ABSTRACT
Based on a multicycle quenching-partitioning-tempering process, a novel process is proposed to treat Fe–2.4C–12.0Cr (mass %) white cast iron balls. It is a destabilizing heat treatment following multicycle quenching and sub-critical treatment (De-MQ-Sct) process. Such a complex process may be simply performed by alternate water quenching and air cooling. For comparison, the white cast iron balls also were treated by conventional normalization (NOR) process and oil-quenching process. The partitioning of carbon from martensite to retained austenite during the De-MQ-Sct process promotes the interaction between carbide precipitation and martensitic transformation. While this interaction is a unique effect only produced by multicycle quenching linking destabilizing and sub-critical treatments, which leads to more, and finer, secondary carbides and more carbon-enriched austenite in De-MQ-Sct sample than those in a NOR or oil-quenching sample. The average hardness of 60 HRC and impact toughness of 12.6 J/cm2 are obtained in De-MQ-Sct white cast iron balls, which are much higher than those in a NOR and oil-quenching ones. The wear behavior measured by pin-on-disk wear tests indicate that the weight loss of De-MQ-Sct sample is only about one-third of the NOR sample and one half of the oil-quenching sample. Microstructural characterization reveals that high hardness-toughness and wear resistance of the De-MQ-Sct balls are mainly attributed to the large quantities of fine secondary carbides and stable carbon-enriched retained austenite.
Introduction
High-chromium white irons are usually hypoeutectic ones, and they are often used in wear environments, such as mineral processing, cement production and steel manufacturing industries, and so on [Citation1–4]. The large quantities of M7C3 chromium carbides in high-chromium white irons provide excellent wear resistance. The addition of chromium can form large quantities of carbides in casting irons [Citation4]. The usual production route of high-chromium white irons is casting. In the as-cast condition, a network distribution of coarse eutectic M7C3 type carbides is inevitably formed during solidification and leads to poor fracture properties and relatively high wear rate [Citation5–7]. Moreover, the network eutectic carbides are very stable so that they are not easily eliminated by heat treatment [Citation3,Citation8]. Therefore, the microstructure of high-chromium white irons is improved by various heat treatment methods, such as destabilization heat treatment and sub-critical heat treatment [Citation5,Citation9–12]. Destabilizing heat treatment with relative low austenitizing temperature is used to cause coarse secondary carbides to precipitate [Citation8], which lowers the alloy content in austenite and leads to the martensitic transformation at room temperatures if cooling is fast enough [Citation5]. While sub-critical heat treatment below the austenitizing temperature is used to reduce the retained austenite and obtain a martensitic matrix by the precipitation of large quantities of fine secondary carbides [Citation11,Citation13]. The retained austenite has a high intrinsic fracture toughness [Citation14] and transformation-induced plasticity (TRIP) by strain-induced martensitic transformation [Citation9,Citation10], such as wear induced martensitic transformation [Citation11]. However, it is easy to cause high phase-transformation stress and cracking during the transformation induced by wear [Citation12]. For the above heat treatments, rapid cooling is necessary for white cast irons to avoid as far as possible the formation of pearlite that is unfavorable for the wear resistance. However, because white cast irons have casting defects (such as gas porosities, inclusions) and undesirable residual stress, rapid cooling is most likely to cause the cracking. As a result, air cooling (normalization) or oil-quenching are usually applied so as to avoid cracking during heat treatment, but the air cooling rate usually cannot markedly improve the hardness and/or toughness of hypoeutectic cast irons, while oil cooling leads to the air pollution. As a consequence, it is a challenge for white cast iron to avoid cracking and markedly improve mechanical properties by rapid cooling in shorter processing times. A novel process can solve the issue [Citation15,Citation16]. The core idea of this novel is quenching-partitioning-tempering (Q-P-T) process [Citation17], or multicycle Q-P-T (MQ-P-T) process [Citation18] that links the destabilizing treatment and sub-critical treatment, that is, destabilizing heat treatment following a multicycle quenching and sub-critical treatment (De-MQ-Sct) process. Such a complex De-MQ-Sct processes are simply performed by alternate water quenching and air cooling [Citation15]. Our study clarified the design principle of a novel De-MQ-Sct process and revealed the mechanism of high hardness-toughness and wear resistance of Fe–2.4C–12.0Cr (wt%) white cast irons compared with a conventional NOR process and an oil-quenching process [Citation16].
Experimental procedures
High-chromium white iron balls with diameter of 80 mm, provided by DeXing Casting Co. Ltd. of Jiangxi Copper Corporation, were cast from 1550°C using chilled molds. The NOR or oil-quenching processes are austenitizing at 950°C for two hours followed by air cooling or oil cooling, respectively. Combination with destabilizing heat treatment and sub-critical one, the De-MQ-Sct process is designed as follows. The balls are subjected to destabilizing treatment, namely, austenitizing at 950°C for 2 h, being the same as a NOR process and oil-quenching ones. After that, a white cast iron ball will be slowly cooled from 950°C to near 800°C by air cooling, and during cooling coarse secondary chromium carbides will precipitate, but the transformation of austenite to pearlite should be as far as possible avoided. The lowering of austenite temperature can decrease subsequent quenching stress. Then, the first water quenching takes the temperature of the ball lower to about 600°C, following air cooling for about 50 s. The goal is to form martensite in the surface layers of the ball by transformation of austenite to martensite and precipitation of M7C3 secondary chromium carbides from austenite. Subsequently, the second water quenching is performed and takes the temperature of the balls lower to about 400°C, following air cooling for a relative long time. The goal is to form martensite in the sub-surface layer of the ball and to precipitate more and finer secondary carbides from austenite. Finally, the third water quenching is performed to obtain more martensite by transformation of greater supercooled austenite, and the following air cooling makes the temperature of the ball fall to room temperature, during which martensitic transformation can still occur. The De-MQ-Sct process is recorded by temperature measurement with a WRNK-101 model thermocouple inserted at the center and 10 mm from the surface of the ball. The measured cooling curves are shown in [Citation16]. As a comparison, the cooling curves at the same positions in balls treated by a NOR process and an oil-quenching process are also shown in . It can be found from that the cooling rates of an oil-quenching process and De-MQ-Sct process are very close, and their cooling rates are much greater than that of a NOR process. After heat treatment, disc samples with a diameter of 80 mm for hardness test and samples with a dimension of 10 × 10 × 55 mm3 without a groove for Charpy impact test were prepared by cutting balls along their radial directions. The HRC hardness was measured using a Rockwell hardness tester with a load of 150 kg, and the impact toughness was measured with a PTM2200-D1 impact testing machine. Friction wear tests were conducted using a computer-aided pin-on-disk wear testing machine, and weight loss was measured to evaluate the wear resistance [Citation16]. The microstructure of samples after mechanical tests was characterized by X-ray diffraction (XRD), optical microscope (OM), scanning electron microscope (SEM) and transmission electron microscope (TEM) [Citation16].
Results and discussions
Quantitative analysis of phases and microstructural characterization
Combining the results of XRD and Image-Pro Plus software statistics, the amount of different phases was determined and given in . shows the XRD spectra of samples treated by De-MQ-Sct, oil-quenching, and NOR processes [Citation16]. Phases of hcp M7C3, orthogonal MC3 carbide, fcc austenite, and bcc lattice structure (ferrite and martensite) were detected. However, diffraction peaks of austenite cannot be observed in the NOR sample, and the diffraction peak of M3C cannot be observed in oil-quenching sample. Besides, austenite completely transforms to pearlite in the NOR process, and thus the volume fraction of pearlite is high up to 73.0%. In the oil-quenching sample, there is no pearlite as there was no MC3. However, the pearlite also forms in the De-MQ-Sct process during the two stages of air cooling at the sub-critical temperatures about 600°C and 400°C, and the volume fraction of pearlite is 13.8%. It is clear to see that the amount of M7C3 eutectic carbides in the samples treated by the three different processes is close owing to the same austenitizing temperature. It is worth noting that the volume fraction of M7C3 secondary carbide in the De-MQ-Sct sample is 13.0%, being near one and a half times in the oil-quenching sample and twice that of the NOR sample. However, the volume fraction of martensite in the oil-quenching sample is 65.1%, being the largest amount in three samples. It is worth pointing out that in the De-MQ-Sct sample the volume fraction of retained austenite is high up to 12.2%, being much more than the 8.5% in the oil-quenching sample. The microstructures of the NOR, oil-quenching, and De-MQ-Sct samples were characterized by OM and SEM, as shown in [Citation16]. The microstructure of 0.5 R position of NOR sample is shown in ((a,b)), and that of oil-quenching sample in ((c,d)) and that of De-MQ-Sct sample in ((e,f)). The optical photograph in (a) shows the dendrites with deep gray contrast and bone-like eutectic carbides with bright contrast between dendrites in NOR sample, in which dendrites come from the transformation of proeutectic austenite. The optical photographs of the oil-quenching ((c)) and De-MQ-Sct ((e)) samples show similar morphologies to the NOR sample, namely, the network eutectic carbides follow the dendritic morphology of the proeutectic austenite, and the secondary carbides with bright contrast distribute in matrix, as marked by arrows in (a,c,e). However, the microstructure within dendrites cannot be resolved in either the NOR, oil-quenching or De-MQ-Sct samples. Therefore, the microstructures were further characterized by SEM. Compared with (bdf), in addition to coarse eutectic carbides as a common feature, it can be clearly seen that the sizes of secondary carbide particles in the NOR and oil-quenching samples were close, and their average size is larger than that in De-MQ-Sct sample.
Figure 3. Optical photographs (a, c, and e) and SEM photographs (b, d, and f) for NOR sample (a and b), Oil-quenching sample (c and d) and De-MQ-Sct sample (e and f).
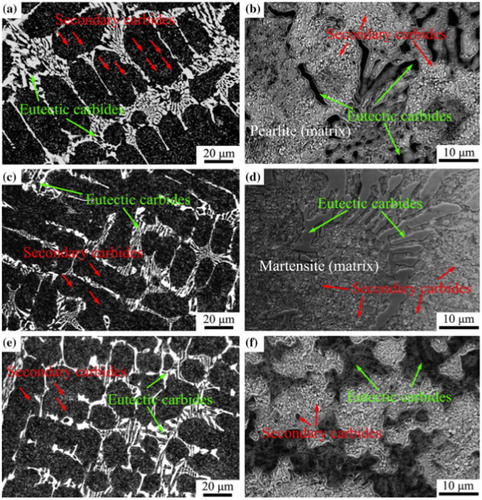
Table 1. The volume fractions of phases in the samples treated, respectively, by three processes.
Hardness and toughness
The hardness distribution of the sample treated by the De-MQ-Sct process, oil-quenching process, and NOR process was measured along a straight line through the center of sample [Citation16]. shows that the average hardness of the De-MQ-Sct sample reaches about 60 HRC, about 17 HRC higher than that of the NOR sample and about 4 HRC higher than that of oil-quenching sample. Additionally, the hardness deviated from the average values are ±1 HRC for De-MQ-Sct sample, ±2.6 HRC for oil-quenching sample, and ±3 HRC for NOR sample. The De-MQ-Sct sample exhibits the minimum deviation in hardness distribution. During the De-MQ-Sct process, the high-chromium cast iron ball experienced multiple stages of air cooling after water quenching, which greatly reduces the temperature difference between surface and center. This effect can increase the homogeneity of microstructure and hardness, but cannot eliminate the difference of cooling rate between the surface and center of ball. The NOR sample exhibits the largest fluctuations of hardness, which is mainly attributed to the large hardness difference between carbides and pearlite. shows the impact toughness of samples treated by the De-MQ-Sct, oil-quenching, and NOR processes [Citation16]. The average impact toughness value of three De-MQ-Sct samples is 12.6 J/cm2, being about four times as the NOR sample and twice as the oil-quenching one.
Table 2. The impact toughness distributions of the samples treated by the three processes.
Wear resistance
shows the results of wear tests at different positions of the balls for three kinds of samples [Citation16]. After the complete test sliding distance of 3670 m, the wear weight loss of the NOR sample is about 61 × 10−4 g at the surface, 66 × 10−4 g at 0.5 R position and 79 × 10−4 g at the center of ball; the wear weight loss of the oil-quenching sample is about 30 × 10−4 g at the surface, 40 × 10−4 g at 0.5 R position, and 54 × 10−4 g at the center of ball; while the wear weight loss of the De-MQ-Sct sample is about 20 × 10−4 g at the surface, 22 × 10−4 g at 0.5 R position and 30 × 10−4 g at the center of ball, being about one third for the NOR sample and one half for the oil-quenching sample in three corresponding positions. It is clear that the De-MQ-Sct sample has the best wear resistance as a result of the highest hardness and toughness. Additionally, there is a trend for three kinds of samples that the weight loss of ball is the largest at the center, followed by the position of 0.5 R and finally the surface. The gradual increase of weight loss from the surface to center of ball is attributed to the difference of microstructures produced by the different cooling rates between surface and center.
As mentioned above, De-MQ-Sct samples exhibit excellent mechanical properties, that are attributed to four advantages of De-MQ-Sct process: (1) multicycle quenching and self-tempering avoids the trend towards cracking; (2) multicycle partitioning of carbon results in the precipitation of more and finer secondary carbides; (3) multicycle partitioning of carbon results in the formation of more carbon-enriched retained austenite; and (4) the interaction between carbide precipitation and martensitic transformation effectively shortens the time of heat treatment. The hardness and toughness of De-MQ-Sct samples are much higher than those of the NOR and oil-quenching samples, as shown in and . The microstructural characterization indicates that the amount (16.1%t) of eutectic carbides in the De-MQ-Sct sample is close to that (19.7%) in the NOR sample and that of the oil-quenching sample (17.4%t) because their austenitizing temperature is same. Therefore, the high hardness of De-MQ-Sct sample is mainly attributed the considerable martensite matrix and more and finer secondary carbides, while in the NOR sample proeutectic austenite transforms to pearlite matrix, and in the oil-quenching sample although the amount of martensite is higher than that in the De-MQ-Sct sample, the amount of secondary carbides is much less than that in the De-MQ-Sct sample, moreover, their average size is much larger than that in the De-MQ-Sct sample. The improvement of impact toughness of the De-MQ-Sct samples, in addition to more and finer secondary carbides, is mainly attributed to large amount of carbon-enriched retained austenite. We measured the variations of martensite content before and after wear tests of the De-MQ-Sct sample and the oil-quenching sample by a magnetic method with Physical Property Measurement System (PPMS) [Citation16]. The result indicates that the amount of martensite in De-MQ-Sct sample remains almost unchanged after wear test, that is, martensitic transformation from retained austenite does not occur in wear loading. In other words, the amount of retained austenite keeps unchanged after wear test. However, for the oil-quenching sample the saturation magnetization after the wear test is higher than that before the wear test. It means that the increase of magnetic phase-martensite accompanies the decrease of retained austenite in wear loading. The retained austenite in the De-MQ-Sct sample is more stable than that in the oil-quenching sample, which is the result of higher carbon content in retained austenite by partitioning of carbon from martensite to retained austenite [Citation17] during the De-MQ-Sct process. Combining this with TEM characterization, we obtained two important conclusions [Citation16]: (1) strain-induced martensitic transformation from retained austenite indeed harms the toughness and wear resistance of white cast iron because twin-type martensite increases the source of crack initiation; (2) stable carbon-enriched retained austenite can markedly enhance the toughness and wear resistance of white cast iron because plastic retained austenite can decrease the cracks in the matrix by deactivating the crack tip and inhibiting crack development [Citation4,Citation15,Citation19], moreover, the cracks grow either continuously in the austenite or trace a zig–zag path through interlocking martensite laths that will require an increased energy for fracture [Citation20]. In general, large amounts of fine secondary carbides and stable carbon-enriched retained austenite play key roles in enhancing the wear resistance of De-MQ-Sct white cast iron.
Conclusions
Fe–2.4C–12Cr white cast balls with 80 mm diameter were heat-treated and their mechanical properties and microstructures were characterized. Main conclusions are described as follows.
Based on MQ-P-T process, a novel process (De-MQ-Sct) is proposed to treat Fe–2.4C–12.0Cr white cast iron balls. Such a complex process is simply performed by alternate water quenching and air cooling. The partitioning of carbon from martensite to retained austenite during the De-MQ-Sct process promotes the interaction between carbide precipitation and martensitic transformation. This interaction is a unique effect only produced by multicycle quenching linking destabilizing and sub-critical treatments, which leads to more and finer secondary carbides and more carbon-enriched austenite in De-MQ-Sct samples than those in NOR or oil-quenching samples.
The high hardness of De-MQ-Sct samples is mainly attributed to large quantities of fine M7C3 secondary carbides. The high impact toughness of De-MQ-Sct samples is mainly attributed to considerable stable carbon-enriched retained austenite and dislocation-type martensite matrix.
The weight loss of De-MQ-Sct sample is about one third of the NOR one and one half of the oil-quenching one. Such a high wear resistance is mainly attributed to large quantities of fine secondary carbides and stable carbon-enriched retained austenite.
Disclosure statement
No potential conflict of interest was reported by the authors.
Additional information
Funding
References
- Svensson LE, Bhadeshia HKDH, Gretoft B, et al. Fe-Cr-C hardfacing alloys for high-temperature applications. J Mater Sci 1986;21:1015–1019. doi: 10.1007/BF01117388
- Neville A, Reza F, Chiovelli S, et al. Characterization and corrosion behavior of high-chromium white cast irons. Metall Mater Trans A. 2006;37:2339–2347. doi: 10.1007/BF02586208
- Pearce JTH, Elwell DWL. Duplex nature of eutectic carbides in heat treated 30% chromium cast iron. J Mater Sci Lett. 1986;5:1063–1064. doi: 10.1007/BF01730284
- Wiengmoon A, Chairuangsri T, Brown A, et al. Microstructural and crystallographical study of carbides in 30wt.%Cr cast irons. Acta Mater. 2005;53:4143–4154. doi: 10.1016/j.actamat.2005.05.019
- Janssen M, Van Leeuwen MB, Mendes de Leon MF. Proceedings of the 14th European Conference on Fracture, A. Neimitz, et al., eds., Emas Publications, London, 2002, pp. 617–625.
- Rodenburg C, Rainforth WM. A quantitative analysis of the influence of carbides size distributions on wear behaviour of high-speed steel in dry rolling/sliding contact. Acta Mater. 2007;55(7):2443–2454. doi: 10.1016/j.actamat.2006.11.039
- Bedolla-jacuinde A, Aguilar SL, Hernandez B. Eutectic modification in a low-chromium white cast iron by a mixture of titanium, rare earths, and bismuth: I. effect on microstructure. J Mater Eng Perform. 2005;14:149–157. doi: 10.1361/10599490523300
- Wiengmoon A, Pearce JTH, Chairuangsri T. Relationship between microstructure, hardness and corrosion resistance in 20wt.%Cr, 27wt.%Cr and 36wt.%Cr high chromium cast irons. Mater Chem Phys. 2011;125:739–748. doi: 10.1016/j.matchemphys.2010.09.064
- Gasan H, Erturk F. Effects of a destabilization heat treatment on the microstructure and abrasive wear behavior of high-chromium white cast iron investigated using different characterization techniques. Metall Mater Trans A. 2013;44A:4493–5005.
- Tabrett CP, Sare IR, Ghomashchi MR. Microstructure-property relationships in high chromium white iron alloys. Int Mater Rev. 1996;41:59–82. doi: 10.1179/imr.1996.41.2.59
- Wang J, Li C, Liu H, et al. The precipitation and transformation of secondary carbides in a high chromium cast iron. Mater Charact. 2006;56(1):73–78. doi: 10.1016/j.matchar.2005.10.002
- Wang J, Zuo RL, Sun ZP, et al. Influence of secondary carbides precipitation and transformation on hardening behavior of a 15 Cr–1 Mo–1.5 V white iron. Mater Charact. 2005;55:234–240. doi: 10.1016/j.matchar.2005.06.002
- Liu H-H, Wang J, Shen B-L, et al. Effects of deep cryogenic treatment on property of 3Cr13Mo1V1.5 high chromium cast iron. Mater Des. 2007;28:1059–1064. doi: 10.1016/j.matdes.2005.09.007
- Laird II G, Powell GLF. Solidification and solid-state transformation mechanisms in Si alloyed high-chromium white cast irons. Metall Mater Trans A. 1993;24:981–988. doi: 10.1007/BF02656520
- Jia X, Hao Q, Zuo X, et al. High hardness and toughness of white cast iron: the proposal of a novel process. Mater Sci Eng A. 2014;618:96–103. doi: 10.1016/j.msea.2014.08.075
- Jia X, Zuo X, Liu Y, et al. Metall Mater Trans A. 2015.
- Hsu TY. Design of structure, composition and heat treatment process for high strength steel. Mater Sci Forum. 2007;561–565:2283–2286. doi: 10.4028/www.scientific.net/MSF.561-565.2283
- Zuo XW, Chen NL, Gao F, et al. Development of multi-cycle quenching–partitioning–tempering process and its applications in engineering. Int Heat Treat Surf Eng. 2014;8:15–23. doi: 10.1179/1749514813Z.00000000078
- Zackay VF, Parker ER, Fahr D, et al. The enhancement of ductility in high-strength steels. ASM Trans Quart. 1967;60:252–259.
- Webster D. Increasing the toughness of the martensitic stainless steel AFC 77 by control of retained austenite content, ausforming and strain aging(retained austenite content control, strain aging and ausforming to improve toughness of high strength martensitic stainless steel without strength loss). ASM Trans Quart. 1968;61:816–828.