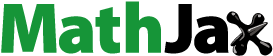
ABSTRACT
A material-structure integrated design method is proposed in this paper, with which micropillar and microwedge arrayed surfaces are fabricated based on a novel nanoparticle-reinforced silicone rubber composite (NRSRC) with high mechanical strength and strong surface adhesion. It is found that the micropillar-arrayed surface and the microwedge-arrayed surface show a normal adhesive strength of 50.9 kPa and a shear adhesive strength of 137.3 kPa, respectively, which are much higher than those of previously reported adhesive surfaces made by pure soft polymers. Furthermore, the microwedge-arrayed surface shows not only strong and stable adhesion on rough and smooth substrates but also an obvious anisotropy in the adhesion property. The latter consequently leads to an easy control of the attachment/detachment switch, which is evidenced by a mechanical gripper with a microwedged surface. Therefore, firmly picking up and easily releasing a heavy glass plate can be realized. All these results demonstrate the apparent advantages of the present composite-based fibrillar surfaces in achieving reliable and reversible adhesion and should have promising applications for manufacturing advanced adhesive devices, such as mechanical fixtures, portable climbing equipment and space robots.
Graphical Abstract
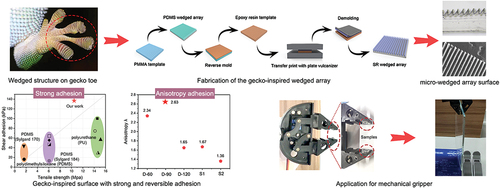
1. Introduction
Geckos have evolved fibrillar structures on their feet to achieve not only firm adhesion on the vertical wall or even ceiling but also an exceptional ability to quickly attach to and detach from solid surfaces. Such a strong and reversible adhesive performance has attracted much interest from bionic researchers. The strong adhesion of the gecko is attributed to the accumulation of van der Waals forces generated by the hierarchical fibrillar structures [Citation1,Citation2], while the easy transition between attachment and detachment is due to the strong anisotropy in the adhesive property of fibrillar structures [Citation3,Citation4]. Inspired by these mechanisms, many efforts have been made to fabricate gecko-mimicking fibrillar surfaces with specific adhesive functions, which should have tremendous potential applications in medical devices, climbing equipment, space robots and so on [Citation5–7].
In the fabrication of gecko-inspired adhesive surfaces, soft polymers such as polydimethylsiloxane (PDMS) are always used as base materials due to their easy processing, high deformability, and softness, which is analogous to outer skin tissues. According to the geometry of the fibrillar structure consisting of millions of microscale setae, micropillar arrays are commonly constructed on soft polymers using photolithography or 3D printing technologies [Citation8]. Cylindrical micropillars with flat tips are the easiest-processed structure, but may lead to a lower adhesion of the surface than those of the flat surface on a smooth substrate [Citation8–12]. For example, the adhesion strength of flat PDMS surfaces is normally lower than 10 kPa, which is higher than that of many previously-reported microstructured PDMS surfaces [Citation11,Citation13–15]. As yet, many literatures were focused on not only the adhesion mechanism but also the practical applications of cylindrical micropillar surfaces. The micropillar surfaces have found successful applications in many aspects, such as forming low-cost mass preparation technology, improving the macro adhesion strength, and the designing of gripper structure. Increasing the aspect ratio or decreasing the diameter of cylindrical pillar may result in stronger adhesion than that of a flat surface [Citation9,Citation16], which remains a challenging task in practice due to the difficulty in demolding and easy collapse or bunching of slender micropillars [Citation9,Citation17].
Inspired by the spatula-shaped terminal of gecko setae, attentions have been given to tuning the tip shape of micropillars to improve the adhesion property of micropillar-arrayed surfaces. A group of investigators found that the mushroom-like tip could lead to a much stronger normal adhesion than the flat, spherical and concave tips [Citation18–20]. Subsequent studies reported that adhesive surfaces with mushroom-like pillar arrays show approximately twice the normal pull-off force of that of the flat surface [Citation21,Citation22]. Murphy et al. [Citation23] further fabricated three-level fibrillar surfaces with mushroom-shaped tips, which showed much improved adhesive strength and adhesive energy compared with those of a single-level structured surface. Such a significant enhancing effect can be attributed to not only the larger contact area between the mushroom-like pillars and the substrate but also the reduction in the stress concentration at the contact perimeter, which could help to inhibit crack initiation [Citation22,Citation24,Citation25]. To date, it has been well recognized that mushroom-shaped micropillars can lead to outstanding adhesive properties in the normal direction of gecko-inspired surfaces, which should be very useful for passive and static adhesion cases requiring long-term attachment [Citation10,Citation26], e.g. smooth object graspers and medical patches.
Microscopic observations have found that the fibrillar tissue on the gecko’s foot is a kind of asymmetric structure, which enables the gecko to possess an anisotropically adhesive system that is responsible for its reversible adhesion ability [Citation26,Citation27]. Inspired by this structure–function relationship, a microwedge-arrayed surface structure was prepared, which experiences bending deformation under a tangential load so that directional adhesion can be realized by controlling the contact area. Parness et al. [Citation28] constructed such a microwedge structure on the PDMS surface to achieve a high shear adhesive strength of 17 kPa in a preferred direction and a low counterpart of 10 kPa in the oppositely anti-preferred direction. Tao et al. [Citation29] used ultraprecision diamond cutting technology to prepare a microwedge-arrayed adhesive surface, which showed significantly different normal and shear adhesive strengths in opposite directions. Zhou et al. [Citation26], Day et al. [Citation30] and Simaite et al. [Citation31] conducted similar research to obtain strong and weak shear adhesive strengths in opposite directions of the microwedge structured surface.
Although great progress has been made in the research of gecko-mimicking adhesive surfaces, more robust adhesion and an easier switch between attached and detached states remain goals that are worthy of pursuit in this field. These two functions are closely related to not only material properties but also structural characteristics such as the size, shape and spacing of structure elements [Citation32]. Therefore, a material-structure integrated design should be a feasible way to achieve superior adhesion performance. However, previous designs of gecko-mimicking fibrillar surfaces were mainly focused on the construction of microstructures, possibly leading to a limited improvement of adhesive performance since the material property was not fully exploited.
To date, pure soft polymers have been commonly used as base materials to construct gecko-type fibrillar structures. Their low modulus enables the structure elements to easily bend to increase the contact area but may simultaneously cause collapse of the elements. Furthermore, the low strength of soft polymers could cause a break of the structural elements or even the whole surface during the loading process, leading to a malfunction of the adhesive surface. Particularly, some preferable elastomers for fabricating fibrillar adhesive surfaces, e.g. the commercially available PDMS product, possess a low surface energy in addition to poor mechanical properties [Citation13,Citation15,Citation33–35]. This material property facilitates the demolding and curing processes of microstructured surfaces but severely limits the improvement of the surface adhesion. To address these problems, modifications of soft polymers are necessary to improve the mechanical properties and adhesive properties of the base materials while retaining their superior flexibility. Unfortunately, little attention has been given to this issue in existing research on gecko-inspired adhesive surfaces.
Recently, a bulk modification method for silicone rubber has been developed to prepare a nanoparticle-reinforced silicone rubber composite (NRSRC) integrating high strength, strong adhesion and excellent flexibility [Citation36]. This silicone rubber composite is further used as a base material to fabricate gecko-mimicking fibrillar surfaces. Cylindrical micropillar and microwedge arrays are constructed on the NRSRC. The adhesive properties of the corresponding microstructured surfaces are measured, and the effects of pillar diameter, wedge spacing and substrate roughness on the adhesion performance are investigated to find the optimal structure patterns. Comparisons between adhesive properties of the composite-based surfaces and those of existing adhesive surfaces made by pure polymers, as well as a practical application of the micro-wedged-arrayed surface in a mechanical gripper, are finally provided to show the advantage of the present adhesive surface based on a material-structure integrated design.
2. Sample preparation and instruments
2.1 Materials and instruments
A NRSRC with high strength and strong adhesion, which is prepared by a bulk modification of the silicone rubber with surface modified nano-silica and silicon adhesion promoter [Citation36], is used as a base material of the present fibrillar surfaces. The tensile strength and elongation of such NRSRC material can reach up to 10.4 MPa and 591%, respectively, and the Yong’s modulus is 5.07 MPa. Due to the use of nano-silica and silicone adhesion promoter, the viscoelasticity of the NRSRC is much higher than that of the commercially available PDMS product (Sylgard 184). The surface energy of the NRSRC is the same as that of PDMS base material since no surface modification is involved in the fabrication of the composite. The outstanding surface adhesion of the NRSRC material is attributed to the formation of hydrogen bonding between the surface and the substrate, which is originate from the active hydroxy groups contained in the NRSRC. In the fabrication of NRSRC materials, the silicone adhesion promoter consisting of hydroxy terminated PDMS chains is firstly synthesized and then added into the NRSRC crosslinking network. When the NRSRC material adhere to a substrate, the molecular chains containing hydroxy groups will gradually diffused into the contact interface, and the hydrogen bonding gradually forms with the increase of time. Detailed information about the fabrication method and material properties of the NRSRC is provided in the Supplementary Material.
The PDMS elastomer (Sylgard 184) and epoxy resin (E-51), which were purchased from the Dow Corning company and Shandong Yusuo Chemical Technology Co., LTD, respectively, are used to prepare the template of fibrillar surfaces with micropillar or microwedge structures. Commercially available 1 H,1 H,2 H,2 H-perfluorodecyltriethoxysilane (C16H19F17O3Si) and ethanol are used as surface modifiers for the template to avoid adhesion during demolding.
The pull-off test setup to measure the normal adhesive strength of micropillar structured surfaces is shown in ), which mainly consists of a glass disc probe and a 0–500 g load cell (GSO-500, Transducer Techniques). A micropillar-arrayed surface sample with an area of 5 mm 5 mm is attached to a glass substrate under a pre-pressure, and the pre-pressure is removed when the sample firmly adheres to the substrate. During the test, the glass disc probe moves downward slowly to approach and contact the sample. After the applied force reaches a preset pressure, the probe starts to retract until it completely separates from the sample. The contact force at the separation between the probe and sample is recorded, which is divided by the sample area (apparent area, here is 5 mm
5 mm) to obtain the normal adhesive strength. The moving speed of the probe is kept at 25 μm/s, and the normal adhesive strengths for different preset pressures are measured.
Figure 1. Experimental setups of (a) the normal adhesion test of micropillar-arrayed surfaces (left: schematics; right: image) and (b) the shear adhesion test of microwedge-arrayed surfaces.
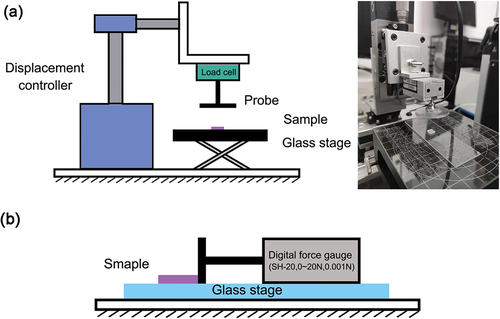
The shear adhesive strength of the microwedge-arrayed surfaces is measured by a digital force gauge (SH-20, HANDPI, 0 ~ 20 N, 0.001) equipped with a panel probe, as shown in ). The area of the microwedged surface sample is also taken as 5 mm 5 mm. A normal pre-pressure is applied on the sample by hand, which is removed when the sample firmly adheres to the substrate. Following this step, a shear force is applied to the sample by pushing the force gauge and the test starts. When the sample debonds from the substrate, the maximum shear force is recorded, which is also divided by the apparent sample area to obtain the shear adhesive strength. To evaluate the anisotropic adhesion performance of the microwedge-arrayed surface, pushing forces along two opposite directions are applied. For a given microwedged surface, the direction to obtain a stronger shear adhesion is named the preferred direction, while its opposite counterpart is named the anti-preferred direction.
The morphologies of the micropillar-arrayed and microwedge-arrayed surfaces are inspected by scanning electron microscopy (SEM, type: Supra 55, Zeiss, Germany), and the roughness profiles of the frosted glass substrates are observed and characterized with laser scanning confocal microscopy (LSCM, LEXT OLS5100, Olympus).
2.2 Fabrication of composite-based fibrillar surface samples
The fabrication of micropillar-arrayed surface samples is schematically illustrated in ). Silicon wafer templates with microhole arrays of 20, 30, 40 and 50 μm in diameter are firstly prepared via a photolithography technique, in which the hole depth and the spacing between two adjacent holes are fixed to be 20 μm and 10 μm, respectively. These templates are immersed in a 1% perfluorosilane ethanol solution for 2 hours and then dried in an oven at 105°C for 1 hour to avoid adhesion between the templates and samples during demolding. The PDMS mixed with a crosslinker at a weight ratio of 10% is poured onto the treated silicon wafer template to produce micropillar arrays with flat tips [Citation34]. Such PDMS arrays are then covered by epoxy resins and cured at 150°C for 10 minutes to produce an epoxy resin template, which is also immersed in 1% perfluorosilane ethanol solution for 2 hours. Subsequently, the epoxy resin templates are imprinted on the NRSRC base material with the plate vulcanizer (XLB-D400 × 400/630, 23 MPa) at 170°C for 10 minutes. Four kinds of cylindrical micropillar-arrayed surface samples with different pillar diameters of 20 μm, 30 μm, 40 μm and 50 μm are finally obtained after demolding, which are named C-20, C-30, C-40 and C-50, respectively.
Figure 2. Schematics of the fabrication of (a) cylindrical micropillar-arrayed surfaces and (b) microwedge-arrayed surfaces.
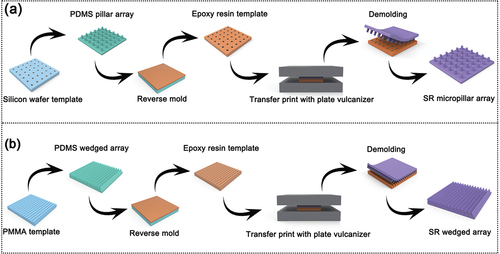
The fabrication of microwedge-arrayed surface samples is similar to the process of micropillar-arrayed surfaces, which is depicted in ). The only difference lies in the preparation of the template. The microwedge-arrayed templates made by polymethylmethacrylate (PMMA) are processed with a Nanoform X Ultra-Precision Machining System (Precitech Corporation). Three kinds of wedge arrays with different wedge spacings of 60 μm, 90 μm and 120 μm are prepared, which are denoted D-60, D-90 and D-120, respectively. The inclined angle, height and width of the wedge element are fixed to be 25°, 180 μm and 84 μm, respectively.
Four kinds of micropillar-arrayed samples, three kinds of microwedge-arrayed samples and a flat surface sample are involved in the present research. Eight specimens for each kind of surface sample are fabricated, and the corresponding adhesive strength takes an average value from the eight testing results with a satisfying convergence.
3. Results and discussion
3.1 Surface morphology
) shows the morphologies at different magnifications of the micropillar-arrayed surface with a pillar diameter of 50 μm (C-50) (samples with other diameters are given in Fig. S2 of the Supplementary Material). According to the observation, the mean area densities of the micropillars with diameters of 20 μm, 30 μm, 40 μm and 50 μm are 35%, 44%, 50% and 55%, respectively. Meanwhile, ) shows the overall morphology, the side view and top view of the microwedge-arrayed surface with a wedge spacing of 90 μm (D-90). Images of surface samples with wedge spacings of 60 μm and 120 μm are provided in Fig. S3 of the Supplementary Material. The asymmetric pattern of the microwedges endows the surface with an anisotropically adhesive property.
Figure 3. The surface morphologies of (a) micropillar-arrayed surfaces with a pillar diameter of 50 μm (from left to right: schematics of the whole surface, SEM images of the top view of micropillar arrays at different magnifications) and (b) microwedge-arrayed surfaces with a wedge spacing of 90 μm (from left to right: schematics of the whole surface, SEM images of the side and top views of microwedge arrays).
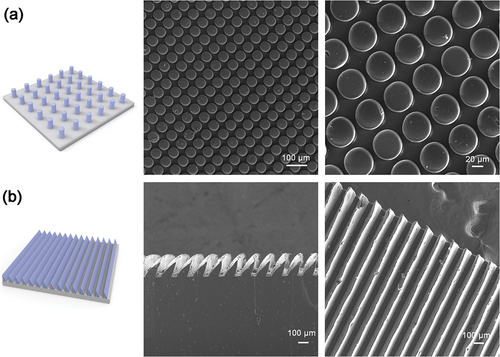
3.2 Normal adhesion of micropillar-arrayed surfaces
Using the pull-off test setup in ), the normal adhesive strengths of C-20, C-30, C-40 and C-50 micropillar-arrayed samples are measured. The variation in the contact force on the sample during the whole test is shown in ), in which the testing process includes 3 stage. Firstly, the test probe approaches the sample with a speed of 25 μm/s and a pre-set pressure of 2.5 N until a complete contact is realized. The contact force in this stage is negative and increases monotonically with the time. When the contact force is balanced with the pre-set pressure, let the probe be fixed for 10s to reduce the viscoelastic effect. Subsequently, the probe retracts under the same speed of 25 μm/s until it detaches from the sample, and the maximum pull-off force (positive) at the end of this stage is extracted to calculate the normal adhesive strength.
Figure 4. Testing results of normal adhesion of micropillar-arrayed surfaces: (a) The variation in the contact force of the C-50 sample with time; (b) The effect of preset pressure on the normal adhesive strength of micropillar surfaces with different pillar diameters; (c) Normal adhesive strengths of micropillar surfaces with different pillar diameters; (d) Normal adhesive strengths of the C-50 sample and the NRSRC flat surface.
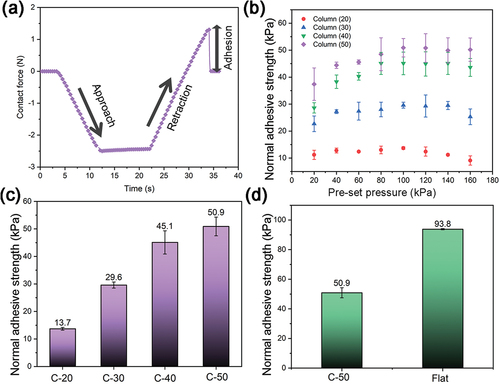
) shows the effect of the preset pressure on the normal adhesive strength. When the preset pressure is below 100 kPa, its increase leads to monotonic increases in the normal adhesive strengths of the four kinds of samples, possibly due to the enlargement of the contact area under a larger pressure. When the preset pressure exceeds 100 kPa, the normal adhesive strengths of the C-50 and C-40 samples remain almost unchanged, while those of the C-30 and C-20 samples, especially the latter, show a noticeable decrease with increasing preset pressure. Such a weakening adhesion performance of the C-30 and C-20 samples may be due to the easy collapse of their slender micropillars at a high pressure [Citation24,Citation37,Citation38]. Therefore, the preset pressure in the tests is taken to be 100 kPa, at which all micropillar surfaces could reach their largest normal adhesive strengths.
) presents histograms of the normal adhesive strengths of four kinds of micropillar-arrayed surfaces made by NRSRCs. The normal adhesive strength increases monotonically with increasing pillar diameter. The C-50 sample shows the largest normal adhesive strength of 50.9 kPa, which is much larger than the previously reported one of micropillar surfaces made by a commercially available PDMS (Sylgard 184) (lower than 10 kPa) [Citation9,Citation19,Citation38–40]. Such a significant improvement in adhesion is mainly due to the material properties of the NRSRC base material, e.g. the high modulus, the high viscoelasticity, and the formation of interface hydrogen bonding between surface and substrate. Admittedly, the existing polymer-based adhesive surface with mushroom-like pillar arrays shows a higher adhesive strength than that of the present C-50 sample. For examples, the adhesive strength of PVS (Polyvinyl siloxane)-based mushroom-shaped pillar arrays can reach 60kPa [Citation21,Citation28], while the adhesive strength of a polyurethane (PU) elastomer-based mushroom-shaped fibrillar surface is as high as 100 kPa or 200 kPa [Citation41]. Such outstanding adhesion performance is basically due to the mushroom tip structure responsible for the alleviation of stress concentration at the contact perimeter [Citation24,Citation25,Citation42,Citation43].
) shows that the normal adhesive strength of the C-50 sample is obviously lower than that of the flat surface made by the same material. This phenomenon was also found in existing studies on cylindrical micropillar-arrayed surfaces [Citation9,Citation44]. The above adhesion performances of micropillar structured surfaces can be further explained with a theoretical model proposed by Chen et al. [Citation45], in which the normal adhesive force of a single fiber of the fibrillar surface is expressed as
where a is the radius of the actual contact area between the cylindrical fiber and the rigid substrate, R is the fiber radius, and
are the Young’s modulus and Poisson’s ratio of the fiber, respectively, and
is the work of adhesion of the contact interface.
is a dimensionless function of the ratio
, which can be taken as a constant between 0.4 and 0.5 [Citation45]. EquationEq. (1)
(1)
(1) shows that the normal adhesive force of a fiber element increases with increasing contact area, fiber stiffness and interfacial adhesive energy. Therefore, since the present NRSRC material possesses a much higher modulus and a much stronger interfacial adhesion than PDMS Sylgard 184 (see Fig. S4 in the Supplementary Material), the corresponding micropillar structured surfaces should exhibit a higher normal adhesive strength than their counterparts made by the PDMS. For NRSRC-based micropillar surfaces, the one with a larger pillar diameter should have a larger contact area (the micropillar spacing is fixed to be 10 μm), consequently leading to a better adhesion performance. However, the effective contact area of cylindrical micropillar structured surfaces is always smaller than that of a flat surface, resulting in a lower adhesive strength.
3.3 Shear adhesion of microwedge-arrayed surfaces
Using the digital force gauge in ), the shear adhesive strengths of microwedge-arrayed surfaces with different wedge spacings and that of the NRSRC flat surface are measured, as shown in ). When the shear force is applied in a preferred direction, the D-90 sample shows a larger shear adhesive strength than that of the flat surface, while the D-60 sample and D-120 sample exhibit lower and comparable shear adhesive strengths, respectively, compared with that of the flat surface. The shear adhesive strength of the D-90 sample is as high as 137.3 kPa, which is much larger than the previously reported shear adhesive strengths of microwedged surfaces made by pure polymers [Citation28,Citation29].
Figure 5. Testing results of shear adhesion of microwedge-arrayed surfaces: (a) Shear adhesive strengths in preferred and anti-preferred directions of microwedged surfaces with different wedge spacings, in which the shear adhesive strength of the NRSRC flat surface is also presented; (b) The anisotropic adhesion parameters of the present microwedged surfaces and those of previously reported microwedged surfaces [Citation26,Citation29].
![Figure 5. Testing results of shear adhesion of microwedge-arrayed surfaces: (a) Shear adhesive strengths in preferred and anti-preferred directions of microwedged surfaces with different wedge spacings, in which the shear adhesive strength of the NRSRC flat surface is also presented; (b) The anisotropic adhesion parameters of the present microwedged surfaces and those of previously reported microwedged surfaces [Citation26,Citation29].](/cms/asset/955690c3-f8a5-48f4-a308-6035fae677ee/tsnm_a_2168783_f0005_c.jpg)
The shear adhesive strengths in the anti-preferred direction of microwedged surfaces are also measured, which are significantly smaller than their counterparts in the preferred direction and that of the flat surface, indicating an obvious anisotropy in the shear adhesion performance. Such an anisotropic behavior can be evaluated by a ratio between the shear adhesive strengths in the preferred and anti-preferred directions [Citation26],
where and
are the shear adhesive strengths in the preferred and anti-preferred directions, respectively. ) presents the values of the anisotropy parameter
for the present D-60, D-90, and D-120 samples and two recently reported microwedged samples made by pure PDMS [Citation26,Citation29]. Among them, the D-90 sample shows the largest
, indicating that such a microwedge structure is preferable to realize strong and reversible adhesion.
To disclose the mechanism behind the strong shear adhesion of microwedged surfaces, ) depict the respective deformation patterns of three kinds of microwedge arrays under a shear force in the preferred direction. Clearly, the microwedge elements bend to contact the substrate, leading to a larger contact area and consequently a stronger adhesion than those of a flat surface. However, if the wedge spacing is relatively small, such as the D-60 sample, the neighboring wedge elements are likely to adhere to each other during the bending process, as illustrated in ). This problem severely restrains the bending deformation of wedge elements so that the contact area is limited. When the wedge spacing increases to 90 μm, the adhesion between neighboring wedges can be eliminated, as shown in ). All wedge elements can adequately bend to form a sufficiently large contact area. For the D-120 sample in ), although the wedge adhesion can also be avoided, the number of wedge elements becomes relatively small due to the excessively large spacing, which results in a smaller contact area than that of the D-90 sample. Therefore, the D-90 sample shows a superior shear adhesion performance over the other two.
Figure 6. Deformation patterns of the microwedge elements of the (a) D-60, (b) D-90 and (c) D-120 samples under a shear force in the preferred direction.
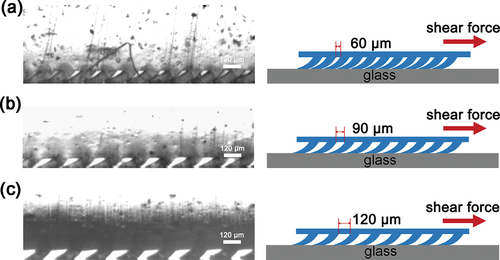
Furthermore, ) presents the shear adhesive strength of the D-90 sample during 100 attachment/detachment cycles, in which the blue dashed line represents the linear fitting of the measuring data. The fluctuation of the testing results is within 15%, which can be attributed to some inevitable factors in the experiments, e.g. the contamination of dust on the surface, the change of deforming states of wedge elements in different cycles, the misalignment between the surface and substrate and the vibration of loading devices. According to the linear fitting of the fluctuating data, the shear adhesive strength decreases by about 11% during the cycles, possibly owing to the dust contamination to the surface and the failure of some wedge elements. However, the shear adhesive strength can still maintain more than 85% of its initial counterpart when the cycle is over, indicating a fairly good reusability of the present NRSRC-based microwedge surface.
Figure 7. The shear adhesion performance of the D-90 sample: (a) The variation of the shear adhesive strength during 100 attachment/detachment cycles, in which the blue dashed line represents the linear fitting of the fluctuating data; (b) A phase diagram of tensile strength versus shear adhesive strength for the present D-90 sample compared with existing microwedged surfaces made by pure polymers [Citation23,Citation28–30,Citation39,Citation46–50].
![Figure 7. The shear adhesion performance of the D-90 sample: (a) The variation of the shear adhesive strength during 100 attachment/detachment cycles, in which the blue dashed line represents the linear fitting of the fluctuating data; (b) A phase diagram of tensile strength versus shear adhesive strength for the present D-90 sample compared with existing microwedged surfaces made by pure polymers [Citation23,Citation28–30,Citation39,Citation46–50].](/cms/asset/62e6e8d6-77d6-4350-a756-7f9c384f561f/tsnm_a_2168783_f0007_c.jpg)
The experimental result in ) suggests not only that the adhesion property of the microstructured surface is stable but also that the use of the NRSRC base material with high strength could effectively prevent the mechanical failure of the surface. The latter aspect was difficult to realize in previously reported gecko-inspired adhesive surfaces made by pure silicone elastomers [Citation33]. Some stronger polymers, such as polyurethane (PU), were used to fabricate adhesive fibrillar surfaces with a better load-bearing capacity, but their low adhesion and reduced deformability limit the improvement of adhesion performance of the surface. Such a dilemma can be well overcome by the present microwedge-arrayed surface made by NRSRC, as shown in ), in which the D-90 sample exhibits a superior shear adhesive strength and a fairly good strength in comparison with the existing PDMS- and PU-based adhesive surfaces. Therefore, through the present material-structure integrating design, a good match between the adhesion property and mechanical property of fibrillar surfaces can be achieved.
3.4 Adhesion of microwedged surfaces on a rough substrate
To check the usability of the surface in different service conditions, the adhesive property of microwedge-arrayed surfaces on a rough substrate is also tested. Several frosted glasses with different surface roughnesses are used for the test, and their roughness profiles are characterized by the LSCM in a laser scanning mode, as shown in Fig. S5 in the Supplementary Material. presents the variations in the shear adhesive strengths of the microwedge-arrayed surfaces and that of the NRSRC flat surface with the substrate roughness. The shear adhesions of the three kinds of microwedged surfaces all weaken with increasing surface roughness, possibly due to the decrease in the contact area between wedge elements and surface asperities. However, the shear adhesive strength of the flat surface reaches a maximum value at the substrate roughness of
, which may be due to the good match between the rough topographies of the composite surface (
) and the substrate with such a roughness, as schematically depicted in ).
Figure 8. The shear adhesive strengths of the present microwedged surfaces and the NRSRC flat surface on substrates with different roughnesses.
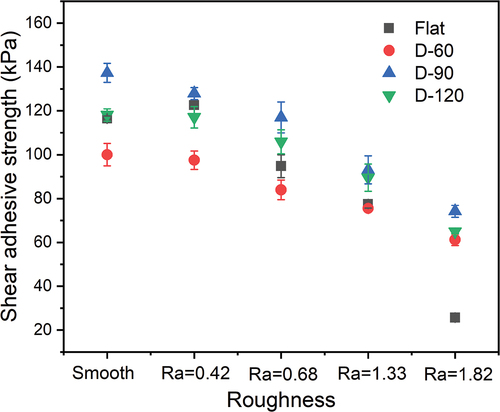
Figure 9. The adhesion on a rough substrate. (a) The roughness profile of the NRSRC flat surface; (b) Schematic of the adhesion between the NRSRC flat surface and a smooth substrate; (c) Schematic of a good match between the rough topologies of the NRSRC flat surface and the substrate with a roughness of 0.42; (d) Schematic of the adhesion between the microwedge elements and the rough substrate.
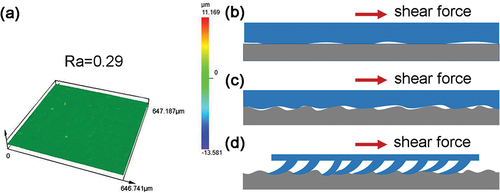
Moreover, when the substrate roughness is as large as 1.82, all three kinds of microwedged surfaces exhibit significantly higher shear adhesive strengths than that of the flat surface. Among them, the shear adhesive strength of the D-90 sample can reach up to 80 kPa, which is still larger than those of the PDMS-based microwedged surface on a smooth substrate [Citation26,Citation29]. This means that, even though the contact area of microwedges on a rough substrate is much reduced, as illustrated in ), the surface could retain a fairly good adhesion performance by taking advantage of the highly adhesive property of the base material and an optimum wedge spacing. Such a synergistic effect of material and structure enables the present microwedged surface to have a wider applicability, in contrast to its previous counterparts that can only maintain good shear adhesion on a smooth surface [Citation25,Citation51–53].
The above results show that, through a material-structure integrated design, either the micropillar-arrayed or the microwedge-arrayed surface shows much improved mechanical strength and adhesive strength as compared with its previously reported counterparts with the same microstructure. Specially, the design of an asymmetric structure endows the microwedge-arrayed surface a directional adhesion ability and a stable adhesion on the rough surface, which should enormously broaden the application prospect of such surface.
3.5 A mechanical gripper with a microwedged surface
The present microwedge-arrayed surface is finally applied in a mechanical gripper to directly show its superior adhesion performance. As imaged in ), the D-90 sample with an area of 5 mm × 5 mm is attached to the tongs of a gripper connected to a controller and a battery. This gripper is then used to transport two kinds of smooth glass plates, i.e. a light one with a weight of 112.5 g (15 cm × 15 cm × 2 mm) and a heavy one with a weight of 400 g (20 cm × 15 cm × 5 mm). For comparison, the original gripper without any microstructured surface on its tongs is also used to transport the same objects.
Figure 10. An application of the present microwedged surface in a mechanical gripper: (a) A gripper with its tongs attached by the D-90 sample, which is manipulated by a controller powered by a battery; (b) Transportation of a light glass plate (15 cm × 15 cm × 2 mm, 112.5 g) by the gripper with the D-90 microwedged surface; (c) Transportation of a heavy glass plate (20 cm × 15 cm × 5 mm, 400 g) by the gripper with the D-90 microwedged surface; (d) Transportation of the same glass plate by the original gripper without any microwedged surface on its tongs.
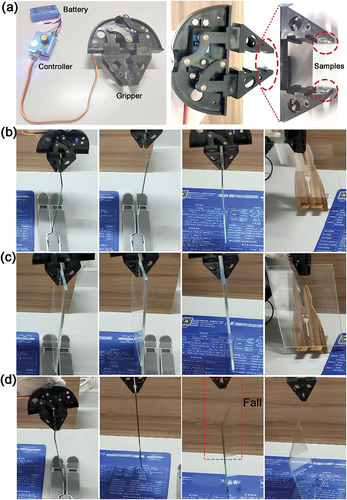
As shown in ) and video S1, the gripper attached by the D-90 sample can firmly pick up either the light glass plate or the heavy one, move them to the destination and easily release them. This result demonstrates the strong and reversible adhesive function of the present microwedged surface, which should have promising prospects in realizing the ability of smart equipment to grasp or transport objects. In contrast, ) and video S2 show that the gripper without the microwedged surface cannot even firmly hold the glass plate, not to mention the transporting and releasing behaviors.
The working mechanism of the aforementioned gripper with a microwedged surface can be briefly explained by . Firstly, the gripper clamps the glass plate to apply a normal pressure (the left graph in ). When the glass is picked up and moved, an upward shear force along the preferred direction is applied by the gripper to counterbalance the gravity of the glass, under which the wedge elements bend with their long sides to yield a large contact area so that the adhesion with glass can be enhanced (the middle graph in ). When the gripper is loosened to release the glass at the destination, the shear force is simultaneously released, and the elastic wedge elements should return to their original states under a slight pressure (the right graph in ). As a result, the contact area is significantly reduced, and the adhesion becomes too weak to hold the glass.
4. Conclusions
A material-structure integrated design method is proposed in this paper to fabricate gecko-inspired fibrillar surfaces, in which a strong and highly adhesive nanoparticle reinforced silicone rubber composite is used as a base material of micropillar-arrayed and microwedge-arrayed surfaces. Taking advantages of the high strength and strong adhesion of the composite, both kinds of microstructured surfaces exhibit superior adhesive performances over their previously reported counterparts made by pure soft polymers. In particular, the microwedged surface with an optimum wedge spacing shows an excellent match between strength and adhesion, good reusability and obvious directional adhesion compared to existing microwedge-arrayed surfaces based on pure polymers. All these advantages enable such a surface to be successfully applied in a mechanical gripper to conveniently and reliably transport objects of different weights. The present research based on material-structure integration provides an enlightening idea for the design of adhesive functional surfaces, which should be helpful for manufacturing advanced adhesive devices in the medical, space and military industries.
Supplemental Material
Download MS Word (2.5 MB)Supplemental Material
Download GIF Image (801.8 KB)Supplemental Material
Download GIF Image (3.4 MB)Acknowledgments
The work reported here is supported by NSFC through Grants (No. 12032004, No. 12293000, No. 12293002, No. 12272043) and Natural Science Foundation of Henan (No. 202300410088) as well as Innovation Demonstration Project of Henan (No. 201111211400).
Disclosure statement
No potential conflict of interest was reported by the author(s).
Supplementary material
Supplemental data for this article can be accessed online at https://doi.org/10.1080/19475411.2023.2168783
Additional information
Funding
References
- Autumn K, Liang YA, Hsieh ST, et al. Adhesive force of a single gecko foot-hair. Nature. 2000;405(6787):681.
- Autumn K, Sitti M, Liang YA, et al., Evidence for van der Waals adhesion in gecko setae, Proc. Natl. Acad. Sci. USA. 2002;99(19) :12252–12256.
- Yao H, Gao H. Mechanics of robust and releasable adhesion in biology: bottom–up designed hierarchical structures of gecko. J Mech Phys Solids. 2006;54(6):1120–1146.
- Chen S, Gao H. Bio-inspired mechanics of reversible adhesion: orientation-dependent adhesion strength for non-slipping adhesive contact with transversely isotropic elastic materials. J Mech Phys Solids. 2007;55(5):1001–1015.
- Shintake J, Cacucciolo V, Floreano D, et al. Soft robotic grippers. Adv Mater. 2018;e1707035. DOI:10.1002/adma.201707035
- Jiang H, Hawkes EW, Fuller C, et al. A robotic device using gecko-inspired adhesives can grasp and manipulate large objects in microgravity. Sci Rob. 2017;2(7):eaan4545.
- Song S, Drotlef D-M, Majidi C, et al., Controllable load sharing for soft adhesive interfaces on three-dimensional surfaces, Proc. Natl. Acad. Sci. USA. 2017;114(22):E4344–E4353.
- Chen Y, Meng J, Gu Z, et al. Bioinspired multiscale wet adhesive surfaces: structures and controlled adhesion. Adv Funct Mater. 2019;30(5):1905287.
- Greiner C. A.n.d. Campo, E. Arzt, adhesion of bioinspired micropatterned surfaces: effects of pillar radius, aspect ratio, and preload, Langmuir: the ACS. J Surfaces & Colloids. 2007;23:3495–3502.
- Kasem H, Tsipenyuk A, Varenberg M. Biomimetic wall-shaped hierarchical microstructure for gecko-like attachment. Soft Matter. 2015;11(15):2909–2915.
- Peressadko A, Gorb SN. When less is more: experimental evidence for tenacity enhancement by division of contact area. J Adhes. 2010;80(4):247–261.
- Kappl M, Kaveh F, Barnes WJ. Nanoscale friction and adhesion of tree frog toe pads. Bioinspiration & biomimetics. 2016;11(3):035003.
- Liu J, Yao Y, Li X, et al. Fabrication of advanced polydimethylsiloxane-based functional materials: bulk modifications and surface functionalizations. Chem Eng J. 2021;408:127262.
- Paretkar D, Kamperman M, Schneider A, et al. Bioinspired pressure actuated adhesive system. Materials Science & Engineering C-Materials For Biological Applications. 2011;31(6):1152–1159.
- Wolf MP, Salieb-Beugelaar GB, Hunziker P. PDMS with designer functionalities—Properties, modifications strategies, and applications. Prog Polym Sci. 2018;83:97–134.
- Kamperman M, Kroner E, Del Campo A, et al. Functional adhesive surfaces with “gecko” effect: the concept of contact splitting. Adv Eng Mater. 2010;12(5):335–348.
- Geim AK, Dubonos SV, Grigorieva IV, et al. Microfabricated adhesive mimicking gecko foot-hair. Nature Materials. 2003;2(7):461–463.
- Boesel LF, Greiner C, Arzt E, et al. Gecko-inspired surfaces: a path to strong and reversible dry adhesives. Advanced Materials. 2010;22(19):2125–2137.
- Del Campo A, Greiner C, Álvarez I, et al. Patterned Surfaces with Pillars with Controlled 3D Tip Geometry Mimicking Bioattachment Devices. Advanced Materials. 2007;19(15):1973–1977.
- Li X, Bai P, Li X, et al. Robust scalable reversible strong adhesion by gecko-inspired composite design. Friction. 2021;10(8):1192–1207.
- Gorb S, Varenberg M, Peressadko A, et al. Biomimetic mushroom-shaped fibrillar adhesive microstructure. J R Soc Interface. 2007;4(13):271–275.
- Heepe L, Varenberg M, Itovich Y, et al. Suction component in adhesion of mushroom-shaped microstructure. J R Soc Interface. 2011;8(57):585–589.
- Murphy MP, Aksak B, Sitti M. Gecko-inspired directional and controllable adhesion. Small. 2009;5(2):170–175.
- Liu Q, Tan D, Meng F, et al. Adhesion Enhancement of Micropillar Array by Combining the Adhesive Design from Gecko and Tree Frog. Small. 2021;17(4):e2005493.
- Heepe L, Gorb SN. Biologically Inspired Mushroom-Shaped Adhesive Microstructures. Annual Review of Materials Research. 2014;44(1):173–203.
- Zhou T, Ruan B, Che J, et al. Gecko-Inspired Biomimetic Surfaces with Annular Wedge Structures Fabricated by Ultraprecision Machining and Replica Molding. ACS omega. 2021;6(10):6757–6765.
- Hu H, Tian H, Shao J, et al. Discretely supported dry adhesive film inspired by biological bending behavior for enhanced performance on a rough surface. ACS App Mat & Interfaces. 2017;9(8):7752–7760.
- Parness A, Soto D, Esparza N, et al. A microfabricated wedge-shaped adhesive array displaying gecko-like dynamic adhesion, directionality and long lifetime. J Royal Soc Interface. 2009;6(41):1223–1232.
- Tao D, Gao X, Lu H, et al. Controllable anisotropic dry adhesion in vacuum: gecko inspired wedged surface fabricated with ultraprecision diamond cutting. Adv Funct Mater. 2017;27(22):1606576.
- Day P, Eason EV, Esparza N, et al. Microwedge machining for the manufacture of directional dry adhesives. J Micro Nano-Manuf. 2013;1(1). DOI:10.1115/1.4023161
- Simaite A, Temple B, Karimi MA, et al. Understanding the influence of silicone elastomer properties on wedge-shaped microstructured dry adhesives loaded in shear. J Royal Soc Interface. 2018;15(20180551):20180551.
- Arzt E, Quan H, McMeeking RM, et al. Functional surface microstructures inspired by nature – from adhesion and wetting principles to sustainable new devices. Pro Mater Sci. 2021;100778.
- Johnston ID, McCluskey DK, Tan CKL, et al. Mechanical characterization of bulk Sylgard 184 for microfluidics and microengineering. J Micromech Microeng. 2014;24(3):035017.
- Li C, Wang S, Liu M, et al. Directional Transportation on Microplate-Arrayed Surfaces Driven via a Magnetic Field. ACS applied materials & interfaces. 2021;13(31):37655–37664.
- Shahsavan H, Zhao B. Bioinspired Functionally Graded Adhesive Materials: Synergetic Interplay of Top Viscous–Elastic Layers with Base Micropillars. Macromolecules. 2013;47(1):353–364.
- Liu J, Yao Y, Chen S, et al. A new nanoparticle-reinforced silicone rubber composite integrating high strength and strong adhesion. Compos Part A Appl Sci Manuf. 2021;151:106645.
- Tan D, Wang X, Liu Q, et al. Switchable Adhesion of Micropillar Adhesive on Rough Surfaces. Small. 2019;15(50):e1904248.
- Barreau V, Hensel R, Guimard NK, et al. Fibrillar Elastomeric Micropatterns Create Tunable Adhesion Even to Rough Surfaces. Advanced Functional Materials. 2016;26(26):4687–4694.
- Wang X, Tan D, Hu S, et al. Reversible Adhesion via Light-Regulated Conformations of Rubber Chains. ACS Appl Mater Interfaces. 2019;11(49):46337–46343.
- Hensel R, Moh K, Arzt E. Engineering micropatterned dry adhesives: from contact theory to handling applications. Adv Funct Mater. 2018;28(28):1800865.
- Kim S, Sitti M. Biologically inspired polymer microfibers with spatulate tips as repeatable fibrillar adhesives. Applied Physics Letters. 2006;89(26):261911.
- Wang Y, Hu H, Shao J, et al. Fabrication of well-defined mushroom-shaped structures for biomimetic dry adhesive by conventional photolithography and molding. ACS applied materials & interfaces. 2014;6(4):2213–2218.
- Shi Z, Tan D, Wang Z, et al. Switchable Adhesion on Curved Surfaces Mimicking the Coordination of Radial-Oriented Spatular Tips and Motion of Gecko Toes. ACS applied materials & interfaces. 2022;14(27):31448–31454.
- Castellanos G, Arzt E, Kamperman M. Effect of viscoelasticity on adhesion of bioinspired micropatterned epoxy surfaces. Langmuir. 2011;27(12):7752–7759.
- Chen SH, Xu G, Soh AK. Robust Nanoadhesion Under Torque. Tribology Letters. 2008;29(3):235–239.
- Jin K, Cremaldi JC, Erickson JS, et al. Biomimetic Bidirectional Switchable Adhesive Inspired by the Gecko. Advanced Functional Materials. 2014;24(5):574–579.
- Hao Z, LianWei W, ShiXing J, et al. Fabrication and adhesion of hierarchical micro-seta. Chinese Science Bulletin. 2012;57(11):1343–1349.
- Jin K, Tian Y, Erickson JS, et al. Design and fabrication of gecko-inspired adhesives. Langmuir. 2012;28(13):5737–5742.
- Tian Y, Qi H, Wu H, et al. Friction behavior of gecko-inspired polydimethylsiloxane micropillar array with tailored Young’s modulus by incorporation of ZrO2 particles. Chem Phys Lett. 2021;763:138202.
- Aksak B, Murphy MP, Sitti M. Adhesion of biologically inspired vertical and angled polymer microfiber arrays. Langmuir. 2007;23(6):3322–3332.
- Kasem H, Varenberg M. Effect of counterface roughness on adhesion of mushroom-shaped microstructure. J R Soc Interface. 2013;10(87):20130620.
- Wang K, Shen R-J, He B. Influence of surface roughness on wet adhesion of biomimetic adhesive pads with planar microstructures. Micro & Nano Letters. 2012;7(12):1274–1277.
- Shi W, Cheng X, Cheng K. Gecko-inspired adhesives with asymmetrically tilting-oriented micropillars. Langmuir. 2022;38(29):8890–8898.