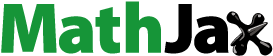
Abstract
The performance of strain hardening cement-based composite (SHCC) under various exposure conditions such as chloride-induced accelerated corrosion, capillary water absorption (CWA), electrical resistivity (ER), and freezing-thawing (CDF) tests is reported. SHCC was compared with two reference mortars; one is the same strength class as the SHCC (M1), and the other is a high strength class (M2). Both cracked and uncracked beam specimens were tested. Results from the investigation show that, in SHCC, the corrosion potential is a function of crack width. It is suggested that the half-cell corrosion potential measurement technique may not truly reflect the corrosion state of an embedded steel bar in SHCC. The result of the CDF test reveals that after 42 cycles of freeze-thaw attacks, SHCC performed better than M1 and M2.
Public Interest Statement
The durability of reinforced concrete (RC) structures is a critical issue in the sustainability of these structures. Aggressive conditions are known to affect their performance over time due to corrosion of the embedded steel reinforcement, which results from chemical ingress. Strain hardening cement-based composites (SHCC) is now used to overlay traditional RC structure to extend their service life. For scrutinizing the optimum performance of SHCC, its durability under various exposure conditions must be known. Therefore, this study has investigated the performance of SHCC samples in relation to two types of mortar samples under various exposure conditions such as chloride-induced accelerated corrosion, capillary water absorption, electrical resistivity, capillary suction of de-icing solution and freeze-thaw tests. It is found that the performance of SHCC is better than the two mortars used in this study. Therefore, successful use of SHCC in RC structures may improve durability as well as extend its service life.
1. Introduction
Durability of reinforced concrete (RC) structures is now one of the most discussed issues among researchers worldwide (Aziz, Aleem, Heikal, & Didamony, Citation2005). In the last few decades, many researches have focused on the corrosion of steel bars in RC, being one of the major causes of durability problems (Audenaert, Marsavina, & De Schutter, Citation2009; Glass & Buenfeld, Citation1997; Kobayashi, Iizuka, Kurachi, & Rokugo, Citation2010; Wang, Jansen, & Shah, Citation1997). Inappropriate designs in terms of low concrete cover and excessive water to cement (w/c) ratio, in addition to poor construction quality, can be the major factors for the corrosion of steel bars. Typically, the corrosion of steel can be classified as carbonation and chloride-induced corrosion. Carbonation is a slow corrosion process, and it is often distributed over the length of steel bars. On the other hand, chloride-induced corrosion is considered the most severe corrosion attack. In chloride-induced corrosion, corrosion is localised, and significant pitting depths or holes can be found on the steel bars, which ultimately reduce the reinforcing capacity of steel bars.
The susceptibility of steel bars to corrosion in RC structures is accelerated by the location of RC structures along coastal areas and the application of de-icing salt in concrete bridges, pavements and parking areas. Corrosion is then triggered as salt water penetrates into concrete. This penetration is enhanced by the poor microstructure as well as the presence of cracks formed in concrete from various loads, hence allowing chemical substances to reach the steel surface where corrosion begins (Audenaert et al., Citation2009; Thomas, Citation1996). Moreover, cracks beyond the acceptable widths in concrete accelerate the deterioration process (Schiessl & Raupach, Citation1997). Often more cracks can be seen in the RC structures due to corrosion of steel itself especially when the tensile force generated by the volume of corrosion product is higher than the concrete tensile strength (Bossio, Monetta, Bellucci, Lignola, & Prota, Citation2015; Chen & Mahadevan, Citation2008; Paul, Babafemi, Conradie, & van Zijl, Citation2017). Therefore, crack control is one of the important parameters for consideration in designing RC structures.
When the crack widths are below a certain threshold level, it becomes difficult for chemical substances to penetrate in concrete and start the deterioration process (Audenaert et al., Citation2009; Kobayashi et al., Citation2010). Depending on the exposure condition and type of structure, the threshold crack width varies in a range of 0.1–0.4 mm (ACI Committee 224). Various kinds of synthetic micro fibres are used in concrete to prevent any plastic shrinkage cracking or the formation of other types of cracks. However, most of the fibres do not improve the strength and strain capacity of the matrix after the cracks appear in the concrete. For this reason, strain hardening cement-based composite (SHCC) was introduced in the construction industry for its multiple fine cracking behaviour under tensile and flexural loading conditions. In SHCC, even after the first crack, strength and strain/deformation increase due to its crack bridging capacity and forms lots of fine multiple cracks (Li, Citation1993; Li, Mishra, & Wu, Citation1995).
The durability of SHCC in aggressive media has much to do with the fine multiple cracks formed under load and the crack width under load. Since it is a relatively new material, a general framework for dealing with the problems of such material regarding durability is necessary (Mechtcherine, Citation2012). Although SHCC has been successfully applied in some projects as a partial replacement for traditional concrete/mortar (Kanakubo et al., Citation2003; Kunieda & Rokugo, Citation2006) for extending the expected lifetime of RC structures, knowledge on the long-term durability performance of SHCC is still limited.
Current research on SHCC indicates that the mechanical behaviour of this material can improve structural performance of RC structures. SHCC is known to have a higher tensile and flexural strength, ductile capacity and most importantly, lower average crack widths than normal concrete (Boshoff, Citation2007; Li et al., Citation1995; Mechtcherine et al., Citation2011; Paul & van Zijl, Citation2013). The influence of cracks on the durability of SHCC has been investigated using different durability tests. These tests include as water and chloride penetration as reported by several researchers (Lepech & Li, Citation2009; Paul, Citation2015; Sahmaran & Li, Citation2009; van Zijl et al., Citation2012; Wittmann, Wang, Zhang, Zhao, & Beltzung, Citation2011; Zhang et al., Citation2010). These studies revealed that SHCC with average crack width up to 60 μm has similar water permeability as uncracked mortar specimen. However, the permeability of SHCC increases with increase in the number of cracks and crack widths (Lepech & Li, Citation2009). Similar behaviour was observed with capillary water absorption (CWA) test in damaged SHCC specimens after applying 50 and 100% (ultimate load was 40 MPa) compressive loads on them (Wittmann et al., Citation2011).
The corrosion of steel bars in concrete is related to the water absorption and electrical resistivity (ER). Lower water absorption defines the lower permeability of concrete. Impermeable concrete is less prone to any corrosion damage. Similarly, the electrical resistivity of concrete is usually a good indication of transport rate of chloride ion penetration and can often be related to the corrosion potential. On the other hand, freezing-thawing (CDF) test is used to evaluate the resistance of concrete to the deterioration caused by repeated freezing and thawing in the presence of salt water. Typically, when water freezes, it expands by about 9%. As the water in the moist concrete freezes, it produces pressure in the pores of the concrete. The accumulative effect of successive freeze-thaw cycles and disruption of paste and aggregate can eventually cause expansion and crack, scaling, and crumbling of the concrete. For that reason, it is imperative to consider the durability performance of concrete if it is subjected to freeze-thaw exposure.
In general, concrete durability is influenced by many factors. Therefore, as a relatively new material, SHCC performance evaluated in relation to these factors may provide valuable information for designers when considering this material for the structural application. Although this study did not cover measuring of chloride content in concrete, it must be kept in mind that, chloride penetration in concrete causes significant durability problems. The influence of chloride penetration in SHCC was broadly discussed in a recent publication (Paul, van Zijl, Babafemi, & Tan, Citation2016).
In this study, SHCC performance was observed under various exposure conditions such as chloride-induced accelerated corrosion, capillary water absorption (CWA), electrical resistivity (ER), capillary suction of de-icing solution and freeze-thaw (CDF) tests. In the corrosion test, specimens were tested in the cracked and uncracked states, while in other tests, the specimens were uncracked. For comparison, two mortar types were tested under the same exposure conditions, and their performances were compared with the SHCC performance. The composition of Mortar 1 is similar to the SHCC except that there are no fibres in the mortar. Mortar 2 is the traditional mortar used for the repair of RC structures.
2. Testing of specimens
Material proportion used for SHCC and mortars are shown in Table . CEM I 42.5 cement and Class F grade fly ash (FA) were used as binders in the mix. Table shows the oxide compositions of cement and FA, determined by X-ray fluorescence (XRF). Sand with a particle size ranging from 0.1 to 0.25 mm was used in SHCC and M1. In M2, sand particle sizes were in a range of 0.1 to 4.0 mm. The fineness moduli of the sands used in M1 and M2 were 1.90 and 3.2, respectively. PVA fibres of 12 mm length and 0.4 mm diameter were used as a micro fibre of SHCC. Additives such as viscosity modifying agent (VMA) and superplasticizer (SP) were added to the mixes to control the SHCC mix for better fibre distribution. After mixing, fresh concrete properties such as slump flow and air content were measured. Four specimens with a cross section of 40 × 40 × 160 mm3 were cast from each mix type per testing age to determine the mechanical properties such as compressive and flexural strength (BS EN 196-1:2016, Citation2016), at different curing ages (28, 57, 90 and 120 days).
Table 1. Materials composition in the matrix (kg/m3)
Table 2. Oxide compositions (% of total wt.) of cement and fly ash
After performing the flexural strength test of the specimens, 40 mm sided cubes were cut out from both edges of the centrally broken specimens and tested for compressive strength. Small dumbbell shaped specimens with a cross sectional area of 30 mm wide and 16 mm thick were used in the direct tensile tests. Three specimens from each type of concrete mix were tested in direct tensile tests.
2.1. Specimen preparation for corrosion potential test
A 10 mm diameter steel bar with a cover of 15 mm was embedded in all SHCC, M1 and M2, see Figure (a) and (b). For the uncracked specimens, two specimens each from SHCC and mortar types (M1 & M2) were used. For the cracked specimens, six specimens from SHCC and two from each mortar type were used. Sixteen beam type specimens each 100 × 100 × 500 mm3 were cast for investigating the corrosion potential of SHCC and mortars. After 48 hrs of casting, all the specimens were demoulded and cured by complete immersion in water for 28 days. After that, the specimens were taken out from the water and put in a controlled climate room at an ambient temperature of 21 ± 2°C and a 50 ± 5% relative humidity until the testing started. At 30 days after casting, cracks were induced manually by applying loads on the specimens. The manual load was applied by tightening the bolts at both ends of the specimens as shown in Figure (b). Note that, all the specimens were loaded (without measuring the load) up to a certain deformation level. The deformations for SHCC, M1 and M2 specimens were 5, 2 and 2 mm, respectively. Figure (c) shows the uncracked specimens under corrosion test.
Figure 1. (a) Position of ERE20 reference electrode and (b) specimens under sustained load for corrosion test.
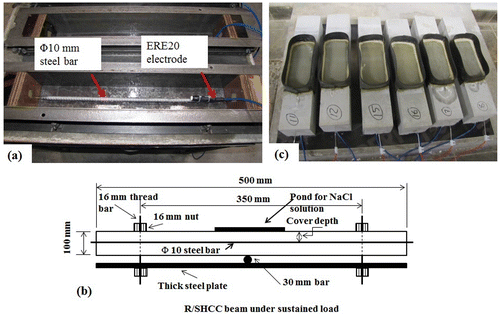
In the SHCC specimens, all the cracks were localised over an approximate length of 150–180 mm in the middle of the SHCC, M1 and M2. Few cracks were also observed away from the middle portion of the specimens. A pond of chloride solution was then made over the cracked surface with an approximate area of 200 × 100 mm2 as shown in Figure (b), using a non-absorbent rubber. About 3.5% NaCl solution was used for cyclic wetting (3 days) and drying (4 days) to simulate the exposure of accelerated chloride-induced corrosion test. The investigation is limited only to the corrosion potential and depassivation (breaking of the protective thin film made from different oxides on the steel surface) of steel bar in both SHCC, M1 and M2.
For measuring the corrosion potential from the specimens, one ERE20 reference electrode was placed inside each specimen mould next to the embedded steel before the casting of concrete (see Figure (a)). ERE20 reference electrode is a long-lasting half-cell, which has a fixed potential value in a range of 195 to 200 mV and is made from manganese dioxide (MnO2) in a very alkaline (pH 13.5) electrolyte. It was placed in a stainless steel case and with a membrane of cement mortar ensuring good affinity with the concrete. The potential was collected automatically by connecting the electrode (on the cathode side) and the steel bar (on anode side) to the data logger.
2.2. Preparation of specimens for CWA, ER and CDF tests
CWA test was performed in accordance with DIN 52617 (Citation1987) for all types of specimens at 33 days after casting. Four-disc shaped specimens with a dimension of 100 mm diameter, and 20 mm thickness were prepared from each mix types. After 48 h of casting, all the specimens were stored in a controlled climate room until the testing date. At 30 days, the curved surface was sealed with epoxy so that water could not penetrate. At 33 days, testing was started and one directional water penetration (see Figure (a)) was allowed through the cast surfaces of the specimens. Readings were recorded up to 14 days. On the first day, readings were collected more frequently (least frequency of reading is done per 1 h) and after that, at least of one reading per day was taken. It should be noted that the water depth along the 20 mm thickness of specimen was approximately 1 mm, which was maintained throughout the test duration. CWA coefficient (w) was then calculated for both SHCC, M1 and M2 using Equation (Equation1(1)
(1) ).
(1)
(1)
where W is the area-based water intake (kg/m2), and t is the time (h).
For the ER test, one beam (same size as for corrosion specimen) from each type of concrete was cast. Furthermore, three core samples (50 mm diameter and 50 mm length) were collected from the centre of each beam by drilling at 92 days after casting day. After 28 days of continuous water curing, specimens were kept in a controlled temperature and humidity room until testing. In the ER test, charges at different frequencies were applied through the specimen from both ends as shown in Figure (b), and the specimen’s resistivity was observed. ER values were calculated in the dry and wet states of the specimens using Equation (Equation2(2)
(2) ). Dry ER values were measured directly after collecting the specimens by drilling. ER was also measured at the wet state of the specimen to study the influence of moisture on the specimens. The specimens were kept in water for 48 h and then dried for 4 h before obtaining the wet ER values.
(2)
(2)
where R is the electrical resistance of the specimen (it is a ratio of applied voltage and obtained current, Ω), A is the cross-section area of the specimen and l is the length of the specimen.
Finally, for the CDF test, four specimens with a cross section of 150 × 150 × 50 mm3 from each mix type were used. These specimens were cut out from a beam with a size of 150 × 150 × 700 mm3. All the specimens were prepared as per DIN CEN/TS 12390-9 (Citation2006) recommendation for a maximum of 42 freeze-thaw cycles. Five faces of the specimens were sealed tightly with rubber strips and glued with silicon so that no leakage occurs between the specimen surface and the rubber strip as shown in Figure (c). Only one face with a surface area of 150 × 150 mm2 was open, and this face was subjected to freeze-thaw cycles at a temperature of 20°C. About 3% NaCl solution was used for CDF test which was applied on top of the open surface of each specimen having an approximate depth of 3 mm. Mass loss of the specimens was determined from the scaled materials obtained at 7, 14, 28 and 42 freeze-thaw cycles. Equation (Equation3(3)
(3) ) was used to calculate the total amount of mass loss of the specimen. All scaled materials were collected from the surface using a brush during the wet stage and then dried in an oven at a maximum temperature of 110°C. The first cycle of freeze-thaw was started when the specimens were 60 days old.
Total amount of mass loss (Mloss,n) of the specimen after ‘n’ cycles is calculated as:(3)
(3)
where ms is the mass of scaled material from n cycles (kg), and A is the test surface area (m2) of the specimen.
3. Results and discussion
3.1. Slump flow and mechanical properties of SHCC, M1 and M2
Slump flow and percentage of air content in SHCC, M1 and M2 were measured according to ASTM C1437 (Citation2015), and ASTM C185 (Citation2015) and the values are shown in Table . Different slump values were obtained for the different batches of mixes. However, the average slump flow was not varied significantly one from another. Table shows that SHCC has the highest air content, and this can be attributed to the inclusion of fibres in the mix thereby creating more voids compared to the M1 and M2 specimens. Besides, M1 has lower air content compared to M2. It should be noted that mortar mix M2 has almost 3 times the sand content of M1, hence higher air content. A significant increase in sand content has been acknowledged to increase the air content of concrete mix (Portland Cement Association, Citation1998).
Table 3. Fresh and 28-day mechanical properties of SHCC and mortars
The mechanical properties of the specimens show that M2 has the highest ultimate compressive (fuc) and tensile (fut) strength than the two other mixes. SHCC and M1 have similar compressive strength, but SHCC shows a significantly higher flexural (fuf) and tensile strength. Therefore, for the same cement matrix, the presence of fibres leads to increased flexural and tensile strength compared with the matrix without fibres. The strain was also measured during the tensile test to confirm the strain hardening behaviour of SHCC. It was found that the SHCC used in this study has approximately 1.5–2% tensile strain capacity. Note that, because of the brittle behaviour of M1 and M2, the strain capacities of these specimens could not be measured.
Figure shows the compressive and flexural strength development of SHCC, M1 and M2 up to 120 days. Compared to M2, the strength development in SHCC and M1 was higher after 28 days. Continuous hydration of a large amount of FA in SHCC and M1 would have led to this strength development. Note that the ultimate tensile strength and strain of SHCC depends on its mix design and optimum fibre content (Boshoff, Citation2007; Li et al., Citation1995). Nevertheless, the ultimate compression and tensile strengths are obtained for M2 because of its lowest water/cement ratio, which is approximately equal to 0.5 and half of the water/cement ratio of SHCC and M1. As shown in Figure , after 57 days, the rate of strength development in M2 is lower than SHCC. From 57 to 120 days, the rate of compressive strengths development in SHCC, M1 and M2 are 20, 19 and 1%, respectively, while flexural strength is 11, 5 and 8%, respectively.
3.2. Corrosion potential performance of SHCC, M1 and M2
Table shows the crack properties of the different cracked and uncracked specimens tested. These cracks were measured at the loaded state of the specimens. The applied load and deformations are already described in Section 2.1. Nevertheless, the major focus is the relation of the corrosion of the embedded steel bar to the crack properties. For the crack properties such as number of cracks, crack width and crack spacing, photos were taken from the specimen’s cracked surface with the aid of a portable hand-held camera (dnt DigiMicro Mobile camera, UK). The photo image showing the crack width is then analysed and measured by the software attached to the camera depending on the image resolution chosen.
Table 4. Details of cracks and maximum corrosion potential in cracked SHCC and mortars specimens
In the particular type of SHCC used in this study, only fewer cracks were noticed on the specimens’ surface, and the crack frequency was not evenly distributed (approximate crack spacing was 15–18 mm). This response is understandably based on the lower strain value obtained in the tensile test of the SHCC specimen. Furthermore, the lower strain and less number of cracks in the SHCC may be due to the lower volume of fibre content (<2%) in the matrix, as well as the manual application of load on the specimen in the steel frame for the corrosion test. According to Table , the number of cracks developed in SHCC is higher than the M1 and M2 where no fibres were used.
Table shows the number of cracks, the average crack width, the maximum crack width and the corrosion potential in the cracked SHCC, M1 and M2. It is interesting to see that the smaller crack widths (total and maximum) in the SHCC specimens lead to lower corrosion potential and at higher crack widths, the potential response is higher. A doubling in the total and maximum crack widths lead to a 22 and 34% increase, respectively, in the corrosion potential reading in SHCC specimens tested. For M1 and M2, the trend is not quite clear. However, it is known that the position of the anode and cathode in the corroded steel bar is dependent on the movement of ions, which is related to the density of concrete (Broomfield, Citation2007). Therefore, the electrochemical process in the different matrices or for different crack patterns may vary, and as a result, different corrosion potentials can be observed.
Figure shows the corrosion potential reading found in the different cracked and uncracked SHCC, M1 and M2 at different periods. Cracked specimens show significantly higher potential values soon after the application of chloride. These potential values are more than the recommended values given by ASTM C876-09 (Citation2009) for predicting the probability of steel corrosion in concrete. A similar response was also observed in a previous study (Paul & van Zijl, Citation2014), where a high potential was found in SHCC immediately after applying the chloride solution. It should be noted that corrosion is an electrochemical process. As the chloride solution comes in contact with the steel bar, the potential value changes significantly even though no major corrosion activity has occurred in the steel bar. Furthermore, the high potential value can also be attributed to the lack of sufficient oxygen at the steel surface in the concrete. In this regard, the matrix composition plays an important role since the denser the matrix, the lesser the availability of oxygen in the matrix.
It can, therefore, be said that a high negative potential in concrete specimens with a denser microstructure due to the addition of a large amount of binder (cement, FA, ground granulated blast-furnace slag) exposed to aggressive media does not necessarily portend higher corrosion. In this case, other corrosion measurement methods such as polarisation resistance technique, electrochemical impedance spectroscopy, and galvanostatic pulse technique may be more suitable than half-cell potential method.
Currently, there is limited research result available which correlate crack properties with the corrosion of steel bars in SHCC. It is believed that the probability of corrosion is increased with increased crack width (Vidal, Castel, & Francois, Citation2004), which is the background of crack width limitation by design standards for durability of RC. However, some light was shed on the importance of crack spacing and width for corrosion rate in RC and SHCC (Arya & Ofori-Darko, Citation1996; Paul & van Zijl, Citation2016).
It should be noted that, for the first 10 weeks (Figure ), all the specimens were subjected to continuous cyclic wetting and drying exposure condition in chloride solution, and after that, no solution was applied to the specimens. Except in M2, the depassivation period in the cracked specimens is not clear since significantly higher potential values were found just after the application of chloride solution. After 8 weeks of cyclic chloride application, corrosion stain was observed on top of two cracked M2 specimens as shown in Figure (c)). On the other hand, no corrosion stain was observed in M1 and SHCC specimens (see Figure (a) and (b)). However, the same M2 specimens show a lower corrosion potential value than the other two. The half-cell potential measurements provide a classification of the corrosion activity of the steel and indicate locations where the steel is potentially corroding. However, potentials cannot be used to estimate the rate of corrosion of the steel or the condition of the concrete (Elsener, Andrade, Gulikers, Polder, & Raupach, Citation2003). Therefore, it can be said that the corrosion potential does not show the real corrosion status in the specimen. This method may be a good indication of depassivation of a steel bar in concrete since the higher potential value (towards more negative value) defines higher possibility of corrosion activities (Broomfield, Citation2007; Elsener et al., Citation2003). In the uncracked specimens, potential value in the SHCC and M1 specimens started changing after 3 and 6 weeks, respectively, while in M2 no change is noticed. The above result can be described in two ways: first, there is the possibility that the inclusion of fibre in the matrix might have increased the chances of corrosion. Second, the current corrosion potential technique may need to be calibrated for a different type of matrix such as SHCC, which is showing higher corrosion potential reading though no real corrosion activity appears on the surface (Figure (a)).
3.3. CWA performance of SHCC, M1 and M2
Much lower water absorption was found in M2 than in SHCC and M1 as shown in Figure . The average capillary water absorption coefficient (w) was calculated to be 4.58, 5.87 and 0.40 kg/m2.hr1/2 for SHCC, M1 and M2, respectively. Note that, the w values were obtained from Figure by applying Equation (1). In the case of SHCC and M1, w was calculated from the initial linear portion of the graph and for M2, it was calculated as the slope from the intercept to the reading up to 24 h. The water absorption results also confirm the higher corrosion potential value of SHCC and M1 in Figure . This indicates that, for this particular type of SHCC matrix, the permeability can be high and promotes faster water and chloride penetration.
The higher w values of SHCC and M1 in comparison with M2 can be explained by their different material compositions. SHCC and M1 contain a large amount of binder (cement and FA), and there is a possibility that hydration may not occur in all the binder with the mixed water. Therefore, further hydration process may occur in the un-hydrated binder particles (FA) when specimens were in contact with water during CWA test. It should be noted that the curing process for this test was different from other tests. In this case, air dry curing method was followed as per DIN 52617 (Citation1987). Therefore, the lower water to binder ratio (w/b) of SHCC and M1 (w/b = 0.37) may be a reason for faster water absorption in the matrix compared to higher w/b of M2 (w/b = 0.47). It is also clear from Figure that within 1 h, the water saturated all SHCC and M1 specimens, but no water is observed on the surface even after 14 days of CWA test. On the other hand, after 11 days it was noted that all the M2 specimens were saturated and water was seen on the surface of two specimens. Although all the specimens were absorbing water for 14 days, however from Figure , it can be seen that after 1 day the rate of water absorption was not significant especially for SHCC and M1. In Figure , the reason for the stiffer slope of SHCC and M1 was confirmed by the faster water absorption (within 30 min to 1 h) in these specimens as shown in Figure .
3.4. ER performance of SHCC, M1 and M2
Figure shows the ER of SHCC and mortars specimens at both dry and wet conditions. A higher ER value was found in SHCC and M1 in both dry and wet conditions than in M2. However, in all cases, the dry specimens show higher ER than their wet counterparts as expected. Very fine aggregate and more binder in SHCC and M1 lead to fewer pores inside the matrix, which may be the reason for a higher ER value than in M2. Also, the dense microstructure of concrete has higher resistance against the current flow, and the dense microstructure is often related to the material composition, particles grading, compaction and curing. Therefore, the ER value can differ for concrete and mortar having different material composition. Concrete resistivity is also related to the presence of moisture in concrete. This is because the electrical current through the concrete is conducted by ions in the moisture (Neville, Citation2003). Lower ER values were found in all types of specimens in the wet stage. It may be explained by the presence of water in the pores of wet specimens, which allowed more current to pass through the specimens. Due to the changes in the applied frequency from 0.10 to 100 kHz, SHCC and M1 show a significant reduction in resistance. Conversely, this change was not significant in M2 specimens. The lower electrolyte resistance may be the reason for corrosion stain seen in cracked M2 specimens in Figure (c)). The addition of blast furnace slag and silica fume in addition to Portland cement in concrete has also been reported to have some influence on the ER; ER is increased when they are used in concrete over Portland cement only (Neville, Citation2003). Perhaps, the addition of FA in SHCC and M1 (dry stage and at 100 Hz) could have been responsible for the increase in ER of about 213 and 140% higher over M2 where only Portland cement is used.
3.5. CDF performance of SHCC, M1 and M2
The performance of SHCC and mortar specimens in CDF test is shown in Figure . It is quite clear from the figure that SHCC has a better performance against CDF attack than M1 and M2. After 42 cycles of freeze-thaw attacks, less than 0.35 kg/m2 mass loss was found in SHCC. On the other hand, just after 7 cycles, significant mass losses were found in both M1 and M2 specimens, but the loss in M2 was very high compared to M1. After 7 cycles, the mass loss in M1 was not significant, whereas almost double mass loss was found in M2 specimens from 7 to 14 cycles. Therefore, the denser matrix and lower air content in M1 than M2 may have been responsible for the better performance in CDF. Scaled materials were evident at more than 5 mm depth from the surface of M2 specimens. Therefore, increased strength of traditional mortar (as in sample M2) may not offer increased resistance against freeze-thaw attack. Conversely, SHCC with similar water absorption capacity to M1 is still more stable because fibres bridge the matrix and increase the tensile force. Therefore, the tensile force generated by freezing of de-icing salt in concrete pores is not sufficient to create any damage in the SHCC specimen. Figure shows the specimen’s surface after 28 and 42 cycles of freeze-thaw attack and the excessively higher mass loss of M2 specimens can be observed from Figure .
4. Conclusions and recommendations
This research has focused on some important parameters such as corrosion, capillary water absorption, electrical resistivity and freeze-thaw attack, which are the key parameters of a design service-life modelling for reinforced concrete structures. From the outcome of this research, it can be said that, depending on the importance of a structure, SHCC may be used as a partial or full replacement in traditional concrete or mortar application. From this research work, the following conclusions can be made.
The half-cell corrosion potential using ERE20 MnO2 is correlated to the total and maximum crack widths in SHCC specimens. A doubling in total and maximum crack widths led to a 22 and 34% increase in corrosion potential reading in SHCC specimens tested here. Therefore, in reinforced concrete, crack properties such as the number of cracks, average crack width, maximum crack width and total crack width must be considered in the corrosion activities.
At the initial stage of capillary water absorption test, significantly higher water absorption was found in SHCC and M1 than in M2. However, the reason for this behaviour is not quite clear since only limited number of specimens was used in this research, and more future research is recommended in this regard. Nevertheless, it is assumed that a large amount of un-hydrated binder (FA) in the matrix of SHCC and M1 may contribute faster absorption of water than the matrix with a lower binder of M2. The water mass gain from 1 h to 14 days for the different specimens of SHCC, M1 and M2 were about 14.3% (4.2–4.8 kg/m2), 11.6% (4.3–4.8 kg/m2) and 109% (1.1–2.3 kg/m2), respectively.
In electrical resistivity test, the influence of FA is shown in the bigger resistance in SHCC and M1 compared to that of M2. Also at a higher frequency, M2 shows lower electrical resistivity than SHCC and M1.
SHCC has significantly higher resistance against freeze-thaw attack than M1 and M2 used in this research. After 42 cycles of freeze-thaw attack, M1 and M2 show up to 400 and 2,200% higher mass loss respectively than SHCC.
Funding
The work was financially supported by the German-South African Year of Science 2013 SPIN project.
Acknowledgements
This part of the research work has been performed in the lab of BAM Federal Institute for Materials Research and Testing, Berlin, Germany. The first author would like to express his sincere thanks to the staff of the laboratory and workshop of BAM lab. The financial assistance provided by the German-South African year of science 2013 SPIN project towards this work is hereby acknowledged.
Additional information
Notes on contributors
Suvash Chandra Paul
Dr Suvash Chandra Paul is currently a research fellow at Singapore Centre for 3D Printing, School of Mechanical and Aerospace Engineering, Nanyang Technological University, Singapore. He obtained his PhD in Civil Engineering in 2015 at Department of Civil Engineering, Stellenbosch University, South Africa. His research interest is in the areas of the mechanical and durability performance of strain hardening cement-based materials (SHCC), recycled concrete aggregate, sustainable construction materials and 3D concrete printing.
Adewumi John Babafemi
Dr Adewumi Jhon Babafemi is currently a postdoctoral research fellow at the Department of Civil Engineering, Stellenbosch University, South Africa, where he also obtained his PhD in Civil Engineering in 2015. He is also a lecturer at Obafemi Awolowo University, Ile-Ife, Nigeria. His research interest is in the area of fibre reinforced concrete (FRC), creep of FRC, use of supplementary cementitious materials in concrete and durability studies of concrete. He is currently investigating the mechanisms responsible for the creep of cracked steel and macro synthetic fibre reinforced concrete.
References
- Arya, C., & Ofori-Darko, F. K. (1996). Influence of crack frequency on reinforcement corrosion in concrete. Cement and Concrete Research, 26, 345–353.10.1016/S0008-8846(96)85022-8
- ASTM C1437-15. (2015). Standard test method for flow of hydraulic cement mortar. West Conshohocken, PA: ASTM International.
- ASTM C185-01. (2015). Standard test method for air content of hydraulic cement mortar. West Conshohocken, PA: ASTM International.
- ASTM C876. (2009). Standard test method for corrosion potentials of uncoated reinforcing steel in concrete. West Conshohocken, PA: ASTM International.
- Audenaert, K., Marsavina, L., & De Schutter, G. (2009). Influence of cracks on the service life of concrete structures in a marine environment. Key Engineering Materials, 399, 153–160.10.4028/www.scientific.net/KEM.399
- Aziz, M. A. E., Aleem, S. A. E., Heikal, M., & Didamony, H. E. (2005). Hydration and durability of sulphate-resisting and slag cement blends in Caron’s Lake water. Cement and Concrete Research, 35, 1592–1600.10.1016/j.cemconres.2004.06.038
- Boshoff, W. P. (2007). Time-dependant behaviour of engineered cement-based composite (PhD thesis). Stellenbosch: Department of Civil Engineering, Stellenbosch University.
- Bossio, A., Monetta, T., Bellucci, F., Lignola, G. P., & Prota, A. (2015). Modeling of concrete cracking due to corrosion process of reinforcement bars. Cement and Concrete Research, 71, 78–92.10.1016/j.cemconres.2015.01.010
- Broomfield, J. P. (2007). Corrosion of steel in concrete understanding, investigating and repair (2nd ed.). New York, NY: Taylor & Francis.
- BS EN 196-1:2016. (2016). Methods of testing cement. Part 1: Determination of strength. BSI Standards Limited. ISBN 9780580845802.
- Chen, D., & Mahadevan, S. (2008). Chloride-induced reinforcement corrosion and concrete cracking simulation. Cement and Concrete Composites, 30, 227–238.10.1016/j.cemconcomp.2006.10.007
- DIN 52617. (1987). Bestimmung des Wasseraufnahmekoeffizienten von Baustoffen (German).
- DIN CEN/TS 12390-9. (2006). Frost und Frost Tausalz Widerstand Abwitterung (German).
- Elsener, B., Andrade, C., Gulikers, J., Polder, R., & Raupach, M. (2003). Half-cell potential measurements – Potential mapping on reinforced concrete structures. Materials and Structures, 36, 461–471.10.1007/BF02481526
- Glass, G. K., & Buenfeld, N. R. (1997). Chloride threshold level for corrosion of steel in concrete. Corrosion Science, 39, 1001–1013.10.1016/S0010-938X(97)00009-7
- Kanakubo, T., Kabele, P., Fukuyama, H., Uchida, Y., Suwada, H., & Slowik, V. (2003). Strain hardening cement composite: Structural design and performance. In K. Rokugo & T. Kanda (Eds.), RILEM state-of-the-art report (Vol. 6, pp. 1–90). Dordrecht: Springer
- Kobayashi, K., Iizuka, T., Kurachi, H., & Rokugo, K. (2010). Corrosion protection performance of high performance fibre reinforced cement composites as a repair material. Cement and Concrete Composites, 32, 411–420.10.1016/j.cemconcomp.2010.03.005
- Kunieda, M., & Rokugo, K. (2006). Recent progress on HPFRCC in Japan. Journal of Advanced Concrete Technology, 4, 19–33.10.3151/jact.4.19
- Lepech, M., & Li, V. C. (2009). Water permeability of engineered cementitious composites. Cement and Concrete Composites, 31, 744–753.10.1016/j.cemconcomp.2009.07.002
- Li, V. C. (1993). From micromechanics to structural Engineering – The design of cementitious composites for civil engineering applications. Journal of Structural Mechanics and Earthquake Engineering, 10, 37–48.
- Li, V. C., Mishra, D. K., & Wu, H. (1995). Matrix design for pseudo-strain-hardening reinforced cementitious composites. Materials and Structures, 28, 586–595.10.1007/BF02473191
- Mechtcherine, V. (2012). Towards a durability framework for structural elements and structures made of strengthened with high-performance fibre-reinforced composites. Construction and Building Materials, 31, 94–104.10.1016/j.conbuildmat.2011.12.072
- Mechtcherine, V., Silva, F. A., Butler, M., Zhu, D., Mobasher, B., Gao, S. L., & Mader, E. (2011). Behaviour of strain hardening cement-based composite under high strain rates. Journal of Advanced Concrete Technology, 9, 51–62.10.3151/jact.9.51
- Neville, A. M. (2003). Properties of Concrete (5th ed.). Harlow: Prentice Hall.
- Paul, S. C. (2015). The role of cracks and chlorides in the corrosion of reinforced strain hardening cement based composites (PhD thesis). Stellenbosch: Department of Civil Engineering, Stellenbosch University.
- Paul, S. C., & van Zijl, G. P. A. G. (2013). mechanically induced cracking behaviour in fine and coarse sand strain hardening cement based composites (SHCC) at different load levels. Journal of Advanced Concrete Technology, 11, 301–311.10.3151/jact.11.301
- Paul, S. C., & van Zijl, G. P. A. G. (2014). Crack formation and chloride induced corrosion in reinforced strain hardening cement-based composites (R/SHCC). Journal of Advanced Concrete Technology, 12, 340–351.10.3151/jact.12.340
- Paul, S. C., & van Zijl, G. P. A. G. (2016). Chloride-induced corrosion modelling of cracked reinforced SHCC. Archives of Civil and Mechanical Engineering, 16, 734–742.10.1016/j.acme.2016.04.016
- Paul, S. C., van Zijl, G. P. A. G., Babafemi, A. J., & Tan, M. J. (2016). Chloride ingress in cracked and uncracked SHCC under cyclic wetting-drying exposure. Construction and Building Materials, 114, 232–240.10.1016/j.conbuildmat.2016.03.206
- Paul, S. C., Babafemi, A. J., Conradie, K., & van Zijl, G. P. A. G. (2017). Applied voltage on corrosion mass loss and cracking behaviour of steel reinforced SHCC and mortar specimens. Journal of Materials in Civil Engineering. doi:10.1061/(ASCE)MT.1943-5533.0001807
- Portland Cement Association (1998). Control of air content in concrete. Concrete Technology Today, 19(1), 1–8.
- Sahmaran, M., & Li, V. C. (2009). Influence of microcracking on water absorption and sorptivity of ECC. Materials and Structures, 42, 593–603.10.1617/s11527-008-9406-6
- Schiessl, P., & Raupach, M. (1997). Laboratory studies and calculations on the influence of crack width on chloride-induced corrosion of steel in concrete. ACI Materials Journal, 94, 56–62.
- Thomas, M. (1996). Chloride thresholds in marine concrete. Cement and Concrete Research, 26, 513–519.10.1016/0008-8846(96)00035-X
- van Zijl, G. P., Wittmann, F. H., Oh, B. H., Kabele, P., Toledo Filho, R. D., Fairbairn, E. M., ... Lepech, M. D. (2012). Durability of strain-hardening cement-based composites (SHCC). Materials and Structures, 45, 1447–1463.10.1617/s11527-012-9845-y
- Vidal, T., Castel, A., & Francois, R. (2004). Analyzing crack width to predict corrosion in reinforced concrete. Cement and Concrete Research, 34, 165–174.10.1016/S0008-8846(03)00246-1
- Wang, K., Jansen, D. C., & Shah, S. P. (1997). Permeability study of cracked concrete. Cement and Concrete Research, 27, 381–393.10.1016/S0008-8846(97)00031-8
- Wittmann, F. H., Wang, P., Zhang, P., Zhao, T., & Beltzung, F. (2011). Capillary absorption and chloride penetration into neat and water repellent SHCC under imposed strain. In R. D. Toledo Filho, F. A. Silva, E. A. B. Koenders, and E. M. R. Fairbairn (Eds.), 2nd International RILEM Conference on Strain Hardening Cementitious Composites (SHCC2-Rio) (pp. 165–172). Rio de Janeiro: RILEM Publications SARL.
- Zhang, P., Wittmann, F. H., Zhao, T. J., Lehmann, E. H., Tian, L., & Vontobel, P. (2010). Observation and quantification of water penetration into strain hardening cement-based composites (SHCC) with multiple cracks by means of neutron radiography. Nuclear Instruments and Methods in Physics Research Section A: Accelerators, Spectrometers, Detectors and Associated Equipment, 620, 414–420.10.1016/j.nima.2010.04.119