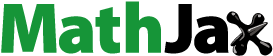
ABSTRACT
Three anaerobic reactors for treating starch wastewater as the Anaerobic Digester (AD), Up-flow Anaerobic Sludge Blanket (UASB) reactor, and Internal Circulation (IC) reactor, were assessed in terms of energy supply and economic factors pertaining to biogas production. For all three reactors, more than 90% of heat loss was derived from the substrate heating loss. When the Chemical Oxygen Demand (COD) of wastewater exceeded 15,000mg/L, the UASB and IC reactors produced excess energy and achieved an economic surplus throughout the year. The UASB and IC reactors reached energy equilibrium throughout the year when the influent COD was 11,195.44mg/L, and 9,844.67mg/L, respectively. The economic equilibrium of the UASB and IC reactors was achieved for influent COD of 12,984mg/L and 11,561mg/L, respectively. The energy and economic equilibria of the AD could not be achieved throughout the year with influent COD concentrations ranging from 5,000mg/L to 20,000mg/L.
1. Introduction
In China, starches are widely used in the food industry as an ingredient in processed products. Annual starch production has increased to more than 10 million t, generating approximately 60 million m3 of starch wastewater from approximately 600 starch production plants [Citation1,Citation2]. Anaerobic biological treatment is a suitable technology for treating starch wastewater and can generate a large amount of biogas [Citation3]. Anaerobic digestion is a complex process carried out by many different microorganisms and consists of four sequential steps: hydrolysis, acidogenesis, acetogenesis, and methanogenesis [Citation4]. It is generally advantageous for removing organic matter from wastewater because of its high efficiency and low environmental impact [Citation5]. However, the initial hydrolysis rate of sludge is highly sensitive to temperature. Research has shown that methanogenic bacteria could be generated at a temperature of approximately 35°C; however, when the temperature decreased from 35°C to 15°C, COD removal efficiency decreased by 32% [Citation6,Citation7]. To maintain a suitable temperature, anaerobic reactors thus need to be heated, especially in the cold season. Therefore, it is very important to calculate and evaluate the energy efficiency and economic cost of heating different types of anaerobic reactors before constructing the wastewater treatment plant.
Three generations of anaerobic reactors exist for wastewater treatment. The Anaerobic Digester (AD) is a typical first-generation reactor, which has a low organic loading rate system that uses completely mixed wastewater and anaerobic sludge [Citation8]. The Up-flow Anaerobic Sludge Blanket (UASB) reactor is a typical second-generation anaerobic reactor, which can maintain a large amount of activated sludge, sufficient sludge age, and high organic load [Citation9]. The Internal Circulation (IC) reactor is a typical third-generation anaerobic reactor, which can process fully mixed wastewater and activated sludge [Citation10]. The IC reactor maintains a large amount of sludge to achieve high efficiency. Various studies have focused on the energy requirements and losses of the AD and UASB reactors. G. Gebremedhin, Wu, Gooch, Wright and Inglis [Citation11] developed a fundamental but comprehensive mathematical model for predicting the energy requirements to operate a UASB digester at a specified temperature. The model accounts for heat loss/gain by influent and effluent flows, the digester floor, the top-covering material and walls, and frozen ground surrounding the digester walls. Their results showed a total heat loss of 10.15 × 106 kJ on January 20th and 3.973 × 106 kJ on June 20th. A dynamic energy balance model was applied to evaluate the energy balance of a pilot AD [Citation12].
The anaerobic reactor not only demands energy, but also supplies it. It can transform organic matter from wastewater into biogas (namely, renewable energy) [Citation12–Citation14]. Many factors, including influent wastewater COD concentration, Hydraulic Retention Time (HRT), influent wastewater temperature, and reactor temperature, can influence biogas production in anaerobic reactors [Citation15–Citation17]. The maximum methane yield of 155 mL CH4/g-COD was obtained for stillage mixtures with 25% (v/v) water in the feed and at an Organic Loading Rate (OLR) of 17.1 g-COD/(L.d) [Citation18]. The methane concentration of the biogas ranged from 50% to 75% [Citation19–Citation21].
Many studies have reported on ways to heat anaerobic reactors [Citation12,Citation22,Citation23]. Lübken, Wichern, Schlattmann, Gronauer and Horn used a combined heat and power (CHP) unit to produce electrical and thermal energy from biogas; the former was used to pump and stir, while the latter was used to offset the heat loss from the reactor [Citation12]. However, the net energy yield and energy efficiency of the three generations of anaerobic reactors used to treat starch wastewater remain unclear. The feasibility of an air source heat pump (ASHP) was investigated for an urban anaerobic digestion process. Modern ASHP manufacturers claim to achieve a coefficient of performance (COP) of 4–5 with an outdoor temperature as low as 5–7°C and a hot water temperature of 35°C at the discharge point [Citation22].
Anhui Province is the main production area of sweet potato starch in China. It produces as much as about 40% of the country’s sweet potato starch. The planting area for sweet potatoes in the province is 0.67 million hm2, and about 300 million ton of starch wastewater is generated each year. Local river water is seriously polluted by the starch wastewater; for example, the COD of the Liu ditch is known to reach values as high as 364 mg/L in winter of 2016, while that of Wulihu ditch was 650 mg/L, and most of the aquatic organisms in river were dead due to lack of dissolved oxygen.
Continued research on anaerobic treatment technologies that can effectively treat starch wastewater, protect the environment, and even produce biogas, which can be used as fuel or heating purposes. Notably, only a few studies have focused on energy loss and demand for heating IC reactors. Moreover, there are no comparative studies of the energy requirements and losses for the AD, UASB, and IC reactors treating the same amount of starch wastewater or wastewater with similar characteristics. Therefore, this study analyses the treatment needs of a starch production plant, which generates about 500 t/d of starch wastewater. In order to evaluate the annual energy consumption of this proposed anaerobic treatment plant, an energy balance model was set up to assess the energy demand and cost input for three generations of anaerobic reactors, namely, the AD, UASB, and IC reactors.
2. Materials and methods
2.1. The starch processing plant
The starch processing plant in this study is located in Fuyang City, Anhui Province of China, and produces about 500 t/d of starch wastewater from starch processing. AD, UASB and IC reactor will be selected to treat the starch wastewater, the COD concentration of which fluctuates between 5,000 and 20,000 mg/L. The operation parameters of the three anaerobic reactors are listed in according to the volume of wastewater generated (500 t/d). The tanks of the reactors are made of anti-corrosion carbon steel and insulated by polyurethane spray foam, which provides a uniform covering without seams and results in low heat loss. According to the water quality requirements for the treatment of the project, the HRT is set to be 64 h, 23 h, and 5 h for the AD, UASB and the IC reactors, respectively. These reactors were operated under mesophilic conditions at 35°C, and the COD removal efficiency was calculated using the average of various influent COD concentrations.
Table 1. Parameters of the AD, UASB, and IC reactors [Citation24, Citation25].
2.2. Energy balance modelling of the anaerobic reactors
To maintain an optimum state for anaerobic bacteria, the reactor needs to be heated by input energy to maintain the temperature at about 35°C. Notably, anaerobic reactors can convert starch wastewater into biogas and generate energy as an output. The balance between energy input and output is a matter of great concern to practitioners in the field. To study the energy balance of anaerobic reactors treating starch wastewater, the energy flow diagram accounts for the heat loss through both influent and effluent flows, the top-covering material and walls, the environment surrounding the reactor walls, and the heat gain through the biogas produced by the reactors ().
The basic equation for the energy balance model is
where (W) is the net energy production of the reactor. The variable
(W) is the energy generated by the biogas,
(W) is the heat requirement for substrate heating, and
(W) is the radiation heat loss of the reactor. When
is negative, the anaerobic reactor requires extra energy to be supplied; otherwise, it will produce excess biogas
(m3d−1), which can be used to supply for the surrounding residents.
2.3. Heat energy loss
When the designed temperature of the anaerobic reactor differs from the ambient temperature, the reactor experiences heat loss. The substrate loss and radiation loss
are two primary aspects associated with heat loss from the three anaerobic reactors (). The substrate heating loss is defined as the energy required to heat the substrate to the designated temperature, which can be determined as follows:
where c is the heat capacity of the starch wastewater (kJ kg−1 K−1), and is the reactor inflow rate (m3s−1).
is the effluent temperature (°C) and was set as the reaction temperature (35°C) in this study. The variable
is the influent temperature (°C). Typically, the temperature of wastewater is quite similar to that of ambient river water. Thus, this study set the influent temperature using local monthly water temperature data for 2014 (). Radiation heat loss,
transfers through the walls and roof of the reactor and continues through the insulation, and is calculated as follows:
Figure 2. Average monthly water temperature and air temperature in Fuyang City, Anhui Province, in 2014.
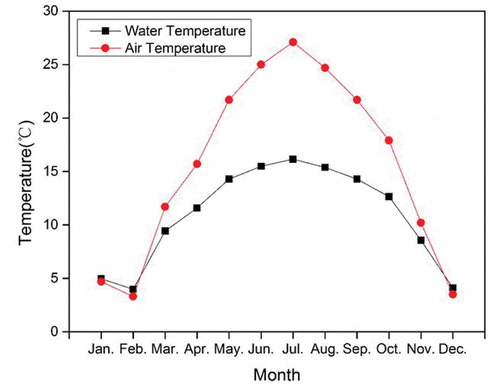
where KW is the heat transfer coefficient of the reactors’ wall (assumed to be 37.30 (W/(m·°C)), LW is the thickness of the reactors’ wall (m), and KI is the heat transfer coefficient of the reactor’s insulation (which is constant at 0.008 (W/(m·°C)). LI is the thickness of the reactors’ insulation (m), A is the surface area of the reactor tank (m2), is the designed reactor temperature (°C), and
is the ambient temperature (°C), which was set using the local monthly air temperature data for 2014 ().
2.4. Energy supplied by biogas generated by the anaerobic reactor
In this study, a mesophilic temperature (35°C) was chosen, and starch wastewater was used as the substrate. The theoretical biogas yield from the anaerobic reactors treating the starch wastewater can be determined using Equation (1):
where is the theoretical biogas production rate (m3/d);
is the amount of wastewater treated (m3/d);
is the influent COD concentration (mg/L) of the wastewater;
is the COD removal efficiency (%); and
is the conversion factor between COD and biogas (m3 biogas/kg COD). These conversion factors are 0.35, 0.60, and 0.60 for the AD, UASB, and IC reactors, respectively [Citation20].
The energy supplied by the biogas is regarded as the heat energy generated by a biogas-fired boiler, and is calculated as follows:
Where is volume of biogas produced (m3d−1),
is the methane content (%) in the biogas (assumed to be 60%) [Citation19],
is the calorific value of methane (kJ·m−3) (assumed to be 37,50 MJ/m3) [Citation21], and
is the thermal efficiency of the biogas-fired boiler (%, assumed to be 85%).
2.5. Economic assessment of energy balance
The economics of the wastewater treatment operation is an important indicator of whether the treatment system is feasible, and the cost of energy input is a crucial consideration for the starch production plant to decide which type of anaerobic reactor to adopt. If is positive according to Equation (1), the anaerobic reactor can generate excess biogas (not counting that required for heating the reactor), and the economic output of the reactor is calculated as follows:
where is the volume of excess biogas,
is the price per unit of biogas (assumed to be 1.1 RMB/m3), and
is the total profit.
If is negative, natural gas is used to represent the supplementary heat source to express its use in economic terms.
where is the volume of supplementary natural gas,
is the caloric value of the natural gas (taken as 35,588 MJ/m3),
is the price per unit of natural gas (3.0 RMB/m3), and
is the total supplementary price.
3. Results and discussion
3.1. Heat loss of anaerobic reactors
The monthly heat loss for the AD, UASB, and IC reactors is calculated using Equations (2) and (3) and shown in . It is obvious that the total heat loss fluctuated significantly in different seasons, with the lowest value recorded in summer and the highest in winter. For example, the heat loss for the AD, UASB, and IC reactors in February was 815.58 kW, 793.30 kW, and 769.62 kW, respectively, which far exceeds the corresponding values of 472.69 kW, 467.14 kW, and 461.24 kW in July. For all the three reactors, the substrate heat loss accounts for a large portion of the total heat loss, and the radiation heat loss only constitutes a small fraction. Moreover, the annual total heat loss is quite similar for all the three reactors. The annual energy loss of the AD, UASB, and IC reactors is quite similar, at 7,474.52 kW, 7,310.86 kW, and 7,136.99 kW, respectively. The annual substrate heat loss for the AD, UASB, and IC reactors accounts for 94.0%, 96.0%, and 98.3% of their respective total heat losses. The annual radiation heat loss for the AD, UASB, and IC reactors is 466.40 kW, 302.75 kW, and 128.88 kW respectively; the values are quite dissimilar because of the difference in the sizes of the three reactors.
3.2. Biogas production and heat energy supply
The biogas produced by the AD, UASB and IC reactors treating the starch wastewater of different COD concentrations is calculated using Equation (4) and presented in . The heat energy supplied by the biogas is intended to be used as a heat source in a biogas-fired boiler, which has a mechanical efficiency of approximately 80%. The heat energy supplied by the biogas value is calculated according to Equation (5) (). It shows that the biogas produced and the heat energy supplied by it for the three reactors increases with the rise in COD concentration of the starch wastewater. The biogas produced and the heat energy supplied by it for the UASB and IC reactors are much higher than those for the AD. The values for the IC reactor are approximately twice as high as those of the AD, and slightly higher than those of the UASB reactor.
Table 2. Biogas produced and heat supplied by the biogas for the three anaerobic reactors at different COD concentrations.
3.3. Energy balance analysis of the anaerobic reactors
According to the basic equation for the energy balance model expressed in Equation (1), the negative value of net energy production means that the thermal energy supplied by biogas is less than the heat loss of the anaerobic reactors, and the reactor needs supplementary heat to maintain a constant temperature. When the heat energy supplied by biogas is higher than the heat loss of the anaerobic reactors, the net energy production is positive, and the anaerobic reactor becomes an energy exporter.
The net energy production for the heat loss and biogas energy supply for the AD are calculated using Equation (1) and shown in . It is obvious that the net energy production is closely related to the influent COD concentration of starch wastewater, and the energy increases as the COD concentration rises. When the influent COD concentration of starch wastewater was less than or equal to 15,000 mg/L, the net energy production is negative for each month (i.e. throughout the year), indicating that the AD needs external energy to maintain its temperature at 35°C. However, for a COD concentration of 20,000 mg/L, the net energy production value was 49.64 kW, 85.58 kW, 105.78 kW, 82.55 kW, 49.64 kW from May to September respectively, indicating that the heat produced by the biogas exceeded the heat loss of the reactor. To maintain a constant temperature for an entire year, the AD requires supplementary heat of 5,970.49 kW, 4,235.07 kW, 2,615.35 kW, and 532.85 kW for influent COD concentrations of 5,000 mg/L, 10,000 mg/L, 15,000 mg/L, and 20,000 mg/L, respectively.
shows the net energy production of the UASB reactor. It obviously differs from that of the AD, the net energy produced by the UASB reactor in a whole year was positive for influent COD concentrations of 15,000 mg/L and 20,000 mg/L, which indicates that the biogas generated from the UASB reactor can not only provide heat to maintain its own temperature, but can also export energy. The annual energy surplus was 2,804.14 kW and 6,175.80 kW at influent COD concentrations of 15,000 mg/L and 20,000 mg/L, respectively. When the COD concentration of starch wastewater was 10,000 mg/L, the net energy values were 43.02 kW, 61.75 kW, and 40.21 kW from June to August, respectively. When the influent COD concentration was less than 5,000 mg/L, the reactor needed significant energy in addition to the heat provided by the biogas throughout the year, and the supplementary energy accounted for 46.9%–68.7% of the heat loss, with a monthly average of 57.8%. The annual supplementary heat required was 4,335.87 kW and 964.20 kW at influent COD concentrations of 5,000 mg/L and 10,000 mg/L, respectively.
The IC reactor’s net energy production is shown in . Similar to the AD and UASB reactors, the energy supplied by the biogas to the IC reactor could not counteract its heat loss for any month, and the annual supplementary heat required was 3,765.32 kW for a COD concentration of 5,000 mg/L. For the full year, the annual energy surplus was 3.01 kW, 4,168.01 kW, and 7,936.35 kW for influent COD concentrations of 10,000 mg/L, 15,000 mg/L and 20,000 mg/L respectively. These values are much higher than those for the AD and UASB reactors. The annual supplementary heat needed at an influent COD concentration of 5,000 mg/L was 3,765.32 kW.
3.4. Energy and economic evaluation of annual net energy production
The fitted regression equation between the annual net energy production of the anaerobic reactors and the COD concentrations of starch wastewater can be obtained using the above-mentioned results of the three anaerobic reactors, and the results are displayed in . The energy balance values (i.e. assuming a net energy production value of Y = 0 kW) for the AD, UASB, and IC reactors were 21,805.41 mg/L, 11,195.44 mg/L, and 9,844.67 mg/L, respectively, of COD according to the fitted regression equation.
Using the equations concerning economic assessment (Equations 6–9) for energy balance, the annual economic input or output for the three anaerobic reactor types as per the influent COD concentration can be obtained (). It can be calculated that the annual economic balance (i.e. the point at which the cost of reactor insulation is equal to earnings from excess biogas energy output) for the AD, UASB, and IC reactors was reached at influent COD concentrations of 22,251 mg/L, 12,984 mg/L, and 11,561 mg/L, respectively. The annual input cost for heating the AD, UASB, and IC reactors was 1,540,245 RMB/yr, 1,118,551 RMB/yr, and 971,363 RMB/yr for starch wastewater with an influent COD of 5,000 mg/L; and 1,092,548 RMB/yr, 270,545 RMB/yr, and 77,119 RMB/yr for a COD of 10,000 mg/L, respectively. When the influent COD concentrations of starch wastewater were 15,000 and 20,000 mg/L, both the UASB and IC reactors could produce surplus biogas energy (i.e. energy beyond the self-heating requirement), thus generating economic values of 371,926 RMB/yr and 806,091 RMB/yr, and 545,528 RMB/yr and 1,030,183 RMB/yr, respectively. However, the AD still entailed an input cost of 659,698 RMB/yr and 166,562 RMB/yr respectively for heating, even when the influent COD of wastewater was 15,000 and 20,000 mg/L.
4. Conclusions
The energy and economic benefits of the AD, UASB, and IC reactors at different starch influent wastewater COD concentrations were evaluated in this study. The salient conclusions are as follows:
Over 90% of heat loss was derived from substrate heat loss, which should therefore be considered on a priority basis to achieve the optimal reactor temperature.
The net energy production and economic efficiency of the UASB and IC reactors were comparable. These reactors outperformed the AD on both parameters. The annual economic balance for the AD, UASB, and IC reactors was reached at influent COD concentrations of 22,251 mg/L, 12,984 mg/L, and 11,561 mg/L, respectively.
When biogas generated by the anaerobic reactors was used as a heat source, the IC and UASB reactors achieved energy and economic surpluses at COD concentrations greater than 15,000 mg/L for the whole year.
The energy and economic equilibria of AD Reactor cannot be achieved throughout the year at influent COD concentrations of 5,000 mg/L to 20,000 mg/L.
Disclosure statement
No potential conflict of interest was reported by the authors.
Additional information
Funding
References
- Xue F, Gao B, Zhu Y, et al. Pilot-scale production of microbial lipid using starch wastewater as raw material. Bioresour Technol. 2010;101:6092–6095.
- Lu N, Zhou S-G, Zhuang L, et al. Electricity generation from starch processing wastewater using microbial fuel cell technology. Biochem Eng J. 2009;43:246–251.
- Antwi P, Li J, Boadi PO, et al. Efficiency of an upflow anaerobic sludge blanket reactor treating potato starch processing wastewater and related process kinetics, functional microbial community and sludge morphology. Bioresour Technol. 2017;239:105–116.
- Zhang C, Su H, Baeyens J, et al. Reviewing the anaerobic digestion of food waste for biogas production. Renew Sust Energ Rev. 2014;38:383–392.
- Harris PW, McCabe BK. Review of pre-treatments used in anaerobic digestion and their potential application in high-fat cattle slaughterhouse wastewater. Appl Energy. 2015;155:560–575.
- Carrère H, Dumas C, Battimelli A, et al. Pretreatment methods to improve sludge anaerobic degradability: a review. J Hazard Mater. 2010;183:1–15.
- Chong S, Sen TK, Kayaalp A, et al. The performance enhancements of upflow anaerobic sludge blanket (UASB) reactors for domestic sludge treatment – a state-of-the-art review. Water Res. 2012;46:3434–3470.
- González-Fernández C, Sialve B, Bernet N, et al. Effect of organic loading rate on anaerobic digestion of thermally pretreated Scenedesmus sp. biomass. Bioresour Technol. 2013;129:219–223.
- Hulshoff Pol LW, de Castro Lopes SI, Lettinga G, et al. Anaerobic sludge granulation. Water Res. 2004;38:1376–1389.
- Luo G, Li J, Li Y, et al. Performance, kinetics behaviors and microbial community of internal circulation anaerobic reactor treating wastewater with high organic loading rate: role of external hydraulic circulation. Bioresour Technol. 2016;222:470–477.
- Gebremedhin KG, Wu B, Gooch C, et al. Heat transfer model for plug-flow anaerobic digesters. Trans ASABE. 2005;48:777–785.
- Lübken M, Wichern M, Schlattmann M, et al. Modelling the energy balance of an anaerobic digester fed with cattle manure and renewable energy crops. Water Res. 2007;41:4085–4096.
- Ferrer I, Garfí M, Uggetti E, et al. Biogas production in low-cost household digesters at the Peruvian Andes. Biomass Bioenergy. 2011;35:1668–1674.
- Fu X, Yang Y, Dong W, et al. Spatial structure, inequality and trading community of renewable energy networks: a comparative study of solar and hydro energy product trades. Energy Policy. 2017;106:22–31.
- Donoso-Bravo A, Bandara WMKRTW, Satoh H, et al. Explicit temperature-based model for anaerobic digestion: application in domestic wastewater treatment in a UASB reactor. Bioresour Technol. 2013;133:437–442.
- Bandara WMKRTW, Kindaichi T, Satoh H, et al. Anaerobic treatment of municipal wastewater at ambient temperature: analysis of archaeal community structure and recovery of dissolved methane. Water Res. 2012;46:5756–5764.
- Sumino H, Takahashi M, Yamaguchi T, et al. Feasibility study of a pilot-scale sewage treatment system combining an up-flow anaerobic sludge blanket (UASB) and an aerated fixed bed (AFB) reactor at ambient temperature. Bioresour Technol. 2007;98:177–182.
- Kaparaju P, Serrano M, Angelidaki I. Optimization of biogas production from wheat straw stillage in UASB reactor. Appl Energy. 2010;87:3779–3783.
- Lansing S, Botero RB, Martin JF. Waste treatment and biogas quality in small-scale agricultural digesters. Bioresour Technol. 2008;99:5881–5890.
- D. Santos IFS, Barros RM, Tiago Filho GL. Electricity generation from biogas of anaerobic wastewater treatment plants in Brazil: an assessment of feasibility and potential. J Clean Prod. 2016;126:504–514.
- Coskun C, Akyuz E, Oktay Z, et al. Energy analysis of hydrogen production using biogas-based electricity. Int J Hydrogen Energy. 2011;36:11418–11424.
- Curry N, Pillay P. Integrating solar energy into an urban small-scale anaerobic digester for improved performance. Renewable Energy. 2015;83:280–293.
- Lindorfer H, Braun R, Kirchmayr R. Self-heating of anaerobic digesters using energy crops. Water Sci Technol. 2006;53:280–293.
- Lübken M, Wichern M, Schlattmann M, Gronauer A,Horn H. Modelling the energy balance of an anaerobic digester fed with cattle manure and renewable energy crops. Water Research. 2007;41:4085–4096.
- Luo G, Li J, Li Y, Wang Z, Li W, Li A. Performance, kinetics behaviors and microbial community of internal circulation anaerobic reactor treating wastewater with high organic loading rate: role of external hydraulic circulation. Bioresource Technology. 2016;222:470–477.