Abstract
A novel alloy design, designated as 1·2C–1·5Cr–5Al, has been proposed with high aluminium(∼5 wt-%) and more carbon(∼1·2 wt-%) addition into the classical 1C–1·5Cr bearing steel for lowering density and improving performance simultaneously, which is approximate 8 wt-% lighter than convention. In order to understand preliminarily the suitability of the novel alloy for bearing application, the martensite starting temperature and hardness, related to microstructure evolution and mechanical properties, respectively, after partial austenitisation treatment with undissolved carbides have been investigated carefully. The martensite starting temperature is comparable with conventional 1C–1·5Cr alloy. The hardness of 860±3 HV20 achieved is much higher than convention.
Introduction
Steels, containing approximate 0·8–1·1 wt-% of carbon and less than 3 wt-% of substitutional solutes in total, have served for through hardened bearings overwhelmingly in mass marketCitation1,Citation2 for over a century since the typical 1C–1·5Cr alloy was proved to be suitable for bearing application by ball bearing tests by Stribech in 1901Citation3 and then adopted in practice by Fichtel and Sachs in 1905.Citation2,Citation4 The supersaturated high carbon in martensite combined with the retained chromium enriched hard cementite guaranteed the very high hardness up to approximate 800 HV20 in bearings.Citation5 The microstructures were achieved by a partially austenitisation with ∼3–4% of undissolved cementite followed by quenching and tempering.Citation6–Citation8
Both rolling contact fatigue properties and wear resistance get improved with the increase in hardness for bearings.Citation5 Large carbon content can achieve high hardness by solid solution strengthening in martensite. Carbon, however, intensively suppresses the martensite starting temperature and therefore increases the volume fraction of untransformed austenite that is not desired in the point view of dimensional stability since the metastable austenite could be induced to transform into martensite during service,Citation9 furthermore the soft retained austenite would deteriorate the overall hardness. The hardness of martensite ceases to increase with its carbon concentration until approximate 800 HV has been achieved.Citation10,Citation11
A novel alloy design has been proposed by a combination of high aluminium and higher carbon addition (1·2C–5Al wt-%) into the classical 52100 bearing steel (1C–1·5Cr). Aluminium increases martensite starting Ms temperature,Citation12,Citation13 and therefore would compromise the suppress of Ms due to more carbon addition and the martensite fraction transformed consequently could be kept the same as convention. It is hence potential for the Al bearing high carbon alloy to achieve higher hardness in the freshly hardened condition compared with conventional 52100 alloys. In addition, high aluminium addition decreases the density of the steel owing to both the mass reduction led by light atoms and lattice parameter expansion led by light atom replacement.Citation14–Citation16 The initial microstructure in hot rolled condition has been characterised first. The microstructure and anticipated high hardness of the alloys heat treated with a dilatometer have been investigated carefully in order to primarily manifest suitability of the novel designed alloy for higher performance bearing application, in which the alloys have been partially austenitisation with some undissolved cementite in a series temperature followed by quenching.
Alloy design and experimental
The addition of light element aluminium into a steel, standing in the substitutional lattice position of iron, could reduce the overall density of the steel.Citation14–Citation16 Equilibrium phase diagram, phase constitution, as well as density of alloys were calculated by using ThermoCalc combined with TCFE6 database. A low density steel for bearings, designated as 1·2C–1·5Cr–5Al, was designed based on 1C–1·5Cr alloyCitation17 with addition of more carbon and high aluminium. The density of alloys are calculated by ThermoCalc and shown in , based on the chemical compositions of actually manufactured 1·2C–1·5Cr–5Al alloy and nominal 1C–1·5Cr alloy (in ). The novel alloy decreases its density to 7·078 g cm−3 in the condition of full BCC due to 5 wt-% of aluminium addition, compared with 7·665 g cm−3 in convention, which indicates the novel alloys is approximate 8% lighter ().
1. Density decrease in 1·2C–1·5Cr–5Al alloy compared with conventional 1C–1·5Cr steel in microstructure of fully martensite (BCC) or pearlite (BCC+cementite), indicated by ThermoCalc
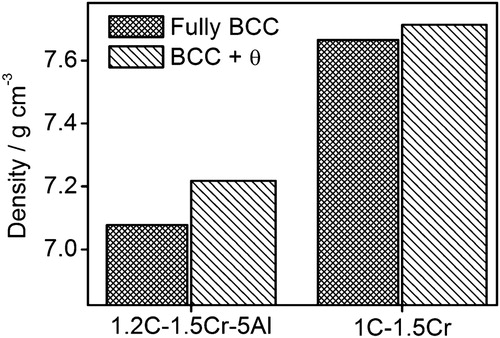
Table 1. Chemical compositions of experimental alloy compared with nominal 1C–1·5Cr alloy/wt-%
The suppression of Ms temperature leads to more austenite leaving untransformed and destroys the dimensional stability of bearing component during service by the stress induced martensite transformation.Citation18,Citation19 In the new alloy, 0·2 wt-% of carbon increase would suppress the martensite transformation temperature for 84·6°C, while 5 wt-% of aluminium in alloy could enhance 150°C, according to the empirical equation for estimating martensite starting (Ms) temperature with chemical compositions as follows:Citation12where the alloy elements in wt-%. The designed 1·2C–1·5Cr–5Al steel would not depress the martensite transformation compared with conventional 1C–1·5Cr alloys, and therefore could be suitable for bearing application in the point view of dimensional stability.
The alloy was manufactured as an approximate 50 kg ingot of dimension of Φ120×600 mm using a vacuum furnace. The ingot was reheated to 1200°C for 3 h (rate to 1200°C not monitored) for forging to make 60×60 mm slabs followed by air cooling. The slabs were then reheated to 1200°C for 3 h and hot rolled into 6×100 mm in thickness and width with the temperature between 1100 and 900°C followed by air cooling. The accurate heat treatments were conducted on a push rod Formastor-F II high-speed dilatometer with radio frequency induction heating and using cylindrical samples of 3mm in diameter and 10 mm in length, where the alloy was partially austenitised at the temperature between 750 and 950°C for 1 h followed by quenching at the rate of 20°C s−1. The austenitisation time were prolonged to 1 h, compared with 20 min in convention, to be considered to reach approximately the equilibrium in the novel 1·2C–1·5Cr–5Al alloy, since the high aluminium addition retards the kinetics of ferrite–austenite transformation.Citation20
The microscopy samples were prepared using standard methods and etched in 2 vol.-% natal. High resolution observations combined with wavelength dispersive spectroscopy (WDS) microanalysis were done using the electron scanning microscopy of a field emission electron probe microanalyser (JEOL JXA-8530F) operating at 20 kV accelerating voltage and 10·8 mm work distance. Hardness was measured with at least six tests for each sample on an FM-700 Vickers hardness tester with 10 s dwelling time, using 20 kgf loading.
Results and discussions
The novel 1·2C–1·5Cr–5Al alloy designed for bearing application in as hot rolled condition is consisted of almost full pearlite dispersed with very small amount of secondary phase (), revealed as prior austenite after pearlite formation.
2. Microscopy of as hot rolled alloy, indicated almost full pearlite dispersed with very small amount of secondary phase, prior austenite after pearlite formation
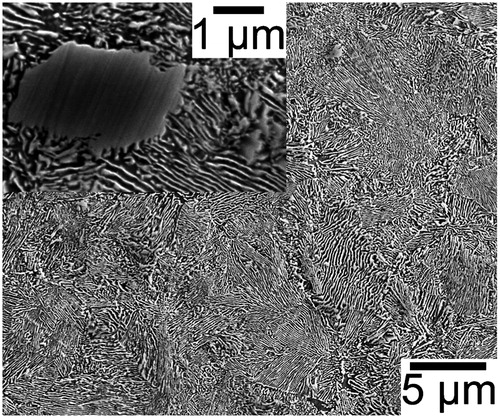
In order to investigate the possibility to improve hardness in the new design of alloy of 1·2C–1·5Cr–5Al, the alloy was partially austenitised with undissolved carbide for 1 h at 750, 770, 790, 810, 830, 850, 870, 910 and 950°C respectively, hence followed by quenching. The ferrite could not fully dissolve during austenitising up to 870°C (), in which carbon enriched into intercritical austenite due to its depletion from ferrite. The carbon enhancement suppressed its Ms temperature. Consequently, no martensite transformation was observed in dilatation curves until austenitisation temperature reach 830°C (). With the dissolution of ferrite, the carbon content in the austenite decreased during heat treatment with temperature rising and as a result that Ms temperature elevated gradually to the peak of 190°C ( and ) when ferrite fully transformed at 910°C (). The carbide dissolved gradually with the heating temperature increase, revealed as both fraction and size became smaller (), which led to an increase in carbon in austenite. Carbon in austenite consequently increased when austenitisation at 950°C compared with at 910°C, resulted in an Ms temperature slight decrease (). Fraction of austenite untransformed could be estimated by undercooling below Ms temperature according to the Koistinen–MarburgerCitation21 equationwhere fRA is the fraction of untransformed austenite at the quenching temperature QT. In order to keep the quenching temperature in uniform, all the heat treated specimens for microstructure characterizations and hardness tests were held in a mixture of ice and water for 1 h after dilatometer treatment. The QT accordingly should be 0°C in the Koistinen–Marburger equation hereby. The minimum fraction of austenite retained was approximate 0·12 according to measured Ms temperature (), which is comparable with the conventional 1C–1·5Cr steels.Citation22 The hardness in the freshly quenching condition have been achieved approximate 860±3 HV20 () with negligible fraction of carbide (). The combination addition of more carbon and high aluminium was proved to improve hardness of 60 HV in fresh martensite compared with the maximum hardness of 800 HV in conventional 1C–1·5Cr bearing steels achieved by martensite combined with extra hardness owing to ∼4 wt-% of carbide,Citation10,Citation11 since the aluminium increases Ms temperature and therefore permits more carbon in martensite when keeping transformed fraction.
3. Electronic microscopies of alloy partially austenitised at a 750°C, b 770°C, c 790°C, d 810°C, e 830°C, f 850°C, g 870°C, h 910°C and i 950°C respectively, followed by quenching, where α, γ and α′ represent ferrite, austenite and martensite respectively
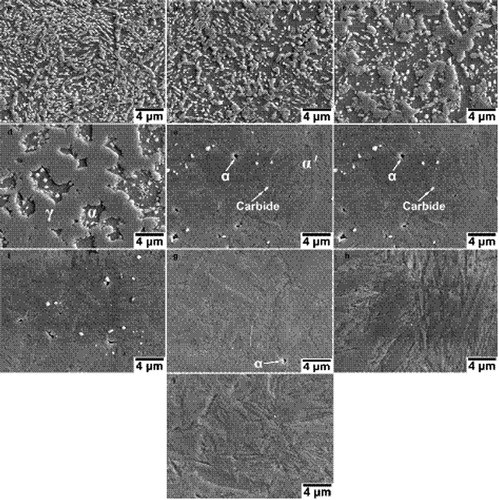
4. Martensitic transformation followed with partially austenitisation for 1 h at temperature from 750 to 950°C characterised by dilatation curve, where there was no martensitic transformation observed until austenitisation temperature reach 830°C
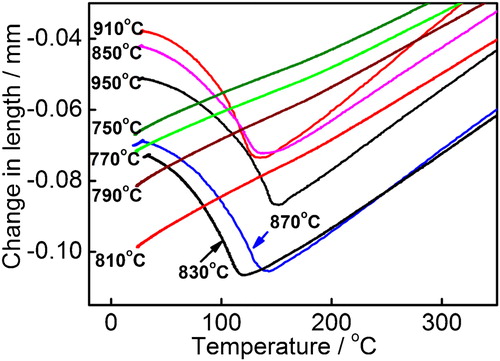
5. a martensite starting Ms temperature and austenite fraction untransformed at frozen temperature; b hardness achieved
Microstructure evolution change with austenitisation temperature
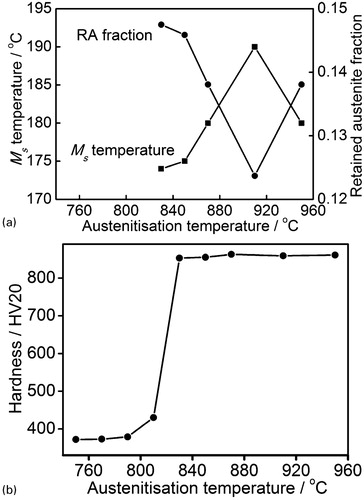
shows a typical Cr enrichment in carbide revealed by mapping of C, Cr, Mn and Al by wavelength dispersive spectroscopy (WDS) microanalysis, during partially austenitisation at 850°C for 1 h, which are in accordance with the nature for Cr enriching into carbide in bear steels. Thermodynamics calculation indicates 20 wt-% of Cr can enrich into cementite, and as high as 36 wt-% into M7C3 carbide in the new 1·2C–1·5Cr–5Al alloy ().
Conclusions
The novel alloy 1·2C–1·5Cr–5Al was designed with high aluminium (∼5 wt-%) and more carbon (∼1·2 wt-%) addition into the conventional 1C–1·5Cr bearing steels. The new alloy is approximate 8 wt-% lighter than convention due to aluminium addition. The 5 wt-% of aluminium addition could enhance martensite starting Ms temperature for 150°C, which compromises its suppression by extra carbon addition. The Ms temperature and austenite fraction retained after partial austenitisation with undissolved carbide are manifested to be comparable with convention, which enriched in chromium during austenitisation heat treatment. The peak hardness has achieved at 860±3 HV20 in the freshly quenched alloy partially austenitised at 910°C for 1 h, which is approximate 10% enhanced compared with convention. The microstructure and hardness, as well as the low density, achieved in the novel alloy have exhibited the potential for high performance bearing application.
Acknowledgements
The research was financially supported by the National Natural Science Foundation of China (grant no. 51204051), as well as by the Fundamental Research Funds for the Central Universities (grant nos. N120507001 and N120607001).
Notes
This paper is part of a special issue on Adventures in the Physical Metallurgy of Steels
References
- Bamberger EN: ‘Materials for rolling element bearings’, in ‘Bearing design – historical aspects, present technology and future problems’, (ed. Anderson W J), 1–46; 1980, San Antonio, TX, ASME.
- Cappel J, Weinberg M and Flender R: ‘The metallurgy of roller-bearing steels’, Steel Grips, 2004, 2, 261–268.
- Hengerer F: ‘The history of SKF3’, Ball Bear J., 1987, 231, 2–11.
- Tsubota K, Sato T, Kato Y, Hiraoka K and Hayashi R: ‘Bearing steels in the 21st century’, in ‘Bearing steels: into the 21st century’, (ed. Hoo J J C and Green W B), 202–215; 1998, West Conshohocken, Pennsylvania, American Society for Testing of Materials.
- Bhadeshia HKDH: ‘Steels for bearings’, Progr. Mater. Sci., 2012, 57, 268–435.
- Bhadeshia HKDH: ‘The driving force for martensitic transformation in steels’, Met. Sci., 1981, 15, 175–177.
- Bhadeshia HKDH: ‘Thermodynamic extrapolation and the martensite-start temperature of substitutionally alloyed steels’, Met. Sci., 1981, 15, 150–178.
- Beswick JM: ‘Fracture and fatigue crack propagation properties of hardened 52100 steel’, Metall. Mater. Trans. A, 1989, 20A, 1961–1973.
- Anon.: ‘Crucible 52CB bearing steel data sheet’, Technical report 8–62, Crucible Steel Company of America, Pittsburgh, PA, USA, 1962.
- Bhadeshia HKDH and Edmonds DV: ‘Bainite in silicon steels: a new composition property approach I’, Met. Sci., 1983, 17, 411–419.
- Bhadeshia HKDH and Edmonds DV: ‘Bainite in silicon steels: a new composition property approach II’, Met. Sci., 1983, 17, 420–425.
- Andrews KW: ‘Empirical formulae for the calculation of some transformation temperatures’, J. Iron Steel Inst., 1965, 7, 721–727.
- Mintz B: ‘The influence of aluminium on the strength and impact properties of steel’, Proc. Int. Conf. on ‘TRIP-aided high strength ferrous alloys’, 379–382; 2002, Ghent, Mainz.
- Howell RA and Van Aken DC: ‘A literature review of age hardening Fe-Mn-Al-C alloys’, Iron Steel Technol., 2009, 6, 193–212.
- Suh DW and Kim NJ: ‘Low-density steels’, Scr. Mater., 2013, 68, (6), 337–338.
- Yi HL, Chen P, Hou ZY, Hong N, Cai HL, Xu YB, Wu D and Wang GD: ‘A novel design: partitioning achieved by quenching and tempering (Q–T & P) in an aluminium-added low-density steel’, Scr. Mater., 2013, 68, 370–374.
- Hollox GE, Hobbs RA and M.Hampshire J: ‘Lower bainite bearings for adverse environments’, Wear, 1981, 68, 229–240.
- Anon.: ‘Crucible 52CB bearing steel data sheet’, Technical report 8–62, Crucible Steel Company of America, Pittsburgh, PA, USA, 1962.
- Pearson PK: ‘The history and future of aircraft turbine engine bearing steels’, in ‘Bearing steels: into the 21st century’, (ed. Hoo J J C), 335–353; 1998, West Conshohocken, PA, ASTM.
- Chen P, Wang GD and Yi HL: ‘Transformation into austenite from ferrite plus cementite in high aluminium-bearing steels’, Metall. Mater. Trans. A, to be published.
- Koistinen PP and Marburger RE: ‘A general equation prescribing the extent of the austenite-martensite transformation in pure iron-carbon alloys and plain carbon steels’, Acta Metall., 1959, 7, 59–60.
- Sommer C, Christ H.-J and Mughrabi H: ‘Non-linear elastic behaviour of the roller bearing steel SAE 52100 during cyclic loading’, Acta Metall. Mater., 1991, 39, 1177–1187.