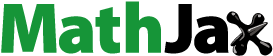
ABSTRACT
This research aims to experiment with the integration of agricultural solid wastes into the manufacturing process of cementitious materials, ensuring that the resulting products exhibit satisfactory durability and mechanical properties. In this study, geopolymer composite (GP) was prepared using ground granulated blast furnace slag (BFS) and Arachis hypogaea (AH) fine dry peels as an example of agriculture waste is commonly available in Egypt. Some selected GP mixes were reinforced by nano magnetite (Fe3O4,NF). The prepared GP was cured for 28 days at two different circumferences, a normal curing at 25°C or hydrothermal curing at 60°C/0.02MPa. The setting times and compressive strength of the different types of manufactured general purpose (GP) were evaluated. The durability of the prepared GP against firing as well as H2SO4 acid (5%) attack were measured. The findings demonstrated that BFS/AH based GP offered diminished setting times and GP mixes hydrothermally cured at 60°C/0.02MPa adopted higher mechanical properties than those cured normally at room temperature. Besides, incorporation of AH dry peels up to 10% in GP manufacturing boosted the mechanical properties during the first 3 days for GP mixes cured at room temperature. Additionally, in comparison to the reference mix, the blended mix showed an accepted resistance to the effect of firing and astonishing resistance to acid attack. Admixing GP with 1% NF improved its durability in the two deterioration actions studied.
Introduction
In recent decades, the world faces many environmental and economic challenges due to the continuous development of many industries. One of these industries is the cement industry. However, cement industry has many environmental hazardous issues because of the gas emissions which threaten human health and the environmental safety [Citation1–4]. In addition, the use of huge amounts of energy and large quantities of raw resources are serious defects that face this industry [Citation5–8]. One other hand, huge tons of agricultural waste were accumulated in the surrounding forming many economic and pollution problems. Most agriculture residues were generally left behind or burned in fields. A fraction of these wastes is used in land filling or wood industry which is not a reasonable solution for managememt and benefit of the huge amounts of these wastes [Citation9,Citation10]. Several studies have been done and revealed that the ash of agriculture wastes contains a high percent of amorphous silica and could be consider as a pozzolanic material in blended cement manufacture [Citation11,Citation12]. Recycling of agriculture wastes for production sustainable cementitious materials presents a solution for conserving resources, cost effective and cleans the environment [Citation13,Citation14]. Agriculture wastes can also serve as aggregates in concrete with high strength and excellent durability [Citation15,Citation16]. Meanwhile, consider to the knowledge of authors, few research were used the dry powders of the agriculture wastes in the manufacture of cementitious materials that may be more economic and green treatment.
Geopolymer composites (GP) had received a great attention recently as a solution for more green and sustainable binder that could replace the traditional Portland cement (PC) [Citation17,Citation18]. In contrast to traditional cement, GP manufacture does not consume the energy needed for grinding or firing the raw materials in cement kiln. Indeed, there will be no impacts of CO2 or dust emission on the environment [Citation19–21]. Many attempts have been done to fabricate GP from industrial wastes to reduce the cost and mitigate their accumulation risks in the future. Blast furnace slag [Citation18], fly ash [Citation22], clay bricks [Citation23], glass waste [Citation24], marble dust [Citation25,Citation26] and kiln dust [Citation27] are examples of industrial wastes had been incorporated in GP fabrication. From technical point, GP offers many attractive properties like, the fast setting and hardening, acceptable mechanical properties, good performance in acidic and the corrosive ions medium [Citation28,Citation29]. However, GP based on dry agricultural wastes has not been assessed yet by the researchers.
Admixing cement or concrete by nanoparticles is a common strategy for enhancing the workability, improving the durability and ultimate strength [Citation30–33]. Nano-sized magnetite (Fe3O4) served as reinforcing particles in building materials, acting as a robust filler that diminishes pore size and contributes to a denser structure [Citation34]. The present study seeks to examine the performance of GP prepared from the dry powder of BFS and Arachis hypogaea (AH) fine peels. The physico-mechanical characterizations and durability in fire and acid circumferences were evaluated.
Experimental procedures
Materials characteristics
Granulated blast furnace slag (BFS), with a specific gravity equal 2.85 g/cm3, derived from Helwan factory for steel, Helwan provinces, Cairo. XRD of BFS were provided in . Arachis hypogaea (AH) peels were supplied from our local stores. The peels were rinsed, oven-dried at 60°C for three hours, and subsequently crushed to achieve a particle size ≤70 µm with a specific gravity equal 0.238 g/cm3. FTIR of AH is apparent in . According to , two broad bands, observed at 3361 and 1641 cm−1, are indicative of the stretching vibrations of (–OH) groups in alcohols. Additionally, there are three distinct spectral bands centered at 2891, 1867, and 1411 cm−1, which correspond to the vibrational modes of the C=O bond in ketones and aldehydes. Furthermore, a sharp band at 990 cm−1 is associated with the stretching of the C=C bond in unsaturated fatty acids. Chemical oxides composition of BFS and AH were inspected via XRF and shown in . Sodium hydroxide (NaOH) with 99% purity, Sodium silicates (purity 98%) were used as alkaline activator for GP fabrication. Nano Fe3O4 (NF) was prepared via sol-gel method as mentioned in our pervious study [Citation33,Citation35]. shows SEM of nano Fe3O4 (NF).
Table 1. Chemical oxide % of BFS and AH.
GP preparation
Various dry general-purpose (GP) powders were created by substituting blast furnace slag (BFS) with 0, 2.5, 5, 10, and 15 wt.% from Arachis hypogaea dry fine peels (AH) peels. The GP dry blend was then homogenized by milling in a ball mill for a duration of 6 hours. illustrates the notation of each GP mix and its composition. The mixture of NaOH (6 M) and Na2Si2O3 (4 M) by volume ratio 1:1 was used as alkaline activator. Preparation of GP done by adding the GP dry mix to the alkaline solution with W/S ratio 1:2 with continuous mixing in mixing machine for 3 minutes. The acquired paste was molded into cubic samples using 1-inch cubic molds. Subsequently, the samples underwent curing in two conditions: hydrothermal conditions at 60°C/0.02MPa in an oven and at room temperature at 25 ± 2° ° C in RH = 99% for twenty-eight days.
Table 2. GP notation and their composition.
Testing
Vicat apparatus was utilized to determine the setting times consider to ASTM C191 [Citation36]. Compressive strength (CS) was assessed for every GP sample after 1,3,7 and 28 days corresponding to ASTM C109 M-20a [Citation37] utilizing the Ton-Industries compressive strength machine with a maximum load capacity of 60 tons. At each test, CS was measured for three cubes and the mean value was adopted.
Durability tests
The durability of the prepared GP was tested against firing and attack by acid. Firing test was applied as follow. After curing the GP samples for 28 days (at 60°C or at room temperature), the hardened cubes were dried at 80°C in a dryer for 12 hours. Subsequently, they were fired at 300°C, 600°C, and 800°C for 3 hours in a muffle furnace (with a firing rate of 10°C/min). Following the firing process, the cubes gradually cooled to room temperature. The compressive strength (CS) of the fired cubes was evaluated, and the residual strength percentage (RS%) was determined according to EquationEquation 1(1)
(1) :
CS₀ and CSt represent the strengths values before and after heating, respectively.
Acid resistance was inspected for GP pastes cured for 28-days, all hardened cubes were dried at 80°C in an dryer for 12hrs then immersed in 2N sulfuric acid up to 60 days. After 15,30, 45 and 60 days of stay in acid solution, the cubes were removed, gentle washed and subjected to compressive strength test [Citation26,Citation38]. XRD was performed using cobalt target (λ = 0.17889 nm), and filter made of nickel under 40 kV and 40 mA with a scanning range spanned from 5 to 60 (2θ°), and a scanning speed of 1s/step and a resolution of 0.02/step. Thermo-gravimetric test was performed using TGA: TA devices, model SDT Q600 for identifying the phases formed while the geopolymerization of the diverse geopolymer specimens. SEM micrographs for the formed hydrates were inspected using SEM – Quanta 250 FEG device.
Results and discussion
Setting times
Setting times of the geopolymer pastes synthesized by replacing BFS with different proportions of AH (0%,2.5%,5%,10% and 15%) are demonstrated in . Notably, setting time depends mainly on two parameters; (i)the amount of aluminum silicate sourced from the used precursors and/or (ii)the concentration of the alkaline operator used. Here, mixture of NaOH/Na2Si2O3, is acting as Na2O source, exhibited the capacity to dismantle and dissolve the amorphous alumino-silicate content across the started precursors to initiate the polymerization process. Setting times for mix B were 127 and 184 minutes, while as, shorter times were recorded for the blended mixes [Citation39]. Furthermore, as the % of replacement increase the setting times diminished. This fact can be related to the filling action of fine AH powders which blocked the pores and accelerated the initial hardening of the paste. Besides, the highwater absorptivity of AH peels removed the excess water from GP system leading to quick drying of the paste and accelerating the setting process. Setting times are additionally more diminished when GP mix reinforced by 1% NF, mix AH10-F. Such behavior can be related to dispersion of NF particles in blended system which possesses a seeded nucleation phenomena on which the GP networks started to build up, fill the pores and accelerate the setting process [Citation40,Citation41].
Compressive strength
depicts the compressive strength (CS, in MPa) of different GP pastes made from BFS and fine AH peels, cured either at room temperature or hydrothermally at 60°C/0.02MPa for a duration of twenty-eight days. Generally, for all pastes, the CS was increased continuously throughout the testing period. The sustained and continuous rise in compressive strength with processing time is contingent upon the advancement of polymerization reactions and the reinforcement of the general-purpose (GP) skeleton through the deposition of two primary hydrate phases: calcium silicate hydrates (C-S-H) gels and calcium-aluminate-silicate hydrates (C-A-S-H) gel as verified by XRD testing. GP hydrothermally cured at 60°C/0.02MPa reported CS values higher than GP cured at room temperature. Hydrothermal curing of GP pastes accelerates the geopolymerization reactions compared to room curing leading to accumulation of more hydration/geopolymerization products [Citation42,Citation43]. Blended GP pastes cured at room temperature and containing 2.5; mix AH2.5, exhibit a development in the compressive strength up to 7 days than control mix (B mix). While the GP paste containing 5 or 10 % of AH show boosting in strength during the first three days of geopolymerization reaction. This behavior can be responded to the formation of geopolymerization hydrates like as, C-S-H, C-A-S-H and magnesium aluminum silicate hydrate (M-A-S-H). Furthermore, the filling characteristic of dry AH peels blocks the pores and boost the strength in early treatment period. Whiles, and due to the low quantity of GPs᾿hydrates as well as the low mechanical properties of MASH, low compressive strength were observed for AH-blend GP after 28-days. Higher replacement of AH peels, 15 wt.%, did not exhibit the same astonishing compressive strength especially at later curing times in violation with the control mix and about 45 % reduce in CS was recorded for AH15 mix at 28 days. This can be resulted from the lower content of slag in this mix (high pazzolanic material) by less active one; AH dry peels and subsequently, less hydrated phases are formed in AH15 mix compared to the other blended mixes.
Figure 3. Compressive strength of the different GP samples when curing at (a) room temperature, (b) 60°C/0.02MPa.
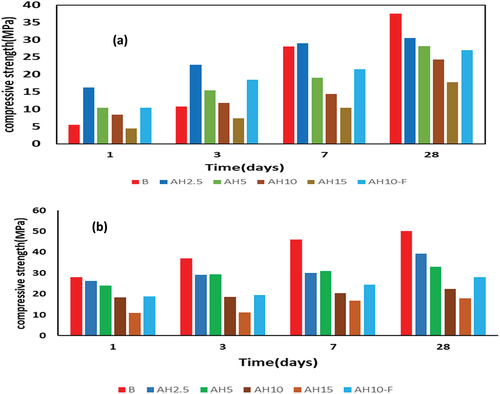
Blended GP pastes cured hydrothermally at 60°C/0.02MPa showed a drop in the given strength compared to B mix cured at the same condition. The reduction in CS for GP mixes hydrothermally cured increases as the % of AH increase in the blended paste and became more notable in the later curing times. Such finding can be related to high activation of BFS by thermal curing at 60 °C/0.02MPa leading to acceleration and fast condensation/polymerization of geopolymeric fragments of cross-linked aluminosilicate oligomers [Citation44]. On other side, AH dry peels not highly affected by the thermal activation. Furthermore, the cellulose fibers of AH dry peels hinder the appropriate backing between GP chains leading to lose the matrix of blended GP with a lower strength [Citation45]. For improving the CS of the fabricated blended GP, 1% of nano Fe3O4 (NF) was admixed to AH10 (mix AH10-F). AH10-F mix shows a development in CS after 1, 3, 7 and 28 days of normal curing at 25°C by about 23.8, 63.7, 49.3 and 11.1% for AH10-F compared to AH10 mix. Besides, AH10-F mix offers CS values higher than B mix after 1 and 3 days. Meanwhile, for GP mixes cured hydrothermally at 60° C/0.02MPa, AH10-F shows boosting in CS by 5.5, 7, 21 and 28.5 % compared to AH10 at the four tested curing ages. This reflects the positive impact of NF to improve the geopolymerization products which could be related to the catalytic effect of NF which improves the geopolymerization reactions leading to high amounts of the hydration products at low curing times [Citation19].
Durability action
Fire resistivity test
demonstrates the residual strength (RS)t for B, AH5, AH10 and AH10-F mixes that cured at room temperature after firing at 300, 600 and 800°C for 3 hrs and gradually cooled to room temperature in desiccators. Evidently, all the tested samples show a notable reduced in CS through firing at 300°C temperatures. The decline in compressive strength (CS) is amplified for all general-purpose (GP) samples as the firing temperature increases from 300 to 800 °C. RSt for B, AH5, AH10 and AH10-F mixes cured at room temperature then fired at 300° C were 61, 53, 50 % and 54.5 % respectively. While through firing at 800°C, all tested composites had tremendous loss in their RSt magnitudes samples. Reduction in RSt can be responded to thermal degradation of the hydrated phases, which is especially leaning on the kind and amount of geopolymer hydrates subsequently responded to the model for the initial precursors and the circumference of the hydrates growth [Citation21,Citation46]. Nevertheless, GP with NPs, AH10-F mix, appeared a lower reduced in CS upon firing in violation of its analog without NPs, mix AH10. The resistance to the effects of firing is linked to the effective spreading of Fe3O4 nanoparticles through the geopolymer matrix and the accumulation of a higher yield of hydrated products in this mixture [Citation24,Citation33,Citation47]. Similar behavior coexists for GP mixes hydrothermally cured at 60° C/0.02MPa then fired at various temperatures, . Moreover, all GP samples hydrothermally cured at 60°C/0.02MPa pretend more resistivity to the firing actions than those normally cured at room temperatures. RSt for B, AH5, AH10 and AH10-F samples cured at 60 °C/0.02MPa and fired at 300 °C were 88, 43, 52 and 55 respectively. Firing at 800 °C resulted in RSt values 42, 38, 26 and 58 % respectively.
Acid resistivity
Acid resistivity test is conducted on GP mixes which are cured at 25°C or hydro-thermally cured at 60 °C/0.02MPa. This is done via exposure to the 28-hydrated samples to H2SO4 (5%) solution for 60 days. illustrates RS % for every GP sample. Control mix (B) shows a subsequent reduced in CS via exposure to H2SO4 solution and it recorded RS at 15,30, 45 and 60 days; 72, 48,40 and 30% respectively. This reflects the destructive effect occur via acid exposure which is related to the deposition of expansive products due to the reaction between geopolymer hydrates and Sulfate ions present in the immersion solution [Citation47,Citation48]. In the pervious investigation conducted by Allahverdi and Skvˇara, they examined the resistance of a geopolymer composed of a combination of fly ash and slag to sulfuric acid [Citation49]; the deterioration occurred via acid exposure is arising from the exchange of Ca+2 within the geopolymer network with H+ or H3O+ ions existing in the immersion solution, this process leads to a reaction between Ca+2 and sulfate, resulting in the formation of gypsum. which subsequent transformed into Ettringite at later times of exposure. The extent of this reaction depends on the rate of H+ and SO4−2 penetration through geopolymer matrix, period of exposure and the concentration of exposed acid. The accumulation of both gypsum and Ettringite induces an internal stress and prohibit the microcracks formation combined by strength loss. Meanwhile, all the blended mixes showed improvement in RS% via acid exposure during the first 30 days or may extended to 45 days as in AH10 cured at room temperature. This is followed by gradual loss in strength up to 60 days of processing and all the blended mixes offered RS% higher than the control sample at all times of acid exposure. This delay in the destructive effect of acid attack in blended GP mixes can be responded to the filling actions of fine AH dry peels and which blocks the pores hinders the further penetration of either SO4−2 or H+ ions through the pores which slow their degradation action with GP network matrix.
GP phase composition
TG/DTG
demonstrates TG/DTG curves of B and AH10 samples that normally cured for twenty-eight days at room temperature. Evidently, the two GP samples show a gradual weight reduced by heating up to 1000°C. According to TG data, weight loss can be classified into three stages at three different temperature ranges considered were 25–300°C, 300–600°C, and 600–1000°C. The percentage weight loss for all combinations at different stages is presented in . The initial stage of weight loss, occurring between 25 and 300°C, shows the highest weight loss, attributed to the elimination of unbound water and the partial breakdown of CSH and CASH gels [Citation19]. The middle stage takes place between 300–600 °C, which is done by releasing silicates or aluminate hydroxyl groups from all the hydrated patterns. The final stage, that leads to the least wt. loss %, is due to decarbonation of some CaCO3, which takes places due to carbonation of the samples.
Table 3. Weight loss % for B & AH10 mixes at various temperature stages.
DTG curves for B and AH10 mixes show two main wide endothermic peaks. The 1st endotherm is located between 195–205°C which is correlated to the removal of uncombined H2O and the partial decomposition of the CSH gel in GP mixes. The 2nd endotherm is located at 410° C for B mix which is responded for complete decomposition of all hydration gels as (CASH and NSH). This 2nd endotherm is much widening in AH10 mix due to the sintering of hydrocarbons and oil evolution which are the main components of AH dry peels powders [Citation12,Citation50].
XRD
Phase compositions of different GP hydrates were explored via XRD test. displays XRD diffractograms obtained for B, AH10 and AH10-F that hydrothermally cured at 60°C/0.02 MPa for 3, 28 days. XRD diffractogram of B mix after three days shows peaks at 2θ = 27.799°, 29.27° which assigned to CSH gel (PDF# 00-033-0306, 00-034-0002) as well as at 2θ = 30.8° and 32.21ͦ characterized to CASH (PDF# 00-020-0452) as the main controlling hydrated phases [Citation19,Citation51]. The existence of these phases in the GP matrix of B mix due to plenty of Ca+2 ions sourced from slag [Citation52]. Furthermore, peaks are noticed at 2θ = 26.4° which assigned to quartz and at 31.33° and 32.56°, these peaks can be attributed to nonactivated gehlenite (PDF# 01-079-2423) and akermanite (PDF# 01-079-2424), respectively. Similar peaks are observed for AH10 after three days of curing indicating the same hydrates are formed in the blended mixes and presence of AH dry peels does not change the phases formed in the geopolymerization reactions. However, after Twenty-eight days of hydrothermal curing, the sharpness of the hydrated fields is increased which confirms the tracking of the geopolymerization process besides peaks due to CaCO3 are strongly appeared especially in B pattern [Citation21].
shows XRD diffractogram for B and AH10 after heating at 300°C for 3 hrs. Obviously, the XRD patterns of the two tested samples show nearly disappearance of the peaks associated with the gehlenite and akermanite phases, this suggests the activation of the remaining unreacted phases through the hydrothermal process [Citation38,Citation40,Citation53]. On other hand, there is boosting in the sharpness of the peaks characterized to CSH and CASH phases due to increasing in their crystallization via the thermal treatment at 300°C. Besides, peaks due to N-C-A-S-H are appeared in XRD diffraction chart of B and AH-10. Crystlline hydrates have less mechanical properties than the gel or semi-crystal hydrates and this explain the low values of compressive strength recorded for all mixes by thermal treatment at 300°C. Firing B and AH10 samples at 800°C lead to the vanishing of the broad bands, underscoring its transformation into new dehydrated phases with elevated crystallinity, such as wollastonite (CaSiO3, PDF# 00-043-1460), gehlenite (Ca2Al2SiO7), and akermanite (Ca2MgSi2O7), as depicted in . These dehydrated phases exhibit diminished mechanical characteristics [Citation50]. Such findings align with the compression data.
Microstructure
On day 28 of hydrothermal curing at 60°C/0.02MPa, B, AH10 and AH10-F mixtures were underwent scanning electron microscopy (SEM) analysis to indentify their microstructures. Notably, image B illustrates a dense structure comprised of significant quantities of hydration products, primarily semi-crystalline calcium silicate hydrate (C-S-H) and calcium-aluminate-silicate hydrate (C-S-A-H), that interconnected the unreacted slag particles, . On other hand, AH10 image patented a looser structure in which AH fibers are covered with cubic plates of C-S-A-H, . GP chains are clearly appeared in AH10-F image which confirmed the role of NF for catalyzing and promoting the geopolymerization process and building up the GP networks, . SEM results validated the previous findings from mechanical, XRD and TGA tests.
SEM microscopic images of B mix fired at 800°C show a porous microstructure resulting from the degradation and regeneration of the akermanite phase, characterized by weak hydraulic properties [Citation20,Citation54], is considered the primary factor behind the significant decrease in strength values observed for the slag fired at 800°C, . For AH10 sample heated at 800° C, SEM image shows a notable deep cracks which confirmed the poor fire resisitivity of blended mix comapred with their analogue B sample, . However the fire resistance is much improved by admiximing the blended GP by NF as shown in AH10-F microgrphs, Fg 10-c. Similar behavior was observed for GP mixes attacked by H2SO4 for 60 days as shown in SEM images in . Minor cracks appeared in AH10 mix impeded with AH fibers, while in AH10-F image Ettringite rods are appeared interloked with semicrystals of C-S-H & C-A-S-H [Citation55].
Conclusions
In our study, we tried to use AH dry fine peels in the formation of GP composites of acceptable mechanical characteristics and good durability in two deterioration circumferences. According to our finding the following conclusions can be summarized as:
BFS/AH-based GP offered diminished setting times which responded for the filling action of AH fine dry peels and its high-water absorptivity as well.
GP mixes hydrothermally cured at 60°C/0.02MPa adopted higher mechanical properties than those cured normally at room temperature. This interrupted to thermal activation of BFS which accelerates the geopolymerization stages.
Incorporation of AH dry peels by 2.5, 5 and 10% in GP manufacturing boosted the compressive strength during the first 3 days for GP mixes normally cured at room temperature. 15% replacement reduces the strength by 45%.
In comparison to the reference mix, the blended cubes showed a lower resistance to the effect of firing and astonishing resistance to acid effect. This delay in the destructive effect of acid attack in blended GP cubes may be responded for the filling actions of fine AH dry peels which blocks the pores and hinders the further penetration of either SO4−2 or H+ ions.
However, Admixing GP by 1 % NF improves its mechanical properties and its durability in the two deterioration actions studied.
Authors’ contribution
D.M.: Take part the experiments and data representation, revision and editing, F.A.S: Investigation, take part in experiments, M.H: Supervision, study investigation, revision and editing .F.S.H: Supervision, data analysis and interpretation, study investigation, original draft writing, revision and editing,
Declarations
Data and materials for this work can be shared upon request.
Disclosure statement
No potential conflict of interest was reported by the author(s).
Additional information
Funding
References
- Gartner E, Hirao H. A review of alternative approaches to the reduction of CO2 emissions associated with the manufacture of the binder phase in concrete. Cem Concr Res. 2015;78:126–142. doi:10.1016/j.cemconres.2015.04.012
- Kelly FJ, Fussell JC. Air pollution and public health: emerging hazards and improved understanding of risk. Environ Geochem Health. 2015;37(4):631–649. doi:10.1007/s10653-015-9720-1
- Josa A, Aguado A, Cardim A, et al. Comparative analysis of the life cycle impact assessment of available cement inventories in the EU. Cem Concr Res. 2007;37(5):781–788. doi:10.1016/j.cemconres.2007.02.004
- Tosti L, van Zomeren A, Pels JR, et al. Technical and environmental performance of lower carbon footprint cement mortars containing biomass fly ash as a secondary cementitious material. Resour Conserv Recycl. 2018;134:25–33. doi:10.1016/j.resconrec.2018.03.004
- Scrivener KL, John VM, Gartner EM. Eco-efficient cements: potential economically viable solutions for a low-CO2 cement-based materials industry. Cem Concr Res. 2018;114:2–26. doi: 10.1016/j.cemconres.2018.03.015
- Raheem AA, Adenuga OA Wood ash from bread bakery as partial replacement for cement in concrete. 2013 [cited 2020 Dec 7]. Available from: http://penerbit.uthm.edmy/ojs/index.php/IJSCET
- Karim MR, Hashim H, Abdul Razak H, et al. Characterization of palm oil clinker powder for utilization in cement-based applications. Constr Build Mater. 2017;135:21–29. doi:10.1016/J.CONBUILDMAT.2016.12.158
- Siang OJM, Hanifi RM, Nazahiyah AS, et al. Properties of sugarcane fiber on the strength of the normal and lightweight concrete. MATEC Web Conf. 2017;103:01021. doi: 10.1051/matecconf/201710301021
- Ferronato N, Torretta V. Waste mismanagement in developing countries: a review of global issues. Int J Environ Res Public Health. 2019;16(6):1060. doi:10.3390/ijerph16061060
- Abdel-Gawwad HA, Heikal EE, El-Didamony H, et al. Recycling of concrete waste to produce ready-mix alkali activated cement. Ceram Int. 2018;44(6):7300–7304. doi: 10.1016/j.ceramint.2018.01.042
- Udoeyo FF, Dashibil PU. Sawdust ash as concrete material. J Mater Civ Eng. 2002;14(2):173–176. doi: 10.1061/(ASCE)0899-1561(2002)14:2(173)
- Lozano FJ, Lozano R. Assessing the potential sustainability benefits of agricultural residues: biomass conversion to syngas for energy generation or to chemicals production. J Clean Prod. 2018;172:4162–4169. doi:10.1016/j.jclepro.2017.01.037
- Moraes J, Font A, Soriano L, et al. New use of sugar cane straw ash in alkaliactivated materials: a silica source for the preparation of the alkaline activator. Constr Build Mater. 2018;171:611–621. doi:10.1016/j.conbuildmat.2018.03.230
- Rattanachu P, Toolkasikorn P, Tangchirapat W, et al. Performance of recycled aggregate concrete with rice husk ash as cement binder. Cem Concr Compos. 2020;108:103533. doi: 10.1016/j.cemconcomp.2020.103533
- Khan R, Jabbar A, Ahmad I, et al. Reduction in environmental problems using rice-husk ash in concrete. Constr Build Mater. 2012;30:360–365. doi:10.1016/j.conbuildmat.2011.11.028
- Liew KM, Sojobi AO, Zhang L. Green concrete: prospects and challenges. Constr Build Mater. 2017;156:1063–1095. CrossRef. doi: 10.1016/j.conbuildmat.2017.09.008
- Osei DY. Experimental assessment on coconut shells as aggregate in concrete. Int J Eng Sci Invention. 2013;2:7–11.
- Sonawane YN, Chitte CJ. Waste coconut shell as a partial replacement of coarse aggregate in concrete mix-an experimental study. Int J Sci Res. 2016;5:649–651.
- Fadel O, Hehal EE, Hashem FS, et al. Mechanical properties, resistance to fire and durability for sulfate ions of alkali activated cement made from blast furnace slag- fine metakaolin. Egy J Chem. 2020;63:4821–4831.
- Zawrah M, Gado R, Khattab R. Optimization of slag content and properties improvement of metakaolin-slag geopolymer mixes. Open Mater Sci J. 2018;12(1):40–57. doi: 10.2174/1874088X01812010040
- Abo-El-Enein SA, Hashem FS, Amin MS, et al. Physico-chemical characteristics of cementitious building materials derived from industrial solid wastes. Constr Build Mater. 2016;126 983–990. doi: 10.1016/j.conbuildmat.2016.09.112
- Shekhovtsova J, Zhernovsky I, Kovtun M, et al. Estimation of fly ash reactivity for use in alkali-activated cements - a step towards sustainable building material and waste utilization. J Cle Prod. 2018;178:22–33. doi:10.1016/j.jclepro.2017.12.270
- Robayo RA, Mulford A, Munera J, et al. Alternative cements based on alkali-activated red clay brick waste. Constr Build Mater. 2016;128 163–169. doi: 10.1016/j.conbuildmat.2016.10.023
- Hashem FS, Hekal EE, Abdel Naby MM, et al. Mechanical properties and durability performance against fire, gamma ray and bio-fouling of hardened Portland cement pastes incorporating lead bearing wastes. Mater Chem Phys. 2021;272:272 124–997. doi: 10.1016/j.matchemphys.2021.124997
- Hassan A, Arif M, Shariq M. Use of geopolymer concrete for a cleaner and sustainable environment – a review of mechanical properties and microstructure. J Clean Prod. 2019;223:704–728. doi:10.1016/j.jclepro.2019.03.051
- Selim FA, Hashem FS, Amin MS. Mechanical, micro-structural and acid resistance aspects of improved hardened Portland cement pastes incorporating marble dust and fine kaolinite sand. Constr Build Mater. 2020;251:118–992. doi:10.1016/j.conbuildmat.2020.118992
- Abdel-Gawwad HA, Heikal M, Mohammed MS, et al. Sustainable disposal of cement kiln dust in the production of cementitious materials. J Cle Prod. 2019;232:1218–1229. doi:10.1016/j.jclepro.2019.06.016
- Bakharev T, Sanjayan JG, Cheng YB. Resistance of alkaliactivated slag concrete to acid attack. Cem Concr R. 2003;33(10):1607–1611. doi:10.1016/S0008-8846(03)00125-X
- Deja J, Malolepszy J. Resistance of alkali-activated slag mortars to chloride solution. Spec Public. 1989;114:1547–1564.
- Nazari A, Riahi S. Computer-aided design of the effects of Fe2O3 nanoparticles on split tensile strength and water permeability of high strength concrete. Mater Des. 2011;32(7):3966–3979. doi:10.1016/j.matdes.2011.01.064
- Madandoust R, Mohseni E, Mousavi SY, et al. An experimental investigation on the durability of self-compacting mortar containing nano-SiO2, nano-Fe2O3 and nano-CuO. Constr Build Mater. 2015;86:44–50. doi:10.1016/j.conbuildmat.2015.03.100
- Amin MS, El-Gamal SMA, Hashem FS. Fire resistance and mechanical properties of carbon nanotubes – clay, bricks wastes (homra) composites cement. Constr Build Mater. 2015;98:237–249. doi:10.1016/j.conbuildmat.2015.08.074
- El-Gamal SMA, Hashem FS, Amin MS. Influence of carbon nano tubes, nanosilica and nano-metakaolin on some morphological-mechanical properties of oil well cement pastes subjected to elevated water curing temperature and regular room air curing temperature. Constr Build Mater. 2017;146:531–546. doi:10.1016/j.conbuildmat.2017.04.124
- Amin MS, El-Gamal SMA, Hashem FS. Effect of addition of nano-magnetite on the hydration characteristics of hardened Portland cement and high slag cement pastes. J Ther Anal Cal. 2012. doi: 10.1007/s10973-012-2663-1
- Hashem FS. Adsorption of methylene blue from aqueous solutions using Fe3O4/bentonite nanocomposite. Hydrol Curr Res. 2013;3(5):143.
- C. ASTM, 191. Standard test method for time of setting of hydraulic cement by vicat needle. USA: ASTM International; 2004.
- ASTM. C109-standard test method for compressive strength of hydraulic cement mortars. West Conshohocken, PA: ASTM International; 2008.
- Hashem FS, Razek TA, Mashout HA. Rubber and plastic wastes as alternative refused fuel in cement industry. Constr Build Mater. 2019;212:275–282. doi:10.1016/j.conbuildmat.2019.03.316
- Mashout HA, Razek TA, Amin MS, et al. Performance of nano titania-reinforced slag/basalt geopolymer composites. J Eng Appl Sci. 2023;70(1):106. doi: https://doi.org/10.1186/s44147-023-00278-6
- Hashem FS, Amin MS, El-Gamal SMA. Improvement the acid resistance of Portland cement pastes using rice husk ash and cement kiln dust as additives. J Ther Anal Cal. 2012;111(2):1391–1398. doi: 10.1007/210973-012-2458-4
- Anjaneyulu CM, Malikarjuna M, Prasad JV. Impact of nano titanium dioxide on geopolymer concrete. Inter J Res Pub Rev. 2021;2(12):484–493.
- Ramadan M, Habib A, Hazem MM, et al. Synergetic effects of hydrothermal treatment on the behavior of toxic sludge-modified geopolymer: immobilization of cerium and lead, textural characteristics, and mechanical efficiency. Contr Build mater. 2023;367(27):130249. doi: 10.1016/j.conbuildmat.2022.130249
- Hazem M, Hashem FS, Amin MS, et al. Mechanical and microstructure characteristics development of hardened oil well cement pastes incorporating fly ash and silica fume at elevated temperature. J Taibah Univer Sci. 2020;14(1):155–167. doi: 10.1080/16583655.2020.1711998
- Hajimohammadi A, Provis JL, van Deventer JSJ. Time-resolved and spatially resolved infrared spectroscopic observation of seeded nucleation controlling geopolymer gel formation. J Colloid Inter Sci. 2011;357(2):384–392. doi: 10.1016/j.jcis.2011.02.045
- Alsubari B, Shafigh P, Ibrahim Z, et al. Properties of eco-friendly self-compacting concrete containing modified treated palm oil fuel ash. Constr Build Mater. 2018;158:742–754. doi:10.1016/j.conbuildmat.2017.09.174
- Heikal M, Zaki ME, Ibrahim SM. Characterization, hydration, durability of nano-Fe2O3-composite cements subjected to sulphates and chlorides media. Constr Build Mater. 2021;1(269):121310. doi:10.1016/j.conbuildmat.2020.121310
- Abo-El-Enein S, El-Hosiny F, El-Gamal S, et al. Gamma radiation shielding, fire resistance and physicochemical characteristics of Portland cement pastes modified with synthesized Fe2O3 and ZnO nanoparticles. Constr Build Mater. 2018;173:687–706. doi:10.1016/j.conbuildmat.2018.04.071
- Gominˇsek T, Lubej A, Pohar C. Continuous precipitation of calcium sulfate dihydrate from waste sulfuric acid and lime. J Chem Technol Biotechnol. 2005;80(8):939–947. doi: 10.1002/jctb.1266
- Allahverdi A, Skvara F. ´ sulfuric acid attack on hardened paste of geopolymer cements part 1. Mechanism of corrosion at relatively high concentrations. Cer Sil. 2005;49:225–229.
- Türker HT, Balçikanli M, Durmuş İH, et al. Microstructural alteration of alkali activated slag mortars depend on exposed high temperature level. Constr Build Mater. 2016;104:169–180. doi:10.1016/j.conbuildmat.2015.12.070
- Mahmoud A, Kishar EA, Ahmed DA. Resistance of alkali activated slag to sulphate attack and elevated temperatures. J Scient Rese Sci. 2018;35(1):315–329. doi:10.21608/jsrs.2018.25530
- Nasr D, Pakshir AH, Ghayour H. The influence of curing conditions and alkaline activator concentration on elevated temperature behavior of alkali activated slag (AAS) mortars. Constr Build Mater. 2018;190:108–119. doi:10.1016/j.conbuildmat.2018.09.099
- Bernal SA, Provis JL, Rose V, et al. Evolution of binder structure in sodium silicate-activated slag-metakaolin blends. Cem Concr Compos. 2011;33(1):46–54. doi:10.1016/j.cemconcomp.2010.09.004
- Abdel-Gawwad HA, Mohammed MS, Heikal M. Ultralightweight porous materials fabrication and hazardous lead-stabilization through alkali-activation/sintering of different industrial solid wastes. J Clean Prod. 2020;244:118742. doi:10.1016/j.jclepro.2019.118742
- Abubakar AU, Baharudin KS. Properties of concrete using tanjung bin power plant coal bottom ash and fly ash. Int J Sustain Constr Eng Technol. 2012;3:56–69.