Abstract
Layered composite materials have become an increasingly interesting topic in industrial development. Cold roll bonding (CRB), as a solid phase method of bonding same or different metals by rolling at room temperature, has been widely used in manufacturing large layered composite sheets and foils. In this paper, we provide a brief overview of a technology using layered composite materials produced by CRB and discuss the suitability of this technology in the fabrication of layered composite materials. The effects of process parameters on bonding, mainly including process and surface preparation conditions, have been analyzed. Bonding between two sheets can be realized when deformation reduction reaches a threshold value. However, it is essential to remove surface contamination layers to produce a satisfactory bond in CRB. It has been suggested that the degreasing and then scratch brushing of surfaces create a strong bonding between the layers. Bonding mechanisms, in which the film theory is expressed as the major mechanism in CRB, as well as bonding theoretical models, have also been reviewed. It has also been showed that it is easy for bcc structure metals to bond compared with fcc and hcp structure metals. In addition, hardness on bonding same metals plays an important part in CRB. Applications of composites produced by CRB in industrial fields are briefly reviewed and possible developments of CRB in the future are also described.
Introduction
Metallic composite materials, as part of a large group of materials, have been used for several decades [Citation1–13]. As modern industries develop further, there is a continuous increase in the production and use of composite materials. Among composite material technologies, the production of composite sheets by cold roll bonding (CRB) has also exhibited rapid growth and development in recent years due to its unique service performance features [Citation2–10]. A considerable amount of work has been performed on CRB [Citation1–10] and cold bonding by press, extrusion and shear [Citation2] commonly used in industries for cold bonding. CRB is a solid phase operation in which metals may be bonded by rolling at room temperature [Citation1]. CRB is also referred to cold pressure welding by rolling [Citation1–6], bonding by cold rolling [Citation7], clad sheet by rolling [Citation8], and cold roll bonding [Citation9, Citation10].
CRB can be used on a large number of materials. In addition, materials that cannot be bonded by traditional fusion often respond well to cold bonding [Citation2]. CRB causes bonding by adhesion and this requires the surfaces to be clean and to be an interatomic distance apart [Citation3, Citation4]. However, surface cleanliness is difficult to achieve without a controlled atmosphere [Citation2, Citation14, Citation15]. Under industrial or laboratory conditions without the provision of protective environments, complete cleanliness is simply not achievable. Therefore, the normal pressure is expected to be sufficiently large to satisfy bonding. The process parameters affecting the bond strength involve the surface preparation and deformation conditions [Citation4–12, Citation16], specimen size [Citation6], the storage time between surface preparation and bonding [Citation6], and the time during which the normal pressure is applied [Citation2].
In comparison with other methods, CRB is simple and can be easily automated. CRB is also considered as one of the promising methods of bonding materials from foils [Citation17–19]. Rolling is capable of producing the high interfacial pressure required to induce strong bonding between components. Recently, Tsuji et al [Citation20, Citation21] have developed an accumulative roll bonding (ARB) technique, in which a severe plastic deformation is applied in rolling. In this technique, two sheets are bonded together in a single rolling pass. By repeating this process on the same sample, a larger strain accumulation can be achieved in a composite sample. The evolution of microstructures and mechanical properties during ARB at room temperature was studied for composite sheets or strips, including Al [Citation21], Al-based alloy [Citation22], Cu–Ag alloy [Citation23], Zr-based alloy [Citation24], IF steel [Citation21, Citation25], Al/Ni [Citation26, Citation27], and Al/steel [Citation28], and multilayer foils, including Ti/Al/Nb [Citation29], Ti/Zr/Ni [Citation30], Ti/Ni [Citation31, Citation32], Al/Pt [Citation33], Al/Hf [Citation33], and Cu/Nb [Citation34]. However, interests in ARB are focused on mechanisms of grain refinement and the effect of strain on microstructural evolution and there is a little discussion about how to successfully bond two pieces of metals by rolling.
In this paper, the effects of process parameters on bonding, including surface preparation, metal hardness, crystal structure and deformation condition, as well as bonding mechanisms and theoretical models, are summarized and analyzed. As a comparison, the successful bonding by ARB operation has also been summarized for different materials rolled at room temperature. Applications of CRB to the bonding of same or different metals in industrial fields are specified and possible developments of CRB in the future are also described.
CRB
The schematic illustration of CRB for the production of layered materials is presented in figure . In this process (figure ), two or more sheets, plates or strips of metals or alloys are stacked together and then passed through a pair of rolls until an appropriate deformation is achieved to produce a solid state bonding between the original individual metal pieces. Before roll bonding, the surfaces to be bonded must be properly cleaned and prepared to remove any surface layers (figure ) [Citation1, Citation3, Citation4, Citation12]. During bonding, a high reduction in the thickness of the materials (capable of up to 50% or more in a single rolling pass) is achieved under a high pressure at the roller [Citation6]. The high reduction generates a great amount of heat and creates virgin surfaces on the materials being bonded. A bond (normally a mechanical bond) in the layered composite is thus obtained through interfacial mechanical and atomic affinity between the two metals. In general, an annealing treatment is performed after rolling (figure ) in order to increase the bond strength because the annealing treatment is expected to develop a strong metallurgical bond at the original interface of the metals [Citation18, Citation21]. After the above processes, the composite materials can be further processed by any conventional manufacturing processes to required sizes. They can be roll-formed, drawn and joined into a required component or part. As composite materials can be produced by roll bonding and further processed in coil form, their manufacturing has a high productivity and is economically cost-effective.
Evaluation of bonding quality
There are several methods used for quantifying the bond strength of layered materials, such as tension test, tensile shear test [Citation35–38], slide shear test [Citation39], multistep shear test [Citation40], peeling test [Citation16, Citation39], roller drum peel test [Citation41], and T-peel test [Citation9, Citation42]. Also, there are some methods used for the qualitative evaluation of the bond, such as bend test, torsion test, impact test and fatigue test [Citation17, Citation43]. Figure schematically illustrates the tensile shear test of bimetallic composites, which is the most widely used method for determining the bond strength.
The qualitative evaluation of the bond is performed only to determine the relative bonding quality. Testing the bond strength of thin clad metals is difficult despite the fact that the peeling test has an advantage compared with the other methods for assessing the bond strength [Citation34]. Such a difficulty arises because of the number of different metal combinations. In addition, it should be noted that the bond strength is reduced by the mechanical forces exerted during sample preparation. The American Society of Testing Materials (ASTM) and the American Society of Mechanical Engineering (ASME) have defined a variety of acceptance tests for thick clad metals used in the pressure vessel industry [Citation44], but these are not applicable to thin materials.
Manesh has recently proposed a new method, namely, an electrical resistivity test, which is used to assess the bonding quality of Cu/Al [Citation39] and Al/steel [Citation44]. The difference between the experimental and theoretical resistivities may be considered as the inherent resistivity of the bond, which would approach zero for ideal bonding. More details of the resistivity test have been described by Manesh [Citation44]. It is also shown that the resistivity test can be used as a nondestructive test for evaluating the bonding quality of Cu/Al [Citation39] and Al/steel [Citation44], and a calibration diagram has been established for the evaluation of the bonding quality. However, it is the shear strength of the bond that determines the usefulness of the layered composites in subsequent metal forming processes, such as deep drawing, stretch forming and combining the two metals [Citation25]. Thus, the bond strength mentioned in this paper is determined by a tensile shear test, unless otherwise indicated. Kendall [Citation45] addressed several methods for measuring interface properties using fracture mechanics by a cracking test, and much work has also been performed to calculate and predict the interface properties using the theory of material mechanics [Citation46–50]. When applied, it will benefit greatly the development of new bonding processes and the improvement of bonding evaluation.
Parameters affecting bonding
Many research studies on the parameters governing bonding have been carried out to understand the complex nature of the bonding mechanisms, and the conditions of the process have been well defined empirically. It has been reported that the roll bonding of metals is affected by various factors, such as the amount of deformation [Citation3, Citation15, Citation16, Citation35, Citation51–53], the type of metal under consideration [Citation54], the temperature of bonding [Citation8, Citation55, Citation56], the amount of enforcement pressure [Citation57, Citation58], the time of bonding [Citation6, Citation41, Citation57], the metal purity [Citation54], the lattice structure [Citation54], the surface preparation conditions [Citation1–4, Citation8, Citation16, Citation35, Citation51–53, Citation57, Citation59], the geometry of the deformation zone (shape factor) [Citation60], the stacking sequence [Citation61], the number of layers [Citation62], the layer thickness [Citation63, Citation64] and the type of post-heat treatment [Citation28, Citation41, Citation59, Citation65]. The difference in bonding condition leads immediately to expansion and divergence of the technological bonding methods. The main problem of this divergence is the difficulty in the genera1 analytical description, which is based mostly on the analysis and synthesis of existing processes and on experimental results. A new system model as a type of classification model is advanced and the technology is applied in industries for the production of bars, sheets and plates [Citation54]. The present article simply classifies parameters according to their effects into two groups: basic parameters and surface conditions.
Basic parameters
Although many important factors affect the bonding quality, for practical purposes, the following can be readily controlled: the rolling load, rolling speed, reduction in thickness and shape factor in rolling.
Rolling conditions.
It is obviously impossible for bonding to occur only by placing metal surfaces in contact; thus, the rolling pressure was regarded as the most important parameter [Citation4, Citation6, Citation66]. The metals must be pressed together with a sufficient force to plastically deform and insure large contact areas [Citation66]. The distribution of normal pressure in the roll gap has been measured experimentally using a photoelastic dynamometer [Citation67]. Results for the bond strength as a function of distance from the center of the bond were compared with those for a normal rolling pressure [Citation6]. It was found that increasing pressure up to a certain value increased the bond strength, but further increases in pressure had no effect.
Early experiments showed that there was a relationship between the maximum theoretical bond strength and the percentage reduction [Citation6]. It was found that the maximum strength did not develop until reduction greatly exceeded the threshold deformation, which is called the threshold reduction Rt [Citation2–6]. Rt is defined as the minimum percentage reduction that consistently results in bonding emerging from the roll gap [Citation4].
Figure shows the bond strength in shear as function of deformation reduction for bonds produced by CRB [Citation6, Citation57]. It can be found that bonding is not realized until a certain threshold deformation is reached. Beyond Rt, the bond strength increases rapidly with deformation and then slightly increases corresponding to the strength of the weaker metal for different materials [Citation57]. A previous work has also shown that in all cases, the bond strength can reach a base or maximum value at about 60–70% deformations, whereas Rt for bonding varies from one metal to another. However, bond strengths at very large deformations were difficult to obtain. Multipass rolling, instead of one-pass rolling, was carried out using aluminum and copper [Citation6], and it was found that no bonding could be achieved unless the first pass was sufficient to initiate bonding. A large deformation requires an enormous rolling force, which often exceeds the load capacity of conventional mills. Asymmetrical rolling gives distinct indications of the possibility of reducing the load by cross-shear cold rolling [Citation10].
Experiments of different rolling speeds were also carried out by Vaidyanath et al [Citation6], and the effect of strain rate on the deformation of aluminum produced by ARB was studied [Citation68]. Results revealed that lowering the roll speed decreased the threshold reduction [Citation6]. It can be related to, to some extent, the insufficient extrusion of virgin metals through cracks resulting from the fracture of the oxide film or work-hardening layer in a short time; thus, there was difficulty in bringing two surfaces with large areas into contact. In addition, high speeds can result in width changes on the top and in the following parts of specimens [Citation68].
Shape factor in rolling.
The geometry of the deformation zone or the shape factor in rolling has a great effect on bond formation and bond strength [Citation39, Citation60]. Abbasi et al [Citation39] defined the shape factor as
where L is the chordal length of the roll contact arc, h=(h0+hf)/2 is the mean thickness of the strip, r=(h0−hf)/h0 is the reduction in thickness, h0 and hf are respectively the initial and final thicknesses of the strip, and R is the roller radius. In cold rolling, it is possible to provide various shape factors by changing the parameters.
An investigation of the effect of varying the initial thickness of aluminum showed that the bond strength decreased with increasing initial thickness. However, it was found that the strength increased until the width/thickness ratio attained a value of about 6, and thereafter, the strength remained constant [Citation6]. Another investigation [Citation69] showed that a large width/thickness ratio produced a small interfacial extension for a given overall deformation, and bonding was more difficult. Results for the impact behavior of composites indicate that the impact energy increases with the number of layers [Citation62]. Also, it can be concluded that the impact energy of the composite is more sensitive to the number of layers than to the adhesive composition. In addition, the crack growth resistance of the layered materials is related to the layer thickness to some degree [Citation63]. The effects of layer number and layer dimensions may be related to the features of materials to be bonded and the stress or strain state; thus, a strong relationship should be established among the dimensions of the specimen, rolling parameters and material features.
Surface conditions
Metal surfaces are typically rough, and when two absolutely clean surfaces are pressed together, contact is expected. In practice, metal surfaces are covered with oxide films and other surface contaminants [Citation1, Citation3, Citation4, Citation11], such as grease, chemical compounds remaining after pickling, and adsorbed moisture, which inhibit bonding, at least at room temperature. Consequently, the significance of the surface before CRB is another important variable factor influencing the bond strength. Different forms and significance levels of surface preparation processes in CRB, including mechanical, thermal and chemical treatments, have been extensively investigated and discussed [Citation1–4, Citation53, Citation70, Citation71].
Adsorbed contaminants
The existence of a contaminant film would inhibit but would not prevent bonding and the decrease in bond strength [Citation3, Citation4, Citation6, Citation12]. To determine the importance of adsorbed contaminants, a series of tests were performed to relate the baking-out temperature of the surface to the increase in bond strength [Citation3]. Results revealed that the bond strength increased progressively with baking-out temperature with heating in air at temperatures above 250 °C or above 180 °C in vacuum. The marked increase in bond strength brought about by heating suggests that the major action of good surface preparation is the removal of layers of adsorbed contaminants. However, baking out at a temperature as high as 600 °C did not produce strong bonds, such as those related to scratch brushing [Citation3]. It therefore indicated that there were other significant factors affecting bonding, since heating at 600 °C did not completely remove all adsorbed materials.
Johnson and Keller [Citation14] examined the adhesion of small specimens under light loads in an ultrahigh-vacuum system, contaminants being removed from the surfaces and the pressure being reduced to maintain cleanliness during the experiments. When the surfaces were brought together under light loads, many, but not all, metals bonded together. Sherwood and Milner [Citation15] have also investigated the effect of vacuum machining on the cold bonding of some metals and found that the threshold deformation required for bonding decreases practically to zero when the surface contamination decreases below a critical level with aluminum, copper, cadmium and nickel. The threshold deformation for the bonding of harder metals, such as iron and titanium, also markedly decreases, but not to zero.
Oxide films
Composites of aluminum, copper, lead and tin were rolled after scratch brushing the surfaces and being exposed to the atmosphere for periods of 2 min to 10 days [Citation6]. The resulting bond strengths were found to decrease markedly with exposure for the first 15 min. Another investigation [Citation13] also indicated that Rt decreased with decreasing oxide thickness. It seemed that the decrease in bonding ability was relative to the increase in the thickness of the oxide film; however, a different investigation has shown that the aluminum surface with a thick anodized layer has in fact good bonding properties [Citation5].
From the results of earlier work, it appeared that the ratio of the hardness of the oxide film to that of the metal might be an important factor determining the bonding ability [Citation3]. In a previous investigation, it was suggested that a weak relationship exists between the hardness ratio of oxide to metal and the threshold deformation for some non-work-hardening metals [Citation53]. For work-hardening metals, such as aluminum and copper, there is also a weak relationship between the hardness ratio and the threshold deformation in the case of hardening aluminum and copper with different amounts of deformation [Citation53]. More extensive tests demonstrated that the ratio of film hardness to metal hardness, in the majority of common metals and alloys, is likely to be an unimportant factor in determining the bond ability [Citation53].
Placing oxide free metals in contact does not result in bonding unless there is also some shear displacement as the two surfaces come into contact. Gold was selected owing to the complete absence of the oxide film [Citation12]. It was found that, at the pressure where bonding occurred in wire-brushed specimens, highly polished specimens degreased in acetone did not bond. This behavior should be associated with the local deformation. Agers and Singer [Citation69] considered that the local deformation at the interface is more important than the macroscopic deformation. It seems that the importance of the shear displacement, besides increasing the contact area, is that it destroys the continuity of any adsorbed contaminants, which may contaminate the surface due to adsorbed air or water vapor.
Surface preparation methods
To produce a satisfactory bond in CRB, it is essential to remove the layers between the surfaces of two metals to be bonded [Citation1, Citation3, Citation4, Citation12, Citation71]. These layers are composed of oxides, adsorbed ions (ions of sulfur, phosphor and oxygen), grease, and humidity and dust particles [Citation44]. A large number of surface preparations have been investigated [Citation3, Citation4, Citation12, Citation71], which can be classified into three groups [Citation71]: (a) chemical cleaning (b) mechanical cleaning and (c) the establishment of a brittle cover layer.
Figure shows the effects of different types of surface preparation on bonding of aluminum composites [Citation3]. It was found that degreasing followed by scratch brushing gave the best bonding properties. When the procedure was reversed, Rt was higher and a lower bond strength was obtained, while electropolished surfaces did not bond even with an approximate 80% deformation. Scratch brushing is not only for cleaning but also for providing rough surfaces [Citation8], which provide a greater amount of surface asperities and promote a localized shear deformation that breaks unavoidable surface oxide films during roll bonding, contributing to the bonding of two metals [Citation53]. Consequently, surface roughening by scratch brushing greatly improved the bonding quality, reduced the pressure required to initiate bonding and gave some of the highest bond strengths. However, it has also been suggested that there exists an optimum surface preparation method for a combination of different metals with different properties [Citation35, Citation72]. For example, semibright and electroless Ni platings were optimum for the roll bonding of Al/Al, the electroless Ni plating of Cu/Cu, and the scratch brushing of Al/Cu and Al/steel.
Figure 4 Effects of different types of surface preparation on bonding of aluminum composites [Citation3] (reproduced with permission from TWI Ltd).
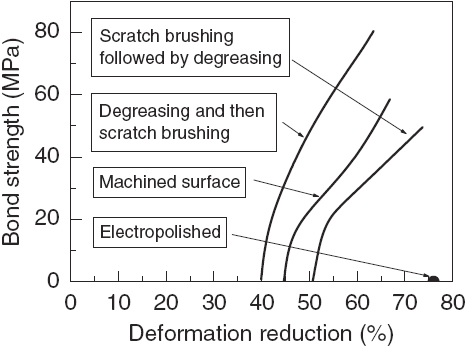
Lubricant conditions.
An investigation on CRB has been carried out under three lubrication conditions [Citation9]: no lubrication (μ≈0.15), poor lubrication (μ≈0.13) and normal lubrication (μ≈0.11). It was found that the maximum peeling force increased with increasing coefficient of friction. Moreover, the results showed that at a small deformation and a small coefficient of friction, bonding was not successful. The results also showed that Rt decreased with increasing coefficient of friction. Manesh [Citation44] has also studied the effect of friction on the bond strength of an Al clad steel strip, and the obtained results indicated that the bond strength of the Al clad steel strip increased with an increase in friction factor. This is because the mean roll pressure increases with increasing coefficient of friction between the outer layers and the rolls [Citation57, Citation58]. However, it should be noted that a large friction typically results in an excessive load and damage to the surface of the work piece.
Post-heat treatment of CRB
CRB followed by heat treatments has been carried out for aluminum, copper and steel in the temperature range of 50–900 °C depending on the type of metal [Citation73, Citation74]. In all cases, it has been shown that short-time heating at low temperatures can produce an increase in bond strength before the onset of recovery and recrystallization. The degree of improvement was marked for bonding achieved with a small deformation, and it was suggested that thermally activated short-range atomic movements were responsible for producing an improved bond. If the metallic regions are only partially bonded, heat treatment will complete bonding. If the oxide film is soluble in the metal, the treatment at a sufficiently high temperature will cause complete failure of the interface [Citation68]. In addition, brittle phases will be formed and will grow at the contact interface for some metals with increasing temperature [Citation65]; thus, an optimum time-dependent annealing temperature will be determined in the metals, achieving suitable formability and bond strength.
Bonding mechanisms and theoretical models
Bonding mechanism
Over the past decades, many attempts have been made to explain the mechanism of CRB [Citation4, Citation11, Citation12, Citation66, Citation69, Citation75, Citation76]. Optical microscopy (OM), scanning electron microscopy (SEM) and others analytical methods have shown that there are several bonding mechanisms involved in CRB [Citation10–13, Citation53, Citation66]. Four theories have been proposed thus far to explain the mechanism of CRB, i.e. the film theory [Citation4, Citation10, Citation12, Citation16, Citation54, Citation77], energy barrier theory [Citation4, Citation12], diffusion bonding theory [Citation78] and recrystallization theory [Citation75].
Vaidyanath et al [Citation6] have expressed that the film theory is the major mechanism of CRB because of the low rolling temperature. It has been found that bonding can be obtained when deformation causes fresh metal surfaces to be exposed and that the deformation reaches a value sufficiently large to establish contact bonding between two sheets. The fracture of the work-hardened surface layer or oxide film and the extrusion of virgin metals through the cracks played very important roles in the real contact between metals. Such a mechanism has been confirmed by optical and scanning electron microscopies [Citation10–13]. Bay [Citation11] suggested two mechanisms, namely, the fracture of the work-hardened surface layer and that of the contaminant film of oxides and water. Mohamed and Washbush [Citation12] established a basis indicating that the bonding ability was attributed to differences in stacking fault energy and hardness ratio and plastic properties of the oxide. Regarding the energy barrier theory, Parks [Citation75] considered that the barrier is recrystallization, because even when clean surfaces were brought into contact, no bonding occurred, indicating the presence of an energy barrier that must be overcome before bonding.
Figure [Citation1, Citation4] shows the simplified illustration of the film theory mechanisms suggested by researchers, namely, the fracture and extrusion of the work-hardened surface layer. In fact, the bond strength and mechanical properties of the composite are generally governed by both the rolling conditions and materials. Previous studies [Citation1–6, Citation53, Citation75, Citation76, Citation79] on the CRB of metals suggested that the reactions between metal bonds involved a three-stage process of (i) development of physical contact, (ii) activation of the surfaces in contact and (iii) interaction within the materials being bonded. It is believed that the mechanical bond between the metals first develops during rolling and then a strong metallurgical bond develops at the interface of the metals during CRB or following the heat treatment. However, the complex interface formed during rolling after surface preparation is not yet fully understood. There also exist more difficulties in analyzing the process and bonding mechanisms in detail.
Bonding theoretical models
Although several hypotheses on the nature of the controlling parameters have been made and some theoretical models have been developed for CRB, a quantitative decision is still difficult to make. Thus far, some theoretical models have been developed for roll bonding [Citation1, Citation6, Citation9, Citation11, Citation52, Citation76]. Vaidyanath et al [Citation6] have proposed the following equation for predicting the bond strength:
(2)
where σB is the bond strength, σ0 is the strength of the base metal, and Rf is the final reduction at the end of the rolling pass. In this model, the bonded area is proportional to Rf. Subsequently, Wright et al [Citation1] have proposed another relationship between the bond efficiency and the rolling deformation:
(3)
where H is the empirical hardening factor and Rt is the reduction in threshold deformation.
On the basis of the oxide and contaminant film mechanisms, Bay [Citation11] proposed a theoretical model showing the basic effects of both surface and normal pressures on the bond strength, and the equation is:
(4)
where ψ is the fraction of the film layer with respect to the total area, Y the surface exposure of the bond interface surface, p the normal pressure on base metal surfaces, pE the extrusion pressure, and Y′ the threshold surface exposure for the contaminant film.
Recently, Hosseini and Kokabi [Citation9] have developed a new approach for estimating bond efficiency from peel test results for a 5754-aluminum alloy used as the testing material. Das and Nafari [Citation80] suggested that the electronic interaction has an important role in bonding two metals and developed a theoretical model using the density functional formalism. However, the general mechanism of bonding during rolling is still unclear; thus, there are some difficulties in precisely determining the bond strength using theoretical models, particularly in the case of bonding different metals.
Discussion
Cold bonding map of metals
Figure shows the map including different materials for successful cold bonding by rolling and/or by applying pressure [Citation2–6, Citation12, Citation57, Citation68–71, Citation76, Citation79, Citation81–84] and ARB [Citation20–33, Citation85] according to the lattice structure and hardness of the metal at room temperature.
Figure 6 Map including different metals for successful cold bonding by rolling and/or by applying pressure and ARB according to lattice structure and hardness of metals.
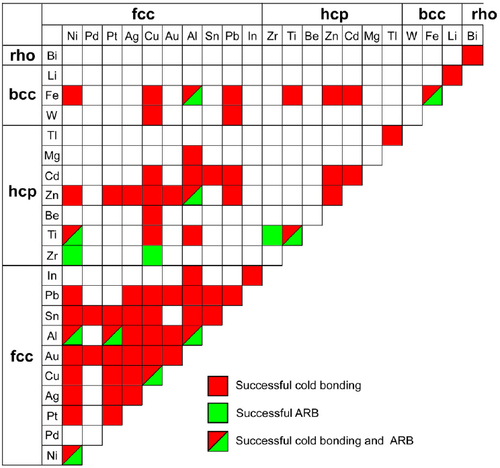
From figure , it can be found that metals with a face-centered-cubic (fcc) lattice structure are best suited for cold bonding, provided that they do not work-harden rapidly. Aluminum and copper are most easily cold bonded. Other fcc metals that may be cold-bonded readily are gold, silver, and platinum. Hexagonal metals, namely, magnesium, cadmium and zirconium, have bonding properties considerably inferior to those of cubic metals, namely, aluminum, copper, iron and lead. This is shown by a higher threshold deformation and a lower maximum strength. The reason suggested for this is that with the hexagonal metals, the two oxide films break up independently of each other, as opposed to coherent break up with the cubic metals, thus inhibiting bonding over a larger extended interface [Citation53]. In addition, the work hardening at the interface possibly becomes pronounced or fracture occurs elsewhere in the piece for hcp or bcc metals compared with fcc ones.
Hardness and hardness ratio
Figure shows the relationship between hardness and Rt for same metals [Citation6, Citation53] and figure shows the relationship between hardness ratio and Rt for different metals during rolling at room temperature [Citation4, Citation57]. It should be noted that the hardness is an approximate value.
Figure indicates that Rt for bonding varies from one metal to another, and it is noted that Rt generally increases with an increase in hardness for the same materials. Thus, it is necessary to increase the deformation reduction in the bonding of harder materials. However, the trend disagrees with the results of Tylecote et al [Citation53], who showed that increasing the hardness of a metal by prestraining made small-tool bonding easier. For this reason, the effects of prestraining on the bond strengths of aluminum and copper were investigated [Citation6]; it was found that aluminum increasing the initial hardness caused no effect, whereas copper made bonding more difficult. Thus, the results of Tylecote et al [Citation53] were not fundamental to CRB but specific to small-tool bonding, which was probably due to the alternation of the deformation pattern and/or the bonding area [Citation6].
It should be pointed out that the hardness ratio is the value of high to low hardness in the two different metals in figure . Different materials exhibit different ductilities, indicating that plastic deformation differs in metals during rolling. Only by increasing the amount of deformation during CRB, the process can introduce a deformed region into the interior of the harder material, maximally exposing the fresh metal to potential bonding. Decreasing the hardness or hardness ratio of metals to be bonded can decrease Rt, which is helpful for bonding. However, for different hardness ratios, the bonding experiment of metals was only performed between copper and other metals; thus, the nature of bonding may be not necessary for bonding many other metals. Although there are many research studies on the bonds of different metals [Citation2, Citation16–18, Citation39, Citation58, Citation78], hardness data for the tested materials have not been indicated in the literature. A previous investigation [Citation86] indicated that different metal combinations have different interfacial bonding mechanisms: some bonding mechanisms depend on metallurgic bonding, others depend on mechanical force and metal bonding. Therefore, more data and information are necessary to support the regularity and further study is needed in the future.
Applications of composites produced by CRB
CRB is applicable to most of the ductile metals and their alloys, such as copper, aluminum, lead, zinc, nickel, silver, platinum, gold, palladium, and cadmium. Published reports indicate that various methods have been used in bonding same and different metal combinations for at least 50 years. Layered composite materials have been widely used in industries as well as in our daily life.
Cold bonding has many advantages over hot roll bonding; for example, it is carried out at low temperatures, and thus, undesirable phase transformations and/or microstructures can be avoided. Moreover, it yields good surface quality and is low cost, which has recently become possible, because of the new materials that can be made. As it is performed at room temperature, there are no thermal effects on the parts being bonded, and it is fast, simple and inexpensive to operate.
Metallic composite materials can be produced in plate, strip, foil, tube, rod and wire forms. Traditionally, layered composites have provided many solutions in terms of functionality or cost saving or both. Functionalities provided by different metals can be grouped into structural, thermal, electrical, magnetic, corrosion resistant, joining and cosmetic applications [Citation87]. For example, in corrosion resistant applications, layered composite metals can be divided using the following systems [Citation87, Citation88]. (1) Noble metal system, which is a relatively inexpensive base metal covered with a corrosion-resistant metal on the surface, for examples, stainless steel/steel, Ni alloy/steel, Pt/steel, and Au/brass. (2) Corrosion barrier system, which is a combination of two or more metals to form a barrier to prevent perforation galvanically, which otherwise will occur on each of the metals owing to pitting corrosion, for example, low-carbon steel/304 stainless steel for chloride-ion-containing environment applications, Cu/430 stainless steel/Cu for communication cable shields buried in acidic soil. (3) Sacrificial metal system, in which an active metal (Zn, Al, or Mg) of the galvanic series is bonded to protect a more noble metal. Al/stainless steel composites are good examples of this system [Citation43, Citation89]. (4) Diffusion-alloyed system, in which a new alloy surface is formed by diffusion where such an alloy surface is difficult to produce by conventional methods. The FeCrAl alloy produced by the diffusion annealing of an Al/FeCr/Al composite is a good example of such a system. Finally, a complex multilayer system is used for dual environments or multiple requirements. The Ti/stainless steel/Ni composite sheet used as the bipolar electrode in a fuel cell is one such application [Citation87]. The Ni/stainless steel/Cu composite used for a bottom battery cap is another example, where the outer Ni surface layer provides low contact resistance and atmospheric corrosion resistance; cosmetic appearance thick stainless steel in the core is for strength and deep drawing, perforation corrosion resistance and total low cost, and the Cu surface layer provides an electrode contact surface for electrochemical cell performance [Citation87].
Table 1 shows some applications of composites produced by CRB. By using composites, such as an Al/Cu plate with 80% Al, the weight of building plates is reduced by half compared with those of conventional Cu plates [Citation2]. On the other hand, composites, such as the Al/steel used for an automotive trim, possess good combination of properties; the steel provides strength and good appearance, whereas the aluminum can be easily fabricated and can protect the auto body from galvanic corrosion [Citation2, Citation92]. Mechanical behaviors and formability of multilayer composite materials have been studied, and mechanisms responsible for many of their unique properties have been proposed [Citation89, Citation99–101]. The evaluation of the composites would be beneficial for better understanding of the deformation mechanism and would greatly promote the applications of the composites in industrial fields.
Some applications of different metals produced by CRB.
All metals are surrounded by surface layers (such as oxide layers), which must be disrupted if they are to be bonded. Cold roll bonding, carried out at room temperature, relies upon the use of high compressive pressures. This provides interfacial deformations of 50% to 60% that break the oxide layers to expose a fresh, uncontaminated metal that makes contact. However, it is highly specialized with respect to design and materials to be bonded. As the bonds are formed in the solid state and are difficult to inspect, reliance must be placed on process control. However, there are many gaps to fill in the knowledge of the fundamentals of cold bonding and it is hoped that an extensive research work should be carried out. For the development of new methods of production and new forms of products, it is necessary to carry out a wide range of theoretical and experimental investigations on deformation in rolling.
Currently, there are some problems to be solved and some limitations to be overcome to produce composites by CRB.
There are some difficulties in explaining the mechanism of CRB and evaluating bond quality by relating mechanical properties to interface behaviors. | |||||
A few research studies or reports are focused on the service performance characteristics of composites produced by CRB, such as drawing quality, compatibility of deformation and anisotropic property. | |||||
Attention should be paid to the recycling, particularly for different metal bonds, and lowering of the cost of composites, depending on the material design and requirement. |
It is believed that the range of CRB applications will increase considerably and that the process will be enhanced if the threshold deformation can be reduced and the process made less sensitive to surface preparation. The use of cross-shear cold rolling (CSCR) has shown the advantage of significantly reducing the rolling load compared with conventional cold rolling while still ensuring the same primary bond strength [Citation10, Citation102, Citation103]. In cross-shear roll bonding, two identical work rolls are driven at different peripheral speeds; thereby, a shear zone in the central region of the roll gap is established in the latter case. The relative sliding at the interface between the two metals is enhanced at the entrance, whereas the plastic flow of the two metals becomes more homogenous at the exit of the roll gap [Citation102]. The application of the cross-shear roll bonding of an Al–Zn alloy to a mild steel was shown to yield a higher bond strength than conventional roll bonding [Citation103]. Improvements of up to 20–23% in bond strength were observed, and the strongest bond was obtained at a reduction of 50%, whereas 65% was required in the case of conventional roll bonding [Citation103].
Conclusions
In this paper, we provide a brief overview of CRB and its applications, and discuss the feasibility of this technology in the fabrication of metallic layered-structure interconnects. Our general conclusions are as follows: good bonds can be formed only if there is an intimate contact between metals, which allows an interatomic attractive force to operate. An adequate pressure must be applied to provide a sufficient deformation so that surface films or contaminants are broken or removed. The scratch brushing of surfaces to be bonded can improve CRB; thus, it may be reasonable to conclude that roughness is one of the important factors affecting bonding. It also shows that it is easy for bcc structure metals to bond and that hardness on bonding same metals and hardness ratio on bonding different metals play important roles in CRB. Although there are some problems to be solved and some limitations to be overcome to produce composites by CRB, the process will be enhanced if the critical values of deformation can be reduced and the process made less sensitive to surface preparation. The use of cross-shear cold rolling (CSCR) has shown the advantage of significantly reducing the rolling load compared with conventional cold rolling.
Acknowledgment
The authors wish to express their appreciation to TWI Ltd and Maney Publishing for the permission to reproduce figures.
References
- WrightP KSnowD ATayC K 1978 Met. Technol. 1 24
- BayN 1986 Met. Construct. 8 486
- VaidyanathL RMilnerD R 1960 Br. Weld. J. 1 1
- CaveJ AWilliamsJ D 1973 J. Inst. Met. 101 203
- DonelanJ A 1959 Br. Weld. J. 6 5
- VaidyanathL RNicholasM GMilnerD R 1959 Br. Weld. J. 6 13
- JiangYPengD SLuDLiL X 2000 J. Mater. Process. Technol. 105 32 http://dx.doi.org/10.1016/S0924-0136(00)00553-7
- YahiroAMasuiTYoshidaTDolD 1991 ISIJ Int. 31 647 http://dx.doi.org/10.2355/isijinternational.31.647
- HosseiniH R MKokabiA H 2002 Mater. Sci. Eng. A 335 186 http://dx.doi.org/10.1016/S0921-5093(01)01925-6
- PanDGaoKYuJ 1989 Mater. Sci. Technol. 5 934
- BayN 1983 Weld. Res. Suppl. 5 137
- MohamedH AWashbushJ 1975 Weld. Res. Suppl. 9 302
- CantalejosN ACusminskyG 1972 J. Inst. Met. 100 20
- JohnsonK IKellerD V 1967 J. Appl. Phys. 38 1896 http://dx.doi.org/10.1063/1.1709780
- SherwoodW CMilnerD R 1969 J. Inst. Met. 97 1
- ManeshH DTaheriA K 2004 Mater. Sci. Technol. 20 1064
- KarakozovE SVasilevV NParaevS A 1991 Weld. Int. 5 300
- LuoJ GAcoffV L 2004 Mater. Sci. Eng. A 379 164 http://dx.doi.org/10.1016/j.msea.2004.01.021
- BarlowC YNielsenPHansenN 2004 Acta Mater. 52 3967 http://dx.doi.org/10.1016/j.actamat.2004.05.012
- SaitoYUtsunomiyaHTsujiNSakaiT 1999 Acta Mater. 47 579 http://dx.doi.org/10.1016/S1359-6454(98)00365-6
- TsujiNItoYSaitoYMinaminoY 2002 Scr. Mater. 47 893 http://dx.doi.org/10.1016/S1359-6462(02)00282-8
- TsujiNIwataTSatoMFujimotocSMinaminoY 2004 Sci. Technol. Adv. Mater. 5 173 http://dx.doi.org/10.1016/j.stam.2003.10.019
- OhsakiSKatoSTsujiNOhkuboTHonoK 2007 Acta Mater. 55 2885 http://dx.doi.org/10.1016/j.actamat.2006.12.027
- HsiehP JHungY PHuangJ C 2003 Scr. Mater. 49 173 http://dx.doi.org/10.1016/S1359-6462(03)00207-0
- SahaRRayaR KBhattacharjeeD 2007 Scr. Mater. 57 257 http://dx.doi.org/10.1016/j.scriptamat.2007.03.055
- SauvageXDindabG PWildebG 2007 Scr. Mater. 56 181 http://dx.doi.org/10.1016/j.scriptamat.2006.10.021
- MinG HLeeJ MKangS BKimH W 2006 Mater. Lett. 60 3255 http://dx.doi.org/10.1016/j.matlet.2006.03.001
- ManeshH DTaheriA K 2003 J. Alloys Compounds 361 138 http://dx.doi.org/10.1016/S0925-8388(03)00392-X
- ZhangR GAcoffV L 2007 Mater. Sci. Eng. A 463 67 http://dx.doi.org/10.1016/j.msea.2006.06.144
- DindaG PRosnerHWildeG 2005 Scr. Mater. 52 577 http://dx.doi.org/10.1016/j.scriptamat.2004.11.034
- InoueHIshioMTakasugiT 2003 Acta Mater. 51 6373 http://dx.doi.org/10.1016/j.actamat.2003.08.009
- DingH SLeeJ MLeeB RKangS BNamT H 2005 Mater. Sci. Eng. A 408 182 http://dx.doi.org/10.1016/j.msea.2005.07.055
- HebertR JPerepezkoJ H 2004 Scr. Mater. 50 807 http://dx.doi.org/10.1016/j.scriptamat.2003.11.047
- JhaS CDelagiR GForsterJ AKrotzP D 1993 Metall. Mater. Trans. A 24 15 http://dx.doi.org/10.1007/BF02669597
- ZhangWBayN 1997 Weld. Res. Suppl. 8 326
- KunduSGhoshMChatterjeeS 2004 ISIJ Int. 44 1882 http://dx.doi.org/10.2355/isijinternational.44.1882
- GuessT RAllredR EGerstleF P 1977 J. Test. Eval. 5 84
- ForsterJ AJhaSAmatrudaA 1993 J. Miner. Met. Mater. Soc. 6 35
- AbbasiMSalehiM TTaheriA K 2001 Z. Metallk. 92 423
- BlickensderferRBurrusJ M 1984 J. Test. Eval. 12 3
- ButlinJMackayC A 1979 Sheet Met. Ind. 11 1063
- ChenC YChenH LHwangW S 2006 Mater. Trans. 47 1232 http://dx.doi.org/10.2320/matertrans.47.1232
- MooreJ JWilsonD VRobertsW T 1981 Mater. Sci. Eng. A 48 113 http://dx.doi.org/10.1016/0025-5416(81)90071-9
- ManeshH D 2006 Mater. Sci. Technol. 22 634 http://dx.doi.org/10.1179/174328406X83914
- KendallK 1998 Mater. Sci. Technol. 14 504
- LugscheiderEReimannHKnotekO 1977 Weld. Res. Suppl. 6 189
- KolmogorovV LZalazinskyA G 1998 J. Mater. Process. Technol. 75 157 http://dx.doi.org/10.1016/S0924-0136(97)00320-8
- KassapoglouCLagaceP A 1986 Trans. ASME 53 744
- PaganoN JPipesR B 1973 Int. J. Mech. Sci. 15 679 http://dx.doi.org/10.1016/0020-7403(73)90099-4
- KimD MHongC S 1992 Compos. Sci. Technol. 43 147 http://dx.doi.org/10.1016/0266-3538(92)90005-N
- LeH RStucliffeM P FWangP ZBursteinG T 2004 Acta Mater. 52 911 http://dx.doi.org/10.1016/j.actamat.2003.10.027
- ZhangWBayN 1997 Weld. Res. Suppl. 10 417
- TylecoteR FHowdDFurmidgeJ E 1958 Br. Weld. J. 1 21–38
- LukaschkinN DBorissowA PErlikhA I 1997 J. Mater. Process. Technol. 66 264 http://dx.doi.org/10.1016/S0924-0136(96)02538-1
- AnJLuYXuD WLiuY BSunD RYangB 2001 J. Mater. Eng. Pref. 10 131 http://dx.doi.org/10.1361/105994901770345123
- YanHLenardJ G 2004 Mater. Sci. Eng. A 385 419
- McEwanK J BMilnerD R 1962 Br. Weld. J. 9 406
- TabataTMasakiSAzekuraK 1989 Mater. Sci. Technol. 5 377
- NicholasM GMilnerD R 1962 Br. Weld. J. 9 469
- TaheriA KMajlessiS A 1992 J. Mater. Eng. Pref. 2 285 http://dx.doi.org/10.1007/BF02648629
- PaganoN JPipesR B 1971 J. Compos. Mater. 5 50 http://dx.doi.org/10.1177/002199837100500105
- MaroufB TBagheriRMahmudiR 2004 Mater. Lett. 58 2721 http://dx.doi.org/10.1016/j.matlet.2004.03.024
- OsmanT MLewandowskiJ JLesuerD R 1997 Mater. Sci. Eng. A 229 1 http://dx.doi.org/10.1016/S0921-5093(97)00001-4
- HerakovichC T 1982 J. Compos. Mater. 16 216 http://dx.doi.org/10.1177/002199838201600305
- ManeshH DTaheriA K 2003 Mater. Des. 24 617
- BurtonM S 1954 Weld. J. 33 1051
- SmithC LScottF HSylwesttrowiczW 1952 J. Iron Steel Inst. 170 347
- TsujiNToyodaTMinaminoYKoizumiYYamaneTKomatsuMKiritaniM 2003 Mater. Sci. Eng. A 350 108 http://dx.doi.org/10.1016/S0921-5093(02)00709-8
- AgersB MSingerA R 1964 Br. Weld. J. 11 313
- RollasonE C 1959 Br. Weld. J. 6 1
- ClemensenCJuelstorpOBayN 1986 Metal Const. 10 625
- ZhangWBayN 1997 Weld. Res. Suppl. 9 361
- AbbasiMTaheriA KSalehiM T 2001 J. Alloys Compound 319 233 http://dx.doi.org/10.1016/S0925-8388(01)00872-6
- TylecoteR FWynneE J 1963 Br. Weld. J. 6 385
- ParksJ M 1953 Weld. J. Suppl. 32 209
- BayN 1986 Metal Const. 6 369
- WuH YLeeSWangJ Y 1998 J. Mater. Process. Technol. 75 173 http://dx.doi.org/10.1016/S0924-0136(97)00323-3
- MitaniYVargasRZavalaM 1984 Thin Solid Films 111 37 http://dx.doi.org/10.1016/0040-6090(84)90346-8
- PengX KWuhrerRHenessGYeungW Y 1999 J. Mater. Sci. 34 2029 http://dx.doi.org/10.1023/A:1004543306110
- DasM PNafariN 1986 Solid State Commun. 58 29 http://dx.doi.org/10.1016/0038-1098(86)90880-X
- DurstG 1956 J. Met. 3 328
- HolmesE 1959 Br. Weld. J. 6 29
- MuktepavelaFManiksJ 1998 Nanostruct. Mater. 10 479 http://dx.doi.org/10.1016/S0965-9773(98)00090-7
- MovahediMMadaah-HosseiniH RKokabiA H 2000 Mater. Sci. Eng. A at press, doi: 10.1016/j.msea.2007.10.019
- NakamuraTKitaharaHLeeJ GTsujiN 2007 Mater. Sci. Forum 561–565 685
- LiY TDuZ YMaC Y 2002 Trans. Nonferrous Met. Soc. China 12 814
- ChenLYangZJhaBXiaGStevensonJ W 2005 J. Power Sources 152 40 http://dx.doi.org/10.1016/j.jpowsour.2005.01.055
- ASM Handbook vol 13 A Corrosion 1993 pp 687
- MooreJ JWilsonD VRobertsW T 1981 Mater. Sci. Eng. A 48 123 http://dx.doi.org/10.1016/0025-5416(81)90072-0
- BaeD SKimS KLeeS PShibayamaTBaeD H 2007 Key Eng. Mater. 345–346 1497
- KorshchikovV DZasukhaP FEshchenkoV FNikiforovV K 1968 STAL in English 5 416
- CoomanB C DDillenHStormsHBultinckIBuyssePRitchieI GKuhnMFiorucciM 1994 J. Alloys Compounds 211–212 619 http://dx.doi.org/10.1016/0925-8388(94)90581-9
- PendrousR CBramleyA NPollardG 1984 Met. Technol. 11 280
- MengLZhangLZhouS PYangF T 2003 Mater. Sci. Technol. 19 779 http://dx.doi.org/10.1179/026708303225002785
- KavaranaF HRavichandranK SSahayS S 2000 Scr. Mater. 42 947 http://dx.doi.org/10.1016/S1359-6462(00)00318-3
- QuinnJ P 1971 Met. Progress 100 91
- CooperD R 1974 Sheet Metal Ind. 51 42
- MalimT H 1966 Iron Age 198 57
- LesuerD RSynC KSherbyO DWadsworthJLewandowskiJ JHuntW H 1996 Int. Mater. Rev. 41 169
- BordeauxFYavariR 1990 Z. Metallk. 81 130
- SemiatinS LPiehlerH R 1979 Metall. Trans. A 10 97 http://dx.doi.org/10.1007/BF02686412
- ZhangWBayN 1994 Int. J. Join. Mater. 6 157
- BayNBjerregaardHPetersenS BSantosC H G 1994 J. Mater. Process. Technol. 45 1 http://dx.doi.org/10.1016/0924-0136(94)90309-3