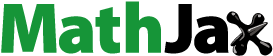
Abstract
In this work, we report a counter-intuitive activation of abnormal grain growth (AGG) in randomly-oriented fine grains (FGs) in an L-PBF Al–Mg–Sc–Zr alloy, which is unlikely from perspectives of curvature-driven grain growth, crystallographic texture or strain-induced boundary migration. The observed spontaneous AGG is understood in light of the growth instability of an arbitrary grain in an evolving particle-pinned polycrystalline aggregation. A generalized criterion for AGG is hence proposed, which efficaciously explains the observed susceptibility of FGs to AGG, the presence of multiple AGG activation sites, and the asynchrony of AGG activation.
1. Introduction
In recent years, additive manufacturing of high-performance aluminium alloys using laser powder bed fusion (L-PBF) technique has received extensive attention [Citation1–4]. Sc/Zr-modified aluminium alloys are hence of great interest as they provide good L-PBF processability and excellent mechanical properties [Citation5–13]. L-PBF processing of these alloys are known to create a ‘bi-modal’ heterogenous structure, consisting of columnar coarse grains (CGs) and equiaxed fine grains (FGs). However, to exploit the precipitation hardening of Al3 (Sc,Zr) nanoprecipitates, Sc/Zr-containing alloys needs to be aged at temperature typically exceeding 300°C, reaching as high as 500°C [Citation5,Citation8,Citation12,Citation14–19]. Tailoring the microstructure and performance of these alloys hence require a thorough understanding on the concurrent response of the heterogenous grain structure during thermal exposure at elevated temperatures, which is still lack in literature.
In general, grain growth in polycrystalline materials may occur either as a uniform growth of the entire grain structure (normal grain growth, NGG), or as a discontinuous growth of a minority of grains at the expense of others (abnormal grain growth, AGG) [Citation20–22]. Naturally, the activation of AGG suggests that the selected grains have acquired a growth advantage over their counterparts. This could originate from a ‘curvature’ advantage due to larger size [Citation20,Citation23–25]; or from a favourable grain boundary energy or mobility often correlated with crystallographic texture [Citation25–29]; or due to strain-induced boundary migration (SIBM) [Citation30–34]. In this light, AGG activation seems unlikely for FGs in L-PBF Al–Mg–Sc–Zr alloys: FGs are not only much smaller in size than CGs, but also have much weaker crystallographic textures than CGs. [Citation6,Citation10,Citation35]; FGs are also reported to be less capable in dislocation storage [Citation9,Citation10], limiting their potential for strain-induced boundary migration (SIBM).
In this work, however, we report a counter-intuitive AGG activation in randomly-oriented FGs of a typical L-PBF processed Al–Mg–Sc–Zr alloy. To understand the observed AGG, we generalize P. R. Rios's idea and discuss the grow instability of arbitrary grain in an arbitrarily evolving particle-pinned polycrystalline aggregation. Our generalized reasoning satisfactorily explains the observed susceptibility of FGs to AGG, asynchrony AGG activation and multiple sites of AGG activation.
2. Materials and methods
Pre-alloyed commercial feedstock powder (Bright Laser Technologies Co. Ltd., Xi’an, China) with chemical composition Al-4.31Mg–0.65Sc–0.22Zr–0.24Mn–0.12Ti (wt.%) is used in the present work. All specimens are built by L-PBF on a 3D Systems ProX DMP 200 device equipped with DMP ProX Manufacturing control software. A hexagonal checkerboard scanning strategy with 90° interlayer rotation is employed. Operating laser power, laser scanning speed, hatching distance and layer thickness are set at 252 W, 500 mm/s, 90 and 30 µm, respectively. L-PBF as-built specimens are first direct-aged in air furnace at 325°C for 4 h to introduce nanoscale Al3 (Sc, Zr) precipitates, followed by immediate water quenching, then subjected to thermal exposure in air furnace either at elevated temperature of 500°C for 2–24 h or at a lower temperature of 300°C for 96 h.
Grain structure of the as-built, direct-aged and thermal-exposed specimens are investigated by electron backscattered diffraction (EBSD) technique using a TESCAN LYRA 3 scanning electron microscope (SEM) device (with Oxford Instruments Nordlys Max 3 EBSD detector). To better reveal the characteristic bi-modal grain structure, EBSD characterization is conducted on specimen surfaces parallel to L-PBF building direction. EBSD data analysis and visualization are performed using HKL Channel 5 software.
Nanoscale Al3 (Sc, Zr) precipitates after direct ageing at 325°C/4 h or thermal exposure at 500°C/2 h are characterized by transmission electron microscopy (TEM) using FEI Talos F200X and F200X G2 device, both operating at 200 kV. TEM foils parallel to L-PBF building direction with 3 mm in diameter are prepared first by mechanical thinning, followed by twin-jet electropolishing using 30 vol. % nitric acid methanol solution at approx. −30°C and ion milling on a Gatan PIPS 695 device.
3. Results
A typical bi-modal grain structure is observed from the L-PBF as-built specimen (Figure ), with CGs distributed near the centre of each fan-shaped melt-pool and interconnected FG belt of approximately 5–15 µm width distributed near the melt pool boundaries. Mean grain diameter of overall grain structure and FG region are determined to be 1.49 and 0.70 µm, respectively. The mean aspect ratio of equiaxed FGs is determined to be 1.55. Grain boundary misorientation profile in FG region is very close to the well-known Mackenzie distribution [Citation36], which corresponds to ideal randomly-oriented polycrystalline aggregation. This is in accordance with weak texture determined from (100) polarogram of the FG region with a maximum polar density of 1.78 MUD [Figure (d)]. In comparison, the (100) polarogram derived from interior of CG region [Figure (e)] indicate the presence of stronger texture with a maximum polar density of 11.51 MUD, resulted from epitaxial growth of grains with preferred orientation during L-PBF solidification.
Figure 1. Grain structure of L-PBF Al–Mg–Sc–Zr alloy as-built specimen. (a) EBSD band-contrast image of overall grain structure. (b) Enlarged inverse polar figure (IPF) map acquired from boxed [blue-coloured in (a)] equiaxed FG region; (c) Grain boundary misorientation profile acquired from (b), presented together with Mackenzie random distribution profile; (d) (100) polarogram acquired from FG region [(b)]; (e) (100) polarogram acquired from boxed [red-coloured in (a)] columnar CG region.
![Figure 1. Grain structure of L-PBF Al–Mg–Sc–Zr alloy as-built specimen. (a) EBSD band-contrast image of overall grain structure. (b) Enlarged inverse polar figure (IPF) map acquired from boxed [blue-coloured in (a)] equiaxed FG region; (c) Grain boundary misorientation profile acquired from (b), presented together with Mackenzie random distribution profile; (d) (100) polarogram acquired from FG region [(b)]; (e) (100) polarogram acquired from boxed [red-coloured in (a)] columnar CG region.](/cms/asset/1a181e17-2c33-41be-9db6-9b53a0e86a39/tmrl_a_2366878_f0001_oc.jpg)
After direct ageing at 325°C/4 h, FG and CG regions remain clearly distinguishable [Figure (a)]. FGs demonstrates a mean grain diameter of 0.76 µm with no evidence of AGG. Grain boundary misorientation profile in FG region remains close to random [Figure (d)]. Hence, we conclude that direct-ageing at 325°C/4 h leads to no fundamental difference in the grain structure. Kernel average misorientation (KAM) map [Figure (b)] reveals that local misorientation is low over the entire grain structure, suggesting that driving force for SIBM is low. TEM dark-field image confirms the presence of a dispersion of fine spherical Al3 (Sc, Zr) precipitates with L12 structure [Figure (e)], with mean radius of ∼1.5 nm. Al3 (Sc, Zr) precipitates not only introduce pronounced precipitation hardening effect [Citation7,Citation10,Citation16,Citation37,Citation38], but also exert strong pinning on grain boundaries, retarding recrystallization and grain growth [Citation39,Citation40], hence stabilizing the fine grain structure generated by L-PBF.
Figure 2. Microstructure of L-PBF Al–Mg–Sc–Zr alloy after direct-ageing at 325°C/4 h. (a) EBSD band-contrast image of overall grain structure; (b) KAM map corresponding to (a); (c) Enlarged IPF map acquired from boxed FG region in (a). (d) Grain boundary misorientation profile acquired from (c), shown together with Mackenzie random distribution. (e) TEM dark-field image of Al3 (Sc, Zr) nanoprecipitates, with corresponding SAED patterns shown in inset image; (f) Statistics of Al3 (Sc, Zr) precipitate. Radius distribution for precipitates with radius of 1–3 nm is shown in enlarged inset image, which comprises >95% of total valid precipitate counts. The mean precipitate radius determined from TEM images is 1.5 ± 0.6 nm.
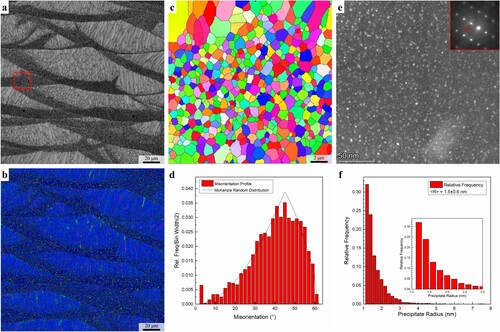
After thermal exposure at elevated temperature of 500°C for 2 h, large abnormal grains are clearly identified, whose near-equiaxed morphology clearly differs from pre-existing elongated CGs [Figure (a)]. Notably, some abnormal grains appear to be embedded in the belt-shaped regions originally occupied by FGs [two typical examples are marked with white dashed line in Figure (a)]. Furthermore, abnormal grain which is surrounded by 21 equiaxed neighbouring grains and has no contact with CGs or other abnormal grains can be identified [circled grain in Figure (c)]. The mean aspect ratio for all 21 neighbouring grains is determined to be 1.40, which is comparable to (even smaller than) the mean aspect ratio of equiaxed FGs prior to thermal exposure (1.55). The presence of abnormal grain fully embedded in equiaxed FGs and the belt-shaped arrangement of impinged abnormal grains strongly suggest the activation of AGG in randomly-oriented FGs.
Figure 3. Microstructure of L-PBF Al–Mg–Sc–Zr alloy after direct-ageing at 325°C/4 h and thermal exposure at 500°C/2 h (a) EBSD IPF map of overall grain structure; (b) KAM map corresponds to (a); (c) Enlarged EBSD IPF map in adjutant to an abnormal grain. Notice that the abnormal grain has no direct contact with other abnormal grains or CGs; (d) KAM map correspond to (c); (e) TEM dark-field image of Al3 (Sc, Zr) nanoprecipitates, with corresponding SAED patterns shown in inset image; (f) Statistics of Al3 (Sc, Zr) precipitate radius distribution. The mean precipitate radius determined from TEM images is 5.2 ± 1.9 nm.
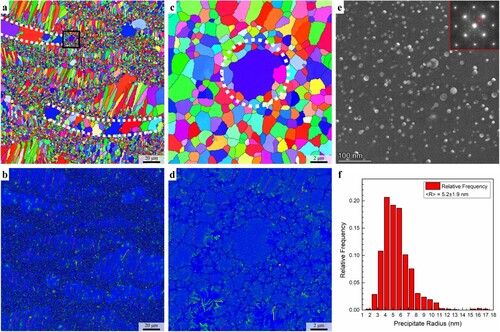
After thermal exposure at 500°C, three features in the grain structure are worth attention. Firstly, intragrain misorientation for the captured abnormal grain is low and do not show significant intragrain heterogeneity [Figure (b,d)]. This greatly differs from expected feature for abnormal grains induced by SIBM, where co-existing strain-free zones with low local misorientation and ‘to-be-consumed’ zones with high local misorientation are expected [Citation33,Citation34]; Secondly, within the FG region, AGG of selected grains co-exists with the NGG of the rest ‘matrix’ FGs, as the mean grain diameter determined from Figure (c) excluding the marked abnormal large grain reaches over 1 µm (1.06 µm). This is enabled by coarsening of Al3 (Sc, Zr) precipitates, whose mean radius is observed to increase more than three-fold from ∼1.5 nm [Figure (f)] to ∼5.2 nm [Figure (f)] after thermal exposure. For second phase particles of a given volume fraction , Zener pinning exerted on grain boundaries
is inversely proportional to the particle radius
[Citation22,Citation41–43]. Hence, thermal exposure led to a continuous decrease of Zener pinning from Al3 (Sc, Zr) particles, enabling the grain growth of FGs. Finally, an asynchrony of AGG initiation is clearly observed: while in some FG regions, impinged abnormal grains have almost completely overtaken the original belt-shaped FG region between melt pools [e.g. regions marked with white dashed lines in Figure (a)], in other FG regions, AGG grains are still surrounded by unconsumed FGs indicating that AGG has just begun to develop [e.g. Figure (c)]. This asynchrony highlights the role of local environment and further stochastic factors in triggering AGG. These features would be discussed in more detail in the discussion section.
After extended thermal exposure at 500°C for up to 24 h, AGG continues to develop in L-PBF Al–Mg–Sc–Zr alloy, invades and consumes both FGs and CGs [Figure (a,c,e)]. No evidence supporting SIBM-induced AGG is found from local misorientation profile [Figure (b,d,f)]. In sharp contrast, after prolonged exposure at 300°C/96 h, no evidence of AGG activation has been found in the FG region, and the mean grain diameter of FGs (0.77 µm) is close to that after direct-ageing. Since Al3 (Sc, Zr) precipitates are known to coarsen very slowly at this temperature [Citation44], it is expected that a strong Zener pinning is maintained, hence suppressing both NGG and AGG behaviour of FGs. Again, KAM map [Figure (h)] suggest that SIBM is unlikely to dictate the grain structure evolution at 300°C.
4. Discussion
To understand the counter-intuitive activation of AGG in the randomly-oriented FGs [c. f. Figure (a,c)], it is important to notice two essential features of the present phenomenon. On one hand, co-existing AGG of selected grains and NGG of ‘matrix’ FGs enabled by decaying Zener pinning (i.e. ) suggests that AGG arises spontaneously as a result of individual growth rate of abnormal grains outcompeting that of the matrix FG aggregation. On the other hand, the observed asynchrony of AGG not only highlights the role of local environment of abnormal grains, but also suggest that both deterministic and stochastic factors must be considered to account for the discovered phenomenon. This assertion is in line with existing mathematical deduction, which proved that without considering fluctuation of local environment for ‘candidate’ abnormal grain, spontaneous AGG initiation is impossible in an aggregation with quasi-stationary NGG kinetics [Citation45,Citation46].
In this context, Rios has incorporated these elements to propose that when Zener pinning is decaying with time (i.e. ), the largest grain in the aggregation (with size
) can indeed activate AGG if it locates in a favourable local environment with below-average pinning strength
[Citation29,Citation47], and the minimal local pinning fluctuation
required is given by[Citation47]:
(1)
(1) Here
is a dimension-related constant,
and
are grain boundary mobility and energy, respectively.
originates from Hillert’s proposal of minimum required radius for grains to grow in a pinning-free aggregation. Dimensionless ratio
is defined as
.
However, application of Equation (1) is confined to the case where no grain growth is possible unless being unpinned by decaying of . Moreover, grain growth of matrix grains enabled by such unpinning is assumed to be a self-similar one, which is not necessarily the case in reality [Citation48–51]. Most importantly, Equation (1) considers only grain with largest radius
to be valid candidate for AGG, while the observed impingement of multiple abnormal grains clearly indicates multiple simultaneous sites of AGG activation. In this light, here we present a more generalized form of Rios’s criterion, which releases all abovementioned assumptions and hence is applicable to arbitrary grain in polycrystalline aggregation evolving in arbitrary manner.
Following Hillert and Rios et al. [Citation20,Citation47], curvature-driven growth rate of an individual grain of radius in an aggregation with critical radius
is given by:
(2)
(2) Both term
and
evolves with time. Therefore, at any given time instance, the instant growth rate for grain with instant radius
would be zero
:
(3a)
(3a) which is equivalent to
(3b)
(3b) On the other hand, for a ‘candidate’ abnormal grain with arbitrary size
in a favourable local environment, its instant growth rate is given by:
(4)
(4)
Rearranging Equation Equation(4)(3b)
(3b) using Equation Equation(3)
(3a)
(3a) would give:
(5)
(5) As the grain boundary pinning decays
, both the matrix and abnormal grains grow. To initiate AGG, potential abnormal grains must grow faster than the entire aggregation, which is portraited by:
(6)
(6)
The growth kinetic of the entire aggregation, portraited by the evolution of with time, is obtained by rearranging and differentiating Equation (3b):
(7)
(7) Inserting Equation (5) and Equation (7) into Equation (6), the generalized AGG criterion is eventually given by:
(8)
(8) Or alternatively in ‘relative’ value by dividing Equation (8) with Equation (3b)
(9)
(9) By taking
(alias
),
(i.e. matrix growth is self-similar) and
(alias
), Equation (8) regresses into Equation (1), proving that Equation (8) is a compatible generalization of Rios’s original reasoning. However, comparing with Equation (1), the generalized Equation (8) does not require that NGG must be initially fully-pinned. Instead, influence of ongoing matrix grain growth can be taken into account by using a finite value of
(alias
). Furthermore, non-static evolution of grain size distribution during growth of matrix is also considered via term
, and a presumed time-invariant grain size distribution is not necessary.
By detaching the radius of candidate grain with
, our generalized reasoning shows that in addition to a few largest grains with
, any growing grain of arbitrary size is also capable of activating AGG, given that it has a favourable local environment with sufficient local pinning fluctuation
so that Equation (8) [or Equation (9)] is satisfied. This explains the observation of multiple AGG activation sites, which is clearly indicated by impingement of multiple AGG grains. Furthermore, the idea of a sufficient local fluctuation of pinning is required for AGG activation acknowledges the role of both deterministic and probabilistic factors, hence is in line with observed asynchrony of AGG activation and development across the grain structure and is consistent with Rios’s original idea.
Equation (8) and Equation (9) also explains the observed susceptibility of FGs with smaller grain size. Physically, a smaller value of right-hand side of Equation (8) or (9) corresponds to easier AGG activation as a smaller fluctuation of local pinning is required. During the grain growth of matrix grains,
moves from its initial value
towards
Footnote1, giving a distribution drifting rate . As a result, the right-hand side of Equation (8) or Equation (9) increase monotonically with increasing
, suggesting that grain aggregation of smaller grain size is in general more susceptible to AGG. Therefore, for the present L-PBF Al–Mg–Sc–Zr alloy, AGG activation is easier in FGs.
Finally, two interesting conclusions on the proposed generalized criterion is worth noticing. Firstly, the right-hand-side of Equation (9) decreases monotonically as long as.
(10)
(10) As a first approximation,
is estimated with Hillert’s quasi-stationary growth kinetic [Citation20]
(11)
(11) the right-hand side of Equation (10) is thus at the order of
(12)
(12) Physically, this implies that once a particular grain of interest has activated AGG, sustaining its growth advantage would become increasingly easier as long as Equation (10) [or as a first approximation, Equation (12)] is satisfied, which well reflects the nature of AGG as an instability of grain growth. Secondly, it is worth noticing that the grain boundary mobility
and grain boundary energy
appearing in Equation (8) [or Equation (9)] originates from the growth kinetic equation of the candidate grain, Equation Equation(5)
(4)
(4) . Hence, a higher
or
for the candidate grain would lower the right-hand-side of Equation (8) [or Equation (9)], resulting in easier activation of AGG as a smaller local pinning fluctuation is required. In this light, a higher temperature not only enables the growth competition between candidate grain(s) and the entire aggregation, but also makes AGG activation easier by elevating the grain boundary mobility
[Citation22], which is consistent with the present observation.
5. Conclusions
In this work, evidence of AGG activation in randomly-oriented FGs are found in a L-PBF processed Al–Mg–Sc–Zr alloy during thermal exposure at elevated temperature of 500°C. The observed spontaneous AGG from initially uniform FG region is considered to be enabled by spatially heterogenous and temporally instable grain boundary pinning exerted by Al3 (Sc, Zr) nanoprecipitates. In this light, a generalized Rios’s criterion is proposed to describe the growth instability for a grain of arbitrary size in a polycrystalline aggregation evolving in arbitrary growth kinetic. The generalized criterion well explains the observed susceptibility of FGs to AGG, presence of multiple AGG activation sites, and asynchrony of AGG activation. The present work is expected to provide new insights into understanding the coupled evolution of nanoprecipitates and grain structure in additive-manufactured alloys as well as the fundamental cause of AGG in a heterogenous polycrystalline aggregation.
Disclosure statement
No potential conflict of interest was reported by the author(s).
Additional information
Funding
Notes
1 At , no matrix grain can obtain a positive growth rate [c. f. Equation (1)], hence
indicates fully-pinning of matrix grain growth.
References
- Olakanmi EO, Cochrane RF, Dalgarno KW. A review on selective laser sintering/melting (SLS/SLM) of aluminium alloy powders: processing, microstructure, and properties. Prog Mater Sci. 2015;74:401–477. doi:10.1016/j.pmatsci.2015.03.002
- Martin JH, Yahata BD, Hundley JM, et al. 3D printing of high-strength aluminium alloys. Nature. 2017;549(7672):365–369. doi:10.1038/nature23894
- Zhang JL, Song B, Wei QS, et al. A review of selective laser melting of aluminum alloys: processing, microstructure, property and developing trends. J Mater Sci Technol. 2019;35(2):270–284. doi:10.1016/j.jmst.2018.09.004
- Aboulkhair NT, Simonelli M, Parry L, et al. 3D printing of aluminium alloys: additive manufacturing of aluminium alloys using selective laser melting. Prog Mater Sci. 2019;106:100578, doi:10.1016/j.pmatsci.2019.100578
- Schmidtke K, Palm F, Hawkins A, et al. Process and mechanical properties: applicability of a scandium modified Al-alloy for laser additive manufacturing. Phys Proc. 2011;12:369–374. doi:10.1016/j.phpro.2011.03.047
- Spierings AB, Dawson K, Voegtlin M, et al. Microstructure and mechanical properties of as-processed scandium-modified aluminium using selective laser melting. Cirp Ann-Manuf Techn. 2016;65(1):213–216. doi:10.1016/j.cirp.2016.04.057
- Spierings AB, Dawson K, Kern K, et al. SLM-processed Sc- and Zr- modified Al-Mg alloy: mechanical properties and microstructural effects of heat treatment. Mater Sci Eng A. 2017;701:264–273. doi:10.1016/j.msea.2017.06.089
- Croteau JR, Griffiths S, Rossell MD, et al. Microstructure and mechanical properties of Al-Mg-Zr alloys processed by selective laser melting. Acta Mater. 2018;153:35–44. doi:10.1016/j.actamat.2018.04.053
- Wang Z, Lin X, Kang N, et al. Strength-ductility synergy of selective laser melted Al-Mg-Sc-Zr alloy with a heterogeneous grain structure. Addit Manuf. 2020;34:101260.
- Wang Z, Lin X, Kang N, et al. Laser powder bed fusion of high-strength Sc/Zr-modified Al–Mg alloy: phase selection, microstructural/mechanical heterogeneity, and tensile deformation behavior. J Mater Sci Technol. 2021;95:40–56. doi:10.1016/j.jmst.2021.03.069
- Wang Z, Lin X, Wang J, et al. Remarkable strength-impact toughness conflict in high-strength Al-Mg-Sc-Zr alloy fabricated via laser powder bed fusion additive manufacturing. Addit Manuf. 2022;59:103093.
- Jia Q, Rometsch P, Kürnsteiner P, et al. Selective laser melting of a high strength Al Mn Sc alloy: alloy design and strengthening mechanisms. Acta Mater. 2019;171:108–118. doi:10.1016/j.actamat.2019.04.014
- Jia Q, Zhang F, Rometsch P, et al. Precipitation kinetics, microstructure evolution and mechanical behavior of a developed Al–Mn–Sc alloy fabricated by selective laser melting. Acta Mater. 2020;193:239–251. doi:10.1016/j.actamat.2020.04.015
- Marquis EA, Seidman DN. Nanoscale structural evolution of Al3Sc precipitates in Al (Sc) alloys. Acta Mater. 2001;49(11):1909–1919. doi:10.1016/S1359-6454(01)00116-1
- Fiocchi J, Tuissi A, Biffi CA. Heat treatment of aluminium alloys produced by laser powder bed fusion: a review. Mater Des. 2021;204:109651.
- Fuller CB, Seidman DN, Dunand DC. Mechanical properties of Al (Sc, Zr) alloys at ambient and elevated temperatures. Acta Mater. 2003;51(16):4803–4814. doi:10.1016/S1359-6454(03)00320-3
- Chen H, Chen Z, Ji G, et al. Experimental and modelling assessment of ductility in a precipitation hardening AlMgScZr alloy. Int J Plast. 2021;139:102971, doi:10.1016/j.ijplas.2021.102971
- Chen X, Chen H, Ma S, et al. Insights into flow stress and work hardening behaviors of a precipitation hardening AlMgScZr alloy: experiments and modeling. Int J Plast. 2024;172:103852.
- Knipling KE, Karnesky RA, Lee CP, et al. Precipitation evolution in Al–0.1Sc, Al–0.1Zr and Al–0.1Sc–0.1Zr (at.%) alloys during isochronal aging. Acta Mater. 2010;58(15):5184–5195. doi:10.1016/j.actamat.2010.05.054
- Hillert M. On the theory of normal and abnormal grain growth. Acta Metall. 1965;13(3):227–238. doi:10.1016/0001-6160(65)90200-2
- Gottstein G, Shvindlerman LS. Grain boundary migration in metals: thermodynamics, kinetics, applications. 2nd ed. Boca Raton: CRC press; 2009.
- Humphreys FJ, Hatherly M. Recrystallization and related annealing phenomena. 2nd ed. Oxford: Elsevier; 2012.
- Gladman T. On the theory of the effect of precipitate particles on grain growth in metals. Proc R Soc Lond A. 1966;294(1438):298–309. doi:10.1098/rspa.1966.0208
- Rios P. Abnormal grain growth in pure materials. Acta Metall Mater. 1992;40(10):2765–2768. doi:10.1016/0956-7151(92)90346-G
- Aota LS, Bajaj P, Zilnyk KD, et al. The origin of abnormal grain growth upon thermomechanical processing of laser powder-bed fusion alloys. Materialia. 2021;20:101243.
- Dunn CG, Walter JL. Secondary recrystallization. In: Margolin H, editor. Recrystallization, grain growth and textures. Ohio: ASM; 1966. p. 461.
- Abbruzzese G, Lücke K. A theory of texture controlled grain growth—I. Derivation and general discussion of the model. Acta Metall. 1986;34(5):905–914. doi:10.1016/0001-6160(86)90064-7
- Eichelkraut H, Abbruzzese G, Lücke K. A theory of texture controlled grain growth—II. Numerical and analytical treatment of grain growth in the presence of two texture components. Acta Metall. 1988;36(1):55–68. doi:10.1016/0001-6160(88)90028-4
- Rios PR. Abnormal grain growth development from uniform grain size distributions due to a mobility advantage. Scripta Mater. 1998;38(9):1359–1364. doi:10.1016/S1359-6462(98)00052-9
- Srolovitz D, Grest G, Anderson M. Computer simulation of grain growth—V. Abnormal grain growth. Acta Metall. 1985;33(12):2233–2247. doi:10.1016/0001-6160(85)90185-3
- Bozzolo N, Agnoli A, Souaï N, et al. Strain induced abnormal grain growth in nickel base superalloys. Mater Sci Forum. 2013;753:321–324. doi:10.4028/www.scientific.net/MSF.753.321
- Jin S, Kang B, Kong T, et al. Strain-induced abnormal grain growth of Fe foils. J Alloys Compd. 2021;853:157390.
- Chen K, Huang DJ, Li H, et al. Avoiding abnormal grain growth when annealing selective laser melted pure titanium by promoting nucleation. Scripta Mater. 2022;209:114377.
- Chen K, Li H, Lim CH, et al. Fine grains within narrow temperature range by tuning strain-induced boundary migration dominated recrystallization for selective laser melted Inconel 718. Scripta Mater. 2022;219:114882.
- Spierings AB, Dawson K, Heeling T, et al. Microstructural features of Sc- and Zr-modified Al-Mg alloys processed by selective laser melting. Mater Des. 2017;115:52–63. doi:10.1016/j.matdes.2016.11.040
- Mackenzie JK. Second paper on statistics associated with the random disorientation of cubes. Biometrika. 1958;45(1-2):229–240. doi:10.1093/biomet/45.1-2.229
- Kendig KL, Miracle DB. Strengthening mechanisms of an Al-Mg-Sc-Zr alloy. Acta Mater. 2002;50(16):4165–4175. doi:10.1016/S1359-6454(02)00258-6
- Røyset J, Ryum N. Scandium in aluminium alloys. Int Mater Rev. 2005;50(1):19–44. doi:10.1179/174328005X14311
- Jones MJ, Humphreys FJ. Interaction of recrystallization and precipitation: the effect of Al3Sc on the recrystallization behaviour of deformed aluminium. Acta Mater. 2003;51(8):2149–2159. doi:10.1016/S1359-6454(03)00002-8
- Ferry M, Hamilton NE, Humphreys FJ. Continuous and discontinuous grain coarsening in a fine-grained particle-containing Al-Sc alloy. Acta Mater. 2005;53(4):1097–1109. doi:10.1016/j.actamat.2004.11.006
- Smith CS. Grains, phases, and interfaces: an introduction of microstructure. Trans AIME. 1948;175:15–51.
- Nes E, Ryum N, Hunderi O. On the Zener drag. Acta Metall. 1985;33(1):11–22. doi:10.1016/0001-6160(85)90214-7
- Manohar PA, Ferry M, Chandra T. Five decades of the Zener equation. ISIJ Int. 1998;38(9):913–924. doi:10.2355/isijinternational.38.913
- Fuller C, Seidman D. Temporal evolution of the nanostructure of Al (Sc, Zr) alloys: part II-coarsening of Al (Sc, Zr) precipitates. Acta Mater. 2005;53(20):5415–5428. doi:10.1016/j.actamat.2005.08.015
- Thompson CV, Frost HJ, Spaepen F. The relative rates of secondary and normal grain growth. Acta Metall. 1987;35(4):887–890. doi:10.1016/0001-6160(87)90166-0
- Chen Y, Chen Y, Dan C, et al. On the incompatibility of steady-state assumption and abnormal grain growth in the presence of homogenous pinning. Metall Mater Trans A. 2024;55(1):20–25. doi:10.1007/s11661-023-07227-1
- Rios PR. Abnormal grain growth development from uniform grain size distributions. Acta Mater. 1997;45(4):1785–1789. doi:10.1016/S1359-6454(96)00284-4
- Atkinson HV. Theories of normal grain-growth in pure single-phase systems. Acta Metall. 1988;36(3):469–491. doi:10.1016/0001-6160(88)90079-X
- Fortes MA. The kinetics of grain growth in the scaling and transient regimes. Scripta Mater. 1997;37(5):679–684. doi:10.1016/S1359-6462(97)00139-5
- Wakai F, Enomoto N, Ogawa H. Three-dimensional microstructural evolution in ideal grain growth—general statistics. Acta Mater. 2000;48(6):1297–1311. doi:10.1016/S1359-6454(99)00405-X
- Svoboda J, Fratzl P, Zickler GA, et al. A new treatment of transient grain growth. Acta Mater. 2016;115:442–447. doi:10.1016/j.actamat.2016.05.020