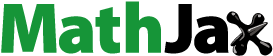
ABSTRACT
As one of the most promising materials for environmental barrier coatings (EBCs) applications, rare-earth (RE) silicates possess good high-temperature stability, coefficients of thermal expansion (CTEs) close to those of Si-based ceramics, low thermal conductivities, and excellent hot-corrosion resistances to water vapor and calcia-magnesia-aluminosilicate (CMAS) molten salts. With the gradual understanding on thermophysical properties of rare-earth silicates, more and more researches focus on their CMAS hot-corrosion behavior, which is strongly related to the formation of corrosion products, infiltration of CMAS glass, and the final failure caused by stress-induced microcracks. In this review, the dependences of CMAS properties and sticking behavior on the composition of CMAS are introduced. Then the CMAS hot-corrosion processes of different rare-earth silicates containing rare-earth disilicates, rare-earth monosilicates, and rare-earth oxyapatites are evaluated, as well as different corrosion reactions and potential failure mechanisms during these processes. Wherein, the formation of corrosion products and the infiltration of CMAS depend on the RE: Si ratio, species of rare-earth cations, or other additives, which lead to the research prospects to modification strategies of rare-earth silicates, including the entropy-stabilized solid-solution, the composite technology and microstructure-tailored coatings. The outlook for further investigation is also highlighted.
Introduction
Developing advanced gas turbines with excellent properties such as high flow ratio, high thrust-weight ratio and high inlet temperature has attracted considerable attention [Citation1]. Among these properties, the high inlet temperature plays a vital role in achieving a high thrust-weight ratio and high thermal efficiency [Citation2]. At present, the Ni-based superalloys widely applied as hot sections of turbines usually withstand temperatures of above 1075°C, which cannot meet the requirements for advanced aero-engines [Citation3]. Accordingly, high-performance ceramics with excellent properties at high temperatures have been developed to fabricate hot section components. Among them, Si-based ceramics are recognized as admirable materials to replace traditional Ni-based superalloys to fabricate hot sections in turbine, such as SiC, Si3N4, etc [Citation4]. However, Si-based ceramics and ceramic matrix composites (CMCs) suffer from attacks by the robust combustion environment, wherein contains oxygen, water vapor, volcanic ash, etc [Citation5,Citation6]. Si-based ceramics usually generate dense SiO2 film by oxidation, which reacts with water vapor to generate gaseous Si(OH)4. This results in the recession of Si-based ceramics, which could reach 1 μm/h for CMC materials with increasing temperature to 1300°C [Citation5]. Besides, silicates existing in-service environment originate from airborne dust, runway pieces, volcanic ash, and ambient dust or fly ash in turbine. These silicates, uniformly named as CMAS (Calcia-magnesia-aluminosilicate) crash the inner surface of turbine and deposit on it, resulting in melting and corrosion behavior [Citation7,Citation8]. The failures caused by corrosion and blockage of cooling hole lead to disastrous consequences, as shown in [Citation9]. Therefore, thermal protective coatings named environmental barrier coatings (EBCs) are necessary to prevent Si-based ceramics from attacks in a harsh chemical environment [Citation10–12].
Figure 1. Military aircraft flying during a sand storm in an arid region. Image insert-mineral dust particles passing through the gas turbine and corroding the ceramic coatings and metallic surfaces of the hot section components. Reproduced with permission from Reference [Citation9], © The American Ceramic Society 2013.
![Figure 1. Military aircraft flying during a sand storm in an arid region. Image insert-mineral dust particles passing through the gas turbine and corroding the ceramic coatings and metallic surfaces of the hot section components. Reproduced with permission from Reference [Citation9], © The American Ceramic Society 2013.](/cms/asset/06702d94-f448-4d36-ac7b-bd7c3d745492/thts_a_2019389_f0001_oc.jpg)
According to the purpose of industrial applications, the following properties are required for EBC materials [Citation13]: (a) good phase stability at high temperatures which avoids the failure of coating integrity due to phase transformation; (b) coefficients of thermal expansion (CTEs) close to substrate materials of Si-based ceramics or CMCs, which avert delamination or cracking of coating caused by the stress due to the mismatch of CTEs; (c) good chemical compatibility, which avoids harmful reactions with substrate materials; (d) excellent hot-corrosion resistances to ambient environment which correspond mainly to the resistances to water vapor and CMAS glass; (e) low thermal conductivity which can decrease the temperature of substrate [Citation14]. EBCs have evolved over about three generations. The first-generation mullite/yttria-stabilized-zirconia (YSZ) coatings are eliminated due to the mismatch of CTEs between YSZ and mullite, which will lead to cracks and provide channels for diffusing media [Citation15–18]. The second-generation Si/mullite-baria-strontia aluminosilicate (BSAS) mixed top coat is easy to peel in prolonged service at high temperatures, which is attributed to the formation of glass phases [Citation19–22]. While, rare-earth silicates meet almost all the requirements for applying as environmental barrier coatings, which have attracted great attention because of its CTEs close to Si-based ceramics, high-temperature phase stability, good chemical compatibility with substrates, low thermal conductivity and excellent resistances to hot corrosion by water vapor and CMAS molten salts [Citation23–26].
Therefore, rare-earth silicates are believed to be the most prospective materials applied as the topcoat, which constitute an integrated EBC structure with Si bond layer. Different from the previous two generations of coating, its failure is mostly due to cracks or fracture by stresses, which result from the volume strain due to phase transition during the process of corrosion, the large difference between CTEs of rare-earth silicates and penetrated CMAS glass, and the growth of thermally grown oxide in the Si bond layer.
Crystal structures and thermophysical properties of rare-earth silicates
The most common rare-earth silicates composed of RE2O3 and SiO2 are RE2SiO5, RE2Si2O7 and RE9.33Si6O26. Rare-earth silicates form different crystal structures according to different RE2O3: SiO2 ratios and the radii of rare-earth cations. There exist two crystal structures for a RE2O3: SiO2 ratio of 1: 1, and seven crystal structures for a RE2O3: SiO2 ratio of 1: 2, while RE9.33Si6O26 only exists one crystal structure for all rare-earth cations [Citation27]. Main mechanical properties and thermophysical properties of some rare-earth for application of EBCs are listed in [Citation14,Citation28–37].
Table 1. Mechanical and thermophysical properties of rare-earth monosilicates.
RE2SiO5 is comprised of [SiO4] tetrahedra and [REOm] polyhedra, as shown in [Citation28,Citation38]. The space group of X1-RE2SiO5 is P21/c, which consists of rare-earth cations with large ionic radii of La–Gd. However, the space group of X2-RE2SiO5 is C2/c, which consists of rare-earth cations with small ionic radii of Tb–Lu. The coordination numbers of rare-earth cations are 7 and 9 in X1-RE2SiO5, as well as 6 and 7 in X2-RE2SiO5. The calculated high-temperature thermal conductivities of X2-RE2SiO5 (RE = Lu, Yb, Tm, Er, Ho, Y, Dy) are ∼1 W·m−1·K−1. The CTE of rare-earth monosilicate is increasing when increasing temperature, and reach 6.94–8.84 × 10−6 K−1 at 1473 K. There exist seven crystal structures for RE2Si2O7, containing α, β, γ, δ, A, and G, as shown in . Wherein, CTEs of rare-earth disilicates with the same crystal structures possess similar CTEs. β-RE2Si2O7 and γ-RE2Si2O7 own CTEs close to Si-based ceramics. However, the thermal conductivities of rare-earth disilicates are higher than those of rare-earth monosilicates. The crystal structure of RE9.33Si6O26 apatite phase is shown in (Gd9.33(SiO4)6O2 as an example) [Citation39]. The apatite phase also consists of [REOm] polyhedra and [SiO4] tetrahedra, where the coordinate numbers of rare-earth cations are 6 and 9. Usually, the CTEs of RE9.33Si6O26 are much higher than those of Si-based ceramics, which may lead to its disuse as EBC materials [Citation40,Citation41]. However, the outstanding resistance of RE9.33Si6O26 to CMAS corrosion may attract attention on its potential of RE9.33Si6O26 as a type of EBC material.
Figure 2. Crystal structures of rare-earth monosilicates: (a) X1-RE2SiO5, (b) X2-RE2SiO5 Reproduced with permissions from Reference [Citation28], © Elsevier Ltd. 2015, and Reference [Citation38], © Elsevier Ltd. 2018.
![Figure 2. Crystal structures of rare-earth monosilicates: (a) X1-RE2SiO5, (b) X2-RE2SiO5 Reproduced with permissions from Reference [Citation28], © Elsevier Ltd. 2015, and Reference [Citation38], © Elsevier Ltd. 2018.](/cms/asset/dbf86a53-ac84-467b-824f-ab2ec613bb16/thts_a_2019389_f0002_oc.jpg)
Figure 3. Crystal structures of rare-earth disilicates plotted with the biggest thermal expansion axis oriented vertically: (a) α-RE2Si2O7; (b) β-RE2Si2O7; (c) γ-RE2Si2O7; (d) δ-RE2Si2O7; (e) A-RE2Si2O7; and (f) G-RE2Si2O7. Reproduced with permission from Reference [Citation35], © The American Ceramic Society 2013.
![Figure 3. Crystal structures of rare-earth disilicates plotted with the biggest thermal expansion axis oriented vertically: (a) α-RE2Si2O7; (b) β-RE2Si2O7; (c) γ-RE2Si2O7; (d) δ-RE2Si2O7; (e) A-RE2Si2O7; and (f) G-RE2Si2O7. Reproduced with permission from Reference [Citation35], © The American Ceramic Society 2013.](/cms/asset/ae922067-007e-40e7-838f-cc78760c796d/thts_a_2019389_f0003_oc.jpg)
Figure 4. Crystal structure of Gd9.33(SiO4)6O2: (a) view of the ab plane, (b) schematic of the ab plane, (c) c-direction for Gd1 sites and (d) c-direction for Gd2 sites. Reproduced with permission from the open access Ref. [Citation39].
![Figure 4. Crystal structure of Gd9.33(SiO4)6O2: (a) view of the ab plane, (b) schematic of the ab plane, (c) c-direction for Gd1 sites and (d) c-direction for Gd2 sites. Reproduced with permission from the open access Ref. [Citation39].](/cms/asset/1203d8a8-65a1-4fac-b0f0-18f714a1f047/thts_a_2019389_f0004_oc.jpg)
It can be found from the above that CTE of rare-earth silicate mostly depends on its crystal structure. Rare-earth silicates with the same crystal structure but different rare-earth cations possess similar CTEs. For rare-earth silicates with the same crystal structure, the resistances of [REOx] polyhedra to thermal deformation determine their CTEs [Citation29,Citation42,Citation43]. For rare-earth monosilicates, the anomalous dependence of lattice conductivity on RE atomic mass originated from the specific role of RE elements on affecting heterogeneous atomic bonding and strong vibrational anharmonicity [Citation30]. For rare-earth disilicates or rare-earth oxyapatites with different rare-earth cations, their experimental thermal conductivities are similar.
Although most of rare-earth silicates (mainly rare-earth monosilicates and rare-earth disilicates) exhibit suitable performance, some problems should be noticed when they are applied as coatings, containing the decomposition during rare-earth during spraying process, thermal decomposition in water vapor environment, and so on. The former points out the importance of adjusting the RE: Si ratio of powders before spaying to the coating phase after spraying [Citation44]. The latter emphasizes the necessity of screening rare-earth silicate species or regulating proportions of rare-earth silicates in coatings, which could improve the stability of EBC in-service environment [Citation45,Citation46]. The last but not least is the consumption of coating materials or failure resulted from the CMAS attack.
Properties of CMAS glass and its sticking behavior on the topcoat of the EBCs
Two kinds of materials, rare-earth silicates and the corrosion medium – CMAS glass, are involved in the CMAS hot-corrosion behavior. The composition of CMAS glass determines its coefficient of thermal expansion, melting temperature, viscosity and crystallization property. Melting temperature decides the temperature above which CMAS glass fuses to corrode rare-earth silicates significantly. Viscosity governs the penetration rate of molten CMAS glass into EBC coatings along grain boundaries, cracks or other defects. After CMAS penetration, cracks in coating materials easily generate or even propagate if the CTE of CMAS glass is prominently different from that of coating material. Besides, the composition of both CMAS glass and the composition of rare-earth silicate determine the corrosion products together. The sticking behavior of CMAS on the topcoat of the EBCs decides the corrosion reaction time between CMAS and the topcoat material, which usually depends on the composition of CMAS, material type of topcoat, and the surface morphology of topcoat. Therefore, verifying the influence of composition on the properties of CMAS glass is necessary to analyze and further predict the CMAS hot-corrosion behavior of rare-earth silicate.
Wiesner et al. [Citation47] used rotating spindle viscometer to measure the viscosity of CMAS glass with a nominal composition of 23.3CaO–6.4MgO–3.1Al2O3–62.5SiO2–4.1Na2O–0.5K2O–0.04Fe2O3(mol.%) at temperatures ranging from 1215°C to 1520°C, and found that the viscosity of CMAS glass decreases with increasing temperature. The equally important finding is that the values determined by Fluegel and FactSage models are close to the experimentally measured viscosity of CMAS glass. Jia et al. [Citation48] evaluated the effects of SiO2: CaO molar ratio on the viscosity, structure, and properties of the CMAS glass. The melt viscosity decreases with increasing temperature. Moreover, with decreasing the SiO2: CaO ratio, the melt viscosity decreases, which is due to the change of the glass network structure. This means that CMAS glass with a low SiO2: CaO ratio generally infiltrates along grains boundaries or other defects more quickly. Webster et al. [Citation49] calculated the viscosity of each glasse with different amounts of TiO2. Although the viscosity decreases from 3.1 to 1.3 Pa·s at 1300°C and from 0.7 to 0.4 Pa·s at 1500°C, the glass surrounding the crystalline phase possesses a much lower viscosity than CMAS. For example, the viscosities of glass surrounding CaTiO3 and diopside are 6.7 and 15.2 Pa·s at 1300°C, 1.3 and 2.9 Pa·s at 1500°C, respectively. This means that adding TiO2 as a component of coating materials is probably conducive to the crystallization of CaTiO3 or diopside, which decreases the melt viscosity. Hence, clarifying the influence of different additives on the properties of CMAS glass is beneficial to broadening horizons and purposing new strategies to improve the resistance of rare-earth silicate to CMAS corrosion.
Actually, CMAS glass particles usually collide with coatings as a form of droplets, so it is quite necessary to make clear how the molten CMAS droplets impact on the surface of coatings. Some literature attempted to clarify this interaction or the wetting behavior of melt on the coating surface. Song et al. [Citation50] studied the wettability and spreading behavior of volcanic ash by the sessile drop method. Particles densify driven by surface tension until forming a large droplet with inner gas bubbles and crystals, which spread on the surface. As crystals in droplets dissolve into the melt, the wetting regime transforms from heterogeneous to homogeneous. The wetting of molten volcanic ash droplets is determined by deducing both the viscosity and microstructural evolution. Subsequent research also supports this conclusion [Citation51] As shown in , splash morphology tends to form on smooth surfaces with radial jetting and break-up, while circular- and disc-like splats tend to form on rough surfaces, which results from asperities on rough surfaces restricting flow. Surface properties and in-flight characteristics of molten volcanic ash droplets are the main determinants of the splat accumulation in TBCs, which could be broadened to EBCs. Except for experiments, first-principle calculation also offers some interesting wetting mechanism of CMAS melt on coating surfaces, which can be broadened from TBCs to EBCs. Li et al. [Citation52] studied the wetting process of CMAS melt on yttria-stabilized-zirconia (YSZ) surface at 1523 K by molecular dynamics simulations and claimed that the distribution of oxygen ions on the YSZ surface layer is the determinant affecting the wettability and even corrosion of CMAS on YSZ thermal barrier coatings.
Figure 5. Initial impact behavior of molten volcanic ash droplets on APS TBCs (column I), EB-PVD TBCs (column II), and Al2O3 (column III) substrates. The left, middle, and right sub-columns in each column illustrate the photographs, SEM images, and Si elemental mappings corresponding to the SEM images of various substrates impacted by the molten volcanic ash droplets with torch distances from 50 mm to 125 mm, respectively. Reproduced with permission from Reference [Citation35], © Elsevier Ltd. 2019.
![Figure 5. Initial impact behavior of molten volcanic ash droplets on APS TBCs (column I), EB-PVD TBCs (column II), and Al2O3 (column III) substrates. The left, middle, and right sub-columns in each column illustrate the photographs, SEM images, and Si elemental mappings corresponding to the SEM images of various substrates impacted by the molten volcanic ash droplets with torch distances from 50 mm to 125 mm, respectively. Reproduced with permission from Reference [Citation35], © Elsevier Ltd. 2019.](/cms/asset/a8bd902a-b26f-4bfe-99bd-038a8819a6c1/thts_a_2019389_f0005_oc.jpg)
More than that, Song et al. [Citation53] emphasized the possibly severe underestimates of the thermal hazard due to the overestimates of sticking temperature, which results from the inaccuracy of the substitution of sand or dust proxy for volcanic ash. They parameterized the ash-sticking behavior based on experiments of same volcanic ash in the world and developed a model to assess the deposition probability of volcanic ash in jet engines. As shown in , in the process of heating, all kinds of volcanic ashes go through four stages, corresponding to four characteristic temperatures: a shrinkage temperature (ST); a deformation temperature (DT); a hemispherical temperature (HT); and a flow temperature (FT). This embodies the initial contacting behavior of volcanic ashes on the surface. And furthermore, characteristic temperatures for volcanic ashes with different components are different. This is meaningful for the assessment of initial melting and sticking behavior of different volcanic ash, which can be used to guide the analysis of CMAS hot-corrosion behavior.
Figure 6. Geometric characterization of volcanic ash compacts at the characteristic temperatures: (a) Geometrical definition of four characteristic temperatures (ST, DT, HT and FT) in the volcanic ash melting process, (b) distribution of the four characteristic temperatures for the nine volcanic ash, ordered as a function of SiO2 content, (c) typical behavior observed during a test, (d) back-scattered electron images of corresponding microstructures of the volcanic ash at the four characteristic temperatures. Reproduced with permission from the open access Ref. [Citation53].
![Figure 6. Geometric characterization of volcanic ash compacts at the characteristic temperatures: (a) Geometrical definition of four characteristic temperatures (ST, DT, HT and FT) in the volcanic ash melting process, (b) distribution of the four characteristic temperatures for the nine volcanic ash, ordered as a function of SiO2 content, (c) typical behavior observed during a test, (d) back-scattered electron images of corresponding microstructures of the volcanic ash at the four characteristic temperatures. Reproduced with permission from the open access Ref. [Citation53].](/cms/asset/6a838dff-d727-4f98-9bd0-ec68ca4bd509/thts_a_2019389_f0006_oc.jpg)
To sum up, the property of glass depends on the composition, which influence the CMAS hot-corrosion behavior notably. The sticking temperature and wetting temperature of glass with different compositions on the topcoat are different. Meanwhile, the viscosity of glass determines the infiltration of CMAS glass along defects in the topcoat, as well as the degree of CTE mismatch between CMAS, apatite and rare-earth silicate. This means a lot to the failure induced by CMAS corrosion in the rare-earth silicate topcoat, which is introduced in part 5.
Corrosion reactions and microstructural evolution during CMAS hot corrosion
For RE2Si2O7
To definite the reactions occurring in the process of CMAS corrosion, the thermochemical behaviors of Y2Si2O7 and Yb2Si2O7 were evaluated with three types of CMAS glass possessing CaO: SiO2 ratios relevant to gas turbine systems [Citation54]. For CaO-rich CMAS compositions, RE2Si2O7 (RE = Y, Yb) dissolves into the molten CMAS and generates apatite. While as the CaO content decreases in CMAS, the amount of apatite phase formed decreases. Compared to CaO-rich CMAS compositions, RE2Si2O7 exhibits significantly lower reactivity with CaO-lean CMAS compositions, which may allow molten CMAS to infiltrate into coating materials via grain boundaries. Further, Stokes et al. [Citation55] analyzed thermochemical interactions between RE2Si2O7 (RE = Er, Dy, Gd, Nd) and CMAS glass. Crystalline reaction products are comprised of RE2Si2O7, SiO2 and Ca2 + yRE8 + x(SiO4)6O2+3x/2 + y apatite. Increased CaO: SiO2 ratios in CMAS and cation size of RE3+ improve reactivity, which results in the variation in the stoichiometry and lattice parameters of the formed apatite. In addition, only a small amount of SiO2 crystallizes in the corrosion process with most amorphous SiO2. The content of Ca2+ in apatite precipitates is the highest after corrosion of Dy2Si2O7, and the lowest after corrosion of Nd2Si2O7, which attributes to strain reduction in the crystal structure. It is possible to reduce the strain by increasing the amount of the same size cation in the structure for small Dy3+ and by decreasing in vacancy formation when maintaining Ca: RE close to the 1: 1 ratio of a defect-free structure for large Nd3+.
Liu et al. [Citation56] investigated the CMAS corrosion behavior of rare-earth disilicates (RE2Si2O7, RE = Yb, Lu, La, Gd, Eu, Sc, Y) roughly. RE2Si2O7 reacts with CMAS above 1250°C and generates various reaction zones at the interfaces. Different corrosion products are detected to be Ca3La6(SiO4)6, Ca2La8(SiO4)6O2, Ca2Gd8(SiO4)6O2, Ca2Eu8(SiO4)6O2, Ca3Sc2Si3O12 and Ca4Y6(SiO4)6O have been detected. As shown in , two reaction zones formed: for the RE2Si2O7 (RE = Yb, Lu, La, Eu, and Gd), the reaction zones dissolve into the molten CMAS and separate from the RE2Si2O7; However, as for RE2Si2O7 (RE = Sc and Y), the reaction zones do not dissolve into the molten CMAS. The formed dense reaction zones are believed to inhibit the infiltration of molten melt into the RE2Si2O7. Turcer et al. [Citation57,Citation58] studied the high-temperature (1500°C) interactions of dense polycrystalline ceramics, γ-Y2Si2O7, β-Yb2Si2O7 and β-Sc2Si2O7, with the CMAS glass. Needle-like Y-Ca-Si apatite grains form at the interface between γ-Y2Si2O7 and CMAS. However, β-Yb2Si2O7 and β-Sc2Si2O7 almost do not generate new corrosion products with CMAS. Although almost no reaction occurs in the corrosion process, molten CMAS glass penetrates into the grain boundaries, which leads to blisteri cracking damage attributed to the through-thickness dilatation-gradient, as shown in . Similarly, Wiesner et al. [Citation59] explored the interaction between Yb2Si2O7 and CMAS glass at temperatures ranging from 1200°C to 1500°C, and found that the dissolution of Yb2Si2O7 into molten melt as well as the CMAS penetration along grain boundaries lead to significant microstructural damage. The higher the temperature, the lower the viscosity of melt is and the more severe the damage is. The CMAS corrosion behavior of Y2Si2O7 at temperatures ranging from 1200°C to 1500°C also reveals the weak resistance, which caused by the formation of apatite layer and the infiltration of CMAS along both grain boundaries and porous channels, especially at high temperatures above 1400°C [Citation60].
Figure 7. The BSE images of cross sections of RE2Si2O7 after CMAS corrosion in water vapor at 1400 °C for 10 h and EDS analysis of the reaction zone. (a), and (b) Yb2Si2O7, (c), and (d) Lu2Si2O7, (e), and (f) La2Si2O7, (g), and (h) Gd2Si2O7, (i), and (j) Eu2Si2O7, (k), and (l) Sc2Si2O7, and (m), and (n) Y2Si2O7. Reproduced with permission from Reference [Citation56], © Elsevier Ltd. 2013.
![Figure 7. The BSE images of cross sections of RE2Si2O7 after CMAS corrosion in water vapor at 1400 °C for 10 h and EDS analysis of the reaction zone. (a), and (b) Yb2Si2O7, (c), and (d) Lu2Si2O7, (e), and (f) La2Si2O7, (g), and (h) Gd2Si2O7, (i), and (j) Eu2Si2O7, (k), and (l) Sc2Si2O7, and (m), and (n) Y2Si2O7. Reproduced with permission from Reference [Citation56], © Elsevier Ltd. 2013.](/cms/asset/d089ec8a-ee02-43d6-8f53-b083b396d951/thts_a_2019389_f0007_ob.jpg)
Figure 8. SEM images of cross-section of β-Yb2Si2O7 pellet interacted with CMAS at 1500°C for 24 h: (A) low (whole pellet) and (B, D) high magnification. (C) Ca elemental mapping corresponding to (D). The dashed boxes in (A) illustrate regions where high-magnification SEM images in (B) and (D) were collected from. Reproduced with permission from Reference [Citation57], © Elsevier Ltd. 2018.
![Figure 8. SEM images of cross-section of β-Yb2Si2O7 pellet interacted with CMAS at 1500°C for 24 h: (A) low (whole pellet) and (B, D) high magnification. (C) Ca elemental mapping corresponding to (D). The dashed boxes in (A) illustrate regions where high-magnification SEM images in (B) and (D) were collected from. Reproduced with permission from Reference [Citation57], © Elsevier Ltd. 2018.](/cms/asset/e913bd3c-0e05-46fd-8e84-860e62ea7c9b/thts_a_2019389_f0008_oc.jpg)
Poerschke et al. [Citation61] depicted three stages of the corrosion process by analyzing the interactions between Y2Si2O7 and CMAS. Y2Si2O7 firstly dissolves into the melt at Stage I, which improves the total content of liquid, involving the increased concavity on the surface. Meanwhile, the dissolution of Y2Si2O7 increases the concentrations of SiO2 and YO1.5 and decreases the concentrations of other oxides in the melt. Further dissolution of Y2Si2O7 causes the localized concentration peak, resulting in the crystallization of apatite at Stage II. The reaction is described generally by Equation (1):
(1)
(1) The actual reactions deviate from Equation (1) due to the equilibrium between apatite and melt varying with the Ca: Si ratio in residual melt. Apatite grains crystallized initially possess a higher concentration of CaO than that in Ca2Y8(SiO4)6O2, which decreases as the reaction proceeds until decreasing to ∼12 mol.% at the end of Stage II. In stage III, the composition of melt locates at an equilibrium field including Y2Si2O7 with no reaction occurring anymore. The Ca: Si ratio keeps decreasing from the initial value of 0.72 until the plateau at ∼0.23 (13/57).
It can be seen that blister cracks originated from the infiltration of CMAS melt along grain boundaries is the root cause of failure when rare-earth disilicates applied as EBC materials. Although apatite grains crystallize in the melt containing dissolved Y2O3, the formation would cease under the restrictions of Ca: Si ratio, which results in the infiltration of melt along grain boundaries or defects.
For RE2SiO5
CMAS hot-corrosion behavior of RE2SiO5 can be described as a dissolution-reprecipitation process. Thermodynamic allows rare-earth monosilicate to dissolve into the CMAS melt, which reprecipitates as Ca-Y apatite silicates [Citation62]. The mechanism relates to the growth of a thin and dense apatite layer at the surface in Y2SiO5 [Citation63]. This reaction keeps ongoing due to the transformation of CMAS constituents along the apatite grain boundaries, which are covered by continuous nanoscale amorphous thin films. The continuous nucleation and broadening of new crystals at the interface limit the growth of former crystals, which finally separate from the interface and are surrounded by the melt, resulting in the coarsening. The broad texture is basically retained, yet the coarsening is anisotropic owing to crystallographic constrains, which causes isolation of crystals and the extension of the intergranular amorphous regions. Ongoing reaction and variations on the properties of melt increase the sizes of apatite grains at the interface. Ahlborg et al. [Citation64] highlighted the preferential CMAS attack at grain boundaries, which is provided by the low-melting particles located between grains, as shown in . Wherein, the lighter phase of this eutectic is rich in Al, Mg, Si, and Yb, while the dark phase is rich in Al, Ca, Mg, and Si. The low-melting particles were found to penetrate the whole specimen cross-section with a bulk thickness of ∼4 mm.
Figure 9. SEM images of Yb2SiO5 interacted with CMAS for 200 h. (a), (b), (c) and (d) low and high-magnification surface BSE images of Yb2SiO5 interacted with CMAS at 1500°C for 200 h. Reproduced with permission from Reference [Citation64], © Elsevier B.V. 2013.
![Figure 9. SEM images of Yb2SiO5 interacted with CMAS for 200 h. (a), (b), (c) and (d) low and high-magnification surface BSE images of Yb2SiO5 interacted with CMAS at 1500°C for 200 h. Reproduced with permission from Reference [Citation64], © Elsevier B.V. 2013.](/cms/asset/5ff2561f-5070-42b7-a418-f4adc58ac9b2/thts_a_2019389_f0009_ob.jpg)
Both compositions of CMAS and the type of rare-earth cation in RE2SiO5 influence the crystallization preference and corrosion resistance. For the Iceland volcanic ash owing a low CaO concentration, Yb2SiO5 reacts slowly with it at the interface. Crystals in the melt are mainly self-crystallizing products, such as Sodian-anorthite (Ca,Na)(Al,Si)2Si2O8, Aluminian-augite Ca(Mg,Fe,Al)(Si,Al)2O6, Albite Na(Si3Al)O8, and Analcime NaAlSi2O6/H2O. However, CMAS with a higher CaO concentration reacts more easily and vigorously with Yb2SiO5 due to the high concentration of corrosive elements (CaO in CMAS), resulting in rapid growth of the apatite reaction layer [Citation65]. Poerschke et al. [Citation66] assessed the phase equilibria in the CaO–SiO2–Y2O3 system at 1400°C and 1600°C, as well as the measurement of melting temperature of each ternary phase and the shape of the liquid field at 1600°C. They pointed out that the apatite phase which exists theoretically between Ca4Y6(SiO4)6(O□) and Y9.33□0.67(SiO4)6O2, exhibits good stability over a small range from Ca0.5□0.5Y9(SiO4)6O2 to Ca2.5Y7.5(SiO4)6(O1.75□0.25) at 1400°C and 1600°C, where the square symbols represent the corresponding vacancies. This reveals possible thermodynamics in the CMAS corrosion process.
In order to research the dependence of phase stability of RE2SiO5 under attacks from CMAS on the type of rare-earth cations, Tian et al. [Citation67] investigated the corrosion behaviors of RE2SiO5 at 1300 °C. The CMAS interacts with RE2SiO5 (RE = Lu, Yb, Tm, Er, Y, Ho, Dy, and Tb) to form RE-Si apatite. The thickness of reaction layer almost decreases linearly with decreasing the ionic radius of RE, which is due to the decreased reactivity of RE2SiO5 with small RE, as shown in . They put forward that the difference of optical basicity (OB) between RE2SiO5 and CMAS plays an important role in screening EBC candidates through exploring the variation on chemical activity. The OB theory originates from the Lewis acid–base theory, and is usually applied to assess chemical reactivity of oxides glasses [Citation67]. Value of OB characterizes electron acceptor power of metal cation and electron donor power of oxygen ion in metal oxides. The smaller the difference of optical basicity between RE2SiO5 and CMAS, the higher the resistance of rare-earth monosilicate to CMAS is. Jiang et al. [Citation68] investigated hot corrosion of RE2SiO5 (RE = Y, Lu, Yb, Eu, Gd, and La) with different cation substitutions under the CMAS attack at 1200°C. The research also supports the dependence of CMAS resistance of RE2SiO5 on the radius of RE cation. They put forward that the stability of RE2SiO5 under the attack from CMAS depends on the degree of distortion in O-RE coordinated polyhedra. This is due to the easily destroyed RE-O bonds which are displaced by Ca2+ during the CMAS corrosion process. However, they found that garnet phase also crystallized on the top of RE2SiO5 samples except for the well-known Ca-RE oxyapatite. Furthermore, the interaction between CMAS and rare-earth monosilicates leads to the enrichment of SiO2, prompting monosilicates to form disilicates, and the latter exhibits better resistance toward CMAS attack than rare-earth monosilicates. The differences in reaction products may be due to the differences in corrosion temperatures, which are 1300°C and 1200°C, respectively. When the CMAS does not melt, it tends to self-crystallize, and generates garnet phase or RE2Si2O7 by the consumption of Al2O3, MgO and SiO2. The research of Kim et al. [Citation69] supported this view, which reveals the emergence of Ca2Gd8Si6O26 apatite with increasing corrosion temperature from 1200°C to 1300°C. Furthermore, Poerschke et al. [Citation70] illustrated the reduced potency of Yb2O3 compared to Gd2O3 for crystallizing apatite, which causes the presence of alternate silicate reaction products that apparently grow too slowly to arrest the infiltration.
Figure 10. Comparison of infiltration depths for some EBC and TBC candidates after corrosion of simulated Ca33Mg9Al13Si45O151.5 at various temperatures for different time. Reproduced with permission from Reference [Citation67], © Elsevier Ltd. 2018.
![Figure 10. Comparison of infiltration depths for some EBC and TBC candidates after corrosion of simulated Ca33Mg9Al13Si45O151.5 at various temperatures for different time. Reproduced with permission from Reference [Citation67], © Elsevier Ltd. 2018.](/cms/asset/36b6b93f-71f7-4ae9-9dfb-abaa5130ab5b/thts_a_2019389_f0010_oc.jpg)
For oxyapatite (Ca2RE8Si6O26 or RE9.33Si6O26)
Besides rare-earth monosilicates and disilicates which have been often discussed, the CMAS hot-corrosion behavior of oxyapatite is also motivating, despite the fact that the CTEs of oxyapatite such as RE9.33Si6O26 are much higher than those of Si-based ceramics. Sleeper et al. [Citation71] studied the thermochemical interactions between Ca2Y8Si6O26 apatite and CMAS at temperatures ranging from 1200°C to 1500°C. Ca3Y2(Si3O9)2 cyclosilicate phase arises at 1200°C and 1300°C, and is not detected at 1400°C and 1500°C. Although no new phase forms, the CMAS melt penetrates along pores and grain boundaries above 1400°C. At elevated temperatures, apatite grains also dissolve into the melt, and reprecipitate as a form of needle within the amorphous phase during cooling. Although no phase transformation occurs in the process which is different from rare-earth monosilicates and disilicates (there exists phase transformation during the same dissolution-reprecipitation process for the latter two materials), Ca2Y8Si6O26 apatite still seems to be only effective to prevent the infiltration of CMAS at temperatures below 1200°C. However, the rare-earth oxyapatite RE9.33Si6O26 (RE = Gd, Nd and La, without CaO in ingredient) appears to be a promising CMAS corrosion-resistant material. Zhang et al. [Citation72] found that the reprecipitated Ca-RE apatite layer is dense in RE9.33Si6O26 rather than a reaction layer mixed with CMAS melt in the sacrificial materials (such as Gd2Zr2O7, Y2SiO5, Y2Si2O7, etc.), as shown in , even though both of which are controlled by the dissolution-reprecipitation mechanism. Meanwhile, the thickness of the precipitated layer in La9.33Si6O26 is the highest due to the higher solubility of La in CMAS melt. However, CMAS melt attacks the grain boundaries, cracks or defects of RE9.33Si6O26 apatite as well, penetrating throughout the materials. These results provide new insights into the delayed penetration by the formation of dense reprecipitated layer due to rapid crystallization.
Figure 11. BSE images of cross-section of RE apatite pellets interacted with CMAS at 1300°C from 10 min to 24 h. (a–c) low magnification images, illustrating an overview of three rare-earth apatite silicates interacted with CMAS and (d–f) corresponding high-magnification images from the center region of the interaction zone. Reproduced with permission from Reference [Citation72], © Elsevier Ltd. 2020.
![Figure 11. BSE images of cross-section of RE apatite pellets interacted with CMAS at 1300°C from 10 min to 24 h. (a–c) low magnification images, illustrating an overview of three rare-earth apatite silicates interacted with CMAS and (d–f) corresponding high-magnification images from the center region of the interaction zone. Reproduced with permission from Reference [Citation72], © Elsevier Ltd. 2020.](/cms/asset/046e3fec-40e6-474a-9f4b-66212db308a8/thts_a_2019389_f0011_oc.jpg)
Besides, Costa et al. [Citation73] measured the formation enthalpies of formation of Ca-RE oxyapatites (RE = Yb, Er, Y, Dy, Nd, Gd and Sm) by high-temperature solution calorimetry. The oxyapatite is more stable with a fully stoichiometric composition compared to defected structures. Their stability increases with decreasing the ionic potential of rare-earth cations and ionic field strength, namely increases with their ionic radius. This is effective to accurately calculate and predict phase equilibria, which could guide the in-depth investigation on the CMAS corrosion mechanism.
For three different types of rare-earth silicates, the main reaction product by CMAS corrosion is mainly Ca-RE apatite phase. And simultaneously, the nucleation and growth of apatite grains follow dissolution-reprecipitation mechanism. However, the ratio of RE: Si in rare-earth silicates determines the corrosion rate and the maximum reaction limit. The formation of apatite for rare-earth disilicates consumes CaO but increases the concentration of SiO2 in melt, which decreases the Ca: Si ratio. With decreasing the Ca: Si ratio to the equilibrium value, the formation of apatite ceases. For rare-earth monosilicates, the formation of apatite consumes both CaO and SiO2 in melt, but only CaO for rare-earth oxyapatites. The consumption of SiO2 for rare-earth monosilicates sometimes induces the formation of garnet phase, which is barely found in rare-earth disilicates and rare-earth oxyapatites. The difference in corrosion reaction influences the property of melt during the corrosion process and the crystallization of melt. Due to the same dissolution-reprecipitation process, apatite layer exists between rare-earth silicates and residual CMAS melt. The density of apatite layer is strongly associated with the type of rare-earth cation. Besides, for some rare-earth disilicates which almost do not generate apatite phase, CMAS melt easily penetrates along grain boundaries, resulting in blister cracks.
Stress evolution and failure of rare-earth silicates induced by CMAS
In the field of EBCs, there exist many types of stresses induced by the thermal mismatch. Thermal mismatch could originate from several aspects: (1) the CTE mismatch between different coatings in EBC structure or between the EBC and the Si-based ceramic substrate[Citation74–77]; (2) the thermal mismatch between decomposition products formed in the water vapor environment and the un-corroded topcoat[Citation46,Citation78]; (3) phase transition of TGO (SiO2) in the bond layer which is formed by the oxidation of Si in bond layer[Citation79–81]; (4) the thermal mismatch between CMAS-induced apatite layer and rare-earth silicate, and between the infiltrated CMAS glass along grain boundaries and rare-earth silicate[Citation82–85]. In this review, the fourth is the main focus.
The failure of EBCs caused by CMAS corrosion can be illustrated in , related to the meltage of CMAS on the coating, partial dissolution of EBC materials into the melt, and the formation of corrosion products. After cooling, the mismatch of CTEs between reaction products and coating materials probably leads to the initiation of cracks and spallation, which is detrimental to component longevity. Summers et al. [Citation84] developed a model for the failure prediction of EBCs upon the interaction with CMAS, which is involved in models of reaction thermodynamics, thermophysical properties, and fracture mechanics. For thermodynamics, Thermo-Calc with the python extension and the TCOX6 database has been used to calculate coating consumption and reaction product volumes, with gradual addition of yttrium disilicates into fully molten CMAS. Thermophysical properties of most phases apart from deposits come from previous literature, meanwhile CTE and glass transition temperatures of the deposit are obtained by empirical models, which can adapt to variation in composition of the deposit caused by corrosion reaction. Fracture mechanics are analyzed by calculating the energy release rates (ERR) for penetrating cracking and for spallation through finite element analysis (FEA). The FEA model is composed of a substrate of 10 mm thickness and 20 mm half-width, a yttrium disilicate coating of either 200 or 400 μm (H0), and a deposit with initial thickness between 0 and 1000 μm. The temperature drops from 1573 to 273 K. The existing interpenetrating melt in the apatite layer has been ignored and a spallation crack length of 10H0 has been used to ensure steady-state. All layers are set as stress-free, and an in-plane deposit prestrain is defined to confirm that the in-plane strain in the deposit is zero.
Figure 12. The potential sequence of events in coating failure due to silicate deposits involves accumulation of molten deposit and reaction of deposit with EBC at elevated temperatures followed by cracking and spallation upon cooling. Reproduced with permission from Reference [Citation84], © The American Ceramic Society 2020.
![Figure 12. The potential sequence of events in coating failure due to silicate deposits involves accumulation of molten deposit and reaction of deposit with EBC at elevated temperatures followed by cracking and spallation upon cooling. Reproduced with permission from Reference [Citation84], © The American Ceramic Society 2020.](/cms/asset/227c36da-289a-4c42-ac5d-2a02984a84a0/thts_a_2019389_f0012_ob.jpg)
As a result, CaO-lean CMAS results in minimal risk or failure, while CaO-rich CMAS poses a serious threat to the integrity of coatings. The CTEs of CaO-lean deposits are low and close to those of SiC/SiC composites, and interact with yttrium disilicates weakly, meaning no new phase formed. In contrast, the CTEs of CaO-rich deposits are much higher than those of SiC/SiC composites. Over time, CaO in CaO-rich deposits consumes by reacting with the EBC topcoat, whose CTE thereupon decreases to that of SiC/SiC composites. Nonetheless, CTE of the new formed apatite phase is mismatched. The additional result is the higher consumption of the yttrium disilicate topcoat than reacted with Ca-lean deposits. Whereas other oxides (Al2O3, MgO, FeOx, etc.) play decidedly secondary roles. Penetrating cracks terminate possibly within the EBC layer due to the residual compression stresses or generate the spallation of EBC. Furthermore, they declare that the thicker the critical thickness for spallation, the higher the degree of subsequent spallation, which poses a challenge of tailoring the CMAS resistance of rare-earth silicates. In one word, the antithesis of residual compression state and residual tension state in multilayered coatings leads to the transition from penetrating cracking to spallation. The ERR for the penetrating crack decreases when cracks extend into the compressive layer. With a positive CTE mismatch between EBC material and SiC/SiC composites, penetrating cracking is the preferred mode.
Stolzenburg et al. [Citation85] investigated the interaction of CMAS with Yb2Si2O7-based multilayer EBCs using a combination of high-energy synchrotron X-ray techniques, especially focusing on the dependences of phase-specific stresses and lattice spacings on temperatures, the interaction of CMAS with nanoporosity and the formation of cracks in the coating. The diffraction performed in transmission is realized by combining the small Bragg angles and penetration power associated with high X-ray energies (60 keV). Determined by the beam size of 100 × 40 μm2 for all wide-angle X-ray scattering (WAXS) measurements, samples should be translated 40 μm vertically for each measurement, from the topcoat surface into a depth of 1.5 or 0.5 mm into the SiC/SiC composites. This ensures that the functional relationship between lattice spacing or stresses and depth is determined. Then strains and stresses can be calculated from the Debye ring patterns. Small-angle X-ray scattering (SAXS) data can be concluded to characterize the pore size distribution and total porosity. X-ray computed tomography (XCT) measurement can be used to evaluate the damage evolution. Their results show that molten CMAS induces a decrease in lattice parameters of surface coating material (Yb2Si2O7) due to the exchange of Yb3+ and Ca2+. CMAS corrosion results in compressive stresses in the EBC topcoat after cooling. Thermal mismatch during solidification of CMAS induces through-cracks in the EBC topcoat, which are derived from the surface of CMAS glass. Besides, CMAS can infiltrate into pores in the EBC topcoat, similar to the previous referred infiltration along grain boundaries, which causes blister cracks. The compressive stresses in the EBC topcoat correspond to the calculation result in the CMAS corrosion of yttrium disilicates, when the formation of apatite phase is not considered.
Cai et al. [Citation86] proposed a possible mechanism of the failure in APS TBCs induced by CMAS penetration under thermal cyclic loading, which reveals the influences of creep time and CMAS penetration depth on the spallation of coatings. The importance of tailoring the coating microstructure, especially avoiding sharp horizontal microstructures is emphasized, as well as developing a suitable operating strategy of in-service gas turbines. However, the influence of coating microstructure on failure and corresponding stress analysis were barely researched in EBCs.
In summary, compressive stresses in the EBC topcoat after cooling, namely the thermal mismatch during the solidification of CMAS glass lead to through-cracks in EBCs. Meanwhile, if CMAS glass infiltrates into defects in EBCs without corrosion reaction, the thermal stresses induced by the CTE mismatch between CMAS glass and EBC topcoats lead to blister cracks. Therefore, for assessment of EBC failure due to CMAS, the formation of corrosion products, the variation in properties (CTE, viscosity, etc.) of CMAS glass, as well as the surface microstructural morphology of the topcoat in EBCs are considered as the directions of research needed.
Coating optimization and its influence on CMAS corrosion behavior
Entropy-stabilized rare-earth silicate solid-solution strategy
In recent years, entropy-stabilized solid-solution technology has been used as a strategy to mediate the properties containing CTEs, thermal conductivities and corrosion resistances of rare-earth silicates. The entropy-stabilized solid-solution is an effective way to reduce thermal conductivity, mediate the CTE, and mitigate hot-corrosion attacks from water vapor and CMAS molten salt. Turcer et al. [Citation87] investigated the high-temperature (1500°C) interactions between polycrystalline ceramics Yb2Si2O7, Yb1.8Y0.2Si2O7, YbYSi2O7, and Y2Si2O7 and three CMAS glass systematically. All the Yb2-xYxSi2O7 solid solutions are pure β-phase. The introduction of Y into Yb site in Yb2Si2O7 encourages the formation of apatite during the corrosion process, which does not form in the case Yb2Si2O7 and is not as extensive as in the case of Y2Si2O7. This eliminates the formation of blister cracks which formed in case of Yb2Si2O7, reducing the microstructural collapse caused by CMAS corrosion. In addition, Sun et al. [Citation88] investigates the CMAS hot-corrosion behavior of a new multi-component β-(Er0.25Tm0.25Yb0.25Lu0.25)2Si2O7 disilicate. Their research demonstrates that the resistance of multi-component (Er0.25Tm0.25Yb0.25Lu0.25)2Si2O7 solid-solution to CMAS at 1500°C is significantly improved than single-component rare-earth disilicate, such as γ-Y2Si2O7, β-Sc2Si2O7, β-Yb2Si2O7 and β-Lu2Si2O7[Citation56,Citation89], as verified by the unconsumed melt and the absence of blister crack, as shown in . The improvement of CMAS resistance is attributed to slow dissolving rate of (Er0.25Tm0.25Yb0.25Lu0.25)2Si2O7 in molten melt through the high entropy stabilization and the enhanced grain boundary stability. Accordingly, solid-solution strategy is a promising way to control the dissolving rate in melt, the reprecipitation in melt and improve the grain boundary stability, which provides a guiding direction of rare-earth silicate materials applying as EBCs to prevent CMAS corrosion.
Figure 13. Low- and high-magnification images of the reaction front in the cross-section of (Er0.25Tm0.25Yb0.25Lu0.25)2Si2O7 after CMAS corrosion at 1500°C for 4 h ((a) and (b)) and 50 h ((c) and (d)). Reproduced with permission from Reference [Citation88], © Elsevier Ltd. 2020.
![Figure 13. Low- and high-magnification images of the reaction front in the cross-section of (Er0.25Tm0.25Yb0.25Lu0.25)2Si2O7 after CMAS corrosion at 1500°C for 4 h ((a) and (b)) and 50 h ((c) and (d)). Reproduced with permission from Reference [Citation88], © Elsevier Ltd. 2020.](/cms/asset/02b2553f-bd66-4363-95db-b6745f5ef62a/thts_a_2019389_f0013_oc.jpg)
Rare-earth silicate composite strategy
Not only the entropy-stabilized solid-solution, but also the rare-earth silicate composite strategy is applied to improve corrosion-resistant properties of EBCs materials[Citation24,Citation90–100]. This strategy can be divided roughly into two types: major rare-earth silicates with other additives of metallic oxides, and mixed silicates composed of rare-earth monosilicate and rare-earth disilicate.
Zhang et al. [Citation90] fabricated a tri-layer structure containing silicon, mullite and Yb2SiO5 by plasma spray-physical vapor deposition (PS-PVD) on SiC/SiC CMC. The Al film deposition on the surface of Yb2SiO5 topcoat facilitates the formation of interface between CMAS and Yb2SiO5 coating in the Al-modified EBCs. Besides hindering the penetration of molten melt by the overlay, CMAS may react with the overlay to generate Yb-Al–Si-O phase with a higher melting point. Simultaneously, Al-modification reduces the formation of non-stoichiometric materials with higher concentrations of anion, cation vacancies and defects, resulting in the lower elementary diffusion of CMAS into the Yb2SiO5 coating, which can be described by the reaction at the interface as Equation (2):
(2)
(2) Nieai et al. [Citation91] fabricated Yb2SiO5/YSZ composite pellets with different amounts of YSZ by pressureless sintering and investigated their CMAS hot-corrosion behavior at 1400°C. A better corrosion resistance to CMAS is attributed to the existence of Yb4Zr3O12 and Ca3ZrSi2O9. The barrier oxide phases such as Ca2Al2SiO7, Ca3ZrSi2O9, and the formation of dense Al5Y3O12 during the dissolution-reprecipitation process reduce the further infiltration of CMAS into pellets.
Wolf et al. [Citation92] developed three kinds of ytterbium silicate mixtures with different Yb2SiO5: Yb2Si2O7 ratios, which possess not only CTEs close to Si-based ceramics, but also excellent CMAS resistances. There exist less cracks in mixtures with increasing the content of Yb2SiO5, meaning lower stress levels, which is due to the small CTE mismatch among the Yb silicates mixtures, the remaining CMAS and the apatite layer formed. The reaction layer in the corroded ytterbium silicate mixture at 1400°C becomes thickened with increasing the content of Yb2SiO5. It’s worth noting that the thicknesses of reaction layer in some Yb silicate mixtures are even less than that in pure Yb2SiO5. Two possible factors are proposed by Wolf et al: (1) the optimization of the interface layer structure, and (2) a dense and continuous reaction layer at the interface due to the initial increased apatite precipitation rate. A high dissolving rate of Yb2Si2O7 increases rapidly the concentration of Yb2O3 at the interface, resulting in a rapid increase of the Yb2O3 concentration up to the threshold value of precipitation, which causes the increased initial apatite precipitation rate. The improved CMAS resistance of mixed phase ytterbium silicate environmental barrier coating was also verified by Webster et al. [Citation98]. They found that adding 20 vol.% Yb2SiO5 to Yb2Si2O7 drastically improves the overall resistance to CMAS infiltration at 1300°C, which is also attributed to the formation of dense and continuous crystallization layer of apatite.
Tailoring the microstructural morphology of coating
Although rarely mentioned in the EBCs, the microstructural morphology of coatings influences the infiltration rate and CMAS resistance significantly. For example, Steinberg et al. [Citation101] fabricated a 7YSZ coating with feathery structures, which endow the coating with a better resistance to erosion and degradation than a normal columnar normal structure. Liu et al. [Citation102] emphasized the outstanding positive effect of the micro-sized island protrusions with nano-sized villous structures in hindering the spreading and penetrating of molten CMAS ashes corrosion on the coating surface. Shan et al. [Citation103] confirmed the importance of tailoring the microstructure of pores (porosity, size, and shape) existing in coatings on mitigating CMAS damage.
In environmental barrier coatings, Poerschke et al. [Citation61] compared the difference in CMAS hot-corrosion behavior between Y2Si2O7 coating and Y2Si2O7 pellet samples. As shown in , the recession depth for the pellets is obviously less than that for the coatings during the initial 10 min corrosion. After that, the recession depth for the pellets is similar than for the coatings after CMAS corrosion for 4 and 24 h. The formed apatite grains in the pellet ample is smaller than that in the coating at each time interval, which formed more vertically aligned. In addition, there remained many apatite grains and large pores in the residual deposit above the reaction layer for the coating sample, which were not formed for the pellet. However, the difference in reaction layer morphology does not determine the overall recession degree. This supports the responsibility of investigating the CMAS hot-corrosion behavior with the dense rare-earth silicate ceramics as the corrosion substrates. However, the influence of microstructural morphology of coating on the CMAS corrosion resistance is still waiting to be further explored, especially the combined infiltration-reaction kinetics of CMAS into rare-earth silicate coatings.
Figure 14. Low- and high-magnification images of the reaction front for (a, c, e) APS YDS and (b, d, f) sintered pellets. The bottom portion of each inset is unreacted material, the lighter phase in the top of the insets is apatite, and darker phase is residual glass. The larger dark globular regions in (a, c, e) are pores. Reproduced with permission from Reference [Citation61], Elsevier 2018.
![Figure 14. Low- and high-magnification images of the reaction front for (a, c, e) APS YDS and (b, d, f) sintered pellets. The bottom portion of each inset is unreacted material, the lighter phase in the top of the insets is apatite, and darker phase is residual glass. The larger dark globular regions in (a, c, e) are pores. Reproduced with permission from Reference [Citation61], Elsevier 2018.](/cms/asset/e1247bed-cd29-4cf2-91ea-826adce8396a/thts_a_2019389_f0014_ob.jpg)
Therefore, solid-solution strategy, composite strategy, and the surface morphology modification are considered as effective strategies to improve the resistance of rare-earth silicates to CMAS hot corrosion as the topcoats in EBCs. The core is to change corrosion reaction thermodynamics to change the equilibrium concentration, form a denser reaction layer, or reduce the growth rate of reaction layer. And simultaneously, the surface morphology modification, which has been provided as an effective way to decrease the infiltration of CMAS in TBCs, may also be introduced in EBCs to delay CMAS corrosion.
Conclusion and outlooks
As one of the most promising materials for environmental barrier coatings, rare-earth silicates possess excellent high-temperature stability, suitable coefficients of thermal expansion, low thermal conductivity, and excellent hot-corrosion resistances to both water vapor and CMAS molten salts.
The composition of CMAS glass determines its CTE, viscosity, melting temperature, and even the sticking temperature, which influences the penetration rate of CMAS glass along grain boundary, thermal stress, and initial melting and sticking behaviors.
CMAS corrosion behaviors of all kinds of rare-earth silicates relates to the dissolution-reprecipitation mechanism, which determines the formation of dominant corrosion product-apatite. The corrosion reactions are different in the CMAS corrosion associated with rare-earth monosilicates and rare-earth disilicates, which mainly corresponds to the consumption or production of SiO2. The production of SiO2 in the CMAS corrosion process of rare-earth disilicates leads to the equilibrium of reactions, where the Ca: Si ratio reaches a fixed value. SiO2 seems not to participate in the CMAS corrosion reaction of rare-earth silicate oxyapatite such as RE9.33Si6O26.
Besides the RE: Si ratio in rare-earth silicates, the type of rare-earth cations also influences the CMAS corrosion behavior. For rare-earth monosilicates, the smaller the radius of rare-earth cation, the smaller the difference between optical basicity of rare-earth silicate and CMAS is, and the lower the thickness of recession layer is. For rare-earth disilicates, some barely react with CMAS to generate apatite, such as Sc2Si2O7 and Yb2Si2O7, while others like Y2Si2O7 possess a high reactivity with CMAS.
The infiltration of CMAS along grain boundaries and microstructural defects also threatens the application of rare-earth silicates as EBC materials since residual thermal stresses occurring during CMAS corrosion due to the CTE mismatch, which may be limited by improving the stability of grain boundary.
Cracks in the environmental barrier coatings arise from the mismatch between CTEs of coating materials and corrosion products or penetrated CMAS glass. These cracks are mostly penetrating cracks which formed during the solidification of CMAS glass, which may terminate within the EBC layer or propagate into the coating underneath, the former of which tends to cause the spallation of EBC.
Different modification strategies of rare-earth silicates as EBCs mainly mediate the CMAS corrosion behavior by influencing the initial formation rate and density of the initial corrosion product layer, as well as strengthening the stability of grain boundaries, which contains the solid-solution strategy, the composite strategy. Tailoring microstructural morphology of coatings is also verified as an effective way to reduce the infiltration of CMAS, however, it is rarely applied in the EBCs.
EBCs usually need specific properties due to its application, containing high-temperature phase stability, CTEs close to the Si-based ceramics, high-temperature phase stability, low thermal conductivity, and nice corrosion resistances under attacks from water vapor and CMAS. Based on the requirements for properties of EBCs, especially the CMAS corrosion resistance, research prospects in the CMAS hot-corrosion behaviors of rare-earth silicates for EBCs are expected as follows: (1) sticking behavior of CMAS droplets on rare-earth silicate coatings; (2) crystallization behavior of apatite during hot corrosion of multi-component rare-earth silicates; (3) synergetic influence of different additives on the formation of corrosion product layer, which hinders the infiltration of CMAS glass; (4) grain boundary (GB) engineering in rare-earth silicates to improve high-temperature stability during thermal cycling; (5) multi-scale modeling of the thermo-mechano-chemical interaction among CMAS molten salt, rare-earth silicates and harsh EBCs environments; (6) high-temperature failure and lifetime prediction of rare-earth silicate EBCs during thermal cycling.
Disclosure statement
No potential conflict of interest was reported by the author(s).
Additional information
Funding
References
- Yu Z, Zhao H, Wadley HNG. The vapor deposition and oxidation of platinum- and yttria-stabilized zirconia multilayers. J Am Ceram Soc. 2011;94(8):2671–2679.
- Clarke DR, Oechsner M, Padture NP. Thermal-barrier coatings for more efficient gas-turbine engines. MRS Bull. 2012 Oct;37(10):891–902.
- Padture NP, Gell M, Jordan EH. Thermal barrier coatings for gas-turbine engine applications. Science. 2002 Apr 12;296(5566):280–284.
- Ohnabe H, Masaki S, Onozuka M, et al. Potential application of ceramic matrix composites to aero-engine components. Compos Part A Appl S. 1999;30(4):489–496.
- Parthasarathy TA., Cox B, Sudre O, Przybyla C, Cinibulk MK. Modeling environmentally induced property degradation of SiC/BN/SiC ceramic matrix composites. J Am Ceram Soc. 2017;101:973–997.
- Jacobson NS. Corrosion of silicon-based ceramics in combustion environments. J Am Ceram Soc. 1993 Jan;76(1):3–28.
- Poerschke DL, Jackson RW, Levi CG. Silicate deposit degradation of engineered coatings in Gas turbines: progress Toward models and materials solutions. Annu Rev Mater Res. 2017;47:297–330.
- Levi CG, Hutchinson JW, Vidal-Setif MH, et al. Environmental degradation of thermal-barrier coatings by molten deposits. MRS Bull. 2012 Oct;37(10):932–941.
- Costa G, Harder BJ, Wiesner VL, et al. Thermodynamics of reaction between gas-turbine ceramic coatings and ingested CMAS corrodents. J Am Ceram Soc. 2019 May;102(5):2948–2964.
- Günthner M, Schütz A, Glatzel U, et al. High performance environmental barrier coatings, Part I: passive filler loaded SiCN system for steel. J Eur Ceram Soc. 2011;31(15):3003–3010.
- Liu J, Zhang L, Liu Q, et al. Polymer-Derived SiOC-barium-strontium aluminosilicate coatings as an environmental barrier for C/SiC composites. J Am Ceram Soc. 2010;93(12):4148–4152.
- Lee KN. Special issue: environmental barrier coatings. Coatings. 2020 Jun;10(6):512.
- Lee KN. Current status of environmental barrier coatings for Si-based ceramics. Surf Coat Tech. 2000 Nov;133:1–7.
- Turcer LR, Padture NP. Towards multifunctional thermal environmental barrier coatings (TEBCs) based on rare-earth pyrosilicate solid-solution ceramics. Scr Mater. 2018;154:111–117.
- Lee KN, Jacobson NS, Miller RA. Refractory oxide coatings on Sic ceramics. MRS Bull. 1994 Oct;19(10):35–38.
- Lee KN. Key durability issues with mullite-based environmental barrier coatings for Si-based ceramics. J Eng Gas Turb Power. 2000 Oct;122(4):632–636.
- Lee KN, Miller RA. Development and environmental durability of mullite and mullite/YSZ dual layer coatings for SiC and Si3N4 ceramics. Surf Coat Technol. 1996 Dec 1;86(1-3):142–148.
- Mesquita-Guimaraes J, Garcia E, Miranzo P, et al. Mullite-YSZ multilayered environmental barrier coatings tested in cycling conditions under water vapor atmosphere. Surf Coat Technol. 2012 Sep 25;209:103–109.
- Lee KN, Fox DS, Eldridge JI, et al. Upper temperature limit of environmental barrier coatings based on mullite and BSAS. J Am Ceram Soc. 2003 Aug;86(8):1299–1306.
- Liu D, Kyaw ST, Flewitt PEJ, et al. Residual stresses in environmental and thermal barrier coatings on curved superalloy substrates: Experimental measurements and modelling. Mat Sci Eng A-Struct. 2014 Jun 12;606:117–126.
- Cojocaru CV, Levesque D, Moreau C, et al. Performance of thermally sprayed Si/mullite/BSAS environmental barrier coatings exposed to thermal cycling in water vapor environment. Surf Coat Technol. 2013 Feb 15;216:215–223.
- Richards BT, Zhao H, Wadley HNG. Structure, composition, and defect control during plasma spray deposition of ytterbium silicate coatings. J Mater Sci. 2015;50(24):7939–7957.
- Xu Y, Hu X, Xu F, et al. Rare earth silicate environmental barrier coatings: present status and prospective. Ceram Int. 2017;43(8):5847–5855.
- Xu Y, Li J. Preparation and molten salt corrosion research of composite environmental barrier coatings of Lu2Si2O7 and Lu2SiO5. Mater Res Innovations. 2014;18(sup4):S4-958–S4-962.
- Zhou Y-C, Zhao C, Wang F, et al. Theoretical prediction and experimental investigation on the thermal and mechanical properties of bulk β-Yb2Si2O7. J Am Ceram Soc. 2013;96(12):3891–3900.
- Xu Y, Yan Z. Investigation on the preparation of Si/mullite/Yb2Si2O7 environmental barrier coatings onto silicon carbide. J Rare Earth. 2010;28(3):399–402.
- Bondar IA. Rare-earth silicates. Ceram Int. 1982;8(3):83–89.
- Tian Z, Zheng L, Wang J, et al. Theoretical and experimental determination of the major thermo-mechanical properties of RE2SiO5 (RE = Tb, Dy, Ho, Er, Tm, Yb, Lu, and Y) for environmental and thermal barrier coating applications. J Eur Ceram Soc. 2016;36(1):189–202.
- Li Y, Wang J, Wang J. Theoretical investigation of phonon contributions to thermal expansion coefficients for rare earth monosilicates RE2SiO5 (RE = Dy, Ho, Er, Tm, Yb and Lu). J Eur Ceram Soc. 2020;40(7):2658–2666.
- Li Y, Luo Y, Tian Z, et al. Theoretical exploration of the abnormal trend in lattice thermal conductivity for monosilicates RE2SiO5 (RE = Dy, Ho, Er, Tm, Yb and Lu). J Eur Ceram Soc. 2018;38(10):3539–3546.
- Sun Z, Li M, Zhou Y. Recent progress on synthesis, multi-scale structure, and properties of Y–Si–O oxides. Int Mater Rev. 2014;59(7):357–383.
- Fujii S, Ioki A, Yokoi T, et al. Role of phonons on phase stabilization of RE2Si2O7 over wide temperature range (RE = Yb, Gd). J Eur Ceram Soc. 2020;40(3):780–788.
- Tian Z, Zheng L, Li Z, et al. Exploration of the low thermal conductivities of γ-Y2Si2O7, β-Y2Si2O7, β-Yb2Si2O7, and β-Lu2Si2O7 as novel environmental barrier coating candidates. J Eur Ceram Soc. 2016;36(11):2813–2823.
- Luo Y, Wang J, Li J, et al. Theoretical study on crystal structures, elastic stiffness, and intrinsic thermal conductivities of β-, γ-, and δ-Y2Si2O7. J Mater Res. 2015;30(4):493–502.
- Fernandez-Carrion AJ, Allix M, Becerro AI. Thermal expansion of rare-earth pyrosilicates. J Am Ceram Soc. 2013 Jul;96(7):2298–2305.
- Wu R, Pan W, Ren X, et al. An extremely low thermal conduction ceramic: RE9.33(SiO4)6O2 silicate oxyapatite. Acta Mater. 2012;60(15):5536–5544.
- Tian C, Liu J, Cai J, et al. Direct synthesis of La9.33Si6O26 ultrafine powder via sol–gel self-combustion method. J Alloys Compd. 2008;458(1-2):378–382.
- Tian Z, Zhang J, Zhang T, et al. Towards thermal barrier coating application for rare earth silicates RE2SiO5 (RE = La, Nd, Sm, Eu, and Gd). J Eur Ceram Soc. 2019;39(4):1463–1476.
- Rodríguez-García MM, Ciric A, Ristic Z, et al. Narrow-band red phosphors of high colour purity based on Eu3+-activated apatite-type Gd9.33(SiO4)6O2. J Mater Chem C. 2021;9(23):7474–7484.
- Qu Z, Sparks TD, Pan W, et al. Thermal conductivity of the gadolinium calcium silicate apatites: effect of different point defect types. Acta Mater. 2011 Jun;59(10):3841–3850.
- Masubuchi Y, Higuchi M, Kodaira K. Reinvestigation of phase relations around the oxyapatite phase in the Nd2O3-SiO2 system. J Cryst Growth. 2003 Jan;247(1-2):207–212.
- Lofaj F, Satet R, Hoffmann MJ, et al. Thermal expansion and glass transition temperature of the rare-earth doped oxynitride glasses. J Eur Ceram Soc. 2004;24(12):3377–3385.
- Becher PF, Waters SB, Westmoreland CG, et al. Compositional Effects on the properties of Si-Al-RE-based oxynitride glasses (RE = La, Nd, Gd, Y, or Lu). J Am Ceram Soc. 2004;85(4):897–902.
- Garcia E, Sotelo-Mazon O, Poblano-Salas CA, et al. Characterization of Yb2Si2O7-Yb2SiO5 composite environmental barrier coatings resultant from in situ plasma spray processing. Ceram Int. 2020 Sep;46(13):21328–21335.
- Lange A, Braun R, Mechnich P, et al. Y2sio5 environmental barrier coatings for niobium silicide based materials. Mater High Temp. 2015 Jan;32(1-2):74–80.
- Maier N, Rixecker G, Nickel KG. Formation and stability of Gd, Y, Yb and Lu disilicates and their solid solutions. J Solid State Chem. 2006 Jun;179(6):1630–1635.
- Wiesner VL, Vempati UK, Bansal NP. High temperature viscosity of calcium-magnesium-aluminosilicate glass from synthetic sand. Scr Mater. 2016;124:189–192.
- Jia R, Deng L, Yun F, et al. Effects of SiO2/CaO ratio on viscosity, structure, and mechanical properties of blast furnace slag glass ceramics. Mater Chem Phys. 2019 May 15;233:155–162.
- Webster RI, Opila EJ. The effect of TiO2 additions on CaO–MgO–Al2O3–SiO2 (CMAS) crystallization behavior from the melt. J Am Ceram Soc. 2018;102(6):3354–3367.
- Song W, Lavallee Y, Wadsworth FB, et al. Wetting and spreading of molten volcanic Ash in Jet engines. J Phys Chem Lett. 2017 Apr 20;8(8):1878–1884.
- Song J, Yang S, Fukumoto M, et al. Impact interaction of in-flight high-energy molten volcanic ash droplets with jet engines. Acta Mater. 2019 Jun 1;171:119–131.
- Li B, Chen Z, Zheng H, et al. Wetting mechanism of CMAS melt on YSZ surface at high temperature: First-principles calculation. Appl Surf Sci. 2019 Jul 31;483:811–818.
- Song W, Lavallee Y, Hess KU, et al. Volcanic ash melting under conditions relevant to ash turbine interactions. Nat Commun. 2016 Mar 2;7:10795.
- Stokes JL, Harder BJ, Wiesner VL, et al. High-Temperature thermochemical interactions of molten silicates with Yb2Si2O7 and Y2Si2O7 environmental barrier coating materials. J Eur Ceram Soc. 2019 Dec;39(15):5059–5067.
- Stokes JL, Harder BJ, Wiesner VL, et al. Effects of crystal structure and cation size on molten silicate reactivity with environmental barrier coating materials. J Am Ceram Soc. 2019;103(1):622–634.
- Liu J, Zhang L, Liu Q, et al. Calcium-magnesium-aluminosilicate corrosion behaviors of rare-earth disilicates at 1400 °C. J Eur Ceram Soc. 2013 Dec;33(15-16):3419–3428.
- Turcer LR, Krause AR, Garces HF, et al. Environmental-barrier coating ceramics for resistance against attack by molten calcia-magnesia-aluminosilicate (CMAS) glass: part II, β-Yb2Si2O7 and β-Sc2Si2O7. J Eur Ceram Soc. 2018;38(11):3914–3924.
- Turcer LR, Krause AR, Garces HF, et al. Environmental-barrier coating ceramics for resistance against attack by molten calcia-magnesia-aluminosilicate (CMAS) glass: part I, YAlO3 and γ-Y2Si2O7. J Eur Ceram Soc. 2018;38(11):3905–3913.
- Wiesner VL, Scales D, Johnson NS, et al. Calcium–magnesium aluminosilicate (CMAS) interactions with ytterbium silicate environmental barrier coating material at elevated temperatures. Ceram Int. 2020;46(10):16733–16742.
- Wiesner VL, Harder BJ, Bansal NP. High-temperature interactions of desert sand CMAS glass with yttrium disilicate environmental barrier coating material. Ceram Int. 2018;44(18):22738–22743.
- Poerschke DL, Shaw JH, Verma N, et al. Interaction of yttrium disilicate environmental barrier coatings with calcium-magnesium-iron alumino-silicate melts. Acta Mater. 2018;145:451–461.
- Zhao H, Richards BT, Levi CG, et al. Molten silicate reactions with plasma sprayed ytterbium silicate coatings. Surf Coat Technol. 2016;288:151–162.
- Grant KM, Kramer S, Seward GGE, et al. Calcium-Magnesium alumino-silicate interaction with Yttrium Monosilicate environmental barrier coatings. J Am Ceram Soc. 2010 Oct;93(10):3504–3511.
- Ahlborg NL, Zhu D. Calcium–magnesium aluminosilicate (CMAS) reactions and degradation mechanisms of advanced environmental barrier coatings. Surf Coat Technol. 2013;237:79–87.
- Jang B-K, Feng F-J, Suzuta K, et al. Corrosion behavior of volcanic ash and calcium magnesium aluminosilicate on Yb2SiO5 environmental barrier coatings. J Ceram Soc Jpn. 2017;125(4):326–332.
- Poerschke DL, Barth TL, Fabrichnaya O, et al. Phase equilibria and crystal chemistry in the calcia-silica-yttria system. J Eur Ceram Soc. 2016 Jun;36(7):1743–1754.
- Tian Z, Zhang J, Zheng L, et al. General trend on the phase stability and corrosion resistance of rare earth monosilicates to molten calcium magnesium aluminosilicate at 1300 degrees C. Corros Sci. 2019 Mar;148:281–292.
- Jiang FR, Cheng LF, Wang YG. Hot corrosion of RE2SiO5 with different cation substitution under calcium-magnesium- aluminosilicate attack. Ceram Int. 2017 Aug 15;43(12):9019–9023.
- Kim SH, Kim BN, Nagashima N, et al. High-temperature corrosion of spark plasma sintered Gd2SiO5 with volcanic ash for environmental barrier coatings. J Eur Ceram Soc. 2021 May;41(5):3161–3166.
- Poerschke DL, Hass DD, Eustis S, et al. Stability and CMAS resistance of ytterbium-silicate/hafnate EBCs/TBC for SiC composites. J Am Ceram Soc. 2015;98(1):278–286.
- Sleeper J, Garg A, Wiesner VL, et al. Thermochemical interactions between CMAS and Ca2Y8(SiO4)6O2 apatite environmental barrier coating material. J Eur Ceram Soc. 2019;39(16):5380–5390.
- Zhang H, Lu J, Shan X, et al. A promising molten silicate resistant material: rare-earth oxy-apatite RE9.33(SiO4)6O2 (RE = Gd, Nd or La). J Eur Ceram Soc. 2020;40(12):4101–4110.
- Costa G, Harder BJ, Bansal NP, et al. Thermochemistry of calcium rare-earth silicate oxyapatites. J Am Ceram Soc. 2019;103(2):1446–1453.
- Goddio F, von Bomhard AS, Grataloup CC. Thonis-Heracleion: memory and reflections of the saite history. J Egypt Archaeol. 2020 Jun;106(1-2):171–186.
- Jang B-K, Nagashima N, Kim S, et al. Mechanical properties and microstructure of Yb2SiO5 environmental barrier coatings under isothermal heat treatment. J Eur Ceram Soc. 2020;40(7):2667–2673.
- Zhong X, Zhu T, Niu Y, et al. Effect of microstructure evolution and crystal structure on thermal properties for plasma-sprayed RE2SiO5 (RE = Gd, Y, Er) environmental barrier coatings. J Mater Sci Technol. 2021;85:141–151.
- Hu X, Xu F, Li K, et al. Water vapor corrosion behavior and failure mechanism of plasma sprayed mullite/Lu2Si2O7-Lu2SiO5 coatings. Ceram Int. 2018;44(12):14177–14185.
- Lv B, Qu Z, Xu B, et al. Water vapor volatilization and oxidation induced surface cracking of environmental barrier coating systems: A numerical approach. Ceram Int. 2021;47(12):16547–16554.
- Chen D, Harmon R, Dwivedi G, et al. In-flight particle states and coating properties of air plasma sprayed ytterbium disilicates. Surf Coat Technol. 2021;417:127186.
- Richards BT, Young KA, de Francqueville F, et al. Response of ytterbium disilicate–silicon environmental barrier coatings to thermal cycling in water vapor. Acta Mater. 2016;106:1–14.
- Lu Y, Wang Y. Formation and growth of silica layer beneath environmental barrier coatings under water-vapor environment. J Alloys Compd. 2018;739:817–826.
- Nieto A, Walock M, Ghoshal A, et al. Layered, composite, and doped thermal barrier coatings exposed to sand laden flows within a gas turbine engine: Microstructural evolution, mechanical properties, and CMAS deposition. Surf Coat Technol. 2018 Sep 15;349:1107–1116.
- Harder BJ, Ramirez-Rico J, Almer JD, et al. Chemical and mechanical consequences of environmental barrier coating exposure to calcium-magnesium-aluminosilicate. J Am Ceram Soc. 2011 Jun;94:S178–S185.
- Summers WD, Poerschke DL, Begley MR, et al. A computational modeling framework for reaction and failure of environmental barrier coatings under silicate deposits. J Am Ceram Soc. 2020;103(9):5196.
- Stolzenburg F, Kenesei P, Almer J, et al. The influence of calcium–magnesium–aluminosilicate deposits on internal stresses in Yb2Si2O7 multilayer environmental barrier coatings. Acta Mater. 2016;105:189–198.
- Cai Z, Hong H, Peng D, et al. Stress evolution in ceramic top coat of air plasma-sprayed thermal barrier coatings due to CMAS penetration under thermal cycle loading. Surf Coat Technol. 2020;381:125146.
- Turcer LR, Padture NP. Rare-earth pyrosilicate solid-solution environmental-barrier coating ceramics for resistance against attack by molten calcia–magnesia–aluminosilicate (CMAS) glass. J Mater Res. 2020;35(17):2373–2384.
- Sun L, Luo Y, Tian Z, et al. High temperature corrosion of (Er0.25Tm0.25Yb0.25Lu0.25)2Si2O7 environmental barrier coating material subjected to water vapor and molten calcium–magnesium–aluminosilicate (CMAS). Corros Sci. 2020;175:108881.
- Tian Z, Ren X, Lei Y, et al. Corrosion of RE2Si2O7 (RE = Y, Yb, and Lu) environmental barrier coating materials by molten calcium-magnesium-alumino-silicate glass at high temperatures. J Eur Ceram Soc. 2019;39(14):4245–4254.
- Zhang X, Zhou K, Liu M, et al. CMAS corrosion and thermal cycle of Al-modified PS-PVD environmental barrier coating. Ceram Int. 2018;44(13):15959–15964.
- Nieai AA, Mohammadi M, Shojaie-Bahaabad M. Hot corrosion behavior of calcium magnesium aluminosilicate (CMAS) on the Yb2SiO5-8YSZ composite as a candidate for environmental barrier coatings. Mater Chem Phys. 2020 Mar 1;243:122596.
- Wolf M, Mack DE, Guillon O, et al. Resistance of pure and mixed rare earth silicates against calcium-magnesium-aluminosilicate (CMAS): A comparative study. J Am Ceram Soc. 2020;103(12):7056–7071.
- Darthout É, Quet A, Braidy N, et al. Lu2O3-SiO2-ZrO2 coatings for environmental barrier application by solution Precursor plasma spraying and influence of Precursor chemistry. J Therm Spray Technol. 2013;23(3):325–332.
- Boakye EE, Mogilevsky P, Parthasarathy TA, et al. Processing and testing of RE2Si2O7 fiber-matrix interphases for SiC-SiC composites. J Am Ceram Soc. 2016 Feb;99(2):415–423.
- Vu HD, Nanko M. Crack-Healing behavior and mechanical strength recovery of 5 vol% silicon carbide particle dispersed Yttrium Monosilicate composites. Mater Trans. 2019;60(1):149–155.
- Feng F-J, Jang B-K, Park JY, et al. Effect of Yb2SiO5 addition on the physical and mechanical properties of sintered mullite ceramic as an environmental barrier coating material. Ceram Int. 2016;42(14):15203–15208.
- Darthout É, Gitzhofer F. Structure stabilization by zirconia pinning effect of Y2Si2O7 environmental barrier coatings synthesized by solution precursor plasma spraying process. Surf Coat Technol. 2017;309:1081–1088.
- Webster RI, Opila EJ. Mixed phase ytterbium silicate environmental-barrier coating materials for improved calcium-magnesium-alumino-silicate resistance. J Mater Res. 2020 Sep 14;35(17):2358–2372.
- Nguyen ST, Nakayama T, Suematsu H, et al. Self-healing behavior and strength recovery of ytterbium disilicate ceramic reinforced with silicon carbide nanofillers. J Eur Ceram Soc. 2019;39(10):3139–3152.
- Nguyen ST, Nakayama T, Suematsu H, et al. Strength improvement and purification of Yb2Si2O7-SiC nanocomposites by surface oxidation treatment. J Am Ceram Soc. 2017 Jul;100(7):3122–3131.
- Steinberg L, Naraparaju R, Heckert M, et al. Erosion behavior of EB-PVD 7YSZ coatings under corrosion/erosion regime: effect of TBC microstructure and the CMAS chemistry. J Eur Ceram Soc. 2018 Dec;38(15):5101–5112.
- Liu SH, Ji G, Li CJ, et al. Novel long laminar plasma sprayed hybrid structure thermal barrier coatings for high-temperature anti-sintering and volcanic ash corrosion resistance. J Mater Sci Technol. 2021 Jul 20;79:141–146.
- Shan X, Chen WF, Yang LX, et al. Pore filling behavior of air plasma spray thermal barrier coatings under CMAS attack. Corros Sci. 2020 May 1;167:108478.