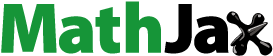
ABSTRACT
There is plethora of parameters to take into consideration during designing of the 2D MXene. Some of them are crucial for obtaining particular morphology others are important for purity and surface chemistry. While the latter mainly corresponds to Mene etching and delamination, the first and second ones are critical from material design point of view. In other words, how we synthesise and prepare the MAX phase truly determines the efficiency and feasibility of the process of MXene synthesis. Therefore, these two (MAX and MXene) stages are considered in this study as a step-wise aporoach in which changing of each single parameter may highly influence the final product. As can be seen, preparation of the MXene materials with repeteable features and properties is a great challenge that needs special attention in the upcoming future.
KEYWORDS:
Introduction
Since the discovery of the unique properties of graphene, the interest in two-dimensional (2D) materials has greatly increased [Citation1]. There are already recognised basic characteristics of materials characterised by a two-dimensional (2D) crystal structure. The family of 2D materials is still expanding and can be divided into several smaller groups i.e.: transition metal dichalcogenides (e.g. MoS2, WS2, MoSe2, WSe2, MoTe2, WTe2) [Citation2], nitrides (e.g. GaN, h-BN, h-AlN, h-GaN, Ca2N) [Citation3], di-transition metal sulphides, selenides and phosphides (e.g. Zr2S, Hf2S, Ti2S, Ti2Se, Zr2Se, Hf2Se, Ta2P, Ta2P, W2P, Nb2P, etc.) [Citation3,Citation4], organic materials (e.g. organic and metal-organic covalent frameworks) [Citation5], metal oxides and hydroxides [Citation6,Citation7], Xenes (e.g. graphene, phosphorene, borophene, silicene, stanene, germanene) [Citation8], as well as MXenes (e.g. Ti2C, Ti3C2, Ti4C3, Ti2N, etc.) [Citation9].
The youngest member of this group, as well as one of the most exciting from those mentioned above, is the MXenes. They can also be named as early transition metal carbides, nitrides, carbonitrides and their hybrids. They were first discovered in 2011 by Michael Naguib, Michel Barsoum and Yuri Gogotsi from Drexel University, USA [Citation10]. They are obtained from the so-called MAX phases [Citation11] and are characterised by many intriguing properties [Citation9]. The individual stages of MXene preparation are summarised in .
In this work, we discuss the challenges in the management of MAX phase properties for future applications in MXenes technology. This journey begins with the parent MAX phases that are the starting materials for the preparation of MXenes. Methods of their synthesis and their properties can have a huge impact on the bioactive properties of their derivatives – MXenes. Also, the purity of the reactants, the phase composition of the product of synthesis, the course of the grinding process, etching as well as the delamination processes are considered to influence properties of the final 2D flakes.
The parent MAX phases
MAX phases are also named ‘Nowotny-phases’ due to the work of Hans Nowotny in the 1960s [Citation12,Citation13] or ternary ‘T-phases’, ‘H-phases’ or ‘Hagg-phases’ [Citation13–15]. The group of Nowotny described over 100 carbides and nitrides. The research on Nowotny phases was boosted around the mid-1990s, when a group of Michel W. Barsoum synthesised almost single-phase Ti3SiC2. The innovative material was called the ‘MAX phase’ [Citation11,Citation16]. It should be noted that ‘MAX phase’ reflects the composition of the material i.e. Mn+1AXn, where M is an early transition metal (e.g. Ti); A is a metal of group 13 or 14 (e.g. Al or Si); X is carbon or/and nitrogen atoms; while; n = 1, 2, and 3 or even higher. The n = 4 allows preparation of ‘514ʹ phases such as e.g. (Ti0.5, Nb0.5)5AlC4 [Citation17]. In fact, the obtained (Ti0.5, Nb0.5)5AlC4 MAX phase is the mixture of other numerous phases, mostly of a nonlayered structure.
Structures of the MAX phases can be systematised into six individual groups of the M2AX (phase 211), M3AX2 (phase 312), M4AX3 (phase 413), M5AX4 (phase 514), M6AX5 (phase 615), and M7AX6 (phase 716) [Citation18] (the crystal structure of phases 211, 312 and 413 is shown in ). All of them can be described as hexagonal unit cells of the M6X octahedral of the P63/mmc space group, interleaved with single 2D layers composed of the A element. It should also be noted that the M6X octahedra are twinned with respect to each other. It has been shown that the 211 phases are characterised by the lattice parameters of a ~ 3 Å and c ~ 13 Å. Whereas the 312 phases c ~ 18 Å; and c ~ 23–24 Å for the 413 phases [Citation17]. Thus, it can be seen that these materials are generally anisotropic. Due to the presence of covalent-metal-ion bonds, MAX phases are, like ceramics, characterised by good oxidation stability, thermal stability, a relatively high melting point and high strength properties. Like metals, they show good electrical and thermal conductivity, good resistance to thermal shocks, resistance to abrasive wear and are relatively easily machined [Citation18–21]. Such a diverse set of MAX phase properties predisposes them to many applications, i.e.: protective barriers, materials for work at elevated temperatures, abrasion-resistant materials and many others [Citation22–26].
The family of MAX phases has developed vigorously since boosting the research by Professor Barsoum and co-workers. Since then many other MAX phases have been explored e.g.: Ti2CdC, Ti2GaC, Ti2GaN, Ti2InN, Zr2InN, or Nb2GaC [Citation24]. Processes for the MAX phase preparation are carried out using various techniques [Citation25,Citation26]. These methods can be divided into those which incorporate stoichiometric mixtures of elements (powders) [Citation27] as well as techniques for thin films preparation [Citation28,Citation29]. In this study, the most interesting are the methods that allow the obtaining of MAX phases in the form of powders because the powders are the starting material for the production of MXene phases.
MAX phase preparation of the powders and bulk materials includes such methods as Hot pressing (HP) [Citation30,Citation31], Hot isostatic pressing (HIP) [Citation32], Slip casting (SC) [Citation33], Self-propagating high-temperature synthesis (SHS) [Citation34–36], Pressure-assisted self-propagating high-temperature synthesis (PSHS) [Citation14,Citation37], as well as Spark Plasma Sintering (SPS) [Citation38] and Mechanical alloying (MA) [Citation39,Citation40]. For all of these methods, the content of component A is extremely important. This component is reactive at high temperature and undergoes partial oxidation and evaporation, which usually forces it to be added in some excess. In Ti/Al/C systems this component is Al. The appropriate proportion of Al and the ratio of Al/C allows obtaining MAX phases with high purity. The most viable problem with their synthesis mentioned above is purity. It is, however, widely known that every single batch of MAX material is a de facto mixture of different phases of unique mass composition that is usually difficult to repeat. The mentioned methods usually involve mixing precursor powders in an appropriate molar ratio, which is then processed with the chosen method. The most widely used method for the preparation of MAX phases is the SHS method. This method allows the production of large amounts of material; however, the synthesis product is usually porous, which predisposes the SHS method to the production of powders rather than dense materials. For the preparation of the Ti3AlC2 MAX phase, it involves mixing elemental powders (Ti, Al and graphite) or Ti3Al with graphite powder and subsequent pressing to enable better control over the SHS process.
However still, after ignition, the development of the highly exothermal synthesis is practically uncontrollable. The parameters of temperature and soaking time cannot be controlled and are unrepeatable [Citation11]. It should be noted that the purity of the powders used is also a matter of concern due to the fact that every additional element will also be transferred to the final MXene [Citation41]. Then, the equipment used needs to enable the local ignition so that the reaction can self-propagate until the substrates are fully consumed. Moreover, the final composition of the MAX material obtained after a particular process relates to many factors and also strictly depends on the applied method of synthesis () [Citation42]. For example, in the case of Ti3AlC2 and Ti2AlC, the SHS process is the kind of equilibrium in which the thermodynamic stability of Ti3AlC2 and Ti2AlC is different depending on process conditions. Bai et al. [Citation43] revealed the reaction mechanism in which Ti3AlC2 is formed together with the presence of Ti2AlC. It should be noted that the energy for TiC formation is rather low so that it forms easily. After the formation of octahedral Ti6C two different reaction paths occur that compete thermodynamically with each other. The first one leads to the Ti2AlC which is also thermodynamically more stable in relation to Ti3AlC2. Then, the Ti2AlC directly transforms into Ti3AlC2 which is indeed difficult especially since this is an additional step in the reaction pathway. The second path leads from Ti6C octahedral to TiC, which in turn transforms into Ti3AlC2.
Table 1. Synthesis conditions and phase composition of MAX phase. Adopted from [Citation42].
In addition to Ti3AlC2, a large amount of Ti2AlC is present in the final product as well as cubic TiC. When we consider a mixture of elemental powders (i.e. Ti, Al and C), in this Ti-Al-C system the first action that occurs is the exothermic reaction between Ti and Al. Subsequently, the exothermic reaction in the Ti–C system is induced and thus generates a high temperature. Due to the presence of high temperatures, the Ti-Al liquid is formed. The previously formed TiC is dissolved and the Ti-Al liquid is further formed. Finally, the Ti3AlC2 is formed between the TiC and the molten Ti-Al. As can be seen, the final product consists of Ti3AlC2, Al3Ti as well as TiC and the wt% of the Ti3Al2 is usually far below 80% [Citation38]. Ti3SiC2 is the second most frequently studied system. In this case, the Ti3SiC2 reaction path runs through the intermediate phases. Carbon and silicon diffuse into titanium and form TiCx and Ti5Si3Cx, these phases, in turn, react to form Ti3SiC2 [Citation44].
The best method to control MAX phase synthesis parameters is the Spark Plasma Sintering (SPS) technique. The SPS method is usually used for reactive sintering of dense MAX phases. However, applying modifications to the die allows the obtaining of porous MAX phases that are later easier to granulate to powder. This solution makes the synthesis process very similar to the SHS method with the difference that it is possible to control the parameters of the process.
As can be seen from the literature data, summarised in , the SPS method allows the synthesis of almost pure MAX phases (of course with strict control of the contributions of individual components of the synthesis reaction). The purity of the MAX phases after the synthesis process is extremely important due to the quality of the final product, which are the MXene phases. As can be seen, all of the unwanted reaction by-products can be present in the final MAX phase. They can also be present in the MXene (if not all Al3Ti is dissolved in hydrofluoric acid) as well as probably – in 2D flakes e.g. small amounts of cubic TiC are attached to edges of 2D flakes. Therefore, it is not only necessary to select and optimise the MAX phase synthesis parameters, but also subsequent processes. Usually, the grinding process is carried out after the synthesis step. This conducted in a rotary-vibratory or planetary mill in a chosen solvent (e.g. isopropanol) [Citation30]. WC balls are used as a milling medium. Due to the fact that the obtained MAX phase is a hard type of material, the problem of surface abrasion of the used milling balls should be minimised. It should be, however, noted that both milling balls, as well as a container in which the product is placed, can be subjected to surface-abrasion during the milling process. Accordingly, optimisation of the grinding parameters is very important. Nevertheless, the final product is usually contaminated with materials used for grinding. In the milling process, it is also extremely important to obtain particles of the right size. In paper [Citation45] the influence of Ti3AlC2 particle size on the production process of MXene phases was proved. The reduction in particle size from 53 to 38 µm allowed to reduce etching (50% HF) time from 19 to 2 hours. The same nature of changes was also observed for other MAX phases [Citation46].
Table 2. Synthesis of Ti3AlC2 MAX phase using Spark Plasma Sintering (SPS) process with different conditions and starting materials. Adopted from [Citation33].
The synthesis of the MAX phase’s thin films can also be carried out using several different techniques. These include physical vapour deposition (PVD) [Citation20,Citation47,Citation48], chemical vapour deposition (CVD) [Citation49,Citation50], and Solid-state reactions (SR) [Citation51,Citation52]. There is also a lot of room for research on Atomic Layer Deposition (ALD) which should enable the control to the MAX phases structure on the level of layer-by-layer deposition [Citation53,Citation54]. The first and most commonly used method of synthesising MAX thin film is the CVD method. Already in 1972, Nickl et al. studied the possibility of the synthesis of Ti3SiC2 by CVD using TiCl4-SiCl4-CCl4-H2 as precursors and introduced a deposition ternary diagram at 1200°C and 100,000 Pa. The second most commonly used method for the synthesis of MAX film is the PVD method. This method involves sputtering material from a target and then depositing it on the substrate. So far, such phases as Ti3SiC2, Ti3GeC2, Ti2AlN and V2AlC have been obtained by PVD method [Citation50,Citation51,Citation55,Citation56].
As can be seen, the optimisation of the MAX phase’s synthesis for high repeatability is an additional challenge for technologists. This also includes the synthesis of MAX phases of thin films [Citation57,Citation58]. However, when taking into consideration the aspect of purity, there is no doubt that the MAX thin films prepared using e.g. PVD processes are characterised with much higher purity in comparison to bulk MAX phases. The reason is the number of processing steps to which MAX phases’ precursors and final products are subjected. In the case of the PVD process, the only critical step in which impurities can be incorporated into the final material involves the process of vapour deposition that is also connected with the purity of the starting targets.
Parent non-MAX phases
Several studies also revealed the possibility of synthesising MXenes from types of starting materials other than MAX phases. This allows a significant expansion of the number of obtainable materials with better properties than, e.g. Ti3C2. One of such materials is Zr3C2Tx which shows much higher thermal stability, up to 1200 °C, compared to Ti3C2Tx (800 °C) [Citation59]. Others also analysed other MXene obtained from non-MAX phase precursors. Meshikian et al. [Citation60] reported the preparation of the Mo2C MXene by the etching of gallium layers from a parent Mo2Ga2C ternary metal carbide. It should be noted that the Mo2Ga2C cannot be considered as the MAX phase due to the composition of Mn+1An+1Xn instead of Mn+1AXn. It is presumed that the Mo2C MXene is a promising thermoelectric material [Citation61]. These materials were also studied by other authors [Citation62,Citation63]. Subsequently, Zhou et al. [Citation33] synthesised Zr3C2 MXene from Zr3Al3C5 by etching energetically-favourable Al3C3 layers contrary to only aluminium. In this case, the non-MAX phase Zr3Al3C5 material was characterised with a different composition i.e. Mn+2An+2Xn. Exciting research was presented by Zha et al. [Citation64] They attempted to obtain Hf3C2 from Hf3Al4C6. However, as a result of etching with HF, they obtained cubic HfC. This is due to the presence of strong Hf-C bonds. To obtain MXene, they added a small amount of Si to HF-Al-C to form Hf3[Al(Si)]4C6. As a result of selective etching of [Al(Si)]4C4, they obtained Hf3C2-MXene.
Synthesis of MXenes
The synthesis of MXene phases was developed by Naguib et al. [Citation65]. In the MAX phases, the element A is more reactive than MX; therefore, it can be etched using aqueous solution of HF acid. In the case of Ti3AlC2 phases, the reactions during etching occur as follows:
According to reaction 1, the HF reacts with Al to form AlF3, which is then removed with distilled water during the powder washing. The Al place is occupied by functional groups -OH, = O and/or -F (reaction 2 and 3). The process of MXene phases synthesis is schematically shown in .
Figure 3. Scheme of MXene synthesis from MAX phases [Citation65].
![Figure 3. Scheme of MXene synthesis from MAX phases [Citation65].](/cms/asset/344a5236-b47e-4ca3-b4df-1064966ac9be/ymte_a_1968102_f0003_b.gif)
The factors affecting the synthesis of MXene from MAX phases are particle size, etching time and acid concentration. All of these factors affect the efficiency of the process and the structure of the finished product. In addition, the type of MAX phases also have a great impact on the synthesis process. The number of layers n and the type of element M affect the conditions of the etching process. Higher M-A binding energy and more layers require a higher acid concentration and/or longer etching time. In the final step, two methods are used to separate the exfoliated MXene into single flakes. The first is to sonicate the exfoliated MXene in isopropanol or methanol. Due to the relatively strong bonds between the individual layers, the sonication process gives low efficiency. In addition, the obtained layers are significantly fragmented, which makes it impossible to obtain large flakes. The second method is intercalation that breaks the bonds between the layers and separates them from each other. This method has been successfully applied to the delamination of Ti3C2Tx by Mashtalir et al. [Citation66]. As mentioned above, the parameters of the individual synthesis steps affect the structure and properties of the obtained MXene phases. Shortening the etching time translates into a reduction of surface oxidation and a decrease in the formation of defects. This in turn has a significant influence on the electrical conductivity of the MXene phases. In general, the smaller the defect concentration and the larger the flake size, the higher the electrical conductivity. This can be achieved through mild etching conditions and the elimination of the sonication step from the delamination process [Citation9].
The resulting family of MXenes
MAX phases are considered as the primary starting material for MXenes. The unique feature of these materials applicable for the 2D-world is that the M-X bonds are strong of a covalent-metallic-ionic character and the M-A bonds are much weaker. According to this, these materials are described as 2D layers (having the composition of Mn+1Xn) chemically linked via layers of the A element [Citation30]. The already identified MXenes were presented in . Several new types of MXenes phases with not only single metal but also with several metals or with carbon and nitrogen (carbonitrides) can now be distinguished. More specifically, the original division of the MXenes has been expanded into new types of structures.
Figure 4. The family of Mn+1Xn phases characterised with the formulas of M2X, M3X2, and M4X3 (i.e. M = early transition metal; X = C and/or N, NA = not available) were categorised as following: mono-M elements; solid solution of M elements, as well as ordered double-M elements. Also, the solid solutions of the X element result in obtaining carbonitrides (i.e. C,N) [Citation67,Citation68].
![Figure 4. The family of Mn+1Xn phases characterised with the formulas of M2X, M3X2, and M4X3 (i.e. M = early transition metal; X = C and/or N, NA = not available) were categorised as following: mono-M elements; solid solution of M elements, as well as ordered double-M elements. Also, the solid solutions of the X element result in obtaining carbonitrides (i.e. C,N) [Citation67,Citation68].](/cms/asset/296d349d-28bf-43a4-b342-16efe15e8809/ymte_a_1968102_f0004_oc.jpg)
The family was primarily divided into three different formulas of M2X, M3X2, and M4X3 (i.e. M = early transition metal; X = C and/or N). These correspond to the aforementioned groups of the 211, 312, and 413 stoichiometries. Subsequently, the MXenes phases can be further categorised into mono-M elements, a solid solution of two different M elements as well as ordered double-M elements. The mono-M elements correspond to the simple compositions of e.g. Ti3C2, Ti2C, and Nb4C. More complicated systems include a solid solution of a minimum of two different M elements. These include (Ti,V)3C2 or (Cr,V)3C2. The situation in which one transition metal occupies the perimeter layers and another fills the central M layers was recognised and connected with MAX phases characterised by the presence of ordered double-M elements. The examples are related to Mo2TiC2 or Mo2Ti2C3 [Citation9,Citation33,Citation68–70]. In these MAX phases, molybdenum atoms occupy the outer M layers whereas titanium atoms occupy central M layers. It should be also remembered that the additional variations of the possible compositions come from the X-element. The presence of both carbon and nitrogen in interleaving X layers results in obtaining carbonitrides e.g. Ti3(C,N)2.
Modification of MXenes surface
Recently, there has been a growing interest in surface modification of MXene phases. Such solutions have already been used in the case of other materials. Li and co-authors modified the surface of carbon nanotubes by electroless plating to make them magnetic [Citation71]. In addition, Wozniak and co-authors researched surface modifications of multilayer graphene and graphene oxide by Ni-P, and Al2O3 coating, respectively [Citation72–74]. The work aimed to improve composites’ mechanical and tribological properties reinforced with modified phases through a better bonding at the matrix–reinforcement interface. Similar assumptions were used by others authors for the MXene phases. Petrus et al. applied a coating containing 3% Y2O3 and 3% Al2O3 using the sol-gel method on the Ti3C2 surface [[Citation75]]. The microstructure of the powder before and after the modification process is shown in . As a result of the research, they found that the application of surface modification affects the stability of Ti3C2 particles in a solution of water and isopropanol (). Coated particles had greater stability in water and slightly lower in isopropanol compared to uncoated particles. Moreover, they did not observe significant differences between the water and isopropanol stability for the coated particles.
Figure 5. Microstructure of powders a) Ti3C2-MXene unmodified, b) Ti3C2-MXene modified with Y2O3 and Al2O3 [Citation75].
![Figure 5. Microstructure of powders a) Ti3C2-MXene unmodified, b) Ti3C2-MXene modified with Y2O3 and Al2O3 [Citation75].](/cms/asset/c75ed126-8290-4ee6-afa7-e8de3f22f0ed/ymte_a_1968102_f0005_b.gif)
Figure 6. Zeta potential od Ti3C2Tx and modified Ti3C2Tx in different solutions [ [Citation75]].
![Figure 6. Zeta potential od Ti3C2Tx and modified Ti3C2Tx in different solutions [ [Citation75]].](/cms/asset/0ce3b2cd-875f-446b-8106-30d1ee128354/ymte_a_1968102_f0006_oc.jpg)
The use of particles with Al2O3/Y2O3 coating in composites based on SiC improved the mechanical properties compared to composites with unmodified MXene. Moreover, a change in the phase composition of the obtained composites was observed. In the case of sinters containing modified MXene, a greater content of the α-SiC phase was observed. The authors explain the increase in the content of the α-SiC phase by the presence of a liquid phase resulting from the reaction of Al2O3-TiO2 and Y2O3-TiO2. The mechanism of MXene degradation during the composite sintering process has also changed. Both composites with the addition of modified and unmodified MXene exhibit carbon structures resulting from the degradation of MXene. However, they are less defective in composites reinforced with modified MXene. The authors explain the change in the mechanism of MXene decomposition by the presence of oxides deposited on the MXene surfaces. Their presence is expected to increase the amount of the liquid phase and accelerate the diffusion of Ti from inside the MXene. As a result, a faster ordering of the remaining carbon structure can take place.
Similar research results were presented by Cygan at all [Citation76]. The authors produced Al2O3 composites reinforced with Ti3C2 unmodified and covered with Mo and Ti coatings. As a result of the sintering process of Al2O3 with the addition of two-dimensional Ti3C2 phases at the temperature of 1300 °C, MXene particles were completely degraded. In addition, despite the high density of sinters, it was not possible to perform hardness and KIC measurements using the indenter method due to the high brittleness of the material. To minimise the oxidation effect of MXene, the particles were covered with metallic, Ti, and Mo coatings. The coatings were applied with the PVD method. In the case of sinters with surface-modified MXene phases, graphite-like structures were observed apart from the TiC phase (). This proves that the oxidation mechanism of Ti3C2 particles has changed. The authors explain that the formation of such structures occurs during MXene degradation without oxygen. In addition, they observed an increase in hardness of about 10% and 15% in the case of KIC for sinters with the addition of surface-modified MnSe compared to pure Al2O3. The improvement of mechanical properties is related to carbon structures that act as a reinforcing phase (similar to MLG).
Figure 7. Microstructure of the Al2O3 sinter with the addition of Ti3C2-Mo a-b) 1 wt.%, C) 2 wt.% and EDS analysis [Citation76].
![Figure 7. Microstructure of the Al2O3 sinter with the addition of Ti3C2-Mo a-b) 1 wt.%, C) 2 wt.% and EDS analysis [Citation76].](/cms/asset/c3500d9c-02dd-4cff-a1e1-881f6760d027/ymte_a_1968102_f0007_oc.jpg)
The basis of the presented studies can be concluded that the surface modifications of MXene phases contribute to improving their stability at elevated temperatures and allow the shape of the properties of composites with their participation.
Applications of MXenes
Due to its unique 2D structure and excellent properties, MXene is used in energy storage, biomedicine, electronics, photonics, and catalysis. There are also reports of the use of MXene as a reinforcement phase in composites based on polymer, metal and ceramic matrix [Citation76–84]. However, a major problem in the production of composites is the low thermal stability of MXene. Despite the low thermal stability and the difficulty of preserving MXene in consolidated composites. It is possible to shape the microstructure and strength properties of composites by adding MXene.
One of the biggest and most promising areas of MXene application is energy storage. Shortly after their discovery, Naguib et al. [Citation85] observed that Ti2C had a reversible capacity five times higher than the MAX Ti2AlC phase and showed a stable capacity of 225 mAhg−1. Zhu et al. [Citation86] researched structural and electronic properties of Li decorated Nb2C and Nb2CX2. Obtained research results, specific capacities of 305 mAh/g, and low diffusion barrier for Li on Nb2C, make Nb2C a promising electrode material for Li-ion batteries. Wang et al. [Citation87] investigated Ti3C2 as the S cathode host for Li-S batteries. They showed that unmodified Ti3C2 could not be used in Li-S batteries because of too strong interactions between the decomposition of Li2Sn/S8 and Ti3C. Functional terminated Ti3C can achieve high performance in Li-S batteries. S and O were selected as the best functional groups for Ti3C2 surface modification.
Recently, T3C2 has been extensively studied as potential material for gas and biosensors. Studies have shown that T3C2 can successfully detect gases such as ethanol, methanol, acetone, and ammonia at room temperature [Citation88]. In addition, it has been shown that the functionalization of the MXene surface allows increasing the selectivity of gas sensors. Mo2CO2 and V2CO2 have been shown to have selectivity towards NO, while Nb2CO2 and Ti2CO2 towards NH3 [Citation89]. Liu et al. [Citation90] investigated the use of Ti3C2 to produce biosensors for the detection of NO2− in water samples. Another use of MXene was proposed by Rakhi et al. [Citation91]. They designed a biosensor to detect glucose in the presence of other electroactive substances using Au/MXene nanocomposites.
Research on MXena is also being conducted concerning the possible storage of hydrogen. Hydrogen molecules are predicted to adsorb to the MXene surface in molecular form and then dissociate to hydrides. In contrast, hydrogen molecules in the second and third surface layers are adsorbed in the molecular form. The research showed that the possible hydrogen storage capacity of Ti2C, Sc2C, Cr2C, and V2C [Citation92–94] is about 7% by weight.
Since some MXene (Ti2CO2, Zr2CO2, Hf2CO2, Sc2CO2, and Sc2CF2) are semiconductors with light absorption in the visible light region and good catalytic properties, they are potential candidates for photocatalytic applications. An example of such a reaction is the production of hydrogen by splitting water into semiconductor substrates with the help of sunlight, which consists of generating an electron-hole pair (by absorbing sunlight) in a photocatalytic material [Citation93]. Research also indicates that the use of MXen heterostructures with other semiconductors, e.g. TiO2, can be used in various photocatalytic reactions, can significantly improve the photocatalytic activity of MXene [Citation92].
As mentioned before, the large number of MXene that can be produced, their unique properties, and 2D structures allow them to be used in many important industries. Moreover, because these materials are relatively poorly tested. There remain a lot of possibilities for new MXene applications.
Conclusions
The MXene phases are of great interest because of their properties. However, their synthesis is still very difficult. As described above, the procedure for producing MXene is a multi-step process. Starting from the synthesis of the MAX phases to the delamination process and a number of intermediate steps. Each of these steps has a significant impact on the efficiency of the synthesis process but also on the quality of the final product. Therefore, it is necessary to optimise each of the processes and care for the purity of the product at every technological stage. The multi-stage process requires an interdisciplinary approach to the synthesis of MXene phases. Knowledge and skills in the synthesis of MAX phases and further processing processes such as delamination or exfoliation are necessary. Only careful attention to all these steps will allow the development of a high-performance process to obtain high-quality MXene phases.
Disclosure statement
No potential conflict of interest was reported by the author(s).
Additional information
Funding
References
- Novoselov KS, Geim AK, Morozov SV, et al. Electric field in atomically thin carbon films. Science. 2004;306(5696):666–669.
- Manzeli S, Ovchinnikov D, Pasquier D, et al. 2D transition metal dichalcogenides. Nat Rev Mater. 2017;2(8):1–15.
- Paciĺ D, Meyer JC, Girit Ç, et al. The two-dimensional phase of boron nitride: few-atomic-layer sheets and suspended membranes. Appl Phys Lett. 2008;92(13):133107.
- Yin J, Wu B, Wang Y, et al. Novel Elastic, Lattice Dynamics and Thermodynamic Properties of Metallic Single-Layer Transition Metal Phosphides: 2H-M 2P (Mo2P, W2P, Nb2P and Ta2P) - IOPscience. J Phys. 2018;30:135701–135709.
- Colson JW, Dichtel WR. Rationally Synthesized Two-Dimensional Polymers. Nat Chem. 2013;5(6):453–465.
- Ma R, Sasaki T. Nanosheets of Oxides and Hydroxides: ultimate 2D Charge-Bearing Functional Crystallites. Adv Mater. 2010;22(45):5082–5104.
- Treacy MMJ, Rice SB, Jacobson AJ, et al. Electron Microscopy Study of Delamination in Dispersions of the Perovskite-Related Layered Phases K[Ca2Nan−3NbnO3n+1]: evidence for Single-Layer Formation. Chem Mater. 1990;2(3):279–286.
- Molle A, Goldberger J, Houssa M, et al. Buckled Two-Dimensional Xene Sheets. Nat Mater. 2017;16(2):163–169.
- Anasori B, Lukatskaya MR, Gogotsi Y. 2D Metal Carbides and Nitrides (MXenes) for Energy Storage. Nat Rev Mater. 2017;2(2):1–17.
- Naguib M, Kurtoglu M, Presser V, et al. Two-Dimensional Nanocrystals Produced by Exfoliation of Ti3AlC2. Adv Mater. 2011;23(37):4248–4253.
- Barsoum MW. MN+1AXN Phases: a New Class of Solids; Thermodynamically Stable Nanolaminates. Prog Solid State Chem. 2000;28(1–4):201–281.
- Jeitschko W, Nowotny H. Die Kristallstruktur von Ti3SiC2-Ein Neuer Komplexcarbid-Typ. Monatshefte für Chemie. 1967;98(2):329–337.
- Nowotny VH. Strukturchemie Einiger Verbindungen Der Übergangsmetalle Mit Den Elementen C, Si, Ge, Sn. Prog Solid State Chem. 1971;5:27–70.
- Goc K, Prendota W, Chlubny L, et al. Structure, Morphology and Electrical Transport Properties of the Ti3AlC2 Materials. Ceram Int. 2018;44(15):18322–18328.
- Jeitschko W, Nowotny H, Benesovsky F. Kohlenstoffhaltige Ternäre Verbindungen (H-Phase). Monatshefte für Chemie. 1963;94(4):672–676.
- Barsoum MW, El-Raghy T. Synthesis and Characterization of a Remarkable Ceramic: ti3SiC2. J Am Ceram Soc. 1996;79(7):1953–1956.
- Zheng L, Wang J, Lu X, et al. (Ti0.5Nb0.5)5AlC4: a New-Layered Compound Belonging to MAX Phases. J Am Ceram Soc. 2010;93(10):3068–3071.
- Barsoum MW, El-Raghy T. The MAX Phases: unique New Carbide and Nitride Materials: tertiary Ceramics Are Soft and Machinable, yet Heat-Tolerant, Strong and Lighweight. Am Sci. 2001;89(4):334–343.
- Barsoum MW, Radovic M. Elastic and Mechanical Properties of the MAX Phases. Annu Rev Mater Res. 2011;41(1):195–227.
- Barsoum MW. MAX Phases. Wiley-VCH Verlag GmbH & Co. KGaA: Weinheim, Germany; 2013. ISBN 9783527654581
- Farle AS, Kwakernaak C, van der Zwaag S, et al. A Conceptual Study into the Potential of Mn+1AXn-Phase Ceramics for Self-Healing of Crack Damage. J Eur Ceram Soc. 2015;35(1):37–45.
- Barsoum MW, Brodkin D, El-Raghy T. Layered Machinable Ceramics for High Temperature Applications. Scr Mater. 1997;36(5):535–541.
- Frodelius J, Sonestedt M, Björklund S, et al. Ti2AlC Coatings Deposited by High Velocity Oxy-Fuel Spraying. Surf Coat Technol. 2008;202(24):976–5981.
- Sonestedt M, Frodelius J, Sundberg M, et al. Oxidation of Ti2AlC Bulk and Spray Deposited Coatings. Corros Sci. 2010;52(12):3955–3961.
- Walter C, Sigumonrong DP, El-Raghy T, et al. Towards Large Area Deposition of Cr2AlC on Steel. Thin Solid Films. 2006;515(2):389–393.
- Utili M, Agostini M, Coccoluto G, et al. Ti3SiC2 as a Candidate Material for Lead Cooled Fast Reactor. In Proceedings of the Nuclear Engineering and Design; Holland, 2011 May 1; Vol. 241, pp.1295–1300.
- Nechiche M, Gauthier-Brunet V, Mauchamp V, et al. Synthesis and Characterization of a New (Ti1-ε,Cuε)3(Al,Cu)C2 MAX Phase Solid Solution. J Eur Ceram Soc. 2017;37(2):459–466.
- Jeitschko W, Nowotny H, Benesovsky F. Die H-Phasen: ti2CdC, Ti2GaC, Ti2GaN, Ti2InN, Zr2InN Und Nb2GaC. Monatshefte für Chemie. 1964;95(1):178–179.
- Zhang P, Zhang Y, Sun Z. Spontaneous Growth of Metal Whiskers on Surfaces of Solids: a Review. J Mater Sci Technol. 2015;31(7):675–698.
- Advances in Science and Technology of Mn+1AXn Phases | ScienceDirect Available online: https://www.sciencedirect.com/book/9781845699918/advances-in-science-and-technology-of-mn-and-1axn-phases accessed on (2020 Jul 20
- Sun ZM. Progress in Research and Development on MAX Phases: a Family of Layered Ternary Compounds. Int Mater Rev. 2011;56(3):143–166.
- Zhou A. Methods of MAX-phase synthesis and densification – II. In: Advances in Science and Technology of Mn+1AXn Phases. Elsevier; Woodhead Publishing, 2012. p. 21–46.
- Eklund P, Rosen J, Persson POA. Layered ternary M n+1 AXn phases and their 2D derivative MXene: an overview from a thin-film perspective. J Phys D Appl Phys. 2017;50(11):113001–113015.
- Zhou Y, Sun Z, Chen S, et al. In-Situ Hot Pressing/Solid-Liquid Reaction Synthesis of Dense Titanium Silicon Carbide Bulk Ceramics. Mater Res Innovations. 1998;2(3):142–146.
- Wang XH, Zhou YC. Microstructure and Properties of Ti3AlC2 Prepared by the Solid-Liquid Reaction Synthesis and Simultaneous in-Situ Hot Pressing Process. Acta Materialia. 2002;50(12):3143–3151.
- Tzenov NV, Barsoum MW. Synthesis and Characterization of Ti3AlC2. J Am Ceram Soc. 2004;83(4):825–832.
- Lis J, Chlubny L, Łopaciński M, et al. Ceramic Nanolaminates-Processing and Application. J Eur Ceram Soc. 2008;28(5):1009–1014.
- Ghosh NC, Harimkar SP. Consolidation and synthesis of MAX phases by Spark Plasma Sintering (SPS): a review. In: Advances in Science and Technology of Mn+1AXn Phases. Materials Science, Elsevier; 2012. p. 47–80.
- Li J-F, Matsuki T, Watanabe R. Mechanical-Alloying-Assisted Synthesis of Ti3SiC2 Powder. J Am Ceram Soc. 2004;85(4):1004–1006.
- Li S-B, Zhai H-X. Synthesis and Reaction Mechanism of Ti3SiC2 by Mechanical Alloying of Elemental Ti, Si, and C Powders. J Am Ceram Soc. 2005;88(8):2092–2098.
- Zhang H, Dai FZ, Xiang H, et al. Phase Pure and Well Crystalline Cr2AlB2: a Key Precursor for Two-Dimensional CrB. J Mater Sci Technol. 2019;35(8):1593–1600.
- Lis J, Miyamoto Y, Pampuch R, et al. Ti3SiC-Based Materials Prepared by HIP-SHS Techniques. Mater Lett. 1995;22(3–4):163–168.
- Bai Y, He X, Li Y, et al. Rapid synthesis of bulk Ti2 AlC by self-propagating high temperature combustion synthesis with a pseudo–hot isostatic pressing process. J Mater Res. 2009;24(8):2528–2535.
- El-Raghy T, Barsoum MW. Processing and Mechanical Properties of Ti3SiC2: i, Reaction Path and Microstructure Evolution. J Am Ceram Soc. 2004;82(10):2849–2854.
- Mashtalir O, Naguib M, Dyatkin B, et al. Kinetics of Aluminum Extraction from Ti3AlC2 in Hydrofluoric Acid. Mater Chem Phys. 2013;139(1):147–152.
- Naguib M, Halim J, Lu J, et al. New Two-Dimensional Niobium and Vanadium Carbides as Promising Materials for Li-Ion Batteries. J Am Chem Soc. 2013;135(43):15966–15969.
- Zhou A, Wang C, Huang Y. A Possible Mechanism on Synthesis of Ti3AlC2. Mater Sci Eng A. 2003;352(1–2):333–339.
- Li SB, Zhai HX, Bei GP, et al. Formation of Ti3AlC2 by mechanically induced self-propagating reaction in Ti–Al–C system at room temperature. Mater Sci Technol. 2006;22(6):667–672.
- Rozmysłowska-Wojciechowska A, Wojciechowski T, Ziemkowska W, et al. Surface Interactions between 2D Ti 3 C 2 /Ti 2 C MXenes and Lysozyme. Appl Surf Sci. 2019;473:409–418.
- Högberg H, Eklund P, Emmerlich J, et al. Epitaxial Ti2n GeC, Ti 3GeC2, and Ti4 GeC 3MAX-phase thin films grown by magnetron sputtering. J Mater Res. 2005;20(4):779–782.
- Palmquist JP, Jansson U, Seppänen T, et al. Magnetron Sputtered Epitaxial Single-Phase Ti3SiC2 Thin Films. Appl Phys Lett. 2002;81(5):835–837.
- Wilhelmsson O, Palmquist JP, Lewin E, et al. Deposition and Characterization of Ternary Thin Films within the Ti-Al-C System by DC Magnetron Sputtering. J Crystal Growth. 2006;291(1):290–300.
- Fakih H, Jacques S, Berthet MP, et al. The Growth of Ti3SiC2 Coatings onto SiC by Reactive Chemical Vapor Deposition Using H2 and TiCl4. Surf Coat Technol. 2006;201(6):3748–3755.
- Fakih H, Jacques S, Dezellus O, et al. Phase Equilibria and Reactive Chemical Vapor Deposition (RCVD) of Ti 3SiC 2. J Phase Equilib Diffus. 2008;29(3):239–246.
- Darwin PS, Zhang J, Zhou Y, et al. Synthesis and elastic properties of V2AlC thin films by magnetron sputtering from elemental targets. J Phys D Appl Phys. 2009;42(18):185408–185416.
- Joelsson T, Flink A, Birch J, et al. Deposition of Single-Crystal Ti2 AlN Thin Films by Reactive Magnetron Sputtering from a 2Ti: alCompound Target. J Appl Phys. 2007;102(7):074918.
- Dolique V, Jaouen M, Cabioc’H T, et al. Formation of (Ti,Al) NTi2AlN Multilayers after Annealing of TiNTiAl (N) Multilayers Deposited by Ion Beam Sputtering. J Appl Phys. 2008;103(8):083527.
- Cabioch T, Alkazaz M, Beaufort MF, et al. Ti2AlN Thin Films Synthesized by Annealing of (Ti+Al)/AlN Multilayers. Mater Res Bull. 2016;80:58–63.
- Fahrenholtz WG, Hilmas GE, Talmy IG, et al. Refractory Diborides of Zirconium and Hafnium. J Am Ceram Soc. 2007;90(5):1347–1364.
- Eklund P, Beckers M, Jansson U, et al. Mn + 1AXn Phases: materials Science and Thin-Film Processing. Thin Solid Films. 2010(518): 1851–1878.
- Khazaei M, Arai M, Sasaki T, et al. Yoshio Sakka Two-Dimensional Molybdenum Carbides: potential Thermoelectric Materials of the MXene Family. Phys Chem Chem Phys. 2014;16(17):7841–7849.
- Halim J, Kota S, Lukatskaya MR, et al. Synthesis and Characterization of 2D Molybdenum Carbide (MXene). Adv Funct Mater. 2016;26(18):3118–3127.
- Hu C, Lai -C-C, Tao Q, et al. Mo2Ga2C: a new ternary nanolaminated carbide. Chem Comm. 2015;51(30):6560–6563.
- Zha XH, Zhou J, Eklund P, et al. Non-MAX Phase Precursors for MXenes. 2D Metal Carbides and Nitrides (MXenes): Structure, Properties and Applications. 2019;53–68. DOI:10.1007/978-3-030-19026-2_4
- Naguib M, Mashtalir O, Carle J, et al. Two-Dimensional Transition Metal Carbides. ACS Nano. 2012;6(2):1322–1331.
- Mashtalir O, Naguib M, Mochalin VN, et al. Intercalation and Delamination of Layered Carbides and Carbonitrides. Nat Commun. 2013;4(1):1–7.
- Li Z, Wu Y. 2D Early Transition Metal Carbides (MXenes) for Catalysis. Small. 2019;15(29):1804736.
- Meshkian R, Näslund LÅ, Halim J, et al. Synthesis of Two-Dimensional Molybdenum Carbide, Mo2C, from the Gallium Based Atomic Laminate Mo2Ga2C. Scr Mater. 2015;108:147–150.
- Zhou J, Zha X, Chen FY, et al. A Two-Dimensional Zirconium Carbide by Selective Etching of Al3C3from Nanolaminated Zr3Al3C5. Angew Chem. 2016;55(16):5008–5013.
- Halim J, Kota S, Lukatskaya MR, et al. Synthesis and Characterization of 2D Molybdenum Carbide (MXene). Adv Funct Mater. 2016;26(18):3118–3127.
- Li Q, Fan S, Han W, et al. Coating of Carbon Nanotube with Nickel by Electroless Plating Method. Japanese Journal of Applied Physics, Part 2: Letters . 1997;36(Part 2, No. 4B):L501.
- Wozniak JT, Trzaska M, Cieślak G, et al. Preparation and Mechanical Properties of Alumina Composites Reinforced with Nickel-Coated Graphene. Ceram Int. 2016;42(7):8597–8603.
- Wozniak J, Kurtycz P, Broniszewski K, et al. Properties of Alumina Matrix Composites Reinforced with Nickel-Coated Graphene. In Proceedings of the Materials Today: Proceedings, Aveiro, Portugal; Elsevier Ltd, 2015 Jan 1; Vol. 2, pp. 376–382.
- Wozniak J, Jastrzębska A, Cygan T, et al. Surface Modification of Graphene Oxide Nanoplatelets and Its Influence on Mechanical Properties of Alumina Matrix Composites. J Eur Ceram Soc. 2017;37(4):1587–1592.
- Petrus M, Wo J, Cygan T; et al. Materials Influence of Ti 3 C 2 T x MXene and Surface-Modified Ti 3 C 2 T x MXene Addition on Microstructure and Mechanical Properties of Silicon Carbide Composites Sintered via Spark Plasma Sintering Method. 2021, doi:10.3390/ma14133558.
- Cygan T, Wozniak J, Petrus M, et al. Microstructure and Mechanical Properties of Alumina Composites with Addition of Structurally Modified 2d Ti3c2 (Mxene) Phase. Materials. 2021;14(4):1–18.
- Gong K, Zhou K, Qian X, et al. MXene as Emerging Nanofillers for High-Performance Polymer Composites: a Review. Compos Part B Eng. 2021;217:108867.
- Xiao-Yang S, Fan-Yan C, Qi-Huang D, et al. Preparation and Property of MXene/Copper Alloy Composites. Journal of Inorganic Materials. 2018;33(6):603.
- Zhou W, Zhou Z, Fan Y, et al. Significant Strengthening Effect in Few-Layered MXene-Reinforced Al Matrix Composites. 2020;9:148–154. http://mc.manuscriptcentral.com/tmrl
- Zhang J, Li S, Hu S, et al. Chemical Stability of Ti3C2 MXene with Al in the Temperature Range 500–700 °C. Materials. 2018;11. DOI:10.3390/MA11101979.
- Hu J, Li S, Zhang J, et al. Mechanical Properties and Frictional Resistance of Al Composites Reinforced with Ti3C2Tx MXene. Chinese Chemical Letter. 2020;31(4):996–999.
- Wozniak J, Petrus M, Cygan T, et al. Silicon Carbide Matrix Composites Reinforced with Two-Dimensional Titanium Carbide – manufacturing and Properties. Ceram Int. 2019;45(6):6624–6631.
- Wozniak J, Petrus M, Cygan T, et al. Influence of MXene (Ti3C2) Phase Addition on the Microstructure and Mechanical Properties of Silicon Nitride Ceramics. Materials. 2020;13:5221.
- Petrus M, Woźniak J, Cygan T, et al. Silicon Carbide Nanocomposites Reinforced with Disordered Graphitic Carbon Formed in Situ through Oxidation of Ti3C2 MXene during Sintering. Arch Civil Mech Eng. 2021;21(3):1–12.
- Naguib M, Come J, Dyatkin B, et al. MXene: a Promising Transition Metal Carbide Anode for Lithium-Ion Batteries. Electrochem commun. 2012;16(1):61–64.
- Zhu J, Chroneos A, Schwingenschlögl U. Nb-Based MXenes for Li-Ion Battery Applications. Phys Status Solidi (RRL) Rapid Res Lett. 2015;9(12):726–729.
- Wang D, Li F, Lian R, et al. A General Atomic Surface Modification Strategy for Improving Anchoring and Electrocatalysis Behavior of Ti3C2T2 MXene in Lithium–Sulfur Batteries. ACS Nano. 2019;13(10):11078–11086.
- Lee E, VahidMohammadi A, Prorok BC, et al. Room Temperature Gas Sensing of Two-Dimensional Titanium Carbide (MXene). ACS Appl Mater Interfaces. 2017;9(42):37184–37190.
- Review-Recent Exploration of Two-Dimensional MXenes for Gas Sensing. From a Theoretical to an Experimental View. doi:10.1149/2.0152003JES.
- Liu H, Duan C, Yang C, et al. A Novel Nitrite Biosensor Based on the Direct Electrochemistry of Hemoglobin Immobilized on MXene-Ti3C2. Sens Actuators B Chem. 2015;218:60–66.
- Cappello V, Marchetti L, Parlanti P, et al. Ultrastructural Characterization of the Lower Motor System in a Mouse Model of Krabbe Disease. Scientific Reports. 2016;6:1–15.
- Yadav A, Dashora A, Patel N, et al. Study of 2D MXene Cr2C Material for Hydrogen Storage Using Density Functional Theory. Appl Surf Sci. 2016;389:88–95.
- Hu Q, Wang H, Wu Q, et al. Two-Dimensional Sc2C: a Reversible and High-Capacity Hydrogen Storage Material Predicted by First-Principles Calculations. Int J Hydrogen Energy. 2014;39(20):10606–10612.
- Hu Q, Sun D, Wu Q, et al. MXene: a New Family of Promising Hydrogen Storage Medium. J Phys Chem A. 2013;117(51):14253–14260.