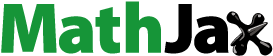
Abstract
Improving the performance of storage units is important for saving energy. An implicit approach has been combined with the adaptive grid in this modelling for the presentation of solidification inside the tank with a sinusoidal cold surface. Not only the implementation of curved will but also the inclusion of nanoparticles was assumed as a passive technique for expediting freezing. The scalars were extracted by the Galerkin approach. The formulation of nanomaterial features was done by considering uniform concentration inside the domain. Increasing the fraction of CuO can reduce the freezing time from 2211.13 to 1943.72 s and 1675.37 s if the blade shape is selected. The augmentation of shape factor and fraction of nanomaterial lead to the reduction of freezing time by about 6.98% and 24.23%, respectively. The results proved that ϕ has a stronger effect than other active parameters.
1. Introduction
Because of the great ability of PCM in saving heat, it can be applied for different usages [Citation1–3]. For these applications, various kinds of PCM can be implemented [Citation4–8] which depend on the type of usages and ranges of temperature [Citation9–12]. If the material has low conductivity, it can reduce the speed of the process [Citation13–16]. To remove this drawback and ameliorate the amount of stored energy, different remedies have been suggested [Citation17–20]. Several researchers offered passive approaches, such as adding nanoparticles to modify the feature of PCM [Citation21–23]. Besides, mounting fins can augment the movement of the solid front [Citation23–26]. Lacroix and Benmadda [Citation27] utilized the special style of fins with variable sizes to increase the hot flow penetration. They utilized a fixed style grid incorporating implicit methods and showed that augmenting the length of the fin can enhance the melting process.
The reduction of the period of melting phenomena within a finned enclosure was scrutinized in Ref. [Citation28]. The authors prepared an experimental system and considered various ranges of heat flux. They proved that the completion time augments with the rise of the number of fins. The charging process with close contact with nanoparticles was analysed by Hu et al. [Citation29]. The authors added graphene powder to the paraffin and conducted an empirical test. They discovered that augmenting a fraction of nanomaterial more than 3%wt could lead to a reverse effect. The optimization of the configuration of fins was premeditated by Deng et al. [Citation30] who exploited FVM in modelling, involving buoyancy force impact. They depicted that the arrangement of fins can play a key role in minimizing the period of the process. The container with edges was scrutinized by Tian et al. [Citation31] to evaluate the melting. They applied various types of fins and found that copper fins could show the best performance in which the period of melting was reduced by 41.6%.
In previous articles, the authors tried to suggest a new approach for reducing the time of the process and they found that adding additives in addition to changing geometry can be helpful. In this attempt, two different shapes of nanoparticles made from copper oxide were mixed with water. The container was filled with NEPCM and it had one right sinusoidal wall to maintain cold conditions. The model of the present unsteady problem was solved by the Galerkin method. It was verified first and then the impacts of active factors were illustrated in results.
2. Solidification process and modelling
The container, as depicted in Figure , contains three insulated walls and one sinusoidal cold right wall. The applied PCM is H2O which can be mixed with CuO nanoparticles to enhance the thermal treatment. The concentration of powders is lower than 0.07 and a uniform concentration was applied for all positions inside the domain. Since the velocity has a low role in freezing, the equations become simpler as below [Citation32]:
(1)
(1)
(2)
(2) To discover the required properties needed for solving Equation (1), the below equations have been implemented [Citation32]:
(3)
(3)
(4)
(4)
(5)
(5)
(6)
(6)
The main assumption for utilizing the above equation is considering a homogeneous mixture for nanomaterial and also in deriving knf, the impact of shape factor has been included. For finding the solution, the Galerkin approach was utilized incorporating an adaptive grid, as suggested by Sheikholeslami, [Citation33] who published several papers in this field. The utilizing time-dependent grid and automatic time step make this approach more powerful.
3. Results and discussion
The development of a powerful numerical approach for simulating the transient problem involving implicit technique has been utilized in the current attempt. Freezing of water within a container with a sinusoidal wall was modelled with nanoparticles (CuO). The inner sinusoidal wall makes the solid front a curved shape and dispersing nanomaterial augments the process. Although gravity has some effect on this process, to reduce the computational cost, this effect has been ignored because liquid water has a low velocity during freezing. Galerkin approaches for this work have been implemented to solve the two remaining equations and the amounts of T and S have been extracted in each time step. For more description of nanomaterial impact, two factors were analysed:shape factor and the fraction of nanoparticles. The grid should be denser near the region of the solid front and this note was applied in this study, as demonstrated in Figure . Low deviation, shown in Figure in comparison with the previous publications [Citation33,Citation34], proves the nice accuracy of the present model.
Figure 3. Testing accommodation of the code with Ref. [Citation33,Citation34].
![Figure 3. Testing accommodation of the code with Ref. [Citation33,Citation34].](/cms/asset/0af0d1ae-9d34-4670-8413-a0365885bbdd/tusc_a_2141030_f0003_oc.jpg)
The efficacy of active factors on the distribution of scalars has been illustrated in Figures and . In these figures, the amounts of S and T inside the various positions of the domain in three time levels were demonstrated. The NEPCM begins to convert ice near the sinusoidal wall. Both factors can augment the conduction mode, thus reducing the required time of the process. With increasing the mass of nanoparticles, the time of phenomena changes from 2211.13 to 1675.32 and 1943.72 s when blade and cylinder particles are utilized. Also, altering the shape factor can change the time from 2023.29 to 1943.72 s (when ϕ = 0.02) and from 1801.09 to 1675.37 s (when ϕ = 0.04). Augmenting ϕ has a more sensible impact on this process. Figures and portray the impact of ϕ on the promotion of freezing with reporting heat released profile in addition to solid front curves. With the inclusion of more nanomaterial, the conduction can play a more effective role and quicker freezing can take place. The volume of solid PCM surges as the time augments which compromises lower latent heat. A greater value of S can be seen when a higher level of ϕ is utilized.
Figure 4. How m can change the freezing behaviour.
The shape factors depicted in Figures and show a greater speed of solidification. The shape of particles canimpact the performance of the system and the result shows that higher levels of this parameter can increase the amount of solid fraction and the time of achieving the full solid phase declines. It can be seen from time-dependent graphs that the amount of latent heat will be decreased with the augmentation of time and considering a higher shape factor can also reduce this function. The time for converting whole liquid to ice is essential in analysing the system illustrated in Figure . The time for reaching SF = 1 has been derived for all cases and according to those data, correlations have been derived and have been shown as contours and plots. When m = 4.8 and 8.6, augmenting ϕ from 0 to 0.02 leads the freezing time to reduce by about 8.49% and 12.09%. Also, this change can be more effective when ϕ reaches 0.04 and freezing time declines about 18.54% and 24.23%. As the shape factor grows, the time declines by about 3.93% and 6.89%. With the growth of ϕ from 0.02 to –0.04, the time can be reduced by around 10.98% and 13.8%.
4. Conclusion
Nanoparticles with two shapes were considered the technique of increment of the rate of freezing in this research. The governing equations were simplified by involving the assumption of neglecting the impact of the velocity of liquid NEPCM. The container has three insulated walls and one sinusoidal cold wall. As anticipated, the freezing starts from the vicinity of the curved wall and the ice front goes to the outer wall as time increases. The formulation of nanomaterial was based on a single-phase model and unsteady terms were modelled based on an implicit technique. To obtain the solution to the present problem, the Galerkin method was incorporated and distributions of solid fraction and T were extracted in various time steps. The verification, based on previous numerical data, shows great accuracy of the present approach. For more accurate results, the mesh has been considered as time-dependent in which a denser grid was applied near the position of SF = 0.95. The performances of systems with various levels of active parameters have been presented in the outputs. In the freezing process, the velocity of PECM is not high and the chief mechanism during the phenomena is conduction. Thus, changing the features of PCM with the inclusion of nanoparticles can help expedite the process. The features of NEPCM were measured by considering the assumption of a uniform fraction of particles within the domain. The time of reaching SF = 1 was estimated for all cases and accordingly, contours and plots were derived. As m grows the time drops about 3.93% and 6.89%. With the growth of ϕ from 0.02 to –0.04, the time can be reduced by about 10.98% and 13.8%. Given m = 4.8 and 8.6, increasing ϕ from zero to 0.02 leads the discharging time to decrease about 8.49% and 12.09%. Also, this alteration can be more effective when ϕ reaches 0.04 and solidification time reduces by about 18.54% and 24.23%. The NEPCM begins to convert ice near the sinusoidal wall. Both factors can augment the conduction mode, thus decreasing the required time of the process. By augmenting the mass of nanoparticles, the time of phenomena alters from 2211.13 to 1675.32 s and 1943.72 s when blade and cylinder particles were utilized. Also, altering the shape factor can change the time from 2023.29 to 1943.72 s (when ϕ = 0.02) and from 1801.09 to 1675.37 s (when ϕ = 0.04). With the inclusion of more nanomaterial and increasing shape factor, the conduction can play a more effective role and faster solidification can take place. The volume of solid PCM rises as time increases which offer lower latent heat and the temperature of the domain decreases. A greater amount of S can be seen when a higher level of m and ϕ is incorporated. The quickest process takes 1675.37 s when m = 8.6 and ϕ = 0.04.
Disclosure statement
No potential conflict of interest was reported by the author(s).
References
- Qin Y. Numerical modeling of energy storage unit during freezing of paraffin utilizing Al2O3 nanoparticles and Y-shape fin. J Energy Storage. 2021;44(Part B):103452. DOI:10.1016/j.est.2021.103452
- Othman HA, Rguigui H, Altoum SH, et al. Nanomaterial efficacy on freezing of PCM with involvement of numerical simulation. J Mol Liq. 2022;362:119658. DOI:10.1016/j.molliq.2022.119658
- Sheikholeslami M. Numerical analysis of solar energy storage within a double pipe utilizing nanoparticles for expedition of melting. Sol Energy Mater Sol Cells. 2022;245:111856. DOI:10.1016/j.solmat.2022.111856
- Omri M, Bouterra M, Ouri H, et al. Entropy generation of nanofluid flow in hexagonal microchannel. J Taibah Univ Sci. 2022;16(1):75–88. DOI:10.1080/16583655.2022.2031567
- Samylingam I, Aslfattahi N, Kadirgama K, et al. Improved thermophysical properties of developed ternary nitrate-based phase change material incorporated with MXene as novel nanocomposites. Energy Eng. 2021;118(5):1253–1265. DOI:10.32604/EE.2021.016087
- Wang T, Almarashi A, Al-Turki YA, et al. Approaches for expedition of discharging of PCM involving nanoparticles and radial fins. J Mol Liq. 2021;329:115052. DOI:10.1016/j.molliq.2020.115052
- Chu Y-M, Nazir U, Sohail M, et al. Enhancement in thermal energy and solute particles using hybrid nanoparticles by engaging activation energy and chemical reaction over a parabolic surface via finite element approach. Fractal Fract. 2021;5(3):17. Article 119. DOI:10.3390/fractalfract5030119
- Algehyne EA, Aldhabani MS, Saeed A, et al. Mixed convective flow of Casson and Oldroyd-B fluids through a stratified stretching sheet with nonlinear thermal radiation and chemical reaction. J Taibah Univ Sci. 2022;16(1):193–203. DOI:10.1080/16583655.2022.2040281
- Sheikholeslami M. Analyzing melting process of paraffin through the heat storage with honeycomb configuration utilizing nanoparticles. J Energy Storage. 2022;52(Part B):104954. DOI:10.1016/j.est.2022.104954
- Chu Y-M, Abu-Hamdeh NH, Ben-Beya B, et al. Nanoparticle enhanced PCM exergy loss and thermal behavior by means of FVM. J Mol Liq. 2020;320(Part B):114457. DOI:10.1016/j.molliq.2020.114457
- Guo Z, Yang J, Tan Z, et al. Numerical study on gravity-driven granular flow around tube out-wall: effect of tube inclination on the heat transfer. Int J Heat Mass Transfer. 2021;174:121296. DOI:10.1016/j.ijheatmasstransfer.2021.121296
- Huang K, Su B, Li T, et al. Numerical simulation of the mixing behaviour of hot and cold fluids in the rectangular T-junction with/without an impeller. Appl Therm Eng. 2022;204:117942. DOI:10.1016/j.applthermaleng.2021.117942
- Chang H, Han Z, Li X, et al. Experimental investigation on heat transfer performance based on average thermal-resistance ratio for supercritical carbon dioxide in asymmetric airfoil-fin printed circuit heat exchanger. Energy. 2022;254:124164. DOI:10.1016/j.energy.2022.124164
- Veera Krishna M, Ameer Ahammad N, Algehyne EA. Unsteady MHD third-grade fluid past an absorbent high-temperature shrinking sheet packed with silver nanoparticles and non-linear radiation. J Taibah Univ Sci. 2022;16(1):585–593. DOI:10.1080/16583655.2022.2087396
- Chu Y-M, Hajizadeh MR, Li Z, et al. Investigation of nano powders influence on melting process within a storage unit. J Mol Liq. 2020;318:114321. DOI:10.1016/j.molliq.2020.114321
- Guo Z, Tian X, Wu Z, et al. Heat transfer of granular flow around aligned tube bank in moving bed: experimental study and theoretical prediction by thermal resistance model. Energy Convers Manage. 2022;257:115435. DOI:10.1016/j.enconman.2022.115435
- Cui W, Si T, Li X, et al. Heat transfer analysis of phase change material composited with metal foam-fin hybrid structure in inclination container by numerical simulation and artificial neural network. Energy Rep. 2022;8:10203–10218. DOI:10.1016/j.egyr.2022.07.178
- Wu Y, Zhao Y, Han X, et al. Ultra-fast growth of cuprate superconducting films: dual-phase liquid assisted epitaxy and strong flux pinning. Mater Today Phys. 2021;18:100400. DOI:10.1016/j.mtphys.2021.100400
- Guo C, Zhang Z, Wu Y, et al. Synergic realization of electrical insulation and mechanical strength in liquid nitrogen for high-temperature superconducting tapes with ultra-thin acrylic resin coating. Supercond Sci Technol. 2022;35:075014. DOI:10.1088/1361-6668/ac6e0d
- Li J, Han C, Ou X, et al. Concentrated electrolyte for high-performance Ca-ion battery based on organic anode and graphite cathode. Angew Chem Int Ed. 2022;61. DOI:10.1002/anie.202116668
- Zhang X, Tang Y, Zhang F, et al. A novel aluminum-graphite dual-ion battery. Adv Energy Mater. 2016;6(11):1502588. DOI:10.1002/aenm.201502588
- Hamdi AYED, Othman HA, Zhang Y, et al. Thermal storage evaluation in existence of nano-sized additives by mean of numerical method. J Energy Storage. 2022;55(Part B):105582. DOI:10.1016/j.est.2022.105582
- Han M, He H, Kong W, et al. High-performance electret and antibacterial polypropylene meltblown nonwoven materials doped with boehmite and ZnO nanoparticles for air filtration. Fibers Polym. 2022. DOI:10.1007/s12221-022-4786-8
- Chu Y-M, Yadav D, Shafee A, et al. Influence of wavy enclosure and nanoparticles on heat release rate of PCM considering numerical study. J Mol Liq. 2020;319:114121. DOI:10.1016/j.molliq.2020.114121
- Rehman WU, Khan SU-D. Thermoplastic polyurethane conjugated antimony doped tin oxide nanocomposite for enhanced electrical and thermal conductivity. Synth Met. 2020;269:116570.
- Majid A, Iqbal J, Ali A. Structural, optical and magnetic properties of Ce–GaN based diluted magnetic semiconductor. J Supercond Novel Magn. 2011;24(1):585–590.
- Lacroix M, Benmadda M. Numerical simulation of natural convection-dominated melting and solidification from a finned vertical wall. Numer Heat Transfer, Part A Appl. 1997;31(1):71–86.
- Acır A, Emin Canlı M. Investigation of fin application effects on melting time in a latent thermal energy storage system with phase change material (PCM). Appl Therm Eng. 2018;144:1071–1080.
- Hu N, Zhu Z-Q, Li Z-R, et al. Close-contact melting heat transfer on a heated horizontal plate: revisited in the presence of nano-enhanced phase change materials (NePCM). Int J Heat Mass Transfer. 2018;124:794–799.
- Deng S, Nie C, Jiang H, et al. Evaluation and optimization of thermal performance for a finned double tube latent heat thermal energy storage. Int J Heat Mass Transfer. 2019;130:532–544.
- Tian L-L, Liu X, Chen S, et al. Effect of fin material on PCM melting in a rectangular enclosure. Appl Therm Eng. 2020;167:114764.
- Sheikholeslami M. Finite element method for PCM solidification in existence of CuO nanoparticles. J Mol Liq. 2018;265:347–355. DOI:10.1016/j.molliq.2018.05.132
- Sheikholeslami M. Numerical simulation for solidification in a LHTESS by means of nano-enhanced PCM. J Taiwan Inst Chem Eng. 2018;86:25–41.
- Ismail K, Alves C, Modesto M. Numerical and experimental study on the solidification of PCM around a vertical axially finned isothermal cylinder. Appl Therm Eng. 2001;21:53–77.