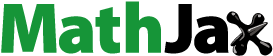
ABSTRACT
The tensile and shear mechanical properties of laver were investigated in order to reduce the tensile and shear forces, tensile and shear energies consumption during the harvesting and processing. Loading rate, harvest time and origin were selected as the effect factors for laver tensile and shear tests, while mathematical models of the variation of tensile and shear mechanical properties with three factors were also developed. The following results were obtained: tensile force, shear force, tensile energy and shear energy of laver are affected by loading rate, harvest time and origin. Tensile force, shear force and shear energy were generally inversely proportional to the loading rate, while tensile energy was generally positively proportional to the loading rate. The minimum values are 0.0557 N, 0.1650 N, 0.7267 N.mm and 0.7393 N.mm, respectively. Tensile force, shear force and tensile energy all increased with increasing harvest time, while shear energy decreased with increasing harvest time. The maximum values are 0.1581 N, 0.4437 N, 1.5367 N.mm and 1.5177 N.mm, respectively. Both tensile and shear forces (0.0857 N, 0.2549 N) were greatest in Dalian for the first harvest of laver. However, the first harvest of Qingdao laver has the lowest tensile and shear energy. The microstructure after stretching and shearing changed significantly with normally shaped cells deformed and ruptured. The changes in microstructure were consistent with the macro-mechanical properties, verifying the reliability of the test data.
Introduction
Laver (Porphyra yezoensis Ueda) is a nutritious and economically important seaweed,[Citation1,Citation2] which is mainly used as human food, such as sushi, snacks and pickles.[Citation3] Laver harvesting and processing treatment is a prerequisite for any subsequent applications, it still requires a lot of manual involvement in China, the high labor intensity, low production efficiency and poor product quality during the harvesting and processing are very prominent and have seriously affected the development of the laver industry.[Citation4,Citation5] The reasonable design of tool forces parameters and the reduction of power consumption are crucial for the devices development of laver harvesting and processing equipment and achieving high energy efficiency.[Citation6]
Laver is a biological material, in the process of tensile and shearing, firstly, all will go through the elastic deformation stage, the deformation in this stage can be recovered, when beyond the elastic deformation point, gradually enter the plastic stage, when the external force exceeds the tensile and shear force of laver, the thalli of laver will break, the maximum force resisting damage in tension is the tensile force of laver, and the maximum force resisting damage in shear is the shear force of laver. Generally speaking, the tensile and shear of plant leaves are the process of collision contact between the tool and the material, and the force between tool and leaves is random and nonlinear, and it is more difficult to explore the relationship between them by traditional theoretical analysis and calculation methods. Hence, fundamental physical mechanical experimental test methods are generally applied to study the tensile and shear mechanical properties of leaves.[Citation6–9]
Many national and international authors have conducted studies that the tensile and shear properties of crops are influenced by loading rate, harvest time and origin. Chen et al.[Citation10] investigated the effect of tensile rate on the tensile strength of kelp, and the results showed that the tensile rate and the tensile strength of kelp were positively correlated. Literature[Citation11] investigated the effect of loading rate on the tensile and shear strength of laver, showing that the tensile and shear strength of laver generally tended to increase with increasing loading rate. Hassan-Beygi et al.[Citation12] found that the tensile force of saffron stalk significantly increased with increasing loading rate. In order to obtain the required parameters for the basic mechanical properties of corn bract for the corn peeling device, Li et al.[Citation13] found that the mean tensile fracture force of the third bract of two corn species increased with increasing harvest time and that the mean tensile fracture energy increased and then decreased. Diao[Citation14] reported a large difference in the maximum tensile force on wheat straw between different geographical areas. There was no significant differences in the tensile force of the tobacco leaves between the different origins.[Citation15] Chen et al.[Citation16] found that the shear force of maize stem increased with delay in maize harvest at different harvesting dates. The same conclusion was also reported by Guo for maize stem.[Citation17] Liu et al.[Citation18] reported that the cutting speed was positively related to the cutting force and cutting energy of oil tree peony stems. McRandal and McNulty[Citation19] found that the shear energy of forage grasses decreased with loading rate. Studies in the literature[Citation20] have shown no significant differences in shear force between different origins of tobacco leaves. In order to obtain mechanical property parameters for the design of apple mechanization equipment, Zhang et al. conducted tensile, shear, compression and microstructure tests on Fuji apple peel and pulp, and obtained values for minimum tensile strength, shear strength and compression strength, and also found that the microstructure of apples changed significantly after damage, and the changes in microstructure were consistent with the changes in macroscopic mechanical properties, verifying the reliability of the test data.[Citation21] Li et al. conducted tests such as tensile, tearing and microstructural tests on two varieties of potato peel to obtain parameters such as tensile strength, modulus of elasticity and tearing strength of the peel, and also concluded that the load-bearing capacity of the peel is related to the shape and size of the epidermal cells, among other things.[Citation22]
The above analysis of the literature indicates that loading rate, harvest time and origin play an important role in the tensile and shear processes of crops. However, according to the present study, studies on tensile and shear properties have focussed on the roots, stems and leaves of terrestrial plants but little research has been done on the tensile and shear mechanical properties of the aquatic plant laver. Loading rate, harvest time and origin also play an important role in studies affecting tensile and shear properties of terrestrial plants, and these factors are not consistent and regular for different plant materials in terms of tensile force, shear force, tensile energy and shear energy. Therefore, in order to provide a basis for the design of the laver harvesting and processing device, this study applies basic knowledge and fundamental methods of materials mechanics to the determination of the tensile and shear mechanical properties of laver by using a high degree of digital test equipment with loading rate, harvest time and origin as influencing factors and microstructure test, the results of the study provide parametric support for research on harvesters and processing machines for laver and similar seaweeds.
Materials and methods
Test materials
The laver for tensile and shear mechanical properties tests was collected from the farming origins of Xingshu Village, Dalian City, Liaoning Province (39°17”55.9” N, 122°09”26.6” E), Chanshan Village, Qingdao City, Shandong Province (36°23”41.5” N, 120°52”34.1” E) and Gaogongdao Village, Lianyungang City, Jiangsu Province (34°42”14.8” N, 119° 28” 59.9” E), and the harvest times were Dalian, Qingdao and Lianyungang for the first harvest (early December 2020, namely D1, Q1 and L1), Lianyungang for the second harvest (late December 2020, namely L2) and Lianyungang for the third harvest (mid-January 2020, namely L3) of laver. To maintain freshness, they were kept in the freezer (0.5°C) instantly after harvesting, and the test was carried out under nonstop testing conditions over a 24-h period to ensure that the laver was close to its original state after harvesting and to prevent changes in the water content of the laver from causing it to spoil.
Test device and method
The Texture Analyzer (TMS-PRO type, Food Technology Co., LTD, Sterling, VA, USA) with a sensor range of 1000 N and an accuracy of 0.015% was used for testing the tensile and shear mechanical properties of laver. The sample shown in for testing the tensile and shear mechanical properties was cut into a dumbbell shape according to the shape and dimensions in GB/T1040.3–2006.[Citation10] It is known from the above literature that the tensile and shear mechanical properties are influenced by the loading rate, harvest time and origin. Therefore, the loading rate, harvest time and origin were selected as the test factors, and the tensile force, shear force, tensile energy and shear energy were used as the evaluation indicators (). Each group of tests was repeated 30 times and the mean and standard deviation of the test indicators were calculated.
Table 1. Factors and levels of tensile and shear mechanical properties experiments.
Tensile Mechanical Properties Test: In the tensile mechanical properties test, a latex pad is wrapped around the sample chuck of the texture analyzer in order to avoid crushing of the laver sample during clamping and to ensure that it can be held reliably. The range of the load cell was set to 25 N, and the pretest speed was set to 50 mm/min. The test speeds were set to 10 mm/min, 20 mm/min, 30 mm/min, 40 mm/min and 50 mm/min, the posttest speed was set to 100 mm/min, the trigger force was set to 0.1 N, the tensile distance was set to 50 mm and the probe retraction height was set to 20 mm. The sensor collected the tensile force during the tensile process, and the relationship curve between the tensile force and displacement was drew by the computer. The force at fracture was recorded as tensile force of the laver. Tensile energy is the energy consumption required to fracture a material and is the internal energy generated by the deformation of the material under external load. The tensile energy is the area under the load-displacement curve between the test start point and the point of maximum load. The tensile energy is calculated as follows[Citation13,Citation23–25]:
where Eg is the tensile energy (N.mm), Fn and Fn+1 are values of tensile loads (N), and Dn and Dn+1 are values of the specimen’s elongation (mm).
Shear Mechanical Properties Test: During the shear mechanical properties test, the laver sample was placed flat on the test platform of the texture analyzer and held in place using the self-made shear clamp () in order to prevent the laver from moving during the tool shear. Latex pads were also used in the shear test, placed at both ends of the sample to avoid crushing and to hold them reliably. A standard straight shear tool was used in the shear test. The parameters set of the load cell, trigger force, test speed and posttest speed was the same as those in the tensile test. The probe retraction height was set to 40 mm. The sensor collected the shear force during the shear process, and the relationship curve between the shear force and displacement was drew by the computer. The force at fracture was recorded as shear force of the laver, and the shear energy is calculated as follows[Citation6]:
Where Es is the shear energy, N.mm; s is the tool displacement, mm; Fc is the force applied by the testing machine; a is the tool displacement when contact with the laver, mm; b is the tool displacement when cut off the laver.
Microstructure Test: When the laver samples were stretched and sheared in the tensile and shear tests, the fractured samples were immediately removed and the 10 mm section beyond the fracture position was retained, placed on a slide, followed by a coverslip for fixation, and finally placed on the stage of microscope (OLYMPUS, model CX41, Olympus Corporation, Shenyang, Liaoning, China) for observation, while pictures of the observed tissue structure were recorded and saved.
Statistical analysis
Experimental data were analyzed using one-way analysis of variance (ANOVA) and regression analysis by SPSS 26.0 statistical software (SPSS Inc., Chicago, IL, USA). Duncan’s method was applied to the multiple comparisons of mean values p < 0.05 indicated a significant difference and p < 0.01 indicated a highly significant difference.
Results
Tensile mechanical properties of laver
shows the load – displacement curve of the tensile test of laver. Curve is non-linear with no biological yield point. The curve has two parts. The first part is OA, which is curved and the displacement increases faster than the tensile force, probably because the unstretched laver sample is a strip of micro-buckling and the deformation at the beginning of the stretch is higher, and the tensile force is not evenly distributed. The second part is AB, which is approximately a straight line segment, at this stage the bending of the laver test specimen in the direction of the force gradually disappears, the deformation characteristics follow Hooke’s law and the tensile force tends to be uniform. With the gradual increase in tensile force and displacement, the tensile force reaches a maximum at point B and the laver sample begins to fracture. shows the fracture sites of laver samples under tensile test. In , there is only one peak in the tensile curve for laver, which indicates that the tensile fracture pattern of the laver specimen is dominated by a simultaneous fracture of the tissue cells.[Citation21,Citation26] The irregularity of the edges at the site of the break in the laver sample is easily seen in the .
Figure 3. Results of tensile mechanical properties. (a) The load–displacement curve of the tensile test of laver; (b) Macroscopic view of fracture sites of laver samples under tensile test; (c) Effect of loading rate on tensile force; (d) Effect of loading rate on tensile energy; (e) Effect of harvest time on tensile force; (f) Effect of harvest time on tensile energy; (g) Effect of origin on tensile force; (h) Effect of origin on tensile energy. The different uppercase and lowercase letters indicate a significant difference between group (p < 0.05), while same uppercase and lowercase letters indicate no significant difference between group (p > 0.05).
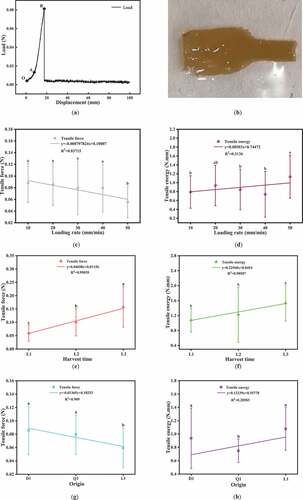
Figure 4. Results of shear mechanical properties. (a) The load–displacement curve of the shear test of laver; (b) Macroscopic view of fracture sites of laver samples under shear test; (c) Effect of loading rate on shear force; (d) Effect of loading rate on shear energy; (e) Effect of harvest time on shear force; (f) Effect of harvest time on shear energy; (g) Effect of origin on shear force; (h) Effect of origin on shear energy. The different uppercase and lowercase letters indicate a significant difference between group (p < 0.05), while same uppercase and lowercase letters indicate no significant difference between group (p > 0.05).
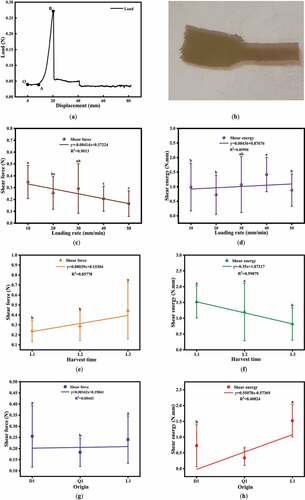
As shown in , when the levels of other factors were fixed (except for the loading rate), it can be observed that loading rate had a significant effect on the tensile force and tensile energy (p < 0.05) and the tensile force and tensile energy of laver satisfied the linear relationship with origin, respectively. As the loading rate increased (from 10 mm/min to 50 mm/min), the tensile force showed an overall decreasing trend, and there is an overall upward trend in tensile energy. The maximum tensile force at a loading rate of 10 mm/min was 0.0882 N, which is 1.58 times the minimum tensile force of 0.0557 N at a loading rate of 50 mm/min. Tensile forces at 10 mm/min, 20 mm/min, 30 mm/min, 40 mm/min and 50 mm/min differed markedly, but not from 10 mm/min to 40 mm/min. The tensile energy at a loading rate of 40 mm/min is the smallest, the average value is 0.7393 N.mm, and the tensile energy at a loading rate of 50 mm/min is the largest, the average value is 1.1350 N.mm, increasing by 53.52% compared to 40 mm/min. The results show that stretching laver at higher rates reduces the tensile force, but increases the tensile energy.
The experiment and fitting results of harvest time on tensile force and energy are illustrated in . As can be seen, the harvest time had a significant effect on the tensile force and tensile energy of laver (p < 0.05), and both tensile force and tensile energy tended to increase with harvest time. There were significant differences in tensile energy between L1, L2 and L3 laver, but not between L1 and L2. L3 laver had the highest tensile force and tensile energy, were 0.1581 N and 1.5367 N.mm, 2.66 and 1.43 times of L1, respectively. Due to the differences in the growth stages of laver, it is easy to see that pulling off the first harvest of laver requires less tensile force and consumes less energy.
The obtained experimental data by fitting the relationship between origin and tensile force and energy are shown in . There was a significant difference (p < 0.05) in the tensile force and tensile energy of laver by origin. For tensile force, L1 was significantly different from D1, Q1, while D1 and Q1 were not significantly different. L1 laver had the lowest tensile force of 0.0594 N. D1 laver had the highest tensile force of 0.0857 N, an increase of 44.28% compared to L1. However, for tensile energy, Q1 laver had the lowest tensile energy at 0.7487 N.mm and L1 laver had the highest tensile energy at 1.0773 N.mm, which was 1.44 times higher than Q1.
Shear mechanical properties of laver
The load – displacement curve of the shear test of laver is shown in . From , it can be seen that the shearing of laver can be divided into two stages, the first stage is OA, in this stage, the applied load is very small and almost constant, probably because the laver specimen is in a bulkling state, when the tool is in contact with the laver, the force applied is only used to make the bulkling laver cells gradually stretch; the second stage is AB, in this stage, as the tool squeezes the laver, the turgor pressure of the laver tissue cells is increasing, thus it can be seen that the applied load gradually increases; Meanwhile, the tissue cells of the laver begin to deform under shearing forces and thus the spacing between the cells becomes smaller and smaller; as the tool further squeezes the laver, the turgor pressure of the laver tissue cells increases sharply and reaches the maximum value (point B), the laver specimen is sheared and point B can be used as the shearing point of the specimen. Also, in , the shear fracture curve of laver has only one peak, indicating that the shear fracture pattern of the laver sample is dominated by the simultaneous rupture of tissue cells. The fracture sites of laver samples under shear test are shown in .[Citation21,Citation27] The figure shows that the fracture edge of the laver sample is relatively flat under shear test conditions.
As shown in , when the levels of other factors were fixed (except for the loading rate), it can be observed that loading rate had a significant effect on the shear force and shear energy and the shear force and shear energy of laver satisfied the linear relationship with origin, respectively. The overall trend of shear force and shear energy decreases with the loading rate. The minimum shear force was 0.1650 N for the loading rate of 50 mm/min, and the maximum shear force was 0.3478 N for the loading rate of 10 mm/min, an increase of 110.79% compared to the loading rate of 50 mm/min. The difference in shear energy between 10 mm/min, 20 mm/min, 40 mm/min and 50 mm/min was significant. There was no significant difference in shear energy between 10 mm/min (0.9860 N.mm), 20 mm/min (0.7267 N.mm) and 50 mm/min (0.8810 N.mm). Increasing shear rate reduces shear force and shear energy while ensuring shear efficiency.
The experiment and fitting results of harvest time on shear force and energy are illustrated in . Harvest time had a significant effect on the shear force and shear energy of laver. Shear force was directly proportional to harvest time, with significant differences in shear force for L1, L2 and L3 (p < 0.05), but no significant differences for L1 and L2 (p > 0.05). Shear energy tended to decrease with the harvest time, with L3 having the lowest shear energy at 0.8177 N.mm and L1 having the highest shear energy at 1.5177 N.mm, a decrease of 46.12% compared to L1.
The obtained experimental data by fitting the relationship between origin and shear force and energy are shown in . Shear force and shear energy of laver were significantly influenced by origin (p < 0.05), with Q1 and D1, L1 having significant effects on shear force, and D1 and L1 having no significant effects on shear force. The maximum shear force for D1 laver was 0.2549 N, 1.39 times that of the minimum Q1 (0.1828N). For shear energy, L1 laver has the highest shear energy of 1.5177 N.mm, which is 4.44 times higher than the minimum Q1 (0.3417 N.mm).
Microstructure properties of laver
Microscopic view of normal laver cells is shown in . Cell shape is dense, long rod-shaped and polygonal.[Citation28] The cells are small and closely spaced, and the cytosol is smooth and viscous. show the microscopic view of the fracture sites of the laver samples under tensile and shear tests, respectively. The microstructure of the cells after stretching of laver is shown in : some cells first underwent deformation, with the stretching of laver samples, relative sliding between cells became relatively large, and their regular shape was destroyed. As the stretching distance became greater, the cells underwent permanent deformation and damage: sliding, deformation, and rupture. Cytosol flowed along the surface of the stretch break, irregularly at the ends of the break. Viscous flow of cytosol is evident along the fractured surface and is not regular correspondingly. Under the tensile test, the edge of the laver sample was irregular at the break and the arrangement of the edge cells was disorganized, consistenting with the morphology of the fracture edge of the sample obtained macroscopically in . The microstructure of sheared laver cells is shown in : some cells first experienced misalignment, mutual misalignment between laver cells became progressively greater with the shearing of laver samples, and their shape deformed as they do so. As shear displacement increased, the cells underwent misshaping, deformation and fracture. Cytosol also flowed along the surface of the shear break obviously, irregularly at the ends of the break.[Citation21,Citation27,Citation29] The edge of the laver sample was flat at the break under the shear test. The cells at the edge of the laver were aligned flush under the shear test, consistenting with the morphology of the fracture edge of the sample obtained macroscopically in . Changes in the microstructure of laver coincided with changes in tensile and shear properties, suggesting that the macroscopic mechanical properties of laver are closely related to its microstructure.
Figure 5. Microscopic views of laver samples. (a) Microscopic view of normal laver cells; (b) Microscopic view of fracture sites of laver samples under tensile test; (c) Microscopic view of fracture sites of laver samples under shear test.
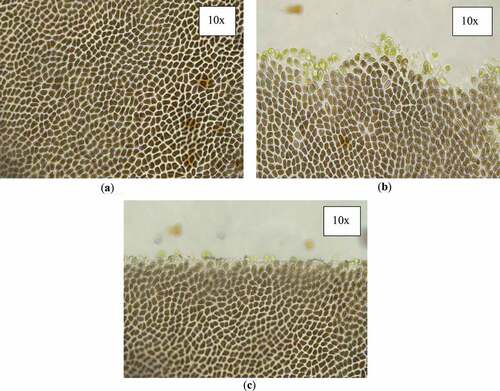
In this study, by observing the microstructure of laver cells, we found that when laver was stretched, more cytosol flowed out and laver cells were more damaged; when laver was sheared, less cytosol flowed out and the damage was relatively small. During the harvesting process of laver, laver is rotated and cut by the knife, the knife will shear laver, laver will also resist the shear of the knife, the force of laver resisting the shear fracture process is the shear force of laver in this study; Due to its soft texture, some of the laver may be stretched and torn, so there is also stretching of the laver by the tool during the harvesting process. The force of the laver resisting the stretching and breaking process is the laver tensile force in this study, and the tool also consumes energy in the process of stretching and shearing the laver, which is the tensile and shear energy in this study. Therefore, during the harvesting process, part of the laver is stretched and part is sheared. Tensile and shear forces are the more intuitive elements of the laver harvesting process, while the damage to laver from stretching and shearing is different; in addition, laver is also a root stubble crop, and after one harvest, the roots must be left stubble before the laver can continue to grow and be harvested next time. Shearing is less damaging to the laver and facilitates the regrowth of the stubble roots. Stretching is more damaging to the laver and the stubble may be affected by damage to the marginal cells and subsequent growth. In the processing of laver, the laver is also chopped by rotating the knives. In the processing of laver, as in the harvesting process, some of the laver is stretched, and some of the laver is sheared. The knives also consume energy in the process of stretching and shearing the laver, and more cytosol is lost when laver is stretched than when it is sheared, which also leads to a higher loss of nutrients.[Citation30,Citation31] Therefore, in the actual harvesting and subsequent processing of laver, it is preferred that the laver be cut in order to reduce the cell damage and cytosol loss of laver, and also to reduce the consumption of tensile and shear energy during harvesting and processing. In summary, the results obtained from this study on the tensile and shear mechanical properties of laver can be used to support research on harvesting and processing equipment for laver and similar seaweeds.
Discussion
Effect of harvest time on tensile and shear force of laver
In this study, the tensile force of laver increased with increasing harvest time. Li et al.[Citation13] showed that the tensile fracture force of corn bract increased with harvest time, Jacobs et al.[Citation23] found that the tensile fracture force of seven tropical grass stems generally increased with increasing maturity, all of which are consistent with the results of this study, the reason for this may be that as maturity increases, the fibers of laver, corn bracts and grass stems all increase, and therefore the tensile force increased. The study by Kim[Citation32] exhibited that the fiber of Undaria pinnatipida showed an increasing tendency with the harvest time. Studies in the literature[Citation33] have shown a significant positive correlation between the acidic detergent fiber and tensile resistance of the five grasses stem. The study by Oke et al.[Citation34] showed that the tensile load of sorghum stalk generally showed a decreasing trend with increasing harvest time, which presents the opposite conclusion to the results of the present study, probably due to the decrease in moisture content of sorghum stalk with increasing harvest time, which resulted in a decrease in toughness and therefore a decrease in tensile force. For the study of peanut stalk tensile force, Chen[Citation35] reported the same conclusion.
In this work, the shear force of laver increased with harvest time. Guo et al.[Citation17] studied the effect of harvest time on shear force of maize stalk, the results showed that shear force increased with advancing maturity of maize. The reason for this may be that the shear force is influenced by the cross-sectional area of both the laver and maize stalk samples, with the diameter of the maize stalk increasing as the growth period increases[Citation16,Citation36] and the thickness of the laver increasing,[Citation11,Citation37,Citation38] the cross-sectional area of the samples increases accordingly and therefore the shear force increases. Studies in the literature[Citation39] have shown that the shear force of oil rapeseed leaves gradually decreased as the harvest time was delayed, probably because the moisture content of oil rapeseed leaves gradually decreased as the growing period was extended,[Citation13] and thus the shear force decreased. The same conclusion was obtained by Wang et al.[Citation40] and Chen et al.[Citation16] for the study of the effect of moisture content on citrus fruit stems and maize stems.
Effect of loading rate on tensile and shear energy of laver
In this experiment, the tensile energy of laver showed an increasing trend with increasing loading rate. For saffron stalk study,[Citation12] rose flower stem study[Citation41] and pyrethrum flower stem study,[Citation42] tensile energy increased with loading rate. In agreement with the conclusions obtained in this study, the reason may be that at low loading rates there is ample room for crack expansion within the laver, stalk for saffron and stem for rose and pyrethrum flower; when the loading rate increases, the cracks do not have time to expand sufficiently, hindering the fracture process and therefore leading to an increase in the fracture energy required for crack expansion.[Citation43] However, Van der Wal and Gaymans[Citation44] studied the effect of test speed on polypropylene rubber blend and found that the tensile fracture energy decreased rapidly with test speed at lower test speeds. Differences in samples and test procedures may explain the differences in tensile energy between laver and polypropylene rubber blend at different loading rates, Jacobs et al.[Citation23] showed that differences in samples and testing procedures affect the tensile mechanical properties of grasses.
In this study, the shear energy of laver showed an overall decreasing trend with increasing loading rate. Studies in the literature[Citation45] have also shown that, shear energy of sorghum stalk was reduced with an increase in loading rate, this may be due to the fact that both laver and sorghum stalk is viscoelastic materials[Citation7] and go through two stages of compression deformation and fracture during shear, in the first stage the fibers are extruded and deformed, as the loading rate increases the proportion of the extrusion stage before cutting decreases, i.e. the distance traveled by the tool extruding laver and sorghum stalk decreases and the shear energy with a consequent decrease.[Citation46,Citation47] For energy cane stems study,[Citation48] sugarcane stalks study[Citation49] and barley straw study,[Citation50] the shear energy increased with increasing loading rate. The reason for this may be that at relatively high rates more energy is transferred to the test material and this energy may be absorbed by impact, vibration and deflection.[Citation51]
Effect of origin on tensile and shear force of laver
In this work, there was a significant difference in the tensile force and shear force of laver from different origins. In the literature,[Citation14,Citation52] the tensile properties of wheat straw and the shear properties of dendrobium officinale were studied in different regions, and significant differences were found between the tensile force of wheat straw and the shear force of dendrobium officinale in different regions, which is the same as the conclusion of this study, probably because laver, wheat straw and dendrobium officinale came from different origins, and the geographical environment and climatic conditions differed between the origins, thus the tensile properties showed variability. Shimada[Citation53] reported that the growth rates of laver from Kikonai, Hakodate and Esan Promontory in Japan were different. Morikawa and Mine[Citation54] found that thalli and cell wall of laver thickened under conditions of high salinity. A study by Zhang et al.[Citation55] on the relationship between laver growth and environmental factors showed that the relative growth rate of laver was negatively correlated with temperature, significantly positively correlated with salinity and positively correlated with pH. For a study on the tensile force of flue-cure tobacco cultivars in three neighboring counties in Bijie, China, Literature[Citation15] and[Citation20] reported the differences in tensile and shear force between the three regions were not significant, which was not consistent with the results obtained in this experiment, probably because the three regions are located in close geographical proximity and have similar geographical and climatic conditions.[Citation56]
Conclusion
The tensile and shear properties of laver in China were investigated by a combination of physical mechanical tests and analysis of variance. The results showed that the loading rate, harvest time and origin had significant effects on the tensile force, shear force, tensile energy and shear energy of laver (p < 0.05). The main conclusions of this research can be summarized as followed: (i) Tensile force (0.0557 ~ 0.0882 N), shear force (0.1650 ~ 0.3478 N) and shear energy (0.7267 ~ 1.4180 N.mm) were generally inversely proportional to the loading rate, while tensile energy (0.7393 ~ 1.1350 N.mm) was generally positively proportional to the loading rate. Under the same conditions of origin and harvest time, stretching laver at higher rates reduces the tensile force, but increases the tensile energy, and increasing shear rate reduces shear force and shear energy while ensuring shear efficiency. (ii) Tensile force (0.0594 ~ 0.1581 N), tensile energy (1.0773 ~ 1.5367 N.mm) and shear force (0.2403 ~ 0.4437 N) all increased with increasing harvest time, while shear energy decreased with increasing harvest time (0.8177 ~ 1.5177 N.mm). At a fixed loading rate and origin, pulling off the first harvest of laver requires less tensile force and consumes less energy. (iii) Both tensile and shear forces were greatest in Dalian for the first harvest of laver, with values of 0.0857 N and 0.2549 N, respectively, and the tensile and shear energies of the first harvested laver from Qingdao are minimal, with values of 0.7487 N.mm and 0.3417 N.mm respectively. (iv) The macro-mechanical properties of laver are closely related to its microstructure, verifying the reliability of the test data. The data obtained from the tensile and shear mechanical properties tests provide the basis for the design and optimization of harvesting and processing machines for laver and similar seaweed and leaf plants.
Author Contributions
Conceptualization, G.M., W.L., and J.T.; methodology, G.M., W.L., J.T., S.N., C.Z., Z.S. and Q.Z.; investigation, G.M., W.L., J.T., S.N. and H.Z.; writing – original draft preparation, W.L.; writing – review and editing, G.M., X.L. and W.L.; supervision, G.Z. and G.M.; funding acquisition, X.L. and G.M. All authors have read and agreed to the published version of the manuscript.
Acknowledgments
The authors are grateful Meng Li and Yongsheng Ma from the School of Food Science and Engineering, Dalian Ocean University, for providing equipment and technical support in the process of the experiment. We are also grateful to our other colleagues, such as Yurui Wang, Guojie Wang and Yilin Zhai in the lab for their help during the experiment.
Disclosure statement
No potential conflict of interest was reported by the author(s).
Additional information
Funding
References
- Rao, A. R.; Ravishankar, G. A. Sustainable Global Resources of Seaweeds; SpringerSpringer: Cham, SwitzerlandCham, Switzerland, 2022Vol. 1. pp. 3–656
- Cao, R.; Hu, M. Y.; Zhao, L.; Wang, L. Z.; Liu, Q. Flavor Characteristics of Different Crops of Laver (Porphyra Yezoensis) During One Harvest Cycle. J. Ocean Univ. China. 2021, 20(01), 213–220. DOI: 10.1007/s11802-021-4447-3.
- Rao, A. R.; Ravishankar, G. A. Sustainable Global Resources of Seaweeds; SpringerSpringer: Cham, SwitzerlandCham, Switzerland, 2022Vol. 2. pp. 3–650
- Tang, J. H. Dynamic Analysis and Equipment Development for Laver (Porphyra Yezoensis) Harvesting; Dalian Ocean University: China, 2022.
- Tang, J. H.; Li, X. C.; Zhang, G. C.; Lu, W.; Ni, S.; Zhang, H. B.; Zhang, Q.; Zhai, Y. L.; Mu, G. Research Progress of Mechanized Harvesting Equipment and Technology of Laver. Fish. Mod. 2022, 49(03), 1–9.
- Wang, W.; Wang, S. L.; Zhang, J. Q.; Lv, X. L.; Yi, Z. Y. Experiment and Research on Cutting Mechanical Properties of Little Cabbage. Appl. Sci. 2022, 12(4), 2060. DOI: 10.3390/app12042060.
- Ma, Y. H. Agricultural Material Science; Chemical Industry Press: Beijing, China, 2015; pp. 1–159.
- Guo, J.; Han, F.; Zhou, Y.; Li, J.; Jiang, Y. L.; Jiang, T. T.; Liu, E. X.; Duan, J. L. Research on the Physical Characteristic Parameters of Banana Bunches for the Design and Development of Postharvesting Machinery and Equipment. Agric. 2021, 11(4), 362. DOI: 10.3390/agriculture11040362.
- Qiu, M. M.; Meng, Y. M.; Li, Y. Z.; Shen, X. B. Sugarcane Stem Cut Quality Investigated by Finite Element Simulation and Experiment. Biosyst. Eng. 2021, 206, 135–149. DOI: 10.1016/j.biosystemseng.2021.03.013.
- Chen, T. C. Study on Mechanical Properties of Kelp and Design of Mechanisms for Knotting Kelp; Southeast University: China, 2018.
- Lu, W.; Li, X. C.; Zhang, G. C.; Tang, J. H.; Ni, S.; Zhang, H. B.; Zhang, Q.; Zhai, Y. L.; Mu, G. Research on Biomechanical Properties of Laver (Porphyra Yezoensis Ueda) for Mechanical Harvesting and Postharvest Transportation. AgriEngineering. 2022, 4(1), 48–66. DOI: 10.3390/agriengineering4010004.
- Hassan-Beygi, S. R.; Ghozhdi, H. V.; Khazaei, J. Picking Force of Saffron Flower and Shear Strength of Saffron Stalk. Electron. J. Pol. Agric. Univ. 2010, 13(1), 1–11.
- Li, Z. Y.; Fu, J.; Luo, X. W. Tensile Properties and Fracture Mechanisms of Corn Bract for Corn Peeling Device Design. Agric. 2021, 11(8), 796. DOI: 10.3390/agriculture11080796.
- Diao, H. M. Study on the Basic Properties of Wheat Straw from Different Areas; Nanjing Agricultural University: China, 2014.
- Yu, Q. W.; Du, J. S.; Chen, X.; Liang, W.; Shen, Y. J.; Du, H. W.; Zhang, Y. H.; Zhang, Y. J. Analysis on Mechanical Properties of Three Flue-Cured Tobacco Cultivars in Bijie Tobacco Growing Area. Hunan Agric. Sci. 2018, 04, 78–80, 84.
- Chen, Y. X.; Chen, J.; Zhang, Y. F.; Zhou, D. W. Effect of Harvest Date on Shearing Force of Maize Stems. Livest. Sci. 2007, 111(1–2), 33–44. DOI: 10.1016/j.livsci.2006.11.013.
- Guo, Y. J.; Hu, X. L.; Liu, Q. F. Study on Shearing Force of Maize Stalk at Different Harvesting Time. J. of Anhui Agric. Sci. 2013, 41(21), 9133–9135.
- Liu, J. M.; Zhao, D.; Zhao, J. Study of the Cutting Mechanism of Oil Tree Peony Stem. For. 2020, 11(7), 760. DOI: 10.3390/f11070760.
- McRandal, D. M.; McNulty, P. B. Impact Cutting Behaviour of Forage Crops I. Mathematical Models and Laboratory Tests. J. Agric. Eng. Res. 1978, 23(3), 313–328. DOI: 10.1016/0021-8634(78)90104-X.
- Xu, B.; Jiang, H. Y.; Fan, M. D.; Chen, Y. Q.; Wang, R. L.; Du, J. S.; Zhang, Y. H. Threshing and Redrying Technology Based on Typical Mechanical Characteristics of Tobacco Leaves of Cv. “CB-1”. Tob. Sci. Technol. 2020, 53(07), 80–86,106.
- Zhang, X. J.; Yin, L. X.; Shang, S. Q.; Chung, S. -O. Mechanical Properties and Microstructure of Fuji Apple Peel and Pulp. Int. J. Food. Prop. 2022, 25(1), 1773–1791. DOI: 10.1080/10942912.2022.2107006.
- Li, J. W.; Ma, Y. H.; Tong, J.; Ma, Z. C.; Wang, L. D.; Yu, J. T. Mechanical Properties and Microstructure of Potato Peels. Int. J. Food. Prop. 2018, 21(1), 1395–1413. DOI: 10.1080/10942912.2018.1485031.
- Jacobs, A. A. A.; Scheper, J. A.; Benvenutti, M. A.; Gordon, I. J.; Poppi, D. P.; Elgersma, A. Tensile Fracture Properties of Seven Tropical Grasses at Different Phenological Stages. Grass Forage Sci. 2011, 66(4), 551–559. DOI: 10.1111/j.1365-2494.2011.00812.x.
- Su, Y.; Cui, T.; Zhang, D. X.; Xia, G. Y.; Gao, X. J.; He, X. W.; Xu, Y. Effects of Shape Feature on Compression Characteristics and Crack Rules of Maize Kernel. J. Food Process Preserv. 2020, 44(1), e14307. DOI: 10.1111/jfpp.14307.
- Demirel, C.; Kabutey, A.; Herak, D.; Gurdil, G. A. K. Numerical Estimation of Deformation Energy of Selected Bulk Oilseeds in Compression Loading. IOP Conf. Ser Mater. Sci. Eng. 2017, 237, 1–5. DOI: 10.1088/1757-899X/237/1/012004.
- Wang, J. X.; Cui, Q. L.; Li, H. B.; Liu, Y. P. Experimental Research on Mechanical Properties of Apple Peels. J. Eng. Technol. Sci. 2015, 47(6), 688–705. DOI: 10.5614/j.eng.technol.sci.2015.47.6.8.
- SuFen, Z. Marine Algae and Algae Culture Science; National Defense Industry Press: Beijing, China, 2012; p. 115.
- Wang, J. X. Apple Peel Multiscale Mechanical Properties Test and Microstructure Analysis; Shanxi Agricultural University: China, 2016.
- Hao, Y. F. Design and Application of Detection Platform for Micro Mechanical Properties of Agricultural Materials; China: Zhejiang University, 2021.
- Yada, S.; Chen, J. K.; Toda, M. Analysis of Cutting Mechanism of the Roll Type Nori Harvester. La mer. 1996, 34, 25–32.
- Morita, M.; Morita, K. High Performance Raw Seaweed Cutting Device. J.P. Patent 609,790,2B2, 22 March 2017.
- Kim, S.-K. Essentials of Marine Biotechnology; Springer: Nature Switzerland AG, 2019; pp. 145–196.
- Benvenutti, M. A.; Gordon, I. J.; Poppi, D. P.; Crowther, R.; Spinks, W.; Moreno, F. C. The Horizontal Barrier Effect of Stems on the Foraging Behaviour of Cattle Grazing Five Tropical Grasses. Livest. Sci. 2009, 126(1–3), 229–238. DOI: 10.1016/j.livsci.2009.07.006.
- Oke, B. O.; Kaul, R. N.; Mittal, J. P. Physical and Mechanical Properties of Sorghum (Sorghum Bicolor) Stalk Harvested at Various Intervals After Grain Maturity. Agric. Wastes. 1984, 11(1), 31–45. DOI: 10.1016/0141-4607(84)90053-2.
- Chen, Z. Y. Experimental Study on Axial-Flow Peanut Picking Device with Bending-Tooth Screw Roller; Shenyang Agricultural University: China, 2017.
- Iwaasa, A. D.; Beauchemin, K. A.; Buchanan-Smith, J. G.; Acharya, S. N. Effect of Stage of Maturity and Growth Cycle on Shearing Force and Cell Wall Chemical Constituents of Alfalfa Stems. Can. J. Anim. Sci. 1996, 76(3), 321–328. DOI: 10.4141/cjas96-048.
- Niwa, K.; Furuita, H.; Yamamoto, T. Changes of Growth Characteristics and Free Amino Acid Content of Cultivated Porphyra Yezoensis Ueda (Bangiales Rhodophyta) Blades with the Progression of the Number of Harvests in a Nori Farm. J. Appl. Phycol. 2008, 20(5), 687–693. DOI: 10.1007/s10811-007-9273-5.
- Masuda, Y.; Yamada, H.; Yokoo, K.; Kawamur, Y. Changes of the Water Content Rate and the Thickness of Cell Wall in Nori Thalli on Every Harvest. Bull. Saga Prefectural Ariake Fish. Res. Dev. Cent. 2014, 27, 55–59.
- Sun, L. X.; Sun, H.; Wang, Y. N.; Zhang, J. D.; Huang, M. The Study on Bolt Quality of Rape for Oilseed-Vegetable-Dual-Purpose in Different Picking Periods. Qual. Saf. Agro-Prod. 2021, 02, 74–79.
- Wang, Y.; Yang, Y.; Zhao, H. M.; Liu, B.; Ma, J. T.; He, Y.; Zhang, Y. T.; Xu, H. B. Effects of Cutting Parameters on Cutting of Citrus Fruit Stems. Biosyst. Eng. 2020, 193, 1–11. DOI: 10.1016/j.biosystemseng.2020.02.009.
- Heidari, A.; Chegini, G. R. Determining the Shear Strength and Picking Force of Rose Flower. Electron. J. Pol. Agric. Univ. 2011, 14(2), 1–11.
- Khazaei, J.; Rabani, H.; Ebadi, A.; Golbabaei, F. Determining the Shear Strength and Picking Force for Pyrethrum Flower. AIC Paper No: 02-221, CSAE. 2002, Mansonville, Que: Canada.
- Wu, X. Y. Study on Fracture Behavior of Hydraulic Concrete Based on DIC and Acoustic Emission Technology; China: Yangzhou University, 2022.
- Van der Wal, A.; Gaymans, R. J. Polypropylene–Rubber Blends: 3. The Effect of the Test Speed on the Fracture Behaviour. Polym. 1999, 40(22), 6045–6055. DOI: 10.1016/S0032-3861(99)00214-1.
- Chattopadhyay, P. S.; Pandey, K. P. Mechanical Properties of Sorghum Stalk in Relation to Quasi-Static Deformation. J. Agric. Eng. Res. 1999, 73(2), 199–206. DOI: 10.1006/jaer.1999.0406.
- Song, Z. H.; Song, H. L.; Geng, A. J.; Li, Y. D.; Yan, Y. F.; Li, F. D. Experiment on Cutting Characteristics of Cotton Stalk with Double Supports. Trans. Chin. Soc. Agric. Eng. 2015, 31(16), 37–45.
- Song, S. Y.; Zhou, H. P.; Jia, Z. C.; Xu, L. Y.; Zhang, C.; Shi, M. H.; Hu, G. M. Effects of Cutting Parameters on the Ultimate Shear Stress and Specific Cutting Energy of Sisal Leaves. Biosyst. Eng. 2022, 218, 189–199. DOI: 10.1016/j.biosystemseng.2022.03.011.
- Mathanker, S. K.; Grift, T. E.; Hansen, A. C. Effect of Blade Oblique Angle and Cutting Speed on Cutting Energy for Energycane Stems. Biosyst. Eng. 2015, 133, 64–70.
- Taghijarah, H.; Ahmadi, H.; Ghahderijani, M.; Tavakoli, M. Shearing Characteristics of Sugar Cane (Saccharum Officinarum L.) Stalks as a Function of the Rate of the Applied Force. Aust. J. Crop Sci. 2011, 5(6), 630–634.
- Tavakoli, H.; Mohtasebi, S. S.; Jafari, A. Effect of Moisture Content and Loading Rate on the Shearing Characteristics of Barley Straw by Internode Position. Agric. Eng. Int. CIGR J. 2009, 11, 1176–1186.
- Johnson, P. C.; Clementson, C. L.; Mathanker, S. K.; Grift, T. E.; Hansen, A. C. Cutting Energy Characteristics of Miscanthus X Giganteus Stems with Varying Oblique Angle and Cutting Speed. Biosyst. Eng. 2012, 112(1), 42–48.
- Chen, Y. L.; Zhong, C. F.; Xu, Y. N.; Du, B.; Ren, Y. H.; Li, P. Study on Quality Differences of Dendrobium Officinale in Different Areas. Food Ferment. Ind. 2020, 46(8), 123–130.
- Shimada, Y. Physiological and Morphological Characters of the Three Wild Strains of Porphyra Yezoensis Collected from Hokkaido. Aquic. Sci. 2010, 58(4), 473–479.
- Morikawa, T.; Mine, T. The Effect of Salinity on the Thallus Thickness of Pyropia Yezoensis. Bull. Saga Prefectural Ariake Fish. Res. Deve. Cent. 2017, 28, 1–3.
- Zhang, X.; Wang, H.; Fang, E. J.; Gao, Y.; Guo, B.; Liu, K. F.; Xu, X. F.; Chen, W. Preliminary Study on the Cultivation of Porphyra Yezoensis in Bohai Bay. Mar. Sci. Bull. 2019, 21(01), 87–96.
- Yang, H. Q.; Zhou, J. H.; Li, Y. P.; Ma, W. G.; Yang, C.; Duan, F. Y.; Hu, J. J. Analysis of Physical Characteristics of Tobacco Leaves from Different Cultivars and Different Production Areas in Yunnan. Acta Tab. Sin. 2008, 14(06), 30–36.