Abstract
Background: Knowledge regarding the performance of densified biomass in biochemical processes is limited. The effects of densification on biochemical conversion are explored here. Results: Pelleted corn stover samples were generated from bales that were milled to 6.35 mm. Low-solids acid pretreatment and simultaneous saccharification and fermentation were performed for pelleted and ground stover (6.35 and 2 mm) formats. Monomeric xylose yields were significantly higher for pellets (∼60%) than for ground formats (∼38%). Pellets achieved approximately 84% of theoretical ethanol yield; ground stover formats had similar profiles, reaching approximately 68% theoretical ethanol yield. Pelleted and 6.35-mm ground stover were evaluated using a ZipperClave® reactor under high-solids, process-relevant conditions for multiple pretreatment severities (Ro); feedstock reactivity increased slightly following combined pretreatment and enzymatic hydrolysis for three of five severities tested. Conclusion: Pelleting did not render corn stover more recalcitrant to dilute-acid pretreatment under low- or high-solids conditions, and even enhanced ethanol yields.
Mean ± 1 standard deviation; n = 4 for 6.35-mm and 2-mm formats; n = 3 for pellet meal due to a problem with high-performance liquid chromatography injection volume in one replicate.
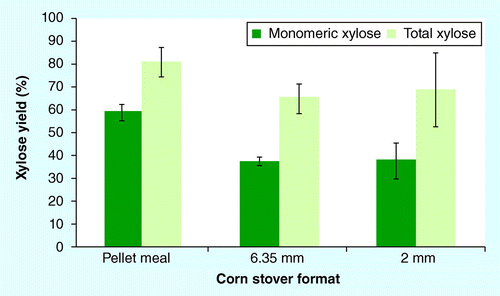
Mean ± 1 standard deviation; n = 4 for 6.35-mm and 2-mm formats; n = 3 for pellet meal due to problem with high-performance liquid chromatography injection volume in one replicate.
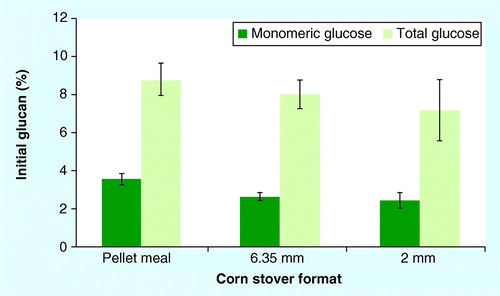
Mean ± 1 standard deviation; n = 4.
TEY: Theoretical maximum ethanol yield.
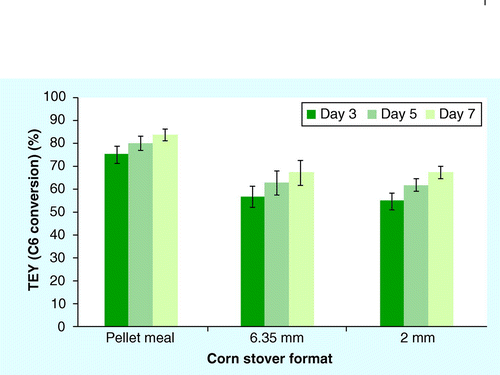
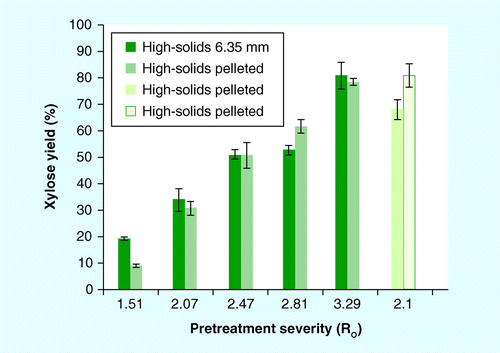
Mean ± 1 standard deviation; n = 3.
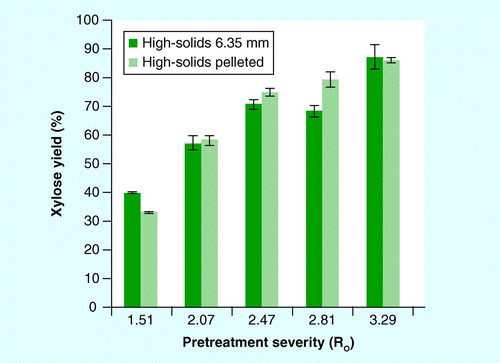
Mean ± 1 standard deviation; n = 3.
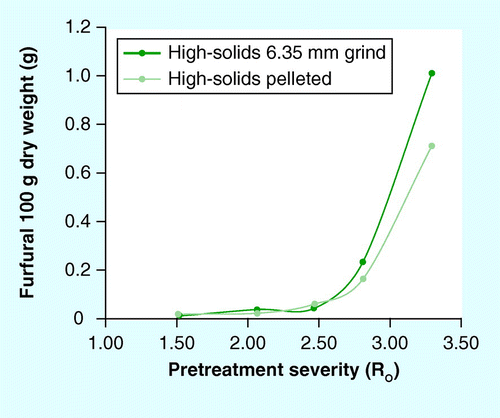
Mean ± 1 standard deviation; n = 3.
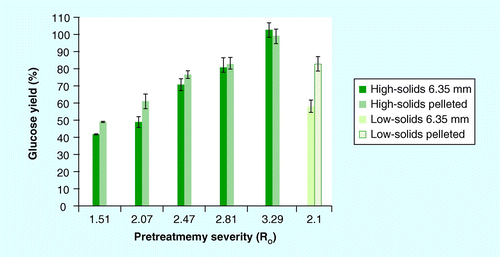
Reactivity is defined as the fraction of the glucose and xylose released from pretreatment and enzymatic hydrolysis, divided by the initial mass of glucose and xylose in the native feedstock.
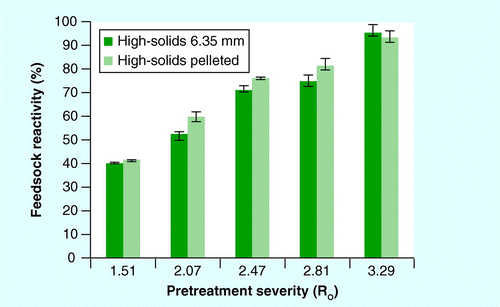
(A) Native corn stover at 700× magnification and (B) native corn stover at 100× magnification; (C) pelleted corn stover at 700× magnification and (D) pelleted corn stover at 440× magnification.
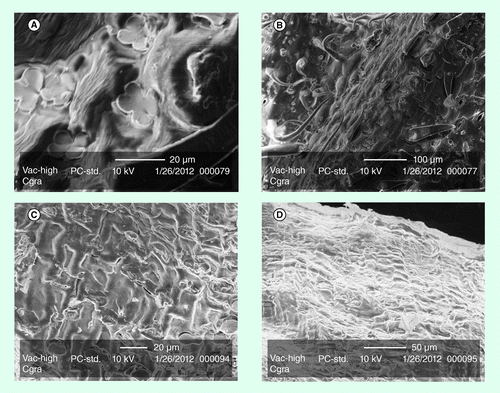
There is a significant difference between treatments (p ≤ 0.05) if the letters above the bars are different (Bonferroni post-hoc adjustments).
BET: Brunauer–Emmett–Teller.
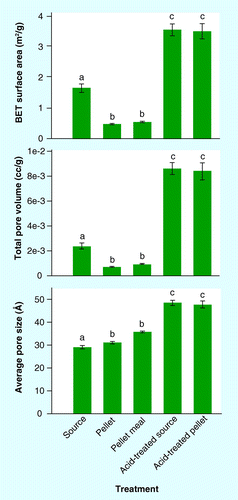
Global demands for energy, diminishing petroleum reserves and growing concerns about climate change have prompted considerable interest in lignocellulosic biomass as a sustainable and renewable energy source. Under the US Energy Independence and Security Act of 2007, the RFS mandates the use of 36 billion gallons per year (BGY) of renewable fuels by 2022, of which 16 BGY are to be derived from cellulosic ethanol Citation[1]. Recent estimates of a baseline scenario suggest that 600 million dry tons of biomass will be available by 2022 to supply sufficient feedstock for achieving this goal, with the potential to produce more than 20 BGY of cellulosic ethanol Citation[2]. The costs associated with acquiring such quantities of biomass are significant, with an estimated cost of US$60 per dry matter ton. A consistent supply of high-quality, economical feedstock is critical to achieving national biofuels goals Citation[3]; however, low-density biomass feedstocks pose challenges to supply chain operations and hinder the large-scale use of biomass for biofuel production. Consequently, increasing the bulk density of biomass through mechanical densification offers logistical benefits that translate into improvements in handling, storage stability and transportation costs Citation[4].
The development of a uniform format, solid feedstock supply system is critical to achieve a consistent supply of feedstock with enhanced physical properties for bioenergy production Citation[5]. The economics and physical properties of densified biomass formats produced from agricultural residues have been explored in several studies Citation[6–9]. Pelleting of biomass can increase unit density of raw biomass resources by as much as tenfold Citation[10], resulting in a flowable and durable product that is compatible with existing biomass supply system infrastructure. Biomass pellets are produced from raw, ground material that is conditioned with heat and/or moisture, compacted and extruded through a die Citation[6,11]. It has been shown that activating or softening the natural binders in biomass, such as lignin, through a combination of moisture and temperature during the process of densification, is key to the development of particle–particle bonding required for pellet durability Citation[7]. The degree of lignification contributes strongly to biomass recalcitranceCitation[12], and its alteration during the process of densification could impact biomass reactivity to pretreatment and enzymatic hydrolysis Citation[13].
The process of extrusion, which is similar to pelleting, has been shown to enhance sugar recoveries for switchgrass and prairie cord grass Citation[14]. However, there are limited studies that examine the impact of densification on biomass pretreatment and bioconversion. A recent study by Shi et al. demonstrated that there were no negative impacts on sugar yields following ionic liquid pretreatment of mixed feedstock pellets (equal masses of switchgrass, lodgepole pine, corn stover and eucalyptus) relative to the mixed flour format Citation[15]. Rijal et al. reported that the enzymatic hydrolysis of ground and pelleted switchgrass increased glucose and xylose yields by 37 and 42%, respectively, relative to the original biomass following soaking in aqueous ammonia pretreatment Citation[13]. The yield improvements measured for pelleted switchgrass were attributed to reduced particle size, shear development and thermal softening during the pelletization process. Theerarattananoon et al. showed that enzymatic conversion of cellulose (ECC) for pelleted biomass was equivalent to, or greater than, the corresponding unpelleted material for corn stover, big bluestem, wheat straw and sorghum stalk Citation[11]; in particular, wheat straw pellets achieved the highest ECC of 94.1%. The improved yields were attributed to the opening of the biomass structure prior to dilute-acid pretreatment through the process of pelleting. This study also demonstrated that the conditions of the pelleting process had a significant effect on biomass composition; the glucan content of the biomass was positively affected by die thickness and negatively affected by mill screen size, while the opposite trend was observed for xylan content. Given the improved sugar yields upon enzymatic hydrolysis for pelleted biomass relative to the unpelleted source materials as described above Citation[11,13], it may be postulated that the process of densification causes shearing of biomass tissue, which translates into increased surface area and improved accessibility for enzymatic action.
The specific surface area of pretreated biomass is thought to aid in sugar release for enzymatic hydrolysis Citation[16]. Chen et al. showed an increase in surface area of rice straw correlated to improved accessibility of cellulose to enzymatic degradation upon implementation of an integrated pretreatment process of dilute-acid and steam explosion Citation[17]. In addition, the diameter of pores in plant cell walls has a strong influence on enzymatic accessibility to cellulose Citation[18]. Cellulases are reported to range in size from 4 to 13 nm, which exceeds the diameter of most pores present in plant cell walls Citation[19]; the small pore size and reduced surface area of native plant cell walls are important factors that pose severe limitations to enzymatic accessibility and, thereby, contribute to the natural recalcitrance of plant biomass Citation[12].
In this study, we sought to investigate the performance implications of biomass densification on bioconversion to ethanol. Pelleted corn stover was used as a model densified feedstock. The objectives of the present study were to:
▪ Examine whether pelleting renders corn stover more recalcitrant to low-solids, dilute-acid pretreatment; | |||||
▪ Determine whether pelleting is detrimental to ethanol yields in the fermentation of dilute-acid pretreated biomass; | |||||
▪ Examine the effects of pelleting and dilute-acid pretreatment on surface area and pore diameter; | |||||
▪ Understand the impact of pelleting on combined pretreatment and enzymatic saccharification at process-relevant conditions, across increasing pretreatment severities. |
Materials & methods
▪ Materials
Corn stover was single-pass harvested and baled in Palo Alto County (IA, USA) between September and November 2010. The stover was baled and stored field-side for approximately 9 months. Bales were shipped to the Idaho National Laboratory (Idaho Falls, ID, USA) in June 2011. The average moisture content of the bales as received was approximately 13% (wet basis), and bales were stored outdoors prior to grinding and densification.
Saccharomyces cerevisiae D5A was obtained from the American Type Culture Collection (Manassas, VA, USA). Accellerase® 1500 enzyme complex (exoglucanase/endoglucanase activity 54 filter paper units [FPU]/ml) was provided by Genencor® (Rochester, NY, USA).
▪ Pellet production
Six bales were fed through a two-stage, full-scale grinding process using the feedstock process demonstration unit (PDU) at the Idaho National Laboratory. First, material was fed through a Vermeer BG-480 (Pella, IA, USA), which has two horizontal grinding drums with swinging hammers powered by two 200 HP motors Citation[20], and passed through a 25.4-mm screen. The second stage of grinding was completed by feeding the 25.4-mm screened stover through a Bliss hammer mill (Bliss Industries LLC; Ponca City, OK, USA) with a 6.35-mm screen. Corn stover pellets were generated from the resulting 6.35-mm screened material with a Bliss pellet mill (Pioneer 200) in June 2011. The Bliss Pioneer 200 pellet mill is rated for 5 tons/h and operates at approximately 200 amps/motor (dependent upon crop type and moisture content). The die has a 12:1 length-to-diameter ratio, with a 6.35-mm diameter and an effective length of 7.62 cm. The optimal moisture content of feed for the pellet mill is approximately 10–12%. Steam injection was used to preheat the biomass to 65.6°C, and on the day the stover was pelleted, the die temperature was recorded at 98°C using an infrared thermometer.
The formats used for comparison in this study were:
▪ Source material, which underwent a two-stage grinding process, was screened to less than 6.35 mm and used as the feed material for the pellet mill; | |||||
▪ Source material that was subsequently ground using a laboratory knife mill (Thomas Wiley Laboratory Mill, Model 4, 1 HP; Thomas Scientific, Swedesboro, NJ, USA) with a screen size of 2 mm (circular shaped screen opening); | |||||
▪ Pellets; | |||||
▪ Pellet meal that was generated with a 2-mm screen on the laboratory knife mill described previously. |
▪ Bulk density, durability & calorific value
The bulk density and durability of corn stover pellets were measured according to standard American Society of Agricultural and Biological Engineers S269.4 Citation[21]. Prior to testing, pellets were sieved through a 5.6-mm screen to remove fines. Quadruplicate 500-g samples of sieved pellets were placed in the tumbling device and then tumbled for 10 min at 50 rpm, in a dust-tight enclosure. After tumbling for 10 min, the sample was removed, sieved and the percent of whole pellets was calculated. This procedure was performed twice for a total of eight replicates. Pellet durability is a quality parameter that represents the physical strength and the ability of a pellet to remain intact during storage, handling and transportation Citation[10,22]. The calorific value of pellets was measured using a LECO AC600 bomb calorimeter according to the standard ASTM D5865-10a Citation[23].
▪ Particle size distribution
A dynamic image analyzer, Camsizer (HORIBA Instruments, Inc.; Irvine, CA, USA), equipped with two digital cameras, was used to analyze particle characteristics. This method was reported to be highly correlated with a well-accepted static/quantitative technique using light microscopy (r > 0.9 for both aspect ratio and sphericity) Citation[24]. Particle size distribution (PSD) was determined according to a standardized method developed by the ISO Citation[25]. Particle distribution was calculated based on volume, which was defined using an ellipsoid model; diameter was calculated based on Xc min, the greatest width of a particle projection at a right angle.
▪ Compositional analysis
The chemical composition for corn stover grinds (6.35 and 2 mm) and pellets (ground to 2 mm) were measured according to the National Renewable Energy Laboratory’s (NREL) Laboratory Analytical Procedures for standard biomass analysis Citation[26]. Briefly, biomass was extracted using water followed by ethanol, then a two-stage acid hydrolysis of the extracted material was performed. The resulting hydrolysis liquor was analyzed for monomeric sugars, sugar degradation products and organic acids using high-performance liquid chromatography (HPLC) with a refractive index detector (Waters; Milford, MA, USA). The acid hydrolysis and HPLC analysis were performed as described by NREL Citation[27]. Sugars were analyzed on an Aminex HPX-87P carbohydrate column with a mobile phase of 18 MΩ nanopure water at a flow rate of 0.6 ml/min at 85°C. Duplicate 50 µl injections were performed for each sample. Acid-soluble lignin fractions were analyzed using ultraviolet-visible spectroscopy.
▪ Low-solids pretreatment
Dilute-acid pretreatment was conducted using an autoclave method as previously described Citation[28]. The low-solids pretreatment was conducted at a solid loading of 3.3% (w/w) using dilute sulfuric acid (0.8% H2SO4 w/w) and an autoclave at 121°C for 30 min. Briefly, 3.3 ± 0.5 g (recorded to the nearest 0.0001 g) of biomass was added to a 500 ml Erlenmeyer flask, followed by the addition of 100 ml of 0.8% H2SO4 (w/w). Flasks were autoclaved at 121°C, 145 kPa for 30 min. Flasks were then cooled to 23°C, and the pretreated biomass and hydrolysis liquor were filtered in a vacuum manifold through Gooch crucibles lined with Whatman™ (Buckinghamshire, UK) binder-free glass microfiber type GF/D filters with 2.7-µm particle retention. Residual biomass was recovered from pretreatment flasks by rinsing with deionized water; this water was further used to rinse the biomass contained in the Gooch crucibles and collected with the pretreatment liquor in a 200-ml volumetric flask. The pretreatment liquor was brought to a final volume of 200-ml with deionized water that was used to wash the pretreated solids. The biomass was then washed with deionized water until the pH of water filtrate was between 5.5 and 7.0.
Soluble components in pretreatment liquors (monomeric, oligomeric and total sugars) were measured using previously described techniques Citation[29]. Total xylose and glucose are defined as the sum of their monomeric and oligomeric forms. Furfural dehydration products were not measured in pretreatment liquor for the low-severity pretreatment experiments. Liquor samples were neutralized and filtered prior to HPLC analysis. Samples of hydrolysis liquors were analyzed by an HPLC (Waters) equipped with an autosampler and refractive index detector. Sugars were analyzed on an Aminex HPX-87P carbohydrate column with a mobile phase of 18 MΩ nanopure water at a flow rate of 0.6 ml/min at 85°C. Duplicate 50 µl injections were performed for each sample.
▪ Simultaneous saccharification & fermentation of low-solids pretreated materials
Simultaneous saccharification and fermentation (SSF) was performed anaerobically at 30°C and 100 rpm in 60 ml serum vials using S. cerevisiae D5A and Accellerase 1500. Yeast extract–peptone–dextrose (YPD) agar and broth were used for the cultivation of S. cerevisiae D5A. In this study, YPD broth was prepared by dissolving 10 g yeast extract, 20 g peptone, and 50 g dextrose in 1 l of distilled water, while YPD agar was prepared with 20 g/l dextrose and the addition of 20 g/l agar. For the preparation of 10X yeast extract–peptone, 100 g of yeast extract and 200 g of peptone were dissolved in 1 l of distilled water. Phosphate-buffered saline (PBS) was prepared to a final concentration of 11.8 mM phosphate buffer, 200 mM NaCl, 2.7 mM KCl and pH 7. Citric acid buffer was prepared to a final concentration of 1.0 M and pH 4.5. Media and buffers were prepared aseptically and sterilized by filtration with 0.2 µm filter and/or by autoclave at 121°C and 145 kPa.
A single, colony-forming unit of S. cerevisiae D5A that was grown on YPD agar was used to inoculate 300 ml of YPD broth in a 2-l Erlenmeyer flask. This culture was incubated at 30°C and 175 rpm for 24 h and grown until a 1/100 dilution of the culture in YPD broth reached an optical density of a sample measured at 600 nm wavelength of 9.5–11. The yeast culture was centrifuged at 4°C and 4500 rpm for 5 min, and the supernatant was discarded. Yeast pellets were re-suspended in 300 ml of PBS and then centrifuged at 4°C and 4500 rpm for 5 min. Washed pellets were re-suspended in approximately 100 ml of PBS in order to achieve an optical density of a sample measured at 600 nm wavelength of 15 for a 1:20 dilution of the yeast concentrate.
SSF vials contained 1 g of pretreated biomass (dry weight basis) in a fermentation volume of 30 ml. Following addition of pretreated biomass, water was added to a volume of 24 ml, which accounted for the moisture content of biomass. Serum vials were purged with ultra high-purity nitrogen gas in order to remove residual oxygen, and then sealed with butyl rubber stoppers and aluminum closures. Sealed vials were autoclaved at 121°C and 145 kPa for 30 min and then placed in a walk-in cooler at 4°C immediately. After vials were cooled to approximately 30°C, 5 ml of enzyme cocktail – containing 3 ml 10X yeast extract–peptone, 1.5 ml citric acid buffer and 0.5 ml enzyme mixture (Accelerase 1500 at 15 FPU/g dry weight biomass) – were injected by syringe. Lastly, 1 ml of concentrated S. cerevisiae D5A in PBS was injected to a final volume of 30 ml. Vials were incubated at 30°C and 100 rpm for ethanol production. The vials were then analyzed for ethanol by injecting 200 ml of the headspace gas for gas chromatographic analysis with a flame ionization detector (HP 6890 equipped with autosampler; Hewlett-Packard; Palo Alto, CA, USA). The percentages of maximum theoretical ethanol yield (TEY) were calculated based on the fraction of glucan in pretreated biomass solids according to NREL’s Laboratory Analytical Procedures Citation[30].
▪ High-solids pretreatment
High-solids pretreatment (25% w/w) was conducted on both pelleted and 6.35-mm ground stover using dilute sulfuric acid pretreatment under process-relevant conditions with a ZipperClave® reactor (Parker Autoclave Engineers; Erie, PA, USA) as previously described Citation[31], followed by enzymatic hydrolysis of the washed pretreated solids. Although not directly scalable to commercial or pilot scale, the ZipperClave is a batch reactor with internal mixing, heated by direct steam injection for rapid heating Citation[32]. The reactor is capable of pretreating 0.3 kg of biomass at high-solids loadings (≤25% w/w). These capabilities simulate key process parameters that can provide valuable insight into the pretreatment performance of biomass under commercially relevant processing conditions. Both pelleted corn stover and 6.35-mm ground stover were pretreated using five different pretreatment conditions, listed in . All materials were pretreated using 0.8% H2SO4 (w/w). To compare sugar yields between the low-solids, one pretreatment severity (Ro = 2.07) was used as a point for comparison between the low-solids pretreatment methods. Triplicate experiments were performed for both feedstock types (corn stover pellets and 6.35-mm ground stover) and each pretreatment condition. For each pretreatment condition, the following protocol was used.
The corn stover, either pellets or 6.35-mm ground, was added to the canister followed by an addition of 0.8% H2SO4 to achieve a 25% solids loading (w/w). The resulting slurry was mixed for 5 min and then loaded into the ZipperClave reactor. After the reactor was sealed, mixing was initiated followed by steam injection into the top and bottom of the reactor, achieving reaction temperature in 30–45 s; reaction time began when the target temperature was reached. At the end of the reaction, steam was vented through the top plate and into a condenser. Following depressurization, the canister was removed and placed into an ice bucket to quench the reaction. Any remaining solids on the impellor and head plate were rinsed, collected and analyzed for percent total solids. The hydrolyzate, rinsate and condensate were weighed and then analyzed for sugars, organic acids and inhibitors, as previously described Citation[29].
▪ Enzymatic digestion of high-solids dilute-acid pretreated materials
Both ground (stover screened to <6.35 mm) and pelleted corn stover, pretreated in the ZipperClave, were subjected to enzymatic hydrolysis, as previously described Citation[30]. The pretreated materials were washed prior to enzymatic hydrolysis and the solids content of the wet solids was determined prior to saccharification. Nonpretreated pellets and 6.35-mm ground stover were used as controls to compare with the pretreated materials. The enzymatic hydrolysis was conducted at 20% solids loading, using CTec2® (15 FPU/ml; Novozymes; Franklinton, NC, USA) at an enzyme loading of 20 mg of cellulase/g dry wt of pretreated washed solids. All enzymatic hydrolysis studies were carried out for 5 days at 50°C. At the end of the assay, the samples were filtered and the liquors analyzed for soluble sugars using standard methods Citation[29]. To calculate glucose release in the washed solids, the concentration of glucose released (g/g dry wt) during enzymatic hydrolysis was multiplied by the mass of insoluble solids remaining after pretreatment, determined by the fraction of insoluble solids analysis. Glucose yield was determined by dividing glucose release by the mass of initial glucose in the biomass sample.
▪ Scanning election microscopy
Scanning electron microscopy (SEM) was performed with a JEOL JCM-5000 NeoScope™ in high vacuum mode (JEOL; Arvada, CO, USA). Micrographs were taken of raw biomass samples (7.6-cm source material and pellets) in order to identify morphological differences among biomass formats that occurred as a result of densification.
▪ Gas adsorption
The Brunauer–Emmett–Teller (BET) surface area, pore volume and pore size for source, pelleted and pretreated corn stover was determined by nitrogen adsorption at 77 K (Autosorb iQ, Quantachrome Instruments; Boynton Beach, FL, USA). Corn stover samples were dried at 80°C under vacuum for a minimum of 24 h and a maximum of 113 h. Before vacuum drying, source material, pellets and pellets ground to 2 mm were dried in an oven at 80°C for a minimum of 24 h and a maximum of 310 h. Drying times varied because of sample form and nature, and samples were considered dry if the sample was isolated and the pressure rise was less than 21 µm/min. Pellets were broken to approximately 1.27 cm in length before drying, and five pellets were placed into the Quantachrome sample cells for each replicate (1.8–2.0 g). Sample cell bulbs were filled approximately halfway with source material, ground pellets and acid-pretreated samples (0.2–1.7 g). Autosorb iQ software (ASiQwin V2.0, Quantachrome Instruments) was used to obtain BET surface area, total pore volume and average pore size data from nitrogen adsorption curves. BET surface area was determined using 11 adsorption points in the relative pressure range from 0.05 to 0.30.
▪ Statistical analysis
Data presented are the mean of at least three replicates unless otherwise noted, and error bars represent one standard deviation (SD). All statistical analyses were performed in the open-source language R (version 2.15.2) Citation[33] or StatPlus®: mac 2009 (AnalystSoft Inc. 2010). One-way analysis of variance (ANOVA) was performed to identify significant differences, and Tukey’s honest significant difference (HSD) test was performed for multiple-level comparisons of statistical equivalency. Two-way ANOVA was used to identify significance in feedstock reactivity experiments.
For BET gas adsorption studies, one-way ANOVA was used to determine how surface area, pore volume, and pore size were affected by pelleting. A Bonferroni adjustment was used to control for experiment-wise error rate, and differences were considered significant at a level of p ≤ 0.05. Total pore volume data was log10, transformed to meet the assumptions related to normality and homogeneity of variance.
Results & discussion
▪ Physical properties, size distribution & composition of corn stover
The physical and thermal properties of the corn stover pellets produced with the feedstock PDU were measured. The moisture content of the pellets was 11.3%. High-quality corn stover pellets were produced with the feedstock PDU and had a measured durability of 98.5 ± 0.6%; this complies with the standard durability requirement for pellets during handling and transportation, which establishes a minimum limit of 97.5% Citation[22]. Pelleting the 6.35-mm ground source material improved bulk density by 4.3-times (from 149 to 645 kg/m3). The bulk density and energy density of the corn stover pellets produced with the feedstock PDU (645 kg/m3 and 16.55 MJ/kg) were approximately half that for coal (1346 kg/m3 and 31.75 MJ/kg).
The average PSD parameters for each of the ground corn stover formats are presented in . There was no significant difference between the geometric mean particle size (D50) of the 6.35-mm source material or the pellet meal (p > 0.05), while the geometric mean particle size for the 2-mm ground source material was approximately 33% less than the other two formats (p < 0.001; ). The particle diameters for the 84th and 16th percentiles of PSDs were significantly different for all three stover formats (p < 0.001). The 6.35-mm source material had the widest range of variation (D84 = 2.27 mm; D16=0.30 mm) and least uniform particle size, as calculated by the size range variation coefficient (%) Citation[34].
Compositional data suggest that neither grinding nor pelleting had a significant effect on the chemical composition of the corn stover formats examined here. Glucan and xylan contents were reduced slightly for pelleted corn stover (31.3 ± 0.5% and 20.8 ± 0.6%, respectively) compared with the ground formats (33.2 ± 0.6% and 25.1 ± 1.8% for 6.35 mm; 32.1 ± 1.4% and 21.% ± 1.2% for 2 mm), although these differences were not significant (p > 0.05). There were no significant differences in lignin content among the three corn stover formats tested (p > 0.05). Similar glucan, xylan and lignin compositional data for corn stover have been reported previously Citation[32,35]. In addition, results from this study are consistent with recent reports that examined the effect of pelleting on composition and sugar yields for a variety of biomass feedstocks, including corn stover, wheat straw, big bluestem, sorghum stalks and switchgrass Citation[11,13].
▪ Low-solids dilute-acid pretreatment
Monomeric and total xylose yields and ethanol yields were measured following dilute-acid pretreatment and SSF, respectively. provides the average monomeric and total xylose yields following dilute-acid pretreatment. Monomeric xylose yields are a critical performance parameter used to assess the efficacy of dilute-acid pretreatment Citation[32]. Under the low-severity pretreatment conditions examined here, monomeric xylose yields were significantly higher for the pellet meal (Tukey’s HSD p < 0.01) than for the other formats tested with a monomeric xylose yield of 59.3 ± 3.4% (mean ± SD; ). Average monomeric xylose yields were similar (∼38%) for both the 6.35-mm and 2-mm formats. There were no significant differences in average total xylose yield among the three stover formats (p > 0.05; ). The 2-mm corn stover format exhibited high variability in both monomeric and total xylose yields (SD 7.1 and 15.8%, respectively). The average total xylose yield achieved with pellet meal (81%) under the low-severity conditions examined here (Ro = 2.07) was similar to what has been achieved under high-severity, dilute sulfuric acid pretreatment conditions using a continuous, pilot-scale reactor with corn stover ground to less than 1.9 cm at a 30% solids loading Citation[32]. Findings by Rijal et al. demonstrated that pelleting of switchgrass was not detrimental to the efficacy of dilute-acid pretreatment Citation[13]. The improved monomeric xylose yields achieved with the corn stover pellets, and total xylose yields that are comparable with what has been achieved under high-severity, commercially relevant pretreatment conditions, may suggest that densification and, more specifically, pelleting, has the potential to reduce the severity of pretreatment conditions that are required for bioconversion.
The fraction of initial glucan solubilized during low-solids, dilute-acid pretreatment for corn stover formats is shown in . There were no significant differences in either monomeric or total glucose solubilized upon dilute-acid pretreatment among the formats tested (p > 0.05); glucan hydrolysis yields ranged from 7.2% for the 2-mm grind to 8.8% for pellet meal, with solubilized glucose present in predominantly oligomeric form . These results are consistent with earlier studies that have demonstrated cellulose hydrolysis upon dilute-acid pretreatment yields only a small fraction of the total glucose available in the native material Citation[31,36,37]. Previous reports have suggested that the presence of oligomeric glucose in pretreatment hydrolyzates corresponds to the depolymerization of amorphous glucan contained in the structure of cellulose microfibrils Citation[36,38].
▪ SSF of low-solids pretreated materials
Beyond maximizing xylose yields during pretreatment, the key measure for assessing the efficacy of dilute-acid pretreatment is achieving maximum sugar release from the enzymatic hydrolysis of cellulose in pretreated biomass for fermentation Citation[32]. Results from laboratory-scale SSF demonstrated that the pellet meal achieved the highest average % TEY of the formats examined (Tukey’s HSD p < 0.001), reaching nearly 84% TEY from glucan by the end of the experiment . The conventional ground formats, 6.35- and 2-mm grinds, had similar profiles, achieving nearly 68% of TEY by day 7. Actual ethanol yields on day 5 of the fermentation were also compared for each format, with pellet meal, 6.35- and 2-mm formats producing 0.15 ± 0.006, 0.12 ± 0.009 and 0.12 ± 0.004 g ethanol/g pretreated biomass, respectively. The pellet meal had higher yields compared with the other formats tested (ANOVA p < 0.001; Tukey’s HSD p < 0.001). No differences were seen in ethanol yield between 6.35- and 2-mm stover formats (p > 0.05). It is important to note that, although pellet composition was slightly reduced in glucan content relative to the other formats tested, pelleted corn stover still achieved significantly higher actual ethanol yields, in addition to increased % TEY. The improved ethanol yields measured in SSF for pretreated corn stover pellets relative to the 6.35- and 2-mm grinds suggest that pelleting enhances saccharification of structural glucan for fermentation, which has the potential to enhance ethanol production from biomass feedstocks.
Theerarattananoon et al. recently reported that ECC from pelleted biomass was either equivalent to or higher than conversion yields that were achieved with the corresponding unpelleted samples following dilute-acid pretreatment Citation[11]; these results implied that under optimized conditions, pretreated pelleted biomass may enhance glucose recovery from cellulose. In a study by Rijal et al., the effect of pelleting on sugar yields upon enzymatic hydrolysis for untreated and pretreated biomass was examined Citation[13]; the untreated pellets had higher glucose yields upon enzymatic hydrolysis than the untreated, original biomass (D50 ∼7.7 mm). For dilute-acid pretreated biomass, pellets had significantly higher glucose yields than the original biomass at 24 h, while soaking in aqueous ammonia resulted in glucose yields that were 36% greater for pellets than for original biomass at 24 h.
Extrusion has been shown to increase the ethanol yield and fermentation efficiency of sorghum Citation[39]; the improvements in bioconversion were attributed to depolymerization of starch, increased free sugars and destruction of native biomass structures as a result of the extrusion process.
▪ High-solids dilute-acid pretreatment & enzymatic hydrolysis of source & pelleted materials
Differences between the 6.35-mm source and pelleted corn stover were evident prior to pretreatment. After adding acid and mixing for 5 min, the pelleted material did not dissolve into the bulk liquor and remained as distinct pellets in the aqueous phase prior to pretreatment. The source corn stover was very hygroscopic: after mixing for 5 min, no free liquid was observed. However, after pretreatment, the slurries from both the pelleted and source corn stover (Ro = 2.47) were similar, both in color and volume of pretreated solids. Material recovery after pretreatment of the source and pelleted stover was 95.3 ± 5.2% and 102.98 ± 2.2%, respectively. Final sugar yields were normalized to 100% of material recovery.
In the high-solids pretreatment experiments, the corn stover pellets had glucan and xylan contents of 36.1 and 27.2%, respectively. The composition of the source material was similar in glucan content (36.8%) with an increase in measured xylan (32.3%). The increased xylan content of the 6.35-mm ground material may be attributed to the heterogeneous nature of this material and high cob content of the stover bales that were used in this study, rather than as a result of pelleting. Previous work has shown that corn cobs are enriched in xylan relative to other fractions of corn stover Citation[40]. Additionally, sampling and splitting techniques may have contributed to the compositional variations that were observed here.
Xylose yields from pretreatment alone and pretreatment plus enzymatic hydrolysis of washed solids is shown in . Maximum xylose release was achieved at a severity of Ro = 3.29 for both pretreated (80.8 and 78.6%) and enzymatic hydrolysis of washed, pretreated stover (86.5 and 86.1%) for the 6.35-mm source and pellets, respectively. Soluble xylose yield (monomeric plus oligomeric) for both feedstock formats increased with increasing pretreatment severity (Ro = 1.51–3.29) for both pretreatment configurations . Enzymatic hydrolysis of the washed pretreated solids increased xylose yield for all samples compared with pretreatment alone.
Comparison of both feedstock formats revealed no significant differences in xylose yields for either pretreatment alone or pretreatment plus enzymatic hydrolysis, with the exception of Ro = 2.81; xylose yield was approximately 10% higher for pelleted stover compared with source material at this severity based on one-way ANOVA (p < 0.05). The percentage of monomeric xylose of the total xylose yield was higher for the 6.35-mm source relative to the pelleted stover for all severities tested. At the highest pretreatment severity (Ro = 3.29), the percentage of monomeric xylose was 74 and 95% of the total xylose, for the pelleted and source stover, respectively. This is in contrast to the results of the low-solids pretreatment data, which showed higher monomeric xylose yield from the pelleted material. A higher fraction of oligomeric xylose from dilute-acid pretreatment would suggest a less-optimal pretreatment condition. For pretreatment alone, xylose yields for pellets were greater in the low-solids (56%; Ro = 2.1) than the high-solids (31%; Ro = 2.07) pretreatment, but no difference was present for the source material (38%).
Furfural production from the dilute-acid pretreatment of the pelleted and source stover was low for all samples ; concentrations ranged from 0.1 to 4.63 g/l in the condensed flash vapors. The highest furfural concentrations translated to 1.17 and 0.71 g furfural per 100 g of dry wt. Furfural production was higher for the 6.35-mm ground compared with the pelleted stover .
Results for cellulose hydrolysis from combined pretreatment and enzymatic hydrolysis are shown in . Glucose yield increased with increased pretreatment severity, although pretreatment contributed less than 10% to the final glucose yield, primarily monomeric glucose. The majority of glucose was released from enzymatic hydrolysis of the washed solids. Glucose yields were higher in the low-solids (58 and 83%; Ro = 2.1) than the high-solids (49 and 61%; Ro = 2.07) pretreatment for the pretreated source and pelleted materials, respectively. The highest glucose yield was achieved at Ro = 3.29 in the high-solids pretreatment (103 and 98%) for source and pelleted materials, respectively. Glucose yields at this severity overestimated glucose release, given that the accuracy decreases as 100% yield of glucan is approached. Enzymatic hydrolysis of the nonpretreated source and pelleted stover were 11.2 and 19.5%, respectively. Comparing glucose yield across feedstock format using two-way ANOVA, the only statistically significant (p < 0.05) differences occurred at Ro = 2.07, with an approximately 12% increase in glucose yield for the pelleted versus the source stover. For all other severities, there was no difference between the two materials.
Feedstock reactivity is useful for comparing biomass performance across varying pretreatment severities and providing a measure of biomass recalcitrance to a given conversion process and set of conditions. Reactivity is defined as the fraction of the glucose and xylose released from pretreatment and enzymatic hydrolysis, divided by the initial mass of glucose and xylose in the native feedstock. shows the response of the two feedstock formats as a function of combined pretreatment and enzymatic hydrolysis. Results from a two-way ANOVA identified a small but significant increase from pelleting stover at Ro of 2.07, 2.47 and 2.81, with p-levels of 0.00095, 0.01893 and 0.0205, respectively. No difference in reactivity was observed at the lowest severity , and at the highest severity, pellets had slightly lower feedstock reactivity.
Comparison between the low- and high-solids pretreatment at similar severity (Ro = 2.1 vs 2.07, respectively) and identical acid concentration showed different results. The pelleted stover at low-solids pretreatment showed a significant increase in both xylose and glucose yield compared with the high-solids pretreatment. While the severity was similar, different combinations of time and temperature can produce similar, if not identical, severity having different effects on sugar release. While 0.8% H2SO4 (w/w) was used for pretreatment in both the low- and high-solids pretreatment conditions, the increased solids loading (3.3 vs 25% w/w) reduced the acid loading on a per mass basis (mg acid/g dry wt of biomass) for the high-solids pretreatment; the mass of acid per mass of solids was significantly higher in the low-solids pretreatment. These factors would contribute to the yield differences between these two pretreatment regimes .
Xylose and glucose yields obtained from both low- and high-solids pretreatment experiments suggest that pelletizing of corn stover did not increase biomass recalcitrance. Consistent with previous work, increased sugar yields were observed in the pelleted stover, relative to the 6.35-mm source stover, from low-solids pretreatment, and at a few conditions for under high-solids pretreatment and high-solids pretreatment followed by enzymatic hydrolysis Citation[11,13]. However, no clear trend for glucose and xylose release was identified. Feedstock reactivity increased slightly for pelleted stover, relative to the 6.35-mm source material, for three of five pretreatment severities.
▪ Scanning election microscopy
Scanning electron micrographs of native and pelleted corn stover are shown in . These images reveal significant morphological differences between native corn stover source material and pellets, although no specific structural or chemical alterations were identified with SEM that could be attributed to the improved sugar and ethanol yields that were measured during dilute-acid pretreatment and SSF . A recent report examining the effect of pelleting on sugar yields in enzymatic hydrolysis of switchgrass attributed the increased yields to the grinding and heating of biomass prior to pelleting, although no specific mechanisms have been identified Citation[13]. Other factors that may have a role in the improved yields measured here include tissue shearing, mixing and heating that occur during pelleting, which disturb biomass structure and may increase enzyme access to cellulose Citation[11].
▪ Gas adsorption studies
The BET theory of nitrogen adsorption was employed in order to elucidate differences in the surface area, pore volume, and pore diameter of the pelleted corn stover and the corresponding unpelleted source material. Surface area and pore volume of corn stover were lower following pelleting, even if the material was subsequently ground to a 2-mm pellet meal (Bonnferroni p < 0.01; & ). Acid pretreatment of source material and pellets increased surface area and pore volume, compared with untreated source material and pellets (Bonnferroni p < 0.001; & ); however, there was no difference between acid-pretreated source material and acid-pretreated pellets (Bonnferroni p > 0.05; & ). Average pore size increased when corn stover was pelleted and was greatest following acid pretreatment of source corn stover and pellets (Bonnferroni p < 0.01), but there was no significant difference in pore size between acid-pretreated source material and acid-pretreated pellets (Bonnferroni p > 0.05). The increased pore size of the untreated pellet meal (3.59 nm) relative to the 6.35-mm source material (2.90 nm) may provide some basis for the improved TEYs achieved with pellet meal. The measured pore sizes for the pretreated pellets (4.77 nm) and pretreated source material (4.84 nm) are consistent with mesopore sizes required for cellulose accessibility by enzymes Citation[19]. Mesopores larger than 4–5 nm were reported to be associated with the surface area available for enzymatic attack, because smaller pores hinder enzymatic access Citation[41].
Some criticisms to the use of BET gas adsorption for measuring surface area and mesoporosity of biomass and pretreated materials have been reported. The sample preparation and oven drying required for BET analysis may result in decreased surface area and pore volume due to collapse of pore structures during cell wall drying Citation[19,42], thereby reducing the overall nitrogen accessible porosity Citation[41]. For some Ammonia Fiber Expansion (AFEX™) pretreatment conditions, BET analysis has been shown to underestimate surface area by ten- to 15-fold Citation[43,44]. Previous studies have demonstrated that increased specific surface area of pretreated biomass correlates with improved sugar release upon enzymatic hydrolysis Citation[16]. Considering the drawbacks associated with gas adsorption techniques for measuring surface area and pore diameter, along with the demonstrated associations of increased surface area and pore diameter with enhanced sugar yields, it may be possible that this technique was not suitable for the examination of pelleted biomass performed here. Further work is needed to understand the relationship between surface area and pore diameter in pelleted biomass, enhanced xylan removal upon dilute-acid pretreatment and improved ethanol yields in fermentation.
Conclusion
Pelleting corn stover had no adverse impact on pretreatment efficacy, as compared with unpelleted source material for both low-solids pretreatment, and SSF and high-solids pretreatment and enzymatic hydrolysis. Corn stover pellet meal had significantly higher monomeric xylose yields upon dilute-acid pretreatment, and total xylose yields were similar for pellet meal, 6.35- and 2-mm ground material. Solubilized glucan during low-solids pretreatment was similar for all formats examined and consistent with findings from the literature. Pellet meal achieved the highest ethanol yields of the formats tested here. Micrographs from SEM revealed obvious morphological differences among pelleted and unpelleted corn stover. Results from BET gas adsorption studies demonstrated that, although corn stover pellets and pellet meal initially had significantly larger pore diameter than the source material, these differences were not apparent following dilute-acid pretreatment. The combined results suggest that pelleting corn stover does not have a negative impact on pretreatment efficacy. The improved monomeric xylose yields achieved with pellet meal under the low-solids pretreatment condition indicate the potential for a reduction in required pretreatment severity for pelleted biomass; however, further studies will be required in order to elucidate whether the improved monomeric xylose yields are scalable to higher solid loading.
The conditions used for the high-solids pretreatment were representative of process-relevant conditions. Incorporation of mixing, increased severity and higher solid and acid loading for larger scale pretreatment systems resulted in a slight increase in overall sugar yields, as seen in three of the five pretreatment severities. Future work includes pretreatment of pelleted and nonpelleted feedstocks under continuous conditions to further assess the impact of densification on biomass recalcitrance. The enhanced ethanol yield upon fermentation and slightly increased sugar yield upon enzymatic hydrolysis highlight the potential for pelleted biomass to play an important role in the production of biomass-derived fuels beyond the densification-related benefits for storage, handling and transportation.
Future perspective
Densification will play a critical role in the development of the cellulosic bioenergy industry through its impact on transportation, handling and long-term storage of biomass feedstock materials. These systems will be highly location dependent with significant variability in feedstock type, the quantity of available feedstock, the timeframe for harvesting and collecting the feedstock, weather considerations relating to storage options, and the infrastructure restrictions that govern the quantities of biomass that can be transported on the roadways Citation[5]. The monumental task of displacing 30% of the 2004 gasoline use with biofuels by 2030 (60 BGY) will require more than 700 million dry matter tons of lignocellulosic biomass materials, from a diverse variety of resources. Densification provides a uniform size, density and moisture content that will facilitate transport using conventional logistical systems, including the nation’s commodity-scale grain handling systems and storage structures. The increased bulk density of densified materials will allow highly efficient large-capacity transport of commodity-formatted materials. The improved long-term storage characteristic of densified materials is of greatest importance. Bales of biomass material and feedstock resources will be more resilient to unpredictable environmental conditions. This will also minimize the variability of the commodity-scale feedstock resource, promote greater quality assurance of feedstock materials and provide the opportunity to import materials from large supply areas.
Table 1. Pretreatment conditions for high-solids pretreatment experiments using the ZipperClave®.
Table 2. Particle size distribution parameters (mean ± 1 standard deviation; n = 3) of corn stover formats†.
Table 3. Degrees of freedom, F-values and p-values from a one-way analysis of variance for Brunauer–Emmett–Teller surface area, total pore volume and average pore size.
Utilizes mechanical and thermal processing for the agglomeration of small particles into larger particles; a process whereby finely ground biomass can be converted into a dense, flowable and durable product, through application of heat and/or moisture and extrusion of ground material through a die.
Describes the complex structural and chemical nature of plant material that makes it resistant to microbial/enzymatic attack and hinders the depolymerization of structural sugars; there is difficulty in conversion of biomass to soluble sugars.
Microbial-mediated conversion of organic matter into a source of energy (e.g., conversion of biomass to ethanol via fermentation).
Increasing the density of biomass; densification is thought to be a key process in the development of a commodity-scale biomass feedstock supply system.
Results & discussion
▪ Pelleting corn stover did not have a negative impact on the efficacy of dilute-acid pretreatment. In this study, pellet meal produced significantly higher monomeric xylose yields during pretreatment than conventionally ground source material. The improved monomeric xylose yields achieved with pellet meal may offer potential for a reduction in pretreatment severity for pelleted biomass. | |||||
▪ The highest ethanol yields were achieved with pelleted corn stover during simultaneous saccharification and fermentation, which may suggest that the pelleting process increases enzymatic access to cellulose. | |||||
▪ Micrographs from scanning electron microscopy revealed obvious morphological differences among pelleted and unpelleted corn stover. | |||||
▪ Results from gas adsorption studies demonstrated that, although corn stover pellets and pellet meal initially had significantly larger pore diameter than the source material, these differences were not apparent following dilute-acid pretreatment. | |||||
▪ Both pretreatment regimes, low- and high-solids, demonstrated that biomass recalcitrance did not increase as a result of pelleting. In addition, examination of several pretreatment severities at high-solids loading revealed that overall sugar release was higher in the pelleted versus 6.35-mm ground material; however, with increased severity, the two materials showed little difference in overall sugar release. |
Conclusion
▪ These results suggest that pelleting corn stover does not have a negative impact on pretreatment efficacy, and the improved monomeric xylose yields achieved with pellet meal indicate the potential for a reduction in required pretreatment severity for pelleted biomass. The enhanced ethanol yields upon fermentation demonstrate that pelleted biomass holds promise as an important feedstock for the production of ethanol fuels beyond the densification-related benefits for storage, handling and transportation. | |||||
▪ The conditions used for the high-solids pretreatment represent some process-relevant conditions for larger scale pretreatment systems, suggesting that these results may scale to larger continuous pretreatment regimes. |
Acknowledgements
The authors are grateful for technical assistance from numerous colleagues at the Idaho National Laboratory: D Bruhn, C Breckenridge, D Stevens, W Smith, R Emerson, M Phanphanich, C Rae, N Yancey, K Aycock, B Shay, D Pace, C Conner, S Morgan and S Rossberg; and at the National Renewable Energy Laboratory: D Templeton, E Wolfrum and B Gailford.
Financial & competing interests disclosure
This work is supported by the US Department of Energy under Department of Energy Idaho Operations Office Contract No. DE-AC07-05ID14517. The US Government retains and the publisher, by accepting the article for publication, acknowledges that the US Government retains a nonexclusive, paid-up, irrevocable, worldwide license to publish or reproduce the published form of this manuscript, or allow others to do so, for US Government purposes. The authors have no other relevant affiliations or financial involvement with any organization or entity with a financial interest in or financial conflict with the subject matter or materials discussed in the manuscript apart from those disclosed.
No writing assistance was utilized in the production of this manuscript.
References
- Energy Independence and Security Act of 2007. Public Law 110–140 (2007).
- Perlack RD, Stokes BJ. US Billion-Ton Update: Biomass Supply for a Bioenergy and Bioproducts Industry. US Department of Energy, Oak Ridge National Laboratory, Oak Ridge, TN, USA, 227 (2011).
- Hess JR, Foust TD, Hoskinson R, Thompson D. Roadmap for Agriculture Biomass Feedstock Supply in the United States. US Department of Agriculture, Washington, DC, USA, 97 (2003).
- Hess JR, Wright CT, Kenney KL. Cellulosic biomass feedstocks and logistics for ethanol production. Biofuel. Bioprod. Bioref.1(3),181–190 (2007).
- Hess J, Wright C, Kenney K, Searcy E. Uniform-Format Solid Feedstock Supply System: A Commodity-Scale Design to Produce an Infrastructure-Compatible Bulk Solid from Lignocellulosic Biomass – Executive Summary. Idaho National Laboratory, Idaho Falls, ID, USA (2009).
- Larsson SH, Thyrel M, Geladi P, Lestander TA. High quality biofuel pellet production from pre-compacted low density raw materials. Bioresour. Technol.99(15),7176–7182 (2008).
- Kaliyan N, Morey RV. Natural binders and solid bridge type binding mechanisms in briquettes and pellets made from corn stover and switchgrass. Bioresour. Technol.101(3),1082–1090 (2010).
- Mani S, Tabil LG, Sokhansanj S. Effects of compressive force, particle size and moisture content on mechanical properties of biomass pellets from grasses. Biomass Bioenerg.30(7),648–654 (2006).
- Mani S, Tabil LG, Sokhansanj S. Specific energy requirement for compacting corn stover. Bioresour. Technol.97(12),1420–1426 (2006).
- Tumuluru JS, Wright CT, Hess JR, Kenney KL. A review of biomass densification systems to develop uniform feedstock commodities for bioenergy application. Biofuel. Bioprod. Bioref.5(6),683–707 (2011).
- Theerarattananoon K, Xu F, Wilson J et al. Effects of the pelleting conditions on chemical composition and sugar yield of corn stover, big bluestem, wheat straw, and sorghum stalk pellets. Bioproc. Biosyst. Eng.35(4),615–623 (2012).
- Himmel ME, Ding SY, Johnson DK et al. Biomass recalcitrance: engineering plants and enzymes for biofuels production. Science315(5813),804–807 (2007).
- Rijal B, Igathinathane C, Karki B, Yu M, Pryor SW. Combined effect of pelleting and pretreatment on enzymatic hydrolysis of switchgrass. Bioresour. Technol.116,36–41 (2012).
- Karunanithy C, Muthukumarappan K. Effect of extruder parameters and moisture content of switchgrass, prairie cord grass on sugar recovery from enzymatic hydrolysis. Appl. Biochem. Biotech.162(6),1785–1803 (2010).
- Shi J, Thompson VS, Yancey NA, Stavila V, Simmons BA, Singh S. Impact of mixed feedstocks and feedstock densification on ionic liquid pretreatment efficiency. Biofuels4(1),63–72 (2013).
- Guo G-L, Chen W-H, Chen W-H, Men L-C, Hwang W-S. Characterization of dilute acid pretreatment of silvergrass for ethanol production. Bioresour. Technol.99(14),6046–6053 (2008).
- Chen W-H, Pen B-L, Yu C-T, Hwang W-S. Pretreatment efficiency and structural characterization of rice straw by an integrated process of dilute acid and steam explosion for bioethanol production. Bioresour. Technol.102(3),2916–2924 (2011).
- Chesson A, Gardner PT, Wood TJ. Cell wall porosity and available surface area of wheat straw and wheat grain fractions. J. Sci. Food Agric.75(3),289–295 (1997).
- Adani F, Papa G, Schievano A, Cardinale G, D’Imporzano G, Tambone F. Nanoscale structure of the cell wall protecting cellulose from enzyme attack. Environ. Sci. Technol.45(3),1107–1113 (2010).
- Yancey NA, Wright CT, Conner CC, Tumuluru JS. Optimization of preprocessing and densification of sorghum stover at full-scale operation. In: Proceedings of the ASABE 2011 Annual International Meeting. American Society of Agricultural and Biological Engineers, Louisville, KY, USA (2011).
- American Society of Agricultural and Biological Engineers. S269.4. Cubes, Pellets, and Crumbles-Definitions and Methods for Determining Density, Durability, and Moisture Content. American Society of Agricultural and Biological Engineers, St Joseph, MI, USA (2007).
- BSI. EN 15210-15211:2009 – Solid Biofuels – Determination of Mechanical Durability of Pellets and Briquettes. BSI, London, UK (2010).
- ASTM. D5865-10a. Standard Test Method for Gross Calorific Value of Coal and Coke. ASTM, Philadelphia, PA, USA (2010).
- Miller NA, Henderson JJ. Quantifying sand particle shape complexity using a dynamic, digital imaging technique. Agron. J.102(5),1407–1414 (2010).
- ISO. 13322-13322. Particle Size Analysis – Image Analysis Methods – Part 2: Dynamic Image Analysis Methods. ISO, Geneva, Switzerland (2006).
- National Renewable Energy Laboratory. NREL Standard Biomass Analytical Procedures 2011. National Renewable Energy Laboratory, Golden, CO, USA (2011).
- Sluiter A, Hames B, Ruiz R et al.Determination of Structural Carbohydrates and Lignin in Biomass: Laboratory Analytical Procedure. National Renewable Energy Laboratory, Golden, CO, USA (2008).
- Duguid KB, Montross MD, Radtke CW, Crofcheck CL, Shearer SA, Hoskinson RL. Screening for sugar and ethanol processing characteristics from anatomical fractions of wheat stover. Biomass Bioenerg.31(8),585–592 (2007).
- Sluiter A, Hames B, Ruiz R, Scarlata C, Sluiter J, Templeton D. Determination of Sugars, Byproducts, and Degradation Products in Liquid Fraction Process Samples: Laboratory Analytical Procedure. National Renewable Energy Laboratory, Golden, CO, USA (2008).
- Dowe N, Mcmillan J. SSF Experimental Protocols-Lignocellulosic Biomass Hydrolysis and Fermentation: Laboratory Analytical Procedure. National Renewable Energy Laboratory, Golden, CO, USA (2008).
- Weiss ND, Nagle NJ, Tucker MP, Elander RT. High xylose yields from dilute acid pretreatment of corn stover under process-relevant conditions. Appl. Biochem. Biotechnol.155,418–428 (2009).
- Weiss ND, Farmer JD, Schell DJ. Impact of corn stover composition on hemicellulose conversion during dilute acid pretreatment and enzymatic cellulose digestibility of the pretreated solids. Bioresour. Technol.101(2),674–678 (2010).
- R Development Core Team. R: A Language and Environment for Statistical Computing. R Foundation for Statistical Computing, Vienna, Austria (2012).
- Igathinathane C, Melin S, Sokhansanj S et al. Machine vision based particle size and size distribution determination of airborne dust particles of wood and bark pellets. Powder Technol.196(2),202–212 (2009).
- Templeton D, Sluiter A, Hayward T, Hames B, Thomas S. Assessing corn stover composition and sources of variability via NIRS. Cellulose16(4),621–639 (2009).
- Lloyd TA, Wyman CE. Combined sugar yields for dilute sulfuric acid pretreatment of corn stover followed by enzymatic hydrolysis of the remaining solids. Bioresour. Technol.96(18),1967–1977 (2005).
- Wyman CE, Dale BE, Elander RT, Holtzapple M, Ladisch MR, Lee YY. Comparative sugar recovery data from laboratory scale application of leading pretreatment technologies to corn stover. Bioresour. Technol.96(18),2026–2032 (2005).
- Thompson DN, Chen H-C, Grethlein HE. Comparison of pretreatment methods on the basis of available surface area. Bioresour. Technol.39(2),155–163 (1992).
- Zhan X, Wang D, Bean SR, Mo X, Sun XS, Boyle D. Ethanol production from supercritical-fluid-extrusion cooked sorghum. Ind. Crop Prod.23,304–310 (2006).
- Decker SR, Sheehan J, Dayton DC et al. Biomass conversion. In: Kent and Riegel’s Handbook of Industrial Chemistry and Biotechnology. Kent JA (Ed.). Springer-Verlag, New York, NY, USA, 1449–1548 (2007).
- Chesson A. Plant degradation by ruminants: parallels with litter decomposition in soils. In: Driven by Nature: Plant Litter Quality and Decomposition. Cadisch G, Giller KE (Eds). CAB International, Wallingford, UK, 52–65 (1997).
- Papadopoulos AN, Hill CAS, Gkaraveli A. Determination of surface area and pore volume of holocellulose and chemically modified wood flour using the nitrogen adsorption technique. Eur. J. Wood Wood Prod.61(6),453–456 (2003).
- Chandra RP, Esteghlalian AR, Saddler JN. Assessing substrate accessibility to enzymatic hydrolysis by cellulases. In: Characterization of Lignocellulosic Materials. Hu T (Ed.). Blackwell Publishing Ltd, Oxford, UK, 60–80 (2009).
- Chundawat SPS, Donohoe BS, da Costa Sousa L et al. Multi-scale visualization and characterization of lignocellulosic plant cell wall deconstruction during thermochemical pretreatment. Energ. Environ. Sci.4(3),973–984 (2011).