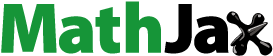
ABSTRACT
Throughout their service life, carbon fiber reinforced epoxy composites are exposed to a range of environmental conditions. The long-term durability of these composites is an ongoing concern because exposure to moisture can degrade the polymeric matrix and deteriorate the mechanical properties of the composite. Carbon fiber reinforced epoxy composites are sensitive to their environments via humidity, elevated temperatures, and liquid exposure. This paper reviews the moisture uptake behavior and diffusion characteristics of continuous carbon fiber epoxy composites which will serve as a good source for understanding the moisture diffusion behavior of these composites in hot/wet environments.
Graphical abstract
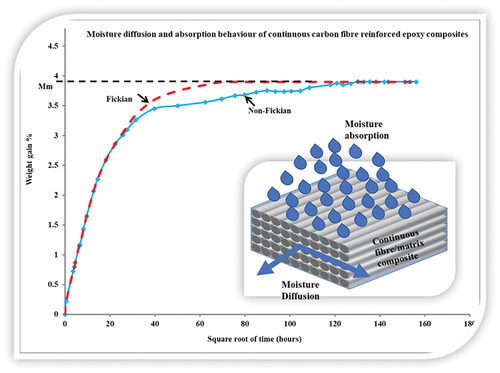
1. Introduction
It is a common principle in engineering practice and nature that the combination of two or more distinct constituents or materials forms a composite material, which may have more desirable properties than that of the individual materials. The idea of making composites for engineering use arises from their remarkable properties such as high stiffness, high strength, excellent corrosion resistance, low density, and often low cost. The constituent materials have significantly different physical and chemical properties coupled by an interface, giving composites distinct properties unobtainable in a single material. Composites in general consist of a continuous phase called the matrix and a discontinuous phase embedded in the continuous matrix to enhance its performance called reinforcement which is normally stiffer and stronger than the matrix. An additional phase called “Interphase” exists between the matrix and the reinforcement due to the chemical interactions between them or to other processing effects. The function of the matrix is to bind the reinforcement in a desired distribution and orientation and to enable easier processing. Composite properties are strongly affected by the properties of the components, their distribution, the interface between them, and the geometry of the reinforcing phase[Citation1, Citation2]. It is convenient to classify modern composites into three groups: Metal matrix composites (MMCs), Ceramic matrix composites (CMCs), and Polymer matrix composites (PMCs). Although composites are often thought of as new materials such as carbon fiber-reinforced epoxy resin and carbon fiber reinforced aluminum and copper MMCs, they have a long history with early bricks being straw embedded in mud, concrete being a mixture of stones in cement and there are many natural fiber composites and green composites such as bone and wood.[Citation3–6] As it is known that composite materials give a range of possibilities for designers, composite materials have found many applications in various branches of industry including chemical, aerospace, energy, automotive, sport, and offshore industries.[Citation7,Citation8]
2. Carbon fiber reinforced epoxy composites
Fiber-reinforced polymer composites, , with continuous fiber reinforcements have the highest mechanical properties. The most common materials used as the matrix for composites are polymers.[Citation9–10] This is due to their significant advantages such as low cost, good chemical resistance, and easy processibility, however, their low strength, modulus, and operating temperature limit their use. Moreover, it is important to consider the matrix’s processing history which affects the matrix and the interface properties.[Citation4,Citation11] The thermal stability of PMCs is determined by the stability of the matrix; therefore, the matrix determines the operating temperature of PMCs.[Citation12–13] The main polymer matrix materials used in high-performance fiber composites fall into two types: thermoset polymers such as epoxies and polyesters, and thermoplastic polymers such as polyether-ether ketone (PEEK) and nylons. This classification of polymers under these two types is according to their thermal response and the effect of heat on their properties.[Citation14] Epoxy resins and continuous carbon fibers are currently the most widely used materials for producing continuous fiber reinforced polymer composites used in a large variety of engineering applications.
2.1. Epoxy resins
Epoxies are some of the most versatile polymeric materials and are considered to be mechanically robust polymers with good strength, temperature resistance, and chemical resistance. These resins are thermosetting polymers, and they have various applications as adhesives, high-performance coatings, and structural composite materials. Epoxy resins are the favored choice for applications that require higher strength, good temperature resistance, and excellent chemical resistance. This is because of the polar hydroxyl and ether groups which improve adhesion to the fiber.[Citation15] The common types of epoxy resins are diglycidyl ether of bisphenol-A (DGEBA), tetraglycidyl ether of diamino-diphenyl methane (TGDDM), triglycidyl p-amino phenol (TGAP) and epoxy novolac. Cross-linking of the epoxy groups can be achieved either by using boron tri-fluoride, di- or tri-amines, or acid anhydrides, which all lead to the production of hydroxyl groups in the polymer chains.[Citation16] The multiplicity of reaction pathways provides usually molecularly heterogeneous, highly cross-linked network structures. Generally, the curing temperature and the initial composition of the reactant mixture determine which reaction process predominates.[Citation17] It is also significant to note that two main reaction pathways cause the formation of hydroxyl end groups. These hydroxyl groups may not completely react because of the configurational limitations in the reacting system leading to a high affinity for penetrant molecules such as water and other liquids causing a significant influence on the polymer properties.[Citation18] Commercial epoxy resin systems will often include thermoplastic particles as toughening agents, as well as plasticizers in some cases. In terms of environmental resistance, epoxy resins are less susceptible to hydrolysis than polyesters, but do have a higher tendency to absorb moisture and thus lose mechanical performance, especially under hot/wet environments.[Citation15,Citation18] The susceptibility of epoxy resins to water absorption is attributed to the large amounts of polar hydroxyl groups in the polymer networks which attract polar molecules such as water. However, water molecules can also possibly be clustered in free-volume microvoids as “free water.” Therefore, it can be said that water absorption is dependent on the free volume in the polymer and the polar group types and their concentrations in the epoxy resins.[Citation19] The averaged properties of epoxy resins are listed in .[Citation20,Citation21]
Table 1. General properties of commonly used epoxy resins[Citation10, Citation20].
Table 2. Medians of Msat and D as a function of epoxy prepolymer type.[21].
2.2. Carbon fiber
In advanced polymer matrix composites, the most used reinforcement is high-performance carbon fibers, . Carbon-fiber epoxies represent about 90% of carbon fiber-reinforced polymers (CFRP) production. The functional requirements of carbon fibers are to have high strength, high stiffness, stability during handling, and low density as fibers are the main load-bearing phase of fiber-reinforced composites.[Citation11] Furthermore, moisture, solvents, acids, or bases have virtually no effect on carbon fibers at room temperature.[Citation22] Therefore, the mechanical properties of the composite are dependant mainly on the fiber properties which do not change significantly with moisture absorption. Carbon fibers are very thin filaments with a diameter between 5–10 μm which are much thinner compared to human hair.[Citation10] Generally, the current technology for producing carbon fibers depends on the thermal decomposition of different organic precursors. Commercially, carbon fibers are manufactured from three different precursors: polyacrylonitrile (PAN), cellulosic-based precursor (rayon fibers), or petroleum pitch. The main process used to produce carbon fibers is the process by which PAN is converted to carbon fiber through stabilization and carbonization processes.[Citation1,Citation4,Citation6] There are different grades of carbon fibers including high modulus fibers (HM) which have the highest stiffness, high strength fibers (HS) the strongest fiber, and intermediate modulus fibers (IM) with the least stiffness of the three and strength in between the others.[Citation23] The difference between these grades is the degree of orientation achieved via heat treatment. The high-modulus fibers have more extensive heat treatment which leads to more of the graphite-like plates being aligned along the fibers, which gives higher modulus. The heat treatment leads to more defects, which limits strength. High-strength fibers have less intense heat treatment and less orientation, but fewer defects. Intermediate modulus fibers are between these two. The mechanical properties of these three types of carbon fibers are tabulated in .
Table 3. Mechanical properties of three types of carbon fibers[Citation10].
The orientation, distribution, and concentration of fibers have significant effects on the mechanical properties of the composites. The classification of fiber-reinforced composites depends on the type, length, amount, orientation, and hybridization of the fibers. The properties of fiber composites are very directional, being very stiff and strong parallel to the fibers, but rather weak in shear parallel to the fibers, and very weak in tension perpendicular to the fibers.[Citation11] Uniform unidirectional composites () where all the fibers are in the same orientations provide the maximum properties for the composites, however, such unidirectional composites are unavoidably anisotropic since maximum strength is achieved along the fiber direction and properties decrease in directions away from the fiber direction.[Citation4,Citation6,Citation11] Composites with less directionality can be achieved by stacking layers of fibers at angles varying between 0 and 90º, which gives composite laminates with orthotropic properties but still good mechanical performance. A quasi-isotropic lay-up consists of multiple layers of fibers varying in orientation, and the layers are orientated at equal angles, i.e. 0, ±45, 90°. Quasi-isotropic composites offer overall good strength in all directions. Woven fabrics offer similar bidirectionality with easier handling. Further uniformity of properties can be achieved using a textile formation of the composite by methods such as 3D weaving, braiding, and knitting, .[Citation24]
Figure 3. Types of composites lay-ups and fabrics[Citation24].
![Figure 3. Types of composites lay-ups and fabrics[Citation24].](/cms/asset/09780cb8-873a-4001-86bb-57beba600687/lpte_a_2234461_f0003_oc.jpg)
2.3. Manufacture of carbon fiber composites
The early manufacturing process for fiber-reinforced polymer composites used a hand lay-up technique which is slow and labor-intensive, with poor quality control. Over the last few decades, there has been a rapid development of manufacturing techniques that can provide increased quality and complexity along with rates of mass production. There is no scope here for a detailed review of manufacturing methods and so a very brief overview is given. Generally, the methods used will need to reflect the type of material (thermoset or thermoplastic; continuous or short fiber), the shape and complexity to be produced, the production numbers, and cost constraints. Common methods for thermoset-based composites include hand lay-up, vacuum bagging, resin infusion, resin transfer molding using compression molding equipment, filament winding, and pultrusion. The curing process of fiber-reinforced thermosetting polymers into composite structures involves elevated temperatures and pressures for a predetermined duration of time. The level of these two significant procedure parameters, in addition to their length of time, considerably influences the performance of the product.[Citation25] The one method that does warrant a little more attention is that of pre-preg molding. A pre-preg is a pre-impregnated material comprising fibers coated with a partially cured matrix material. This is supplied in pliable sheets or tapes that are easy to handle. The fibers are normally either unidirectional or in woven fabrics. The pre-preg sheets are laid onto a mold, either by hand or automatically, and then fully cured in an autoclave at elevated temperature with vacuum bagging to ensure the elimination of entrapped air and volatiles. The use of unpressurized ovens or liquid-based systems such as the Quick-step process is also possible. The use of pre-pregs allows improved fiber distribution, resin wetting, and consolidation during curing [Citation26–27] Microwave processing has recently been developed as an alternative curing technique for the curing of carbon fiber-reinforced thermoset composites. This is because it can reduce the processing times of the part and save energy and cost. However, one of the limiting disadvantages of this technique is the lack of suitable microwave transparent tools for the process. Microwave curing is only used with thin CFRP laminates because carbon fibers might suffer from high dielectric loss leading to a reflection of the microwaves and thus leaving the middle layers of a thick composite structure uncured. Moreover, CFRPs components produced using microwaves normally have high void content due to the pressure lack in the process which in turn leads to poor mechanical performance compared to conventionally cured CFRPs. Nevertheless, the effect of microwave processing on mechanical properties is dependent on the microwave process parameters and material types.[Citation28] Additive manufacturing is a new manufacturing technique used to 3D print fiber reinforced composites allowing components to be constructed in very complex geometries, prototyped affordably, and manufactured in small quantities with minimal tooling cost.[Citation29] 3D printing of carbon fiber reinforced composites is still limited to thermoplastic matrix composites.[Citation30–31] However, 3D printing technologies have a big potential to be adopted as the future technique to manufacture carbon fiber reinforced polymer composite materials with lower production costs and a high degree of automation. It is worth mentioning that the moisture absorption behavior of composites is affected by the fabrication method, curing cycle, resin chemical structure, and fiber sizing alongside temperature, humidity, aging medium, and environmental loads.[Citation32] illustrates the effect of the processing method of epoxy-based composites on the moisture content at saturation (Msat) and the diffusion coefficient (D).[Citation21]
Table 4. Moisture diffusion properties of epoxy matrix composites produced using various processing methods[Citation21].
3. Moisture diffusion behavior and kinetics in composites
Polymer composites are often used to replace metals due to their corrosion resistance; however, they can demonstrate sensitivity to their environments. Polymer composites can have reversible or irreversible property changes due to several degradation processes acting alone or together such as thermal cycling, hot/wet exposures, complete immersion in water at various temperatures and dry/wet cyclic conditions, immersion in chemical liquids (including fuel, acids, alkalis, solvents, and oxygen), and ultraviolet (UV).[Citation14,Citation32] The relative significance of each agent depends on the existence and the level of exposure in each case. Various types of damage caused by moisture absorption in polymer matrix composites can occur due to hygrothermal exposure. Moisture absorption in composites can occur when they are in direct contact with water including distilled water, deionized water, humid air, or seawater. The lowest moisture content at saturation is obtained under humid air compared to the highest content when composites are fully immersed in water. The moisture content at saturation in seawater is normally low because the mineral molecules in the water slow down the diffusion of the water molecules through the material. On the other hand, the diffusion rate in the humid air is higher than that in the distilled and deionized water (lowest) and thus allows saturation to be reached rapidly.[Citation21] This confirms the direct correlation between the absorbed content of water and the relative humidity which is represented in Henry’s law (EquationEquation (1)(1)
(1) ).[Citation21]
where Csat is the water concentration at saturation and Ps is the water partial pressure, linked with RH (EquationEquation (2)(2)
(2) ).
Based on these Equations, various models have been adapted to describe the dual moisture absorption in composites including power law (EquationEquation (3)(3)
(3) ); Langmuir (EquationEquation (4)
(4)
(4) ); Dual sorption (EquationEquation (5)
(5)
(5) ); and Flory – Huggins (EquationEquation (6)
(6)
(6) ).[Citation21]
Where a, b, c, and d are coefficients of the solvent activity, υ is the volume, and χ is the interaction coefficient of polymer-solvent. The coefficient b is between 1.3 and 1.8 for pure resins and close to 1 for composite materials. On the other hand, c and d are approximated by the statistical thermodynamic treatment of Langmuir’s [21]. Water molecules may travel into polymer composites by diffusive and/or capillary processes causing either reversible or irreversible changes in the mechanical properties of the composites.[Citation19] Research studies have shown that plasticization and hydrolysis are the main causes of property loss in polymer matrix composites during the hot/wet aging process.[Citation34] Moreover, chemical changes in the polymer matrix composite can occur if it is exposed to cyclic heating above the boiling point of water which causes moisture vaporization.[Citation35–36]
3.1. Diffusion
Liquid absorption will be a combination of both solubility and diffusivity; therefore, it is vital to understand the transport mechanisms of moisture diffusion in polymer matrix composites. It is well established that liquid molecules penetrate the polymer surface when in direct contact with the composite and then progress through the composite’s bulk by the driving force of concentration gradients.[Citation7,Citation34] The random motion of the liquid molecules and how fast they transfer through the bulk of the composite is called diffusion. Diffusion behavior in polymers can be classified as follows[Citation7,Citation37,Citation38,Citation39]:
1- Fickian diffusion in which the diffusion rate is independent of the concentration (case I). For polymers, this occurs when the mobility of the polymer segments is much higher than the diffusion, and so the presence of the liquid molecules does not affect the diffusion. Diffusion in rubbery polymers is in general Fickian because of the fast response of the rubbery polymers to changes in their condition. Many glassy polymers also exhibit Fickian diffusion if there are relatively low levels of liquid solubility.
2- Fickian diffusion in which the rate of diffusion is very much dependent on the concentration (case II). This is most seen where the absorbed liquid causes an increase in polymer segment mobility via plasticization and so makes diffusion easier. This occurs when the diffusion rate is greater than the polymer segment mobility. It is a common case with glassy polymers and strongly absorbing liquids.
3- Non-Fickian or anomalous diffusion which occurs when the polymer segment mobility and diffusion rate are comparable. This diffusion behavior can be counted as an intermediate between the two extremes of diffusion behavior in case I and case II.
Case I and Case II Fickian diffusion and non-Fickian diffusion behavior have been reported by several researchers for moisture diffusion in polymers and polymer matrix composites.[Citation40,Citation41,Citation42,Citation43]
3.2. Fickian diffusion
The major progress in diffusion theory came from the work of Adolf Fick who recognized that diffusion is a dynamic molecular process and realized the difference between a steady state and an actual equilibrium, EquationEquation 7.(7)
(7) The diffusion Equation was described based on the same mathematical basis as Fourier’s law for heat conduction, EquationEquation 8.
(8)
(8) [Citation7]
Where C is the liquid concentration and is equivalent to the temperature T in EquationEquation 8(8)
(8) , whereas D is the and is equivalent to the thermal diffusivity α = k/ρ.c. Fick developed the law of diffusion in which the diffusion coefficient is either concentration-independent (EquationEquation (9))
(9)
(9) or concentration-dependent (EquationEquation 10
(10)
(10) ).
where J is a total one-dimensional flux (kg/m2/s), and D represents the molecular diffusion coefficient (m2s−1).∇C = dC/dx, the concentration gradient (kg/m2), x is the distance term (m), C is the concentration (kg/m3), and t is the time (s).
The moisture absorption process of most polymers correlates greatly with Fick’s laws when the surrounding temperature is below the glass transition temperature (Tg) of the conditioned polymer.[Citation44] During the absorption process, Van-der-Waals bonds between polymer chains will be interrupted by the water molecules causing more freedom in the polymer segment motion.[Citation45] Therefore, the relatively high level of molecular motion is the key reason for the water permeability in polymers.[Citation46] The two major factors which affect moisture transport in polymers are the segmental mobility of polymer chains and structural defects.[Citation47] It is widely recognized that Fick’s model is the most commonly used by researchers because it is simple and mathematically tractable, although, non-Fickian or anomalous diffusion may occur in different cases.[Citation48,Citation49,Citation50,Citation51] Usually, the measurements of diffusion are assessed by measuring the total weight uptake as a function of time, .
Figure 4. Fickian curve fit to moisture absorption of an epoxy resin[Citation52].
![Figure 4. Fickian curve fit to moisture absorption of an epoxy resin[Citation52].](/cms/asset/f8600ae5-597b-4adf-b09a-a5f99d8d4475/lpte_a_2234461_f0004_b.gif)
Moisture absorption curve in which approaches a convergent value after some time is frequently used to experimentally characterize Fickian diffusion behavior. The initial linear region of the weight gain curve goes up to about 60% of the moisture equilibrium (M∞) followed by a gradual approach toward the asymptotic value. The initial moisture uptake in a thin plate, if Fickian diffusion is observed, is given by EquationEquation (11)(11)
(11) .[Citation50,Citation51,Citation52]
where Mt is the mass uptake at time t, M∞ is the moisture equilibrium and h is the plate thickness. The Equation shows that the initial moisture uptake is proportional to the square root of time, and it is this relationship that is most used to find out whether Fickian diffusion is followed.[Citation46–48] This Fickian model shows a direct dependency on M∞, the relative humidity %, and the sample thickness h. Another model developed by Carter and Kibler correlates the diffusion coefficient D to the number of free water molecules n and the number of bound water molecules N as a function of time t (EquationEquation (12)(12)
(12) ). [Citation21]
Generally, diffusion coefficients are obtained using thin plates and the 1-D Fickian model, EquationEquation 13(13)
(13) , where diffusion from the edges can be neglected. This model gives reasonable estimates of D values in the fastest diffusion direction, while diffusion from the edges becomes significant when the fastest diffusion direction is in the plane of the plate. However, it has been claimed that using a 1-D model leads to 50% errors in the derived diffusion coefficients. Therefore, it is essential to consider diffusion from the edges and a 3-D Fickian model with anisotropic diffusion coefficients can be used, EquationEquation (14)
(14)
(14) .[Citation50]
where a, b, and c are the plate dimensions along the x, y, and z axes respectively. Dx, Dy, and Dz are the diffusion coefficients along the respective axes. However, for diffusion coefficients obtained experimentally, if the thickness of the plate is very small compared to the other dimensions, then the edges can be neglected, and EquationEquation (15)(15)
(15) can be used to derive D values. If the edge effects on all six surfaces need to be considered where the thickness of the sample is comparable to its length and width, then edge correction factors (f) need to be used. Several edge correction factors[Citation53,Citation54,Citation55] have been derived and used to account for the effect of diffusion through smaller faces, .
Table 5. Edge correction factors.
s derived from EquationEquation (15)
(15)
(15)
3.3. Non-Fickian diffusion
The anomalous diffusion is used when departures from Fickian behavior occur. Commonly, material type, environmental condition, and materials exposure history are the main features controlling the degree of deviation. Some of these deviations may arise from the initial structure of the material, but others can result from material degradation. Generally, the structural change in the polymers causes anomalous diffusion. These changes can be attributed to diffusional mobility or to the internal stresses developed as diffusion is in progress[Citation38,Citation56]. It has been reported by many researchers that in many cases a deviation from Fickian diffusion was observed.[Citation50,Citation51, Citation57,Citation58,Citation59,Citation60,Citation61,Citation62,Citation63,Citation64,Citation65,Citation66,Citation67,Citation68,Citation69,Citation70,Citation71,Citation72,Citation73,Citation74,Citation75,Citation76,Citation77,Citation78] There are several features of composite materials reported in these studies that are known to contribute to a departure from Fickian diffusion including matrix plasticization, nonuniform fiber structure, fiber/matrix interfacial debonding, applied or residual stresses, voids, micro-cracking and chemical degradation of the matrix. Many models such as Dual – Fick model[Citation62, Citation63] and the Carter and Kibler model[Citation64, Citation66] have been developed and recommended to account for non-Fickian diffusion in polymer matrix composites, but there is not a single general theory to describe it.
A simple methodology based on the time-dependent response of epoxy resins, comparable to the viscoelastic relaxation of mechanical properties was proposed by[Citation67,Citation68] to characterize non-Fickian diffusion coefficients from moisture mass gain data. The non-Fickian diffusion model was used for predicting the moisture uptake profile through the thickness of the epoxy resin plates. Moreover, the Langmuir diffusion model, a dual-mode absorption model, is frequently used to describe non-Fickian diffusion. This is based on the assumption that the molecules of the penetrant are either dissolved in the polymer and hence can diffuse or are absorbed in the free volume micro-voids and are then locally immobilized.[Citation64] Bonniau et al[Citation69] compared the classical single-phase Fickian and the two-phase Langmuir diffusion theories by employing the diffusion models to water absorption data of glass epoxy composites. Typical deviations from Fickian behavior are demonstrated in . Type I proposes the existence of bound and unbound water molecules. The bound water molecules in the occupied volume of the resin can cause swelling in the polymer. Whereas the unbound water molecules residing in the free volume don’t cause any swelling. On the other hand, two-phase diffusion, known as Type II deviation, is noticed in some cases, especially in hot and wet conditions. Such severe two-stage moisture absorption has been attributed to fiber/matrix interfacial debonding, polymer relaxation, and/or microcrack formation on the material surface.[Citation7, Citation56, Citation70,Citation71,Citation72] Several researchers[Citation73,Citation74,Citation75,Citation76,] found that moisture absorption in polymers and their composites is significantly affected by defects, changes in the free volume fraction, swelling stresses, Poisson's contraction, and external load and these factors might lead to deviation from Fickian behavior.
3.4. Solubility
Solubility is defined as the amount of solute that can be dissolved under equilibrium conditions in a unit volume of a solvent (such as a polymer matrix).[Citation77] Henry’s law is the simplest treatment of solubility in which solubility is proportional to the partial pressure of the surrounding liquid or gas. Marsh et al[Citation78] generalized Henry’s law to account for that, EquationEquation 16.(16)
(16)
where H is the solution enthalpy, P is the pressure of the vapor, A is a constant and was given as 2.05 × 10−10 for epoxy resin, and M∞ is the saturation level. Usually, solubility differs from system to system and depends on chemistry, curing degree, and other factors within each system, encompassed in the constant A above. Another treatment uses a solubility parameter (δ) which generally depends on the chemical and structural similarity between the polymer and the liquid, EquationEquation 17.(17)
(17) [Citation79]
where ∆E is the energy of vaporization to a gas; V represents the molar volume of the components. Moreover, with increasing differences between the solubility parameters of the polymer δp and the solubility parameters of the solvent δs, the solubility decreases. So, the quantity (δp – δs) 2 should be as small as possible to give favorable mixing. Interestingly, solubility can be improved when firstly, both liquid and polymer have a compatible nature of secondary bond forces (similar solubility parameters), secondly when the liquid molecular volume is small, and finally when the cross-link density is low and the free volume in the polymer is high. For polymers, solubility parameters can be determined by measuring the degree of solubility of a polymer in various solvents for which the solubility parameters are known. Alternatively, a group contribution method can give the solubility parameter of a polymer by assembling the solubility parameter of each molecular group in a polymer and the overall solubility parameter can be determined.[Citation18,Citation80] Parvatareddy at al[Citation81] attributed the effect of various solvents on polymers to the difference in the solubility parameters between solvent and polymer. In addition to absorption, it was to some extent responsible for environmental stress cracking (ESC) in carbon fiber-reinforced composites. A similar correlation between ESC and the solubility parameters has been reported by.[Citation82] Solubility is proportionally related to temperature as at high temperatures, the entropy contribution increases and the elastic resistance of the polymer decreases leading to an increase in solubility.[Citation18] In general, moisture absorption in polymers is related to the availability of molecular-sized holes in the body of the polymer and the affinity of the polymer and water. Generally, epoxy resins have a moderate amount of free volume at 50–150 ̊C below Tg and a relatively strong affinity to water because of polar hydroxyl groups generated during curing. Therefore, the two possible approaches to moisture absorption are[Citation83,Citation84]:
Free volume absorption. This mode assumes that water molecules move between free-volume holes and so it depends on the cross-linked density of the polymer. In this case, bonding between water molecules and epoxy is believed to be unimportant.
Hydrogen bonding. This mode assumes that hydrophilic sites exist in the network of the polymer and that water molecules are attracted to these sites and can easily bond to certain hydrophilic functional groups such as hydroxyl or amine.
During the absorption process, the moisture content at equilibrium approaches a constant value when the material is fully immersed in water, EquationEquation 18(18)
(18) , while the value of moisture equilibrium varies when the material is subjected to humid environments with relative humidity ɸ, EquationEquation 19.
(19)
(19) [Citation85]
where a and b are constants, dependent on the material type, and derived from a linear regression fit to the moisture content data.[Citation49] Moreover, the relation between the moisture contents of the composite, (M∞)c, the fiber, (M∞)f, and the neat resin, (M∞)r cab be theoretically given in EquationEquation 20.(20)
(20) [Citation86,Citation87]
where Wf is the weight fraction of fibers. Carbon and glass fibers do not absorb moisture while polymer and natural fibers do absorb moisture. So, (M∞)c and (M∞)r are related by the expression (EquationEquation 21(21)
(21) ):
Loos et al [88] examined the validity of this Equation by comparing the values of M∞ of both unidirectional graphite/epoxy composites and neat epoxy resin. An excellent agreement between the measured and calculated values was obtained. Changes in the value of M∞ may occur after reaching the maximum asymptotic value of M∞. That is due to many reasons such as cracks developing in the material leading to an increase in M∞, and loss of material because of leaching or cracking which decreases the value of M∞. Generally, the normalized weight gain of the composite should be the same as that of the resin for an ideal composite with no effect of interface on moisture uptake.[Citation7, Citation50, Citation51] The dependency of equilibrium moisture content on temperature is not as well established because other researchers[Citation89, Citation90] have noticed either positive or negative dependency of equilibrium uptake on temperature, while others found no temperature dependences.[Citation91,Citation92] However, the effect of temperature on solubility is well established in fundamental thermodynamics theories and can be expressed by Van’t Hoff’s, EquationEquation 22(22)
(22) :
Integrating this Equation with taking into account the narrow temperature range of normal water uptake measurements, gives the following expression (EquationEquation 23(23)
(23) ):
where Cs is the saturation concentration, ∆H is the heat of dissolution, M∞(T) is the moisture content at equilibrium as a function of temperature, -∆Habs is the heat of absorption per mole of absorbed water molecules and M0 is a temperature-independent constant. As a result, when the temperature, the equilibrium moisture uptake increases because of the endothermic diffusion process.[Citation78] It was also found that as the temperature decreases increases the equilibrium moisture uptake may increase in an exothermic absorption.[Citation55] There are many factors affecting the equilibrium moisture content including thermal history, existing damage in the composite, and the chemical stability of the resin. The maximum amount of moisture at saturation may exceed the thermodynamic equilibrium value. This is generally due to the presence of voids, cracks, fiber-matrix interface, defects, and long-term changes in solubility.[Citation45]
4. Moisture absorption-induced damages in carbon fiber-epoxy composites
4.1. Swelling
Swelling in polymers occurs as a result of liquid molecules being absorbed into the polymer leading to volume expansion that changes the state of residual stresses in the composite material.[Citation93] The main reasons behind swelling in composite materials include the hydrophobic nature of most engineering fibers, the difference in the physical, chemical, and mechanical properties between fiber and matrix,[Citation3] plasticization which leads to a reduction of the glass transition temperature of the composite.[Citation93,Citation94] Generally, the severity of swelling is strongly dependent on the solubility, the molecular volume of the absorbed liquid, and the material stiffness. Swelling-induced internal stresses in polymer composite may lead to irreversible damage, such as debonding between the fiber and the matrix or microcracks.[Citation21] Internal stresses produced by swelling can occur as a result of the non-uniform distribution of the absorbed liquid, and the differences in the swelling behavior between the matrix and the fibers. In general, fiber swelling increases the matrix tension and puts the fibers into tension, while matrix swelling decreases any residual tension in the matrix and puts it under compression. Furthermore, the stiffness of the fiber can hinder matrix swelling, and in this case, anisotropic swelling is common.[Citation94,Citation95] However, the stresses at the surface edges are normally high enough to produce cracks. After exposure to cyclic moisture absorption, micro-cracks, and interface debonding tend to coalesce and expand.[Citation21] As a result of the swelling stress, microcracks can form especially under transient conditions which, with sorption and desorption processes, can cause significant stresses in composites. For example, when swelling is perpendicular to the fibers in a unidirectional lamina, which is greater than the parallel direction, swelling-induced interlaminar cracking occurs due to complex stress contributions and stresses generated between laminates.[Citation95] It is important to understand the swelling behavior of polymer composites to determine any change resulting from water sorption in their properties such as strength and modulus.[Citation93,Citation94,Citation95,Citation96] Generally, swelling is less pronounced with small liquid molecules, low absorption, and glassy polymers. In this case, the liquid molecules can fit into existing free-volume holes without any volume expansion. With larger levels of absorption and more flexible polymers, swelling is more likely. The swelling in a polymer composite due to water absorption was carried out by Ref.[Citation56] It was reported that despite the very modest swelling that water initially produced, volume was noticed to increase proportionally to water absorption once a critical uptake threshold was exceeded. Sahlin et al[Citation17] investigated the effect of methanol and other liquids on epoxy resin and they found that samples exposed to methanol uptake showed a volume increase. This is because of the interaction between resin’s free hydroxyl group and methanol hydroxyl group through hydrogen bonding. This can interrupt the resin’s intermolecular hydrogen bonding and lead to an expansion into the network of the resin. It was noticed that the volume of the resin reduced back to its original unswollen dimensions when methanol-absorbed specimens were subject to a desorption process.
4.2. Plasticisation
Plasticization, which occurs due to liquid molecular absorption in polymers or fibers, is caused by the replacement of the intermolecular bonding (hydrogen bonds) between polymer chains by liquid molecules. This increases the free volume leading to easier movement of the polymer chains resulting in a decrease in the glass transition temperature (Tg) of the polymer which in some cases can be reduced by up to 100°C. However, the degree of plasticization is dependent on the Tg value and solubility.[Citation7] Kambour et al[Citation97] noted that the degree of plasticization increases with solubility, which is greater when the equilibrium solubility is higher. Typically, important changes occur when Tg is lower than the operating temperature of the material, and the solubility is at high levels.[Citation18] The plasticizing effect is usually reversible when liquid is removed, but it can become irreversible when polymers and composites are subjected to liquid absorption at elevated temperatures. The irreversible effects may be due to the chemical degradation of the matrix, interface failure, and the expansion of the internal voids.[Citation98] On the contrary, plasticization can improve the material toughness, increase the creep rate and stress relaxation, enhance the diffusion coefficient, and lead to environmental stress cracking in the polymer, but at the same time, decreases the stiffness and strength of the material noticeably.[Citation99,Citation100]
4.3. Chemical degradation
The selection of materials for engineering applications is primarily dependent on the severity of the environment. Generally, epoxy resins have a greater solvent and thermal resistance than other polymers, although they are more difficult to process and more expensive. Most of the epoxy resins used in composite applications have high resistance to corrosion and strong chemicals such as strong acids, salt solutions, and oxidative agents. However, many liquids are known to affect the performance of epoxy matrix composite adversely through chemical degradation and chain scission of the polymer matrix.[Citation101] It is well known that the degradation of polymers with specific functional groups can occur by a chemical reaction when polymers are exposed to fluids. Chemical degradation triggers hydrolysis of the bonds at the interface. The reaction at the interface between matrix/fiber may cause various morphological modifications to the interphase region,[Citation19,Citation21]. Hydrolysis is the most typical reaction of the chemical degradation in liquids, where polymers with ester bonds in the main or/and crosslinking chains such as epoxy resins undergo chemical attack by water, acids, and alkalis leading to dissolution and leaching of water-soluble polymer molecules followed by chain scission of the polymer. Additionally, the dissolution products may react with the polymer molecules, leading to further degradation.[Citation37] Oxidation is another type of chemical reaction where unsaturated bonds in the resin formations will be attacked by oxidizing agents such as oxygen or ozone, causing severe oxidative corrosion.[Citation102] Xiao et al[Citation103] investigated the changes in the chemical structure of epoxy resin after water absorption at 90 ̊C followed by complete drying. It also characterized the degradation products produced during hygrothermal aging. It was found that after hygrothermal aging, oxygen was gained by the epoxy resin while some nitrogen was lost, and the increased oxygen content in the epoxy resin was primarily in the type of functional groups such as C-O and N-CO-N which led to scission of the epoxy backbone chains. The results showed that besides the backbone structure of DGEBA, the degradation products also contain the – NH-C≡N form, a higher concentration of carbon-nitrogen bonds, and – NH groups. Additionally, the tertiary amine groups react with water to produce N-H and – OH bonds in the resin chains, and the products of the reaction might experience further reactions either with the crosslink chains or with each other. Wazzan et al[Citation104] investigated the effects of a high-concentration KOH solution on the chemical stability of epoxy resin and its carbon fiber-reinforced composites. Specimens prepared with different volume fractions were exposed to KOH solution at different temperatures and for different periods. It was observed that the thermal influence and the attack of the alkaline solution caused chemical degradation of the specimens. It was also noticed that carbon/epoxy samples with a 50% fiber volume fraction showed better chemical stability compared to un-reinforced samples. The effect of NaOH and H2SO4 on cured epoxy resin at different temperatures was examined by Ref.[Citation102] The results revealed three types of chemical degradation in epoxy resins including surface reaction, formation of a corrosion layer, and penetration type. The kinetics of each type are depended on the resin’s chemical structure, liquid diffusion in the resin, and the reactivity between resins and liquids. Another study reported a reduction in the thickness of carbon fiber composites caused by chemical corrosion.[Citation86] Moreover, degradation of the carbon fiber/epoxy composite occurs on the galvanic coupling of carbon-fiber composites with metals in multi-material structures in aqueous media. The degradative processes are directly related to the electrically conductive nature and surface chemistry of carbon fibers.[Citation105]
5. Moisture absorption behavior of carbon fiber/epoxy composites
Carbon fiber reinforced epoxy composites are often used in applications where they might be in direct contact with water, humidity, and other liquids. These environments can affect the short-term or long-term performance of these composite materials.[Citation3,Citation7] Epoxy resin in carbon fiber composites normally absorbs a small amount of moisture from the surrounding environments but even this small amount can potentially be damaging.[Citation3,Citation7] Therefore, the diffusion mechanism and saturation level in these composites are dependent on the relative humidity as well as the temperature of the surrounding environments. The amount of absorbed water by composites depends on the matrix type, which after a long time of exposure can lead to degradation and deterioration of the composite’s properties.[Citation71,Citation106,Citation107,Citation108,Citation109] However, the absorption process may take weeks to months before a significant amount of moisture is absorbed by the composite, and considerably longer periods (i.e. 1–4 years) before the composite is saturated.[Citation3, Citation7, Citation33, Citation50, Citation51, Citation58, Citation108, Citation109] Based on the research studies on moisture absorption into fiber reinforced polymer composites, it can be discussed that although most of the polymer matrix composites follow Fickian diffusion, deviations from Fick’s law in cross-linked and glassy polymers such as epoxy resins may occur when molecular relaxations or morphological effects dominate the movement of diffusing species in polymers.[Citation3,Citation7,Citation8,Citation48,Citation49,Citation50,Citation51,Citation52,Citation53,Citation54,Citation55,Citation56,Citation57,Citation58,Citation59,Citation60,Citation61,Citation62,Citation63,Citation64,Citation65] A commonly seen type of moisture ingress behavior is shown in , which shows true Fickian behavior for 65% RH and dual-mode absorption for 100% RH. In this case, a quasi-equilibrium stage follows the initial Fickian behavior seen in the early stage. The dual-mode absorption leads to a gradual slow and continuous weight increase, which increases the time to reach the final equilibrium.[Citation7, Citation50, Citation51, Citation58, Citation59, Citation106, Citation108]
Water molecules may enter the bulk of composites via capillary flow in which water ingresses through the pores and along the fiber-matrix interface due to hydrolytic breakdown[Citation119] or via microcracks or other forms of microdamage.[Citation111] The absorbed moisture may lead to significant mechanical and physicochemical changes that toughen the matrix and/or degrade the interface between matrix and fiber by interface debonding or micro-cracking.[Citation112] The resistance of the polymer matrix to moisture absorption is dependent on the molecular structure and state of cure of the polymer which determines the extent of reversible and irreversible damage in composites.[Citation113] With composites based on carbon fibers and epoxy resins, epoxy resin is mainly responsible for moisture absorption as the carbon fibers don’t absorb water significantly. This makes it easier to study and determine the diffusion properties of a composite material using these fibers because the absorption in the polymer is only considered in the analysis. However, the service life of carbon fiber/epoxy composites spans several decades, therefore, the design with these composite materials requires the ability to study and predict changes in composite properties as a function of environmental exposure, including matrix properties and the integrity of fiber-matrix interfaces.[Citation3, Citation7,Citation110,Citation111,Citation112,Citation113]
There are many potential variables affecting the water absorption in carbon fiber-reinforced epoxy composites. The diffusion rate and absorbed quantities of moisture into these composites are affected and dependent upon the relative humidity and temperature of the conditioning environment, polymer chemistry, material structure, and the water absorption mechanisms.[Citation7, Citation19, Citation50] The effect of hot/wet aging on neat epoxy resins and their composites has been covered in several research studies.[Citation51, Citation59, Citation88,Citation106,Citation114,Citation115,Citation116,Citation117,Citation118,Citation119,Citation120,Citation121,Citation122,Citation123,Citation124] It has been demonstrated that the aging effects in carbon fiber/epoxy composites generally take place very unevenly from the surface and edges into the bulk of the composite.[Citation115] The exposure of graphite-epoxy composites to humid air with a relative humidity of 20, 40, 60, and 100% and different temperatures ranging between 322 and 366 K was examined by Loos et al .[Citation88] Fickian behavior was followed and the maximum moisture content (M∞) of the composites showed dependency on relative humidity but not on temperature. The values of M∞ and the transverse diffusivity of the composite were estimated using the M∞ and diffusivity of the resin. This estimation assumes that the resin and the composite were cured identically. At high temperatures, significant changes in the composite behavior were observed, including the generation of cracks which increased the diffusion. Moisture absorption in unidirectional IM7 carbon fiber/epoxy composite material was examined in various relative humidifies at a constant temperature of 25°C.[Citation93] The moisture content at saturation and diffusion rate rapidly increased with increasing the relative humidity, .[Citation93] Similar results were reported by Ref[Citation116] on UD carbon fiber epoxy composite (Hexcell 8552/IM7) exposed to different relative humidity environments at 70°C for one year. Additionally, significant chemical changes in the material were observed mainly at the surface, while major physical property changes were detected much deeper in the material as microcracking and variations of glass-transition-temperature (Tg). These changes were the main ones responsible for the higher water-absorption levels and the late rate-acceleration at higher RH%. Fickian behavior was also observed by Lee et al[Citation117] studying the water absorption kinetics in graphite/epoxy composites. A deviation from Fickian behavior at high temperatures (90 and 100°C) was observed due to the formation of internal cracks. Zhou and Lucas[Citation118] studied water absorption in unidirectional graphite/epoxy composites at various temperatures for more than 8000 h to estimate the effects of water environments on absorption behavior. The hygrothermal effects were investigated by the measurement and analysis of weight change, hygrothermal induced swelling, formation of surface crack, and mass loss at the surface. These graphite/epoxy composites showed a mixture of Fickian and non-Fickian diffusion behavior. The deviation from Fickian diffusion was discussed to be due to chemical modification and physical damage to the epoxy resin caused during absorption. Rather surprisingly, the non-Fickian behavior observed was more evident at lower exposure temperatures. Two different absorption stages were observed by Korkees[Citation7, Citation51, Citation119] studying the water absorption behavior of unidirectional and ±45°Carbon fiber reinforced 977–2 epoxy composites under hygrothermal environments. Water absorption in these composites followed non-Fickian behavior at longer times, especially at high temperatures. This behavior continued for at least 4 years, . The non-Fickian behavior in this stage was attributed to matrix relaxation and to the changes in its morphology where the matrix is about to saturate. The moisture contents at equilibrium are not dependent on the conditioning temperature but the long-term solubility increased with temperature. The diffusion coefficients on the contrary are strongly dependent on the temperature and relative humidity of the conditioning environments. Furthermore, diffusion of saturated salt water, diesel fuel, jet A fuel, and aviation oil in the same graphite-epoxy composites was investigated by Ref.[Citation88] The experimental results exhibited Fickian diffusion behavior. In addition, it was found that the amount of absorbed liquid in diesel fuel, jet A fuel, and aviation oil case is dependent on the immersion time but is insensitive to the temperature, while, for saturated salt water, M∞ is dependent on both immersion time and temperature.
Figure 7. Moisture absorption behavior of carbon fiber/epoxy composites at different relative humidity atmospheres[Citation93].
![Figure 7. Moisture absorption behavior of carbon fiber/epoxy composites at different relative humidity atmospheres[Citation93].](/cms/asset/1a5f8555-d17f-4ff0-8fa3-161c03df11aa/lpte_a_2234461_f0007_oc.jpg)
Figure 8. Moisture uptake curves and diffusion coefficients of carbon fiber/977–2 epoxy composite immersed in water at different temperatures and relative humidities[Citation7, Citation51, Citation119].
![Figure 8. Moisture uptake curves and diffusion coefficients of carbon fiber/977–2 epoxy composite immersed in water at different temperatures and relative humidities[Citation7, Citation51, Citation119].](/cms/asset/f026f8a7-84e3-42f6-818d-6a445820754e/lpte_a_2234461_f0008_oc.jpg)
One of the important factors that control the diffusion mechanism of water molecules in composites is the fiber architecture. This is a critical aspect to take into account where the surfaces of the edges are exposed to moisture and the non-homogenous anisotropy structure of the material becomes vital in determining the diffusion rate of fiber reinforced composites. To understand the effects of fiber orientations and arrangements on the diffusion mechanism into carbon fiber/epoxy composites, the directional diffusion into unidirectional carbon fiber-reinforced M21 epoxy composites was investigated with long‐term exposure to different environmental conditions.[Citation7,Citation50,Citation51] Initial Fickian absorption was observed in the short-term stage followed by a slower second stage that continues for up to 3 years, . The absorption behavior was controlled by the fibers’ architecture and the water diffusion rate along the fibers was about three times faster than that across the fibers and about seven times faster than through the thickness, . The diffusivities across the fibers and through-thickness were 40% and 13% of that along fibers respectively. The diffusivity along the fibers in this case was believed to be close to that of the unreinforced resin. The effect of the thicknesses of the composite samples was also considered as a variable and a decrease in diffusion rate at saturation was observed with increasing the thickness, . Moreover, the analysis of the moisture diffusion rates of unidirectional T800H/3633 carbon fiber reinforced epoxy composites, reported that the diffusion rate along the fibers is 20 times faster than that in the transverse direction.[Citation40] Almudaihesh et al[Citation106] investigated the moisture absorption performance of unidirectional, plain, and twill weave CFRP composites with different stacking sequences. After a full immersion in still natural water at 70°C for 40 days, a significant variation in the total mass gains of the composites was seen between the different sequences in each composite type compared to the small variation observed between the different fiber architectures, . The surface area to volume ratio of the samples is believed to be the reason behind these variations. Moreover, the QI samples were impacted at various impact energies and water mass gain increased with increasing the impact energy. This is in good agreement with[Citation108] and.[Citation124] The greater weight increase seen at high impact energies is a result of a higher damage volume and the larger amount of cracks at the surface allowing fast ingress to the damage volume.[Citation106, Citation108, Citation124] Moisture diffusion in 3D braided and unidirectional carbon/epoxy composites in different mediums including distilled water, phosphate-buffered saline, HCl, and NaOH solutions was studied by Ref.[Citation86] The diffusion of distilled water and phosphate-buffered saline (PBS) in both composites followed Fickian behavior while non-Fickian diffusion was followed by the composites in the HCl and NaOH solutions. No change in the diffusion pattern for each medium was observed for the unidirectional and 3D composites suggesting that fiber structure didn’t affect the diffusion behavior. However, the diffusion parameters of the two composites were different in each medium studied, and the parameters of the 3D composite were lower due to its stronger geometrical hindrance to the diffusion of moisture molecules. It is also worth mentioning that the diffusion of PBS was found to be slower than that of distilled water due to the existence of large ions. Additionally, NaOH uptake was found to increase rapidly in the initial stage but quickly drop, which is likely due to the alkaline-induced degradation in the polymer matrix. Furthermore, no saturation was reached for composites in HCl where the diffusion was affected by the degradation of the matrix. Arao et al[Citation120, Citation121] analyzed the moisture diffusion properties of carbon fiber/epoxy composites with various lay-ups considering the composite anisotropy and the dimensional changes. The moisture uptake in these composites followed Fickian behavior, . The diffusion along the fibers was also reported to be 2–4 times larger than diffusion in the transverse and the through- thickness directions. However, the data from these studies showed that the laminate thickness and lay-up sequence had no effects on the diffusion coefficients. Water absorption in dry unidirectional continuous fiber T700 carbon/epoxy composite laminates with sealed edges was studied by Ref.[Citation42] The water molecules instantly penetrated the surface of the laminate to a certain depth followed by slow diffusion toward the laminate center. This phenomenon was named “moisture shock”. As a final point, the importance of studying the directional diffusion into carbon fiber composites is well presented in these research studies, and it can be discussed that the moisture-induced micro deformation in the composites can be predicted under constant conditions if the maximum moisture content and the diffusion coefficient for each direction are known.
Figure 9. Directional diffusion in UD carbon fiber/epoxy composites[Citation7,Citation50,Citation51].
![Figure 9. Directional diffusion in UD carbon fiber/epoxy composites[Citation7,Citation50,Citation51].](/cms/asset/e11e09c4-e672-4d85-988c-730584d66360/lpte_a_2234461_f0009_oc.jpg)
Figure 10. Effect of composite thickness on moisture diffusion in UD carbon fiber-epoxy composites[Citation7,Citation50,Citation51].
![Figure 10. Effect of composite thickness on moisture diffusion in UD carbon fiber-epoxy composites[Citation7,Citation50,Citation51].](/cms/asset/ec03682b-dd27-46d0-9b51-0249a2ca7afe/lpte_a_2234461_f0010_oc.jpg)
Figure 11. Weight gain of various types and lay-ups of carbon fiber/epoxy composites[Citation106].
![Figure 11. Weight gain of various types and lay-ups of carbon fiber/epoxy composites[Citation106].](/cms/asset/6578781f-266e-4eba-99c8-0f63c13cadbf/lpte_a_2234461_f0011_oc.jpg)
Figure 12. Moisture absorption into different CFRP composites[Citation120].
![Figure 12. Moisture absorption into different CFRP composites[Citation120].](/cms/asset/e0843446-3468-4e17-bd59-988010f79c01/lpte_a_2234461_f0012_b.gif)
It is well established that the diffusion mechanism of moisture into thick composite components is usually a slow process even though moisture absorption in the surface layers of the composite practically starts immediately when in contact with the hot/wet environments.[Citation3, Citation42, Citation51, Citation59, Citation119, Citation122] A comprehensive moisture ingress study was conducted by Ref[Citation122] to investigate the moisture diffusion behavior of thin and thick-ply carbon fiber/epoxy composites in various environments including 85% RH/70°C, 65% RH/70°C and 45% RH/70°C. An initial Fickian diffusion behavior was observed for thin and thick composites in the first stage, but instead of maintaining a maximum saturation level in the second stage, the composites continued to absorb water at a slower rate. However, the moisture content in the thin-ply composite was higher compared to the thicker-ply composites. On the contrary, the diffusion rate of the thin-ply composites was lower compared to the thick-ply composites. This was most noticeable for the quasi-isotropic composites compared to the unidirectional laminates. The largest difference in diffusion coefficients was a result of changing relative humidity.
Carbon fiber/epoxy composites are normally manufactured to near-net-shape but in some applications, additional machining such as cutting, and drilling may be required which may lead to significant damage to the surface of the composite. Delamination and microcracking are the major damages obtained after cutting and drilling fiber/polymer composite materials. These kinds of damages often limit the use of carbon fiber composites for structural applications.[Citation125] Various techniques have been used to understand and measure the severity of machining-induced delamination and microcracking to improve the performance of composite parts and assemblies. Visualization techniques for the measurement of delamination damage are quite challenging for nontransparent composites like carbon fiber – reinforced epoxy composites. The researchers used different techniques for the visual measurement of the delamination; there was no consistent procedure followed within the same method making the results not strictly comparable.[Citation125,Citation126,Citation127,Citation128,Citation129] Moisture absorption in quasi-isotropic carbon/epoxy composites with machined and molded edges was examined by Ref.[Citation112] Weight gain plots revealed that the moisture absorption is higher for specimens with machined edges than molded edges with a mass gain of around 0.80% and 0.75% respectively. This is attributed to the microcracks and damages of the fiber/matrix interface of the fibers oriented at 90° and ±45°Caused by the machining process and led to capillary diffusion. Karbhari et al[Citation123] studied the water uptake in a high-volume fraction (69%) pultruded unidirectional carbon fiber/epoxy composite at temperatures of 23, 37.8, and 60°C and for 36 months. A two-stage diffusion with the Fickian first stage and relaxation/deterioration-dominated second stage was reported. The rate constants including first-stage diffusion rate D and second-stage relaxation coefficient k increased with increasing the immersion temperature. High temperatures also increased the degree of swelling which resulted in an increased desorption rate. This is because the hygrothermal effects caused irreversible aging in the form of fiber/matrix interface de-bonding, voids, and micro-cracks which provided new paths for diffusion. The maximum value of uptake over the entire period of the study,[Citation123] M∞ increased with the immersion temperature. Moreover, the durability behavior of pultruded unidirectional carbon fiber-reinforced composite plates immersed in water and seawater at room temperature was analyzed by Ref.[Citation71] Fickian diffusion behavior was observed for the composites in both water and seawater. The research revealed that seawater immersion leads to higher moisture content at saturation than water immersion. This was attributed to the blister-induced damages on the composite surfaces in seawater which afford larger residence sites. However, the diffusion coefficient in seawater was lower than that in water, and this is due to the high concentration of dissolved salts in seawater that hinder water diffusion by the osmosis process.
The use of graphene nanoparticles to modify and enhance the mechanical properties of polymers and fiber reinforced polymer composites has been of particular interest to researchers due to the superior properties of graphene.[Citation60,Citation124,Citation130] Therefore, it was hypothesized that although it is well established that carbon fibers hinder water molecules’ movements through the resin, the introduction of graphene nanoparticles to carbon fiber/epoxy composites may also hinder the path of the water molecules and slow down the absorption process further. In a study carried out by Korkees et al ,[Citation124] the absorption behavior of water and ethanol in woven carbon fiber/epoxy composites modified with NH2 functionalized graphene before and after impact was investigated. Three-stage diffusion mechanism was observed for water and ethanol in the composites. However, the inclusion of NH2-graphene nanoparticles slowed down the diffusion rate of both ethanol and water in this composite, by 46.4% (before impact) and 44.8% (after impact). Moreover, the incorporation of functionalized graphene nanoparticles in carbon fiber/epoxy composites was reported in another study[Citation60] to improve the resistance of the composite to water absorption by 43.9%. Two-stage water uptake was observed by the graphene-modified composite in this study[Citation60] which was immersed in water at different temperatures. This behavior was attributed to resin relaxation. In both studies,[Citation60,Citation124] it was argued that the increased resistance to moisture diffusion in the graphene-modified composites is due to the creation of additional barriers against water absorption and further reduction of the intermolecular movements of the epoxy resin.
Furthermore, researchers have investigated other characteristics and tactics in order to improve the resistance of carbon fiber/epoxy composites to moisture diffusion. The moisture absorption behavior of carbon fiber/epoxy laminated composites with surface-treated carbon fibers was investigated by Ref[Citation84] at various RH% and constant temperature of 25°C. The moisture uptake of the untreated and silane-treated carbon fiber composites followed Fickain’s behavior with a similar percentage of moisture absorbed by both composites. The reported behavior of moisture uptake is similar to the work reported by Lee et al .[Citation117] The effect of two different curing systems at room temperature and post-curing temperature on the moisture mass gain of carbon fiber/epoxy composite was measured at 24°C and 60°C aging temperatures. The post-curing increased the moisture content at equilibrium for pure epoxy regardless of the conditioning temperature, while the maximum moisture content of the post-cured composite increased only at the high-aging temperature. The diffusion rate for both the epoxy resin and the carbon fiber composite increased with increasing the aging temperature. The increase in the free volume caused by post-curing led to the increase in the saturation moisture content in the post-cured epoxy resin compared to the room-cured epoxy resin at both the conditioning temperatures. The reduction in the moisture content at the equilibrium of the post-cured composites compared to room-cured composites could be down to the weak carbon fiber-epoxy interface in the room-cured composite.[Citation32]
6. Moisture absorption into epoxy resins
The mechanism of moisture diffusion in epoxy resins has been widely studied.[Citation59,Citation131,Citation132] The impact of relative humidity on the amount of absorbed water by epoxy-based composites has been extensively investigated in the literature.[Citation21,Citation50,Citation51,Citation58,Citation60,Citation122,Citation124,Citation133,Citation134,Citation135,Citation136] It is well established that the moisture molecules transport in polymers is directly correlated to the molecular-sized nanovoids within the polymer and the affinity between the polymer and water molecules.[Citation124] The extent of volume change caused by hydrogen-bonded water is significantly less than the volume of absorbed moisture which suggests that a considerable part of absorbed water resides in the polymer nanovoids.[Citation19,Citation133,Citation134,Citation135] Additionally, the absorbed moisture in epoxy resins mostly leads to plasticization, hydrolysis, chemical degradation, and microvoids formation in the polymer which may significantly affect the resin properties.[Citation134] The impact of the number of nanovoids (holes) in epoxy resin on the equilibrium moisture uptake and also the interaction between water molecules and polymer network was investigated by Ref.[Citation135] A great tendency for water molecules to be positioned inside the holes and to have further access to the polar sites was observed, which greatly affects the maximum water content. Furthermore, the coloration of the epoxy resin might occur when exposed to a humid environment due to chemical degradation.[Citation137,Citation138,Citation139] Water absorption in epoxy resins usually varies depending on the resin type and the curing process. The water absorption rate of different types of epoxy resins may differ by a factor of 10, and by a factor of up to three for the same resin with a different curing agent.[Citation138] A research study by Adamson[Citation140] showed that water molecules interacted with hydrophilic groups in epoxy resin by forming hydrogen bonds. On the contrary, Woo et al[Citation141] found that water molecules exist as clusters within the epoxy resin and were not bound to polar groups. Further information on the water-epoxy interaction nature was provided by Ref.[Citation142] The discussion concluded that the movement of the water molecules in epoxy resins is hindered by the water molecules migrating from one site to another with an approximate residence time of (7 × 10−10 s) but that the hopping doesn’t involve a specific hydrogen-exchange mechanism.[Citation142] Furthermore, no evidence of free water and tightly bound water in the resin was given in this study. Water absorption and desorption in an epoxy resin (DGEBA/DDA) at elevated temperatures (90°C) were studied by Ref.[Citation96] The analysis of the weight gain curves showed that water diffusion is Fickian and that the increase in the initial weight was followed by a decrease at longer times although no visible moisture-induced damage was noticed. This weight loss was attributed to the degradation of the epoxy due to hydrolysis reactions. Delasi et al[Citation143] examined the influence of absorbed water on the properties of six neat epoxy resins and three epoxy composites. The diffusion coefficients, activation energy, and activation entropy for water diffusion were in good agreement between five of the epoxy resins. Due to the resemblance between D for the five epoxy resins, samples showed similar moisture diffusion kinetics at the applied temperatures. Comparable equilibrium moisture concentrations at the same relative humidity were observed with similar reductions in the glass transition temperature (Tg) caused by the plasticization. Most of the water in the five resins was noticed to be bonded to the resin at low relative humidity. While, at higher RH, most of the water was bonded to the filler or was accumulated at epoxy phase boundaries for the inorganic filler/epoxy sample. This didn’t affect the filled epoxy’s Tg but led to differences in D, activation energy, and entropy of filled resin from unfilled resins. The characteristics of water diffusion in epoxy systems (DGEBA-TETA) with various amounts of plasticizer THIOCOL were studied by Ref[Citation144] at different temperatures. The existence of the plasticizer changes the material’s structure by producing different crosslinking densities and hydrophilic character. Jacobs and Jones’ model which assumes that epoxy resin is a two-phase system was used to analyze the results. The first phase which is homogeneous and nonpolar contains the main part of the absorbed water, while the second phase has a different density and a hydrophilic character. The overall diffusion showed deviation from Fickian behavior, although the model considers the diffusion in each phase to be Fickian. At low temperatures and independent of the plasticizer content, the samples gave the same results, whereas, at higher temperatures, the diffusion rate increased with increasing the plasticizer amount. Popineau et al[Citation66] observed the non-Fickian behavior of water in epoxy resin due to the existence of mobile and bound diffusant molecules. Non-Fickian diffusion of water in an insufficiently cured epoxy resin was observed by Ref.[Citation145] This is because the further post-curing and oxidation of the resin occurred during the absorption process. Moreover, the absorption-desorption cycle effectively increased the preexisting free volume in the resin and rendered the following absorption process different from the original one.[Citation145] Furthermore, the difference between the experimentally produced absorption and re-sorption curves by Ref[Citation145] is due to the reversible changes in network conformations and not caused by irreversible damage to the resin. Abdel-Kader et al[Citation146] studied water absorption in epoxy resins prepared with the same epoxide (diglycidyl ether of bisphenol A) but with five different hardeners. The curing agents used in the epoxy formulations had an important influence on water absorption. Water absorption in these epoxy resins followed Fickian behavior but this behavior was strongly affected by the physical aging and the degree of crosslinking in the network. The experimental results of Nogueira et al[Citation147] showed an increase in diffusivity and permeability with temperature, where increasing the temperature in the lower crosslink density epoxy led to an increase in the water absorption level. This was thought to be due to the greater molecular mobility which is restricted in the higher cross-linked epoxies. Furthermore, the relaxation time of the ambient cured epoxy was found to be strongly dependent on the absorption temperature despite the water level in all cases is similar. Similar results were obtained by Ref[Citation148] who studied the effects of long-term water absorption at different temperatures on the relaxation time of ambient cured epoxy. They also reported that the formation of multi-bound water molecules and a heterogeneous network structure led to broader glass-rubber transitions at 37.8 ̊C and 60 ̊C.
Apart from water, other small molecules such as gasoline, oil, acids, and solvents may diffuse into epoxy resins and affect the mechanical performance. The behavior of other liquids can also shed light on the physical and chemical mechanisms possible. This can extend to mixtures, where the equilibrium between the liquid components and the polymer may be complex. Apart from absorption, plasticization, and swelling; polymers such as epoxy resin may also have other degradation reactions such as oxidation, hydrolysis (chain scission), transesterification, and salt formation.[Citation7, Citation59, Citation102, Citation149, Citation150] The diffusion of water and low molecular weight organic liquids in cured epoxy resin with different amounts of the crosslinking agent was studied by Ref.[Citation17] Fickian behavior was observed at the initial stage and deviations from Fick’s law were noticed at the long-term stages attributed to the resin relaxation phenomena. In addition, the equilibrium content of water (~5.6–7.1%) increased with increasing the cross-linking agent amount. This may seem surprising as the extra crosslinking hinders molecular movement, however, additional crosslinking agents provide higher concentrations of polar groups. Additionally, the diffusion behavior of methanol was anomalous and could be correlated to the dynamic changes in the specimen dimensions. Water-ethanol absorption in different epoxy polymers was carried out by Ref[Citation105] and different absorption behavior was detected due to the difference in hydrophilicity and absorbent-dependent phase transitions of these different polymers. Tusda et al[Citation102] also studied the effect of NaOH and H2SO4 on cured epoxy resin at different temperatures. In the NaOH solution, there was an initial absorption with a weight increase followed by a weight loss due to resin degradation. The absorption behavior in H2SO4 demonstrated similar behavior of initial liquid absorption followed by degradation, but the weight loss was much higher than that in the NaOH solution. The diffusion of water-acetic acid solutions in epoxy resins was slower than in the concentrated acid.[Citation151] That is because the water molecules in the diluted acid control the diffusion rate and swelling. The Fickian model was not suitable to describe the diffusion mechanism in this study due to the effects of swelling and the voids in the polymer. Furthermore, since the interactions between the molecules in the mixtures are stronger than penetrant/epoxy interactions, only voids can be filled up which leads to non-Fickian diffusion. The absorption of several industrial chemical liquids/solvents in 977–2 epoxy resin was studied by Ref.[Citation59] The weight uptake curves showed a two-stage absorption process for water, ethanol, methanol, and their mixtures as well as for heptane. On the contrary, a three-stage absorption was witnessed for butyl format, decalin, and their mixtures. This deviation from Fickian behavior was attributed to polymer chain relaxation and swelling. The diffusion properties of all liquids are mainly affected by their polarity, molecular size, and their interaction with the polymer chains. Furthermore, the presence of more soluble liquid in the binary liquid mixtures enhanced the solubility of the other liquid in the mixture.[Citation59]
7. Effect of temperature on moisture diffusion in carbon fiber/epoxy composites
Composites in most engineering applications may be exposed to a wide range of temperatures, where elevated temperature (below 100°C) generally facilitates moisture absorption. The temperature of the conditioning environment plays a critical role in the degradation process of the polymer matrix composite.[Citation136] The mechanism of moisture absorption in carbon fiber/epoxy composites is highly influenced by the surrounding temperature in a complex manner where increasing the temperature leads to accelerated aging by changing the diffusion rate and mechanism as well as the solubility.[Citation152,Citation153,Citation154] Increased temperature leads to an increased diffusion rate due to increased molecular mobility and free volume.[Citation152] It has been reported that the moisture content at saturation in epoxy resins and their fiber-reinforced polymer composites is either independent of temperature[Citation21] or dependent on temperature.[Citation19] However, exposure to high temperatures reduces the water solubility parameter while it doesn’t affect that of the polymers.[Citation21] Moisture diffusion is a thermally or energy-activated process and the diffusion coefficient D increases rapidly with temperature.[Citation55] This dependency on temperature can be commonly expressed via an Arrhenius Equation (24).
where Ea represents the activation energy of diffusion, D0 is the pre-exponential factor, T is the temperature, and R is the gas constant.
Within a range of temperatures from room temperature to 100°C, many studies have not found any significant difference in equilibrium absorption. The effect of hygrothermal temperature on moisture absorption in unidirectional carbon fiber-reinforced epoxy composites was examined by Ref.[Citation155] Two-stage diffusion behavior was observed at all temperatures of 35, 70, 85, and 95°C. The equilibrium water content at 95°C was lower than that at 35°C. A slight effect of humidity at elevated temperatures was witnessed, with a higher diffusion coefficient and lower saturation for the samples conditioned in water at 70°C compared to 95% RH at 70°C. Water absorption in graphite/epoxy composites at various temperatures of 45, 60, 75, and 90°C was studied by Ref.[Citation118] The data exhibited Fickian diffusion behavior at 45, 60, and 75°C but deviation from the Fickian mechanism was observed at 90°C as well as a weight loss after immersion for 1300 h. The specimens demonstrated no changes in the dimensions but showed obvious multiple cracks after 3400 h of immersion in water at 75 and 90°C. De`Neve et al[Citation156] investigated water absorption by an epoxy resin at various temperatures 40, 55, and 70°C, and 100% relative humidity. The moisture absorption behavior was not strictly Fickian but rather sigmoidal. In addition, the diffusion rate was found to be temperature-dependent, while equilibrium absorption values were not temperature related. Irreversible changes to polymers and composites may occur due to moisture absorption at elevated temperatures such as cracking, debonding, and chemical degradation. These changes to the polymers and composites will also affect their water absorption behavior correspondingly.[Citation55] In some other cases, polymer composites are suddenly subjected to high-temperature environments in which temperature may surpass 100°C for no longer than a few minutes. This rapid heating above Tg which is regularly followed by rapid cooling is called thermal spiking. Thermal spiking can influence the rates of moisture absorption in composites, where polymer composites absorb considerably more moisture than under normal constant hygrothermal conditions, which can also cause mechanical damage to the composites. Although the exact details vary with material system and exposure history, the mechanism of thermal spiking effects is as follows. The free volume in the polymer matrix increases with temperature, continuing above 100°C. At the same time, moisture will diffuse into this additional free volume. If the composite is rapidly cooled below Tg, the moisture can be trapped or frozen into the extra free volume which in turn is frozen in.[Citation56,Citation157] On the other hand, compressive stresses can build up at the surface due to rapid heating, where the surface temperature goes above Tg while there is no time for the moisture to escape since the temperature inside the material is still low. As the surface temperature is above Tg these stresses are rapidly relaxed. After a short time, the temperature becomes uniform and desorption occurs, leading to tension in the surface layer. These tensile stresses may further increase due to rapid cooling and that can cause surface cracking. The effect of moisture absorption as a consequence of thermal spiking on the mechanical properties of carbon fiber-reinforced epoxy composites was carried out by Ref.[Citation158] Thermal spiking resulted in increased moisture content for all composites. The maximum absorption increase took place at a spiked temperature of 140 and 160°C. No microcracks or voids were seen in the wet and thermally spiked composites. Clark et al[Citation159] applied a range of temperature and humidity conditions on two different graphite/epoxy laminates to study the moisture absorption in these laminates. Experimentally, several combinations of spiking and moisturizing conditions were used to determine the influences of thermal spiking. Damage in the laminates occurred by thermal spiking when moisture was present. Moreover, thermal spiking during the absorption stage was found to be more severe than the spiking of the material conditioned to equilibrium moisture. Kerasek et al[Citation160] also examined the diffusion behavior of graphite fiber/epoxy composites at 60°C/95% RH and 70°C/95% RH environments. The results showed that the higher the temperature, the higher the moisture uptake rate. There was no evidence of a non-Fickian absorption at a higher temperature which could be due to the surface-induced crystallization in the epoxy resin at or close to the polar surface of the carbon fibers.[Citation94]
8. Effects of composite structure on moisture diffusion
8.1. Fiber/Matrix interface
The fiber/matrix interface is most vital and critical in providing durability and reliability of these potential composite materials, . The interface must be of high quality for the composite to resist moisture-induced degradation and to maintain the composite properties on exposure to moisture.[Citation161] In addition, fibers must be well-bonded to the fibers to maximize the stress transfer between the fibers, achieve a good resistance to crack propagation and chemical attack, and minimize fiber pull-out.[Citation162] It is well known that during the carbonization stage of carbon fibers, produced carbon atoms provide strength and stability to the fiber but their disordered arrangement leads to weak interaction with all types of matrix materials.[Citation6] Therefore, the surface of carbon fibers is normally modified to promote better adhesion to the matrix. The surfaces of carbon fibers are often treated using oxidation treatment, electrochemical method, plasma treatment, and high energy irradiation to change the fiber surface from nonpolar to polar to enhance the wettability between carbon fibers and matrix.[Citation6,Citation163] Several research studies proposed a theory in which coupling agents were used as surface treatment that can use the hydrolytic intrusion of water as a mean of stress relaxation without interrupting the bond between polymer matrix and fiber.[Citation4,Citation18,Citation92–94,Citation153,Citation154,Citation155,Citation156,Citation157,Citation158,Citation159,Citation160,Citation161,Citation162,Citation163,Citation164,Citation165]
Water absorption in fiber-reinforced composites can lead to the degradation of the interfacial area between the fiber and the matrix by hydrolysis and chemical attack.[Citation92,Citation94] This in turn causes a reduction in the stress transfer between fiber and matrix which in turn deteriorate the mechanical properties. Ageing of graphite – fabric reinforced epoxy composites in boiling water can destroy the adhesion between the fibers and the matrix and form voids in the resin.[Citation165] The degradation of the interface in carbon fiber/epoxy composites due to moisture has been reported to have both reversible and irreversible effects. This is dependent on the temperature of the surrounding environment, the applied mechanical stress, and the type of fiber surface treatment.[Citation93, Citation94, Citation165] A comparison between the moisture uptake curves of both unidirectional carbon fiber composites and neat resin was conducted to determine the effect of interface on moisture diffusion by Ref.[Citation55] The high strength of the fiber/matrix interface constrained the motion of the long-range chains of the matrix and thus reduced moisture uptake in the relaxation-controlled long-term stage. The study also found that prolonged moisture absorption at high temperatures damaged the interface causing interfacial cracking. The fiber/Matrix interface degradation in UD carbon fiber composites, , reported by Ref[Citation106] was attributed to the low sizing levels of the UD fibers and therefore allow easier degradation of the interface. This is following the proposed theory where the mechanism of water penetration is primarily moving through the matrix increasing the number of cracks and consequently the interface debonding. Moreover, even though a substantial weakening may occur at the interface during hygrothermal aging, the strong interfacial bond for carbon fiber/epoxy may eliminate the possibility of non-Fickian absorption. This may also be the reason that the moisture is not transported in the composite bulk by capillary diffusion but by the diffusive route only.[Citation94] Furthermore, the deterioration of the carbon fiber/epoxy interface appeared after 60 days of immersion in demineralized water. Seawater was more aggressive in weakening the interface and its long-term effect was more evident than the demineralized water.[Citation8] The interfacial degradation was attributed to either chemical degradation caused by hydrolysis at the interface or mechanical degradation caused by swelling and large stresses leading to the matrix being pulled away from the fiber.[Citation8]
Figure 14. SEM images of the carbon fiber/epoxy interface of carbon fiber composites[Citation106].
![Figure 14. SEM images of the carbon fiber/epoxy interface of carbon fiber composites[Citation106].](/cms/asset/c8f992da-df6a-4de6-a89c-3101071aea32/lpte_a_2234461_f0014_b.gif)
8.2. Volume fraction
The volume fraction of the fibers has been considered in prior research to be an important parameter that can significantly influence the moisture diffusivity of fiber reinforced polymer composites. The effect of the volume fraction of the matrix (Vm) on the hygrothermal behavior and diffusion characteristics of unidirectional carbon fiber/epoxy composite laminates was investigated by Ref,[Citation155] . The diffusion rate increased with increasing the matrix volume fraction during the initial stage of water uptake. This effect is mainly due to the changes in the effective length of the water diffusion path because of the anisotropic fiber arrangement. Ray[Citation94] studied the moisture uptake kinetics of fiber-reinforced epoxy composites with various fiber volume fractions. The results for both composites exhibited Fickian behavior in the initial stages followed by deviations in the later stages. This was attributed to the formation of microcracks and micro-damage which were induced by hygrothermal shock cycles. In this study, increasing the fiber volume fraction didn’t influence the diffusion kinetics but affected the moisture content at saturation. Moreover, the high fiber loading in pultruded carbon fiber/epoxy composites was found to have a considerably lower diffusivity in the transverse direction, and therefore transport along the fiber direction dominates the diffusion in these composites.[Citation123]
Figure 15. Weight gain curves (a) and diffusion coefficients (b) for UD carbon fiber composites with various matrix volume ratios[Citation155].
![Figure 15. Weight gain curves (a) and diffusion coefficients (b) for UD carbon fiber composites with various matrix volume ratios[Citation155].](/cms/asset/3f1a1219-0885-4e8c-a4f3-05a94154d2c1/lpte_a_2234461_f0015_b.gif)
8.3. Fiber arrangement
The arrangement and orientation of the fibers have been considered critical aspects of controlling moisture absorption in carbon fiber reinforced epoxy composites which normally affect the diffusion path of water molecules. The influence of fiber orientation angle on moisture absorption was investigated by Ref[Citation111] for a (T300/5208) carbon fiber composite material. The fiber angle affected the moisture diffusion in the composite, as shown in . The 0° fiber angle plates reached saturation quite quickly, with the moisture absorption being slower as the angle increases. This is because as the angle to the fiber increases, the fibers form more of a diffusion barrier. An investigation was carried out by Choi et al[Citation155] to study the effect of fiber orientation on the water absorption mechanism in the through-the-thickness direction in a carbon fiber/epoxy laminate with 0̊, 45̊, and 90̊ fiber orientations, . The laminate with 0̊ fiber angle has the highest diffusion rate corresponding to water diffusion along the fibers, while specimens with a 90° fiber angle have the lowest diffusion coefficient. That is because the 90° fibers cause the water molecules to move around following a longer path compared to 0° fiber laminate. Therefore, increasing the fiber angle from 0° to 90° decreased the diffusion rate by 60%. Moisture diffusion into unidirectional (UD) and cross-ply carbon fiber/epoxy composites at 90% RH and 80 ̊C was examined by Ref.[Citation166] The cross-ply composites had a slower diffusion rate compared to UD composites, and the maximum moisture content M∞ was 1.8%wt for UD composites compared to 1.4%wt for the cross-ply composites. Zai et al[Citation167] measured the weight gain as a function of exposure time (at 80 ̊C) for carbon fiber/epoxy laminates with different stacking sequences as shown in . A reasonable Fickian behavior was followed, and the moisture absorption was not uniform, with higher absorption content of 5.3% observed for the unidirectional composites compared to 4.9% for the [9012]s and 4.5% for the [±45]3s specimens. More complex stacking sequences had lower water absorption, but it should be emphasized that the absorption time was quite short, and samples did not reach saturation.[Citation167] The effect of fiber structure on moisture diffusion in 3D braided and unidirectional composites was examined by Ref.[Citation87] In this study, the carbon fiber composites, and the epoxy samples showed similar absorption curves, despite the epoxy samples absorbing much more water. This is because the fibers reduce the amount of resin and act as a physical barrier to water diffusion. The 3D composites did have a lower diffusion rate than the unidirectional composites. Water diffusion rates in UD carbon fiber composites were noted to be greater by Ref[Citation106] than the rates of 2 × 2twill and plain-woven carbon fiber composites manufactured using the same epoxy resin. This was attributed to the linear paths of the fiber in UD composites which provide fast water ingress along the interface compared to the weave patterns in the woven structures which provide a long and complex path for moisture access along the interface. In another study conducted by Ref[Citation168] examining the water absorption in laminated UD and cross-ply carbon fiber composites, the mass gain of the cross-ply laminates was slightly larger than that of the UD laminates.
Figure 16. Effect of fiber orientation on the average moisture concentration during cyclic exposure[Citation111].
![Figure 16. Effect of fiber orientation on the average moisture concentration during cyclic exposure[Citation111].](/cms/asset/7bf1f654-0c73-417c-9c5f-2ca875cbba47/lpte_a_2234461_f0016_b.gif)
Figure 17. Moisture absorption curves (a) and diffusion rates for unidirectional laminates with various fiber angles[Citation155].
![Figure 17. Moisture absorption curves (a) and diffusion rates for unidirectional laminates with various fiber angles[Citation155].](/cms/asset/e6dcad39-a1cd-4e62-ad52-e072c2d1a03f/lpte_a_2234461_f0017_b.gif)
Figure 18. Moisture absorption curves for the carbon fiber/epoxy of different stacking sequences[Citation167].
![Figure 18. Moisture absorption curves for the carbon fiber/epoxy of different stacking sequences[Citation167].](/cms/asset/ee087e95-57d4-4a46-83ac-2f478b44ebed/lpte_a_2234461_f0018_b.gif)
8.4. Voids
Voids which are cavities of various sizes and shapes are common defects in polymer matrix composites. They are formed by the entrapment of air or volatiles in the resin bulk during composite manufacturing.[Citation169] Voids formed during composite production or service may have significant effects on the moisture uptake in polymer matrix composites. Choi et al[Citation155] investigated the effect of void content on the hygroscopic behavior of carbon fiber/epoxy composite laminates. An anomalous Fickian diffusion behavior was followed by all composites regardless of the voids volume fraction (Vv), (a). However, there is a slight increase in the saturation level with an increasing number of voids. The analysis of the effect of voids on diffusion coefficient showed rather unexpected behavior with a reduction in the diffusion rate at 3% Vv followed by a slight increase with increasing the void volume ratio up to 5.6%. A subtraction method of the measured diffusion rate values from the corrected diffusion coefficients with no voids was adopted and therefore the decoupled void effect on the diffusion rate of the composites remained negligible up to 3% Vv and begins increasing above 3%, (b). These results should be treated with some caution as changing void content without affecting other properties is very difficult. Voids can be found in composites in many shapes and sizes. Research carried out by Ref[Citation170] examined these factors by using carbon/epoxy composites exposed to hygrothermal conditioning to study the moisture absorption behavior. The diffusion coefficient and the maximum water content were significantly dependent on the content of the voids, where the amount of absorbed water more than doubled with the presence of only 1% voids in the composite.
Figure 19. Moisture absorption behavior (a) and diffusion coefficients (b) for laminates with various void volume ratios[Citation155].
![Figure 19. Moisture absorption behavior (a) and diffusion coefficients (b) for laminates with various void volume ratios[Citation155].](/cms/asset/ab05a6cc-2d27-42e6-a31e-36356a424e14/lpte_a_2234461_f0019_b.gif)
9. Moisture desorption and re-sorption
As water exposure can be cyclic and variable, especially in humid environments, desorption and subsequent re-sorption are important processes when considering the service environment of composite material.[Citation19,Citation154] On desorption, the effects of water absorption can be reversed even if major modifications to the composite characteristics took place during the aging process. In the case when composites are exposed to severe conditions, significant damage may occur during this aging process and reversibility can be lost.[Citation171,Citation172] Therefore, moisture desorption is usually conducted to describe the degree of reversibility of water absorption and to determine the possible effects of chemical and structural changes, interfacial debonding, and micro-cracking. Generally, water desorption in composites involves two processes including the thermally activated desorption of water from the resin network and the capillary flows along cracks formed in the matrix and/or at the interface.[Citation92] Therefore, an increase in the desorption rates is a result of such processes due to an increase in the area/volume ratio in the cracked materials.[Citation92] Desorption normally takes longer than absorption and non-post-cured materials may never completely dry because of bound sites for the water where water molecules are chemically bonded to the resin, therefore, to remove all water, it is probably necessary to heat above Tg.[Citation173,Citation174] The plasticizing effect of water during water absorption normally leads to a reduction in Tg and enhances the polymer chain relaxation leading to a relaxed network structure, . On the contrary, during desorption, the removal of water molecules suppresses the relaxation and thus no changes to network structure occur.[Citation174]
Figure 20. The situations during absorption and desorption[Citation174].
![Figure 20. The situations during absorption and desorption[Citation174].](/cms/asset/23e5eaa5-801b-49f6-8476-1b691bfad87c/lpte_a_2234461_f0020_oc.jpg)
An investigation into desorption in high Vf pultruded carbon fiber/epoxy composites was carried out by Ref[Citation123] after 3 years of immersion in water. Since desorption is slow at the same temperature as that of absorption, a higher temperature of 60 ̊C was used for the desorption test. This is because of the strong interaction between water molecules and functional groups of the resin which results in their separation only at elevated temperatures. Boinard et al[Citation175] reported similar results. One point to note is that both these studies reported almost complete water removal. Karbhari et al[Citation123] found that composite specimens immersed in water for extended durations experienced structural relaxation with the swollen segmental confirmation of the hygrothermally aged resin were different from the original composites. Since the swollen structure enhances moisture diffusion, increasing the immersion temperature is expected to result in a higher degree of swelling and thus increase the desorption diffusivity. Correspondingly, fiber-matrix interfacial debonding, the existence of voids and micro-cracks in the composite thickness due to hygrothermal aging were found to play a main role in increasing desorption diffusivity by providing new paths for diffusion and wicking of water.[Citation3, Citation7, Citation154] Chateauminois et al[Citation92] provided information on the desorption behavior of epoxy resin and glass/epoxy composites after isothermal water absorption at various temperatures. Water absorption at elevated temperatures induced a particular change in the desorption behavior of the composite due to the occurrence of microstructural damage. The major change in desorption behavior took place between 50 and 70 ̊C and this suggests that the temperature limit for hygrothermal interfacial damage lies in this range of temperatures. Additionally, an increase in the desorption rates was observed at 70 and 90 ̊C owing to capillary flow along the debonded interface after aging at these temperatures. The moisture absorption and desorption behavior of epoxy resins were studied by Ref.[Citation176] A small amount of residual moisture remained after the desorption process from a high moisture content at saturation. This small content could only be removed by drying the composite at a relatively high temperature. Desorption behavior in different media was studied by Wan et al[Citation86, Citation87] who examined the desorption behavior of the C3D/Epoxy composite. The specimens conditioned in water and different chemical liquids at 37 ̊C were subjected to desorption at 37 ̊C, and specimens in all liquids showed behavior consistent with Fickian diffusion irrespective of their uptake history. Interestingly, diffusion coefficients for desorption were higher than those during the uptake process, and this is because of the existing diffusion paths such as debonded interfaces and microvoids which formed during the moisture uptake process. These paths were still open during desorption, allowing for the efficient removal of water molecules. Moreover, a small amount of moisture was retained in the composite after desorption. This phenomenon was also reported by Ref[Citation177] who attributed it to the existence of chemisorbed water. On the other hand, the moisture absorption of the C3D/EP composite immersed in HCl was nearly reversible. Specimens immersed in NaOH solution showed a significant weight loss, about 0.24% after saturation, confirming that extensive matrix degradation occurred during absorption. The presence of residual moisture in epoxy resin was also described by Ref.[Citation78,Citation178] From desorption and re-sorption experiments done in this research, structural relaxation was found to be irreversible upon the desorption of water molecules due to the plasticizing influence of the absorbed water. Furthermore, the experimental results demonstrated that the same relaxation process governed the absorption and re-sorption cycles.
Desorption and re-sorption experiments at 70 ̊C were carried out by Ref[Citation55] on carbon fiber reinforced BMI resin to investigate the reversibility of the structural change during absorption. The specimens were dried after the first absorption and used in the second absorption experiment. The re-absorption experiment shows higher diffusivity and moisture content than the first absorption. Arnold et al[Citation58, Citation154] and Korkees et al[Citation119] conducted desorption and reabsorption experiments on epoxy resins and carbon fiber/epoxy composites initially conditioned in water for 330 days, . The data showed an initial rapid drying, but complete drying wasn’t obtained, and a small residual of water remained in the epoxy resin and the carbon fiber composite even after long periods of drying. This is caused by the strongly bonded water molecules, which are difficult to be removed from the resin. Less amount of water remained in the composite than in the neat resin. Moreover, the neat resin and the composite specimens were immersed in water at 70°C after they were initially conditioned in water at 70°C, then dried at 70°C to study the re-absorption behavior of the composite. The diffusion rates during desorption and reabsorption were higher than those noticed during initial conditioning due to the gradual relaxation of the epoxy resin. The relaxation of the resin in both neat resin and composites normally generates a more open structure allowing more water molecules to diffuse and leading to faster desorption and re-absorption. This indicates the irreversibility of the structural change of the polymer network and the history-dependency of diffusion properties.
Figure 21. Desorption and re-absorption behavior and diffusion properties of the carbon fiber/epoxy composites[Citation58, Citation119, Citation154].
![Figure 21. Desorption and re-absorption behavior and diffusion properties of the carbon fiber/epoxy composites[Citation58, Citation119, Citation154].](/cms/asset/f7f7ff23-8321-4b45-aaf2-f27da7c93bfb/lpte_a_2234461_f0021_oc.jpg)
Karbhari et al[Citation123] carried out similar research to test the influence of the prior history (absorption – desorption) on carbon fiber/epoxy composites. After immersion in water for 3 years and then drying, the composites were immersed again in water at different temperatures for 2 months. The re-absorption process followed Fickian behavior and moisture content levels increased with temperature and were higher than those of initial immersion. Moreover, the re-absorption diffusion coefficients were higher than those of initial absorption. This is owing to the effects of both hygrothermal history and the composite damage occurring through the initial immersion, desorption, and re-absorption. Other researchers found increased absorption and diffusivity during re-absorption studies in various glassy polymers and have linked it to anomalous diffusion behavior,[Citation145,Citation179,Citation180]. After exposing the material to the absorbent during the first absorption stage, a higher diffusion and higher saturation level have been observed during subsequent re-sorption experiments, which have been attributed to structural relaxation by several authors.[Citation145,Citation181] The network structure of the material was observed to be different from the original material after desorption owing to the “frozen-in” segmental conformation leading to higher absorption in the re-sorption process. Numerous researchers have also noticed that annealing the desorbed material makes the re-sorption behavior very similar to that of the first absorption.[Citation145,Citation181] This proves that the physical nature of the penetrant molecules rather than the chemical nature induced structural changes in the material.[Citation174]
10. Concluding remarks
Structural continuous carbon fiber reinforced epoxy composites are normally subjected to a range of hygrothermal environments (hot/wet) throughout their service life. In this review paper, current studies focusing on the ingress of moisture into carbon fiber-reinforced epoxy composites were reviewed comprehensively with particular attention to the composite structure. Based on the review, the following remarks can be outlined:
In hot/wet environments, uncertainty about the long-term stability of carbon fiber reinforced epoxy composites is still the main concern for the industry. Moisture molecules can easily and rapidly diffuse into the epoxy matrix in the early stages followed by a slow increase in the long-term stage until saturation. Therefore, it is vital to understand the moisture uptake behavior and diffusion mechanisms in these composites because the existence of moisture in these composites can significantly deteriorate their mechanical performance and restrict their long-term use.
The mechanism of moisture uptake and the diffusion properties (M∞ and D) of the continuous carbon fiber/epoxy composites are vastly affected by the temperature and humidity of the surrounding environment. Elevated temperatures increase the molecular mobility and free volume in the epoxy resin leading to changes in the diffusion rate and solubility and accelerating the aging process of the composite.
The most common approaches to moisture absorption into continuous carbon fiber/epoxy composites are the diffusion of water molecules into the free volume in the resin and/or the hydrogen bonding between water molecules and the hydrophilic sites in the epoxy resin network.
Moisture absorption and diffusivity of continuous carbon fiber/epoxy composites are significantly influenced and controlled by the structural features of the composite including carbon fiber/epoxy interface, fiber volume fraction, fiber architecture and orientations, and voids content.
The most widely adopted model to describe the moisture absorption behavior and determine the diffusion rate of carbon fiber reinforced epoxy composites is the Fickian diffusion model. However, research studies have also reported deviation from Fickian behavior in continuous carbon fiber/epoxy composites where a steady and gradual increase in moisture uptake beyond the initial Fickian stage in the long-term stage of absorption is followed.
The non-Fickian diffusion is normally associated with and controlled by material type, environmental conditions, materials exposure history, resin relaxation, or structural changes.
The most frequent moisture-related damages in continuous carbon fiber/epoxy composites are swelling plasticization and chemical degradation. The negative impact of these types of damages includes internal stresses, irreversible damage, reduction of the glass transition temperature, and degradation.
It is important to study and understand the moisture desorption and reabsorption mechanisms in continuous carbon fiber/epoxy composite since the exposure to moisture can be cyclic and variable. Moisture desorption is reported to be faster than the initial moisture absorption but is slower than the moisture reabsorption process in continuous carbon fiber reinforced epoxy composites.
The understanding and determination of the water absorption mechanisms and diffusion characteristics of continuous carbon fiber/epoxy composites can allow improved design capabilities with short-term and long-term exposure to hot/wet environments and aid the prediction of the environmental impact on the composite properties including the properties of the epoxy matrix and the integrity of interface between the carbon fibers and epoxy resin.
Disclosure statement
No potential conflict of interest was reported by the author(s).
Additional information
Notes on contributors
Feras Korkees
Feras Korkees I am a Senior Lecturer in Polymers and Composites at the Material Science and Engineering Department, Swansea University, Wales, UK. My research interest is primarily in the area of long-term lifetime behavior of polymers and composites with a special focus on conventional fiber-reinforced composites, nanocomposites, 3D printed composites, and bio polymers and composites. This involves manufacturing, gravimetric studies, testing of mechanical properties, and the use of a range of analysis techniques (DSC, TGA, FTIR, DMA, NMR Mouse, DEA) for the investigation of physical properties. Most of this research is industrially linked with companies across the UK. In addition to research activities, I teach several courses on polymers and composites to engineering students and I supervise undergraduate and postgraduate research projects across the range of engineering programs at Swansea University.
References
- Agarwal, B. D.; Broutman, L. J.; Chandrashekhara, K. Analysis and Performance of Fiber Composites; New Jersey Wiley: Hoboken, 2018.
- Gerdeen, J. C.; Lord, H. W.; Rorrer, R. A. L. Engineering Design with Polymers and Composites; Crc/Taylor & Francis, Boca Raton, 2006.
- Parkin, C. Modelling Moisture Ingres in Composite Materials. PhD Thesis, Swansea University, 2004.
- Jang, B. Z. Advanced Polymer Composites;Asm International: Materials Park, Oh. Boca Raton, USA: CRC Press, 1994.
- Paulo Davim, J. Green Composites; De Gruyter: Berlin/Boston, 2017; Vol. 7.
- Shirvanimoghaddam, K.; Hamim, S. U.; Karbalaei Akbari, M.; Fakhrhoseini, S. M.; Khayyam, H.; Pakseresht, A. H.; Ghasali, E.; Zabet, M.; Munir, K. S.; Jia, S., et al. Carbon Fiber Reinforced Metal Matrix Composites: Fabrication Processes and Properties. Compos. Part A. 2017, 92, 70–96. DOI: 10.1016/j.compositesa.2016.10.032.
- Korkees, F. Modelling of Water Absorption into Carbon Fiber/Epoxy Composites. Ph.D. Thesis, Swansea University, 2012.
- Zafar, A.; Bertocco, F.; Schjødt-Thomsen, J.; Rauhe, J. C. Investigation of the Long Term Effects of Moisture on Carbon Fiber and Epoxy Matrix Composites. Compos. Sci. Technol. 2012, 72(6), 656–666. DOI: 10.1016/j.compscitech.2012.01.010.
- Sharma, A. K.; Bhandari, R.; Aherwar, A.; Rimašauskienė, R. Matrix Materials Used in Composites: A Comprehensive Study. Mater. Today Proc. 2020, 21, 1559–1562. DOI: 10.1016/j.matpr.2019.11.086.
- Liu, Y.; Zwingmann, B.; Schlaich, M. Carbon Fiber Reinforced Polymer for Cable Structures—A Review. Polym. 2015, 7, 2078–2099. DOI: 10.3390/polym7101501.
- Kelley, A.; Cahn, R. W.; Bever, M. B. Concise Encyclopedia of Composite Materials; Oxford: Pergamon, 1995.
- Callister, W. D. Student Solutions Manual to Accompany Materials Science and Engineering: An Introduction; Wiley, Cop: New York, 2000.
- Clyne, T. W.; Hull, D. An Introduction to Composite Materials; Cambridge University Press: Cambridge, 2019. 10.1017/9781139050586
- Young, R. J.; Lovell, P. A. Introduction to Polymers; CRC Press: Boca Raton, 2011.
- Mark, F. H. Encyclopedia of Polymer Science and Technology, 3rd ed.; John Wiley and Sons, 2004.
- Arnold, J. C. Environmental Effects on Crack Growth in Composites. Compreh. Struct. Integr. 2007, 428–470. DOI: 10.1016/b978-008043749-1/00318-8.
- Mikols, W. J.; Seferis, J. C.; Apicella, A.; Nicolais, L. Evaluation of Structural Changes in Epoxy Systems by Moisture Sorption-Desorption and Dynamic Mechanical Studies. Polym. Compos. 1982, 3, 118–124. DOI: 10.1002/pc.750030304.
- Sahlin, J. J.; Peppas, N. A. Penetrant Transport in Epoxy Resins. Indus. Eng. Chem. Res. 1991, 30(1), 211–217. DOI: 10.1021/ie00049a032.
- Sethi, S.; Ray, B. C. Environmental Effects on Fiber Reinforced Polymeric Composites: Evolving Reasons and Remarks on Interfacial Strength and Stability. Adv. Collo. Interf. Sci. 2015, 217, 43–67. DOI: 10.1016/j.cis.2014.12.005.
- MatWeb. Overview of Materials for Epoxy Cure Resin. Available online: https://www.matweb.com/search/datasheet_print.aspx?matguid=956da5edc80f4c62a72c15ca2b923494 (accessed on 15 January 2023).
- Gillet, C.; Tamssaouet, F.; Hassoune-Rhabbour, B.; Tchalla, T.; Nassiet, V. Parameters Influencing Moisture Diffusion in Epoxy-Based Materials During Hygrothermal Ageing—A Review by Statistical Analysis. Polymers. 2022, 14, 2832. DOI: 10.3390/polym14142832.
- Shalin, R. E. Polymer Matrix Composites; Springer Science & Business Media, 2012.
- Halliwell, S. M. Polymer Composites in Construction; Construction Research Communications Ltd., Crc: Watford, 2000.
- Bergant, Z.; Savin, A.; Grum, J. Effects of Manufacturing Technology on Static, Multi-Frequency Dynamic Mechanical Analysis and Fracture Energy of Cross-Ply and Quasi-Isotropic Carbon/Epoxy Laminates. Polym. Polym. Compos. 2018, 26, 358–370. DOI: 10.1177/0967391118798266.
- Mallick, P. K. Fiber-Reinforced Composites: Materials, Manufacturing, and Design, 3rd ed.; Raton, USA: CRC Press, 2007.
- Davies, L.; Day, R.; Bond, D.; Nesbitt, A.; Ellis, J.; Gardon, E. Effect of Cure Cycle Heat Transfer Rates on the Physical and Mechanical Properties of an Epoxy Matrix Composite. Compos. Sci. Technol. 2007, 67, 1892–1899. DOI: 10.1016/j.compscitech.2006.10.014.
- Davis, R. M. Flexible Composite Prepreg Materials, Patent Application Publication, US 2010/0075144A1, 2010, 1–4.
- Galos, J. Microwave Processing of Carbon Fiber Polymer Composites: A Review. Polym. Compos. 2020, 29(3), 151–162. DOI: 10.1177/0967391120903894.
- Korkees, F.; Allenby, J.; Dorrington, P. 3D Printing of Composites: Design Parameters and Flexural Performance. J. Rapid. Proto. 2020, 26(4), 699–706. DOI: 10.1108/rpj-07-2019-0188.
- Howard, J. C.; Eggbeer, D.; Dorrington, P.; Korkees, F.; Tasker, L. H. Evaluating Additive Manufacturing for the Production of Custom Head Supports: A Comparison Against a Commercial Head Support Under Static Loading Conditions. Proc. Inst. Mech. Eng, Part H. 2020, 234(5), 458–467. DOI: 10.1177/0954411919899844.
- Swart, R.; Korkees, F.; Dorrington, P.; Thurman, J. Evaluation of the Impact Performance and Energy Absorption Capabilities of 3D Printed Composites. J. Rapid. Proto. 2022, 28(9), 1636–1654. DOI: 10.1108/rpj-10-2021-0287.
- Rajaram, A. N.; Gin Boay, C.; Srikanth, N. Effect of Curing on the Hygrothermal Behavior of Epoxy and Its Carbon Composite Material. Compos. Commun. 2020, 22, 100507. DOI: 10.1016/j.coco.2020.100507.
- Broughton, W. R.; Maxwell, A. S. Accelerated Environmental Ageing of Polymeric materials. A National Measurement Good Practice Guide No 103. 2007.
- Ghorbel, I.; Valentin, D. Hydrothermal Effects on the Physico-Chemical Properties of Pure and Glass Fiber Reinforced Polyester and Vinylester Resins. Polym. Compos. 1993, 14(4), 324–334. DOI: 10.1002/pc.750140408.
- Harper, C. A.; Edward, P. M. Plastics Materials and Processes: A Concise Encyclopedia; John Wiley and Sons, 2003. 10.1002/0471459216
- Ray, B. C. Effects of Changing Environment and Loading Speed on Mechanical Behavior of FRP Composites. J. Reinf. Plast. Compos. 2006, 25, 1227–1240. DOI: 10.1177/0731684406059783.
- Marom, G. The Role of Water Transport in Composite Materials. Polym. Perm, 1985, 341–374. DOI:10.1007/978-94-009-4858-7_9.
- Crank, J. The Mathematics of Diffusion, 2nd ed.; J. W. Arrowmith LTD: Bristol, England, UK, 1975.
- Chin, J. W.; Nguyen, T.; Aouadi, K. Sorption and Diffusion of Water, Salt Water, and Concrete Pore Solution in Composite Matrices. J. Appl. Polym. Sci. 1999, 71(3), 483–492. DOI: 10.1002/(SICI)1097-4628(19990118)71:3<483:AID-APP15>3.0.CO;2-S.
- Aoki, Y.; Yamada, K.; Ishikawa, T. Effect of Hygrothermal Condition on Compression After Impact Strength of CFRP Laminates. Compos. Sci. Technol. 2008, 68, 1376–1383. DOI: 10.1016/j.compscitech.2007.11.015.
- Luo, H. L.; Lian, J. J.; Wan, Y. Z.; Huang, Y.; Wang, Y. L.; Jiang, H. J. Moisture Absorption in VARTMed Three-Dimensional Braided Carbon-Epoxy Composites with Different Interface Conditions. Mater. Sci. Eng. A. 2006, 425, 70–77. DOI: 10.1016/j.msea.2006.03.031.
- Tsai, C. L.; Cheng, M.-C.; Chang, S.-L. Gradient-Dependent Model for Moisture Diffusion in a Polymer Matrix Composite Laminate. J. Compos. Mater. 2006, 41(4), 419–434. DOI: 10.1177/0021998306063794.
- Thwe, M. M.; Liao, K. Effects of Environmental Aging on the Mechanical Properties of Bamboo–Glass Fiber Reinforced Polymer Matrix Hybrid Composites. Compos. Part A. 2002, 33, 43–52. DOI: 10.1016/s1359-835x(01)00071-9.
- Cussler, E. L. Diffusion Mass Transfer in Fluid Systems; 2nd ed.; Cambridge, UK: Cambridge University Press, 1997; pp. 15–18.
- Wolff, E. G. Introduction to the Dimensional Stability of Composite Materials; Lancaster, Pennsylvania, USA: DEStech Publications, Inc, 2004.
- Comyn, J. Polymer Permeability, Chapman & Hall: London, 1985. 10.1007/978-94-009-4858-7.
- Adams, D. F. Properties Characterization Mechanical/Physical/Hygrothermal Properties Test Methods. In Reference Book for Composite Technology, 2nd ed.; Lee, S. M., Ed.; Technomic Publishing Co: USA, 1989; pp. 49–81.
- Gurtin, M. E.; Yatomi, C. On a Model for Two Phase Diffusion in Composite Materials. J. Compos. Mater. 1979, 13, 126–130. DOI: 10.1177/002199837901300204.
- Weitsman, Y. Moisture in Composites: Sorption and Damage. In Fatigue of Composite Materials; Reifsnider, K. L. Ed; Elsevier Science Publishers B.V:1991; pp. 385–429. 10.1016/B978-0-444-70507-5.50013-5
- Arnold, J. C.; Korkees, F.; Alston, S. The Long-Term Water Absorption and Desorption Behavior of Carbon–Fiber/epoxy Composites. In Proceedings of the ECCM15- 15th European Conference on Composite Materials, Venice, Italy, 24-28 June, 2012.
- Korkees, F.; Alston, S.; Arnold, C. Directional Diffusion of Moisture in Carbon Fibre/Epoxy Composites: Experiments and Modeling. 20th international conference on composite materials, Copenhagen, Denmark, 19–24 July 2015.
- Broughton, W. R.; Lodeiro, M. J. Techniques for Monitoring Water Absorption in Fiber-Reinforced Polymer Composites. Available online: https://eprintspublications.npl.co.uk/1840/ (accessed on February 22, 2023).
- Shen, C.-H.; Springer, G. S. Moisture Absorption and Desorption of Composite Materials. J. Compos. Mater. 1976, 10, 2–20. DOI: 10.1177/002199837601000101.
- Starink, M. J.; Starink, L. M. P.; Chambers, A. R. Moisture Uptake in Monolithic and Composite Materials: Edge Correction for Rectanguloid Samples. J. Mater. Sci. 2002, 37, 287–294. DOI: 10.1023/a:1013692026782.
- Bao, L.-R.; Yee, A. F. Effect of Temperature on Moisture Absorption in a Bismaleimide Resin and Its Carbon Fiber Composites. Polym. 2002, 43, 3987–3997. DOI: 10.1016/s0032-3861(02)00189-1.
- Hahn, H. T. Hygrothermal Damage in Graphite/Epoxy Laminates. J. Eng. Mater. Technol. Trans. Asme. 1987, 109, 3–11. DOI:10.1115/1.3225930.
- Weitsman, J. Effect of Fluids on Polymeric Composites-A Review. Report to Office of Naval Research, Mechanical and Aerospace Engineering and Engineering Science, Report MAES98-5.0-CM, University of Tennessee, 1998.
- Arnold, J. C.; Alston, S. M.; Korkees, F. An Assessment of Methods to Determine the Directional Moisture Diffusion Coefficients of Composite Materials. Compos. Part A. 2013, 55, 120–128. DOI: 10.1016/j.compositesa.2013.08.012.
- Korkees, F.; Swart, R.; Barsoum, I. Diffusion Mechanism and Properties of Chemical Liquids and Their Mixtures in 977‐2 Epoxy Resin. Polym. Eng. Sci. 2022, 62(5), 1582–1592. DOI: 10.1002/pen.25946.
- Jarrett, W.; Korkees, F. Environmental Impact Investigation on the Interlaminar Properties of Carbon Fiber Composites Modified with Graphene Nanoparticles. Polymer. 2022, 252, 124921. DOI: 10.1016/j.polymer.2022.124921.
- Harper, B. D.; Staab, G. H.; Chen, R.-S. A Note on the Effects of Voids Upon the Hygral and Mechanical Properties of AS4/3502 Graphite/Epoxy. J. Compos. Mater. 1987, 21(3), 280–289. DOI: 10.1177/002199838702100306.
- Weitsman, Y. J. Effects of Fluids on Mechanical Properties and Performance. Mech. Eng. Ser. 2011, 123–144. DOI: 10.1007/978-1-4614-1059-1_7.
- Placette, M. D.; Fan, X.; Zhao, J.-H.; Edwards, D. A Dual Stage Model of Anomalous Moisture Diffusion and Desorption in Epoxy Mold Compounds. 12th Intl. Conf. On Thermal, Mechanical & Multi-Physics Simulation And Experiments In Microelectronics And Microsystems. 2011. 10.1109/esime.2011.5765824.
- Carter, H. G.; Kibler, K. G. Langmuir-Type Model for Anomalous Moisture Diffusion in Composite Resins. J. Compos. Mater. 1978, 12(2), 118–131. DOI: 10.1177/002199837801200201.
- Korkees, F.; Alston, S.; Arnold, C. Directional Diffusion of Moisture into Unidirectional Carbon Fiber/Epoxy Composites: Experiments and Modeling. Polym. Compos. 2017, 39(S4), E2305–E2315. DOI: 10.1002/pc.24626.
- Popineau, S.; Rondeau-Mouro, C.; Sulpice-Gaillet, C.; Shanahan, M. E. R. Free/Bound Water Absorption in an Epoxy Adhesive. Polymer. 2005, 46(24), 10733–10740. DOI: 10.1016/j.polymer.2005.09.008.
- Roy, S.; Xu, W.; Keun Park, S.; Liechti, K. M. Anomalous Moisture Diffusion in Viscoelastic Polymers: Modeling and Testing. J. Appl. Mech. 2000, 67(2), 391–396. DOI: 10.1115/1.1304912.
- Cai, L.-W.; Weitsman, Y. Non-Fickian Moisture Diffusion in Polymeric Composites. J. Compos. Mater. 1994, 28(2), 130–154. DOI: 10.1177/002199839402800203.
- Bonniau; Bunsell, A. R.; Bonniau, P. A Comparative Study of Water Absorption Theories Applied to Glass Epoxy Composites. J. Compos. Mater. 1981, 15(3), 272–293. DOI: 10.1177/002199838101500306.
- Huang, S.; Fu, Q.; Yan, L.; Kasal, B. Characterization of Interfacial Properties Between Fibre and Polymer Matrix in Composite Materials – a Critical Review. J. Mater. Res. Technol. 2021, 13, 1441–1484. DOI: 10.1016/j.jmrt.2021.05.076.
- Kafodya, I.; Xian, G.; Li, H. Durability Study of Pultruded CFRP Plates Immersed in Water and Seawater Under Sustained Bending: Water Uptake and Effects on the Mechanical Properties. Compos. Part B. 2015, 70, 138–148. DOI: 10.1016/j.compositesb.2014.10.034.
- Whitney, J.; Browning, C. Some Anomalies Associated with Moisture Diffusion in Epoxy Matrix Composite Materials. Adv. Compos. Mater—Environ. Effect, 43–4318. DOI: 10.1520/stp34857s.
- Wan, Y. Z.; Wang, Y. L.; Cheng, G. X.; Han, K. Y. Three-Dimensionally Braided Carbon Fiber-Epoxy Composites, a New Type of Material for Osteosynthesis Devices. I. Mechanical Properties and Moisture Absorption Behavior. J. Appl. Polym. Sci. 2002, 85(5), 1031–1039. DOI: 10.1002/app.10495.
- Alston, S.; Korkees, F.; Arnold, C. Finite Element Modelling of Moisture Uptake in Carbon Fibre/Epoxy Composites: A Multi-Scale Approach. In Proceedings of the ECCM15 Proceedings; ESCM: 15th European Conference on Composite Materials; Venice, Italy, 2012; pp. 24–28.
- Neumann, S.; Marom, G. Free-Volume Dependent Moisture Diffusion Under Stress in Composite Materials. J. Mater. Sci. 1986, 21(1), 26–30. DOI: 10.1007/bf01144694.
- Neumann, S.; Marom, G. Prediction of Moisture Diffusion Parameters in Composite Materials Under Stress. J. Compos. Mater. 1987, 21, 68–80. DOI: 10.1177/002199838702100105.
- Dhakal, H. N.; Zhang, Z. Polymer Matrix Composites: Moisture Effects and Dimensional Stability. Encyclo. Compos. 2012. DOI: 10.1002/9781118097298.weoc178.
- Marsh, L. L.; Lasky, R.; Seraphim, D. P.; Springer, G. S. Moisture Solubility and Diffusion in Epoxy and Epoxy-Glass Composites. IBM J. Res. Develop. 1984, 28(6), 655–661. DOI: 10.1147/rd.286.0655.
- Sperling, L. H. Introduction to Physical Polymer Science; Hoboken Wiley, 2006. 10.1002/0471757128.
- Krevelen, V. Properties of Polymers: Their Correlation with Chemical Structure: Their Numerical Estimation and Prediction from Additive Group Contributions; Elsevier: Amsterdam, 2009.
- Parvatareddy, H.; Heithoff, C.; Clifton, A.; Dillard, D.; Kander, R. Environmental Stress Cracking and Solvent Effects in High-Performance Polymeric Composites. Compos. Mater: Test. Des. 1996, 12, 56–5613. DOI: 10.1520/stp16538s.
- Bernier, G. A.; Kambour, R. P. The Role of Organic Agents in the Stress Crazing and Cracking of Poly(2,6-Dimethyl-1,4-Phenylene Oxide). Macromolecules. 1968, 1(5), 393–400. DOI: 10.1021/ma60005a005.
- Vanlandingham, M. R.; Eduljee, R. F.; Gillespie, J. W. Moisture Diffusion in Epoxy Systems. J. Appl. Polym. Sci. 1999, 71, 787–798. DOI: 10.1002/SICI1097-46281999013171:5<787:AID-APP12>3.0.CO;2-A.
- Pérez-Pacheco, E.; Cauich-Cupul, J. I.; Valadez-González, A.; Herrera-Franco, P. J. Effect of Moisture Absorption on the Mechanical Behavior of Carbon Fiber/Epoxy Matrix Composites. J. Mater. Sci. 2012, 48(5), 1873–1882. DOI: 10.1007/s10853-012-6947-4.
- Shen, C.; Springer, G. S. Moisture Absorption and Desorption of Composite Materials. In Environmental Effects on Composite Material, USA: CRC Press, Taylor & Francis, 1988; Vol. 3, pp. 15–34.
- Wan, Y. Z.; Han, K. Y.; Wang, Y. L.; Huang, Y. Moisture Sorption of a Three-Dimensional Braided Carbon Fiber-Epoxy Composite Under Different Media. J. Appl. Polym. Sci. 2005, 97, 507–512. DOI: 10.1002/app.21768.
- Wan, Y. Z.; Wang, Y. L.; Huang, Y.; He, B. M.; Han, K. Y. Hygrothermal Aging Behavior of VARTMed Three-Dimensional Braided Carbon-Epoxy Composites Under External Stresses. Compos. Part A. 2005, 36(8), 1102–1109. DOI: 10.1016/j.compositesa.2005.01.003.
- Loos, A. C.; Springer, G. S. Moisture Absorption of Graphite-Epoxy Composites Immersed in Liquids and in Humid Air. J. Compos. Mater. 1979, 13, 131–147. DOI: 10.1177/002199837901300205.
- Chaplin, A.; Hamerton, I.; Herman, H. Studying Water Uptake Effects in Resins Based on Cyanate Ester/Bismaleimide Blends. Polymer. 2000, 41(11), 3945–3956. DOI: 10.1016/s0032-3861(99)00603-5.
- El-Sa’ad, L.; Darby, M. I.; Yates, B. Moisture Absorption by Epoxy Resins: The Reverse Thermal Effect. J. Mater. Sci. 1990, 25(8), 3577–3582. DOI: 10.1007/bf00575392.
- McKague, E. L.; Reynolds, J. D.; Halkias, J. E. Moisture Diffusion in Fiber Reinforced Plastics. J. Eng. Mater. Technol. 1976, 98(1), 92–95. DOI: 10.1115/1.3443342.
- Chateauminois, A.; Vincent, L.; Chabert, B.; Soulier, J. P. Study of the Interfacial Degradation of a Glass-Epoxy Composite During Hygrothermal Ageing Using Water Diffusion Measurements and Dynamic Mechanical Thermal Analysis. Polym. 1994, 35(22), 4766–4774. DOI: 10.1016/0032-3861(94)90730-7.
- Cauich-Cupul, J. I.; Pérez-Pacheco, E.; Valadez-González, A.; Herrera-Franco, P. J. Effect of Moisture Absorption on the Micromechanical Behavior of Carbon Fiber/Epoxy Matrix Composites. J. Mater. Sci. 2011, 46(20), 6664–6672. DOI: 10.1007/s10853-011-5619-0.
- Ray, B. C. Temperature Effect During Humid Ageing on Interfaces of Glass and Carbon Fibers Reinforced Epoxy Composites. J. Collo. Interf. Sci. 2006, 298(1), 111–117. DOI: 10.1016/j.jcis.2005.12.023.
- Fields, R. E. Overview of Testing and Certification. Compos, 2001, 734–740. DOI:10.31399/asm.hb.v21.a0003439.
- Xiao, G. Z.; Shanahan, M. E. R. Water Absorption and Desorption in an Epoxy Resin with Degradation. J. Polym. Sci. Part B: Polym. Phys. 1997, 35(16), 2659–2670. DOI: 10.1002/(SICI)1099-0488(19971130)35:16<2659:AID-POLB9>3.0.CO;2-K.
- Kambour, R. P.; Gruner, C. L.; Romagosa, E. E. Biphenol-A Polycarbonate Immersed in Organic Media. Swelling and Response to Stress. Macromol. 1974, 7, 248–253. DOI: 10.1021/ma60038a018.
- Andreopoulos, A. G.; Tarantili, P. A. Water Sorption Characteristics of Epoxy Resin–UHMPE Fibers Composites. J. Appl. Polym. Sci. 1998, 70(4), 747–755. DOI: 10.1002/(SICI)1097-4628(19981024)70:4<747:AID-APP14>3.0.CO;2-U.
- Wang, J. Z.; Dillard, D. A.; Wolcott, M. P.; Kamke, F. A.; Wilkes, G. L. Transient Moisture Effects in Fibers and Composite Materials. J. Compos. Mater. 1990, 24, 994–1009. DOI: 10.1177/002199839002400906.
- Vallittu, P. K. Effect of 180-Week Water Storage on the Flexural Properties of E-Glass and Silica Fiber Acrylic Resin Composite. Int. J. Prosthodontics. 2000, 13, 334–339.
- Roy, S.; Xu, W.-Q. Modeling of Diffusion in the Presence of Damage in Polymer Matrix Composites. Int. J. Solid Struct. 2001, 38, 115–126. DOI: 10.1016/s0020-7683(00)00006-8.
- Tsuda, K. 液体環境における熱硬化性プラスチックの劣化とその機構. J. Japan. Petrol. Instit. 2007, 50(5), 240–248. DOI: 10.1627/jpi.50.240.
- Xiao, G. Z.; Delamar, M.; Shanahan, M. E. R. Irreversible Interactions Between Water and DGEBA/DDA Epoxy Resin During Hygrothermal Aging. J. Appl. Polym. Sci. 1997, 65(3), 449–458. DOI: 10.1002/(SICI)1097-4628(19970718)65:3<449:AID-APP4>3.0.CO;2-H.
- Wazzan, A. A.; Al‐Turaif, H. A.; Daous, M. A. Daous Influence of KOH Solution on the Tensile Strength and Chemical Stability of Carbon Fiber-Reinforced Epoxy Resin Composites. J. Appl. Polym. Sci. 2005, 96, 1682–1690. DOI: 10.1002/app.21634.
- Ofoegbu, S.; Ferreira, M.; Zheludkevich, M. Galvanically Stimulated Degradation of Carbon-Fiber Reinforced Polymer Composites: A Critical Review. Mater. 2019, 12(4), 651. DOI: 10.3390/ma12040651.
- Almudaihesh, F.; Holford, K.; Pullin, R.; Eaton, M. The Influence of Water Absorption on Unidirectional and 2D Woven CFRP Composites and Their Mechanical Performance. Compos. Part B. 2020, 182, 107626. DOI: 10.1016/j.compositesb.2019.107626.
- Kim, H.; Takemura, K. Influence of Water Absorption on Creep Behavior of Carbon Fiber/Epoxy Laminates. Proc. Eng. 2011, 10, 2731–2736. DOI: 10.1016/j.proeng.2011.04.455.
- Korkees, F.; Arnold, C.; Alston, S. Water Absorption and Low-Energy Impact and Their Role in the Failure of ±45° Carbon Fibre Composites. Polym. Compos. 2018, 39(8), 2771–2782. DOI: 10.1002/pc.24269.
- Shetty, K.; Bojja, R.; Srihari, S. Effect of Hygrothermal Aging on the Mechanical Properties of IMA/M21E Aircraft-Grade CFRP Composite. Advance. Compos. Lett. 2020, 29, 2–9. DOI: 10.1177/2633366x20926520.
- Tsai, Y. I.; Bosze, E. J.; Barjasteh, E.; Nutt, S. R. Influence of Hygrothermal Environment on Thermal and Mechanical Properties of Carbon Fiber/Fiberglass Hybrid Composites. Compos. Sci. Technol. 2009, 69, 432–437. DOI: 10.1016/j.compscitech.2008.11.012.
- Boukhoulda, B. F.; Adda-Bedia, E.; Madani, K. The Effect of Fiber Orientation Angle in Composite Materials on Moisture Absorption and Material Degradation After Hygrothermal Ageing. Compos. Struct. 2006, 74, 406–418. DOI: 10.1016/j.compstruct.2005.04.032.
- Cândido, G. M.; Costa, M. L.; Rezende, M. C.; Almeida, S. F. M. Hygrothermal Effects on Quasi-Isotropic Carbon Epoxy Laminates with Machined and Molded Edges. Compos. Part B. 2008, 39, 490–496. DOI: 10.1016/j.compositesb.2007.03.007.
- Ryan, J. M. Relating Moisture Ingress to Component Strength and Stiffness for Carbon-Fiber Composites. Thesis, Swansea University, 2011.
- Cotugno, S.; Larobina, D.; Mensitieri, G.; Musto, P.; Ragosta, G. A Novel Spectroscopic Approach to Investigate Transport Processes in Polymers: The Case of Water–Epoxy System. Polym. 2001, 42(15), 6431–6438. DOI: 10.1016/s0032-3861(01)00096-9.
- Dao, B.; Hodgkin, J.; Krstina, J.; Mardel, J.; Tian, W. Accelerated Ageing versus Realistic Ageing in Aerospace Composite Materials. V. The Effects of Hot/Wet Ageing in a Structural Epoxy Composite. J. Appl. Polym. Sci. 2010, 115(2), 901–910. DOI: 10.1002/app.31029.
- Dao, B.; Hodgkin, J.; Krstina, J.; Mardel, J.; Tian, W. Accelerated Ageing versus Realistic Ageing in Aerospace Composite Materials. IV. Hot/Wet Ageing Effects in a Low Temperature Cure Epoxy Composite. J. Appl. Polym. Sci. 2007, 106(6), 4264–4276. DOI: 10.1002/app.27104.
- Lee, M. C.; Peppas, N. A. Water Transport in Graphite/Epoxy Composites. J. Appl. Polym. Sci. 1993, 47(8), 1349–1359. DOI: 10.1002/app.1993.070470805.
- Zhou, J.; Lucas, J. P. The Effects of a Water Environment on Anomalous Absorption Behavior in Graphite/Epoxy Composites. Compos. Sci. Technol. 1995, 53, 57–64. DOI: 10.1016/0266-3538(94)00078-6.
- Korkees, F.; Arnold, C.; Alston. S. An Investigation of the Long-Term Water Uptake Behavior and Mechanisms of Carbon Fiber/977-2 Epoxy Composites. Polym. Eng. Sci. 2018, 58(12), 2175–2184. DOI: 10.1002/pen.24830.
- Arao, Y.; Koyanagi, J.; Hatta, H.; Kawada, H. Analysis of Time-Dependent Deformation of CFRP Considering the Anisotropy of Moisture Diffusion. Adv. Compos. Mater. 2008, 17, 359–372. DOI: 10.1163/156855108x385276.
- Arao, Y.; Koyanagi, J.; Hiroshi, H.; Kawada, H.; Aoki, Y. Effect of Moisture Absorption on Dimensional Stability in Carbon/Epoxy Composites. In: Proceedings of 16th International Conference on Composite Materials. Kyoto, Japan, 2007, 1–6.
- Blows, R. Development of Novel Thin-Ply Technology for Carbon Fiber Composite Materials. Ph.D. Thesis, Swansea University, 2019.
- Karbhari, V. M.; Xian, G. Hygrothermal Effects on High Vf Pultruded Unidirectional Carbon/Epoxy Composites: Moisture Uptake. Compos. Part B. 2009, 40(1), 41–49. DOI: 10.1016/j.compositesb.2008.07.003.
- Korkees, F.; Morris, E.; Jarrett, W.; Swart, R. Characterization of Moisture Absorption and Flexural Performance of Functionalized Graphene Modified Carbon Fiber Composites Under Low Energy Impact. Polym. Compos. 2023. 6, 3325–3340. DOI: 10.1002/pc.27324.
- Davim, J.; Rubio, J.; Abrao, A. A Novel Approach Based on Digital Image Analysis to Evaluate the Delamination Factor After Drilling Composite Laminates. Compos. Sci. Tech. 2007, 67(9), 1939–1945. DOI: 10.1016/j.compscitech.2006.10.009.
- Geier, N.; Davim, J. P.; Szalay, T. Advanced Cutting Tools and Technologies for Drilling Carbon Fibre Reinforced Polymer (CFRP) Composites: A Review. Compos. Part A: Appl. Sci. Manuf. 2019, 125, 105552. DOI: 10.1016/j.compositesa.2019.105552.
- Gaitonde, V. N.; Karnik, S. R.; Rubio, J. C.; Correia, A. E.; Abrão, A. M.; Davim, J. P. A Study Aimed at Minimizing Delamination During Drilling of CFRP Composites. J. Compos. Mater. 2011, 45(22), 2359–2368. DOI: 10.1177/0021998311401087.
- Babu, J.; Sunny, T.; Alex Paul, N.; Mohan, K. P.; Philip, J.; Paulo Davim, J. Assessment of Delamination in Composite Materials: A Review. Proc. Inst. Mech. Eng. B J. Eng. Manuf. 2016, 230(11), 1990–2003. DOI: 10.1177/0954405415619343.
- Seif, M. A.; Khashaba, U. A.; Rojas-Oviedo, R. Measuring Delamination in Carbon/Epoxy Composites Using a Shadow Moiré Laser Based Imaging Technique. Compos. Struct. 2007, 79(1), 113–118. DOI: 10.1016/j.compstruct.2005.11.039.
- Korkees, F.; Aldrees, A.; Barsoum, I.; Alshammari, D. Functionalised Graphene Effect on the Mechanical and Thermal Properties of Recycled PA6/PA6, 6 Blends. J. Compos. Mater. 2021, 55(16), 2211–2224. DOI: 10.1177/0021998320987897.
- Springer, G. S. Environmental Effects on Composite Materials; USA: CRC Press, Taylor & Francis, 1988.
- Chugang, H. U.; Kim, J.-K. Epoxy-Organoclay Nanocomposites: Morphology, Moisture Absorption Behavior and Thermo-Mechanical Properties. Compos. Interf. 2005, 12(3–4), 271–289. DOI: 10.1163/1568554053971597.
- Cysne Barbosa, A. P.; Fulco, A. P. P.; Guerra, E. S.; Arakaki, F. K.; Tosatto, M.; Costa, M. C. B.; Melo, J. D. D. Accelerated Aging Effects on Carbon Fiber/Epoxy Composites. Compos. Part B. 2017, 110, 298–306. DOI: 10.1016/j.compositesb.2016.11.004.
- Masoumi, S.; Valipour, H. Effects of Moisture Exposure on the Crosslinked Epoxy System: An Atomistic Study. Model. Simul. Mater. Sci. Eng. 2016, 24, 035011. DOI: 10.1088/0965-0393/24/3/035011.
- Soles, C. L.; Chang, F. T.; Bolan, B. A.; Hristov, H. A.; Gidley, D. W.; Yee, A. F. Contributions of the Nanovoid Structure to the Moisture Absorption Properties of Epoxy Resins. J. Polym. Sci. Part B: Polym. Phys. 1998, 36, 3035–3048. DOI: 10.1002/(SICI)1099-0488(199812)36:17<3035:AID-POLB4>3.0.CO;2-Y.
- Zhong, Y.; Cheng, M.; Zhang, X.; Hu, H.; Cao, D.; Li, S. Hygrothermal Durability of Glass and Carbon Fiber Reinforced Composites – a Comparative Study. Compos. Struct. 2019, 211, 134–143. DOI: 10.1016/j.compstruct.2018.12.034.
- Nishizaki, I.; Meiarashi, S. Long-Term Deterioration of GFRP in Water and Moist Environment. J. Compos. Construc. 2002, 6(1), 21–27. DOI: 10.1061/(asce)1090-0268.
- Eckstein, B. H. Moisture Absorption by Epoxy Laminating Resins. ACS Org. Coatings Div, Plast. Chem. Prepr. 1978, 38, 503–509.
- Zhao, H.; Li, R. K. Y. Effect of Water Absorption on the Mechanical and Dielectric Properties of Nano-Alumina Filled Epoxy Nanocomposites. Compos. Part A. 2008, 39(4), 602–611. DOI: 10.1016/j.compositesa.2007.07.006.
- Adamson, M. J. Thermal Expansion and Swelling of Cured Epoxy Resin Used in Graphite/Epoxy Composite Materials. J. Mater. Sci. 1980, 15(7), 1736–1745. DOI: 10.1007/bf00550593.
- Woo, M.; Piggot, J. Water Absorption of Resins and Composites: I. Epoxy Homopolymers and Copolymers. J. Compos. Technol. Res. 1987, 9, 101–107. DOI: 10.1520/ctr10249j.
- Jelinski, L. W.; Dumais, J. J.; Cholli, A. L.; Ellis, T. S.; Karasz, F. E. Nature of the Water-Epoxy Interaction. Macromolecules. 1985, 18, 1091–1095. DOI: 10.1021/ma00148a008.
- Delasi, R.; Whiteside, J. B. Effect of Moisture on Epoxy Resins and Composites. ASTM Inter. eBooks. 1978, 2–19. DOI: 10.1520/stp34855s.
- Maggana, C.; Pissis, P. Water Sorption and Diffusion Studies in an Epoxy Resin System. J. Polym. Sci. B Polym. Phys. 1999, 37(11), 1165–1182. DOI: 10.1002/(SICI)1099-0488(19990601)37:11<1165:AID-POLB11>3.0.CO;2-E.
- Wong, T. C.; Broutman, L. J. Moisture Diffusion in Epoxy Resins Part I. Non-Fickian Sorption Processes. Polym. Eng. Sci. 1985, 25(9), 521–528. DOI: 10.1002/pen.760250903.
- Abdelkader, A. F.; White, J. R. Water Absorption in Epoxy Resins: The Effects of the Crosslinking Agent and Curing Temperature. J. Appl. Polym. Sci. 2005, 98(6), 2544–2549. DOI: 10.1002/app.22400.
- Nogueira, P.; Ramírez, C.; Torres, A.; José Abad, M.; Cano, J.; López, J. A.; López-Bueno, I.; Barral, L. Effect of Water Sorption on the Structure and Mechanical Properties of an Epoxy Resin System. J. Appl. Polym. Sci. 2001, 80(1), 71–80. DOI: 10.1002/1097-4628(20010404)80:1<71:AID-APP1077>3.0.CO;2-H.
- Xian, G.; Karbhari, V. M. Segmental Relaxation of Water-Aged Ambient Cured Epoxy. Polym. Degrad. Stabil. 2007, 92, 1650–1659. DOI: 10.1016/j.polymdegradstab.2007.06.015.
- Chuanga, W. Y.; Young, T. H.; Wang, D. M.; Luoc, R. L.; Sun, Y. M. Swelling Behavior of Hydrophobic Polymers in Water/Ethanol Mixtures. Polym. 2000, 41(23), 8339–8347. DOI: 10.1016/s0032-3861(00)00176-2.
- Jarrett, W.; Jeffs, S. P.; Korkees, F.; Rawson, M. The Opportunities and Challenges of Hybrid Composite Driveshafts and Their Couplings in the Aerospace Industry: A Review. Compos. Struct. 2023, 320, 117203. DOI: 10.1016/j.compstruct.2023.117203.
- Dutheillet, Y.; Mantle, M.; Vesely, D.; Gladden, L. Diffusion of Water-Acetic Acid Mixtures in Epoxy. J. Polym. Sci. B Polym. Phys. 1999, 37(23), 3328–3336. DOI: 10.1002/(SICI)1099-0488(19991201)37:23<3328:AID-POLB8>3.0.CO;2-N.
- Papanicolaou, G. C.; Pappa, A. Water Sorption and Temperature Effects on the Dynamic Mechanical Behavior of Epoxy-Matrix Particulates. J. Mater. Sci. 1992, 27(14), 3889–3896. DOI: 10.1007/bf00545473.
- Devi, L. U.; Bhagawan, S. S.; Nair, K. C. M.; Thomas, S. Water Absorption Behavior of PALF/GF Hybrid Polyester Composites. Polym. Compos. 2011, 32(3), 335–346. DOI: 10.1002/pc.21034.
- Arnold, J. C.; Alston, S.; Korkees, F.; Dauhoo, S.; Adams, R.; Older, R. Design Optimisation of Carbon Fibre Epoxy Composites Operating in Humid Atmospheres. Composites UK 10th Annual Conference: Innovation in Composites. Birmingham, England, UK; 2010.
- Choi, F.; Ahn, K.-J.; Nam, J.; Jae Chun, H. Hygroscopic Aspects of Epoxy/Carbon Fiber Composite Laminates in Aircraft Environments. Compos. Part A. 2001, 32(5), 709–720. DOI: 10.1016/s1359-835x(00)00145-7.
- De’nève, B.; Shanahan, M. E. R. Water Absorption by an Epoxy Resin and Its Effect on the Mechanical Properties and Infra-Red Spectra. Polym. 1993, 34(24), 5099–5105. DOI: 10.1016/0032-3861(93)90254-8.
- Xiang, Z. D.; Jones, F. R. Thermal-Spike-Enhanced Moisture Absorption by Polymer-Matrix Carbon-Fiber Composites. Compos. Sci. Technol. 1997, 57(4), 451–461. DOI: 10.1016/s0266-3538(96)00168-6.
- Hough, J. A.; Karad, S. K.; Jones, F. R. The Effect of Thermal Spiking on Moisture Absorption, Mechanical and Viscoelastic Properties of Carbon Fiber Reinforced Epoxy Laminates. Compos. Sci. Technol. 2005, 65(7–8), 1299–1305. DOI: 10.1016/j.compscitech.2005.01.009.
- Clark, G.; Saunders, D. S.; van Blaricum, T. J.; Richmond, M. Moisture Absorption in Graphite/Epoxy Laminates. Compos. Sci. Technol. 1990, 39, 355–375. DOI: 10.1016/0266-3538(90)90081-f.
- Karasek, M. L.; Strait, L. H.; Amateau, M. F.; Runt, J. Effect of Temperature and Moisture on the Impact Behavior of Graphite/Epoxy Composites: Part II—Impact Damage. J. Compos. Technol. Res. 1995, 17(1), 11–11. DOI: 10.1520/ctr10509j.
- Schutte, C. L. Environmental Durability of Glass-Fiber Composites. Mater. Sci. Eng. 1994, 13, 265–323. DOI: 10.1016/0927-796x(94)90002-7.
- Rogers, K. F.; Sidey, G. R.; Kingston-Lee, D. M. Ballistic Impact Resistance of Carbon-Fiber Laminates. Compos. 1971, 2(4), 237–241. DOI: 10.1016/0010-4361(71)90152-2.
- Ma, L.; Meng, L.; Fan, D.; He, J.; Yu, J.; Qi, M.; Chen, Z.; Huang, Y. Interfacial Enhancement of Carbon Fiber Composites by Generation 1–3 Dendritic Hexamethylenetetramine Functionalization. Appl. Surf. Sci. 2014, 296, 61–68. DOI: 10.1016/j.apsusc.2014.01.039.
- Warrier, S. K.; Majumdar, B. Effects of the Interface on the Fatigue Crack Growth Response of Titanium Matrix Composites: Modeling and Impact on Interface Design. Mater. Sci. Eng A- Struct Mater. Propert. Microstruct. Process. 1997, 237(2), 256–267. DOI: 10.1016/s0921-5093(97)00423-1.
- Walker, L.; Zhi Hu, X. Mode I Delamination Behavior of Short Fiber Reinforced Carbon Fiber/Epoxy Composites Following Environmental Conditioning. Compos. Sci. Technol. 2003, 63(3–4), 531–537. DOI: 10.1016/s0266-3538(02)00224-5.
- Botelho, E. C.; Pardini, L. C. M C Rezende Hygrothermal Effects on the Shear Properties of Carbon Fiber/Epoxy Composites. J. Mater. Sci. 2006, 41(21), 7111–7118. DOI: 10.1007/s10853-006-0933-7.
- Zai, B. A.; Park, M.; Choi, F.; Mehboob, H.; Ali, R. Effect of Moisture Absorption on Damping and Dynamic Stiffness of Carbon Fiber/Epoxy Composites. J. Mech. Sci. Technol. 2009, 23(11), 2998–3004. DOI: 10.1007/s12206-009-0908-0.
- Takeda, S.; Tsukada, T.; Sugimoto, S.; Iwahori, Y. Monitoring of Water Absorption in CFRP Laminates Using Embedded Fiber Bragg Grating Sensors. Compos. Part A. 2014, 61, 163–171. DOI: 10.1016/j.compositesa.2014.02.018.
- Ayanoglu, M. O.; Carlsson, L. A.; Du, E. Effects of Void Content on the Moisture Uptake and Mechanical Strength of a Glass/Epoxy Composite. J. Compos. Mater. 2022, 57(2), 325–336. DOI: 10.1177/00219983221144500.
- Costa, M. L.; Rezende, M. C.; de Almeida, S. F. M. Effect of Void Content on the Moisture Absorption in Polymeric Composites. Polym-Plast. Technol. Eng. 2006, 45(6), 691–698. DOI: 10.1080/03602550600609549.
- Mercier, J.; Bunsell, A. R.; Castaing, P.; Renard, J. Characterisation and Modelling of Aging of Composites. Compos. Part A. 2008, 39(2), 428–438. DOI: 10.1016/j.compositesa.2007.08.015.
- Zhou, J.; Lucas, J. P. Hygrothermal Effects of Epoxy Resin. Part I: The Nature of Water in Epoxy. Polym. 1999, 40, 5505–5512. DOI: 10.1016/s0032-3861(98)00790-3.
- Fleming, J. G.; Rose, T. Graphite Composites for Ocean Ordnance. Available online: https://apps.dtic.mil/sti/citations/AD0770407 (accessed on April 1, 2023).
- Bao, L.-R.; Yee, A. F.; Charles, Y.-C. Lee Moisture Absorption and Hygrothermal Aging in a Bismaleimide Resin. Polym. 2001, 42(17), 7327–7333. DOI: 10.1016/s0032-3861(01)00238-5.
- Boinard, P.; Banks, W. M.; Pethrick, R. A. Changes in the Dielectric Relaxations of Water in Epoxy Resin as a Function of the Extent of Water Ingress in Carbon Fiber Composites. Polym. 2005, 46(7), 2218–2229. DOI: 10.1016/j.polymer.2004.11.103.
- Lin, Y. C.; Chen, X. Investigation of Moisture Diffusion in Epoxy System: Experiments and Molecular Dynamics Simulations. Chem. Phys. Let. 2005, 412(4–6), 322–326. DOI: 10.1016/j.cplett.2005.07.022.
- Moy, P.; Karasz, F. E. Epoxy-Water Interactions. Polym. Eng. Sci. 1980, 20(4), 315–319. DOI: 10.1002/pen.760200417.
- Ciriscioli, P. R.; Jung Lee, W.; Peterson, D. E.; Springer, G. S.; Tang, J. Accelerated Environmental Testing of Composites. J. Compos. Mater. 1987, 21(3), 225–242. DOI: 10.1177/002199838702100303.
- Apicella, A.; Nicolais, L.; Astarita, G.; Drioli, E. Hygrothermal History Dependence of Equilibrium Moisture Sorption in Epoxy Resins. Polym. 1981, 22, 1064–1067. DOI: 10.1016/0032-3861(81)90293-7.
- Johncock, P.; Tudgey, G. F. Epoxy Systems with Improved Water Resistance, and the Non-Fickian Behavior of Epoxy Systems During Water Ageing. British. Polym. J. 1983, 15(1), 14–18. DOI: 10.1002/pi.4980150105.
- Wong; Broutman, L. J. Water in Epoxy Resins Part II. Diffusion Mechanism. Polym. Eng. Sci. 1985, 25(9), 529–534. DOI: 10.1002/pen.760250904.