ABSTRACT
In this study, a series of novel graft copolymers were synthesized by introducing separately the aliphatic polyamide, polyether, and polyester segments to the poly(2-hydroxypropyl acrylate) skeleton. For this purpose, oligomers of poly(3-hydroxy propionate) and poly(α-methyl-β-alanine) with vinyl end-groups were primarily prepared through hydrogen-transfer polymerization of acrylic acid and methacrylamide, respectively. Commercially available poly(ethylene glycol) with methacrylate end-group was used as a third macromonomer in this work. The three graft copolymers of poly(2-hydroxypropyl acrylate) with three degrees of grafting (5, 10, and 20% by mass) were acquired by use of 2-hydroxypropyl acrylate as a monomer, and the three macromonomers as comonomers. Both the “grafting through” strategy and reversible addition-fragmentation chain transfer polymerization (RAFT) method were successfully utilized for the scope of the study. Identical experimental parameters were applied to each macromonomer subgroup to reveal the effects of the macromonomers and their relative quantities on the thermal and spectroscopic properties. Structural and thermal features of the copolymers were determined by using basic characterization methods like FT-IR, 1H-NMR, SLS, TGA, and DSC.
1. Introduction
Poly(2-hydroxypropyl acrylate) is a water-soluble polymer. Furthermore, it is a thermo-responsible polymer exhibiting a lower critical solution temperature (LCST).[Citation1] Reversible addition-fragmentation chain transfer (RAFT) polymerization, an important type of living/controlled radical polymerization, has been used in syntheses of many functional (co)polymers.[Citation2–8] A graft copolymer is a type of copolymer formed by linking two different polymer chains together at a place other than the chain ends. Graft copolymers are branched copolymers in which the ingredients of the side chain are structurally different from the main chain. Graft copolymer syntheses are widely available in the literature.[Citation9–20] In general, there are studies in the literature about graft copolymers and methacrylate-based polymers.[Citation21,Citation22] The “Grafting through” technique, also named the macromonomer method, is one of the simplest routes to obtain graft copolymers with well-defined side chains. In this technique, low molecular weight monomers and polymerizable macromonomers are used to obtain a well-defined graft copolymer. Hydrogen-transfer polymerization (HTP) is realized in the presence of a nucleophilic initiator, a monomer containing a vinyl group, and a mobile proton, such as acrylamide and acrylic acid derivatives.[Citation23–27]
In this study, poly(2-hydroxypropyl acrylate-g-ethylene glycol) [poly(2HPA-g-EG)], poly(2-hydroxypropyl acrylate-g-alpha-methyl beta-alanine) [poly(2HPA-g-mBA)] and poly(2-hydroxypropyl acrylate-g-3-hydroxypropionate) [poly(2HPA-g-3HP)] graft copolymers with three different grafting degrees (5, 10, and 20% by mass) were obtained using the “grafting through” approach and RAFT polymerization method, using 2-hydroxypropyl acrylate as monomer and three different ratios of macro-monomer as co-monomer. The characterizations of the products were accomplished by using multi-instruments such as 1H-NMR, FT-IR, TGA, SLS, and DSC.
2. Experimental
2.1. Materials
Poly(ethylene glycol) methacrylate with Mn = 360 g.mol−1, 2,2′-azobis(2-methylpropionitrile) [AIBN], sodium tert-butoxide (NatBuO), methacrylamide, N,N-dimethylformamide (DMF), methanol, and hydroquinone were supplied by Sigma-Aldrich. Potassium ethyl xanthogenate was received from Fluka. 3-Chloro-1,2-propanediol was bought from Aldrich. Acrylic acid was obtained from Sigma. Formic acid was received from Carlo Erba Reagents. 2-Hydroxypropyl acrylate, tetrahydrofuran (THF), diethyl ether, and ethanol were bought from Merck. 2-Hydroxypropyl acrylate and poly(ethylene glycol) methacrylate were passed through a column filled with neutral alumina to remove inhibitor. THF was refluxed over sodium/benzophenone before distillation. AIBN was recrystallized from methanol before use. All other chemicals/solvents were reagent grade and used as received.
2.2. Instrumentation
Fourier transform infrared (FTIR) spectra of the products were recorded using the Shimadzu IRaffinity spectrometer in ATR mode at a range of 600-4000 cm−1 with 32 scans. A Bruker Ultra Shield Plus, ultra-long hold time 400 NMR spectrometer was used for obtaining the 1H-nuclear magnetic resonance (1H-NMR) spectra using formic acid/CDCl3 as solvent. The elemental analyses of the samples were performed on a Costech ECS 4010 instrument. Thermogravimetric analysis (TGA) measurements were conducted using a Seiko II Exstar 6000 TG/DTA 6200 instrument. The samples were heated at a rate of 10 °C min−1 from 25 to 600 °C under N2 gas. Differential scanning calorimetry (DSC) measurement was obtained by the Hitachi DSC 7000 series thermal analysis system under nitrogen flow. Static light scattering (SLS) measurements were performed by using Malvern Zetasizer Nano Series Nano-ZS with Insmark IR120 model refractometer (solvent: THF; conc.: 1 mg/ml, 0.5 mg/mL, 0.25 mg/mL; temp.: 25 °C; λ = 633 nm) to determine the average molecular weight of the polymer.
2.3. Synthesis of RAFT agent
A similar procedure described in the cited literature was used for the synthesis of the RAFT agent.[Citation28] For example, 6.0 g of 3-chloro-1,2-propanediol was reacted with 16.0 g of potassium ethyl xanthogenate in 100 ml of THF at 40 °C for 120 hours (3-chloro-1,2-propanediol/potassium ethyl xanthogenate = 1/2, mol/mol, approximately). The solution was filtered to remove the unreacted xanthate and by-product (KCl), and then the clear solution was concentrated by a rotary evaporator. RAFT agent was crystallized in cold excess diethyl ether and dried under vacuum at room temperature for 4 days. The yield of the RAFT agent was greater than 60 wt.%. Scheme 1 () outlines the synthesis of the RAFT agent to be used throughout the polymerization reactions.
2.4. Synthesis of poly(3-hydroxypropionate) with vinyl end-group macromonomer (P3HP) by Hydrogen-transfer polymerization
Poly(3-hydroxypropionate) with vinyl end-group (P3HP) macromonomer was obtained as in the cited literature[Citation29] as follows; 5.0 g of acrylic acid, and 33.3 mg of tNaOBu as an initiator were placed in a glass tube under argon flux (tNaOBu/acrylic acid = 1/200, mol/mol, approximately). The reaction mixture was stirred on a hot plate at 90 °C for 72 hours. Then, the viscous resin was poured into an excess amount of diethyl ether to separate P3HP. The yield was greater than 80 wt.%. Scheme 2 () contains the reaction scheme for the synthesis of P3HP.
2.5. Synthesis of poly(α-methyl-β-alanine) with vinyl end-group (PmBA) macromonomer by Hydrogen-transfer polymerization (HTP)
Poly(α-methyl-β-alanine) with vinyl end-group (PmBA) macromonomer was synthesized through base-catalyzed HTP of methacrylamide with a procedure modified used by Roos et al..[Citation30,Citation31] For example, tNaOBu was used as an anionic initiator. Hydroquinone was used as a radical polymerization inhibitor. Mole fractions of the initiator (I) and inhibitor (Inh) in the reaction mixture were adjusted as [M]/[I] = 50 and [M]/[Inh] = 500, respectively. Melt polymerization was carried out using a glass tube in an oil bath at 95 °C for half an hour. The reaction mixture solidified immediately. Excess methanol was then added to the hardened reaction mixture to dissolve unreacted monomer, possible poly(methacrylamide), initiator, and inhibitor residue. Following the vacuum filtration of the suspension mixture, the white solid, PmBA macromonomer, was dried in a vacuum oven at room temperature. Scheme 3 () shows the synthesis of PmBA.
2.6. Synthesis of poly(2-hydroxypropyl acrylate) [P(2HPA)] homopolymer by reversible addition-fragmentation chain transfer (RAFT) polymerization
Poly(2-hydroxypropyl acrylate) [P(2HPA)] homopolymer was synthesized according to the RAFT mechanism. According to the synthesis conditions given in -hydroxypropyl acrylate monomer, RAFT agent, AIBN, and formic acid as a solvent were added to a glass tube to form a homogeneous solution. Nitrogen gas was passed through the solution to create an inert media. After the tube was closed, the polymerization reaction was carried out at 80 °C for 24 hours. Precipitation of the product was achieved by pouring the reaction mixture into diethyl ether. P(2HPA) homopolymer was isolated by decantation and dried under a high vacuum for four days. The reaction stage is shown in Scheme 4 ().
Table 1. Synthesis of poly(2-hydroxypropyl acrylate) homopolymer and poly(2HPA-g-EG) graft copolymer by RAFT polymerization.
Table 2. Synthesis of poly(2HPA-g-mBA) graft copolymer by RAFT polymerization.
2.7. Synthesis of poly(2-hydroxypropyl acrylate-g-ethylene glycol methacrylate) [poly(2HPA-g-Eg)] Graft copolymer by reversible addition-fragmentation chain transfer (RAFT) polymerization
Poly(2-hydroxypropyl acrylate-g-polyethylene glycol methacrylate) [poly(2HPA-g-EG)] graft copolymer was synthesized by the RAFT mechanism. According to the synthesis conditions given in -hydroxypropyl acrylate monomer, polyethylene glycol methacrylate macromonomer, RAFT agent, AIBN, and formic acid were added to a glass tube to form a homogeneous solution. Nitrogen gas was passed through it. After the tube was closed, the polymerization reaction was carried out at 80 °C for 24 hours. Precipitation of the product was achieved by pouring the reaction mixture into diethyl ether. Poly(2HPA-g-EG) graft copolymer was isolated by decantation and dried under a high vacuum for four days. Polyethylene glycol methacrylate macromonomer was grafted onto the 2-hydroxypropyl acrylate skeleton with three grafting degrees of 5, 10, and 20% by mass. The reaction scheme is shown in Scheme 5 ().
2.8. Synthesis of Poly(2-hydroxypropyl acrylate-g-alpha-methyl beta-alanine) [poly(2HPA-g-mBA)] Graft copolymer by reversible addition-fragmentation chain transfer (RAFT) polymerization
Using the RAFT procedure in Section 2.7., synthesis of poly(2-hydroxypropyl acrylate-g-alpha -methyl beta-alanine) [poly(2HPA-g-mBA)] graft copolymer was performed using 2-hydroxypropyl acrylate monomer, poly(alpha-methyl beta-alanine) macromonomer, RAFT agent, AIBN, and formic acid in the amounts shown in . Poly(2HPA-g-mBA) graft copolymer was grafted onto poly(alpha-methyl beta-alanine) homopolymer with three different grafting degrees of 5 wt %, 10 wt %, and 15 wt %. The reaction stage is shown in Scheme 6 ().
2.9. Synthesis of Poly(2-hydroxypropyl acrylate-g-3-hydroxypropionate) [poly(2HPA-g-3HP)] Graft copolymer by reversible addition-fragmentation chain transfer (RAFT) polymerization
Using the RAFT procedure in Section 2.7., synthesis of poly(2-hydroxypropyl acrylate-g-3-hydroxypropionate) [poly(2HPA-g-3HP)] graft copolymer was performed using 2-hydroxypropyl acrylate monomer, poly(3-hydroxypropionate) macromonomer, RAFT agent, AIBN, and formic acid in the amounts shown in . Poly(2HPA-g-3HP)’s with three grafting degrees of 5, 10, 20% by mass were achieved through the introduction of macromonomers onto the growing polymer chain. The reaction stage is shown in Scheme 7 ().
Table 3. Synthesis of poly(2HPA-g-3HP) graft copolymer by RAFT polymerization.
3. Results and discussion
3.1. Synthesis of P(2HPA) homopolymer, Poly(2HPA-g-EG), Poly(2HPA-g-mBA), and poly(2HPA-g-3HP) Graft copolymers by RAFT Polymerization
P(2HPA) homopolymer, poly(2HPA-g-EG), poly(2HPA-g-mBA), and poly(2HPA-g-3HP) graft copolymers were obtained by RAFT polymerization. The synthesis parameters of P(2HPA) homopolymer and poly(2HPA-g-EG) graft copolymer are shown in . The synthesis parameters of poly(2HPA-g-mBA) and poly(2HPA-g-3HP) graft copolymers are given in , respectively.
As shown in , poly(2-hydroxypropyl acrylate) homopolymer was obtained using 2-hydroxypropyl acrylate monomer. The weight average molecular weight of poly(2-hydroxypropyl acrylate) was found to be 54,400 g.mol−1 using SLS measurement as shown in . In addition, poly(2HPA-g-EG) graft copolymer with 5% wt poly2-hydroxypropyl acrylate and 95% wt poly(ethylene glycol) methacrylate, 10% wt poly2-hydroxypropyl acrylate and 90% wt poly(ethylene glycol) methacrylate, 20% wt poly2-hydroxypropyl acrylate and 80% wt poly(ethylene glycol) methacrylate was synthesized in three different compositions. As shown in , poly(2HPA-g-mBA) and poly(2HPA-g-3HP) graft copolymers were also synthesized using the same proportions of poly2-hydroxypropyl acrylate – poly(alpha-methyl beta-alanine), and of poly2-hydroxypropyl acrylate – poly(3-hydroxypropionate), respectively. In the FT-IR spectrum of the poly(2HPA-g-EG) graft copolymer seen in : -OH at approximately 3550 cm−1, aliphatic -CHx at 2947 cm−1, -C = O at 1712 cm−1, -CO of poly(2-hydroxypropyl acrylate) unit at 1149 cm−1, and -CO of poly(ethylene glycol) methacrylate unit at 1072 cm−1. shows that as the percentage of poly(ethylene glycol) methacrylate content in the copolymer increases, the -OC peak intensity of poly(ethylene glycol) methacrylate in the spectrum of the copolymer increases. And max peak intensity is observed at 20% wt poly(ethylene glycol) methacrylate content. In the 1H-NMR spectrum of the poly(2HPA-g-EG) graft copolymer seen in (δ, ppm): 1.2 (-CH3 of poly(2-hydroxypropyl acrylate) unit and of poly(ethylene glycol) methacrylate unit), 1.4 (-CH2 of poly(ethylene glycol) methacrylate unit), 1.6 (-CH2 of poly(2-hydroxypropyl acrylate) unit), 2.2 (-CH of poly(2-hydroxypropyl acrylate) unit), 2.7 (-OH of poly(2-hydroxypropyl acrylate) unit and of poly(ethylene glycol) methacrylate unit), 4.1 (-OCH2 and -OCH of poly(2-hydroxypropyl acrylate) unit), and 5.1 (-OCH2 of poly(ethylene glycol) methacrylate unit). In the FT-IR spectrum of the poly(2HPA-g-mBA) graft copolymer seen in : -NH of poly(alpha-methyl beta-alanine) unit at 3300 cm−1, aliphatic -CHx at 2947 cm−1, -C = O of poly(2-hydroxypropyl acrylate) unit at 1720 cm−1, -C = O of poly(alpha-methyl beta-alanine) unit at 1643 cm−1, -CO of poly(2-hydroxypropyl acrylate) unit at 1157 cm−1, and -CO of poly(alpha-methyl beta-alanine) unit at 1072 cm−1. shows that as the percentage of poly(alpha-methyl beta-alanine) content in the copolymer increases, the -NH peak intensity of poly(alpha-methyl beta-alanine) in the spectrum of the copolymer increases. And max peak intensity is observed at 20% wt. poly(alpha-methyl beta-alanine) content. The same situation is observed for the -OC and -C = O peaks of the poly(alpha-methyl beta-alanine) group. In the 1H-NMR spectrum of the poly(2HPA-g-mBA) graft copolymer seen in (δ, ppm): 1.0 (-CH3 of poly(2-hydroxypropyl acrylate) unit), 1.2 (-CH3 of poly(alpha-methyl beta-alanine) unit), 1.6 (-CH2 of poly(2-hydroxypropyl acrylate) unit), 1.9 (-CH2 of poly(alpha-methyl beta-alanine) unit), 2.2 (-CH of poly(2-hydroxypropyl acrylate) unit), 2.6 (-CH of poly(alpha-methyl beta-alanine) unit), 3.2 (-NCH2 of poly(alpha-methyl beta-alanine) unit), 4.1 (-OCH2 and -OCH of poly(2-hydroxypropyl acrylate) unit), 5.2 (-OH of poly(2-hydroxypropyl acrylate) unit), and 7.5 (-NH of poly(alpha-methyl beta-alanine) unit). The signals reveal that the graft copolymer is composed of 2-hydroxypropyl acrylate and alpha-methyl beta-alanine units. Moreover, the existence of the minor signals (1.4 ppm 2.7 ppm, 4.3 ppm,) coming from the RAFT agent moieties at the chain ends proves the potential living character of the macromolecule. In the FT-IR spectrum of the poly(2HPA-g-3HP) graft copolymer seen in : -OH at approximately 3550 cm−1, aliphatic -CHx at 2947 cm−1, -C = O at 1712 cm−1, -CO of poly(3-hydroxypropionate) unit at 1157 cm−1, and -CO of poly(2-hydroxypropyl acrylate) unit at 1072 cm−1. shows that as the percentage of poly(3-hydroxypropionate content in the copolymer increases, the -OC peak intensity of poly(3-hydroxypropionate) in the spectrum of the copolymer increases. And max peak intensity is observed at 20% wt poly(3-hydroxypropionate) content. In the 1H-NMR spectrum of the poly(2HPA-g-3HP) graft copolymer seen in (δ, ppm): 1.2 (-CH3 of poly(2-hydroxypropyl acrylate) unit and -CH2 linked carbonyl group of poly(3-hydroxypropionate) unit), 1.4 (-CH2 of poly(3-hydroxypropionate) unit), 1.6 (-CH2 of poly(2-hydroxypropyl acrylate) unit), 1.8 (-CH of poly(2-hydroxypropyl acrylate) unit), 2.2 (-CH of poly(2-hydroxypropyl acrylate) unit), 2.7 (-OH of poly(2-hydroxypropyl acrylate) unit and of poly(3-hydroxypropionate) unit), 4.1 (-OCH2 of poly(2-hydroxypropyl acrylate) unit), 4.3 -OCH of poly(2-hydroxypropyl acrylate) unit), and 5.2 (-OCH2 of poly(3-hydroxypropionate) unit).
Figure 9. FT-IR spectra of poly(2-hydroxypropyl acrylate) homopolymer and poly(2HPA-g-EG) graft copolymer.
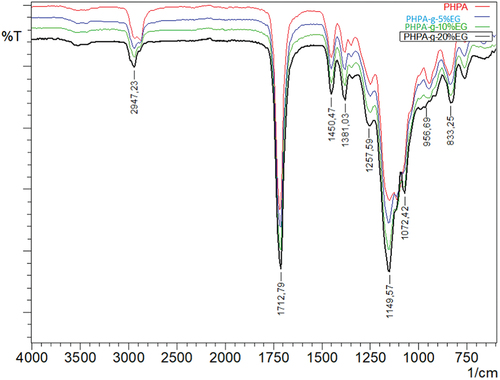
shows DSC thermograms of poly(2-hydroxypropyl acrylate) homopolymer, poly(2HPA-g-EG), poly(2HPA-g-mBA), and poly(2HPA-g-3HP) graft copolymers. As shown in , the glass transition temperature (Tg) value of poly(2-hydroxypropyl acrylate) homopolymer is 16.57 °C. This value is compatible with the value of poly(2-hydroxypropyl acrylate) (22 °C) determined by Eggenhuisen et al..[Citation1] The Tg values of poly(2HPA-g-EG), poly(2HPA-g-mBA), and poly(2HPA-g-3HP) graft copolymers were determined as −12.72 °C, 2.91 °C, and −3.17 °C, respectively. The introduction of poly(3-hydroxypropionate) block into the structure decreased the Tg value of the copolymer the most. The introduction of poly(ethylene glycol) methacrylate block into the structure decreased the Tg value of the copolymer the least. indicated TGA thermograms of poly(2-hydroxypropyl acrylate) homopolymer, poly(2HPA-g-EG) graft copolymer, poly(2HPA-g-mBA) graft copolymer, and poly(2HPA-g-3HP) graft copolymer. According to , the decomposition temperature (Td) value of poly(2-hydroxypropyl acrylate) homopolymer was 388 °C. It can be seen that the second decomposition temperature (Td2) values of the copolymers belong to the poly(2-hydroxypropyl acrylate) block. The first Td values of copolymers belong to the other blocks that compose the copolymers.
4. Conclusion
Poly(2HPA-g-EG), poly(2HPA-g-mBA), and poly(2HPA-g-3HP) graft copolymers with three different grafting degrees were obtained using the “grafting through” approach and RAFT polymerization method, using 2-hydroxypropyl acrylate as monomer and three different ratios of macromonomer as comonomer. The characterizations of the products were obtained by using multi-instruments such as 1H-NMR, FT-IR, TGA, and DSC. These characterizations prove the formation of the graft copolymers.
Disclosure statement
No potential conflict of interest was reported by the author(s).
References
- Eggenhuisen, T. M.; Becer, C. R.; Fijten, M. W. M.; Eckardt, R.; Hoogenboom, R.; Schubert, U. S. Libraries of Statistical Hydroxypropyl Acrylate Containing Copolymers with LCST Properties Prepared by NMP. Macromolecules. 2008, 41, 5132–5140. DOI: 10.1021/ma800469p.
- Chiefari, J.; Chong, Y. K.; Ercole, F.; Krstina, J.; Jeffery, J.; Le, T. P. T.; Mayadunne, R. T. A.; Meijs, G. F.; Moad, C. L.; Moad, E., et al. Living Free-Radical Polymerization by Reversible Addition-Fragmentation Chain Transfer: The RAFT Process. Macromolecules. 1998, 31, 5559–5562. DOI: 10.1021/ma9804951.
- Moad, G.; Chiefari, J.; Chong, Y. K.; Krstina, J.; Mayadunne, R. T. A.; Postma, A.; Rizzardo, E.; Thang, S. H. Living Free Radical Polymerization with Reversible addition-fragmentation Chain Transfer (The Life of RAFT). Polym. Int. 2000, 49, 993–1001. DOI: 10.1002/1097-0126(200009)49:9<993::AID-PI506>3.0.CO;2-6.
- Savaş, B.; Öztürk, T. Synthesis and Characterization of Poly(β‑alanine‑b‑vinyl Benzyl‑g‑vinyl Chloride) Block‑Graft Copolymers by Using Reversible Addition‑Fragmentation Chain Transfer Polymerization and ‘Click’ Chemistry”. J. Polym. Res. 2023, 30, 369. DOI: 10.1007/s10965-023-03753-z.
- Öztürk, T.; Savaş, B.; Meyvacı, E.; Kılıçlıoğlu, A.; Hazer, B. Synthesis and Characterization of the Block Copolymers Using the Novel Bifunctional Initiator by RAFT and FRP Technics: Evaluation of the Primary Polymerization Parameters. J. Polym. Res. 2020, 27, 76. DOI: 10.1007/s10965-020-2043-7.
- Öztürk, T.; Kayğın, O.; Göktaş, M.; Hazer, B. Synthesis and Characterization of Graft Copolymers Based on Polyepichlorohydrin via Reversible Addition-Fragmentation Chain Transfer Polymerization. J. Macromol. Sci. Part A. 2016, 53, 362–367. DOI: 10.1080/10601325.2016.1166002.
- Öztürk, T.; Atalar, M. N.; Göktaş, M.; Hazer, B. One-Step Synthesis of Block-Graft Copolymers via Simultaneous Reversible-Addition Fragmentation Chain Transfer and Ring-Opening Polymerization Using a Novel Macroinitiator. J. Polym. Sci. Part A. 2013, 51, 2651–2659. DOI: 10.1002/pola.26654.
- Öztürk, T.; Göktaş, M.; Savaş, B.; Işıklar, M.; Atalar, M. N.; Hazer, B. Synthesis and Characterization of Poly(vinyl chloride-graft-2-vinylpyridine) Graft Copolymers Using A Novel Macroinitiator by Reversible Addition-Fragmentation Chain Transfer Polymerization. e-Polymers. 2014, 14, 27–34. DOI: 10.1515/epoly-2013-0011.
- Dag, A.; Aydin, M.; Durmaz, H.; Hizal, G.; Tunca, U. Various Polycarbonate Graft Copolymers via Diels-Alder Click Reaction. J. Polym. Sci. Part A. 2012, 50, 4476–4483. DOI: 10.1002/pola.26254.
- Öztürk, T.; Cavicchi, C. A. Synthesis and Characterization of Poly(epichlorohydrin-g-ε-caprolactone) Graft Copolymers by “Click” Chemistry. J. Polym. Mater 2018, 35, 209–220. DOI: 10.32381/JPM.2018.35.02.6.
- Öztürk, T.; Meyvacı, E.; Arslan, T. Synthesis and Characterization of Poly(vinyl chloride-g-ε-caprolactone) Brush Type Graft Copolymers by Ring-Opening Polymerization and “Click” Chemistry. J. Macromol. Sci. Part A. 2020, 57(3), 171–180. DOI: 10.1080/10601325.2019.1680253.
- Savaş, B.; Öztürk, T.; Meyvacı, E.; Hazer, B. Synthesis and Characterization of Comb-Type Graft Copolymers by Redox Polymerization and “Click” Chemistry Method. SN Appl. Sci. 2020, 2(2), 181. DOI: 10.1007/s42452-020-1985-z.
- Savaş, B.; Öztürk, T. Synthesis and Characterization of Poly(vinyl chloride-g-methyl Methacrylate) Graft Copolymer by Redox Polymerization and Cu Catalyzed azide-alkyne Cycloaddition Reaction. J. Macromol. Sci. Part A. 2020, 57(12), 819–825. DOI: 10.1080/10601325.2020.1788393.
- Çolakoğlu, G. N.; Çatıker, E.; Öztürk, T.; Meyvacı, E. Synthesis and Characterization of Brush-type Polyβ-alanine-grafted Polymethyl Methacrylate Using “Grafting Through. Method. Chem. Pap. 2022, 76(2), 869–878. DOI: 10.1007/s11696-021-01908-0.
- Gacal, B.; Durmaz, H.; Tasdelen, M. A.; Hizal, G.; Tunca, U.; Yagci, Y.; Demirel, A. L. Anthracene-Maleimide-Based Diels-Alder “Click Chemistry” As A Novel Route To Graft Copolymers. Macromolecules. 2006, 39(16), 5330–5336. DOI: 10.1021/ma060690c.
- Durmaz, H.; Dag, A.; Cerit, N.; Sirkecioglu, O.; Hizal, G.; Tunca, U. Graft Copolymers via ROMP and Diels-Alder Click Reaction Strategy. J. Polym. Sci. Part A. 2006, 48(24), 5982–5991. DOI: 10.1002/pola.24418.
- Durmaz, H.; Dag, A.; Hizal, G.; Tunca, U. Sequential Double Polymer Click Reactions for the Preparation of Regular Graft Copolymers. J. Polym. Sci. Part A. 2011, 49(5), 1195–1200. DOI: 10.1002/pola.24537.
- Gunay, U. S.; Ozsoy, B.; Durmaz, H.; Hizal, G.; Tunca, U. V‐shaped Graft Copolymers via Triple Click Reactions: Diels-Alder, Copper‐Catalyzed Azide-Alkyne Cycloaddition, and Nitroxide Radical Coupling. J. Polym. Sci. Part A. 2013, 51(21), 4667–4674. DOI: 10.1002/pola.26888.
- Paira, T. K.; Banerjee, S.; Mandal, T. K. Peptide-Poly(ε-caprolactone) Biohybrids by Grafting-From Ring-Opening Polymerization: Synthesis, Aggregation, and Crystalline Properties. J. Polym. Sci. Part A. 2012, 50(11), 2130–2141. DOI: 10.1002/pola.26003.
- Self, J. L.; Zervoudakis, A. J.; Peng, X.; Lenart, W. R.; Macosko, C. W.; Ellison, C. J. L. Graft, and Beyond: Multiblock Copolymers as Next-Generation Compatibilizers. JACS. Au. 2022, 2(2), 310–321. DOI: 10.1021/jacsau.1c00500.
- Villarroya, S.; Zhou, J.; Thurecht, K. J.; Howdle, S. M. Synthesis of Graft Copolymers by the Combination of ATRP and Enzymatic ROP in scCO2. Macromolecules. 2006, 39(26), 9080–9086. DOI: 10.1021/ma061068n.
- Banerjee, S.; Maji, T.; Mandal, T. K. Graft Copolymers Via Combination Of Cationic Polymerization And Atom Transfer Radical Polymerization And Their Phase Separation Into Spherical/Worm-Like Nanostructures. Colloid Polym. Sci. 2014, 292(9), 2217–2226. DOI: 10.1007/s00396-014-3249-1.
- Breslow, D. S.; Hulse, G. E.; Matlack, A. S. Synthesis of poly-β-alanine from Acrylamide. A Novel Synthesis of β-alanine. J. Am. Chem. Soc. 1957, 79(14), 3760–3763. DOI: 10.1021/ja01571a039.
- Saegusa, T.; Kobayashi, S.; Kimura, Y. Hydrogen-transfer Polymerization of Acrylic Acid to Poly(β-propiolactone). Macromolecules. 1974, 7(2), 256–258. DOI: 10.1021/ma60038a021.
- Savaş, B.; Çatıker, E.; Öztürk, T.; Meyvacı, E. Synthesis and Characterization of Poly(α-methyl β-alanine)-poly(ε-caprolactone) Tri Arm Star Polymer by Hydrogen Transfer Polymerization, Ring-Opening Polymerization and “Click” Chemistry. J. Polym. Res. 2021, 28(2), 30. DOI: 10.1007/s10965-020-02367-z.
- Çatıker, E.; Öztürk, T.; Atakay, M.; Salih, B. Synthesis and Characterization of Novel ABA Type Poly(ester-ether) Triblock Copolymers. J. Polym. Res. 2019, 26(5), 123. DOI: 10.1007/s10965-019-1778-5.
- Çatıker, E.; Meyvacı, E.; Atakay, M.; Salih, B.; Öztürk, T. “Synthesis and Characterization of Amphiphilic Triblock Copolymers Including β-alanine/α-methyl-β-alanine and Ethylene Glycol by “Click” Chemistry. Polym. Bull. 2019, 76(4), 2113–2128. DOI: 10.1007/s00289-018-2561-1.
- Öztürk, T.; Göktaş, M.; Hazer, B. One-Step Synthesis of Triarm Block Copolymers via Simultaneous Reversible-Addition Fragmentation Chain Transfer and Ring-Opening Polymerization. J. Appl. Polym. Sci. 2010, 117(3), 1638–1645. DOI: 10.1002/app.32031.
- Savaş, B.; Çatıker, E.; Öztürk, T.; Meyvacı, E. Introduction of 3-Hydroxypropionate Moieties to Polystyrene by “Graft Through” Strategy. ChemistrySelect. 2022, 7(6), e202104193. DOI: 10.1002/slct.202104193.
- Roos, K.; Planes, M.; Hassani, C.; Mehats, J.; Vax, A.; Carlotti, S. Solvent-Free Anionic Polymerization of Acrylamide: A Mechanistic Study for the Rapid and Controlled Synthesis of Polyamide-3. Macromolecules. 2016, 49(6), 2039–2045. DOI: 10.1021/acs.macromol.5b02410.
- Savaş, B.; Çatıker, E.; Öztürk, T.; Meyvacı, E. Synthesis and Characterization of Poly(methyl methacrylate-g-α-methyl-β-alanine) Copolymer Using “Grafting Through” Method. J. Polym. Res. 2021, 28(5), 194. DOI: 10.1007/s10965-021-02551-9.