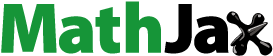
Abstract
The production of biodiesel from transesterification of oils is the currently available alternative to consumable fuels. The study focuses on the performance assessment of a microreactor platform for biodiesel production. Since a microreactor provides better mass transfer and a higher surface-to-volume ratio, this significantly contributes to augmenting the reaction rate of biodiesel production at reduced cost. In this study, firstly the T-shaped microfluidic reactor was fabricated on a PMMA (poly methyl methacrylate) sheet. Then, the kinetics of enzymatic transesterification reaction for biodiesel synthesis in this reactor was investigated. A combination of sunflower oil and methanol was used as feedstock in the presence of lipase from Thermomyces lanuginous as a catalyst and tert-butanol as a solvent. The reaction was carried out under ambient conditions (1 atm and 30 °C) where 285 v% of tert-butanol was loaded to oil with 4 wt% lipase, and the molar ratio of oil to methanol was 1:2.5. Gas Chromatography was used to measure the concentration of biodiesel. The kinetic parameters such as maximum reaction rate (Vmax) and Michaelis –Menten constant (KM) were found to be 0.725 (mol/L.min) and 0.092 mol/L, respectively. High Vmax and low KM values indicated the better performance of the reactor. In addition, a Lineweaver–Burk plot with excellent coefficient of determination (R2) of 99.5% supported the high performance of the microreactor.
1. Introduction
In recent years, there has been a global trend towards replacing non-renewable energy resources. Biodiesel is one such renewable fuel resource that has high potential and plays a crucial role in the sustainability and reduction of greenhouse gases, due to the absence of sulfur and a reduction in the amount of toxic gases released (Demirbas, Citation2007). Biodiesel production found its way into industry in 1988 and since then, it has increased dramatically. For instance, in Europe it has reached a capacity of around nine million tons per year (Luque, Lin, Wilson, & Clark, Citation2016). Biodiesel can be produced from edible oils such as soybean, palm kernel and coconut, non-edible oils such as jatropha, camelina and rice bran, or from side stream while refining soap stock, acidulated soap stock and deodorizer distillates. The demand for oils or lipids for industrial purposes has reached up to 15% for different applications, such as surfactants, detergents and biofuels (Liu, Tan, Zhang, Yan, & Hameed, Citation2010; Luque et al., Citation2016).
Portability, better efficiency, lower sulfur content and aromatic reliability, sustainability and biodegradability of biodiesel are its main advantages over petroleum. The most significant aspects are that it is both renewable and environmentally friendly. Moreover, it can be naturally recycled, and microorganism processes can contribute significantly to its degradation and safer discharge (Zhang, Citation2012). However, in addition to the feature of being a clean source of energy, the fuel is also an economical one.
Traditional biodiesel production methods have a number of limitations, such as high cost, high consumption of energy, a long residence time and low efficiency. To alleviate these problems, a microreactor offers a novel and sustainable approach. Moreover, a microreactor provides a more efficient, more economical “reaction chamber” for the production of biodiesel than those of conventional macro-reactors (Bolivar, Valikhani, & Nidetzky, Citation2019). Continuous flow microreactors enhance both mass transfer and interaction between the phases, which are basic requirements in facilitating the production of biodiesel. Micro mixing configurations such as T-shaped and Y-shaped micro-channels are commonly used to enhance mixing performance in such applications (Natarajan et al., Citation2019; Santana, Silva, & Taranto, Citation2019).
2. Theory
2.1. Transesterification reaction
One of the most commonly used methods in synthesising biodiesel is the transesterification reaction. It is based on the process of exchanging organic groups between ester and alcohol. The raw materials required for the reaction are triglycerides, which can be obtained from animal or plant-based oils and fats and methanol, used due to its high biodiesel yield and feasible price, with the aid of a catalyst. The reaction process follows a three-step mechanism in which triglycerides convert to diglycerides, diglycerides into monoglycerides and monoglycerides into glycerol (Aarthy, Saravanan, Gowthaman, Rose, & Kamini, Citation2014), as follows:
2.2. Enzymatic catalyst
Generally, for any chemical process, catalysts are required due to several reasons: (i) they speed up the reaction, (ii) they help produce products with high yield, (iii) they allow the reaction to work at a much lower temperature, (iv) they can be used repeatedly and (v) they save energy. Therefore, selection of catalyst for a particular reaction is very important. For instance, several types of catalysts such as pure ZnO, nanorods of Hg doped ZnO, multi-walled carbon nanotubes, titanium dioxide, polyaniline (PANI)/ZnO, ZnO/CeO2, ZnO/CuO, a composite of multi-walled carbon nanotube/tungsten oxide, ZnO/Ag/CdO, ZnO/γ-Mn2O3 and V2O5/ZnO nanocomposites are used for removing textile effluent by degradation reaction (Rajendran et al., Citation2016; Saleh & Gupta, Citation2011, Citation2012; Saravanan, Gupta, Mosquera, & Gracia, Citation2014; Saravanan, Gupta, Narayanan, & Stephen, Citation2013, Citation2014; Saravanan, Gupta, Prakash, Narayanan, & Stephen, Citation2013; Saravanan, Karthikeyan, et al., Citation2013; Saravanan, Thirumal, Gupta, Narayanan, & Stephen, Citation2013; Saravanan et al., Citation2015, Citation2016). Similarly, transesterification reaction is conducted in the presence of basic (KOH), acidic (HCl), or enzymatic (e.g., lipase) catalysts (Hossain, Citation2019; Zakir Hossain et al., Citation2016). Among these three methods, lipase catalysed transesterification has been considered as more favorable by many researchers, due to high biodiesel yields. It can also make the product separation easier and can be operated at low temperature and pressure leading to high conversion.
Further, lipases are considered to be the type of enzymes which are able to hydrolyse fat. They play a significant role in digestion and breaking the triglycerides in oils and lipids in the majority of living organisms. Lipases are classified according to their source of origin, such as animals, plants or microorganisms and their properties differ accordingly. One of the most commonly used lipases in industry is Candida Antarctica B, which is commercially known as Novozym435. This lipase, taken from fungi, has shown promising results for biodiesel production (Aarthy et al., Citation2014; Luque et al., Citation2016).
2.3. Microreactor technology
The main attractive features of microreactors are their efficient heat transfer, mass transfer and effective mixing, primarily due to their large surface-to-volume ratios (Suryawanshi, Gumfekar, Bhanvase, Sonawane, & Pimplapure, Citation2018). In addition, the laminar flow of reacted species is a key feature in microscale channels. This develops the efficiency of mixing in microreactors mainly because of the molecular diffusion that predominates in microchannels. In addition, bends in microreactor channels change the direction of the flow, which will lead to better mixing (Aoki, Hasebe, & Mae, Citation2004). Applications where a precise control of the molar ratio between reacted species necessitates having an efficient mixing within the system, which significantly contributes to reducing or eliminating side reactions.
A microreactor is also advantageous when scaling is needed to increase productivity. Scaling of microreactors is based on their numbering up to produce an assembly of microreactors instead of scaling up a pilot plant or an existing reactor in industry (Rizkin, Popovic, & Hartman, Citation2019). The numbering up approach offers profound advantages over the scaling up approach due to the fact that using identical microreactors in parallel produces higher quality than the scaling up of a pilot conventional reactor. Thus, the performance of microreactors remains unchanged through numbering up (Yao, Zhang, Du, Liu, & Yao, Citation2015), which facilitates the use of the same reactors in industry (He et al., Citation2020). In addition, taking into consideration the sustainability of energy sources, microfluidic systems are well aligned to target this aspect, especially because of its economical fabrication and availability (Kockmann, Gottsponer, Zimmermann, & Roberge, Citation2008).
Significant research has been documented for biodiesel production using microreactor systems; however, all of it is complex in design and requires emulsifier to enhance efficiency. This paper aims to construct a simple microreactor platform that does not need any emulsifier to synthesize biodiesel. The kinetics of the enzymatic reaction of biodiesel production has been studied using the Michaelis–Menten model. In addition, the rate of the reaction has been improved.
3. Experimental
3.1. Materials and method
The materials used in this study were T. lanuginous type Lipase solution (Cat. No. 2391 B), sunflower oil, methanol (99.8% purity, Sigma Aldrich, UK) and tert-butanol (from Research Lab Fine Chem Industries, India)
3.2. Reaction setup procedure
To start the experiment, a base was needed to build the reaction conditions3. While the reaction conditions were found to be 50 vol% tert-butanol to oil, 4 wt% lipase to oil and a 1:9 molar ratio of oil to methanol in a batch process, they were as follows in the microreactor: 285% vol% tert-butanol to oil, 4 wt% lipase to oil and 1:2.5 molar ratio of oil to methanol. Therefore, for the experiments, 35 mL of oil was selected as a base for the calculation of the rest of the chemicals: 100 mL of tert-butanol, 1.3 mL lipase and 3.75 mL of methanol. To achieve equal flowrates for the two inlet reservoirs, the chemicals were split evenly as much as possible, according to the details given in .
Table 1. Distribution of the chemicals per inlet of the microfluidic chip.
It is worth mentioning that dealing with tert-butanol at room temperature was a great challenge due to its low boiling point (Tbp=25.6 °C at atmospheric pressure). A lower temperature processing of tert-butanol blocks the microreactor channels. Therefore, the room temperature was controlled at 30 °C in the laboratory.
3.3. Concentration measurement
GC-MS was used to measure the concentration of the products. One of the methods used for gas chromatography quantitative analysis was the external standard calibration. This method requires preparing several standard solutions of methanol and solvent (tert-butanol in this work). Correlation between the peak area and the concentration of methanol was calculated to predict the concentration at any given peak area, according to the Beer-Lambert law principle.
3.4. GC-MS conditions and temperature program
The selected GC-MS column was Capillary DB-624 from Agilent Company. The GC-MS was run at the following operating conditions to get precise readings: The initial column temperature of the GC-MS was maintained at 70 °C for 3 min, then increased linearly at a rate of 25 °C/min. Once the temperature reached 250 °C, it was maintained for 5 min. All samples were injected manually instead of using the auto-injection setup, to guarantee a faster injection rate, hence, more accurate results can be obtained. The manual injection time was 15 sec in comparison with 2 min with the auto-injection setup.
3.5. Microreactor fabrication
An in-house T-shaped microreactor was fabricated. The AutoCAD software package (AutoCAD®, Autodesk 2017) was used to draw the design. An AutoCAD coding was written to mill the design on a poly methyl methacrylate (PMMA) sheet, using a laser beam operated at a velocity of 30 mm/s. The serpentine microchannel geometry was 400 μm width, 780 μm depth and 400 mm length as presented in (), which results in a total volume of 125 mm3. The length of the channel was chosen to produce efficient mixing, according to a previously published study (Yusuf, Redha, Al Meshal, & Shehab, Citation2018). Afterwards, the microreactor () was physically cleaned, then sealed using polyester adhesive laminate (Plastic Art, UK), as shown in . High pressure resistance materials were used as additional sealants to withstand high inlet pressure and thermodynamic resistance in the microchannel. Therefore, a 3 mm PVC laminated sheet (TMI. LLC, Pittsburgh, USA) was cured to secure the channels, followed by a 5 mm metal-based sheet, glued over the laminate, to avoid any leakage. A 2 mm diameter-drilling tool (Toolex Ltd) was used to form the inlets and outlets of the microreactor. Then, 2 mm2 uninsulated bootlace ferrules (RS, Corby, UK) were joined to both inlets and outlets, as illustrated in . The final assembly is presented in which demonstrates the front side of the fabricated microreactor.
3.6. Flowrate setup
A gravitational flow was used to deliver the reactants. The maximum height of this setup produces around 700 µL/min. The inlet flowrate was varied upon changing the height of the input reservoirs (feed syringes), as presented in .
4. Results and discussion
4.1. Flowrate measurement experiment
The range of flowrate in all experiments was 50–300 µL/min. A precise flowrate is a crucial requirement in this application, especially when dealing with microscale devices. Therefore, four runs per flowrate were measured to help improve the precision, as illustrated in .
Table 2. Flowrate measurements.
4.2. Calibration curve determination
A plot of concentrations vs. the GC-MS peak areas is presented in . Three different concentration readings were taken per prepared standard solutions of methanol in tert-butanol. The best linear fit was found with R2 = 0.998, as presented in the graph. Therefore, the concentration of methanol can be calculated using the following equation:
(2)
(2)
4.3. Reaction kinetics evaluation
The rate of reaction was calculated using the following equation:
(3)
(3)
where −rA is the rate of reaction of methanol in (moles/ mL.min), X is the molar conversion in moles reacted/moles fed, FA0 is the molar flowrate of methanol in (moles/time) and V is the volume of reactor in (mL) which is 125 mm3, as mentioned in the fabrication section.
In order to measure the kinetics, the rate expression will be calculated in terms of methanol concentration. Therefore, any decrease in methanol concentration will reflect the amount of biodiesel formed since methanol will be the limiting reactant. EquationEq. (3)(3)
(3) can be rewritten as follows:
(4)
(4)
where CAo is the initial concentration of methanol in (mol/mL), CA is the final concentration of methanol in (mol/mL), is the volumetric flowrate of the feed in (mL/min). The rate of reaction was therefore calculated at different final concentration of methanol, as illustrated in below:
The reduction in methanol concentration in the experiments was an indication for biodiesel production, so the fabricated microreactor proved its suitability for synthesising biodiesel. In addition, the effectiveness of the enzyme used in this work contributes significantly to biodiesel formation. Thus, compared to other types of enzymes, a microbial enzyme is fast to synthesize biodiesel (Wancura et al., Citation2018), inexpensive and more stable, as agreed with Moazeni, Chen, and Zhang (Citation2019). The enzyme substrate mechanism can be explained by the following reaction mechanism:
(6)
(6)
(7)
(7)
(8)
(8)
In this mechanism, the substrate S will bind with the enzyme E to form enzyme-substrate complex, ES. The process of this bond formation is commonly referred to as enzymatic (or protein) crosslinking (Heck, Faccio, Richter, & Thöny-Meyer, Citation2013; Jus et al., Citation2011). The complex is then adsorbed by the surface of the enzyme for the reaction to take place. The product is then released from the enzyme while the enzyme is preserved for more substrates to bind in.
It must be noted that enzymes act apparently as adsorbents, similar to those of porous carbon, activated carbon, carbon nanotubes, fullerene, rich husk and waste carbon (obtained from fertilizer plant, rubber tire, sugar industry etc) and thereby hypothetically the enzyme-substrate reaction mechanisms should follow the adsorption-desorption phenomena (Ahmaruzzaman & Gupta, Citation2011; Gupta, Jain, Ali, Chandra, & Agarwal, Citation2002; Gupta, Nayak, Agarwal, & Tyagi, Citation2014; Gupta et al., Citation2016; Saleh & Gupta, Citation2014). There are various adsorption models available for various adsorption-desorption processes in the literature (Burakov et al., Citation2018; Dil et al., Citation2016; Ghaedi et al., Citation2015; Nekouei, Nekouei, Tyagi, & Gupta, Citation2015), especially adsorption isotherms (Langmuir, Freundlich, Temkin, Frumkin and Flory Huggins) and adsorption kinetics (pseudo fist order, pseudo second order). However, unlike the aforementioned processes, it has been proven that Michaelis-Menten model represents the enzyme-catalysed reaction mechanisms perfectly(Gunawan, Suhendra, Rizkia, & Hasanah, Citation2017). In this study, the experimental data fitted well also with Michaelis-Menten Model, which agrees with previous studies (Saleh & Gupta, Citation2011; Saravanan, Gupta, Narayanan, et al., Citation2013, Citation2014; Saravanan et al., Citation2015). This model is represented by the following formula:
(9)
(9)
where –rA is the rate of disappearance of the substrate in (mol/mL.min), Vmax is the maximum reaction rate in (mol/mL.min), CA is methanol concentration in (mol/mL) and KM is Michaelis constant in (mol/mL).
For plotting purposes, EquationEq. (9)(9)
(9) can be rewritten as follows to yield a linear relationship:
(10)
(10)
Thus, a plot of versus
yields a straight line called Lineweaver–Burk plot, as illustrated in below:
Vmax and KM can be calculated from the intercept and the slope, respectively. Vmax and KM were found to be and
respectively, with a better linearity (R2=0.9952) over a recently published study (Gojun et al., Citation2019). The final form of the Michaelis-Menten kinetic model can be written as follows:
(11)
(11)
The kinetics of the enzymatic transesterification of biodiesel from cooking oil has been compared with previously published works (Al-Zuhair, Dowaidar, & Kamal, Citation2009; Azócar, Navia, Beroiz, Jeison, & Ciudad, Citation2014; Krishna & Karanth, Citation2001; Yadav & Lathi, Citation2004), as illustrated in . The maximum reaction rate constant in comparison with other references is also illustrated in . The fabricated microreactor showed a faster reaction rate when compared with those of some other researchers. This could be mainly attributed to the efficient mixing in micochannels and the appropriate residence time which can lead to higher rate of reaction. In addition, T-shaped microreactors with small microchannel diameters and serpentine pattern fabrication (Santana, Tortola, Silva, & Taranto, Citation2017; Verma, Prakash, Mehta, & Ghosh, Citation2019) is advantageous for achieving a good level of performance over conventional reactors (Franjo, Šalić, & Zelić, Citation2018; Natarajan et al., Citation2019; Shaaban, El-Shazly, & Elkady, Citation2015). The KM value was found small in this study, which indicates lower dependency of methanol concentration on the transesterification in microreactors, which agrees with other researchers (Azócar et al., Citation2014; Halim & Harun Kamaruddin, Citation2008).
Table 3. Comparison between current work and previous work.
The use of the Michaelis–Menten model to study the kinetics of biodiesel synthesis based on transesterification approach with lipase from Thermomyces lanuginosus is limited in literature, as lately revealed (Gojun et al., Citation2019). Recent publications on the kinetics study of lipase-based biodiesel production using the Michaelis–Menten model is illustrated in . The current study shows a better reaction rate over Encinar, González, Sánchez, and Nogales-Delgado (Citation2019), when a commercial lipase (Novozym 435) was used in the latter. Gojun et al. (Citation2019) recently found a better reaction rate using the same lipase as the current study. However, the presented work shows better correlation with data fitting using the Michaelis–Menten model, over the aforementioned study. In addition, the current study is characterized by being less complex, as no emulsifiers were needed to synthesize biodiesel.
Table 4. Reaction rate comparison with references used Michaelis–Menten model to study the kinetics of lipase-based biodiesel production.
In addition, it was found that the maximum % conversion achieved in this work was 68.90% at an inlet flowrate of 50 μL/min (per inlet). Aoki et al reported that a lower flow rate guarantees more residence times with better mixing in microreactors, which leads to a better conversion (Aoki et al., Citation2004). However, the operated flow rate range in this study was restricted by the laboratory facilities, especially while using gravitational flow.
5. Conclusions
The enzymatic transesterification of biodiesel reaction was successfully studied in an in-house fabricated microfluidic reactor of 0.125 mL total volume. The operating conditions for the experiment were at an ambient temperature of 30 °C with the following reactant conditions: 285% of tert-butanol loading, 4 wt% of lipases based on oil weight and oil-to-methanol ratio of 1:2.5. A superior reaction rate (Vmax) of 0.725 mol/L.min, and lower Michaelis –Menten constant (KM) of 0.092 mol/L demonstrated the better performance of the reactor in comparison to conventional reactors. While producing biodiesel in a microfluidic chip was quite challenging due to the viscous nature of oil and biodiesel, which increases the hydrodynamic resistances in microchannels, significant enhancement was shown in the rate of reaction. In addition, the fabricated platform provides several potential features over the macro scale production; it is a scale independent synthesis and economically favourable due to the low cost of the microreactor fabrication. Overall, this microfluidic system can be utilized as an effective pivotal tool with high performance for biodiesel production. Further advanced investigation is necessary to promote the fabricated microreactor performance with different operating temperatures and reactant concentrations, in order to maximize the biodiesel yield. Our current investigations are aligned in this direction.
Disclosure statement
No potential conflict of interest was reported by the author(s).
References
- Aarthy, M., Saravanan, P., Gowthaman, M. K., Rose, C., & Kamini, N. R. (2014). Enzymatic transesterification for production of biodiesel using yeast lipases: An overview. Chemical Engineering Research and Design, 92, 1591–1601. doi:10.1016/j.cherd.2014.04.008
- Ahmaruzzaman, M., & Gupta, V. K. (2011). Rice husk and its ash as low-cost adsorbents in water and wastewater treatment. Industrial & Engineering Chemistry Research, 50(24), 13589–13613. doi:10.1021/ie201477c
- Al-Zuhair, S., Dowaidar, A., & Kamal, H. (2009). Dynamic modeling of biodiesel production from simulated waste cooking oil using immobilized lipase. Biochemical Engineering Journal, 44, 256–262. doi:10.1016/j.bej.2009.01.003
- Aoki, N., Hasebe, S., & Mae, K. (2004). Mixing in microreactors: Effectiveness of lamination segments as a form of feed on product distribution for multiple reactions. Chemical Engineering Journal, 101, 323–331. doi:10.1016/j.cej.2003.10.015
- Azócar, L., Navia, R., Beroiz, L., Jeison, D., & Ciudad, G. (2014). Enzymatic biodiesel production kinetics using co-solvent and an anhydrous medium: A strategy to improve lipase performance in a semi-continuous reactor. New Biotechnology, 31, 422–429. doi:10.1016/j.nbt.2014.04.006
- Bolivar, J. M., Valikhani, D., & Nidetzky, B. (2019). Demystifying the flow: Biocatalytic reaction intensification in microstructured enzyme reactors. Biotechnology Journal, 14(3), 1800244. doi:10.1002/biot.201800244
- Burakov, A. E., Galunin, E. V., Burakova, I. V., Kucherova, A. E., Agarwal, S., Tkachev, A. G., & Gupta, V. K. (2018). Adsorption of heavy metals on conventional and nanostructured materials for wastewater treatment purposes: A review. Ecotoxicology and Environmental Safety, 148, 702–712. doi:10.1016/j.ecoenv.2017.11.034
- Demirbas, A. (2007). Importance of biodiesel as transportation fuel. Energy Policy, 35(9), 4661–4670. doi:10.1016/j.enpol.2007.04.003
- Dil, E. A., Ghaedi, M., Ghaedi, A. M., Asfaram, A., Goudarzi, A. Hajati, S.… Gupta, V. K. (2016). Modeling of quaternary dyes adsorption onto ZnO-NR-AC artificial neural network: Analysis by derivative spectrophotometry. Journal of Industrial and Engineering Chemistry, 34, 186–197. doi:10.1016/j.jiec.2015.11.010
- Encinar, J. M., González, J. F., Sánchez, N., & Nogales-Delgado, S. (2019). Sunflower oil transesterification with methanol using immobilized lipase enzymes. Bioprocess and Biosystems Engineering, 42, 157–166. doi:10.1007/s00449-018-2023-z
- Franjo, M., Šalić, A., & Zelić, B. (2018). Microstructured devices for biodiesel production by transesterification. Biomass Conversion and Biorefinery, 8, 1005–1020. doi:10.1007/s13399-018-0341-7
- Ghaedi, M., Hajjati, S., Mahmudi, Z., Tyagi, I., Agarwal, S., Maity, A., & Gupta, V. K. (2015). Modeling of competitive ultrasonic assisted removal of the dyes – Methylene blue and Safranin-O using Fe3O4 nanoparticles. Chemical Engineering Journal and the Biochemical Engineering Journal, 268, 28–37. doi:10.1016/j.cej.2014.12.090
- Gojun, M., Pustahija, L., Tušek, A. J., Šalić, A., Valinger, D., & Zelić, B. (2019). Kinetic parameter estimation and mathematical modelling of lipase catalysed biodiesel synthesis in a microreactor. Micromachines, 10, 759. doi:10.3390/mi10110759
- Gunawan, E. R., Suhendra, D., Rizkia, B., & Hasanah, M. (2017). Enzymatic kinetics of fatty acids methyl ester from kapok seed oil (Ceiba Petandra) using lipozyme TL IM. American Journal of Applied Sciences, 14(12), 1146–1151. doi:10.3844/ajassp.2017.1146.1151
- Gupta, V. K., Jain, C. K., Ali, I., Chandra, S., & Agarwal, S. (2002). Removal of lindane and malathion from wastewater using bagasse fly ash – A sugar industry waste. Water Research, 36(10), 2483–2490. doi:10.1016/S0043-1354(01)00474-2
- Gupta, V. K., Nayak, A., Agarwal, S., & Tyagi, I. (2014). Potential of activated carbon from waste rubber tire for the adsorption of phenolics: Effect of pre-treatment conditions. Journal of Colloid and Interface Science, 417, 420–430. doi:10.1016/j.jcis.2013.11.067
- Gupta, V. K., Suhas, Tyagi, I., Agarwal, S., Singh, R., Chaudhary, M., … Kushwaha, S. (2016). Column operation studies for the removal of dyes and phenols using a low cost adsorbent. Global Journal of Environmental Science and Management, 2, 1–10. doi:10.7508/gjesm.2016.01.001
- Halim, S. F. A., & Harun Kamaruddin, A. (2008). Catalytic studies of lipase on FAME production from waste cooking palm oil in a tert-butanol system. Process Biochemistry, 43, 1436–1439. doi:10.1016/j.procbio.2008.08.010
- He, W., Gao, Y., Zhu, G., Wu, H., Fang, Z., & Guo, K. (2020). Microfluidic synthesis of fatty acid esters: Integration of dynamic combinatorial chemistry and scale effect. Chemical Engineering Journal and the Biochemical Engineering Journal, 381, 122721. doi:10.1016/j.cej.2019.122721
- Heck, T., Faccio, G., Richter, M., & Thöny-Meyer, L. (2013). Enzyme-catalyzed protein crosslinking. Applied Microbiology and Biotechnology, 97(2), 461–475. doi:10.1007/s00253-012-4569-z
- Hossain, S. M. Z. (2019). Biochemical conversion of microalgae biomass into biofuel. Chemical Engineering & Technology, 42(12), 2594–2607. doi:10.1002/ceat.201800605
- Jus, S., Stachel, I., Schloegl, W., Pretzler, M., Friess, W., Meyer, M. … Guebitz, G. M. (2011). Cross-linking of collagen with laccases and tyrosinases. Materials Science and Engineering: C, 31(5), 1068–1077. doi:10.1016/j.msec.2011.03.007
- Kockmann, N., Gottsponer, M., Zimmermann, B., & Roberge, D. M. (2008). Enabling continuous-flow chemistry in microstructured devices for pharmaceutical and fine-chemical production. Chemistry - A European Journal, 14, 7470–7477. doi:10.1002/chem.200800707
- Krishna, S. H., & Karanth, N. G. (2001). Lipase-catalyzed synthesis of isoamyl butyrate: A kinetic study. Biochimica et Biophysica Acta - Protein Structure and Molecular Enzymology, 1547, 262–267. doi:10.1016/S0167-4838(01)00194-7
- Liu, Y., Tan, H., Zhang, X., Yan, Y., & Hameed, B. H. (2010). Effect of monohydric alcohols on enzymatic transesterification for biodiesel production. Chemical Engineering, 157, 223–229. doi:10.1016/j.cej.2009.12.024
- Luque, R., Lin, C. S. K., Wilson, K., & Clark, J. (2016). Handbook of biofuels production: Processes and technologies. 2nd ed. Elsevier.
- Moazeni, F., Chen, Y. C., & Zhang, G. (2019). Enzymatic transesterification for biodiesel production from used cooking oil, a review. Journal of Cleaner Production, 216, 117–128. doi:10.1016/j.jclepro.2019.01.181
- Natarajan, Y., Nabera, A., Salike, S., Dhanalakshmi Tamilkkuricil, V., Pandian, S., Karuppan, M., & Appusamy, A. (2019). An overview on the process intensification of microchannel reactors for biodiesel production. Chemical Engineering and Processing: Process Intensification, 136, 163–176. doi:10.1016/j.cep.2018.12.008
- Nekouei, F., Nekouei, S., Tyagi, I., & Gupta, V. K. (2015). Kinetic, thermodynamic and isotherm studies for acid blue 129 removal from liquids using copper oxide nanoparticle-modified activated carbon as a novel adsorbent. Journal of Molecular Liquids., 201, 124–133. doi:10.1016/j.molliq.2014.09.027
- Rajendran, S., Khan, M. M., Gracia, F., Qin, J., Gupta, V. K., & Arumainathan, S. (2016). Ce(3+)-ion-induced visible-light photocatalytic degradation and electrochemical activity of ZnO/CeO2 nanocomposite. Scientific Reports, 6, 31641–31641. doi:10.1038/srep31641
- Rizkin, B. A., Popovic, F. G., & Hartman, R. L. (2019). Review article: Spectroscopic microreactors for heterogeneous catalysis. Journal of Vacuum Science and Technology A, 37, 050801. doi:10.1116/1.5108901
- Saleh, T. A., & Gupta, V. K. (2011). Functionalization of tungsten oxide into MWCNT and its application for sunlight-induced degradation of rhodamine B. Journal of Colloid and Interface Science, 362(2), 337–344. doi:10.1016/j.jcis.2011.06.081
- Saleh, T. A., & Gupta, V. K. (2012). Photo-catalyzed degradation of hazardous dye methyl orange by use of a composite catalyst consisting of multi-walled carbon nanotubes and titanium dioxide. Journal of Colloid and Interface Science, 371(1), 101–106. doi:10.1016/j.jcis.2011.12.038
- Saleh, T. A., & Gupta, V. K. (2014). Processing methods, characteristics and adsorption behavior of tire derived carbons: A review. Advances in Colloid and Interface Science, 211, 93–101. doi:10.1016/j.cis.2014.06.006
- Santana, H. S., Silva, J. L., & Taranto, O. P. (2019). Development of microreactors applied on biodiesel synthesis: From experimental investigation to numerical approaches. Journal of Industrial and Engineering Chemistry, 69, 1–12. doi:10.1016/j.jiec.2018.09.021
- Santana, H. S., Tortola, D. S., Silva, J. L., & Taranto, O. P. (2017). Biodiesel synthesis in micromixer with static elements. Energy Conversion and Management, 141, 1–438. doi:10.1016/j.enconman.2016.03.089
- Saravanan, R., Gupta, V. K., Mosquera, E., & Gracia, F. (2014). Preparation and characterization of V2O5/ZnO nanocomposite system for photocatalytic application. Journal of Molecular Liquids, 198, 409–412. doi:10.1016/j.molliq.2014.07.030
- Saravanan, R., Gupta, V. K., Narayanan, V., & Stephen, A. (2013). Comparative study on photocatalytic activity of ZnO prepared by different methods. Journal of Molecular Liquids, 181, 133–141. doi:10.1016/j.molliq.2013.02.023
- Saravanan, R., Gupta, V. K., Narayanan, V., & Stephen, A. (2014). Visible light degradation of textile effluent using novel catalyst ZnO/γ-Mn2O3. Journal of the Taiwan Institute of Chemical Engineers, 45(4), 1910–1917. doi:10.1016/j.jtice.2013.12.021
- Saravanan, R., Gupta, V. K., Prakash, T., Narayanan, V., & Stephen, A. (2013). Synthesis, characterization and photocatalytic activity of novel Hg doped ZnO nanorods prepared by thermal decomposition method. Journal of Molecular Liquids, 178, 88–93. doi:10.1016/j.molliq.2012.11.012
- Saravanan, R., Karthikeyan, S., Gupta, V. K., Sekaran, G., Narayanan, V., & Stephen, A. (2013). Enhanced photocatalytic activity of ZnO/CuO nanocomposite for the degradation of textile dye on visible light illumination. Materials Science & Engineering. C, Materials for Biological Applications, 33(1), 91–98. doi:10.1016/j.msec.2012.08.011
- Saravanan, R., Mansoob Khan, M., Gupta, V. K., Mosquera, E., Gracia, F., Narayanan, V., & Stephen, A. (2015). ZnO/Ag/CdO nanocomposite for visible light-induced photocatalytic degradation of industrial textile effluents. Journal of Colloid and Interface Science, 452, 126–133. doi:10.1016/j.jcis.2015.04.035
- Saravanan, R., Sacari, E., Gracia, F., Khan, M. M., Mosquera, E., & Gupta, V. K. (2016). Conducting PANI stimulated ZnO system for visible light photocatalytic degradation of coloured dyes. Journal of Molecular Liquids., 221, 1029–1033. doi:10.1016/j.molliq.2016.06.074
- Saravanan, R., Thirumal, E., Gupta, V. K., Narayanan, V., & Stephen, A. (2013). The photocatalytic activity of ZnO prepared by simple thermal decomposition method at various temperatures. Journal of Molecular Liquids, 177, 394–401. doi:10.1016/j.molliq.2012.10.018
- Shaaban, M. O. W., El-Shazly, A. H., & Elkady, M. F. (2015). Investigation of factors affect biodiesel production in microreactor with T-mixer. International Proceedings of Chemical, Biological and Environmental Engineering, 88, 11-15. doi:10.7763/IPCBEE
- Suryawanshi, P. L., Gumfekar, S. P., Bhanvase, B. A., Sonawane, S. H., & Pimplapure, M. S. (2018). A review on microreactors: Reactor fabrication, design, and cutting-edge applications. Chemical Engineering Science, 189, 431–448. doi:10.1016/j.ces.2018.03.026
- Verma, R. K., Prakash, R., Mehta, A., & Ghosh, S. (2019). Biodiesel production in a serpentine minireactor—Effect of flow distribution. International Journal of Energy Resources, 43, 3461–3474. doi:10.1002/er.4488
- Wancura, J. H. C., Rosset, D. V., Tres, M. V., Oliveira, J. V., Mazutti, M. A., & Jahn, S. L. (2018). Production of biodiesel catalyzed by lipase from Thermomyces lanuginosus in its soluble form. The Canadian Journal of Chemical Engineering, 96(11), 2361–2368. doi:10.1002/cjce.23146
- Yadav, G. D., & Lathi, P. S. (2004). Synthesis of citronellol laurate in organic media catalyzed by immobilized lipases: Kinetic studies. Journal of Molecular Catalysis B: Enzymatic, 27, 113–119. doi:10.1016/j.molcatb.2003.10.004
- Yao, X., Zhang, Y., Du, L., Liu, J., & Yao, J. (2015). Review of the applications of microreactors. Renewable & Sustainable Energy Reviews, 47, 519–539. doi:10.1016/j.rser.2015.03.078
- Yusuf, H. A., Redha, Z. M., Al Meshal, A. J., & Shehab, H. J. (2018). Experimental and mathematical modelling of reactive dyes decolorization using Fenton oxidation process in a microfluidic system. Desalination and Water Treatment, 116, 305–316. doi:10.5004/dwt.2018.22534
- Zakir Hossain, S. M., Sultana, N., Irfan, M. F., Elkanzi, E. M. A., Al-Aali, Y. A. M., Taha, A., & Manirul Haque, S. (2016). Optimization of biodiesel production from spent palm cooking oil using fractional factorial design combined with the response surface methodology. American Journal of Applied Sciences, 13(11), 1255–1263. doi:10.3844/ajassp.2016.1255.1263
- Zarejousheghani, F., Kariminia, H. R., & Khorasheh, F. (2016). Kinetic modelling of enzymatic biodiesel production from castor oil: Temperature dependence of the Ping Pong parameters. The Canadian Journal of Chemical Engineering, 94(3), 512–517. doi:10.1002/cjce.22408
- Zhang, W. B. (2012). Review on analysis of biodiesel with infrared spectroscopy. Renewable & Sustainable Energy Reviews, 16, 6048–6058. doi:10.1016/j.rser.2012.07.003