Abstract
Permanent-magnet materials are critical components for green energy technologies, but the intrinsic trade-off between saturation magnetization and coercivity limits their achievable energy density. Here, a new concept of ordered structures is proposed to develop high-performance permanent magnets. This strategy enables a rare combination of high magnetization and high coercivity by introducing new magnetization reversal mechanisms associated with ordered structures. Implications and challenges of building ordered structures for strong magnets are discussed. This Perspective aims to draw the attention of materials research community to the emerging ordered magnets and to motivate active investigations on this topic for creating transformative magnets.
GRAPHICAL ABSTRACT
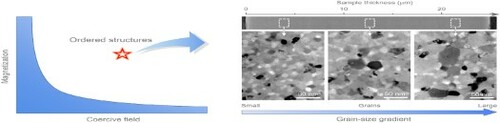
IMPACT STATEMENT
Engineering ordered structures opens up new opportunities to create strong magnets, in which unprecedentedly high properties could be achieved with less alloying content and critical elements.
Background
The compass invented around 1040 AD in ancient China is one of the earliest applications of magnets, in which a magnetic steel needle aligns itself with the Earth’s magnetic field when floated in water or suitably suspended. One can demonstrate the magnetic force field by using one chunk of permanent magnet to attract a piece of ferromagnet such as iron. The force-field strength is determined by the energy density of magnets, usually known as energy product, (BH)max. Magnets with larger (BH)max make magnetic devices smaller and more efficient, ranging from mobile phones and laptops to electric cars and wind turbines [Citation1].
Obtaining a large (BH)max requires a combination of high saturation magnetization (Ms) and high coercivity (Hc)—the reverse field strength needed to reduce the magnetization to zero; and Ms determines the theoretical limit of (BH)max for a magnet [Citation2]. However, the Ms and Hc usually cannot go hand in hand [Citation3,Citation4]. For example, iron (Fe) has the largest room-temperature saturation magnetization (21.6 kG) among ferromagnetic elements and an even larger value (23.5 kG) can be realized by combining Fe and cobalt (Co) into an Fe65Co35 alloy. Unfortunately, both Fe and Fe65Co35 have very small Hc due to their cubic crystal structure, which precludes the development of high energy products.
In the past century, the struggle for large Hc by combining Fe or Co with other elements (i.e. alloying) was the development way of permanent magnets [Citation5]. The milestones of such explorations were the discovery of Samarium-cobalt (Sm-Co) and Neodymium–iron–boron (Nd-Fe-B) rare-earth magnets in the 1960s and in the early 1980s, respectively. A high Hc beyond 30 kOe in Sm-Co magnets and Hc above 20 kOe in Nd-Fe-B magnets have been achieved, and Nd-Fe-B magnets exhibit the highest (BH)max ≈ 59 MGOe achieved to date. However, alloying unavoidably sacrifices the Ms of magnets, as a certain amount of nonmagnetic or weakly magnetic components are used, which limits the (BH)max that can be achieved for a magnet. This is the main reason why the (BH)max of permanent-magnet materials has reached a plateau over the past decades [Citation1,Citation5]. Moreover, alloying that increases the number of elements in magnets makes their recycling and sustainability more difficult, especially at the risk of resource exhaustion of scarce elements in nature such as rare-earth elements. In addition, use of the critical elements also increases the cost of magnets, limiting their widespread applications.
Is it possible to fabricate strong magnets with less alloying content and/or fewer critical elements? To answer this question, we need to deeply understand the role of alloying. The alloying of magnets mainly has two goals. The first one is to achieve the desired uniaxial crystal structures (i.e. tetragonal, hexagonal and rhombohedral) with both high Ms and large anisotropy field (Ha) that determines the physical upper limit of Hc [Citation5]. Rare-earth elements can significantly increase Ha due to asymmetrical 4f shells that lead to a large spin–orbit coupling. The other one is to engineer a microstructure that enables a metastable magnetized state to persist after the magnetization reaches saturation, by suppressing the nucleation of reverse domains and/or hindering the propagation of domain walls under reverse magnetic field. Introducing grain-boundary (GB) phase is the conventional approach to increase Hc, through improving GB structure to eliminate nucleation sites of reverse domains or by pinning of domain walls, but usually at the expense of Ms (Figure ). GB diffusion is another effective route to suppress magnetization reversal, which requires rather scarce and expensive heavy rare earths, e.g. dysprosium (Dy) [Citation5,Citation6].
Figure 1. Engineering strong magnets with ordered structures. The coercive field (coercivity) of permanent-magnet materials is generally enhanced by introducing grain-boundary (GB) phase with alloying at the expense of magnetization. Building ordered structures, e.g. spatial gradient in fine grain sizes with processing techniques can increase coercivity without sacrificing magnetization, making magnets strong and sustainable due to less use of alloying content and/or critical elements.
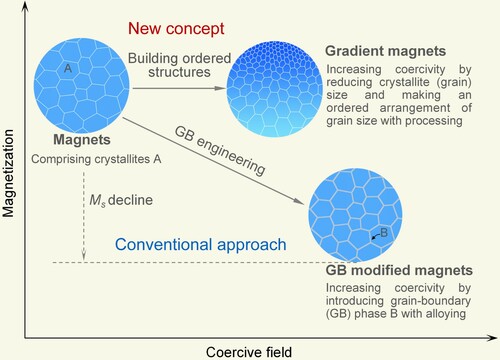
In fact, alloying is not the only way to tailor microstructures and processing techniques also have the potential to do so. For example, the grain size of Nd-Fe-B magnets has important impact on Hc, i.e. Hc increases as grain size decreases, and can be significantly reduced down to 1-3 μm by ball milling and helium jet milling without changing their chemical composition, which leads to an increase in Hc without sacrificing Ms [Citation6]. Unfortunately, further reducing grain size below 1 μm is prohibited with this method, as rare earth element is rather reactive and subject to oxidation in ultrafine Nd-Fe-B powders. Although it is possible to reduce the grain size of Nd-Fe-B magnets down to nanoscale, for example, reaching their single-domain critical size of ∼300 nm with the hot-deformation approach [Citation6,Citation7], the deformed magnets have a fairly inhomogeneous microstructure with randomly distributed deformation defects and grains that have a wide size distribution as compared to those in Nd-Fe-B sintered magnets. Such inhomogeneous microstructure makes their magnetization reversal more random and nonuniform, which limits the increase in Hc and/or worsens the squareness in demagnetization curve [Citation5], as defects including GBs are weak points for nucleation of reverse domains due to low magnetocrystalline anisotropy. During the past decades, tremendous efforts have been made to explore how to suppress nonuniform magnetization reversal in magnets [Citation5–8].
Emerging magnets with ordered structures
More recently, we found the random and nonuniform magnetization reversal can be suppressed by engineering an ordered arrangement of grain sizes, e.g. grain-size gradient in magnets [Citation9]. The fabricated gradient nanostructure exhibits a previously inaccessible directional magnetization reversal that enables an exciting combination of high Ms and high Hc (Figure ).
Nd2Fe14B/α-Fe gradient nanostructures were fabricated by solidifying simpler Nd-Fe-B ternary alloy melt with temperature gradient using the melt-spinning (MS) technique [Citation9]. The temperature gradient between the cooling side (CS) and free side (FS) of MS ribbons results in a gradual decrease in grain size from the FS to the CS for both Nd2Fe14B and α-Fe phases (Figure ). In addition to the grain-size gradient, α-Fe phase gradient can also be achieved by judiciously creating cluster structures in the alloy melt to facilitate heterogeneous nucleation.
Figure 2. Fabrication of gradient nanostructures. Grain-size gradient is achieved by solidifying alloy melt with temperature gradient using the melt-spinning (MS) technique. The temperature gradient between the free side (FS) and the cooling side (CS) of MS ribbons (see the left panel) yields a gradual decrease in grain size from the FS to the CS, i.e. grain-size gradient.
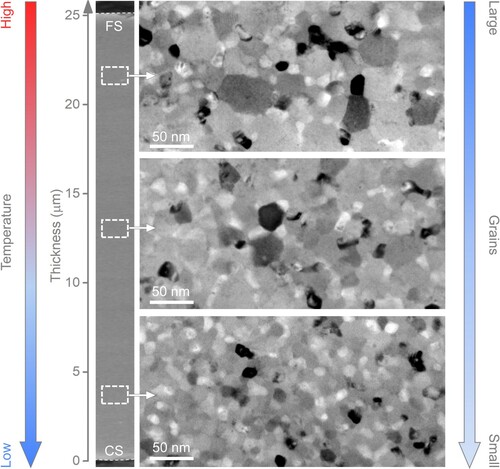
When a material with a random mixture of α-Fe and Nd2Fe14B nanograins is under reverse magnetic field, magnetization reversal occurs in a random and nonuniform manner at weak points such as defects and soft-magnetic α-Fe grains, usually accompanied by the cooperative reversal of clusters of grains. On the contrary, for a material with nano-grained gradient, magnetization reversal occurs in an ordered manner. It initiates in large α-Fe grains and then smaller grains reverse gradually along the gradient direction with increasing reverse fields [Citation9], due to enhanced exchange coupling between the hard and soft magnetic grains and high nucleation field for smaller grains [Citation4,Citation5]. This directional magnetization reversal can suppress the cooperative reversal of clusters of grains occurring in the material with a random mixture of nanograins due to gradually enhanced resistance to reversal, which enables a slower demagnetization process and high Hc. As such, the engineered gradient nanostructures show an exceptional combination of high Ms, high Hc, and large squareness in demagnetization curve, thus yielding the highest energy product (26 MGOe) obtained to date for isotropic magnets.
These discoveries that grain-size gradient has significant impacts on magnetization reversal and magnetic properties open up new opportunities to create strong magnets by engineering ordered structures, in which unprecedentedly high properties could be realized with less alloying content and/or fewer critical elements. For example, bulk nanocomposite magnets with ultrahigh energy products above 30 MGOe have been successfully fabricated by building layered ordered structures, with 20–30% less rare-earth content than pure rare-earth magnets [Citation10]. Less use of rare-earth elements makes magnets cheaper, more recyclable and sustainable.
Prospects and challenges
The concept of ordered structures is not limited to grain ordering. It can be extended to the variations in local chemical compositions/elements and the characteristics involved in the arrangement, distribution, dimensions, and orientations of other structural units such as GBs/interfaces, phases, mesoscale and macroscopic constituents.
Engineering such ordered structures at different scales—from the atomic to the macroscopic—would enable us to break the limitations of chemical elements and create transformative magnets with unprecedentedly high properties. The poor mechanical performance of intermetallic magnets such as low ductility might be improved by intentionally creating ordered structures, e.g. grain-size gradient that allows a superior combination of high strength and large ductility [Citation11–13]. Moreover, the property-variation window of magnets can be greatly broadened by judiciously introducing ordered structures, which enables us to tune magnetic properties at previously inaccessible dimensions. In this new dimension space, long-standing trade-off between conflicting properties could be disentangled and disruptive high-performance materials would be achieved.
Many challenges remain to create the emerging ordered magnets with revolutionary properties. First, new processing techniques need to be devised to build ordered structures in a controlled manner in bulk materials. One of the most challenging tasks is to develop processing techniques to construct multiple ordered structures at various scales, from the atomic scale to the macroscale, within one magnet. Such multi-scale ordered structures found in biological materials exhibit unprecedentedly high properties and functionalities, including electrical, chemical, mechanical, biological, sustainable and multifunctional properties [Citation14–16]. Moreover, establishing quantitative correlations between each structural unit in the ordered structure and magnetic properties is challenging and crucial for optimizing global properties of the ordered magnets. Both experiments and theoretical simulations as well as their combination are required for this goal. At present, simulating ordered structures at extremely-extended-multiple scales (e.g. from the atomic level to the macroscale) remains a tough challenge for existing methods, considering the computation power of current supercomputers. Therefore, new modelling approaches that connect these drastically different scales need to be developed to fully capture the relationship between the ordered structure and performance. All these are quite challenging tasks. But if we can overcome these technical and scientific challenges, the emerging ordered magnets could yield unprecedentedly high properties with less critical rare-earth elements, which is a worthwhile goal in itself.
Acknowledgements
The authors thank Y. T. Zhu, L. Lu and J. M. Liu for helpful discussion and L. Lou and Y. X. Hua for plotting Figures.
Disclosure statement
No potential conflict of interest was reported by the author(s).
Additional information
Funding
References
- Jones N. The pull of stronger magnets. Nature. 2011;472:22–23.
- Sellmyer DJ. Strong magnets by self-assembly. Nature. 2002;420:374–375.
- Zhang XY. Heterostructures: new opportunities for functional materials. Mater Res Lett. 2020;8:49–59.
- Li XH, Lou L, Song WP, et al. Novel bimorphological anisotropic bulk nanocomposite materials with high energy products. Adv Mater. 2017;29:1606430.
- Coey JMD. Perspective and prospects for rare earth permanent magnets. Engineering. 2020;6:119–131.
- Hono K, Sepehri-Amin H. Prospect for HRE-free high coercivity Nd-Fe-B permanent magnets. Scripta Mater. 2018;151:6–13.
- Yue M, Zhang XY, Liu JP. Fabrication of bulk nanostructured permanent magnets with high energy density: challenges and approaches. Nanoscale. 2017;9:3674–3697.
- Coey JMD. Hard magnetic materials: a perspective. IEEE Trans Magn. 2011;47:4671–4681.
- Lou L, Li YQ, Li XH, et al. Directional magnetization reversal enables ultrahigh energy density in gradient nanostructures. Adv Mater. 2021;33:2102800.
- Huang GW, Li XH, Lou L, et al. Engineering bulk, layered, multi-component nanostructures with high energy density. Small. 2018;14:1800619.
- Zhu YT, Ameyama K, Anderson PM, et al. Heterostructured materials: superior properties from hetero-zone interaction. Mater Res Lett. 2021;9:1–31.
- Li XY, Lu L, Li JG, et al. Mechanical properties and deformation mechanisms of gradient nanostructured metals and alloys. Nat Rev Mater. 2020;5:706–723.
- Lu K. Stabilizing nanostructures in metals using grain and twin boundary architectures. Nat Rev Mater. 2016;1:16019.
- Wegst UGK, Bai H, Saiz E, et al. Bioinspired structural materials. Nature Mater. 2015;14:23–36.
- Meyers MA, McKittrick J, Chen PY. Structural biological materials: critical mechanics-materials connections. Science. 2013;339:773–779.
- Katiyar NK, Goel G, Hawi S, et al. Nature-inspired materials: emerging trends and prospects. NPG Asia Mater. 2021;13:56.