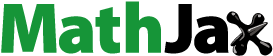
Abstract
Diamond/aluminum composite material has the advantages of high thermal conductivity, low expansion, and lightweight, which has a wide range of application prospects in the field of electronic packaging thermal management. However, the serious interface problems between diamond and aluminum limit the full play of the thermal conductivity of composite materials. A reasonable interface design can maximize the thermal conductivity of composite materials. This article focuses on the interface modification of diamond/aluminum composites, briefly describing the theoretical basis of interface design, the research status of interface modification, interface reaction and composite stability, and prospects for diamond/aluminum composites material development.
The rapid development of information technology has promoted the progress of electronic devices to integration, miniaturization, and lightweight. Back in 1965, Intel co-founder Gordon Moore formulated his famous Moore’s law: The number of transistors on a chip would double every 12 months. However, the high integration of electronic components makes the power density increase continuously, and the calorific value rises sharply. The problem of heat dissipation poses a severe challenge to the development of the electronic information industry. A new international roadmap for semiconductor technology will no longer follow Moore’s Law if the heat dissipation problem has not been solved [Citation1–3]. The heat dissipation problem has increasingly promoted the development of thermal management materials. Common thermal management materials include polymers, ceramics, metals, and metal matrix composites. Among these, metal matrix composite has become one of the research hotspots. It uses metal or alloy as the matrix, utilizes the second phase with high quality to strengthen the body, displaying excellent performance of each component. lists the main properties of common metals and metal-based thermal management materials [Citation4]. Among them, metals such as Al and Cu are low-cost, easy to process, and exhibit high thermal conductivity, but their high thermal expansion coefficient limits their application. Invar and Kovar alloys have a low thermal expansion coefficient, but low thermal conductivity and high density. W-Cu, Mo-Cu, SiC/Al, and other materials have thermal expansion coefficients matching with semiconductor materials such as Si and GaAs, but their thermal conductivity is mostly below 200w/(m k), which is difficult to meet the heat dissipation requirements of high-power integrated circuits.
Table 1. Performance of common metals and metal-based thermal management materials [Citation4].
In recent years, with the fast advancement of diamond preparation technology, the quality of synthetic diamond has been greatly improved and the preparation cost has been decreasing significantly. Metal matrix composites reinforced by diamond are highly competitive in the race of thermal management materials because of their excellent thermal conductivity, adjustable coefficient of thermal expansion and lightweight.
However, in diamond/metal matrix composites, diamond mainly conducts heat by phonons, while metal mainly conducts heat by free electrons. In the process of heat transfer, due to the different vibration frequencies and amplitudes of phonons and electrons, they will scatter strongly at the interface, resulting in the generation of interface thermal resistance [Citation5–8]. Taking diamond/aluminum composites as an example, due to the extremely poor wettability of diamond and aluminum, there are various defects at the composite interface, such as interface products, inclusion layer, pores, interface debonding caused by thermal matching, etc. these defects will interact with phonons, limiting the free path of phonons and increasing the interfacial thermal resistance per unit area. Therefore, for diamond/metal matrix composites, the interface directly determines whether the full potential of high thermal conductivity of diamond can be achieved in the composites. The smaller the interface thermal resistance, the better the heat conduction enhancement effect of diamond, and the higher the thermal conductivity of the composite material.
Aiming at the problem of interfacial compatibility and interfacial modification of diamond/aluminum matrix composites, this paper reviews the theoretical basis of the necessity of interfacial modification, the research status of interfacial modification, interfacial reaction products and material stability.
1. The theoretical basis of diamond/Al interface modification
The thermal conductivity of diamond/aluminum matrix composites can be predicted according to the theoretical model. The commonly used calculation models are H-J (Hasselman-Johnson) model and the DEM (Differential Effective Medium) model.
The expression of H-J model is as follows [Citation9]:
(1-1)
(1-1)
In which λ is thermal conductivity, V is volume fraction, α is diamond particle radius, hc is interfacial thermal conductance, and subscripts c, r and m represent composite material, diamond reinforcement and metal matrix respectively. When the interfacial thermal resistance is neglected (ie hc→+∞), the above formula can be simplified to the classical Maxwell-Eucken formula:
(1-2)
(1-2)
When there is a great difference between the thermal conductivity of the reinforced body and the matrix, the predicted value calculated by H-J model has a great deviation from the actual value, while the theoretical value obtained by DEM model is closer to the experimental value [Citation10]. The expression of DEM model is as follows [Citation10, Citation11]:
(1-3)
(1-3)
where,
is the effective thermal conductivity after considering the enhanced volume radius α and the interface thermal conductivity
and the expression is as follows:
(1-4)
(1-4)
According to the DEM model, for a given metal matrix and diamond reinforcement, the thermal conductivity of the composites mainly depends on the interfacial thermal conductance. The interfacial thermal conductance is affected not only by the interface bonding state, but also by the interfacial composition, phase and thickness. After surface modification of diamond, through different heat treatment technology and composite densification process, the surface transition layer may react with diamond and metal matrix, forming carbide on the diamond side, and forming intermetallic compound on metal matrix side, forming multiple interface layers. The typical interface physical model of diamond/metal matrix composites is shown in [Citation12].
Figure 1. Typical interface physical model of diamond/metal matrix composites [Citation12].
![Figure 1. Typical interface physical model of diamond/metal matrix composites [Citation12].](/cms/asset/b1054883-3ddc-40fd-97d8-78dce4dd6e2d/tfdi_a_2050953_f0001_c.jpg)
According to the calculation formula of composite interface thermal conductivity h analogy resistance, the following formula can be obtained:
(1-5)
(1-5)
Where, is the interfacial thermal conductance between the interface i and (i + 1), l(i-1)→ i is the thickness between the interface (i-1) and the interface i, λ(i-1)→ i is the thermal conductivity of the interface i.
The interface thermal conductivity hi between adjacent interfaces can be calculated using a phonon mismatch model (AMM), as shown below [Citation13–15]:
(1-6)
(1-6)
where ρ is density, c is specific heat, v is Debye sound velocity, and subscripts 1 and 2 represent matrix and reinforcement respectively.
The unmodified ideal interfacial thermal conductance can be calculated by formula (1–6), while the modified interfacial thermal conductance of composite materials can be calculated by formula (1–5) to obtain the following formula (1–7):
(1-7)
(1-7)
where, C, M and I represent carbide, the metal layer and intermetallic compound respectively.
In summary, according to the DEM model and AMM model, on the basis of good bonding state and suitable thickness, if the interface layer has higher thermal conductivity, higher Debye sound velocity and lower solubility in the matrix, an enhanced phonon-electron coupling propagation at the interface will be achieved, thus obtaining better interfacial thermal conductance and improving the thermal conductivity of the composites.
2. Research status of interface modification
At present, extensive research has been carried out on the interfacial modification of diamond/aluminum composites, which is mainly divided into two directions: simulation and experiment. In the aspect of simulation, many researchers use the first principles to calculate and analyze the bonding strength between diamond and metal and the characteristics of interface products, which provides theoretical guidance and experimental direction for interface modification. In terms of experiments, many researchers have optimized diamond surface metallization (W, Ti, Mo, B, Zr, Si), matrix alloying (Al-Si, Al-Ti) and composite material forming and preparation technology to obtain a good bonding interface.
2.1. First-principles calculation of interface design
In recent years, the first-principles calculation based on density functional theory has also become an effective means to study the interface and thermal conductivity of materials [Citation16–19]. By analyzing the interface properties using the first principles, the design experiment of the diamond/aluminum composite interface can be further expounded in theory, and the theoretical basis for diamond surface metallization and matrix alloying can be provided.
Zhang [Citation20] calculated the interface properties of diamond/aluminum by first principles. The interfacial adhesion work of diamond (100)/aluminum (111) is 5.85 J/m2, which is greater than that of diamond (111)/aluminum (111) is 4.14 J/m2, and the interface bonding is stronger. At the same time, there is more charge transfer between Al and C at the diamond (100)/ aluminum (111) interface, and the trend of forming an Al-C bond is greater, and the bond energy is stronger, as shown in . Furthermore, the influence of Al4C3 on the diamond (100)/aluminum (111) interface is calculated. The introduction of Al-C is beneficial to the formation of covalent bonds at the interface, improves the bonding between diamond and aluminum, and increases the interfacial adhesion work to 9.72 J/m2. Zhao [Citation18] explained the reason why the α-Al nucleus tends to form on Al4C3(0001) at the center of the C terminal by first-principles calculation. Sznajder [Citation21] calculated and studied the adsorption process of carbon atoms on al nitride and the influence of some point defects on the mechanical stability and energy stability of diamond/Al nitride interface by using first-principles.
Figure 2. Differential charge density image of model: (a), (b) Diamond (111)/Al(111); (c), (d) diamond(100)/Al(111) [Citation20].
![Figure 2. Differential charge density image of model: (a), (b) Diamond (111)/Al(111); (c), (d) diamond(100)/Al(111) [Citation20].](/cms/asset/702eba19-0f4f-4f9a-ac47-bb0b88248bea/tfdi_a_2050953_f0002_c.jpg)
The above reports gave reasonable explanations of the experimental phenomenon from the point of view of atomic bonding and charge transfer, but only simply explains the non-wetting behavior between diamond and aluminum and the reasons for the poor interfacial bonding between diamond and aluminum. The method of enhancing the interfacial bonding strength of diamond/aluminum composite was not further explored, but the direction was pointed out for enhancing the interfacial bonding strength. Therefore, many scholars began to use the method of doping metal elements to calculate the interfacial bonding strength between diamond and aluminum. Metallization of the diamond surface with W is a research hotspot in recent years.
Wang [Citation22, Citation23] calculated and studied the mechanical and thermodynamic properties of Al4W, Al5W and Al12W under pressure by using the first principles. Elastic calculation results show that Al4W, Al5W and Al12W have stable mechanical properties under the pressure of 0–20 Gpa. Al4W and Al12W change from brittle to ductile when the pressure is greater than 15 GPa. At constant volume (Cv), the effects of temperature and pressure on heat capacity are opposite. The heat release and heat storage capacity of Al12W is greater than that of Al4W and Al5W. The results show that W coating can form metal compounds of Al and W on the surface of Al substrate, while Al4W, Al5W and Al12W have good mechanical and thermodynamic properties, which not only ensure the bonding strength between interfaces but also contribute to heat transfer at the interface.
In addition, the bonding strength between diamond and W needs to be designed. Therefore, Song [Citation24] carried out a series of first-principles calculations to predict the diffusion parameters of carbon in tungsten and evaluated the effect of temperature on them. It is found that carbon atoms tend to occupy the interstitial position of octahedron rather than that of the tetrahedron, and the minimum energy path of carbon atom diffusion is through the interstitial position of a tetrahedron. Yi Huaixing [Citation25] used the generalized gradient approximation in density functional theory to optimize the three structures of tungsten carbide crystals and obtained the stable configuration with the lowest energy. On this basis, he calculated its thermodynamic properties under high temperature and pressure. The results show that the pressure has a great influence on the volume ratio V/V0, the heat capacity is close to the Dulong-Petit limit at high temperature, the thermal expansion coefficient α increases slowly above 600 K at a given pressure, the Debye temperature theta ΘD is much less affected by temperature than by pressure, and the Green-Eisen coefficient γ varies greatly under low pressure.
KaixuanGu [Citation26] has studied the structure, adhesion work, bonding properties and electronic properties of two diamond (001)/Cr3C2 (001) interface models by first-principles calculation. The results show that the two interfaces have higher adhesion work and smaller interface distance, which is attributed to the strong covalent C-C bond and C-Cr bond with ionic characteristics. Pang [Citation27] systematically studied the interface structure, interface stability, wettability and bonding properties of ZrC/diamond. The calculation results showed that the configuration of the C-terminated ZrC surface on the bridged surface of diamond is better, with larger bonding work and less interfacial energy. Wu [Citation28] used the first principle method based on density functional theory to study the atomic structure and electronic properties of the Al (111)/Mo2C (0001) interface and the effect of Mo doping on interfacial adhesion work. The analysis of binding work and interface energy shows that the bonding strength and interface stability of the Mo- terminated interface is better than those of the C- terminated interface, in which the Mo-fcc-Al interface is the best and the C-hcp-Al interface is the worst. The study of the electronic structure shows that the interaction between interface atoms forms metal bonds, and the doping of Mo into the Al matrix will weaken the bonding of the Al/Mo2C interface.
2.2. Diamond surface metallization
To solve the problem of poor interface bonding between diamond and aluminum, diamond/aluminum composites were prepared after the diamond was coated with a metal layer. The metal layer on the surface can form carbides at the interface, which can not only form chemical bonds with diamond but also closely combine with aluminum matrix, which is beneficial to the enhancement of interfacial bonding. At present, the main metallization elements used to improve the interface between diamond and aluminum are W, Ti, Mo, B, Zr, Si and so on.
2.2.1. W and its carbide interface layer
Due to the relatively high intrinsic thermal conductivity, the W interface layer has gradually become a research hotspot in the interfacial modification of diamond/aluminum composites [Citation29–34]. Through the evaluation of the multi-layer interface model of the carbide-metal-intermetallic compound, the W and Mo interface layer of thickness in nanometre-scale with higher intrinsic thermal conductivity plays a significant role in reducing the interfacial thermal resistance of diamond/aluminum composites [Citation14].
Yang [Citation31] coated the surface of diamond particles with a W coating of 35–130 nm in thickness by magnetron sputtering and prepared diamond/aluminum composites by vacuum infiltration. It is found that the existence of W coating improves the interfacial bonding between diamond and the aluminum matrix, and the thermal conductivity of the composite reaches a maximum value of 622 Wm−1K−1 when the thickness of W coating is 45 nm. W can be diffused into the aluminum matrix to a certain extent to form a solid solution interface layer. When diamond/aluminum composites with a W coating thickness of 45 nm are prepared by gas pressure infiltration, W atoms can be diffused into the matrix during infiltration and replace Al atoms in the matrix to form Al5W [Citation23] interface layer, as shown in . The Al5W layer with a thickness of 0.5 nm can be formed at the interface when the infiltration time is 20 min. prolonging the infiltration time can promote the formation of the Al5W interface layer. when the infiltration time is increased from 10 min to 60 min, the thermal conductivity of the composite increases from 520 Wm−1K−1 to 620 Wm−1K−1. After W-plating treatment, in addition to the improvement of the thermal properties of the composites, the mechanical properties are also improved. The diamond/aluminum composites with a w-plating of 45 nm in thickness have the best thermal and mechanical stability. After 720 h wet heat treatment, the thermal and mechanical properties of the composites are reduced by about 3%, while the composites without w-plating are lower than that of diamond (111) The matrix desorption phenomenon occurs on the surface [Citation33].
Figure 3. Surface morphology and interface structure of diamond/Al(W) composite prepared by gas pressure infiltration: (a) SEM image of composite; (b) XRD pattern of composite; (c) STEM HAADF (The high angle annular dark field scanning transmission electron microscopy)image of interface; (d) A zoomed-in STEM ABF(The annular bright field scanning transmission electron microscopy) image of the diamond/Al interface and the corresponding atomic structure of each component on the interface [Citation32].
![Figure 3. Surface morphology and interface structure of diamond/Al(W) composite prepared by gas pressure infiltration: (a) SEM image of composite; (b) XRD pattern of composite; (c) STEM HAADF (The high angle annular dark field scanning transmission electron microscopy)image of interface; (d) A zoomed-in STEM ABF(The annular bright field scanning transmission electron microscopy) image of the diamond/Al interface and the corresponding atomic structure of each component on the interface [Citation32].](/cms/asset/7c5fa645-a444-4d3e-b8c1-b1b8ce6bc410/tfdi_a_2050953_f0003_c.jpg)
2.2.2 Ti and its carbide interface layer
In addition to W, Ti interface layer has also attracted the attention of many researchers [Citation35–37]. However, due to the low thermal conductivity of Ti and its carbides, it is necessary to precisely control the thickness of Ti interface layer to achieve good performance improvement.
In the process of material preparation, Ti can not only react with diamond particles to form TiC but also react with the aluminum matrix to form a new phase. In the presence of oxygen, it is possible to form TiO2. Che [Citation35] studied the microstructure change process of Ti coating in the process of preparing diamond/aluminum composite by gas pressure infiltration. The results showed that the Ti coating on diamond particles consists of three layers, including fine TiC grains, TiC columnar grains and dispersed Ti grains. In the infiltration process of molten aluminum, dispersed Ti particles react with Al to form Al3Ti particles in the Al matrix, while the two TiC layers remain unchanged, as shown in . However, during the subsequent cooling process, due to Al diffusion and the reaction between Al and TiC, Al4C3 particles are formed along the grain boundaries of TiC columnar grains, as shown in . Through the optimization, the thickness of TiC coating can be reduced from 500 nm to 200 nm, thus reducing the interfacial thermal resistance of the composite, and the highest thermal conductivity of 650 Wm−1K−1 can be obtained. Base on this, Yang [Citation38] studied the composition changes of diamond Ti coating after melting and found that Ti coating was composed of TiC in the inner layer and TiO2 in the outer layer, and TiC in the inner layer was closely combined and difficult to be removed in the process of melting and infiltration. Matrix fracture is the main fracture mode of composites, which together with the step fracture of diamond particles shows that there is a strong interfacial bonding between diamond particles with titanium coating and aluminum matrix. When heated from 30 °C to 50 °C, the CTE of 50% Ti-plated diamond/Al composites is 5.07 × 10−6K−1, and when heated from 30 °C to 200 °C, the CTE of the composites is 9.27 × 10−6K−1.
Figure 4. Schematic diagram of the interface structure of diamond (Ti)/Al composite material: (a) during infiltration process (b) after infiltration process [Citation35].
![Figure 4. Schematic diagram of the interface structure of diamond (Ti)/Al composite material: (a) during infiltration process (b) after infiltration process [Citation35].](/cms/asset/fae60baf-0f27-4a78-9e3b-a6bb235cd2a0/tfdi_a_2050953_f0004_c.jpg)
Like W coating, suitable Ti coating is also beneficial to improve the mechanical properties of composite materials. Zhang [Citation39] used the molten salt plating method to form Ti coating on a diamond surface at 850 °C, and prepared diamond/aluminum composite by gas pressure infiltration method. The results of its mechanical properties showed that with the increase of titanium coating thickness, the tensile, compressive and flexural strength of the composite are improved, and the failure strain first increases and then decreases, the maximum value is reached when the titanium plating time is 120 min.
2.2.3 Mo and its carbide interface layer
The physical properties of Mo and W are similar, and the intrinsic thermal conductivity is higher, but Mo and Al may form new phases at the interface, which is not conducive to the improvement of thermal conductivity.
By comparing diamond/copper and diamond/aluminum composites with Mo2C coating [Citation40], it is shown that the Mo2C layer plays different roles in diamond/copper and diamond/aluminum composites. When the Mo2C layer is introduced at the interface between diamond and copper, the thermal conductivity of diamond/copper composites increases, and when the thickness of the Mo2C layer is 500 nm, the thermal conductivity of diamond/ copper composites reaches the highest value 657 Wm−1K−1, as shown in . In contrast, due to the formation of harmful particulate phase (Al12Mo), the thermal properties of diamond/Al composites deteriorate with the presence of the Mo2C layer, as shown in . Therefore, Mo2C is favorable to the interfacial bonding between diamond and copper but unfavorable to the bonding between diamond and aluminum. The reason for this phenomenon is that [Citation41] C-2p and Al-3p or Cu-3d electrons have different degrees of hybridization, and the adhesion work of the diamond /Al interface is stronger than that of the diamond/Cu interface [Citation41]. Mo atom has little effect on the charge transition of Al-C interface and limited enhancement effect on diamond /Al interface. At the diamond/Cu interface, Mo atoms enhance the delocalization of Cu-3d orbit and the overlap with C-2p orbit, which greatly enhances the interface interaction. Due to the coupling with the Mo-4d state, the C-2p orbital at the diamond/Al interface forms a trough near the Fermi level, which is not conducive to the electron heat conduction at the interface. In the diamond/copper system, the addition of Mo makes the C-2p orbit delocalized and forms a wave peak near the Fermi level, which is conducive to interfacial heat transfer. Therefore, Mo is an effective interface modifying element to improve the interfacial thermal conductance of diamond/copper composites, but it is not suitable for aluminum matrix composites.
Figure 5. The thermal conductivity and XRD pattern of diamond/copper and diamond/aluminum composites with Mo2C coating: (a) thermal conductivity of diamond/Cu composites at different plating times, (b) thermal conductivity of diamond/Al composites at different plating times (c) XRD pattern of diamond/aluminum composite material containing Mo2C coating [Citation40].
![Figure 5. The thermal conductivity and XRD pattern of diamond/copper and diamond/aluminum composites with Mo2C coating: (a) thermal conductivity of diamond/Cu composites at different plating times, (b) thermal conductivity of diamond/Al composites at different plating times (c) XRD pattern of diamond/aluminum composite material containing Mo2C coating [Citation40].](/cms/asset/90adac5a-3edb-4fe2-b618-5f366b8ff8be/tfdi_a_2050953_f0005_c.jpg)
2.2.4. Other elements and their carbide interface layers
Different coatings have different effects on the properties of interfacial modified composites due to the difference in solid solubility and intrinsic thermal conductivity in the matrix. In addition to the above coating elements, other types of coatings have also been preliminarily explored and achieved different effects.
Sun [Citation42] prepared diamond/aluminum composite material containing B4C coating by powder metallurgy method, and the addition of B4C coating significantly increased the bending strength. When the volume fraction of diamond particles containing B4C coating was 30 wt.%, the maximum bending strength reached 261.2 MPa.It is about twice that of the same volume fraction diamond/Al composite (140.1 MPa) without interface modification. The thermal conductivity increases with the increase of the diamond volume fraction. When the diamond volume fraction is 50%, the thermal conductivity of the composite has the highest value (352.7 Wm−1K−1), and the bending strength increases with the decrease of the diamond volume fraction.
Li [Citation43] transformed the magnetron sputtered Zr coating on the diamond surface into ZrC layer by heat treatment and then prepared diamond/ aluminum composites by gas pressure infiltration method. The results showed that the 450 nm ZrC layer on the diamond surface greatly reduces the content of Al4C3 in diamond/Al composites, but the formation of Al4C3 is not completely restricted. After the interfacial modification of ZrC coating, the thermal conductivity of the composite decreases from 709 Wm−1K−1 unmodified to 572 Wm−1K−1 modified, which is mainly due to the low thermal conductivity of the ZrC interfacial layer.
Li [Citation44] coated diamond surface with Si layer by magnetron sputtering, formed SiC layer on the diamond surface after heat treatment, and then prepared diamond/Aluminum composite containing SiC coating by vacuum melting technology. After interfacial modification, the Al matrix adhered evenly to diamond (100) and diamond (111) surfaces, which improved the heat conduction between diamond reinforcement and Al matrix. After the diamond surface is coated with SiC coating, the thermal conductivity of the composite increases from 590 Wm−1K−1 to 666 Wm−1K−1, an increase of 12.9%.
In general, due to the poor wettability of diamond and aluminum and the selective adhesion of aluminum matrix to diamond (111) and (100) crystal planes, pores and cracks tend to occur at the interface of diamond/Aluminum composites, which will lead to a sharp decline in heat conduction. After metalized interfacial modification of the diamond surface, the interfacial bonding of diamond/aluminum composites is improved obviously, thermal conductivity is improved significantly, thermal expansion coefficient and mechanical properties are improved accordingly. To play a good interface bonding effect, the metalized elements on the surface need to have the following conditions: The coating elements are strong carbide forming elements, which can not only react with diamond to generate carbide but also can have certain diffusion in the aluminum matrix to achieve a good combination with the matrix; The coating elements and carbides should have as high thermal conductivity as possible to minimize the weakening effect on the high thermal conductivity of composites. The thickness and structure of the coating interface should meet the appropriate conditions to improve the interface bonding and ensure the good performance of thermal conductivity. Therefore, reasonable interface design is the key to obtaining high thermal conductivity diamond/aluminum composites.
2.3. Matrix alloying
Matrix alloying is another important method commonly used in the interfacial modification of diamond/aluminum composites. Alloying elements can form carbides between diamond and aluminum interfaces to strengthen interfacial bonding, and can also prevent excessive Al4C3 phase formation, which has a good influence on the improvement of thermal conductivity. At present, the main elements of diamond/Aluminum matrix alloying alloy are Si, Ti, etc.
Si is one of the most commonly used elements in the matrix alloying of diamond/Aluminum composites. The addition of Si can reduce the formation of Al4C3 at the interface because the reaction between Si and diamond generates the SiC phase at the interface, which hinders the reaction between Al and diamond. Guo [Citation45] added 0-40wt.% Si into Al matrix and prepared diamond/aluminum composites by pressure infiltration. It was found that the thermal conductivity of diamond/aluminum composites reached a maximum of 532 Wm−1K−1 when the content of Si was 12.2 wt.%. Mizuuchi [Citation46] prepared diamond/aluminum composites with 5 wt.% Si content by spark plasma sintering. The relative density of diamond in the composites is more than 99% and the volume fraction is 35%–50%. The test results show that the thermal conductivity of the composite reaches 552 Wm−1K−1 when the volume fraction of the diamond is 50%. Although the addition of Si can inhibit the formation of Al4C3, the thermal conductivity of the composites will decrease with the prolongation of contact time between diamond and matrix during gas pressure infiltration, because prolonging the contact time will increase the formation of Al4C3 [Citation47].
Some researchers have also explored the effect and mechanism of Al-Si alloy on the composites. Zhang [Citation48] added Si element to Al matrix and prepared Al-Si/diamond composites by spark plasma sintering. The addition of Si helps the material to form molten metal during sintering, effectively fillings the pores between diamond particles and promoting densification. Therefore, when the volume fraction of diamond is in the range of 25% to 55%, the relative density of Al-Si/diamond composites sintered at 863 K is more than 99.0%. In addition, the wettability with diamond can be improved by alloying molten Al with Si, and the interfacial bonding can be strengthened by the evaporation condensation mechanism. The eutectic silicon precipitated at the interface reduces the thermal expansion mismatch between diamond and aluminum and increases the interfacial thermal conductance. The thermal conductivity of Al-Si/diamond composites containing 55 vol% diamond reaches 412 Wm−1K−1. In the temperature range of 323–573 K, the CTE value is 7.3 × 10-6∼13.6 × 10-6 K-1, compared with the untreated Al/diamond composite, which is reduced by 1.6 × 10−6 K−1.
In addition to the addition of the Si element for alloying, the addition of Ti to the Al matrix to form an alloy can also enhance the interfacial bonding. Zhang [Citation49] added 0.5–4.0 wt.%Ti to Al matrix, and diamond /aluminum composites were prepared by gas pressure infiltration. The mechanical properties of the Al-Ti/diamond composite increase with the increase of alloying element titanium content. When the content of Ti is 4.0 wt%, a 2 μm TiC interface layer is formed between Al and diamond, and the tensile strength reaches the highest value of 153 MPa.
Good results can also be obtained by comprehensively using diamond surface metallization and matrix alloying to modify the interface. Liu [Citation50] first coated TiC on the diamond surface, and then selected 6061 aluminum alloy as the matrix material and prepared diamond (TiC)/6061 aluminum alloy composites with a volume fraction of 50% by powder metallurgy. The results show that the nanometer TiC coating can effectively improve the bonding between diamond and alloy matrix. The relative density of the prepared composites is 99.6%, which is higher than that of 96.7% of the composites without interfacial modification. In addition, the bending strength of the modified material is 396 MPa, which is 35% higher than that of untreated material. However, due to the addition of interfacial modification elements, the thermal conductivity of both matrix and reinforcement decreased, and the final thermal conductivity of the composite only increased by 13.4%.
Guo [Citation51] compared the two methods of diamond surface metallization and matrix alloying. They found that both methods are helpful to improve the adhesion of the matrix to the diamond surface. When the content of Si in the matrix is 12.2 wt%, the thermal conductivity of the composite is 534 Wm−1K−1 and the thermal expansion coefficient is 8.9 × 10−6 K−1. However, the interfacial thermal resistance of the composites metalized by Ti coating increases due to the addition of Ti, the thermal conductivity is 514 Wm−1K−1 and the thermal expansion coefficient is 11.9 × 10−6 K−1.
In conclusion, adding alloying elements into the aluminum matrix can improve the wettability between matrix and diamond, form a stable interface structure, and prevent harmful interface reactions, which is an economical and efficient interface modification method. The addition of alloying elements will have two opposite effects on the properties of the composites: on one hand, the addition of alloying elements can effectively improve the interfacial bonding between diamond and matrix, which is beneficial to the improvement of thermal conductivity; on the other hand, the addition of alloying elements increases the scattering of hot carriers, weakens the thermal conductivity of aluminum matrix, and adversely affects the thermal conductivity of the composites. Compared with the surface metallization of diamond, the thermal conductivity of the composites prepared by matrix alloying is relatively low, so through the effective control of the composition and structure of the interface, balancing these two effects is particularly important for the different effects of matrix alloying.
2.4. Optimization of the composite material preparation process
The preparation methods of diamond/aluminum composites are mainly divided into two types, one is the solid-phase method, which includes spark plasma sintering and vacuum hot pressing sintering, and the other is the liquid phase method, which includes squeeze casting and gas pressure-assisted infiltration.
2.4.1. Gas pressure infiltration method
Because of the poor wettability between diamond and aluminum, avoiding holes and voids at the interface that can hinder phonon and electron heat transfer is the key to giving full play to the heat conduction efficiency of diamond/aluminum composites. The gas pressure infiltration method can realize the densification preparation of composite materials, which is very beneficial for the improvement of thermal conductivity and has been widely used by researchers [Citation32, Citation35, Citation38–40, Citation43]. Through the optimization of the preparation process, the interface structure of the composites can also be controlled to achieve a good bond between the aluminum matrix and diamond reinforcement.
At present, composites with thermal conductivity over 700 Wm−1K−1 can be obtained by optimizing the process parameters such as infiltration temperature, pressure and time. Monje [Citation52] by adjusting the quality of diamond, infiltration temperature and reaction time, the thermal conductivity of the composites can be higher than that of 740 Wm−1K−1. Weber [Citation53] fabricated 63 vol.% diamond/aluminum matrix composites by gas pressure-assisted infiltration (750 °C, 5–6 MPa), the thermal conductivity is 760 Wm−1K−1 and the thermal expansion coefficient is only 5.7 ppm/K. Zhang [Citation54] by optimizing the temperature and pressure of infiltration, the thermal conductivity of the composites prepared under the optimum conditions of 800 °C and 0.8 MPa reached more than 760 Wm−1K−1. In addition to factors such as temperature, time and pressure, the atmosphere during infiltration will also have an impact. Nitrogen reacts with the aluminum matrix, thus hindering the formation of Al4C3 at the interface. With the increase of infiltration temperature, osmotic pressure and holding time, the thermal conductivity of diamond/aluminum composites prepared in nitrogen atmosphere decreases, but the composites prepared in argon atmosphere show the opposite trend [Citation55]. The maximum thermal conductivity obtained in a nitrogen atmosphere is 494 Wm−1K−1, which is lower than the maximum value of 564 Wm−1K−1 in an argon atmosphere. This is because, in the initial stage of infiltration, nitrogen will lead to the roughening of the diamond surface, which is beneficial to the increase of the specific surface area of diamond particles thus improving the interfacial bonding and thermal conductivity. Although the inhibition of nitrogen on Al4C3 formation increases with the further reaction of nitrogen at the interface, the inherent thermal conductivity of diamond decreases due to the reaction with nitrogen. When this adverse effect outweighs the favorable effect, the thermal conductivity of aluminum/diamond composites prepared in a nitrogen atmosphere begins to decline.
2.4.2. Vacuum hot pressing sintering
Vacuum hot pressing sintering can realize the diffusion bonding of the composite interface by controlling the heating rate, sintering temperature, sintering pressure and time, and at the same time controlling the interface reaction speed to obtain better thermal conductivity of the composites. Long [Citation56] prepared aluminum matrix composites reinforced by 50 vol.% diamond grains by vacuum hot pressing sintering at 60 MPa sintering pressure, and the thermal conductivity of the composites was 321 Wm−1K−1, 112 Wm−1K−1 higher than that of pure aluminum (209 Wm−1K−1). At 298 K to 573 K, the thermal expansion coefficient of the composites is 13.2 × 10−6/K to 8.3 × 10−6/K. Tan [Citation57–59] fabricated aluminum matrix composites reinforced by diamond particles with different volume fractions by systematically optimizing vacuum hot pressing sintering parameters. A small amount of Al4C3 phase is formed between diamond and aluminum matrix by controlling the interfacial reaction, which greatly improves the interfacial bonding of the composites even without any interfacial modification. The thermal conductivity of 55 vol.% diamond/aluminum composites is 567 Wm−1K−1, which is more than 90% of the theoretical calculated value [Citation57].
2.4.3. Spark plasma sintering
Compared with vacuum hot pressing, spark plasma sintering has a faster heating rate and shorter sintering time. Mizuuchi [Citation60] prepared diamond/aluminum composites by spark plasma sintering of diamond particles, pure aluminum and 5056 aluminum-magnesium alloy. The relative bulk density of diamond particles reached 97%, and the thermal conductivity of the composites with a diamond content of 45.5 vol.% was 403 Wm−1K−1. The diamond/aluminum composite with 5 wt.% Si content prepared by spark plasma sintering has a thermal conductivity of 552 Wm−1K−1 when the volume fraction of diamond is 50% [Citation46]. Zhang [Citation48] prepared matrix alloyed diamond/Al-Si composites by spark plasma sintering.
2.4.4. Squeeze casting
Squeeze casting makes the liquid metal into the diamond reinforced body with the assistance of mechanical pressure, and squeeze casting can produce composites with higher density and fewer pores. However, the thermal conductivity of the composites is not high due to the formation of a large amount of Al4C3 phase in the extrusion casting process [Citation36, Citation61, Citation62]. Wang [Citation63] optimized the extrusion casting process to change the non-adhesion state between diamond and aluminum into selective adhesion through higher penetration temperature, and to obtain a better overall bonding effect by extending the contact time between liquid aluminum and diamond. With the enhancement of interfacial bonding, the thermal conductivity and bending strength of the composites increased from 321 Wm−1K−1 to 606 Wm−1K−1 by 89% and 98 MPa to 220 MPa by 89%, respectively.
Generally speaking, different preparation methods have their own advantages and disadvantages and have different effects on the properties of the composites. The solid-state method represented by spark plasma sintering and vacuum hot pressing sintering is easy to control the volume fraction of diamond and aluminum, and the lower preparation temperature reduces the formation of Al4C3. However, there will be some pores formed in the composites prepared by the solid-state method, and the density is relatively low, so it is difficult fulfill the thermal conductivity potential of the diamond. In contrast, the liquid phase method represented by gas pressure infiltration and squeeze casting has a higher density because the liquid metal fills the gap of diamond particles. However, the higher preparation temperature increases the difficulty of controlling the interfacial reaction and places a greater demand on equipment. At present, the gas pressure infiltration method is widely used, the uniform distribution of gas pressure can ensure the densification of the composites, and the thermal conductivity of the composites is higher than 700 Wm−1K−1.
2.5. Reinforcement configuration design optimization
Improving the configuration of diamond reinforcement can transform the discrete interface reinforced by particles into a continuous interface enhanced by a three-dimensional network, and a good effect of interface optimization can also be achieved.
Aiming at the interface problem of diamond/aluminum matrix composites, a large number of researchers have improved the interface bonding from three aspects: surface metallization of diamond, matrix alloying and preparation process optimization. However, the configuration of diamond reinforcement which can be ignored easily and its distribution in the metal matrix are more important for the improvement of thermal conductivity. This is because the configuration of the composite directly affects the heat conduction path of phonons and electrons, and the construction of fast heat conduction channel through configuration optimization is of great help to heat conduction.
Some researchers have explored a new way to improve the thermal conductivity of composites from the optimization of diamond particle configuration. Mizuuchi [Citation64] optimized the configuration of the composites by using diamond particles of different sizes to increase the packing density of the reinforcements. The relative packing density of diamond reinforcements with two kinds of particle sizes can reach more than 99%, which is higher than that of single diamond particles. When different particles are mixed, the thermal conductivity of the composites with a 70% volume fraction of diamond can reach 578 Wm−1K−1. Tan [Citation65] prepared diamond/aluminum composite material by powder metallurgy method, and studied the influence of particle size ratio (PSR)PSR on the dispersion of diamond particles. The results show that the thermal conductivity of 40 and 50 vol.% diamond /Al composites increases by 21% (from 389 to 472 Wm−1K−1) and 42% (from 442 Wm−1K−1 to 628 Wm−1K−1) as PSR increases from 0.225 to 0.9, and diamond particles tend to be connected. Chen [Citation66] prepared diamond/aluminum composites by vacuum hot pressing sintering and pressure infiltration. The composites obtained by pressure infiltration have a higher density (99.13%) and higher thermal conductivity (673 Wm−1K−1). The analysis of the heat transfer model shows that the pressure infiltration process can form diamond particles to bridge and form a fast heat conduction channel, which has a great contribution to the improvement of thermal conductivity.
The traditional diamond particle reinforcement is a distributed configuration, and its transformation into a connected three-dimensional configuration will greatly improve the thermal conductivity of the composites [Citation67–70]. Maiorano [Citation71] designed a multi-component layered structure by combining aluminum foam and diamond/aluminum composites. The longitudinal thermal conductivity of the material is in the range of 137–435 Wm−1K−1, while the transverse thermal conductivity is 156 Wm−1K−1. Compared with aluminum foam, the thermal conductivity is greatly improved. Zhang [Citation67] successfully prepared a three-dimensional foam diamond by chemical vapor deposition (CVD), as shown in . After compounding with aluminum matrix by gas pressure infiltration, the thermal conductivity of the composite reached the thermal conductivity of 315.7 Wm−1K−1 when the volume of diamond was only 4.6 vol.%, which was 54% higher than that of pure aluminum. In addition, the composite of foam diamond and paraffin wax shows a faster thermal response than pure copper [Citation68]. The thermal conductivity of the composite with epoxy resin is increased by 10 times [Citation69], which shows that the three-dimensional network structure has good thermal conductivity.
Figure 6. SEM images of three-dimensional diamond foam: (a) (b) are the diamond foam under different magnifications (c) (d) are the diamond/Al composite under different magnifications [Citation67].
![Figure 6. SEM images of three-dimensional diamond foam: (a) (b) are the diamond foam under different magnifications (c) (d) are the diamond/Al composite under different magnifications [Citation67].](/cms/asset/52c01a1a-0006-485f-b7c9-d766eeaa8c7d/tfdi_a_2050953_f0006_b.jpg)
Compared with diamond particle/aluminum matrix composites, the optimized three-dimensional network diamond/aluminum matrix composites transform the discrete particle interface into a continuous network interface. On one hand, the reduction of the number of interfaces solves the interface problem of diamond/aluminum composites; on the other hand, the transformation of thermal conductivity configuration turns the low thermal conductivity channel of diamond-carbide-aluminum into the high thermal conductivity channel of the diamond-aluminum interpenetrating framework. The efficient improvement of thermal conductivity of diamond/aluminum matrix composites is realized, and the excellent thermal conductivity potential of the diamond is fully achieved.
3. Research on interface reaction products and material stability
In diamond/aluminum composites, the interfacial reaction will occur between diamond particles and the aluminum matrix to form Al4C3. Although this can increase interfacial bonding to a certain extent, the thermal conductivity of Al4C3 is low (140 Wm−1K−1), which hinders the full play of thermal conductivity, and its easy hydrolysis seriously affects the stability of the composites. Based on the interface reaction mechanism of diamond/aluminum composites, the researchers explored the interface structure which is closely related to the stability of diamond/aluminum composites, and then optimized the properties of the materials.
The Al4C3 and amorphous carbon can be observed at the interface of diamond/aluminum composites prepared by pressure infiltration, and the amorphous carbon is related to the formation of Al4C3 [Citation61, Citation72, Citation73]. The research of Monje [Citation74] shows that the formation of Al4C3 has a certain orientation. When the preparation temperature is 750 °C, there are carbides on the (100) plane of diamond, while there are almost no carbides on the (111) plane. This research result is consistent with the research of Kleiner [Citation75] that the carbon atoms on the (100) surface of the diamond are easily separated from the diamond surface to form a saw-tooth shape, and Al4C3 is formed in the pits nearby, while the (111) surface does not react with the aluminum matrix.
Che [Citation76] studied the formation mechanism of Al4C3 on the diamond surface in detail and found that the nucleation of Al4C3 particles is an uneven nucleation process. The nucleation rate of Al4C3 depends on the nucleation sites provided on the (100) and (111) surfaces during the heating process, and the active site density on the (100) surface is higher during the initial heating period, so the nucleation rate on the (100) surface is higher than that on the (111) surface. The growth of Al4C3 grains is controlled by the diffusion process and Ostwald ripening. The transverse and longitudinal growth of Al4C3 grains on the (100) plane is mainly affected by the diffusion of carbon atoms. The efficiency of Ostwald ripening is low, so Al4C3 formed is smaller, more uniform and has high density.
The formation of Al4C3 can be suppressed thus improving the stability by using surface metallization of diamond [Citation35, Citation43], matrix alloying [Citation45] and optimization of the preparation process [Citation55, Citation57]. Lu [Citation77] proposed a method to evaluate the reliability of diamond/ aluminum composites, that is, to judge the degree of hydrolysis by collecting CH4 produced during Al4C3 hydrolysis. It was found that the hydrolysis process of Al4C3 was controlled by the diffusion of water. The soaking time of the composites was extended from 5 days to 115 days, the thermal conductivity decreased from 467 Wm−1K−1 to 347 Wm−1K−1, and the tensile strength decreased from 105 MPa to 61 MPa. Li [Citation44] synthesized the SiC layer on the diamond surface. The thermal conductivity of diamond/aluminum composites not only increased from 590 Wm−1K−1 to 666 Wm−1K−1 but also increased by 12.9%. After being soaked in water for 500 h, the thermal conductivity of diamond/aluminum composites with silicon carbide coating decreased by only 6.31%. However, the thermal conductivity of diamond/ aluminum composites without interfacial modification decreased by 22.54% after the same treatment. The results showed that the addition of Si element to Al by matrix alloying can reduce the production of Al4C3 [Citation78]. The mechanism is that the decrease of the solubility of C element in diamond in Al solution and the preferential precipitation of Si on the surface of diamond particles can promote the reaction between Al4C3 and Si and inhibit the formation of Al4C3. In addition, the increase of density of diamond/ aluminum composites hinders the contact between Al4C3 and water.
4. Conclusion and outlook
Due to the advantages of high thermal conductivity, low expansion and lightweight, diamond/aluminum composites have a wide application prospect in national defense, aerospace, electronic information and other fields. Thanks to the continuous progress of interface optimization technology, the thermal conductivity of diamond/aluminum composites prepared in a large number of studies has reached more than 600 Wm−1K−1, and some studies have even reported that the thermal conductivity has exceeded 700 Wm−1K−1. This shows that the design of the interface layer and the control of the diamond surface state play an important role in improving the thermal conductivity of diamond/aluminum composites. Therefore, to give full play to the excellent thermal conductivity potential of diamond/aluminum composites, the key lies in the regulation of interface composition and structure, the optimization of the preparation process and the design of reasonable configuration. The methods of interface optimization of diamond/aluminum composites include diamond surface metallization, matrix alloying, preparation process optimization and composite configuration optimization.
For diamond/aluminum composites, the elements that are suitable to be used in surface metallization include W, Ti, Mo, B, Zr, Si. The metal coating on the surface of the diamond can form carbide or spread in the aluminum substrate to strengthen the bonding. However, the thermal conductivity of carbide and the intermetallic compound formed by metal coating and aluminum is generally low, which requires fine control of the thickness of the transition layer. At present, the thickness of the transition layer of surface metallization is generally less than a few hundred nanometers. Matrix alloying elements include Si, Ti, etc. Compared with the surface metallization method, although matrix alloying can strengthen the interfacial bonding, the addition of alloying elements weakens the thermal conductivity of the material, so its thermal conductivity is relatively low. The solid-phase method and liquid-phase method are two main methods for the preparation of diamond/aluminum composites. The temperature required by the solid phase method is low, the volume fraction of the material is easy to control, but the density is relatively low. The liquid phase method is beneficial to the densification of the composites, but the higher preparation temperature increases the difficulty of controlling the interfacial reaction, and the thermal conductivity of the composites can be improved by reasonable process optimization. Improving the configuration of the composite can effectively improve the thermal conductivity, and through the foam diamond structure, the discrete particle interface can be transformed into a continuous network interface, and the number of interfaces can be reduced and a fast heat conduction channel can be constructed at the same time, which is conducive to fulfilling the potential of thermal conductivity.
At present, the research on the influence mechanism of interfacial heat conduction is not in-depth, and the interface design of diamond/aluminum composites is restricted. To realize the accurate control of the interface, efforts still need to be made in the following aspects:
Establish an in-depth theoretical understanding of the interface formation mechanism, clarify the influence of the interface layer on the thermal conductivity, and reveal the coupled heat transfer mechanism at the interface, to provide a clear goal for the design of the interface layer.
Explore the influence mechanism of different interface control methods on Al4C3 production, avoid excessive interfacial reaction products, and fully ensure the stability of diamond/aluminum composites.
The effect of composite configuration on thermal conductivity is further studied, and the “structure-effect relationship” between material configuration and properties is revealed, which provides a new idea for giving full play to the potential of thermal conductivity.
Disclosure statement
No potential conflict of interest was reported by the authors.
Additional information
Funding
Notes on contributors
Zengkai Jiao
Zengkai Jiao, Writing - Review & Editing Preparation, Investigation, Formal analysis, Writing - Original Draft Preparation, Visualization.
Huiyuan Kang
Huiyuan Kang, Methodology, Investigation, Formal analysis, Visualization, Project administration.
Bo Zhou
Bo Zhou, Project administration, Resources, Funding acquisition.
Aolong Kang
Aolong Kang, Methodology, Formal analysis, Investigation.
Xi Wang
Xi Wang, Visualization.
Haichao Li
Haichao Li, Methodology.
Zhiming Yu
Zhiming Yu, Formal analysis.
Li Ma
Li Ma, Writing - Review & Editing Preparation, Project administration, Funding acquisition.
Kechao Zhou
Kechao Zhou, Writing - Review & Editing Preparation, Project administration, Funding acquisition.
Qiuping Wei
Quiping Wei, Writing - Review & Editing Preparation, Project administration, Funding acquisition.
References
- Edwards C. Moore’s law: What comes next?. Commun ACM. 2021; 64(2):12–14.
- Grier DA. Forgetting Moore’s law. Computer. 2021; 54(6):46–48.
- Waldrop MM. The chips are down for Moore’s law. Nature. 2016; 530(7589):144–147.
- Xingcun T. Advanced materials for thermal management of electronic packaging. Springer New York, 2011.
- Zhou HY, Li YQ, Wang HM, et al. Fabrication of functionally graded diamond/Al composites by Liquid-Solid separation technology. Materials. 2021; 14(12):3205.
- Zhou HY, Ran MR, Li YQ, et al. Effect of diamond particle size on the thermal properties of diamond/Al composites for packaging substrate. Acta Metall Sinica. 2021; 57(7):937–947.
- Zhou HY, Ran MR, Li YQ, et al. Improvement of thermal conductivity of diamond/Al composites by optimization of liquid-solid separation process. J Mater Process Technol. 2021; 297:117267.
- Xie HN, Chen YT, Zhang TB, et al. Adhesion, bonding and mechanical properties of Mo doped diamond/Al (Cu) interfaces: a first principles study [J]. Appl Surf Sci. 2020; 527:146817.
- Hasselman DPH, Johnson LF. Effective thermal conductivity of composites with interfacial thermal barrier resistance. J Compos Mater. 1987; 21(6):508–515.
- T R, M JM, W L. Assessing predictive schemes for thermal conductivity against diamond-reinforced silver matrix composites at intermediate phase contrast. Scr Mater. 2006; 56(5).
- Molina J-M, Rhême M, Carron J, et al. Thermal conductivity of aluminum matrix composites reinforced with mixtures of diamond and SiC particles. Scr Mater. 2008;58(5):393–396.
- Zhang L. Research on configuration design, preparation and thermal conductivity of diamond aluminum composite. Central South University, 2019. (In Chinese).
- Li J, Wang X, Qiao Y, et al. High thermal conductivity through interfacial layer optimization in diamond particles dispersed Zr-alloyed Cu matrix composites. Scr Mater. 2015; 109:72–75.
- Tan Z, Li Z, Xiong D-B, et al. A predictive model for interfacial thermal conductance in surface metallized diamond aluminum matrix composites. Materials & Design. 2014; 55:257–262.
- Yuan M, Tan Z, Fan G, et al. Theoretical modelling for interface design and thermal conductivity prediction in diamond/Cu composites. Diamond Relat Mater. 2018; 81:38–44.
- Fathzadeh M, Fahrvandi H, Nadimi E. Electronic properties of graphene-ZnO interface: a density functional theory investigation. Nanotechnology. 2020; 31(2):025710.
- Chen L, Chen ST, Hou Y. Understanding the thermal conductivity of diamond/copper composites by first-principles calculations. Carbon. 2019; 148:249–257.
- Zhao ZY, Zhao WJ, Bai PK, et al. The interfacial structure of Al/Al4C3 in graphene/Al composites prepared by selective laser melting: First-principles and experimental. Mater Lett. 2019; 255:126559.
- Zhang H, Huang Y, et al. First-principles study of Al atom diffusion kinetics on Si surface. J Phys. 2019; 68(20):274–282. (In Chinese)
- Zhu P, Zhang Q, et al. First-principles calculation and interface reaction of diamond/aluminum composite material interface properties. J Phys. 2021;70(17):263–273. (In Chinese)
- Sznajder M. DFT-based modelling of carbon adsorption on the AlN surfaces and influence of point defects on the stability of diamond/AlN interfaces. Diamond Relat Mater. 2020; 103:107694.
- Wang C, Liang SH, Jiang YH. In-situ fabrication and characteristics of an Al4W/Al12W composite using infiltration method. Vacuum. 2019; 160:95–101.
- Wang C, Liang SH, Cui J, et al. First-principles study of the mechanical and thermodynainic propertips of Al4W, Al5W and Al12W under pressure. Vacuum. 2019; 169:108844.
- Song C, Kong XS, Liu CS. First-principles studies on carbon diffusion in tungsten. Chinese Phys B. 2019; 28(11):116106.
- Yi HX, Wang JC, et al. First-principles calculations of the structure, mechanics, electronics, optics and thermodynamic properties of tungsten carbide crystals under high temperature and high pressure. J Phys. 2020; 37(02):239–249. (In Chinese)
- Gu KX, Pang MJ, Zhan YZ. Insight into interfacial structure and bonding nature of diamond(001)/Cr3C2(001) interface. J Alloys Compd. 2019; 770:82–89.
- Pang XZ, Yang XY, Yang JB, et al. Investigation on the interface characteristic between ZrC (111) and diamond (111) surfaces by first-principles calculation. Diamond Relat Mater. 2021; 113:108297.
- Wu ZX, Zhan YZ, Xiong L, et al. Properties and electronic structure of Al/Mo2C interfaces: insights from first principle simulation. Philos Mag. 2021; 101(9):1061–1080.
- Chen G, Yang W, Xin L, et al. Mechanical properties of Al matrix composite reinforced with diamond particles with W coatings prepared by the magnetron sputtering method. J Alloys Compd. 2018; 735:777–786.
- Ji G, Tan Z, Lu Y, et al. Heterogeneous interfacial chemical nature and bonds in a W-coated diamond/Al composite. Mater Charact. 2016; 112:129–133.
- Yang W, Chen G, Wang P, et al. Enhanced thermal conductivity in diamond/aluminum composites with tungsten coatings on diamond particles prepared by magnetron sputtering method. J Alloys Compd. 2017; 726:623–631.
- Che Z, Li J, Wang Q, et al. The formation of atomic-level interfacial layer and its effect on thermal conductivity of W-coated diamond particles reinforced Al matrix composites. Compos Part A: Appl Sci Manuf. 2018; 107:164–170.
- Xin L, Tian X, Yang W, et al. Enhanced stability of the diamond/Al composites by W coatings prepared by the magnetron sputtering method. J Alloys Compd. 2018; 763:305–313.
- Zhang C, Cai Z, Wang R, et al. Microstructure and thermal properties of Al/W-coated diamond composites prepared by powder metallurgy. Mater Design. 2016; 95:39–47.
- Che Z, Wang Q, Wang L, et al. Interfacial structure evolution of Ti-coated diamond particle reinforced Al matrix composite produced by gas pressure infiltration. Compos Part B: Eng. 2017; 113:285–290.
- Wu JH, Zhang HL, Zhang Y, et al. The role of Ti coating in enhancing tensile strength of Al/diamond composites. Mater Sci Eng – Struct Mater Prop Microstruct Process. 2013; 565:33–37.
- Liang X, Jia C, Chu K, et al. Thermal conductivity and microstructure of Al/diamond composites with Ti-coated diamond particles consolidated by spark plasma sintering [J]. J Compos Mater. 2012; 46(9):1127–1136.
- Yang B, Yu J-K, Chen C. Microstructure and thermal expansion of Ti coated diamond/Al composites. Trans Nonferrous Metals Soc China. 2009; 19(5):1167–1173.
- Zhang H, Wu J, Zhang Y, et al. Mechanical properties of diamond/Al composites with Ti-coated diamond particles produced by gas-assisted pressure infiltration. Mater Sci Eng A. 2015; 626:362–368.
- Ma S, Zhao N, Shi C, et al. Mo2C coating on diamond: Different effects on thermal conductivity of diamond/Al and diamond/Cu composites. Appl Surf Sci. 2017; 402:372–383.
- Xie H, Chen Y, Zhang T, et al. Adhesion, bonding and mechanical properties of Mo doped diamond/Al (Cu) interfaces: a first principles study. Appl Surf Sci. 2020; 527:146817.
- Sun Y, Zhang C, He L, et al. Enhanced bending strength and thermal conductivity in diamond/Al composites with B4C coating. Sci Rep. 2018; 8(1):11104.
- Li N, Wang L, Dai J, et al. Interfacial products and thermal conductivity of diamond/Al composites reinforced with ZrC-coated diamond particles. Diamond Relat Mater. 2019; 100:107565.
- Li X, Yang W, Sang J, et al. Low-temperature synthesizing SiC on diamond surface and its improving effects on thermal conductivity and stability of diamond/Al composites. J Alloys Compd. 2020; 846:156258.
- Guo C, He X, Ren S, et al. Effect of (0–40) wt. % Si addition to Al on the thermal conductivity and thermal expansion of diamond/Al composites by pressure infiltration. J Alloys Compd. 2016; 664:777–783.
- Mizuuchi K, Inoue K, Agari Y, et al. Processing of diamond particle dispersed aluminum matrix composites in continuous solid–liquid co-existent state by SPS and their thermal properties. Compos Part B: Eng. 2011;42(4):825–831.
- Edtmaier C, Segl J, Rosenberg E, et al. Microstructural characterization and quantitative analysis of the interfacial carbides in Al(Si)/diamond composites. J Mater Sci. 2018; 53(22):15514–15529.
- Zhang Y, Li J, Zhao L, et al. Effect of metalloid silicon addition on densification, microstructure and thermal–physical properties of Al/diamond composites consolidated by spark plasma sintering. Mater Design. 2014;63:838–847.
- Zhang H, Wu J, Zhang Y, et al. Effect of metal matrix alloying on mechanical strength of diamond Particle-Reinforced aluminum composites. J Mater Eng Perform. 2015; 24(6):2556–2562.
- Liu XY, Wang WG, Wang D, et al. Effect of nanometer TiC coated diamond on the strength and thermal conductivity of diamond/Al composites. Mater Chem Phys. 2016; 182:256–262.
- Guo C-Y, He X-B, Ren S-B, et al. Thermal properties of diamond/Al composites by pressure infiltration: comparison between methods of coating Ti onto diamond surfaces and adding Si into Al matrix. Rare Met. 2016; 35(3):249–255.
- Monje IE, Louis E, Molina JM. On critical aspects of infiltrated Al/diamond composites for thermal management: Diamond quality versus processing conditions. Compos Part A: Appl Sci Manuf. 2014; 67:70–76.
- Weber L, Tavangar R. Diamond-based metal matrix composites for thermal management made by liquid metal Infiltration-Potential and limits. Linsmeier C, Reinelt M, editor, 1st International Conference on New Materials for Extreme Environments, Stafa-Zurich: Trans Tech Publications Ltd, 2009, pp. 111–115.
- Zhang Y, Li J, Zhao L, et al. Optimisation of high thermal conductivity Al/diamond composites produced by gas pressure infiltration by controlling infiltration temperature and pressure. J Mater Sci. 2015; 50(2):688–696.
- Li C, Wang X, Wang L, et al. Interfacial characteristic and thermal conductivity of Al/diamond composites produced by gas pressure infiltration in a nitrogen atmosphere [J]. Mater Design. 2016; 92:643–648.
- Long J, Li X, Fang D, et al. Fabrication of diamond particles reinforced Al-matrix composites by hot-press sintering. Int J Refract Met Hard Mater. 2013; 41:85–89.
- Tan Z, Li Z, Fan G, et al. Fabrication of diamond/aluminum composites by vacuum hot pressing: process optimization and thermal properties. Compos Part B: Eng. 2013; 47:173–180.
- Tan Z, Li Z, Fan G, et al. Diamond/aluminum composites processed by vacuum hot pressing: Microstructure characteristics and thermal properties. Diamond Relat Mater. 2013; 31:1–5.
- Tan Z, Ji G, Addad A, et al. Tailoring interfacial bonding states of highly thermal performance diamond/Al composites: Spark plasma sintering vs. vacuum hot pressing. Compos Part A: Appl Sci Manuf. 2016; 91:9–19.
- Mizuuchi K, Inoue K, Agari Y, et al. Thermal conductivity of diamond particle dispersed aluminum matrix composites fabricated in solid–liquid co-existent state by SPS. Compos Part B: Eng. 2011;42(5):1029–1034.
- Beffort O, Khalid FA, Weber L, et al. Interface formation in infiltrated Al(Si)/diamond composites. Diamond Relat Mater. 2006; 15(9):1250–1260.
- Wu JH, Zhang HL, Zhang Y, et al. Effect of copper content on the thermal conductivity and thermal expansion of Al-Cu/diamond composites. Mater Design. 2012; 39:87–92.
- Wang P, Xiu Z, Jiang L, et al. Enhanced thermal conductivity and flexural properties in squeeze casted diamond/aluminum composites by processing control. Mater Design. 2015; 88:1347–1352.
- Mizuuchi K, Inoue K, Agari Y, et al. Bimodal and monomodal diamond particle effect on the thermal properties of diamond-particle-dispersed Al–matrix composite fabricated by SPS. Microelectron Reliab. 2014;54(11):2463–2470.
- Tan Z, Xiong D-B, Fan G, et al. Enhanced thermal conductivity of diamond/aluminum composites through tuning diamond particle dispersion. J Mater Sci. 2018; 53(9):6602–6612.
- Chen PJ, Zeng YC, et al. Analysis of thermal conductivity of diamond/Al composites prepared by hot-press sintering and pressure infiltration. Funct Mater. 2016;47(10):10184–10188. (In Chinese)
- Zhang L, Wei Q, An J, et al. Construction of 3D interconnected diamond networks in Al-matrix composite for high-efficiency thermal management. Chem Eng J. 2020; 380:122551.
- Liu RX, Luo GQ, Li Y, et al. Microstructure and thermal properties of diamond/copper composites with Mo2C in-situ nano-coating. Surf Coatings Technol. 2019; 360:376–381.
- Ye W, Wei Q, Zhang L, et al. Macroporous diamond foam: a novel design of 3D interconnected heat conduction network for thermal management. Mater Design. 2018; 156:32–41.
- An JJ, Wei QP, et al. Effect of surface modification of foamed copper on high quality foamed diamond by chemical vapor deposition. Surf Technol. 2020; 49(3):97–105. (In Chinese)
- Maiorano LP, Molina JM. Guiding heat in active thermal management: One-pot incorporation of interfacial nano-engineered aluminium/diamond composites into aluminium foams. Compos Part A. 2020:133(2020):105859.
- Philippe G, E KU, A KF, et al. Site-specific specimen preparation by focused ion beam milling for transmission electron microscopy of metal matrix composites. Microsc Microanal: Off J Microsc Soc Am. Microbeam Anal Soc Microscop Soc Canada. 2004; 10(2):311–316.
- Khalid FA, Beffort O, Klotz UE, et al. Microstructure and interfacial characteristics of aluminium-diamond composite materials. Diamond Relat Mater. 2004; 13(3):393–400.
- Monje IE, Louis E, Molina JM. Interfacial nano-engineering in Al/diamond composites for thermal management by in situ diamond surface gas desorption. Scr Mater. 2016;115:159–163.
- Kleiner S, Khalid FA, Ruch PW, et al. Effect of diamond crystallographic orientation on dissolution and carbide formation in contact with liquid aluminium. Scr Mater. 2006; 55(4):291–294.
- Che Z, Zhang Y, Li J, et al. Nucleation and growth mechanisms of interfacial Al4 C3 in Al/diamond composites. J Alloys Compd. 2016; 657:81–89.
- Lu Y, Wang X, Zhang Y, et al. Aluminum carbide hydrolysis induced degradation of thermal conductivity and tensile strength in diamond/aluminum composite. J Compos Mater. 2018; 52(20):2709–2717.
- Lu CJ, Lu Chenjun, Xu J, et al. Performance decline and suppression of diamond/Al (or AlSi alloy) composites. J Compos Mater. 2019; 36(03):669–676. (In Chinese)