Abstract
Lead-free piezoelectric ceramics (1−x)(Na0.5K0.5)NbO3-xBiFeO3 (x=0∼0.07) were synthesized by the solid-state reaction. Differential scanning calorimetry (DSC) measurements revealed that an increase in the amount of BiFeO3 dopant resulted in a decrease in the orthorhombic-tetragonal and tetragonal-cubic phase transition temperature of the material. One percent BiFeO3 additive suppressed grain growth, which not only benefits the sintering of ceramics but also enhances the piezoelectric and ferroelectric properties, where d33=145pC/N, kp=0.31, Qm=80, Pr=11.3 μC cm−2 and Ec=16.5 kV cm−1. As xBF>0.01, both piezoelectric and ferroelectric properties decreased rapidly with an increasing amount of dopant.
Introduction
To conquer the toxicity of widely used PZT-based piezoelectric materials, many lead-free materials, including Bi-based [Citation1, Citation2], BaTiO3-based [Citation3, Citation4], and alkaline niobate- based compounds [Citation5–8], have been studied. Among these materials, the perovskite structure (Na, K)NbO3 forms a morphotropic phase boundary, similar to the PZT, with the ratio of sodium to potassium near 1:1. It shows excellent characteristics such as a high Curie point and relatively high piezoelectricity. However, a dense ceramic body for (Na, K)NbO3 is difficult to obtain by ordinary sintering. In order to resolve this problem, two methods have been used. One is to develop new techniques such as hot-pressing [Citation9], spark plasma sintering [Citation10] and reactive template grain growth [Citation11], but all of these techniques are relatively high in cost. The other is to modify (Na, K)NbO3 ceramics by using dopant to form solid solutions. So far, doped materials have been grouped into two perovskite compounds (Na, K)NbO3-A+1B+5O3 and (Na, K)NbO3-A+2B+4O3. For example, (Na, K)NbO3-LiNbO3 [Citation12, Citation13], (Na, K)NbO3-LiTaO3 [Citation14], (Na, K)NbO3-LiSbO3 [Citation15, Citation16], and (Na, K)NbO3-BaTiO3 [Citation17] have been studied and found to show better sintering characteristics and piezoelectric properties than nondoped materials.
BiFeO3 a rhombohedrally distorted perovskite-type A+3B+3O3 structure with the space group R3c has a high Curie temperature of about 820–850 °C. It has been successfully applied to PZT ceramics to form a solid solution in order to lower the hot-pressing temperature and improve the piezoelectric properties [Citation18].
In the present study, we attempt to prepare (1−x)(Na0.5K0.5)NbO3-xBiFeO3 by the traditional solid- state reaction method and obtain improved piezoelectric, ferroelectric and ceramic sintering properties of the as-prepared material with a suitable BiFeO3 dopant.
Experiment
The traditional solid-state reaction was used to prepare (1−x) (Na0.5K0.5)NbO3-xBiFeO3 (abbreviated to KNN-BF100x) ceramics. Analytical reagent oxides and carbonates (Nb2O5, Bi2O3, Fe2O3, K2CO3 and Na2CO3) were used as starting materials. They were accurately weighed in the desired composition and milled for 10 h by planetary milling with zirconia balls and alcohol media. After calcination at 900 °C for 5 h, the powders were ground in mortar and pressed into pellets of 11 mm in diameter and 1 mm in thickness using 5 wt.% PVA as binder. After burning off the PVA, the pellets were sintered at 1100 °C for 3 h. Silver paste was fired on both sides of the samples as the electrodes for the piezoelectric measurements. The ceramic samples were poled in 100 °C silicon oil under 3 kV mm−1 for 15 min.
The crystal structures were determined using an x-ray diffractometer (Mac Science, M21XVHF22). The morphologies of the samples were studied by field-emission scanning electron microscopy (FE-SEM, LEO1530). The piezoelectric constant d33 was measured using a quasi-static d33 meter (China Academy of Acoustics, ZJ-3). The P-E hysteresis loop was measured at room temperature using a ferroelectric tester (aixACCT, TF Analyzer 2000) at 50 Hz. The electromechanical coupling coefficients kp and mechanical quality factor Qm were calculated by a resonance-antiresonance method with an impedance analyzer (Agilent, HP4194A). The phase transition of samples was determined by differential scanning calorimetery (TA, DSC TA-Q200) with a heat rate of 20 °C min−1.
Results and discussion
Figure shows the XRD patterns of KNN-BF powders calcined at 900 °C for 5 h. The phase structure of the samples with xBF<0.07 of dopant was a single perovskite phase. With xBF=0.07, a second phase, K2Nb4O11, appeared. With increasing BF content, the splitting between two diffraction peaks of (001) and (100) near 22° as well as (002) and (200) near 45° gradually disappears, indicating the phase transition from an orthorhombic to a pseudocubic phase. A MPB between the ferroelectric orthorhombic and the pseudocubic phase was determined to be at approximately 0.01x0.03.
The DSC heating curves of KNN-BF were measured to reveal the phase transition temperatures (figure ). According to the phase diagram [Citation19], the KNN solid solution was orthorhombic at room temperature and it underwent two phase transitions from the orthorhombic to the tetragonal phase (O–T) at 190 °C and from the tetragonal to the cubic phase (Tc) at 400 °C. Figure indicated endothermic peaks at 189 °C and 414 °C for KNN. At xBF=0.01, the transition temperature Tc decreased from 414 °C to 374 °C and the O–T transition temperature decreased from 189 °C to 97 °C. With the BiFeO3 content increasing, KNN-BF exhibited similar behavior but the peak of phase transitions became obscure compared with the undoped KNN. Thus, the O–T transition temperature is difficult to determine exactly above room temperature.
The SEM micrograph of KNN-BF powders showed cubic shapes (see figure (a)) and BiFeO3 obviously suppressed the grain growth of the ceramics from about 1 μm at xBF=0 to about 100 nm at xBF=0.01 (see figure (b)). The driving force for grain growth originated from the surface energy of grains, which was released during the grain growth. When the dopant BiFeO3 concentration was higher than the critical one (xBF=0.01), the energy required for grain growth could not be supplied. In the present case, the particle size of the 0.01-BiFeO3-doped sample was smaller than that of KNN, which benefited the sintering of the ceramics.
Figure 3 SEM micrograph of KNN-BF powders calcined at 900 °C for 5 h with (a) x=0 and (b) x=0.01, and SEM micrographs of fracture surface of KNN-BF ceramics sintered at 1100 °C for 3 h with (c) x=0 and (d) x=0.01.
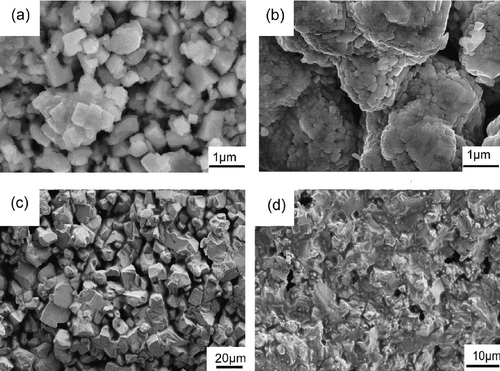
Figures (c) and (d) show the SEM micrographs of the fracture surface of KNN-BF ceramics sintered at 1100 °C for 3 h. For pure KNN ceramics, the sizes of grains were still of micron order, and the grain boundary was clear, and many distinct pores existed even in the grain boundary sintered at 1100 °C (see figure (c)). The loose structure and high porosity were due to the phase stability of KNN ceramics, which is limited to 1140 °C [Citation19]. Therefore, the high sintering temperature was not suitable and the grains did not grow sufficiently to pure KNN. According to Powell’s suggestion that the liquid phase might be caused by impurities in the bodies, the adding of BF might induce additional liquid-phase sintering. The liquid phase was inferred to be formed in the specimens (see figure (d)) and to have assisted the densification of the ceramics during the sintering with the doping of BF.
Figure (a) shows d33 of KNN-BF ceramics as a function of the content of BF, with the highest d33 of about 145 pC/N occurring at xBF=0.01. When xBF>0.01, d33 rapidly decreased with increasing xBF. This phenomenon was ascribed to the ferroelectric nature. Figure (b) shows the P-E hysteresis loop of KNN-BF ceramics at room temperature. As could be seen, the remanent polarization Pr and the coercive field Ec of KNN-BF depended on the amount of BiFeO3. For xBF=0.01, the KNN-BF possessed higher Pr and Ec than those of pure KNN. For xBF>0.01, Pr of KNN-BF was lower than that of pure KNN and Ec was similar to the Ec of pure KNN. Piezoelectric ceramics with higher remanent polarization Pr exhibits higher piezoelectric properties. Higher remanent polarization indicates a higher degree of orientation of the ferroelectric domain near the MPB composition. This is the reason why d33 of KNN-BF at xBF=0.01 is the highest. The kp, εr, tan δ and Qm of KNN-BF at xBF=0.01 were 0.31, 265, 0.046 and 80, respectively.
Conclusion
The effects of BiFeO3 dopant on the ferroelectric properties and microstructure were investigated in the KNN-BF system. BiFeO3 (xBF=0.01) could suppress the grain growth, which not only benefits the sintering of ceramics but also enhances the piezoelectric and ferroelectric properties. The optimum piezoelectric and ferroelectric properties are d33=145 pC/N, kp=0.31, Qm=80, Pr=11.3 μC cm−2 and Ec=16.5 kV cm−1.
Acknowledgments
This work was financially supported by the National Natural Science Foundation of China (No 20571009, 20731001, 50725415), and Funds of the Ministry of Education of China for PCSIRT.
References
- NagataHYoshidaMMakiuchiYTakenakaT 2003 Japan. J. Appl. Phys. 42 7401 http://dx.doi.org/10.1143/JJAP.42.7401
- SuzukiMNagataHOharaJFunakuboHTakenakaT 2003 Japan. J. Appl. Phys. 42 6090 http://dx.doi.org/10.1143/JJAP.42.6090
- RherigP WParkS EMcKinstryS TMessingG LJonesBShroutT M 1999 J. Appl. Phys. 86 1657 http://dx.doi.org/10.1063/1.370943
- YuZAngCGuoR YBhallaA S 2002 J. Appl. Phys. 92 1489 http://dx.doi.org/10.1063/1.1487435
- GuoYKakimotoKOhsatoH 2004 Solid State Commun. 129 279 http://dx.doi.org/10.1016/j.ssc.2003.10.026
- MatsubaraMYamaguchiTSakamotoWKikutaKYogoTHiranoS 2005 J. Am. Ceram. Soc. 88 1190 http://dx.doi.org/10.1111/j.1551-2916.2005.00229.x
- ZhenY HLiJ F 2006 J. Am. Ceram. Soc. 89 3669 http://dx.doi.org/10.1111/j.1551-2916.2006.01313.x
- SunCXingX RChenJDengJ XLiLYuR BQiaoL JLiuG R 2007 Eur. J. Inorg. Chem. 1884 http://dx.doi.org/10.1002/ejic.200601131
- JaegerR EEgertonL 1962 J. Am. Ceram. Soc. 45 208 http://dx.doi.org/10.1111/j.1151-2916.1962.tb11127.x
- ZhangB PLiJ FWangKZhangH L 2006 J. Am. Ceram. Soc. 89 1605 http://dx.doi.org/10.1111/j.1551-2916.2006.00960.x
- SaitoYTakaoHTaniTNonoyamaTTakatoriKHommaTNagayaTNakamuraM 2004 Nature 432 84 http://dx.doi.org/10.1038/nature03028
- GuoYKakimotoK IOhsatoH 2004 Appl. Phys. Lett. 85 4121 http://dx.doi.org/10.1063/1.1813636
- DuH LTangF SLuoF AZhouW CQuS BPeiZ B 2007 Mater. Sci. Eng. B 137 165 http://dx.doi.org/10.1016/j.mseb.2006.09.031
- GuoYKakimotoK IOhsatoH 2005 Mater. Lett. 59 241 http://dx.doi.org/10.1016/j.matlet.2004.07.057
- YangZ PChangYLiuBWeiL L 2006 Mater. Sci. Eng. A 432 292 http://dx.doi.org/10.1016/j.msea.2006.06.034
- ZhangSXiaR UShroutT RZangGWangJ 2007 Solid State Commun. 141 675 http://dx.doi.org/10.1016/j.ssc.2007.01.007
- LeeH JRyuHBaeM SChoY KNahmS 2006 J. Am. Ceram. Soc. 89 3529 http://dx.doi.org/10.1111/j.1551-2916.2006.01197.x
- KanekoSDongDMurakamiK 1998 J. Am. Ceram. Soc. 81 1013
- JaffeBCookW RJaffeH 1971 Piezoelectric Ceramics London Academic