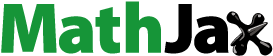
ABSTRACT
The emergence of 4D printing from additive manufacturing has opened new frontiers in crashworthiness application. Energy-absorbing structures with fixed geometrical shapes and irreversible deformation stages can be programmed such that after mild or extreme deformation, their initial shapes, properties and functionalities can be recovered with time when actuated by external stimuli. This survey delves into the recently-accelerated progress of shape memory/recovery energy-absorbing metamaterials (EAMM) and energy-absorbing smart/intelligent structures (EASS). First, the introduction gives some fundamental concepts of metamaterials and their application to energy-absorbing structures. Next, some common 3D printing technologies that have led to 4D printed EAMM and EASS are succinctly described. Shape memory materials, their functional properties and recovery process, are then discussed. Finally, various recoverable/reversible energy absorbers with their future challenges and perspectives, are presented. With well-tailored 4D printed EAMM and EASS, reusability with minimal maintenance and higher energy absorption capacity can be retained.
1. Introduction
In recent years, the production of complex 3D printed structures for energy-absorbing purposes has garnered much interest especially in the automotive, marine, building and aerospace industries (Li, Zhi, and Fan Citation2022; Zhang et al. Citation2021; Alomarah et al. Citation2020; Habib et al. Citation2017; Isaac and Duddeck Citation2022). Lightweight potentials, customised structural parts, ease in producing complex structures and relatively low cost of production, are some of the attractive benefits of 3D printed energy-absorbing structural parts. However, due to the printing techniques of parts produced by additive manufacturing, the mechanical strength and crushing performance are generally lower than their traditional subtractive manufacturing counterpart. Moreover, most parts fabricated either by the conventional techniques or by 3D printing technology, have rigid boundaries making them undergo permanent deformation when subjected to various loading conditions. After these deformation stages (i.e. elastic and plateau deformation stages), the energy absorber enters the densification stage where the energy absorption of the crushed structure is stopped. At the onset of densification, the energy dissipated is converted into internal strain energy of the bulk material. Consequently hereafter, the 3D-printed structurally deformed part must be replaced to ensure continuous protective functionality. However, replacement of parts can be time-consuming, expensive, and therefore, requires a viable solution. The introduction of 4D printing to fabricate energy-absorbing structure provides a viable route of re-using the deformed parts by recovering them to their original shapes. This promising possibility of 4D printing technology has made it a subject of many research interests (van Manen et al. Citation2021; Teoh et al. Citation2018; Wu et al. Citation2018; Zhang, Demir, and Gu Citation2019; Falahati et al. Citation2020). The term 4D printing simply involves the inclusion of a stimulus-responsive mechanism to actuate a 3D-printed metamaterial or smart structure. This is usually achieved by introducing the 3D-printed metamaterial to suitable active substance that can transform the characteristic and response behaviour of metamaterials and structures. The recent exploits of 4D printing technology to realising shape change and shape recovery metamaterials and structures have never been more promising than in the past years.
During the crushing of 4D printed energy-absorbing structures fabricated via the 3D printing technology, the permanent deformation stage or the densification point can be avoided, and the deformed structure reversed to its original shape with the appropriate stimulus-responsive mechanism. Specific materials with self-responsive functional properties can be utilised in the fabrication of energy absorbers. Such materials are usually referred to as intelligent materials, smart materials or metamaterials. Though, intelligent and smart materials are used interchangeably, it is worth noting that while smart material responds to stimuli and it is an essential constituent (i.e. programmable matter) of 4D printing technology, it does not self-optimise or autonomously repair itself when damaged. On the other hand, intelligent material does not only respond to stimuli, but it can also self-optimise or self-repair, for example, its mechanical damage, and restore its material functionalities. Whatever the case, these materials have the potential to change their properties with time (i.e. as the 4th dimension) when acted upon by external stimuli. They can enable the shape recovery of crushed energy-absorbing metamaterial structures with significant improvement in their mechanical properties and crushing performances. Different shape memory materials (SMMs) have been studied in recent times. They include shape memory polymer (SMP), shape memory composite (SMC i.e. sometimes called shape memory polymer composite), shape memory alloy (SMA), shape memory hybrid (SMH) and shape memory gels (hydrogels). A survey of SMMs for energy-absorbing application is given in Section 3. The process of shape transformation/change and shape recovery of energy absorber is achieved by stimuli-responsive actions (i.e. exposure to light, heat, water, pH, magnetic field, etc.) However, the correct shape memory material pathway is first determined by shape memory programming procedures such as shape deformation, shape fixation, removal of external stresses, etc.
The response mechanisms in SMMs can either take an irreversible one-way path or a reversible two-way path, which result in either one-way or two-way shape memory effects (SMEs), respectively. In one-way SME, each recovery stage must be reprogrammed i.e. setting the temporary shape manually (Lee, An, and Chua Citation2017). In this case, the SMM remains in its temporary deformed state after the external load is removed (i.e. during unloading) and returns to its original shape with the aid of an external stimulus-responsive action as shown in (a). On the other hand, two-way SME is characterised by reversibility. That is, the two fixed or permanent shapes can be reversed with or without the application of external stress as illustrated in (b). This paper deals mostly on recoverable energy-absorbing metamaterials (EAMM) and smart structures that follow a one-way path SME. However, some authors have replaced the ‘recoverable’ term with ‘reversible’ even though their investigations followed a one-way SME (Namvar et al. Citation2022; Bodaghi et al. Citation2020). Reversibility or two-way path SME has been seldom investigated owing to dearth of SMM with such characteristic function. However, Wu et al. (Citation2018) attempted to investigate reversibility of structures made via 4D printing technology. Moreover, depending on the shape memory metamaterials, some identified parameters such as shape fixity and shape recovery ratios, can be used to evaluate their shape memory performances (Zhao et al. Citation2018; Roudbarian et al. Citation2022).
Shape recovery of metamaterials is achieved by different response mechanisms depending on the types of SMMs and the applications. For example, the mechanism of SMP can either be a one-way or two-way memory effect as already stated; however, multiple SME can occur as expatiated by Xia et al. (Citation2021). This SMP mechanism is either based on phase transition, reversible or molecular switches. Tao et al. (Citation2020b) demonstrated that SMP can be temperature-controlled during deformation and recovery stages. In their investigation, a 4D printed lattice structure made from Verowhite metamaterial was subjected to high temperature compression between 50°C to 70°C. Between these temperatures, it was observed that the SMP structure was capable of changing its stiffness owing to its large elastic modulus. Moreover, above the upper limit glass transition temperature (), the metamaterial was totally recovered to its original state after the unloading process. With decreasing temperature, recoverability decreased and finally, at 50°C, the crushed metamaterial remained in its deformed state. However, for the case of SMA, a martensitic or/and austenitic transformation behaviour is required for achieving shape recovery (Lee, An, and Chua Citation2017; Lu et al. Citation2019). A detailed explanation of the transformation phases between austenite (i.e. higher temperature phase) and martensite (i.e. lower temperature phase) is given by Lu et al. (Citation2019). Typically, the transition temperature (
) of SMA from austenitic to martensitic phase ranges from −100°C to 150°C (Zafar and Zhao Citation2020; Otsuka and Ren Citation1999)
Recovery of EAMM and EASS can be observed in a hysteresis stress–strain curve. This curve typically has three stages – the loading, unloading and recovery stages. For example, a typical stress–strain curve is schematically represented in . During compression loading at OA, the material undergoes inelastic deformation. Further loading results in deformation at the plateau region. Additional heating of the material at or above causes it to soften and thereby, retaining a temporary shape. When the load is removed from the metamaterial at AB (i.e. unloading) a spring effect occurs which depends on the nature of the metamaterial, structural type, number of cycles and the ambient temperature (Keshavarzan, Kadkhodaei, and Forooghi Citation2020). At this stage, partial shape recovery could occur. Moreover, the spring effect permits the metamaterial to be used in applications where repeated energy absorption is highly desired (Johnston and Kazancı Citation2021). With appropriate stimulus-induced mechanism (i.e. cooling or heating, depending on the application), the deformed metamaterial can be fully or partly recovered at BO (i.e. strain recovery) with dissipated internal energy captured in the space OAB. Moreover, the absorbed energy is evaluated by the area section OBA
. The magnitude of the energy absorbed largely depends on the metamaterial and the nature of structural deformation; for instance, the existence of plastic hardening behaviour of SMP (Bodaghi et al. Citation2020). Under ideal conditions, it is worth noting that the temporal deformation of SMM can be perfectly fixed and recovered to its original shape after the application of a stimulus-responsive mechanism. However, this is not so because both the crystalline phase and the distribution of molecular structure of the SMM are not in their idealised state (Dong et al. Citation2021a).
Figure 2. Illustration of a typical hysteresis stress-strain curve showing loading, unloading and recovery stages of metamaterial with dissipated internal energy, absorbed energy and SME.
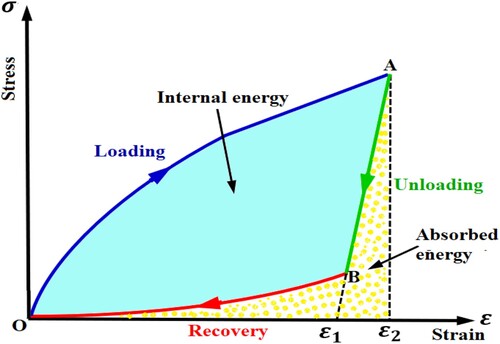
Several physical stimulus-responsive media including ultra-violet light, heat, temperature, moisture, etc., are currently being investigated to ascertain their suitability for structural deformation, shape change and shape recovery (Patil and Sarje Citation2021; Sun et al. Citation2019). During the loading of 4D printed EASS, initial deformation typically occurs and sometimes the metamaterials undergo large deformation (Roudbarian et al. Citation2022). Moreover, the introduction of external stimulus during the deformation process initiates shape change by further deforming the structure. After these deformations and preliminary shape change processes during unloading, the shape recovery stage is usually actuated by external stimulus. For instance, it was observed by Serjouei et al. (Citation2022) that by applying heat to some deformed 4D-printed sandwiched structures, their initial hexagonal and square horseshoe configurations, were fully recovered. Also, in the investigation carried out by Liu, Liu, and Ma (Citation2022), five multicellular structures fabricated using the laser powder bed fusion technology with triangular, quadrilateral, pentagonal, hexagonal and octagonal shapes (i.e. designated as TMS, QMS, PMS, HMS and OMS, respectively) were designed. Their energy absorption capacity and recoverability potentials were investigated by subjecting them to loading causing 15% deformation. It was observed that the shape memory effects of each of the six multicellular structures return a recovery rate of 0.98, 0.97, 0.98, 0.99 and 0.96, respectively after they were heated in water with a temperature of 100°C. Moreover, the recovery was generally due to the martensitic transformational behaviour of NiTi alloys, and the recorded high recovery rate was ascribed to the small local strain generated by the multicellular structure.
Apart from geometrical features which influence the crushing performance of cellular 3D printed energy absorbers (Isaac and Duddeck Citation2022; Nasrullah, Santosa, and Dirgantara Citation2020), other crushing mode features such as bending, stretching, buckling and twisting dominated modes can also influence their crashworthiness performance significantly (Lin et al. Citation2021). It has been reported that cellular structures with stretching-dominated mode outperform those with bending-dominated ones (Jin et al. Citation2019). Al-Ketan et al. (Citation2018) additively manufactured both sheet-based and strut-based microlattices using triply periodic minimum surface (TPMS) and compared their performance with octet-truss microlattice. They reported that the TPMS with sheet-based topologies exhibited stretching-dominated mode making them superior in mechanical performance over the strut-based and octet-truss microlattices. Informed by these results, energy-absorbing structure achieved via 4D printing technology can be well-programmed and tuned with selected stimuli-responsive actions to produce the desired shapes as well as stimuli bending, stretching, twisting or bending dominated modes during their deformation processes and recovery stages. This was demonstrated in the investigation carried out by Xin et al. (Citation2020). It was shown that chiral auxetic metamaterial fabricated via 4D printing resulted in a deformation process from bending-dominated mode to stretching-dominated mode, typifying a very promising energy-absorbing structure for crashworthiness application. Moreover, the authors observed that after re-heating, the shape and mechanical properties of the auxetic metamaterial were recovered to the initial state it was before loading.
The recovery of EAMM and structures using 4D printing technique is becoming a rapidly developing aspect of impact engineering and crashworthiness applications. Intelligent structures fabricated by 4D printing technology have shown to be self-adaptable, adjustable, controllable/monitorable, deployable, reconfigurable, repairable and tuneable (Ahmed et al. Citation2021; Dong et al. Citation2021b; Alshahrani Citation2021; Dong et al. Citation2021a; Quanjin et al. Citation2020). They can as well be made to exhibit self-bending, self-expanding/shrinking and self-healing (Zolfagharian et al. Citation2018; Wan et al. Citation2020; Xia et al. Citation2021; Bodaghi, Damanpack, and Liao Citation2016). These self-active tendencies of metamaterials are making them more popular and promising in various medical and engineering applications. The aim of this survey is to present the most recent progress of 4D printed metamaterial and structure especially as a promising device for energy absorption in impact and crushing applications. depicts a synopsis of the main contents of this review work. For a better understanding of the subject matter, this explorative survey is divided into several sections. Section one introduces the general responsive mechanisms and shape recovery potentials of metamaterials and smart structures. Section two enumerates the printing technologies employed for realising stimuli-responsive EAMM and structures. In Section three, a survey of shape memory energy-absorbing materials and structures in recent times are presented. Section four explores some of the functional properties and recoverable/reversible structures of typical 4D-printed energy absorbers. Finally, some challenges, prospects, future trends and perspectives of 4D printed EAMM and structures are given in Section five.
2. Printing technologies
The process of 4D printing techniques currently applied to realise functional metamaterials and smart structures simply involves the fabrication of SMMs with well-programmed 3D printing technology. In this Section, various 3D printing techniques that have been used to produce structural prototypes and can enable 4D printing of EAMM and EASS are discussed. gives a list of 3D printing techniques, their printing parameters as well as their advantages and limitations.
Table 1. Summary of commonly utilised 3D printing techniques, printing principles, materials, parameters, advantages and limitations.
2.1. Fused deposition modelling
The fused deposition modelling (FDM) sometimes interchangeably referred to as fused filament fabrication (FFF), is a popular 3D printing technique mostly used for the fabrication of structures which are made from polymer or composite materials. The composite-based material filament is usually derived by mixing polymeric material filament (for example, polylactic acid, PLA) with reinforcement fibre (for example short/continuous carbon or glass fibre). A schematic representation of FDM/FFF technique is shown in (a). The 3D printing process involves the extruding of feed material via a heated nozzle unto a heated surface in a layer-by-layer manner until the desired structural part is completely formed. Moreover, FDM or FFF 4D printed structural parts are commonly obtained by utilising SMP or SMC material feedstocks. Before the printing process of SMP, its initial temperature is usually below the glass transition temperature (i.e. the temperature where a material moves from a glass-like and rigid state to a rubber-like and flexible state) which makes it very stable at this temperature. During the FDM or FFF printing process, the temperature of the polymer-based metamaterial increases above the glass temperature. At this point, the correct programming which incorporates loading above the glass transition temperature is performed and monitored until it reaches the point where the temperature falls below the glass transition temperature. This allows the SMP printable part to display a temporary shape with a pre-strain. The distribution of the pre-strain in the polymer-based metamaterial is affected by the structural and printing process parameters. This pre-strain disappears when the SMP is heated at a temperature higher than that of the glass transition temperature and consequently, the 4D printed part recovers its initial shape (Wang and Li Citation2020). Moreover, to achieve optimum printing results, different FDM process parameters can be tested and evaluated during the printing process (Hosseinzadeh, Ghoreishi, and Narooei Citation2023). The process parameters peculiar to FDM or FFF include feed rate, layer thickness, nozzle speed, nozzle temperature, bed temperature, printing temperature, extrusion width, cooling time, etc.
Figure 4. Representation of commonly utilised 3D printing techniques suitable for 4D printing of energy absorbing metamaterials and smart structures (a) fused deposition modelling (Isaac and Duddeck Citation2022) (b) direct ink writing (c) Stereolithography apparatus (Davoudinejad Citation2021) (d) Digital light projection (Li et al. Citation2020) (e) Selective laser melting and selective laser sintering (Isaac and Duddeck Citation2022) (f) Inkjet (Magazine et al. Citation2022).
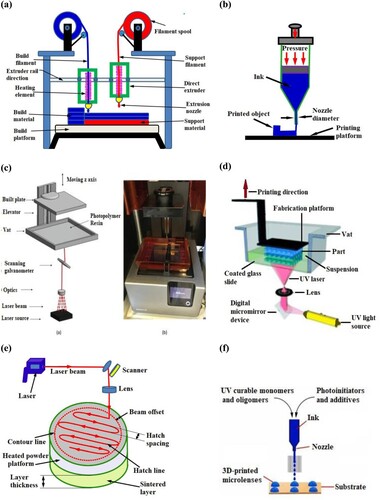
Liu et al. (Citation2018) demonstrated the possibility of realising a 4D printed energy absorber using FDM printing technology. The authors fabricated a 4D printed thin-walled origami tube made from a PLA-based SMP filament using a 3D printer with a nozzle temperature and a printing speed of 200°C and 50 mm/s, respectively. Similarly, Namvar et al. (Citation2022) used the FDM technology to fabricate 4D printed PLA-based auxetic energy-absorbing structures. They investigated the reversibility, energy absorption capacity and mechanical behaviour of the structures under quasi-static compression. Other researchers who have used the FDM technology to realise 4D printed energy-absorbing structures have been given in the literature (Bodaghi et al. Citation2020; Liu et al. Citation2020). However, apart from using FDM or FFF 3D printing technology to fabricate polymer-based metamaterial and structures, the technique has also been used to realise composite-based smart structural devices. Kang et al. (Citation2018) fabricated a 4D-printed SMC actuator by using FDM technology. The SMC was obtained by first fabricating a nylon-based SMP and then two nitinol wires were incorporated into it. The resulting SMC was covered with PLA to foster its flexibility. With three bending points as reference points in the 4D printed SMC, a reversible actuation caused by variations in temperature and phase transformation, was realised. In another recent work carried out by Zeng et al. (Citation2022), a FFF printing technology was utilised to fabricate lattice structures made by combining thermoplastic PLA-based SMP with continuous carbon fibre. The 4D printed samples were subjected to low-velocity isothermal compression and thermo-mechanical cycle loading conditions to determine their temperature-dependent mechanical and shape memory properties, respectively. The results of their findings indicate a promising potential of using 4D printed SMC lattice structure not only to address applications where there are variable stiffnesses in mechanical properties owing to temperature differences but also to realise highly efficient deployable structures especially for the aerospace industry.
2.2. Direct ink writing
Whereas the FDM/FFF technology is flexible in the utilisation of thermoplastics or composite filaments, the direct ink writing (DIW) also known as liquid deposition modelling (LDM), mostly utilises viscoelastic photocurable material and liquid-like polymeric materials including those with thermosetting properties. Both the former and latter techniques are categorised as extrusion-based technology because of the extrusion of the feed material via the nozzle during printing. However, DIW is characterised by micro-nozzles which results in better resolution of the printable part than the FDM technology. In DIW, a pressure is applied to the viscoelastic material which is extruded by a moving nozzle and writes the object layer-by-layer directly on the printing platform as illustrated in (b). The printability of the viscous ink material can be ascertained by measuring its rheological properties such as yield stress, viscosity and elastic modulus (Fu et al. Citation2022). Owing to the free choice of material selection offered, the availability of printing ink materials and the convenience in the fabrication process of multi-material structures, the DIW technology has continuously gained more popularity in recent years (Wan et al. Citation2020; Chen et al. Citation2019; Rocha et al. Citation2020).
2.3. Stereolithography apparatus
The stereolithography apparatus (SLA) technique is one of the vat-photopolymerisation 3D printing technology that utilises resin (i.e. polyester, polycarbonate, polyether, etc.,) to fabricate layered structures via cross-linked polymers. The structures are built in a layer-by-layer manner after exposing the resin to ultraviolet (UV) laser beam (as shown in (c)), hence, causing the resin monomers to induce free radical polymerisation. During SLA process, the first layer undergoes photo-induced polymerisation and the subsequent layers follow the same photo-induced process, thereby, forming the subsequent layer on top of the previous layer until the structural device is completely printed. This technique has the advantage of producing structural prototypes with very high resolution as well as desirable surface finish. However, certain process parameters such as curing depth, photopolymer width, etc., can significantly influence the resolution of the printed structure. The utilisation of SLA technology has enabled the fabrication of very high performance and responsive energy-absorbing structures. For instance, Pasini et al. (Citation2022) recently utilised the SLA technique to design a 4D printed re-entrant honeycomb structure with the goal of investigating its temperature memory effect. The photopolymer resin used for fabricating the honeycomb structure was obtained by mixing methacrylic acid esters with liquid photo-initiator which upon exposure to UV light, changed into a solid state.
2.4. Digital light projection
A similar SLA, vat-photopolymerisation technique, which utilises UV light for photocuring is the digital light projection (DLP) also known as digital light processing. Unlike SLA technology, in which the UV light moves from one point to another for curing the resin, the DLP on the other hand, has stationary UV light which cures each resin layer at a time as shown in (d). The curing process results in less accurate and poor-quality prints when compared to those fabricated via the SLA technique. However, the curing process in DLP technique enhances its printing speed, thereby, enabling the printing of larger structures with fewer details and lesser manufacturing time, than its SLA technique counterpart. Keshavarzan, Kadkhodaei, and Forooghi (Citation2020) used the DLP technique to design and manufacture cellular lattice structures made from resin with shape memory property. A 405 nm wavelength UV light with 30 µm resolution in x and y directions, was utilised to cure the resin and induce polymerisation. The layers formed were built along z-axis until the lattice structural part was created. Energy absorption capacity and recoverability of different DLP-manufactured rhombic and body-centred lattice structures were compared under several programming schemes. In another investigation carried out by Yang et al. (Citation2019), lightweight metamaterial was fabricated using a combination of projection micro-SLA and DLP techniques. The high precision micro-SLA had the capacity to rapidly produce micro-structures via a maskless projection with the aid of digital dynamic mask. The lightweight micro-lattices fabricated were tested for impact mitigation, reconfigurable and deployable capabilities. Moreover, in recent times, DLP and DIW have been combined in a single 3D printing technology to realise functional materials with high printing speed and high resolution (Peng et al. Citation2021).
2.5. Selective laser melting and selective laser sintering
Selective laser melting (SLM) and selective laser sintering (SLS) are classified under the powder bed fusion technology. These techniques utilise high-energy laser beam to selectively fuse very fine powdered raw material as shown in (e). Unlike FDM and SLA, the SLM and SLS do not require structural support during the printing process, consequently, allowing the printed structure to be realised faster than their FDM and SLA counterparts. While the commonly utilised powdered raw material for SLM technique is restricted to metal-based powder, the SLS technique on the other hand, has a wider industrial application which accommodates not only metal-based powder but also polymer-based or composite-based powdered raw materials (Yuan et al. Citation2017; Wu et al. Citation2020). The former utilises very fine-grain metallic powder, while the latter utilises thermoplastic polymers with fine-grain sizes. Moreover, SLS polymer-based fabrication does not require the use of gas injection, however, for SLS metal-based fabrication, it is required to inject the printing chamber with protective gas to minimise oxidative effect due to high sintering temperature of the powdered material (Khorsandi et al. Citation2021). It is noteworthy that SLS-based metamaterials and structures with shape memory effects have been seldom explored in many fields of study including energy absorbers for crashworthiness application. A plausible reason for this untapped research area is due to the extreme difficulty in obtaining suitable material for the manufacturing process. However, very recently, Ouyang et al. (Citation2022) developed a polymer-based metamaterial (i.e. polyurethane with reversible dyes) that can be utilised in the SLS 4D printing technology. The metamaterial was combined with carbon nanotube to form an SLS-4D printed composite which was reported to exhibit both self-healing and shape memory effects.
Energy-absorbing devices with SMA characteristic features using the SLM technology is emerging with meticulous research efforts ongoing. The most promising SMA for SLM-manufactured parts is the nickel and titanium alloy, popularly known as nitinol (i.e. NiTi). However, the NiTi printed structure manufactured via the SLM technique suffers from a reduction in Ni content owing to low evaporation temperature (Zafar and Zhao Citation2020). In contrast to the demerit encountered by the Ni content, the Ti content in nitinol, however, increases in its phase transformation temperature. To ensure the full functionality of NiTi-SLM printed structure, it is of good practice to introduce more Ni content during the fabrication of structures made from NiTi alloy. This alloy can as well be combined with other materials to produce metamaterials and smart structures. In a recent investigation, Hassanin et al. (Citation2020) combined the properties of nitinol with auxetic material to form a 4D printed re-entrant auxetic structure. The energy absorbed by the meta-material 4D printed structure subjected to ballistic impact was reported to be higher than those made from solid steel and solid nitinol alloy. Another novel study which focused on the use of laser powder bed fusion to 4D print different shapes of multicellular structures and evaluate their energy absorption efficiencies, has been reported by Liu, Liu, and Ma (Citation2022).
2.6. Inkjet
The inkjet printing technology has the advantage of low cost and works by depositing tiny droplets on the printing surface or substrate as illustrated in (f). The nozzle diameter of the inkjet printers can be as small as 20–30 μm with ink droplets of about 1.5pL (Manthiram, Zhao, and Li Citation2012). Consequently, they exhibit very high printing resolution with high possibility of realising intricates and complex parts. Some process parameters such as layer thickness, droplet frequency, droplet spacing, number of printed layers, etc., have been shown to influence the quality of the printed structure (Colton et al. Citation2021). This implies that the inkjet technology, if not properly handled, could produce coarse printed parts. Liu et al. (Citation2020) utilised the inkjet technology to fabricate a 4D printed metamaterial which exhibited zero Poisson ratio. The printed metamaterial was prepared using a photo-crosslinkable SMP material, some printing inks including isobornylacrylate, acrylic monomer and oligomer, etc., and lastly, a photo initiator. The 4D-printed metamaterial was subjected to multiple loading cycles. It was reported that the 4D-printed metamaterial possessed the capacity to recover its shape during the deformation process. Another 4D printed cylindrical origami metamaterial, fabricated via the inkjet technology was investigated by Tao et al. Citation2020a. The photocuring cross-linking resulted in a glassy SMP with a high cross-linking density. A rubber-like and soften state of the SMP metamaterial was observed as the temperature increased above its glass transition temperature of 70°C. Moreover, when the temperature changed, the SMP was transformed to glassy and rubber-like state. In a similar investigation performed by the same authors and co-workers (Tao et al. Citation2020b), a 4D printed multi-stable micro-lattice metamaterial was fabricated using a multi-material inkjet technology. The multi-stable materials have the potential of adjusting stiffness, deformation and recovery effects.
3. Shape memory energy-absorbing metamaterials
In this section, various SMMs which have and can be adopted to realising EAMM and structures are discussed. gives some typical SMMs, their base materials and mechanical properties that could be used for the investigation of smart energy absorbers with shape memory/recoverable effects.
Table 2. Mechanical properties of typical SMMs that could be adopted for EAMM and EASS.
3.1. Shape memory polymers
Programmable polymeric materials with the potential of memorising its configuration, fixing its mechanical deformation and recovering its shape when triggered by external stimuli are referred as shape memory polymers (SMP). These SMP materials may be derived either from thermoplastics or thermoset polymers. The thermoplastic polymers include polylactic acid (PLA), polyamide (PA or nylon), thermoplastic polystyrene (PS), polypropylene (PP), polyethylene (PE), polyether ether ketone (PEEK), polyvinylchloride (PVC), acrylonitrile butadiene styrene (ABS), and thermoplastic polyurethane (TPU); while the thermoset polymers include epoxy resin (ER), polyester resin (PESR), polyurethane (PU), vinyl ester (VE) and thermoset polystyrene (PS). Thermoplastic polymers with SME are physically crosslinked and have been extensively applied in various industrial sectors. On the other hand, thermoset polymers with SME are chemically crosslinked and have limited application especially in 4D printing of EAMM and structures. However, thermoset SMP has better mechanical characteristic functions and higher shape recovery than the thermoplastics ones owing to its covalently crosslinked polymer chain network (Xie et al. Citation2016) and its loss in physical crosslink integrity due to mechanical deformation (Xiao et al. Citation2015). Thermosets SMP are obtained by adding linear monomers or thermoplastics into thermosets-shape memory matrix systems. Moreover, SMPs are generally easier to tailor their mechanical properties than their metallic and alloy counterparts. They also have higher recoverable strength and lightweight advantage which makes them more suitable in deployable aircraft (Huang et al. Citation2010). lists some SMP materials which could be adopted for realising energy-absorbing smart structures. The most utilised SMP material is the PLA material. This material has been extensively used because of its low cost, relatively good mechanical strength, short recovery period and satisfactory high recovery rate. The utilisation of PLA material for SMP has also attracted interest in several industrial sectors owing to their bio-driving and bio-degradable characteristics (Mehrpouya et al. Citation2021).
Barletta, Gisario, and Mehrpouya (Citation2021) utilised a PLA material via the FDM technology to fabricate a 4D printed lightweight energy-absorbing sandwich-like configuration as shown in . The SMP was obtained by combining a PLA filament with a 96% approximate amount of L-isomer content, an approximate amount of 1.25 KDa molecular weight and an approximate amount of 1.6 KDa polydispersity index. Also, a 10% TPU elastomer was added to the PLA. The shape memory properties of the configuration were explored by investigating various operations of the printer such as the nozzle temperature, printing speed and laser thickness. Also, they study the activation temperature which enables the shape recovery of the configuration after it was subjected to a constant deformation quasi-static loading. Using differential scanning calorimetry, the glass temperature of the PLA filament was found to be 57°C. To actuate the SMP, it was heated in water at temperatures of 65°C, 75°C and 85°C. These temperature differences triggered the SMP responses classifying them, therefore, as thermo-responsive SMPs.
Figure 5. Architecturally 4D printed sandwich structure before and after deformation (Barletta, Gisario, and Mehrpouya Citation2021).
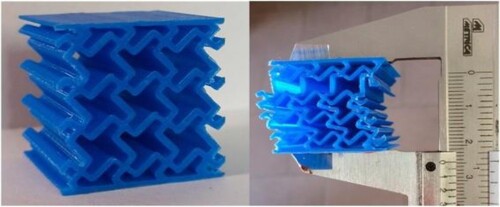
Another thermo-responsive SMP with PLA as the base material and glass transition temperature of 64°C was investigated by Liu et al. (Citation2018). The 4D printed shape memory origami device was subjected to crushing load. The shape recovery characteristics as well as the recovery load were largely affected by the shape recovery temperature and the manner with which the shape memory origami device was loaded. Under the application of constant loading, the recoveries of deformed samples were realised after they had been heated to 90°C. Two types of loading were used, namely – the folding and unfolding loading conditions. It was observed that the latter loading condition applied to the origami device recovered faster to their original shape than when the former loading condition was applied. This result was attributed to the rate at which heat was conducted during different loading conditions.
Recovery temperatures of SMPs are often higher than their . Moreover, heating them below their
under constant stress, retains their default shape. However, heating them above their
stimulates their recovery ability. Above this
, the flexible part softens with movement in the crosslinks (Keshavarzan, Kadkhodaei, and Forooghi Citation2020). This implies that rigidity is low at high temperature and high at low temperature (Tobushi et al. Citation2009). The mechanism that enables the shape recovery of SMP metamaterial and structure has been identified as dual-segment system (Huang et al. Citation2010), that is, it can be divided into elastic and transition segments as illustrated in (a). At higher temperature, the SMP softens more than at lower temperature. At low temperature, for example in (a), the thermo-responsive SMP remains hard. With the increase in temperature and during loading, the SMP metamaterial becomes amenable to deformation as seen in (b). Upon cooling, the SMP becomes hard again under certain constrained condition and strain energy of deformation is stored as depicted in (c). When the constraint is removed, i.e. (d), the SMP retains a temporary shape. Finally, upon heating above the
, the SMP metamaterial is almost or fully recovered to its original shape as shown in (e).
Figure 6. Illustration of one-way mechanism shape recovery of thermo-responsive SMP (a) original state with hard part, showing elastic segment in green and the transition segment in blue (b) deformation programming stage under compressive loading and increased temperature resulting in softened part (c) loading removed, part constrained and temperature decreased, resulting in hardened part (d) constraint removed and parts cooled, resulting in temporary deformed shape (e) metamaterial heated above , resulting in softened part and full shape recovery.
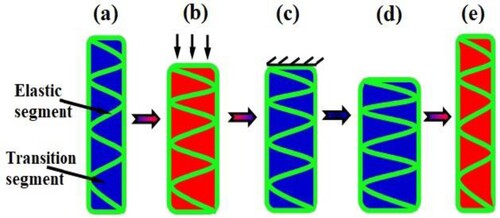
To further buttress the above concept, Bodaghi et al. (Citation2020) fabricated a reversible/recoverable energy-absorbing auxetic metamaterial using the 4D printing technology. The printed meta-structure was a combination of both soft and hard components. In the analysis of the thermo-mechanical behaviour of the shape-based energy-absorbing structure, two concepts namely, cold-programming and strain recovery, were introduced. It was noted that the programmable procedure between the initial original shape and the temporary shape during unloading was the cold-programming procedure, while the programmable procedure between the transition stage of the temporary shape and the material being recovered to its original shape was the strain recovery procedure as shown in (a). The meta-structure was subjected to compressive loading-unloading and then cooled. The investigated auxetic re-entrant meta-structure was reported to recover its original shape at the end of heating–cooling stage as shown in (b). Furthermore, research has found that some SMP can exhibit two or more primary shapes when exposed to stimuli. This type of SMP is called triple shape memory polymer (Joshi et al. Citation2020) or multiple shape memory polymer/material (Ding et al. Citation2019), respectively.
Figure 7. Behaviour of 4D printed auxetic meta-structure (a) cold programming and strain recovery procedures (b) deformation stages during start and end of loading as well as unloading, heating-cooling and recovery taken from Bodaghi et al. (Citation2020).
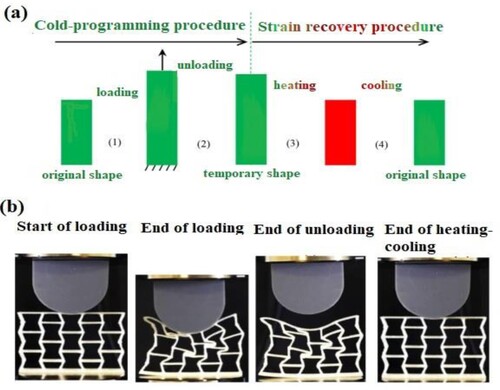
3.2. Shape memory composites
This is also another programmable metamaterial whose components could constitute a SMP or SMA and a fibre-matrix material (Zeng et al. Citation2022). It could also be obtained by mixing SMPs or SMAs with reinforcement additives such as carbon nanotubes (CNT), graphene platelets, nanofillers, etc. That is, SMC has been reported to include at least one SMP or SMA (Huang et al. Citation2010; Tobushi et al. Citation2009). Also, SMP can combine with SMA to form a shape memory polymer composite (Kang et al. Citation2018). Like the SMP, the of SMC is also a very important parameter. That is, the recovery capability of SMC has been reported to be a function of its
. Dong et al. (Citation2021b) combined two polymeric materials (i.e. PLA and TPU) with CNT to form a SMC filament prepared by using a single screw extruder. The 3D FDM device was upgraded, and the SMC filament was introduced into it to fabricate a 4D printed auxetic composite which could serve as an adaptive energy absorbing structure. The fabricated SMC structure was reported to have a very high electro-responsive shape recovery capability.
Research has shown that SMC metamaterials give higher mechanical performance than SMP metamaterial. For example, Choong et al. (Citation2020) added nanosilica particles into SMP resin to form a SMC. This was achieved by mixing nanosilica suspension into a photopolymer resin via a magnetic mixer after which a centrifugal vacuum was used to thoroughly stir the mixture. The SMC (i.e. ) photopolymer was transferred to a bottom-up of the DLP printing technology where the samples were printed as rectangular bars. The
of the sample and its viscoelastic properties were measured with the aid of a dynamic mechanical analysis. The mechanical properties of the sample were tested at room temperature and at temperature above the
. The shape memory behaviour of the SMC printed bars was characterised using the dynamic mechanical analysis. As expected, before deformation, the sample was heated above its
and then allowed to cool below its
to fix the deformation. After this, unloading followed which facilitated the recovery of part of the strain. Finally, the sample was reheated above its
and the shape recovery ability of the sample was measured. The mechanical properties of the SMC were compared with that of the SMP (i.e. without the
particles). Results showed that SMC outperformed SMP in mechanical properties (i.e. improved elongation at break and Young’s modulus) both at room and elevated temperature (i.e. temperature above
). Therefore, by adding appropriate amount (wt%) of nanoparticles or nanofillers to SMP resin, the mechanical performance of the resulting SMC can be improved significantly.
To further accentuate the improved mechanical performance of SMC structure over SMP structures, Liu et al. (Citation2023) blended two SMPs (i.e. PLA and TPU) with iron oxide () particles using FDM 3D printer to realise a 4D printed re-entrant honeycomb structure. Before the realisation of these auxetic structures, some rectangular shapes specimen composed of PLA/TPU/
SMC were 3D printed and their SME were investigated. The PLA crystalline region was the fixing phase while the amorphous or non-crystalline region of the SMC was the switching phase that enabled the formation of temporary shapes. That is, at temperature above the
, the mobility of the non-crystalline region of PLA was reinforced and a temporary deformation shape was realised. Moreover, the blending of small amount of TPU to the PLA acted as a toughness agent which prevented the PLA from irreversible damage during deformation and shape recoverability. Further, the addition of different
particles helped to trigger the magnetic field for SME. Thus, SMC have higher capacity than the SMP in terms of improved mechanical performance and as such has promising potential in device where high load carrying capacity is desired. Moreover, for SMC containing fibre reinforcement, it was shown that the fibre contents had significant effect on the tensile properties (Dong et al. Citation2021a). However, to prevent the reduction of shape memory performance for SMC with fibre incorporation, careful design and optimisation should be carried out by regulating both the printing process parameters and fibre contents.
3.3. Shape memory metals and alloys
In recent times, metals and alloys exhibiting SME are being increasingly investigated in various research sectors and industries. Stimulus-responsive metallic material can be mechanical responsive i.e. thermo-responsive, magneto-responsive, etc. However, there is still very limited research carried out to investigate the mechanical performance, crushing characteristics and SME of different metals and their alloys. The most investigated metallic alloy utilised to explore the shape memory behaviour of SMA is the nitinol alloy (Liu, Liu, and Ma Citation2022; Xiong et al. Citation2021). Despite its wide application for SME, its utilisation especially in the SLM technology to fabricate 4D printed nitinol structures has suffered some challenges. For example, there is still the challenge of pores formation and crack propagation during the SLM fabrication process. In the investigation of SME of nitinol that was carried out by Xiong et al. (Citation2019), two SLM-printing parameters such as the laser scanning length and laser scanning direction were considered. It was shown that these two parameters could address the poor tensile ductility resulting from the inner defects and severe unidirectional columnar grains encountered during the SLM fabrication process. The inner defects included pores and cracks while the columnar grain facilitated crack propagation. The SLM-NiTi sample and SLM-NiTi parts were subjected to uniaxial tensile test and the shape memory behaviour of both the sample and the parts were explored at various tensile deformation ranging from 2 to 8%. For the compressive test of 50% deformation, a shape recovery rate of 99% was achieved for the SLM nitinol parts after being heated, as shown in .
Figure 8. Compression of structural part made from nitinol alloy and showing very high shape recovery percentage ratio (Xiong et al. Citation2019).
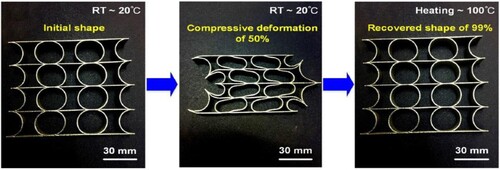
Some common problems with using metal to fabricate architectural designs such as the energy absorbers are the mechanical instability and low satisfaction of strain recoverability arising from the material constituents. However, using SMA, these challenges can be addressed by providing it with self-strengthening effect with little or no formation of localised deformation bands. In a recent study carried out by Xiong et al. Citation2021, nitinol SMA honeycomb and lattice structures were fabricated, and the SME were compared with aluminium honeycomb structure void of SME. It was shown that the SMA nitinol structures resulted in a more significant improvement of shape recoverability than the honeycomb structures void of SME. The results of their findings open new possibilities of exploring SMAs, for example, copper-based (i.e. Cu-SMA) or iron-based (i.e. Fe-SMA), to fabricate 4D printed EAMM and EASS with high mechanical performance and satisfactory shape recoverability.
3.4. Shape memory hybrids
Shape memory hybrids (SMHs) are one of the most recent material design members in the family of SMM. They are formed by combining two or more materials such that the combined properties of the hybrid material or structure produces a SME. Unlike the SMC where at least one of the SMM constituents can produce SME, the individual material constituents making up the SMH, on the other hand, cannot produce SME. All the constituents must combine to give a SMH. The mechanism of SMH is similar to that of the SMP (Sun et al. Citation2012; Wang et al. Citation2012.) which involves two or more segments or domains (i.e. elastic-transition segments/domains). SMH is typically formed by combining a matrix with an inclusion. The matrix or inclusion can be made from metals, organic/inorganic, polymers, composite materials, etc., which do not exhibit SME. However, the combination of the matrix and inclusion without any chemical reaction between them results in SME. Generally, the of SMH is obtained from the softening temperature of the inclusion when in its original form. With the proper material selection, it is easier to predict the main function and properties of SMH. Thermo-responsive and pressure-responsive energy-absorbing SMH materials and structures are promising areas to explore. For example, the thermo-responsive behaviour of SMH metamaterial was investigated by Wang et al. (Citation2012). In their study, plastic sponge (which represents the matrix or elastic component) was filled with P407 gel (which represents the inclusion or transition components) to form a sponge-P407 gel hybrid material. The thermo-responsive SME of the SMH was investigated and the results showed that the SMH material recovered its shape in about 50 s upon immersion in water at 0°C. However, the SMH material took 57 min to fully recover its shape when it was immersed in water at 20°C. The faster shape recovery outcome was attributed to the melting of the gel component in water at 0°C, while the slower shape recovery was due to the dissolution of the gel component in water at 20°C.
4. Recoverable energy-absorbing structures
Here, the mechanical and crushing performance of different 4D printed energy absorbing structures, their functional properties as well as their shape recoverability potentials, are discussed. Shape recoverability of intelligent materials and structures has been studied since the past half-decade (Wan, Yu, and Sun Citation2022; Pirhaji et al. Citation2022; Wang et al. Citation2020;). This shape recoverability in intelligent energy-absorbing 4D printed structures is gradually gaining popularity especially in the transportation industry. It is quite interesting to study how stimulus-responsive mechanical actions can change and recover the shapes of energy-absorbing structures during deformation and when operating under different environmental conditions.
To begin with the deformation and recoverability of various energy absorbing intelligent structures, some important parameters which describe their crushing performance as well as recoverability indexes must be defined. Some of these important crushing parameters include the initial peak load (), energy absorption (EA), specific energy absorption (SEA) and crushing load efficiency (CLE). During loading, the
gives an indication of the effectiveness of the energy absorber. Lower
with respect to the subsequent peak loads in a force-displacement diagram results in better crushing performance. The EA is the crushing load (
) along the displacement (x) over crushing distance (
). The SEA is the EA per unit mass (m) of the structure and the CLE can be obtained by dividing the mean crushing load (
) by the peak crushing load
during deformation. The mathematical relationships of the main crushing parameters defined above are given in Equations (1, 2 and 3), respectively (Isaac Citation2020; Hamzehei et al. Citation2022).
(1)
(1)
(2)
(2)
(3)
(3)
For composite and polymer-based 4D-printed energy-absorbing smart structure with shape memory effects and reversibility, the shape fixity ratio (SFR) and strain recovery rate (SRR) are very important shape memory indicators that determine the shape memory performance. The SFR measures the amount of storage deformation. It is the ability of the temporarily deformed material to fix the programmed shape after unloading. It is expressed as (Xiao et al. Citation2015):
(4)
(4) where
,
and
represent the number of cycles, fixed strain after stress relaxation (Rahmatabadi et al. Citation2022), and the maximum applied strain obtained after the stretching step (i.e. after unloading and before cooling), respectively. For SMP and SMC, it is known from the hysteresis curve that during the application of strain and deformation programming, strain is recovered. This is not so with most metals and alloys because they quickly lose their reversible strains. The SRR, therefore, measures the ability of the SMM to recover its original configuration. It is given by the relation (Keshavarzan, Kadkhodaei, and Forooghi Citation2020):
(5)
(5) where
are the residual strains obtained at the end of the two cycles. Moreover, the SRR has been reported not only to be dependent on the level of stored strain during programming but also on the deposition direction during the printing process (Abuzaid, Alkhader, and Omari Citation2018).
4.1. Lattice structures
Lattice structures fabricated by 3D printing technology have been shown to possess high specific strength and stiffness. Consequently, they have been extensively studied as energy absorbers (Andrew, Verma, and Kumar Citation2021; Sharma and Hiremath Citation2022; Farrokhabadi et al. Citation2022). Moreover, in recent times, cellular lattice structures with excellent energy absorption and shape recovery potential have been fabricated via the 4D printing technology (Dong et al. Citation2021b; Li et al. Citation2021; Davami et al. Citation2019). These programmable energy absorbing lattice metamaterials and meta-structures are capable of adapting and mechanically adjusting to environmental changes. For instant, as a requirement during automatic deployment, temperature stimulation is given to metamaterials and intelligent structures. To demonstrate this, Tao et al. (Citation2020b) fabricated such intelligent metamaterial and investigated their deformation, shape fixity and recovery behaviours. Their designed multi-stable lattice metamaterial was realised using the 4D printing technology (i.e. inkjet 3D printer plus a SMP made from Verowhite and RGD8530 with a of 53°C). A compressive strain of 0.54 was applied to the lattice metamaterial at a temperature of 70°C which resulted in a buckling deformation mode as shown in . During loading, observable compressive buckling modes of 30 to 93 N and 1 to 1.6 N were recorded at 50°C and 70°C, respectively. Moreover, during this compressive loading condition, between 50°C and 70°C, the lattice metamaterial could change its stiffness severely. The lattice metamaterial was cooled to 25°C which resulted in the self-locking of the lattice microstructure to enable shape fixing. To recover the lattice original shape, it was heated at 75 °C.
Figure 9. Compressive deformation stages at various cooling, heating and recovery temperatures (a) experimental measurement (b) finite element approximation (Tao et al. Citation2020b).
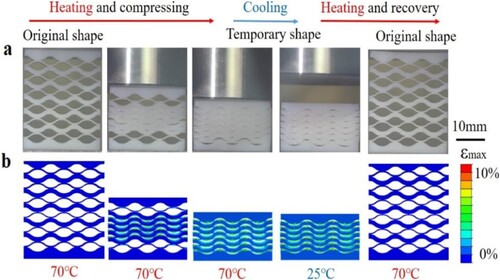
The cell geometry (Dong et al. Citation2021b) and topological arrangement of lattice structures play a significant role in the crushing performance and energy recoverability potential. This was demonstrated by Keshavarzan, Kadkhodaei, and Forooghi (Citation2020) who investigated the energy absorption and SME of two lattice topologies namely – rhombic and body-centered cubic (BCC) and compared their results with cylindrical bulk samples. These structures were fabricated using 4D printing (i.e. DLP printer and SMP resins). Firstly, the investigations were carried out in different environmental conditions which were indicated as the cold, warm and hot programming schemes. Quasi-static deformation rates at 1.0 and 0.6 mm/min were given to the bulk samples and lattice structures, respectively. The was found to be 83°C and thermomechanical test below the
(i.e. 20°C) and above the
(i.e. 110°C) at various cycles, were performed. It was observed that at all conditions, the various SMP energy absorbers indicated almost similar strain rate recovery. However, results showed that the recovery of the induced energy, the mechanical performance (i.e. stiffness and strength) and energy absorption capacity of the rhombic lattice structure outperformed the BCC lattice and cylindrical bulk samples. Carefully selecting the correct 4D-printed metamaterial lattice topologies can optimise the energy absorption capacity and the recovery of induced energy.
Some topological lattice structures such as the face-centered cubic (FCC) lattices are stretching-dominated during their plateau deformation stage compared to the BCC lattices which are bending-dominated (Jin et al. Citation2019). Consequently, the FCC lattice structures have better mechanical and crushing performances than their BCC lattices counterpart. With this background knowledge, Zhao et al. (Citation2023) recently investigated the mechanical strength, EA, SEA, CLE and shape memory behaviour of some stretching-dominated lattice structures. The metamaterial lattices were fabricated using FDM technology with SMP resin and SMH material consisting of PLA and . With SMP resin, various topological metamaterial structures were obtained by modifying both their parametric and gradient conditions. For the mechanical properties of the metamaterial lattice structure, it was reported that increasing the truss diameter resulted in increased compressive stiffness and decreased Poisson ratio. However, when the length and height of the metamaterial lattice structures were increased, the Poisson ratio increased. In terms of the crushing performance, both the EA and SEA values increased with increased truss diameter which resulted in highly significant CFE. However, increasing the length per unit cell of the lattice meta-structure resulted in increased porosity and consequently, reduced SEA values. Moreover, to obtain their SME, the lattices were heated to 90°C and then subjected to a 50% deformation. They were further cooled from 90°C to 20°C; unloaded while maintaining their fixed deformation, and finally reheated from 20°C to 90°C to recover their original shapes.
Lightweight 4D printed composite lattice structures have also shown promising potentials especially in the reduction of initial peak force, improved energy absorption and better shape recovery rate. In a study with SMC horseshoe lattice structure, it was discovered that compression stiffness as well as initial peak load were significantly lowered and were strongly temperature dependent (Zeng et al. Citation2022). The 4D printed energy-absorbing horseshoe lattice structures were fabricated via the FFF technology with the SMC material consisting of a PLA-based SMP and a carbon fibre-reinforced plastic (CFRP). Various horseshoe lattice configurations were realised by varying the horseshoe amplitudes (i.e. 2, 4 and 6 mm) as shown in . Reports indicated that the shape recovery capabilities were influenced by the wave-like amplitudes of the horseshoe lattice structures at various loading displacements. Under these maximum loading displacements i.e. 2, 5, 10, 20 mm, the shape fixity values were approximately 0.84, 0.89, 0.92 and 0.93, respectively, while their corresponding shape recovery values were 0.94, 0.91, 0.91 and 0.84, respectively.
Figure 10. Different 4D printed horseshoe lattice configurations with varying amplitudes and made from SMC material (Zeng et al. Citation2022).
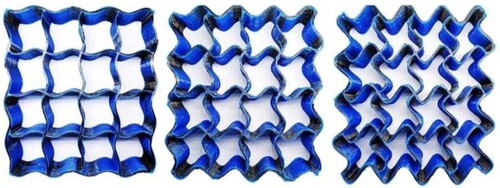
The mechanical behaviour of meta-structural lattice under cyclic loading has also been given attention in recent times. Yousefi et al. (Citation2022) investigated the mechanical performance, energy absorption and recoverability of PA 12 auxetic meta-structures subjected to cyclic loading as shown in (a). The investigation was performed up to the eleventh cycle and deformation of the structures was observed at the start of loading, end of loading and end of unloading. However, at the end of unloading, it was revealed that the auxetic lattice meta-structures were unable to attain full recovery of their original shapes owing to residual plastic strain generated at their middle sections. The force-displacement hysteresis curves for all cyclic loadings are shown in (b). It can be seen that the number of cycles at different strain values influences the dissipated internal and absorbed energy significantly. Moreover, after the unloading stage, the residual plastic strain can be released by heating the lattice mata-structures and consequently, enabling full recovery to their original shape. This shape recovery of meta-structures was demonstrated by Hamzehei et al. (Citation2022) where they utilised the 4D printing technology to realise recoverable energy absorbers with zero Poisson ratio as depicted in (c).
Figure 11. (a) Mechanical behaviour of auxetic meta-structure subjected to cyclic loading (Yousefi et al. Citation2022) (b) force-displacement hysteresis curves of meta-structure for all cyclic loadings at different strains (Yousefi et al. Citation2022) (c) shape recovery of energy absorbing lattice meta-structures after heat-cooling proceedure (Hamzehei et al. Citation2022).
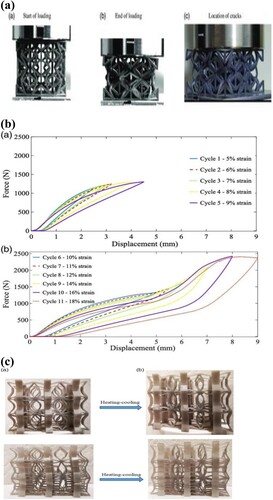
4.2. Honeycomb structures
In recent years, there have been quite a good number of research efforts on the crushing performance of 3D-printed honeycomb structures made from different materials which do not exhibit SME. However, in the investigation carried out by Cheng et al. (Citation2021), it was reported that a 3D-printed honeycomb structure made from continuous CFRP and fabricated via the FFF technology can recover its original shape within 5 s under thermal stimulation. Their investigation introduced the great potential of recoverability for well-tailored honeycomb structures realised via 3D printing technology.
Currently, honeycomb structures with improved mechanical and crushing performance as well as desirable SME are being fabricated using 4D printing technology (Pasini et al. Citation2022; Liu, Liu, and Ma Citation2022; Ji et al. Citation2020). Moreover, to improve toughness and resistance to shearing, 4D printed honeycomb with auxetic properties can be realised. Such auxetic honeycomb meta-structures including re-entrant, chiral and anti-chiral designs, have negative Poisson’s ratio effect and tuneable mechanical properties. Ji et al. (Citation2020) fabricated a re-entrant honeycomb structure made from SMP using the inkjet 3D printing technology. The realised 4D-printed auxetic structure was reported to have adjustable stiffness, repeated energy absorption capacity, shape fixity and recovery potential. The adjustable stiffness and rigidity were realised when the temperature of the re-entrant honeycomb structure dropped to 30°C from a of 60°C. This adjustable stiffness is a promising advantage in the aerospace industry where variations of aircraft wings are employed to enhance flight performance. Also, along the temperature scale, for application involving changing environmental conditions, 4D-printed re-entrant honeycomb metamaterial with temperature memory effects (TME) can be used as viable methods that allow for tuning the recoverability of auxetic cells. Such TME auxetic structures have the capability not just to remember their original shapes but also their deformation temperatures (Pasini et al. Citation2022).
Reversible/recoverable energy absorption and auxetic property of re-entrant honeycomb structures were further explored by Namvar et al. (Citation2022). The 4D printed structures with PLA as base material were designed as re-entrant honeycomb structure with negative Poisson’s ratio, re-entrant/hexagonal honeycomb hybrid structure with zero Poisson’s ratio, and hexagonal honeycomb structure with positive Poisson ratio as shown in (a). Their mechanical responses and recoverability were evaluated after subjecting them to quasi-static compression loading and loading-unloading programming processes. As expected, the re-entrant metamaterial outperformed the other two in terms of energy absorption. However, in terms of their shape fixity and shape recovery rate, the re-entrant structure was 74.53% and 100%, respectively; the re-entrant/hexagonal hybrid structure was 77.4% and 100%, respectively and the hexagonal structure was 79.66% and 100%, respectively. The compressive deformation and recovery stages for the 4D printed meta-structural types are described in (b–d), respectively.
Figure 12. Various design configurations under loading, unloading, heating-cooling and shape recovery (a) different modified honeycomb structures (b) auxetic re-entrant honeycomb structure (c) mixed re-entrant with honeycomb structure (d) conventional honeycomb structure (Namvar et al. Citation2022).
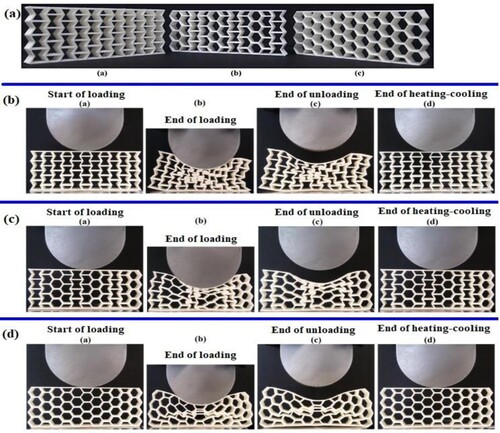
4.3. Sandwich structures
Sandwich structure utilised as an energy absorber consists of two face-sheets (i.e. the impacted and the fixed surfaces) and a core between the face-sheets architecturally connected. The core which usually deforms during impact can be designed to meet specific applications. Both the core and face-sheets can either be made from the same material or from different materials. This architectural sandwich structure has lightweight advantage with excellent specific stiffness and strength. Current research has explored the possibilities of using 3D printing with SMM to manufacture smart sandwich metamaterial energy-absorbing devices. The effects of design and process parameters on energy absorption and recoverability of the 4D-printed sandwich metamaterials are meticulously taken into consideration. For example, in the research carried out by Serjouei et al. (Citation2022), the printing parameters and core shape of the shape memory PLA-based architectural sandwich structure realised via the FDM technology, were investigated. The different architectural cores (i.e. square and hexagonal horseshoe patterns) were made from the same SMP material with the face-sheets as seen in . The FDM printing process parameters taken into consideration were nozzle temperature, printing speed and layer height. It was reported that increased layer height from 0.1 to 0.3 mm, reduced the compression load. However, increased nozzle temperature from 190°C to 220°C, increased compression load. Lastly, the increased printing speed from 50 to 90 mm/s was less significant in terms of the compressive load. Moreover, the hexagonal horseshoe pattern resulted in higher compressive load than those of square horseshoe metamaterial sandwich structures.
Figure 13. Architectural 4D printed sandwich structures (a) square horseshoe pattern (b) hexagonal horseshoe pattern (Serjouei et al. Citation2022).
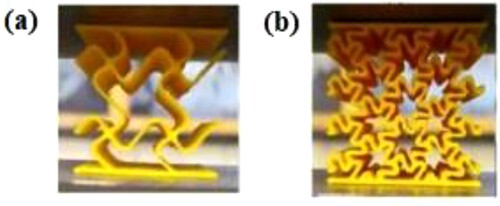
A similar investigation of utilising same material, fabrication technique and process parameters including activation temperature has been performed by Barletta, Gisario, and Mehrpouya (Citation2021). The activation temperature parameter was reported to significantly influence the recovery rate of the 4D-printed sandwich structure. In another investigation performed by Mehrpouya et al. (Citation2022), the change in core design was shown to give the highest effect on the energy absorption of 4D-printed sandwich structure. Other recent researchers who have explored 4D-printed reversible/recoverable energy-absorbing sandwich structures have been reported in the literature (Mehrpouya et al. Citation2020). For example, Bodaghi et al. (Citation2020) fabricated 4D-printed auxetic sandwich structure made from dual materials (i.e. soft and hard filament materials) which has elasto-plastic and hyper-elastic properties. The hard filament material was a polyurethane SMP with a of 60°C while the soft material was a FlexPro filament material. The sandwich architectural design using dual material showed the ability of creating non-linear stiffness with energy dissipation and recovery effects.
4.4. Origami and tubal structures
Origami metamaterials can be obtained by bringing panels together along their edges, forming creases where folding occurs during loading. The folding nature of origami structure allows them to possess bistable behaviour (Kamrava et al. Citation2017), negative Poisson ratio (Yasuda and Yang Citation2015) and shape-changing characteristics (Liu et al. Citation2018). Additionally, to achieve high strength and lightweight properties of energy-absorbing structures, origami and tubal structures have been adopted (Tao et al. Citation2020a; Joshi et al. Citation2020; Lin et al. Citation2020). Different kinds of origami and tube structures have emerged in recent times (Townsend et al. Citation2020; Li, Zhi, and Fan Citation2022; Yang et al. Citation2018). However, the Miura-origami structure has become popular due to its simplicity in construction and emerging application usage as metamaterial. The compressive behaviour and shape memory property of FDM 4D printed Miura-origami tessellation and tube structures made from PLA-based SMP, were investigated by Liu et al. (Citation2018). The influence of shape recovery temperature and how different loading conditions (i.e. unfolding and folding loading) affect the shape memory of origami and tubal metamaterial, were investigated. It was observed that both the shape recovery temperature and the different loading conditions, significantly influenced the shape memory behaviour of both origami and tubal structures. That is, under unfolding loading condition, the 4D-printed metamaterial origami structure recovered faster than when subjected to folding loading condition. This was a result of the different heat conduction rate at the different loading conditions. Moreover, for a recovery force at 90°C and under unfolding loading of the origami structure, the recoverability was more than twice of all other structures at same temperature of folding and unfolding loading, as shown in .
Figure 14. Effect of loading conditions on shape memory of origami structure during (a) unfolding load (b) folding load (Liu et al. Citation2018).
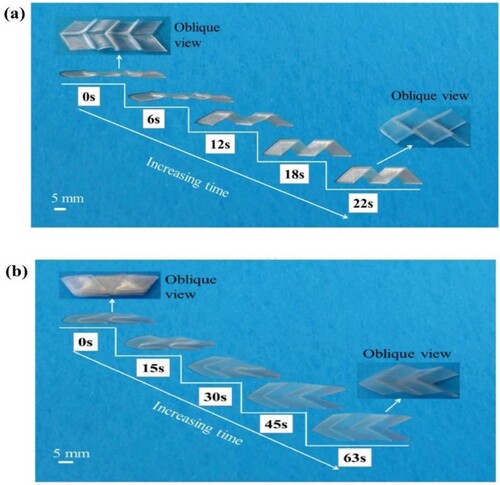
Origami structure obtained by 4D printing technology can be thermally tuneable and have been found capable of switching from rigid protection mode to flexible shock absorption mode as well as exhibiting SME (Tao et al. Citation2020a). (a) illustrate both the shape programming and shape recovery processes of a SMP origami meta-structure with a of 70 °C subjected to compressive loading as depicted in (b). During temperature rise above the
, the structure softens and act like a rubber. As the temperature falls below the
, the structure hardens. At this stage, when the load is removed, the structure assumes a temporary shape and upon heating above the
, it recovers its original shape. Moreover, for the SMP origami structure under folding deformation and as the temperature changes from 30°C, 40°C, 50°C and 60°C, the mechanical and crushing performance were influenced. Stiffness and load-bearing properties with elastic modulus decreased with rising temperatures as shown in (c). As temperature decreased, the internal and absorbed energy also decreased, see (d) and consequently, decreased SEA values, see (e). However, the effect of temperature on the deformation mode of the 4D-printed origami structure was reported to be insignificant.
Figure 15. Deformation programming and recovery stages as well as mechanical and crushing performances of SMP origami structure (a) shape programming and shape recovery processes of origami metamaterial (b) origami structure under compressive loading (c) effect of temperature variation on Young’s modulus (d) effect of temperature on the internal energy and energy absorption (e) effect of temperature on the SEA (Tao et al. Citation2020a).
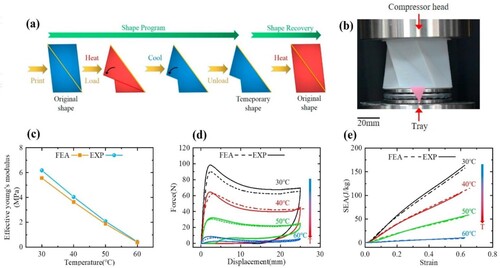
4.5. Auxetic metamaterials and meta-structures
Metamaterials and meta-structures with negative Poisson ratio (NPR) have been fabricated using the 4D printing technology. These structures are usually referred as auxetic structures because of their potential to either reduce in size transversally when compressed longitudinally or to increase in size transversely after being stretched longitudinally. Various forms of auxetic meta-materials including re-entrant (Hassanin et al. Citation2020), chiral, re-entrant chiral and anti-chiral, etc., have emerged in recent times (Usta, Türkmen, and Scarpa Citation2021; Zhang, Lu, and You Citation2020). Xin et al. (Citation2020) developed a 4D printed chiral metamaterial made from PLA-based SMP. The chiral metamaterial possessed the ability of transforming the collapse mode from bending dominated to stretching dominated mode. This tuneable mechanical characteristic function as well as the recoverable potential of the chiral metamaterial makes it a promising adaptive energy-absorbing structural device. In another investigation carried out by Pasini et al. (Citation2022), a 4D printed re-entrant honeycomb auxetic structure made from photopolymer resin and fabricated via the SLA technique was developed to investigate its shape recovery tuneability. The 4D printed re-entrant meta-structure possessed the ability to recover its original shape as well as remembered its deformation temperature. That is, the recovery process was a function of both time and temperature. As the deformation temperature increased from 60°C to 100°C (i.e. above its of 30°C), the shape fixity showed excellent values. However, shape recovery was almost unaffected by the deformation temperature and as a result, all the re-entrant auxetic structures recovered their original shapes. In a recent study carried out by Dong et al. (Citation2021b), a 4D printed electro-induced auxetic meta-structure made from SMC and fabricated using an upgraded FDM technique was developed to study the mechanical properties, SME and NPR effects. The SMC was obtained by combining conducive hybrid filament blend (i.e. PLA/TPU/CNT) reinforced with continuous carbon fibre. It was revealed that the auxetic electro-induced meta-structure displayed high activation capabilities by various stimuli-responsive actions.
4.6. Performance of reversible/recoverable structures
summarises the main crushing performance, shape memory performance and the type of response mechanisms of some selected 4D printed energy-absorbing structures investigated in recent times. Multi-cellular (MC) lattice structures give good crushing performance; however, the geometrical shape of the lattice structures significantly influence their crushing performance. The investigation carried out by Liu, Liu, and Ma (Citation2022) showed that the pentagonal MC lattice structure outperformed other shaped MC lattices in terms of EA, SEA and CLE. In particular, the SEA and CLE of pentagonal MC structure improved by 88% and 128%, respectively over that of quadrilateral MC lattice structure. However, the hexagonal MC lattice showed a slightly higher recovery rate over the pentagonal MC lattice structure. Also, it is seen from that the most utilised triggered response mechanism for shape recovery of the meta-structures is by heating them above their after unloading has taken place. Moreover, apart from the thermal responsive action commonly adopted, Liu et al. (Citation2023) recently utilised a magneto-responsive mechanism to recover the shape of 3D printed re-entrant honeycomb structure with a height recovery ratio of 0.955. Finally, it is observed that the re-entrant honeycomb structures in demonstrated a very high potential of shape recovery rates. It can be inferred that the negative Poisson ratio of auxetic metamaterials does not only positively influence the crushing performance but also their shape recovery performance. Therefore, future investigations could be carried out to demonstrate the effects of auxetic meta-structural design on shape memory performance.
Table 3. Summary of selected recent findings on the crushing and shape memory performances of 4D printed EAMM and EASS.
It should be noted that various 3D printing techniques are currently being developed to improve their performance and to meet the present application of recoverable/reversible energy absorbers in deployable aircraft, impact and crushing mitigation. However, during 3D printing of these metamaterials to produce 4D printed meta-structures, interfaces, pores, cracks and defects are developed intrinsically. Mechanical stresses are concentrated in these defective areas which result in the reduction of mechanical strength and energy-absorbing efficiency of the 4D printed meta-structures. Moreover, these defects, small deviation in mechanical properties and anisotropic effects resulting from the 3D printing techniques, make them susceptible to degradation after repeated actuation and shape-changing process. Sustaining repeatability of the actuation process of recoverable/reversible energy absorbing structure is crucial for effective performance. However, the degree of internal defects during fabrication and the deterioration of mechanical strength during repeated cycles undermine this performance and are highly dependent on the type of SMMs as well as the fabrication techniques. For example, the FDM or FFF technique which mostly utilises polymer or composite-based metamaterials generates more internal defects than SLM technique which is mostly associated with metal or alloy-based metamaterials. For meta-structures fabricated via the metal additive manufacturing, the annealing of metallic metamaterials can relieve their residual stresses, enhance their mechanical performance during cyclic loading and improve their reusability/repeatability. This was demonstrated by Tan et al. (Citation2019) where they showed that annealed steel metamaterial improved repeatability than the unannealed ones. However, the compressive strength and energy dissipation of such steel metamaterials decreased due to the annealing effect. To accentuate the effect of defects on reusability of resin-based meta-structure after shape recovery, a study was undertaken by Hamzehei et al. (Citation2022). In their investigation, it was observed that fracture due to bending of some part of the walls, influenced repeatability of the 4D printed meta-structural model ‘D’ after two cyclic loadings of the original material, as shown in the force-displacement curve of . However, in their original form, for meta-structural model ‘A’, (i.e. without defect) at first and second cyclic loadings, the force-displacement characteristic curves can be seen to be approximately the same. Therefore, indicating repeatability of the energy-absorbing mata-structure after initial shape recovery.
Figure 16. Force-displacement curves showing the effect of defects on the reusability of two meta-structural models after shape recovery (Hamzehei et al. Citation2022).
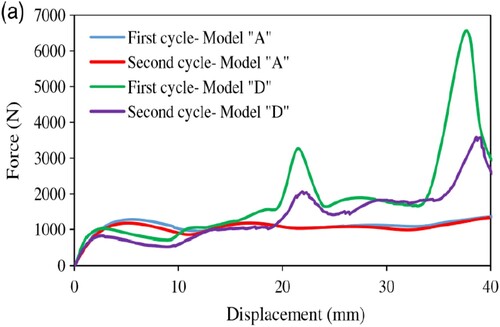
4.7. Application of reversible/recoverable structures
The various applications of 4D printed energy-absorbing structures have been shown to include crash mitigation in high-speed vehicular structures, automotive passive safety, highway safety, personal safety and packaging of valuables, etc (Bodaghi et al. Citation2020; Ganilova and Low Citation2018). These meta-structures have also been used in blasting and ballistic impact as well as shock protection and vibration damping (Zhou et al. Citation2015; Yang and Ma Citation2019). Moreover, 4D-printed reversible/recoverable energy-absorbing meta-structures with negative stiffness can be applied in shock isolation owing to their long plateau region exhibited during compression (Tan et al. Citation2019). In addition, 4D-printed reversible energy absorber using porous nitinol can find application in medical implants due to their promising potential of protection against peak loads and propagation of shock waves (Köhl et al. Citation2011). Finally, it is expected that the tuneable mechanical properties, crushing characteristics, shape recoverability and reusability which 4D printed energy absorbing structures promise, will in the future, find novel applications especially in the transportation, aviation, aerospace, building, marine and medical industrial sectors.
5. Challenges, future trends and perspectives
4D printed recoverable energy-absorbing metamaterial, as developing research in various fields including environmental science, impact engineering and many structural crashworthiness applications, is opening new possibilities for structural adaptability, controllability, deployability and tuneability. New functionalities, improved mechanical properties and desirable crushing performance can be achieved by a well-programmed shape recovery energy absorbing metamaterial and structure. However, there are still several deficiencies to overcome in terms of materials, 4D printing technologies and their processing parameters. Moreover, effective quality standards as well as fully informed and trained personnel are some of the bottlenecks to overcome in the fabrication of 4D printed EAMM. These technical skills and qualified personnel are needed to avoid or substantially minimise the divergence from 3D part design to the execution of 4D printed prototype. This section gives some of the lingering challenges, proffer where necessary, viable solutions to these challenges and attempt to provide future perspectives of 4D printed EAMM and EASS.
Most recoverable/reversible energy absorbers are made from smart materials or SMM as mentioned in this review. However, very few of these materials are in production which have restricted research into the field of 4D printed energy absorbers. Moreover, many of these meta-structural energy absorbers have been made from SMP where most of the polymer-based material are typically obtained from PLA probably because of its low , availability and biodegradability. However, there are quite a number of polymer-based materials as highlighted in that are yet to be explored in 4D recoverable/reversible energy absorbing structures. For example, PEEK material when co-extruded with continuous metallic fibre in 4D printing has been reported to be endowed with multiple SME (Zhou et al. Citation2022). Generally, to obtain a high energy absorption for SMPs, they must be heated above their
. compares the
of different polymer-based materials. It is seen that PEEK material has a very high
compared to most of the polymer-based SMPs. Hence, higher heat requirement is needed to heat the metamaterial above
, and consequently, higher procurement cost. However, the mixing of appropriate additives and ensuring compatibilisation effect of the resulting mixture, can be a veritable means of lowering the high
. Therefore, research efforts should be geared toward achieving reduced
for SMP materials that have high
values. Also, more investigations into new thermoset SMPs should be carried out as this type of metamaterials has been understood, from this review, to have better mechanical properties than its thermoplastic counterpart.
Table 4. Comparison of glass transition temperatures of different polymer-based materials.
Apart from 4D printed metamaterial and meta-structure of energy absorbers which are SMP-based, there are still very few investigations into those which are SMH-based, SMC-based and SMA-based. For instance, it was observed in this review that shape memory metals and alloys (except the commonly utilised NiTi-based SMA) have been rarely applied for recoverable/reversible energy absorbers owing to their low fatigue resistance which causes rapid loss of their reversible strain. To this end, future efforts are welcomed to investigate shape memory metals and alloys that have high retention of reversible strain during unloading process. Moreover, very limited studies have been undertaken to understand the full functional properties, crushing characteristics and recovery responses of 4D printed energy absorbers made from SMMs blended with nanocomposites and nanofillers. That is, it is possible to blend SMPs, SMCs, SMAs and SMHs with nanocomposites, nanotubes, nanofillers or geopolymers. These aspects are a promising perspective which largely depend on the development of compatible materials such as multifunctional polymers, composites and their hybrids. Though, from the perspective of reversible and recoverable energy-absorbing structures, 4D printing technology is still in its promising stage of development. However, with multifunctional polymers, composites and their hybrids, novel recoverable/reversible energy-absorbing smart structures with improved functionalities and properties can be realised. For example, such improvement in material properties can be observed in the degree of the metamaterial’s biodegradability, stiffness, strength, toughness, stimulus response and force of actuation under various environmental conditions. Therefore, research can be ventured into developing novel synthetic, bio-compatible and multi-component metamaterials offering new functionalities, wider range of properties, enhanced energy absorption, multi-functional triggered mechanisms and fast recovery responses.
The technological integration of 4D printing in the impact and crash mitigation sector is a welcomed development and is creating new possibilities in the fabrication of more complex structures. However, one factor that demands wider attention is the printing methodology adopted to realising meta-structural energy absorbers. For instance, it is seen in this review that the most utilised technique in realising 4D printed energy absorber is the FDM technology. Other 3D printing processes such as SLS, SLM, DIW, SLA, etc., for making 4D printed EAMM and EASS as mentioned in this survey, have been seldom utilised. The FDM printing technology still has the limitation of fabricating shape memory metamaterials that require high resolution. Furthermore, other challenges such as delamination caused by internal defects, material filament buckling during fabrication for SMPs, and material clogging in the nozzle for SMC (Razzaq et al. Citation2022), could be observed during the printing process. Therefore, research should be carried out on improving the design of several existing but unexplored 3D printing techniques; and developing novel printing methodologies suitable for 4D printing of smart structures. For example, optimising the process parameters during fabrication to enable more efficient printing processes and higher resolution of the 4D printed product. Moreover, for fabricating multi-metamaterial and multi-metacomponents, combined efforts should be put towards developing novel 4D printing software or application suitable and flexible for realising smart energy-absorbing structures.
Another future challenge is the long-term sustainability of 4D printed energy absorbers after repeated actuation and recoverability. It is seen in this review that smart energy-absorbing structures are subjected to programming deformation, repeated actuation and shape-changing process. These effects could possibly lead to the 4D printed meta-structure degrading with time. It is, therefore, necessary to ensure during fabrication, programming and recovering stages, that the continuous shape-changing process of recoverable/reversible energy absorbing structure is repeatable for a sustained period without losing its shape fixity and shape recoverability rate. Finally, improved actuation pathways with well-tailored mechanical deformation that accompanies a predetermined programming and recovering process are expected to be investigated and implemented in the foreseeable future.
6. Summary and conclusion
The introduction of 4D printing is paving ways to novel possibilities of realising complex and multi-functional structures in various industrial sectors. One such application is the fabrication of 4D printed EAMM and smart structures which has made significant progress in recent times. This review has surveyed the most recent progress in 4D printed EAMM and smart structures. It has also discussed the current trends in metamaterials, 4D printing processes, programming deformations and recovering stages of various meta-structures adopted for energy absorption application. Based on this review, 4D printing technology simply involves the utilisation of smart or intelligent metamaterials with 3D printing techniques to produce energy absorbers which after deformation can recover their original shapes when actuated by stimuli-responsive mechanisms. The smart or intelligent metamaterials investigated include SMPs, SMCs, SMAs and SMHs. However, a wide range of these metamaterials is yet to be explored for recoverable/reversible energy-absorbing structures. To this end, the review has highlighted some of these challenges, proffered viable solutions and routes to overcome these challenges, as well as presented some future perspectives. Currently, novel 4D printed energy-absorbing structures including various designed lattice structures, honeycomb structures, architectural sandwich structures, origami and tubal structures are emerging. These smart or intelligent 4D printed structures obtained via 3D printing processes first undergo load deformation, through shape programming, then unloading and finally shape recovery. Thus, making them exhibit certain self-attributes including self-repairability, self-adoptability and self-recoverability with unique functionalities. In conclusion, by carefully selected SMMs with well-tailored 4D printing technological and programmable procedures, it is interestingly plausible to obtain improved mechanical properties (i.e. lightweight - specific strength and specific stiffness), tuneable crushing performance (i.e. SEA, EA and CLE) as well as high degree of shape fixity and recoverability.
Disclosure statement
No potential conflict of interest was reported by the authors.
Additional information
Notes on contributors
Chukwuemeke William Isaac
Chukwuemeke William Isaac studied Mechanical Engineering at the University of Ibadan, Nigeria and further obtained a research master's degree in Computational Mechanics at École Centrale de Nantes in 2013. He proceeded to obtain his PhD in Applied Mechanics at the University of Ibadan in 2018. He then worked as a Postdoctoral fellow in the Department of Measurement, Faculty of Automatic Control, Silesian University of Technology (SUT) until 2021. He is currently an Assistant Professor in the Department of Machine Technology, Faculty of Mechanical Engineering, SUT, where he is actively engaged in the research of additively manufactured polymer-based, composite-based, and metal-based energy absorbing structures.
Fabian Duddeck
Fabian Duddeck studied civil engineering at the Technical University of Munich (TUM) finishing with a PhD (1997) and a Habilitation in Mechanics (2001). Then, he worked at BMW/Munich until 2005 when he became Reader of Computational Mechanics at Queen Mary University of London (until 2020). In addition, he was Maître de Conférences at École des Ponts ParisTech (2006–2016). Since 2010, he is professor for Computational Mechanics at TUM leading a research group on optimization of structures for aerospace and automotive problems (e.g., crashworthiness). His group is working on structural optimization, nonlinear model order reduction, isogeometric analysis, uncertainty. propagation, material modeling, crashworthiness, etc.
References
- Abuzaid, W., M. Alkhader, and M. Omari. 2018. “Experimental Analysis of Heterogeneous Shape Recovery in 4d Printed Honeycomb Structures.” Polymer Testing 68: 100–109. doi:10.1016/j.polymertesting.2018.03.050
- Ahmed, A., S. Arya, V. Gupta, H. Furukawa, and A. Khosla. 2021. “4D Printing: Fundamentals,: Materials, Applications and Challenges.” Polymer 228: 123926. doi:10.1016/j.polymer.2021.123926
- Alía, C., J. A. Jofre-Reche, J. C. Suárez, J. M. Arenas, and J. M. Martín-Martínez. 2015. “Influence of Post-Curing Temperature on the Structure,: Properties, and Adhesion of Vinyl Ester Adhesive.” Journal of Adhesion Science and Technology 29 (6): 518–531. doi:10.1080/01694243.2014.995910
- Alomarah, A., S. H. Masood, I. Sbarski, B. Faisal, Z. Gao, and D. Ruan. 2020. “Compressive Properties of 3D Printed Auxetic Structures: Experimental and Numerical Studies.” Virtual and Physical Prototyping 15 (1): 1–21. doi:10.1080/17452759.2019.1644184
- Alshahrani, H. A. 2021. “Review of 4D Printing Materials and Reinforced Composites: Behaviors, Applications and Challenges.” Journal of Science: Advanced Materials and Devices 6 (2): 167–185. doi:10.1016/j.jsamd.2021.03.006
- Al-Ketan, O., R. Rezgui, R. Rowshan, H. Du, N. X. Fang, and R. K. Abu Al-Rub. 2018. “Microarchitected Stretching-Dominated Mechanical Metamaterials with Minimal Surface Topologies.” Advanced Engineering Materials 20 (9): 1800029. doi:10.1002/adem.201800029
- Andrew, J. J., P. Verma, and S. Kumar. 2021. “Impact Behavior of Nanoengineered, 3D Printed Plate-Lattices.” Materials & Design 202: 109516. doi:10.1016/j.matdes.2021.109516
- Barletta, M., A. Gisario, and M. Mehrpouya. 2021. “4D Printing of Shape Memory Polylactic Acid (PLA) Components: Investigating the Role of the Operational Parameters in Fused Deposition Modelling (FDM).” Journal of Manufacturing Processes 61: 473–480. doi:10.1016/j.jmapro.2020.11.036
- Barmouz, M., and A. H. Behravesh. 2017. “Shape Memory Behaviors in Cylindrical Shell PLA/TPU-Cellulose Nanofiber Bio-Nanocomposites: Analytical and Experimental Assessment.” Composites Part A: Applied Science and Manufacturing 101: 160–172. doi:10.1016/j.compositesa.2017.06.014
- Bhanushali, H., S. Amrutkar, S. Mestry, and S. T. Mhaske. 2022. “Shape Memory Polymer Nanocomposite: A Review on Structure–Property Relationship.” Polymer Bulletin 79 (6): 3437–3493. doi:10.1007/s00289-021-03686-x
- Bodaghi, M., A. R. Damanpack, and W. H. Liao. 2016. “Self-expanding/Shrinking Structures by 4D Printing.” Smart Materials and Structures 25 (10): 105034. doi:10.1088/0964-1726/25/10/105034
- Bodaghi, M., A. Serjouei, A. Zolfagharian, M. Fotouhi, H. Rahman, and D. Durand. 2020. “Reversible Energy Absorbing Meta-Sandwiches by FDM 4D Printing.” International Journal of Mechanical Sciences 173: 105451. doi:10.1016/j.ijmecsci.2020.105451
- Chen, K., L. Zhang, X. Kuang, V. Li, M. Lei, G. Kang, Z. L. Wang, and H. J. Qi. 2019. “Dynamic Photomask-assisted Direct ink Writing Multimaterial for Multilevel Triboelectric Nanogenerator.” Advanced Functional Materials 29 (33): 1903568. doi:10.1002/adfm.201903568
- Cheng, Y., J. Li, X. Qian, and S. Rudykh. 2021. “3D Printed Recoverable Honeycomb Composites Reinforced by Continuous Carbon Fibers.” Composite Structures 268: 113974. doi:10.1016/j.compstruct.2021.113974
- Choong, Y. Y. C., S. Maleksaeedi, H. Eng, S. Yu, J. Wei, and P. C. Su. 2020. “High Speed 4D Printing of Shape Memory Polymers with Nanosilica.” Applied Materials Today 18: 100515. doi:10.1016/j.apmt.2019.100515
- Colton, T., C. Inkley, A. Berry, and N. B. Crane. 2021. “Impact of Inkjet Printing Parameters and Environmental Conditions on Formation of 2D and 3D Binder Jetting Geometries.” Journal of Manufacturing Processes 71: 187–196. doi:10.1016/j.jmapro.2021.09.024
- Davami, K., M. Mohsenizadeh, M. Munther, T. Palma, A. Beheshti, and K. Momeni. 2019. “Dynamic Energy Absorption Characteristics of Additively-Manufactured Shape-Recovering Lattice Structures.” Materials Research Express 6 (4): 045302. doi:10.1088/2053-1591/aaf78c
- Davoudinejad, A. 2021. “Vat Photopolymerization Methods in Additive Manufacturing.” In Additive Manufacturing, edited by Juan Pou, Antonio Riveiro, and Paulo J. Davim, 159–181. Amsterdam: Elsevier.
- Ding, H., X. Zhang, Y. Liu, and S. Ramakrishna. 2019. “Review of Mechanisms and Deformation Behaviors in 4D Printing.” The International Journal of Advanced Manufacturing Technology 105 (11): 4633–4649. doi:10.1007/s00170-019-03871-3
- Ding, J., Y. Zhu, and Y. Fu. 2014. “Preparation and Properties of Silanized Vapor-Grown Carbon Nanofibers/Epoxy Shape Memory Nanocomposites.” Polymer Composites 35 (2): 412–417. doi:10.1002/pc.22675
- Dodiuk, H., I. Belinski, A. Dotan, and S. Kenig. 2006. “Polyurethane Adhesives Containing Functionalized Nanoclays.” Journal of Adhesion Science and Technology 20 (12): 1345–1355. doi:10.1163/156856106778456573
- Dong, K., H. Ke, M. Panahi-Sarmad, T. Yang, X. Huang, and X. Xiao. 2021a. “Mechanical Properties and Shape Memory Effect of 4D Printed Cellular Structure Composite with a Novel Continuous Fiber-Reinforced Printing Path.” Materials & Design 198: 109303. doi:10.1016/j.matdes.2020.109303
- Dong, K., M. Panahi-Sarmad, Z. Cui, X. Huang, and X. Xiao. 2021b. “Electro-induced Shape Memory Effect of 4D Printed Auxetic Composite Using PLA/TPU/CNT Filament Embedded Synergistically with Continuous Carbon Fiber: A Theoretical & Experimental Analysis.” Composites Part B: Engineering 220: 108994. doi:10.1016/j.compositesb.2021.108994
- Fakirov, S., F. J. Baltá Calleja, and M. Krumova. 1999. “On the Relationship Between Microhardness and Glass Transition Temperature of Some Amorphous Polymers.” Journal of Polymer Science Part B: Polymer Physics 37 (13): 1413–1419. doi:10.1002/(SICI)1099-0488(19990701)37:13<1413::AID-POLB7>3.0.CO;2-Q
- Fakirov, S., and B. Krasteva. 2000. “On the Glass Transition Temperature of Polyethylene as Revealed by Microhardness Measurements.” Journal of Macromolecular Science, Part B 39 (2): 297–301. doi:10.1081/MB-100100386
- Falahati, M., P. Ahmadvand, S. Safaee, Y. C. Chang, Z. Lyu, R. Chen, L. Li, and Y. Lin. 2020. “Smart Polymers and Nanocomposites for 3D and 4D Printing.” Materials Today 40: 215–245. doi:10.1016/j.mattod.2020.06.001
- Farrokhabadi, A., M. M. Ashrafian, A. H. Behravesh, and S. K. Hedayati. 2022. “Assessment of Fiber-Reinforcement and Foam-Filling in the Directional Energy Absorption Performance of a 3D Printed Accordion Cellular Structure.” Composite Structures 297: 115945. doi:10.1016/j.compstruct.2022.115945
- Fu, P., H. Li, J. Gong, Z. Fan, A. T. Smith, K. Shen, T. O. Khalfalla, et al. 2022. “4D Printing of Polymeric Materials: Techniques,: Materials, and Prospects.” Progress in Polymer Science 126: 101506. doi:10.1016/j.progpolymsci.2022.101506
- Ganilova, O. A., and J. J. Low. 2018. “Application of Smart Honeycomb Structures for Automotive Passive Safety.” Proceedings of the Institution of Mechanical Engineers, Part D: Journal of Automobile Engineering 232 (6): 797–811. doi:10.1177/0954407017708916
- Gao, Q., W. H. Liao, and L. Wang. 2020. “An Analytical Model of Cylindrical Double-Arrowed Honeycomb with Negative Poisson’s Ratio.” International Journal of Mechanical Sciences 173: 105400. doi:10.1016/j.ijmecsci.2019.105400
- Gao, Y., G. Zhu, S. Xu, T. Ma, and J. Nie. 2018. “Biodegradable Magnetic-Sensitive Shape Memory Poly (ε-Caprolactone)/F e3 O 4 Nanocomposites.” Journal of Applied Polymer Science 135 (1): 45652. doi:10.1002/app.45652
- Gogoi, S., and N. Karak. 2016. “Biobased Waterborne Hyperbranched Polyurethane/NiFe 2 O 4@ rGO Nanocomposite with Multi-Stimuli Responsive Shape Memory Attributes.” RSC Advances 6 (97): 94815–94825. doi:10.1039/C6RA16848E
- Habib, F. N., P. Iovenitti, S. H. Masood, and M. Nikzad. 2017. “In-plane Energy Absorption Evaluation of 3D Printed Polymeric Honeycombs.” Virtual and Physical Prototyping 12 (2): 117–131. doi:10.1080/17452759.2017.1291354
- Hamzehei, R., A. Serjouei, N. Wu, A. Zolfagharian, and M. Bodaghi. 2022. “4D Metamaterials with Zero Poisson’s Ratio, Shape Recovery, and Energy Absorption Features.” Advanced Engineering Materials 24 (9): 2200656. doi:10.1002/adem.202200656
- Hassanin, H., A. Abena, M. A. Elsayed, and K. Essa. 2020. “4D Printing of NiTi Auxetic Structure with Improved Ballistic Performance.” Micromachines 11 (8): 745. doi:10.3390/mi11080745
- Hosseinzadeh, M., M. Ghoreishi, and K. Narooei. 2023. “4D Printing of Shape Memory Polylactic Acid Beams: An Experimental Investigation Into FDM Additive Manufacturing Process Parameters,: Mathematical Modeling, and Optimization.” Journal of Manufacturing Processes 85: 774–782. doi:10.1016/j.jmapro.2022.12.006
- Huang, W. 2002. “On the Selection of Shape Memory Alloys for Actuators.” Materials & Design 23 (1): 11–19. doi:10.1016/S0261-3069(01)00039-5
- Huang, W. M., Z. Ding, C. C. Wang, J. Wei, Y. Zhao, and H. Purnawali. 2010. “Shape Memory Materials.” Materials Today 13 (7–8): 54–61. doi:10.1016/S1369-7021(10)70128-0
- Isaac, C. W. 2020. “Crashworthiness Performance of Green Composite Energy Absorbing Structure with Embedded Sensing Device Providing Cleaner Environment for Sustainable Maintenance.” Sustainable Materials and Technologies 25: e00196. doi:10.1016/j.susmat.2020.e00196
- Isaac, C. W., and F. Duddeck. 2022. “Current Trends in Additively Manufactured (3D Printed) Energy Absorbing Structures for Crashworthiness Application–a Review.” Virtual and Physical Prototyping 17 (4): 1058–1101. doi:10.1080/17452759.2022.2074698
- Ji, L., W. Hu, R. Tao, B. Liao, Z. Wan, W. Wu, L. Xi, and D. Fang. 2020. “Compression Behavior of the 4D Printed Reentrant Honeycomb: Experiment and finite Element Analysis.” Smart Materials and Structures 29 (11): 115016. doi:10.1088/1361-665X/ababe4
- Jin, N., F. Wang, Y. Wang, B. Zhang, H. Cheng, and H. Zhang. 2019. “Failure and Energy Absorption Characteristics of Four Lattice Structures Under Dynamic Loading.” Materials & Design 169: 107655. doi:10.1016/j.matdes.2019.107655
- Jing, X., H. Y. Mi, X. F. Peng, and L. S. Turng. 2015. “The Morphology,: Properties, and Shape Memory Behavior of Polylactic Acid/Thermoplastic Polyurethane Blends.” Polymer Engineering & Science 55 (1): 70–80. doi:10.1002/pen.23873
- Johnston, R., and Z. Kazancı. 2021. “Analysis of Additively Manufactured (3D Printed) Dual-Material Auxetic Structures Under Compression.” Additive Manufacturing 38: 101783. doi:10.1016/j.addma.2020.101783
- Joshi, S., K. Rawat, C. Karunakaran, V. Rajamohan, A. T. Mathew, K. Koziol, V. K. Thakur, and A. S. S. Balan. 2020. “4D Printing of Materials for the Future: Opportunities and Challenges.” Applied Materials Today 18: 100490. doi:10.1016/j.apmt.2019.100490
- Kamrava, S., D. Mousanezhad, H. Ebrahimi, R. Ghosh, and A. Vaziri. 2017. “Origami-based Cellular Metamaterial with Auxetic, Bistable, and Self-Locking Properties.” Scientific Reports 7 (1): 1–9. doi:10.1038/srep46046
- Kang, M., Y. Pyo, J. Young Jang, Y. Park, Y. H. Son, M. Choi, J. Wan Ha, Y. W. Chang, and C. S. Lee. 2018. “Design of a Shape Memory Composite (SMC) Using 4D Printing Technology.” Sensors and Actuators A: Physical 283: 187–195. doi:10.1016/j.sna.2018.08.049
- Keramati, M., I. Ghasemi, M. Karrabi, H. Azizi, and M. Sabzi. 2016. “Dispersion of Graphene Nanoplatelets in Polylactic Acid with the Aid of a Zwitterionic Surfactant: Evaluation of the Shape Memory Behavior.” Polymer-Plastics Technology and Engineering 55 (10): 1039–1047. doi:10.1080/03602559.2015.1132458
- Keshavarzan, M., M. Kadkhodaei, and F. Forooghi. 2020. “An Investigation Into Compressive Responses of Shape Memory Polymeric Cellular Lattice Structures Fabricated by Vat Polymerization Additive Manufacturing.” Polymer Testing 91: 106832. doi:10.1016/j.polymertesting.2020.106832
- Khorsandi, D., A. Fahimipour, P. Abasian, S. S. Saber, M. Seyedi, S. Ghanavati, A. Ahmad, et al. 2021. “3D and 4D Printing in Dentistry and Maxillofacial Surgery: Printing Techniques, Materials, and Applications.” Acta Biomaterialia 122: 26–49. doi:10.1016/j.actbio.2020.12.044
- Ko, K., S. Jin, S. E. Lee, and J. W. Hong. 2020. “Impact Resistance of Nacre-like Composites Diversely Patterned by 3D Printing.” Composite Structures 238: 111951. doi:10.1016/j.compstruct.2020.111951
- Konuray, O., A. García, J. M. Morancho, X. Fernández-Francos, À Serra, F. Ferrando, M. García-Alvarez, and X. Ramis. 2019. “Hard Epoxy Thermosets Obtained via Two Sequential Epoxy-Amine Condensations.” European Polymer Journal 116: 222–231. doi:10.1016/j.eurpolymj.2019.04.018
- Köhl, M., M. Bram, A. Moser, H. P. Buchkremer, T. Beck, and D. Stöver. 2011. “Characterization of Porous, Net-Shaped NiTi Alloy Regarding its Damping and Energy-absorbing Capacity.” Materials Science and Engineering: A 528 (6): 2454–2462. doi:10.1016/j.msea.2010.11.055
- Lee, A. Y., J. An, and C. K. Chua. 2017. “Two-way 4D Printing: A Review on the Reversibility of 3D-Printed Shape Memory Materials.” Engineering 3 (5): 663–674. doi:10.1016/J.ENG.2017.05.014
- Lee, S. G., J. H. Lee, K. Y. Choi, and J. M. Rhee. 1998. “Glass Transition Behavior of Polypropylene/Polystyrene/Styrene-Ethylene-Propylene Block Copolymer Blends.” Polymer Bulletin 40 (6): 765–771. doi:10.1007/s002890050320
- Li, P., Y. Han, W. Wang, Y. Liu, P. Jin, and J. Leng. 2017. “Novel Programmable Shape Memory Polystyrene Film: A Thermally Induced Beam-Power Splitter.” Scientific Reports 7 (1): 1–10. doi:10.1038/s41598-016-0028-x
- Li, F., X. Ji, Z. Wu, C. Qi, Q. Xian, and B. Sun. 2020. “Digital Light Processing 3D Printing of Ceramic Shell for Precision Casting.” Materials Letters 276: 128037. doi:10.1016/j.matlet.2020.128037
- Li, X., X. Yu, J. W. Chua, H. P. Lee, J. Ding, and W. Zhai. 2021. “Microlattice Metamaterials with Simultaneous Superior Acoustic and Mechanical Energy Absorption.” Small 17 (24): 2100336. doi:10.1002/smll.202100336
- Li, Q., X. Zhi, and F. Fan. 2022. “Quasi-static Compressive Behaviour of 3D-Printed Origami-Inspired Cellular Structure: Experimental, Numerical and Theoretical Studies.” Virtual and Physical Prototyping 17 (1): 69–91. doi:10.1080/17452759.2021.1987051
- Lin, K., D. Gu, K. Hu, J. Yang, H. Wang, L. Yuan, X. Shi, and L. Meng. 2021. “Laser Powder Bed Fusion of Bio-inspired Honeycomb Structures: Effect of Twist Angle on Compressive Behaviors.” Thin-Walled Structures 159: 107252. doi:10.1016/j.tws.2020.107252
- Lin, Z., L. S. Novelino, H. Wei, N. A. Alderete, G. H. Paulino, H. D. Espinosa, and S. Krishnaswamy. 2020. “Folding at the Microscale: Enabling Multifunctional 3D Origami-Architected Metamaterials.” Small 16 (35): 2002229. doi:10.1002/smll.202002229
- Liu, K., L. Han, W. Hu, L. Ji, S. Zhu, Z. Wan, X. Yang, et al. 2020. “4D Printed Zero Poisson’s Ratio Metamaterial with Switching Function of Mechanical and Vibration Isolation Performance.” Materials & Design 196: 109153. doi:10.1016/j.matdes.2020.109153
- Liu, Z., W. Liu, and W. Ma. 2022. “Investigation of Design and Self-recovery Characteristics of Multicellular Energy-Absorbing Structures Manufactured via Laser Powder Bed Fusion.” AIP Advances 12 (7): 075201. doi:10.1063/5.0098507
- Liu, H., F. Wang, W. Wu, X. Dong, and L. Sang. 2023. “4D Printing of Mechanically Robust PLA/TPU/Fe3O4 Magneto-Responsive Shape Memory Polymers for Smart Structures.” Composites Part B: Engineering 248: 110382. doi:10.1016/j.compositesb.2022.110382
- Liu, Y., W. Zhang, F. Zhang, X. Lan, J. Leng, S. Liu, X. Jia, et al. 2018. “Shape Memory Behavior and Recovery Force of 4D Printed Laminated Miura-Origami Structures Subjected to Compressive Loading.” Composites Part B: Engineering 153: 233–242. doi:10.1016/j.compositesb.2018.07.053
- Logakannan, K. P., V. Ramachandran, J. Rengaswamy, and D. Ruan. 2020. “Dynamic Performance of a 3D re-Entrant Structure.” Mechanics of Materials 148: 103503. doi:10.1016/j.mechmat.2020.103503
- Lu, H. Z., C. Yang, X. Luo, H. W. Ma, B. Song, Y. Y. Li, and L. C. Zhang. 2019. “Ultrahigh-performance TiNi Shape Memory Alloy by 4D Printing.” Materials Science and Engineering: A 763: 138166. doi:10.1016/j.msea.2019.138166
- Luo, L., F. Zhang, and J. Leng. 2021. “Multi-performance Shape Memory Epoxy Resins and Their Composites with Narrow Transition Temperature Range.” Composites Science and Technology 213: 108899. doi:10.1016/j.compscitech.2021.108899
- Ma, S. C., H. L. Lin, and T. L. Yu. 1993. “Glass Transition Temperature, Free Volume, and Curing Kinetics of Unsaturated Polyester.” Polymer Journal 25 (9): 897–907. doi:10.1295/polymj.25.897
- Magazine, R., B. van Bochove, S. Borandeh, and J. Seppälä. 2022. “3D Inkjet-Printing of Photo-Crosslinkable Resins for Microlens Fabrication.” Additive Manufacturing 50: 102534. doi:10.1016/j.addma.2021.102534
- Manthiram, A., X. Zhao, and W. Li. 2012. “Developments in Membranes, Catalysts and Membrane Electrode Assemblies for Direct Methanol Fuel Cells (DMFCs).” In Functional Materials for Sustainable Energy Applications, edited by John A. Kilner, Stephen J. Skinner, Stuart J. C. Irvine, and Peter P. Edwards, 312–369. Philadelphia: Woodhead.
- Mehrpouya, M., T. Edelijn, M. Ibrahim, A. Mohebshahedin, A. Gisario, and M. Barletta. 2022. “Functional Behavior and Energy Absorption Characteristics of Additively Manufactured Smart Sandwich Structures.” Advanced Engineering Materials 24 (9): 2200677. doi:10.1002/adem.202200677
- Mehrpouya, M., A. Gisario, A. Azizi, and M. Barletta. 2020. “Investigation on Shape Recovery of 3D Printed Honeycomb Sandwich Structure.” Polymers for Advanced Technologies 31 (12): 3361–3365. doi:10.1002/pat.5020
- Mehrpouya, M., H. Vahabi, S. Janbaz, A. Darafsheh, T. R. Mazur, and S. Ramakrishna. 2021. “4D Printing of Shape Memory Polylactic Acid (PLA).” Polymer 230: 124080. doi:10.1016/j.polymer.2021.124080
- Moon, J., J. Choi, and M. Cho. 2016. “Programmed Shape-Dependence of Shape Memory Effect of Oriented Polystyrene: A Molecular Dynamics Study.” Polymer 102: 1–9. doi:10.1016/j.polymer.2016.08.096
- Namvar, N., A. Zolfagharian, F. Vakili-Tahami, and M. Bodaghi. 2022. “Reversible Energy Absorption of Elasto-Plastic Auxetic, Hexagonal, and AuxHex Structures Fabricated by FDM 4D Printing.” Smart Materials and Structures 31 (5): 055021. doi:10.1088/1361-665X/ac6291
- Nasrullah, A. I. H., S. P. Santosa, and T. Dirgantara. 2020. “Design and Optimization of Crashworthy Components Based on Lattice Structure Configuration.” Structures 26: 969–981. doi:10.1016/j.istruc.2020.05.001
- Ohki, T., Q. Q. Ni, N. Ohsako, and M. Iwamoto. 2004. “Mechanical and Shape Memory Behavior of Composites with Shape Memory Polymer.” Composites Part A: Applied Science and Manufacturing 35 (9): 1065–1073. doi:10.1016/j.compositesa.2004.03.001
- Otsuka, K., and X. Ren. 1999. “Recent Developments in the Research of Shape Memory Alloys.” Intermetallics 7 (5): 511–528. doi:10.1016/S0966-9795(98)00070-3
- Ouyang, H., X. Li, X. Lu, and H. Xia. 2022. “Selective Laser Sintering 4D Printing of Dynamic Cross-linked Polyurethane Containing Diels–Alder Bonds.” ACS Applied Polymer Materials 4 (5): 4035–4046. doi:10.1021/acsapm.2c00565
- Pasini, C., N. Inverardi, D. Battini, G. Scalet, S. Marconi, F. Auricchio, and S. Pandini. 2022. “Experimental Investigation and Modeling of the Temperature Memory Effect in a 4D-Printed Auxetic Structure.” Smart Materials and Structures 31 (9): 095021. doi:10.1088/1361-665X/ac8031
- Patil, A. N., and S. H. Sarje. 2021. “Additive Manufacturing with Shape Changing/Memory Materials: A Review on 4D Printing Technology.” Materials Today: Proceedings 44: 1744–1749. doi:10.1016/j.matpr.2020.11.907
- Peng, X., X. Kuang, D. J. Roach, Y. Wang, C. M. Hamel, C. Lu, and H. J. Qi. 2021. “Integrating Digital Light Processing with Direct Ink Writing for Hybrid 3D Printing of Functional Structures and Devices.” Additive Manufacturing 40: 101911. doi:10.1016/j.addma.2021.101911
- Pirhaji, A., E. Jebellat, N. Roudbarian, K. Mohammadi, M. R. Movahhedy, and M. A. Zaeem. 2022. “Large Deformation of Shape-Memory Polymer-based Lattice Metamaterials.” International Journal of Mechanical Sciences 232: 07593. doi:10.1016/j.ijmecsci.2022.107593
- Quanjin, M., M. R. M. Rejab, M. S. Idris, N. M. Kumar, M. H. Abdullah, and G. R. Reddy. 2020. “Recent 3D and 4D Intelligent Printing Technologies: A Comparative Review and Future Perspective.” Procedia Computer Science 167: 1210–1219. doi:10.1016/j.procs.2020.03.434
- Rahmatabadi, D., M. Aberoumand, K. Soltanmohammadi, E. Soleyman, I. Ghasemi, M. Baniassadi, K. Abrinia, M. Bodaghi, and M. Baghani. 2022. “4D Printing Encapsulated Polycaprolactone-Thermoplastic Polyurethane with High Shape Memory Performances.” Advanced Engineering Materials 25: 2201309. doi:10.1002/adem.20220130
- Razzaq, M. Y., J. Gonzalez-Gutierrez, G. Mertz, D. Ruch, D. F. Schmidt, and S. Westermann. 2022. “4D Printing of Multicomponent Shape-Memory Polymer Formulations.” Applied Sciences 12 (15): 7880. doi:10.3390/app12157880
- Rocha, V. G., E. Saiz, I. S. Tirichenko, and E. García-Tuñón. 2020. “Direct Ink Writing Advances in Multi-material Structures for a Sustainable Future.” Journal of Materials Chemistry A 8 (31): 15646–15657. doi:10.1039/D0TA04181E
- Romanova, N., L. Shafigullin, A. Gabdrakhmanov, and S. Buyatova. 2019. “Thermal Properties of Products Based on ABS/PC.” In MATEC Web of Conferences (Vol. 298, p. 00016). EDP Sciences.
- Roudbarian, N., E. Jebellat, S. Famouri, M. Baniasadi, R. Hedayati, and M. Baghani. 2022. “Shape-memory Polymer Metamaterials Based on Triply Periodic Minimal Surfaces.” European Journal of Mechanics-A/Solids 96: 104676.
- Sanchez, E. M. S., C. A. C. Zavaglia, and M. I. Felisberti. 2000. “Unsaturated Polyester Resins: Influence of the Styrene Concentration on the Miscibility and Mechanical Properties.” Polymer 41 (2): 765–769. doi:10.1016/S0032-3861(99)00184-6
- Serjouei, A., A. Yousefi, A. Jenaki, M. Bodaghi, and M. Mehrpouya. 2022. “4D Printed Shape Memory Sandwich Structures: Experimental Analysis and Numerical Modeling.” Smart Materials and Structures 31 (5): 055014. doi:10.1088/1361-665X/ac60b5
- Sharma, D., and S. S. Hiremath. 2022. “Bio-inspired Repeatable Lattice Structures for Energy Absorption: Experimental and Finite Element Study.” Composite Structures 283: 115102. doi:10.1016/j.compstruct.2021.115102
- Sterzyński, T., J. Tomaszewska, K. Piszczek, and K. Skórczewska. 2010. “The Influence of Carbon Nanotubes on the PVC Glass Transition Temperature.” Composites Science and Technology 70 (6): 966–969. doi:10.1016/j.compscitech.2010.02.013
- Sun, L., W. M. Huang, Z. Ding, Y. Zhao, C. C. Wang, H. Purnawali, and C. Tang. 2012. “Stimulus-responsive Shape Memory Materials: A Review.” Materials & Design 33: 577–640. doi:10.1016/j.matdes.2011.04.065
- Sun, Y. C., Y. Wan, R. Nam, M. Chu, and H. E. Naguib. 2019. “4D-printed Hybrids with Localized Shape Memory Behaviour: Implementation in a Functionally Graded Structure.” Scientific Reports 9 (1): 1–13. doi:10.1038/s41598-018-37186-2
- Tan, X., S. Chen, S. Zhu, B. Wang, P. Xu, K. Yao, and Y. Sun. 2019. “Reusable Metamaterial via Inelastic Instability for Energy Absorption.” International Journal of Mechanical Sciences 155 (2019): 509–517. doi:10.1016/j.ijmecsci.2019.02.011
- Tao, R., L. Ji, Y. Li, Z. Wan, W. Hu, W. Wu, B. Liao, L. Ma, and D. Fang. 2020a. “4D Printed Origami Metamaterials with Tunable Compression Twist Behavior and Stress-Strain Curves.” Composites Part B: Engineering 201: 108344. doi:10.1016/j.compositesb.2020.108344
- Tao, R., L. Xi, W. Wu, Y. Li, B. Liao, L. Liu, J. Leng, and D. Fang. 2020b. “4D Printed Multi-Stable Metamaterials with Mechanically Tunable Performance.” Composite Structures 252: 112663. doi:10.1016/j.compstruct.2020.112663
- Teoh, J. E. M., J. An, X. Feng, Y. Zhao, C. K. Chua, and Y. Liu. 2018. “Design and 4D Printing of Cross-folded Origami Structures: A Preliminary Investigation.” Materials 11 (3): 376. doi:10.3390/ma11030376
- Tobushi, H., E. Pieczyska, Y. Ejiri, and T. Sakuragi. 2009. “Thermomechanical Properties of Shape-Memory Alloy and Polymer and Their Composites.” Mechanics of Advanced Materials and Structures 16 (3): 236–247. doi:10.1080/15376490902746954
- Townsend, S., R. Adams, M. Robinson, B. Hanna, and P. Theobald. 2020. “3D Printed Origami Honeycombs with Tailored out-of-Plane Energy Absorption Behavior.” Materials & Design 195: 108930. doi:10.1016/j.matdes.2020.108930
- Usta, F., H. S. Türkmen, and F. Scarpa. 2021. “Low-velocity Impact Resistance of Composite Sandwich Panels with Various Types of Auxetic and non-Auxetic Core Structures.” Thin-Walled Structures 163: 107738. doi:10.1016/j.tws.2021.107738
- van Manen, T., S. Janbaz, K. Jansen, and A. A. Zadpoor. 2021. “4D Printing of Reconfigurable Metamaterials and Devices.” Communications Materials 2 (1): 1–8. doi:10.1038/s43246-021-00165-8
- Wan, X., L. Luo, Y. Liu, and J. Leng. 2020. “Direct ink Writing Based 4D Printing of Materials and Their Applications.” Advanced Science 7 (16): 2001000. doi:10.1002/advs.202001000
- Wan, M., K. Yu, and H. Sun. 2022. “4D Printed Programmable Auxetic Metamaterials with Shape Memory Effects.” Composite Structures 279: 114791. doi:10.1016/j.compstruct.2021.114791
- Wang, C. Y., and M. D. Ediger. 2000. “Spatially Heterogeneous Dynamics in Thermoset Resins Below the Glass-Transition Temperature.” Journal of Polymer Science Part B: Polymer Physics 38 (17): 2232–2239. doi:10.1002/1099-0488(20000901)38:17<2132::AID-POLB30>3.0.CO;2-J
- Wang, C. C., W. M. Huang, Z. Ding, Y. Zhao, and H. Purnawali. 2012. “Cooling-/water-responsive Shape Memory Hybrids.” Composites Science and Technology 72 (10): 1178–1182. doi:10.1016/j.compscitech.2012.03.027
- Wang, Y., and X. Li. 2020. “An Accurate Finite Element Approach for Programming 4D-Printed Self-morphing Structures Produced by Fused Deposition Modeling.” Mechanics of Materials 151: 103628. doi:10.1016/j.mechmat.2020.103628
- Wang, Z., C. Luan, G. Liao, J. Liu, X. Yao, and J. Fu. 2020. “Progress in Auxetic Mechanical Metamaterials: Structures, Characteristics, Manufacturing Methods, and Applications.” Advanced Engineering Materials 22 (10): 2000312. doi:10.1002/adem.202000312
- Wu, Y., L. Sun, P. Yang, J. Fang, and W. Li. 2021. “Energy Absorption of Additively Manufactured Functionally Bi-graded Thickness Honeycombs Subjected to Axial Loads.” Thin-Walled Structures 164: 107810. doi:10.1016/j.tws.2021.107810
- Wu, H., O. Wang, Y. Tian, M. Wang, B. Su, C. Yan, K. Zhou, and Y. Shi. 2020. “Selective Laser Sintering-Based 4D Printing of Magnetism-Responsive Grippers.” ACS Applied Materials & Interfaces 13 (11): 12679–12688. doi:10.1021/acsami.0c17429
- Wu, J., Z. Zhao, X. Kuang, C. M. Hamel, D. Fang, and H. J. Qi. 2018. “Reversible Shape Change Structures by Grayscale Pattern 4D Printing.” Multifunctional Materials 1 (1): 015002. doi:10.1088/2399-7532/aac322
- Xia, Y., Y. He, F. Zhang, Y. Liu, and J. Leng. 2021. “A Review of Shape Memory Polymers and Composites: Mechanisms,: Materials, and Applications.” Advanced Materials 33 (6): 2000713. doi:10.1002/adma.202000713
- Xiao, X., D. Kong, X. Qiu, W. Zhang, Y. Liu, S. Zhang, F. Zhang, Y. Hu, and J. Leng. 2015. “Shape Memory Polymers with High and low Temperature Resistant Properties.” Scientific Reports 5 (1): 1–12. doi:10.9734/JSRR/2015/14076
- Xie, F., L. Huang, J. Leng, and Y. Liu. 2016. “Thermoset Shape Memory Polymers and Their Composites.” Journal of Intelligent Material Systems and Structures 27 (18): 2433–2455. doi:10.1177/1045389X16634211
- Xin, X., L. Liu, Y. Liu, and J. Leng. 2020. “4D Printing Auxetic Metamaterials with Tunable,: Programmable, and Reconfigurable Mechanical Properties.” Advanced Functional Materials 30 (43): 2004226. doi:10.1002/adfm.202004226
- Xiong, Z., M. Li, S. Hao, Y. Liu, L. Cui, H. Yang, C. Cui, et al. 2021. “3D-printing Damage-Tolerant Architected Metallic Materials with Shape Recoverability via Special Deformation Design of Constituent Material.” ACS Applied Materials & Interfaces 13 (33): 39915–39924. doi:10.1021/acsami.1c11226
- Xiong, Z., Z. Li, Z. Sun, S. Hao, Y. Yang, M. Li, C. Song, P. Qiu, and L. Cui. 2019. “Selective Laser Melting of NiTi Alloy with Superior Tensile Property and Shape Memory Effect.” Journal of Materials Science & Technology 35 (10): 2238–2242. doi:10.1016/j.jmst.2019.05.015
- Yang, C., M. Boorugu, A. Dopp, J. Ren, R. Martin, D. Han, W. Choi, and H. Lee. 2019. “4D Printing Reconfigurable, Deployable and Mechanically Tunable Metamaterials.” Materials Horizons 6 (6): 1244–1250. doi:10.1039/C9MH00302A
- Yang, H., and L. Ma. 2019. “Multi-stable Mechanical Metamaterials by Elastic Buckling Instability.” Journal of Materials Science 54: 3509–3526. doi:10.1007/s10853-018-3065-y
- Yang, K., S. Xu, S. Zhou, and Y. M. Xie. 2018. “Multi-objective Optimization of Multi-Cell Tubes with Origami Patterns for Energy Absorption.” Thin-Walled Structures 123: 100–113. doi:10.1016/j.tws.2017.11.005
- Yasuda, H., and J. Yang. 2015. “Reentrant Origami-Based Metamaterials with Negative Poisson’s Ratio and Bistability.” Physical Review Letters 114 (18): 185502. doi:10.1103/PhysRevLett.114.185502
- Yousefi, A., S. Jolaiy, M. Lalegani Dezaki, A. Zolfagharian, A. Serjouei, and M. Bodaghi. 2022. “3D-Printed Soft and Hard Meta-Structures with Supreme Energy Absorption and Dissipation Capacities in Cyclic Loading Conditions.” Advanced Engineering Materials 25 (4): 2201189.
- Yuan, S., F. Shen, J. Bai, C. K. Chua, J. Wei, and K. Zhou. 2017. “3D Soft Auxetic Lattice Structures Fabricated by Selective Laser Sintering: TPU powder Evaluation and Process Optimization.” Materials & Design 120: 317–327. doi:10.1016/j.matdes.2017.01.098
- Yue, C., M. Li, Y. Liu, Y. Fang, Y. Song, M. Xu, and J. Li. 2021. “Three-dimensional Printing of Cellulose Nanofibers Reinforced PHB/PCL/Fe3O4 Magneto-Responsive Shape Memory Polymer Composites with Excellent Mechanical Properties.” Additive Manufacturing 46: 102146. doi:10.1016/j.addma.2021.102146
- Zafar, M. Q., and H. Zhao. 2020. “4D Printing: Future Insight in Additive Manufacturing.” Metals and Materials International 26 (5): 564–585. doi:10.1007/s12540-019-00441-w
- Zeng, C., L. Liu, W. Bian, J. Leng, and Y. Liu. 2022. “Temperature-dependent Mechanical Response of 4D Printed Composite Lattice Structures Reinforced by Continuous Fiber.” Composite Structures 280: 114952. doi:10.1016/j.compstruct.2021.114952
- Zhang, Z., K. G. Demir, and G. X. Gu. 2019. “Developments in 4D-Printing: A Review on Current Smart Materials, Technologies, and Applications.” International Journal of Smart and Nano Materials 10 (3): 205–224. doi:10.1080/19475411.2019.1591541
- Zhang, J., H. Huang, G. Liu, H. Zong, and C. Zhang. 2021. “Stiffness and Energy Absorption of Additive Manufactured Hybrid Lattice Structures.” Virtual and Physical Prototyping 16 (4): 428–443. doi:10.1080/17452759.2021.1954405
- Zhang, J., G. Lu, and Z. You. 2020. “Large Deformation and Energy Absorption of Additively Manufactured Auxetic Materials and Structures: A Review.” Composites Part B: Engineering 201: 108340. doi:10.1016/j.compositesb.2020.108340
- Zhao, T., R. Yu, X. Li, B. Cheng, Y. Zhang, X. Yang, X. Zhao, Y. Zhao, and W. Huang. 2018. “4D Printing of Shape Memory Polyurethane via Stereolithography.” European Polymer Journal 101: 120–126. doi:10.1016/j.eurpolymj.2018.02.021
- Zhao, W., C. Yue, L. Liu, J. Leng, and Y. Liu. 2023. “Mechanical Behavior Analyses of 4D Printed Metamaterials Structures with Excellent Energy Absorption Ability.” Composite Structures 304: 116360. doi:10.1016/j.compstruct.2022.116360
- Zhou, J., X. Deng, Y. Yan, X. Chen, and Y. Liu. 2015. “Superelasticity and Reversible Energy Absorption of Polyurethane Cellular Structures with Sand Filler.” Composite Structures 131: 966–974. doi:10.1016/j.compstruct.2015.06.059
- Zhou, Y., Y. Yang, A. Jian, T. Zhou, G. Tao, L. Ren, J. Zang, and Z. Zhang. 2022. “Co-extrusion 4D Printing of Shape Memory Polymers with Continuous Metallic Fibers for Selective Deformation.” Composites Science and Technology 227: 109603. doi:10.1016/j.compscitech.2022.109603
- Zolfagharian, A., A. Kaynak, S. Y. Khoo, and A. Kouzani. 2018. “Pattern-Driven 4D Printing.” Sensors and Actuators A: Physical 274: 231–243. doi:10.1016/j.sna.2018.03.034