Abstract
The conventional method used for glass melting is air-fuel firing, which is inefficient, energy-intensive and time-consuming. In this study, an innovative in-flight melting technology was developed and applied to glass production for the purposes of energy conservation and environmental protection. Three types of heating sources, radio-frequency (RF) plasma, a 12-phase alternating current (ac) arc and an oxygen burner, were used to investigate the in-flight melting behavior of granulated powders. Results show that the melted particles are spherical with a smooth surface and compact structure. The diameter of the melted particles is about 50% of that of the original powders. The decomposition and vitrification degrees of the prepared powders decrease in the order of powders prepared by RF plasma, the 12-phase ac arc and the oxygen burner. The largest heat transfer is from RF plasma to particles, which results in the highest particle temperature (1810 °C) and the greatest vitrification degree of the raw material. The high decomposition and vitrification degrees, which are achieved in milliseconds, shorten the melting and fining times of the glass considerably. Our results indicate that the proposed in-flight melting technology is a promising method for use in the glass industry.
Introduction
Glass products, such as sheet glass, container glass, fiberglass and optical glass, have become a part of people's daily life. Most glass is produced by the typical Siemens-type melter fired in air with heavy oil or natural gas as the fuel. This type of melter has been used for more than 140 years because of its good large-scale performance and continuous melting system [Citation1]. The model of the conventional fuel-fired melter is shown in figure (a). The crushed raw material is added to the melter on a large scale and is heated by a burner torch located above with a thermal efficiency of 50%. The heat transfer from the burner flame to the raw material and the flame temperature are low, and it usually takes several days to obtain homogeneous glass. A long time is required for the dissolution of SiO2 in the melting process and the escape of bubbles in the glass melt in the fining process. According to the US Department of Energy, 70% of the energy consumed in US flat-glass production is in the melting and fining stages. Because fossil fuels are used, greenhouse gases such as CO2 and NOx are emitted, which have a negative environmental impact. Many improvements have been made in increasing energy efficiency and extending the furnace life, such as by using more efficient burners and more insulation materials, improving the furnace design as well as by using oxygen instead of air [Citation2–5]. However, these improvements have not changed the fundamental technology, thus their effects on energy conservation and the reduction of emissions have been limited.
Figure 1 Models of conventional fuel-fired melter (a) and new in-flight melter (b) (capacity 800 ton day- 1).
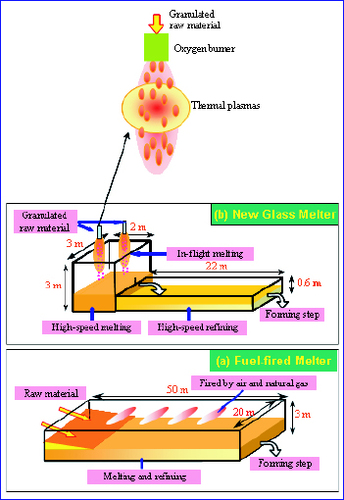
With the rapid increase in the demand for glass and the crises of energy and global warming, increasing the productivity while minimizing the energy usage and the effect on the environment is a crucial issue. To reduce the energy consumed in glass production, the key is to decrease the melting and fining times. Heating sources with a high temperature and high energy efficiency are necessary to reduce the vitrification time. Thermal plasmas have received considerable attention due to their unique advantages such as high enthalpy, high chemical reactivity, alterable oxidation or reduction atmosphere in accordance with required chemical reaction, easy and rapid generation of high temperatures, long residence time as well as rapid quenching rate [Citation6]. Thermal plasmas, therefore, have been widely applied for material processing, such as the synthesis of nanoparticles, chemical vapor deposition (CVD) and plasma spraying [Citation7–9]. High temperatures of thermal plasmas make it easy to melt raw glass powders quickly. Reducing the formation of bubbles in molten glass is an effective method of shortening the fining time. This can be achieved by releasing the decomposed gases from the raw material during powder injection. The resulting improvement of melting efficiency and the reduced use of fossil fuel can decrease the emissions of greenhouse gases.
Under the support of a New Energy and Industrial Technology Development Organization (NEDO) project, an innovative in-flight glass melting technology was developed, as shown in figure (b). Granulated raw material with a small diameter is dispersed in the melter, where the particles are in full contact with the plasma or burner flame. The high heat transfer and the high temperature of hybrid plasmas melt the raw material rapidly. In addition, the decomposed gases of carbonates and sulfate are removed while the particles are still in-flight to reduce the fining time considerably. In contrast with the conventional technology, the total vitrification time is evaluated to be only 2–3 h for the same rate of productivity as that obtained using the fuel-fired melter.
In the present work, the granulated raw materials of two types of glass were heated by RF plasma, a 12-phase ac arc and an oxygen burner to investigate the feasibility of in-flight melting technology for glass production. The vitrification degree, decomposition degree, morphology, average diameter and the composition of powders were characterized by various techniques. Also, the in-flight melting behavior of particles was studied and the results for different heating sources were compared to provide guidelines for the glass industry.
Experimental
Two typical raw materials were used in the experiments: those for soda-lime glass and alkali-free glass. To improve the fluidity of powders for feeding and melting efficiency, the raw material was granulated into spherical powders by the spray-drying method. A mixture of SiO2, Na2CO3 and CaCO3 was used to prepare the soda-lime glass with a target composition of 16Na2O–10CaO–74SiO2 in mass%. SiO2, H3 BO3, Al2O3, BaCO3 and Sb2O3 were introduced to prepare the alkali-free glass with a target composition of 49SiO2–15B2O3–10Al2O3–25BaO–1Sb2O3 in mass%. The average diameters of the raw materials of soda-lime glass and alkali-free glass were 51 and 80 μm, respectively.
Three types of heating sources, RF plasma, a 12-phase ac arc and an oxygen burner, were used to melt the glass raw materials. Figure shows a schematic of the RF plasma apparatus. It mainly consists of a power supply, a plasma torch, a powder feeder and a reaction chamber. The typical operating conditions were as follows: torch power: 10 kW; work frequency: 4 MHz; total pressure: 101.3 kPa; plasma gas: 2.0 litres min-1 (Ar); sheath gas: 22 litres min- 1 (Ar) + 2 litres min- 1 (O2); carrier gas: 20 litres min- 1 (Ar); feed rate: 30 g min- 1. The powders were quenched after melting and collected on a water-cooled substrate 340 mm below the nozzle.
The schematic of the combination of the 12-phase ac arc and oxygen burner is shown in figure . The 12-phase ac arc consists of an ac power supply, 12 electrodes, a reaction chamber and a powder feeder. A detailed electrical circuit diagram of the transformers used for converting from 3-phase ac to 12-phase ac is given in Matsuura et al [Citation10]. The 12 electrodes are divided into two layers: 6 lower electrodes and 6 upper electrodes. The configuration of the 12 electrodes is symmetrically arranged with an angle of 30° to the horizontal. The total power of the 12-phase arc is 36 kW with 87% efficiency for an input voltage of 190 V and an input current of 220 A. The discharging voltage and current of each electrode are 25–45 V and 80–100 A, respectively. The granulated powders of the raw materials were injected into the chamber at a feed rate of 30 g min- 1 with a flow rate of the carrier gas of 20 litres min- 1 (air). Argon as the sheath gas was introduced at a flow rate of 36 litres min- 1 to prevent the electrodes from oxidation. The prepared powders were quenched on a stainless-steel pan at a distance of 920 mm below the nozzle.
The oxygen burner, which consisted of a nozzle with cooling water, an ignition torch and the fuel and oxygen feeding system, is installed above the furnace chamber. Propane (C3 H8) was used as the fuel. The combustion power of the burner was 38 kW, and the flow rates of C3 H8 gas, the primary oxygen and the secondary oxygen were 25, 12 and 105 litres min- 1, respectively. The feed rate and flow rate of the carrier gas were the same as the 12-phase arc. Figure shows the plasmas and flame of the different heating sources without powder loading.
Figure 4 Plasmas and flame of different heating sources: (a) RF plasma; (b) 12-phase arc plasma; and (c) oxygen burner flame.
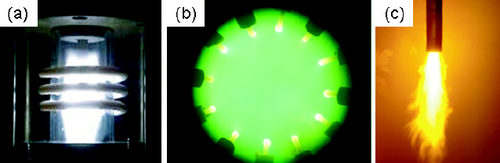
The morphology of the particles was observed by scanning electron microscopy (SEM) using a JSM5310 instrument (Jeol, Japan), and the average diameter was evaluated by analyzing the SEM images. The structures of the powders were determined by x-ray diffractometry (XRD), which was carried out using a Miniflex instrument (Rigaku, Japan) with CuKα radiation at 30 kV and 15 mA. The data were collected in the 2θ range of 3–90° with a step size of 0.02° min and a scan speed of 4° min- 1. TG8120 thermogravimetric apparatus (Rigaku, Japan) was used to perform the thermogravimetric (TG) analysis. The range of measured temperatures was 20–1200 °C with a rate of increase of 10 °C min- 1. The contents of Na2 O, B2 O3 and Fe ions in the prepared powders were analyzed by inductively coupled plasma (ICP) spectroscopy using a Prodigy spectrometer (Leeman, USA). The content of Fe3 + in the glass powders was measured by electron spin resonance (ESR) using an ESP300E spectrometer (Bruker, Germany). The modulation frequency is 50 kHz and the microwave frequency is 9.68 GHz with a power of 50 mW.
Results and discussion
SEM photographs of the raw materials and prepared powders heated by RF plasma, the 12-phase ac arc and the oxygen burner are shown in figure . The granulated particles of the raw materials have a rough surface and porous structure, as observed from figures (a) and (e). The melted particles in the prepared samples are spherical shape with a smooth surface and compact structure. Some partly melted particles, however, still retained a similar morphology to the original after heat treatment. Moreover, their surface contains some small pores, which were formed by the release of the decomposed gas from inside the particle. The average diameter of the prepared powders is less than 50% of the original diameter. The proportion of the incompletely melted particles is least in the samples prepared by the RF plasma and largest in the samples treated by the oxygen burner. The heat transfer from the heating source to the particles mainly depends on the Reynolds number and the temperature difference between the heating medium and the particle surface. The Reynolds number, which is a function of relative velocity, has little variation among the three types of heating sources, but the heating temperature varies considerably. Hence, the heating temperature has a very strong effect on the heat transfer to the particles. The lowest temperature, achieved by the burner flame (about 2500 °C), results in the least heat transfer to the particles, which is responsible for the incompletely melted particles. Compared with the soda-lime glass powders, the alkali-free glass powders are more difficult to melt under the same operating conditions.
Figure 5 SEM images of soda-lime glass powders: (a) raw material; (b) heated by RF plasma; (c) heated by 12-phase ac arc; (d) heated by oxygen burner, and alkali-free glass powders; (e) raw material; (f) heated by RF plasma; (g) heated by 12-phase ac arc; and (h) heated by oxygen burner.
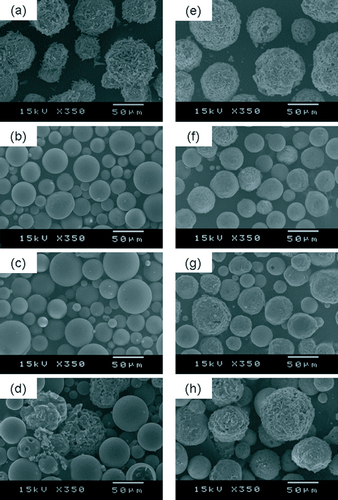
XRD analysis was performed to determine the structures of powders before and after melting. As seen from figure (a), the diffraction peaks of SiO2, Na2 CO3 and CaCO3 are clearly represented in the XRD pattern of the raw material before being heated. Only SiO2 peaks appear in the patterns of samples treated by RF plasma and the 12-phase ac arc, indicating that the carbonates are almost fully decomposed during in-flight melting. However, the sample prepared by the oxygen burner still contains a few diffraction peaks of carbonates. The alkali-free glass samples treated by the 12-phase ac arc and oxygen burner still contain some peaks of BaCO3; however, the sample prepared by RF plasma does not exhibit these peaks, as shown in figure (b). This is attributed to the greater energy transfer to the particles from RF plasma, which leads to the greater decomposition of the compounds. For both treated samples, the intensity of the SiO2 (101) main peak increases in the order of RF plasma, the 12-phase ac arc and the oxygen burner. The increase in the amount of crystal SiO2 in samples treated by the burner indicates that the reactions among compounds are less vigorous and the amorphous structure with glass characteristics is less prevalent in these samples.
Figure 6 XRD patterns of raw material and prepared powders: (a) soda-lime glass powders; and (b) alkali-free glass powders.
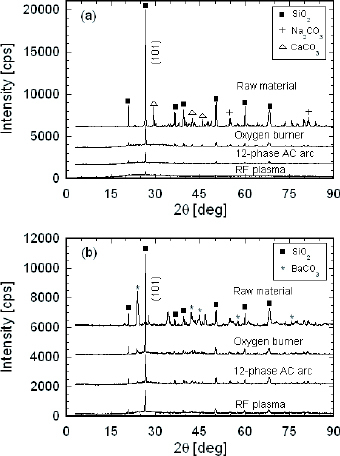
The vitrification reaction is the process of converting materials into a glassy amorphous solid that is free of any crystalline structure. It is difficult to characterize this complicated process because of its many physical and chemical reactions. In this paper, the vitrification degree is simply defined as the ratio of reacted SiO2 in the treated powders to the total crystal SiO2 in the raw material. The internal standard method of XRD was used to measure the vitrification degree with ZnO as the standard material [Citation11]. The vitrification degree of the samples treated by different heating sources is presented in figure . The vitrification degree of powders treated by RF plasma is highest, which is consistent with the above diffraction peak analysis. According to the numerical analysis of Hossain et al [Citation12], the temperature and velocity of RF plasma are more than 4000 K and 45 m s-1 at the torch exit under a carrier gas flow rate of 9 litres min- 1, respectively. The in-flight time of powders from the nozzle exit to the substrate is less than 8 ms at the centerline. The high temperature and velocity of RF plasma ensure that the melting reaction finishes within milliseconds, which decreases the melting time markedly. In addition, the vitrification degree of alkali-free glass powders is lower than that of soda-lime glass powders, which is in agreement with the SEM images.
The fining of glass is an important and indispensable process in the glass industry. Its purpose is to remove the large number of bubbles formed by the decomposed and dissolved gas in molten glass. If the decomposed gas can be released from the raw material while it is still in-flight, it will reduce the formation of bubbles and thus decrease the fining time. The TG curves of the raw material and the prepared powders synthesized by the different heating sources are shown in figure . The TG curves of both soda-lime and alkali-free glass raw materials exhibit two main stages with total mass losses of 20.5 and 10.1%, respectively. For the soda-lime glass raw material, the first mass loss is ascribed to the release of physically adsorbed H2O and CO2 from the compound at the temperature of 50–100 °C. The second large mass loss between 300 and 700 °C is due to the decomposition of carbonates (Na2CO3 and CaCO3). For the alkali-free glass raw material, the removal of physically adsorbed H2O and the decomposition of H3 BO3 occur at 97 and 140 °C, respectively, in the first stage. The second mass loss is due to the decomposition of BaCO3 between 500 and 800 °C. The TG curves of the powders treated by RF plasma show no obvious mass loss during heat treatment, indicating that the raw materials almost completely decomposed during in-flight melting. The mass loss in the curves of samples prepared by the oxygen burner is the least one.
Figure 8 TG curves of raw material and prepared powders: (a) soda-lime glass powders; and (b) alkali-free glass powders.
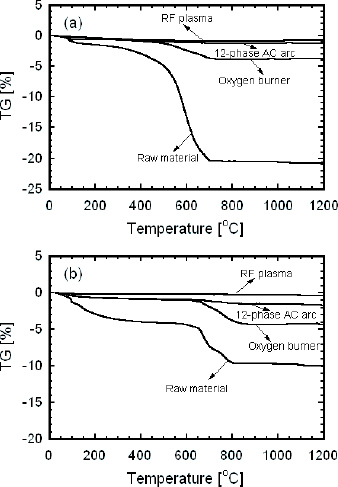
The decomposition degree, defined as the ratio of the mass loss of the prepared powders to the mass loss of the raw material during heat treatment, was analyzed quantitatively. The decomposition degree of the powders prepared by RF plasma is highest, as shown in figure . The decomposition degrees of alkali-free glass powders are lower than those of soda-lime glass powders. This result is similar to the variation of vitrification degree, as mentioned above. There are two main factors that affect the melting behavior. The viscosity of alkali-free glass is so high that the vitrification reaction is slower than that of soda-lime glass at the same temperature [Citation13]. Since the reaction and melting first occur on the surface of the particles, then propagate inward inside, the higher viscosity of molten glass on the surface will delay the melting reaction and the removal of the decomposed gases inside the particles. Furthermore, the larger average diameter of the alkali-free glass raw material particles reduces the rate of heat transfer due to the greater heat conduction inside each particle. According to our previous experiments [Citation14], the viscosity of glass has a greater effect on the vitrification. The clear and transparent glass sample with few bubbles reported by Yao et al [Citation15] demonstrates that in-flight glass melting technology can reduce the burden of the subsequent fining process by removing the decomposed gases while the powders are in-flight.
The main function of Na2 O in soda-lime glass and B2O3 in alkali-free glass is to reduce the viscosity and softening point of each glass. The volatilization of these volatile materials occurs when they are exposed to a high temperature. Their content has a direct effect on the properties of respective glasses. Hence, it is important to measure their change in content after heat treatment. The content of Na2O and B2O3 in samples treated by the different heating sources was analyzed by ICP spectroscopy, and then the volatilization degree was calculated, the results of which are shown in figure . The highest volatilization degree of Na2O and B2O3 for the powders can be attributed to the largest energy transfer to the particles due to the high plasma temperature (about 10 000 °C). For practical glass production, the high volatilization of materials increases the cost of production and damages the furnace crown. Therefore, methods of improving the melting efficiency and reducing the volatilization rate should be considered.
To investigate the melting temperature of particles during in-flight melting, 0.05 mass% Fe2O3 was initially added into the soda-lime glass raw material. The redox equilibrium of iron in silicate glass melts is commonly expressed by the reaction (1) [Citation16]:
(1)
Johnston [Citation17] and Paul [Citation18] reported that log(FeO/Fe2O3), which depends on the melting temperature (T) of glass, has a linear relationship with 1/T. The melting temperature of the particles can be calculated from this linear function by measuring the total amounts of Fe ions and Fe3+ ion. The detailed measurement of the particle temperature using the redox method will be discussed in a forthcoming paper by Funabiki et al. The measured temperatures of particles obtained during heat treatment are shown in figure . The results show that the temperatures of particles heated by the different heating sources decreases in the order of RF plasma, the 12-phase ac arc and the oxygen burner. The difference in particle temperature achieved by the RF plasma and the oxygen burner is 160 °C, which means that the heat transfer from the flame of the burner to the particles is smaller. This convincingly explains the lowest vitrification, decomposition and volatilization degrees of powders heated by the oxygen burner.
During heat treatment, because of energy losses in the coupling RF and the transmission line, and radiation and convection losses, only part of the energy can be transferred to the particles. The thermal efficiencies of the three types of heating sources were compared to provide valuable guidelines for the effective utilization of energy. Here, the thermal efficiency is defined as the ratio of the energy transfer to particles to the energy input into the apparatus. On the basis of [Citation19–26], the thermal efficiencies of RF plasma, the 12-phase ac arc and the oxygen burner were estimated to be about 2, 28 and 40%, respectively. Although the high thermal efficiency of the oxygen burner can improve the energy utilization rate, the low heating temperature of the burner flame leads to a long vitrification time and high energy consumption. Combining the advantages of the high temperature of plasma and the high thermal efficiency of the oxygen burner, a hybrid apparatus using RF plasma or a 12-phase arc with an oxygen burner has been developed to improve glass quality and increase productivity with minimum energy consumption.
Conclusion
Innovative in-flight melting technology was successfully developed to melt granulated glass raw materials, and the effects of different heating sources on the melting behavior of particles were investigated. Results show that the decomposition, vitrification and volatilization degrees of samples treated by RF plasma are the highest. The viscosity of glass has a strong effect on the vitrification reaction. Different particle temperatures lead to various vitrification degrees of the raw materials because of the amount of heat transferred. The high vitrification degree achieved within milliseconds reveals that the new in-flight melting technology can reduce energy consumption and shorten the production cycle.
Acknowledgment
The financial support provided by the Strategic Development of Energy Conservation Technology Project of NEDO (New Energy and Industry Technology Development Organization, Japan) is gratefully acknowledged.
References
- RossC P 2004 Am. Ceram. Soc. Bull. 83 18
- DantsisT YZeibotsA ABisnietseL AMarenaM VGushchinS NKutinV B 1980 Glass Ceram. 37 362 http://dx.doi.org/10.1007/BF01141897
- BondarevK TPopovO NInshiiV ABokovaA S 1977 Glass Ceram. 34 700 http://dx.doi.org/10.1007/BF00695454
- DzyuzeV Y 2004 Glass Ceram. 61 101 http://dx.doi.org/10.1023/B:GLAC.0000034058.85671.ba
- ShampD EStarkT FElliottJ RHowardL E 1995 US Patent No. 5417732, 23 May
- WatanabeTShigetaMAtsuchiN 2006 Int. J. Heat Mass Transfer 49 4867 http://dx.doi.org/10.1016/j.ijheatmasstransfer.2006.05.039
- HeberleinJ 2002 Pure Appl. Chem. 74 327 http://dx.doi.org/10.1351/pac200274030327
- ShigetaMWatanabeT 2007 J. Phys. D: Appl. Phys. 40 2407 http://dx.doi.org/10.1088/0022-3727/40/8/S20
- KawajiriKNishiyamaH 2006 Thin Solid Films 506–507 660 http://dx.doi.org/10.1016/j.tsf.2005.08.360
- MatsuuraTTaniguchiKWatanabeT 2006 Thin Solid Films 515 4240 http://dx.doi.org/10.1016/j.tsf.2006.02.086
- WillisD E 1972 Chromatographia 5 42 http://dx.doi.org/10.1007/BF02270655
- HossainM MYaoYOyamatsuYWatanabeTFunabikiFYanoT 2006 WSEAS Trans. Heat Mass Transfer 1 625
- BansalN PDoremusR H 1986 Handbook of Glass Properties London Academic
- YaoYHossainM MWatanabeTFunabikiFYanoT 2008 Thin Solid Films at press
- YaoYHossainM MOyamatsuYWatanabeTFunabikiFYanoT 2007 Trans. Mater. Res. Soc. Japan 32 509
- KressV CCarmichaelI S E 1988 Am. Mineral. 73 1267
- JohnstonW D 1964 J. Am. Ceram. Soc. 47 198 http://dx.doi.org/10.1111/j.1151-2916.1964.tb14392.x
- PaulA 1985 J. Non-Cryst. Solids 71 269 http://dx.doi.org/10.1016/0022-3093(85)90296-0
- HossainM MYaoYWatanabeT 2008 Thin Solid Films at press
- FauchaisPVardelleA 1997 IEEE Trans. Plasma Sci. 25 1258 http://dx.doi.org/10.1109/27.650901
- GutsolAChirokovAFridmanAWorekW 2001 Proc. 2nd Int. Conf. on Computational Heat and Mass Transfer, Brazil
- CogdellR J 1990 Foundations of Electrical Engineering Englewood Cliffs, NJ Prentice-Hall
- MatsumotoK 1996 Plasma Sources Sci. Technol. 5 245 http://dx.doi.org/10.1088/0963-0252/5/2/018
- BeerkensR G CVanlimptH A CJacobsG 2004 Glass Sci. Technol. 77 47
- SchmittPSchuermansBGeigleK PPoinsotT 2005 Proc. ECCOMAS Thematic Conf. on Computational Combustion, Lisbon, Portugal
- SchmittPPoinsotTSchuermansBGeigleK 2007 J. fluid Mech. 570 17 http://dx.doi.org/10.1017/S0022112006003156