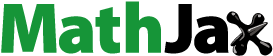
Abstract
Based on the introduction of periodic vibration equipment in a sorption fluids system, the effect of an active mechanism on the heat and mass transfer enhancement in an absorber and the coefficient of performance (COP) enhancement in an absorption chiller was investigated. Different combinations of frequency (15–30 Hz), amplitude (0.1–0.4 mm), and flow rate (0.1–0.5 m3/h), with and without additive (2EH), were compared quantitatively. The results indicated the heat and mass transfer coefficients of the absorber and the COP of the absorption chiller significantly improved—by about 50% under certain conditions. There was a critical value for the amplitude (0.2 mm) and an optimal frequency (25 Hz) in the current study. The additive and solution flow rate also affected performance, but no exclusive conclusion was obtained from our experiment. A properly controlled and applied active mechanism would be of great value not only for the absorption chiller, but also for other chemical engineering applications. The results also begin to fill the knowledge gap between the analysis of mechanical motion and absorption chiller technology. The next phase of work is to find the active mechanism of heat and mass transfer enhancement from the microflow perspective.
Introduction
Social and economic development today must face the threat that primary energy sources are becoming increasingly exhausted. A lithium bromide absorption chiller is an effective refrigeration system that uses low-grade thermal energy for cooling. However, the refrigeration efficiency of an absorption chiller is lacking when compared to a mechanical vapor compression cycle. In recent years, because of the ever-growing price of energy on the one hand, and the existing battle against greenhouse gas (GHG) emissions on the other, absorption refrigeration systems have caught the attention of many researchers and industries. The heat and mass transfer enhancement from a lithium bromide absorption chiller has become a primary focus of current research (Ali Aroon and Khansary Citation2017; Hosseinnia, Naghashzadegan, and Kouhikamali Citation2017; Mortazavi and Moghaddam Citation2016; Mortazavi, Nasr Isfahani, Bigham, and Moghaddam Citation2015; Yang, Du, Niu, Zhang, and Li Citation2014). Among the components in an absorption chiller, the absorber is the most important element of the absorption cooling cycle, and its characteristics have significant effects on the entire system’s performance (Nabil, Bechir, and Slimane Citation2014; Schmid and Spindler Citation2016; Xu, Zhang, and Xiao Citation2016).
A typical absorber made of a conventional lithium bromide absorption system includes a bundle of horizontal tubes with the absorbent solution being sprayed by drippers. The solution is introduced in the tubes as droplets from the drippers. It then flows in the form of liquid film on the tubes. After impingement, the solution spreads over the surface of tube as a fluid film. Because of gravity, the liquid film forms droplets on the underside of the tubes. This style of falling-film absorber is used in most absorption machines because it has several advantages, such as the high heat transfer coefficient, relatively low pressure drop, and sufficient absorption process compared to other tube arrangements. The absorption efficiency depends on many parameters, such as solution flow rate, tube geometry, and surface wetting, which governs flow around and between the tubes (Lazrak et al. Citation2016; Li, Liu, and Liu Citation2016; Shirazi, Taylor, White, and Morrison Citation2016; Thangavelu, Myat, and Khambadkone Citation2017). Although the absorption chiller can use waste heat as an extra energy resource (Barrera et al. Citation2012; Gomri Citation2010), the general adoption is still constrained by its relatively low coefficient of performance (COP). The main barrier to high performance lies in the heat and mass transfer of the absorber side. Because of this, there has been a continuous attempt among previous studies to improve the efficiency of heat and mass transfer of the absorber for both active and passive techniques.
There are many different types of active methods, all of which aim to accelerate heat and mass transfer through the motion mechanism. Heat transfer coefficients were significantly improved in a heat pump over thin fluid films via rotating disks (Aoune and Ramshaw Citation1999). Mechanically induced vibration, as another active technique, including flow-induced vibration on heat exchangers (Cheng, Luan, Du, and Xu Citation2009) and the interfacial mixing effect of vibration in absorbers (Tsuda and Perez-Blanco Citation2001), was also examined in several studies. Another active mechanism, the ultrasound vibration enhancement method, was also investigated (Kiani, Sun, and Zhang Citation2012). In the presence of vibration, heat and mass transfer were both improved regardless of the type of oscillating motion in almost all cases. Since passive techniques are more developed, they proved useful and were widely used to enhance the heat and mass transfer in absorbers. Their application in falling film absorbers with horizontal tubes can be divided into two main categories: (1) tube surface transmutation and (2) solution additives. From these, the primary desired outputs are improving the wettability of the tubes, reducing the surface tension of solution, and increasing the mixing effect over the fluid film. The positive enhancement effect of passive techniques such as surface treatments and roughness, inserted enhancement devices, swirl-flow devices, and geometrical modifications have been tested on a variety of different components and devices (Bergles and Manglik Citation2013). Not surprisingly, the effect of surface treatment and roughness on heat transfer coefficients of falling film absorbers can be found in the literature (Hoffmann, Greiter, Wagner, Weiss, and Alefeld Citation1996; Park, Cho, and Kang Citation2004). Additives are widely used in commercial absorption chillers and are easier and less expensive to apply than other passive methods.
Great potential exists to achieve the required process intensification through (1) development of active heat and mass transfer enhancement techniques and (2) combining the active enhancement mechanism with previously proven and widely used passive enhancement techniques in transport processes. However, the application of active and passive methods together in a falling-film absorber with horizontal tubes and LiBr–water as a working solution may lead to different levels of improvement (Chen, Lin, and Lai Citation2013; Liu, Xu, Han, and Wang Citation2004; Monroy Melendez Citation2010), or even possible deteriorations, of the heat and mass transfer coefficients. Investigating the comprehensive enhancement mechanisms, especially the active mechanism for heat and mass transport processes in absorption devices, becomes an essential step prior to the onset of experimentation and modeling to provide design tools for any of these techniques. Currently, mechanical motion is hardly used in industry to enhance heat and mass transfer and very little research has been conducted in this area.
During the heat and mass transfer process, the vibration movement path can be divided into three general forms—up–down, right–left, or circulatory paths. The motion, then, of the film solution on the tube walls tends to keep its initial moving path due to its inertia force, but also is dragged by the tube movement path due to the friction force of the tube surface (Chen et al. Citation2013; Liu, Xu, and Han 2004). Its resultant movement behavior falls somewhere in between. It is constantly scrubbing between the tube wall and solution bulk, and at the same time, the solution bulk undergoes a disturbance due to the vibration movement, which improves the heat and mass transfer between the tube wall and solution bulk and concurrently encourages the mixing effect (Bergles and Manglik Citation2013). Still, this contention, though true to the best knowledge of the authors, needs to be further proven through theoretical and experimental tests. Although a considerable heat and mass transfer enhancement due to vibration can be expected, the previous studies did not provide a comprehensive and consistent conclusion on the approach, mechanism, or performance in order to support a generalization in falling-film absorbers. More research is needed to understand the effect in terms of the nature and magnitude of the simultaneous use of this active method with passive techniques in falling-film absorbers with a horizontal arrangement of tubes.
Therefore, this study aimed to consider the simultaneous application of an active mechanism with a widely used passive technique. Experiments were conducted to identify the effects of periodic vibration frequency (15–30 Hz) and amplitude (0.1–0.4 mm) on absorption chiller performance. Some other factors, including the flow rate (0.1–0.5 m3/h) and additives, which could impact the effects of heat and mass transfer (Gao, Liu, and Yan Citation2017; Gilani and Ahmed Citation2015; Wang, Wu, and Wang Citation2015) and COP, were also investigated quantitatively. The experiment was separated into two main groups—conditions without additive and conditions with additive (2EH). Comparisons of flow rate (i.e., film thickness), vibration frequency, and vibration amplitude were considered under each condition and compared across the two groups.
Experimental apparatus and tests
According to our preliminary tests, there are several influence factors in heat and mass transfer of a falling film when periodic vibration is introduced to the lithium bromide absorber. These factors include vibration frequency, vibration amplitude, and solution flow rate. In order to consider all of these influence factors, the experimental apparatus consisted of an absorption chiller, an electric vibration system, a sensing and data acquisition system, an in-line concentration detector, and a thermostatic water loop system, as described in .
The absorption chiller provides the absorption process of the falling film; the electric vibration system is installed under the absorption chiller to generate periodic vibration; the sensing and data acquisition system measures and records the heat and mass transfer information of each component; the in-line concentration detector captures the real-time concentrations of weak and strong solutions; and the thermostatic water loop system keeps the cooling and heating water at a constant temperature. Detailed parameters for installation and specifications of each device are given in a previous study (Shen, Yu, and Lau Citation2016). The goal of the current study is to explore the differences in heat and mass transfer and in the COP inside an absorption chiller with and without vibration. Since the heat and mass transfer calculations are so important in making these comparisons, the temperatures, solution flow rates, and solution concentrations in the system were recorded. The procedure to obtain heat and mass transfer information in an absorber has been explored and is detailed in our early discussions (Shen et al. Citation2016).
There are several influence factors on the heat and mass transfer and COP when periodic vibration is introduced to a lithium bromide absorption chiller. These include vibration frequency, vibration amplitude, and solution flow rate. Since additives may have some effect on the mechanism motion, this experiment was separated into a test without additive and a test with the 2EH additive. Six sets of combinations were compared, as grouped in . The ranges of the experimental parameters were determined after tests for the most suitable vibration frequencies and amplitudes that will not result in resonance.
Table 1. Summary of experiment sets.
Experimental results and discussion
The effects of flow rate, frequency, and amplitude without additive
This section discusses the effects of solution flow rate, vibration frequency, and vibration amplitude on heat and mass transfer and COP without additive. Heat and mass transfer and COP enhancement under various combinations are illustrated in . In , it is observed that with different solution flow rates (i.e., film thickness), heat and mass transfer and COP show various improvements under the same vibration condition. With a relatively high solution flow rate, such as 0.5 m3/h, there are very few enhancements of heat and mass transfer inside the absorber and COP in the whole absorption chiller. While under the medial range 0.2–0.4 m3/h of solution flow rate, there are remarkable enhancements of heat and mass transfer and COP, especially under the 0.2–0.3 m3/h condition.
Fig. 2 The effect of different solution flow rates on the heat and mass transfer enhancement (fixed condition at frequency 25 Hz, amplitude 0.2 mm, and without additive).
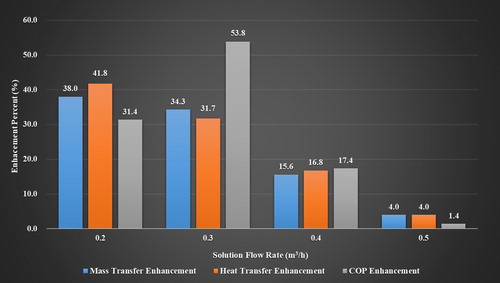
Fig. 3 The effect of different amplitudes on the heat and mass transfer enhancement (fixed condition at frequency 25 Hz, flow rate 0.2 m3/h, and without additive).
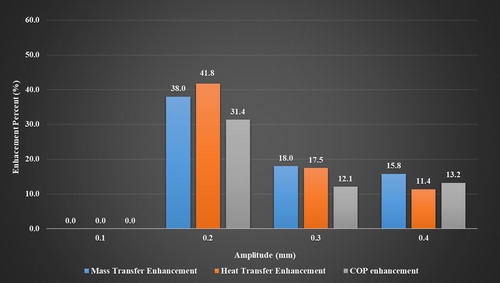
Fig. 4 The effect of different frequencies on the heat and mass transfer enhancement (fixed condition at amplitude 0.2 mm, flow rate 0.3 m3/h, and without additive).
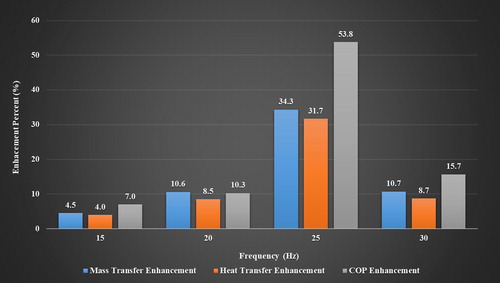
The solution flow rate represents the film thickness, which is suggested as follows (Jayasekara and Halgamuge Citation2013):
(1)
(1)
where Г is the liquid mass flow rate pass unit width,
is the dynamic viscosity of lithium bromide solution,
is the density of lithium bromide solution,
is the steam density under the absorption pressure,
is the gravitational acceleration, and
is the film thickness allocation angle in the vertical direction.
According to EquationEq. (1)(1)
(1) , it is clearly indicated that film thicknesses are quite different under various solution flow rates. For example, the film thicknesses are 0.20, 0.25, 0.29, and 0.33 mm under a solution flow rate of 0.2, 0.3, 0.4, and 0.5 m3/h, respectively. Generally, a higher solution flow rate means a higher solution spray density, which also causes greater film thickness on the tubes. It becomes more difficult to remove and replace the thicker fluid film under the same periodic vibration, which in turn hinders the heat and mass transfer and COP to some extent. Therefore, a very high solution flow rate is not able to significantly enhance the heat and mass transfer process and COP, but a medial range tends to show much better performance due to an appropriate thickness of fluid film.
shows the results under different vibration amplitudes with the flow rate and the vibration frequency and amplitude fixed. It can be observed that there is virtually no (or very little) enhancement of heat and mass transfer and COP under the condition of very low amplitude. That is, this very small vibration amplitude did not induce the film surface to move and produce vortices inside the film. When amplitude is 0.2 mm, the periodic vibration begins to show a very positive effect on heat and mass transfer. The positive effect of amplitude continues from 0.2 mm to 0.4 mm. Considering that a larger amplitude may consume more energy without better enhancement, the amplitude 0.2 mm was selected as optimal in this test. Also of note is that the thickness of liquid film is almost equal to the vibration amplitude when the heat and mass transfer coefficients reach maximum. Therefore, it can be assumed that the enhancement of heat and mass transfer and COP under the periodic vibration might be more significant when the film thickness is nearly equal to the vibration amplitude. However, this hypothesis still needs further study and a theory of this phenomenon is yet undeveloped.
In it can be seen that different frequencies result in various enhancements in the absorber chiller. The frequency 25 Hz presents much better reinforcement throughout the whole test, and triples the enhancement rate when compared to 20 Hz and 30 Hz, and it reaches eightfold compared to 15 Hz. Thus, for this particular type of absorption chiller, 25 Hz is suggested to be the best frequency to improve the performances of heat and mass transfer and COP. By comparing with experimental data in the following section, it is also shown that the frequency 25 Hz has better enhancement under all conditions. Summarized results for the controlled tests are shown in , where varied parameters are highlighted. Film thickness, amplitude to thickness ratio, enhancement percentage, and vibration duration are all considered.
Table 2. Experimental parameters settings and results under various combinations of each factor (without 2EH additive).
The effects of flow rate, frequency, and amplitude with 2EH additive
Passive techniques are more developed, have proven useful, and are widely used to enhance heat and mass transfer in absorbers. In this section, the 2EH additive was mixed together with the lithium bromide solution to further investigate the effects of flow rate, frequency, and amplitude on heat and mass transfer and COP. The summarized results for the controlled tests are shown in , where the varied parameters are highlighted, and the film thickness, amplitude to thickness ratio, enhancement percentage, and vibration duration are considered.
Table 3. Experimental parameters settings and results under various combinations of each factor (with 2EH additive).
Similar to the results without additive, it is indicated that different solution flow rates also result in various influences on the heat and mass transfer enhancement and COP after adding the 2EH additive, as described in . However, compared to the effect of flow rate without additive in , the enhancement rate is not as significant, although their trends are generally the same. For example, improvements are similar to under the solution flow rate range of 0.2–0.4 m3/h. As illustrated in and , it is also shown that the peak performances, with or without additive, both have a solution flow rate of 0.2 m3/h (i.e., 0.2 mm film thickness).
Fig. 5 The effect of different solution flow rates on the heat and mass transfer enhancement (fixed condition at frequency 25 Hz, amplitude 0.2 mm, and with 2EH additive).
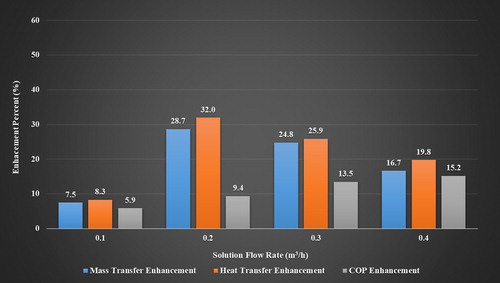
As illustrated in , the amplitudes of 0.2 mm and 0.3 mm present a greater enhancement during the periodic vibration. Similar to the effects of vibration frequency, the differences of enhancement rate with and without additive also lie in the relatively low amplitude (i.e., 0.1 mm) condition. The improvement with 2EH additive reaches as much as 18%, while there is almost no enhancement for the situation without additive, shown in . There are more commonalities for the heat and mass transfer and COP with and without additive. For one, their enhancement trends are somewhat similar at amplitudes above 0.1 mm, but with different improvement rates. Also, an amplitude 0f 0.2 mm presents the best performance in both cases.
Fig. 6 The effect of different amplitudes on the heat and mass transfer enhancement (fixed condition at frequency 25 Hz, flow rate 0.2 m3/h, and with 2EH additive).
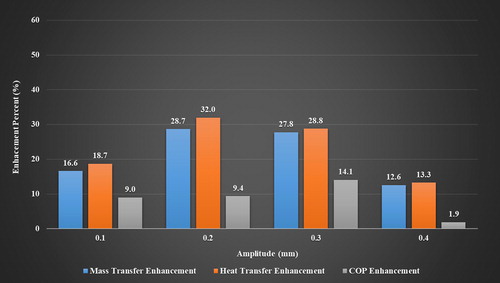
As depicted in , a frequency of 25 Hz presents a greater enhancement under the action of periodic vibration. The improvement rate and optimal frequency are similar to those without additive in . Under the other three frequencies (15, 20, and 30 Hz), the enhancements with additive are just a little greater than those without additive. Whether there is an additive or not shows little impact on the optimal frequency for peak performance of an absorption chiller, found to be about 25 Hz in the current study. However, there are still some differences for the frequencies 20 Hz and 30 Hz. For the falling-film absorption with additive, the improvements of heat and mass transfer are more than 20% under improvements at the frequencies 20 Hz and 30 Hz. For the falling-film absorption without additive, the improvements of heat and mass transfer decrease to about 10%. This may be partially attributed to the periodic vibration, which leads to a larger range of peak frequency.
Fig. 7 The effect of different frequencies on the heat and mass transfer enhancement (fixed condition at amplitude 0.2 mm, flow rate 0.3 m3/h, and with 2EH additive).
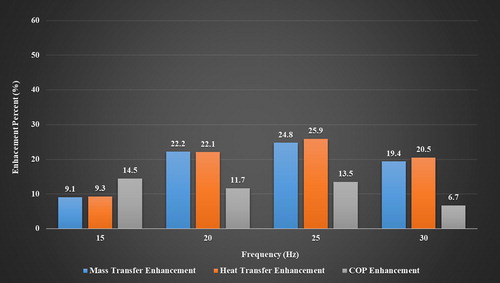
It should be noted that the 2EH additive tends to decrease the maximum enhancement rate and increases the minimum enhancement rate under the conditions of different frequencies, amplitudes, and flow rates, which leads to a more uniform distribution and a larger optimization range of heat and mass transfer and COP improvement. This may be contributed to some overlap of the additive and vibration effect, as the passive and active mechanisms both tend to enhance molecular activity and break the surface tension of fluid film. Therefore, it is more appropriate to employ the 2EH additive to enhance the heat and mass transfer and COP when each determining factor is relatively low or very high, while for medial range of different determining factors, the 2EH may produce a passive effect on the heat and mass transfer and COP enhancement when the periodic vibration is introduced into the whole absorption chiller system.
Discussion of heat and mass transfer and COP enhancements
At present, there remains a lack of systematic understanding of heat and mass transfer and COP enhancements inside an absorber device when the active and passive mechanisms are introduced. The heat and mass transfer inside an absorber is a complicated and coupled process. There are many factors that might impact performance, including the solution flow rate, vibration frequency and amplitude, and fluid additive. Improvements of heat and mass transfer and COP may be caused by the differences in thickness and distribution between the unsaturated layer and saturated layer of the falling film. A previous numerical study on a LiBr solution film performed by Bo et al (Bo, Ma, Lan, Chen, and Chen Citation2012) may suggest some possible explanations, but they only investigated the solution film motion with a small disturbance at the entrance, which is quite different from our experiments. As shown in , a disturbance at the absorber solution entrance has generated a remarkable fluctuation on the fluid film, which clearly indicates that the fluctuation will be much more intense when there is a continuous periodic vibration on the whole absorber system. Under the action of periodic vibration, the movement path of fluid film can be divided into three general forms of up–down, right–left, or circulatory paths. Regardless of which, from one hand, the film solution on the tubes tends to keep its initial moving path due to its inertial force, and from the other, it is dragged by the tube movement path due to the friction force of the tube surface. However, its real movement behavior falls somewhere in between. The periodic vibration will be accompanied by a reciprocating inertia force, which makes equipment move up and down obviously. Therefore, the fluid film may move forward in a way similar to peaks and valleys in waves during periodic vibration, producing a fluctuation on the solution film and reducing the thickness of fluid film. A thinner film decreases the heat transfer resistance through the fluid film and a fluctuating surface increases the mass transfer across the liquid–vapor interface. If the LiBr solution remains on the falling film too long after saturation, the system will have no future performance improvement during the absorption and saturation period.
Fig. 8 The distribution of liquid film with a fluctuation at the absorber solution entrance (Bo et al. Citation2012).
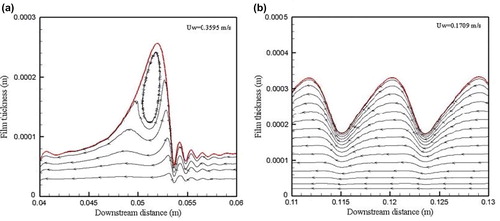
As illustrated in , the distribution of wall shear stress also plays an important role in the fluid film thickness, which further affects the heat and mass transfer processes. In our foregoing experiments, the variations of its direction may produce a backflow effect or even the separation of a boundary layer and consequently generate a large number of viscous vortices inside the liquid films. Specifically, there would be constant scrubbing between tube wall and solution bulk while the solution bulk undergoes a disturbance due to the vibration movement. Therefore, the thermal conduction inside the original liquid film is gradually replaced by the forced convection. The rotational motions of a vortex destroy the internal structure of a boundary layer and bring the low-temperature solution from the near-wall region to the gas–liquid interface. During the absorption process of the falling film, this fluctuation of liquid film improves the temperature uniformity and cooling efficiency, increases the liquid film speed at the interface, and produces extra turbulent disturbance in the gas phase, which is very beneficial for the strong solution to absorb the water steam. It should be noted that more research is still needed to further understand the comprehensive effect of the simultaneous use of this active method with passive techniques in falling-film absorbers with a horizontal arrangement of tubes (also one of our future studies).
Fig. 9 The effect of frequency on the interface velocity with a fluctuation at the absorber solution entrance (Bo et al. Citation2012).
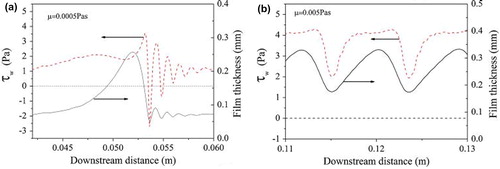
Conclusions
Heat and mass transfer inside an absorber is a complicated and coupled process. There are many factors that might impact the performance, including the solution flow rates and the working conditions of the components. In this study, an active mechanism for enhancing heat and mass transfer was designed and constructed. Performance was evaluated when periodic vibration was introduced to the absorption chiller. Experiments were conducted to identify the effects of vibration frequency and amplitude on absorber performance. Other factors, including flow rate and solution additive, that could impact heat and mass transfer were also investigated. Based on the results for the commercial chiller used, the following conclusions are drawn:
The vibration mechanism on the chiller can impact the heat and mass transfer process in the absorber; therefore, it might be applicable for commercial manufacturers as a technology to improve the performance of absorption chillers.
There is an optimal combination of vibration frequency and amplitude that can best enhance the heat and mass transfer. For this absorption chiller, the optimal conditions are 25 Hz and 0.2–0.3 mm. Without additive, there is a nearly 40% enhancement at the optimal conditions. With 2EH additive, the enhancement is still nearly 30–35%. Although there are also some impacts from other vibration combinations, they seem to be less effective compared to the optimal set.
The presence of the additive changes the performance in terms of the enhancement percentage of heat and mass transfer in the absorber when vibration is introduced.
Additional findings from our experiments include better performance when the amplitude is close to the film thickness. Also, when compared to conditions without additive, the additive seems to increase the optimal range of each factor to some extent. However, these findings are preliminary, and more experiments should be done before a theoretical analysis can be performed.
Additional information
Funding
References
- Ali Aroon, M., and M.A. Khansary. 2017. Generalized similarity transformation method applied to partial differential equations (PDEs) in falling film mass transfer. Computers & Chemical Engineering 101:73–80.
- Aoune, A., and C. Ramshaw. 1999. Process intensification: Heat and mass transfer characteristics of liquid films on rotating discs. International Journal of Heat and Mass Transfer 42(14):2543–56.
- Barrera, M.A., R. Best, V.H. Gómez, O. García-Valladares, N. Velázquez, and J. Chan. 2012. Analysis of the performance of a GAX hybrid (Solar-LPG) absorption refrigeration system operating with temperatures from solar heating sources. Energy Procedia 30:884–92.
- Bergles, A.E., and R.M. Manglik. 2013. Current progress and new developments in enhanced heat and mass transfer. Journal of Enhanced Heat Transfer 20(1):1–15.
- Bo, S., X. Ma, Z. Lan, H. Chen, and J. Chen. 2012. Numerical simulation on wave behaviour and flow dynamics of laminar–wavy falling films: Effect of surface tension and viscosity. Canadian Journal of Chemical Engineering 90(1):61–68.
- Chen, R.-H., Y.-J. Lin, and C.-M. Lai. 2013. The influence of horizontal longitudinal vibrations and the condensation section temperature on the heat transfer performance of a heat pipe. Heat Transfer Engineering 34(1):45–53.
- Cheng, L., T. Luan, W. Du, and M. Xu. 2009. Heat transfer enhancement by flow-induced vibration in heat exchangers. International Journal of Heat and Mass Transfer 52(3):1053–57.
- Gao, H., B. Liu, and Y. Yan. 2017. Numerical simulation of bubbles motion in lifting pipe of bubble pump for lithium bromide absorption chillers. Applied Thermal Engineering 115:1398–406.
- Gilani, S.I.-u.-H., and M.S.M.S. Ahmed. 2015. Solution crystallization detection for double-effect LiBr–H2O steam absorption chiller. Energy Procedia 75:1522–28.
- Gomri, R. 2010. Investigation of the potential of application of single effect and multiple effect absorption cooling systems. Energy Conversion and Management 51(8):1629–36.
- Hoffmann, L., I. Greiter, A. Wagner, V. Weiss, and G. Alefeld. 1996. Experimental investigation of heat transfer in a horizontal tube falling film absorber with aqueous solutions of LiBr with and without surfactants. International Journal of Refrigeration 19(5):331–41.
- Hosseinnia, S.M., M. Naghashzadegan, and R. Kouhikamali. 2017. Numerical study of falling film absorption process in a vertical tube absorber including Soret and Dufour effects. International Journal of Thermal Sciences 114:123–38.
- Jayasekara, S., and S.K. Halgamuge. 2013. Mathematical modeling and experimental verification of an absorption chiller including three dimensional temperature and concentration distributions. Applied Energy 106:232–42.
- Kiani, H., D.W. Sun, and Z. Zhang. 2012. The effect of ultrasound irradiation on the convective heat transfer rate during immersion cooling of a stationary sphere. Ultrasonics Sonochemistry 19(6):1238–45.
- Lazrak, A., F. Boudehenn, S. Bonnot, G. Fraisse, A. Leconte, P. Papillon, and B. Souyri. 2016. Development of a dynamic artificial neural network model of an absorption chiller and its experimental validation. Renewable Energy 86:1009–22.
- Li, Z., L. Liu, and J. Liu. 2016. Variation and design criterion of heat load ratio of generator for air cooled lithium bromide–water double effect absorption chiller. Applied Thermal Engineering 96:481–89.
- Liu, Y.-l., S.-m. Xu, and W. Han. 2004. Experimental study of falling film absorption in a swaying tube using TFE/NMP as working fluid. Journal–Dalian University of Technology 44(1):65–69.
- Liu, Y.-l., S. Xu, W. Han, and B. Wang. 2004. Experimental study of falling film absorption in a swaying tube using TFE/NMP as working fluid. Journal of Dalian University of Technology 1:015.
- Monroy Melendez, D. 2010. Effect of ultrasonic vibration on the mass transfer coefficient in a sieve plate scrubber. Clemson University, Clemson, SC.
- Mortazavi, M., and S. Moghaddam. 2016. Laplace transform solution of conjugate heat and mass transfer in falling film absorption process. International Journal of Refrigeration 66:93–104.
- Mortazavi, M., R. Nasr Isfahani, S. Bigham, and S. Moghaddam. 2015. Absorption characteristics of falling film LiBr (lithium bromide) solution over a finned structure. Energy 87:270–78.
- Nabil, B.H., C. Bechir, and G. Slimane. 2014. Global modeling of heat and mass transfers in spiral tubular absorber of a water–lithium bromide absorption chiller. International Journal of Refrigeration 38:323.
- Park, C.W., H.C. Cho, and Y.T. Kang. 2004. The effect of heat transfer additive and surface roughness of micro-scale hatched tubes on absorption performance. International Journal of Refrigeration 27(3):264–70.
- Schmid, F., and K. Spindler. 2016. Experimental investigation of the auxiliary gas circuit of a diffusion absorption chiller with natural and forced circulation. International Journal of Refrigeration 70:84–92.
- Shen, Z., Y. Yu, and J. Lau. 2016. Experimental setup and methodology on active mechanisms for enhancing heat and mass transfer in sorption fluids. ASHRAE Transactions 122(2):122–133..
- Shirazi, A., R.A. Taylor, S.D. White, and G.L. Morrison. 2016. A systematic parametric study and feasibility assessment of solar-assisted single-effect, double-effect, and triple-effect absorption chillers for heating and cooling applications. Energy Conversion and Management 114:258–77.
- Thangavelu, S.R., A. Myat, and A. Khambadkone. 2017. Energy optimization methodology of multi-chiller plant in commercial buildings. Energy 123:64–76.
- Tsuda, H., and H. Perez-Blanco. 2001. An experimental study of a vibrating screen as means of absorption enhancement. International Journal of Heat and Mass Transfer 44(21):4087–94.
- Wang, J., J. Wu, and H. Wang. 2015. Experimental investigation of a dual-source powered absorption chiller based on gas engine waste heat and solar thermal energy. Energy 88:680–89.
- Xu, Y.-j., S.-j. Zhang, and Y.-h. Xiao. 2016. Modeling the dynamic simulation and control of a single effect LiBr–H2O absorption chiller. Applied Thermal Engineering 107:1183–91.
- Yang, L., K. Du, X. Niu, Y. Zhang, and Y. Li. 2014. Numerical investigation of ammonia falling film absorption outside vertical tube with nanofluids. International Journal of Heat and Mass Transfer 79:241–π50.