ABSTRACT
Dehydrogenation of TiH2 powder is an important method for preparing low-cost titanium powder. In this study, a novel dehydrogenation process of titanium hydride powder was developed based on the fluidization principle. TiH2 powder with particle sizes of <75 μm was placed evenly on the fluidization bed in a specially designed reactor and dehydrogenated at 560°C for 120 min with argon gas flowing from the bottom to top of the reactor. The resulting powder was analyzed using X-ray diffractometry, scanning electron microscopy, Hall flowmeter and laser scattering particle size analyzer. It was evident that a Ti powder with a small amount of TiH1.5 was obtained after the dehydrogenation process at a relatively low temperature. The edges and corners of the particles became rounded due to the thermodynamic driving force originated from the reduction of particle surface areas. The fluidity of powder was also improved due to the increase of sphericity of the powder particles during dehydrogenation. After dehydrogenation, the particle size range became smaller, and the average particle size increased, showing that slight sintering of the very fine titanium particles occurs.
Introduction
Titanium and its alloys have low density, high specific strength, good ductility and fracture toughness, high corrosion resistance and good biological compatibility, and thus are widely used in the fields of aerospace, chemical engineering and biomedical equipment manufacturing [Citation1–3]. However, their applications are highly limited by their high costs. If the costs of titanium and titanium alloys can be significantly lowered, they are highly desirable materials for manufacturing land-based and marine-based civil and military vehicles. Fabrication of near-net shaped titanium and titanium alloy components by powder metallurgy processes is one effective way of lowering the cost. In this, low-cost titanium powder produced by hydrogenation and dehydrogenation (HDH) process is needed. On the basis of HDH, some researchers proposed Motive-HDH (MHDH) method, which further reduced the cost and energy consumption of titanium powder produced by the HDH method [Citation4]. In HDH and MHDH processes, titanium sponge absorbs hydrogen to form titanium hydride which is brittle and easy to be ground into powder particles. Thus, TiH2 powder is an important raw material, and dehydrogenation process of TiH2 powder has a great significance in the field of titanium powder metallurgy [Citation5].
In previous studies [Citation6–10], TiH2 powder is normally dehydrogenated in vacuum and at temperature higher than 680°C. This process is prone to powder particle sintering, therefore, the dehydrogenation rate and temperature need to be strictly controlled. After high-temperature dehydrogenation, product has to be mechanically ground and screened in an inert gas to obtain a Ti powder. The cost of producing Ti powder using this method is relatively low cost, but the powder has irregular particle shapes and poor fluidity which limits its applications. The Ti powder with near spherical and good fluidity can be obtained by additional spheroidizing with the help of a particle composite system (PCS) [Citation11,Citation12]. In order to obtain a high-quality titanium powder, some researchers have proposed a new dehydrogenation method. He et al. [Citation13] prepared ultrafine Ti powder through the process of hydrogenation, mechanical pulverization, inhibitor (NaCl) coating, vacuum dehydrogenation and inhibitor removal. An ultrafine titanium powder with a controlled oxygen content was obtained by dehydrogenizing at 630°C for 2 h and then removing NaCl. Guo et al. [Citation14] and Wang et al. [Citation15] synthesized spherical titanium powder with fine and even-sized particles, a good fluidity, a high sphericity and low oxygen content by Radio-frequency (RF) plasma. Recently, Qin et al. [Citation16] realized the spheroidization of titanium powder by fluidization principle. After treating at 450°C for 10 min, the modified morphology and size distribution of the Ti powder particles improved the flowability of the powder. Compared with their research, this study designed a different fluidization apparatus, using titanium hydride powder with a particle size of <75 µm as raw material, and realized the dehydrogenation of titanium hydride powder and the improvement of sphericity and flowability of particles in this apparatus.
Experimental procedure
The dehydrogenation experiment was carried out in a fluidization bed equipment (as shown schematically in ), which mainly consisted of a cyclone separator, a fluidized bed reactor, a mica induction coil, a hot air gun and a control panel, with argon as the fluidizing gas. A titanium hydride powder with particle sizes of <75 μm and a purity of 99.8% was produced by hydrogenation of sponge titanium followed by mechanical grinding. Its chemical composition is shown in . 600 g of TiH2 powder was evenly placed on the fluidization plate in a specially designed fluidized bed reactor [Citation17]. The air in the reactor is pushed out by flowing argon through Channel 1 for 2 min. Then Channel 1 was closed, and Channel 2 with a heating device was open. The flow rate of argon through Channel 2 was adjusted to 0.3 L/min. The incoming argon and the wall of the reactor were heated simultaneously. Dehydrogenation of the TiH2 powder is generally carried out at temperatures above 500°C [Citation18], so after the temperature in the reactor exceeded 560°C, the flow rate was adjusted to 0.7 L/min. The reactor was kept at the temperature for 120 min., and then the heaters were switched off. Cooling argon with a flow rate of 0.3 L/min was passed into the reactor through Channel 1 to cool the powder quickly, and at the same time, room temperature air was passed through the cooling shunt flange outside the reactor through Channel 3 to speed up the cooling process until the temperature in the reactor dropped below 100°C.
Table 1. Chemical composition of the TiH2 powder used in the study.
The powder samples were taken from inside the reactor and analyzed using an X-ray diffractometer (XRD) (Bruker DB Discover) and the sizes and morphologies of the powder particles in the as-received and dehydrogenated powders were examined by scanning electron microscopy (SEM) (X-max20, ZEISS SIGMA). The fluidity of the as-received and dehydrogenated powders was assessed by means of a calibrated funnel (Hall flowmeter, BT-200). The particle size distribution was studied by laser particle size analyzer (HORIBA, LA-920).
Results and discussion
After dehydrogenation reaction, a small fraction of the powder (about 10%) was distributed on the inner wall of the reactor, and the rest was evenly distributed on the fluidized plate, as shown in . Powder samples were taken from these two places for analysis. shows the XRD patterns of as-received TiH2 powder and samples obtained after dehydrogenation. The powder obtained from the inner wall of the reactor and the fluidized plate both have obvious dehydrogenation effect. As shown in , after dehydrogenation, the TiH2 peaks disappeared, and Ti and TiH1.5 peaks appeared, with the intensity of the Ti peaks being dominant in the XRD patterns of the dehydrogenated powder samples. This shows that the TiH2 was mostly dehydrogenated after the reaction, and the resulting powder contains a small amount of TiH1.5.
Figure 3. XRD patterns of as-received TiH2 powder and the dehydrogenated powders from the surface center and inner wall of the reactor, respectively.
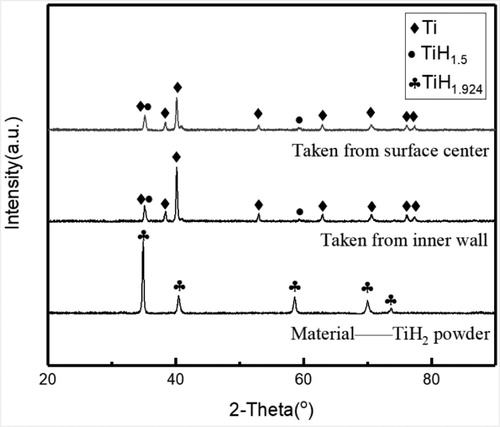
The sizes and morphologies of the Ti powder particles taken from as-received TiH2 powder, the powder at the surface center of the fluidization plate and the powder on the inner wall of the reactor are shown in . As shown in (a), the as-received TiH2 powder particles were irregular and equiaxed in shapes with many sharp edges and corners. After dehydrogenation, the edges and corners of particles became rounded, and the sphericity of the particles was improved. By comparing the SEM images in (b,c), we can see that the sphericity of the Ti powder particles taken from the surface center of the fluidization plate is better than that of the Ti powder particles from the inner wall.
Figure 4. SEM images of powder particles from. (a) as-received TiH2 powder, (b) dehydrogenated Ti powder from the surface center, and (c) dehydrogenated Ti powder from the inner wall of the reactor.
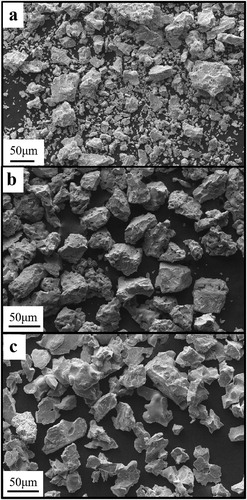
The schematic diagram of fluidized bed reactor is shown in . When the fluidizing gas passed upward through the bed layer at a certain speed, particles were no longer supported by fluidization plate, but by frictional force of the fluid. Meanwhile, powder particles can flow freely in the bed layer, having larger reaction areas. The fluidized bed can strengthen both heat and mass transfer between the powder particles and the argon gas. Thus, the efficiency of dehydrogenation is significantly improved [Citation19,Citation20]. In previous studies [Citation4,Citation6,Citation7], dehydrogenation of TiH2 powder was carried out at clearly higher temperatures than those used in this study. NaCl coated/hydrogenation-dehydrogenation combined method prepared ultrafine Ti powder with a particle size of 6.16 µm, dehydrogenizing at 630°C for 2 h [Citation13]. The dehydrogenation temperature and time were similar to this study. However, NaCl coated/hydrogenation-dehydrogenation combined method solved the problem of sintering powder at a high temperature and produced a much finer powder than that in this study. In RF plasma method [Citation14,Citation15], TiH2 powder was heated to several thousand kelvin to be dehydrogenated and melted. The titanium droplets would then be rapidly cooled in the protective atmosphere to form spherical titanium powder. This approach prepared Ti powder with finer particles, better flowability and higher sphericity than this study. However, this method requires specific instruments and conditions to complete, and the cost is high.
During fluidization, edges and corners of powder particles became more rounded due to the thermodynamic driving force originated from reduction of the surface areas of the powder particles. The mass transfer required for changing the shapes of the particles can take place through surface diffusion and evaporation and condensation in the same ways of mass transfer that occurs during powder sintering [Citation21]. The constant colliding and rubbing of the powder particles during reaction may also assist with the change of the particle shapes. Thus, the sphericity of the powder particles would be improved. There is still a small amount of TiH1.5 in the product powder caused by insufficient dehydrogenation. This deficiency can be overcome by adjusting dehydrogenation temperature, dehydrogenation time and gas flow rate. On the other hand, the small amount of TiH1.5 in the powder might be beneficial to the use of powder.
shows the particle size distributions of as-received TiH2 powder and the dehydrogenated Ti powders from the surface center and the inner wall of the reactor. It reveals that after dehydrogenation, the particle size range became smaller. D50 of three samples mentioned above were, respectively, 24.4, 28.0, 42.1 µm. This shows that the very fine Ti powder particles were slightly sintered during fluidization. That is why D50 of dehydrogenated Ti powder was larger than that of TiH2. The sintering of the powder taken from the inner wall was more serious. The reason is likely to be the relatively higher temperature and lower particle moving rate near the reactor wall.
Figure 6. Particle size distribution of (a) as-received TiH2 powder, (b) dehydrogenated Ti powder from the surface center, and (c) dehydrogenated Ti powder from the inner wall of the reactor.
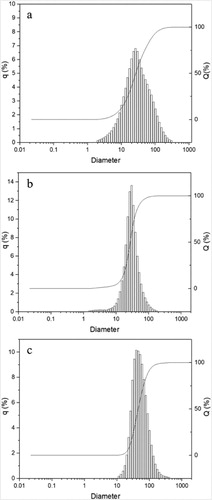
The fluidity was measured by the time taken by 50 g of powder flowing through the 2.5 mm diameter aperture of a Hall flowmeter. The result of powders taken from the surface center was 40.8 s/50 g. As-received TiH2 powder and the powder taken from the inner wall of the reactor could not come out of the funnel of the Hall flowmeter at all, so they were considered to be non-fluid. The angle of repose (θ) is the angle between the slope of a powder pile formed freely and the horizontal plane, and it also reflects the fluidity of the powder. A powder with a smaller θ has better fluidity. The angle of repose of as-received TiH2 and dehydrogenated Ti powder samples from the surface center of the fluidization plate and the inner wall of the reactor were measured to be 37.2°, 23.6° and 26.5°, respectively, as shown in . It can be seen that the angles of repose of the dehydrogenated Ti powder samples obtained from the two places were clearly smaller than that of the as-received TiH2 powder, suggesting that the fluidity of the dehydrogenated Ti powder is significantly improved. It can be envisaged that the reason for this improvement of powder fluidity is the change of particle shapes from those with many sharp edges and corners to those with rounded edges and corners and the improvement of sphericity of the powder particles during dehydrogenation, as shown in . We can also see that the fluidity of the Ti powder particles taken from the surface center of the fluidization plate is better than that of the Ti powder particles from the inner wall, implying that fluidization plays a critical role in enhancing the effect of heat treatment on the change of particle shapes.
Figure 7. Images showing the measurments of the angles of repose of the as-received TiH2 powder, powder from the surface center of the fluidization plate and powder from the inner wall of the reactor.
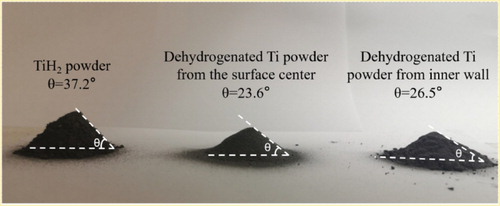
It was found that a small fraction of the powder was partially sintered and adhered to the inner wall of the reactor during the process of dehydrogenation. The thermodynamic driving force of the sintering is the reduction of lower surface energy of the powder particles, while the high surface diffusion rate assists with establishing bonding between the particles even though the dehydrogenation temperature of 560°C (833 K) is a relatively low homologous temperature of titanium with a melting point of 1668°C (1942K). The fine particle sizes which correspond to a large specific surface area and a smaller momentum near the inner wall of the reactor all contributed to sintering. In this experiment, the lumpy titanium powder on the inner wall could be easily crushed to produce a powder with a particle size <75 µm, suggesting that the degree of sintering of the titanium powder is very small. Sintering is unfavorable for the dehydrogenation of the TiH2 powder particles and the spheroidization of the dehydrogenated Ti powder particles, so the parameters such as fluidized bed structure, reaction temperature and velocity of gas flow should be optimized to avoid the occurrence of sintering as much as possible. In the meantime, slight sintering of the very fine powder particles is beneficial, since it causes a decrease of the particle size range, evidenced by the particle size distribution of the dehydrogenated Ti powder.
Conclusions
A novel dehydrogenation process of titanium hydride powder was developed based on the fluidization principle. A TiH2 powder with particle sizes of <75 μm was successfully dehydrogenated using the specially designed fluidization bed reactor and processing temperature and time of 560°C and 120 min. A Ti powder with a small amount of TiH1.5 was obtained after the dehydrogenation reaction. The powder particle shapes were clearly changed with the sharp edges and corners becoming rounded during the dehydrogenation reaction, leading to a significant improvement of sphericity of the powder particles and fluidity of the dehydrogenated Ti powder. The particle size range became smaller and the particle size was larger after dehydrogenation. The dehydrogenation process was accompanied by slight low-temperature sintering of the dehydrogenated Ti powder particles at the inner wall, and this is likely caused by the large specific surface areas of the fine Ti powder particles and reduced momentum of the particles near the inner wall of the reactor.
Acknowledgements
This work was financially supported by Department of Science and Technology, Liaoning Province, China (No. XLYC1802080), and National Training Program of Innovation and Entrepreneurship for Undergraduate students (Project No. 201910145094).
Disclosure statement
No potential conflict of interest was reported by the author(s).
Additional information
Funding
References
- Yang SS, Gwak J-N, Lim T-S, et al. Preparation of spherical titanium powders from polygonal titanium hydride powders by radio frequency plasma treatment. Mater Trans. 2013;54(12):2313–2316.
- Valiev RZ, Semenova IP, Latysh VV, et al. Nanostructured titanium for biomedical applications. Adv Eng Mater. 2008;10(8):1–4.
- Bhowmik S, Benedictus R, Poulis JA, et al. High-performance nanoadhesive bonding of titanium for aerospace and space applications[J]. Int J Adhes Adhes. 2009;29:259–267.
- Huang Y, Tang HP, Wu YJ, et al. Research of low-cost titanium and titanium-alloy powder produced by MHDH. Rare Met Mater Eng. 2008;37(z3):826–829.
- Sharma B, Vajpai SK, Ameyama K, et al. Microstructure and properties of beta Ti–Nb alloy prepared by powder metallurgy route using titanium hydride powder. J Alloys Compd. 2016;656:978.
- Hong Y, Qu T, Shen HS, et al. Preparation of titanium powder by hydrogenation dehydrogenation. Chinese J Rate Metal. 2007;31(3):311–315.
- Wang Z, Yang SL. Preparation of titanium powder by hydrogenation dehydrogenization technology. Metal Mat Metall Eng. 2014;42(5):23–27.
- Huang GM, Lei T, Fang SM, et al. Research progress of preparation powders by titanium hydrogenation. Titanium Ind Prog. 2010;27(6):6–9.
- Hou DX. Production of low oxygen titanium powder by hydrogenation dehydrogenation in Japan. Nonferr Min Metall. 1997;2:31–34.
- Wang Z, Shao HP, Ye Q, et al. Preparation of TiAl alloy powders by reaction of titanium hydride and aluminum in high vacuum. J Funct Mater. 2014;000(10):10045–10048.
- Hao XY, Gai GS, Wu YX, et al. Shape modification of HDH Ti powder and its mechanism analysis. Rare Met Mater Eng. 2009;38(S3):264–266.
- Zou X, Wu YX, Gai GS, et al. Effects of spheroidization on particle characteristics and feedstock rheologies of HDH Ti powder. Powder Metall Ind. 2006;16(5):1–4.
- He W, Jiang Y, Du Y, et al. Fabrication and properties of ultrafine Ti powder by NaCl coated/hydrogenation-dehydrogenation combined method. The Chinese J Nonferr Metal. 2012;22(1):158–164.
- Guo ZM. Preparation of micro-spherical titanium powder by RF plasma. Rare Metal Mater Eng. 2013;42(6):1291–1294.
- Wang JJ, Hao JJ, Guo ZM, et al. Preparation of spherical tungsten and titanium powders by RF induction plasma processing. Chinese J Rare Metal. 2015;34(6):431–435.
- Ding WW, Chen G, Qin ML, et al. Low-cost Ti powders for additive manufacturing treated by fluidized bed. Powder Technol. 2019;350:117–122.
- Zheng Y. A fluidizing device and method for dehydrogenation of titanium hydride powder. CN:202010489127.X[P]. 2020.06.02.
- Kennedy AR, Lopez VH. The decomposition behavior of as-received and oxidized TiH2 foaming-agent powder. Mater Sci Eng A. 2003;357(1–2):258–263.
- Fan LS. Gas-liquid-solid fluidization engineering. New York: Butterworths; 1989.
- Li YD. (2009). Study on gas-solid flow model of fluidized bed based on Fluent Software. Unpublished doctoral dissertation, Chongqing University, Chungking.
- German RM. Sintering theory and practice. New York: Wiley-Interscience; 1996.