ABSTRACT
High entropy alloys have excellent thermal stability due to its sluggish diffusion effect. Here, we investigated the phase, microstructural and strength stabilities of FeCrNiTiAl alloy. Results show that as-cast alloy exhibits dendrite, interdendrite and eutectic microstructures. No new phase is detected after aging at 800–1100°C for 144 h, while a small change in the phase content of Laves phase is observed. After exposure at high temperature, the alloy maintains the petal-like morphology, and a small extent of grain coarsening is observed. As compared to the as-cast condition, the relative content of each element remains unchanged. A small decrease in the microhardness can be observed after exposure. But there is no variation in microhardness after exposure for 72 h. These results demonstrate the excellent thermal stabilities of FeCrNiTiAl alloy.
Introduction
High entropy alloys (HEAs) have been developed recently, which provide a new strategy to design novel alloys [Citation1]. The high entropy and sluggish diffusion effect in kinetics in HEAs leads to simple body-centered or face-centered structure, which is different from traditional alloys where many intermetallics appear generally. HEAs exhibit high hardness and strength, excellent creep-resistance and oxidation-resistance at high temperature, good wear-resisting property and good corrosion resisting property [Citation2–5]. Therefore, the studies on high entropy alloy are of theoretical and engineering importance. HEAs are promising materials at high temperatures [Citation6–8]. Apart from heat resistance, the HEAs components servicing at high temperature also demand excellent thermal stability in order to avoid failures. Therefore, the study of thermal stability is very important to evaluate service safety for HEAs components. FeCrNiTiAl HEAs offer a low cost that is resulted from the application of Fe element and show a good application prospect [Citation9,Citation10].
There are several main component alloy composition characteristics in HEAs [Citation11–14]. The typical one is numerous compositions. Another one is sluggish diffusion effect. The diffusion of atoms in the HEAs matrix is much more difficult than in the traditional alloy matrix [Citation15,Citation16]. It has already been reported [Citation17,Citation18] that sluggish diffusion would affect the phase nucleation, growth and distribution, and morphology of new phase through diffusion-controlled phase transformation. Due to the sluggish diffusion effect the alloy has excellent thermal stability. Besides, two phases HEAs show a better performance in thermal stability [Citation19–21]. However, a systemically deep investigation on the thermal stability of FeCrNiTiAl alloy is needed [Citation10,Citation22,Citation23]. The objective of this paper is to evaluate the high temperature stability of FeCrNiTiAl alloy and examine the phase, microstructure and mechanical properties after high temperature exposure systemically. FeCrNiTiAl shows a good performance in both structure stability and mechanical properties stability. After aging at 800–1100°C for 144 h, only a small change in the phase content of Laves phase is observed. After aging at high temperature, the alloy maintains the petal-like morphology. A small decrease in the microhardness can be observed. But there is no variation in microhardness after exposure for 72 h. These results demonstrate the excellent thermal stabilities of FeCrNiTiAl.
Materials and methods
FeCrNiTiAl alloy was obtained by vacuum melting. The mole ratio of Fe, Cr, Ni, Ti, Al in this alloy is 1:1:1:1:1. The samples were taken from as-cast ingots followed by soaking at 800°C, 900°C, 1000°C and 1100°C in the atmosphere for 24, 48, 72 and 144 h, respectively. Subsequently, the microstructure was characterized by a FEI Quanta-400F scanning electron microscope (SEM) operated at back-scatter electron (BSE) mode. The chemical compositions were analyzed by an energy dispersive spectrometry (EDS). The samples were also analyzed by X-ray diffraction (XRD, Rigaku D8 Advance) using Cu Ka radiation (k = 0.15406 nm) at a scanning grate of 4°/min within a 2θ range of 20–100° to determine the phase constitution. And the microstructures were also examined by field emission scanning electron microscopy (FESEM, QUANTA FEG250), and transmission electron microscopy (TEM, FEI Tecnai G2) coupled with selected area electron diffraction (SAED). To gain an insight into the effect of high temperature exposure on mechanical properties, micro-hardness test (HXS-1000AK) was performed for the specimen suffering from high temperature exposure. 5 points are tested in different areas of samples in different states of the alloy, and the average value is taken to characterize the hardness value of the alloy in different states. In the microhardness test, the test load is selected as 0.1 kg.
Results and discussion
As-cast microstructure
shows the as-cast microstructure of FeCrNiTiAl. One can see the dendrite microstructure from (b), which is composed of the dendrite (A), interdendrite (B) and eutectic microstructures(C). Different from the tree-like dendrite in the traditional alloy, this alloy exhibits a petal-like microstructure composed of dendrite and interdendrite microstructure. In fact, the petal-like microstructure is a special dendrite microstructure. It can result from elastic anisotropy [Citation24]. The preferred orientation growth of grains is inhibited due to elastic anisotropy. Thus, the whole dendrite bifurcation is obvious, which makes the morphology of dendrites change from ‘dendritic’ to ‘petal’. The EDS analysis on regions A, B and C are shown in , showing that the Cr element prefers to aggregate in interdendrite (BCC2), while Ni and Al prefer to be distributed in dendrite (BCC1). The composition of the eutectic microstructure shows an approximately average value of the dendrite and interdendrite.
Figure 1. As-cast microstructure in FeCrNiTiAl alloy shown by metallograph (a) and secondary electron image (b).
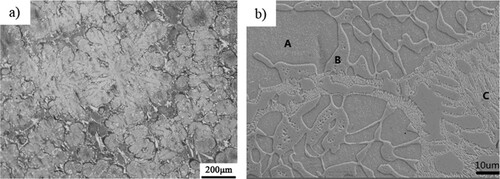
Table 1. Element distributions in as-cast alloy (atom%).
The XRD patterns of as-cast alloy are shown in . Two body-centered cubic structures are identified, in which BCC1 shows a cell parameter of 2.9533 Å and BCC2 shows a cell parameter of 2.9250 Å. And splitting of diffraction peaks at 2θ of 44° and 97° appear.
(a) shows the TEM bright field image of the as cast dendrite of the alloy. As shown in (b), the energy spectrum analysis shows that region A is the region rich in Ni and region B is the region rich in Cr. Combined with the previous energy spectrum analysis, region A corresponds to the structure in dendrite and region B corresponds to the structure in interdendrite. (c,d) shows the selected electron diffraction patterns corresponding to regions A and B. It can be both dendrite and interdendrite are body centered cubic structures, and the results are consistent with the XRD results.
The thermal stability
The phases of specimens that suffered from high-temperature exposure at 800°C, 900°C, 1000°C and 1100°C for 24, 48, 72 and 144 h were identified by XRD. One can see from that the specimen suffered from high-temperature exposure shows a change in the position of the peak with the highest intensity compared with the origin one. This change of intensity may be caused by the change of preferred orientation after aging at 900°C [Citation25,Citation26]. Apart from this, a new peak appears at 2θ of 40°, suggesting that a small amount of Laves phases will precipitate during the aging process. Laves phases in our alloy is composed of L21 and C14 phases. L21 phase is composed mainly of Ni, Fe, Ti and Al. And, C14 phase is composed mainly of Cr, Fe and Ti. We concluded these two phases into Laves phase for their similar influence on this alloy. And the alloy will show a stronger intensity in this new peak at 1000°C than that at 800°C and 900°C. But when the aging temperature increases to 1100°C, XRD analysis shows the same results as those of as-cast, which indicates that no Laves phase appears. This can be explained that Laves phase can be produced at the temperature lower than 1050°C. At the same time, one can see that the precipitation of Laves phase is an atom diffusion-controlled process, and obeys Arrhenius law. Atom diffusion rate can be thought of as an exponential function of temperature, and a parabolic function of diffusion time. Thus, aging temperature shows a more obvious impact on precipitation amount than the aging time. The results can be confirmed by the XRD analysis shown in . It can be seen that the relative intensities of diffraction peaks show small changes with increasing aging time, but larger changes with increasing aging temperature.
Figure 4. XRD analysis results at various aging temperature and time at (a) 800°C, (b) 900°C, (c) 1000°C and (d) 1100°C.
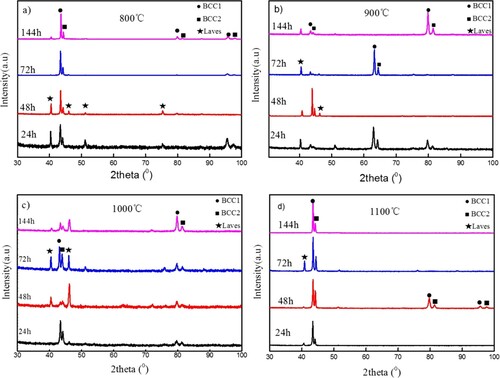
In a word, the aging at 800–1100°C for a long time 144 h does not produces new phase, while only results in a small change in Lavas phase content, suggesting that the HEAs phase at high temperature is relative stable.
The Metallography microstructures after aging at 800–1100°C are shown in and . Point EDS analysis is performed at some temperatures for 144 h. It can be seen that the morphology does not change during aging at high temperatures for a long time, and the petal-like morphology of dendrite remains unchanged. Grains will grow with a small degree, but the growing degree tendency is weak. This can be attributed to the sluggish effects due to the large crystal distortion and many kinds of alloying constitutes. This sluggish effect results in a small grain growth rate.
Figure 5. Metallographic microstructures after aging at 800°C, 900°C for (a) 800°C – 24 h, (b) 800°C – 48 h, (c) 800°C – 72 h, (d) 800°C – 144 h, (e) 900°C – 24 h, (f) 900°C – 48 h, (g) 900°C – 72 h and (h) 900°C – 144 h, respectively.

Figure 6. Metallographic microstructures after aging at (a) 1000°C for 24 h, (b) 1000°C for 48 h, (c) 1000°C for 72 h, (d) 1000°C for 144 h, (e) 1100°C for 24 h, (f) 1100°C for 48 h, (g) 1100°C for 72 h and (h) 1100°C – 144 h, respectively.
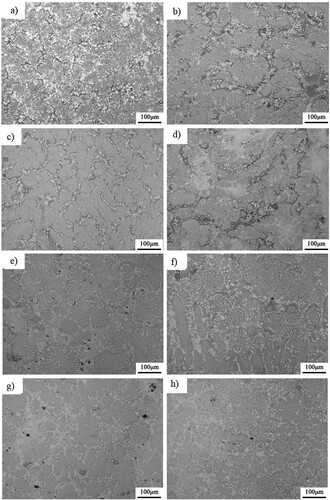
lists compositions distributions of alloy elements at various heat treatment (800–1100°C) for 144 h of regions marked by numbers in . One can see that there are no changes in the relative contents of all alloying elements in dendrite and interdendrite. These results suggest that the diffusion of alloying elements between BCC1 and BCC2 solute is difficult. Therefore, the microstructure of this alloy exhibits good thermal stability.
Figure 7. SEM images of FeCrNiTiAl alloy after aging at (a) 800°C for 144 h, (b) 900°C for 144 h, (c) 1000°C for 144 h, (d) 1100°C – 144 h, respectively. The compositions distribution of regions marked by numbers is listed in .
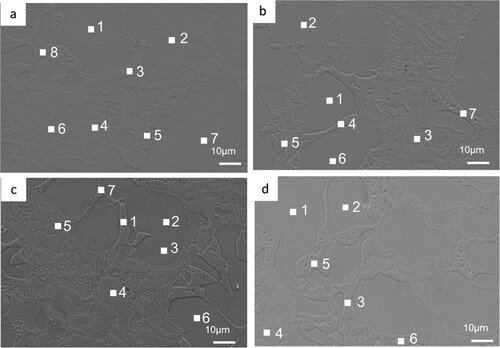
Table 2. Distributions of alloying elements at various heat treatment (at%) of regions marked by numbers in .
A Micro-hardness test was performed on the specimens treated at 800, 900, 1000 and 1100°C for various times. The load was selected to be 0.1 kg. gives hardness value curves with correlated aging times. It can be seen that the micro-hardness decreases with increasing aging time and tends to a stable value after an aging time of 72 h. The alloy exhibits a value of 500 HV in micro-hardness at an aging time of 144 h, only showing a decrease of 30 HV than 530 HV of as-casting alloy. The hardness at 1000°C shows a sharp decrease within 48 h, then varies slightly after holding for 48 h. It will reach 446 HV when the alloy is aged for 144 h. This is because there are more and more Laves precipitation in the alloy at 1000°C, which reduces the elastic internal stress of the dendrite structure, and then the hardness value of the alloy decreases significantly. Therefore, one can see that although the hardness after aging at various temperatures will decrease slightly compared with as-cast microstructure, it remains almost unchanged after aging for 72 h, suggesting that this alloy exhibits high stability in hardness. Hardness is proportional to strength generally. Thus, this HEA shows excellent thermal stability.
Conclusions
As-cast FeCrNiTiAl alloy exhibits dendrite, dendrite, interdendrite and eutectic microstructures.
Aging at 800–1100°C for 144 h cannot produce new phase, but results in the change in Laves phase content.
The alloy shows typical petal-like morphology after aging at high temperature, and grains grow at a certain extent, but the growing tendency is not obvious.
Although the hardness of aging alloy will decrease compared with that of as-cast structure, it remains unchanged when the aging time is longer than 72 h.
Disclosure statement
No potential conflict of interest was reported by the author(s).
Additional information
Funding
References
- Zhang Y, Qiao J-W, Liaw PK. A brief review of high entropy alloys and serration behavior and flow units. J Iron Steel Res Int. 2016 Jan;23(1):2–6. doi:https://doi.org/10.1016/S1006-706X(16)30002-4. PubMed PMID: WOS:000373035000002.
- Nong Z-S, Zhu J-C, Yu H-L, et al. First principles calculation of intermetallic compounds in FeTiCoNiVCrMnCuAl system high entropy alloy. Trans Nonferr Metals Soc China. 2012 Jun;22(6):1437–1444. doi:https://doi.org/10.1016/S1003-6326(11)61338-1. PubMed PMID: WOS:000306275100026.
- Li B-Y, Peng K, Hu A-P, et al. Structure and properties of FeCoNiCrCu0.5Alx, high-entropy alloy. Trans Nonferr Metals Soc China. 2013 Mar;23(3):735–741. doi:https://doi.org/10.1016/S1003-6326(13)62523-6. PubMed PMID: WOS:000324003100023.
- Lee C-F, Shun T-T. Effect of Fe content on microstructure and mechanical properties of Al0.5CoCrFexNiTi0.5 high-entropy alloys. Mater Charact. 2016 Apr;114:179–184. doi:https://doi.org/10.1016/j.matchar.2016.02.018. PubMed PMID: WOS:000374602300021.
- Sriharitha R, Murty BS, Kottada RS. Alloying, thermal stability and strengthening in spark plasma sintered AlxCoCrCuFeNi high entropy alloys. J Alloys Compd. 2014 Jan 15;583:419–426. doi:https://doi.org/10.1016/j.jallcom.2013.08.176. PubMed PMID: WOS:000326035200072.
- Liu Y-X, Cheng C-Q, Shang J-L, et al. Oxidation behavior of high-entropy alloys AlxCoCrFeNi (x = 0.15, 0.4) in supercritical water and comparison with HR3C steel. Trans Nonferr Metals Soc China. 2015 Apr;25(4):1341–1351. doi:https://doi.org/10.1016/S1003-6326(15)63733-5. PubMed PMID: WOS:000354034600040.
- Chen Q-S, Lu Y-P, Dong Y, et al. Effect of minor B addition on microstructure and properties of AlCoCrFeNi multi-compenent alloy. Trans Nonferr Metals Soc China. 2015 Sep;25(9):2958–2964. doi:https://doi.org/10.1016/S1003-6326(15)63922-X. PubMed PMID: WOS:000361883800016.
- Li J, Jia W, Wang J, et al. Enhanced mechanical properties of a CoCrFeNi high entropy alloy by supercooling method. Mater Des. 2016 Apr 5;95:183–187. doi:https://doi.org/10.1016/j.matdes.2016.01.112. PubMed PMID: WOS:000371295200021.
- Tang Z, Senkov ON, Parish CM, et al. Tensile ductility of an AlCoCrFeNi multi-phase high-entropy alloy through hot isostatic pressing (HIP) and homogenization. Mater Sci Eng A. 2015;647:229–240. doi:https://doi.org/10.1016/j.msea.2015.08.078.
- Lin C-M, Tsai H-L. Evolution of microstructure, hardness, and corrosion properties of high-entropy Al0.5CoCrFeNi alloy. Intermetallics. 2011;19(3):288–294. doi:https://doi.org/10.1016/j.intermet.2010.10.008.
- George EP, Raabe D, Ritchie RO. High-entropy alloys. Nat Rev Mater. 2019;4(8):515–534. doi:https://doi.org/10.1038/s41578-019-0121-4.
- Wang F, Inoue A, Kong FL, et al. Formation, thermal stability and mechanical properties of high entropy (Fe,Co,Ni,Cr,Mo)-B amorphous alloys. J Alloys Compd. 2018;732:637–645. doi:https://doi.org/10.1016/j.jallcom.2017.10.227.
- Laplanche G, Bonneville J, Varvenne C, et al. Thermal activation parameters of plastic flow reveal deformation mechanisms in the CrMnFeCoNi high-entropy alloy. Acta Mater. 2018;143:257–264. doi:https://doi.org/10.1016/j.actamat.2017.10.014.
- Li D, Li C, Feng T, et al. High-entropy Al0.3CoCrFeNi alloy fibers with high tensile strength and ductility at ambient and cryogenic temperatures. Acta Mater. 2017;123:285–294. doi:https://doi.org/10.1016/j.actamat.2016.10.038.
- Murty BS, Yeh JW, Ranganathan S, et al. High-entropy alloys. 2nd ed. Murty BS, Yeh JW, Ranganathan S, et al., editors. Amsterdam: Elsevier; 2019.
- Miracle DB, Senkov ON. A critical review of high entropy alloys and related concepts. Acta Mater. 2017 Jan 1;122:448–511. doi:https://doi.org/10.1016/j.actamat.2016.08.081. PubMed PMID: WOS:000389556300043; English.
- Liu WH, Wu Y, He JY, et al. Grain growth and the Hall–Petch relationship in a high-entropy FeCrNiCoMn alloy. Scr Mater. 2013;68(7):526–529. doi:https://doi.org/10.1016/j.scriptamat.2012.12.002.
- Tsai KY, Tsai MH, Yeh JW. Sluggish diffusion in Co–Cr–Fe–Mn–Ni high-entropy alloys. Acta Mater. 2013;61(13):4887–4897. doi:https://doi.org/10.1016/j.actamat.2013.04.058.
- Yang D, Liu Y, Jiang H, et al. A novel FeCrNiAlTi-based high entropy alloy strengthened by refined grains. J Alloys Compd. 2020;823. doi:https://doi.org/10.1016/j.jallcom.2020.153729.
- Yang DN, Liu Y, Qu N, et al. Effect of fabrication methods on microstructures, mechanical properties and strengthening mechanisms of Fe0.25CrNiAl medium-entropy alloy. J Alloys Compd. 2021 Dec 25;888. doi:https://doi.org/10.1016/j.jallcom.2021.161526. PubMed PMID: WOS:000704828000004; English.
- Han T, Liu Y, Liao M, et al. Refined microstructure and enhanced mechanical properties of AlCrFe2Ni2 medium entropy alloy produced via laser remelting. J Mater Sci Technol. 2022;99:18–27. doi:https://doi.org/10.1016/j.jmst.2021.05.033.
- Tang Z, Senkov ON, Parish CM, et al. Tensile ductility of an AlCoCrFeNi multi-phase high-entropy alloy through hot isostatic pressing (HIP) and homogenization. Mater Sci Eng A Struct Mater Prop Microst Proces. 2015 Oct 28;647:229–240. doi:https://doi.org/10.1016/j.msea.2015.08.078. PubMed PMID: WOS:000364250100029.
- Butler TM, Weaver ML. Oxidation behavior of arc melted AlCoCrFeNi multi-component high-entropy alloys. J Alloys Compd. 2016 Jul 25;674:229–244. doi:https://doi.org/10.1016/j.jallcom.2016.02.257. PubMed PMID: WOS:000373612500033.
- Biner SB. Programming phase-field modeling. Cham: Springer International Publishing; 2017.
- Reiberg M, Duan C, Li X, et al. High-temperature phase characterization of AlCrFeNiTi compositionally complex alloys. Mater Chem Phys. 2022;275. doi:https://doi.org/10.1016/j.matchemphys.2021.125272.
- Wolff-Goodrich S, Marshal A, Pradeep KG, et al. Combinatorial exploration of B2/L21 precipitation strengthened AlCrFeNiTi compositionally complex alloys. J Alloys Compd. 2021;853. doi:https://doi.org/10.1016/j.jallcom.2020.156111.