frequencies.
Developing sustainable soundproof material for aerospace and automotive applications is the need of the manufacturing industry. Recently, studies focused on developing composites with fly ash as a filler material for structural and insulation applications. Fly ash can be introduced as a filler material in basalt fibre reinforced composites to enhance the sound absorption and damping properties of the structures. The studies on the effect of fly ash content and moisture gain on acoustic and vibration characteristics of basalt fibre re-enforced composites are yet to be reported. In this work, the influence of fly ash as a filler in basalt fibre epoxy-composite on vibrational and acoustic characteristics is primarily examined. The specimens with different percentage of filler material were fabricated by adopting vacuum bagging technique. To examine the impact of ageing on the material properties, vibrational and acoustic tests were repeated on the aged specimens at the end of the ageing period of 3 months. The test results were compared with results of the pristine specimens to assess the influence of moisture absorption on the damping and acoustic properties of the Basalt/Fly Ash-Epoxy composites.
2. Materials and procedures
2.1. Materials
Bidirectional basalt fibres with a density of 2.8 g/cc, an average thickness of 0.5 mm, and an airborne weight of 400 GSM were purchased from Composites Tomorrow in Vadodara, India. Lapox L-12 epoxy resin, which has a lengthy pot life of 45 minutes at room temperature, was used as the matrix system. The curing ingredient employed was Lapox K-6. Both components were procured from Yuje Enterprises, Bangalore, India. Fly ash was used as the filler material and was procured from the Udupi Thermal Power Plant in Karnataka, India. Laminates were prepared by incorporating four layers of Basalt fibre at a 60% weight fraction. Matrix material was prepared by mixing Epoxy and Hardener with a mixing ratio of 10:1. Using different fly-ash percentages by matrix weight at 0, 10, 15 and 20 wt.%, four fly-ash reinforced basalt fibre laminate compositions were prepared. To ensure a uniform distribution of the epoxy, the laminate was then manually stacked on top of one another on a flat plate mould. The fibres were uniformly impregnated with matrix material using vacuum bagging technique. The prepared laminates were cured for 24 hours at room temperature using a vacuum bagging technique. The manufacturing process adopted in the research work is shown in . The density of the cured laminates was estimated as per Archimedes principle and is shown in . The specimens for vibration and acoustic test were cut to the required dimensions as per the standards, using the Abrasive Water Jet Machining technique.
Table 1. Specifications of cured composite laminates.
2.2. Artificial ageing
Artificial ageing process was performed by immersing the specimens in distiled water for 3 months in ambient conditions. The moisture gain of the specimens were monitored periodically using a digital weighing scale with an accuracy of 0.001 g. The moisture absorption in the laminates at frequent intervals was calculated using the gravimetric Equation (1) [Citation23]:
where Wg is the percentage of moisture gain, W1 is the specimen’s dry weight, and W2 is the specimen’s wet weight. Using the findings, the curve for moisture gain was plotted (), and the specimen’s moisture absorption behaviour was examined using Fick’s diffusion equation. The bulk diffusion coefficient (Dz) of the specimen is estimated according to Equation (2) [Citation23]:
where Mt is the percentage of absorbed moisture at the saturation point, h is the thickness of the specimen. T1 and T2 were picked from the first linear section of the curve, and M1 and M2 were the percentages of the absorbed moisture, corresponding to times T1 and T2, respectively.
2.3. Vibration test
Vibration tests were carried out in accordance with ASTM E756–05 [Citation24] standard in order to understand the impact of filler material on the vibration and damping characteristics of the composite. The tests were conducted in fixed-free boundary conditions as shown in . A PCB accelerometer of sensitivity 101.6 mV/g was fixed at the free end of the specimen to measure the free vibration response of the specimen. NI-9234, a data acquisition (DAQ) interface and NI-LabVIEW 2016 software was used to acquire the experimental data.
2.4. Acoustic testing
The acoustic tests were carried out in accordance with ISO 10,534–2:1998 [Citation25] utilising a BSWA Tech SW422 Impedance Tube configuration as shown in . Transmission loss values were taken for the frequency range of 63–6300 Hz using two specimens with a diameter of 99 mm and 29 mm (). Transmission Loss (TL) of a particular material indicates the effectiveness of the material when used as an acoustic barrier. The portion of transmitted incident energy is called the power transmission coefficient of sound and is represented by the symbol . Transmission loss of the material can be expressed using Equation (3) [Citation26].
3. Results and discussions
3.1. Moisture absorption behaviour
shows the water absorption behaviour of the Basalt/Fly ash and Epoxy composites, and the moisture diffusion coefficient of different specimens is shown in . During the initial ageing period (10–15 days), a rapid absorption of moisture was observed in all the specimens. In the second phase, the moisture gain was steady and slow and followed a linear trend. The moisture absorption curve of all the specimens followed Fickanian Diffusion curve. The diffusion coefficient of the specimens clearly indicates that the moisture gain depends on the percentage of Fly ash content in the composite. BF0FA absorbed 10.41% of moisture at the end of the ageing period. BF10FA, BF15FA and BF20FA specimens absorbed 13.61%, 18.37% and 19.89% of moisture at the end of the ageing period, respectively. Fibre-matrix interphase plays a vital role in the moisture absorption behaviour of the FRP. Absence of filler content in BF0FA resulted in better fibre/matrix interphase and showed higher resistance to moisture ingression. As the filler content is increased, the adhesion between fibre/matrix interphase is reduced and resulted in a higher rate of moisture ingression. The study also indicates that Fly ash is a hydrophilic material and hence increases capillary action of moisture between the laminas. The incorporation of Fly ash with Basalt fibre can produce higher percentage of void content in the material. The presence of these voids in the material will initiate the moisture absorption and the absorbed moisture is stored in these cavities. The presence of moisture in the material will reduce fibre/matrix interface and will result in corrosion of Basalt fibres. These phenomena will reduce the overall structural properties (performance) of the material.
Table 2. Percentage weight change and diffusion coefficient of aged specimen.
3.2. Vibrational analysis
The effect of addition of filler material and ageing on the dynamic properties of Basalt/Fly ash-Epoxy composite was studied using free vibration experiments. The damping ratio of the Basalt/Fly ash-Epoxy composite was calculated from the time domain graph obtained from the free-vibration experiments and by using Equation (4) [Citation26]:
where is the logarithmic decay, Xn-1 and Xn are amplitudes of oscillation at times tn-1 and tn, respectively, and
is the damping ratio.
The addition of fly ash reinforces the composite laminates. It was observed that the effect of increase in mass of the specimen due to the addition of fly ash is less than the effect of increase in stiffness of the specimen, which led to an increase in natural frequency, as given by the following equation[Citation26]:
where is the material’s natural frequency, k is the stiffness, and m is the modal mass in kg.
) shows the natural frequency and stiffness of the pristine and aged Basalt/Fly ash-Epoxy composites. The natural frequency and stiffness of the pristine and aged composites has increased with the addition of filler content. Further investigation of the specimens after the ageing process revealed an increase in mass due to the presence of moisture in the aged specimens but the stiffness decreased and the effect of reduction of stiffness is less than the increase in mass. Due to this, the natural frequency of the specimens was also found to decrease with the ageing process.
Furthermore, the value of the damping ratio for the material was calculated using Equation (6) [Citation26].
where c is the damping coefficient and cc represents the critical damping coefficient of the material.
The damping ratio of the specimen is the cumulative effect of the inherent damping ratio of the matrix, the fibre and the relative displacement between the matrix and the fibre. shows the effect of moisture gain and filler content on damping properties of the Basalt/Epoxy composites. From the experimental data, it was observed that the damping ratio peaked for the BF10FA specimen, indicating the optimum mixing of fillers within the epoxy at that percentage. As observed in the current work, for a concentration above 10%, the reinforcing effect is resulting in an increase in the stiffness. The relative displacement between the matrix and the fibre is reduced resulting in the reduction in the damping ratio. The damping ratio, natural frequency and the stiffness of the specimens display a similar trend in which case the specimen stiffness and the natural frequency increased as the weight concentration of the Fly ash was increased. Considering the experimental data, it is evident that the percentage stiffness reduction is less than the percentage of moisture gain, which causes an overall increase in the specimen’s damping ratio as it ages. The absorption of moisture results in additional damping effect apart from the inherent damping of the matrix, fibre and the fibre-matrix interphase. The result is the overall improvement in the damping ratio of the specimens with ageing in the current observation period. The weight gain due to moisture ingression in BF0FA was 10.45%, while the stiffness reduction was about 12.5% (). All the specimens revealed the same pattern. This demonstrates unequivocally how weight gain and stiffness loss lead to an overall improvement in damping ratio for all the specimens as they are exposed to moisture environment. Similar experimental studies conducted by Pratheesh et al. [Citation27] and Gu Jian et al. [Citation28] observed that the addition of fly ash filler in the matrix material enhanced the damping factor of the polymer matrix composites.
3.3. Acoustic analysis
3.3.1. Transmission loss of pristine specimens
The sound absorption tests were conducted using an impedance tube. The test was performed within a frequency range of 60 Hz to 6500 Hz. ) shows the transmission loss behaviour of pristine and aged Basalt/Fly ash-Epoxy composites. All the specimens showed similar values of transmission loss for frequencies up to 3000 Hz. The specimens peaked between the frequency range of 1000–3000 Hz and then continued to fall. For frequencies ranging between 1000 and 2000 Hz, the BF20FA specimen displayed a peak transmission loss of about 14 dB followed by the BF10FA specimen with a peak of 21 dB at 2000 Hz, the highest among all specimens. The BF0FA specimen showed a peak of 16 dB in the final frequency of 6300 Hz. Out of all the specimens used, the BF15FA specimen showed the most gradual changes in transmission loss throughout, with no evident peak as compared to the other specimens.
Figure 7. Effect of fly ash content and moisture on transmission loss of basalt/epoxy composites a) BF0FA, b) BF10FA, c) BF15FA, d) BF20FA.
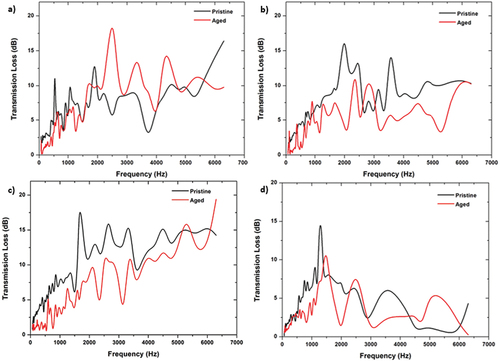
The velocity of wave propagation through solids is given by Equation (7) [Citation29]:
where E is the elastic modulus and ρ is the specimen density. The denser the material, larger the velocity of wave propagation. It can be concluded that with the increase in density, transmission loss wase lowered. This is also evident from the experimental results, where the peak value of TL was shown by pristine specimen and with increase in the weight percentage of fillers, the overall TL values of the specimens were reduced. The transmission loss decreases as density increases and similar kind of results were observed in studies conducted by Novais et al. [Citation30], Arenas et al. [Citation31] and Haung et al. [Citation32].
3.3.2. Transmission loss of aged specimens
However, among the aged specimens, the BF0FA specimen has the maximum peak of 22 dB at roughly 2500 Hz (). All specimens exhibit the same pattern as the pristine tests: a constant TL pattern up to 2000 Hz, then discrete peaks in the 2000–3000 Hz region. The BF15FA specimen, on the other hand, exhibited a significantly more distinct decrease in TL values at higher frequencies, with a maximum of 19 dB at 6300 Hz (). Hence, the medium’s stiffness or density have a direct impact on the transmission loss. The pristine specimen of the studied laminate has the lowest density, and density rises as the reinforcing levels do. Reduction in stiffness of all the aged specimens improved the transmission loss characteristics. The aged-pristine specimen, however, has demonstrated the best acoustic characteristics in the current study.
4. Conclusion
In this study, Basalt/Epoxy composites containing different weight percentage of Fly ash (0%, 10%, 15% and 20%) were successfully fabricated using vacuum bagging technique. The free vibration and acoustic performance of the pristine and the aged specimens were investigated using vibration and Impedance tube set up and following conclusions were drawn from the obtained results.
Addition of Fly ash has increased the density, natural frequency, and stiffness of the composites. The moisture ingression rate of the specimens was also increased with the addition of higher percentage of Fly ash.
The addition of 10% fly ash particles increased the pristine and aged specimen’s damping property by 9%. In comparison to 10% fly ash addition, the damping ratio of the specimens with 15% and 20% Fly ash was reduced by 10% and 35%, respectively.
The acoustic tests showed that the sound absorption capability of all the specimens were marginally improved with ageing due to a general decrease in the specimen stiffness. The best specimen evaluated was the unblemished aged specimen. It can be concluded that, there is no apparent advantage by adding reinforcement with respect to acoustic properties, however damping properties improved with increase in the filler concentration.
The analysis of experimental results showed that the addition of fly ash material into basalt fibre reinforced composites enhanced the damping property of the material, and the developed material can be a potential substitute material for the interior applications of automotives. Fly ash is a by product of thermal power plants which usually end up as a land fill. By utilising fly ash as a filler, eco friendly and sustainable products can be manufactured.
Author contributions
Prajwal Jayaraman – Methodology, Formal Analysis, Data Curation and Writing – Original Draft and Writing; Sriharsha Hegde – Conceptualisation, Methodology, Formal Analysis, Data Curation, Writing – Review & Editing; Thara Reshma I V – Data Curation and Supervision and Writing – Review & Editing; Padmaraj N H – Conceptualisation, Methodology, Formal Analysis, Writing – Original Draft and Writing.
Acknowledgements
The authors were greatly thankful to Manipal Institute of Technology, Manipal Academy of Higher Education for providing the composite manufacturing and testing facility.
Disclosure statement
No potential conflict of interest was reported by the author(s).
Data availability statement
The data will be made available on request.
References
- Chowdhury IR, Pemberton R, Summerscales J. Developments and industrial applications of basalt fibre reinforced composite materials. J Compos Sci. 2022;6(12):6. doi: 10.3390/jcs6120367
- Madenci E, Özkılıç YO, Aksoylu C. The effects of eccentric web openings on the compressive performance of pultruded GFRP boxes wrapped with GFRP and CFRP sheets. Polymers. 2022;14(21):14. doi: 10.3390/polym14214567
- Aksoylu C, Onuralp Özkılıç Y, Emrah Madenci AS. Compressive behavior of pultruded GFRP boxes with concentric openings strengthened by different wrappings. Polymers. 2022;14(19):14. doi: 10.3390/polym14194095
- Bheel N. Basalt fibre-reinforced concrete: review of fresh and mechanical properties. J Build Pathol Rehabil. 2021;6(1):1–9. doi: 10.1007/s41024-021-00107-4
- Liu H, Yu Y, Liu Y, et al. A review on basalt fiber composites and their applications in clean energy sector and power grids. Polymers. 2022;14(12):14. doi: 10.3390/polym14122376
- Surana I, Pandya DJ, Padmaraj NH, et al. Influence of filler material on mechanical and vibration properties of basalt/epoxy composites. Mater Res Express. 2019;6(8):6. doi: 10.1088/2053-1591/ab279e
- Nautiyal M, Shrinet A, Mechanical RM. Thermal and morphological characterization of basalt fibre composite-a review. IOP Conf Ser: Mater Sci Eng. 2020;810(1):810. doi: 10.1088/1757-899X/810/1/012043
- Adesina A. Performance of cementitious composites reinforced with chopped basalt fibres – an overview. Constr Build Mater [Internet]. 2021;266:120970. doi:10.1016/j.conbuildmat.2020.120970
- Monaldo E, Nerilli F, Vairo G. Basalt-based fiber-reinforced materials and structural applications in civil engineering. Compos Struct [Internet]. 2019;214:246–263. doi: 10.1016/j.compstruct.2019.02.002
- Dhand V, Mittal G, Rhee KY, et al. A short review on basalt fiber reinforced polymer composites. Compos Part B Eng [Internet]. 2015;73:166–180. doi: 10.1016/j.compositesb.2014.12.011
- Wei B, Song S, Cao H. Strengthening of basalt fibers with nano-SiO2–epoxy composite coating. Mater Des. 2011;32(8–9):4180–4186. doi: 10.1016/j.matdes.2011.04.041
- Militký J, Kovačič V, Rubnerová J. Influence of thermal treatment on tensile failure of basalt fibers. Eng Fract Mech. 2002;69:1025–1033. doi: 10.1016/S0013-7944(01)00119-9
- Ramraji K, Rajkumar K, Sabarinathan P. Mechanical and free vibration properties of skin and core designed basalt woven intertwined with flax layered polymeric laminates. Proc Inst Mech Eng Part C J Mech Eng Sci. 2020;234(22):4505–4519. doi: 10.1177/0954406220922257
- Hegde S, Padmaraj NH, Siddesh V, et al. Experimental investigation of mechanical sustainability and acoustic performance of fly ash cenosphere/epoxy polymer composites. J King Saud Univ Eng Sci [Internet]. 2021; doi: 10.1016/j.jksues.2021.11.002
- Madenci E, Özkılıç YO, Aksoylu C, et al. Experimental and analytical investigation of flexural behavior of carbon nanotube reinforced textile based composites. Materials. 2023;16(6):2222. doi: 10.3390/ma16062222
- Madenci E, Özkılıç YO, Aksoylu C, et al. Buckling analysis of CNT-Reinforced polymer composite beam using experimental and analytical methods. Materials. 2023;16(2):614. doi: 10.3390/ma16020614
- Nandanwar A, Kiran MC, Varadarajulu KC. Influence of density on sound absorption coefficient of fibre board. Open J Acoust. 2017;7(1):1–9. doi: 10.4236/oja.2017.71001
- Bulut M, Yavuz Ö, Ahmet B, et al. Mechanical and dynamic properties of basalt fiber ‑ reinforced composites with nanoclay particles. Arab J Sci Eng [Internet]. 2020;45(2):1017–1033. doi: 10.1007/s13369-019-04226-6
- Srivastava D, Srivastava K, Gehlot CL. Studies on mechanical and thermal properties of epoxy/fly ash/nanofiller nanocomposite: a review. Int J Civ Eng Technol. 2020;11(2):120–139. doi: 10.34218/IJCIET.11.2.2020.013
- Raja RS, Manisekar K, Manikandan V. Effect of fly ash filler size on mechanical properties of polymer matrix composites. Int J Mining Metall Mech Eng. 2013;1:34–38.
- Pavan A, Dayananda P, Vijaya KM, et al. Influence of seawater absorption on vibrational and tensile characteristics of quasi-isotropic glass/epoxy composites. J Mater Res Technol. 2019;8(1):1427–1433. doi: 10.1016/j.jmrt.2018.10.008
- Liqiang Q, Xu Kl J, Liu K. Porous sound-absorbing materials prepared from fly ash. Environ Sci Pollut Res. 2019;26(22):22264–22272. doi: 10.1007/s11356-019-05573-5
- Wang JUN, Gangarao HOTA, Liang R, et al. Durability and prediction models of fiber-reinforced polymer composites under various environmental conditions: a critical review. J Reinf Plast Compos. 2016;35(3):179–211. doi: 10.1177/0731684415610920
- ASTM. Standard test method for measuring vibration-damping properties of materials. Annu B ASTM Stand. 2005;5:14.
- ISO-10534. Determination of sound absorption coefficient and impedance in impedance tubes. Part 2 Transf method. ISO. 1998;10534:1–27.
- Sujatha C. Vibration and acoustics measurement and signal analysis. New Delhi: Tata McGraw Hill Educ. Priv. Ltd; 2015.
- Pratheesh K, Narayanasamy P, Prithivirajan R, et al. Cenosphere filled epoxy composites: structural, mechanical, and dynamic mechanical studies. Biomass Convers Biorefinery [Internet]. 2023; doi: 10.1007/s13399-023-04154-4
- Gu J, Wu G, Zhao X. Damping properties of fly ash/epoxy composites. J Univ Sci Technol Beijing Miner Metall Mater (Eng Ed). 2008;15(4):509–513. doi: 10.1016/S1005-8850(08)60096-1
- Shaid Sujon MA, Islam A, Nadimpalli VK. Damping and sound absorption properties of polymer matrix composites: A review. Polym Test [Internet]. 2021;104:107388. doi: 10.1016/j.polymertesting.2021.107388
- Novais RM, Carvalheiras J, Senff L, et al. Multifunctional cork – alkali-activated fly ash composites: A sustainable material to enhance buildings’ energy and acoustic performance. Energy Build [Internet]. 2020;210:109739. doi: 10.1016/j.enbuild.2019.109739
- Arenas C, Luna-Galiano Y, Leiva C, et al. Development of a fly ash-based geopolymeric concrete with construction and demolition wastes as aggregates in acoustic barriers. Constr Build Mater. 2017;134:433–442. doi: 10.1016/j.conbuildmat.2016.12.119
- Hung TC, Huang JS, Wang YW, et al. Inorganic polymeric foam as a sound absorbing and insulating material. Constr Build Mater. 2014;50:328–334. doi: 10.1016/j.conbuildmat.2013.09.042