Abstract
One form of damage due to rolling contact fatigue is the formation of localised regions of extremely hard material forming within the body of a bearing. These regions have a relatively homogeneous structure and hence etch mildly with respect to the surrounding unaffected matrix. They, therefore, appear white in a darker background when examined using optical microscopy. We assess here the cause of this damage and propose solutions that are backed by evidence that already is available. The issue is important because of the spate of unexpected failures in large wind turbine bearings and of generic importance in determining the life of more well behaved bearing applications.
Introduction
A bearing has to sustain static as well as cyclic loads in order to achieve the dual role of minimising friction between the moving parts of a machine and of transmitting loads. A typical bearing will contain rolling elements such as balls, held between raceways. When the element moves over the raceway, it induces a momentary system of Hertzian stresses that reach a maximum below the contact surface. In a rotating bearing, such cycles are repeated on each occasion that the roller traverses a selected point on the raceway, the affected region experiencing a combination of cyclic torsion with a compressive mean stress superimposed in phase.Citation1–Citation3 The magnitudes of the stresses are of the order of 2 GPa. This kind of loading induces subsurface microstructural damage.
Steels are capable of sustaining such punishment during service; furthermore, the useful life of the component can be estimated reliably when the operating conditions are known and controlled. There are three alloys most common in bearing applications, all heat treated to hardness levels of 60–62 HRC in the regions subjected to the greatest contact stresses. Their nominal compositions are listed in . M50 and M50NiL are secondary hardening, aeroengine bearing variants in which the tempered martensite is strengthened by the precipitation at high temperatures (≃550°C) of carbides that are rich in Mo, Cr and V.Citation4–Citation6 M50NiL is case hardened to achieve the required properties in the surface region, with a core toughness that is not matched by high carbon bearing steels. In contrast, the 52100 steel has proeutectoid cementite particles a few micrometres in size, and much finer iron based carbides that result from low temperature tempering ( < 200°C).Citation7
Damage
It has been observed in recent years that the large bearings used in wind turbines have an erratic tendency to fail well before their intended service lives (e.g. Ref. 10). As a consequence, failure investigations have proliferated with the focus on microstructural changes, such as the ones that are the subject of this assessment.
It might be expected from the rotational symmetry of the bearing that damage should be uniformly spread as a band concentric with the circumference of the bearing raceway. In 52100 steel, microstructural change is indeed found in the form of mechanically tempered, dark etching regions where the local hardness is slightly reduced ().Citation11,Citation12 However, the most pernicious form of subsurface microstructural damage is not uniformly spread, but is localised below the contact surface because it initiates at defects, such as non-metallic inclusions. This form of localised damage is readily recognised as regions that etch lighter than the surrounding steel;Citation9,Citation13,Citation14 some details of damage are apparent in the scanning electron micrograph shown in .Footnote* They are associated inevitably with microscopic cracks so that the local compliance is reduced,Citation15 leading to an intense focusing of deformation. So much so that cementite particles are taken into solution by a process akin to mechanical alloying, and the hardness of the damaged regions increases dramatically.Footnote†
1. a Uniform layer of dark etching region on circumferential section, following 107 rotations while subjected to contact stress of 3·3 GPa at 70°C. Micrograph courtesy of T. B. Lund. b Three-dimensional form of dark etching microstructure. c White etching regions emanating from inclusion. Reproduced with permission of Elsevier, from Ref. 23. d Irregular white etching regions associated with axial crack on bearing. Micrograph courtesy of R. Errichello, GEARTECH. e Typical sequence of damage evolution. Fatigue index is measure of heterogeneous strains within material. Adapted from
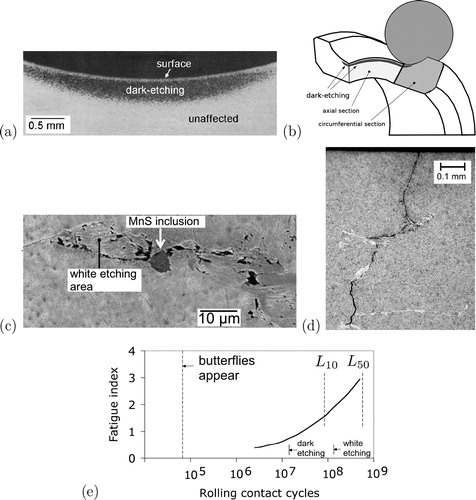
This brief explanation of white etching regions does not do justice to all that is reported on the subject, but a key issue is whether the regions are a symptom or the cause of damage. To quote Dovrak,Citation26 ‘Either the crack propagates around the white etching [sic] or white etching forms around the cracks, but we are not sure why’. This confusion hinders the development of clear solutions to the problem. The purpose here is to present an interpretation of key data and therefore the methods that should eliminate the problem. The characteristics of white etching regions can be listed as follows:
(i) | they initiate at pre-existing defects or heterogeneities such as voidsCitation27,Citation28 | ||||
(ii) | hydrogen enhances the formation of white etching regions (e.g. Ref. 29) | ||||
(iii) | the regions have experienced intense plastic deformation resulting in a mechanical homogenisation of phases and a nanostructureCitation30–Citation32 | ||||
(iv) | the regions are mechanically mixed, resulting in the dissolution of cementite and a concomitant increase in the carbon concentration of the ensuing solid solutionCitation33,Citation34 | ||||
(v) | the regions are, therefore, harder than the surroundings.Citation34–Citation36 The hardness of the white region is in excess of 1000 HV, which compares against ∼750 HV for the tempered martensite matrix | ||||
(vi) | white etching regions are easily identified using routine metallographic techniques; they are therefore prominent, visible signs of damage and hence readily blamed for failure in cursory studies | ||||
(vii) | in terms of a typical L10 bearing life of about 108 contact cycles, it is well established that white etching regions initiated at defects (‘butterflies’) make an appearance at < 105 cycles but do not cause the failure of bearings; the chronology of damage evolution is illustrated in , so the appearance of butterflies per se does not correspond to failure. |
Hypothesis and solutions
As pointed out above, the hard regions that etch white are frequently identified with the cause of premature bearing failure. The proposed mechanisms for the formation of white etching regions include diverse phenomena such as severe localised deformation, adiabatic shear, carbide dissolution and low temperature recrystallisation.Citation9,Citation10,Citation14,Citation32 These ideas miss the obvious observation that white etching matter is associated with pre-existing defects such as inclusions with weak interfaces,Citation9,Citation23,Citation37,Citation38 pores originating from processing or microscopic cracks associated with martensite plates or separated prior austenite grain boundaries. The inevitable conclusion is that defects in the steel precede the formation of white matter.
The hypothesis, therefore, is that the primary process in damage evolution begins with the initiation of a microscopic crack.Citation30 This then develops into the white matter by the rubbing together of the crack surfaces, causing intense, localised mechanical deformation under the action of rolling contact stresses.Citation9,Citation39,Citation40 The design of better bearing steels depends on a clarification of this issue. With this hypothesis, a solution to the elimination of white etching regions would rely on an increased resistance to cracking, i.e. in making tougher steel.Citation30
Such a hypothesis is able to explain all the observations listed in the preceding section. Hydrogen enhances the formation of white etching matter because it reduces the fracture toughness of the steel and hence promotes cracking. Routine observations on the influence of hydrogen on white matter formation continue to be attributed to enhanced localised plasticity without supporting evidence or a theory for the localisation of white matter itself;Citation29 all the observations can in fact be explained by enhanced brittle cracking due to hydrogen, which then leads to white matter resulting from crack-face friction under the influence of stress. It should not therefore be surprising that large systems of cracks develop in hydrogen charged specimens subjected to rolling contact loading, which are less frequent in uncharged samples, and that the cracks are associated with irregular white etching regions.Citation40 The idea that collision between fractured surfaces is necessary to produce white matter is vividly illustrated by a surface initiated axial crack shown . The crack is not uniformly decorated with white etching material, which occurs only on the crack faces that are normal to the compression axis of the contact stress. Those roughly parallel to the axis do not show the white etching areas. The localisation of strain is known to be strongly dependent on the crack orientation relative to the stress.Citation15
The role of hydrogen, therefore, appears simply to be to embrittle the steel and hence provide the parted surfaces that initiate localised plastic deformation. Indeed, any embrittlement mechanism, for example the decoration of austenite grain surfaces by phosphorus, will have the same effect as hydrogen on the development of white etching regions.Citation9 Thus, the introduction of microscopic cracks in bearing steel before rolling contact fatigue testing dramatically increases the occurrence of white-etching regions.Citation41 This latter work shows at the same time that cracks likely precede the formation of white etching regions.
The intense localisation of plastic deformation occurs because the cracked region has a lower compliance, so the surfaces of the cracks repeatedly beat or slide against each other. The intense deformation breaks up the proeutectoid cementite and forces it into solid solution in a process that is well understood in other contexts.Citation42–Citation48 It is interesting that the reduction in compliance in a microscopically cracked bearing steel subjected subsequently to rolling contact fatigue resulted in a better life than a corresponding sample that was integral before testing.Citation41,Citation49
Carbon is the most potent contributor to the strength of steel when in solid solution. The hardness of the white etching region is measured to be greater than that of the surrounding matrix by at least 250 HV. The proeutectoid cementite would add ∼0·18 wt% of carbon to the solid solution (p. 278 in Ref. 9), causing a hardness increase of 170 HV,Citation50 the residue presumably being associated with the fine scale of the structure in the white etching region together with the absorption of the minute carbides resulting from the tempering heat treatment. It is perhaps even more significant in the present context that the region would be greatly embrittled by this dissolved carbon so that the initiating crack would be more likely to propagate as the white etching region grows, but not beyond the confines of the white area, provided that the critical stress intensity for unstable fracture is not reached. Therefore, one solution would be to eliminate the proeutectoid cementite in the microstructure, either using lower carbon bearing steel or by changing the final heat treatment. Experimental carbide-free bearing steel does not exhibit white matter formation during rolling contact fatigue,Citation51 and a martensitic steel containing only tempering carbides showed a lower propensity to form white matter than one containing proeutectoid cementite.Citation52 It is worth emphasising that even if white matter forms in a carbide-free steel, its hardness cannot be as high as that associated with white matter that consumes carbides.
It is sometimes considered that the proeutectoid cementite is needed in the microstructure to facilitate the divorced eutectoid reactionCitation53,Citation54 that helps soften the steel in preparation for manufacturing operations. However, heat treatments can be designed so that the proeutectoid cementite need not be present in the final microstructure.Citation55 Indeed, carbide-free structures are now being investigated for low alloy bearing steels;Citation51,Citation55 more expensive steels containing a large solute content, such as the Cronidur 30,Citation56,Citation57 are already available for specialist aerospace applications, with a low carbon concentration that avoids carbides that are undissolved at the austenitisation temperature.
Another option is to make the proeutectoid cementite more thermodynamically stable by increasing the chromium concentration of the steel. (It has been reported, for example, that enhancing the chromium concentration in a stainless steel helped reduce the formation of white matter, although the reason was speculated to be the prevention of hydrogen accumulation at defects by chromium.Citation58) Evidence from M50 and M50NiL suggests a much reduced tendency to form hard white matter and associated cracks in this class of secondary hardening steels, probably because the resulting alloy carbides are much more stable than cementite.Citation9 The persistent carbides in these secondary hardening steels are used to explain the accumulation of plastic strain in affected regions that are not localised.Citation59
Butterflies are known to form at high contact stresses even in the M50/M50NiL alloys,Citation21 but have not been reported in any study from bearings that have experienced service.Citation60 Indeed, rolling contact fatigue is not a key feature in the failure of aeroengine bearings: the vast majority of operational failures in M50/M50NiL bearings are due to surface distress;Citation61–Citation63 although such distress can initiate cracks that grow by a fatigue mechanism, leading eventually to spalling, the important distinction is that initiation does not begin below the surface where rolling contact stresses are maximal.
A longer term solution is to make tougher bearing steels that have a ductile failure mechanism in the stress affected region. A steel based on a nanostructured mixture of bainitic ferrite and retained austeniteCitation64 is a candidate for a new class of bearing steels. Rolling contact fatigue tests demonstrate butterfly-like cracks emanating from inclusions, but without the associated white matter. Furthermore, damage in the stress affected regions is ductile, with voids forming at interfaces, linking as the test progresses, with considerable branching of the links.Citation51 Steels with these structures have a proven record of good wear,Citation65,Citation66 fatigue and rolling contact fatigue resistanceCitation67 although proper bearing tests have never been attempted. They can also be manufactured on a large scale.Citation68,Citation69
In summary, the following assertions may help focus investigations on current steel technologies, on the performance of wind turbine bearings, and on the development of future generations of bearing steels:
(i) | cracks likely precede the formation of hard white etching regions, which are a consequence of the localisation of plastic deformation due to the collision of crack faces under the influence of repeated contact stresses; to prevent the formation of hard white etching regions, it is necessary to avoid cracking and hence to improve the toughness of bearing steels | ||||
(ii) | hydrogen embrittles the steel, thus increasing the tendency for cracking and hence for the formation of hard white etching matter; the mechanism by which the hydrogen embrittles is not terribly relevant in this process; we know with complete certainty that it embrittles the steel; there are at least 38 000 publications on hydrogen in steels; all that is necessary is to avoid diffusible hydrogen or render it innocuous when it does enter the steel | ||||
(iii) | the removal of relatively coarse proeutectoid cementite in 52100 type steel should reduce the tendency for the formation of hard white etching matter; if the hardness of these regions is sufficiently reduced in this process, then they may become benign; an increase in the thermodynamic stability of the cementite must also help in this respect | ||||
(iv) | it is obvious that tougher bearing steels are required and those that fail by a ductile rather than a brittle mechanism; one way forward is the carbide-free bearing steel, some examples of which are promising | ||||
(v) | there already exists sufficient characterisation of white etching regions, at many different resolutions.Citation14,Citation32,Citation34,Citation38,Citation39,Citation70–Citation77 Further experiments of this type are likely to yield diminishing value. |
Notes
* Typical examples of the three-dimensional shape and other details can be found in Ref. 9.
† A different form of white etching damage known as bands that are below but inclined to the contact surface can also occur during the late stages of bearing life, particularly when the contact stresses are exaggerated relative to those encountered during service.Citation16 These bands in 52100 steel are denuded in carbon and hence are soft relative to the matrix;Citation9,Citation17–Citation20 the same is true of similar bands found in M50 bearings.Citation21 These softened bands are not associated with cracks or failure and hence are not discussed further. Other forms of white matter resulting from machining or other fabrication operationsCitation22 are not relevant to the present discussion.
References
- Fujita S., Matsuoka S. and Murakami T.: ‘Effect of hydrogen on fatigue behaviour of bearing steel under cyclic torsion with compressive mean stress’, in ‘Mechanics of materials’, 241–243; 2000, Tokyo, Japan Society of Mechanical Engineers.
- Fujita S., Matsuoka S. and Murakami Y.: ‘Effect of hydrogen on mode II fatigue behavior and microstructural change of bearing steel under cyclic torsion with a compressive axial mean stress’, Trans. Jpn Soc. Mech. Eng. A, 2009, 75A, 201–210.
- Burkart K., Bomas H., Schroeder R. and Zoch H.-W.: ‘Rolling contact and compression–torsion fatigue of 52100 steel with special regard to carbide distribution’, in ‘Advances in rolling contact fatigue strength testing and related substitute technologies’, (ed. Beswick J. M.., 218–236; 2012, West Conshohocken, PA, ASTM International.
- Bridge J. E., Maniar G. N. and Philip T. V.: ‘Carbides in M50 high-speed steel’, Metall. Trans., 1971, 2, 2209–2214.
- Decaudin B., Djega-Mariadassou C. and Cizeron G.: ‘Structural study of M50 steel carbides’, J. Alloys Compd, 1995, 226, 208–212.
- Hetzner D. W. and van Geertruyden W.: ‘Crystallography and metallography of carbides in high alloy steels’, Mater. Charact., 2008, 59, 825–841.
- Vetters H., Dong J., Bornas H., Hoffmann F. and Zoch H.-W.: ‘Microstructure and fatigue strength of the roller-bearing steel 100Cr6 (SAE 52100) after two-step bainitisation and combined bainitic–martensitic heat treatment’, Int. J. Mater. Res., 2006, 97, 1432–1440.
- Zaretsky E. V.: ‘Rolling bearing steels – a technical and historical perspective’, Mater. Sci. Technol., 2012, 28, 58–69.
- Bhadeshia H. K. D. H.: ‘Steels for bearings’, Prog. Mater. Sci., 2012, 57, 268–435.
- Errichello R., Sheng S., Keller J. and Greco A.: Proc. Wind Turbine Tribology Seminar, Golden, CO, USA, February 2012, US Department of Energy, Tech. Rep. DOE/GO-102012-3496.
- Jones A. B.: ‘Metallographic observations of ball bearing fatigue phenomena’, Proc. Symp. on ‘Testing of bearings’, ASTM STP 70, 35–52; 1947, Philadelphia, PA, ASTM International.
- Bush J. J., Grube W. L. and Robinson G. H.: ‘Microstructural and residual stress changes in hardened steel due to rolling contact’, ASM Trans., 1961, 54, 390–412.
- Tricot R., Monnot J. and Lluansi M.: ‘How microstructural alterations affect fatigue properties of 52100 steel’, Met. Eng. Q., 1972, 12, 39–47.
- Evans M.-H.: ‘White structure flaking in wind turbine gearbox bearings: effects of “butterflies” and white etching cracks’, Mater. Sci. Technol., 2012, 28, 3–22.
- Anderson P. M., Fleck N. A. and Johnson K. L.: ‘Localization of plastic deformation in shear due to microcracks’, J. Mech. Phys. Solids, 1990, 38, 681–699.
- Bhadeshia H. K. D. H.: ‘Bearing steels, editorial’, Mater. Sci. Technol., 2012, 28, 1–2.
- Buchwald J. and Heckel R. W.: ‘An analysis of microstructural changes in 52100 steel bearings during cyclic stressing’, Trans. ASM, 1968, 61, 750–756.
- Beswick J. M.: ‘Measurement of carbon levels in structurally transformed SAE 52100 ball bearing steel by microprobe analysis’, Pract. Metallogr, 1975, 12, 200–206.
- Österlund R., Aucouturier M. and Vingsbo O.: ‘High resolution autoradiography determination of carbon diffusion during rolling contact fatigue in ball bearings’, Scand. J. Metall., 1981, 10, 67–72.
- Polonsky I. A. and Keer L. M.: ‘On white etching band formation in rolling bearings’, J. Mech. Phys. Solids, 1995, 43, 637.
- Forster N. H., Rosado L., Ogden W. P. and Trivedi H. K.: ‘Rolling contact fatigue life and spall propagation characteristics of AISI M50, M50 NiL, and AISI 52100. Part III: metallurgical examination’, Tribol. Trans., 2010, 53, 52–59.
- Umbrello D. and Rotella G.: ‘Experimental analysis of mechanisms related to white layer formation during hard turning of AISI 52100 bearing steel’, Mater. Sci. Technol., 2012, 28, 205–212.
- Evans M.-H., Richardson A. D., Wang L. and Wood R. J. K.: ‘Effect of hydrogen on butterfly and white etching crack (WEC) formation under rolling contact fatigue (RCF)’, Wear, 2013, 306, 226–241.
- Furumura K., Murakami Y. and Abe T.: ‘Development of long life bearing steel for full lubrication and for poor and contaminated lubrication’, Motion Control, 1996, 1, 30–36.
- Johnston G. B., Andersson T., Amerongen E. V. and Voskamp A.: ‘Experience of element and full-bearing testing of materials over several years’, in ‘Rolling contact fatigue testing of bearing steels’, (ed. Hoo J. J. C.., 190–205; 1982, Philadelphia, PA, ASTM.
- Dovrak P.: ‘NREL's gearbox collaborative provides more insight why gearboxes fail – and a solution’, 2013, http://www.windpowerengineering.com/design/mechanical/gearboxes/nrels-gearbox-collaborative-provides-more-insight-why-gearboxes-fail-and-a-solution-2/.
- Styri H.: ‘Fatigue strength of ball bearing races and heat-treated 52100 steel specimens’, Proc. ASTM, 1951, 51, 682–700.
- Selecka M. and Salak A.: ‘Durability and failure of powder forged rolling bearing rings’, Wear, 1999, 236, 47–54.
- Uyama H., Yamada H., Hidaka H. and Mitamura N.: ‘The effects of hydrogen on microstructural change and surface originated flaking in rolling contact fatigue’, Tribol. Online, 2011, 6, 123–132.
- Hiraoka K., Nagao M. and Isomoto T.: ‘Study of flaking process in bearings by white etching area generation’, J. ASTM Int., 2007, 3, 234–240.
- Hiraoka K., Fujimatsu T., Hashimoto K., Fukumoto S. and Yamamoto A.: ‘Crystallographic analyses on cracks initiated by rolling contact fatigue in high carbon chromium bearing steel’, Mater. Sci. Forum, 2007, 561–565, 2151–2154.
- Grabulov A., Ziese U. and Zandbergen H. W.: ‘TEM/SEM investigation of microstructural changes within the white etching area under rolling contact fatigue and 3-D crack reconstruction by focused ion beam’, Scr. Mater., 2007, 57, 635–638.
- Becker P. C.: ‘Microstructural changes around non-metallic inclusions caused by rolling-contact fatigue of ball-bearing steels’, Met. Technol., 1981, 8, 234–243.
- Grabulov A., Petrov R. and Zandbergen H. W.: ‘EBSD investigation of the crack initiation and TEM/FIB analyses of the microstructural changes around the cracks formed under rolling contact fatigue’, Int. J. Fatigue, 2010, 32, 576–583.
- Loy B. and McCallum R.: ‘Mode of formation of spherical particles in rolling contact fatigue’, Wear, 1973, 24, 219–228.
- Osterlund R., Vingsbo O., Vincent L. and Guiraldenq P.: ‘Butterflies in fatigued ball bearings – formation mechanisms and structure’, Scand. J. Metall., 1982, 11, 23–32.
- Evans M.-H., Wang L., Jones H. and Wood R. J. K.: ‘White etching crack (WEC) investigation by serial sectioning, focused ion beam and 3-D crack modelling’, Tribol. Int., 2013, 65, 146–160.
- Evans M.-H., Richardson A. D., Wang L., Wood R. J. K. and Anderson W. B.: ‘Confirming subsurface initiation at non-metallic inclusions as one mechanism for white etching crack (WEC) formation’, Tribol. Int., 2014, 75, 87–97.
- Grabulov A.: ‘Fundamentals of rolling contact fatigue’, PhD thesis, University of Belgrade, Serbia, 2010.
- Vegter R. H. and Slycke J. T.: ‘The role of hydrogen on rolling contact fatigue response of rolling element bearings’, J. ASTM Int., 2010, JAI, 102543.
- Solano-Alvarez W. and Bhadeshia H. K. D. H.: ‘White-etching matter in bearing steel. Part II: distinguishing cause and effect in bearing steel failure’, Metall. Mater. Trans. A, 2014, 45A, 4916–4931.
- Kalish D. and Cohen M.: ‘Structural changes and strengthening in the strain tempering of martensite’, Mater. Sci. Eng., 1970, 6, 156–166.
- Languillaume J., Kapelski G. and Baudelet B.: ‘Cementite dissolution in heavily cold drawn pearlitic steel wires’, Acta Mater., 1997, 45, 1201–1212.
- Danoix F., Julien D., Sauvage X. and Copreaux J.: ‘Direct evidence of cementite dissolution in drawn pearlitic steels observed by tomographic atom probe’, Mater. Sci. Eng. A, 1998, A250, 8–13.
- Ivanisenko Y., Lojkowski W., Valiev R. Z. and Fecht H. J.: ‘The mechanism of formation of nanostructure and dissolution of cementite in a pearlitic steel during high pressure torsion’, Acta Mater., 2003, 51, 5555–5570.
- Perez M., Sidoro C., Vincent A. and Esnouf C.: ‘Microstructural evolution of martensitic 100Cr6 bearing steel during tempering: from thermoelectric power measurements to the prediction of dimensional changes’, Acta Mater., 2009, 57, 3170–3181.
- Kozeschnik E. and Bhadeshia H. K. D. H.: ‘Influence of silicon on cementite precipitation in steels’, Mater. Sci. Technol., 2008, 24, 343–347.
- Maalekian M. and Kozeschnik E.: ‘A thermodynamic model for carbon trapping in lattice defects’, CALPHAD, 2008, 32, 650–654.
- Solano-Alvarez W. and Bhadeshia H. K. D. H.: ‘White-etching matter in bearing steel. Part 1: controlled-cracking of bearing steel’, Metall. Mater. Trans. A, 2014, 45A, 4907–4915.
- Blondeau R., Maynier P., Dollet J. and Vieillard-Baron B.: ‘Estimation of hardness, strength and elastic limit of C- and low-alloy steels from their composition and heat treatment’, Mem. Sci. Rev. Metall., 1975, 72, 759–769.
- Solano-Alvarez W., Pickering E. J. and Bhadeshia H. K. D. H.: ‘Degradation of nanostructured bainitic steel under rolling contact fatigue’, Mater. Sci. Eng. A, 2014, A617, 156–164.
- Sugino K., Miyamoto K., Nagumo M. and Aoki K.: ‘Structural alterations of bearing steels under rolling contact fatigue’, Trans. Iron Steel Inst. Jpn, 1970, 10, 98–111.
- Verhoeven J. D. and Gibson E. D.: ‘The divorced eutectoid transformation in steel’, Metall. Mater. Trans. A, 1998, 29A, 1181–1189.
- Pandit A. S. and Bhadeshia H. K. D. H.: ‘Divorced pearlite in steels’, Proc. R. Soc. A, 2012, 468A, 2767–2778.
- Luo D., Peet M. J., Ooi S. W., Yan P., Yin Z. and Bhadeshia H. K. D. H.: ‘Spheroidisation of hypereutectoid state of nanostructured bainitic steel’, Mater. Sci. Technol., 2014, 30, 1282–1286.
- Böhmer H. J., Hirsch T. and Streit E.: ‘Rolling contact fatigue behaviour of heat resistant bearing steels at high operational temperatures’, Materialwiss. Werkstofftech., 1999, 30, 533–541.
- Carlson D., Pitsko R., Chidester A. J. and Imudo J. R.: ‘The effect of bearing steel composition and microstructure on debris dented rolling element bearing performance’, in ‘Bearing steel technology’, (ed. Beswick J.., 330–345; 2002, West Conshohocken, PA, ASTM International.
- Fujita S. and Mitamura N.: ‘Research of new factors affecting rolling contact fatigue life’, Proc. World Tribology Cong. III, Washington, DC, USA, September 2005, American Society of Mechanical Engineers, 73–74.
- Arakere N. K. and Subhash G.: ‘Work hardening response of M50-NiL case hardened bearing steel during shakedown in rolling contact fatigue’, Mater. Sci. Technol., 2012, 28, 34–38.
- Nygaard J. R., Rawson M., Danson P. and Bhadeshia H. K. D. H.: ‘Bearing steel microstructures after aircraft gas turbine engine service’, Mater. Sci. Technol., 2014, 30, 1911–1918.
- Bamberger E. N.: ‘Status of understanding for bearing materials (n-84-25047 15-37)’, in ‘Tribology in the 80’s’ 2, 773–794; 1984, Cleveland, OH, NASA Lewis Research Centre.
- Averbach B. L. and Bamberger E. N.: ‘Analysis of bearing incidents in aircraft gas turbine mainshaft bearings’, Tribol. Trans., 1991, 34, 241–246.
- Gloeckner P. and Ebert F. J.: ‘Micro-sliding in high-speed aircraft engine ball bearings’, Tribol. Trans., 2010, 53, 369–375.
- Bhadeshia H. K. D. H.: ‘The first bulk nanostructured metal’, Sci. Technol. Adv. Mater., 2013, 14, 014202.
- Sourmail T., Caballero F. G., Garcia-Mateo C., Smanio V., Ziegler C., Kuntz M., Elvira R., Leiro A., Vuorinen E. and Teeri T.: ‘Evaluation of potential of high Si high C steel nanostructured bainite for wear, fatigue applications’, Mater. Sci. Technol., 2013, 29, 1166–1173.
- Bakshi S. D., Leiro A., Prakash B. and Bhadeshia H. K. D. H.: ‘Dry rolling/sliding wear of nanostructured bainite’, Wear, 2014, 316, 70–78.
- Feng X. Y., Zhang F. C., Kang J., Yang Z. N. and Long X. Y.: ‘Sliding wear and low cycle fatigue properties of new carbide free bainitic rail steel’, Mater. Sci. Technol., 2014, 30, 1410–1418.
- Rose A. J., Mohammed F., Smith A. W. F., Davies P. A. and Clarke R. D.: ‘Superbainite: laboratory concept to commercial product’, Mater. Sci. Technol., 2014, 30, 1094–1098.
- Garcia-Mateo C., Sourmail T., Caballero F. G., Smanio V., Kuntz M., Ziegler C., Leiro A., Vuorinen E., Elvira R. and Teeri T.: ‘Nanostructured steel industrialisation: plausible reality’, Mater. Sci. Technol., 2014, 30, 1071–1078.
- O'Brien J. L. and King A. H.: ‘Electron microscopy of stress-induced structural alterations near inclusions in bearing steels’, J. Basic Eng., 1966, 88, 568–572.
- Martin J. A., Borgese S. F. and Eberhardt A. D.: ‘Microstructural alterations of rolling-bearing steel undergoing cyclic contact’, ASME J. Basic Eng., 1966, 88, 555–567.
- Swahn H., Becker P. C. and Vingsbo O.: ‘Electron-microscope studies of carbide decay during contact fatigue in ball bearings’, Met. Sci., 1976, 10, 35–39.
- Harada H., Mikami T., Shibata M., Sokai D., Yamamoto A. and Tsubakino H.: ‘Microstructural changes and crack initiation with white etching area formation under rolling/sliding contact in bearing steel’, ISIJ Int., 2005, 45, 1897–1902.
- Grabulov A., Petrov R. and Zandbergen H. W.: ‘EBSD investigation of the crack initiation and TEM/FIB analyses of the microstructural changes around the cracks formed under rolling contact fatigue (RCF)’, Proc. MS&T08 Conf., Materials Park, OH, USA, October 2008, TMS-AIME, Paper 7.
- Evans M.-H., Richardson A. D., Wang I. and Wood R. J. K.: ‘Tomographic serial sectioning investigation of butterfly and white etching crack (WEC) formation in wind turbine gearbox bearings’, Wear, 2013, 302, 1573–1582.
- Evans M.-H., Walker J. C., Ma C., Wang L. and Wood R. J. K.: ‘A FIB/TEM study of butterfly crack formation and white etching area (WEA) microstructural changes under rolling contact fatigue in 100Cr6 bearing steel’, Mater. Sci. Eng. A, 2013, A570, 127–134.
- Kang J., Williams C., Hosseinkhani B., diaz del Castillo P. E. J. R., Bagot P. A. and Moody M. P.: ‘Atom probe tomography characterization of a white etching area in a bearing steel’, Microsc. Microanal., 2013, 19, 1016–1017.