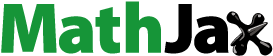
ABSTRACT
High mechanical strength and ionic conductivity of solid-state electrolyte (SSE) are currently conflicting targets that are very difficult to achieve. Polyethylene oxide (PEO) is one of the most common polymers adopted for SSE because of its very high ionic conductivity, but its mechanical strength is very low. This work discusses the manufacturing and testing of PEO blends using polysulfone (PSf) and Lithium bis(trifluoromethanesulfonyl)imide (LiTFSI) to assess the mechanical response under microtensile testing and the ionic conductivity with electrochemical impedance spectroscopy (EIS). Mechanical tests demonstrated a beneficial effect of LiTFSI with significant increase in maximum stress and ductility measured as strain at failure. The blending of PEO and PSf showed promising conductivity values at room temperature with the 90–10 PEO-PSf composition achieving the highest value (1.06 × 10−6 S/cm) and for the 70–30 composition achieving the highest maximum stress (3.5 MPa) with a conductivity of 3.12 × 10−7 S/cm.
Introduction
As the world energy demand increases, energy storage has gained a substantial interest as it plays a key role in many fields from flexible electronics to electric vehicles and renewable energy.[Citation1] Lithium-ion is the most common battery technology, but one of the main concerns is the need for organic liquid electrolytes, which are highly flammable and toxic. The introduction of solid-state electrolyte has solved some of the issues related to degradation, but it does not provide mechanical stability to the battery, making it still prone to damage and requiring the use of heavy shielding. For this reason, there has been a significant effort to develop safer electrolytes, either polymeric, ceramic, or composites, possessing high conductivity and cyclability as well as flexibility and mechanical stability. One of the most studied polymer used as electrolyte is polyethylene oxide (PEO), which is capable of dissolving lithium oxides and can achieve good ionic conductivity at high temperature,[Citation2] but suffers from low mechanical strength. The mechanical strength reported in the literature ranges between 1 and 15 MPa,[Citation3,Citation4] depending on the manufacturing process and molecular weight. On the other hand, there have also been attempts to improve the sustainability of the electrolyte by combining or replacing PEO with natural polymers such as alginate[Citation5] or gum tragacanth,[Citation6] which achieved promising conductivity (3.46 × 10−3 and 1.06 × 10−3 S/cm at RT, respectively), or by using water as a solvent.[Citation7]
One strategy to improve the conductivity of the polymeric electrolyte is the addition of fillers either inactive like SiO2[Citation8] or Al2O3,[Citation9] or active such as Li10GeP2S12[Citation10] or Li1.5Al0.5Ge1.5(PO4)3,[Citation11–13] although the effects of the additives on the mechanical properties are not always reported. Moreno et al.[Citation4] investigated the effect of bentonite blended with low molecular weight (6x105 g/mol LMW) and high molecular weight (4x106 g/mol HMW) PEO, with LiPF6 as lithium salt for an Ethylene Oxide/Lithium (Eo/Li) ratio of 35:1. The bentonite was intercalated with a PEO-salt blend with the same composition of the matrix before mixing them. The tensile strength of LMW-PEO was 0.7 MPa compared with 9.4 MPa for HMW-PEO, and the addition of 3 wt% intercalated bentonite changed the respective values to 7.5 and 8.5 MPa. The conductivity at room temperature was increased from 1.23 × 10−9 S/cm to 1.81 × 10−7 S/cm for LMW-PEO and from 2.45 × 10−9 S/cm to 2.48 × 10−8 S/cm for HMW-PEO. Wen et al.[Citation14] used graphene oxide (GO) as a filler for a PEO electrolyte with LiTFSI salt in a 10:1 Eo/Li ratio. The tensile strength of PEO was about 0.2 MPa and increased to the maximum value of 1.31 MPa with the addition of 1 wt% GO. The observed conductivity was 1.5 × 10−6 S/cm, which was 7 times higher than for PEO alone but decreased for further addition of GO.
Li et al.[Citation15] prepared a composite HMW-PEO electrolyte using several wt% of MnO2 nanosheets as filler, and the Lithium salt was LiTFSI in an Eo/Li ratio of 20:1. The best mechanical performances were obtained at 5wt%, with an achieved maximum strength of about 2 MPa, almost twice that of PEO alone. The room temperature conductivity achieved was 1.95 × 10−5 S/cm and 1.38 × 10−5 S/cm for the filled and unfilled compositions, respectively.
Another strategy to increase the conductivity of PEO is blending with other polymers and plasticizers[Citation16] as reviewed by Xue et al.,[Citation2] since the conductivity was higher in the amorphous phase. However, again, the effect over the mechanical properties was not always reported and would be assumed to decrease when the amorphous phase was increased. Wang et al.[Citation17] used an ultrasonic treatment on a PEO-20 wt% LITFSI electrolyte, increasing the conductivity from 1.8 to 3.2 × 10−6 S/cm but this reduced the yield strength from 0.6 to 0.46 MPa. Lee et al.[Citation18] observed a similar behavior in PEO with LITFSI, which decreased from 14.7 MPa to 2.1 MPa, while the addition of different amounts of Li1.4Al0.4Ge1.6(PO4)3 particles increased the elastic modulus, but not the yield stress and did not significantly impact the conductivity. Ramesh et al.[Citation19] studied the mechanical properties of PVC-PEO blend but the conductivity was not discussed. The yield stress they measured for PEO was 0.67 MPa, which increased with PVC content to 3.62 MPa for a 50–50 composition. The addition of a Lithium methanesulfonate reduced the yield stress to one-fifth of the original value at 20 wt%.
Chun-Guey et al.[Citation20] blended PEO and polyacrylonitrile (PAN) with LiClO4 as the Lithium source, and found that the conductivity increased by adding PAN only when the amount of LiClO4 reached 15 wt%, at which composition the room temperature conductivity was 8.2 × 10−8 S/cm and could be maximized with 3 wt% addition of PAN to 1.2 × 10−7 S/cm.
Lim et al.[Citation21] prepared blended PEO and polymethylmethacrylate (PMMA) at different weight ratios with and without silica aerogel and using ethylene carbonate as plasticizers and LiClO4 as lithium source. The molar ratios of polymer to EC and LiClO4 were 9:1 and 6:1, meaning the salt was about 35.3 wt%. The conductivity at 30°C of PEO was 2.53 × 10−5 S/cm, and the maximum conductivity measured was 6.7 × 10−5 S/cm for a PEO:PMMA molar ratio of 8:1. The addition of silica aerogel increased this value to a maximum of 1.47x10−4 S/cm at 8 wt%. Tao et al.[Citation22] produced a PEO/thermoplastic polyurethane (TPU)[Citation23] at different weight ratios and with 30 wt% of LITFSI. The mechanical strength of PEO was just 0.18 MPa and was increased by the addition of TPU to 1.38 MPa for a 1:3 ratio. However, the room temperature conductivity decreased from 10−5 S/cm for the PEO to 10−6 S/cm for the 1:3 TPU/PEO blend.
Xu et al.[Citation24] prepared a similar composition using a TPU and PEO in a 1:3 ratio with LiTFSI in a 18:1 Eo/Li ratio. They also added Li7La3Zr2O12 (LLZO) nanoparticles to increase the overall performance. The unfilled electrolyte showed a tensile strength of 0.28 MPa, which increased to 0.41 MPa with a 10 wt% of nanoparticles addition, while the conductivity at 30 CC was initially in the order of 10−5 S/cm, and increased to 10−4 S/cm with the addition of NPs.
Xu et al.[Citation25] prepared a blended electrolyte containing PEO and polyvinylidene-fluoride (PVDF) in a 7:3 weight ratio and ZnO as filler. The tensile strength of the PEO/PVDF blend was 1.28 MPa and reached a maximum of 2.35 MPa with 2 wt% of ZnO filler. The conductivity measured at room temperature ranged from 2 × 10−5 S/cm to around 6 × 10−5 S/cm, indicating the optimal 2 wt% concentration, since it increased both mechanical and electrical responses compared to other concentrations.
Li et al.[Citation26] produced a similar PEO-PVDF blend at different weight ratios (up to 50–50) and 20 wt% of LiTFSI. The conductivity of the samples at 30°C ranged from 3 × 10−5 S/cm to 4.2 × 10−5 S/cm with a 10 wt% addition of Li6.2Ga0.1La3Zr1.5Bi0.5O12 LLZTO but no mechanical properties were reported. A more complex approach was developed by Hu et al.[Citation27] designing a multicomponent polyether comprising nitroxide radical TEMPO (2,2,6,6-Tetramethylpiperidin-1-yl)oxyl) groups (T), ethylene oxide brushes (E) and cross-linkable allyl moieties (V). This polyether material could work as a cathode and when integrated through crosslinking with a PEO electrolyte containing 50 wt% of LiTFSI achieved a maximum strength of 2.6 MPa, while the PEO alone and the cathode alone demonstrated 1.6 and 1.25 MPa, respectively. The properties of gel-polymer electrolyte instead are mechanically too low for a structural application, Lee et al.[Citation28] produced a gel based on poly(ethylene glycol) diglycidyl ether (PEGDE), bisphenol A diglycidyl ether (BADGE) and polyethyleneimine (PEI) soaked with 1 M LiPF6 in ethylene carbonate/diethylene carbonate, and their most resistive sample achieved a conductivity above 1 mS/cm with a maximum strength around 220 kPa. A similar work by Ye et al.[Citation29] investigated a ternary blend of PEO, PMMA and polyvinylidene fluoride-co-hexafluoropropylene (PVDF-HFP) with a weight ratio of 1:1.5:1 immersed in a plasticizer made of LiTFSI, succinonitrile (SN) and Fluoroethylene carbonate in a weight ratio of 10:2.5:1. A conductivity of 1.08 × 10−5 S/cm at RT was achieved, but mechanical properties were not reported.
One class of polymers that has rarely been used in electrolytes are polysulfone, which are known for their chemical and mechanical stability. Lu et al.[Citation30] synthesized a copolymer based on PEO and polysulfone, using a PEO to LiTFSI ratio of 8:1 and also produced electrolyte with succinonitrile (SN) in a PSF–PEO: SN: LiTFSI weight ratio of 50:35:15. For the best composition of 35 wt% PEO, the conductivity was 10−7 S/cm at 30 C, while the addition of SN increased it to 10−4 S/cm. The tensile strength at breaking was reported to be 14.7 MPa decreasing to 9.6 MPa with the addition of SN. Xu et al.[Citation31] prepared a composite electrolyte from PEO-polyoxyphenylene sulfone-polyvinylacetate (PVA) and LiTFSI for a ratio of 16:1 Eo/Li. The best composition having 30 wt% of PVA and 20 wt% PSf had a room temperature conductivity in the order of 10−5 S/cm, but mechanical properties again were not reported.
In this work, we investigate the mechanical and electrochemical properties of a blend of a low molecular weight polysulfone with PEO to evaluate its suitability as a solid-state electrolyte for a composite structural battery. The blend is obtained using dimethyl sulfoxide as the solvent, since it is nontoxic compared to other common solvents used for solvent casting like acetonitrile and tetrahydrofuran. The blend obtained does possess improved mechanical strength and ionic conductivities at low salt concentration, which suggests that sulfones could be a valuable alternative polymer to blend with PEO to obtain high-performance electrolyte films.
1. Material and method
1.1. Materials
Polyethylene oxide PEO (Molecular weight 4 × 105 from sigma Aldrich), dimethyl sulfoxide (DMSO) (99% from Sigma Aldrich), polysulfone (PSf) (Molecular weight and 30000–40000 Sigma Aldrich) and Lithium Bis(trifluoromethanosulfonyl)imide LiTFSI (99% Sigma Aldrich) were dried before use in a vacuum oven at 50°C (PEO) and 110°C (PSf and LITFSI) overnight to remove excess moisture. Each of the components was dissolved in 4.5 mL DMSO separately using ultrasonication (PS) or stirring for 4 h (PEO). The solutions were mixed together, and the LITFSI salt was added and stirred for another 4 hrs. Different weight ratios of PEOPS, of 100–0, 90–10, 80–20 and 70–30 with a constant 10 wt% LITFSI were manufactured. The solution was then placed in a plasma-cleaned Teflon mold and dried in a vacuum oven at 60°C for 48 h to obtain a self-supporting continuous film with nominal 0.2 mm thickness and 50 × 50 mm area.
1.2. Sample characterization
To characterize the composite films a number of analytical techniques were carried out. X-ray diffraction (XRD) analysis was performed on a Siemens D5000, to determine the degree of crystallinity using the relationship:
where X is the crystallinity degree, Ic is the intensity of the crystalline peaks and It is the total peak intensity.
A Fourier Transformed Infrared (FT-IR) analysis has been conducted on a Jasco FT/IR 6200 with a sensitivity of 4 cm−1 in the range 4000–650 cm−1.
Microtensile testing was performed on a Deben Microtest tensile stage (Deben UK Ltd., Oxford, UK) with a 200 N cell. Samples were cut to obtain dimension of approximately 25 mm of length and 2 mm of width. The force and displacement values measured during the tests whilst applying a constant displacement of 0.1 mm/min were converted into stress and strain value through the relationships:
where σ is the stress expressed in MPa, F is the force expressed in Newton, A is the cross section expressed in mm2, ϵ is strain, Δl is the variation in length and l0 is the initial length of the sample both expressed in mm. The samples were monitored during the tests using an optical microscopy, and images were taken to capture key failure modes.
Impedance Spectroscopy was performed on a potentiostat Gamry 1000E in the range of 3 MHz to 1 hz using a blocking electrode setup with Stainless steel plates, and the conductivity of the electrolyte was calculated according to[Citation32] using the relationship:
where σ is the conductivity in S/cm, t and A are the thickness and surface area of the electrolyte, respectively, and R is the bulk resistance obtained from the impedance spectroscopy. The value of the bulk resistance was obtained by fitting the data using a circuit for non-ideal blocking electrode[Citation33,Citation34] as shown in . Rb represents the bulk resistance of the electrolyte, CPEd is a constant phase element to represent the non-ideal behavior of the geometrical capacitance of the SPE/electrode structure and the CPEe are constant phase elements to represent the non-ideal behavior of the electric double layer at the SPE/electrode interfaces.
2. Results and discussion
2.1. Crystallinity properties
XRD data for different film compositions are shown in , with a single peak at 19° and triple peaks at 23° characteristic of the PEO crystalline phases.[Citation11,Citation33] The broad background/baseline peak from 15° to 30° confirms the presence of a co-existing amorphous phase, while there is no clear peak associated with PEOx:LiTFSI that has been associated as an indication of poor conduction.[Citation35]
The crystallinity of the samples is summarized in . The crystallinity of pure PEO is usually between 60% and 80% depending on the manufacturing process and molecular weight.[Citation26,Citation36] The reduction in crystallinity observed with the addition of salt is in the range between 70% and 55% comparable to similar compositions reported in the literature, because salt has a plasticizing effect.[Citation37–40] On the other hand, the addition of PSf does not appear to induce a significant variation over the crystallinity, as the lowest observed value is 47% for the PEO-PSf 80:20 composition, suggesting that it is not an effective plasticizer.[Citation31] A similar effect has also been observed by Cheng et al.[Citation13] in PVDF-PSf blends where the PSf was influencing nucleation and crystallization rate of PEO.
Table 1. Crystallinity values.
2.2. Mechanical properties
The mechanical properties of the different blends are identified using the force-displacement response measured during the tensile testing on the polymer samples. Engineering stress–strain curves are derived, and the Young’s Modulus and maximum stress are measured. The curves obtained from the tests are reported in .
Figure 4. Stress strain curves of PEO and a blend PEO -PSf 80–20 both without LiTFSI. The strain is expressed in %.
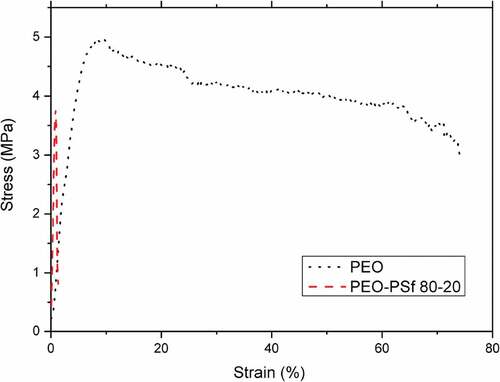
The values obtained are reported in in which the values related to the pure PEO are compared against those measured on the blends with salt.
Table 2. Young’s Modulus and maximum stress values for different blends.
The measured maximum stress of pure PEO was 5 MPa in line with literature data[Citation17,Citation18] where it has been reported as a value between 0.1 and 14 MPa. The addition of PSf shows a different behavior compared to the pure PEO. The blend of PEO and PSf shows a change in ductility as strain at failure, maximum stress and modulus of elasticity. The particular example of the 80–20 PEO-PSf blend compared with PEO for the case where both are without LiTFSI () shows that the modulus of elasticity is significantly higher for the blend (more than double), but the maximum stress is much lower (30% lower than PEO) as is the strain at failure. The PEO-PSf blend has the tendency to show a brittle behavior,[Citation41,Citation42] which might be due to a limited degree of blending in the absence of LiTFSI or a different conformation of the molecular chains, as suggested by FT-IR.
The addition of LiTFSI to the polymer improves the ductility of the PEO-PSf blends and the strain at failure as shown in . This phenomenon has already been reported in the literature[Citation3,Citation37,Citation38] where it has been observed that the addition of LiTFSI reduces the mechanical strength of the PEO. This effect is not observed in the blended polymer samples. While the PEO with LiTFSI can reach a maximum stress of 0.35 MPa, all the blended compositions can sustain a higher maximum stress, with a maximum of 3.5 MPa observed for the PEO-PSf 70–30 case. The variation in terms of elastic modulus is even more pronounced. The PEO alone has a value of 128 MPa, whilst the addition of the salt reduces it to 24 MPa (−75%). Increasing the amount of PSf helps to restore the original value at a concentration of 20 wt% and this further increases up to 208 MPa for 30 wt%. This indicates that the PSf is well integrated within the blend, allowing the film to sustain a higher load even with a similar amount of crystalline and amorphous phases, which indicates that the salt is acting as a compatibilizing agent,[Citation43,Citation44] enhancing the interaction between the PEO and the PSf. This is probably related to the presence of polar groups and the similarity between the salt and the PSf which both possess sulfur and oxygen bonds.
shows the difference in fracture mode between the pure PEO () and the blend with LiTFSI (). The pure PEO shows necking whilst the blend shows a brittle fracture with significant reduction of the transversal cross section as the sample approaches failure. In an actual application, it would be preferable to have a high stiffness with less deformation than the opposite, so the improvement obtained would be suitable for a structural battery application.
2.3. FT-IR analysis
The main peaks for the PEO are visible in and can be associated with different stretching and bending of C-C, C-H and C-O, but a significant one is the triplet centered around 1090 cm−1 which belongs to the C-O-C stretching ()[Citation4] which is typical of the crystalline phase.[Citation45] The reduction in intensity between the pure PEO sample and the other composition is an indication that the crystallinity is reduced. By incorporating PSf in PEO, the absorption band of C-H stretching around 2880 cm−1 () is changed suggesting an interaction between PSf and PEO[Citation46] because of the presence of similar bonds in PSf and LITFSI.
Figure 6. IR spectra of various manufactured blends of PEO-PSf with LiTFSI compared against the spectrum of the pure PEO.
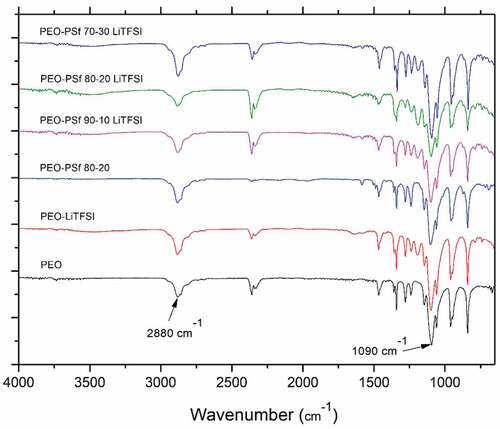
Since they both have SO2 bonds, the main differences are the peak at 1200 cm−1 () which does not appear in the absence of salt and can be assigned to the CF3 stretching[Citation47] and the small peak at 865 cm−1 () which is associated with the benzene ring[Citation31] and does not show up in the absence of PSf. The CF3 peaks changes intensity at different PSf content suggesting a stronger interaction with the PEO-PSf 80–20 blends which would reduce its dissociation and correlate with the lower conductivity of the sample. The two independent peaks at 1359 cm−1 and 1340 cm−1 () can be related to the wagging of the methylene group (-CH3) in the crystalline phase. Its presence further confirms the semi-crystalline nature of the films, these two peaks tend to merge and become broader,[Citation43] suggesting that LiTFSI and PSf combined influenced the crystallinity of PEO and this effect is particularly marked for the PEO-PSf 80–20 blend.
The PEO-PSf 80–20 blend showed a brittle behavior compared to all other films and is the only sample showing a different relative ratio between the peaks at 1250 cm−1 and 1280 cm−1 (). These are associated with CH2 twisting,[Citation48] and according to Kim et al.[Citation49] the relative ratio of these bands can be related to a different chain orientation induced by a different coordination of the ether bonds.
2.4. Electrochemical/electrical properties
Nyquist plots for the various electrolytes measured at 20°C data are presented in , excluding the samples without Lithium salts due to their expected insufficient conductivity in comparison to LiTFSI containing samples.
The electrolyte containing PSf has a higher impedance compared to PEO, but this behavior is non-linear. Conductivity values are calculated from the EIS and reported in . The sample containing 10% of PSf has a slightly lower conductivity 1.06 × 10−6 S/cm compared to the sample without, 1.76 × 10−6 S/cm. The PEO-PSf 80–20 blend resulted in the lowest conductivity of 2.03 × 10−7 S/cm, despite having the lowest crystallinity, which indicates that it is not the only parameter influencing the conductivity, for this system at least, as further confirmed by the properties measured for the PEO-PSf 70–30 blend with a conductivity of 3.12 × 10−7 S/cm.
Table 3. Summary of conductivity values.
The low-temperature conductivity value for the PEO-LiTFSI system is higher than reported in the literature when compared with similar or slightly higher ethylene oxide/lithium ratios.[Citation17,Citation18,Citation40,Citation50] The higher conductivity measured at low concentration of LiTFSI can probably be related to the presence of trapped DMSO, due to its high boiling point, which makes it difficult to fully remove compared to other solvents, which have also been used as electrolytes, as for instance by Xu et al.[Citation51] In fact, the presence of traces of solvent within a solid electrolyte has been discussed as a potential way to improve conductivity,[Citation52] as variations have been observed as dependent on the drying procedure followed.
3. Conclusion
Solid electrolytes with a percentage in weight of PSf equal to 0, 10%, 20% and 30%, and 10% in weight of LiTFSi have been manufactured and tested using DMSO as a casting solvent. Samples were characterized with XRD, FT-IR, microtensile testing and Electrochemical Impedance Spectroscopy. The addition of PSf did not offer a significant impact over the crystallinity of the PEO, in comparison to the added LiTFSI salt. The main FTIR characteristic peaks associated with PSf, LiTFSI salt and PEO were identified, suggesting an interaction between the two polymers. The blends of PEO and PSF were more brittle than PEO, while in the presence of LiTFSI all samples had increasing tensile strength with the amount of PSf. The conductivity values of PEO-PSf blend were lower than the PEO alone, with 10 wt% of PSf reducing the conductivity by less than 50%. It has also been observed that the sample with 30% in weight of PSf had a conductivity slightly higher than the sample with 20% in weight due to a stronger interaction between the PEO-PSf 80–20 and LiTFSI.
Acknowledgments
The authors would like to acknowledge and thank Andrea Preacher for their support with the mechanical testing. All data generated or analysed during this study are included in this published article
Disclosure statement
The authors declare that they have no known competing financial interests or personal relationships that could have appeared to influence the work reported in this work.
Additional information
Notes on contributors
Francesco Gucci
Dr Francesco Gucci obtained his PhD in materials science at Queen Mary University of London in 2019. Dr Gucci later joined Cranfield University as a research fellow in Precision Engineering.
Marzio Grasso
Dr Marzio Grasso is currently a Senior Lecturer at Cranfield University. He graduated in Mechanical Engineering from the University Federico II (Naples) where he also completed a PhD in Engineering of Materials and Structures. He is currently involved in the development and testing of multifunctional materials.
Christopher Shaw
Dr Chris Shaw obtained his BSc(Hons) in Chemistry from the University of Liverpool in 1985 before joining Cranfield University to study an MSc in Molecular. He joined the Microsystems and Nanotechnology Group at Cranfield University in 1997, and is now a Research Fellow in the Surface Engineering and Precision Institute within the Manufacturing Department.
Glenn Leighton
Dr Glenn Leighton is currently working as a Senior Lecturer in functional surface engineering at Cranfield University in the field of materials science & manufacturing. He has a PhD and MSc from Cranfield University in MEMS and Nanotechnology.
Veronica Marchante Rodriguez
Dr Veronica Marchante-Rodriguez studied Chemical Engineering at the University of Alicante. Following that, she started her PhD at the University of Alicante in collaboration with the Chemical Engineering Department and the Optics Department. Dr Marchante-Rodriguez has extensive experience in the application of the nanoclay-based pigments. Currently, she is a Research Fellow in Polymer Nanocomposites at Cranfield University.
James Brighton
Prof James Brighton has over 22 years' experience relating to off road vehicle dynamics, terra-mechanics, tyre and track system modelling, advanced vehicle instrumentation and lightweight material structures and his current clients span the globe.
References
- Colombo, R. L.; Firrao, D. Sulla storia degli studi di frattura in Italia. Frat. ed Integrità Strutt. 2008, 11, 19–24. DOI:10.3221/igf-esis.01.02.
- Xue, Z.; He, D.; Xie, X. Poly(ethylene Oxide)-based Electrolytes for lithium-ion Batteries. J. Mater. Chem. A. 2015, 3(38), 19218–19253. DOI: 10.1039/c5ta03471j.
- Lee, J.; Rottmayer, M.; Huang, H. Impacts of Lithium Salts on the Thermal and Mechanical Characteristics in the Lithiated PEO/LAGP Composite Electrolytes. J. Compos. Sci. 2022, 6(1), 1–9. DOI: 10.3390/jcs6010012.
- Moreno, M.; Quijada, R.; Santa Ana, M. A.; Benavente, E.; Gomez-Romero, P.; González, G. Electrical and Mechanical Properties of Poly(ethylene Oxide)/intercalated Clay Polymer Electrolyte. Electrochim. Acta. 2011, 58(1), 112–118. DOI: 10.1016/j.electacta.2011.08.096.
- Samsudin, A. S.; Suhaimi, N. S.; Ghazali, N. M. The Correlation of Li+ Carrier Towards Immittance Conduction Properties on Alginate-PVA-LiNO3 Complexes-Based Solid Polymer Electrolytes System. J. Electron. Mater. 2023. DOI: 10.1007/s11664-022-10168-x.
- Jenova, I.; Venkatesh, K.; Karthikeyan, S.; Madeswaran, S.; Joice Sheeba, D. Study on the Electrical Properties of Gum Tragacanth - LiClO4 Natural Polymer Electrolyte. Mater. Today Proc. 2022. DOI: 10.1016/j.matpr.2022.12.235.
- Cho, Y.; Lee, S.; Kim, H.; Kim, Y. Lithium Polymer Supercapacitors with water-processable Branched Poly(ethylene Imine)-based solid-state Electrolytes. J. Energy Storage. 2023, 57(October 2022), 106010. DOI: 10.1016/j.est.2022.106010.
- Ji, K. S.; Moon, H. S.; Kim, J. W.; Park, J. W. Role of Functional nano-sized Inorganic Fillers in Poly(ethylene) oxide-based Polymer Electrolytes. J. Power Sources. 2003, 117(1–2), 124–130. DOI: 10.1016/S0378-7753(03)00159-9.
- Tambelli, C. C.; Bloise, A. C.; Rosário, A. V.; Pereira, E. C.; Magon, C. J.; Donoso, J. P. Characterisation of PEO-Al2O3 Composite Polymer Electrolytes. Electrochim. Acta. 2002, 47(11), 1677–1682. DOI: 10.1016/S0013-4686(01)00900-8.
- Zhao, Y.; Wu, C.; Peng, G.; Chen, X.; Yao, X.; Bai, Y.; Wu, F.; Chen, S.; Xu, X. A New Solid Polymer Electrolyte Incorporating Li10GeP2S12 into A Polyethylene Oxide Matrix for all-solid-state Lithium Batteries. J. Power Sources 2016, 301, 47–53. DOI: 10.1016/j.jpowsour.2015.09.111.
- Zhao, Y.; Huang, Z.; Chen, S.; Chen, B.; Yang, J.; Zhang, Q.; Ding, F.; Chen, Y.; Xu, X. A Promising PEO/LAGP Hybrid Electrolyte Prepared by A Simple Method for all-solid-state Lithium Batteries. Solid State Ionics 2016, 295, 65–71. DOI: 10.1016/j.ssi.2016.07.013.
- Neha, B.; Dalvi, A. Fast Ionic PEO-NaCF3SO3-Na3Zr2Si2P3O12 Membranes for all-solid-state Energy Storage Devices. Mater. Sci. Eng. B Solid-State Mater. Adv. Technol. 2023, 289(December 2022), 116252. DOI: 10.1016/j.mseb.2022.116252.
- Cheng, Q.; Cui, Z.; Li, J.; Qin, S.; Yan, F.; Li, J. Preparation and Performance of Polymer Electrolyte Based on Poly(vinylidene Fluoride)/polysulfone Blend Membrane via Thermally Induced Phase Separation Process for Lithium Ion Battery. J. Power Sources. 2014, 266, 401–413. DOI: 10.1016/j.jpowsour.2014.05.056.
- Wen, J.; Zhao, Q.; Jiang, X.; Ji, G.; Wang, R.; Lu, G.; Long, J.; Hu, N.; Xu, C. Graphene Oxide Enabled Flexible PEO-Based Solid Polymer Electrolyte for All-Solid-State Lithium Metal Battery. ACS Appl. Energy Mater. 2021, 4(4), 3660–3669. DOI: 10.1021/acsaem.1c00090.
- Li, Y.; Sun, Z.; Liu, D.; Gao, Y.; Wang, Y.; Bu, H.; Li, M.; Zhang, Y.; Gao, G.; Ding, S., et al. A Composite Solid Polymer Electrolyte Incorporating MnO 2 Nanosheets with Reinforced Mechanical Properties and Electrochemical Stability for Lithium Metal Batteries. J. Mater. Chem. A 2020, 8(4), 2021–2032. DOI: 10.1039/c9ta11542k.
- Yuan, Y., Xiuping, P., Bin, W., Kesi, X., Zhengqian, L., Yitian, M., Bin, Z., Yonghui, S., Hai, L. Solvate Ionic liquid-derived Solid Polymer Electrolyte with Lithium Bis(oxalato) Borate as a Functional Additive for solid-state Lithium Metal Batteries. J. Mater. Chem. A. 2022, 1301–1311. DOI: 10.1039/d2ta07393e.
- Wang, H.; Cui, X.; Zhang, C.; Gao, H.; Du, W.; Chen, Y.; Alves, L. Promotion of Ionic Conductivity of PEO-Based Solid. Polymers. 2020, 13, 1–16. DOI: 10.3390/polym13010001.
- Lee, J.; Howell, T.; Rottmayer, M.; Boeckl, J.; Huang, H. Free-Standing PEO/LiTFSI/LAGP Composite Electrolyte Membranes for Applications to Flexible Solid-State Lithium-Based Batteries. J. Electrochem. Soc. 2019, 166(2), A416–A422. DOI: 10.1149/2.1321902jes.
- Ramesh, S.; Winie, T.; Arof, A. K. Investigation of Mechanical Properties of Polyvinyl chloride-polyethylene Oxide (PVC-PEO) Based Polymer Electrolytes for Lithium Polymer Cells. Eur. Polym. J. 2007, 43(5), 1963–1968. DOI: 10.1016/j.eurpolymj.2007.02.006.
- Wu, C. G.; Wu, C. H.; Lu, M. I.; Chuang, H. J. New Solid Polymer Electrolytes Based on PEO/PAN Hybrids. J. Appl. Polym. Sci. 2006, 99(4), 1530–1540. DOI: 10.1002/app.22250.
- Lim, Y. S.; Jung, H. A.; Hwang, H. Fabrication of PEO-PMMA-LiClO4-Based Solid Polymer Electrolytes Containing Silica Aerogel Particles for All-Solid-State Lithium Batteries. Energies. 2018, 11(10), 2559. DOI: 10.3390/en11102559.
- Tao, C.; Gao, M.-H.; Yin, B.-H.; Li, B.; Huang, Y.-P.; Xu, G.; Bao, -J.-J. A Promising TPU/PEO Blend Polymer Electrolyte for all-solid-state Lithium Ion Batteries. Electrochim. Acta 2017, 257, 31–39. DOI: 10.1016/j.electacta.2017.10.037.
- Dixit, A.; Sabnis, A.; Balgude, D.; Kale, S.; Gada, A.; Kudu, B.; Mehta, K.; Kasar, S.; Handa, D.; Mehta, R., et al. Synthesis and Characterization of Citric Acid and Itaconic acid-based two-pack Polyurethane Antimicrobial Coatings. Polym. Bull. 2023, 80, 2187–2216. DOI: 10.1007/s00289-022-04638-9.
- Xu, H.; Huang, S.; Qian, J.; Liu, S.; Li, L.; Zhao, X.; Zhang, W. Safe solid-state PEO/TPU/LLZO Nano Network Polymer Composite Gel Electrolyte for Solid State Lithium Batteries. Colloids Surfaces A Physicochem. Eng. Asp 2022, 653, 130040. DOI: 10.1016/j.colsurfa.2022.130040.
- Xu, Y.; Li, J.; Li, W. Evolution in Electrochemical Performance of the Solid Blend Polymer Electrolyte (PEO/PVDF) with the Content of ZnO Nanofiller. Colloids Surf. A. 2022, 632(October 2021), 127773. DOI: 10.1016/j.colsurfa.2021.127773.
- Li, J.; Zhu, K.; Yao, Z.; Qian, G.; Zhang, J.; Yan, K.; Wang, J. A Promising Composite Solid Electrolyte Incorporating LLZO into PEO/PVDF Matrix for all-solid-state lithium-ion Batteries. Ionics 2020, 26(3), 1101–1108. DOI: 10.1007/s11581-019-03320-x.
- Hu, W.; You, D.; Wei, W.; Xiong, H. Robust Compound Elastomers of Integrated Polymer Cathode and Electrolyte for high-performance all-solid-state Lithium Battery. J. Power Sources. 2023, 555(October 2022), 232338. DOI: 10.1016/j.jpowsour.2022.232338.
- Lee, D.; Park, C.; Choi, Y. G.; Rho, S.; Lee, W. B.; Park, J. H. Selective and Uniform Li-ion Boosting Polymer Electrolytes for dendrite-less quasi-solid-state Batteries. J. Memb. Sci. 2023, 668(December 2022), 121258. DOI: 10.1016/j.memsci.2022.121258.
- Ye, X.; Liang, J.; Hu, J.; Wu, D.; Li, Y.; Ouyang, X.; Zhang, Q.; Ren, X.; Liu, J. An ultra-thin Polymer Electrolyte for 4.5 V High Voltage LiCoO2 quasi-solid-state Battery. Chem. Eng. J. 2023, 455(P2), 140846. DOI: 10.1016/j.cej.2022.140846.
- Lu, Q.; Fang, J.; Yang, J.; Yan, G.; Liu, S.; Wang, J. A Novel Solid Composite Polymer Electrolyte Based on Poly(ethylene Oxide) Segmented Polysulfone Copolymers for Rechargeable Lithium Batteries. J. Memb. Sci. 2013, 425–426, 105–112. DOI: 10.1016/j.memsci.2012.09.038.
- Xu, L.; Wei, K.; Cao, Y.; Ma, S.; Li, J.; Zhao, Y.; Cui, Y.; Cui, Y. The Synergistic Effect of the PEO-PVA-PESf Composite Polymer Electrolyte for all-solid-state lithium-ion Batteries. RSC Adv. 2020, 10(9), 5462–5467. DOI: 10.1039/c9ra09645k.
- Vadhva, P.; Hu, J.; Johnson, M. J.; Stocker, R.; Braglia, M.; Brett, D. J. L.; Rettie, A. J. E. Electrochemical Impedance Spectroscopy for All-Solid-State Batteries: Theory, Methods and Future Outlook. ChemElectroChem 2021, 8(11), 1930–1947. DOI: 10.1002/celc.202100108.
- Qian, X.; Gu, N.; Cheng, Z.; Yang, X.; Wang, E.; Dong, S. Impedance Study of (PEO)10LiClO4-Al2O3 Composite Polymer Electrolyte with Blocking Electrodes. Electrochim. Acta. 2001, 46(12), 1829–1836. DOI: 10.1016/S0013-4686(00)00723-4.
- Bandeira, M. C. E.; Franco, C. V.; Martini, E. Electrochemical Impedance Spectroscopy of poly{pyrrole-trans-[RuCI2(pmp)4]} Copolymer Films Deposited on Platinum Electrodes. J. Solid State Electrochem. 1999, 3(4), 210–214. DOI: 10.1007/s100080050149.
- Marzantowicz, M.; Dygas, J. R.; Krok, F.; Florjańczyk, Z.; Zygadło-Monikowska, E. Influence of Crystalline Complexes on Electrical Properties of PEO:LiTFSI Electrolyte. Electrochim. Acta. 2007, 53(4), 1518–1526. DOI: 10.1016/j.electacta.2007.03.032.
- Hagberg, J.; Maples, H. A.; Alvim, K. S. P.; Xu, J.; Johannisson, W.; Bismarck, A.; Zenkert, D.; Lindbergh, G. Lithium Iron Phosphate Coated Carbon Fiber Electrodes for Structural Lithium Ion Batteries. Compos. Sci. Technol. 2018, 162(Jul), 235–243. DOI: 10.1016/j.compscitech.2018.04.041.
- Homann, G.; Stolz, L.; Nair, J.; Laskovic, I. C.; Winter, M.; Kasnatscheew, J. Poly(Ethylene Oxide)-based Electrolyte for Solid-State-Lithium-Batteries with High Voltage Positive Electrodes: Evaluating the Role of Electrolyte Oxidation in Rapid Cell Failure. Sci. Rep. 2020, 10(1), 2–10. DOI: 10.1038/s41598-020-61373-9.
- Andrews, W. T.; Liebig, A.; Cook, J.; Marsh, P.; Ciocanel, C.; Lindberg, G. E.; Browder, C. C. Development of a PEO-based Lithium Ion Conductive Epoxy Resin Polymer Electrolyte. Solid State Ionics 2018, 326(August), 150–158. DOI: 10.1016/j.ssi.2018.09.013.
- Carrasco-Amador, J. P.; Diaz-Parralejo, A.; Macías-García, A.; Díaz-Díez, M. Á.; Olivares-Marín, M. Preparation and Characterization of ZrO2/Y2O3/Al2O3-based Microstructured Multilayer sol–gel Coatings. Ceram. Int. 2017, 43(16), 14210–14217. DOI: 10.1016/j.ceramint.2017.07.166.
- Klongkan, S.; Pumchusak, J. Effects of Nano Alumina and Plasticizers on Morphology, Ionic Conductivity, Thermal and Mechanical Properties of PEO-LiCF3SO3 Solid Polymer Electrolyte. Electrochim. Acta. 2015, 161, 171–176. DOI: 10.1016/j.electacta.2015.02.074.
- Vilakati, G. D.; Hoek, E. M. V.; Mamba, B. B. Probing the Mechanical and Thermal Properties of Polysulfone Membranes Modified with Synthetic and Natural Polymer Additives. Polym. Test. 2014, 34, 202–210. DOI: 10.1016/j.polymertesting.2014.01.014.
- Qing Liang, H.; Nan Li, H.; Hao Yu, H.; Ting Zhou, Y.; Kang Xu, Z. Polysulfone Membranes via Thermally Induced Phase Separation. Chin. J. Polym. Sci. 2017, 35(7), 846–856. DOI: 10.1007/s10118-017-1943-4.
- Yang, S.; Liu, Z.; Jiao, Y.; Liu, Y.; Luo, W. Study on the Compatibility and Crystalline Morphology of NBR/PEO Binary Blends. J. Mater. Sci. 2013, 48(19), 6811–6817. DOI: 10.1007/s10853-013-7486-3.
- Wang, S.; Min, K. Solid Polymer Electrolytes of Blends of Polyurethane and Polyether Modified Polysiloxane and Their Ionic Conductivity. Polymer. 2010, 51(12), 2621–2628. DOI: 10.1016/j.polymer.2010.04.038.
- Vrandečić, N. S.; Erceg, M.; Jakić, M.; Klarić, I. Kinetic Analysis of Thermal Degradation of Poly(ethylene Glycol) and Poly(ethylene Oxide)s of Different Molecular Weight. Thermochim. Acta. 2010, 498(1–2), 71–80. DOI: 10.1016/j.tca.2009.10.005.
- Kim, H. W.; Park, H. B. Gas Diffusivity, Solubility and Permeability in polysulfone-poly(ethylene Oxide) Random Copolymer Membranes. J. Memb. Sci. 2011, 372(1–2), 116–124. DOI: 10.1016/j.memsci.2011.01.053.
- Rey, I.; Lassègues, J. C.; Grondin, J.; Servant, L. Infrared and Raman Study of the PEO-LiTFSI Polymer Electrolyte. Electrochim. Acta. 1998, 43(10–11), 1505–1510. DOI: 10.1016/S0013-4686(97)10092-5.
- Waly, A. L.; Abdelghany, A. M.; Tarabiah, A. E. Study the Structure of Selenium Modified Polyethylene oxide/polyvinyl Alcohol (PEO/PVA) Polymer Blend. J. Mater. Res. Technol. 2021, 14, 2962–2969. DOI: 10.1016/j.jmrt.2021.08.078.
- Kim, K.; Kuhn, L.; Alabugin, I. V.; Hallinan, D. T. Lithium Salt Dissociation in Diblock Copolymer Electrolyte Using Fourier Transform Infrared Spectroscopy. Front. Energy Res. 2020, 8(September), 1–17. DOI: 10.3389/fenrg.2020.569442.
- Ben Youcef, H.; Garcia-Calvo, O.; Lago, N.; Devaraj, S.; Armand, M. Cross-Linked Solid Polymer Electrolyte for All-Solid-State Rechargeable Lithium Batteries. Electrochim. Acta. 2016, 220, 587–594. DOI: 10.1016/j.electacta.2016.10.122.
- Xu, D.; Wang, Z. L.; Zhang, L. L.; Zhang, X. B.; Zhang, X.-B. Novel DMSO-based Electrolyte for High Performance Rechargeable Li-O2 Batteries. Chem. Commun. 2012, 48(55), 6948–6950. DOI: 10.1039/c2cc32844e.
- Foran, G.; Mankovsky, D.; Verdier, N.; Lepage, D.; Prébé, A.; Aymé-Perrot, D.; Dollé, M. The Impact of Absorbed Solvent on the Performance of Solid Polymer Electrolytes for Use in Solid-State Lithium Batteries. iScience 2020, 23(10), 1–16. DOI: 10.1016/j.isci.2020.101597.