Abstract
This manuscript reports a novel process of high-temperature laser shock peening (HTLSP) for surface strengthening of single-crystal ceramics such as sapphire and reveals its fundamental mechanisms. HTLSP at 1200°C can induce a high compressive residual stress on the surface of sapphire while minimize the damage of laser-driven shock waves. Transmission electron microscopy characterizations revealed high dislocation densities near the surface, suggesting that plastic deformation at an ultrahigh strain rate was generated by the high shock wave pressure. The HTLSP-induced compressive residual stress can significantly improve the hardness and fracture toughness of sapphire, while maintain its outstanding optical transmittance.
GRAPHICAL ABSTRACT
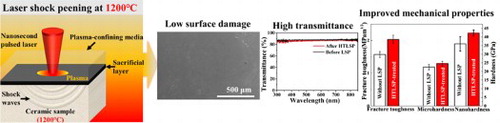
IMPACT STATEMENT
This manuscript reports a novel process of high-temperature laser shock peening for surface strengthening of single-crystal ceramics, and reveals mechanisms related to the interactions between laser-driven shock waves and ceramics.
Acknowledgements
This material is based upon work supported by the National Science Foundation under Grant No. CMMI-1563145. Manufacturing and characterization analyses were performed at the NanoEngineering Research Core Facility (part of the Nebraska Nanoscale Facility), which is partially funded from the Nebraska Research Initiative.
Disclosure statement
No potential conflict of interest was reported by the author(s).