ABSTRACT
This study addresses the oxidation of ammonia (NH3) at temperatures between 423 and 673 K by selective catalytic oxidation (SCO) over a copper-based, rare earth composite metal material that was prepared by coprecipitating copper nitrate, lanthanum nitrate, and cerium nitrate at various molar ratios. The catalysts were characterized using Brunner, Emmett, and Teller spectroscopy, Fourier-transform infrared spectroscopy, X-ray diffraction, ultraviolet–visible spectroscopy, cyclic voltammetric spectroscopy, and scanning electron microscopy. At a temperature of 673 K and an oxygen content of 4%, approximately 99.5% of the NH3 was reduced by catalytic oxidation over the 6:1:3 copper-lanthanum-cerium (molar ratio) catalyst. Nitrogen (N2) was the main product of this NH3-SCO process. Results from the activity and selectivity tests revealed that the optimal catalyst for catalytic performance had the highest possible cerium content and specific surface area (43 m2/g).
NH3 is an important chemical product of diverse industrial processes, including ammonium nitrate production, livestock feedlots, urea manufacturing, N2 fertilizer production, fossil fuel combustion, petroleum refining, and the refrigeration industry. This work addresses the oxidation of NH3 by copper-based, rare earth composite metal materials with various relevant parameters. The effectiveness of this catalyst for NH3 removal by SCO is investigated.
INTRODUCTION
Ammonia (NH3) is a toxic, highly reactive inorganic gas with a pungent odor under ambient conditions that has been reported to be potentially harmful to public health and the environment.Citation1–4 Typical biological and physicochemical treatments, which use biofilters, stripping, scrubbing with water, postcombustion controls, and electrochemical oxidation methods, all induce a phase transformation and may yield contaminated sludge or adsorbent that requires further treatment. The maintenance and operating costs associated with these physical and chemical methods are high. Accordingly, it is important to improve methods for the removal and control of NH3 from air and waste streams, especially as the laws and regulations regarding environmentally safe discharges are becoming increasingly strict.
Recently, catalytic oxidation methods have been developed to enhance the effectiveness of advanced oxidation process technologies. Dedicated catalysts potentially shorten the reaction time for oxidation and allow it to proceed under milder operating conditions. One scheme for mitigating NH3 pollution is the selective catalytic oxidation (SCO) of NH3 to produce nitrogen (N2) and water.Citation5,Citation6 The catalytic oxidation of NH3 has been reported to proceed as follows:
The SCO-NH3 process should be selective for N2 (Equationeq 1) and should prevent further N2 oxidation (Equationeqs 2 and Equation3). Earlier work on catalytic NH3 decomposition was reviewed by Il'chenko,Citation7–9 who focused on the reaction mechanism of NH3 oxidation and compared catalytic activities. Several catalysts containing palladium (Pd), nickel (Ni), molybdenum (Mo), and copper (Cu) (with ZSM-5, aluminum oxide [Al2O3], and other oxides as supports) have previously been used to oxidize gaseous NH3 Citation10–15. For instance, Li et al.Citation10 studied the catalytic oxidation of NH3 in a wet stream by a Pd-ZSM-5 catalyst between 473 and 623 K. Amblard et al.Citation11 demonstrated excellent selective conversion of NH3 to N2 (>90%) using a γ-Al2O3-supported Ni catalyst in an SCO process. Moreover, Wang et al.Citation12 developed Ni-based catalysts for oxidizing the fuel gas generated by gasifying biomass and found that fresh Ni-based catalysts were more active for NH3 decomposition at lower temperatures and that the partial pressure of hydrogen in the flue gas determined the extent of NH3 oxidation. For a fixed-bed microreactor operating between 873 and 1023 K with a gas hourly space velocity (GHSV) of 1800–3600 hr−1, Liang et al.Citation13 reported 98.7 and 99.8% NH3 conversion on nitrided MoNx/α-Al2O3 and Ni-MoNy/α-Al2O3 catalysts, respectively. Schmidt-SzałowskiCitation14 developed a hypothetical model for the effects of these catalysts, describing their activity and selectivity in oxidizing NH3. Recently, HungCitation15 described the catalytic oxidation of NH3 in a gaseous stream using a nanoscale Cu-cerium (Ce) bimetallic catalyst at temperatures between 423 and 673 K and at a GHSV of 92,000 hr−1. Bimetallic nanoscale structures exhibit the synergistic effects of maximum NH3 reduction activity and maximum N2 selectivity.
In previous work,Citation16 it was found that Cu, lanthanum (La), and Ce metals exhibited remarkable activities and capacities to elucidate the reduction characteristics of NH3 conversion in a wet oxidation system. In addition, as has been previously reported,Citation17 the interactions between Cu, lanthanum oxide, and the Ce are complex because synergistic effects may enhance catalytic characteristics. However, few studies have investigated the use of the Cu-based rare earth composite metal materials (Cu-La-Ce ternary catalysts) for the catalytic gaseous-phase oxidation of NH3. To facilitate the application of the catalytic oxidation technique, the activity of Cu-La-Ce ternary catalysts for NH3 oxidation and decomposition via SCO was investigated under various molar ratios and reaction parameters. Finally, the obtained catalysts were characterized using Brunner, Emmett, and Teller spectroscopy (BET), Fourier-transform infrared spectroscopy (FTIR), X-ray diffraction (XRD), ultraviolet–visible spectroscopy (UV-Vis), cyclic volta-mmetric spectroscopy (CV), and scanning electron microscopy (SEM).
MATERIALS AND METHODS
Preparation of Cu-Based Rare Earth Composite Metal Materials
Cu-based, rare earth composite metal materials (Cu-La-Ce ternary catalysts) were prepared by coprecipitation with copper(II) nitrate (GR grade, Merck), lanthanum(II) nitrate (GR grade, Merck), and cerium(III) nitrate (GR grade, Merck) in four molar ratios: 6:1:3, 6:2:2, 7:1:2, and 7:2:1. These compounds were then calcined in an airstream at 773 K for 4 hr and the resulting powder was made into tablets using acetic acid as a binder. The tablets were reheated to 573 K to burn off the binder from the Cu-La-Ce composite. The tablets were then crushed and sieved into various particle sizes ranging from 0.15 to 0.25 mm for later use. A detailed catalyst preparation method has been described elsewhere.Citation18
Characterization of the Solid Phase
The specific surface areas of the composite catalysts were determined by the physical adsorption of N2 at 77 K using a BET surface area analyzer (ASAP 2000, Micro-meritics). Diffuse reflectance FTIR spectra of the phase species on the catalyst were measured at room temperature using a Bruker Vector 22 FTIR spectrometer equipped with a diffuse reflectance attachment with a resolution of 4 cm−1. UV-Vis absorption spectra of the solid sample were obtained using a spectrophotometer (MCPD-3000, Otsuka Electronics). The reflectance was measured in relation to a barium sulfate (BaSO4) standard. X-ray diffractograms were generated using a Diano-8536 diffractometer with a CuKα radiation source. During analysis, the sample was scanned from 20° to 80° at a rate of 0.4°/min. CV experiments were conducted at room temperature with an electrochemical analyzer (CHI 6081d), using a three-electrode electrochemical cell to investigate the redox state of the powder samples. The working electrode was a glassy carbon electrode, and samples were scanned at a rate of 10 mV/sec as the potential cycled between −0.2 and 1.2 V. The counter electrode was a platinum wire, and a saturated hydrogen electrode was used as the reference electrode. Sulfuric acid (H2SO4; 0.5 M) was used as the electrolyte solution. SEM (JEOL, JSM-6400) was used to elucidate the morphology of the catalysts and to collect information on the catalyst surfaces.
Reaction System
Experiments were conducted in a tubular fixed-bed flow quartz reactor. The typical reactant gas (GHSV = 92,000 hr−1) was composed of helium (He) with 1000 parts per million (ppm) NH3 and 4% oxygen (O2); it flowed into the inlet of the reactor. A mass flow regulator was used to independently control the flows of NH3 and O2. Highly purified He was used as a carrier gas at a flow rate ranging from 8 to 13 L/min and was controlled using a mass flow meter (830 Series Side-Trak, Sierra). The mass of each catalyst was 1 g, and the empty-bed volume was approximately 1.2 cm3. Five grams of hydrophilic inert γ-Al2O3 spheres were used to increase the interfacial area between the solid and the gas phases and to increase the mass transfer of NH3 from the gaseous streams. This approach resembled that of Hung,Citation15 who also conducted experiments on the catalytic oxidation of NH3. A reaction tube with a length of 300 mm and an inner diameter of 28 mm was placed inside of a split-tube furnace. The tube containing the catalyst was placed in the same furnace. Temperature was measured using two type-K thermocouples (KT-110, Kirter), each with a diameter of 0.5 mm, located in front of and behind the catalytic bed. The thermocouples were also connected to a proportional-integral-derivative controller (FP21, Shimaaen) to maintain the temperature in the tube within ±0.5%.
Analyses
Before and after the reaction, the samples were automatically injected through a sampling valve into a gas chromatograph (Shimadzu GC-14A) equipped with a thermal conductivity detector. A stainless steel column (Porapak Q 80/100 mesh) was used to isothermally (373 K) separate and determine the concentrations of nitrous oxide (N2O). The peak areas were calculated electronically using a data integrator (CR-6A, Shimadzu). Dilute H2SO4 was used to scrub the residual NH3 from the gas and the amount present was measured using a Merck kit (Merck, Spectroquant Pharo 300). The concentrations of nitric oxide (NO), nitrogen dioxide (NO2), and O2 in the gas samples were continuously monitored during the catalytic reaction at a consistent location using a portable flue gas analyzer (IMR-3000). Each temperature was maintained for 90 min to allow the system to reach steady state, which typically occurred after 20 min. Data were collected after the SCO reaction reached steady state. Most experiments were repeated to ensure reproducibility, and similar results were always obtained.
RESULTS AND DISCUSSION
Catalysts with various Cu, La, and Ce contents were prepared, characterized, and tested for their effectiveness for SCO. plots the catalytic activities measured for the Cu-La-Ce samples of interest as a function of temperature. NH3 was converted even at 423 K. The extent of NH3 conversion over all of the composite catalysts increased with temperature: At 673 K, conversion reached 99.5, 97.7, 95.6, and 94.3% over 6:1:3, 6:2:2, 7:1:2 and 7:2:1 (Cu-La-Ce) ternary catalysts, respectively. Notably, the optimal catalyst exhibited the highest possible molar ratio of Ce. However, shows that the 6:1:3 catalyst did not perform as well as the 6:2:2 and 7:2:1 catalysts in the temperature range 573–623 K.
Figure 1. Dependence of NH3 content on the temperature of the Cu-La-Ce ternary catalyst. Test conditions: 1000 ppm NH3, 4% O2, and GHSV = 92,000 hr−1.
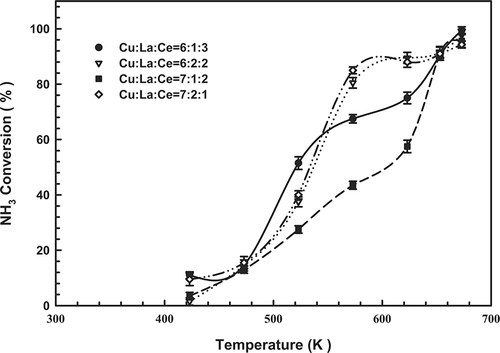
The adsorptive and catalytic behavior of a catalyst is strongly influenced by the extent and texture of its exterior surface. summarizes the properties of the test catalysts as determined by BET analysis, including specific surface area. For a molar ratio of 6:1:3, the specific surface area was 43 m2/g. This surface area decreased slightly to 27 m2/g for a molar ratio of 7:2:1. This test showed that the catalysts associated with higher loads caused metal sintering, which may have reduced catalytic activity. Clearly, the molar ratios of metals play an important role in activating the generated surface, and an increase in surface area may be the main factor that promotes catalytic activity.
shows a comparison of the FTIR spectra at various molar ratios of fresh catalyst and also confirms the presence of a copper(II) oxide (CuO)-like phase and a cerium(IV) oxide (CeO2) phase on the surface of the Cu-La-Ce ternary catalyst. The CuO-like phase on the catalyst surface is associated with a peak at approximately 1384 cm−1 Citation19,Citation20; peaks associated with the CeO2 phase and La3+ cations that are adsorbed onto CuO clusters are seen at 1524 and 1635 cm−1, respectively.Citation21 In previous reports,Citation22 CuO and CeO2 were thought to exhibit strong synergistic effects when prepared as a composite CuO/CeO2 binary catalyst. Therefore, the catalytic activity of the CuO-lanthanum(III) oxide (La2O3)-CeO2 ternary oxide catalyst system for oxidizing NH3 could be explained by the reversible redox behavior of CuO-La2O3-CeO2 couples, which promote the functional reaction mechanism.Citation23
Figure 3. FTIR patterns for the various catalysts tested: molar ratios of (a) 6:1:3, (b) 6:2:2, (c) 7:1:2, and (d) 7:2:1.
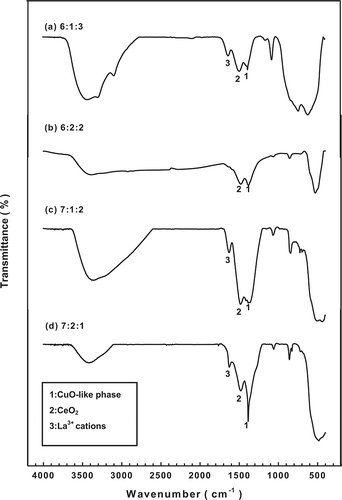
shows the XRD patterns for the various fresh Cu-La-Ce ternary catalysts, which verify the presence of the CuO, La2O3, and CeO2 phases. The dominant CuO diffraction peaks appear near 2θ = 35.4926° and 38.7593°. This result established that CuO is the most active phaseCitation14 and is consistent with data from Hung et al.Citation17 and Ning et al.Citation24 As reported previously, La2O3 can be converted to lanthanum hydroxide (La(OH)3). However, under the oxidation conditions present over the Cu-La-Ce catalyst, the oxidation state of Ce can vary between Ce3+ and Ce4+. An earlier investigation revealed that CeO2 is the most active phase in the catalytic reaction because it is a good promoter of O2 storage capacity, and some noble metals have been used as major catalysts in this process.Citation25 The CeO2 in a Cu catalyst may be assumed to promote the formation of the active phase of CuO during NH3 oxidation. Consistent with these results, X-ray powder diffraction confirmed the presence of CuO, La2O3, and CeO2 active sites on the Cu-La-Ce ternary catalyst. These XRD peak intensities were strongest for the 6:1:3 Cu-La-Ce ternary catalyst.
Figure 4. XRD patterns for the various catalysts tested: molar ratios of (a) 6:1:3, (b) 6:2:2, (c) 7:1:2, and (d) 7:2:1.
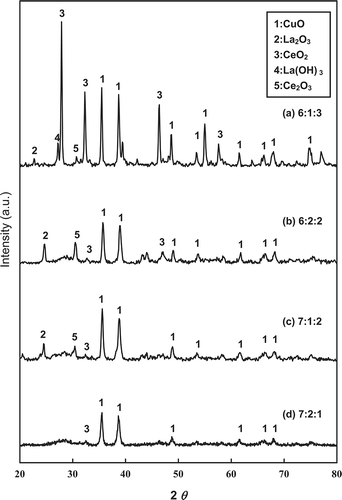
UV-Vis studies were conducted to gain further information on the state of Cu, La, and Ce species in the fresh catalysts; spectra are shown in . Generally, bands were observed in the ranges of 300–350 nm and 700–900 nm and were attributed to the Cu2+-O2− electronic transition species and the d-d transitions of Cu2+ in an octahedral environment with Oh symmetry, respectively. The formation of Cu species is in agreement with Carvalho et al.,Citation26 who described the reductive effect of NH3 on Cu-La-Ce ternary metal catalysts. As in the XRD spectra, the 6:1:3 Cu-La-Ce ternary catalyst in the UV-Vis spectrum produced the strongest peaks of the tested catalysts.
To characterize the redox state of the catalysts, redox profiles were generated by CV. shows the CV profiles of the fresh and aged Cu-La-Ce ternary catalysts. The CV plots demonstrate that the fresh catalysts have greater reversible redox capacities than their aged version, as shown by reduction peaks at 0.2 and 0.18 V. This reversible redox ability may explain the substantial activity of the catalysts. Along these lines, an earlier investigation demonstrated that CeO2 is the most active phase in a catalytic reaction because it is a strong promoter of O2 storage. When it is present in a Cu catalyst, it can be assumed to promote the formation of the active phase of CuO during NH3 oxidation. In the work presented here, the catalytic activity of the Cu-La-Ce ternary catalyst system in NH3 oxidization is explained by the storage and release of O2 by O2 buffers. The Ce(III)-La(III)-Ce (IV) redox couples lead to the formation of O2 vacancies and enhance O2 mobility, thereby promoting the bifunctional mechanism of the catalyst.Citation27
Figure 6. Cyclic voltammograms of the tested catalysts in a 0.5 M H2SO4 electrolyte solution, recorded at a scan rate of 10 mV/sec.
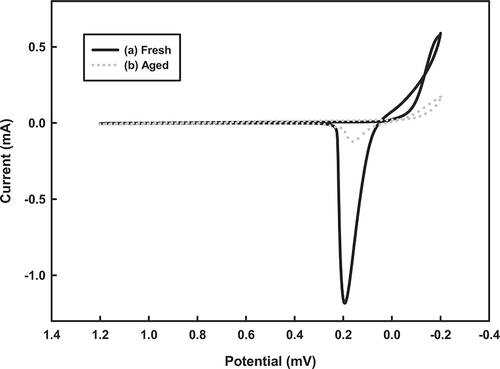
The overall selectivity of N2 production (defined as S N2 = 2[N2]/(2[N2] + [NO] + 2[N2O])) varied from 10 to 70%, NO production (S NO = [NO]/(2[N2] + [NO] + 2[N2O])) varied from 0 to 20%, and NH3 conversion (initial concentration 1000 ppm) varied from 11 to 99.5% (). N2 gas is formed primarily by the dissociation of NO, which is produced by the oxidation of adsorbed NH3 Citation28. Accordingly, these results suggest that NH3 and O2 may be adsorbed onto specific sites on the 6:1:3 catalyst, promoting the rapid conversion of NH3 to N2 and water. Consequently, N2 was the dominant gas detected in the resultant stream, along with a small amount of NO. This result is similar to that obtained by Curtin et al.Citation29
Figure 7. Relationship between NH3 conversion, N2 yield, and NO yield at various temperatures using the 6:1:3 Cu-La-Ce catalyst. Test conditions: 1000 ppm NH3, 4% O2, 423–673 K, and GHSV = 92,000 hr−1.
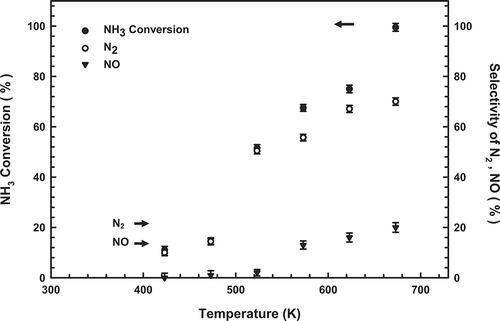
SEM was used to elucidate the surface morphological changes of the 6:1:3 Cu-La-Ce ternary catalyst; the surface structures of the fresh and aged catalysts are shown in . The surface of the catalyst was more aggregated and crystalline in than in , indicating that the disaggregated and dispersed phases in were formed when the surface of the catalyst was aged or when poisoning occurred because of plugging, which implies that porosity changed. These crystal phases may be responsible for the high activity of the catalysts. These results also confirm that catalyst dispersion phenomena increase the efficiency of NH3 removal.
CONCLUSIONS
This study demonstrates an environmentally friendly technology for SCO of NH3 by Cu-based rare earth composite metal materials. Cu-La-Ce ternary catalysts were prepared by coprecipitation in various molar ratios and were found to promote the oxidation of NH3. N2 was the main product of NH3-SCO over the 6:1:3 Cu-La-Ce catalyst. The overall byproduct selectivity of NO production varied from 0 to 20%, N2 production ranged from 10 to 70%, and NH3 conversion ranged from 11 to 99.5%. The synthesized 6:1:3 Cu-La-Ce catalyst exhibited the highest specific surface area (43 m2/g), which is associated with higher catalytic performances. Further studies on the reaction kinetics will be conducted in the future. This work shows that the NH3-SCO process has the potential to treat streams highly contaminated with NH3 and could improve the ability of industrial plants to achieve regulatory discharge standards.
ACKNOWLEDGMENTS
The author thanks the National Science Council of the Republic of China, Taiwan, for partial financial support of this research under contract no. NSC 98-2221-E-132-003-MY3.
REFERENCES
- Ou , H.H. , Liao , C.H. , Liou , Y.H. , Hong , J.H. and Lo , S.L. 2008 . Photocatalytic Oxidation of Ammonia over Microwave-Induced Titanate Nanotubes . Environ. Sci. Technol. , 42 : 4507 – 4512 .
- Geng , Q. , Guo , Q. , Cao , C. , Zhang , Y. and Wang , L. 2008 . Investigation into Photocatalytic Degradation of Gaseous Ammonia in CPCR . Ind. Eng. Chem. Res. , 47 : 4363 – 4368 .
- Wu , L.C. and Chung , Y.C. 2009 . Replacement of Hazardous Chromium Impregnating Agent from Ag/Cu/Cr Impregnated Active Carbon (ASC) Using Triethylenediamine to Remove Hydrogen Sulfide, Trichloro-methane, Ammonia, and Sulfur Dioxide Gases . Journal of the Air & Waste Management Association , 59 : 258 – 265 . doi: 10.3155/1047-3289.59.3.258
- Chen , L. , Hoff , S. , Cai , L. , Koziel , J. and Zelle , B. 2009 . Evaluation of Wood Chip-Based Biofilters to Reduce Odor, Hydrogen Sulfide, and Ammonia from Swine Barn Ventilation Air . Journal of the Air & Waste Management Association , 59 : 520 – 530 . doi: 10.3155/1047-3289.59.5.520
- Escandón , L.S. , Ordóñez , S. , Díez , F.V. and Sastre , H. 2002 . Ammonia Oxidation over Different Commercial Oxidation Catalysts . React. Kinet. Catal. Lett. , 7 : 61 – 67 .
- Darvell , L.I. , Heiskanen , K. , Jones , J.M. , Ross , A.B. , Simell , P. and Williams , A. 2003 . An Investigation of Alumina-Supported Catalysts for the Selective Catalytic Oxidation of Ammonia in Biomass Gasification . Catal. Today , 81 : 681 – 692 .
- Il'chenko , N.I. and Golodets , G.S. 1975 . Catalytic Oxidation of Ammonia. I. Reaction Kinetics and Mechanism . J. Catal. , 39 : 57 – 72 .
- Il'chenko , N.I. and Golodets , G.S. 1975 . Catalytic Oxidation of Ammonia. II. Relationship between Catalytic Properties of Substances and Surface Oxygen Bond Energy . J. Catal. , 39 : 73 – 86 .
- Il'chenko , N.I. 1976 . Catalytic Oxidation of Ammonia . Russ. Chem. Rev. , 45 : 1119 – 1134 .
- Li , Y. and Armor , J.M. 1997 . Selective NH3 Oxidation to N2 in a Wet Stream . Appl. Catal. B. , 13 : 131 – 139 .
- Amblard , M. , Burch , R. and Southward , B.W.L. 2000 . A Study of the Mechanism of Selective Conversion of Ammonia to Nitrogen on Ni/γ-Al2O3 under Strongly Oxidizing Conditions . Catal. Today , 59 : 365 – 371 .
- Wang , W. , Padban , N. , Ye , Z. , Andersson , A. and Bjerle , I. 1999 . Kinetic of Ammonia Decomposition in Hot Gas Cleaning . Ind. Eng. Chem. Res. , 38 : 4175 – 4182 .
- Liang , C. , Li , W. , Wei , Z. , Xin , Q. and Li , C. 2000 . Catalytic Decomposition of Ammonia over Nitrided MoNx/α-Al2O3 and NiMoNy/α-Al2O3 Catalysts . Ind. Eng. Chem. Res. , 39 : 3694 – 3697 .
- Schmidt-Szałowski , K. , Krawczyk , K. and Petryk , J. 1998 . The Properties of Cobalt Oxide Catalyst for Ammonia Oxidation . Appl. Catal. A. , 175 : 147 – 157 .
- Hung , C.M. 2008 . Decomposition Kinetics of Ammonia in Gaseous Stream by a Nanoscale Copper-Cerium Bimetallic Catalyst . J. Hazard. Mat. , 150 : 53 – 61 .
- Hung , C.M. , Lou , J.C. and Lin , C.H. 2003 . Removal of Ammonia Solutions Used in Catalytic Wet Oxidation Processes . Chemosphere , 52 : 989 – 995 .
- Hung , C.M. , Lou , J.C. and Lin , C.H. 2004 . Catalytic Wet Oxidation of Ammonia Solution: Activity of the Copper-Lanthanum-Cerium Composite Catalyst . J. Envir. Eng. , 130 : 193 – 200 .
- Hung , C.M. 2009 . The Effect of the Calcination Temperature on the Activity of Cu-La-Ce Composite Metal Catalysts for the Catalytic Wet Oxidation of Ammonia Solution . Powder Technol. , 191 : 21 – 26 .
- Skårman , B. , Grandjean , D. , Benfield , R.E. , Hinz , A. , Andersson , A. and Wallenberg , L.R. 2002 . Carbon Monoxide Oxidation on Nanostructured CuOx/CeO2 Composite Particles Characterized by HREM, XPS, XAS, and High-Energy Diffraction . J. Catal. , 211 : 119 – 133 .
- Sadykov , V.A. , Bunina , R.V. and Alikina , G.M. 2001 . Supported CuO+Ag Partially Stabilized Zirconia Catalysts for the Selective Catalytic Reduction of NOx under Lean Burn Condition . J. Catal. , 200 : 117 – 130 .
- Centi , G. and Perathoner , S. 1998 . The Role of Ammonia Adspecies on the Pathways of Catalytic Transformation at Mixed Metal Oxide Surfaces . Catal. Rev. Sci. Eng. , 40 : 175 – 208 .
- Sedmak , G. , Hočevar , S. and Levec , J. 2003 . Kinetics of Selective CO Oxidation in Excess of H2 over the Nanostructured Cu0.1Ce0.9O2-y Catalyst . J. Catal. , 213 : 135 – 150 .
- Liu , H. , Wang , H. , Shen , J. , Sun , Y. and Liu , Z. 2008 . Promotion Effect of Cerium and Lanthanum Oxides on Ni/SBA-15 Catalyst for Ammonia Decomposition . Catal. Today , 131 : 444 – 449 .
- Ning , W. , Shen , H. and Liu , H. 2001 . Study of the Effect of Preparation Method on CuO-ZnO-Al2O3 Catalyst . Appl. Catal. A , 211 : 153 – 157 .
- Golunski , S.E. , Hatcher , H.A. , Rajaram , R.R. and Truex , T.J. 1995 . Origins of Low-Temperature Three-Way Activity in Pt/CeO2 . Appl. Catal. B: Environ. , 5 : 367 – 376 .
- Carvalho , M.C.N.A. , Passos , F.B. and Schmal , M. 2000 . The Behavior of Cu/ZSM-5 in the Oxide and Reduced Form in the Presence of NO and Methanol . Appl. Catal. A. , 193 : 265 – 276 .
- Shan , W. , Feng , Z. , Li , Z. , Zhang , J. , Shen , W. and Li , C. 2004 . Oxidative Steam Reforming of Methanol on Ce0.9Cu0.1Oy Catalysts Prepared by Deposition-Precipitation, Coprecipitation, and Complexation-Combustion Methods . J. Catal. , 228 : 206 – 217 .
- Bradely , J.M. , Hopkinson , A. and King , D.A. 1995 . Control of a Biphasic Surface Reaction by Oxygen Coverage: the Catalytic Oxidation of Ammonia over Pt {100} . J. Phys. Chem. , 99 : 17032 – 17042 .
- Curtin , T. , Regan , F.O. , Deconinck , C. , Knűttle , N. and Hodnett , B.K. 2000 . The Catalytic Oxidation of Ammonia: Influence of Water and Sulfur on Selectivity to Nitrogen over Promoted Copper Oxide/Alumina Catalysts . Catal. Today , 55 : 189 – 195 .