ABSTRACT
Eight types of coals of different rank were selected and their fundamental combustion characteristics were examined along with the conversion of volatile nitrogen (N) to nitrogen oxides (NOx)/fuel N to NOx. The activation energy, onset temperature, and burnout temperature were obtained from the differential thermogravimetry curve and Arrhenius plot, which were derived through thermogravimetric analysis. In addition, to derive the combustion of volatile N to NOx/fuel N to NOx, the coal sample, which was pretreated at various temperatures, was burned, and the results were compared with previously derived fundamental combustion characteristics. The authors' experimental results confirmed that coal rank was highly correlated with the combustion of volatile N to NOx/fuel N to NOx.
Low-rank coals are abundant in several regions throughout the world. However, despite their quantity and relatively low market price, these low-rank coals have not been used because of a lack of existing studies. Therefore, this paper presents the characteristics of NOx emission and fundamental combustion on coal combustion with coals having different rank to investigate the effect of coal rank on coal combustion.
INTRODUCTION
Pollutants such as carbon monoxide (CO), unburned hydro-carbon, soot, sulfur oxides, and nitrogen oxides (NOx) are emitted by burning coal. In particular, NOx react with hydrocarbon to generate ozone and photochemical oxides such as peroxyacetyl nitrate [CH3(CO)OONO] under the presence of sunlight. Moreover, NOx have become the main cause of acid rain based on conversion to nitric acid and nitrates.Citation1 Although NOx are produced during combustion by the oxidation of nitrogen within the fuel, they may also form from molecular nitrogen existing in the air, such as thermal NOx. Therefore, NOx possess characteristics different from those of sulfide, chloride, heavy metals, and others, which are the other pollutants commonly found in fuel.
In general, NOx refer to nitric oxide (NO), nitrogen dioxide (NO2), and nitrous oxide (N2O),Citation2 with NO2 and N2O being commonly ignored because they are generated in such small quantities.Citation3 NOx generated by the combustion of coal are classified into thermal NOx, caused by the thermal fixation of nitrogen in the air,Citation4 prompt NOx, produced by reaction with radicals (C and CH2) produced from the fuel,Citation5 and fuel NOx, produced from N components in the fuel,Citation6 depending on the origin of the nitrogen and mechanism of production. Among them, fuel NOx accounted for 75–95% of all NOx, whereas NOx oxidized from volatile N and char N constituted 50–70% and 20–30%, respectively. Therefore, reducing the emission of NOx during coal combustion is dependent on the regulation of fuel NOx rather than thermal NOx. The amount of fuel NOx can vary significantly, depending on coal reactivity, nitrogen content, coal composition, and the combustion conditions.Citation7 Accordingly, research has focused on methods to effectively control NOx using flue gas recirculation, burner out of service, over-fired air, reburning, fuel and air staging, low NOx burner, 2-step combustion, and others. However, the characteristics of fuel NOx generation depending on the type of coal (NOx generation caused by volatile N and char N) as opposed to the combustion method or conditions have not been extensively considered.
Therefore, eight types of coal were selected to examine the characteristics of fundamental combustion as well as NOx generation from the ratio of volatile N to NOx and char N to NOx.
EXPERIMENTAL PROCEDURES
Experimental Methods
A simplified diagram of the experimental device used in this research is shown in . Heating was generated at a constant velocity using a muffle furnace, and the device comprised a gas injection part, combustion part, and analyzing part. The whole gas supply pipe was manufactured from stainless steel, and the part into which coal is flowed during combustion was specially manufactured as a Y-type pipe combined with two-way and three-way valves. The combustion part was a special quartz pipe with an i.d. of 8 mm, an o.d. of 10 mm, and a height of 70 mm. Quartz wool was used to fix the coal. In addition, the quartz pipe was specially treated so that the wool would not be shoved toward the bottom upon increased pressure. A K-type thermocouple was mounted in contact with the top part of the quartz wool to measure the burning temperature, which was controlled by the same type of thermocouple as in the combustion furnace. The flow rate of injected O2/Ar from the cylinder was controlled using a mass flow controller (MKS Instruments, Colorado Springs, CO). To measure cocentration of emitted NOx, NO and NO2 were measured using a TESTO 360 analyzer (Testo AG, Lenzkirch, Germany), and H2O was completely removed before injection into the analyzer.
The combustion experiment used a specially manufactured experimental device previously reported by the authors' groupCitation8 instead of a drop tube furnaceCitation9 to perform B1 combustion (batch combustion method 1). B1 combustion raised the temperature of the combustion furnace in a constant rate of 10 °C/min within a combustion furnace filled with coal. When the coal was burning, the combustion gas was measured. In addition, to distinguish the conversion of char N to NOx from that of volatile N to NOx, the coal sample was burned again after drying at various temperatures using argon gas.
Coal Characterizations
Eight types of coals of various ranks were selected for use as samples. In addition, elementary analysis of the coals was performed using a TruSpec (LECO Corporation, St. Joseph, MI) and SC-432DR (LECO Corporation), proximate analysis with an automatic proximate analyzer (LECO Corporation), and ash analysis using an inductively coupled plasma optical emission spectrometer (PerkinElmer Life and Analytical Sciences, Waltham, MA). As shown in , anthracite was ∼10% volatile matter (VM), whereas bituminous coal and pitch coal and lignite were ∼30 and 30 to 50%, respectively. Anthracite had the highest content of ash (greater than 40%), whereas bituminous coal had ∼15% and pitch coal-lignite was in the range of 5 to 20%. The coal used in each combustion experiment was sifted using 40- to 50-sized mesh to obtain uniform combustion.
Table 1. Physical analysis for various coals
Activation Energy and Differential Thermogravimetry
The analysis of activation energy was complex because the reaction velocity at which coals are burned varies, depending on the temperature of the combustion reaction. Therefore, the activation energy was analyzed by following the method suggested by Serageldin and Pan.Citation10
The reaction velocity equation of the coal combustion reaction, such as response of a could be represented as
where A is the frequency factor, E is activation energy, and T is temperature.
The linear heating rate can be represented as
If Equationeqs 1, Equation2, and Equation3 are integrated, they become
The right-hand side of Equationeq 4 is not an exact integral. Thus, if u = E/RT is substituted instead and the following relation is used,
If a log is taken, it becomes Equationeq 6 for n ≠ 1.
If n=1, it becomes Equationeq 7:
is almost constant in the temperature range at which the reaction occurs. If
1/T of Equationeq 7 are plotted, the activation energy can be calculated from the slope, which is represented by −E/RT. Thermogravimetric analysis (TGA) of coal is very complex because of the presence of various components. Therefore, the activation energy was computed by the method suggested by Serageldin and Pan.Citation10 A linear interval appeared in the Arrhenius plot performed for TGA. If the activation energy at each interval is E, the total activation energy can be expressed as
where Mn is the weight ratio of the coal sample in the temperature range of each interval.
On the other hand, differential thermogravimetry (DTG), which is a concept on the decreasing rate of weight, depending on the temperature. In other words, it is to plot, , where M is the weight of the coal sample and T is the time for which the unit is percent per minute.
RESULTS AND DISCUSSION
Fundamental Combustion Characteristics
High temperature TGA is widely used for the analysis of coal combustion. Cumming and McLaughlinCitation11 reported that thermal analysis could be used to select the type of coal, whereas Serageldin and PanCitation10 explained the methods for deriving the activation energy from the results of the TGA of coal. As shown in , TGA was also performed to determine the fundamental combustion characteristics of the eight types of coal. In addition, a DTG curve was derived from the result of TGA to clearly distinguish between the starting and ending burning temperature. As shown in , the Arrhenius plot of the TGA results was constructed to determine the activation energy. Ng et al.Citation12 analyzed pore volume depending on coal type and were able to explain the correlation between morphological characteristics and rank. Therefore, to determine the effects on the morphological and fundamental combustion characteristics of coal, the results of the Brunnauer-Emmett-Toller (BET) and Barett-Joyner-Halenda (BJH) analyses as shown in were arranged into . Anthracite and bituminous coal of high rank generally possess high activation energy, whereas pitch coal and lignite have low activation energy. This observation highlights a direct correlation between the starting and ending burning temperatures. It was confirmed that the starting and ending burning temperatures were in the low temperature range for pitch coal and lignite and were relatively high for bituminous coal and anthracite. Therefore, the starting and ending burning temperatures decreased as the amount of VM in the coal was increased. Furthermore, Ng et al.Citation12 reported that the specific surface area of the BET analysis did not correlate with coal rank, whereas pore volume showed close correlation. As shown in , the specific surface areas shared similarity based on the different pore size and distribution of the coals. However, the average pore size of coal was directly related with rank because it is based on the formation mechanism.
Table 2. Combustion characteristics of each coal using TGA and morphological analysis of coals
NOx Emission Characteristics of Coals Using B1 Combustion
The B1 combustion method was used to examine NOx generation characteristics from fuel N of each coal type. According to the authors' previous research, B1 combustion produced data on concentration behavior depending on the burning time and temperature of target coals. The mass of total generated NOx was then determined. shows the NOx generated by the B1 combustion of coal. Because the theoretical air content of coal was not considered, NOx emitted to burn coals using various feeding rate of gases (0.5–1.5 L/min) is represented. The results show that the same amount of NOx was emitted as the amount of N content in the coals. The amount of emitted NOx was similar, beginning at 1 L/min, depending on the injected gases. With an increase in the amount of fed gases, the amount of NOx generation was increased at below 1 L/min. However, the amount of generated NOx converged toward a certain amount above 1 L/min. This trend appeared for every type of coal used in the experiment and could be explained by the fact that the amount of fuel N dissociated at the corresponding temperature was limited.
Figure 4. Outlet NO concentration on coal combustion according to feeding flows used B1 combustion (coal: 0.2 g).
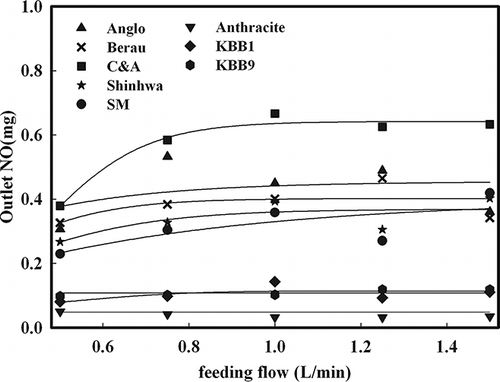
To further investigate the suppression of NOx generation below 1 L/min of injected gas, the intensity of N2 generated under the same combustion conditions was measured using quadrupole mass (Pfeiffer Vacuum GmbH, Asslar, Germany) and is represented in . It was confirmed that N2 generation below 1 L/min of injected gas was relatively larger compared with conditions above 1 L/min. The authors previously reportedCitation8 that generated NOx was decreased by the reduction of NO to N2 by hydrocarbon intermediate generation material existing in the fuel-rich zone (λ < 1)Citation13; in other words, the reaction progressed along path 1 in . Likewise, the results of this research show that NOx generation was suppressed when gases were injected at a rate below 1 L/min because of the conversion of fuel N to N2 rather than NO. Therefore, N2 generation by path 1 inhibits the conversion of fuel N to NO.
Volatile N and Char N to NOx
The previous section considered the characteristics of NOx generation for all eight types of coal. In this section, NOx generated from volatile N was separated from that generated from char N by examining the ratio of NOx generated from volatile N among fuel NOx of coals according to it. is the result, which shows measured NOx generated to burn by B1 combustion, cooling to room temperature again after drying of each coal sample to increase to the desired temperature by Ar, an inert gas (after production as char at the desired temperature). A certain amount of NOx was generated by each coal at a dry temperature of 700 °C, because only NOx generated from char N was emitted after removal of volatile N by Ar. Therefore, NOx emission by coal without dry processing is derived from volatile N. Each type of coal converted volatile N to NOx/total fuel N to NOx, as shown in . The reason NOx emission was not compared with the amount of NOx generated from volatile N but instead was represented as the ratio of volatile N to NOx and total fuel N to NOx is that a problem could arise if it is simply compared with the amount because of different N contents, depending on target coal. As shown in , volatile N to NOx/total fuel N to NOx was highly correlated with VM/(VM + FC), which indicates VM content rather than the H2O content of coal. The plot in was constructed to clarify this concept. As a result, volatile N to NOx/total fuel N to NOx was directly related to the coal rank.
Table 3. Volatile matter contents and the NO emission characteristics of various coals
CONCLUSION
Eight types of coal of different rank were selected to determine the fundamental combustion characteristics of the conversion of volatile N and char N to NOx.
1. | On the basis of the Arrhenius plot and DTG curve of the TGA, the activation energy and starting and ending burning temperatures were derived. Bituminous coal and anthracite of high rank showed relatively high activation energies as well as high starting and ending burning temperatures, whereas pitch coal and lignite showed low activation energy as well as low starting and ending burning temperatures. | ||||
2. | When subjected to B1 combustion, emitted NOx was closely related to the N content of coal. In addition, the effect of injected gases showed that NOx emission was suppressed because of the formation of N2 in a reduced atmosphere under air-deficient conditions. Therefore, it was confirmed that the amount of generated NOx converged toward a certain level under air-rich conditions. | ||||
3. | The NO conversion ratio of volatile N to fuel N for the coal samples showed similar characteristics, but the conversion of fuel N to NOx converted as the dry temperature was increased. In other words, the conversion of char N to NOx was identical for every type of coal. In addition, the volatile N/fuel N ratio showed a linear relationship with coal rank as opposed to H2O content. |
REFERENCES
- Muzio , L.J. and Quartucy , G.C. 1997 . Implementing NOx Control - Research to Application . Prog. Energy Combust. Sci. , 23 : 233 – 266 .
- Biener , J. , Baumer , M. , Wang , J. and Madix , R.J. 2000 . Electronic Structure and Growth of Vanadium on TiO2(110) . Surf. Sci. , 450 : 12 – 26 .
- Vander Lans , R.P. , Glarborg , P. and Dam-Johansen , K. 1997 . Influence of Process Parameters on Nitrogen Oxide Formation in Pulverized Coal Burners . Prog. Energy Combust. Sci. , 23 : 349 – 377 .
- Zel'dovich , Y.B. 1946 . The Oxidation of Nitrogen in Combustion and Explosions . Acta Phys. Chim. URSS , 21 : 577 – 625 .
- Fenimore , C.P. 1971 . “ Formation of Nitric Oxide in Premixed Hydrocarbon Flames ” . In Proceedings of the 13th Symposium on Combustion , 373 Pittsburgh , PA : The Combustion Institute .
- Fenimore , C.P. and Jones , G.W. 1957 . Nitrio Oxide Decomposition at 2200–2400°K . J. Phys. Chem. , 61 : 654 – 657 .
- Jung , K.S. , Keener , T.C. and Khang , S.J. 2001 . Compositional Factors Affecting NOx Emissions from Ohio Coals . Fuel Process. Technol. , 74 : 49 – 61 .
- Kim , S.S. , Choi , H.J. , Lee , H.D. , Kim , J.K. and Hong , S.C. 2009 . A Study on Fuel NOx Emission Characteristics in Coal Combustion . J. Korean Ind. Eng. Chem. , 20 : 675 – 680 .
- Han , W. , Park , C.S. , Choi , S.I. , Lee , I.H. and Yang , H.S. 1999 . Studies on Coal Combustion Characteristics and NOx Emission and Reduction in the Drop Tube Furnace . Korean Soc. Combust. , 4 : 85 – 95 .
- Serageldin , M.A. and Pan , W.P. 1983 . Coal: Kinetic Analysis of Thermogravimetric Data . Thermochim. Acta , 71 : 1 – 14 .
- Cumming , J.W. and McLaughlin , J. 1982 . The Thermogravimetric Behaviour of Coal . Thermochim. Acta , 57 : 253 – 272 .
- Ng , S.H. , Fung , D.P.C. and Kim , S.D. 1984 . Some Physical Properties of Canadian Coals and Their Effects on Coal Reactivity . Fuel , 63 : 1564 – 1569 .
- Jang , G.H. , Chang , I.G. , Sun , C.Y. , Chon , M.H. and Yang , G.M. 1999 . “ Effect of Air Staging on NOx Reduction in Pulverized Coal Combustion ” . In Proceedings of the 19th KOSKO Symposium , 149 Seoul , , Republic of Korea : KOSKO .