ABSTRACT
In this study, potential of the air-diffusion channels to maintain the desired controlled atmosphere condition in the storage chambers was evaluated. The diffusion channels of different combination in length (60, 120, 180, 240 mm) and diameter (3, 6, 9, 12 mm) were installed in the storage chambers of 2 L capacity. Tomato samples (0.805 kg) were taken in the chambers and stored at 10°C. Oxygen concentration in the chambers was measured periodically until the end of storage period. The tomatoes were stored upto 40 days under the channel length of 180 mm and diameter of 9 mm with harvest-fresh appearance, better texture and colour. The experimental results showed that the oxygen concentration ranging from 7% to 15% was maintained depending on the channel length and its tendency was found directly proportional to the channel diameter and inversely related to the channel length. Simultaneously, respiration rate of tomato was determined by closed respiration system to facilitate working with diffusion channel model. A model was developed based on Fick’s first law of gas diffusion to predict the channel length. The model was fitted to the experimental data and channel lengths were calculated theoretically in the ranges between 30 and 320 mm. The predicted channel lengths maintained the oxygen concentration between 4% and 16% irrespective of the channel diameters. The predicted results were in accordance with the experimental results. The model was very useful in predicting the diffusion channel length and establishing the controlled atmosphere condition for storage of tomatoes.
Introduction
Tomato (Solanum lycopersicum) is one of the most consumed vegetables worldwide. It is a climacteric vegetable, so it is highly perishable in nature that encounters several problems in its transportation, storage, and marketing.[Citation1] It has been estimated that the postharvest losses of tomato range from 20% to 50% in tropical countries.[Citation2] Therefore, an increase in postharvest life of tomato is really desirable to reduce the losses during supply chain. One of the major physiological activities in the postharvest life of tomato is respiration. Fresh tomatoes generally have higher respiration rates that indicate more active metabolism and subsequently a faster deterioration rate in the normal course of time.[Citation3] Respiration involves the consumption of oxygen (O2) for oxidative breakdown of organic components into simple molecules such as carbon dioxide (CO2) and water (H2O) with concurrent release of energy and other intermediates which can be used by the cell for synthetic reactions.[Citation4] Respiration rates and deterioration rates can be minimized by storing the produce in controlled/modified atmospheric condition at low temperature. Modified atmosphere can be achieved by maintaining the natural interplay between respiration rate of the commodity and transfer of gases through the storage that lead to an atmosphere richer in CO2 and poorer in O2.[Citation5] Controlled atmosphere storage (CAS) has been defined as a form of storage where the concentration of gas is initially modified according to optimal conditions and then maintained during the period of storage.[Citation6] Over ripening, senescence, ethylene production rates, and some physiological alterations such as mould growth, rotting, decay, butt discolouration can be minimized greatly in CAS condition.[Citation7,Citation8] The levels of both O2 and CO2 concentrations during storage affect the quality of the final product. Absence of O2 results in development of off-flavours, and presence of high CO2 concentration (more than 5% for tomato) may cause physiological injures.[Citation9]
There are different techniques such as O2 control system, CO2 control system, hypobaric system, membrane system, and diffusion channel system to provide the desired gas composition in the storage environment depending on the degree of control of the gases.[Citation6,Citation10] The final O2 concentration in the storage chamber depends on the permeability of the membrane and area available for O2 transfer. Moreover, for those commodities that need a high concentration of O2 during storage, the use of polymeric membranes has not been successful due to their low O2 permeability.[Citation11] Among different techniques, the diffusion channel system is indeed a potential alternative for products that cannot be packed in polymeric films, and is capable of maintaining a specific steady-state gas composition in CAS systems over a longer period of time, relatively insensitive to changes in barometric pressure and fluctuations in the storage room temperature, provides great flexibility in the design of storage chamber, and materials used are considerably less expensive and are structurally simple.[Citation12] Diffusion channel system works on the principle of Fick’s first law of gas diffusion. Diffusion channel is a hollow tube fitted with an airtight storage chamber in which produce is stored and other end of the tube is exposed to the atmosphere. As a result of consumption of O2 and liberation of CO2 during respiratory process of the stored commodity, a great change in concentration of gases inside the storage chamber occurs. With respect to ambient condition, O2 concentration decreases and that of CO2 increases at rates depending on respiration rate of the produce. This creates a concentration gradient between inside and outside the chamber. Diffusion of gases takes place through the channel due to concentration gradient of gases between inside and outside the storage chamber, thus modified atmosphere is created inside the chamber which is beneficial for storage. The rate of diffusion of gases is dependent on length and cross-sectional area of the channel and gas concentration gradients between the chamber and ambient air. The gas composition in the storage chambers could easily be altered by varying the dimensions of diffusion channels.[Citation12–Citation16]
There is not much research work on the concept of diffusion channel system to enhance the shelf life of fruits and vegetables. Some researchers have published their research work on diffusion channel system. Emond et al.[Citation11] studied the gas exchanges through a perforation (considered as channel of zero length) and developed a model to predict the gas exchanges through the perforation. Baugerod[Citation12] proved that the diffusion channel system is capable of maintaining the steady-state O2 concentration from 1.5% to 18% depending on the mass of stored product, and length and cross-sectional area of the diffusion channel. Ratti et al.[Citation13] showed the influence of diffusion channel length on the concentration of O2 in the storage chambers but no theoretical interpretation of the experimental data. Ratti et al.[Citation14] developed mathematical model based on the molecular diffusion theory and this model includes the effect of mass of the produce, length and cross-sectional area of the diffusion channel on the final gas composition in the storage chamber. Different combinations of diffusion channel length (0.6, 3, 7, 12, 18, and 25 cm) and cross-sectional area (0.04, 0.18 and 1.15 cm2) were tested for storage of broccoli at 0°C.[Citation15] The length and cross-sectional area have a significant effect on the final O2 steady-state concentration. Fick’s first law of molecular diffusion theory was used to predict the required length of diffusion channel. Spinach was stored up to 30 days at 2°C under diffusion channel length of 0.18 m and cross-sectional area of 4×10−6 m2 with best colour and freshness.[Citation16] CO2 produced by the respiring spinach was completely scrubbed using calcium hydroxide, and O2 was maintained in the range of 1–5%. The O2 steady-state levels decreased with an increase in length and became more distinct as the cross-sectional area increased. A model was developed based on Fick’s first law of molecular diffusion for predicting the length of diffusion channel. Stewart et al.[Citation17] confirmed that the Cavendish bananas (also a climacteric fruit) can be stored for 42 days at 15°C under diffusion channel systems (4, 7, and 10 cm channel length). The shortest diffusion channel achieved 5% CO2 and 3% O2 in 12–16 days. Karthiayani et al.[Citation18] stored banana (Musa acuminate) under diffusion channel system (length: 5, 10, 15, and 20 cm and inner diameter: 3, 5, and 7 mm) at room temperature, 24°C and 14°C. They showed that the shelf life of banana can be increased 3–4 -folds as compared with control. They also developed a model using non-linear multiple regression to fit the observed data, and the model was found to be useful in determining the length of the diffusion channel for required steady-state O2 concentration for banana.
Since the polymeric membranes have low O2 permeability, maintaining required O2 concentration in the storage is not feasible. The use of diffusion channel system is theoretically able to handle the whole range of possible O2 concentrations in the storage. The main objective of this work is to develop mathematical model to predict the optimal length of diffusion channel to maintain the steady-state O2 concentration in the storage.
Theory of modelling
Fick’s first law of gas diffusion
CAS involves atmospheric gas mixtures and their diffusion characteristics. Gas diffusion describes the spread of particles through random motion from regions of higher concentration to regions of lower concentration. Diffusion occurs in response to a concentration gradient and is expressed as change in concentration due to a change in position. The gas diffusion generally obeys Fick’s first law of gas diffusion, which states that the gas flux moves from region of higher concentration to region of lower concentration, with a magnitude that is proportional to the concentration gradient. The movement of gases is due to the random motion of the individual molecules caused by their kinetic energy. The molecular diffusion is typically described mathematically using Fick’s first law of gas diffusion[Citation19] as follows:
where NA is the rate of gas diffusion per unit area per unit time (mol m−2 s−1), DAB is the diffusion coefficient that describes the speed of gas that diffuses from region A to region B (m2 s−1), CA is the concentration of gas in A, ∂x is the distance between where the object started and ended after diffusion, (−) sign indicates that NA is positive when movement is down the gradient. In steady-state conditions, diffusion rate of a gas is proportional to the concentration difference across the material and the area perpendicular to the diffusion.[Citation20]
Development of modelling
The molecular diffusion theory on diffusion of O2 through diffusion path was adopted in this study to develop a mathematical model to predict the optimal length of diffusion channel as described by Ratti et al.[Citation14] for storage of cauliflower. This model takes into account the functionality between the mass of the produce, final O2 concentration level in the storage chamber, diffusion channel length, and its cross-sectional area. While modelling process, the following key assumptions have been made. (i) total pressure in the chamber is 1 atm; (ii) the temperature is constant; (iii) the concentration of O2 in the chamber is uniform at any time; (iv) the diffusion process is binary, since the CO2 produced by the stored commodity is chemically scrubbed off, thus O2 and N2 are diffusing; (v) there is no concentration gradient for nitrogen (N2) between the outside and the inside, thus O2 will be diffusing in a stagnant N2 gas; (vi) the diffusion coefficient of O2 in N2 is constant; and (vii) diffusion of gases in the chamber is one-dimensional.
shows the diffusion of O2 into a storage chamber through the diffusion path. The mass balance is written for a strip of the diffusion channel of length Δz. For a binary gas mixture, the general equation that describes the flux of the diffusing substance (O2) into a stagnant gas (N2) based on molecular diffusion can be stated as follows:
where is the O2 molar flux (mol cm−2 h−1), c is the total gas molar concentration (mol cm−3),
is the diffusion coefficient of O2 gas through diffusion channels (cm2 h−1),
is the O2 mole fraction in sealed storage chamber (dimensionless), z is the spatial coordinate (cm). Under steady-state condition, the amount of O2 utilized in the respiration process is equal to that diffusing into the chamber. Applying boundary conditions to the diffusion channel system
The mass flux of O2 can be obtained by rearranging Eq. (2) and integrating with proper limits of boundary conditions.
where L is the length of the diffusion channel (cm), is the O2 mole fraction in air (dimensionless),
is the O2 mole fraction in storage chambers installed in diffusion channel. Under steady-state conditions, the O2 consumed by the commodity is equal to the O2 diffusing through the channel into the chamber. The O2 consumed in the respiration process can be expressed numerically as follows:
where is the mass of O2 consumed in the respiration process (mg O2),
is the respiration rate as a function of O2 (mg O2 kg−1 h−1), Ms is the mass of the stored products (kg), t is the time (h). Under steady-state condition (z = 0), the mass flux of O2 can be written as
where AC is the cross-sectional area of the diffusion channel (cm2), is the O2 molecular weight (kg mol−1), t is the time (h). Equating Eqs. (5) and (6) and simplifying, we get
The length of diffusion channel required to maintain a desired steady-state O2 concentration inside the storage chamber can be obtained by equating Eqs. (4) and (7)
The following model was adopted to predict the respiration rate of tomato as a function of O2 and CO2 concentration:[Citation21]
where r is the respiration rate (mg O2 kg−1 h−1 or mg CO2 kg−1 h−1), is the O2 concentration (mol cm−3),
is the CO2 concentration (mol cm−3), K1 is the constant (mg kg−1 h−1), K2 is the constant (mol O2 mol total−1), K3 is the inhibition constant (dimensionless). The inhibition constant (K3) for CO2 concentration was tended to zero as the rate of CO2 evolution during the respiration process is not same as the rate of O2 consumption. The constant K3 was negligible in either case, which nullifies the effect of changing CO2 concentration on the respiration rate.[Citation21] Hence, the respiration rate was assumed only as a function of O2 concentration as follows:
To facilitate working with the diffusion channel model, the concentration of O2 is expressed as O2 mole fraction and stated as follows:
At steady-state condition, concentration of O2 can be expressed as follows:
Substituting Eqs. (11) and (12) in Eq. (8) can be written as:
Diffusion coefficient of oxygen
The diffusion coefficient () of O2 into N2 can be determined with following key assumptions: (i) length of diffusion channel is unity, (ii) Fick’s law defines this transport process clearly, (iii) O2 concentration in the chamber is uniform at any time (steady state). Based on these assumptions, the diffusion coefficient of O2 through diffusion channels can be calculated by following equation:[Citation22]
where Qm is the mass flow rate of O2 through diffusion channel (mg h−1), Δl is the unit length of diffusion channel (cm), Δc is the difference in gas concentration between inlet and outlet end of the diffusion channel (mg cm−3).
where a1 and a2 are constants.
Materials and methods
Sample preparation
The popular tomato variety Roma in the West Bengal (India) was selected for this study. The matured tomatoes at breaker stage of ripeness (definite break in colour from green to tannish-yellow, pink, or less than 10% red coloration[Citation23]) and uniform size were procured from a farmer field. The tomatoes were transported to the lab immediately after harvest. The harvested tomatoes were graded manually and washed in chlorinated water with the concentration of 100 mg L−1 to remove adhering dirt on their surface.[Citation24] The tomato samples of 0.805 kg were chosen since the selected storage chamber’s capacity was 2 L and two-third of the headspace in the chambers was kept as free volume.
Experimental design
The experiments were designed with four levels of diffusion channel length (60, 120, 180, and 240 mm) and four levels of channel diameter (3, 6, 9, and 12 mm) as independent variables and gas concentration as dependent variable. The diffusion channels (fibre glass tubes) of different geometries were purchased from Hindusthan Industrial Syndicate, Kolkata, India. The geometries of diffusion channel were selected based on the information available in the previous studies.[Citation14–Citation17] Different symbols () were used to denote different treatments with three replicates. Factorial completely randomized design using AGRESS software package (P ≤ 0.05) was used for analysis of the effect of different lengths and diameters of the diffusion channel on gas concentration in the storage chambers. The storage temperature of 10°C was selected as recommended by the previous research (fresh tomatoes stored at around 10°C were more favourable as compared with high temperature (24–30°C) for prolonged shelf life and to retain fresh tomato quality,[Citation25] and postharvest recommendations indicate that tomatoes, including cherry and grape tomatoes, should be stored at 10°C or higher to avoid chilling injury[Citation26]).
Table 1. Treatment details of the experiments.
Fabrication of experimental setup
The storage chambers of 2 L capacity made up of polyethylene tetrachloride (PET) were used for conducting the experiments. The experimental setup () was fabricated in such a way that four holes were provided on the lid. A silicone septum was fitted in the first hole to facilitate the withdrawal of gas sample from the chamber for analysis. Brass nipples with rubber gaskets were connected in second and third holes and tightened with nuts. Rubber tubes of length 200 mm were connected to these nipples and closed by pinch clips after purging gas. In the fourth hole, a conical-shaped hallow rubber cork was fitted. The diffusion channel of required size was rigidly fixed in the rubber cork. The joints were crammed by melted paraffin wax to secure air tightness. The absence of air bubble ensured the air tightness of diffusion chambers.
Experimental procedure
The experimental chambers were washed with chlorinated water of concentration 500 mg L−1 and wiped completely by cotton cloth. Calcium hydroxide (50 g kg−1) with tomato wrapped in a tissue paper was placed at the bottom of the each storage chamber to prevent any accumulation of CO2 and absorb condensed moisture within the storage chambers.[Citation14–Citation16] The tomato samples (Ms = 0.805 kg) were taken in the storage chambers. About two-third of headspace was left in the chambers as free volume. The chambers were provided perfect air tightness by top lid and wrapped with Teflon tape. To achieve a fast pull-down O2 level inside the chamber, the storage chamber with tomato sample was flushed with N2 until O2 level is brought down to required level (6%). The selected gas mixture was flushed from one sampling port, and the other sampling port was opened as gas outlet to atmosphere. The gas was flushed for about 3–5 min. During flushing, diffusion channels were closed with a thin wax plate. At the end of flushing, both inlet and outlet ports were closed with pinch clips. The storage chambers were transferred to the cold room where the temperature of 10°C was maintained throughout the storage period. The chambers were kept in vertical position until end of the storage period.
Measurement of respiratory gases
The storage chambers were allowed to sit for about 30 min for their temperature to come to equilibrium with room temperature. The first gas samples were drawn without breaking the wax cover of channel opening. The readings indicated that gas concentrations in the chamber were uniform. The wax plate was then removed from the diffusion channels and the gases were allowed to diffuse. Gas samples of 0.5 mL were drawn periodically from each chamber through the silicone septum using syringes. The gas samples were analysed for CO2 and O2 concentration (%) using gas chromatograph (SRI 8610A model, SRI Instruments, USA) equipped with thermal conductivity detector and operating at an oven temperature of 45°C and detector temperature of 100°C using helium as the carrier gas. Calculation of concentration of the gases was made with the Peak Simple software. The standard gas mixture (purchased from Span Gas Equipments Ltd., Mumbai) was analysed, and calibration curves were developed for determining the amount of components in experimental gas mixture quantitatively.
Determination of respiration rate
Respiration rate of tomato was measured using the closed respiration system, which involves monitoring the O2 and CO2 concentrations as a function of time inside a closed chamber containing the tomatoes. The respiration rate can be measured by observing the concentration of O2 consumption or CO2 evolution per unit time per unit weight of the produce[Citation27,Citation28] (it can be expressed by mg O2 kg−1 h−1 or mg CO2 kg−1 h−1). The experimental respiration rate was calculated periodically using the data such as difference in gas concentration per time, weight of the stored produce, and free volume of the chamber. The mass concentration of O2 and CO2 inside the closed experimental chamber were determined and plotted as a function of time. Curve fitting was done using second-order polynomial regression equation.[Citation29] The fitted polynomial was differentiated to determine the change of rate of gas concentrations. The first derivative of the regression functions were used to obtain the experimental respiration rates as a function of O2 consumption () and CO2 evolution (
)[Citation30]
where [O2] is the oxygen concentration (%), [CO2] is the carbon dioxide concentration (%), d[O2] is the change in concentration of O2 with time, d[CO2] is the change in concentration of CO2 with time, dt is the difference in time between two gas measurements (h), P is the gas pressure (1 atm), Ma is the mean molecular mass of air (g mol−1), Vf is the free volume of the chamber (L), R is the gas constant in the ideal gas equation (0.08206 L atm mol−1 K−1), T is the temperature of the gas (K), Wp is the weight of the stored tomatoes (kg). The negative sign in Eq. (18) signifies that the O2 concentration in the chamber decreases with time.
Results and discussion
The respiration rate of tomato was obtained through the closed respiration system experiments at 10°C. Kandasamy et al.[Citation21] reported detailed experiment as well as calculation procedures. The experimental respiration data were used to estimate the respiration rate model constants in Eq. (9). The respiration rates were plotted as a function of O2 and CO2 concentration (). The model was then fitted to the experimental data. The respiration rate model constants K1, K2, and K3 in Eq. (9) were determined by non-linear regression with experimental data using Gauss–Newton procedure for non-linear least squares. The regression described that the experimental data, that is, O2 concentration was very well (R2 = 0.970), whereas CO2 concentration was fair (R2 = 0.812) for tomato. The results of fitting for K1, K2, and K3 were 208.552, 526.810, and 0.007, respectively. Constant K3 is quite close to zero and nullifies the influence of CO2 concentration on respiration rate. Therefore, the respiration rate of tomato was considered mainly as a function of O2 concentration.[Citation21] The inhibition parameter K3, calculated as the rate of CO2 evolution, was inversely related to temperature, whereas the one calculated as the rate of O2 consumption was directly proportional to the temperature. This is because the rate of CO2 evolution during the respiration process is not same as the rate of O2 consumption. The parameter K3 was negligible in either case which nullifies the effect of changing CO2 concentration on the respiration rate.[Citation21] As the inhibition constant K3 for CO2 concentration in Eq. (9) was negligible, the model was modified mainly as a function of O2 concentration (Eq. 10).
Figure 3. Respiration rate of tomato: (a) function of O2, (b) function of CO2 concentration at 10°C.
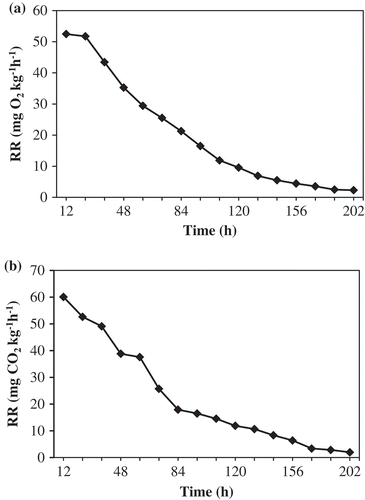
To facilitate working with the diffusion channel model, the concentration of O2 was expressed as O2 mole fraction (Eq. 11). The respiration rate of tomato in sealed storage chambers was calculated as a function of O2 molar fraction. The respiration rate was plotted against the O2 molar fraction. Curve fitting was done using non-linear regression equation as shown in . Constants K1 and K2 in Eq. (11) were obtained from experimental data through the curve fittings. Results of fitting for K1 and K2 were 13.764 mg kg−1 h−1 and 14.328 mol O2 mol total−1, respectively. The predictions of the respiration rate model [Eq. (11) with fitted constants] are shown in together with experimental results. The linear tendency shown by the model in this range of O2 concentrations is in accordance with the predictions of enzymatic reaction theory.
The diffusion coefficient of O2 () through the diffusion channel was determined through Eq. (14) by fitting the experimental data, and the results obtained are presented in . The diffusion coefficient of O2 depends on length and cross-sectional area of the diffusion channel, mass flow rate of O2 through diffusion channels, and difference in gas concentration between inlet and outlet end of the diffusion channel.[Citation22] It is clearly noticed from that the decreasing trend in diffusion coefficient of O2 was observed when increasing the channel length and diameter.
Table 2. Different parameters for predicting the model for diffusion channel length.
The constants a1 and a2 were obtained through Eqs. (15) and (16), respectively, by fitting the experimental data such as diffusion coefficient of O2 through the channel (), constants (K1 and K2), and total gas molar concentration, that is, 3.466 mol cm−3. Results of fitting for a1 and a2 are presented in . The constant a1 was found to be varied because the diffusion coefficient of O2 varied depending on the channel length and cross-sectional area. O2 molecular weight (), O2 mole fraction in sealed chamber (
), and O2 mole fraction in air (
) were 32 kg mol−1, 0.025, and 0.189, respectively. Moreover, O2 mole fraction in storage chambers equipped with diffusion channel (
) was determined using experimental data and the results obtained are presented in .
The diffusion channel length model (Eq. 17) was fitted to the experimental data () and the results obtained were found negative. Since the length cannot be negative, the model (Eq. 17) was rewritten as follows:
Then the corrected model (Eq. 20) was fitted to the experimental data, and channel lengths were obtained. Predicted length of diffusion channel for maintaining the steady-state O2 concentration is presented in . The channel lengths, respectively, were predicted in the range of 120–320 mm, 80–170 mm, 30–80 mm, and 30–60 mm for maintaining the O2 concentration of 4%, 8%, 12%, and 16% irrespective of the channel diameter (3, 6, 9, and 12 mm). It is clearly noticed that the longer diffusion channel maintained lower range of O2 steady-state concentration, whereas shorter diffusion channel maintained higher range of O2 steady-state concentration irrespective of the channel diameter. These results were confirmed with the results reported by Ratti et al.[Citation14] for cauliflower, Chimphango[Citation16] for spinach, and Karthiayani et al.[Citation18] for banana. The model (Eq. 20) developed for predicting the length of diffusion channel fits the experimental data well when individual channel diameters were considered, and is more appropriate for establishing the controlled atmosphere condition for storage of tomato. The model suggests that the desired O2 level in the storage chambers for any length can be precisely obtained if the diameter of the channel is known. To get same O2 level as in a chamber installed with a shorter diffusion channel length of a small diameter, one can use a longer diffusion channel of a larger diameter. A parallel trend was observed when these results (predicted) were compared with the experimental results.
Figure 5. Predicted length of diffusion channel for maintaining the steady-state O2 concentration at 10°C (error with 5% value).
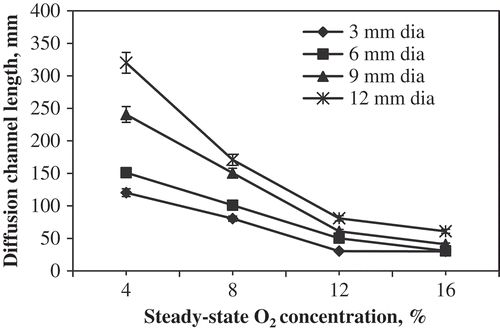
The steady-state O2 concentration in experimental storage chambers equipped with diffusion channel at 10°C is presented in . From the figure, it is noticed that the longer diffusion channel (240 mm) maintained lower O2 concentration (7–9%), whereas shorter diffusion channel (60 mm) maintained higher O2 concentration (11–15%) depending on the channel diameter. On the other hand, higher channel diameter (12 mm) maintained higher O2 concentration (9–15%), whereas lower channel diameter (3 mm) maintained lower O2 concentration (7–12%) depending on the channel length. It is evident from the results that the steady-state O2 concentration was inversely proportional to the length of channel and directly proportional to the channel diameter. The statistical analysis showed that the effect of different length and diameter of the diffusion channel on concentration of O2 was found to be significant at 5% level. Similar trends in the steady-state O2 concentration under diffusion channel system were observed by Chimphango[Citation16] and Karthiayani et al.[Citation18] for modified atmosphere packaging of spinach and banana, respectively. Moreover, the tomatoes were stored up to 40 days at 10°C under diffusion channel length of 180 mm and diameter of 9 mm (Treatment 11) with harvest-fresh appearance, better texture, good colour, retained nutritional values, and good marketability conditions.
Conclusion
The experimental results showed that the diffusion channel system can well maintain the O2 concentration in the storage chamber. The model for predicting length of diffusion channel fits the experimental data well when individual channel diameters were considered and was more appropriate for establishing the controlled atmosphere condition for storage of tomato. The fitted model closely represented the experimental results and can be used to predict the length of diffusion channel for the same commodity. The model suggests that the desired O2 level in the storage chambers for any length can be precisely obtained if the diameter of the channel is known. The model was very useful for predicting the diffusion channel length and more appropriate for establishing the controlled atmosphere condition for storage of tomato.
References
- Pila, N.; Gol, N.B.; Ramanarao, T.V. Effect of Postharvest Treatments on Physico-chemical Characteristics and Shelf Life of Tomato (Lycopersicon esculentum Mill.) Fruits during Storage. American-Eurasian Journal of Agriculture and Environmental Sciences 2010, 9(5), 470–479.
- Arah, I.K.; Ahorbo, G.K.; Anku, E.K.; Kumah, E.K.; Amaglo, H. Postharvest Handling Practices and Treatment Methods for Tomato Handlers in Developing Countries: A Mini Review. Advances in Agriculture 2016, Doi: 10.1155/2016/6436945, 1–8.
- Wills, R.B.H.; McGlasson, W.B.; Graham, D.; Lee, T.H.; Hall, E.G. Post Harvest. An Introduction to the Physiology and Handling of Fruits and Vegetables. 3rd ed.; AVI: New York, 1989.
- Kader, A.A.; Zagory, D.; Kerbel, E.L. Modified Atmosphere Packaging of Fruits and Vegetables. Critical Review in Food Science and Nutrition 1989, 28, 1–30.
- Fonseca, S.C.; Oliveira, F.A.R.; Brecht, J.K. Modelling Respiration Rate of Fresh Fruits and Vegetables for Modified Atmosphere Packages: A Review. Journal of Food Engineering 2002, 52, 99–119.
- Raghavan, G.S.V.; Gariepy, Y. Structure and Instrumentation Aspects of Storage Systems. Acta Horticulture 1985, 157, 5–30.
- Kader, A.A. Prevention of Ripening in Fruits by Use Controlled Atmospheres. Food Technology 1980, 34(3), 51–54.
- Tasdelen, O.; Bayindirli, L. Controlled Atmosphere Storage and Edible Coating Effects on Storage Life and Quality of Tomatoes. Journal of Food Processing and Preservation 1998, 22, 303–320.
- Yang, C.C.; Chinnan, M.S. Modeling the Effect of O2 and CO2 on Respiration and Quality of Stored Tomatoes. Transactions of the American Society of Agricultural Engineers 1988, 31, 920–925.
- Kandasamy, P.; Moitra, R.; Shanmugapriya, C. Preservation of Fruits and Vegetables under Various Techniques of Controlled Atmosphere Storage. Indian Food Industry Journal 2011, 30(4), 23–35.
- Emond, J.P.; Castaigne, F.; Toupin, C.J.; Desilets, D. Mathematical Modeling of Gas Exchange in Modified Atmosphere Packaging. Transactions of the American Society of Agricultural Engineers 1991, 34, 239–245.
- Baugerod, H. Atmosphere Control in Controlled Atmosphere Storage Rooms by means of Controlled Diffusion Through Air-filled Channels. Acta Horticulturae 1980, 116, 179–185.
- Ratti, C.; Raghavan, G.S.V.; Gariepy, Y. Respiration Rate Model and Modified Atmosphere Packaging of Fresh Cauliflowers. Journal of Food Engineering 1996, 28, 297–306.
- Ratti, C.; Rabies, H.R.; Raghavan, G.S.V. Modelling Modified Atmosphere Storage of Fresh Cauliflower using Diffusion Channels. Journal of Agricultural Engineering Research 1998, 69, 343–350.
- http://www.digitool.library.mcgill.ca/thesisfile23291.pdf
- http://www.researchgate.net/profile/Annie_Chimphango/publication/30004853_Diffusion_channel_system_for_controlled_atmosphere_storage_of_spinach/links/0fcfd5123222c87916000000.pdf
- Stewart, O.J.; Raghavan, G.S.V.; Goldena, K.D.; Gariepy, Y. MA Storage of Cavendish Bananas using Silicone Membrane and Diffusion Channel Systems. Postharvest Biology and Technology 2005, 35, 309–317.
- Karthiayani, A.; Varadharaju, N.; Siddharth, M. Modified Atmosphere Storage of Banana (Musa acuminata) using Diffusion Channel and Mathematical Modelling of Steady-state Oxygen Concentration within the Package. Journal of Food, Agriculture & Environment 2014, 12 (3&4), 19–23.
- Brogioli, D.; Vailati, A. Diffusive Mass Transfer by Non-equilibrium Fluctuations: Fick’s Law Revisited. Physics Review 2001, 63, 012105:1–4.
- Gebhart, B. Heat Conduction and Mass Diffusion; New York: McGraw Hill Inc., 1993.
- Kandasamy, P.; Moitra, R.; Mukherjee, S. Measurement and Modelling of Respiration Rate of Tomato (Cultivar Roma) for Modified Atmosphere Storage. Recent Patents on Food, Nutrition & Agriculture 2015, 7, 62–69.
- Singh, D.; Muir, W.E.; Sinha, R.N. Apparent Coefficient of Diffusion of Carbon Dioxide through Samples of Cereals and Rapeseed. Journal of Stored Products Research 1984, 20, 169–175.
- Gautier, H.; Verdin, V.D.; Benard, C.; Reich, M.; Buret, M.; Bourgaud, F.; Poessel, J.; Veyrat, C.C.; Genard, M. How Does Tomato Quality (Sugar, Acid and Nutritional Quality) Vary with Ripening Stage, Temperature and Irradiance? Journal of Agriculture and Food Chemistry 2008, 56, 1241–1250.
- Zhuang, R.Y.; Beuchat, L.R.; Angulo, F.J. Fate of Salmonella Montevideo on and in Raw Tomatoes as Affected by Temperature and Treatment with Chlorine. Applied and Environmental Microbiology 1995, 61(6), 2127–2131.
- Maul, F.; Sargent, S.A.; Sims, C.A.; Baldwin, E.A.; Balaban, M.O.; Huber, D.J. Tomato Flavor and Aroma Quality as Affected by Storage Temperature. Journal of Food Science 2000, 65(7), 1228–1237.
- Roberts, P.K.; Sargent, S.A.; Fox, A.J. Effect of Storage Temperature on Ripening and Postharvest Quality of Grape and Mini-pear Tomatoes. Proceedings of the Florida State Horticultural Society 2002, 115, 80–84.
- Lee, D.S.; Haggar, P.E.; Lee, J.; Yam, K.L. Model for Fresh Produce Respiration in Modified Atmosphere based on Principles of Enzyme Kinetics. Journal of Food Science 1991, 56(6), 1580–1585.
- Hagger, P.E.; Lee, D.S.; Yam, K.L. Application of an Enzyme Kinetic based Respiration Model to Closed System Experiments for Fresh Produce. Journal of Food Process Engineering 1992, 15, 143–157.
- Gong, S.; Corey, K. Predicting Steady-state Oxygen Concentrations in Modified Atmosphere Packages of Tomatoes. Journal of the American Society of Horticultural Science 1994, 119(3), 546–550.
- Song, Y.; Kim, H.K.; Yam, K.L. Respiration Rate of Blueberry in Modified Atmosphere at Various Temperatures. Journal of the American Society of Horticultural Science 1992, 117(6), 925–929.