Abstract
Mesoporous material RH-MCM-41 was synthesized with rice husk silica by a hydrothermal method. It was used as a support for bimetallic platinum−iron catalysts Pt–Fe/RH-MCM-41 for phenol hydroxylation. The catalysts were prepared by co-impregnation with Pt and Fe at amounts of 0.5 and 5.0 wt.%, respectively. The RH-MCM-41 structure in the catalysts was studied with x-ray diffraction, and their surface areas were determined by nitrogen adsorption. The oxidation number of Fe supported on RH-MCM-41 was + 3, as determined by x-ray absorption near edge structure (XANES) analysis. Transmission electron microscopy (TEM) images of all the catalysts displayed well-ordered structures, and metal nanoparticles were observed in some catalysts. All the catalysts were active for phenol hydroxylation using H2O2 as the oxidant at phenol : H2O2 mole ratios of 2 : 1, 2 : 2, 2 : 3 and 2 : 4. The first three ratios produced only catechol and hydroquinone, whereas the 2 : 4 ratio also produced benzoquinone. The 2 : 3 ratio gave the highest phenol conversion of 47% at 70 °C. The catalyst prepared by co-impregnation with Pt and Fe was more active than that prepared using a physical mixture of Pt/RH-MCM-41 and Fe/RH-MCM-41.
Introduction
In this work, we focused on the utilization of RH-MCM-41 synthesized with rice husk silica by a hydrothermal method as a support for bimetallic platinum−iron catalysts, labeled as Pt–Fe/RH-MCM-41. The support with a high surface area provides high metal dispersion and enhances catalytic performance. The catalysts were characterized by several methods and tested for phenol hydroxylation.
Rice husk is a by-product of rice milling and could be considered as an agricultural waste. Because it consists of about 30 wt.% silica along with organic components, silica with a purity greater than 98 wt.% can be extracted by acid leaching and calcination. There have been studies that used rice husk silica as a starting material of mesoporous material referred to as RH-MCM-41 [Citation1–3]. RH-MCM-41 has one-dimensional hexagonal mesopores (pore sizes 2–50 nm). Grisdanurak et al synthesized RH-MCM-41 under ambient conditions and used it effectively as adsorbents for volatile chlorinated organic compounds [Citation2]. The hydrophobicity of RH-MCM-41 from ambient synthesis could be further modified by silylation with silanes [Citation3]. In this work, RH-MCM-41 was prepared by a conventional hydrothermal method with rice husk silica and co-impregnated with Pt and Fe solution to obtain bimetallic catalysts, denoted Pt–Fe/RH-MCM-41. The catalysts were characterized by x-ray diffraction (XRD) analysis, transmission electron microscopy (TEM) and x-ray absorption near edge structure (XANES) analysis. The surface areas of both RH-MCM-41 and bimetallic catalysts were determined by N2 adsorption–desorption measurement. The catalysts were tested for phenol hydroxylation to produce catechol and hydroquinone (equation below). These products are useful chemicals in several applications, for example, photographic chemicals, antioxidants, flavoring agents, polymerization inhibitors and pharmaceuticals [Citation4]. The process involved the reaction of phenol with 30% H2 O2, which is simple and produces no pollution.
Phenol oxidation on Pt catalysts supported on graphite in a stirred tank reactor was studied, and the selectivity of its products was found to depend on the degree of oxygen coverage of the platinum surface [Citation6]. The overoxidized Pt was considered favorable for the formation of hydroquinone, whereas the partly oxidized platinum deemed favorable for the formation of catechol. Phenol hydroxylation on Fe catalysts was also reported for various supports, temperatures and phenol : H2 O2 mole ratios [Citation7–14]. The highest conversion reported (60%) was obtained on Fe/MCM-41 with ∼ 10 wt.% Fe at 70 ° C at a phenol : H2 O2 mole ratio of 1 : 1 [Citation7]. The mechanism of reaction with H2 O2 solution over Fe/MCM-41 was proposed as follows: Fe3 + reacts with H2 O2 to form OH radicals, which then react with phenol to form catechol and hydroquinone [Citation7]. In addition, phenol conversion rate of 58.5% was obtained from Fe/Al-MCM-41 catalyst with 10 wt.% Fe at 40 ° C [Citation9]. The XRD patterns of MCM-41 and Al-MCM-41 showed a decrease in intensity with a high amount of Fe added. In our previous work, the catalytic performances of bimetallic Pt–Fe catalysts with 5 wt.% Fe supported on RH-MCM-41 and Al-RH-MCM-41 were compared, and Pt–Fe/RH-MCM-41 gave a higher conversion [Citation16]. Although it was expected that supports with higher acidity would be more active, the addition of Al resulted in a significant decrease in the surface area of MCM-41, which could explain the poorer performance. Thus, in this work, we focused on using only RH-MCM-41 as a support. Phenol : H2 O2 mole ratio was varied and the catalytic performance of the bimetallic Pt–Fe/RH-MCM-41 catalyst was compared with that of a physical mixture of Pt/RH-MCM-41 and Fe/RH-MCM-41.
Experimental
Silica preparation and synthesis of RH-MCM-41
Rice husk silica with 98% purity and an amorphous phase was prepared similar to that in our previous work [Citation1]. It was used as the silica source for the synthesis of RH-MCM-41 with a method modified from [Citation17]. A starting gel with a molar composition of 4SiO2 :1CTAB:0.29H2 SO4 :400H2 O (CTAB= cetyltrimethyl ammonium bromide) was prepared. Gel pH was adjusted to 11 with H2 SO4 and the gel was crystallized in a Teflon-lined autoclave at 100 ° C under a static condition for 3 days. The RH-MCM-41 powder was separated by centrifugation, washed with distilled water, dried and calcined at 540 ° C for 6 h to remove the template.
Catalyst preparation and characterization
Solutions of FeCl3 and H2 PtCl6·6H2 O with a sufficient concentration to produce a Pt/Fe catalyst with Pt and Fe amounts of 0.5 and 5 wt.% were impregnated into the RH-MCM-41 support. After being dried at 100 °C overnight and calcined at 300 °C for 2 h, a catalyst denoted 0.5Pt5Fe/RH-MCM-41 was obtained. In addition, other catalysts were prepared by a similar procedure for comparison including 5Fe/RH-MCM-41, 0.5Pt/RH-MCM-41 and a physical mixture of 0.5Pt/RH-MCM-41 and 5Fe/RH- MCM-41. The physical mixture was prepared by mixing 0.05 g of 5Fe/RH-MCM-41 and 0.05 g of 0.5Pt/RH- MCM-41 and grinding for 30 min.
The RH-MCM-41 support and all the prepared catalysts were characterized by XRD using CuKα radiation on a Bruker AXS D5005 diffractometer, by N2 adsorption–desorption measurement at −196 °C in the relative pressure (P/P0) range of 0.01–0.99 on a micromeritics (ASAP 2010) analyzer, and by TEM at an operating voltage of 120 kV on a JEOL JEM 2010. In addition, the oxidation of Fe in 0.5Pt5Fe/RH-MCM-41 and 5Fe/RH-MCM-41 was determined by XANES with the Fe K-edge energy at room temperature in the transmission mode at the Synchrotron Light Research Institute (public organization). The linear background, determined by the least-squares fitting of the pre-edge experimental points, was subtracted from the experimental spectrum and the maximum of the Fe peak was compared with reference materials.
Catalytic testing on phenol hydroxylation
The 0.5Pt5Fe/RH-MCM-41 catalyst (0.05 g), phenol and H2 O2 solution (30% weight by volume) were mixed in a round bottle equipped with a magnetic stirrer and a reflux condenser. The phenol : H2 O2 mole ratios were 2 : 1, 2 : 2, 2 : 3 and 2 : 4 and the reaction was carried out at 70 °C for 3 h. Sampling was conducted every hour and the solution was separated from the catalyst and analyzed using a gas chromatograph (Shimadzu GC14-A) equipped with a capillary column and a flame ionization detector. Temperatures of the GC injector and column were 220 and 190 °C, respectively. The most suitable reactant ratio was used to test the physical mixture of 0.5Pt/RH-MCM-41 and 5Fe/RH-MCM-41.
To confirm the benefit of using a mesoporous support, the catalytic performance of 0.5Pt5Fe/RH-MCM-41 was compared with that of 0.5Pt5Fe/RH-SiO2 under similar testing conditions mentioned above.
Results and discussion
The XRD patterns of the calcined RH-MCM-41, 0.5Pt/RH-MCM-41, 5Fe/RH-MCM-41 and 0.5Pt5Fe/ RH-MCM-41 are shown in figure (a). The parent RH-MCM-41 showed a strong peak at 2.3° and small peaks at 4.0° and 4.5°, corresponding to the 100, 110 and 200 reflections of a hexagonal lattice, respectively [Citation18]. The intensity of the main peak decreased after metal addition indicating a decrease in RH-MCM-41 crystallinity. The metal interacted with the surface of RH-MCM-41 and caused partial structural destruction. No peaks of Fe or Pt in the RH-MCM-41 supported samples were detected by XRD, indicating that metal particles dispersed well on RH-MCM-41.
Figure 1 (a) XRD patterns and (b) N2 adsorption isotherms of RH-MCM-41- and RH-MCM-41-supported catalysts.
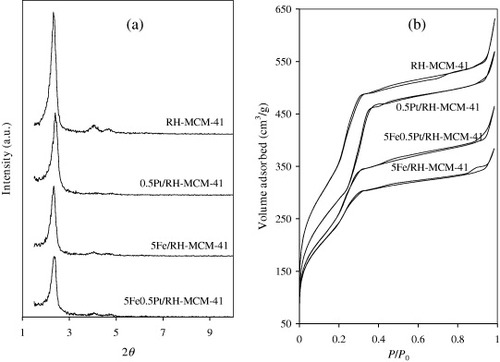
The N2 adsorption isotherms of RH-MCM-41, 5Fe/ RH-MCM-41, 0.5Pt/RH-MCM-41 and 0.5Pt5Fe/RH- MCM-41 are shown in figure (b). All isotherms were type IV, typical of mesoporous materials. At the beginning, the adsorbed amount increased rapidly and then saturated owing to monolayer adsorption at the external surfaces. The amount of adsorbed N2 increased again before reaching a nearly constant volume. This range corresponded to N2 adsorbed in the mesopores of RH-MCM-41 and the catalyst samples. The adsorbed amounts of N2 in all the catalysts were lower than that in the parent RH-MCM-41 indicating that the surface areas of the catalysts decreased after the metal loading. However, the amount of adsorbed N2 in this range for the catalyst samples did not increase sharply as in RH-MCM-41, indicating that some mesopores might have collapsed during the metal loading. Another possible explanation of the decrease in surface area was that the pores of RH-MCM-41 were blocked by metal particles.
Table shows the crystallinities of 0.5Pt/RH-MCM-41, 5Fe/RH-MCM-41 and 0.5Pt5Fe/RH-MCM-41 relative to that of the parent RH-MCM-41. The calculation was conducted by comparing the area of the main XRD peak of the catalyst samples with that of the parent RH-MCM-41. Table also shows the surface area from nitrogen adsorption. Both the crystallinity and surface area of RH-MCM-41 decreased after the metal loading.
Table 1 Relative crystallinities and surface areas of RH-MCM-41- and RH-MCM-41-supported catalysts.
The TEM images of RH-MCM-41 (figure (a)) show an ordered structure of a regular hexagonal array. TEM images of all the catalysts showed well-ordered structures. Metal nanoparticles were observed in some of the catalysts.
Figure 2 (a) TEM images of RH-MCM-41 and RH-MCM-41-supported catalysts and (b) Fe K-edge XANES spectra of Fe-containing catalysts compared with reference materials.
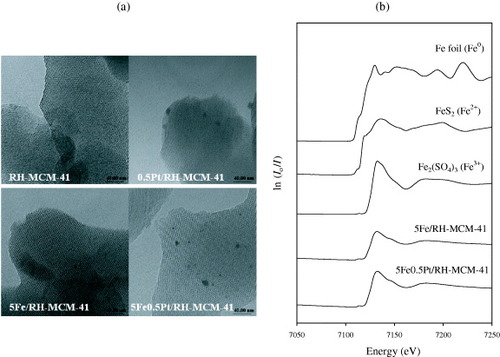
The Fe K-edge XANES spectra of 5Fe/RH-MCM-41 and 0.5Pt5Fe/RH-MCM-41 were compared with standards with Fe0, Fe2 + and Fe3 + in figure (b). The edge position and shape of the XANES spectra of Fe in both 5Fe/RH-MCM-41 and 0.5Pt5Fe/RH-MCM-41 were similar to those of standard Fe3 +, indicating that the oxidation state of Fe in these catalysts was 3 +.
Table shows the catalytic performance of the 0.5Pt5Fe/RH-MCM-41 catalyst for phenol hydroxylation at phenol:H2 O2 mole ratios of 2 : 1, 2 : 2, 2 : 3 and 2 : 4. The conversion of phenol increased with the amount of H2 O2. Although the conversion was highest when the phenol : H2 O2 mole ratio was 2 : 4, the selectivity for catechol was lower than those at the other ratios because another product, namely, benzoquinone from further oxidation, was also detected. Because the first three ratios produced only catechol and hydroquinone and the highest conversion among these ratios was obtained when the phenol : H2 O2 mole ratio was 2 : 3, this ratio is considered the most suitable for phenol hydroxylation over the 0.5Pt5Fe/RH-MCM-41 catalyst.
Table 2 Catalytic performances of 5Fe0.5Pt/RH-MCM-41 for phenol hydroxylation at 70 °C at various phenol : H2O2 mole ratios.
The catalytic performance of 0.5Pt5Fe/RH-MCM-41 was compared with that of the physical mixture of 0.5Pt/RH-MCM-41 and 5Fe/RH-MCM-41 at 70 °C at a phenol : H2 O2 mole ratio of 2 : 3. The conversions of phenol are compared in figure nd the selectivities are shown in table . The bimetallic 0.5Pt5Fe/RH-MCM-41 catalyst prepared by co-impregnation gave a higher phenol conversion with similar selectivities. This result confirmed that the presence of both Pt and Fe on the same RH-MCM-41 support could improve catalytic performance.
Figure 3 Percent conversions of phenol on 5Fe0.5Pt/RH-Silica, 5Fe0.5Pt/RH-MCM-41 and physical mixture of 0.5Pt/RH-MCM-41 and 5Fe/RH-MCM-41.
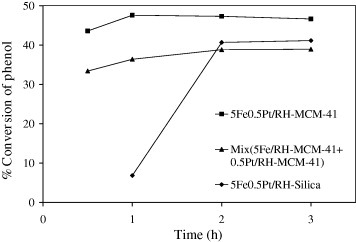
Table 3 Selectivities for phenol hydroxylation of 5Fe0.5Pt/RH-MCM-41, physical mixture of 0.5Pt/RH-MCM-41 and 5Fe/RH-MCM-41, and 5Fe0.5Pt/RH-SiO2 at phenol : H2O2 mole ratio of 2 : 3 at 70 °C.
Jia et al [Citation19] used diatomite containing 0.94 wt.% Fe as a catalyst for phenol hydroxylation. The conversion of phenol at the same amount of catalysts (0.5 g) was 40%, similar to that obtained in this work when the phenol : H2 O2 mole ratio was 1:1. However, the diatomite required longer reaction time (6 h) and higher temperature (80 °C) than 0.5Pt5Fe/RH-MCM-41. The higher Fe loading in our catalyst and good dispersion on a high surface area of RH-MCM-41 might explain this because there were more available active sites for the reaction. The conversion in this work also increased when the phenol : H2 O2 mole ratio was increased to 2 : 3. Our proposed mechanism of phenol hydroxylation with H2 O2 solution over Fe/MCM-41 is as follows: Fe3 + reacts with H2 O2 to form hydroxyl radicals, which react with phenol to form catechol and hydroquinone [Citation7]. In addition, the side reaction produces O2 and H+, and O2 may cover Pt to generate OH radicals for hydroxylation.
The catalytic performance of 0.5Pt5Fe/RH-MCM-41 was also compared with that of 0.5Pt5Fe/RH-SiO2 to confirm the contribution of a mesoporous support. Because the surface area of RH-MCM-41 was significantly higher than that of RH-SiO2 (1335 versus 235 m2 /g), better metal dispersion and better catalytic performance were expected. The results in figure and table show that phenol hydroxylation on 0.5Pt5Fe/RH-SiO2 occurred more slowly and gave a lower conversion of phenol. Thus, the dispersion of Pt–Fe catalysts on mesoporous RH-MCM-41 could improve catalytic performance.
Conclusions
When a 5Fe0.5Pt/RH-MCM-41 catalyst was prepared by co-impregnation, its crystallinity and surface area decreased upon metal addition. Metal particles could be observed on MCM-41 and the oxidation state of Fe was 3 +. The catalyst was active for phenol hydroxylation using H2 O2 as the oxidant at various phenol : H2 O2 mole ratios of 2 : 1, 2 : 2, 2 : 3 and 2 : 4. The first three ratios produced only catechol and hydroquinone, whereas the 2 : 4 ratio produced benzoquinone; thus, the 2 : 3 ratio is considered most suitable for phenol hydroxylation. The catalyst prepared by co-impregnation with Pt and Fe was more active than a physical mixture of 0.5Pt/RH-MCM-41 and 5Fe/RH-MCM-41. The catalytic performance of 5Fe0.5Pt/RH-MCM-41 was better than that of 0.5Pt5Fe/RH-SiO2 because the RH-MCM-41 support had a significantly higher surface area, resulting in a better metal dispersion.
Acknowledgment
Funding for this research was provided by Suranaree University of Technology and Synchrotron Light Research Institute (Public Organization) Grant 2-2548/PS01.
References
- KhemthongPPrayoonpokarachSWittayakunJ 2008 Kor. J. Chem. Eng. 25 861 http://dx.doi.org/10.1007/s11814-008-0142-y
- GrisdanurakNChiarakornSWittayakunJ 2003 Kor. J. Chem. Eng. 20 950 http://dx.doi.org/10.1007/BF02697304
- ChiarakornSAreerobTGrisdanurakN 2007 Sci. Technol. Adv. Mater. 8 110 http://dx.doi.org/10.1016/j.stam.2006.11.011
- MatsumotoATsutsumiKGrünMUngerK 1999 Micropor. Mesopor. Mater. 32 55 http://dx.doi.org/10.1016/S1387-1811(99)00089-X
- KannanSDubeyAKnözingerH 2005 J. Catal. 231 381 http://dx.doi.org/10.1016/j.jcat.2005.01.032
- MasendeZ P GKusterB F MPtasinskiK JJanssenF J J GKatimaJ H YSchoutenJ C 2006 Catal. Today 79–80 357 http://dx.doi.org/10.1016/S0920-5861(03)00064-6
- ChoiJYoonSJangSAhnW 2006 Catal. Today 111 280 http://dx.doi.org/10.1016/j.cattod.2005.10.037
- WuCKongYGaoFWuYLuYWangJDongL 2008 Micropor. Mesopor. Mater. 113 163 http://dx.doi.org/10.1016/j.micromeso.2007.11.013
- PreethiM E LRevathiSSivakumarTManikandanDDivakarDRupaA VPalanichamiM 2008 Catal. Lett. 120 56 http://dx.doi.org/10.1007/s10562-007-9249-8
- LiuHLuGGuoYGuoYWangJ 2008 Micropor. Mesopor. Mater. 108 56 http://dx.doi.org/10.1016/j.micromeso.2007.03.027
- HaoWLuoYDengPLiQ 2001 Catal. Lett. 2–4 73
- LetaïefSCasalBArandaPMartín-LuengoM ARuiz-HitzkyE 2003 Appl. Clay Sci. 22 263 http://dx.doi.org/10.1016/S0169-1317(03)00079-6
- MohamedM MEissaN A 2003 Mater. Res. Bull. 38 1993 http://dx.doi.org/10.1016/j.materresbull.2003.09.015
- AbboH STitinchiS JPrasadRHandS 2005 J. Mol. Catal. A: Chem. 225 225 http://dx.doi.org/10.1016/j.molcata.2004.09.007
- ParkJWangJChoiK YDongWHongSLeeC W 2006 J. Mol. Catal. A: Chem. 247 73 http://dx.doi.org/10.1016/j.molcata.2005.11.037
- ChumeeJGrisdanurakNNeramittagapongAWittayakunJ 2007 Proc. 14th Regional Symp. Chem. Eng. (Indonesia) 74
- ParkK-CYimDIhmS 2002 Catal. Today 74 281 http://dx.doi.org/10.1016/S0920-5861(02)00024-X
- JingHGuoZMaHEvansD GDuanX 2002 J. Catal. 212 22 http://dx.doi.org/10.1006/jcat.2002.3779
- JiaYHanWXiongGYangW 2007 Sci. Technol. Adv. Mater. 8 106 http://dx.doi.org/10.1016/j.stam.2006.10.003