ABSTRACT
Calcination is the second step in a washing-calcination-conversion system in which treated municipal solid waste incinerator fly ash and bottom ash can be reused as raw material in the cement industry and can decompose or stabilize hazardous compounds, reduce residue amounts, and alter residue characteristics. In this research, only fly ash is discussed. Chloride reduction is important if treated fly ash is to be reused in cement; however, the relationship between washed fly ash properties and chloride reduction by calcination is not well understood. This study used washed residues of three types of fly ash—raw fly ash (RFA) from the boiler or economizer of an incineration system, fly ash collected in a bag filter injected with calcium hydroxide (Ca(OH)2) for acid removal (CaFA), and fly ash collected in a bag filter injected with sodium bicarbonate (NaHCO3) for acid removal (NaFA)—in calcination experiments with varying temperature (400–1100 °C) and atmosphere (100% nitrogen [N2] at 25 mL/min or 10% oxygen [O2] [90% N2] at fluxes of 25, 50, and 75 mL/min). From the perspective of chloride reduction, heating to 1000 °C with 1-hr heating time, 1-hr holding time, and an atmosphere of 10% O2/90% N2 was most suitable for calcination. Under these conditions, chloride levels were reduced by 91, 52, and 96% in washed residues of RFA, CaFA, and NaFA, respectively. Among the washed residues, the weight of the washed residue of NaFA decreased the most.
This research presents the reduction of chlorine and washing of three kinds of fly ash (RFA, CaFA and NaFA) during the calcination process. By comparing the results of those fly ashes, it is shown that NaHCO3 is better than Ca(OH)2 as a neutralization reagent to treat exhaust gas from an incineration chamber because chlorine is more easily eliminated from NaFA than from CaFA. The reduction of other elements is also presented, as well as the X-ray diffraction analysis of some samples by which the mechanism of the calcination process is analyzed.
INTRODUCTION
Fly ash from municipal solid waste incinerators (MSWIs) is hazardous waste because it contains considerable concentrations of heavy metals and dioxins.Citation1–3 Melting, stabilization/solidification, and acid extraction, among other processes, have been used to treat fly ash.Citation4 However, these technologies have shortcomings.Citation4 For example, melting is expensive, which is unpopular even in developed counties such as Japan, and melting produces melting fly ash with even higher concentrations of heavy metals than incineration fly ash. Regarding stabilization/solidification, the volume of the final product is normally bigger than that of the original fly ash, and there are potential risks of heavy metal release, especially at the landfill site, and some reagents are relatively expensive. As to acid extraction, it is a complicated process, and the resulting wastewater may also cause environmental problems.Citation4–8 As a more environmentally friendly alternative, the authors propose a washing-calcination-conversion system in which the MSWI fly ash is washed first and then sent back to the original incinerator to process the calcination treatment. The fly ash finally goes out with the bottom ash and is then conversed to be reused as raw material in the cement industry (hereafter referred to as the “WCCB system”). In this research, only fly ash is discussed.
The WCCB system has many merits. It solves the problem of dioxins, polychlorinated biphenyls (PCBs), and other complex organic compounds in fly ash by heating the treated fly ash in rotary kilns used in the cement industry.Citation9 Concentrated heavy metals can also be recovered from fly ash using this system, or they can be stabilized by the cement crystal structure. As to the wastewater discharged in the washing step, it is either pretreated and then sent to a wastewater treatment plant or further processed to recover salt.Citation10 Thus, by reusing compounds found in fly ash, natural resources can be conserved. The gross cost of this system was calculated for a MSWI of 600 t/day, and approximately 160 Japanese yen (JPY)/t of municipal solid waste (MSW) (equal to ∼$1.95 [U.S.]) is paid for fly ash treatment from MSWI. However, the chloride concentration of the final WCCB product is critical because there are strict limits on chloride levels in the final product of cement, the standard of which is 350 parts per million (ppm) according to the Japanese industry standard.Citation5,Citation11 The washing process of the WCCB system was studied, and the influence of different alkaline reagents (e.g., calcium hydroxide [Ca(OH)2] and sodium bicarbonate [NaHCO3]) used for acid gas removal in MSWI air pollution control systems on the washing process was examined. It was found that fly ash collected by a bag filter resulting from neutralizing the exhausted gas through injecting NaHCO3 (NaFA) is better than fly ash collected by a bag filter resulting from neutralizing the exhausted gas through Ca(OH)2 (CaFA) for chloride reduction by washing, and washing frequency is more effective than mixing time and the liquid-to-solid ratio for removing chlorides in the washing process.Citation12 With the relatively acceptable operation parameters chosen for the washing steps, more than 88% chlorine can be reduced.Citation12–14 The authors have previously explained chloride speciation in the three kinds of fly ash and chloride behavior in the fly ash washing process; this research strongly supported the washing condition chosen because most of the chlorine in fly ash existed as soluble chlorides such as sodium chloride (NaCl), potassium chlo-ride (KCl), and calcium chloride (CaCl2).Citation14–17 It is reasonable to set washing as the first step to remove chlorides because experiments to heat fly ash were first conducted at 1000 °C for 1 hr and the reduction of chlorides is much less than that in washing experiments. However, washed fly ash was found to still contain considerable chlorine concentration, 3.98% in washed NaFA, 2.67% in washed CaFA, which is close to the concentration of insoluble chlorides in fly ash, 3.05% in NaFA and 2.11% in CaFA, and still much higher than the Japanese industrial standard level, indicating that the washed residue must be further treated.Citation12,Citation15–17; most chlorides have a low melting point,Citation21 so calcination may evaporate some chlorides, thereby reducing the chlorine content of fly ash. As to the exhausted gas generated during the calcination process, because the authors meant to use the incinerator to process the calcination step, it will be treated together with the exhaust gas from the combustion chamber of the incinerator. The additional cost of calcination would be minimal because this step could occur in an incinerator. Although, in the practical plant, the washed residue would be sent to the incinerator from the very beginning of the incinerator with the fresh MSW, the trend of the results should be similar to those of this study.
The purpose of study presented here was to determine the operation parameters for the process of calcinating washed fly ash and to compare the effectiveness of the two alkaline reagents, Ca(OH)2 or NaHCO3, for the purposes of recycling fly ash as a raw material for use in the cement industry. Previous research on calcination or sintering has mainly focused on the leaching behavior of heavy metals, the decomposition of dioxins, and the physical and chemical properties of the sintered product.Citation18–20 The goal was to reduce residue weight and chlorine content. However, because the final product is to be used in the cement industry, chlorine concentration was a more important factor than weight. Washed residue from three kinds of fly ash was used: raw fly ash (RFA) from the boiler or economizer of an incineration system, CaFA, and NaFA. Previous studies have focused primarily on RFA or CaFACitation18–20,Citation22–24; few calcinating experiments have used NaFA.
EXPERIMENTAL MATERIALS AND METHODS
Experimental Materials
Three kinds of fly ashes were collected from continuous MSWIs (stokers) in Japan. The exhausted gas was neutralized by dry injection. The elemental concentration of those fly ashes is shown in , and the checking method has been described in the authors' previous research.Citation15 Washed residues from the washing experiment (first step: liquid [mL]: solid [g] = 3:1, mixing speed = 150 rpm, mixing time = 5 min; second step: liquid:solid = 3:1, mixing speed = 150 rpm, mixing time = 10 min; dried at 105 °C for ∼24 hrCitation11) of the three kinds of fly ash—RFA-II#, CaFA-II#, and NaFAII#—were used. The compositions of the three kinds of residue were examined by X-ray fluorescence (XRF; XRF-1700, Shimadzu Corporation) and ion chromatography (DX-AQ AI-450, Dionex Company, Ltd.). lists the elemental compositions of these washed residues and shows that NaFA-II# has a higher concentration of Zn, Br, and Pb than RFA-II# or CaFA-II#. The insoluble portion of Zn, Br, and Pb in NaFA-II# might be more than those in RFA-II# or CaFAII# because they are residues from washing experiments.
Table 1. Element content of RFA, CaFA, and NaFA (wt %)
Table 2. Element content of RFA-II#, CaFA-II#, and NaFA-II# (wt %)
Experimental Methods
Washed residues were heated in high-temperature tube ovens (KRB-24HH, Isuzu Seisakusho Company, Ltd.; KTF-045, Kyoto Thermo System Company, Ltd.).
Heating temperature, atmosphere, and heating time might be important factors in the calcination process.Citation22 To determine the relative importance of these factors, thermogravimetric-differential thermal analysis (TG-DTA) of the samples was carried out and some preliminary experiments were performed. TG-DTA and preliminary experiment results revealed that heating temperature was the most critical parameter and that there was little difference between 100% nitrogen (N2) and 10% oxygen (O2) (with 90% N2 for balance, the authors meant to use the high-temperature zone in the original incinerator to process the calcination process, where the concentration of O2 in the atmosphere is near 10%). Thus, the temperature was first varied from 400 to 1100 °C, considering the wide range of temperatures found in MSWIs and rotary kilns in the cement industry, and the atmosphere was fixed at 100% N2 supplied at a flux of 25 mL/min. After a relatively good temperature was chosen for reducing chlo-rides, the influence of heating atmosphere on the results under conditions of 10% O2 (90% N2) at 25, 50, and 75 mL/min was tested. Details of the experimental designs are shown in and for experiments I and II, respectively. Heating time refers to the time required to heat the tube, including the sample, from room temperature to the target temperature, and the dwell time refers to how long the tube, including the sample, was maintained at the target temperature.
Table 3. Experiment design of the formal experiments I
Table 4. Experiment design of the formal experiments II
Every experimental condition was repeated in triplicate. Each time, a ±5-g sample was loaded in a combustion boat (14 × 12 × 140 mm3). The chlorine concentration of each sample was checked twice by XRF, and some samples were also examined by ion chromatography with respect to the mass of the residue at the corresponding temperature.
RESULTS AND DISCUSSION
Heating Temperature
The standard deviation of loss of residue (LOR) was calculated using Equationeq 1 for each repeated experiment. The maximum standard deviations for RFA-II#, CaFA-II#, and NaFA-II# were 0.44, 1.05, and 0.69%, respectively.
presents the LOR values and chlorine concentration of the calcinated residues. From the figure, it can be seen that temperature had a very significant effect on LOR values and chlorine concentration of the calcinated products of RFA-II#, CaFA-II#, and NaFA-II#, especially CaFA-II# and NaFA-II#. For example, at 1000 °C, the LOR values for RFAII#, CaFA-II#, and NaFA-II# were 7.54, 23.2, and 27.7%, respectively, and the chlorine concentrations were 0.226, 1.51, and 1.31%, respectively. LOR values continued to increase with increasing heating temperature. However, chlorine concentration exhibited a different pattern. For NaFA and CaFA, chlorine concentration gradually increased with increasing heating from room temperature to 800 °C, and then at temperatures above 800 °C, chlorine concentration declined sharply. For RFA, this turning point occurred at ±600–700 °C. The first gradual increase in chlorine concentration (from room temperature to the turning point) might be due to the loss of chlorine-free compounds from the residues, and the latter sharp decrease may be due to the sublimation of chlorides.
Determining the Appropriate Heating Temperature
EquationEquation 2 was used to calculate the left derivative of the LOR curves because that value represents the rate of change of y (i.e., LOR value and/or chlorine amount) at the corresponding point. The results are shown in . For chlorine amount, on the basis of the results shown in , the total amount of chlorine remaining in the residue after calcination () and the left derivative of the corresponding curve () were calculated. The amount of chlorine remaining was calculated using Equationeq 3 on the basis of 100 g of each type of fly ash (RFA-II#, CaFA-II#, and NaFA-II#).
Figure 2. Data processing from : (a) left derivative of LOR curve, (b) chlorine amount left in the residue, and (c) left derivative of chlorine left curve.
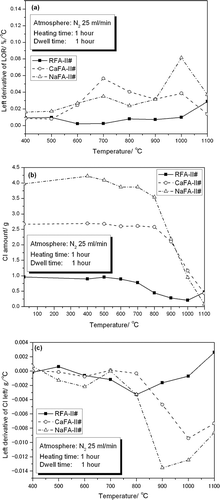
where x 1,x 2 is the heating temperature and y 1,y 2 is the corresponding LOR value or the weight of chlorine for each washing experiment.
shows that the maximum left derivative value of the LOR curve occurred at 1100, 700, and 1000 °C for RFAII#, CaFA-II#, and NaFA-II#, respectively. The maximum rate of decrease in chlorine levels occurred at 800, 1000, and 900 for RFA-II#, CaFA-II#, and NaFA-II#, respectively (). A second maximum occurred at 1000 °C for NaFA-II#. Because the end product of this process is to be used in the cement industry, chlorine concentration is the most important parameter. Thus, the heating temperature was set to 1000 °C; the high-temperature zone of the incinerator will be used for calcination.
Weight loss of the residues was likely directly related to fly ash composition. Because all of the samples of RFA-II#, CaFA-II#, and NaFA-II# were obtained from the washing experiment and dried at 105 °C for 24 hr, they all likely contained some hydratesCitation22–26 that would lose their combined water upon heating. In addition, compounds with low melting or boiling points would be volatilized. In addition to chlorine, variations in elemental concentrations in the residues were also checked by XRF. lists the elements that exhibited significant reductions in concentration or might be related to chlorine or chlorides; for example, at 1100 °C, the concentration of Pb was so low that it could not be detected by XRF. Other elements for which the concentrations were considerably reduced during the calci-nation process included S, K, and Zn. Levels of Na clearly decreased in CaFA-II# and NaFA-II# but not in RFA-II#. Concentrations of C were also examined. shows levels of total carbon (TC) and inorganic carbon in the three fly ashes. Loss of TC accounted for approximately 20% of the total loss of mass in CaFA-II# and NaFA-II# and less than 5% in RFA-II#. However, sulfur dioxide (SO2) is thought to be emitted at temperatures between 1050 and 1140 °C because of the decomposition of some sulfates,Citation27–30 and there might be some oxides of nitrogen (NOx).Citation27–31 Thus, the loss of weight was attributable to four fly ash components: hydrates, TC, chlorides, SO2, and unknown compounds.
Table 5. Contribution of some elements to the LOR of calcinated RFA-II#, CaFA-II#, and NaFA-II# at 1000 and 1100 °C
Table 6. TC and inorganic carbon value of RFA-II#, CaFA-II#, and NaFA-II#
Comparison of the Three Types of Fly Ash
The LOR mass percent and the loss of chlorine weight percent were greater in NaFA-II# than in CaFA-II# ( and ). For example, at 1000 °C, the LOR value of NaFA-II# was 27.7%, that of CaFA-II# was 23.2%, and the corresponding LOR value of RFA-II# was 7.54%. The losses of chlorine weight percent in these three residue types, as defined using Equationeq 4, were 76.2, 56.3, and 78.2% for NaFA-II#, CaFA-II#, and RFA-II# respectively.
The injection of NaHCO3 in the calcination process was more effective than the injection of Ca(OH)2 at reducing chlorine levels in residues because the washed residue from NaFA (NaFA-II#) released more chloride than the washed residue from CaFA (CaFA-II#) under the same conditions. This difference may be due to differences in chloride speciation and speciation of other components between CaFA-II# and NaFA-II#. An earlier study found that CaFA-II# contained more CaCl2 and insoluble chlorides than did NaFA II#,Citation16 and insoluble chlorides are strongly related to CaCl2. TG-DTA experiments on NaCl, KCl, and CaCl2·2 H2O found that when the temperature reached 1000 °C, the weight of NaCl and KCl reached zero after ±20 and ±10 min, respectively, but more than 60 min were required for the weight of CaCl2·2 H2O to reach zero.Citation17 Thus, CaCl2·2 H2O may be more difficult to get rid of than NaCl and KCl.
Discussion of Choice of Atmosphere and the Corresponding Flux
shows the LOR values and chlorine concentration results from experiment II. The results for RFA-II#-7#, CaFAII#-7#, and NaFA-II#-7# from experiment I are included for comparison. The LOR value under a pure N2 gas atmosphere was always greater than that under a 10% O2 gas atmosphere, especially for CaFA-II#. An atmosphere of 10% O2 better removed chlorides from RFA-II# and NaFA-II# than an atmosphere of N2, especially for NaFA-II#. For CaFA-II#, pure N2 gas performed better than 10% O2 gas (90% N2) at reducing chlorides; however, this difference was not significant. Thus, considering the atmospheres of the high-temperature zones of MSWIs and rotary kilns in the cement industry, an atmosphere of 10% O2 (90% N2) was chosen for the experiments.
Figure 3. Experimental results of formal experiment II: (a) LOR weight and (b) chlorine concentration in the residue.
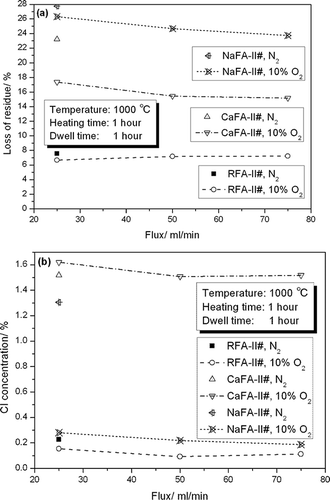
Flux of 10% O2 was compared at 25, 50, and 75 mL/min. To enable comparison with the experiments under the N2 atmospheric conditions, the minimum flux was set at 25 mL/min. The maximum flux was set at 75 mL/min. indicates that, with respect to the LOR value of RFA-II#, the most effective flux value was 75 mL/min. For CaFA-II# and NaFA-II#, the lowest gas flux value was most effective. Given the current flux range, the influence of gas flux on reducing the amount of residue and chlorine was not apparent. RFAII# and CaFA-II# had the lowest chlorine concentration in the final residue at a flux of 50 mL/min, whereas in NaFA-II# the minimum occurred at a flux of 75 mL/min. On the basis of these results, it was decided to adopt a 10% O2 (90% N2) flux of 50 mL/min.
The reason that O2 gas accelerates the reduction of chlorides in residue is thought to be that oxygen atoms replace chlorine in some compounds, forming some silicates such as wollastonite (CaSiO3).Citation32–34 The X-ray diffraction (XRD) results of experiment II () were checked and it was found that the intensity of gehlenite (Ca2Al2SiO7) in CaFA-II# samples clearly increased under the 10% O2 atmosphere and increased with increasing flux, which is very obvious for the samples of CaFA-II#. For example, the intensity around 2θ= 31.3 for CaFA-II-11# is approximately 2 times of that of CaFA-II#-7#, which might be the position for the 100% intensity of pure Ca2Al2SiO7 according to the International Center for Diffraction Data (ICDD) card (PDF#73-2041) because the XRD experiments were done at an approximately similar volume of sample. However, the influence of O2 was not so strong in NaFA-II# and RFA-II#, which showed almost no change.
Figure 4. XRD results of samples in formal experiment II: (a) RFA-II#, (b) CaFA-II#, and (c) NaFA-II#.
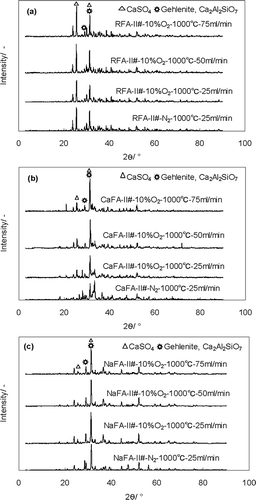
In the preliminary experiments, the influence of dwell time was tested using RFA-II# and it was found that 1 hr was better than 0.5 hr. Thus, the conditions chosen for calcination were a heating time of 1 hr, a dwell time of 1 hr, a temperature of 1000 °C, and an atmosphere of 10% O2 at 50 mL/min. These conditions were chosen based on the results of the calcination experiments presented here and the goal of reducing chlorine content. However, when considering the WCCB system as a whole and with respect to energy use, cost, and practicality, the calcination conditions may change, as would the washing process conditions. For example, 1000 °C is not a widely used temperature in incinerators, although in some parts of incinerators or in some incinerators such a temperature can be reached. With respect to the atmosphere, if the high-temperature zone of an incinerator or the low-temperature zone of a rotary kiln is used to calcinate treated fly ash, the atmosphere cannot be changed because it is a fixed operation condition for both types of plants.
CONCLUSIONS
The calcination process can clearly be used to reduce the chlorine content of washed residue of the three kinds of tested fly ash. On the basis of the TG-DTA and preliminary experiments, experiments I and II were set up in which the heating temperature was varied from 400 to 1100 °C and atmospheres of 100% N2 at 25 mL/min and 10% O2 (90% N2) were tested at 25, 50, and 75 mL/min. A heating temperature of 1000 °C, an atmosphere of 10% O2 (90% N2), a heating time of 1 hr, and a dwell time of 1 hr produced the best results. Under these conditions, chlorine levels were reduced by 91, 52, and 96% in washed residues of RFA, CaFA, and NaFA, respectively. Of the three types of washed residue, the NaFA residue had the greatest reduction in weight. The chlorine concentration in the calcinated NaFA-II# was lower than that in the calcinated CaFA-II#, although the chlorine concentration in NaFA-II# was almost 1.5 times that in CaFA-II#. Thus, as an alkaline reagent in the incineration system to neutralize acid compounds in discharge gas (i.e., to reduce the chlorine content of fly ash by calcinations), NaHCO3 performed better than Ca(OH)2.
ACKNOWLEDGMENTS
The authors gratefully acknowledge the contributions of Ogasahara Shogo to the calcination experiments. The authors thank the Ministry of Education, Culture, Sports, Science, and Technology of Japan for financial assistance (Grant-in-Aid for Scientific Research [B]). The authors thank the Scientific Research Foundation of Renmin University of China (Basic Scientific Research Specific Foundation of Central Universities).
REFERENCES
- Chang , F.Y. and Wey , M.Y. 2006 . Comparison of the Characteristics of Bottom Ash and Fly Ashes Generated from Various Incineration Process . J. Hazard. Mater. , 138 : 594 – 603 .
- Olie , K. , Vermeulen , P.L. and Hutzinger , O. 1977 . Chlorodibenzo-p-Dioxins and Chlorodibenzofurans are Trace Components of Fly Ash and Flue Gas of Some Municipal Incinerators in the Netherlands . Chem. , 6 : 455 – 459 .
- Riber , C. , Fredriksen , G.S. and Christensen , T.H. 2005 . Heavy Metal Content of Combustible Municipal Solid Waste in Denmark . Waste Manage. Res. , 23 : 126 – 132 .
- Sakai , S. , Sawell , S.E. and Chandler , A.J. 1996 . World Trends in Municipal Solid Waste Management . Waste Manage. , 16 : 341 – 350 .
- Oygard , J.K. , Gjengedal , E. and Mage , A. 2005 . Mass-Balance Estimation of Heavy Metals and Selected Anions at a Landfill Receiving MSWI Bottom Ash and Mixed Construction Wastes . J. Hazard. Mater. , 123 : 70 – 75 .
- Mizutani , S. , van der Sloot , H.A. and Sakai , S. 2000 . Evaluation of Treatment of Gas Cleaning Residues from MSWI with Chemical Agents . Waste Manage. , 20 : 233 – 240 .
- Huang , W. and Lo , J. 2004 . Synthesis and Efficiency of a New Chemical Fixation Agent for Stabilizing MSWI Fly Ash . J. Hazard. Mater. , B112 : 79 – 86 .
- Ferreira , C. , Ribeiro , A. and Ottosen , L. 2003 . Possible Applications for Municipal Solid Waste Fly Ash . J. Hazard. Mater. , 96 : 201 – 216 .
- Bolwerk , R. Co-Processing of Waste and Energy Efficiency by Cement Plants . Presented at the Intergovernmental Panel on Climate Change Conference . October 21–22 , Vienna , Austria.
- Aubert , J.E. , Husson , B. and Vaquier , A. 2004 . Use of Municipal Solid Waste Incineration Fly Ash in Concrete . Cement Concrete Res. , 34 : 957 – 963 .
- 2003 . JIS R5210 Ordinary Portland Cement , Tokyo , , Japan : Japanese Industrial Standards Committee .
- Zhu , F. , Takaoka , M. , Oshita , K. and Takeda , N. 2009 . Comparison of Two Kinds of Fly Ashes with Different Alkaline Reagents in Washing Experiments . Waste Manage. , 29 : 259 – 264 .
- Zhu , F. , Takaoka , M. , Shiota , K. , Oshita , K. , Kitajima , Y. and Morisawa , S. Sound Recycling System for Fly Ash from Municipal Solid Waste Incinerator to Be Raw Material in Cement Industry—the Study of Calcinating Process of Washed Fly Ash . Presented at WASCON 2009—Sustainable Management of Waste and Recycled Materials in Construction . June 3–5 , Lyon , France.
- Mangialardi , T. 2003 . Disposal of MSWI Fly Ash through a Combined Washing-Immobilisation Process . J. Hazard. Mater. , 98 : 225 – 240 .
- Zhu , F. , Takaoka , M. , Shiota , K. , Oshita , K. and Kitajima , Y. 2008 . Chloride Chemical Form in Various Types of Fly Ash . Environ. Sci. Technol. , 42 : 3932 – 3937 .
- Zhu , F. , Takaoka , M. , Oshita , K. , Morisawa , S. , Tsuno , H. and Kitajima , Y. 2009 . Chloride Behavior in Washing Experiments of Two Kinds of Municipal Solid Waste Incinerator Fly Ash with Different Alkaline Reagents . Journal of the Air & Waste Management Association , 59 : 139 – 147 . doi: 10.3155/1047-3289.59.2.139
- Zhu , F. , Takaoka , M. , Oshita , K. , Kitajima , Y. , Inada , Y. , Morisawa , S. and Tsuno , H. 2010 . Chlorides Behavior in Raw Fly Ash Washing Experiments . J. Hazard. Mater. , 178 : 547 – 552 .
- Wunsch , P. , Greilinger , C. , Bieniek , D. and Kettrup , A. 1996 . Investigation of the Binding of Heavy Metals in Thermally Treated Residues from Waste Incineration . Chem. , 32 : 2211 – 2218 .
- Ward , D.B. , Goh , Y.R. , Clarkson , P.J. , Lee , P.H. , Nasserzadeh , V. and Swithenbank , J. 2002 . A Novel Energy-Efficient Process Utilizing Regenerative Burners for the Detoxification of Fly Ash . Process Safety Environ. Protect. , 80 : 315 – 324 .
- Xhrouet , C. , Nadin , C. and Pauw , E.D. 2002 . Amines Compounds as Inhibitors of PCDD/Fs De Novo Formation on Sintering Process Fly Ash . Environ. Sci. Technol. , 36 : 2760 – 2765 .
- Lide , D.R. 1965 . CRC Handbook of Chemistry and Physics: A Ready-Reference Book of Chemical and Physical Data , 72nd , Boca Raton , FL : CRC .
- Wey , M. , Liu , K. , Tsai , T. and Chou , J. 2006 . Thermal Treatment of the Fly Ash from Municipal Solid Waste Incinerator with Rotary Kiln . J. Hazard. Mater. , 137 : 981 – 989 .
- Casa , G.D. , Mangialardi , T. , Paolini , A.E. and Piga , L. 2007 . Physical-Mechanical and Environmental Properties of Sintered Municipal Incinerator Fly Ash . Waste Manage. , 27 : 238 – 247 .
- Chou , S. , Lo , S. , Hsieh , C. and Chen , C. 2009 . Sintering of MSWI Fly Ash by Microwave Energy . J. Hazard. Mater. , 163 : 357 – 362 .
- Birnin-Yauri , U.A. and Glasser , F.P. 1998 . Friedel's Salt, Ca2Al(OH)6(Cl, OH)·2H2O: Its Solid Solutions and Their Role in Chloride Binding . Cement Concrete Res. , 28 : 1713 – 1723 .
- Yamamoto , K. , Nishino , K. , Doi , M. and Yokoyama , R. The Increase of Ignition Loss in Wet Bottom Ash . Presented at the 15th Annual Conference of the Japan Society of Waste Management Experts . Takamatsu , Japan. pp. 1066 – 1068 . C6–8
- Bethanis , S. , Cheeseman , C.R. and Sollars , C.J. 2002 . Properties and Microstructure of Sintered Incinerator Bottom Ash . Ceramics Int. , 28 : 881 – 886 .
- Slavo , V.M. , Campostrini , R. , Maurina , S. , Carturan , G. , Mongheddu , M. , Budroni , G. and Cocco , G. 2000 . Bauxite ‘Red Mud’ in the Ceramic Industry, Part 1: Thermal Behaviour . J. Euro. Ceramics Soc. , 20 : 235 – 244 .
- Stern , K.H. and Weise , E.L. 1966 . High Temperature Properties and Decomposition of Inorganic Salts , Vol. Part 1: Sulphates , Gaithersburg , MD : National Standard Reference Data Series; National Bureau of Standards .
- Polettini , A. , Pomi , R. , Trinci , L. , Muntoni , A. and Mastro , S.L. 2004 . Engineering and Environmental Properties of Thermally Treated Mixtures Containing MSWI Fly Ash and Low-Cost Additives . Chem. , 56 : 901 – 910 .
- Stern , K.H. and Weise , E.L. 1972 . High Temperature Properties and Decomposition of Inorganic Salts, Part 3: Nitrates and Nitrites , Gaithersburg , MD : National Standard Reference Data Series; National Bureau of Standards .
- Shor , T.J. and Dial , C. 2000 . Volatilization of Cobalt, Technetium, and Uranium Isotopes from Soils through Salt Amendment and Calcination . J. Environ. Radioact. , 48 : 35 – 48 .
- Watanabe , N. , Inoue , S. and Ito , H. 2000 . Chlorine Promotes Antimony Volatilization in Municipal Waste Incineration . J. Mater. Cycles Waste Manage. , 2 : 10 – 15 .
- Fraissler , G. , Joller , M. and Brunner , T.I. 2009 . Obernberger, Influence of Dry and Humid Gaseous Atmosphere on the Thermal Decomposition of Calcium Chloride and Its Impact on the Remove of Heavy Metals by Chlorination . Chem. Eng. Process. Proc. Intens. , 48 : 380 – 388 .