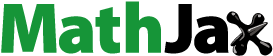
ABSTRACT
High-temperature shape memory alloys (HTSMAs) show enormous potential for applications as energy conversion devices, actuators and sensors in automotive, aerospace, and energy exploration industries, but they suffer from strength decrease and microstructural instability at elevated temperatures, rendering it difficult to achieve satisfactory high-temperature superelasticity. Here, a novel Ti20Hf15Zr15Cu25Ni25 high-entropy HTSMA exhibiting large superelasticity with a fully recoverable strain of 4.0% at temperatures up to 285°C is designed with the high-entropy alloy concept by employing the sluggish diffusion and severe lattice distortion effects to suppress thermal softening. This work illuminates the design of novel high-performance functional materials for high-temperature applications.
GRAPHICAL ABSTRACT
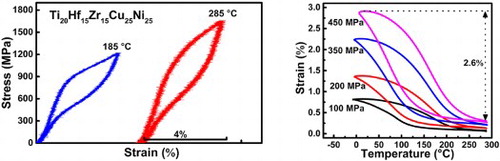
IMPACT STATEMENT
A novel high-entropy high-temperature shape memory alloy exhibiting large complete superelastic recovery is designed by employing the sluggish diffusion and severe lattice distortion in high-entropy alloys to suppress thermal softening.
1. Introduction
The rapid development of automotive, aerospace, manufacturing, and oil and gas exploration industries urgently demands high-temperature shape memory alloys (HTSMAs) that are used as solid-state energy conversion devices, actuators and sensors at elevated temperatures above 100°C [Citation1,Citation2]. Owing to the reversible phase transformation between the high-temperature, high-symmetry austenitic phase and the low-temperature, low-symmetry martensitic phase, HTSMAs have the potential to recover a large shape change upon removal of applied stress (superelasticity) or upon heating (shape memory effect) [Citation1,Citation3]. Therefore, these alloys exhibit very promising application prospects in rocket motors, gas turbines, automotive actuators, pressure transducers and so on [Citation1,Citation2].
During the past decades, increasing efforts have been devoted to the exploration of high-performance HTSMAs [Citation1,Citation4–7]. However, there remains a major challenge in developing such alloys with satisfactory high-temperature superelasticity. As is well known, the superelasticity of shape memory alloys occurs only if the yield strength σy is higher than the critical stress required for stress-induced martensitic transformation σSIM; otherwise, the deformation is dominated by permanent plastic deformation via dislocation slip, leading to irrecoverable strain. Nevertheless, while σSIM of shape memory alloys increases as the difference between the operating temperature and the transformation temperature increases, σy decreases with increasing temperature [Citation1], and thus σSIM could easily surpass σy at high temperatures. Moreover, HTSMAs frequently face the problem of microstructural instability, such as precipitate formation, dislocation recovery and vacancy diffusion at elevated temperatures [Citation8]. The above thermal softening activities render it very difficult to achieve perfect high-temperature superelasticity in HTSMAs. It is imperative to look for viable means to develop high-performance HTSMAs.
The recently proposed high-entropy alloy concept has inspired the exploration of novel alloys with unprecedented properties [Citation9,Citation10]. Particularly, the high-entropy alloy concept can be used to design alloys with excellent resistance to thermal softening [Citation11]. The core effect of sluggish diffusion could effectively suppress the diffusion-controlled processes at elevated temperatures such as vacancy diffusion and grain boundary sliding [Citation12,Citation13] and the severe lattice distortion creates large energy barriers for thermally-activated dislocation motion [Citation13–15], both contributing to the suppression of thermal softening. Meanwhile, the sluggish diffusion does not inhibit the occurrence of diffusionless martensitic transformation [Citation16] and associated functional properties [Citation16–20]. Therefore, it is expected that the high-entropy alloy concept can be used to design HTSMAs with superb superelastic and shape memory properties. Here in this work, we report a novel Ti20Hf15Zr15Cu25Ni25 high-entropy HTSMA with large perfect superelasticity. This alloy was designed as follows: noticing the conventional Ni45.3Ti29.7Hf20Cu5 HTSMA reported in the literature [Citation21], we applied the high-entropy alloy concept and obtained the equiatomic composition Ti25Hf25Ni25Cu25, but it shows an austenitic transformation finish temperature Af of only ∼60°C; to raise Af and to further increase the lattice distortion, the composition Ti20Hf15Zr15Cu25Ni25 was finally designed. The as-cast alloy exhibits high-temperature superelasticity with a large fully recoverable strain of 4.0% at temperatures up to 285°C. Furthermore, it shows excellent shape memory effect with a recoverable strain of 2.6%. The present work paves the way for designing advanced HTSMAs with exceptional functionalities at elevated temperatures.
2. Materials and methods
The polycrystalline Ti20Hf15Zr15Cu25Ni25 (at.%) high-entropy alloy was prepared by arc melting in water-cooled copper crucible using high-purity raw materials. The as-cast button ingots were cut into specimens with different size for different measurements. Differential scanning calorimetry (DSC, NETZSCH 214 Polyma) was used to determine the phase transformation temperatures. The microstructure was examined by using a scanning electron microscope (SEM, Zeiss Supra 55) and a transmission electron microscope (TEM, Tecnai F20) operated at 200 kV. The element distribution was determined by the energy dispersive spectroscopy (EDS) in SEM. The crystal structure at different temperatures was studied by X-ray diffraction (XRD, PW 3040 X′Pert PRO) using Cu-Kα radiation with a wavelength λ = 1.5405 Å.
The high-temperature superelastic properties were investigated by using a mechanical testing machine (Instron-5966) equipped with a temperature control chamber. Specimens with a size of Φ2 × 4 mm3 were cut with the axial direction (also the loading direction) perpendicular to the solidification direction of the button ingot; they show relatively coarse dendritic microstructure and no strong texture parallel to the loading direction is expected. The stress-strain curves were measured in compression mode at different constant temperatures from 185°C to 285°C with a strain rate of 2.1 × 10−4 s−1. The strain was recorded by an advanced non-contacting video extensometer. The shape memory effect was examined by measuring the strain-temperature curves under different constant stresses with a dynamic mechanical analyzer (DMA Q800) equipped with a three-point bending clamp, using a specimen of 25 × 3 × 0.5 mm3.
3. Results and discussion
The backscattered electron images taken in the planes perpendicular to and parallel to the solidification direction of the as-cast Ti20Hf15Zr15Cu25Ni25 button ingot are shown in Figure a and b, respectively. Typical dendritic structure can be clearly observed (Figure b), which is formed due to the difference in melting points of the constituent elements. Actually, the dendritic structure is commonly observed in the as-cast high-entropy alloys. The element distribution was determined by using EDS (Figure c). A quantitative analysis of the compositions of the dendritic and interdendritic regions was also performed (see Table for the results). Clearly, the distribution of the elements is not homogeneous across the dendritic and interdendritic regions (Figure c). The dendritic region with bright contrast in the backscattered electron image is rich in Hf and Ni and lean in Ti, Zr and Cu, while the interdendritic region with dark contrast is rich in Ti, Zr and Cu and lean in Hf and Ni (Table ). The dendritic microstructure may increase the strength and decrease the ductility.
Figure 1. Backscattered electron images taken in the planes (a) perpendicular to and (b) parallel to the solidification direction (SD) of the button ingot. (c) EDS maps of the elements Ti, Hf, Zr, Cu and Ni, taken from the area the backscattered electron image of which is shown in the upper left panel.
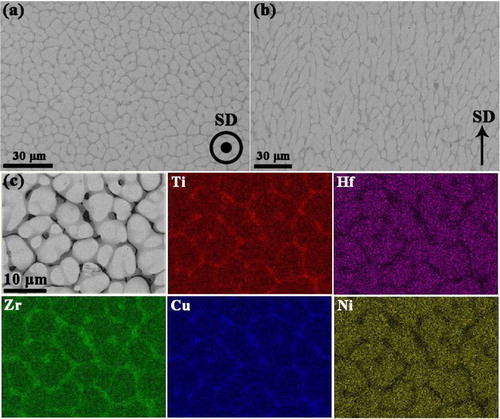
Table 1. Average chemical compositions (at.%) of the dendritic and interdendritic regions for the Ti20Hf15Zr15Cu25Ni25 alloy.
The XRD patterns collected at 200°C and −100°C are shown in Figure a. At 200°C, the major phase is the cubic B2 austenite, with a small amount of coexisting monoclinic B19′ martensite. The lattice constant of the cubic B2 austenite is aA = 3.172 Å, and the lattice parameters of the monoclinic B19′ martensite are aM = 3.331 Å, bM = 4.216 Å, cM = 4.781 Å, and β = 100.3°. When the temperature is decreased to −100°C, although there still exists residual austenite, the intensities of the martensitic peaks become stronger and several new martensitic peaks appear (Figure a), implying that the volume fraction of martensite increases during cooling. Therefore, the present high-entropy alloy shows martensitic transformation during cooling.
Figure 2. (a) X-ray diffraction patterns measured at 200°C and −100°C. The letters ‘A’ and ‘M’ in the indices denote austenite and martensite, respectively. (b) DSC curve recorded with a heating and cooling rate of 10°C/min.
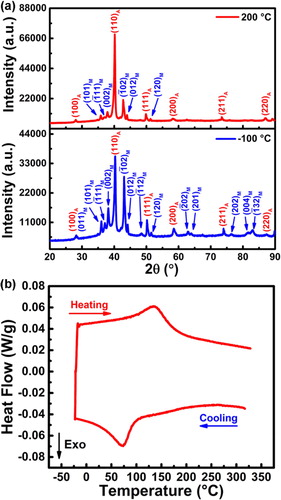
The DSC curve for the Ti20Hf15Zr15Cu25Ni25 high-entropy alloy is depicted in Figure b. Exothermic and endothermic peaks corresponding respectively to the martensitic and reverse austenitic transformations can be clearly observed, demonstrating the reversibility of the transformation. The martensitic transformation start temperature Ms and the Af are 101 and 179°C, respectively. The present high-entropy alloy shows a relatively large thermal hysteresis (Af–Ms = 78°C) and broad phase transformation intervals, which, on the one hand, could be due to the inhomogeneous element distribution (Figure and Table ) and, on the other hand, could be ascribed to the imperfect geometric compatibility between austenite and martensite, as presented below. As mentioned above, the interdendritic region is rich in Ti, Zr and Cu and lean in Hf and Ni; it is possible that the interdendritic region is non-transformable during cooling since our experience obtained during composition tuning suggests that both substitution of Cu for Ni and substitution of Ti or Zr for Hf lead to significant decrease of transformation temperature. According to the geometric nonlinear theory of martensite, the thermal hysteresis is to a large extent governed by the geometric compatibility at the interface between martensite and austenite [Citation22–24]. The geometric compatibility can be characterized by the middle eigenvalue λ2 of the transformation stretch tensor U. If λ2 is close to 1, the stress transition layer at the interface between martenstie and austenite could be greatly reduced or even eliminated, and thus the martensitic transformation has a very narrow thermal hysteresis [Citation23]. Based on the lattice parameters of martensite and austenite determined from the XRD experiments (Figure a), the λ2 is calculated to be 0.9584. This value deviates from 1, which indicates that the geometric compatibility is not very good in the Ti20Hf15Zr15Cu25Ni25 high-entropy alloy. In spite of the relatively large thermal hysteresis (Af–Ms = 78°C), the martensitic transformation in the present Ti20Hf15Zr15Cu25Ni25 high-entropy alloy is still thermoelastic in nature since the thermal hysteresis is below 100°C [Citation1,Citation3]. This serves as the basis for the functional properties demonstrated below.
To examine the high-temperature superelasticity, we measured the stress-strain curves at different constant temperatures ranging from 185°C to 285 °C (above Af). Strikingly, the present Ti20Hf15Zr15Cu25Ni25 high-entropy alloy exhibits perfect high-temperature superelasticity with large recovery. The applied strain of 4% can be fully recovered after unloading and thus the recoverable strain is as large as 4.0%. The maximum recoverable strain may be even larger if a higher strain is applied. The maximum temperature at which the large perfect superelasticity occurs is as high as 285°C. This remarkable perfect high-temperature superelasticity has never been achieved before in high-entropy alloys. It is worth mentioning that the precipitation strengthened conventional Ni50.3Ti29.7Hf20 HTSMA shows a recoverable strain of 3.0% in the temperature range 180−220°C [Citation25]. As displayed in Figure , the superelastic stress-strain response of the present high-entropy alloy is dependent on the test temperature; σSIM increases with the increase of temperature. Noteworthily, the applied stress is as high as 1.65 GPa at 285°C and the present alloy still exhibits perfect high-temperature superelasticty, suggesting that the yield strength is higher than 1.65 GPa at this temperature. This confirms that the Ti20Hf15Zr15Cu25Ni25 high-entropy alloy shows high yield strength at high temperatures.
Figure 3. Stress-strain curves recorded at different constant temperatures ranging from 185°C to 285°C.
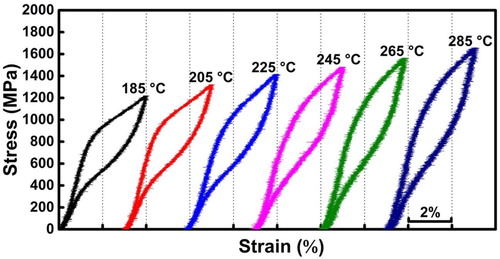
TEM observation on the fine microstructure of the Ti20Hf15Zr15Cu25Ni25 high-entropy HTSMA was conducted at room temperature. Figure a shows a bright-field TEM image and Figure b displays the selected area electron diffraction (SAED) pattern taken from the area enclosed by the circle in Figure a. No nanoscale precipitates can be observed from Figure a and there are no diffractions from precipitates in the SAED pattern. In fact, the SAED pattern contains diffractions from both B19′ martensite and B2 austenite, consistent with the XRD results (Figure a). In addition, the (011) type I twinning of B19′ martensitic variants can be clearly identified (Figure b). As indicated from the high-resolution TEM image in Figure c and the inverse fast Fourier transform image in Figure d, the atomic positions deviate from the ideal lattice points and a large amount of kinks and bends in the lattice layers are visible (Figure d), similar to those observed in a Nb25Mo25Ta25W25 high-entropy alloy [Citation26]. This clearly demonstrates the severe lattice distortion in the present Ti20Hf15Zr15Cu25Ni25 alloy. The severe lattice distortion is caused by the difference in atomic radii of constituent elements (namely the atomic size misfit); particularly, in the present high-entropy alloy the atomic sizes of Zr and Hf are significantly larger than Ti, Ni and Cu. The severe lattice distortion results in remarkable solid solution hardening and it also produces large energy barriers for (and thus reduces) thermally-activated dislocation motion. As a result, the present Ti20Hf15Zr15Cu25Ni25 high-entropy alloy shows high yield strength at high temperatures and thus large perfect high-temperature superelasticity. Moreover, it is possible that the sluggish diffusion in the high-entropy alloy suppresses the diffusion-controlled processes including vacancy diffusion and grain boundary sliding [Citation12,Citation13], and this may also contribute to the large perfect high-temperature superelasticity.
Figure 4. (a) Bright-field TEM image. (b) Selected area electron diffraction pattern taken from the area enclosed by the circle in (a), which is from the dendritic region. The subscripts ‘A’, ‘M’ and ‘T’ in the indices denote austenite, martensite and twin, respectively. (c) High-resolution TEM image taken from an area with coexisting austenite (A) and martensite (M). The A and M regions were identified from the corresponding fast Fourier transform patterns (not shown) of these regions. (d) Inverse fast Fourier transform image for the area enclosed by the rectangle in (c).
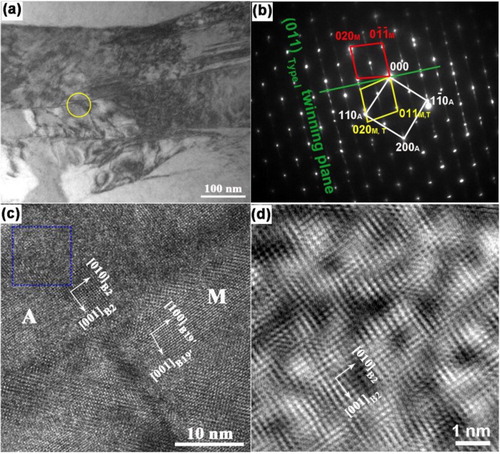
Since shape memory devices usually operate with a restoring bias force during service, the shape memory effect was investigated by load-biased thermal cycling tests. Figure a shows the strain-temperature curves recorded with the three-point bending mode during load-biased thermal cycling under different constant stresses for the Ti20Hf15Zr15Cu25Ni25 high-entropy alloy. The determination of the recoverable strain εrec and irrecoverable strain εirr is illustrated in this figure. The εrec and εirr are plotted as a function of stress in Figure b. The present alloy exhibits perfect shape memory effect with no εirr when the stress is in the range of 100−450 MPa (Figure a). The εrec is 0.7% under 100 MPa and it increases to 2.6% under 450 MPa. The increase in εrec with increasing applied stress is due to the increase in volume fraction of preferably selected martensitic variants. Under the higher stress level of 550 MPa, a small εirr (0.15%) appears and the εrec decreases to 2.4% (Figure b). This could be attributed to the occurrence of plastic deformation by dislocation slip and martensite stabilization under this stress level. Noteworthily, the present Ti20Hf15Zr15Cu25Ni25 high-entropy alloy exhibits a maximum εrec of as high as 2.6%, which is actually a high shape memory strain. Figure c shows the stress dependence of transformation temperatures Ms and Af extracted from the strain-temperature curves (Figure a). It is clear that the phase transformation temperatures increase almost linearly with the stress and the Ms and Af increase from 109°C to 153°C and from 196°C to 231°C, respectively, as the stress increases from 100 MPa to 550 MPa. Actually, the relationship between the applied stress and the transformation temperatures T follows the Clausius-Clapeyron relation: , where ΔH is the transformation enthalpy change, T0 is the equilibrium temperature, and εtr is the transformation strain. Based on the linear fittings of the experimental data extracted from Figure a, the dσ/dT values for Ms and Af for the present Ti20Hf15Zr15Cu25Ni25 high-entropy alloy are 10.12 and 13.20 MPa/°C, respectively, which are comparable with those reported for traditional Ni-Ti-Pd (5.9–8.4 MPa/°C) [Citation27] and Ni-Ti-Hf (8–12.5 MPa/°C) [Citation28] HTSMAs.
Figure 5. (a) Strain-temperature curves measured with the three-point bending mode during load-biased thermal cycling under different stresses. The determination of the recoverable strain εrec and irrecoverable strain εirr is illustrated. (b) εrec and εirr plotted as a function of stress. (c) Stress dependence of Ms and Af.
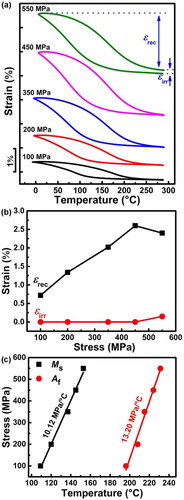
4. Conclusions
A novel Ti20Hf15Zr15Cu25Ni25 high-entropy high-temperature shape memory alloy with large perfect superelasticity has been designed by employing the sluggish diffusion and severe lattice distortion effects in high-entropy alloys. The as-cast alloy exhibits high-temperature superelasticity with a fully recoverable strain of as high as 4.0% at temperatures up to 285°C. Furthermore, it shows excellent shape memory effect with a recoverable strain of 2.6% under a stress of 450 MPa. This study provides a strategy for developing high-performance high-temperature functional materials for applications at elevated temperatures in automotive, aerospace, manufacturing, and energy exploration industries.
Disclosure statement
No potential conflict of interest was reported by the authors.
Additional information
Funding
References
- Ma J, Karaman I, Noebe RD. High temperature shape memory alloys. Int Mater Rev. 2010;55:257–315.
- Jani JM, Leary M, Subic A, et al. A review of shape memory alloy research, applications and opportunities. Mater Des. 2014;56:1078–1113.
- Otsuka K, Ren X. Physical metallurgy of Ti–Ni-based shape memory alloys. Prog Mater Sci. 2005;50:511–678.
- Beyer J, Mulder JH. Recent developments in high temperature shape memory alloys. Trans Mater Res Soc Jpn. 1994;18B:1003–1008.
- Koval YN. High temperature shape memory effect in some alloys and compounds. Mater Sci Forum. 2000;327-328:271–278.
- Saghaian SM, Karaca HE, Tobe H, et al. Effects of aging on the shape memory behavior of Ni-rich Ni50.3Ti29.7Hf20 single crystals. Acta Mater. 2015;87:128–141.
- Hsieh SF, Wu SK. A study on ternary Ti-rich TiNiZr shape memory alloys. Mater Charact. 1998;41:151–162.
- Firstov GS, Van Humbeeck J, Koval Y. High-temperature shape memory alloys some recent developments. Mater Sci Eng A. 2004;378:2–10.
- Yeh JW, Chen SK, Lin SJ, et al. Nanostructured high-entropy alloys with multiple principal elements: novel alloy design concepts and outcomes. Adv Eng Mater. 2004;6:299–303.
- Cantor B, Chang ITH, Knight P, et al. Microstructural development in equiatomic multicomponent alloys. Mater Sci Eng A. 2004;375-377:213–218.
- Tsai MH, Yeh JW. High-entropy alloys: a critical review. Mater Res Lett. 2014;2:107–123.
- Tsai KY, Tsai MH, Yeh JW. Sluggish diffusion in Co-Cr-Fe-Mn-Ni high-entropy alloys. Acta Mater. 2013;61:4887–4897.
- Chen J, Zhou X, Wang W, et al. A review on fundamental of high entropy alloys with promising high–temperature properties. J Alloys Compd. 2018;760:15–30.
- Guo W, Dmowski W, Noh JY, et al. Local atomic structure of a high-entropy alloy: an x-ray and neutron scattering study. Metall Mater Trans A. 2013;44A:1994–1997.
- Maresca F, Curtin WA. Mechanistic origin of high strength in refractory BCC high entropy alloys up to 1900K. Acta Mater. 2020;182:235–249.
- Firstov GS, Kosorukova TA, Koval YN, et al. High entropy shape memory alloys. Mater Today Proc. 2015;2:S499–S503.
- Chen CH, Chen YJ. Shape memory characteristics of (TiZrHf)50Ni25Co10Cu15 high entropy shape memory alloy. Scr Mater. 2019;162:185–189.
- Firstov GS, Kosorukova TA, Koval YN, et al. Directions for high-temperature shape memory alloys’ improvement: straight way to high-entropy materials? Shap Mem Superelasticity. 2015;1:400–407.
- Piorunek D, Frenzel J, Jöns N, et al. Chemical complexity, microstructure and martensitic transformation in high entropy shape memory alloys. Intermetallics. 2020;122:106792.
- Canadinc D, Trehern W, Ma J, et al. Ultra-high temperature multi-component shape memory alloys. Scr Mater. 2019;158:83–87.
- Karaca HE, Acar E, Ded GS, et al. Microstructure and transformation related behaviors of a Ni45.3Ti29.7Hf20Cu5 high temperature shape memory alloy. Mater Sci Eng A. 2015;627:82–94.
- Cui J, Chu YS, Famodu OO, et al. Combinatorial search of thermoelastic shape-memory alloys with extremely small hysteresis width. Nat Mater. 2006;5:286–290.
- Zarnetta R, Takahashi R, Young ML, et al. Identification of quaternary shape memory alloys with near-zero thermal hysteresis and unprecedented functional stability. Adv Funct Mater. 2010;20:1917–1923.
- Zhang Z, James RD, Müller S. Energy barriers and hysteresis in martensitic phase transformations. Acta Mater. 2009;57:4332–4352.
- Bigelow GS, Garg A, Padula II SA, et al. Load-biased shape-memory and superelastic properties of a precipitation strengthened high-temperature Ni50.3Ti29.7Hf20 alloy. Scr Mater. 2011;64:725–728.
- Zou Y, Maiti S, Steurer W, et al. Size-dependent plasticity in an Nb25Mo25Ta25W25 refractory high-entropy alloy. Acta Mater. 2014;65:85–97.
- Kockar B, Atli KC, Ma J, et al. Role of severe plastic deformation on the cyclic reversibility of a Ti50.3Ni33.7Pd16 high temperature shape memory alloy. Acta Mater. 2010;58:6411–6420.
- Karaca HE, Saghaian SM, Basaran B, et al. Compressive response of nickel-rich NiTiHf high-temperature shape memory single crystals along the [111] orientation. Scr Mater. 2011;65:577–580.