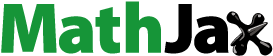
Abstract
Al matrix composites with the strain-delocalization effect were fabricated by spark plasma sintering using graphene nanosheets decorated with Cu nanoparticles (Cu NPs@GNS) as reinforcement. The Joule heat, thermal stress-induced dynamic crystallization and the abnormal grain growth facilitate shorter diffusion paths of Cu atoms in the Al matrix thus generating a supersaturated solid solution near the GNS/Al interface. Thereby, the intragranular plate-like -Al2Cu was generated in the adjacent grains of GNS so that the strain-delocalization effect was realized. The combination of excellent strain hardening ability, transgranular fracture mode and elongated crack path results in strength-ductility synergy.
IMPACT STATEMENT
Al matrix composites reinforced by graphene nanosheets decorated with Cu nanoparticles fabricated by spark plasma sintering was applied to realize simple and rapid fabrication of composites with strain-delocalization effect.
GRAPHICAL ABSTRACT
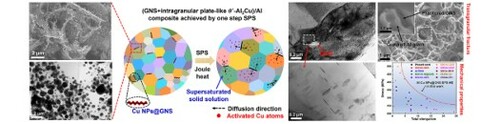
Al matrix composites (AMCs), due to their low density, extraordinary comprehensive properties and good adaptability to the harsh service environment, are now considered promising materials for structural and functional applications in many fields [Citation1]. Especially graphene, with its outstanding functional and mechanical properties, was considered an ideal reinforcement for the Al matrix [Citation2]. Great efforts have been made to take good advantage of graphene in Al for making super composites [Citation3–5]. However, the common results exhibited limited strength enhancement in absolute values, while the elongation of the composite was sacrificed to a large level. Generally, the low strength or ductility of Al-graphene composites was triggered by the agglomeration of graphene nanosheets and more importantly ascribed to the interface-related problems [Citation6,Citation7]. It is worth noting that the significant difference in thermal expansion coefficient between reinforcement and Al matrix leads to a high-level stress concentration [Citation8], causing an accidental fracture and, finally, an early failure of composites. The key idea to tackle this problem relies on strain delocalization to alleviate the internal stress near the interface. One possible way is to apply severe mechanical blending mixing, such as ball milling, to incorporate dispersed reinforcements into the grain interiors, thus eliminating the intergranular thermal stress [Citation9]. However, graphene nanosheets with a large aspect ratio could be subjected to severe structural damage during the mixing process. Another promising strategy aims to obtain densely dispersed intragranular intermetallic compounds (IMC) by diffusion and precipitation to balance the high-level stress in grain boundaries [Citation10]. A typical example could be the plate-like -Al2Cu in Al–Cu alloys, featured in its large aspect ratio and the resulted extraordinary strain hardening capability during matrix deformation [Citation10,Citation11]. Nonetheless, the knotty drawback is that the high-temperature heat treatment process would accelerate the interfacial reaction of Al and graphene to produce the hazardous phase of Al4C3, which damaged the structural integrity of graphene and lowered the overall properties of the composites [Citation12]. Hence, it has remained an open question how to maintain the structural integrity of graphene and relieve the stress concentration problem to achieve a balanced strength-ductility relationship at the same time.
Theoretically, it is possible to stimulate diffusion-precipitation process under a mild condition if the reaction kinetics could be improved. Herein, we selected graphene nanosheets decorated with Cu nanoparticles (Cu NPs@GNS) as the reinforcement and applied spark plasma sintering (SPS), which is a widely-used method for rapid consolidation to obtain bulk composites. The spark discharge, Joule heating and electrical diffusion between powder particles accelerate the Cu element to diffuse into the Al matrix adjacent to the GNS. Subsequently, the fast-cooling rate of SPS contributes to precipitation segregation and yields to uniformly-dispersed intragranular -Al2Cu. Without solution and ageing treatment, the structural integrity of graphene was well protected during the whole process, and this helped achieve a superb strength-ductility properties in the final products. This work provides a kinetic-based design and the experimental basis for realizing the simple and rapid synthesis of AMCs with a strain delocalization effect.
The Cu NPs@GNS were prepared by the in-situ synthesis assisted by the NaCl template [Citation13]. As shown in Figure S1, the Cu NPs in the size of 20–100 nm are dispersed on the surface of GNS. In Figure S2(c), the thermogravimetry and differential scanning calorimetry curve show that the mass fraction of Cu NPs in Cu NPs@GNS is 66.2 wt.%. The characterization and analysis of Cu NPs@GNS powders are provided in Supplementary Material. Theoretically, the small-sized metal particles possess the high chemical activity and lower the energy barrier to diffuse into the Al matrix. After ball milling with Al powders followed by SPS sintering and hot extrusion, the densified bulk composites with 2.16 wt.% Cu NPs@GNS reinforcement was obtained (Al–Cu NPs@GNS-SPS-HE). The detailed fabrication and characterization procedure are observed in Supplementary Material. The typical microstructures of Al–Cu NPs@GNS-SPS-HE composite are presented in . GNS mainly exists at the grain boundary rather than in the grain interior ((a)). The Cu NPs decorated on the surface of GNS in the reinforcement powders no longer existed. Alternatively, the intragranular plate-like phase with an average lateral size of about 200 nm was validated in the grains adjacent to GNS ((b)), the position relation is schematically illustrated in (k), which is similar to the of -Al2Cu in Al–Cu alloy after artificial ageing [Citation14,Citation15]. To verify and determine the composition of the plate-like phase, energy-dispersive spectroscopy (EDS) was applied to detect its elemental composition. Plates with different visual fields were selected for characterizing, as indicated by the bright-field of scanning TEM (STEM) images displayed in (d) and (f). In (e) and (g), the EDS line scans indicate that the plates contain only Al and Cu, suggesting that Al–Cu precipitates were produced during the sintering process. The high-resolution TEM (HRTEM) image in (h) and (i) verify
-Al2Cu by the FFT images in the insets. Moreover, the FFT result is shown in (h) and (i) also revealed a latent orientation relationship between
-Al2Cu and Al matrix as
//
&[
]Al2Cu//[
]Al,
//
& [
]Al2Cu//[
]Al and
//
&[
]Al2Cu//[
]Al. Additionally, the parallel planes can be verified using the compound stereographic projection with a Wulff net based on the orientation relationships (Figure S3) [Citation16]. Besides, based on the mismatch theory, the limited lattice misfit between
and
suggests a coherent and robust interface bonding between
-Al2Cu and Al [Citation17]. As reported in the previous work, the
-Al2Cu distributed in the grain interiors can effectively strengthen the matrix and facilitate the storage of many dislocations during the deformation process [Citation18]. Therefore, this unique microstructure enables intragranular
-Al2Cu traps mobile dislocations near the Al-GNS interface during the deformation process, thus achieving the strain delocalization effect. Moreover, the interface of Al-GNS was also observed ((c)), exhibiting that a clean interface structure was maintained with an integrated GNS structure. It indicates that the energy was dissipated during the alloying process to inhibit the reaction between GNS and Al, which is different from what is reported in the literature [Citation19,Citation20]. The underlying mechanism could be that the activation energy of forming Al2Cu is lower than that of Al4C3, which significantly weakens the Al-C interfacial reaction, thus prohibiting the growth of Al4C3 [Citation21].
Figure 1. (a–c) TEM images of Al–Cu NPs@GNS-SPS-HE composite; bright-field STEM images (d and f), the corresponding EDS line scan spectra of Al and Cu elements (e and g); (h and i) HRTEM characterization of -Al2Cu and interface; (k) Schematic diagram of the microstructure of Al–Cu NPs@GNS-SPS-HE sample.
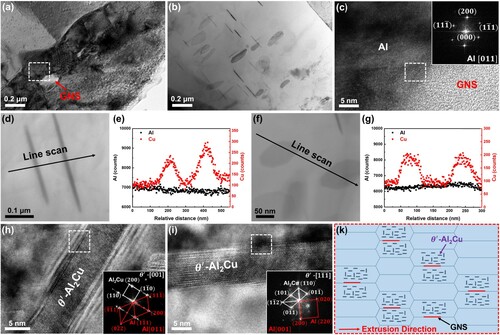
To investigate the abnormal formation mechanism of -Al2Cu in the Al–Cu NPs@GNS-SPS-HE composite, we fabricated composite by a commonly-used cold-pressing, sintering and hot-extrusion (Al–Cu NPs@GNS-CPS-HE) at the same sintering temperature for comparison. The result demonstrated that different sintering techniques lead to distinct microstructures. As presented in (a) and (b), the Cu NPs@GNS hybrid structure remained intact in the Al–Cu NPs@GNS-CPS-HE composite after cold pressing, sintering and hot extrusion, which demonstrates that the Cu NPs on the surface of GNS can inhibit the interfacial reaction between Al and GNS. Combining the HRTEM interface structure characterization in (c), only
-Al2Cu nanoparticles formed due to the in-situ reaction between Cu NPs and Al [Citation22], the morphology of which is different from the plate-like
-Al2Cu generated in Al–Cu NPs@GNS-SPS-HE composite ((b)).
Figure 2. (a–c) TEM images and (d) schematic diagram of the microstructure of Al–Cu NPs@GNS-CPS-HE composite; (e–g) the microstructure of solution and ageing Al–Cu NPs@GNS-CPS-HE composite.
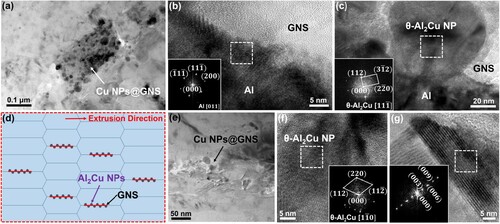
The above results lead us to revisit the sintering mechanism of SPS, in which process the unique precipitation phase of -Al2Cu was formed. The different reaction processes of the two composites are illustrated in for comparison. Benefited by the direct contact between Cu NPs@GNS and Al powders during the preordered ball milling step, Joule heat was generated instantly in the gap of Al particle and Cu NPs@GNS upon the energizing of the direct current pulse due to the discharge effect [Citation23]. This effect caused Cu NPs to escape from the surface of GNS and rapidly diffuse into grains adjacent to GNS to form supersaturated solid solutions. Holding at a high temperature, the high elastic strain caused by the thermal stress induced dynamic crystallization and the abnormal grain growth of the Al matrix [Citation24], which could be validated by the EBSD recrystallization analysis in Figure S4(b) and (d). This effect also facilitates shorter diffusion paths of Cu atoms in Al and thus the formation of a supersaturated solid solution near the GNS/Al interface [Citation25]. Generally, the precipitates are related to heat treatment time and cooling rate in Al alloy. For Al–Cu NPs@GNS-SPS-HE composite, the cooling process is shorter due to the high cooling rate. Meanwhile, GNS adjacent to Al grains can accelerate the precipitation behavior of the Al–Cu phase and shorten the precipitation process [Citation26]. Hence, only metastable
-Al2Cu was nucleated and distributed in the grains adjacent to GNS under the high-speed cooling rate. Moreover, a more significant nucleated
-Al2Cu leads to the rapid decrease in Cu supersaturation, which can further inhibit the precipitation of the stable phase
-Al2Cu. Thus, the
-Al2Cu was gradually precipitated and eventually dispersed evenly in the whole grain interiors.
Figure 3. The schematic of reaction processes in Al–Cu NPs@GNS-SPS-HE and Al–Cu NPs@GNS-CPS-HE composites during sintering.
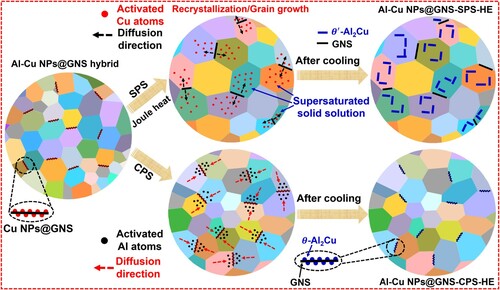
On the other hand, compared with the Al–Cu NPs@GNS-SPS-HE composite before hot extrusion, the EBSD result of Al–Cu NPs@GNS-CPS-HE composite before hot extrusion in Figure S4(a) and (c) indicates an 11% decrease in the relative recrystallization fraction and a 43% reduction in the average grain size. So it validates the speculation mentioned above that the unique sintering mechanism of SPS was the main cause of the abnormal precipitation of -Al2Cu. Alternatively, the insufficient driving force for Cu diffusion in the regular cold-pressing and sintering merely yields to interact with the Al matrix at the Al-GNS interface. During the sintering process, the interdiffusion of Cu and Al atoms resulted in forming a Cu-rich zone at the interface. Because of the long holding time 6 times that of SPS, and the much slower cooling rate, the Al–Cu compounds nucleated and developed into the equilibrium state. Hence, the inter-diffusion products of stable
-Al2Cu NPs were only discerned near the interface. After T6 heat treatment, the number of Cu NPs on the surface of GNS was significantly reduced ((e)), suggesting that part of the Cu NPs was dissolved into the matrix after ong-time heating at 520 °C. Unexpectedly, only Al–Cu IMC products,
-Al2Cu NPs, were detected in the composite ((f)). Meanwhile, the Al4C3 formed during the high-temperature heat-treatment was also discovered ((g)), which plays a detrimental role to the mechanical properties of composite [Citation12]. Comparatively, the variation of the grain structures after hot-extrusion of the SPS and CPS composites becomes negligible, as indicated by the EBSD results in Figure (a) and (b). Compared to the microstructure of Al–Cu NPs@GNS-SPS-HE composite, the stress and strain are mainly concentrated at the Al-GNS interface during the deformation process, thus leading to negligible strain partitioning in the adjacent grains at the Al-GNS interface.
Figure 4. EBSD inverse pole figures of (a) Al–Cu NPs@GNS-SPS-HE and (b) Al–Cu NPs@GNS-CPS-HE composites; (c) the engineering stress-strain curves, (d) the true stress-true strain curves, (e) the strain hardening rate curves and (f) strength and ductility of Al–Cu NPs@GNS-SPS-HE composite prepared in this work compared with AMCs reinforced with graphene and other alloy-based composites reported in previous studies.
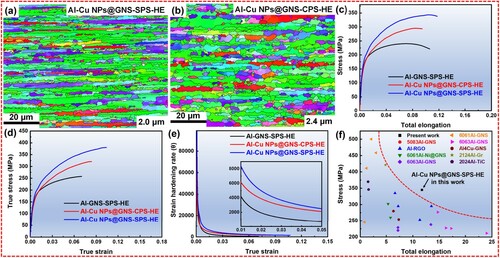
To emphasize the substantial improvement in mechanical property of Al–Cu NPs@GNS-SPS-HE composite with a strain delocalization effect, the curves of the same amount of GNS-reinforced AMCs (Al-GNS-SPS-HE) and Al–Cu NPs@GNS-CPS-HE composites are presented for comparison. In Figure S2(b), (d) and (e), the TEM images and Raman spectrum show that the GNS also exhibits a nanosheet structure with fewer defects. The mechanical properties of composites are presented in (c)–(e) and Figure S6(b). As expected, the Al–Cu NPs@GNS-SPS-HE composite possesses the highest tensile strength, total elongation, uniform elongation and strain hardening ability compared with two other composites. For composites, interface, grain boundary and precipitates can be used as dislocation storage sites to promote strain hardening. It has been reported that -Al2Cu distributed in grain interiors can effectively store dislocation and improve the strain hardening behavior of the matrix [Citation10]. Combined with the microstructure observation of different composites, the difference in strain hardening ability is mainly induced by the distribution of Al2Cu. As shown in Figure S5, in the Al-GNS-SPS-HE composite, the structure of GNS was destroyed and reacted with Al to form Al4C3, thus leading to much weaker strength and elongation than that of Al–Cu NPs@GNS-SPS-HE composite. In contrast, the mechanical properties of Al–Cu NPs@GNS-CPS-HE composite are enhanced to a limited extent by interfacial modification. Moreover, it is validated that the tensile strength of the Al–Cu NPs@GNS-CPS-HE composite exhibits scarce enhancement after heat treatment, suggesting a negligible strengthening effect of interfacial Al2Cu NPs (Figure S6).
To explain the improved mechanical properties of Al–Cu NPs@GNS-SPS-HE composite were caused by the distribution of Al–Cu precipitates, the corresponding Cu NPs particles were added into the Al matrix to prepare Al–Cu alloy by SPS and hot extrusion (Al–Cu-SPS-HE alloy). The microstructure and mechanical property of Al–Cu-SPS-HE alloy is described in Figure S7 and Support information. After observation, it can be deduced that the different properties between Al–Cu NPs@GNS-CPS-HE and Al–Cu NPs@GNS-SPS-HE are more dependent on the microstructure. In (f), Al–Cu NPs@GNS-SPS-HE composite possesses a competitive strength-ductility synergy compared with other AMCs, such as Al-RGO [Citation27], 2xxx Al alloy-GNS [Citation28,Citation29], 6xxx (or 5xxx) Al alloy-GNS [Citation19,Citation20,Citation30–32] and 2024Al alloy-TiC [Citation33]. Because of the similar grain structure (recrystallization, Kernel Average Misorientation distribution and Schmidt factor) of Al–Cu NPs@GNS-SPS-HE and Al–Cu NPs@GNS-CPS-HE composites (Figure S8), the role of delicate IMC microstructure is highlighted in this work in achieving superior mechanical properties of composites.
The fracture morphologies can be used to explain better the variation in strength and ductility of the different composites. In general, the macroscopic fracture surface of all the three composites demonstrates typical plastic fracture features with coarse and deep dimples (Figure S9(a)–(c)). However, the enlarged view of the fracture surface tells a different story. For the Al-GNS-SPS-HE composite, an obvious GNS pull-out phenomenon can be detected at the bottom of a dimple ((a)), which indicates that weak interfacial bonding causes the Al matrix to be torn apart along with the Al-GNS interface and finally leads to a prefailure of the composite. In contrast, the cracked Cu NPs@GNS can be found inside the dimples of Al–Cu NPs@GNS-CPS-HE composite thanks to the robust interfacial bonding of Al and GNS improved by -Al2Cu ((b)). Furthermore, a more interesting phenomenon can be found for the magnified fracture surface of Al–Cu NPs@GNS-SPS-HE composite. As shown in (c), the fractured GNS exists in the dimples but remained in intimate contact with the adjacent torn grains, which evidenced the transformation of the fracture mode into a transgranular type. The crack propagates through the Al grain and ends upon reaching the GNS/Al interface, resulting in an obvious crack deflection and passivation characteristic, which benefits to an improved fracture elongation [Citation16,Citation34]. Meanwhile, the simultaneous fracture of GNS and Al grains was also found in other interfacial regions of the fracture surface of the composite (Figure S9(d)-(f)), which is believed to be the universal character in this composite. The fracture modes of composites can be better understood in a schematic diagram, as shown in (d)–(f).
Figure 5. SEM images of fracture surface for (a) Al-GNS-SPS-HE, (b) Al–Cu NPs@GNS-CPS-HE and (c) Al–Cu NPs@GNS-SPS-HE; diagrammatic drawing of fracture process for (d) Al-GNS-SPS-HE, (e) Al–Cu NPs@GNS-CPS-HE and (f) Al–Cu NPs@GNS-SPS-HE composites. TEM images of (g–h) Al–Cu NPs@GNS-SPS-HE and (i and j) Al–Cu NPs@GNS-CPS-HE composites after tensile test.
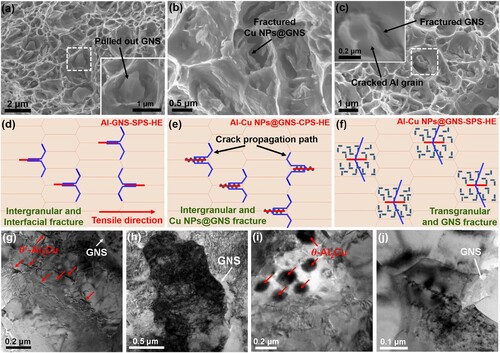
To better explain the reasons leading to the different fracture modes of the composites, the TEM microstructure of composites after the tensile test was analyzed as well. For Al–Cu NPs@GNS-SPS-HE composite, many dislocations and deformed Al microstructures were observed near -Al2Cu in (g), which can prompt the strain hardening process of the Al–Cu NPs@GNS-SPS-HE composite to conduce to obtaining the high strength and considerable ductility simultaneously. Therefore, during the process of deformation, the deformation strain/stress gradient would be concentrated not only at the Al-GNS interface but also around
-Al2Cu. As the plastic deformation proceeded, the strength of the grain region adjacent to GNS containing
-Al2Cu hardened gradually. Hence, this process induced dislocations trapped in the adjacent grains of GNS rather than just piled up near the Al-GNS interface, which helps relieve the interfacial stress concentration ((h)). This plastic deformation mode could postpone the strain localization of the micro-cracks near the Al-GNS interface, which restrained the instability and propagation of the crack [Citation35].
In addition, the synergistic distribution effect of GNS and -Al2Cu also leads to stress redistribution near the crack tip during fracture. The transgranular fracture type indicates it consumed more energy for cracks moving forward, thus blunting the convergence of microcracks. A schematic diagram of the deformation process is shown in Figure S10. The resulting stress redistribution would cause larger regions to participate in the deformation, and the cracks would be nucleated from a larger region instead of just being concentrated at the grain boundaries and interfaces [Citation36]. In this way, the cracks were initiated from the areas in the grain interiors with high stress and finally converged and evolved into a transgranular fracture. This fracture mode can also absorb more energy during crack propagation and thus postpone the formation of main cracks, thus improving the plastic deformation capability of composite [Citation13,Citation37]. As a result, dislocation strengthening and load transfer play important roles in enhancing the mechanical properties [Citation6,Citation10]. In contrast, the dislocations and deformation regions were mainly concentrated near the interface of Al and Cu NPs@GNS for Al–Cu NPs@GNS-CPS-HE composite, as shown in (i) and (j). Thereby, dislocation strengthening plays a negligible contribution during deformation.
To conclude, the AMCs reinforced by Cu NPs@GNS with tailored strain-delocalization effect have been successfully fabricated by a simple and rapid method using Cu NPs@GNS as reinforcement and the SPS technology. Thanks to the unique sintering mechanism of SPS, uniform plate-like -Al2Cu could be produced directly during the sintering process without heat treatment. The formation of intragranular nanophases not only effectively blocks dislocation movement, thus contributing to a significant dislocation strengthening effect, but also relieves the severe stress concentration near the graphene/Al interface and leads to transgranular fracture mode to achieve a train-delocalization effect. Meanwhile, the Cu-diffusion effect also prohibits the formation of hazardous Al4C3. As a result, a balanced strength of ∼340 MPa and fracture elongation of ∼11% were achieved simultaneously. This work provides a promising and facile strategy for designing and preparing advanced AMCs with optimized overall mechanical properties.
Supplemental Material
Download MS Word (28.2 MB)Disclosure statement
No potential conflict of interest was reported by the author(s).
Additional information
Funding
References
- Garg P, Jamwal A, Kumar D, et al. Advance research progresses in aluminium matrix composites: manufacturing & applications. J Mater Res Technol. 2019;8(5):4924–4939.
- Li Z, Guo Q, Li ZQ, et al. Enhanced mechanical properties of graphene (reduced graphene oxide)/aluminum composites with a bioinspired nanolaminated structure. Nano Lett. 2015;15(12):8077–8083.
- Tjong SC. Recent progress in the development and properties of novel metal matrix nanocomposites reinforced with carbon nanotubes and graphene nanosheets. Mater Sci Eng R Rep. 2013;74(10):281–350.
- Zhang X, Zhao NQ, He CN. The superior mechanical and physical properties of nanocarbon reinforced bulk composites achieved by architecture design-A review. Prog Mater Sci. 2020;113:100672.
- Yang M, Liu Y, Fan TX, et al. Metal-graphene interfaces in epitaxial and bulk systems: a review. Prog Mater Sci. 2020;110:100652.
- Yang LZ, Zhou BZ, Ma LS, et al. Architectured interfacial interlocking structure for enhancing mechanical properties of Al matrix composites reinforced with graphene nanosheets. Carbon N Y. 2021;183:685–701.
- Xu R, Tan ZQ, Xiong DB, et al. Balanced strength and ductility in CNT/Al composites achieved by flake powder metallurgy via shift-speed ball milling. Compos A: Appl Sci Manuf. 2017;96:57–66.
- Yang M, Weng L, Zhu HX, et al. Simultaneously enhancing the strength, ductility and conductivity of copper matrix composites with graphene nanoribbons. Carbon N Y. 2017;118:250–260.
- Han TL, Wang FC, Li JJ, et al. Simultaneously enhanced strength and ductility of Al matrix composites through the introduction of intragranular nano-sized graphene nanoplates. Compos Part B-Eng. 2021;212:108700.
- Teixeira JD, Bourgeois L, Sinclair CW, et al. The effect of shear-resistant, plate-shaped precipitates on the work hardening of Al alloys: towards a prediction of the strength-elongation correlation. Acta Mater. 2009;57(20):6075–6089.
- Santos-Güemes R, Bellón B, Esteban-Manzanares G, et al. Multiscale modelling of precipitation hardening in Al-Cu alloys: dislocation dynamics simulations and experimental validation. Acta Mater. 2020;188:475–485.
- Bartolucci SF, Paras J, Rafiee MA, et al. Graphene-aluminum nanocomposites. Mat Sci Eng A. 2011;528(27):7933–7937.
- Zhang X, Shi CS, Liu EZ, et al. Effect of interface structure on the mechanical properties of graphene nanosheets reinforced copper matrix composites. ACS Appl Mater Inter. 2018;10(43):37586–37601.
- Gao YH, Yang C, Zhang JY, et al. Stabilizing nanoprecipitates in Al-Cu alloys for creep resistance at 300°C. Mater Res Lett. 2019;7(1):18–25.
- Gao YH, Guan PF, Su R, et al. Segregation-sandwiched stable interface suffocates nanoprecipitate coarsening to elevate creep resistance. Mater Res Lett. 2020;8(12):446–453.
- Rong XD, Zhang X, Zhao DD, et al. In-situ Al2O3-Al interface contribution towards the strength-ductility synergy of Al-CuO composite fabricated by solid-state reactive sintering. Scr Mater. 2021;198:113825.
- Wang FC, Li JJ, Shi CS, et al. Orientation relationships and interface structure in MgAl2O4 and MgAlB4 co-reinforced Al matrix composites. ACS Appl Mater Inter. 2019;11(45):42790–42800.
- Milligan B, Ma D, Allard L, et al. Crystallographic orientation-dependent strain hardening in a precipitation-strengthened Al-Cu alloy. Acta Mater. 2021;205:116577.
- Shao PZ, Chen GQ, Ju BY, et al. Effect of hot extrusion temperature on graphene nanoplatelets reinforced Al6061 composite fabricated by pressure infiltration method. Carbon N Y. 2020;162:455–464.
- Shao PZ, Yang WS, Zhang Q, et al. Microstructure and tensile properties of 5083 Al matrix composites reinforced with graphene oxide and graphene nanoplates prepared by pressure infiltration method. Compos A: Appl Sci Manuf. 2018;109:151–162.
- Han TL, Liu EZ, Li JJ, et al. A bottom-up strategy toward metal nano-particles modified graphene nanoplates for fabricating aluminum matrix composites and interface study. J Mater Sci Technol. 2020;46:21–32.
- Li HY, Chen WG, Dong LL, et al. Interfacial bonding mechanism and annealing effect on Cu-Al joint produced by solid-liquid compound casting. J Mater Process Tech. 2018;252:795–803.
- Queudet H, Lemonnier S, Barraud E, et al. One-step consolidation and precipitation hardening of an ultrafine-grained Al-Zn-Mg alloy powder by spark plasma sintering. Mat Sci Eng A. 2017;685:227–234.
- Shi HL, Gan WM, Esling C, et al. Elastic strain induced abnormal grain growth in graphene nanosheets (GNSs) reinforced copper (Cu) matrix composites. Acta Mater. 2020;200:338–350.
- Liu X, Zhao QL, Jiang QC. Effects of cooling rate and TiC nanoparticles on the microstructure and tensile properties of an Al-Cu cast alloy. Mat Sci Eng A. 2020;790:139737.
- Han TL, Wang FC, Li JJ, et al. Effect of GNPs on microstructures and mechanical properties of GNPs/Al-Cu composites with different heat treatment status. J Mater Sci Technol. 2021;92:1–10.
- Jiang YY, Tan ZQ, Xu R, et al. Tailoring the structure and mechanical properties of graphene nanosheet/aluminum composites by flake powder metallurgy via shift-speed ball milling. Compos A: Appl Sci Manuf. 2018;111:73–82.
- Pu BW, Sha JW, Liu EZ, et al. Synergistic effect of Cu on laminated graphene nanosheets/AlCu composites with enhanced mechanical properties. Mat Sci Eng A. 2019;742:201–210.
- El-Ghazaly A, Anis G, Salem HG. Effect of graphene addition on the mechanical and tribological behavior of nanostructured AA2124 self-lubricating metal matrix composite. Compos A: Appl Sci Manuf. 2017;95:325–336.
- Wu GH, Yu ZH, Jiang LT, et al. A novel method for preparing graphene nanosheets/Al composites by accumulative extrusion-bonding process. Carbon N Y. 2019;152:932–945.
- Yu ZH, Yang WS, Zhou C, et al. Effect of ball milling time on graphene nanosheets reinforced Al6063 composite fabricated by pressure infiltration method. Carbon N Y. 2019;141:25–39.
- Liu G, Zhao NQ, Shi CS, et al. In-situ synthesis of graphene decorated with nickel nanoparticles for fabricating reinforced 6061Al matrix composites. Mat Sci Eng A. 2017;699:185–193.
- Yang HB, Tian S, Gao T, et al. High-temperature mechanical properties of 2024 Al matrix nanocomposite reinforced by TiC network architecture. Mat Sci Eng A. 2019;763:138121.
- Roy U, Zhou M. A computational framework for predicting the fracture toughness of metals as function of microstructure. J Mech Phys Solids. 2020;142:103955.
- Tan Z, Wang L, Xue YF, et al. A multiple grain size distributed Al-based composite consist of amorphous/nanocrystalline, submicron grain and micron grain fabricated through spark plasma sintering. J Alloy Compd. 2018;737:308–316.
- Wu H, Fan GH, Huang M, et al. Fracture behavior and strain evolution of laminated composites. Compos Struct. 2017;163:123–128.
- Zhang X, Shi CS, Liu EZ, et al. Achieving high strength and high ductility in metal matrix composites reinforced with a discontinuous three-dimensional graphene-like network. Nanoscale. 2017;9(33):11929–11938.