Abstract
Dynamically vulcanized EPDM/PP (ethylene-propylene-diene/polypropylene) elastomers reinforced with various amounts of organoclay were prepared using octylphenol-formaldehyde resin and stannous chloride dehydrate as vulcanizing agents. The effects of organoclay on vulcanization characteristics, rheological behavior, morphology, thermal stability and thermomechanical properties were studied. Experimental results showed that organoclay affected neither the vulcanization process nor the degree of vulcanization chemically. X-ray analysis revealed that these organoclay-filled thermoplastic vulcanizates (TPVs) were intercalated. With respect to the mechanical properties, organoclay increased both the strength and degree of elongation of TPVs. The morphological observation of fractured surfaces suggested that organoclay acted as a nucleating agent in TPVs, improving their mechanical properties. However, adding organoclay reduced the thermal stability of TPVs by decomposing the swelling agents in the organoclay.
Introduction
Thermoplastic vulcanizates (TPVs) based on EPDM/PP blends are a unique class of thermoplastic elastomers that can be processed at elevated temperatures, in molten state. During the processing, the rubber phase is vulcanized using appropriate curatives upon mixing with a thermoplastic polymer. These materials have the performance of conventional vulcanized rubber. Morphologically, TPVs are characterized by the presence of finely dispersed, micron-scale and cross-linked rubber particles distributed in a continuous thermoplastic matrix [Citation1–7]. Many commercial TPVs, owing to their excellent wear ability, low density and relatively low cost, have been developed for various applications, such as automotive parts, cable insulation, footwear, packaging and medical devices [Citation8–10].
Montmorillonite, an inorganic substance, contains layered silicates of dimensions 100×100×1 nm [Citation3, Citation11]. Isomorphic substitution in the layers generates negative charges that are typically counterbalanced by cations that are present in the interlayer galleries [Citation12, Citation13]. The nanocomposite structure depends on the structure of the dispersed clay particles in a polymer matrix, which is generally classified as either intercalated or exfoliated. In the intercalated state, the clay is dispersed as a lamellar structure, and polymer chains penetrate between the silicate layers of the clay. The exfoliated structure is characterized by the complete delamination of clay particles, and individual silicate layers are dispersed throughout the polymer matrix. The dispersion of such layers substantially enhances mechanical and thermal properties, water absorption, flame retardancy and gas barrier properties beyond those of neat polymer matrix [Citation14–33].
Thakkar and Goettler reported that clay fillers used in TPV elastomer reduce the size of the dispersed elastomer phase [Citation26]. Mishra et al described the use of maleic anhydride-functionalized polypropylene as a compatibilizer and found that the resulting nanocomposite is intercalated [Citation34]. Lee and Goettler studied the structure-property relationships of TPVs/clay nanocomposite, which indicate that the dispersion of the clay filler affects the mechanical properties of the nanocomposite [Citation35]. Naderi et al investigated the effect of the clay concentration of a PP/EPDM/compatibilizer/clay system on the microstructure and mechanical properties [Citation36].
In our earlier work, the vulcanizing characteristics, mechanical properties, morphologies, intermolecular interactions and thermal properties of EPDM/PP blends were associated with the type of curatives added (peroxides, phenolic resins, and hydrosilylation) [Citation37]. Experimental results showed that EPDM/PP blends could be improved using complex curatives. The main goal of this study is to evaluate the effect of organoclay on the vulcanization characteristics, rheological behavior, morphology, thermal stability and thermomechanical properties of EPDM/PP TPVs, in which octylphenol-formaldehyde resin and stannous chloride dehydrate were used as vulcanizing agents.
Experimental details
Materials
The polymers used were ethylene-propylene-diene rubber (Vistalon 7001, ethylene content 73 wt.%, ENB content 5 wt.%) manufactured by ExxonMobil Chemical (USA) and homopolymer polypropylene (PT101N grades, MFI 1.6 g/10 min, density 0.905 g cm-3) manufactured by Taiwan Polypropylene. Octylphenol-formaldehyde resin (SP-1045) was produced by Schenectady International Inc. Organoclay (model No.: PK8320), an alkyl ammonium-modified montmorillonite with a cation-exchange capacity of 106 meq/100 g ±10%, were generously supplied by Pal Kong Inc. (Taiwan). Phenol-type antioxidant (RICHNOX 1010) was purchased from RICH Chemical Inc. (Taiwan). Stannous chloride dehydrate (SnCl2) was produced by ACROS (USA). Zinc oxide (ZnO) was purchased from Yung Chyang Chemical Industries (Taiwan). Homopolymer polyethylene wax (A-C® 6 grade) was produced by Honeywell Inc. (USA). Paraffinic process oil (SUNPAR® 2280 grade) was produced by Vulchem Inc. (Taiwan).
Sample preparation
The TPVs used in this study consisted of EPDM, PP, process oil, clay, curatives and other additives, as shown in table 1. They were prepared by dynamic vulcanization using an intermeshing twin-screw extruder (Werner and Pflederer, Model-ZSK 26 MEGA compounder) with a rotor speed of 800 rpm. During this process, the EPDM elastomer was vulcanized in situ into rubber during melt mixing with the thermoplastic at 170–190 °C.
Recipes for the preparation of organoclay-filled EPDM/PP TPVs.
Vulcanization characteristics
The vulcanization characteristics of organoclay-filled EPDM/PP elastomers were determined using a Brabender Plasticorder (PLASTOGRAPH®) with a cam-type mixed head (N50H) at 190 °C and a rotor speed of 40 rev min−1. The changes in torque with time were recorded.
X-ray measurement
X-ray diffraction experiments were conducted on a Rigaku D/Max RC x-ray diffractometer using CuKα radiation (λ=0.15418 nm) at 40 kV and 100 mA at a scanning rate of 2° min−1.
Rheological studies
Rheological studies were conducted using a capillary rheometer (Dynisco LCR7000) at 190 °C at shear rates of 3250–5000 s−1. The capillary length-to-diameter ratio was 20 mm/1 mm with a compound entrance angle of 120°. The preheating time for each sample was 5 min.
Thermogravimetric analysis
Thermogravimetric analysis (TGA) was carried out using a thermogravimetric analyzer (TA instrument) in a nitrogen atmosphere from 30 to 600°C at a heating rate of 20 °C min−1.
Analysis of dynamic mechanical properties
Dynamic mechanical data were obtained using a dynamic mechanical analysis (DMA) instrument (TA Q800) using the following parameters: frequency 1 Hz, scan rate 5 °C min−1, temperature range −80 to - 40 °C.
Measurement of mechanical properties
Tensile strength and the degree of elongation at break were measured with a Universal Tensile Tester with a tension velocity of 500 mm min−1 in compliance with ASTM D412C specifications. Thermal aging test was performed in an oven at 135 °C for 168 h.
Morphological analysis
The morphology was measured using a JEOL JSM6360 scanning electron microscope (SEM). Gold was sputtered onto the fractured surface of the samples before the analysis.
Results and discussion
Vulcanization characteristics
Figure presents the vulcanization behavior of EPDM/PP TPV and organoclay-filled EPDM/PP TPV (TPV12). It is divided into three parts. The first part (before 6 min) represents the melting of the blend; the second part around 6–7 min represents vulcanization. As soon as the vulcanizing agents (octylphenol-formaldehyde resin and stannous chloride dehydrate) are added in this stage, torque increases sharply, indicating that the rubber phase begins to respond to the vulcanization. Finally, a steady torque, which is related to the degree of vulcanization, is reached in the third part (vulcanization equilibrium). Regarding the effect of adding organoclay on the vulcanization degree of the EPDM/PP elastomer (TPV12), a comparison of the melting region with the vulcanization region revealed the same increase in torque (approximately 2 Nm) within the same time period (at about 7 min). Because the equilibrium torque depends on the degree of vulcanization, a similar increase in the torques of these TPVs is reached within a similar reaction time, demonstrating that organoclay chemically affects neither the vulcanization process nor the degree of vulcanization.
However, organoclay content affected the equilibrium torque values of organoclay-filled EPDM/PP TPVs. Figure shows plots of the equilibrium torque values of EPDM/PP TPVs with various organoclay contents. Generally, adding inorganic additives to a polymer matrix enhances mechanical properties (e.g. stress, hardness, torque value and viscosity) [Citation38]. Conversely, adding low-molecular-weight organic compounds as a plasticizer lowers torque value and viscosity properties [Citation26]. Since the organoclay was composed of both low-molecular-weight alkyl ammonium, which was used as a swelling agent, and inorganic silicate, the final properties of the nanocomposite result from the combination of two opposite effects. The experimental results revealed the effect of low-molecular-weight alkyl ammonium on TPV3, which has a lower equilibrium torque value than the neat TPV. Furthermore, when the organoclay content exceeded 3 phr, the effect of the inorganic silicate was enhanced, thereby increasing organoclay content. Therefore, the equilibrium torque values of these TPVs were higher than those of the neat TPV and increased with organoclay content, as shown in figure .
X-ray diffraction analysis
All the structures of the organoclay-filled EPDM/PP TPVs were characterized by x-ray diffraction. Figure shows a spectral comparison of the x-rays scattered from the organoclay in the reflection mode with organoclay-filled EPDM/PP TPVs. The basal spacing d001=1.26 nm of the organoclay was calculated using the Bragg formula λ = 2d sin θ. The position of the diffraction peak shifted from 6.3° to 7.0° in organoclay-filled EPDM/PP TPVs compared to the original organoclay. This shift corresponds to an increase in the basal spacing to about 1.40 nm due incorporation of polymer chains between organoclay silicates [Citation39].
Rheological studies
The flow behavior of polymer melts formed by different processes is a key to the manufacture of articles with good finish and dimensional tolerance. Therefore, the rheological behavior of a melt is very important in determining overall processability. Figure plots the apparent shear viscosity of EPDM/PP TPVs versus apparent shear rate, indicating that shear viscosity decreases as shear rate increases. Figure shows the shear viscosities of various TPVs at 190 °C and a shear rate of 5000 s−1. The shear viscosities initially decrease (TPV3) and then increase (TPV6, TPV9 and TPV12). These results were similar to those of the equilibrium torque values, which were affected by the combined effects of low-molecular-weight alkyl amine and inorganic silicate.
Thermogravimetric analysis
The temperature at which a polymer loses 5% of its weight when using TGA has been found effective for evaluating the thermal stability of a polymer [Citation40, Citation41]. The variations in the initial decomposition temperatures (5% weight loss) of organoclay, neat TPV and organoclay-filled TPV (TPV12) were obtained from the TGA test, as shown in figure . Organoclay exhibits two weight loss temperatures, 100 and 250 °C, which correspond, respectively, to the evaporation of moisture and the decomposition of the swelling agent, alkyl ammonium, used to produce organoclay [Citation42, Citation43]. The neat EPDM/PP TPV decomposes at 380 °C. Because the nanocomposites contain organoclay, they are less thermally stable than the neat TPV. Figure shows the 5% weight loss temperature of EPDM/PP TPV with various organoclay contents.
Figure 7 Thermal degradation temperatures (5% weight loss) of organoclay-filled EPDM/PP TPVs. The dotted line indicates the linear regression of the 5% weight loss temperature of all the samples.
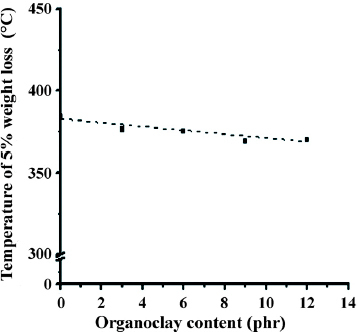
Further rheological studies are conducted to elucidate the thermal stability of organoclay-filled EPDM/PP TPVs. As shown in figure , the decrease in shearing viscosity at 350 °C increases with both the organoclay content of EPDM/PP TPVs and the resident time in the capillary rheometer. These results are consistent with the TGA results.
Analysis of dynamic mechanical properties
Figure shows the DMA diagrams of all TPV samples at a frequency of 1 Hz. Phase separation causes EPDM/PP TPVs to have two characteristic peaks—at the glass transition temperature (Tgα) of EPDM of around - 20 °C, and the glass transition temperature (Tgβ) of PP of around 20 °C. When EPDM/PP was filled with organoclay, the organoclay did not affect the characteristic peak of EPDM in DMA (figure ). However, at the characteristic peak of PP, Tgβ temperature increased to about 3–7 °C because of the interaction between the organoclay and the PP polymer chain. Additionally, the storage modulus of these TPVs at 25 °C increased with organoclay content, as shown in figure , indicating that organoclay effectively increased the stiffness of the resulting polymer.
Mechanical properties
Figures and show the tensile strength and elongation of TPVs before and after the thermal aging (135 °C and 168 h), respectively. The addition of organoclay increased the tensile stress at break, depending on organoclay content, as shown in figure . Also, thermal ageing reduced the tensile stress at break, which was maintained at more than 85% of the original strength for all TPVs. Furthermore, adding organoclay markedly increased the degree of elongation, as shown in figure , in agreement with previous report [Citation44]. Additionally, thermal aging reduced the degree of elongation of EPDM/PP TPVs, which was maintained at 90% or more of the original value.
Morphological analysis
Figure shows the fractured surfaces of EPDM/PP TPVs with and without organoclay. The white lines in the fractured segments were formed by stretch-induced crystallization when preparing fractured samples, which was often observed in the crystallizable polymer [Citation45]. Furthermore, organoclay is reportedly a nucleating agent in the crystalline polymer system [Citation46, Citation47]. The organoclay-filled TPVs contain more dispersed lines than the neat TPV, suggested that organoclay acts as a nucleating agent in this system.
Conclusions
EPDM/PP TPVs reinforced with various organoclay contents were prepared using octylphenol-formaldehyde resin and stannous chloride dehydrate as vulcanizing agents. Experimental results suggest that organoclay affects neither the vulcanization process nor the degree of vulcanization. X-ray analysis indicates that these organoclay-filled TPVs are intercalated. The organoclay increases both the strength and degree of elongation of TPVs. The strength was maintained at 85% and more of the original value after the thermal aging. However, adding organoclay reduced the thermal stability of TPVs by decomposing the swelling agents in the organoclay.
References
- NaskarKNoordermeerJ W M 2006 J. Elast. Plast. 38 2 http://dx.doi.org/10.1177/0095244306060215
- MousaA 2005 Int. J. Polym. Mater. 54 7 http://dx.doi.org/10.1080/00914030490499099
- Van DuinMMachadoA V 2005 Polym. Degrad. Stab. 90 340 http://dx.doi.org/10.1016/j.polymdegradstab.2005.04.050
- NaskarKKokotDNoordermeerJ W M 2004 Polym. Degrad. Stab. 85 831 http://dx.doi.org/10.1016/j.polymdegradstab.2004.03.016
- GoharapeyFKatbabA ANazockdastH 2003 Rubber Chem. Technol. 76 1
- HuangHLiuXIkeharaT 2003 J. Appl. Polym. Sci. 90 824 http://dx.doi.org/10.1002/app.12579
- GoharpeyFKatbabA ANazockdastH 2001 J. Appl. Polym. Sci. 81 2531 http://dx.doi.org/10.1002/app.1694
- NaderiGhRazavi NouriM 1999 Iran. Polym. J. 8 37
- BhowmickA KInoueT 1993 J. Appl. Polym. Sci. 49 1893 http://dx.doi.org/10.1002/app.1993.070491104
- GhoreishyM H RRazavi NouriM 2000 Plast. Rubber Compos. 29 5
- AkelahAMoetA 1994 J. Appl. Polym. Sci., Appl. Polym. Symp. 153 55
- GiannelisE P 1996 Adv. Mater. 29 8
- AlexandreMDuboisP 2000 Mater. Sci. Eng. 1 28
- PicardEVermogenAGerardJ FEspucheE J 2007 Membr. Sci. 292 133 http://dx.doi.org/10.1016/j.memsci.2007.01.030
- DavidJ CArgentinaA L 2005 Chem. Mater. 17 13 http://dx.doi.org/10.1021/cm0302680
- YingweiDSalvatoreILuigiSLuigiN 2005 Macromol. Symp. 228 115 http://dx.doi.org/10.1002/masy.200551010
- JacquelotEEspucheEGerardJ FDuchetJMazabraudP 2006 J. Polym. Sci. B 44 431 http://dx.doi.org/10.1002/polb.20707
- OsmanM AMittalVSuterU W 2007 Macromol. Chem. Phys. 208 68 http://dx.doi.org/10.1002/macp.200600444
- AlexandreMDuboisP 2000 Mater. Sci. Eng. 28 1 http://dx.doi.org/10.1016/S0927-796X(00)00012-7
- MessermithP BGiannelisE P 1995 J. Polym. Sci. A 33 1047 http://dx.doi.org/10.1002/pola.1995.080330707
- GilmanJ WKashiwagiTLichtenhanJ D 1997 SMPE J. 33 40
- GilmanJ W 1999 Appl. Clay Sci. 15 31 http://dx.doi.org/10.1016/S0169-1317(99)00019-8
- ZhuJWilkieC A 2000 Polym. Int. 49 1158 http://dx.doi.org/10.1002/1097-0126(200010)49:10<1158::AID-PI505>3.0.CO;2-G
- SuSWilkieC A 2003 J. Polym. Sci. A 41 1124 http://dx.doi.org/10.1002/pola.10659
- VaiaR AVasudevanSKrawiecWScanlonL GGiannelisE P 1995 Adv. Mater. 7 154 http://dx.doi.org/10.1002/adma.19950070210
- ThakkarHGoettlerL A 2003 Rubber World 44 229
- BharadwajR KMehrabiAThompsonA K 2002 Polymer 43 3699 http://dx.doi.org/10.1016/S0032-3861(02)00187-8
- KrookMAlbertssonA CGeddeU WHedenqvistM S 2002 Polym. Eng. Sci. 42 1238 http://dx.doi.org/10.1002/pen.11027
- ChangJ HParkK MChoDYangH SIhnK J 2001 Polym. Eng. Sci. 41 1514 http://dx.doi.org/10.1002/pen.10850
- SekelikD JStepanovE VNazarenkoSSchiraldiDHiltnerABaerE 1999 J. Polym. Sci. B 37 847 http://dx.doi.org/10.1002/(SICI)1099-0488(19990415)37:8<847::AID-POLB10>3.0.CO;2-3
- WangZ FWangBQiNZhangH FZhangL Q 2005 Polymer 46 719 http://dx.doi.org/10.1016/j.polymer.2004.12.002
- RibeiroS P SEstevãoL M RNascimentoR S V 2008 Sci. Technol. Adv. Mater. 9 024408 http://dx.doi.org/10.1088/1468-6996/9/2/024408
- Al-SagheerFAliA A MMuslimSAhmadZ 2006 Sci. Technol. Adv. Mater. 7 111 http://dx.doi.org/10.1016/j.stam.2005.10.001
- MishraJ KRyouJ HKimG HHwangK JKimIHaC S 2004 Mater. Lett. 58 3481 http://dx.doi.org/10.1016/j.matlet.2004.07.003
- LeeK YGoettlerL A 2004 Polym. Eng. Sci. 44 1103 http://dx.doi.org/10.1002/pen.20103
- NaderiGLafleurP GDuboisC 2007 Polym. Eng. Sci. 47 207 http://dx.doi.org/10.1002/pen.20673
- TsaiYTsaiP YWuY TLeuM TWuJ H 2008 J. Elast. (at press)
- MishraJ KHwangK JHaC S 2005 Polymer 46 1995 http://dx.doi.org/10.1016/j.polymer.2004.12.044
- TranN HWilsonM AMilevA SDennisG RKannangaraG S KLambR N 2006 Sci. Technol. Adv. Mater. 7 786 http://dx.doi.org/10.1016/j.stam.2006.07.001
- OkamotoMMoritaSKotakaT 2001 Polymer 42 2685 http://dx.doi.org/10.1016/S0032-3861(00)00642-X
- BergmanJ SChenHGiannelisE PThomasM GCoatesG W 1999 Chem. Commun. 21 2179 http://dx.doi.org/10.1039/a905540a
- XieWGaoZPanW PHunterDSinghAVivaR 2001 Chem. Mater. 13 2979 http://dx.doi.org/10.1021/cm010305s
- XieWGaoZLiuKPanW PVaiaRHunterDSinghA 2001 Thermochim. Acta 367–368 339 http://dx.doi.org/10.1016/S0040-6031(00)00690-0
- PramanikMSrivastavaS KSamantarayB KBhowmickA K 2002 J. Polym. Sci. B 40 2065 http://dx.doi.org/10.1002/polb.10266
- TanniruMMisraR D K 2006 Mater. Sci. Eng. A 424 53 http://dx.doi.org/10.1016/j.msea.2006.02.034
- NaderiGLafleur PierreGDuboisC 2007 Polym. Eng. Sci. 47 207 http://dx.doi.org/10.1002/pen.20673
- TiongS CBaoS PLiangG D 2005 J. Polym. Sci. B 43 3112 http://dx.doi.org/10.1002/polb.20596