Abstract
Fouling of heat exchangers in the chemical industry, oil & gas industry, district heating, power plants, among others, results in a loss of performance which leads to production stops for cleaning and therefore increased operation costs. One approach to mitigate fouling is to alter the properties of the metal surface. A coating to be successful in any plate heat exchanger (PHE) application needs to have a good adhesion to the metal but also keep the heat transfer through the metal plates as unaltered as possible. This requires a thin coating with a relatively good thermal conductivity. The plates in a PHE are subjected to plate-to-plate contact point wear when in operation which also puts an extra requirement for the coating. To be suitable, the coating needs to have a good mechanical stability to resist this plate-to-plate wear. Alfa Laval has a long experience in coating plates for diverse applications and in this paper two case studies will be presented. One in the paper industry and the other in the biofuel industry. A new type of multilayer Teflon™ coating from Chemours was used, specifically designed to show excellent fouling release properties along with limited thicknesses (30–50 microns).
Disclosure statement
No potential conflict of interest was reported by the author(s).
Additional information
Notes on contributors
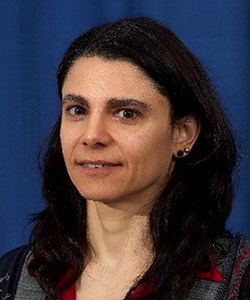
Olga Santos
Olga Santos received Diploma in Chemical Engineering (Instituto Superior Tecnico, Lisbon, Portugal, 1999), Ph.D. in Food Engineering (Lund University, Sweden, 2004) as a part of an EU project where different coatings were applied onto stainless steel with the aim at reducing fouling of heat exchangers in the dairy industry. Over 20 years of research experience in the field of fouling (proteins, milk, water, etc.), cleaning and anti-fouling coatings. More than 10 years of experience with plate heat exchangers, both in failure investigations (corrosion, fatigue) and in fouling control/prevention. Adjunct lecturer at the department of physical chemistry at Lund university since July 2021 working mainly with surface chemistry. Areas of expertise are solid surface characterization, interactions of polymers, proteins and salts at solid surfaces, coating systems suitable for application onto plate heat exchangers. Currently working as a Material Specialist at the Materials Technology and Chemistry R&D lab at Alfa Laval in Sweden.
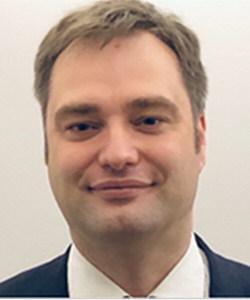
Nico Smets
Nico Smets is the global technology manager for TeflonTM coatings at Chemours, focusing on providing nonstick, resistant, and sustainable solutions for the industry. Prior to Chemours, he served in R&D management roles within the coating sector for Eastman Chemical and PPG. His experience spans various coating chemistries and applications for industrial markets. He has a master’s degree in chemical engineering from the University of Antwerp.
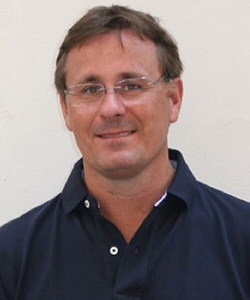
Clemens Wictor
Clements Wictor has a B.Sc. in Mechanical Engineering (HTH, Halmstad, 1999), with a technical background in mechanical engineering of heat exchanger technology and material handling technology. Main competencies are in product development and project management. Area of expertise is in mechanical engineering focusing on design of gasketed plate heat exchanger frames and channel plates including pressure vessel calculations according to EN13445 (PED) and ASME code. Project managing focus has been technology development projects from idea phase to technical proof of concept including lab testing and setting up field test installations at customer’s sites and projects to improve gasketed plate heat exchangers performance in terms of reduced fouling and improved corrosion resistance. Currently working as Industrialization Project Manager with focus on Alfa Laval’s food and pharma technology development projects and global manufacturing setup for Alfa Laval´s pharma heat exchangers.
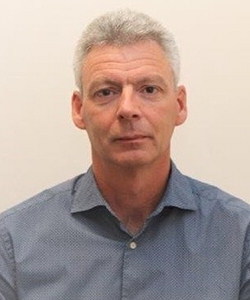
Magnus Nilsson
Magnus Nilsson received the M.Sc. degree from the Mechanical Engineering Department, Lund University in 1994. He has Several years of managing experience in different R&D departments in various product groups within Alfa Laval, focusing on building innovative culture and strong competitive product portfolios. Current role, Head of Technology Development GPHE (Gasketed Plate Heat Exchanger) with focus not only to further develop the GPHE portfolio by using new technologies but also exploring new applications areas to apply Alfa Laval core technologies.