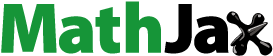
Abstract
As a relatively young additive manufacturing technology, Electron Beam Powder Bed Fusion (EB-PBF) attracts increasing attention in academics and industry. Especially, the last five years have seen an explosion in machine and process development as well as material research for EB-PBF. Compared to other additive manufacturing approaches, e.g., the more widely used laser powder bed fusion, EB-PBF shows various unique features and advantages for processing high-performance metallic components. In this article, recent advancements in the realm of EB-PBF over the past five years are reviewed.
1. Introduction
We are now living in an era, where the world is undergoing a great digital industrial revolution (Haleem & Javaid, Citation2019). One of the most important fundamental elements of this revolution is Additive Manufacturing (AM) that enables us to produce components with customized and precise geometries based on digital model data and layer-upon-layer fabrication principle (Khajavi, Partanen, & Holmström, Citation2014). Among all AM technologies, Powder Bed Fusion (PBF), during which powder layers are selectively melted using a high-energy heat source (e.g., highly focused laser beam or electron beam), is one of the most promising approaches to produce high-performance materials with almost unlimited geometrical freedom. The most common beam source is infrared Nd:YAG laser with a wavelength of ∼1 µm for Laser Powder Bed Fusion (L-PBF) (Lee et al., Citation2017). Compared to L-PBF, Electron Beam Powder Bed Fusion (EB-PBF) uses a high-power electron beam (Ackelid & Additive, Citation2009; Körner, Citation2016) instead of a laser beam as a heat source to fuse metallic powder feedstock, layer-by-layer, into bulk components (Azam, Rani, Altaf, Rao, & Zaharin, Citation2018; Gokuldoss, Kolla, & Eckert, Citation2017; Murr et al., Citation2012).
During EB-PBF, electrons are emitted by heating a tungsten filament or a lanthanum hexaboride (LaB6) cathode and are accelerated to about half of the speed of light using an electric voltage of 60 kV (Sigl, Lutzmann, & Zäh, Citation2006; Zhong et al., Citation2017). In order to reduce the possible collision between the fast-moving electrons and air molecules, EB-PBF takes place under vacuum or controlled vacuum conditions with a low helium pressure of less than 1 Pa (Ackelid, Citation2017; Pasang et al., Citation2019; Scharowsky, Bauereiß, & Körner, Citation2017). Thus, contamination and oxidization of metallic powders with a high affinity to ambient gases (e.g., oxygen and nitrogen) are minimized. With the help of electromagnetic lenses, the electron beam is focused and moved with an ultra-high deflection speed of up to 10 km/s, which allows innovative heating and melting strategies, such as quasi-multibeam scanning (Körner, Citation2016). After the electron bombardment of the powder bed, most of the kinetic energy of electrons is converted into heat, which enables local selective sintering or melting (Sigl et al., Citation2006). Since the absorption and reflection mechanisms of electrons are different from those of photons, EB-PBF usually shows much higher energy absorbance than L-PBF (especially for some materials with high optical reflectivity, such as copper) (Cosslett & Thomas, Citation1965). Compared to the laser, the electron beam can penetrate significantly deeper into powder particles. The typical penetration depth in the case of EB-PBF is of the order of 101–102 µm depending on the atomic number of the material and the speed of electrons (i.e., accelerating voltage). While laser beam can only reach a penetration depth of several tens of nanometers causing relatively high surface temperature and strong evaporation (Klassen, Citation2018; Klassen, Bauereiß, & Körner, Citation2014).
As the first step of EB-PBF, a metal blade consisting of several pieces of thin metal scrapers spreads a powder layer with defined thickness onto a preheated metal start plate placed in the build tank. Typically, powders with good flowability, low oxygen content and spherical particle morphology produced by means of inert gas atomization or Plasma Rotating Electrode Process (PREP) are used for EB-PBF (Dawes, Bowerman, & Trepleton, Citation2015; Vock et al., Citation2019). Second, a defocused electron beam scans the entire surface of this powder layer several times to reach a desired preheating temperature. During the preheating process, the formation of sintering necks between the particles takes place. Depending on different powder materials, the preheating temperature ranging between ∼400 °C (for pure copper (Lodes, Guschlbauer, & Körner, Citation2015; Guschlbauer, Osmanlic, & Körner, Citation2017)) and ∼1000 °C (for nickel-based alloys (Körner et al., Citation2018; Chandra et al., Citation2018)) can be applied. Without this preheating process, the loosely packed particles could be negatively charged, causing high repulsive forces greater than the weight of individual particles. Thus, a so-called “smoke effect” could take place, which leads to an explosion-like powder spreading in the whole process chamber and to the termination of the entire EB-PBF process (Galati & Iuliano, Citation2018; Körner, Citation2016; Milberg & Sigl, Citation2008). Owing to this smoke phenomenon, coarse metallic powders with a particle size distribution between ∼40 µm and ∼150 µm showing a relatively high weight of individual particles and low electrical resistance are mainly used for EB-PBF; while finer powders with an average particle size d50 of ∼30 µm are utilized for L-PBF (Bhavar et al., Citation2014; Guschlbauer, Momeni, Osmanlic, & Körner, Citation2018; Tiberto, Klotz, Held, & Wolf, Citation2019; Vayssette, Saintier, Brugger, Elmay, & Pessard, Citation2018). Although coarse powders exhibit better flowability for the powder feeding process and the productivity can be enhanced when using coarse powders as well as higher layer thickness, the EB-PBF-processed components generally show much higher roughness of lateral surfaces (Ra of ∼25 µm) than that of laser-produced parts (Ra of ∼10 µm) (Bhavar et al., Citation2014; Eschey, Lutzmann, & Zaeh, Citation2009; Rausch, Markl, & Körner, Citation2018; Triantaphyllou et al., Citation2015; Vayssette et al., Citation2018). After preheating, the slightly sintered powder layer exhibits sufficient electrical conductivity and mechanical stability to prevent the “smoke effect” (Markl, Lodes, Franke, & Körner, Citation2017). Owing to the high preheating temperature, components fabricated through EB-PBF show a low level of residual stress (Mladenov, Koleva, Koleva, & Dzharov, Citation2016; Sochalski-Kolbus et al., Citation2015). Thus, less geometric distortion and crack formation are observed in the EB-PBF-produced components compared to the L-PBF-processed parts (Sochalski-Kolbus et al., Citation2015). Furthermore, due to the high process temperature, an in situ heat treatment occurs during EB-PBF, affecting the final properties of printed parts (Sames et al., Citation2017). After preheating, the sintered powder layer is selectively melted using a focused electron beam. In this selective melting phase, the peak temperatures of the melt pool can easily reach more than 3000 K due to high beam power and good energy absorbance (Klassen, Forster, Juechter, & Körner, Citation2017). Under vacuum conditions during EB-PBF, the boiling point of a substance significantly decreases according to the Clausius-Clapeyron law (Clapeyron, Citation1834; Clausius, Citation1850). In order to protect the build chamber from metal vapor condensation, heat shield sets should be used (). In addition, heat shields surrounding the powder bed also ensure a homogeneous temperature distribution during EB-PBF via reflecting heat radiation back into the confined build area (Boone, Zhu, Smith, Todd, & Willmott, Citation2018). Subsequent to the selective melting and solidification, the build platform is lowered down by a single layer thickness, and the above-mentioned process cycle is repeated until all layers are completed. Lastly, the cooling process is carried out after EB-PBF by flooding the process chamber with inert gas. After EB-PBF, the non-melted but slightly sintered powder is removed by blasting process using the identical powder particles, which can be reused for the next EB-PBF jobs. A detailed description of the EB-PBF process steps is given in the authors’ previous review article published in 2016 (Körner, Citation2016). Owing to the fast control of the beam position, high energy absorbance, low oxidation and contamination risk, in situ heat-treatment as well as low thermal stress and distortion resulting from the high preheating temperature, EB-PBF is thought to be one of the most promising AM technologies for near net shape fabrication of fully dense metallic objects with high productivity.
Figure 1. Schematic design of EB-PBF systems: Triode vs. diode. (a) and (c): Typical Arcam machine equipped with a triode electron beam gun and powder hoppers as powder feeder in the vacuum chamber. (b) and (d): Typical Freemelt ONE machine with a diode electron beam gun and two liftable powder tanks for build and powder feed in the vacuum chamber.
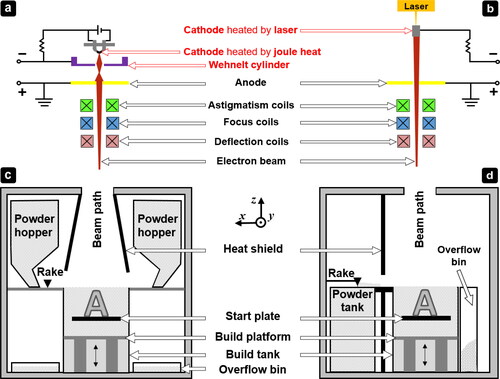
In the last decade, research activities in the realm of EB-PBF have vastly grown, and great progress has been achieved. In this review article, the main focus lies on recapping recent research results (especially in the last five years) concerning the development of EB-PBF machines (Section 2), new process monitoring technologies (Section 3), understanding of interactions between various physical and chemical effects during EB-PBF (Sections 4 and 5) as well as new materials for EB-PBF (Section 6).
2. Commercial EB-PBF systems
The first commercial EB-PBF machine for AM was launched in 2002 by Arcam AB in Sweden. For many years, Arcam AB was the single EB-PBF machine provider worldwide. Currently, in the realm of EB-PBF, Arcam AB (GE) is still a dominant company providing mature industrial machines (Kowen, Citation2020). In the last two decades, Arcam has released various machine types for different applications: A-series with optional new open-source software for high-temperature materials, Q-series with high printing accuracy (using single-crystalline LaB6 cathode) for metal orthopedic implants and Spectra-series for large parts. In 2016, Arcam AB was taken over by GE (General Electric, USA). Since the acquisition, many new companies have entered the EB-PBF market. In 2017, a Chinese company, QuickBeam, has released its first commercial open-source EB-PBF device. In the same year, Freemelt AB was founded in Sweden by a team with a wealth of experience in AM of metallic components and electron beam gun design (Almeida & Vasco, Citation2019; Kowen, Citation2020). In 2019, Freemelt AB has developed and sold its first open-source Freemelt ONE EB-PBF system with a little vacuum chamber and small build tanks especially for the purpose of material and process development in a cost-efficient way. In 2021, Wayland Additive located in UK and Jeol Ltd. based in Japan also entered the EB-PBF market. In May 2021, Wayland Additive has announced its first sale of an industry-scaled Calibur3 system equipped with an innovative in-process monitoring module. At the same time, Jeol Ltd. has brought its JAM-5200EBM to the EB-PBF market. briefly summarizes commercial machines available on the EB-PBF market and their specifications.
Table 1. Comparison of different EB-PBF machines available on the market.
As one of the most important key elements of an EB-PBF device, a thermionic electron beam gun is used in all EB-PBF machines (Negi et al., Citation2019). Electrons are generated by direct heating (e.g., resistive heating) or indirect heating (e.g., laser heating) of the cathode composed of tungsten or LaB6 with a V-shaped tip. Compared to the tungsten filament, the LaB6 cathode shows a significantly higher current density per unit surface area owing to its much lower work function and operating temperature (Fomenko, Citation2012; Knudsen, Citation2001; Richardson, Citation1929). The electron beam produced using LaB6 is characterized by higher stability. The diameter of a 60 kV beam generated using a tungsten filament may significantly increase with beam power. In contrast, the spot size of the electron beam emitted from LaB6 only slightly increases with beam power. In addition, the price and lifetime of single-crystalline LaB6 are higher than those of tungsten filament. The common lifetime values of tungsten and LaB6 cathodes are ∼80 h and ∼800 h, respectively. and b compare the typical designs of electron beam guns installed in Arcam and Freemelt machines. In all Arcam EB-PBF systems, the cathode (tungsten or single-crystalline LaB6) is directly heated based on resistive effects; while the poly-crystalline LaB6 cathode in the Freemelt ONE systems is indirectly heated using a laser. shows a typical triode electron thermionic gun with three electrodes (cathode, Wehnelt cylinder and anode) installed in Arcam EB-PBF systems; while illustrates a diode design (two electrodes: cathode and anode) of the electron beam gun applied in the Freemelt ONE systems. Via using the Wehnelt cylinder in the triode design (), the beam current can be immediately regulated by setting the bias voltage between the Wehnelt cylinder and the cathode. The function of the Wehnelt electrode is to create a potential threshold, leading to an accumulation of electrons between the Wehnelt cylinder and the cathode (Ziegler, Graafsma, Zhang, & Frenken, Citation2014). The electrons can only be emitted and accelerated towards the anode, when the potential threshold is overcome (Ziegler et al., Citation2014). This potential threshold is controllable by varying the Wehnelt voltage, so that the emitted electron current can be defined (Ul-Hamid, Citation2018; Ziegler et al., Citation2014). In addition, using the Wehnelt cylinder, the electron emission from the lateral surfaces of the cathode could be suppressed; i.e., the Wehnelt electrode also serves as an electron-optical lens that shapes the electron beam (Ul-Hamid, Citation2018). Nevertheless, owing to the electron accumulation between the Wehnelt and the cathode, an undesired arc trip problem could take place during EB-PBF, interrupting the electron beam and the melting process (Taylor, Manzo, & Flansburg, Citation2016). For the diode electron beam gun in the Freemelt ONE systems (), the beam current is controlled by the temperature of the cathode (i.e., by laser power); thus, the regulation of the beam current is not as fast as in the triode electron beam gun with the Wehnelt electrode. During preheating on the Freemelt ONE systems, the beam current is ramped up to reach target values, which might require several hundreds of milliseconds. In addition, in order to keep the cathode warm during the whole EB-PBF process, a so-called “idle scan strategy” was developed by Freemelt; i.e., the cathode always emits electrons during the whole EB-PBF process even outside of the preheating and the melting period. According to the default setting of the “idle scan”, the electron beam that is highly defocused scans a certain area with a low beam current (e.g., 0.2 mA) and a high scan speed, outside of the preheating and melting period. However, scan speed, beam focus, beam current, position and scan pattern are freely definable during the “idle scan”; e.g., the idle scan pattern could be identical to the preheating pattern, or the idle scan position could also be a predefined parking position outside the preheating area. The general idea of the idle scan is to have a perpetually warm cathode that emits electrons. Owing to the absence of the Wehnelt that controls the beam current and affects the beam shape, the shape and the diameter of the electron beam generated by means of the diode electron gun barely change, when varying the beam power during EB-PBF. Additionally, by using the “idle scan strategy”, the electron accumulation in front of the cathode, which results from the Wehnelt voltage in the triode gun, does not take place in the Freemelt ONE systems. Thus, the arc trip problem observed in the triode gun design will not occur in the case of the diode electron gun. For both diode and triode configurations, the electrons emitted from the cathode are accelerated to ∼45% of the speed of light in a vacuum using a high voltage (e.g., 60 kV) between cathode and anode (Sigl et al., Citation2006). The accelerated electron beam passes then through a series of electromagnetic coils (lenses). Deflection coils are responsible for quick control of the beam position and the scan speed. However, after the beam deflection, the circularity of the electron beam varies for different incident locations; the astigmatism coils can correct the shape of the incident beam at different positions. In addition, focus coils are used to define the intensity distribution of the electron beam (e.g., defocused beam for preheating).
In the vacuum chamber beneath the electron beam column, powder feeding and raking as well as selective melting take place. In the vast majority of industry-scaled EB-PBF systems (e.g., Arcam, QuickBeam, Jeol and Wayland machines), the powder is gravity-delivered from hoppers (see and insets in ). Thus, good powder flowability (e.g., coarse powders with a spherical particle shape) is required. In addition, this gravity powder feed method is not optimal for processing powder blends composed of particles with different levels of size and specific weight; e.g., finer and heavier particles tend to sediment resulting in a possible demixing effect. Freemelt ONE with a small vacuum chamber uses an additional powder feed tank fully filled with powder (), which is mechanically lifted in the height direction after each layerwise printing process. During the raking process, the powder bed in the build tank is dropped down by a single layer thickness; simultaneously, powder particles are raked from the feed tank to the build tank (). Based on this powder feed principle, fine powders with poorer flowability and even powder blends can also be easily fed and raked. Owing to the small build chamber, the Freemelt ONE can be quickly cleaned within several hours, if powder should be changed. During EB-PBF, different sensors and detectors in the vacuum chamber are used to monitor the printing process; e.g., the chamber pressure and the gas composition resulting from material evaporation can be measured using pressure sensors and mass spectrometer, respectively. In addition, based on different imaging modules integrated with the EB-PBF machines, online process monitoring is achievable for in situ control of print quality (see Section 3).
3. Process monitoring for EB-PBF
So far, various online process monitoring approaches have been developed to ensure high process stability and good print quality during EB-PBF (Grasso, Remani, Dickins, Colosimo, & Leach, Citation2021). Currently, high-speed imaging in the visible range is being widely implemented to investigate melt pool phenomena (Hankwitz, Ledford, Rock, O’Dell, & Horn, Citation2021; Ledford et al., Citation2019; Scharowsky, Bauereiß, Singer, & Körner, Citation2012; Scharowsky, Osmanlic, Singer, & Körner, Citation2014) (e.g., melt pool formation, gas evaporation, balling effects etc.), powder smoking (Eschey et al., Citation2009; Zäh & Kahnert, Citation2006) and spatter effect (Hankwitz et al., Citation2021) during EB-PBF. In Arcam commercial systems, a LayerQam™ imaging module based on a high-resolution optical camera is used to evaluate print accuracy and defects in each layer being printed (Boone et al., Citation2018; Everton, Hirsch, Stravroulakis, Leach, & Clare, Citation2016). In addition, during EB-PBF, it is very important to control and monitor the thermal history that significantly affects the microstructural properties of the final printed components. In common EB-PBF machines, powder bed temperature is displayed by determining the temperature of the bottom side of the start plate using a single thermocouple (Wolf et al., Citation2020). However, the surface temperatures are much higher than the displayed process temperature. The monitoring of the temperature (gradient) of the layer being fabricated can be achieved employing InfraRed (IR) thermography using thermal cameras, allowing for recording thermal videos of the whole build process (Boone et al., Citation2018; Raplee et al., Citation2017; Ridwan, Mireles, Gaytan, Espalin, & Wicker, Citation2014). By evaluating the temperature distribution and thermal inhomogeneities of each molten layer, it was successful to in situ detect defects (e.g., pores and surface warping) being in good accordance with those inside the final samples (Grasso et al., Citation2021; Raplee et al., Citation2017). Via the detection of IR radiation, thermal gradients of a given surface can be easily measured; however, an estimation of absolute temperatures is difficult, which requires the knowledge of the emissivity of the heated surface (Grasso et al., Citation2021; Hankwitz et al., Citation2021). For instance, a change in thermal radiation signals can clearly be observed during EB-PBF, when a transition takes place from powder to melt and to solidified dense or porous material showing different emissivity values (Grasso et al., Citation2021). Nevertheless, the determination of the absolute actual temperature is difficult. In order to measure emissivity-independent true temperature, pyrometers were successfully used to record surface temperatures during the EB-PBF process at a fixed point (Cordero, Mireles, Ridwan, & Wicker, Citation2017). Based on the above-mentioned online monitoring approaches using conventional and IR cameras, it is easy to derive 2D information of the layer being printed. Recently, another very interesting method based on structured light scanning using a fringe projection system available on commercial Wayland EB-PBF systems (Calibur3) has been applied to gain 3D surface topography during the fabrication process. A fringe projection system consists of a projector as well as camera(s) and shows high accuracy in the vertical z-direction allowing for evaluating powder bed defects (e.g., excessive powder delivery and lack of powder) after the raking process and the surface topography of the layer being printed (Liu et al., Citation2020). For conventional and thermal cameras as well as fringe projection systems, protection against heat, metal vapor condensation and harmful x-ray radiation resulting from interactions between the incident electron beam and material is necessary. To prevent heat and x-ray damage, cameras are usually located outside the vacuum chamber behind a leaded glass window. However, during EB-PBF, the glass window can be metalized, reducing its optical transmission. Thus, to minimize metal vapor condensation on the observation window, a rolling Kapton film exhibiting good IR transmission is often utilized as a sacrificial barrier (Grasso et al., Citation2021). Nevertheless, owing to thermal radiation and high temperature during EB-PBF, the Kapton film could be melted. Thus, an alternative approach to protect the glass window from metallization is to use a mechanical shutter only allowing for image acquisition within a short time interval (not suitable for long-time exposure).
All previously mentioned process monitoring methods are also being extensively used in L-PBF machines (Grasso et al., Citation2021). In contrast, owing to the specific process environment (e.g., metallization and x-ray radiation) during EB-PBF, the camera systems used in EB-PBF machines need additional protection requiring extra development effort and costs. However, these aforementioned protective measures are not necessary for ELectron-Optical (ELO) imaging (Arnold, Böhm, & Körner, Citation2020; Arnold, Pobel, Osmanlic, & Körner, Citation2018; Arnold & Körner, Citation2021; Wong et al., Citation2019; Zhao & Lin, Citation2021). During EB-PBF, after injection of the incident electron beam into a small spot of the powder bed, low-energy Secondary Electrons (SE) and high-energy Back Scattered Electrons (BSE) as by-products are emitted from this spot. A part of these emitted SE and BSE can reach the detectors located above the powder bed generating a current signal. When moving the incident electron beam to scan an area of interest, an intensity map (i.e., ELO image) can be derived based on the detection of SE and BSE generated from the scanned spots. That is, during EB-PBF, the electron beam, which heats and melts the powder layer, can also be used for process monitoring in a way comparable to Scanning Electron Microscopy (SEM) (Arnold et al., Citation2018; Pobel, Arnold, Osmanlic, Fu, & Körner, Citation2019). The signal intensity of SE and BSE (brightness in ELO images) depends on the atomic number of the specimen and surface topography. Thus, ELO imaging is optimal to detect defects and surface bulging in the layer being printed. In comparison to other optical monitoring systems, the ELO imaging process is not affected by any temperature effects and is not sensitive to metal vaporization during EB-PBF. ELO imaging has been utilized in the realm of electron beam welding since about 50 years for in situ weld seam monitoring and beam diagnostics (Gillespie, Citation1974). Nevertheless, the first academic experimental test concerning ELO monitoring for EB-PBF was implemented in 2018 by Arnold et al. (Arnold et al., Citation2018) using a retrofitted Arcam S12 device equipped with a new powerful electron beam welding gun and BSE & SE detectors located at the top side of the build chamber. In 2019, the first commercial EB-PBF machine (Freemelt ONE) equipped with an ELO monitoring module was released by Freemelt (). shows a typical process cycle for EB-PBF including ELO scanning of a single layer. Generally, the step of ELO image acquisition is carried out after the selective melting phase by raster scanning the entire final molten surface. The resolution of the derived ELO images depends on the scan line distance, the beam diameter, the scan speed and the sampling rate of the measuring device (Arnold et al., Citation2020).
Figure 2. ELectron-Optical (ELO) process monitoring for EB-PBF (reprinted with permission from (Pobel, Arnold, et al., Citation2019). Copyright Elsevier). (a): Individual steps for EB-PBF and ELO scanning. (b): Representative ELO image for sample quality evaluation and for processing window development on a retrofit Arcam S12 system (Pobel, Arnold, et al., Citation2019). (c): Processing window generated according to ELO images. The green area in (c) indicates a stable process region for EB-PBF of dense Ti-6Al-4V samples with an even surface, while the yellow area corresponds to the process parameters depicted in (b) (Pobel, Arnold, et al., Citation2019).
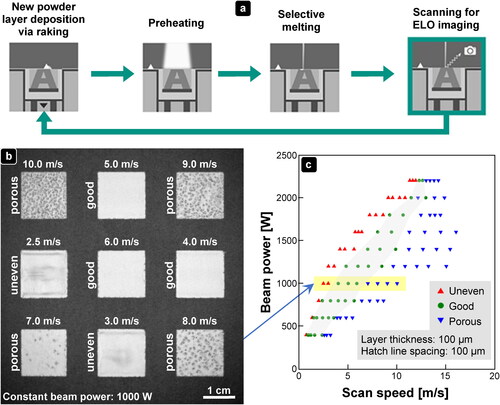
ELO imaging can also be applied for the rapid development of processing windows (Pobel, Arnold, et al., Citation2019). shows an exemplary ELO image of a molten layer for in situ characterization of the surface topography and defects. Based on ELO images, a complete processing window can be determined within a single EB-PBF process () (Pobel, Arnold, et al., Citation2019). Combining with machine learning, the ELO system as a computer vision has the potential to replace the device operator and to achieve automatic development of process parameters or process control (Le Roux et al., Citation2021). In addition, by stacking the ELO images layerwise upon each other, a 3D reconstruction of EB-PBF-processed samples was gained and showed good qualitative accordance with the Computed Tomography (CT) results derived by analyzing the printed parts (Arnold et al., Citation2018). Since the ELO imaging step requires additional time after selective melting (), Arnold et al. demonstrated that BSE and SE acquired during the melting step could also be used for “in operando” ELO imaging to detect pores and surface warping in the layer being fabricated (Arnold et al., Citation2020). The signal intensity maps derived through the in operando ELO imaging showed good accordance with the final topography of the printed samples (Arnold et al., Citation2020). Compared to the ELO detectors installed in the retrofitted Arcam S12 (Arnold et al., Citation2018; Pobel, Arnold, et al., Citation2019) and in the commercial Freemelt ONE systems, which are positioned relatively far away from the powder bed (i.e., at the top side of the build chamber), Wong et al. (Wong et al., Citation2019) and Zhao et al. (Zhao & Lin, Citation2021) integrated ELO detectors composed of electronically conductive materials (e.g., copper) into heat shields. These detectors are located close to the powder bed, so that a part of low-energy SE can also be collected and more topographic information of the powder layer can be gained during EB-PBF. So far, ELO imaging showing high resolution and stability to depict surface information is considered to be one of the most promising in situ monitoring approaches, especially for EB-PBF.
In , an overview of different process monitoring methods for EB-PBF and their strengths is provided.
Table 2. Comparison of different online monitoring methods for EB-PBF.
4. Powder smoking during EB-PBF
As mentioned in Section 1, EB-PBF shows various advantages over the more widely used L-PBF approach. However, the industrial application of EB-PBF is still restricted owing to the limited understanding of interactions between the electron beam and materials. Under certain conditions, an undesired “smoke phenomenon” can take place during EB-PBF leading to the termination of the entire print process (Cordero, Mireles, et al., Citation2017; Sigl et al., Citation2006). If smoke occurs, the entire vacuum chamber has to be cleaned. Simultaneously, the cathode could be contaminated and should be changed, requiring substantial effort and costs. shows a typical powder smoking event (recorded by means of an optical high-speed camera), which generally occurs within a very short time (less than 1 s) (Zäh & Kahnert, Citation2006).
Figure 3. Smoking of a single powder layer during EB-PBF (adapted from (Zäh & Kahnert, Citation2006) under a CC BY 4.0 license).
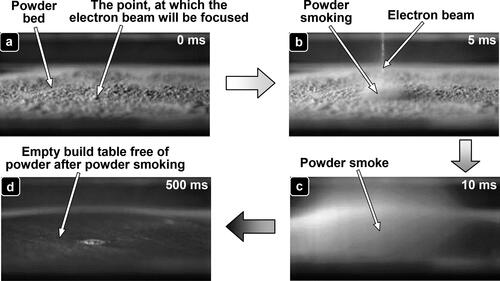
In the last decade, great progress has been achieved in terms of machine and process as well as new material development for EB-PBF (Körner, Citation2016). Nevertheless, the origin of powder smoking is still not deeply understood. Sigl et al. (Sigl et al., Citation2006) and Milberg et al. (Milberg & Sigl, Citation2008) discussed different physical effects, which can result in smoke: (i) residual water (not chemically bonded) adsorbed on the powder surface; (ii) momentum transfer from fast-moving electrons to power particles and (iii) repulsive forces caused by electrostatic charge between particles. As a conclusion of their works, electrostatic forces were thought to be the main reason giving rise to smoke (Milberg & Sigl, Citation2008; Sigl et al., Citation2006). After the electron beam injection into the powder bed, the loosely packed particles are negatively charged, resulting in high Coulomb repulsion forces greater than the weight of individual particles. Qi et al. (Qi, Yan, Lin, W, & Zhang, Citation2006) and Eschey et al. (Eschey et al., Citation2009) claimed that using gas-atomized powder with a spherical particle morphology, smoke could be more often observed during EB-PBF than using water-atomized powder with an irregular particle shape. Moreover, based on experimental observations, the powder becomes more resistant to smoking with increasing particle size and electrical conductivity. Thus, EB-PBF is up to now limited to processing coarse metallic powders owing to the smoke effect. As a consequence, the spatial resolution and the surface finish of EB-PBF-processed parts are inferior to those of L-PBF-fabricated objects (Bhavar et al., Citation2014; Triantaphyllou et al., Citation2015; Vayssette et al., Citation2018).
Methods to prevent smoke events are mainly based on trial-and-error optimization and empirical rules. An efficient method to suppress powder smoking during EB-PBF is to preheat the start plate and the raked powder layer utilizing a highly defocused electron beam, prior to the selective melting step (Cordero, Mireles, et al., Citation2017; Eschey et al., Citation2009; Zäh & Kahnert, Citation2006). Without preheating the start plate (i.e., if the powder layer was directly spread onto the cold start plate), a smoke event would easily be observed by heating the cold powder layer using a defocused electron beam (Sigl et al., Citation2006). After preheating, the sintered powder layer with high electrical conductivity and mechanical stability is less susceptible to smoking (Cordero, Mireles, et al., Citation2017).
Furthermore, it is well known that metal powders are commonly covered by dielectric oxide and hydroxide surface layers with a thickness of several nanometers, whose electrical conductivity increases with temperature according to the Arrhenius law (Di Paola, Citation1989; Phambu, Citation2003; Pollack & Morris, Citation1965; Shim & Kim, Citation2004; Shkolnikov, Shaitura, & Vlaskin, Citation2013; Simmons, Citation1965). Thus, with increasing process temperature and electrical conductivity of the powder layer, the electrostatic charge can be immediately conducted to neighboring particles after the electron injection. Nevertheless, owing to sintering effects during preheating, powder particles within small cavities can be hardly removed after EB-PBF (Pobel, Arnold, et al., Citation2019). Therefore, EB-PBF of objects with hollow channels (e.g., copper inductor) is still a big challenge. So far, different methods have been developed to fabricate components with hollow structures (Franke & Eichler, Citation2019; Karlen et al., Citation2019; Pobel, Arnold, et al., Citation2019; Stephansen, Citation2021; Wildheim & Stephansen, Citation2021).
Recently, Edinger from CANMORA TECH Inc. (Richmond, Canada) published a patent and claimed that EB-PBF of non-sintered Ti-6Al-4V powders could be achieved at low build temperatures via powder conditioning (e.g., heat treatment and mechanical vibration) prior to powder raking; i.e., before the raking step, the powdered feedstock is heated in an external storage container and fed under the action of gravity and a vibration system (Edinger, Citation2021; Sinclair, Edinger, Sparling, Molavi-Kakhki, & Labrecque, Citation2021). The powder temperature in the external container could be significantly lower than the sintering temperature (Edinger, Citation2021). Edinger considered that the dielectric surface layers could be broken after the powder conditioning, making the powdered feedstock more conductive; and the good conductivity can remain under vacuum conditions (Edinger, Citation2021). Similar powder conditioning effects were also observed by Chiba et al. (Chiba, Daino, Aoyagi, & Yamanaka, Citation2021; Chiba, Daino, et al., Citation2021). After ball milling of Inconel 718 powder in the air, the dendritic structure on the powder surface was flattened ( and b) (Chiba, Daino, et al., Citation2021; Citation2021). Simultaneously, Chiba et al. considered that ball milling could introduce plastic strain into the oxide skin layers, leading to an insulator-metal transition (Chiba, Daino, et al., Citation2021). At low temperatures, the virgin Inconel 718 powder showed high electrical resistivity (∼104 Ω·m) owing to insulating oxide skin films and pointed contact areas between particles while the ball-milled powder exhibited significantly lower electrical resistivity (∼10-3 Ω·m) (Chiba, Daino, et al., Citation2021). As depicted in , with increasing temperature up to 800 °C, the electrical resistivity of the virgin and the ball-milled powders drops to a similar low level of ∼10-4 Ω·m (Chiba, Daino, et al., Citation2021; Citation2021). This low level of electrical resistivity remained even after cooling down to room temperature (), indicating the low stability of the oxide and hydroxide surface layers against thermal treatments (Chiba, Daino, et al., Citation2021). According to Chiba et al., after heat treatments or mechanical stimulation, the capacitive reactance component of the oxide and hydroxide surface layers could be eliminated, leading to a low dielectric relaxation time and to the suppression of the charge of the powder (Chiba, Daino, et al., Citation2021). Using ball-milled Inconel 718 powder, Chiba et al. successfully demonstrated that preheating was not required for smoke-less EB-PBF (Chiba, Daino, et al., Citation2021). In addition, Freemelt AB patented a device as an optional module for Freemelt ONE systems, which is positioned over the powder bed and emits electromagnetic radiation (with high frequencies) onto the powder layer to reduce its electrostatic charge (Ljungblad, Citation2021). Under the action of the emitted electromagnetic radiation, electrons of the oxide and hydroxide surface layers can be excited from the valence band to the conduction band, leading to the high electrical conductivity of the powder layer being printed (Ljungblad, Citation2021). Another approach to suppress the powder smoke is the so-called “ProHeat” patented by Freemelt AB (Stephansen, Nilsson, Ljungblad, & Ackelid, Citation2020); i.e., during EB-PBF a movable refractory plate is heated by the electron beam and transfers the absorbed heat to the powder bed for conditioning or preheating the raked powder layer. An alternative method to minimize the smoke phenomenon is to use a process gas. In all Arcam systems, EB-PBF is carried out in a controlled vacuum atmosphere (i.e., helium as a process gas with a low partial pressure of less than 1 Pa (Körner, Citation2016; Ackelid, Citation2017; Markl et al., Citation2017; Ackelid, Citation2015 )). The exact effect of helium on powder smoking is not yet clear. One assumption is that gaseous helium particles with a relatively high electrical conductivity (Nighan, Citation1969) fills the cavities between powder particles and enhances the electrical conductivity of the whole powder bed. Thus, the dissipation time of the electrostatic charge after the injection of the electron beam can be significantly reduced. The “NeuBeam” module of the Wayland EB-PBF systems uses an active stream of ions generated inside the chamber with Argon gas, so that the negatively charged electron beam and the powder bed can be neutralized (Van Den Berg, Hussey, Richardson, & Laidler, Citation2020). In addition, to prevent powder smoking, Jeol developed a so-called "e-Shield" system, whose working principle has been so far not disclosed. The above-mentioned methods to suppress and avoid the smoke phenomenon during EB-PBF are summarized in .
Figure 4. Ball milling and heat treatments to suppress powder smoking during EB-PBF (adapted from (Chiba, Daino, et al., Citation2021; Chiba, Daino, et al., Citation2021) under a CC BY 4.0 license). (a) and (b): Particle shape and surface morphology of virgin and milled Inconel 718 powders. (c): Electrical resistivity of virgin and ball-milled Inconel 718 powder during heat treatments and cool-down procedure Chiba et al., Citation2021; Chiba et al., Citation2021).
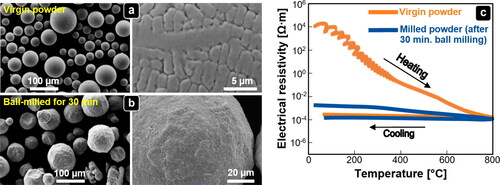
Table 3. Methods to suppress powder smoking during EB-PBF.
In order to predict the smoking effect depending on different powder properties and process parameters, Cordero et al. proposed a simple analytical model of powder bed charging, assuming each spherical metal particle is covered by a thin dielectric oxide layer (Cordero, Mireles, et al., Citation2017). The smoke event occurs, when the maximum electrostatic force is larger than the weight of a single particle (Cordero, Mireles, et al., Citation2017). Nevertheless, in the analytical model proposed by Cordero et al. (Cordero, Mireles, et al., Citation2017), the effect of recoil pressure resulting from material evaporation was not considered, which could be a key factor leading to smoking. According to the model proposed by Cordero et al. (Cordero, Mireles, et al., Citation2017), powder smoking can be suppressed by reducing the beam diameter, when using a highly focused electron beam during preheating; i.e., with increasing beam spot size, the electron beam needs more time to span a single particle, and the particles “retain their charge longer after the beam has passed over them”. Nevertheless, in view of experimental observations in the literature, a defocused electron beam was beneficial in avoiding the smoke event (Eschey et al., Citation2009; Zhong et al., Citation2017). According to the authors’ idea, the contradiction between the analytical calculation (Cordero, Mireles, et al., Citation2017) and the experimental observation (Eschey et al., Citation2009; Zhong et al., Citation2017) is mainly attributed to the fact that the evaporation effect is not taken into account during the physical modeling. shows a schematic of smoke initiation. A highly focused electron beam induces high local temperature () and eventually gives rise to strong material vaporization (), which is according to the authors’ consideration the first stage of the smoke event. During this first stage, primary powder particles are lifted to the atmosphere due to the evaporation pressure. This assumption is supported by the observation of the movement of powder particles during L-PBF at different pressures (Bidare, Bitharas, Ward, Attallah, & Moore, Citation2018; Matthews et al., Citation2016). At atmospheric pressure (i.e., in an Ar atmosphere with a pressure of 105 Pa), the laser plume produces a flow in the ambient atmosphere that entrains particles toward the melt pool (Bidare et al., Citation2018). However, with decreasing ambient pressure, particles are repelled away from the melt pool (Bidare et al., Citation2018). At low pressures, the outward expulsion of nearby particles away from the laser spot is thought to be caused by the vapor pressure p (Matthews et al., Citation2016).
Figure 5. Smoke initiation model EB-PBF. (a): Heating phase: No charge accumulation since conductivity is high enough. (b): Primary powder particles are lifted into the atmosphere due to evaporation pressure. This is also observed during L-PBF (Matthews et al., Citation2016). (c): Evolution of secondary particles due to Coulomb repulsion of primary particles loaded by negative charge.
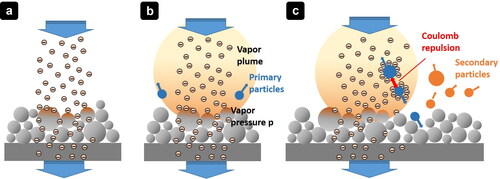
shows how powder particles are transported from their original position into the vacuum owing due to the recoil pressure. As a consequence, these lifted primary particles lose their electrical contact and are strongly charged by the electron beam, see . These primary particles get more and more charged and the resultant Coulomb force drives the particles apart from each other. Some of these particles will move in the direction of the powder bed. When these primary particles impinge into the powder bed, secondary particles are lifted into the atmosphere resulting in an avalanche effect and a catastrophic smoke event. In summary, the smoke phenomenon is thought to be a consequence of the competition between local sintering /melting and gas release effects as well as interparticle electrostatic forces.
Compared to EB-PBF, the evaporation effect during L-PBF under vacuum conditions is more significant, since the penetration depth of the laser beam is typically three orders of magnitude smaller than that of the electron beam (Klassen, Citation2018). Thus, the high surface temperature of powder particles leads to strong evaporation during L-PBF under vacuum conditions. Currently, all commercially available EB-PBF machines are equipped with an electron gun with a maximum accelerating voltage of 60 kV (). From the authors’ point of view, using an electron beam gun with a higher accelerating voltage, even larger beam penetration depth can be achieved, leading to a more homogenous heat distribution during EB-PBF and less material evaporation, so that the smoke phenomenon could be further minimized. In addition, beam power during EB-PBF is the product of the accelerating voltage and the beam current; i.e., with increasing accelerating voltage, fewer electrons are emitted to reach the defined beam power. Therefore, when using high acceleration voltage, the local accumulation of emitted electrons as well as the powder smoking can be suppressed. The above hypothesis should be evaluated by future experimental investigations.
5. EB-PBF powders and their aging behavior
The characteristics of the powder feedstock play a crucial role in EB-PBF process stability and the final properties of the printed components (Clayton, Millington-Smith, & Armstrong, Citation2015; Spierings, Voegtlin, Bauer, & Wegener, Citation2016; Vock et al., Citation2019). As stated in Section 1, in order to minimize the smoke effect, coarse powders with a particle size ranging from ∼40 µm to ∼150 µm are typically used for EB-PBF at the expense of reducing the surface quality of printed parts. In the majority of EB-PBF systems, the powder feedstock is gravity-fed from powder hoppers and raked using a doctor blade (). Thus, EB-PBF usually requires gas-atomized powders with a spherical particle shape and good flowability. Although water-atomized powders are significantly cheaper, the thick oxide layers on the powder surface formed during water atomization result in an irregular particle shape and in reduction of flowability (i.e., water-atomized powders are not optimal for the gravity powder feed method). Nevertheless, using a cheap, irregularly shaped and broadly sized water-atomized Fe-Ni powder with high oxygen content and poor flowability, single layer EB-PBF trials have been recently successfully performed with the help of a vibratory powder feeding system (Sinclair et al., Citation2021); instead of using powder raking, the layer thickness of the water-atomized powder was controlled by vibration amplitude and frequency of the feeder. Although water-atomized powders are less susceptible to powder smoking, undesired balling and spatter effects were often induced when using water-atomized powders (Qi et al., Citation2006). Compared to water-atomized powders, gas-atomized powders as a common feedstock for EB-PBF show significantly lower oxygen content, less contamination, much smoother particle surface, higher sphericity and better flow ability as well as higher price (Dawes et al., Citation2015). Recently, it is reported that powders produced by means of Plasma Rotating Electrode Process (PREP) might be more suitable for EB-PBF (Zhao, Aoyagi, Daino, Yamanaka, & Chiba, Citation2020). PREP powders show even higher sphericity and less to no tiny satellite particles than gas-atomized powders ( and b) (Zhao et al., Citation2020). With increasing sphericity of powder particles, better flowability, higher packing density and homogeneity of the raked powder layer were observed (Muñiz-Lerma, Nommeots-Nomm, Waters, & Brochu, Citation2018). In addition, gas-atomized powders often show internal gas pores (), which could be a source of defects in the final printed samples; while PREP powder particles show an almost perfectly round, sound and dense cross-section () (Zhao et al., Citation2020). Zhao et al. compared the quality of EB-PBF-built Inconel 718 components printed using gas-atomized and PREP powders with a similar particle size distribution () (Zhao et al., Citation2020). The EB-PBF processing window derived by using the PREP Inconel 718 powder is broader (Zhao et al., Citation2020). In addition, even after optimizing process parameters, the samples built using the gas-atomized powder show more microstructural defects than those printed using the PREP powder, which might be explained by the trapped gas pores inside the gas-atomized powder particles as shown in (Zhao et al., Citation2020). However, owing to their high price, PREP powders are currently not widely used for EB-PBF. In addition, gas-atomized powders comprising numerous smaller particles show a higher thermal conductivity than PREP powders (Vock et al., Citation2019); further research efforts are required to figure out whether these small particles and satellites in gas-atomized powders are beneficial for suppressing powder smoking during EB-PBF.
Figure 6. Inconel 718 powders produced by means of Plasma Rotating Electrode Process (PREP) and gas atomization for EB-PBF. The particle size distributions of both powders are comparable (reprinted with permission from (Zhao et al., Citation2020). Copyright Elsevier). (a) and (b): Particle morphology and cross-section of Inconel 718 powders produced by means of different approaches. (c) and (d): Microstructure of EB-PBF-fabricated Inconel 718 parts built under optimal processing conditions and using different powders.
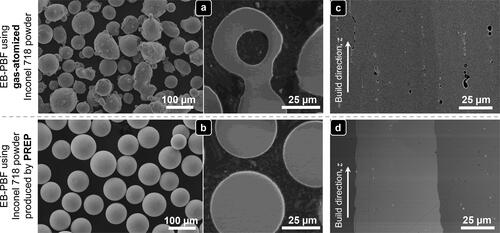
In the course of EB-PBF, only a small fraction of powder is melted and consolidated. As a consequence of the high preheating temperature, the printed parts are surrounded by slightly sintered powder particles. After EB-PBF, the surrounding sintered powder particles have to be removed by means of a powder blasting process using the build powder itself as abrasive media (Hung, Citation2021). Owing to the high feedstock material cost, powder reuse from previous build cycles is an essential step in the whole EB-PBF process chain. After the blasting process, the non-melted but slightly sintered powder particles are sieved to remove agglomerates and reused for the next build jobs. However, during EB-PBF and recycling process (blasting and sieving), the powder undergoes changes in chemical and physical properties owing to thermal and mechanical impact (Shanbhag & Vlasea, Citation2021). It is well known that the oxygen content of powders increased after each EB-PBF and recycling process (Montelione et al., Citation2020; Sun, Aindow, & Hebert, Citation2018; Tang et al., Citation2015). On the one hand, the surface oxidation of the reused powders could be attributed to the trace amount of residual oxygen and humidity in the vacuum chamber. On the other hand, the formation of surface oxides and hydroxides can take place during blasting and sieving as well as storage, when the powder is exposed to the ambient air at room temperature (Gruber, Citation2019).
During EB-PBF of pure copper, samples produced using powders with a high oxygen level of ∼500 ppm exhibited cracks along grain boundaries and poor mechanical properties (low tensile strength and fracture elongation); while good mechanical performance and crack-free microstructures were observed, when using pure copper powders with a low oxygen content of ∼200 ppm for EB-PBF (Guschlbauer, Burkhardt, Fu, & Körner, Citation2020; Guschlbauer et al., Citation2018). Ledford et al. used three different copper powders with various oxygen contents (Ledford et al., Citation2019): with increasing oxygen amount, the true (skeletal) density of the powders decreased (); simultaneously, more submicron oxides and hydroxides were observed on the powder surface. Moreover, during the melting process of EB-PBF, a significant increase in the partial pressure of H2O vapor was detected, when the oxygen content in the copper powders increased () (Ledford et al., Citation2019). The release of the chemically bonded water at high temperatures is attributed to the thermal degradation of hydroxides trapped in copper powders, according to the following chemical reaction (Binnewies & Milke, Citation1999; Malcolm, Citation1998; Shim & Kim, Citation2004):
Figure 7. (a): Three different copper powders with different oxygen amounts and skeletal densities for EB-PBF (adapted from (Ledford et al., Citation2019) under a CC BY 4.0 license). (b): Residual gas analysis of the copper powders with different oxygen amounts during EB-PBF (Ledford et al., Citation2019). (c): According to TGA under flowing nitrogen, with increasing oxygen amount in copper powders, higher weight loss is observed due to the gas expulsion effect caused by thermal degradation of hydroxides (Ledford et al., Citation2019).
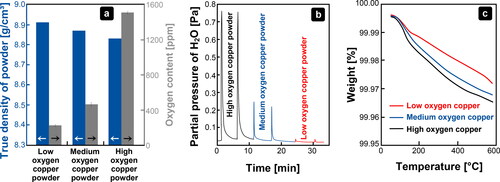
This gas expulsion effect during heating of copper powders was verified utilizing ThermoGravimetric Analysis (TGA) below the melting point () (Ledford et al., Citation2019). According to TGA results, with increasing oxygen amount in copper powders, a slight increase in weight loss at high temperatures was detected (Ledford et al., Citation2019). The gas release effect during EB-PBF induced high melt pool instability, spatter and defects in printed copper parts.
In similarity with the aging effects of copper powders, Gruber et al. observed the formation of Al-rich oxide particulates and a thin oxide/hydroxide layer on the surface of reused Inconel 718 powders, while the virgin Inconel 718 powder showed a clean surface with dendritic structure free of oxide particulates () (Gruber, Citation2019; Gruber, Karimi, Hryha, & Nyborg, Citation2018; Gruber, Luchian, Hryha, & Nyborg, Citation2020). Owing to the long-term exposure to high temperatures (e.g., preheating temperature for Inconel 718 is ∼1000 °C) in the build chamber, selective oxidation of aluminum takes place during EB-PBF, resulting in the formation of Al-rich oxide particulates (Gruber et al., Citation2020). At the same time, with increasing reuse times, the oxygen content in the Inconel 718 powder and in printed objects is significantly enhanced (). It is considered that the oxides and hydroxides on the surface of the reused powders are the sources of non-metallic oxide inclusions inside the EB-PBF-fabricated samples (). These non-metallic inclusions are thought to have negative effects on the mechanical properties of Ni-based superalloys (Gruber, Citation2019). Nevertheless, Guo et al. (Guo, Chen, Wang, & Liu, Citation2021) reported that although a significant increase in oxygen content of reused tantalum powders was observed, the yield and tensile strength values of EB-PBF-built tantalum fabricated using fresh and aged powders are comparable. For the case of EB-PBF of Ti-6Al-4V, oxygen content, elastic modulus, yield and tensile strength of built parts rose lineally with reuse cycle number, while the fracture elongation dropped (Schur et al., Citation2021; Shanbhag & Vlasea, Citation2020; Sun et al., Citation2018; Tang et al., Citation2015); i.e., high oxygen content contributes to enhancing the strength and brittleness of EB-PBF-processed titanium alloys. As reported by Pauzon et al. (Pauzon et al., Citation2021), for the case of titanium-based alloys, the increase in mechanical strength and brittleness with increasing oxygen content can be explained by the high solubility of oxygen in α-Ti (interstitial atom, oxygen solubility up to 33 at.%), providing solid solution strengthening of titanium alloys. In addition, aged Ti-6Al-4V powders showed a less spherical particle shape, a narrower particle size distribution and fewer satellite particles as well as better flowability after several EB-PBF process cycles (Tang et al., Citation2015).
Figure 8. Aging effects of Inconel 718 powder after EB-PBF process cycles (adapted from (Gruber, Citation2019; Gruber et al., Citation2018; Gruber et al., Citation2020) under a CC BY 4.0 license). (a): Particle shape and surface morphology of virgin and reused Inconel 718 powders; and schematic illustration of the formation of oxide particulates on the powder surface after reuse. (b): Oxygen level in reused powders and in as-built parts printed using different aged powders. (c): Network of Al-rich oxides and defects observed in EB-PBF Inconel 718 parts printed using a 30 times reused powder.
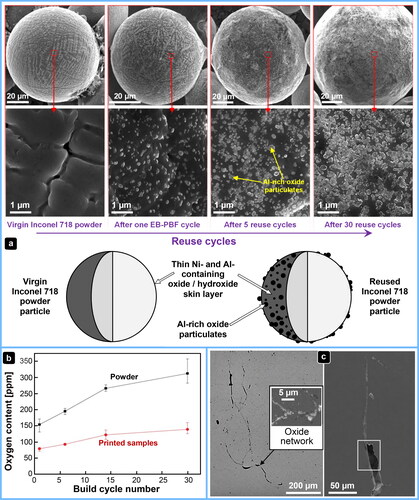
6. EB-PBF materials
In the authors’ previous review article published in 2016, several EB-PBF material systems have been introduced (Körner, Citation2016). In the last five years, remarkable growth and significant achievements have been witnessed in the research and development of new EB-PBF materials. The most common materials used for EB-PBF are weldable. However, EB-PBF can make non-weldable material processable, owing to the high powder bed temperature (e.g., higher than the brittle to ductile transition temperature of the material) reducing thermal stress and risk of crack. As a consequence of the high cooling rates, the microstructures and the mechanical performance of the EB-PBF-derived components could be different from those produced by means of conventional processing methods.
In the following sections, the recent research activities in developing new EB-PBF materials (e.g., Section 6.1 for intermetallics, Section 6.2 for nickel-based alloys, Section 6.3 for multi-materials, Section 6.4 for refractors, Section 6.5 for high entropy alloys, Section 6.6 for Copper-based alloys, Section 6.7 for aluminum-based alloys and Section 6.8 for magnetic materials) and their properties after EB-PBF as well as after post treatments are introduced. A brief overview is summarized in . Since new developments in the realm of EB-PBF never cease and are taking place each passing day, not all EB-PBF materials are listed in and in the following sections (e.g., Iron- and Co-based alloys, which have been detailed in the authors’ previous review article, are not involved).
Table 4. Overview of recently studied material for EB-PBF.
6.1. Intermetallics
Intermetallic compounds consisting of two or more metal elements show unique properties that are different from those of the constituent elements (Gschneidner et al., Citation2003; Nakamura, Citation1995). Compared to conventional metal alloys based on solid solutions, in which the atom position of the constituent elements is randomly distributed in a crystal lattice and the atoms are bonded by relatively weak metallic bonds, intermetallics are characterized by strong covalent and ionic bonds and by long-range-ordered crystal structures with a fixed distribution of atomic positions (George, Yamaguchi, Kumar, & Liu, Citation1994). The long-range-ordered superlattice in intermetallics can be kept up to a high critical temperature, leading to high strength and good creep resistance at elevated temperatures (George et al., Citation1994; Jiao, Luan, & Liu, Citation2016; Mitra & Wanhill, Citation2017; Yamaguchi, Inui, & Ito, Citation2000). Thus, intermetallics are predestined for high-temperature applications, especially in the aerospace and automotive industries (Stoloff, Liu, & Deevi, Citation2000). However, the long-range-ordered crystal structures and the strong chemical bonding reduce dislocation mobility, hinder diffusion processes and result in high brittleness and poor fracture toughness (George et al., Citation1994). Conventional methods to fabricate intermetallics are very complicated and are usually based on investment casting followed by hot isostatic pressing and heat treatments (Bünck, Stoyanov, Schievenbusch, Michels, & Gußfeld, Citation2017). In addition, owing to low process temperatures and the high material brittleness, intermetallics can easily crack, if processed with L-PBF. So far, using EB-PBF that enables high preheating temperatures of more than 1000 °C, dense and crack-free TiAl, NiTi and FeAl have been successfully processed (Adler, Z, & Koerner, Citation2020; Dutkiewicz et al., Citation2020; Dzogbewu, Citation2020; Lin & Chen, Citation2021).
Titanium aluminide is a very promising material to produce turbine blades for jet engines (Chen & Li, Citation2019). Compared to nickel-based superalloys, which are being widely used as turbine blade material, titanium aluminide shows comparable mechanical properties at high temperatures, but much lower specific weight, which is beneficial for saving fuel (Gebisa & Additive, Citation2018). In 2007, Cormier et al. reported the first preliminary attempt to produce dense TiAl parts using an Arcam S12 EB-PBF system and a pre-alloyed Ti-47Al-2Cr-2Nb (at.%) powder (Cormier, Harrysson, Mahale, & West, Citation2007). The addition of Cr and refractory Nb to the binary titanium aluminide system can enhance the material ductility and high-temperature strength, respectively (Appel, Paul, & Oehring, Citation2011; Huang & Hall, Citation1991). After thirteen years of process investigation and material test, the new Boeing 777X aircraft equipped with a GE9X jet engine, which uses Ti-48Al-2Cr-2Nb (at.%) turbine blades produced by means of EB-PBF, has successfully completed its first flight in 2020 (Blakey-Milner et al., Citation2021). According to Todai et al. (Todai et al., Citation2017) and Seifi (Seifi et al., Citation2017), Ti-48Al-2Cr-2Nb (at.%) produced employing EB-PBF showed higher room temperature strength and smaller grain size (due to rapid solidification) than that prepared by conventional casting process; the high-temperature strength of EB-PBF-built Ti-48Al-2Cr-2Nb (at.%) was comparable to that of cast titanium aluminide (Lin & Chen, Citation2021). The operating temperature of Ti-48Al-2Cr-2Nb (at.%) as low-pressure turbine blades is limited to ∼700 °C (Kim & Kim, Citation2018; Reith, Franke, Schloffer, & Körner, Citation2020). In order to further increase the operating temperature, new TNM-B1 (Ti-43.5Al-4Nb-1Mo-0.1B (at.%)) has been developed and produced by conventional isothermal forging to manufacture turbine blades being currently deployed in PW1100G engines (Dzogbewu, Citation2020). The presence of boron in TNM-B1 results in the formation of boride precipitations, which can limit grain coarsening during solidification and during heat treatments owing to grain boundary pinning effects (Appel et al., Citation2011; Clemens et al., Citation2008). Recently, EB-PBF of TNM-B1 with a relative density of ∼99.9% has been achieved using appropriate process parameters (Bieske, Franke, Schloffer, & Körner, Citation2020; Moritz et al., Citation2021). An insufficient energy input leads to the formation of defects (pores, lack of fusion), while excessive energy input induces strong aluminum evaporation, which significantly affects the microstructural feature and mechanical performance (Moritz et al., Citation2021). In order to correct the composition of final built parts and to counteract the aluminum evaporation effect during EB-PBF, slightly excessive aluminum can be added to the pre-alloyed powder feedstock. However, the aluminum evaporation effects can be intentionally used to control the local composition at the spots, where targeted energy input is applied. Zhou et al. (Zhou, Li, et al., Citation2019) successfully tailored the local chemical composition and microstructure as well as mechanical properties by means of selective evaporation of Al during EB-PBF using a pre-alloyed Ti-47Al-2Cr-2Nb (at.%) powder. In addition to Ti-48Al-2Cr-2Nb (at.%) and TNM-B1, whose compositions were originally developed to suit conventional processing technologies (e.g., casting and forging), novel Ti-47.5Al-5.5Nb-0.5W (at.%) has been proposed especially for EB-PBF (Wildheim and Stephansen, Citation2021; Reith et al., Citation2020). As a consequence of the relatively high Al amount, an improvement in room temperature ductility is expected (Reith et al., Citation2020). Furthermore, the addition of W and a high amount of Nb is thought to benefit mechanical properties at high temperatures (Wildheim and Stephansen, Citation2021; Reith et al., Citation2020). Reith et al. (Reith et al., Citation2020) reported that Ti-47.5Al-5.5Nb-0.5W (at.%) produced using EB-PBF followed by Hot Isostatic Pressing (HIP) showed homogeneous microstructures and isotropic mechanical properties at various temperatures. According to Reith et al., the high-temperature yield and tensile strength of EB-PBF-processed and HIPed Ti-47.5Al-5.5Nb-0.5W (at.%) are comparable to those of EB-PBF-built Ti-48Al-2Cr-2Nb (at.%) and TNM-B1 fabricated by casting and HIP (Reith et al., Citation2020); while the room temperature strength and fracture elongation of Ti-47.5Al-5.5Nb-0.5W (at.%) (EB-PBF + HIP) are beyond those of Ti-48Al-2Cr-2Nb (at.%) (EB-PBF) and TNM-B1 (casting + HIP). In , the room temperature mechanical properties of titanium aluminide parts with different compositions and produced using various approaches are sumarized (Reith et al., Citation2020). With the deepening of process and material development, PB-EBF has a high potential to replace other processing approaches to fabricate flawless titanium aluminide with desired mechanical properties. Besides titanium aluminide, EB-PBF of dense and crack-free intermetallic iron aluminide Fe-28Al-5Ti-1.3B (at.%) based on Fe3Al phase with high hardness, good wear and oxidation resistance has been investigated (Adler et al., Citation2020). The alloying of titanium in iron aluminide enhances the material strength via solid solution hardening (Adler et al., Citation2020). Owing to the high cooling rate inherent to the process and the presence of boron in the feedstock, the EB-PBF-fabricated iron aluminide showed a fine-grained microstructure (Adler et al., Citation2020). Compared to cast reference samples, the as-built samples without post heat treatment exhibited higher yield strength between room temperature and 400 °C (Adler et al., Citation2020).
Figure 9. Yield strength and fracture elongation of different titanium aluminide components tested at room temperature in different directions (Biamino et al., Citation2011; Reith et al., Citation2020; Schwaighofer et al., Citation2014; Todai et al., Citation2017) (reprinted with permission from (Reith et al., Citation2020). Copyright Elsevier).
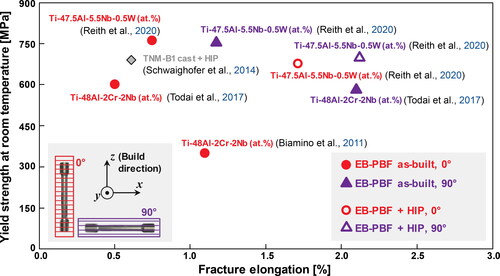
Titanium nickel (nitinol) known as shape memory alloy is characterized by its capability of returning to the original shape owing to a reversible solid-state phase transformation between martensitic and austenitic crystal structures under external thermal or mechanical stimuli (Farber, Zhu, Popovich, & Popovich, Citation2020; Kumar, Shivashankar, & Gopalakrishnan, Citation2020). The temperature-induced and mechanical load-caused shape recovering behaviors are referred to as shape memory effect and superelastic (or pseudo-elastic) effect, which make NiTi as a promising functional material being widely used in medical fields (e.g., as stents) and in microelectromechanical systems (e.g., as microactuators) (Kumar et al., Citation2020). The first trial of EB-PBF of nitinol was performed by Hayat et al. (Hayat et al., Citation2018) in 2017 using a commercial Arcam system and a pre-alloyed powder; nevertheless, the first EB-PBF-built nitinol samples did not show the shape memory effect owing to the presence of undesired Ni3Ti and NiTi2 phases resulting from the high preheating temperature during EB-PBF (Hayat et al., Citation2018). Wang et al. (Wang, Tan, et al., Citation2019) used a powder blend (Ni + Ti powder) for EB-PBF. The preheating stage during EB-PBF induced an exothermic reaction between Ni and Ti causing self-propagating combustion and strong sintering of the whole powder bed (Wang, Tan, et al., Citation2019). Thus, according to Wang et al. (Wang, Tan, et al., Citation2019), feedstock composed of elemental powders is not suitable for EB-PBF of nitinol. In 2019, Zhou et al. produced NiTi with columnar-grained microstructures by means of EB-PBF at a powder bed temperature of 750 °C and using a pre-alloyed PREP powder composed of Ni-48.7Ti (at.%) (Zhou, Li, et al., Citation2019). Owing to the evaporation of Ni during EB-PBF, the final printed samples showed a chemical composition of Ni-49.4Ti (at.%) (Zhou, Li, et al., Citation2019). The as-printed NiTi exhibited superelasticity at room temperature (Zhou, Li, et al., Citation2019). In order to achieve the desired shape memory effect, further research work is needed to precisely control the composition, microstructures as well as phases and precipitates, which significantly depend on the thermal history during EB-PBF and can be affected by post heat treatments.
6.2. Nickel-based alloys
Nickel-based superalloys are characterized by excellent high-temperature strength, high resistance to oxidation and creep deformation at elevated temperatures (Graybill et al., Citation2018; Sanchez et al., Citation2021). Currently, they are being widely used in the aerospace industry as turbine blades with complex geometries (Sanchez et al., Citation2021). So far, different weldable and non-weldable nickel-based superalloys free of cracks have been successfully processed using EB-PBF (). In addition, the effect of process parameters on microstructural properties and mechanical performance of nickel-based superalloys is intensively investigated (Helmer, Bauereiß, Singer, & Körner, Citation2016; Kirka, Greeley, Hawkins, & Dehoff, Citation2017; Raghavan et al., Citation2016). When using different appropriate scan strategies, an isotropic microstructure with Equiaxed Grains (EG) or a textured microstructure with Columnar Grains (CG) were achieved for Inconel 718 samples produced using EB-PBF. The local microstructural properties, which play an important role in the mechanical properties, can be tailored by controlling the EB-PBF process parameters (Helmer, Citation2017; Helmer et al., Citation2016). The static mechanical properties of EB-PBF-fabricated Inconel 718 with CG and EG were investigated in different directions and at different temperatures (Helmer, Citation2017; Körner, Helmer, Bauereiß, & Singer, Citation2014).
EB-PBF is especially interesting to process non-weldable nickel-based superalloys which are characterized by a high amount of precipitation strengthening (Chauvet, Kontis, et al., Citation2018; Lee, Kirka, Ferguson, & Paquit, Citation2020; Lee et al., Citation2018). These alloys are prone to cold as well as hot cracking during processing. Even if the processing parameters during L-PBF are chosen in a way that the crack formation is suppressed, strain age cracking is observed during subsequent heat treatment (Boswell, Clark, Li, & Attallah, Citation2019; Ghoussoub, Tang, Panwisawas, Németh, & Reed, Citation2020; Risse & Broeckmann, Citation2019; Zhang, Yu, He, et al., Citation2019). The origins of crack formation are the high residual stresses within the material due to the extremely high-temperature gradients in combination with the kinetic suppressed precipitation of the hardening γ’ phase (Chauvet, Kontis, et al., Citation2018; Risse & Broeckmann, Citation2019). Due to the high working temperatures during EB-PBF, the level of residual stresses is much lower. In addition, the γ’ phase appears already in the as-built state (Lim et al., Citation2021). Nevertheless, liquation cracking may still occur (Chandra et al., Citation2021). This phenomenon is strongly coupled with the process strategy and the specific composition of the alloy (Lee et al., Citation2020; Wahlmann, Leidel, Markl, & Körner, Citation2021). Especially, minor elements such as boron, which strongly decrease the solidus temperature are considered to be the cause of liquidation cracking (Chauvet, Kontis, et al., Citation2018; Guo, Chaturvedi, & Richards, Citation2000). In the future, these alloys have to be adapted to the specific AM processing conditions.
Not only columnar and equiaxed grain structures (Haines, Plotkowski, Frederick, Schwalbach, & Babu, Citation2018; Helmer, Citation2017; Helmer et al., Citation2016; Körner et al., Citation2014; Raghavan, Stump, Fernandez-Zelaia, Kirka, & Simunovic, Citation2021), but also single-crystalline CMSX-4, Inconel 718 and Inconel 738 have been derived using appropriate EB-PBF process parameters (Chauvet, Kontis, et al., Citation2018; Gotterbarm, Rausch, & Körner, Citation2020; Körner et al., Citation2018; Li et al., Citation2021; Pistor & Körner, Citation2019; Ramsperger, Singer, & Körner, Citation2016; Ramsperger et al., Citation2015). Körner et al. successfully produced CMSX-4 rods with a poly-crystalline shell and a single-crystalline core using a common snake-like hatching pattern with 90° rotations after each layer (Körner et al., Citation2018; Pistor & Körner, Citation2019). According to EBSD (Electron BackScattered Diffraction) IPF-Z map (Inverse Pole Figure), in the single-crystalline core area, a strong <001> fiber texture parallel to the build direction (z-direction) was observed owing to the directional grain growth induced by temperature gradient during EB-PBF (Körner et al., Citation2018). Furthermore, a preferred <011> secondary orientation along the scan direction is detected in the IPF-Y map (Körner et al., Citation2018). This preferred <011> secondary orientation parallel to the scan direction was consistently observed, regardless of using 90° or 180° layer-wise scan rotations (Fernandez-Zelaia, Kirka, Rossy, Lee, & Dryepondt, Citation2021). The fundamental new mechanism of single crystal formation and the origin of this secondary orientation have recently been identified (Pistor, Breuning, & Körner, Citation2021; Pistor & Körner, Citation2021). In contrast to conventional methods to produce single crystals by the growth of a seed crystal, AM single crystals develop by a combination of grain selection and thermo-mechanical deformation combined with texture formation.
AM single crystals are characterized by an unprecedented homogeneity due to the much finer solidification microstructure (Körner et al., Citation2018; Pistor & Körner, Citation2019). After heat treatments, segregation completely disappeared from view, which is not achievable in cast material (Körner et al., Citation2018). This extremely high homogeneity has positive effects on the properties. Compared to conventional cast and heat-treated CMSX-4, the EB-PBF-built and heat-treated single-crystalline CMSX-4 showed comparable Yield Strength (YS) and Ultimate Tensile Strength (UTS) (). Owing to the homogenous distribution of Rhenium, the undesired TCP phases formed at high temperatures were homogeneously distributed all over the heat-treated EB-PBF CMSX-4 sample (Körner et al., Citation2018; Pistor & Körner, Citation2019). Thus, the heat-treated EB-PBF CMSX-4 exhibited highly reliable mechanical properties and good Low Cycle Fatigue (LCF) behaviors (Körner et al., Citation2018). The dynamic mechanical properties are of particular importance for the rotary components (e.g. turbine blades composed of nickel-based alloys) in aero-engines at high temperatures (Helmer, Citation2017). According to Körner et al. EB-PBF-produced single-crystalline CMSX-4 showed after heat-treatment a superior LCF lifetime compared to heat-treated cast materials (Körner et al., Citation2018). The creep resistance behaviors of the heat-treated EB-PBF-processed single-crystalline CMSX-4 were comparable to those of the heat-treated cast CMSX-4 parts (Körner et al., Citation2018). In addition, the EB-PBF-built and heat-treated single-crystalline CMSX-4 parts with a high microstructural homogeneity showed a significantly improved oxidation resistance compared to their conventional counterparts fabricated by means of Bridgman investment casting and heat treatment (Pistor, Hagen, Virtanen, & Körner, Citation2022; Sengupta et al., Citation1994).
Figure 10. Static mechanical properties of the EB-PBF-processed single-crystalline CMSX-4 in the as-built and heat-treated state as a function of temperature (adapted from (Körner et al., Citation2018) under a CC BY 4.0 license). (a): Yield Strength (YS). (b): Ultimate Tensile Strength (UTS). The tensile direction was parallel to the build direction. The yellow area represents literature data for cast and heat-treated material (Terrazas et al., Citation2016).
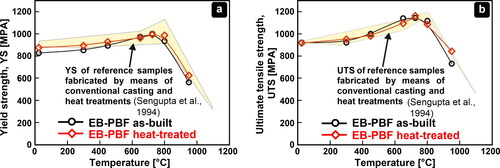
6.3. Multi-materials
Commonly, a pre-alloyed powder with a chemical composition identical to the final printed products is used for EB-PBF to produce samples with uniform properties (Koptyug, Bäckström, Botero, Popov, & Chudinova, Citation2018). However, recent research works reported that EB-PBF showed high potential for in situ alloying powder blends as well as for the fabrication of multi-material composites and even components with a composition gradient (Guo, Ge, & Lin, Citation2015; Katz-Demyanetz, Koptyug, & Popov, Citation2020). The simplest way to fabricate multi-material parts is to print the powder onto a substrate composed of a heterogeneous material, which is in similarity to a joining or cladding process (Zhai et al., Citation2021); e.g., Hinojos et al. (Hinojos et al., Citation2016) and Segura et al. (Segura et al., Citation2019) printed nickel-based objects onto a SS 316L start plate. Another economical and easy approach to produce alloys or composites with desired compositions is to use a powder blend composed of elemental or easily available pre-alloyed powders. In situ alloying of two blended steel-based powders (SS 316L + Colferoloy 103) using EB-PBF has been achieved by Koptyug et al. (Koptyug et al., Citation2020); in the printed samples, microstructural inhomogeneity was observed, which might be explained by the insufficient energy input during melting and the local inhomogeneity of the powder mixture (Koptyug et al., Citation2020). Furthermore, Peng et al. (Peng et al., Citation2016) produced dense and crack-free composite materials with excellent mechanical properties on an Arcam machine using a powder blend composed of 35 wt% Ni-B-Si and 65 wt% WC; the as-built composites showed a homogenous distribution of WC in a Ni-based metal matrix (Peng et al., Citation2016). In addition, EB-PBF of Ti-Ta alloys (Celebi, Gulizia, Doblin, Fraser, & Prentice, Citation2020), Ti-Nb alloys (Surmeneva et al., Citation2020) and Ti-6Al-4V + hydroxyapatite composites (Terrazas et al., Citation2019) for biomedical applications was successfully achieved using appropriate powder blends. However, this approach of using powder blends for EB-PBF would be limited, if strong exothermic reactions (with highly negative enthalpy change) took place during in situ alloying, which could result in self-propagating combustion and a highly sintered powder bed; e.g., as mentioned in Section 6.1, EB-PBF of a powder mixture composed pure Ni and Ti powders was not successful to produce nitinol (Wang, Tan, et al., Citation2019).
In order to reach high microstructural homogeneity and to fabricate compositional gradient materials, Guo et al. developed a special powder feed system for EB-PBF () (Guo et al., Citation2015; W., Lin F, & Guo, Citation2015). Under the action of gravity and vibration, powders (e.g., Ti-47Al-2Cr-2Nb (at.%) and Ti-6Al-4V) in two different hoppers are delivered into an interim box and homogenized as well as fed for EB-PBF (Guo et al., Citation2015). The amounts of different powders delivered into the mixing box can be defined using the appropriate amplitude of the vibration plates beneath the powder hoppers () (Guo et al., Citation2015). Based on this powder feed system, the chemical composition of each layer can be precisely controlled; the as-built Ti-6Al-4V / Ti-47Al-2Cr-2Nb (at.%) samples showed a compositional gradient in the thickness direction (W. et al., 2015). Nevertheless, reuse of the powder bed is, in this case, difficult or impossible.
Figure 11. EB-PBF of multi-materials. (a): Dual-Material feed system with vibration plates and an interim mixing box to define the chemical composition of each raked powder layer and to produce compositional gradient structures (adapted from (Filippov et al., Citation2021) under a CC BY 4.0 license). (b): Special material feed system combining wire-feed and powder-bed to fabricate lamellar composites (according to (Koptyug et al., Citation2020). Copyright Elsevier).
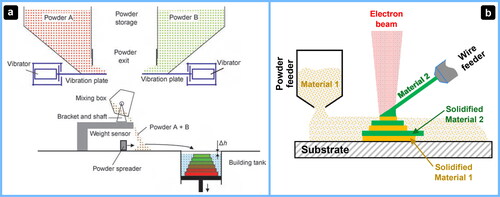
Another muli-material approach is described by Filippov et al. (Filippov et al., Citation2021) where wear-resistant CuAl/B4C multilayer composites are fabricated utilizing a special material feed system combining wire feed (CuAl wire) and powder bed (B4C powder); as depicted in . An electron beam is used as a heat source to melt powder or wire, so that the chemical composition of each layer can be different (Filippov et al., Citation2021).
6.4. Refractory materials
Generally, refractories with high melting points are fabricated through powder metallurgy methods, which however limit the geometric complexity (Morales, Aune, Seetharaman, & Grinder, Citation2003; Philips, Carl, & Cunningham, Citation2020). EB-PBF, during which the energy input and absorption are very high, enables extremely high local processing temperatures and high preheating temperatures. Thus, EB-PBF is considered to be one of the most promising AM technologies to produce dense refractory materials with complex geometries (Philips et al., Citation2020).
The feasibility of processing ultra-high temperature ceramic composites using EB-PBF and a powder blend composed of 70 vol% ZrB2 and 30 vol% ZrSi2 has been proved by Jia et al. (Jia et al., Citation2021). Refractory Nb-5W-2Mo-1Zr (wt.%) with a relative density of ∼99% were successfully produced by means of EB-PBF using a pre-alloyed PREP powder (Yang, Huang, Liu, Guo, & Sun, Citation2021). Owing to the high preheating temperature of 950 °C during EB-PBF, the as-built Nb-5W-2Mo-1Zr (wt.%) underwent an in situ heat treatment (Yang et al., Citation2021). Due to the long-term thermal treatment in the lower areas, the as-built Nb-5W-2Mo-1Zr (wt.%) showed a graded increase in the content of precipitates of (Nb, Zr)C and Nb2C from top to bottom (Yang et al., Citation2021). In addition, EB-PBF of pure molybdenum (Fernandez-Zelaia, Kirka, et al., Citation2021), pure tungsten (Dorow-Gerspach et al., Citation2021; Ren et al., Citation2022; Yang et al., Citation2019), pure tantalum (Tang et al., Citation2020) and pure niobium (Terrazas et al., Citation2016) parts with a relative density of ∼99% and nearly free of cracks has been achieved. Recently, Ren et al. (Ren et al., Citation2022) produced tungsten cuboids with a relative density up to 98.93% using a non-spherical tungsten powder (). The EB-PBF-produced pure Mo and W showed an anisotropic microstructure (Dorow-Gerspach et al., Citation2021; Fernandez-Zelaia, Kirka, et al., Citation2021; Ren et al., Citation2022); e.g., Ren et al. (Ren et al., Citation2022) observed columnar grain structures along the build direction in the EB-PBF-built W samples (). The crystallographic texture in the build direction was adjustable, when using different scan parameters during EB-PBF (Dorow-Gerspach et al., Citation2021).
Figure 12. EB-PBF of pure tungsten (adapted from (Ren et al., Citation2022) under a CC BY 4.0 license). (a): Tungsten powder with an irregular particle shape and a particle size ranging between 65 μm and 105 μm used for EB-PBF. (b): Relative density of the tungsten samples produced using various values of volumetric energy density during EB-PBF. (c): Pure tungsten cuboid with a dimension of 15 × 15 × 20 mm³ produced on an Arcam A2X EB-PBF system using a beam power of 900 w, a layer thickness of 50 µm, a hatch distance of 100 µm, a scan speed of 180 mm/s and a volumetric energy density of 1000 J/mm³. The relative density could reach 98.93%. (d): EBSD IPF-Z maps of the EB-PBF-printed pure tungsten with columnar grains.
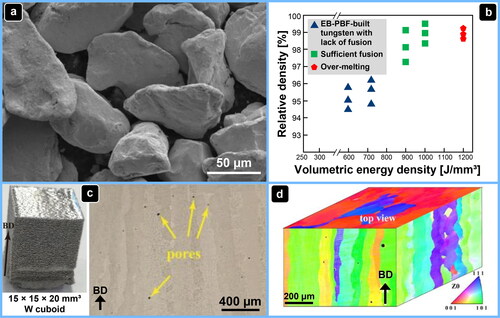
Using EB-PBF and a tantalum PREP powder () with an extremely low oxygen content of ∼90 ppm, Tang et al. fabricated Ta lattice structures showing a minimum diameter of 350 µm for bone implant applications (Tang et al., Citation2020). The EB-PBF-produced tantalum components showed a microstructure with a relative density of ∼99.90% and fine columnar grains (). Owing to the low oxygen content (∼90 ppm), the EB-PBF-printed Ta bulk materials exhibited a fracture elongation of ∼45%, which is significantly higher than the ∼2% fracture elongation of the parts printed by means of L-PBF using a Ta powder with an oxygen content of ∼1800 ppm () (Tang et al., Citation2020). shows a typical stress-strain curve in a three-point bending test of an EB-PBF-built Ta lattice structure with an open porosity of ∼75%. After the bending test, no microcracks were detected according to microstructure analysis, even when the sample was bent over 90° () (Tang et al., Citation2020). This high ductility of EB-PBF-fabricated tantalum with low oxygen content ensures its application as implants, which can sustain damage without producing debris (Tang et al., Citation2020). Currently, EB-PBF-produced Ta bone implants are being widely tested and used in vivo (Tang et al., Citation2020).
Figure 13. EB-PBF of pure tantalum (reprinted with permission from (Tang et al., Citation2020). Copyright Springer Nature). (a):Pure Ta powder with a low oxygen content of ∼90 ppm and a highly spherical particle shape produced by means of PREP. (b):Left: Microstructure of EB-PBF-printed Ta bulk materials with a relative density of ∼99.90% and columnar grains. Right: Room temperature mechanical properties (ultimate tensile strength, yield strength and fracture elongation) of Ta produced by means of EB-PBF (Konyashin et al., Citation2019) and L-PBF (Jiang et al., Citation2021). (c): Three-point bending test of an EB-PBF-built Ta lattice structure with a porosity of ∼75%. (d): After the bending test, the EB-PBF-built Ta lattice structure was bent over 90° and showed no cracks.
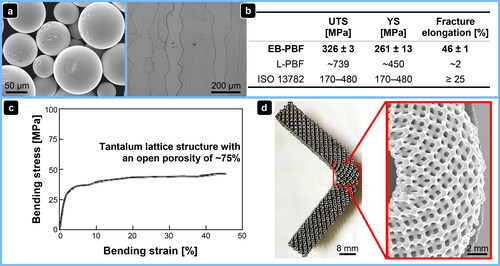
6.5. High entropy alloys (HEA)
Since the proposal of HEA at the beginning of the 2000s, this topic attracts increasing attention and research interest (George, Raabe, & Ritchie, Citation2019; Yeh, Citation2013; Yeh et al., Citation2004; Zhou et al., Citation2017). According to Yeh et al. (Yeh, Citation2013; Yeh et al., Citation2004), HEA are alloys composed of five or more multi-principal elements with near-equimolar ratios. The high mixing entropy of the constituent elements contributes to stabilizing the formation of simple solid solution phases in HEA, such as FCC or BCC structures (George et al., Citation2019; Yeh, Citation2013; Yeh et al., Citation2004). It has been reported that some HEAs simultaneously show high strength due to the solid solution strengthening and good ductility owing to the good dislocation mobility in the simple cubic crystal structures (Chen, Tong, & Liaw, Citation2018; Han et al., Citation2020).
The first attempt to print HEA by means of EB-PBF was carried out by Fujieda et al. in 2015 using a pre-alloyed gas-atomized Al-Co-Cr-Fe-Ni powder (Fujieda et al., Citation2015). As a consequence of the in situ heat treatment inherent to EB-PBF, the lower regions of the as-built Al-Co-Cr-Fe-Ni HEA underwent a long-term thermal treatment and showed coarser grain structures as well as more FCC precipitates located at grain boundaries (Fujieda et al., Citation2015; Kuwabara et al., Citation2018; Shiratori et al., Citation2016). Compared to Al-Co-Cr-Fe-Ni HEA produced through conventional casting, the EB-PBF-built samples exhibited significantly higher compressive strength and ductility owing to the much smaller grain size resulting from high cooling rates during EB-PBF (Fujieda et al., Citation2015; Kuwabara et al., Citation2018; Shiratori et al., Citation2016). The EB-PBF-produced Al-Co-Cr-Fe-Ni showed fine columnar grain structures with a < 001> fiber texture parallel to the Build Direction (BD), leading to anisotropic mechanical properties (Fujieda et al., Citation2015; Kuwabara et al., Citation2018; Shiratori et al., Citation2016).
In addition, another Co-Cr-Fe-Mn-Ni high entropy alloy was processed by Wang et al. using EB-PBF and a pre-alloyed powder (Wang, Tan, et al., Citation2019). The as-built Co-Cr-Fe-Mn-Ni specimens exhibited a relative density of ∼99.4% and a columnar microstructure (Wang, Tan, et al., Citation2019). Based on that work, Cagirici et al. successfully printed parts composed of Co-Cr-Fe-Mn-Ni- n Ti (n = 0.18 mol.%, 0.50 mol.% and 2.00 mol.%, in molar %) utilizing a powder blend containing pre-alloyed Co-Cr-Fe-Mn-Ni powder and pure Ti powder (Cagirici et al., Citation2021). The as-printed Co-Cr-Fe-Mn-Ni- n Ti produced by in situ alloying during EB-PBF showed a good chemical homogeneity (Cagirici et al., Citation2021). The EB-PBF-built Co-Cr-Fe-Mn-Ni-0.18Ti specimens were free of cracks, while surface cracks were observed in the case of EB-PBF of Co-Cr-Fe-Mn-Ni-0.5Ti and Co-Cr-Fe-Mn-Ni-2Ti (Cagirici et al., Citation2021). Compared to the EB-PBF-built Co-Cr-Fe-Mn-Ni (Wang, Tan, et al., Citation2019), the in situ alloyed Co-Cr-Fe-Mn-Ni-0.18Ti (Cagirici et al., Citation2021) exhibited significantly higher hardness owing to the presence of strong secondary phases caused by the addition of Ti. Additionally, Popov et al. (Popov, Katz-Demyanetz, Koptyug, & Bamberger, Citation2019) reported the EB-PBF of Al-Cr-Mo-Nb-Ta using blended elemental powders. During EB-PBF, notable Al evaporation was detected, resulting in a reduction of Al content in the final printed samples (Popov et al., Citation2019). The as-built Al-Cr-Mo-Nb-Ta parts showed a high level of residual porosity that according to Popov et al. could be reduced or eliminated when optimizing process parameters (Popov et al., Citation2019).
6.6. Copper-based alloys
The research activities in EB-PBF of pure copper have been introduced in the authors’ previous review article (Körner, Citation2016). Owing to the high energy absorbance, EB-PBF of pure copper shows various advantages over L-PBF (Bourell, Frazier, Kuhn, & Seifi, Citation2020; Guschlbauer et al., Citation2020; Jiang et al., Citation2021). Based on recent research results, EB-PBF-built pure copper parts have reached a relative density of ∼99.9% and electrical conductivity of 58 MS/m (100% International Annealed Copper Standard) (Raab, Guschlbauer, Lodes, & Körner, Citation2016). Yield and tensile strength as well as fracture elongation of EB-PBF-built copper are comparable to those of rolled and annealed copper (), when using a pure copper powder with a low oxygen content of less than 250 ppm as feedstock (Guschlbauer et al., Citation2020). shows an exemplary component composed of pure copper produced using EB-PBF by Ledford et al. (Ledford et al., Citation2020). If the oxygen content of the initial copper powder used for EB-PBF exceeds a certain level, crack formation along grain boundaries due to the formation of copper oxides could be observed (Guschlbauer et al., Citation2020). Thus, EB-PBF of pure copper demands a careful control of the oxygen level of the powders.
Figure 14. (a): EB-PBF of copper using a pure gas-atomized copper powder with a low oxygen content of ∼250 ppm. Anisotropic mechanical properties of EB-PBF-produced copper (Guschlbauer et al., Citation2020). Dotted lines indicate the tensile and yield strength as well as the fracture elongation of wrought and annealed copper as reference (reprinted with permission from (Guschlbauer et al., Citation2020). Copyright Elsevier). (b): EB-PBF-printed pure copper part with a complex geometry produced by Ledford et al. (reprinted with permission from (Ledford et al., Citation2020). Copyright Elsevier).
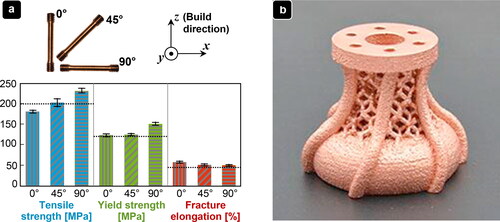
Besides pure copper, various copper-based alloys (e.g., Cu-Cr-Zr (Ordás et al., Citation2021), Cu-Cr (Momeni, Guschlbauer, Osmanlic, & Körner, Citation2018) and Cu-Al (Wolf, Fu, & Körner, Citation2019; Wolf et al., Citation2020)) have been intensively investigated for EB-PBF in the past years. In addition, Cu-Cr, as a pseudo-alloy, in which the constituent elements are miscible as liquids but immiscible in the solid state, has also been successfully processed by means of EB-PBF (Momeni et al., Citation2018). In the microstructure of Cu-25Cr (wt.%) fabricated using EB-PBF and a powder blend (pure copper powder + pure Cr powder), tiny droplet-shaped Cr-rich inclusions with a size of a few hundreds of nanometers are uniformly distributed within a Cu matrix (Momeni et al., Citation2018). A refinement of the Cr phase in the copper matrix could result in enhanced hardness and improved electrical properties (Chen, Ren, Zhao, & Qu, Citation2019; Zhang, Yu, He, et al., Citation2019; Citation2019). Moreover, Periodic Open Cellular Structures (POCS) with dense struts composed of brittle Raney-copper (e.g., Cu-21.5Al (at.%) (Wolf et al., Citation2019) and Cu-70.6Al (at.%) (Wolf et al., Citation2020)) for catalytic applications in chemical reaction engineering have been built utilizing EB-PBF (). After selective leaching of aluminum in a NaOH solution, Catalytic Active Periodic Open Cellular Structures (CAPOCS) containing core-shell structured struts with a nanoporous copper skin layer and a solid core were derived ( b) (Wolf et al., Citation2020). The EB-PBF-processed and selectively leached Raney-copper CAPOCS showed good catalytic activity in methanol synthesis (Wolf et al., Citation2020). The nanoporous skin layer exhibits a high reaction surface area, while the unreacted core ensures sufficient mechanical stability for the reactor application and improves heat transfer () (Wolf et al., Citation2020).
Figure 15. EB-PBF of Raney-copper composed of Cu-70.6Al (at.%) (adapted from (Wolf et al., Citation2020) under a CC BY 4.0 license). (a): CT-cutaway reconstruction of an EB-PBF-processed POCS with dense struts in the as-built state. (b): Microstructure of the cross-section of a dealloyed strut with a nanoporous copper skin layer and a solid core; the inset shows copper ligaments and channels in the nanoporous skin area.

6.7. Aluminum-based alloys
Lightweight aluminum-based alloys are being widely used as structural materials in automotive and aviation industries owing to their high strength-to-weight ratio (Alam & Ansari, Citation2017; Jawalkar & Kant, Citation2015; Kenevisi, Y, & Lin, Citation2021; Vijayakumar, Dhinakaran, Sathish, & Muthu, Citation2021). As the most common way for AM of aluminum-based alloys, L-PBF is extensively investigated to produce various eutectic and near-eutectic aluminum-based alloys, which are less susceptible to hot cracking (Hyer et al., Citation2021). Recently, owing to high energy absorbance, low level of the residual stress of printed parts and vacuum process environment, EB-PBF has been successfully used for AM of high strength aluminum alloys; e.g., EB-PBF of fully dense, crack-free Al2024 (Kenevisi & Lin, Citation2020; Citation2021) and AlSi10Mg (Bian et al., Citation2020) with equiaxed-grained microstructures have been achieved by Kenevisi et al. and Bian et al., respectively, using gas atomized pre-alloyed powders. Nevertheless, owing to evaporation effects during EB-PBF under controlled vacuum conditions, less content of volatile alloy elements (e.g., Al, Mg, Mn etc.) was observed in the as-printed samples compared to that in the initial powdered feedstock (Bian et al., Citation2020; Radulov et al., Citation2019). The evaporation effects in the course of EB-PBF could be reduced by elevating the partial pressure of helium in the vacuum chamber, which however might enlarge the size of the electron beam, resulting in a poorer printing accuracy. In addition, to correct the final composition of the as-built specimens, more amount of volatile constituent elements could be added to the feedstock.
6.8. Magnetic materials
In the last few years, L-PBF of magnetic materials with complex geometries has been extensively investigated (Chaudhary, Mantri, Ramanujan, & Banerjee, Citation2020; Mikler et al., Citation2017; Pham, Kwon, & Foster, Citation2021). Silicon steel (Fe-3Si (wt.%)) showing good saturation magnetization, low coercivity, high permeability as well as relatively good processability is one of the most common soft magnetic materials, which are currently used in almost every electric machine and are easy to be magnetized and demagnetized (Chaudhary et al., Citation2020). For industrial applications, high electrical resistivity of soft magnetic materials is additionally required to reduce power losses caused by eddy current. Thus, high silicon steel Fe-6.5Si (wt.%) with high electrical resistivity has been developed in the last decades at the expense of slightly reducing saturation magnetization (Yang, Fu, Ye, Kübrich, & Körner, Citation2022). In addition, with increasing Si content in the Fe-Si alloy, the ductility and processability significantly decrease. Thus, when using conventional approaches (e.g., rolling and forging) to fabricate Fe-Si soft magnetic materials, Si content is commonly limited. L-PBF-produced Fe-6.5Si-0.5Ni (wt.%) either showed a porose microstructure or microcracks reducing the mechanical stability of the printed samples (Kang et al., Citation2018). Recently, Yang et al. fabricated crack-free and dense Fe-6.5Si (wt.%) by means of EB-PBF at a powder bed temperature of ∼900 °C on a Freemelt ONE machine (Yang et al., Citation2022). Porous and dense Fe-6.5Si (wt.%) produced through EB-PBF exhibited different electrical and magnetic properties as well as various values of power losses, which can be tailored using different process parameters (Yang et al., Citation2022). Besides soft magnetic materials, Radulov et al. (Radulov et al., Citation2019) produced fully dense Al-Mn permanent magnets by means of EB-PBF using a powder that was ball-milled from cast Al-53Mn (wt.%) ingots. In the initial cast Al-Mn alloy for the powder production, 3 wt.% more Mn was supplementarily added to compensate for the evaporation loss of Mn during EB-PBF (Radulov et al., Citation2019). The EB-PBF-built Al-Mn permanent magnets showed good magnetic properties after heat treatments (Radulov et al., Citation2019).
7. New developments
In the last two decades, all the EB-PBF machines, which have been developed, are characterized by the fact that the acceleration voltage is 60 kV, see . Why? The use of higher acceleration voltages is more expensive, the machines are larger and a better shielding of the machine is also necessary. Nevertheless, there are strong physical reasons why higher accelerations voltages (e.g., 120 or 150 kV) are highly interesting and might solve some persistent problems such as the smoke phenomenon or selective evaporation:
At the same power, less charge is necessary. For example, the use of 150 kV instead of 60 kV will reduce the charge by a factor of 2.5;
The penetration depth of the electrons increases with increasing acceleration voltage (Klassen et al., Citation2014). As a consequence, the energy is deposited deeper within the material and the maximum surface temperature strongly decreases;
At higher acceleration voltage, fewer secondary electrons are generated (Reimer, Citation2000).
All these properties appear to be positive for process stability. The number of electrons is expected to be reduced and evaporation, which we assume to initiate smoke, is strongly suppressed. Both effects will have a positive impact on process stability and quality. Thus, we suppose that the use of higher acceleration voltages in EB-PBF has great potential for the future.
8. Summary and outlook
Electron Beam Powder Bed Fusion (EB-PBF) is a very promising additive manufacturing technology, especially suited for producing high-performance metallic components being hard to be processed using other fabrication approaches. Compared to its sister technology (the more mature laser powder bed fusion process), EB-PBF shows unique features and advantages. In the last five years, considerable efforts have been made in the field of machine, process and material development for EB-PBF, both in industry and academia. In this article, recent research activities since 2016 in the realm of EB-PBF have been recapped. In order to further exploit the potential of EB-EBP, the current and future research focuses are summarized as follows:
Better process observation and control via further development and optimization of different process monitoring technologies; especially, the electron-optical imaging system, which is not affected by any temperature and metal vaporization effects, is thought to be one of the most promising in situ monitoring approaches for EB-PBF;
Development of new powdered feedstocks (e.g., in situ alloying using powder blends); control of the quality of (reused) powders; investigation of the powder reuse and its influence on the properties of the printed components;
Deeper understanding of the interactions between the electron beam and materials to completely avoid the powder smoke phenomenon;
Tailoring microstructural properties by adapting processing parameters;
Widening material systems and exploiting new materials for EB-PBF;
New machine concepts with a higher acceleration voltage.
Acknowledgments
The authors wish to thank Ms. Jing Yang, Mr. Daniel Gage, Mr. Christopher Arnold, Mr. Jakob Renner and Mr. Jihui Ye at the University of Erlangen-Nuremberg for their contributions in form of pictures and knowledge.
Disclosure statement
The authors declare that they have no known competing financial interests or personal relationships that could have appeared to influence the work reported in this article.
Additional information
Funding
References
- Ackelid, U. (2015). Method and apparatus for increasing the resolution in additively manufactured three-dimensional articles. US9079248B2.
- Ackelid, U. (2017). Method for additive manufacturing. US20170341142A1.
- Ackelid, U., & Additive, S. M. (2009). Active manufacturing of dense metal parts by Electron Beam Melting. In European International Powder Metallurgy Congress and Exhibition, Euro PM 2009. France: European Powder Metallurgy Association (EPMA).
- Adler, L., Z, F., & Koerner, C. (2020). Electron beam based additive manufacturing of Fe3Al based iron aluminides—Processing window, microstructure and properties. Materials Science and Engineering: A, 785, 139369.
- Alam, T., & Ansari, A. H. (2017). Review on aluminium and its alloys for automotive applications. International Journal of Advanced Technology in Engineering and Science, 5, 278–294.
- Almeida, H., & Vasco, J. (2019). Expectations of additive manufacturing for the decade 2020–2030 [Paper presentation]. In International Conference of Progress in Digital and Physical Manufacturing. Nature Switzerland AG: Springer.
- Appel, F., Paul, J. D. H., & Oehring, M. (2011). Gamma titanium aluminide alloys: Science and technology. Weinheim, Germany: Wiley.
- Arnold, C., & Körner, C. (2021). In-situ electron optical measurement of thermal expansion in electron beam powder bed fusion. Additive Manufacturing, 46, 102213. https://doi.org/10.1016/j.addma.2021.102213.
- Arnold, C., Böhm, J., & Körner, C. (2020). In Operando Monitoring by Analysis of Backscattered Electrons during Electron Beam Melting. Advanced Engineering Materials, 22(9), 1901102. https://doi.org/10.1002/adem.201901102.
- Arnold, C., Pobel, C., Osmanlic, F., & Körner, C. (2018). Layerwise monitoring of electron beam melting via backscatter electron detection. Rapid Prototyping Journal, 24(8), 1401–1406. https://doi.org/10.1108/RPJ-02-2018-0034.
- Azam, F. I., Rani, A. M. A., Altaf, K., Rao, T., & Zaharin, H. A. (2018). An In-Depth Review on Direct Additive Manufacturing of Metals. [Paper presentation]. IOP Conference Series: Materials Science and Engineering, United Kingdom: IOP Publishing.
- Bhavar, V., Kattire, P., Patil, V., Khot, S., Gujar, K., & Singh, R. (2014). A review on powder bed fusion technology of metal additive manufacturing.
- Biamino, S., Penna, A., Ackelid, U., Sabbadini, S., Tassa, O., Fino, P., Pavese, M., Gennaro, P., & Badini, C. (2011). Electron beam melting of Ti–48Al–2Cr–2Nb alloy: Microstructure and mechanical properties investigation. Intermetallics, 19(6), 776–781. https://doi.org/10.1016/j.intermet.2010.11.017.
- Bian, H., Aoyagi, K., Zhao, Y., Maeda, C., Mouri, T., & Chiba, A. (2020). Microstructure refinement for superior ductility of Al–Si alloy by electron beam melting. Additive Manufacturing, 32, 100982.
- Bidare, P., Bitharas, I., Ward, R. M., Attallah, M. M., & Moore, A. J. (2018). Laser powder bed fusion at sub-atmospheric pressures. International Journal of Machine Tools and Manufacture, 130–131, 65–72. https://doi.org/10.1016/j.ijmachtools.2018.03.007.
- Bieske, J., Franke, M., Schloffer, M., & Körner, C. (2020). Microstructure and properties of TiAl processed via an electron beam powder bed fusion capsule technology. Intermetallics, 126, 106929.
- Binnewies, M., & Milke, E. (1999). Thermochemical data of elements and compounds. Weinheim: Wiley-VCH.
- Blakey-Milner, B., Gradl, P., Snedden, G., Brooks, M., Pitot, J., Lopez, E., Leary, M., Berto, F., & Du Plessis, A. (2021). Metal additive manufacturing in aerospace: A review. Materials & Design, 110008.
- Boone, N., Zhu, C., Smith, C., Todd, I., & Willmott, J. (2018). Thermal near infrared monitoring system for electron beam melting with emissivity tracking. Additive Manufacturing, 22, 601–605.
- Boswell, J. H., Clark, D., Li, W., & Attallah, M. M. (2019). Cracking during thermal post-processing of laser powder bed fabricated CM247LC Ni-superalloy. Materials & Design, 174, 107793.
- Bourell, D., Frazier, W., Kuhn, H., & Seifi, M. (2020). Additive manufacturing of copper and copper alloys.
- Bünck, M., Stoyanov, T., Schievenbusch, J., Michels, H., & Gußfeld, A. (2017). Titanium aluminide casting technology development. Journal of the Minerals Metals and Materials Society., 69(12), 2565–2570.
- Cagirici, M., Wang, P., Ng, F. L., Nai, M. L. S., Ding, J., & Wei, J. (2021). Additive manufacturing of high-entropy alloys by thermophysical calculations and in situ alloying. Journal of Materials Science & Technology, 94, 53–66.
- Cakmak, E., Nandwana, P., Shin, D., Yamamoto, Y., Gussev, M. N., Sen, I., Seren, M. H., Watkins, T. R., & Haynes, J. A. (2019). A comprehensive study on the fabrication and characterization of Ti–48Al–2Cr–2Nb preforms manufactured using electron beam melting. Materialia, 6, 100284.
- Celebi, A., Gulizia, S., Doblin, C., Fraser, D., & Prentice, L. (2020). Characterization of tantalum–titanium powders with universal powder bed (UPB) system for electron beam melting Process. Russian Journal of Non-Ferrous Metals, 61(3), 346–353.
- Chandra, S., Tan, X., Narayan, R. L., Wang, C., Tor, S. B., & Seet, G. (2021). A generalised hot cracking criterion for nickel-based superalloys additively manufactured by electron beam melting. Additive Manufacturing, 37, 101633.
- Chandra, S., Tan, X., Wang, C., Yip, Y. H., Seet, G., & Tor, S. B. (2018). Additive manufacturing of a single crystal nickel-based superalloy using selective electron beam melting.
- Chaudhary, V., Mantri, S., Ramanujan, R., & Banerjee, R. (2020). Additive manufacturing of magnetic materials. Progress in Materials Science, 114, 100688.
- Chauvet, E., Kontis, P., Jägle, E. A., Gault, B., Raabe, D., Tassin, C., Blandin, J.-J., Dendievel, R., Vayre, B., Abed, S., & Martin, G. (2018). Hot cracking mechanism affecting a non-weldable Ni-based superalloy produced by selective electron Beam Melting. Acta Materialia, 142, 82–94.
- Chauvet, E., Tassin, C., Blandin, J.-J., Dendievel, R., & Martin, G. (2018). Producing Ni-base superalloys single crystal by selective electron beam melting. Scripta Materialia, 152, 15–19.
- Chen, S., Tong, Y., & Liaw, P. K. (2018). Additive manufacturing of high-entropy alloys: a review. Entropy, 20(12), 937.
- Chen, W., & Li, Z. (2019). Additive manufacturing of titanium aluminides. In Additive Manufacturing for the Aerospace Industry (pp. 235–263). Niederland: Elsevier.
- Chen, Y., Ren, S., Zhao, Y., & Qu, X. (2019). Microstructure and properties of CuCr alloy manufactured by selective laser melting. Journal of Alloys and Compounds, 786, 189–197.
- Chen, Y., Yue, H., Wang, X., Xiao, S., Kong, F., Cheng, X., & Peng, H. (2018). Selective electron beam melting of TiAl alloy: Microstructure evolution, phase transformation and microhardness. Materials Characterization, 142, 584–592.
- Chiba, A., Daino, Y., Aoyagi, K., & Yamanaka, K. (2021). Smoke suppression in electron beam melting of Inconel 718 alloy powder based on insulator–metal transition of surface oxide film by mechanical stimulation. Materials, 14(16), 4662.
- Chiba, A., Kudo, T., Daino, Y., & Aoyagi, K. (2021). Powder for metal additive manufacturing, method for producing same, additive manufacturing device, and control program. Patent EP3854501A1.
- Cho, K., Kawabata, H., Hayashi, T., Yasuda, H. Y., Nakashima, H., Takeyama, M., & Nakano, T. (2021). Peculiar microstructural evolution and tensile properties of β-containing γ-TiAl alloys fabricated by electron beam melting (p. 102091). Ohio: Additive Manufacturing.
- Clapeyron, É. (1834). Mémoire sur la puissance motrice de la chaleur. Journal de L’École Polytechnique, 14, 153–190.
- Clausius, R. (1850). Über die bewegende Kraft der Wärme und die Gesetze, welche sich daraus für die Wärmelehre selbst ableiten lassen. Annalen Der Physik Und Chemie, 155(3), 368–397.
- Clayton, J., Millington-Smith, D., & Armstrong, B. (2015). The application of powder rheology in additive manufacturing. Journal of the Minerals Metals and Materials Society., 67(3), 544–548.
- Clemens, H., Wallgram, W., Kremmer, S., Güther, V., Otto, A., & Bartels, A. (2008). Design of novel β-solidifying TiAl alloys with adjustable β/B2-phase fraction and excellent hot-workability. Advanced Engineering Materials, 10(8), 707–713. https://doi.org/10.1002/adem.200800164.
- Cordero, P. M., Mireles, J., Ridwan, S., & Wicker, R. B. (2017). Evaluation of monitoring methods for electron beam melting powder bed fusion additive manufacturing technology. Progress in Additive Manufacturing, 2(1–2), 1–10.
- Cordero, Z. C., Meyer, H. M., Nandwana, P., & Dehoff, R. R. (2017). Powder bed charging during electron-beam additive manufacturing. Acta Materialia, 124, 437–445. https://doi.org/10.1016/j.actamat.2016.11.012.
- Cormier, D., Harrysson, O., Mahale, T., & West, H. (2007). Freeform fabrication of titanium aluminide via electron beam melting using prealloyed and blended powders. Research Letters in Materials Science, 2007, 1–4.
- Cosslett, V. E., & Thomas, R. N. (1965). Multiple scattering of 5–30 keV electrons in evaporated metal films III: Backscattering and absorption. British Journal of Applied Physics, 16(6), 779–796. https://doi.org/10.1088/0508-3443/16/6/303
- Dawes, J., Bowerman, R., & Trepleton, R. (2015). Introduction to the additive manufacturing powder metallurgy supply chain. Johnson Matthey Technology Review, 59(3), 243–256.
- Dehoff, R. R., Kirka, M., Sames, W., Bilheux, H., Tremsin, A., Lowe, L., & Babu, S. (2015). Site specific control of crystallographic grain orientation through electron beam additive manufacturing. Materials Science and Technology, 31(8), 931–938.
- Deng, D., Peng, R. L., Söderberg, H., & Moverare, J. (2018). On the formation of microstructural gradients in a nickel-base superalloy during electron beam melting. Materials & Design, 160, 251–261.
- Di Paola, A. (1989). Semiconducting properties of passive films on stainless steels. Electrochimica Acta, 34(2), 203–210.
- Dorow-Gerspach, D., Kirchner, A., Loewenhoff, T., Pintsuk, G., Weißgärber, T., & Wirtz, M. (2021). Additive manufacturing of high density pure tungsten by electron beam melting. Nuclear Materials and Energy, 28, 101046.
- Dutkiewicz, J., Rogal, Ł., Kalita, D., Węglowski, M., Błacha, S., Berent, K., Czeppe, T., Antolak-Dudka, A., Durejko, T., & Czujko, T. (2020). Superelastic effect in NiTi alloys manufactured using electron beam and focused laser rapid manufacturing methods. Journal of Materials Engineering and Performance, 29(7), 4463–4473.
- Dzogbewu, T. C. (2020). Additive manufacturing of TiAl-based alloys. Manufacturing Review, 7, 35.
- Edinger, R. (2021). Apparatus and method for dispensing powdered material. Patent WO2020028979A1.
- Ellis, E. A., Sprayberry, M. A., Ledford, C., Hankwitz, J. P., Kirka, M. M., Rock, C. D., Horn, T. J., Katoh, Y., & Dehoff, R. R. (2021). Processing of tungsten through electron beam melting. Journal of Nuclear Materials, 555, 153041.
- Eschey, C., Lutzmann, S., & Zaeh, M. (2009). Examination of the powder spreading effect in electron beam melting (EBM). Solid Freeform Fabrication, TX, August, p. 3–5.
- Everton, S. K., Hirsch, M., Stravroulakis, P., Leach, R. K., & Clare, A. T. (2016). Review of in-situ process monitoring and in-situ metrology for metal additive manufacturing. Materials & Design, 95, 431–445.
- Farber, E., Zhu, J.-N., Popovich, A., & Popovich, V. (2020). A review of NiTi shape memory alloy as a smart material produced by additive manufacturing. Materials Today: Proceedings, 30, 761–767.
- Fernandez-Zelaia, P., Kirka, M. M., Rossy, A. M., Lee, Y., & Dryepondt, S. N. (2021). Nickel-based superalloy single crystals fabricated via electron beam melting. Acta Materialia, 216, 117133.
- Fernandez-Zelaia, P., Ledford, C., Ellis, E. A., Campbell, Q., Rossy, A. M., Leonard, D. N., & Kirka, M. M. (2021). Crystallographic texture evolution in electron beam melting additive manufacturing of pure molybdenum. Materials & Design, 207, 109809.
- Filippov, A., Khoroshko, E., Shamarin, N., Savchenko, N., Moskvichev, E., Utyaganova, V., Kolubaev, E., Smolin, A. Y., & Tarasov, S. Y. (2021). Characterization of gradient CuAl–B4C composites additively manufactured using a combination of wire-feed and powder-bed electron beam deposition methods. Journal of Alloys and Compounds, 859, 157824.
- Fomenko, V. S. (2012). Handbook of thermionic properties: Electronic work functions and Richardson constants of elements and compounds. Switzerland AG: Springer.
- Franke, M., & Eichler, S. (2019). Method for additive manufacturing of a component and component manufactured by that method. Patent US20190178086A1.
- Fujieda, T., Shiratori, H., Kuwabara, K., Kato, T., Yamanaka, K., Koizumi, Y., & Chiba, A. (2015). First demonstration of promising selective electron beam melting method for utilizing high-entropy alloys as engineering materials. Materials Letters, 159, 12–15.
- Galati, M., & Iuliano, L. (2018). A literature review of powder-based electron beam melting focusing on numerical simulations. Additive Manufacturing, 19, 1–20. https://doi.org/10.1016/j.addma.2017.11.001.
- Gao, Y., & Zhou, M. (2018). Superior mechanical behavior and fretting wear resistance of 3D-printed Inconel 625 superalloy. Applied Sciences, 8(12), 2439.
- Ge, W., Lin, F, & Guo, C. (2015). Functional gradient material of Ti-6Al-4V and γ-TiAl fabricated by electron beam selective melting. In Solid freeform fabrication symposium. Tsinghua University.
- Gebisa, A. W., & Additive, L. H. G. (2018). Manufacturing for the manufacture of gas turbine engine components: literature review and future perspectives. In Turbo expo: Power for land, sea, and air. New York: American Society of Mechanical Engineers.
- George, E. P., Raabe, D., & Ritchie, R. O. (2019). High-entropy alloys. Nature Reviews Materials, 4(8), 515–534.
- George, E., Yamaguchi, M., Kumar, K., & Liu, C. (1994). Ordered intermetallics. Annual Review of Materials Science, 24(1), 409–451.
- Ghoussoub, J. N., Tang, Y. T., Panwisawas, C., Németh, A., & Reed, R. C. (2020). On the influence of alloy chemistry and processing conditions on additive manufacturability of Ni-based superalloys. In Superalloys (pp. 153–162). Switzerland AG: Springer.
- Gillespie, C. (1974). Electrooptical scanner for monitoring electron beam welds. NASA STI/Recon Technical Report No. 75, 15958.
- Gokuldoss, P. K., Kolla, S., & Eckert, J. (2017). Additive manufacturing processes: selective laser melting, electron beam melting and binder jetting—Selection guidelines. Materials, 10(6), 672.
- Gotterbarm, M. R., Rausch, A. M., & Körner, C. (2020). Fabrication of single crystals through a µ-helix grain selection process during electron beam metal additive manufacturing. Metals, 10(3), 313.
- Grasso, M. L. G., Remani, A., Dickins, A., Colosimo, B. M., & Leach, R. K. (2021). In-situ measurement and monitoring methods for metal powder bed fusion–an updated review. Measurement Science and Technology, 32(11), 112001.
- Grasso, M., Valsecchi, G., & Colosimo, B. M. (2020). Powder bed irregularity and hot-spot detection in electron beam melting by means of in-situ video imaging. Manufacturing Letters, 24, 47–51. https://doi.org/10.1016/j.mfglet.2020.03.011.
- Graybill, B., Li, M., Malawey, D., Ma, C., Alvarado-Orozco, J.-M., & Martinez-Franco, E. (2018). Additive Manufacturing of nickel-based superalloys [Paper presentation]. International Manufacturing Science and Engineering Conference. New York: American Society of Mechanical Engineers.
- Gruber, H. (2019). Electron beam melting of alloy 718 powder recycling and its effect on defect formation. Chalmers Tekniska Hogskola.
- Gruber, H., Karimi, P., Hryha, E., & Nyborg, L. (2018). Effect of powder recycling on the fracture behavior of electron beam melted alloy 718. Powder Metallurgy Progress, 18(1), 40–48.
- Gruber, H., Luchian, C., Hryha, E., & Nyborg, L. (2020). Effect of powder recycling on defect formation in electron beam melted alloy 718. Metallurgical and Materials Transactions A, 51(5), 2430–2443. https://doi.org/10.1007/s11661-020-05674-8
- Gschneidner, K., Russell, A., Pecharsky, A., Morris, J., Zhang, Z., Lograsso, T., Hsu, D., Lo, C. H. C., Ye, Y., Slager, A., & Kesse, D. (2003). A family of ductile intermetallic compounds. Nature Materials, 2(9), 587–591.
- Guo, C., Ge, W., & Lin, F. (2015). Dual-material electron beam selective melting: Hardware development and validation studies. Engineering, 1(1), 124–130.
- Guo, H., Chaturvedi, M., & Richards, N. (2000). Effect of sulphur on hot ductility and heat affected zone microfissuring in Inconel 718 welds. Science and Technology of Welding and Joining, 5(6), 378–384.
- Guo, Y., Chen, C., Wang, Q., & Liu, M. (2021). Effects of reuse on the properties of tantalum powders and tantalum parts additively manufactured by electron beam powder bed fusion. Materials Research Express, 8(4), 046538.
- Guschlbauer, R., Burkhardt, A. K., Fu, Z., & Körner, C. (2020). Effect of the oxygen content of pure copper powder on selective electron beam melting. Materials Science and Engineering: A, 779, 139106. https://doi.org/10.1016/j.msea.2020.139106.
- Guschlbauer, R., Momeni, S., Osmanlic, F., & Körner, C. (2018). Process development of 99.95% pure copper processed via selective electron beam melting and its mechanical and physical properties. Materials Characterization, 143, 163–170. https://doi.org/10.1016/j.matchar.2018.04.009.
- Guschlbauer, R., Osmanlic, F., & Körner, C. (2017). Herausforderungen Bei Der Additiven Fertigung Von Reinkupfer Mit Dem Selektivem Elektronenstrahlschmelzen. Metall, 71(11), 448–451.
- Haghdadi, N., Whitelock, E., Lim, B., Chen, H., Liao, X., Babu, S. S., Ringer, S. P., & Primig, S. (2020). Multimodal γ′ precipitation in Inconel-738 Ni-based superalloy during electron-beam powder bed fusion additive manufacturing. Journal of Materials Science, 55(27), 13342–13350.
- Haines, M., Plotkowski, A., Frederick, C. L., Schwalbach, E. J., & Babu, S. S. (2018). A sensitivity analysis of the columnar-to-equiaxed transition for Ni-based superalloys in electron beam additive manufacturing. Computational Materials Science, 155, 340–349.
- Haleem, A., & Javaid, M. (2019). Additive manufacturing applications in industry 4.0: a review. Journal of Industrial Integration and Management, 04(04), 1930001.
- Han, C., Fang, Q., Shi, Y., Tor, S. B., Chua, C. K., & Zhou, K. (2020). Recent advances on high‐entropy alloys for 3D printing. Advanced Materials, 32(26), 1903855.
- Hankwitz, J. P., Ledford, C., Rock, C., O’Dell, S., & Horn, T. J. (2021). Electron Beam Melting of Niobium Alloys from Blended Powders. Materials, 14(19), 5536.
- Hayat, M. D., Chen, G., Liu, N., Khan, S., Tang, H. P., & Cao, P. (2018). Physical and tensile properties of NiTi alloy by selective electron beam melting. In Key Engineering Materials. Trans Tech Publ.
- Helmer, H. (2017). Additive Fertigung durch Selektives Elektronenstrahlschmelzen der Nickelbasis Superlegierung IN718: Prozessfenster, Mikrostruktur und mechanische Eigenschaften. Friedrich-Alexander-Universität Erlangen-Nürnberg, Chair of materials science and engineering for metals (WTM) (Doctoral thesis).
- Helmer, H., Bauereiß, A., Singer, R. F., & Körner, C. (2016). Grain structure evolution in Inconel 718 during selective electron beam melting. Materials Science and Engineering: A, 668, 180–187. https://doi.org/10.1016/j.msea.2016.05.046.
- Hinojos, A., Mireles, J., Reichardt, A., Frigola, P., Hosemann, P., Murr, L. E., & Wicker, R. B. (2016). Joining of Inconel 718 and 316 Stainless Steel using electron beam melting additive manufacturing technology. Materials & Design, 94, 17–27.
- Horn, T., Karakurt, I., Ledford, C., Gonzalez, M., Gamzina, D., Luhmann, N. C., & Lin, L. (2018). Additively manufactured WR-10 copper waveguide [Paper presentation]. In 2018 IEEE International Vacuum Electronics Conference (IVEC). IEEE.
- Huang, S.-C., & Hall, E. L. (1991). Effects of Cr additions to binary TiAl-base alloys. Metallurgical Transactions. A, Physical Metallurgy and Materials Science, 22A(11), 2619–2627. https://doi.org/10.1007/BF02851355.
- Hung, W. (2021). Postprocessing of additively manufactured metal parts. Journal of Materials Engineering and Performance, 30(9), 6439–6460.
- Hyer, H., Zhou, L., Mehta, A., Park, S., Huynh, T., Song, S., Bai, Y., Cho, K., McWilliams, B., & Sohn, Y. (2021). Composition-dependent solidification cracking of aluminum-silicon alloys during laser powder bed fusion. Acta Materialia, 208, 116698.
- Jawalkar, C., & Kant, S. (2015). A review on use of aluminium alloys in aircraft components. i-Manager’s. Journal on Material Science, 3(3), 33.
- Jia, Y., Mehta, S. T., Li, R., Chowdhury, M. A. R., Horn, T., & Xu, C. (2021). Additive manufacturing of ZrB2–ZrSi2 ultra-high temperature ceramic composites using an electron beam melting process. Ceramics International, 47(2), 2397–2405.
- Jiang, Q., Zhang, P., Yu, Z., Shi, H., Wu, D., Yan, H., Ye, X., Lu, Q., & Tian, Y. (2021). A review on additive manufacturing of pure copper. Coatings, 11(6), 740.
- Jiao, Z. B., Luan, J. H., & Liu, C. T. (2016). Strategies for improving ductility of ordered intermetallics. Progress in Natural Science: Materials International, 26(1), 1–12. https://doi.org/10.1016/j.pnsc.2016.01.014.
- Juechter, V., Franke, M., Merenda, T., Stich, A., Körner, C., & Singer, R. (2018). Additive manufacturing of Ti-45Al-4Nb-C by selective electron beam melting for automotive applications Vol. 22 (pp. 118–126). Ohio: Additive Manufacturing.
- Kan, W., Chen, B., Peng, H., Liang, Y., & Lin, J. (2019). Formation of columnar lamellar colony grain structure in a high Nb-TiAl alloy by electron beam melting. Journal of Alloys and Compounds, 809, 151673.
- Kang, N., El Mansori, M., Guittonneau, F., Liao, H., Fu, Y., & Aubry, E. (2018). Controllable mesostructure, magnetic properties of soft magnetic Fe-Ni-Si by using selective laser melting from nickel coated high silicon steel powder. Applied Surface Science, 455, 736–741. https://doi.org/10.1016/j.apsusc.2018.06.045.
- Karimi, P., Sadeghi, E., Ålgårdh, J., Olsson, J., Colliander, M. H., Harlin, P., Toyserkani, E., & Andersson, J. (2021). Tailored grain morphology via a unique melting strategy in electron beam-powder bed fusion. Materials Science and Engineering: A, 824, 141820.
- Karlen, E., Mironets, S., Giulietti, D., Versluys, K. J., Fennessy, C. O., & Wentland, W. L. (2019). Powered removal for element formed by powder bed fusion additive manufacturing processes. Patent EP3144081B1.
- Katz-Demyanetz, A., Koptyug, A., & Popov, V. V. (2020). In-situ Alloying as a Novel Methodology in Additive Manufacturing [Paper presentation]. 2020 IEEE 10th International Conference Nanomaterials: Applications & Properties (NAP). IEEE.
- Kenevisi, M. S., & Lin, F. (2020). Selective electron beam melting of high strength Al2024 alloy; microstructural characterization and mechanical properties. Journal of Alloys and Compounds, 843, 155866.
- Kenevisi, M. S., & Lin, F. (2021). Dissolution of Al2Cu Precipitate in Al2024 Additively Manufactured by Electron Beam Melting. Advanced Engineering Materials, 23(9), 2100323.
- Kenevisi, M. S., Y, Y., & Lin, F. (2021). A review on additive manufacturing of Al–Cu (2xxx) aluminium alloys, processes and defects. Materials Science and Technology, 37(9), 805–829.
- Khajavi, S. H., Partanen, J., & Holmström, J. (2014). Additive manufacturing in the spare parts supply chain. Computers in Industry, 65(1), 50–63.
- Kim, Y.-K., Youn, S.-J., Kim, S.-W., Hong, J., & Lee, K.-A. (2019). High-temperature creep behavior of gamma Ti-48Al-2Cr-2Nb alloy additively manufactured by electron beam melting. Materials Science and Engineering: A, 763, 138138.
- Kim, Y.-W., & Kim, S.-L. (2018). Advances in gamma alloy materials–processes–application technology: Successes, dilemmas, and future. JOM, 70(4), 553–560.
- Kirka, M. M., Greeley, D. A., Hawkins, C., & Dehoff, R. R. (2017). Effect of anisotropy and texture on the low cycle fatigue behavior of Inconel 718 processed via electron beam melting. International Journal of Fatigue, 105, 235–243. https://doi.org/10.1016/j.ijfatigue.2017.08.021.
- Kirka, M. M., Lee, Y., Greeley, D. A., Okello, A., Goin, M. J., Pearce, M. T., & Dehoff, R. R. (2017). Strategy for texture management in metals additive manufacturing. JOM Journal of the Minerals Metals and Materials Society., 69(3), 523–531.
- Klassen, A. (2018). Simulation of evaporation phenomena in selective electron beam melting. FAU University Press.
- Klassen, A., Bauereiß, A., & Körner, C. (2014). Modelling of electron beam absorption in complex geometries. Journal of Physics D: Applied Physics, 47(6), 065307.
- Klassen, A., Forster, V. E., Juechter, V., & Körner, C. (2017). Numerical simulation of multi-component evaporation during selective electron beam melting of TiAl. Journal of Materials Processing Technology, 247, 280–288. https://doi.org/10.1016/j.jmatprotec.2017.04.016.
- Knudsen, O. (2001). OW Richardson and the Electron Theory of Matter, 1901–1916. Histories of the Electron: The Birth of Microphysics, 227–254.
- Konyashin, I., Hinners, H., Ries, B., Kirchner, A., Klöden, B., Kieback, B., Nilen, R., & Sidorenko, D. (2019). Additive manufacturing of WC-13% Co by selective electron beam melting: Achievements and challenges, Vol. 84 (p. 105028). International Journal of Refractory Metals and Hard Materials.
- Koptyug, A., Bäckström, M., Botero, C., Popov, V., & Chudinova, E. (2018). Developing new materials for electron beam melting: experiences and challenges. In Materials science forum. Trans Tech Publ.
- Koptyug, A., Popov, V. V., JrVega, C. A. B., Jiménez-Piqué, E., Katz-Demyanetz, A., Rännar, L.-E., & Bäckström, M. (2020). Compositionally-tailored steel-based materials manufactured by electron beam melting using blended pre-alloyed powders. Materials Science and Engineering: A, 771, 138587.
- Körner, C. (2016). Additive manufacturing of metallic components by selective electron beam melting—A review. International Materials Reviews, 61(5), 361–377. https://doi.org/10.1080/09506608.2016.1176289.
- Körner, C., Helmer, H., Bauereiß, A., & Singer, R. F. (2014). Tailoring the grain structure of IN718 during selective electron beam melting [Paper presentation]. MATEC Web of Conferences, 14, p. 08001.
- Körner, C., Ramsperger, M., Meid, C., Bürger, D., Wollgramm, P., Bartsch, M., & Eggeler, G. (2018). Microstructure and mechanical properties of CMSX-4 single crystals prepared by additive manufacturing. Metallurgical and Materials Transactions A, 49(9), 3781–3792. https://doi.org/10.1007/s11661-018-4762-5.
- Kowen, J. (2020). Unrealised potential: The story and status of electron beam powder bed fusion. Metal Additive Manufacturing, 6(2), 119–131.
- Kumar, S., Shivashankar, P., & Gopalakrishnan, S. (2020). A half a decade timeline of shape memory alloys in modeling and applications. ISSS Journal of Micro and Smart Systems, 9(1), 1–32.
- Kuner, M. C., Romedenne, M., Fernandez-Zelaia, P., & Dryepondt, S. (2020). Quantitatively accounting for the effects of surface topography on the oxidation kinetics of additive manufactured Hastelloy X processed by electron beam melting. Additive Manufacturing, 36, 101431.
- Kuwabara, K., Shiratori, H., Fujieda, T., Yamanaka, K., Koizumi, Y., & Chiba, A. (2018). Mechanical and corrosion properties of AlCoCrFeNi high-entropy alloy fabricated with selective electron beam melting. Additive Manufacturing, 23, 264–271.
- Le Roux, L., Liu, C., Ji, Z., Kerfriden, P., Gage, D., Feyer, F., Körner, C., & Bigot, S. (2021). Automatised quality assessment in additive layer manufacturing using layer-by-layer surface measurements and deep learning. Procedia CIRP, 99, 342–347.
- Ledford, C., Rock, C., Carriere, P., Frigola, P., Gamzina, D., & Horn, T. (2019). Characteristics and processing of hydrogen-treated copper powders for EB-PBF additive manufacturing. Applied Sciences, 9(19), 3993.
- Ledford, C., Rock, C., Tung, M., Wang, H., Schroth, J., & Horn, T. (2020). Evaluation of electron beam powder bed fusion additive manufacturing of high purity copper for overhang structures using in-situ real time backscatter electron monitoring. Procedia Manufacturing, 48, 828–838.
- Lee, H., Lim, C. H. J., Low, M. J., Tham, N., Murukeshan, V. M., & Kim, Y.-J. (2017). Lasers in additive manufacturing: A review. International Journal of Precision Engineering and Manufacturing-Green Technology, 4(3), 307–322.
- Lee, Y. S., Kirka, M. M., Ferguson, J., & Paquit, V. C. (2020). Correlations of cracking with scan strategy and build geometry in electron beam powder bed additive manufacturing. Additive Manufacturing, 32, 101031. https://doi.org/10.1016/j.addma.2019.101031.
- Lee, Y., Kirka, M. M., Kim, S., Sridharan, N., Okello, A., Dehoff, R. R., & Babu, S. S. (2018). Asymmetric cracking in Mar-M247 alloy builds during electron beam powder bed fusion additive manufacturing. Metallurgical and Materials Transactions A, 49(10), 5065–5079.
- Li, Y., Kan, W., Zhang, Y., Li, M., Liang, X., Yu, Y., & Lin, F. (2021). Microstructure, mechanical properties and strengthening mechanisms of IN738LC alloy produced by Electron Beam Selective Melting. Additive Manufacturing, 47, 102371. https://doi.org/10.1016/j.addma.2021.102371.
- Li, Y., Yu, Y.-F., Wang, Z.-B., Liang, X.-Y., Kan, W.-B., & Lin, F. (2021). Additive manufacturing of nickel-based superalloy single crystals with IN-738 alloy. Acta Metallurgica Sinica (English Letters), 1–6.
- Li, Y., Yu, Y.-F., Wang, Z.-B., Liang, X.-Y., Kan, W.-B., & Lin, F. (2021). Additive manufacturing of nickel-based superalloy single crystals with IN-738 alloy. Acta Metallurgica Sinica (English Letters), https://doi.org/10.1007/s40195-021-01320-3.
- Lim, B., Chen, H., Chen, Z., Haghdadi, N., Liao, X., Primig, S., Babu, S. S., Breen, A. J., & Ringer, S. P. (2021). Microstructure-property gradients in Ni-based superalloy (Inconel 738) additively manufactured via electron beam powder bed fusion. Additive Manufacturing, 46, 102121. https://doi.org/10.1016/j.addma.2021.102121.
- Lin, B., Chen, W., Yang, Y., F, W., & Z, L. (2020). Anisotropy of microstructure and tensile properties of Ti–48Al–2Cr–2Nb fabricated by electron beam melting. Journal of Alloys and Compounds, 830, 154684.
- Lin, B-c., & Chen, W. (2021). Mechanical properties of TiAl fabricated by electron beam melting—A review. China Foundry, 18(4), 307–316.
- Liu, Y., Blunt, L., Zhang, Z., Rahman, H. A., Gao, F., & Jiang, X. (2020). In-situ areal inspection of powder bed for electron beam fusion system based on fringe projection profilometry. Additive Manufacturing, 31, 100940.
- Ljungblad, U. (2021). Radiation method for additive manufacturing. Patent WO2019185642A1.
- Lodes, M. A., Guschlbauer, R., & Körner, C. (2015). Process development for the manufacturing of 99.94% pure copper via selective electron beam melting. Materials Letters, 143, 298–301. https://doi.org/10.1016/j.matlet.2014.12.105.
- Malcolm, W., Jr (1998). NIST-JANAF thermochemical tables. American Institute of Physics. Gaithersburg, MD: The American Chemical Society.
- Markl, M. (2015). Numerical modeling and simulation of selective electron beam melting using a coupled lattice Boltzmann and discrete element method.
- Markl, M., Lodes, M., Franke, M., & Körner, C. (2017). Additive manufacturing using selective electron beam melting. Welding and Cutting, 16(3), 177.
- Matthews, M. J., Guss, G., Khairallah, S. A., Rubenchik, A. M., Depond, P. J., & King, W. E. (2016). Denudation of metal powder layers in laser powder bed fusion processes. Acta Materialia, 114, 33–42. https://doi.org/10.1016/j.actamat.2016.05.017.
- Mikler, C., Chaudhary, V., Borkar, T., Soni, V., Jaeger, D., Chen, X., Contieri, R., Ramanujan, R., & Banerjee, R. (2017). Laser additive manufacturing of magnetic materials. JOM Journal of the Minerals Metals and Materials Society., 69(3), 532–543.
- Milberg, J., & Sigl, M. (2008). Electron beam sintering of metal powder. Production Engineering, 2(2), 117–122. https://doi.org/10.1007/s11740-008-0088-2.
- Mitra, R., & Wanhill, R. (2017). Structural intermetallics. In Aerospace materials and material technologies (pp. 229–245). Springer.
- Mladenov, G., Koleva, E., Koleva, L., & Dzharov, V. (2016). State of the art of additive manufacturing by selective electron beam melting, 51, 14–24.
- Momeni, S., Guschlbauer, R., Osmanlic, F., & Körner, C. (2018). Selective electron beam melting of a copper-chrome powder mixture. Materials Letters, 223, 250–252.
- Montelione, A., Ghods, S., Schur, R., Wisdom, C., Arola, D., & Ramulu, M. (2020). Powder reuse in electron beam melting additive manufacturing of Ti6Al4V: Particle microstructure, oxygen content and mechanical properties. Additive Manufacturing, 35, 101216.
- Morales, R., Aune, R. E., Seetharaman, S., & Grinder, O. (2003). The powder metallurgy processing of refractory metals and alloys. JOM Journal of the Minerals Metals and Materials Society., 55(10), 20–23.
- Moritz, J., Teschke, M., Marquardt, A., Stepien, L., López, E., Brückner, F., Macias Barrientos, M., Walther, F., & Leyens, C. (2021). Electron beam powder bed fusion of γ-titanium aluminide: Effect of processing parameters on part density, surface characteristics, and aluminum content. metals, 11(7), 1093.
- Muñiz-Lerma, J. A., Nommeots-Nomm, A., Waters, K. E., & Brochu, M. (2018). A comprehensive approach to powder feedstock characterization for powder bed fusion additive manufacturing: A case study on AlSi7Mg. Materials, 11(12), 2386.
- Murr, L. E., Gaytan, S. M., Ramirez, D. A., Martinez, E., Hernandez, J., Amato, K. N., Shindo, P. W., Medina, F. R., & Wicker, R. B. (2012). Metal fabrication by additive manufacturing using laser and electron beam melting technologies. Journal of Materials Science & Technology, 28(1), 1–14.
- Murr, L., Martinez, E., Pan, X., Gaytan, S., Castro, J., Terrazas, C., Medina, F., Wicker, R., & Abbott, D. (2013). Microstructures of Rene 142 nickel-based superalloy fabricated by electron beam melting. Acta Materialia, 61(11), 4289–4296.
- Nakamura, M. (1995). Fundamental properties of intermetallic compounds. MRS Bulletin, 20(8), 33–39.
- Negi, S., Nambolan, A. A., Kapil, S., Joshi, P. S., Manivannan, R., Karunakaran, K., & Bhargava, P. (2019). Review on electron beam based additive manufacturing. Rapid Prototyping Journal, 26(3), 485–498.
- Nighan, W. L. (1969). Electrical conductivity of partially ionized noble gases. Physics of Fluids, 12(1), 162–171.
- Ordás, N., Portolés, L., Azpeleta, M., Gómez, A., Blasco, J. R., Martinez, M., Ureña, J., & Iturriza, I. (2021). Development of CuCrZr via electron beam powder bed fusion (EB-PBF). Journal of Nuclear Materials, 548, 152841.
- Pasang, T., Kirchner, A., Jehring, U., Aziziderouei, M., Tao, Y., Jiang, C. P., Wang, J. C., & Aisyah, I. S. (2019). Microstructure and mechanical properties of welded additively manufactured stainless steels SS316L. Metals and Materials International, 25(5), 1278–1286. https://doi.org/10.1007/s12540-019-00264-9.
- Pauzon, C., Dietrich, K., Forêt, P., Dubiez-Le Goff, S., Hryha, E., & Witt, G. (2021). Control of residual oxygen of the process atmosphere during laser-powder bed fusion processing of Ti-6Al-4V. Additive Manufacturing, 38, 101765. https://doi.org/10.1016/j.addma.2020.101765.
- Peng, H., Liu, C., Guo, H., Yuan, Y., Gong, S., & Xu, H. (2016). Fabrication of WCp/NiBSi metal matrix composite by electron beam melting. Materials Science and Engineering: A, 666, 320–323.
- Pham, T., Kwon, P., & Foster, S. (2021). Additive manufacturing and topology optimization of magnetic materials for electrical machines—A review. Energies, 14(2), 283.
- Phambu, N. (2003). Characterization of aluminum hydroxide thin film on metallic aluminum powder. Materials Letters, 57(19), 2907–2913. https://doi.org/10.1016/S0167-577X(02)01395-2.
- Philips, N., Carl, M., & Cunningham, N. (2020). New opportunities in refractory alloys. Metallurgical and Materials Transactions A, 51(7), 3299–3310.
- Pistor, J., & Körner, C. (2019). Formation of topologically closed packed phases within CMSX-4 single crystals produced by additive manufacturing. Materials Letters: X, 1, 100003.
- Pistor, J., & Körner, C. (2021). A novel mechanism to generate metallic single crystals. Scientific Reports, 11(1), 24482. https://doi.org/10.1038/s41598-021-04235-2.
- Pistor, J., Breuning, C., & Körner, C. (2021). A single crystal process window for electron beam powder bed fusion additive manufacturing of a CMSX-4 type Ni-based superalloy. Materials, 14(14), 3785. https://doi.org/10.1038/s41598-021-04235-2.
- Pistor, J., Hagen, S., Virtanen, S., & Körner, C. (2022). Influence of the microstructural homogeneity on the high-temperature oxidation behavior of a single crystalline Ni-base superalloy. Scripta Materialia, 207, 114301.
- Pobel, C. R., Arnold, C., Osmanlic, F., Fu, Z., & Körner, C. (2019). Immediate development of processing windows for selective electron beam melting using layerwise monitoring via backscattered electron detection. Materials Letters, 249, 70–72. https://doi.org/10.1016/j.matlet.2019.03.048.
- Pobel, C. R., Reichel, S., Fu, Z., Osmanlic, F., & Körner, C. (2019). Advanced process strategy to realize microducts free of powder using selective electron beam melting. The International Journal of Advanced Manufacturing Technology, 103(1-4), 1291–1296. https://doi.org/10.1007/s00170-019-03615-3.
- Pollack, S., & Morris, C. (1965). Tunneling through gaseous oxidized films of AL203. Transactions of the Metallurgical Society of AIME, 233(3), 497–497.
- Popov, V. V., JrKatz-Demyanetz, A., Garkun, A., & Bamberger, M. (2018). The effect of powder recycling on the mechanical properties and microstructure of electron beam melted Ti-6Al-4 V specimens. Additive Manufacturing, 22, 834–843.
- Popov, V. V., Katz-Demyanetz, A., Koptyug, A., & Bamberger, M. (2019). Selective electron beam melting of Al0.5CrMoNbTa0.5 high entropy alloys using elemental powder blend. Heliyon, 5(2), e01188.
- Qi, H., Yan, Y., Lin, F., W, H., & Zhang, R. (2006). Direct metal part forming of 316L stainless steel powder by electron beam selective melting. Proceedings of the Institution of Mechanical Engineers, Part B: Journal of Engineering Manufacture, 220(11), 1845–1853.
- Raab, S. J., Guschlbauer, R., Lodes, M. A., & Körner, C. (2016). Thermal and electrical conductivity of 99.9% pure copper processed via selective electron beam melting. Advanced Engineering Materials, 18(9), 1661–1666. https://doi.org/10.1002/adem.201600078.
- Radulov, I., Popov, V., Jr., Koptyug, A., Maccari, F., Kovalevsky, A., Essel, S., Gassmann, J., Skokov, K., & Bamberger, M. (2019). Production of net-shape Mn-Al permanent magnets by electron beam melting. Additive Manufacturing, 30, 100787.
- Raghavan, N., Dehoff, R., Pannala, S., Simunovic, S., Kirka, M., Turner, J., Carlson, N., & Babu, S. S. (2016). Numerical modeling of heat-transfer and the influence of process parameters on tailoring the grain morphology of IN718 in electron beam additive manufacturing. Acta Materialia, 112, 303–314.
- Raghavan, N., Stump, B. C., Fernandez-Zelaia, P., Kirka, M. M., & Simunovic, S. (2021). Influence of geometry on columnar to equiaxed transition during electron beam powder bed fusion of IN718. Additive Manufacturing, 47, 102209.
- Ramsperger, M., Mújica Roncery, L., Lopez-Galilea, I., Singer Robert, F., Theisen, W., & Körner, C. (2015). Solution heat treatment of the single crystal nickel-base superalloy CMSX-4 fabricated by selective electron beam melting. Advanced Engineering Materials, 17(10), 1486–1493. https://doi.org/10.1002/adem.201500037.
- Ramsperger, M., Singer, R. F., & Körner, C. (2016). Microstructure of the nickel-base superalloy CMSX-4 fabricated by selective electron beam melting. Metallurgical and Materials Transactions A, 47(3), 1469–1480. https://doi.org/10.1007/s11661-015-3300-y.
- Raplee, J., Plotkowski, A., Kirka, M. M., Dinwiddie, R., Okello, A., Dehoff, R. R., & Babu, S. S. (2017). Thermographic microstructure monitoring in electron beam additive manufacturing. Scientific Reports, 7(1), 1–16.
- Raplee, J., Plotkowski, A., Kirka, M. M., Dinwiddie, R., Okello, A., Dehoff, R. R., & Babu, S. S. (2017). Thermographic microstructure monitoring in electron beam additive manufacturing. Scientific Reports, 7(1), 43554. https://doi.org/10.1038/srep43554.
- Rausch, A. M., Markl, M., & Körner, C. (2018). Predictive simulation of process windows for powder bed fusion additive manufacturing: Influence of the powder size distribution. Computers & Mathematics with Applications, https://doi.org/10.1016/j.camwa.2018.06.029.
- Reimer, L. (2000). Scanning electron microscopy: physics of image formation and microanalysis. UK: IOP Publishing.
- Reith, M., Franke, M., Schloffer, M., & Körner, C. (2020). Processing 4th generation titanium aluminides via electron beam based additive manufacturing–characterization of microstructure and mechanical properties. Materialia, 14, 100902.
- Ren, X., Peng, H., Li, J., Liu, H., Huang, L., & Yi, X. (2022). Selective Electron Beam Melting (SEBM) of pure tungsten: Metallurgical defects, microstructure, texture and mechanical properties. Materials, 15(3), 1172.
- Richardson, O. W. (1929). Thermionic phenomena and the laws which govern them. Nobel Lecture, 224–226.
- Ridwan, S., Mireles, J., Gaytan, S., Espalin, D., & Wicker, R. (2014). Automatic layerwise acquisition of thermal and geometric data of the electron beam melting process using infrared thermography. In Proc. Int. Symp. Solid Freeform Fabrication.
- Risse, J., & Broeckmann, C. (2019). Additive manufacturing of nickel-base superalloy in738lc by laser powder bed fusion. Lehrstuhl für Lasertechnik, Dissertation, Rheinisch-Westfälische Technische Hochschule Aachen, Veröffentlicht auf dem Publikationsserver der RWTH Aachen University.
- Rock, C., Lara-Curzio, E., Ellis, B., Ledford, C., Leonard, D. N., Kannan, R., Kirka, M., & Horn, T. (2020). Additive Manufacturing of Pure Mo and Mo + TiC MMC Alloy by Electron Beam Powder Bed Fusion. JOM Journal of the Minerals Metals and Materials Society., 72(12), 4202–4213.
- Sames, W. J., Unocic, K. A., Helmreich, G. W., Kirka, M. M., Medina, F., Dehoff, R. R., & Babu, S. S. (2017). Feasibility of in situ controlled heat treatment (ISHT) of Inconel 718 during electron beam melting additive manufacturing. Additive Manufacturing, 13, 156–165.
- Sanchez, S., Smith, P., Xu, Z., Gaspard, G., Hyde, C. J., Wits, W. W., Ashcroft, I. A., Chen, H., & Clare, A. T. (2021). Powder bed fusion of nickel-based superalloys: A review. International Journal of Machine Tools and Manufacture, 165, 103729.
- Scharowsky, T., Bauereiß, A., & Körner, C. (2017). Influence of the hatching strategy on consolidation during selective electron beam melting of Ti-6Al-4V. The International Journal of Advanced Manufacturing Technology, 92(5-8), 2809–2818. https://doi.org/10.1007/s00170-017-0375-1.
- Scharowsky, T., Bauereiß, A., Singer, R., & Körner, C. (2012). Observation and numerical simulation of melt pool dynamic and beam powder interaction during selective electron beam melting. In Proceedings of the Solid Freeform Fabrication Symposium. Switzerland AG: Springer.
- Scharowsky, T., Osmanlic, F., Singer, R., & Körner, C. (2014). Melt pool dynamics during selective electron beam melting. Applied Physics A, 114(4), 1303–1307.
- Schur, R., Ghods, S., Wisdom, C., Pahuja, R., Montelione, A., Arola, D., & Ramulu, M. (2021). Mechanical anisotropy and its evolution with powder reuse in Electron Beam Melting AM of Ti6Al4V. Materials & Design, 200, 109450.
- Schwaighofer, E., Clemens, H., Mayer, S., Lindemann, J., Klose, J., Smarsly, W., & Güther, V. (2014). Microstructural design and mechanical properties of a cast and heat-treated intermetallic multi-phase γ-TiAl based alloy. Intermetallics, 44, 128–140. https://doi.org/10.1016/j.intermet.2013.09.010.
- Segura, I., Murr, L., Terrazas, C., Bermudez, D., Mireles, J., Injeti, V., Li, K., Yu, B., Misra, R., & Wicker, R. (2019). Grain boundary and microstructure engineering of Inconel 690 cladding on stainless-steel 316L using electron-beam powder bed fusion additive manufacturing. Journal of Materials Science & Technology, 35(2), 351–367.
- Seifi, M., Salem, A. A., Satko, D. P., Ackelid, U., Semiatin, S. L., & Lewandowski, J. J. (2017). Effects of HIP on microstructural heterogeneity, defect distribution and mechanical properties of additively manufactured EBM Ti-48Al-2Cr-2Nb. Journal of Alloys and Compounds, 729, 1118–1135. https://doi.org/10.1016/j.jallcom.2017.09.163.
- Sengupta, A., Putatunda, S. K., Bartosiewicz, L., Hangas, J., Nailos, P. J., Peputapeck, M., & Alberts, F. E. (1994). Tensile behavior of a new single crystal nickel-based superalloy (CMSX-4) at room and elevated temperatures. Journal of Materials Engineering and Performance, 3(5), 664–672. https://doi.org/10.1007/BF02645265.
- Shanbhag, G., & Vlasea, M. (2020). The effect of reuse cycles on Ti-6Al-4V powder properties processed by electron beam powder bed fusion. Manufacturing Letters, 25, 60–63.
- Shanbhag, G., & Vlasea, M. (2021). Powder reuse cycles in electron beam powder bed fusion—Variation of powder characteristics. Materials, 14(16), 4602.
- Shim, J. J., & Kim, J. G. (2004). Copper corrosion in potable water distribution systems: Influence of copper products on the corrosion behavior. Materials Letters, 58(14), 2002–2006. https://doi.org/10.1016/j.matlet.2003.12.017.
- Shiratori, H., Fujieda, T., Yamanaka, K., Koizumi, Y., Kuwabara, K., Kato, T., & Chiba, A. (2016). Relationship between the microstructure and mechanical properties of an equiatomic AlCoCrFeNi high-entropy alloy fabricated by selective electron beam melting. Materials Science and Engineering: A, 656, 39–46.
- Shkolnikov, E. I., Shaitura, N. S., & Vlaskin, M. S. (2013). Structural properties of boehmite produced by hydrothermal oxidation of aluminum. The Journal of Supercritical Fluids, 73, 10–17. https://doi.org/10.1016/j.supflu.2012.10.011.
- Sigl, M., Lutzmann, S., & Zäh, M. (2006). Transient physical effects in electron beam sintering. In 2006 International Solid Freeform Fabrication Symposium Proceedings.
- Simmons J. (1965). Electric-tunnel effect and its use in determining properties of surface oxides. Transactions of the Metallurgical Society of AIME, 233(3), 485.
- Sinclair, C. W., Edinger, R., Sparling, W., Molavi-Kakhki, A., & Labrecque, C. (2021). Vibratory powder feeding for powder bed additive manufacturing using water and gas atomized metal powders. Materials, 14(13), 3548.
- Sochalski-Kolbus, L., Payzant, E. A., Cornwell, P. A., Watkins, T. R., Babu, S. S., Dehoff, R. R., Lorenz, M., Ovchinnikova, O., & Duty, C. (2015). Comparison of residual stresses in Inconel 718 simple parts made by electron beam melting and direct laser metal sintering. Metallurgical and Materials Transactions A, 46(3), 1419–1432.
- Spierings, A. B., Voegtlin, M., Bauer, Tu., & Wegener, K. (2016). Powder flowability characterisation methodology for powder-bed-based metal additive manufacturing. Progress in Additive Manufacturing, 1(1–2), 9–20.
- Stephansen, R. (2021). Freezing method for cleaning an additive manufacturing part. Patent WO2019185651A1.
- Stephansen, R., Nilsson, P., Ljungblad, U., & Ackelid, U. (2020). Open data format for beam scanning in Electron Beam Powder Bed Fusion (E-PBF) [Paper presentation]. 3rd International Conference on Electron Beam Additive Manufacturing, in. Oct., Erlangen, Germany.
- Stoloff, N., Liu, C., & Deevi, S. (2000). Emerging applications of intermetallics. Intermetallics, 8(9–11), 1313–1320.
- Strondl, A., Lyckfeldt, O., Brodin, Hk., & Ackelid, U. (2015). Characterization and control of powder properties for additive manufacturing. JOM Journal of the Minerals Metals and Materials Society., 67(3), 549–554.
- Sun, Y., Aindow, M., & Hebert, R. J. (2018). The effect of recycling on the oxygen distribution in Ti-6Al-4V powder for additive manufacturing. Materials at High Temperatures, 35(1–3), 217–224.
- Surmeneva, M. A., Koptyug, A., Khrapov, D., Ivanov, Y. F., Mishurova, T., Evsevleev, S., Prymak, O., Loza, K., Epple, M., Bruno, G., & Surmenev, R. A. (2020). In situ synthesis of a binary Ti–10at% Nb alloy by electron beam melting using a mixture of elemental niobium and titanium powders. Journal of Materials Processing Technology, 282, 116646.
- Tang, H., Qian, M., Liu, N., Zhang, X., Yang, G., & Wang, J. (2015). Effect of powder reuse times on additive manufacturing of Ti-6Al-4V by selective electron beam melting. JOM Journal of the Minerals Metals and Materials Society., 67(3), 555–563.
- Tang, H., Yang, K., Jia, L., He, W., Yang, L., & Zhang, X. (2020). Tantalum bone implants printed by selective electron beam manufacturing (SEBM) and their clinical applications. JOM Journal of the Minerals Metals and Materials Society., 72(3), 1016–1021.
- Tarafder, P., Rock, C., & Horn, T. (2021). Quasi-static tensile properties of unalloyed copper produced by electron beam powder bed fusion additive manufacturing. Materials, 14(11), 2932.
- Taylor, R. M., Manzo, J., & Flansburg, L. (2016). Certification strategy for additively manufactured structural fittings. In Proceedings of the 27th Annual International Solid Freeform Fabrication Symposium.
- Terrazas, C. A., Mireles, J., Gaytan, S. M., Morton, P. A., Hinojos, A., Frigola, P., & Wicker, R. B. (2016). Fabrication and characterization of high-purity niobium using electron beam melting additive manufacturing technology. The International Journal of Advanced Manufacturing Technology, 84(5-8), 1115–1126.
- Terrazas, C. A., Murr, L. E., Bermudez, D., Arrieta, E., Roberson, D. A., & Wicker, R. B. (2019). Microstructure and mechanical properties of Ti-6Al-4V-5% hydroxyapatite composite fabricated using electron beam powder bed fusion. Journal of Materials Science & Technology, 35(2), 309–321.
- Tiberto, D., Klotz, U. E., Held, F., & Wolf, G. (2019). Additive manufacturing of copper alloys: influence of process parameters and alloying elements. Materials Science and Technology, 35(8), 969–969.
- Todai, M., Nakano, T., Liu, T., Yasuda, H. Y., Hagihara, K., Cho, K., Ueda, M., & Takeyama, M. (2017). Effect of building direction on the microstructure and tensile properties of Ti-48Al-2Cr-2Nb alloy additively manufactured by electron beam melting. Additive Manufacturing, 13, 61–70. https://doi.org/10.1016/j.addma.2016.11.001.
- Triantaphyllou, A., Giusca, C. L., Macaulay, G. D., Roerig, F., Hoebel, M., Leach, R. K., Tomita, B., & Milne, K. A. (2015). Surface texture measurement for additive manufacturing. Surface Topography: Metrology and Properties, 3(2), 024002.
- Ul-Hamid, A. (2018). A beginners’ guide to scanning electron microscopy. Vol. 1. Springer.
- Van Den Berg, J. A., Hussey, M. J., Richardson, W. T., & Laidler, I. (2020). Additive layer manufacture using charged particle beams. Patent US10879039B2.
- Vayssette, B., Saintier, N., Brugger, C., Elmay, M., & Pessard, E. (2018). Surface roughness of Ti-6Al-4V parts obtained by SLM and EBM: Effect on the High Cycle Fatigue life. Procedia Engineering, 213, 89–97. https://doi.org/10.1016/j.proeng.2018.02.010.
- Vijayakumar, M., Dhinakaran, V., Sathish, T., & Muthu, G. (2021). Experimental study of chemical composition of aluminium alloys. Materials Today: Proceedings, 37, 1790–1793.
- Vock, S., Klöden, B., Kirchner, A., Weißgärber, T., & Kieback, B. (2019). Powders for powder bed fusion: A review. Progress in Additive Manufacturing, 4(4), 383–397.
- Wahlmann, B., Leidel, D., Markl, M., & Körner, C. (2021). Numerical alloy development for additive manufacturing towards reduced cracking susceptibility. Crystals, 11(8), 902.
- Wang, C., Tan, X., Du, Z., Chandra, S., Sun, Z., Lim, C., Tor, S., Lim, C., & Wong, C. (2019). Additive manufacturing of NiTi shape memory alloys using pre-mixed powders. Journal of Materials Processing Technology, 271, 152–161.
- Wang, P., Huang, P., Ng, F. L., Sin, W. J., Lu, S., Nai, M. L. S., Dong, Z., & Wei, J. (2019). Additively manufactured CoCrFeNiMn high-entropy alloy via pre-alloyed powder. Materials & Design, 168, 107576.
- Wildheim, M., & Stephansen, R. (2021). Electrochemical cleaning of an additively manufactured part. Patent WO2019185647A1.
- Wimler, D., Lindemann, J., Reith, M., Kirchner, A., Allen, M., Vargas, W. G., Franke, M., Klöden, B., Weißgärber, T., Güther, V., Schloffer, M., Clemens, H., & Mayer, S. (2021). Designing advanced intermetallic titanium aluminide alloys for additive manufacturing. Intermetallics, 131, 107109.
- Wolf, T., Fu, Z., & Körner, C. (2019). Selective electron beam melting of an aluminum bronze: Microstructure and mechanical properties. Materials Letters, 238, 241–244.
- Wolf, T., Fu, Z., Ye, J., Heßelmann, C., Pistor, J., Albert, J., Wasserscheid, P., & Körner, C. (2020). Periodic open cellular Raney‐Copper catalysts fabricated via selective electron beam melting. Advanced Engineering Materials, 22(5), 1901524.
- Wong, H., Neary, D., Jones, E., Fox, P., & Sutcliffe, C. (2019). Pilot capability evaluation of a feedback electronic imaging system prototype for in-process monitoring in electron beam additive manufacturing. The International Journal of Advanced Manufacturing Technology, 100(1–4), 707–720.
- Wong, H., Neary, D., Jones, E., Fox, P., & Sutcliffe, C. (2019). Pilot feedback electronic imaging at elevated temperatures and its potential for in-process electron beam melting monitoring. Additive Manufacturing, 27, 185–198.
- Yamaguchi, M., Inui, H., & Ito, K. (2000). High-temperature structural intermetallics. Acta Materialia, 48(1), 307–322.
- Yang, G., Yang, P., Yang, K., Liu, N., Jia, L., Wang, J., & Tang, H. (2019). Effect of processing parameters on the density, microstructure and strength of pure tungsten fabricated by selective electron beam melting. International Journal of Refractory Metals and Hard Materials, 84, 105040.
- Yang, J., Fu, Z., Ye, J., Kübrich, D., & Körner, C. (2022). Electron beam-based additive manufacturing of Fe93.5Si6.5 (wt.%) soft magnetic material with controllable magnetic performance. Scripta Materialia, 210, 114460. https://doi.org/10.1016/j.scriptamat.2021.114460.
- Yang, J., Huang, Y., Liu, B., Guo, C., & Sun, J. (2021). Precipitation behavior in a Nb-5W-2Mo-1Zr niobium alloy fabricated by electron beam selective melting. Materials Characterization, 174, 111019.
- Yeh, J. W., Chen, S. K., Lin, S. J., Gan, J. Y., Chin, T. S., Shun, T. T., Tsau, C. H., & Chang, S. Y. (2004). Nanostructured high-entropy alloys with multiple principal elements: Novel alloy design concepts and outcomes. Advanced Engineering Materials, 6(5), 299–303. https://doi.org/10.1002/adem.200300567.
- Yeh, J.-W. (2013). Alloy design strategies and future trends in high-entropy alloys. JOM Journal of the Minerals Metals and Materials Society., 65(12), 1759–1771.
- Yoder, S., Nandwana, P., Paquit, V., Kirka, M., Scopel, A., Dehoff, R. R., & Babu, S. S. (2019). Approach to qualification using E-PBF in-situ process monitoring in Ti-6Al-4V. Additive Manufacturing, 28, 98–106. https://doi.org/10.1016/j.addma.2019.03.021.
- Youn, S.-J., Kim, Y.-K., Kim, S.-W., & Lee, K.-A. (2020). Elevated temperature compressive deformation behaviors of γ-TiAl-based Ti–48Al–2Cr–2Nb alloy additively manufactured by electron beam melting. Intermetallics, 124, 106859.
- Yue, H., Peng, H., Li, R., Gao, R., Wang, X., & Chen, Y. (2021). High-temperature microstructure stability and fracture toughness of TiAl alloy prepared via electron beam smelting and selective electron beam melting. Intermetallics, 136, 107259.
- Yue, H.-Y., Peng, H., Su, Y.-J., Wang, X.-P., & Chen, Y.-Y. (2021). Microstructure and high-temperature tensile property of TiAl alloy produced by selective electron beam melting. Rare Metals, 40, 3635–3644.
- Zäh, M., & Kahnert, M. (2006). Den Elektronenstrahl für das selektive Sintern von metallischen Pulvern nutzen. Euro-uRapid2006; Frankfurt/Main, 27, 28.11.
- Zhai, W., Wang, P., Ng, F. L., Zhou, W., Nai, S. M. L., & Wei, J. (2021). Hybrid manufacturing of γ-TiAl and Ti–6Al–4V bimetal component with enhanced strength using electron beam melting. Composites Part B: Engineering, 207, 108587. https://doi.org/10.1016/j.compositesb.2020.108587.
- Zhang, L., Yu, G., He, X., Li, S., Ning, W., & Wang, X. (2019). Phase separated characteristics affected by cooling rate of immiscible Cu-Cr alloy by laser surface melting. Journal of Alloys and Compounds, 772, 209–217. https://doi.org/10.1016/j.jallcom.2018.08.012.
- Zhang, L., Yu, G., Li, S., He, X., Xie, X., Xia, C., Ning, W., & Zheng, C. (2019). The effect of laser surface melting on grain refinement of phase separated Cu-Cr alloy. Optics & Laser Technology, 119, 105577. https://doi.org/10.1016/j.optlastec.2019.105577.
- Zhang, X., Chen, H., Xu, L., Xu, J., Ren, X., & Chen, X. (2019). Cracking mechanism and susceptibility of laser melting deposited Inconel 738 superalloy. Materials & Design, 183, 108105.
- Zhao, D., & Lin, F. (2021). Dual-detector electronic monitoring of electron beam selective melting. Journal of Materials Processing Technology, 289, 116935.
- Zhao, Y., Aoyagi, K., Daino, Y., Yamanaka, K., & Chiba, A. (2020). Significance of powder feedstock characteristics in defect suppression of additively manufactured Inconel 718. Additive Manufacturing, 34, 101277.
- Zhong, Y., Rännar, L.-E., Liu, L., Koptyug, A., Wikman, S., Olsen, J., Cui, D., & Shen, Z. (2017). Additive manufacturing of 316L stainless steel by electron beam melting for nuclear fusion applications. Journal of Nuclear Materials, 486, 234–245. https://doi.org/10.1016/j.jnucmat.2016.12.042.
- Zhou, J., Li, H., Yu, Y., Li, Y., Qian, Y., Firouzian, K., & Lin, F. (2019). Research on aluminum component change and phase transformation of TiAl-based alloy in electron beam selective melting process under multiple scan. Intermetallics, 113, 106575.
- Zhou, L., Yuan, T., Li, R., Tang, J., Wang, G., & Guo, K. (2017). Selective laser melting of pure tantalum: densification, microstructure and mechanical behaviors. Materials Science and Engineering: A, 707, 443–451.
- Zhou, Q., Hayat, M. D., Chen, G., Cai, S., Qu, X., Tang, H., & Cao, P. (2019). Selective electron beam melting of NiTi: Microstructure, phase transformation and mechanical properties. Materials Science and Engineering: A, 744, 290–298.
- Ziegler, A., Graafsma, H., Zhang, X. F., & Frenken, J. W. (2014). In-situ Materials Characterization. Vol. 193. Switzerland AG: Springer.