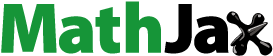
ABSTRACT
A model was developed to predict the impact damage depth of potato. The model consisted of a series of differential equations derived from the force equilibrium on a differential element, which, respectively, governs the relationships among the potato collision displacement and initial collision speed, natural angular frequency of undamped system, and damping ratio. For the collision displacement of potato impact with the rod, the study used the impact test rig and acceleration acquisition system to measure the corresponding values under different experimental conditions. Combined with the determinate experimental data, the mentioned parameters of the model were obtained. According to the model, the obtained maximum value of potato collision displacement was treated as the prediction value of damage depth. The results showed both the experimental values and prediction values of potato damage depth increased with the increment of initial height, and the difference between experimental values and prediction values was less than 8.8%. To evaluate the significant factor of impact damage depth of potato, this study selected the tuber temperature, initial height, tuber mass, and impact material as experiment factors in the orthogonal tests and the order of influencing factors was found to be as follows: initial height > tuber mass > tuber temperature > impact material.
Introduction
Impact damage is the result of short-duration mechanical forces occurred during drops, knocks, and collisions, which is responsible for lowering the quality of potato tubers.[Citation1] What’s more, impact damage of potato is the common phenomenon in the phase of harvesting, sorting, grading, and packing, where the phase of harvesting presents the serious physical injure of potato. It was reported that 70% of the total damage was caused by harvesting.[Citation2] Therefore, the process of harvesting obviously affects the product quality of tubers through direct contact with machine mechanical components.[Citation3] When the tuber collides with the rod-type separating sieve, its damage can occur. To investigate the harvesting damage of potato, some scholars used an instrumented sphere to develop a model of predictive tissue discoloration and to study the abrasion rate of potato tubers in the field experiments.[Citation1,Citation3–Citation5] In terms of simulation, Sang Yongying obtained the collision force curves of potato by ADAMS software.[Citation6] Other researchers used ANSYS software to simulate the collision process between potato and rigid surface and obtained the potato impact damage thresholds[Citation7,Citation8] .
Subsequently, many researchers had focused on the effect of the different factors on impact damage through laboratory tests. Ito et al. investigated the effect of drop height, impact material, and impact angle on the impact damage of potato tubers.[Citation9] Molema et al. reported the influence of the number of impact on potato damage volume and damage depth under the same total collision energy by the pendulum collision device. Meanwhile, the effects of storage time and potassium amount on the impact damage of potato also were investigated.[Citation10] Mathew et al. used a pendulum collision device to study the relationships among potato damage rate and potato tuber temperature, initial height, and impact material.[Citation11] Baritelle et al. studied the effect of specific gravity and cultivar on damage sensitivity of potato[Citation12]. Based on these literatures, the influence factors of potato impact damage mainly included drop height, potato mass, potato tuber temperature, collision material, potato variety, and cultivation conditions.
During the experimental process, the types of used collision equipment usually included a pendulum collision device, free drop collision device, electronic potato, instrumented sphere, and acceleration measuring unit (AMU).[Citation10,Citation11,Citation13–Citation16] Thus, there usually were six evaluation indexes after potato injury, namely, collision pressure, impact acceleration, potato damage volume, damage area, damage depth, and respiratory rate.[Citation10–Citation16] Despite the various researches of potato damage listed here, no such information is available on potato collision mechanical model. Moreover, the analysis of the law of potato collision displacement combined with the mechanical model seems to be overlooked. Then, the comprehensive evaluation of the influence of various factors on potato impact damage has not been reported. Therefore, this article aimed to establish a model and to analyze the primary and secondary sequences that affected the impact damage factors of potatoes.
Material and methods
Model development
The viscoelastic deformation of potato occurs during the process of potato impact with the rod.[Citation17,Citation18] The mechanical model of impact between potato and rod is shown in . The parameters of m, k, and c in respectively, represent the mass of potato, the elastic coefficient, and the damping coefficient. Assuming that the deformation displacement of potato is , its collision speed is
, then the motion differential equation of the model is obtained based on Newton’s law of mechanics.
where is the potato impact acceleration; k is the elastic coefficient; c is the damping coefficient; and
is time. Since the potato and rod will be separated after impact, it can be considered that the impact mechanical model shown in is an underdamped system, that is, the damping ratio satisfies the condition of
. In the case of underdamping, the general solution of Equation (1) is:
where is the amplitude,
; among this,
is the natural angular frequency of the damped system, and
;
is the natural angular frequency of the undamped system, and
;
is damping ratio, and
;
is phase angle, and
;
is attenuation coefficient, and
.
The initial conditions ,
and
are substituted into Equation (2) to obtain
,
. Then, the free motion solution of the differential equation of motion is as follows:
where is the initial collision speed of potato. Substituting
and
into Equation (3) gives the potato collision displacement equation as:
Impact tests
Impact tests were conducted to determine the deformation displacement of potato in Equation (4) when potato impacted with the rod. The potato cultivar is Kexin 1, which was manually harvested at the crop planting base. After harvesting, the ellipsoidal potato without mechanical damage and pests were selected as test materials. After washing in cold water, the potatoes with four kinds of mass (150 ± 5 g, 250 ± 5 g, 350 ± 5 g, and 450 ± 5 g) were stored at the fridge and to produce potato samples at 5 °C, 15 °C, and 23 °C. All tests were completed on the day of harvesting.
The potato impact test rig and acceleration acquisition system were used to perform the experiment. The potato impact test rig mainly included bracket, ruler, light swing rod, clamp, and rod. The acceleration test system consisted of data acquisition and analyzer (AVANT-MI7016, Hangzhou Yiheng Technology Co., Hangzhou, China.), a 6 g-mass acceleration sensor with dimensions of Φ10mm× 22 mm (1A102E, Jiangsu Donghua Testing Technology Co. Jiangsu, China), and computer (). Acceleration data were acquired in in a continuous way with a scanning rate of 5 kHz per axis. After processing the data of an impact event, the acceleration and the duration of each impact were available.
Geyer believed that the mechanical impact data obtained by embedding miniaturized triaxial AMU into potatoes were more reliable and susceptible than those obtained from electronic fruit.[Citation15] Based on this result, an acceleration sensor was implanted into potato to collect collision data in this study. Scilicet, a potato tuber, was selected and drilled blind hole with a diameter of 12 mm along the lateral direction, and the remaining tissue thickness of potato was 20 mm from the bottom of the hole to the collision surface.[Citation15] Then the acceleration sensor was wrapped with foam and waterproof tape and inserted into the blind hole of potato. Finally, the sensor and potato were taped together to prevent the sensor from moving relative to the potato during the collision ().
The potato was placed in the clamp along the longitudinal orientation of the tuber, and it was picked up at a preselected height, then released with noninitial speed. During impact on the rod, the acceleration data of potato were recorded and stored on a computer. The measured acceleration data were integrated twice and the displacement data were obtained. Each potato was conducted once, and each test was completed within 2 min to avoid the test error caused by too large changes of the physical and chemical characteristics of potato tubers.
In order to determine the parameters of potato collision displacement equation (Equation (4)), impact tests were carried out with respect to four parameters (). In the first test, the influence of initial height was tested with six different heights. In the second test, potato tubers at 15 °C collided with 65Mn steel rods from the initial height of 300 mm, and the influence of mass was tested with tubers of four different sizes. Third, all potato tubers at different temperatures collided with 65Mn steel rods from the initial height of 300 mm. Finally, the effect of different impact materials was studied: 65Mn steel rod with diameter 10 mm, 10 mm diameter 65Mn steel rod wrapped in 2 mm PVC plastic (65Mn-Plastic), and 10 mm diameter 65Mn steel rod wrapped in 2 mm rubber (65Mn-Rubber). Each group was repeated 10 times, and the average value of the 10 results was taken as the final result of each group.
Table 1. Program of impact tests.
The potato collision displacement data were analyzed with the help of the statistic analysis software SPSS (version 19.0) by using the nonlinear regression analysis procedure. The values of and
were calculated iteratively. Then, based on formulas of
and
, the values of parameters k and c were, respectively, calculated. After collision, the impacted potato tubers were stored under the condition of room temperature (20 °C~ 22 °C) for 48 h. When the collision site of the potato tuber was browned, several slices were cut parallel to the collision site and until there is no damage. The thickness of each slice was measured using a vernier caliper, and the accumulated thickness was taken as the damage depth of potato.[Citation19]
Orthogonal tests
In order to clarify the significance of the various factors on potato damage, the orthogonal test was conducted. Thereinto, the damage depth of potato was taken as the evaluation index. Meantime, the potato tuber temperature (A), initial height (B), potato tuber mass (C), and collision material (D) with three levels were selected as factors in the experiments (), namely the null-free program (). Each group was repeated 20 times, and the results of 20 experiments were divided into two groups to, respectively, calculate the average value. The measured data were analyzed by SPSS software (version 19.0).
Table 2. Factors and levels.
Table 3. Scheme and results of orthogonal experiment.
Results and discussion
Parameters of the potato collision displacement model
Equation (4) was employed to fit the measured collision displacement of potato, where the known initial collision speed of potato represents the parameter in Equation (4). The different initial collision speeds of potato corresponding to different initial heights are listed in .
Table 4. Parameters of potato collision displacement model corresponding to different initial heights.
It was observed that the correlation coefficient under different initial heights were more than 0.93 (). This meant the model was effective and could predict the collision displacement of potato.
Combined with the results in , it was confirmed the initial height had no significant influence on the natural angular frequency of the undamped system, and the variation range of
corresponding to the six different initial heights was 0.137 ~ 0.139
. The results may be ascribed to the same physical characteristics of potato and impact material at different heights. In other words, during the experiment, the selected potato cultivar was the same, the mass of selected potato tubers was 250 ± 5 g, and impact material was 65Mn.
As the initial height raise, the damping ratio increased, which may be due to the increased damping coefficient (). Usually, the lager speed led to the deeper potato-inserted rod depth at the moment of impact. However, the deeper depth impeded the separation of potato and rod after impacted. Thereby, the damping coefficient between the potato and the rod increased with the deepened depth. shows the damping coefficient
is directly proportional to damping ratio
. That is the result for the larger damping ratio at higher initial height.
The natural angular frequency of the undamped system and damping ratio
under other test conditions are summarized in . The natural angular frequency of the undamped system and damping ratio both declined with the increased potato tuber mass, and both increased with the rising of potato tuber temperature.
Table 5. Potato collision displacement model parameters.
Substituting the parameters in into Equation (4), the curves of prediction collision displacement with changed time at different initial heights were plotted by Matlab software (version 13.0) as shown in ). Compared with the experimental curves in ), the shapes of prediction curves are similar with the measured results at the same initial height. Meanwhile, as the initial height gradually increases, the maximum values of two types of curves increase.
Relationship between the damage depth of potato and the potato collision displacement
According to ), the maximum value of potato collision displacement was conducted as the prediction value of damage depth. Compared to the predicted value with the potato damage depth obtained from the experiment, the relationship between the damage depth of potato and the initial height was obtained, as shown in .
Ito and Mathew put forward that the damage of potato increased linearly with an increase in dropping height.[Citation9,Citation11] Similarly, the experimental values and prediction values of potato damage depth increased with the increased initial height. And the difference between experimental and prediction values ranged from 1.6% to 8.8%. This indicated that potato collision displacement model could be used to predict damage depth of potato well.
Orthogonal test results
From range analysis (), the order of influencing factors on damage depth of potato is as follows: initial height B>tuber mass C>tuber temperature A>impact material D. It can be seen from the results of the range analysis that the higher the initial height, the greater the damage depth of potato (). Danila used an electronic potato to assess the behavior of potato and found that mean impact force increased with the increment of drop height.[Citation13] Rady found that respiration rate increased with the increase of drop height.[Citation14] Based on the above two arguments, it can be inferred that the higher drop height (impact force) caused more serious damage of the potato, and the faster respiration rate accelerated the browning rate of damaged potato. From Equation (4) and the conclusion of Section 3.2, it can be inferred that the initial collision speed of potato is proportional to the collision displacement, and the higher initial height will produce larger initial collision speed; therefore the damage depth of potato is more serious.
It also can be seen from the results of the range analysis, the greater the mass of potato, the greater the damage depth of potato (). This result is consistent with the result from Baritelle and Hyde.[Citation19] They suggested that this result is because of the higher kinetic energy corresponding to larger tuber during impact. Substituted the parameters in into Equation , it was found that with the increased potato mass, the natural angular frequency
of the damped system reduced (). And the natural angular frequency
of the damped system is inversely proportional to the collision displacement (Equation (3)). Therefore, under the same initial collision velocity, the greater the potato mass, the larger the collision displacement, and the deeper the damage depth of potato will be.
Table 6. Natural angular frequency of the damped system corresponding to different initial heights.
The initial height was the most significant factor in influencing the potato collision damage. Therefore, in the process of potato harvesting, reasonably controlling the drop height of potato tubers relative to the device for separating potato and soil is the most effective way to avoid the damage of potato. At the same time, potato varieties with moderate mass can be reasonably selected during the cultivation of potato varieties. This will not only reduce potato yield, but also effectively diminish potato damage during harvesting.
The damage depth of potato increased with the decreased tuber temperature. Similarly, as the temperature increased, bruise threshold values also increased.[Citation11] As shown in , the natural angular frequency of the damped system decreased with the decrease of the tuber temperature. The damage depth of potato at 5 °C and 15 °C was obviously deeper than that of 23 °C. The colder temperatures were believed to decrease the elastic-plastic properties of cell wall materials and made potato tissues more prone to failure.[Citation20] So, in order to reduce the damage of potato, the potato harvest is completed before the low temperature.
The damage depth of potato after collision with 65Mn plastic and 65Mn rubber was smaller than that of 65Mn steel. As shown in , the natural angular frequency of the damped system of potato collision with 65Mn steel rod was smaller than this value of collision with other two materials. Therefore, the damage depth of potato after collision with 65Mn steel rod was greater than that of the other two materials. Ito believed that the potato damage could be developed by attaching a rubber coat onto bars of a potato harvester or digger.[Citation9] Mathew also considered that the cushioning materials performed well in reducing impact damage occurring in the potatoes.[Citation11]
Conclusion
In this study, the potato collision displacement model was investigated by using theoretical and experimental analysis, and then the parameters of this model were obtained. Besides, the order of various factors on potato damage was clarified through orthogonal tests. It was found that the initial height had no significant influence on the natural angular frequency of the undamped system. Meantime, as the initial height increased, the damping ratio increased. The natural angular frequency of the undamped system and damping ratio both decreased with the increased potato tuber mass, and both increased with the elevation of potato tuber temperature. The results also showed the experimental values and prediction values of potato damage depth increased with the initial height increasing. And the difference between experimental values and prediction values was less than 8.8%. This indicated that potato collision displacement model may be reliably used to predict the damage depth of potato. According to the orthogonal tests, the order of influencing factors on damage depth of potato was as follows: initial height B>tuber mass C>tuber temperature A>impact material D. The greater the mass of potato, the deeper the damage depth of potato. At the same time, the damage depth of potato increased with the falling tuber temperature. Additionally, the damage depth of potato after collision with 65Mn-plastic and 65Mn-rubberl was smaller than that of 65Mn steel.
Additional information
Funding
References
- Thomson, G. E.; Lopresti, J. P. Size and Temperature Characteristics of Potatoes Help Predict Injury following Impact Collisions. New Zealand J. Crop Hortic. Sci. 2017, 46, 1–17.
- Peters, R. Damage of Potato Tubers, a Review. Potato Res. 1996, 39, 479–484. DOI: 10.1007/BF02358463.
- Bentini, M.; Caprara, C.; Martelli, R. Harvesting Damage to Potato Tubers by Analysis of Impacts Recorded with an Instrumented Sphere. Biosystems Eng. 2006, 94, 75–85. DOI: 10.1016/j.biosystemseng.2006.02.007.
- Canneyt, T. V.; Tijskens, E.; Ramon, H.; Verschoore, R.; Sonck, B. Development of a Predictive Tissue Discolouration Model Based on Electronic Potato Impacts. Biosystems Eng. 2004, 88, 81–93. DOI: 10.1016/j.biosystemseng.2004.01.005.
- Blahovec, J. Shape of Bruise Spots in Impacted Potatoes. Postharvest Biol. Technol. 2006, 39, 278–284. DOI: 10.1016/j.postharvbio.2005.11.004.
- Sang, Y. Y.; Yu, H. L.; Jia, J. X.; Modeling, P. And Moving Simulation of Vibrating Screen and Tubers on Potato Harvester. Adv. J. Food Sci. Technol. 2012, 195–196, 627–632.
- Guo, S.; Wang, W.; Meng, L. I.; Chen, S.; Junhu, L. I. Research on the Test of Potato Mechanism and Finite Element Analysis for Crash. Machine Des. Manufacturing Eng.. 2016, 45, 56–59.
- Sang, Y.; Zhang, D.; Zhang, M. Study on Bruising Damage Experiment of Potato and Finite Element Analysis. J. China Agric. Univ. 2008, 13, 81–84.
- Ito, M.; Sakai, K.; Hata, S.; Takai, M. Damage to the Surface of Potatoes from Collision. Trans. Asae. 1994, 37, 1431–1433. DOI: 10.13031/2013.28224.
- Molema, G. J.; Verwijs, B. R.; Berg, J. V. V. D.; Breteler, H. Effect of Repetitive Impacts on Subcutaneous Tissue Discolouration in Potato Tubers. Neth. J. Agric. Sci. 1997, 45, 185–198.
- Mathew, R.; Hyde, G. M. Potato Impact Damage Thresholds. Trans. Asae. 1997, 40, 705–709. DOI: 10.13031/2013.21290.
- DăNilă, D. M. Assessing the Potato Impact Response Using a Pendulum Controlled and Designed by Computer. Bull. Transilvania Univ. Brasov. 2015, 8, 65–70.
- DăNilă, D. M.; Gaceu, L. The Difference in Impact Behavior of Fruits and Vegetables Assessed by Digital Potato in Collision with Hard versus Soft Surfaces. J. Ecoagritourism. 2010, 2, 62–66.
- Rady, A.; Soliman, S. Evaluation of Mechanical Damage of Lady Rosetta Potato Tubers Using Different Methods. Int. J. Postharvest Technol. Innovation. 2015, 5, 125–148. DOI: 10.1504/IJPTI.2015.074322.
- Geyer, M. O.; Praeger, U.; König, C.; Graf, A.; Truppel, I.; Schlüter, O.; Herold, B. Measuring Behavior of an Acceleration Measuring Unit Implanted in Potatoes. Trans. Asabe. 2009, 52, 1267–1274. DOI: 10.13031/2013.27770.
- Baritelle, A. L.; Hyde, G. M. Specific Gravity and Cultivar Effects on Potato Tuber Impact Sensitivity. Postharvest Biol. Technol. 2003, 29, 279–286. DOI: 10.1016/S0925-5214(03)00003-6.
- Alves, J.; Peixinho, N.; Silva, M. T. D.; Flores, P.; Lankarani, H. M. A Comparative Study of the Viscoelastic Constitutive Models for Frictionless Contact Interfaces in Solids. Mechanism & Machine Theory. 2015, 85, 172–188. DOI: 10.1016/j.mechmachtheory.2014.11.020.
- Ahmadi, E. Viscoelastic Finite Element Analysis of the Dynamic Behavior of Apple under Impact Loading with Regard to Its Different Layers. Comput. Electronics Agr. 2016, 121, 1–11. DOI: 10.1016/j.compag.2015.11.017.
- Baritelle, A.; Hyde, G.; Thornton, R.; Bajema, R. A Classification System for Impact-Related Defects in Potato Tubers. Am. J. Potato Res. 2000, 77, 143–148. DOI: 10.1007/BF02853938.
- Lancker, J. V. Bruising of Unpeeled Apples and Potatoes in Relation with Temperature and Elasticity. Lebenson Wiss. Technol. 1979, 12, 157–161.