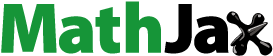
ABSTRACT
Thermochemical processes are considered as a promising technology for sewage sludge management, which could achieve volume reduction, energy and resource recovery, and effective destruction of pathogens. However, there are still many technology limitations and challenges of the thermochemical processes toward industrialization and commercialization. This review first briefly discusses the impact of sewage sludge on environmental sustainability and its current treatment and disposal methods. Typical thermochemical conversion technologies i.e., incineration/combustion, pyrolysis, gasification, and hydrothermal liquefaction for energy and resource recovery from sewage sludge are then comprehensively summarized. Subsequently, the technical challenges of thermochemical conversion of sewage sludge and the solutions that have been and/or are being developed to address the challenges are in-depth analyzed. Meanwhile, the prospects and future directions of the thermochemical technologies are outlined. In addition, the economic analysis and life cycle assessment of thermochemical conversion technologies are evaluated. Finally, the conclusions are put forward.
1. Introduction
Industrial civilization relies on the energy consumption and much of the socioeconomic wealth is based on petroleum-based economy. Petroleum is not only used as principal energy source for transportation fuels but is also the feedstock for the production of many chemicals and materials. However, rapid depletion of petroleum reserve and the environmental emissions including greenhouse gas from petroleum use are the two most serious issues of fossil fuels [Citation1]. Hence, development and utilization of alternative energy sources can greatly alleviate the depletion of fossil resources, and decrease the greenhouse gas emissions [Citation2,Citation3]. Energy crisis and environmental pollution are considered the most critical challenges for sustainable development of the global society.
Sewage sludge, an inevitable by-product of wastewater treatment plants, is regarded as a biomass feedstock for energy (biogas, fuel gas, syngas, biodiesel, bio-oil, etc.) and resource (nutrients, hydrolytic enzymes, biofertilizers, biochar, heavy metals, ash for construction materials production, etc.) recovery due to its high organic and valuable inorganic content [Citation4–6]. About 32–52 million tonnes (~80 wt% water content) of sewage sludge are produced annually in China, and this number may increase by ~10% per year [Citation7]. Usually, sewage sludge obtained from the section of biological treatment in wastewater treatment plants (WWTPs) is used for energy and resource recovery, while its typical components include 59–88% (w/v) of organic matter, composed of 50–55% C, 25–30% O, 10–15% N, 6–10% H with little amount of P and S [Citation8]. Meanwhile, some minerals (e.g. Fe, Ca, K, and Mg) and heavy metals (e.g. Cr, Ni, Cu, Zn, Pb) can also be detected in the sewage sludge [Citation8].
Biochemical conversion (e.g. anaerobic digestion (AD), fermentation) and thermochemical conversion (e.g. incineration/combustion, pyrolysis, gasification, and liquefaction) technologies are traditional methods to recover energy and resources from sewage sludge [Citation9]. In contrast to biochemical conversion, thermochemical conversion can potentially convert the entire organic fraction of the feedstock. Moreover, it is more efficient, taking only a few seconds up to a few hours rather than days for biochemical conversion. More importantly, thermochemical conversion can produce a broad range of products that can be separated for various utilizations. Hence, thermochemical conversion has been considered as an attractive and promising technology for the management/treatment/volume reduction of sewage sludge [Citation10,Citation11]. Although thermochemical conversion of sewage sludge is advantageous over bioconversion, its conversion processes are multi-phase and generally at elevated temperatures, bringing with them many challenges in large-scale operations. For instance, emission of various pollutants, agglomeration and sintering, de-fluidization and high operating cost are major technical challenges in fluidized bed incineration of sewage sludge [Citation12]. Pyrolysis/gasification of sewage sludge is limited by the need of feedstock de-watering and drying, which are energy intensive [Citation13,Citation14]. For gasification, tar formation reduce energy recovery efficiency and increase the cost of investment in gas cleaning system. Although hydrothermal liquefaction can be directly utilized feedstock with high-moisture contents [Citation15], it still has potential challenges such as continuous feeding at high pressures and temperature, recover and reuse of catalyst, and separate of products, etc.
Several review articles have been published on employed thermochemical technologies to recover energy and resources from sewage sludge, focusing on the reaction mechanism, reactor types, reaction parameters, products characteristics and fine processing, etc., while few reports comprehensively summarized and analyzed the main problems existing in thermochemical technologies [Citation16–20]. Although, the previous studies already analyzed the technical limitations in a piecemeal manner and many efforts have been devoted to overcome the challenges towards the industrialization and commercialization of thermochemical technologies, there is still lack of a comprehensive review involving the technical challenges of thermochemical conversion of sewage sludge for energy and resource recovery and limited literatures specifically focused on the effective measures that have been and/or are being developed to overcome the challenges. Therefore, this review aims to discuss the main challenges and analyze the solutions to overcome the challenges in thermochemical conversion of sewage sludge for energy and resource recovery. The economic analysis and life cycle assessment of thermochemical conversion technologies are evaluated. Through this review, it is expected that recovery of energy and resource from sewage sludge by thermochemical technology can be systematically and compendiously understood from fundamentals to implementations.
2. Impact of sewage sludge on environmental sustainability and its current treatment and disposal methods
Sewage sludge is considered as a bioresource since it contains a large amount of non-toxic organic matters and nutrients [Citation21]. However, it also contains heavy metals, toxic organic matters and a large number of pathogenic microorganisms, parasites, etc., and if mishandled, may cause serious secondary pollution to waterbodies, land and atmosphere, and hence impacts on environmental sustainability, as illustrated in . As shown in , the organic and inorganic nitrogen in sewage sludge would form NO2 (a part of which would be nitrified to form NO3−) through a series of physical, chemical and biological interactions with soil colloid, and eventually lead to photochemical smog, destroy the ozone layer and form acid rain. In addition, nitrogen and phosphorus carried by rainwater would enter waterbodies, resulting in eutrophication, one of the most popular environmental pollutions. Proteins in the dead animals and plants are decomposed into NH4+ by microorganisms, and subsequently forms N2 by nitrification and denitrification. Heavy metals can cause serious health problems if they enrich by bioaccumulation and enter into the human body through the food chain. Moreover, pathogens in sewage sludge could spread in various ways, polluting the atmosphere and waterbodies. Therefore, there is an urgent need to find effective management ways towards safe treatment and disposal of sewage sludge.
Currently, as shown in , major ways for sewage sludge disposal or utilization can be divided into three categories: landfill, incineration and land-farming [Citation22]. Landfill has been widely used for sewage sludge disposal in China [Citation23]. The landfill approach has become unpopular and even is prohibited due to the limited landfill sites and the prevalent environmental risks associated with public health. Although incineration can reduce sewage sludge mass by 70% while thermally decomposing toxic and harmful substances [Citation24], the exhaust gases released into the environment can cause multiple environmental issues such as formation of acid rain, contribution to the global climate change and emission of heavy metals to the environment through leaching of the ashes [Citation25,Citation26]. Moreover, incineration is currently considered as a high-cost approach for sewage sludge disposal due to the need of dewatering/drying of the feed [Citation27]. Utilization of sewage sludge for land-farming is increasingly regarded as an insecure disposal route due to the presence of heavy metals and pathogens in sewage sludge, which may eventually deteriorate the quality of soil and cause a potential safety risk [Citation23]. Apart from the above mentioned three major ways for disposal, other alternative ways have been proposed for sewage sludge utilization, as also summarized in , which include (i) land reclamation; (ii) horticulture and landscaping; (iii) forestry; (iv) industrial processes; (v) resource recovery; and (vi) energy recovery [Citation23]. From the perspective of economic feasibility and environmental sustainability, recovering energy and resources from sewage sludge through thermochemical conversion is more promising.
Figure 2. Current and proposed ways for sewage sludge disposal or utilizations. Date based on the statistics of UN-Habitat [Citation23]
![Figure 2. Current and proposed ways for sewage sludge disposal or utilizations. Date based on the statistics of UN-Habitat [Citation23]](/cms/asset/21acb3a0-2609-47ab-80a8-452e88d49558/tcsb_a_1947159_f0002_oc.jpg)
3. Technologies for thermochemical conversion of sewage sludge
Thermochemical technologies are advantageous approaches for managing sewage sludge owing to their promise in recovery of energy and resources, significant volume reduction, effective destruction of pathogens, etc. [Citation28,Citation29]. Main thermochemical technologies include incineration/combustion, pyrolysis, gasification, and hydrothermal liquefaction [Citation30]. In general, the choice of thermochemical technologies depends mainly on the type and quality of feedstock, the desired form of the target products, local emission standards, economic aspects, etc. Comparative analyses of different thermochemical technologies with respect to typical operating conditions, target products and pros and cons, are outlined in . The following section briefly outlines the working principles of the main thermochemical technologies.
Table 1. Comparative analyses of various thermochemical techniques applied for sewage sludge utilization
3.1 Incineration/combustion
Incineration can be defined as a unit operation that employs thermal decomposition via oxidation to convert carbonaceous matter and recover heat [Citation31]. The principal products of incineration are CO2, water, ash, and heat. The heat generated can be further used as energy source for power generation, feedstock drying, steam generation via heat exchange, etc. Ash can be used as the raw material for value-added functional materials production, such as ceramics, bricks, foamed concrete, etc. [Citation32,Citation33]. Whereas, other by-products from combustion such as sulfur and nitrogen compounds, halogens, heavy metals, etc. pose notable environment pollution concerns. Incineration is a high-temperature process in which a part of heat is stored in the flue gas and the remaining is lost to the incinerator walls. Ideally, the feed attains a complete combustion in the following reactions:
However, complete combustion is not usually achievable in an incinerator, as the C may be incompletely combusted to form CO rather than CO2. To ensure that there is sufficient oxygen in the incineration process, excess air with more than a stoichiometric amount of oxygen must be provided.
The fundamental behaviors of sewage sludge in an incinerator/combustor are illustrated in ) [Citation34]. The whole incineration process can be briefly described as follows: when sewage sludge particles are heated, dehydration and devolatilization occur simultaneously from the sewage sludge surface to the interior of the particle, resulting in release of steam and volatiles that pass through and react with the hot layers of char produced from devolatilization; then, the volatiles and light gases burn on the feedstock surface in the presence of oxygen, resulting in an increase of the temperature of the feedstock surface, where the ash layer would melt at a high temperature forming a covering layer of molten ash droplets on the surface. Finally, combustion of the remaining char would facilitate agglomeration of the ash droplets [Citation35].
Figure 3. Working principles of thermochemical technologies: (a) Incineration/combustion of sewage sludge; (b) Pyrolysis of sewage sludge; (c) Step of sewage sludge single particle gasification; (d) Hydrothermal liquefaction of sewage sludge. Modified from [Citation34,Citation36,Citation42]
![Figure 3. Working principles of thermochemical technologies: (a) Incineration/combustion of sewage sludge; (b) Pyrolysis of sewage sludge; (c) Step of sewage sludge single particle gasification; (d) Hydrothermal liquefaction of sewage sludge. Modified from [Citation34,Citation36,Citation42]](/cms/asset/fa1358e6-1dd3-4ce0-9bc2-62e40c1a844e/tcsb_a_1947159_f0003_oc.jpg)
3.2 Pyrolysis
) describes the stages of a sewage sludge pyrolysis process in thermal environment [Citation36,Citation37]. Heat is firstly transferred to the surface of the sewage sludge particle through radiation and/or convection, and then gradually to the interior of the particle. During transient heating of the sewage sludge particle, temperature increases locally, leading first to the evaporation of moisture (dry in stage) and then to the progressive release of pyrolytic volatiles (primary pyrolysis stage). The primary volatiles (denoted by ‘Volatiles-P’ in )) are mainly generated from the thermal scission of chemical bonds of the organics in the sewage sludge, such as proteins, carbohydrates and lipids. The composition of pyrolytic volatiles mainly includes H2O, CO2, CO, H2, CH4, other non-condensable hydrocarbons and condensable organic compounds (i.e. tar) [Citation38].
The residual carbon-rich solids become biochar (denoted as ‘Char-P’ in )), containing a significant portion of mineral matters originally present in the sewage sludge. The condensable volatile species at ambient conditions are denoted as ‘Bio-oil-P’. As the temperature further increases, some of the primary pyrolysis products can participate in a variety of secondary reactions to form secondary products ‘S’, e.g. ‘Volatiles-S’ (as energy recovery), ‘Char-S’ (as resource recovery) and ‘Tar-S’ (as energy recovery) ()).
A complex series of reactions such as cracking, reforming, dehydration, condensation, polymerization, oxidation and gasification reactions can occur simultaneously [Citation39]. The distinction between primary pyrolysis and secondary pyrolysis is not apparent as the secondary reactions of volatiles can occur both in the pores of the particles and/or in the bulk gas. Thus, the primary and secondary reactions can occur simultaneously in different parts of the feedstock particles. The char obtained from the primary pyrolysis stage can act as adsorbent and catalyst in the secondary reactions (cracking reactions and polymerization reactions) to convert the organic vapors into light gases and secondary char. In addition, in the presence of H2O and CO2, char can be gasified into gases through steam gasification and Boudouard reactions [Citation40]. However, the gasification reaction rates of char with H2O and CO2 are generally orders of magnitude lower than those of the primary pyrolysis, the gasification of char is limited. In comparison, the secondary conversion of the primary volatiles is a rapid process, depending on the operational conditions, which has a great influence on the final composition and yield of the volatiles.
3.3 Gasification
Gasification mainly aims to obtain syngas products that can be used directly for heating or further processing into methanol, dimethyl ether or other chemicals by Fischer-Tropsch process [Citation41]. Gasification may be viewed as extension of pyrolysis, in which the feedstock heated firstly undergoes drying and pyrolysis, releasing volatiles and leaving solid residues as char, followed by gas-solid and gas–gas reactions in the presence of a gasifying agent. ) illustrates the four steps of gasification for a single particle of sewage sludge [Citation42]. At about 70–200°C, drying as the first step takes place to remove the moisture. The rate of drying depends on the surface area of the feedstock particle, the recirculation velocity, the relative humidity of the drying gas, the internal diffusivity of moisture within the sewage sludge particle, and the temperature differences between the particle and hot gases. In the secondary or pyrolysis step at about 350–500°C, thermal decomposition of the organics takes place when approx. 60–70 wt% of the feedstock can be converted to a complex liquid fraction, gases and char. The chemical compositions of the sewage sludge, the heating rate, the gasification agent and the reactor temperature have important effects on the products distribution. However, the total yield of pyrolysis products and the amount of char can be roughly estimated from the proximate analysis of sewage sludge (i.e. volatile and fixed carbon content, respectively). The third step is gas-solid reactions that convert the solid carbon (char) into gases, e.g. H2, CO, CO2 and CH4. The carbon oxidation and/or partial oxidation reactions are strongly exothermic, providing significant energy for feedstock drying, pyrolysis, and other endothermic solid-gas reactions. Moreover, hydrogenation reactions might also occur and contribute to the energy requirements of the gasifier. Homogenous gas–gas reactions take place in the fourth step of gasification, affecting the compositions of the final gaseous products.
3.4 Hydrothermal liquefaction
Hydrothermal liquefaction (HTL) is a thermochemical process operating in water or another suitable solvent at elevated temperatures (generally 250–375°C) and high-pressure (5–20 MPa) during which the organic feedstock is broken down into four products, i.e. biocrude oil or bio-oil (the target product), aqueous phase, gas and solid residue [Citation43,Citation44]. The basic reaction pathways for the hydrothermal liquefaction of sewage sludge may be illustrated in ) comprising three major steps [Citation45]: (1) depolymerisation of various biomolecules (e.g. lipids, proteins, and carbohydrates) into monomer or oligomer units; (2) decomposition of the monomers or oligomers by cleavage, dehydration, decarboxylation and deamination, forming fragments of small molecules that are unstable and active; (3) rearrangement of light fragments through condensation, cyclization and polymerization, leading to new compounds: bio-oil, aqueous phase and solid residue.
The depolymerisation of organic feedstock involves a series of dissolution reactions occurring to dissolve the macromolecules (protein, carbohydrates, lipid, etc.) into monomer/oligomer units in water or organic solvent by hydrolytic or solvolytic reactions, facilitated by elevated temperature and pressure. Then, the decomposition step occurs, which involves loss of water, CO2 and removal of amino acid content by dehydration, decarboxylation and deamination reaction, respectively. It is worth noting that the dehydration and decarboxylation reactions reduce the content of oxygen in the bio-oil by forming H2O and CO2, which improves the stability and energy density of the bio-oil product. In the third step, opposite to the initial steps, condensation, cyclization and polymerization reactions of some unstable and reactive decomposition products (free radicals), forming high molecular weight char or bio-oil. If a stabilization agent such as hydrogen is freely available in the process, the free radicals will be capped yielding stable bio-oil products with lower molecular weights.
4. Technical challenges in thermochemical conversion of sewage sludge
4.1 The main technical challenges of sewage sludge incineration
4.1.1 Pollutants emission
Because incineration is carried out in oxidizing atmosphere, the nitrogen- and sulfur-containing compounds in sewage sludge would convert to air pollutants NOx and SOx, causing major environmental problems such as acid rain and photochemical fog [Citation46,Citation47]. HCl and Cl2 can also be detected in the flue gas while incinerating sewage sludge due to the presence of chlorine in the feedstock [Citation48], which leads to corrosion of incinerator [Citation49]. Furthermore, Cl2 would serve as the major chlorinating agent in the formation of toxic polychlorinated dioxins and furans (PCDD/Fs) [Citation50]. PCDD/Fs are not directly derived from sewage sludge, but generated in the post-incineration stage via oxy-chlorination process that can be promoted by the catalytic effects of the metallic species contained in the fly ash [Citation50,Citation51]. Besides, CO and polycyclic aromatic hydrocarbons (PAHs) are also generated from incomplete incineration of organics [Citation52,Citation53]. In addition to the above gas pollutants, fly ash poses existential health risks, e.g. respiratory threats due to its carriage of toxic heavy metals such as mercury and lead, along with other pollutants such as PCDD/Fs [Citation54]. Therefore, controlling/reducing the formation/emission of these pollutants is one of the major technical challenges for the incineration technology.
4.1.2 Operating problems
Fluidized bed incinerators are widely applied for waste disposal, where some operational problems exist, among which bed materials agglomeration is one of the main problems encountered in fluidized bed incineration of sewage sludge. The agglomeration often results from the in-bed formation of low-melting point eutectic mixtures through the reaction of mostly alkali compounds of the sewage sludge with the silica bed materials [Citation55]. In addition, sintering of the bed materials can also occur at high temperatures [Citation56]. Agglomeration and sintering promote the particle growth of the bed material, ultimately resulting in de-fluidization of the bed [Citation53]. Therefore, tackling these operating problems is another challenge in the application of incineration technology for sewage sludge disposal.
4.2 The main technical challenges of sewage sludge pyrolysis/gasification
4.2.1 Tar issue
Tar is a thick, black, highly viscous liquid comprising aromatic compounds (1–5 ring) plus other oxygen-containing hydrocarbons and PAHs [Citation57]. During the pyrolysis/gasification process, tar formation can cause several problems such as forming coke, plugging the filters and lines, etc., resulting in serious operational interruptions. It was reported that the tar content in the syngas from an air-blown circulating fluidized bed biomass gasifier was about 10 g/m3, while the tar content could reach 0.5 to 100 g/m3 in other types of gasifier [Citation58]. However, most applications of syngas require a tar content level as low as 0.05 g/m3 or less [Citation58]. Tar is also harmful to the health of human beings due to the containing teratogenic and carcinogenic compounds. In addition, tar contains significant amounts of energy that can be transferred to product gas. Hence, formation of tar in the pyrolysis/gasification process would not only lead to unacceptable levels of maintenance for downstream equipment, but also lower the energy efficiency of the process.
4.2.2 Catalysts deactivation
In the thermochemical processes, catalyst plays a vital role in improving the reaction efficiency and product quality. Ideally, a catalyst should have high activity, stability, and durability as these will substantially reduce the frequency of catalyst regeneration. In practices, many factors may cause catalyst deactivation, such as fouling, coke/carbon formation, poisoning, sintering, and phase change. For acid- or based-catalyst, the deactivation of catalyst is mainly due to coking, whereas in the case of supported metal catalysts, the deactivation could be due to the formation of coke or the synergy between coking and sintering of the metal. In some cases, the activity of catalysts may be decreased due to the chemical transformations or stream washing of the metals, leading to the loss of active species on the catalyst surfaces. Consequently, the deactivation mechanism between catalysts is different, while it also hinges on the reaction conditions.
Catalyst deactivation is a common issue in catalytic processes, mainly due to poisoning of catalytically active sites by some of the contaminants present in the feed, or due to blockage of active sites and/or pores by the coked formed during the cracking or condensation of reactants and/or products. Sometimes the products formed can decompose on prolonging the reaction time and strongly adsorb on the catalyst surface [Citation59]. Similarly, a catalyst during pyrolysis/gasification of sewage sludge may be deactivated by the fly ash generated in the processes that covers the surface or block the pores of the catalyst. In addition, in catalytic processes operating at high temperatures, thermal degradation of the catalyst might occur in the form of sintering leading to loss of active surface area via structural modification of the metal crystallites in the catalyst or loss of support surface area due to growth of its crystallite size. Metal catalysts may also react with various impurities, such as Cl, S, and O, leading to some changes in phase or formation of new phases, altering the catalyst’s activity [Citation60]. Moreover, the generated CO2 during thermochemical conversion was also identified as a deactivation agent especially for alkali metal carbonates catalysts [Citation61]. In addition to the abovementioned chemical reasons, mechanical reasons such as attrition may also cause catalyst deactivation. In addition to the abovementioned chemical reasons, mechanical reasons such as attrition may also cause catalyst deactivation. It is well known that having well mechanical strength to tolerate high attrition is an essential feature of fluid catalytic cracking (FCC) catalysts, because the catalysts particles needed to be looped continuously in the reaction system. Similarly, attrition causes the catalyst to deactivate is also an important fact in Fischer-Tropsch synthesis while slurry bubble column reactors are employed.
The catalyst deactivation can be evidenced by the reduced reaction rates and declined products quality and quantity [Citation62]. Moreover, from the perspective of industrial application, recycling, regenerate and reuse of the catalyst is very important, considering the green chemistry principles (to minimize waste generation and avoid hazardous reagents in the preparation of fresh catalysts) and the dwindling supply and high price of precious metals used in many catalysts. For organometallic complex catalysts, their recycling and reuse are even more desirable because of their high prices. As such, continued efforts are needed to develop robust catalysts and proper methods for recovery, reactivation and regeneration of the used/deactivated catalysts.
4.2.3 Formation of NOx and SOx precursors
Sewage sludge generally contains about 9 wt% nitrogen and 1 wt% sulfur by dry weight, which would release NOx and SOx precursors in the pyrolysis/gasification process, and may eventually cause secondary pollution of photochemical smog and acid rain [Citation63,Citation64]. For example, nitrogen and sulfur in sewage sludge can be converted to NH3, HCN and H2S gases under reduction conditions, or NOx and SOx under oxidation condition. In order to reduce the formation of nitrogen/sulfur-containing compounds during the pyrolysis/gasification of sewage sludge, many research efforts have been made. For instance, it was found that nitrogen mainly existed as protein in sewage sludge [Citation63,Citation65], and HCN and NH3 were found to be the major nitrogen-containing species derived in the sewage sludge pyrolysis, which can be further converted into NOX. In order to develop measures to minimize the NOX emissions, it is essential to better understand the sewage sludge-nitrogen nexus during pyrolysis/gasification. The nitrogen migration and transformation is a very complex process due to the heterogeneity of sewage sludge and different pyrolysis conditions. For example, Cao et al. [Citation63] found that a high-concentration NH3 was generated in the sewage sludge pyrolysis process, while high-concentration HCN was detected in the study by Tian et al. [Citation66]. Organic sulfur in sewage sludge should not be neglected, including sulphonic acid, sulphoxide, aromatic sulfur and aliphatic sulfur [Citation67], and decomposition of aromatic sulfur and aliphatic sulfur formed sulfur-containing gases in pyrolysis/gasification of sewage sludge. It should also be noted that these sulfur-containing gases would corrode metal surfaces, and be oxidized to SOx.
4.2.4 High moisture content of the feedstock
Sewage sludge in particular secondary sludge contains a high moisture content (generally over 80–90 wt%) needs to be dewatered or dried prior to pyrolysis/gasification treatment, which compromises the energy recovery efficiency, although appropriate moisture content can promote tar decomposition and biochar gasification. In addition, sewage sludge with high moisture content is pasty, which brings great challenges to continuous feeding. For instance, it was reported that the allowable maximum moisture content in the feedstock was about 25 wt% in down-draft gasifier and 50 wt% in up-draft gasifier [Citation68], and the gas yield decreased at the moisture content of over 30% in sewage sludge gasification. Therefore, it is necessary to reduce the moisture content of sewage sludge to an acceptable level prior to feeding it to the pyrolysis or gasification process.
4.3 The main challenges of sewage sludge hydrothermal liquefaction
4.3.1 Batch vs. continuous-flow reactor systems
Although hydrothermal liquefaction (HTL) is a promising technique for conversion of sewage sludge to liquid fuels, some technical challenges need to be addressed. High temperature and high pressure operational conditions require use of pressure reactors. Meanwhile, a corrosive environment formed by subcritical water during the HTL reaction requires resistant materials (e.g. stainless steel) for reactor construction, which leads to a high capital cost. Furthermore, the generated substances with low solubility in water (e.g. coke, tar, and solid residue) are easy to deposit in the reactor or downstream units, which could obstruct the functions of equipment. As such, most of the works on HTL of sewage sludge were carried out in batch reactor system. From the perspective of large-scale industrial applications, a continuous-flow hydrothermal liquefaction system with higher efficiency and economic feasibility should be developed, although continuous-flow HTL of sewage sludge was demonstrated by the Xu’s group at Western University at lab-scale (0.6 kg/h feeding capacity) [Citation69]. However, HTL of sewage sludge is by far lack of commercial-scale installment and operating experience.
4.3.2 Catalysts recovery
The essence of HTL is pyrolysis in hot-compressed water, which theoretically does not require a catalyst [Citation69]. However, in order to increase the efficiency of this process and reduce solid residue yield while increasing bio-oil yield, catalysts are usually employed [Citation70]. Homogeneous catalysts, e.g. alkali catalysts (Na2CO3, NaOH, etc.) and acid catalysts (H2SO4, H3PO4, etc.) have been widely employed in HTL [Citation71]. However, it is a challenge to recover these soluble catalysts from the end product, which requires costly and energy-intensive separation processes [Citation70]. To tackle such challenges, some heterogeneous catalysts (supported metal or metal oxide catalysts) have been tested, which can be easily recovered and possibly reused for several times [Citation72,Citation73]. Whereas, other challenges are associated with the heterogeneous catalysts, such as deactivation due to the leaching loss of metals or poisoning by deposits of tars or inorganics [Citation71].
4.3.3 Product separation
After hydrothermal liquefaction, the obtained products need to be separated. So far, most studies reported in the literatures used organic solvents to extract the biocrude oil from the aqueous phase and solid residues, but few attentions had been paid to the effects of organic solvent on the yield and quality of the biocrude oil products. Employing organic solvent increase the overall cost of HTL process as the solvent need to be recovered by evaporation or distillation, when small molecules of biocrude oil could be lost by evaporation along with the solvent, resulting in reduction in the bio-crude yield. Thus, efficient and cost-effective separation of biocrude oil from HTL remains a challenge.
5. Solutions to the technical challenges and future prospects of thermochemical conversion of sewage sludge
5.1 Reducing the pollutants emission and operating problems in incineration
The formation of pollutants during incineration process depends on operating conditions and fuel characteristics. For example, maintaining optimum excess air ratio and a high enough temperature is crucial to minimize CO in the incineration gases [Citation74]. Both SOx and HCl are acid gases, which can be abated by measures such as in-furnace adding calcium-based compounds (limestone, CaO, or Ca(OH)2), combined with a post-incinerator injection of CaO, or NaHCO3, etc., or co-incinerating with wastes of a high calcium content [Citation75,Citation76]. However, while increasing the SOx capture in the flue gases, the concentration of soluble sulfates in the fly ash or flue gas cleaning residue would increase, resulting in an increase in the concentration of sulfates in the leachate from these residual solids, limiting the calcium recycling. As for NOx, in order to control and/or reduce its emission, incinerator modification (air and/or fuel staging) and De-NOx techniques (selective catalytic reduction or selective non-catalytic reduction) are usually employed [Citation77,Citation78]. As the formation of PCDD/Fs and PAHs are favored in the presence of incomplete incineration products, measures to control these pollutants are the same as those for CO minimization, e.g. good control of the incineration process (excess air and temperature) to ensure complete burnout, as well as using activated carbon or lignite powder particles in the flue gas for adsorptive removal of these compounds [Citation53]. Before removing acid gas in flue gas, an electrostatic precipitator or baghouse filter are usually used to remove fly ash. On the other hand, there are measures to reduce the risk of de-fluidization, including off-line and on-line detection, control of operating parameters and addition of additives to reduce the risk of bed materials agglomeration and sintering.
As introduced above, although there are technologies developed to mitigate the challenges, integrating these technologies into the incineration system is undoubtedly of increased investment. Efforts should be made in developing green engineering approaches: prevention, e.g. to explore: (i) cost-effective higher-efficiency incineration processes with in-furnace pollutants control; (ii) pretreatment of feedstock to reduce the content of pollutants-precursors (e.g. by leaching removal of heavy metals from sewage sludge); (iii) high-efficiency co-incineration technology to reduce various pollutant emissions.
5.2 Strategies for tar minimization/removal
Several approaches are currently available for tar minimization/removal. These include physical treatment, thermal cracking, non-thermal plasmas and catalytic cracking/reforming [Citation79,Citation80]. Physical treatment (e.g. scrubbing and electrostatic precipitation) are operated effectively at lower temperature, thus additional condensation is needed since tar has a high temperature when coming out from the pyrolysis/gasification reactor. Recently, a rotating particle separator was tested for tar removal, but with low efficiency [Citation58]. Thermal cracking of tar is accomplished at a high temperature from 1100°C to 1300°C, hence with poor economic feasibility [Citation81]. While plasmas had also been applied for tar decomposition, this technology is too complex and expensive to be applied at a large scale. However, catalytic cracking/reforming can be an economically viable approach for tar removal and minimization owing to the reduced activation energy of tar decomposition employing catalysts [Citation57]. Various kinds of catalysts such as nickel-based (on Al2O3 or SiO2), noble metal based (Pt, Pd), other transition metals (Fe, Cu, Co), alkali metals (K2CO3), natural minerals (dolomite, olivine), zeolites and carbon-supported (e.g. biochar) catalysts have been investigated on tar minimization/removal in pyrolysis/gasification processes [Citation57]. Nickel-based catalysts were found to be very effective for tar removal and usually were used for syngas or H2 production [Citation82]. Nevertheless, these catalysts are relatively easy to be deactivated by self-sintering and carbon deposition and, especially by sulfur poisoning. Noble metal-based catalysts have high catalytic activity with high sulfur resistance and long-term stability, but they are very expensive. Some other transition metal-based catalysts such as Fe, Cu and Co have also demonstrated moderately active for cracking of biomass tar. To improve the performance of catalysts for tar reforming/cracking, bimetallic or trimetallic catalysts are also studied [Citation83,Citation84]. Alkali metal-based catalysts in-furnace added to the reactor also showed good catalytic ability for reducing tar formation, whereas they could evaporate quickly during the pyrolysis/gasification process, and hence are hard to recover. Natural mineral catalysts (dolomite, olivine) have been widely used for in-furnace cracking/reforming of tar, owing to their abundance and inexpensiveness. However, the natural mineral catalysts are inferior to other catalysts with respect to their catalytic activities and mechanical strengths. Zeolite was identified as a good catalyst owing to its better thermal stability, relatively high tolerance to sulfur and nitrogen compounds and easy regeneration. However, the main drawback of zeolite is the rapid deactivation caused by coke deposition [Citation85]. Carbon-supported catalysts are inexpensive and have a fair performance in the minimization/removal of tar, which can be attributed to the large pore size, high surface area, and the presence of various ash or mineral (serving as catalysts too) contents in the carbons. However, the carbon-supported catalyst has both advantages and disadvantages. On the one hand, it can recover energy through simple gasification or combustion when char is deactivated; On the other hand, it is easy to be gasified in the catalytic reaction process, thus reducing the catalytic activity. Actually, if the coke deposits rate on the surface of carbon-supported catalyst is higher than the coke consumption rate which gasification by steam/CO2, coke deposition will occur. On the contrary, if the coke consumption rate is higher than the coke deposition rate, the refresh of the active site on the surface of carbon-supported could be occurred, promoting the catalytic cracking reaction continues. Thus, seeking the balance between coke consumption rate and coke deposition rate is the key to ensure the effective operation of carbon based catalyst. According to the above analysis, a highly active and durable catalyst is urgently needed for more cost-effective tar minimization/removal and some suggestions are also presented in .
Table 2. Summary of catalysts advantages and disadvantages
5.3 Controlling of NOx and SOx precursors emission in sewage sludge pyrolysis/gasification
The NOx and SOx precursors emission control technologies can broadly be classified into: (i) pre-pyrolysis/gasification approaches that involve the use of low N/S biomass mixed with sewage sludge. The co-processing of sewage sludge and low N/S biomass could effectively reduce the emission of NOx and SOx precursors due to overall reduction in N/S contents in the feed [Citation10,Citation86,Citation87]; (ii) catalytic pyrolysis/gasification, employing suitable catalysts or minerals (e.g. Fe, Ca, Al and other elements) to convert nitrogen compounds to N2 rather than NH3 and HCN. Currently, Fe and Ca salts have been extensively investigated as catalysts for nitrogen conversion in pyrolysis/gasification, although their catalytic mechanisms were found to be different. Fe could catalyze decomposition of NH3 and increase the yield of N2, while Ca could hydrogenate HCN first to form NH3 followed by decomposing NH3 into N2 [Citation88–90]. During sewage sludge pyrolysis, a part of nitrogen is released as volatile-N and the remainder is retained as char-N. Volatile-N can subsequently decompose into N2 on the surface of Fe-based catalysts. Another route for nitrogen transformation is catalytic conversion of char-N to form N2 via the following reactions:
With Ca-based minerals, such as CaO, it can react with pyrrolic-N/pyridinic-N in char to form the non-stoichiometric calcium carbides, i.e. CaCxNy, which can easily decompose into N2:
Sulfur-containing gases are mainly derived from decomposition of organic sulfur in sewage sludge, e.g. aromatic sulfur and aliphatic sulfur, via C-S bond cleavage at low temperatures [Citation91]. H2S was the dominant sulfur-containing gas produced from thermal treatment of sewage sludge [Citation67]. Alkali catalysts/additives have proved effective for reducing the emission of sulfur-containing gases from low-temperature pyrolysis of sewage sludge [Citation92] owing to the alkali-catalyzed C-S bond cleavage at a high temperature or fixation of sulfur in the solid products by the alkali additives [Citation93,Citation94]; (iii) post-pyrolysis/gasification approaches – cold/hot cleaning of the producer gas. Cold gas cleaning includes dry gas cleaning and wet gas cleaning, and hot gas cleaning involves thermal treatment and catalytic treatment, as reviewed extensively by Asadullah [Citation95], and Woolcock and Brown [Citation81].
Although considerable progresses have been made in controlling of NOx and SOx precursors emission in sewage sludge pyrolysis/gasification, the following issues still need to be tackled in the future: (i) the intermediates formed between nitrogen/sulfur and other components especially inorganic species of sewage sludge should be investigated; (ii) functional materials or novel catalysts should be developed for in-situ/ex-situ capture of NOx and SOx precursors or selective enrichment of nitrogen/sulfur species in the char/tar products; (iii) cost-effective new processes such as Ca-looping-based technologies should be developed to suppress emission of NOx and SOx precursors from pyrolysis/gasification of sewage sludge.
5.4 Reduction of moisture content of sewage sludge
Reducing the moisture content of sewage sludge has been commonly achieved by mechanical dewatering (e.g. centrifuging, vacuum filtrating, and belt filter pressing), drying (e.g. tradition thermal drying using hot air, solar drying, fry-drying using hot oil and bio-drying), and mixing with other solid fuels of lower moisture contents, e.g. biomass, coal, etc. [Citation29]. The major advantage of mechanical dewatering is that it is low cost and much easier performed than the thermal methods [Citation96]. However, mechanically dewatered sewage sludge still has a high moisture content, ranging from 80% to 85% [Citation97], which is still not suitable for most of the thermochemical conversion processes except for HTL. A thermal drying step is thus necessary to further reduce the moisture content, whereas it is an energy-intensive process. Recently, various pretreatments (e.g. physical, chemical, and biological conditioning) have been investigated to enhance sewage sludge dewatering [Citation98–100]. Physical conditioning refers to physical methods to change the physicochemical properties of sewage sludge, e.g. by adding skeleton builders (e.g. gypsum, lignite, slag and construction waste, etc. [Citation101,Citation102], or applying thermal [Citation103], microwave [Citation104], ultrasonic pretreatment [Citation105], or their combinations [Citation106,Citation107]. Chemical conditioning is made by adding acids or alkalis [Citation108], surfactants [Citation109], bio-chemical agents [Citation110], coagulant/flocculants [Citation111], or using electrochemical methods, etc., [Citation112]) to change the intrinsic nature of sewage sludge and improve the dewatering performance. Biological conditioning method mainly includes bioleaching, an environmentally friendly and economically sustainable method with a great application promise [Citation99,Citation113].
However, practical operation indicates that the current sewage sludge dewatering is less efficient and of a high cost. Therefore, cost-effective, user-friendly sewage sludge dewatering technologies are still needed. Combination of various synergistic technologies may be used for improving the sewage sludge dewatering efficiency.
5.5 Chemical looping processes towards CO2 capture
Although the use of sewage sludge for energy production is considered to be approximately carbon neutral, negative CO2 emission can be achieved if combined with CO2 capture technology. CO2 capture and storage (CCS) have been recognized as an effective technology for reduction in greenhouse gas emission, but it is still limited by the high operating cost [Citation54,Citation114]. Among other CO2 abating techniques (pre-combustion, oxygen combustion, and post-combustion, etc.), chemical looping processes (CLPs) have emerged as a competitive option because it is capable of minimizing energy loss and intrinsically capturing CO2 [Citation115,Citation116]. CLPs can be classified based on the looping material, i.e., oxygen carrier or CO2 carrier, and the corresponding typical CLPs can be termed as chemical looping combustion (CLC) () and Ca-looping combustion (CaLC) (), respectively.
In a CLC process, an oxygen carrier, most commonly a metal oxide (MexOy) reacts with fuel to produce CO2, H2O and MexOy-1 (Eq. 7), whereas in the air reactor, MexOy-1 is oxidized, as illustrated in Eq. 8. The net chemical reaction is shown in Eq. 9. However, as the air is not mixed with the fuel during the CLC process, a highly concentrated stream of CO2 formed can be efficiently captured after water condensation. Similarly, in a CaLC where a CO2 carrier (usually CaO) is used as a looping material, CO2 could be captured in-situ in the combustor where the CO2 carrier (CaO) is frequently recycled for the capture through the carbonation reaction (Eq. 10). Whereas in the regenerator, CaO is regenerated and CO2-rich gas can be captured by the calcination reaction (Eq. 11). Thus, when sewage sludge/biomass is used as the fuel for CLPs, negative CO2 emissions can be realized.
Although CLPs have many advantages over traditional CCS techniques, they also encounter some big challenges such as the looping materials deactivation and unstable cycle performance, as well as the requirement for separation of the looping materials from ash. Solid fuels, e.g. coal and lignocellulosic biomass are commonly used in CLPs, while use of sewage sludge in CLP is rare due to the high contents of ash, nitrogen and sulfur. In order to increase use of sewage sludge in CLP, future work should be devoted to the following aspects: (i) develop of sewage sludge chemical looping gasification processes for syngas/H2 generation, especially focusing on the process intensification to allow produce syngas/H2 in a single step with in-situ capture of CO2; (ii) research of appropriate looping materials with multifunctional nature and superior oxidation-reduction/carbonation-calcination performance, as well as a low cost, better availability and environmental and safety performance; (iii) systematically analyze the synergistic effect of CO2 capture and nitrogen/sulfur catalytic decomposition in CLPs;
5.6 HTL of sewage sludge coupled with algae cultivation
The ultimate goal of sewage sludge HTL is to convert it into biocrude oil or bio-oil as a substitute for fossil fuels [Citation117]. However, from the perspective of economic feasibility, the HTL process needs to address its technical challenges mainly related to the high operation pressure. On the other hand, in order to further improve the economic performance of the HTL processes, the solid/aqueous/gaseous byproducts from the process should be fully utilized. depicts an integrated process to maximize the economic/environmental benefits and energy sustainability of HTL process by combining sewage sludge HTL and algae cultivation. Four products/byproducts, e.g. solid residue, biocrude oil, aqueous phase with high concentrations of organics and nutrients, and gaseous phase rich in CO2, obtained after sewage sludge HTL could be fully utilized [Citation118]. The solid residues can be used for soil conditioners or as activated carbon-based material for environmental and energy applications [Citation71], while biocrude oil can be used as transportation fuels after upgrading. The handling of the aqueous phase is critical as it accumulates most of the sewage sludge-containing nutrients and some organics, which provides a significant opportunity for nutrients and carbon sources, e.g. for algae cultivation. Typical limitations of algae cultivation and biofuel production are the consumption of water, nutrients, energy and environmental pollution [Citation45]. Therefore, it is a promising solution to direct use of the nutrients and carbon in the aqueous phase from sewage sludge HTL for algae cultivation. After that, the wet algae are harvested for the used as co-feed for the HTL process to recover energy, while recovering nutrients and carbon resources for the next cycle. This suggest that the integrated process not only has the potential to produce energy but also yield great environmental benefits. In addition to direct reuse of the aqueous phase for algae cultivation, catalytic hydrothermal gasification and anaerobic digestion are also interesting alternatives for generation of H2-rich fuel gas and CH4-rich fuel gas, respectively [Citation119,Citation120]. On the other hand, gaseous phase rich in CO2 from sewage sludge HTL can be recovered and reused in algae cultivation.
Figure 5. Synergistic combination of sewage sludge HTL and algae cultivation to maximize the economic and environmental benefits and energy sustainability of the HTL process
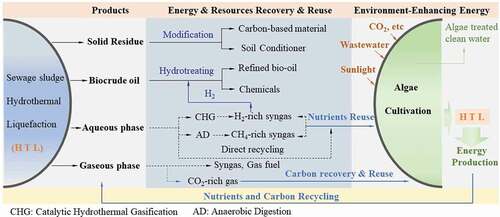
Although it is a promising technology, HTL is still in the early stage for bio-oil production from sewage sludge [Citation121]. More research is needed to address the above-mentioned technical challenges, in particular to reduce the operating costs, while maximizing the energy and resources recycling. Thus, future research should strive to achieve the following: (1) a breakthrough in the development of inexpensive new reactor materials with increased corrosion and fouling resistance under high temperature and pressure conditions; (2) an economically stable continuous feed system for industrial application of HTL; (3) development of catalysts towards target products, while having excellent engineering operability and reduced energy consumption; (4) new separation and upgrading techniques in order to maximize the recovery of valuable products from HTL; (5) increase the growth rate of algae when aqueous phase is used as the growth medium which some inhibitors are in it limit the algae growth.
6. Economic analysis and life cycle assessment
Although incineration is a relatively mature technology for solid waste management, it has been criticized for its high costs and harmful emissions. The costs associated with incineration mainly include capital investment (equipment and devices, infrastructure, and land use, etc.) and operational costs (raw materials, staff salaries, energy consumption and depreciation, etc.). Meanwhile, the costs are also closely related to selection of incineration technology and its scale. For example, for an incineration plant of 1000 t/d, the equipment cost could account for 48.2% of the total investment cost, plus 21.5% and 26.0% of the cost for the construction and installation, respectively [Citation122]. The capital cost of mechanical-grate incineration technology (MGIT) appears to be higher than that of circulating fluidized bed incineration technology (CFBIT). In the estimation of the capital cost, the land cost is an uncertain factor, largely depending on the local economic situation and governmental policy. On the contrary, the operation cost is mainly determined by the type of incineration technology adopted. For example, the operation cost of MGIT ranges from 16.3 US$/t to 32.6 US$/t, compared with from 9.78 US$/t to 19.56 US$/t for CFBIT [Citation122]. The benefits of incineration may come from government subsidies, electric energy recovery, tax incentives, heat generation, etc.
Recently, pyrolysis has been considered as a promising technology for energy and resource recovery from sewage sludge. However, the properties of the pyrolysis products differ substantially. In addition, the environmental sustainability and economic viability of pyrolysis of sewage sludge are largely determined by the process scale, technology selected, sludge collection, transportation costs, etc. For possible profit generation, the cost-associated with the feedstock should not exceed 83 US$/t dry mass for slow pyrolysis and 64 US$/t dry mass for fast pyrolysis [Citation123].
The capital and operational costs of sewage sludge gasification plants largely depend on the plant capacity, type of gasifier and potential reusing of the end products. The capital cost mainly includes costs for collection, transportation and storage of sewage sludge, and the equipment and land costs, etc. Depending on the scale of the gasification plant, the operation cost usually falls into the range of US$15/t to US$230/t [Citation124], in which the auxiliary materials (i.e. chemicals, bed materials, catalysts, etc.) may account for about 3.5–5.7% of the total operation cost [Citation124]. For large-scale sewage sludge gasification plants, the revenue can be derived from the government subsidies and the sale of the end products. In general, government subsidies to sewage sludge gasification range from US$42-166/t [Citation125].
Biocrude produced from HTL of sewage sludge can be used as a substitute for fossil fuels. Different from pyrolysis, HTL does not require drying of sewage sludge, as wet feedstock such as sewage sludge can be directly liquefied without de-watering/drying, which greatly reduces the operation cost of HTL when compared with pyrolysis. In addition, HTL bio-crude oils have a lower water content and higher heating value and hence higher quality than pyrolysis bio-oils. Therefore, HTL offers an economically feasible engineering solution to sewage sludge management.
To assess the environmental implication of thermochemical technologies, life cycle assessment (LCA) has generally employed as a tool to judge the potential of upscaling the thermochemical technologies towards energy and resource recovery. Abuşoğlu et al. [Citation126], employed LCA to compare and analyze an existing incineration plant for heat and power generation with digested sewage sludge in a fluidized bed combustor (FBC) and a hypothetical cement kiln (CK) facility. The results indicated that incineration of sewage sludge in an FBC had a better environment performance than CK in most impact categories (such as global warming, aquatic and terrestrial ecotoxicity, etc.) except the human health category. The main reason could be attributed to the residues of incineration in the CK are immobilized with the generated clinkers whereas the residues from FBC can be recovered and landfilled. Liu et al. [Citation127] carried out an LCA analysis on energy recovery from incineration of dried sludge and used oil. The global warming potential (GWP) decreased from 639.2 to 609.2 tonnes CO2-eq if increasing the substitute proportion of coal by sewage sludge from 10 wt% to 14 wt%. However, if the content of sewage sludge increased further from 14% to 92% in the mixture, the GWP showed an opposite trend and finally reached 3131.8 tonnes CO2-eq, which indicated that co-incineration of sewage sludge and reused oil with coal should be controlled at an optimal substitute proportion so as to minimize the GWP. Superior to incineration processes, gasification of sewage sludge can recover both energy and resources such as syngas, bio-chars as soil conditioners, liquid fuels and valuable chemicals. Previous studies have indicated that the net electrical efficiency of sewage waste gasification (more than 27%) is generally higher than that of incineration process [Citation128,Citation129]. Meanwhile, the GWP of gasification process is less than incineration process too due to the oxygen-deficient atmosphere in the gasifier and production of biochar followed by its storage in soils (carbon sequestration). Ramachandran et al. [Citation130], compared LCA of two processes for electricity generation: a proposed decentralized sewage sludge and woody biomass co-gasification system and an existing system (sewage sludge/biomass incineration + steam turbine). The results indicated the proposed co-gasification system provides a net annual emission reduction of 137.0–164.1 kilotonnes of CO2-eq and an increase in the net electricity generation by 3–24%. Similarly, Houillon and Jolliet [Citation131] performed LCA of pyrolysis of wastewater urban sludge, focusing on energy generation and global warming analysis. It was found that the sludge drying process by electricity and natural gas consumption demands 6.8 GJ/tDM of energy demand and produces 997 kg CO2/tDM. However, reuse of pyrolysis gas enables reduction of 835 kg CO2/tDM. In addition, Li and Feng [Citation132] evaluated the environmental impacts and energy efficiency of an integration of sludge anaerobic digestion (AD) and pyrolysis by LCA. The results indicated that the AD-pyrolysis integrated process had better environmental performance and energy efficiency than pyrolysis only due to the enhanced conversion of sludge to energy by prepositive AD. There are a few LCA studies assessed the generation of bio-crude oil through hydrothermal liquefaction (HTL) process while they are mainly focused on biomass and algae (rarely on sewage sludge), suggesting that HTL has significantly less emissions than incineration [Citation133]. Moreover, Chan et al. [Citation134] verified that HTL has a relatively lower average GWP compared with pyrolysis, whereas compared with gasification, HTL has a relatively higher average GWP due to the subsequent bio-crude upgrading processes for green diesel and/or jet fuel production.
7. Conclusions
The amount of sewage sludge has been continuously increasing with the expansion of global population and urbanization. Traditional treatment methods for sewage sludge, such as landfill and land-farming, are no longer acceptable for future sewage sludge management, and indeed have been banned in more and more countries and regions. As such, environmentally friendly and economically viable technologies are urgently needed for proper handling of sewage sludge. Currently, thermochemical technology is considered as a promising approach for sewage sludge management owing to the multiple advantages such as concurrent volume reduction, pathogens destruction and energy recovery. Despite the promise of the thermochemical platform, the end products usually have unsatisfactory quality due to the complex nature of sewage sludge, and various thermochemical technologies are associated with some technical challenges in operation, as overviewed in this work. Various solutions to addressing these challenges have been and/or are being developed. They include: strategies/technologies for preventing pollutants emission and operating problems in incinerations, tar minimization/removal, control of NOx and SOx precursors emission in pyrolysis/gasification, reducing sewage sludge moisture content, chemical looping process towards CO2 capture, and hydrothermal liquefaction coupled with algae culture, etc. It is expects that this review could shed light on possible industrialization of thermochemical conversion technologies for environmentally sustainable and economically viable management of sewage sludge.
Acknowledgments
The authors acknowledge the financial support from the National Natural Science Foundation of China (21706087) and the Key Research & development program of Zhejiang Province (2020C03088).
Disclosure statement
No potential conflict of interest was reported by the author(s).
Additional information
Funding
References
- Sharma S, Basu S, Shetti NP, et al. Waste-to-energy nexus: a sustainable development. Environ Pollut. 2020;267:115501.
- Wang J, Kang D, Shen B, et al. Enhanced hydrogen production from catalytic biomass gasification with in-situ CO2 capture. Environ Pollut. 2020;267:115487.
- Ramos A, Monteiro E, Silva V, et al. Co-gasification and recent developments on waste-to-energy conversion: a review. Renew Sust Energ Rev. 2018;81:380–398.
- Raheem A, Sikarwar VS, He J, et al. Opportunities and challenges in sustainable treatment and resource reuse of sewage sludge: a review. Chem Eng J. 2018;337:616–641.
- Yang J, Song J, Liang S, et al. Synergistic effect of water content and composite conditioner of Fenton’s reagent combined with red mud on the enhanced hydrogen production from sludge pyrolysis. Water Res. 2017;123:378–387.
- Gao N, Quan C, Liu B, et al. Continuous pyrolysis of sewage sludge in a screw-feeding reactor: products characterization and ecological risk assessment of heavy metals. Energy Fuel. 2017;31(5):5063–5072.
- Zhang J, Jin J, Wang M, et al. Co-pyrolysis of sewage sludge and rice husk/ bamboo sawdust for biochar with high aromaticity and low metal mobility. Environ Res. 2020;191:110034.
- Tyagi VK, Lo S. Sludge: a waste or renewable source for energy and resources recovery? Renew Sust Energ Rev. 2013;25:708–728.
- Graciano JEA, Chachuat B, Alves RMB. Enviro-economic assessment of thermochemical polygeneration from microalgal biomass. J Clean Prod. 2018;203:1132–1142.
- Manara P, Zabaniotou A. Towards sewage sludge based biofuels via thermochemical conversion – a review. Renew Sust Energ Rev. 2012;16(5):2566–2582.
- Xu Q, Tang S, Wang J, et al. Pyrolysis kinetics of sewage sludge and its biochar characteristics. Process Saf Environ. 2018;115:49–56.
- AlQattan N, Acheampong M, Jaward FM, et al. Reviewing the potential of Waste-to-Energy (WTE) technologies for Sustainable Development Goal (SDG) numbers seven and eleven. Renewable Energy Focus. 2018;27:97–110.
- Gao N, Li J, Quan C, et al. Product property and environmental risk assessment of heavy metals during pyrolysis of oily sludge with fly ash additive. Fuel. 2020;266:117090.
- Gao N, Kamran K, Ma Z, et al. Investigation of product distribution from co-pyrolysis of side wall waste tire and off-shore oil sludge. Fuel. 2021;285:119036.
- Lin Y, Chen W, Liu H. Aging and emulsification analyses of hydrothermal liquefaction bio-oil derived from sewage sludge and swine leather residue. J Clean Prod. 2020;266:122050.
- Gao N, Kamran K, Quan C, et al. Thermochemical conversion of sewage sludge: a critical review. 2020;79:100843. Prog Energy Combust.
- Liu Y, Lin R, Man Y, et al. Recent developments of hydrogen production from sewage sludge by biological and thermochemical process. Int J Hydrogen Energ. 2019;44:19676–19697.
- Naqvi SR, Tariq R, Shahbaz M, et al. Recent developments on sewage sludge pyrolysis and its kinetics: resources recovery, thermogravimetric platforms, and innovative prospects. Comput Chem Eng. 2021;150:107325.
- Schnell M, Horst T, Quicker P. Thermal treatment of sewage sludge in Germany: a review. J Environ Manage. 2020;263:110367.
- Awasthi MK, Sarsaiya S, Wainaina S, et al. Techno-economics and life-cycle assessment of biological and thermochemical treatment of bio-waste. Renew Sust Energ Rev. 2021;144:110837.
- Wu B, Dai X, Chai X. Critical review on dewatering of sewage sludge: influential mechanism, conditioning technologies and implications to sludge re-utilizations. Water Res. 2020;180:115912.
- Fonts I, Gea G, Azuara M, et al. Sewage sludge pyrolysis for liquid production: a review. Renew Sust Energ Rev. 2012;16(5):2781–2805.
- Fijalkowski K, Rorat A, Grobelak A, et al. The presence of contaminations in sewage sludge – the current situation. J Environ Manage. 2017;203:1126–1136.
- Malerius O, Werther J. Modeling the adsorption of mercury in the flue gas of sewage sludge incineration. Chem Eng J. 2003;96(1–3):197–205.
- Barbosa R, Lapa N, Boavida D, et al. Co-combustion of coal and sewage sludge: chemical and ecotoxicological properties of ashes. J Hazard Mater. 2009;170(2–3):902–909.
- Li J, Gan J, Hu Y. Characteristics of heavy metal species transformation of Pb, Cu, Zn from municipal sewage sludge by thermal drying. Procedia Environ Sci. 2016;31:961–969.
- Makarichi L, Jutidamrongphan W, Techato K. The evolution of waste-to-energy incineration: a review. Renew Sust Energ Rev. 2018;91:812–821.
- Jiang L, Yuan X, Li H, et al. Co-pelletization of sewage sludge and biomass: thermogravimetric analysis and ash deposits. Fuel Process Technol. 2016;145:109–115.
- Syed-Hassan SSA, Wang Y, Hu S, et al. Thermochemical processing of sewage sludge to energy and fuel: fundamentals, challenges and considerations. Renew Sust Energ Rev. 2017;80:888–913.
- Nunes LJR, Loureiro LMEF, Sá LCR, et al. Evaluation of the potential for energy recovery from olive oil industry waste: thermochemical conversion technologies as fuel improvement methods. Fuel. 2020;279:118536.
- Liang S, Yang L, Chen H, et al. Phosphorus recovery from incinerated sewage sludge ash (ISSA) and reutilization of residues for sludge pretreated by different conditioners. Resour Conserv Recycl. 2021;169:105524.
- Gupt CB, Bordoloi S, Sekharan S, et al. A feasibility study of Indian fly ash-bentonite as an alternative adsorbent composite to sand-bentonite mixes in landfill liner. Environ Pollut. 2020;265:114811.
- Singh N, Shehnazdeep BA, Bhardwaj A. Reviewing the role of coal bottom ash as an alternative of cement. Constr Build Mater. 2020;233:117276.
- Cui H, Ninomiya Y, Masui M, et al. Fundamental behaviors in combustion of raw sewage sludge. Energy Fuel. 2006;20(1):77–83.
- Liang Y, Xu D, Feng P, et al. Municipal sewage sludge incineration and its air pollution control. J Clean Prod. 2021;295:126456.
- Neves D, Thunman H, Matos A, et al. Characterization and prediction of biomass pyrolysis products. Prog Energy Combust. 2011;37(5):611–630.
- Naqvi SR, Tariq R, Hameed Z, et al. Pyrolysis of high ash sewage sludge: kinetics and thermodynamic analysis using Coats-Redfern method. Renew Energ. 2019;131:854–860.
- Hu M, Guo D, Ma C, et al. A novel pilot-scale production of fuel gas by allothermal biomass gasification using biomass micron fuel (BMF) as external heat source. Clean Technol Envir. 2016;18(3):743–751.
- Shen Y, Zhao P, Shao Q, et al. In-situ catalytic conversion of tar using rice husk char-supported nickel-iron catalysts for biomass pyrolysis/gasification. Appl Catal B: Environ. 2014;152-153:140–151.
- Liu Y, Paskevicius M, Sofianos MV, et al. A SAXS study of the pore structure evolution in biochar during gasification in H2O, CO2 and H2O/CO2. Fuel. 2021;292:120384.
- Moreira R, Bimbela F, Gil-Lalaguna N, et al. Clean syngas production by gasification of lignocellulosic char: state of the art and future prospects. J Ind Eng Chem. 2021. DOI:https://doi.org/10.1016/j.jiec.2021.05.040
- Sikarwar VS, Zhao M, Clough P, et al. An overview of advances in biomass gasification. Energ Environ Sci. 2016;9:2939–2977.
- López Barreiro D, Prins W, Ronsse F, et al. Hydrothermal liquefaction (HTL) of microalgae for biofuel production: state of the art review and future prospects. Biomass Bioenerg. 2013;53:113–127.
- SundarRajan P, Gopinath KP, Arun J, et al. Insights into valuing the aqueous phase derived from hydrothermal liquefaction. Renew Sust Energ Rev. 2021;144:111019.
- Gollakota ARK, Kishore N, Gu S. A review on hydrothermal liquefaction of biomass. Renew Sust Energ Rev. 2018;81:1378–1392.
- Hou J, Ma Y, Li S, et al. Transformation of sulfur and nitrogen during Shenmu coal pyrolysis. Fuel. 2018;231:134–144.
- Yu J, Maliutina K, Tahmasebi A. A review on the production of nitrogen-containing compounds from microalgal biomass via pyrolysis. Bioresour Technol. 2018;270:689–701.
- Liu K, Pan WP, Riley JT. A study of chlorine behavior in a simulated fluidized bed combustion system. Fuel. 2000;79(9):1115–1124.
- Khan AA, de Jong W, Jansens PJ, et al. Biomass combustion in fluidized bed boilers: potential problems and remedies. Fuel Process Technol. 2009;90(1):21–50.
- Altarawneh M, Dlugogorski BZ, Kennedy EM, et al. Mechanisms for formation, chlorination, dechlorination and destruction of polychlorinated dibenzo-p-dioxins and dibenzofurans (PCDD/Fs). Prog Energy Combust. 2009;35(3):245–274.
- Weber R, Iino F, Imagawa T, et al. Formation of PCDF, PCDD, PCB, and PCN in de novo synthesis from PAH: mechanistic aspects and correlation to fluidized bed incinerators. Chemosphere. 2001;44(6):1429–1438.
- Gulyurtlu I, Karunaratne DGGP, Cabrita I. The study of the effect of operating parameters on the PAH formation during the combustion of coconut shell in a fluidised bed. Fuel. 2003;82(2):215–223.
- Van Caneghem J, Brems A, Lievens P, et al. Fluidized bed waste incinerators: design, operational and environmental issues. Prog Energy Combust. 2012;38(4):551–582.
- Dindi A, Quang DV, Vega LF, et al. Applications of fly ash for CO2 capture, utilization, and storage. J CO2 Util. 2019;29:82–102.
- Öhman M, Nordin A. The role of Kaolin in prevention of bed agglomeration during fluidized bed combustion of biomass fuels. Energy Fuel. 2000;14(3):737.
- Skrifvars B, Hupa M, Backman R, et al. Sintering mechanisms of FBC ashes. Fuel. 1994;73(2):171–176.
- Hu M, Laghari M, Cui B, et al. Catalytic cracking of biomass tar over char supported nickel catalyst. Energy. 2018;145:228–237.
- Han J, Kim H. The reduction and control technology of tar during biomass gasification/pyrolysis: an overview. Renew Sust Energ Rev. 2008;12(2):397–416.
- Cordero-Lanzac T, Palos R, Hita I, et al. Revealing the pathways of catalyst deactivation by coke during the hydrodeoxygenation of raw bio-oil. Appl Catal B: Environ. 2018;239:513–524.
- Sadooghi P, Rauch R. Mathematical modeling of sulfur deactivation effects on steam reforming of producer gas produced by biomass gasification. Fuel Process Technol. 2013;110:46–52.
- Faba L, Díaz E, Ordóñez S. Recent developments on the catalytic technologies for the transformation of biomass into biofuels: a patent survey. Renew Sust Energ Rev. 2015;51:273–287.
- Okoye PU, Abdullah AZ, Hameed BH. A review on recent developments and progress in the kinetics and deactivation of catalytic acetylation of glycerol—A byproduct of biodiesel. Renew Sust Energ Rev. 2017;74:387–401.
- Cao J, Li L, Morishita K, et al. Nitrogen transformations during fast pyrolysis of sewage sludge. Fuel. 2013;104:1–6.
- Zhang J, Zuo W, Tian Y, et al. Sulfur Transformation during Microwave and Conventional Pyrolysis of Sewage Sludge. Environ Sci Technol. 2017;51(1):709–717.
- Xu M, Li S, Wu Y, et al. Effects of CO2 on the fuel nitrogen conversion during coal rapid pyrolysis. Fuel. 2016;184:430–439.
- Tian F, Li B, Chen Y, et al. Formation of NOx precursors during the pyrolysis of coal and biomass. Part V. Pyrolysis of a sewage sludge. Fuel 2002;81(17):2203–2208.
- Liu S, Wei M, Qiao Y, et al. Release of organic sulfur as sulfur-containing gases during low temperature pyrolysis of sewage sludge. Proc Combust Inst. 2015;35(3):2767–2775.
- Seggiani M, Vitolo S, Puccini M, et al. Cogasification of sewage sludge in an updraft gasifier. Fuel. 2012;93:486–491.
- Elliott DC, Biller P, Ross AB, et al. Hydrothermal liquefaction of biomass: developments from batch to continuous process. Bioresour Technol. 2015;178:147–156.
- Kumar M, Olajire Oyedun A, Kumar A. A review on the current status of various hydrothermal technologies on biomass feedstock. Renew Sust Energ Rev. 2018;81:1742–1770.
- Cao L, Zhang C, Chen H, et al. Hydrothermal liquefaction of agricultural and forestry wastes: state-of-the-art review and future prospects. Bioresour Technol. 2017;245:1184–1193.
- Galadima A, Muraza O. Hydrothermal liquefaction of algae and bio-oil upgrading into liquid fuels: role of heterogeneous catalysts. Renew Sust Energ Rev. 2018;81:1037–1048.
- Navalon S, Dhakshinamoorthy A, Alvaro M, et al. Metal nanoparticles supported on two-dimensional graphenes as heterogeneous catalysts. Coordin Chem Rev. 2016;312:99–148.
- Kaynak B, Topal H, Atimtay AT. Peach and apricot stone combustion in a bubbling fluidized bed. Fuel Process Technol. 2005;86(11):1175–1193.
- Boavida D, Abelha P, Gulyurtlu I, et al. Co-combustion of coal and non-recyclable paper and plastic waste in a fluidised bed reactor. Fuel. 2003;82(15–17):1931–1938.
- Chyang C, Han Y, Wu L, et al. An investigation on pollutant emissions from co-firing of RDF and coal. Waste Manage. 2010;30(7):1334–1340.
- Mahmoudi S, Baeyens J, Seville JPK. NOx formation and selective non-catalytic reduction (SNCR) in a fluidized bed combustor of biomass. Biomass Bioenerg. 2010;34(9):1393–1409.
- Suksankraisorn K, Patumsawad S, Vallikul P, et al. Co-combustion of municipal solid waste and Thai lignite in a fluidized bed. Energy Convers Manage. 2004;45(6):947–962.
- Hu M, Gao L, Chen Z, et al. Syngas production by catalytic in-situ steam co-gasification of wet sewage sludge and pine sawdust. Energy Convers Manage. 2016;111:409–416.
- Hu M, Wang X, Chen J, et al. Kinetic study and syngas production from pyrolysis of forestry waste. Energy Convers Manage. 2017;135:453–462.
- Woolcock PJ, Brown RC. A review of cleaning technologies for biomass-derived syngas. Biomass Bioenerg. 2013;52:54–84.
- Gao N, Salisu J, Quan C, et al. Modified nickel-based catalysts for improved steam reforming of biomass tar: a critical review. Renew Sust Energ Rev. 2021;145:111023.
- Noichi H, Uddin A, Sasaoka E. Steam reforming of naphthalene as model biomass tar over iron–aluminum and iron–zirconium oxide catalyst catalysts. Fuel Process Technol. 2010;91(11):1609–1616.
- Wang L, Hisada Y, Koike M, et al. Catalyst property of Co–Fe alloy particles in the steam reforming of biomass tar and toluene. Appl Catal B: Environ. 2012;121-122:95–104.
- Huang B, Chen H, Kuo J, et al. Catalytic upgrading of syngas from fluidized bed air gasification of sawdust. Bioresour Technol. 2012;110:670–675.
- Fytili D, Zabaniotou A. Utilization of sewage sludge in EU application of old and new methods—A review. Renew Sust Energ Rev. 2008;12(1):116–140.
- Chen G, Yang R, Cheng Z, et al. Nitric oxide formation during corn straw/sewage sludge co-pyrolysis/gasification. J Clean Prod. 2018;197:97–105.
- Xu CC, Donald J, Byambajav E, et al. Recent advances in catalysts for hot-gas removal of tar and NH3 from biomass gasification. Fuel. 2010;89(8):1784–1795.
- Liu Y, Che D, Xu T. Effects of minerals on the release of nitrogen species from anthracite. Energy Sources Part A. 2007;29(4):313–327.
- Xu C, Tsubouchi N, Hashimoto H, et al. Catalytic decomposition of ammonia gas with metal cations present naturally in low rank coals. Fuel. 2005;84(14–15):1957–1967.
- Cheng S, Qiao Y, Huang J, et al. Effect of alkali addition on sulfur transformation during low temperature pyrolysis of sewage sludge. Proc Combust Inst. 2017;36(2):2253–2261.
- Kozłowski M, Wachowska H, Yperman J. Transformations of sulphur compounds in high-sulphur coals during reduction in the potassium/liquid ammonia system☆. Fuel. 2003;82(9):1149–1153.
- Yan J, Yang J, Liu Z. SH radical: the key intermediate in sulfur transformation during thermal processing of coal. Environ Sci Technol. 2005;39(13):5043–5051.
- Liu H, Zhang Q, Hu H, et al. Dual role of conditioner CaO in product distributions and sulfur transformation during sewage sludge pyrolysis. Fuel. 2014;134:514–520.
- Asadullah M. Biomass gasification gas cleaning for downstream applications: a comparative critical review. Renew Sust Energ Rev. 2014;40:118–132.
- Perazzini H, Freire FB, Freire FB, et al. Thermal treatment of solid wastes using drying technologies: a review. Dry Technol. 2016;34(1):39–52.
- Cai L, Chen T, Gao D, et al. Bacterial communities and their association with the bio-drying of sewage sludge. Water Res. 2016;90:44–51.
- Wu Y, Zhang P, Zhang H, et al. Possibility of sludge conditioning and dewatering with rice husk biochar modified by ferric chloride. Bioresour Technol. 2016;205:258–263.
- Liu H, Yang S, Shi J, et al. Towards understanding the dewatering mechanism of sewage sludge improved by bioleaching processing. Sep Purif Technol. 2016;165:53–59.
- Zhang W, Yang P, Yang X, et al. Insights into the respective role of acidification and oxidation for enhancing anaerobic digested sludge dewatering performance with Fenton process. Bioresour Technol. 2015;181:247–253.
- Asakura H, Endo K, Yamada M, et al. Improvement of permeability of waste sludge by mixing with slag or construction and demolition waste. Waste Manage. 2009;29(6):1877–1884.
- Qi Y, Thapa KB, Hoadley AFA. Benefit of lignite as a filter aid for dewatering of digested sewage sludge demonstrated in pilot scale trials. Chem Eng J. 2011;166(2):504–510.
- Neyens E, Baeyens J. A review of thermal sludge pre-treatment processes to improve dewaterability. J Hazard Mater. 2003;98(1–3):51–67.
- Cai C, Liu H, Wang M. Characterization of antibiotic mycelial residue (AMR) dewatering performance with microwave treatment. Chemosphere. 2017;174:20–27.
- Mobaraki M, Semken RS, Mikkola A, et al. Enhanced sludge dewatering based on the application of high-power ultrasonic vibration. Ultrasonics. 2018;84:438–445.
- Rumky J, Ncibi MC, Burgos-Castillo RC, et al. Optimization of integrated ultrasonic-Fenton system for metal removal and dewatering of anaerobically digested sludge by Box-Behnken design. Sci Total Environ. 2018;645:573–584.
- Qiao W, Wang W, Xun R, et al. Sewage sludge hydrothermal treatment by microwave irradiation combined with alkali addition. J Mater Sci. 2008;43(7):2431–2436.
- Li X, Zheng H, Gao B, et al. UV-initiated polymerization of acid- and alkali-resistant cationic flocculant P(AM-MAPTAC): synthesis, characterization, and application in sludge dewatering. Sep Purif Technol. 2017;187:244–254.
- Guan R, Yuan X, Wu Z, et al. Functionality of surfactants in waste-activated sludge treatment: a review. Sci Total Environ. 2017;609:1433–1442.
- Guo J, Nengzi L, Zhao J, et al. Enhanced dewatering of sludge with the composite of bioflocculant MBFGA1 and P(AM-DMC) as a conditioner. Appl Microbiol Biot. 2015;99(7):2989–2998.
- Wei H, Gao B, Ren J, et al. Coagulation/flocculation in dewatering of sludge: a review. Water Res. 2018;143:608–631.
- Masihi H, Badalians Gholikandi G. Employing Electrochemical-Fenton process for conditioning and dewatering of anaerobically digested sludge: a novel approach. Water Res. 2018;144:373–382.
- Chen Z, Hu M, Cui B, et al. The effect of bioleaching on sewage sludge pyrolysis. Waste Manage. 2016;48:383–388.
- Song C, Liu Q, Deng S, et al. Cryogenic-based CO2 capture technologies: state-of-the-art developments and current challenges. Renew Sust Energ Rev. 2019;101:265–278.
- Mendiara T, García-Labiano F, Abad A, et al. Negative CO2 emissions through the use of biofuels in chemical looping technology: a review. Appl Energy. 2018;232:657–684.
- Zhao X, Zhou H, Sikarwar VS, et al. Biomass-based chemical looping technologies: the good, the bad and the future. Energ Environ Sci. 2017;10(9):1885–1910.
- Gao N, Duan Y, Li Z, et al. Hydrothermal treatment combined with in-situ mechanical compression for floated oily sludge dewatering. J Hazard Mater. 2021;402:124173.
- Zhou Y, Schideman L, Yu G, et al. A synergistic combination of algal wastewater treatment and hydrothermal biofuel production maximized by nutrient and carbon recycling. Energ Environ Sci. 2013;6(12):3765–3779.
- Ahmad F, Silva EL, Varesche MBA. Hydrothermal processing of biomass for anaerobic digestion – a review. Renew Sust Energ Rev. 2018;98:108–124.
- He C, Chen C, Giannis A, et al. Hydrothermal gasification of sewage sludge and model compounds for renewable hydrogen production: a review. Renew Sust Energ Rev. 2014;39:1127–1142.
- Toor SS, Rosendahl L, Rudolf A. Hydrothermal liquefaction of biomass: a review of subcritical water technologies. Energy. 2011;36(5):2328–2342.
- Zhao X, Jiang G, Li A, et al. Technology, cost, a performance of waste-to-energy incineration industry in China. Renew Sust Energ Rev. 2016;55:115–130.
- Brown TR, Wright MM, Brown RC. Estimating profitability of two biochar production scenarios: slow pyrolysis vs fast pyrolysis. Biofuel Bioprod Biorefin. 2011;5(1):54–68.
- Watson J, Zhang Y, Si B, et al. Gasification of biowaste: a critical review and outlooks. Renew Sust Energ Rev. 2018;83:1–17.
- Yassin L, Lettieri P, Simons SJR, et al. Techno-economic performance of energy-from-waste fluidized bed combustion and gasification processes in the UK context. Chem Eng J. 2009;146(3):315–327.
- Abuşoğlu A, Özahi E, İhsan Kutlar A, et al. Life cycle assessment (LCA) of digested sewage sludge incineration for heat and power production. J Clean Prod. 2017;142:1684–1692.
- Liu Q, Jiang P, Zhao J, et al. Life cycle assessment of an industrial symbiosis based on energy recovery from dried sludge and used oil. J Clean Prod. 2011;19(15):1700–1708.
- Baratieri M, Baggio P, Bosio B, et al. The use of biomass syngas in IC engines and CCGT plants: a comparative analysis. Appl Therm Eng. 2009;29(16):3309–3318.
- Murphy JD, McKeogh E. Technical, economic and environmental analysis of energy production from municipal solid waste. Renew Energ. 2004;29(7):1043–1057.
- Ramachandran S, Yao Z, You S, et al. Life cycle assessment of a sewage sludge and woody biomass co-gasification system. Energy. 2017;137:369–376.
- Houillon G, Jolliet O. Life cycle assessment of processes for the treatment of wastewater urban sludge: energy and global warming analysis. J Clean Prod. 2005;13(3):287–299.
- Li H, Feng K. Life cycle assessment of the environmental impacts and energy efficiency of an integration of sludge anaerobic digestion and pyrolysis. J Clean Prod. 2018;195:476–485.
- Watson J, Wang T, Si B, et al. Valorization of hydrothermal liquefaction aqueous phase: pathways towards commercial viability. 2020;77:100819. Prog Energy Combust.
- Chan YH, Tan RR, Yusup S, et al. Comparative life cycle assessment (LCA) of bio-oil production from fast pyrolysis and hydrothermal liquefaction of oil palm empty fruit bunch (EFB). Clean Technol Envir. 2016;18(6):1759–1768.