Abstract
Purpose
This study evaluated the influence of thickness increment on degree of conversion (DC), Knoop microhardness (KHN), and polymerization-shrinkage stress (PSS) by photoelasticity of three dental composites.
Methods
For DC and KHN, 45 samples were prepared and divided into nine groups (n=5), according to composite (microhybrid [Filtek Z250 - Z250], bulk-fill flowable [SureFil SDR Flow - SDR], and nanohybrid composite [N’Durance - NDU]) and increment thickness (1, 1.5, and 3 mm). PSS was measured by photoelastic analysis. Composites were placed into a photo-elastic model cavity and light-cured. DC and KHN data were subjected to two-way ANOVA and Bonferroni post hoc test. PSS results were qualitatively evaluated through Kruskal–Wallis test.
Results
SDR showed the highest DC values. At top and bottom surfaces, the highest KHN was obtained by Z250. Z250 showed higher PSS than SDR in 1.5 mm increments. NDU showed higher PSS than SDR in 3 mm increments.
Conclusion
The bulk-fill composite demonstrated better DC and similar KHN and PSS in deeper layers compared to conventional composites. Bulk-fill composites may perform as well as conventional nanohybrid and microhybrid composites.
Introduction
With improvements in adhesive technique and increasing esthetic demand, resin-based composites are indicated for anterior and posterior restorations.Citation1,Citation2 Although these materials present suitable mechanical and physical properties, some clinical aspects may determine the success or failure of dental composite restorations. One of these aspects relates to the thickness of the composite increment added to the cavity and thus the effective polymerization of all increments placed.Citation3 Appropriate light-curing is crucial for resin-based material to present satisfactory mechanical properties, which clinically provide greater longevity to restoration.Citation3,Citation4
Light-curing processes create polymerization-shrinkage stress at adhesive interfaces that may affect marginal integrity and clinical performance.Citation5,Citation6 To minimize this effect, layering has been the most indicated technique for placement of resin composites.Citation2 This technique aims to enable the complete light-curing of composite increments and reduce shrinkage volume, generating lower polymerization-shrinkage stress.Citation2,Citation7 Some studies suggest increments of 2 mm.Citation8,Citation9 However, depending on the cavity depth, increments <2 mm should be inserted in the cavity for best polymerization.Citation4
Nevertheless, the treatment of extensive posterior restorations with direct resin-based composites is time-consuming.Citation10 In order to save time and favor clinical procedures,Citation11 composites have been modified down the years to allow restoration procedures with increments >2 mm or even with a single increment.Citation10,Citation12 Bulk-fill composites emerged, allowing the restoration of deep cavities. Increments up to 4 mm thickness can be properly cured under the right irradiance conditions (exposure times of 40 seconds), with no need of further light exposure.Citation3 Studies suggest that changes in the organic matrix composition of these composites allow a greater degree of conversion in greater depths, reduced polymerization shrinkage, and low shrinkage stress.Citation10,Citation13–Citation15
In the past few years, shrinkage stress of bulk-fill composites has been evaluated in diverse ways. In 2014, El-Daman-houry and PlattCitation16 evaluated polymerization-shrinkage-stress kinetics of bulk-fill composites using tensometry. In 2015, Rosatto et alCitation15 used finite-element analysis to determine shrinkage-stress distributions during restoration with bulk-fill composites, and Fronza et alCitation13 assessed shrinkage stress using composites bonded to acrylic rods attached to a universal testing machine. In 2016, Al Sunbul et alCitation17 in turn measured shrinkage stress using the Bioman instrument. Few studies in literature, however, have used photoelastic analysis to measure shrinkage stress of bulk-fill composites.Citation18,Citation19 The great advantage of photoelastic methods is the ability to visualize all internal stresses, ie, to observe stress patterns throughout the whole sample, allowing the researcher to locate, photograph, and measure qualitatively and quantitatively the magnitude of stresses.Citation20,Citation21
In consideration of the importance of both reducing polymerization stress and maintaining physical properties of dental composites, the purpose of this study was to evaluate the influence of increment thickness on degree of conversion, Knoop microhardness, and polymerization-shrinkage stress by photoelasticity of three dental composites: a microhybrid (Filtek Z250 [Z250]), a bulk-fill flowable (SureFil SDR Flow [SDR]), and a nanohybrid composite (N’Durance [NDU]). The null hypotheses tested were: 1) the thickness of increments would not affect degree of conversion, microhardness, or polymerization-shrinkage stress of composites; and 2) there would not be significant differences in degree of conversion, microhardness, or polymerization-shrinkage stress among the composite-resin restorative materials.
Methods
Details of composites used in this experiment are presented in .
Table 1 Evaluated composites and respective manufacturer information
Degree-of-conversion and Knoop microhardness analyses
A total of 45 samples (n=5) were prepared for degree of conversion and Knoop microhardness analyses. Experimental groups were divided according to composite (Z250, SDR, and NDU) and increment thickness (1, 1.5, and 3 mm). Samples were obtained through single-increment composite placement into individualized cylindrical polytetrafluoroethylene matrices of 1, 1.5, and 3 mm height, with a center hole 2 mm in diameter. A polyester strip was placed on a polytetrafluoroethylene matrix, and above it a 500 g load was positioned for 5 seconds. Composites were light-cured by a polywave light-emitting-diode curing unit (Valo; Ultradent Products, South Jordan, UT, USA) in standard mode: 1,000 mW/cm2 for 20 seconds. The curing unit was positioned directly over the polyester strip. It is worth noting that before experiments began, the light optical power (mW) delivered by the curing unit was measured using a power meter (Ophir Optronics, Jerusalem, Israel). The tip diameter was measured with a digital caliper (Mitutoyo, Tokyo, Japan) and the tip area determined in square centimeters. Irradiance (mW/cm2) was calculated by dividing the optical power by tip area.
The degree of conversion of sample-bottom surfaces was evaluated by Fourier-transform infrared spectroscopy.Citation22 Absorption spectra of cured and uncured composite were recorded with a PerkinElmer Spectrum 100 spectrometer associated with a universal ATR sampling accessory (PerkinElmer, Waltham, MA, USA) with 16 scans at 4 cm−1 resolution using a baseline technique,Citation22 based on the bands 1,638 cm−1 (aliphatic C=C bonds) and 1,608 cm−1 (aromatic component group) as internal standard. The degree of conversion was calculated according to DC (%) = [1 – (R polymer/R monomer)] ×100, where R represents the ratio between aliphatic band absorption at 1,640 cm−1 and aromatic band absorption at 1,610 cm−1, respectively. For microhardness determination, the same samples were assessed with a microhardness tester (HMV 2000; Shimadzu, Kyoto, Japan). A Knoop diamond indenter was used to apply a static load of 10 g for 10 seconds on top and bottom surfaces. For each sample and surface, the averages of five indentations were used in statistical analysis.Citation23
Polymerization-shrinkage stress: photoelastic analysis
A model jaw maxillary second premolar (Manequins Odontológicos Marília, Marília, SP, Brazil) presenting a standard class I cavity (3 mm depth) was subjected to 45 dual impressions using polyvinyl siloxane in light and heavy consistencies (Express XT; 3M, St Paul, MN, USA). The impressions were poured with photoelastic resin (flexible GIV; Polipox, Cesário Lange, SP, Brazil), generating 45 replicas that were divided into nine groups (n=5), according to composite and restoration technique (applied in bulk, applied in two horizontal increments of 1.5 mm or applied in three horizontal increments of 1 mm): group 1, Z250 bulk; group 2, two Z250 increments; group 3, three Z250 increments; group 4, SDR bulk; group 5, two SDR increments; group 6, three SDR increments; group 7, NDU bulk; group 8, two NDU increments; group 9, three NDU increments.
Replicas were stored at 37°C for 24 hours to allow stress relief and complete polymerization of photoelastic resin. Before restoration, the photoelastic replicas were placed between polarizing filters to verify residual stress, and when detected they were stored at 37°C for a further 24 hours until total stress release ().
Internal cavity surfaces were sandblasted with 50 µm aluminum oxide particles (BioArt, São Carlos, SP, Brazil) to improve adhesion. An adhesive layer of Adper Single Bond 2 (3M) was applied on the surfaces following manufacturer’s instructions and light-cured for 20 seconds. Each composite was inserted into the cavity according to restoration techniques: a 3 mm increment was applied in bulk, and three horizontal increments of 1 mm or two horizontal increments of 1.5 mm. In both techniques, each increment was light-cured by the polywave light-emitting-diode curing unit in standard mode – 1,000 mW/cm2 for 20 seconds (20 J/cm2) – positioned directly over the occlusal surface. The light irradiance of the curing unit was checked again with a power meter to ensure constant light intensity.
Photoelastic analysis was performed immediately and at 24 hours after composite curing. Samples were examined with transmission polariscopy (PTH-A-01; Federal University of Uberlândia, Uberlândia, MG, Brazil), in which they were placed between two polarizing lenses over a white-light source, with 90° filter angulation. Constant isochromatic photoelastic fringes were obtained and images recorded with a 10.2-megapixel digital camera (D3000; Nikon, Tokyo, Japan). An isochromatic fringe-order pattern, which points out increasing stress – from 0 (black fringe) to 4 (pink–green transition fringe) – was used for scoring ().Citation24 Shrinkage stress was qualitatively analyzed, dividing the fringe images into seven areas (). Each area was scored 0–4 according to level of stress, comparing the obtained fringes to the fringe-order pattern.Citation25
Table 2 Isochromatic fringe-order pattern according to color change
Statistical analyses
Statistical analyses were performed using SPSS 21.0 (IBM, Armonk, NY, USA). Shapiro–Wilk and Kolmogorov– Smirnov tests were performed to check the results’ normality regarding the degree of conversion and microhardness analyses (P>0.05). Both results were subjected to two-way ANOVA and Bonferroni post hoc testing (α=0.05). Shrinkage-stress results were subjected to a nonparametric test (Mann–Whitney U) and pairwise comparison (α=0.05). Composites and number/thicknesses of increment were evaluated one by one for each area.
Results
Degree of conversion
Results of degree-of-conversion testing are shown in . Regardless of increment thickness, SDR presented the highest degree of conversion, while Z250 and NDU showed the lowest (P<0.0001). Z250 presented a higher degree of conversion in 1 mm increments than in 3 mm increments (P<0.004); however the degree of conversion in 1.5 mm increments was statically similar to that in 1 and 3 mm increments. For NDU, degree of conversion was lower in increments of 3 mm (P<0.025). SDR was the only composite that did not present statistically significant variation in degree of conversion between any increments.
Table 3 Mean (SD) degree of conversion (%) of composites in different increment thicknesses
Knoop microhardness
shows microhardness results of top and bottom surfaces. For composites on both top and bottom surfaces, Z250 presented the highest values for microhardness, while SDR and NDU presented the lowest ones (P<0.018). Top-surface microhardness of 1.5 mm increments was intermediate for NDU and lower for SDR (P<0.009). For all other thickness increments, SDR and NDU presented statistically similar values.
Table 4 Mean (SD) Knoop microhardness of top and bottom surfaces of composites in different increment thicknesses
For all composites, microhardness on top surfaces did not differ significantly between any increments. On the bottom surface, on the other hand, Z250 showed higher microhardness in 1 mm increments than 3 mm increments (P<0.027). The microhardness of 1.5 mm increments was statistically similar to that of 1 and 3 mm increments. Bottom-surface microhardness of SDR and NDU did not differ significantly between increments of 1, 1.5, and 3 mm. Z250 and NDU showed statistical differences between top- and bottom-surface microhardness of 1.5 and 3 mm increments. Top surfaces showed higher values for microhardness than bottom surfaces (P<0.042). SDR was the only composite that showed no difference between top and bottom surfaces for any increment thickness.
Polymerization-shrinkage stress
After qualitative analyses of areas, common shrinkage-stress behavior was observed between areas 1 and 7, 2 and 6, and 3 and 5. As such, the results of these areas were merged. There was no difference in shrinkage-stress rate between samples analyzed immediately and at 24 hours after light-curing either. presents polymerization-shrinkage-stress results for all areas and thickness of increments. Analysis of areas 1 and 7 revealed no statistical difference between shrinkage stress of composites, regardless of number/thickness of increments. SDR presented higher stress when handled with one increment of 3 mm and lower stress when handled with three increments of 1 mm (P=0.016). Stress generated with two increments of 1.5 mm was statistically similar to stress generated with one increment of 3 mm and three increments of 1 mm. Neither Z250 nor NDU shrinkage stresses differed statistically between number/thickness of increments.
Table 5 Fringe-order polymerization-shrinkage stress of composites areas of different thickness
In areas 2 and 6, all composites presented statistically similar values of shrinkage stress when handled with one increment of 3 mm. When handled with two increments of 1.5 mm, however, Z250 showed higher stress than SDR (P=0.008). NDU shrinkage stress did not differ from Z250 or SDR. When handled with three increments of 1 mm, NDU presented higher stress than SDR (P=0.008). Z250 shrinkage stress did not differ statistically from shrinkage stresses of NDU and SDR. Shrinkage stresses of Z250 and SDR did not differ statistically between number/thicknesses of increments. NDU presented higher stress when handled with three increments of 1 mm and lower stress when handled with one increment of 3 mm (P=0.008). Shrinkage stress of two increments of 1.5 mm of NDU was statistically similar to shrinkage stresses of one increment of 3 mm and three increments of 1 mm.
In areas 3 and 5, all composites presented statistical similar values of shrinkage stress when handled with one increment of 3 mm and two increments of 1.5 mm. When handled with three increments of 1 mm, NDU showed higher stress than SDR (P=0.016). Shrinkage stress of Z250 did not differ statistically from shrinkage stress of NDU or SDR. Shrinkage stresses of Z250 and SDR did not differ statistically between number/thickness of increments. NDU presented higher stress when handled with three increments of 1 mm and lower stress when handled with one increment of 3 mm (P=0.016). Shrinkage stress of two increments of 1.5 mm of NDU was statistically similar to shrinkage stress of one increment of 3 mm and three increments of 1 mm. In area 4, there was no statistical difference among shrinkage stress of composites, regardless of number/thicknesses of increments. Likewise, no composite presented statistical difference in shrinkage stress between number/thickness of increments ().
Figure 3 Representative images of polymerization-shrinkage stress obtained by each group.
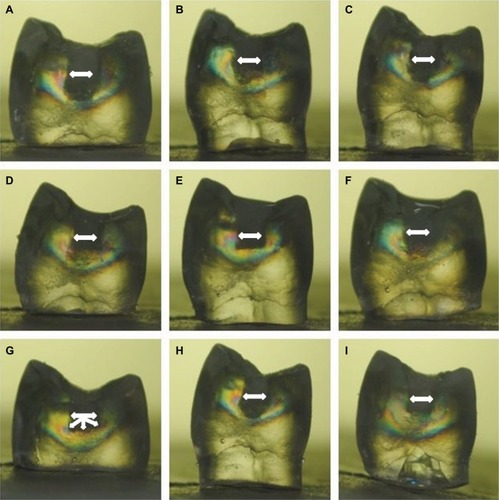
Discussion
This study aimed to evaluate the degree of conversion, Knoop microhardness, and polymerization-shrinkage stress by photoelasticity of three dental composites – a microhybrid (Z250), a bulk-fill flowable (SDR), and a nanohybrid composite (NDU) – submitted to different increment thickness. Both null hypotheses, that thickness of increment would not affect tested properties and that there would not be significant differences in tested properties among composites, were rejected. The highest values for degree of conversion were obtained by SDR, regardless of increment thickness, which is in accordance with previous studies.Citation26,Citation27 SDR presents a photoinitiator group, a modulator of polymerization reaction in urethane dimethacrylate (UDMA). The polymerization modulator reacts with camphorquinone, leading to formation of polymers with low elastic modulus and decreased polymerization stress,Citation10,Citation28,Citation29 thus enabling the placement of composite in increments of up to 4 mm,Citation30 as demonstrated in the results. The presence of amino groups (NH) in the urethane structure of UDMA is responsible for characteristic chain-transfer reactions, which provide an alternative way for further polymerization. These reactions result in increased mobility of radical sites in the network, and thus improve polymerization and conversion of monomer.Citation31 Indeed, interestingly, SDR was the only composite that did not present statistically significant variations in degree of conversion between any increments.
Despite the results obtained for degree of conversion, SDR presents low filler content (44% in volume) associated with prepolymerized particlesCitation30,Citation31 and development of more linear polymer chains, due to slower polymerization reaction.Citation32 This feature led the composite in general to obtain lower microhardness values than the other composites. Similar findings were obtained by Alshali et al, who remarked that Z250 presented higher values of microhardness than SDR.Citation33 It is worth noting, however, that SDR was the only composite that did not show a difference in microhardness values between top and bottom surfaces for any increment thickness, and showed microhardness on top and bottom surfaces similar to NDU in all increment thicknesses, except for 1.5 mm on the top surface. These findings demonstrate the effectiveness of this composite to be uniformly polymerized in increments up to 3 mm with no reduction of its physical properties.
In this context, the composites shades should be considered. SDR presents translucent universal color, while Z250 and NDU are of A2 shade. One may state that polymerization of resinous materials is correlated with light transmission and scattering.Citation3,Citation10,Citation34 Namely, considering material’s translucency, the more translucent the composite, the more effective the composite’s polymerization.Citation34,Citation35 It should be highlighted, however, that not only the shade of composite interferes in translucency property but also its thickness, type, amount, and filler-size content, as well as refraction indices between fillers and matrix resin.Citation35 Therefore, the results for SDR, though showing correlations with shade, are consequence of several factors. Surely, further studies including analysis of composites’ different colors as an influence in their properties must be considered.
The presence of a dimer acid-based monomer of high molecular weight in NDU may slow the reaction and favor the development of more linear polymers as well.Citation32,Citation36 Accordingly, even though the composite has high filler content (65% in volume), the development of linear polymers may have resulted in lower microhardness values than Z250 on both top and bottom surfaces. As elucidated by Ilie and Hickel, the relatively low cross-link density of dimer acid-based dimethacrylates favors the production of polymers with high flexibility but low modulus of elasticity.Citation37 Indeed, though the current literature provides few data concerning the micro-hardness of NDU,Citation38 studies have suggested that composites formulated with dimer acid-based monomers present low mechanical properties.Citation39,Citation40
Herein, one may observe that NDU showed a lower degree of conversion than SDR, with lowest values in 3 mm increments. Studies have revealed great degree of conversion values for NDU, especially at higher depths.Citation38–Citation40 Nevertheless, the presence of a high-molecular-weight monomer should be considered. As well stated by two studies, high-molecular-weight monomers in general present lower mobility during polymerization, thus reducing the final degree of conversion.Citation41,Citation42
According to the manufacturer, Z250 also has high-molecular-weight monomers (bisphenol A diglycidyl ether dimethacrylate, ethoxylated bisphenol A dimethacrylate, and urethane dimethacrylate) associated with high filler content (60% in volume). Although its filler content is slightly lower than that of NDU, the presence of zirconia filler may have influenced the microhardness results. Also, the development of polymers with higher cross-linking may increase composite elastic modulus and thus enhance surface microhardness. Nevertheless, the speed of reaction may increase cross-link density, but shorten the vitrification period of the composite, thereby reducing the degree of conversion.Citation36
Based on polymerization-shrinkage stress (), it is evident that the pattern of stress development in a class I cavity is variable. When bulk filling was performed, stress was similar among composites in all areas. When composites were applied in two horizontal increments of 1.5 mm, stress was similar among composites in five of seven analyzed areas. In areas 2 and 6, Z250 stress was higher than that of SDR. When composites were applied in three increments of 1 mm, on the other hand, stress was similar among composites in only three areas. In areas 2, 3, 5, and 6, NDU showed higher stress than SDR. Although shrinkage in a light-curing composite is assumed to be directed toward the light source,Citation43 the literature has not established a pattern of stress developed from this shrinkage. The results of this study suggest that the stress of each composite is developed in a different direction along the entire cavity, and may depend on composite composition, curing unit, restoration technique, and procedure accuracy.
Clearly, the polymerization efficiency of SDR is notable. The composite showed no statistical difference between shrinkage stress developed from any restoration technique in five analyzed areas. Furthermore, when composites were applied in horizontal increments, in two areas SDR presented lower shrinkage stress than Z250 in 1.5 mm increments. Compared to NDU, SDR presented in four areas lower shrinkage stress in 3 mm increments. However, lower shrinkage stress of this composite was expected, mainly when greater increments were placed into the cavity. The results showed that in general, SDR performed as well as the other composites when inserted into a cavity with high C factor. Equally important, in areas 1 and 7, shrinkage stress of SDR was higher when it was applied in bulk than when it was applied in three increments of 1 mm. An explanation could rely on the fact that all composites shrink in direction to the light source during polymerization.Citation43 Considering areas 1 and 7 were closest to the light source, shrinkage stress could have concentrated more at this point in the case of bulk filling. One may observe, however, that despite presenting higher stress when bulk-applied, in the same areas SDR shrinkage stress in this restoration technique did not differ from Z250 or NDU shrinkage stress.
The behavior of NDU regarding shrinkage stress must be addressed as well. The composite showed no statistical difference between shrinkage stress developed from any restoration technique in three analyzed areas. Nevertheless, in areas 2, 3, 5, and 6, NDU showed lower stress when applied in bulk than handled with three increments of 1 mm. Also, in this last case, the stress generated by NDU was statistically higher than the stress generated by the other composites. Apparently, shrinkage stress developed by NDU is somehow more homogeneous when the composite is applied in bulk. Evidence of this is given in , which shows that NDU was the only composite that presented the same numerical values of shrinkage stress in areas 2, 3, 5, and 6. NDU is considered a low-polymerization-shrinkage material, due to its high filler content and presence of dimer acid derived from dimethacrylate.Citation37,Citation44,Citation45 The presence of dimer acid-based monomer of high molecular weight with lower initial concentration of double bonds and relatively low viscosity provides less polymerization shrinkage.Citation37–Citation40 In addition, as already stated, its relatively low density of cross-linking can produce polymers with high flexibility and low modulus of elasticity.Citation37,Citation44
However, it should be highlighted that when composites were applied in bulk, all presented statistical similar values for shrinkage stress, irrespective of analyzed areas. This was expected from SDR, but not from conventional composites. Surprisingly, Z250 showed no statistical difference in shrinkage stress developed from any restoration technique, which might indicate that this composite presents homogeneous behavior in shrinkage-stress development. One may consider, however, that as Z250 and NDU are not bulk-fill composites, the bottom surfaces of largest increments are less polymerized in these materials, as demonstrated in the results for degree of conversion, ie, the reaction proceeds more slowly, generating a layer with low elastic modulus. This also may have relieved polymerization-shrinkage stress developed in the top surface, thus providing similar results among composites.Citation46 This condition, however, could clinically result in premature failure of the restoration, due to fracture or hypersensitivity.
Conclusion
Within the limitations imposed by this in vitro study, it can be concluded that the investigated bulk-fill composite (SDR) demonstrated a generally better degree of conversion and similar microhardness and incidence of polymerization-shrinkage stress in deeper layers when compared to conventional composites (Z250 and NDU). Findings suggest that bulk-fill composites may perform as well as conventional nanohybrid and microhybrid composites. However, although bulk-fill composites are indicated for single placement, considering the importance of reducing shrinkage stress, incremental filling technique might be beneficial, irrespective of composite type.
Acknowledgments
This work was supported by the State of São Paulo Research Foundation (FAPESP; 2014/02707-7). The authors are grateful to Dr Núbia Inocencya Pavesi Pini for her technical assistance.
Disclosure
The authors report no conflicts of interest in this work.
References
- RueggebergFAFrom vulcanite to vinyl, a history of resins in restorative dentistryJ Prosthet Dent200287436437912011846
- FerracaneJLResin composite—state of the artDent Mater2011271293821093034
- AlqahtaniMQMichaudPLSullivanBLabrieDAlshaafiMMPriceRBEffect of high irradiance on depth of cure of a conventional and a bulk fill resin-based compositeOper Dent201540666267226237638
- AguiarFHAndradeKRLeite LimaDAAmbrosanoGMLovadinoJRInfluence of light curing and sample thickness on microhardness of a composite resinClin Cosmet Investig Dent200912125
- CalheirosFCBragaRRKawanoYBallesterRYRelationship between contraction stress and degree of conversion in restorative compositesDent Mater2004201093994615501322
- FerracaneJLHiltonTJPolymerization stress—is it clinically meaningful?Dent Mater201632111026220776
- ParkJChangJFerracaneJLeeIBHow should composite be layered to reduce shrinkage stress: incremental or bulk filling?Dent Mater200824111501150518433857
- YapAUEffectiveness of polymerization in composite restoratives claiming bulk placement: impact of cavity depth and exposure timeOper Dent200025211312011203797
- EmamiNSöderholmKJHow light irradiance and curing time affect monomer conversion in light-cured resin compositesEur J Oral Sci2003111653654214632692
- FronzaBMAyresAPachecoRRRueggebergFADiasCGianniniMCharacterization of inorganic filler content, mechanical properties, and light transmission of bulk-fill resin compositesOper Dent201742444545528402731
- FrancisAVBraxtonADAhmadWTantbirojnDSimonJFVersluisACuspal flexure and extent of cure of a bulk-fill flowable base compositeOper Dent201540551552325741908
- FurnessATadrosMYLooneySWRueggebergFAEffect of bulk/incremental fill on internal gap formation of bulk-fill compositesJ Dent201442443944924480086
- FronzaBMRueggebergFABragaRRMonomer conversion, microhardness, internal marginal adaptation, and shrinkage stress of bulk-fill resin compositesDent Mater201531121542155126608118
- LeprinceJGPalinWMVanackerJSabbaghJDevauxJLeloupGPhysico-mechanical characteristics of commercially available bulk-fill compositesJ Dent2014428993100024874951
- RosattoCMBicalhoAAVeríssimoCMechanical properties, shrinkage stress, cuspal strain and fracture resistance of molars restored with bulk-fill composites and incremental filling techniqueJ Dent201543121519152826449641
- El-DamanhouryHPlattJPolymerization shrinkage stress kinetics and related properties of bulk-fill resin compositesOper Dent201439437438223865582
- Al SunbulHSilikasNWattsDCPolymerization shrinkage kinetics and shrinkage-stress in dental resin-compositesDent Mater2016328998100627240744
- RullmannISchattenbergAMarxMWillershausenBErnstCPPhotoelastic determination of polymerization shrinkage stress in low-shrinkage resin compositesSchweiz Monatsschr Zahnmed2012122429429922513711
- RullmanIPatynaMJanssenBWillershausenBErnstCPDetermination of polymerization shrinkage of different composites using a photoelastic methodAm J Dent2017301162229178709
- TurcioKHGoiatoMCGennari FilhoHdos SantosDMPhotoelastic analysis of stress distribution in oral rehabilitationJ Craniofac Surg200920247147419305247
- PesqueiraAAGoiatoMCFilhoHGUse of stress analysis methods to evaluate the biomechanics of oral rehabilitation with implantsJ Oral Implantol201440221722824779954
- RueggebergFAHashingerDTFairhurstCWCalibration of FTIR conversion analysis of contemporary dental resin compositesDent Mater1990642412492150824
- GiorgiMCAguiarFHSoaresLEMartinAALiporoniPCPaulilloLADoes an additional UV LED improve the degree of conversion and Knoop Hardness of light-shade composite resins?Eur J Dent20126439640123077419
- ÇehreliSÖzçırpıcıAAYılmazATilted orthodontic micro implants: a photoelastic stress analysisEur J Orthod201335556356721745828
- YamamotoMMiuraHOkadaDKomadaWMasuokaDPhotoelastic stress analysis of different post and core restoration methodsDent Mater J200928220421119496401
- YokeshCAHemalathaPMuthalaguMJustinMRComparative evaluation of the depth of cure and degree of conversion of two bulk fill flowable compositesJ Clin Diagn Res2017118ZC86ZC89
- JainLMehtaDMeenaNGuptaRInfluence of light energy density, composite type, composite thickness, and postcuring phase on degree of conversion of bulk-fill compositesContemp Clin Dent201895147S15229875550
- GiovannettiAGoracciCVichiAChieffiNPolimeniAFerrariMPost retentive ability of a new resin composite with low stress behaviourJ Dent201240432232822305777
- HernandesNMCatelanASoaresGPInfluence of flowable composite and restorative technique on microleakage of class II restorationsJ Investig Clin Dent201454283288
- JangJHParkSHHwangINPolymerization shrinkage and depth of cure of bulk-fill resin composites and highly filled flowable resinOper Dent201540217218025136904
- AlshaliRZSilikasNSatterthwaiteJDDegree of conversion of bulk-fill compared to conventional resin-composites at two time intervalsDent Mater2013299e213e21723845799
- SoaresGPAmbrosanoGMLimaDAEffect of light polymerization time, mode, and thermal and mechanical load cycling on microleakage in resin composite restorationsLasers Med Sci201429254555023314786
- AlshaliRZSalimNASatterthwaiteJDSilikasNPost-irradiation hardness development, chemical softening, and thermal stability of bulk-fill and conventional resin-compositesJ Dent201543220921825511301
- Faria-E-SilvaALFangerCNguyenLHowertonDPfeiferCSImpact of material shade and distance from light curing unit tip on the depth of polymerization of compositesBraz Dent J201728563263729215690
- KimEHJungKHSonSAHurBKwonYHParkJKEffect of resin thickness on the microhardness and optical properties of bulk-fill resin compositesRestor Dent Endod201540212813525984474
- OdianGStep polymerizationPrinciples of PolymerizationHobokenJohn Wiley & Sons, Inc200440185
- IlieNHickelRResin composite restorative materialsAust Dent J201156Suppl 1596621564116
- CzaschPIlieNIn vitro comparison of mechanical properties and degree of cure of a self-adhesive and four novel flowable compositesJ Adhes Dent201315322923623560255
- LuHTrujillo-LemonMGeJStansburyJWDental resins based on dimer acid dimethacrylates: a route to high conversion with low polymerization shrinkageCompend Contin Educ Dent201031Spec214
- FrauscherKEIlieNDepth of cure and mechanical properties of nanohybrid resin-based composites with novel and conventional matrix formulationClin Oral Investig201216514251434
- DewaeleMTruffier-BoutryDDevauxJLeloupGVolume contraction in photocured dental resins: the shrinkage-conversion relationship revisitedDent Mater200622435936516143380
- SideridouITserkiVPapanastasiouGEffect of chemical structure on degree of conversion in light-cured dimethacrylate-based dental resinsBiomaterials20022381819182911950052
- ChandrasekharVRudrapatiLBadamiVTummalaMIncremental techniques in direct composite restorationJ Conserv Dent201720638639129430088
- IlieNHickelRInvestigations on a methacrylate-based flowable composite based on the SDR technologyDent Mater201127434835521194743
- YamasakiLCde Vito MoraesAGBarrosMPolymerization development of “low-shrink” resin composites: reaction kinetics, polymerization stress and quality of networkDent Mater2013299e169e17923849746
- AguiarFHAjudarteKFLovadinoJREffect of light curing modes and filling techniques on microleakage of posterior resin composite restorationsOper Dent200227655756212413219