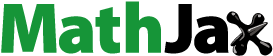
Abstract
This study examines the flow properties of a ternary hybrid nanofluid composed of GO-MoS2-Al2O3 in a base mixture of C2H6O2-H2O (50%–50%) fluid as it moves through a porous longitudinal rectangular fin. The primary objective aimed to analyze the influence of nanoparticle concentration and its shape on the heat transfer rate of the system. Darcy’s model was utilized to analyze the flow and thermal behaviour of the nanofluid within the fin, incorporating temperature-dependent natural convection and radiation effects. The governing thermal equilibrium equation is transitioned to non-dimensional form and numerically solved using the 3 stage Lobatto – IIIa numerical technique, incorporating suitable boundary conditions for convective and insulated tips. The simulation results illustrate the impact of various similarity parameters on the thermal behaviour of the fin and the heat transfer rate. Natural convection, radiation and wet porous parameter are the key similarity parameters that determine the heat transfer rate of our proposed model. In our investigation, the heat transfer rate of convective fin tip was enhanced by 14.61%, 25% and 6.5% compared to an insulated tip for Changing the shapes of the nanoparticle from spherical to lamina, the temperature distribution on the fin enhanced by 23.26%. The findings have significant implications for the design and optimization of thermal management systems in industries.
Introduction
The limitations associated with conventional fluids such as water and ethylene glycol pose a significant challenge for researchers to devise an innovative method to enhance the heat transfer rate. In contrast to metals and carbon nanotubes, conventional fluids have lower thermal conductivity. To counter this issue, the researchers have come out with an idea of mixing nanoparticles of less than 100 nm to the conventional fluid to enhance the fluid flow as well as heat transfer rate. The nano-sized particles prepared from chemically inert materials like copper, silver and gold are believed to have higher thermal conductivity compared to traditional fluid. In addition, thermal conductivity is found higher in metal oxides, such as TiO2, GO, and AL2O3 that can enhance the heat transmission rate.
Gholinia et al. (Citation2020) conducted an investigation of three dimensional flow stagnation of hybrid nanofluid around a circular cylinder by considering ethylene glycol, water and engine oil as base fluids. Nanoparticles SWCNT and MWCNT were added to enhance the thermal conductivity of base fluids. The outcome showed an enhancement in the rate of heat transfer with decrease in the thermal slippage parameter. Also, a significant rise in the temperature was observed in the case of SWCNT as compared to MWCNT, due to its higher thermal conductivity. Gireesha et al. (Citation2020) investigated the performance of moving longitudinal fin embedded in a hybrid nanofluid mixture of MgO and Ag in water by analysing the thermal profile. The outcomes were graphically illustrated and discussed. Venkateswarlu and Satya Narayana (Citation2021) explored the repercussion of viscosity, viscous dissipation on the porous stretching sheets wetted with hybrid nanofluid. It was observed in case of Cu-water, the convergence towards the boundary was faster compared to hybrid nanofluids. In addition to this, the heat transmission enhanced with the change in shape of nanoparticles. The rheological and thermophysical properties of a fluid can be improved by changing the shape of the nanoparticles. Ghadikolaei et al. (Citation2017) analysed the repercussion of the TiO2 and Cu nanoparticles shape on the temperature profile over a stretching sheet in the presence of magnetic field. The findings showed the outperformance of platelet shape over other shapes. MWCNT and Ag nanoparticles mixture in water in a stretched cylinder was analysed by Hosseinzadeh et al. (Citation2021) by taking shape factor of nanoparticles into consideration.
Thermal efficiency of a wet porous radial moving fin in a hybrid nanofluid, considering nanoparticles of various shapes, was analyzed by Keerthi et al. (Citation2022) using the RKF method. The exploration showed a significant effect of the particle shape on fin temperature profile and efficiency. The effect of sink temperature on ambient temperature was analyszed by Maryam Fallah Najafabadi et al. (Citation2021) by numerically solving the governing equations using the radial basis approximation method. The model under investigation was a hot rod and a surrounding air medium. This result indicates a gradual rise in the ambient temperature with an enhancement in the sink temperature. Spinning the nanoparticles added to the base fluid can enhance heat transmission, was explored by Al-Hossainy and Eid (Citation2021). Experimental and computational studies conducted on the PEG-H2O/ZrO2+MgO combination showed an increase in the rate of heat transmission.
In thermal engineering, the fundamental principle to enhance the heat transfer rate is to extend the surface area. This is achieved by adding structures known as fin. The design process involves increasing the surface area that is in contact with the surrounding fluid, effectively improving the efficiency of heat transmission through natural convection process. This aspect is crucial in the design of cooling systems such as in electronic devices, compressors, refrigerators, heat exchange equipment and appliances. The key factors in the design are shape and the dimension of the fin. This is to maximise the reliability and overall thermal performance of the system under consideration. The challenge is to optimize the parameters in the design and improve the thermal efficiency of the system. Analysing the fins of different shapes can yield valuable insights to its behaviour in real world applications.
Ahmad et al. (Citation2020) examined the thermal profile of longitudinal heat exchangers (fins) of different shapes using complex ordinary differential equations (ODE) with boundary values using an innovative approach called the ANN-SOS algorithm. The outcomes were verified and found in agreement with the existing literature. Din et al. (Citation2023) investigated the behavior of an exponential fin. The problem was solved numerically using the shooting technique. It was found that the rate of heat transfer was enhanced in the exponential fin compared to that in the trapezoidal fin. Weera et al. (Citation2023) examined the temperature profile of a dovetail longitudinal porous fin using SCM to solve the ODE governing equation. The outcome showed a decrease in the temperature distribution. Turkyilmazoglu (Citation2021) proposed an optimization of the fin dimension by considering concave–parabolic fin geometry in the analysis. Kezzar et al. (Citation2020) explored the transfer of heat in convective fins of various shapes, considering internal heat generation, variable thermal conductivity and radiation. The examination shows that the exponential profile outperforms over other profiles. Al-Hossainy and Eid (Citation2021) examined the flow of graphene and silica nanofluid mixture over a permeable curved surface that exhibited slippage. The results show a boost in the flow velocity and a decrease in the temperature with surface curvature. Hosseinzadeh et al. (Citation2020) analyzed and experimentally verified a triplex tube heat exchanger incorporating tree-like fins under the influence of a fluid containing MoS2 and TiO2 nanoparticles. The analysis was carried out using the GFEM method, which indicates the outperformance of the tree-like fins, as it considerably reduces the solidification time. Kezzar et al. (Citation2020) examined the temperature profile of a longitudinal fin by solving nonlinear differential equations numerically using fourth-order Runge–Kutta technique, and analytically using the Duan – Rach method. The results showed agreement between the numerical and analytical methods. Kundu and Das (Citation1999) investigated the performance of an eccentric annular fin with variations in the base temperature using a numerical technique. This finding indicates an improvement in the heat transfer rate relative to the concentric fin. The temperature profile was obtained by solving differential equations using the finite difference method. Hussain et al. (Citation2022) investigated the heat transfer rate of the unsteady shear thinning flow behavior of a nanofluid over an exponential shrinking and stretching cylinder. The influence of the nanoparticle concentration on heat transmission was investigated using the Buongiorno model. Goud et al. (Citation2022) examined the heat transmission of a fully wet dovetail fin in a ternary ZnFe2O4 +MnZnFe2O4 +NiZnFe2O4/H2O hybrid nanofluid. The energy balance equation was numerically and analytically solved using the RKF and DTM-Pade approximations. The results showed an improvement in the thermal performance relative to the binary nanofluid. Ahmad et al. (Citation2022) analyzed the flow of a bio-convective Maxwell nanofluid through an exponential stretching sheet. The study showed a drop in the Nusslet number relative to an increase in the Deborah number. Heat transmission analysis of rGO-Fe3O4-TiO2/H2O ternary nanofluid with self-propelled microorganisms was carried out by Puneeth et al. (Citation2022) with assumptions regarding the nanoparticle concentration. A modified Buongiorno model is proposed in this article. The results indicate an enhancement in the velocity profile with mixed convective parameters. Girish et al. (Citation2023) investigated dovetail fins wetted with a hybrid nanofluid. The thermal profile of the proposed model was obtained using numerical techniques and analyzed. Acquiring an accurate analytical solution for nonlinear fins has recently been a challenge for researchers. In alignment with this objective, Wang et al. (Citation2022) analyzed an inclined fin by applying the differential transform method. The unique ability of nano lubricant to reduce corrosion in gaskets and bore pistons and their thermophysical characteristics make them an attractive alternative cooling agents for heat transmission. Gamaoun et al. (Citation2022) investigated a rectangular fin wetted with a ZnO-SAE 50 nanolubricant using the α-PDTM approximation. The results indicated a remarkable improvement in the thermal profile of the fin. Ahmad et al. (Citation2021) investigated the thermal efficiency of a hybrid nanofluid mixture of GO-Ag/kerosene oil on a porous stretching sheet. The model ODE equations were numerically solved using Runge-Kutta’s method to study the effect of the controlling parameters. Hosseinzadeh et al. (Citation2020) studied the impact of various parameters, such as the bio-convection Schmidt number, thermal radiation and Brownian motion on microorganisms. The MHD flow was analysed in the presence of nanoparticles and microorganisms on the surface. The governing equations were numerically solved using Runge-Kutta’s fifth-order method and the results indicated a drop in the microorganism’s profile with an increase in Schmidt number. Fractional calculus has a wide range of applications in various fields. Its usefulness lies in its ability to model complex systems, such as viscoelastic materials, in physics and phenomena with memory effects. Ammembal Gopalkrishna Pai et al. (Citation2024) investigated the thermal behavior of rectangular fin profile under the influence of Spherical shaped TiO2-Ag hybrid Nanoparticles in a water based fluid. The results show a substantial improvement in the thermal efficiency of the rectangular fin. Talbi et al. (Citation2022) investigated the thermal behaviour of longitudinal moving fin wetted with H2O–C2H6O2/GO–MoS2, by obtaining a numerical solution to the governing equation using RKFT45 and analytically using the Duan–Rach approach. Nayan et al. (Citation2022) analyzed the MHD flow characteristics of a hybrid nanofluid using keller box numerical technique over a vertical plate in a porous medium. The outcome showed that the Nusselt number of CuO–water is less than that of Ag–CuO/water, as well as an improvement in the rate of heat transfer of Ag–CuO/water. Jing et al. (Citation2020) applied the FEM and RSM techniques to a rectangular cavity wetted with a hybrid nanofluid with heated fins of various geometries in the presence of magnetic field. Pavithra and Gireesha (Citation2024) investigated the thermal behaviour of the porous moving rectangular fin embedded in a hybrid nanofluid of different nanoparticle shapes using Adomian decomposition Sumudu transformation approach.
In light of broad range of applications and exceptional characteristics of nanoparticles, a detailed investigation on the thermal performance of the proposed model with a novel combination of GO-MoS2-Al2O3 nanoparticles in the base fluid ethylene glycol–water is undertaken. GO nanoparticles enhance the thermal and electrical properties of materials. Due to the high thermal conductivity of GO and MoS2, they are investigated for applications in energy storage devices. GO nanoparticle absorption properties make it a useful material for water treatment solutions. This is particularly relevant in the development of advanced materials for industries like aerospace and automotive. The biocompatibility nature of MoS2 attracts researchers to make use of the material in imaging and drug delivery systems.
In the present investigation carried out, GO-MoS2-Al2O3 nanoparticles added to the base fluid displayed an exceptional properties compared to conventional heat transfer fluids, particularly in terms of enhanced thermal conductivity. The findings demonstrated a notable improvement in the heat transfer rate, with the temperature dispersion over the fin improved by an average of approximately 6% relative to the model posited by Talbi et al. (Citation2022), for various similarity parameters and
In addition, a comparative analysis was carried out in terms of heat transfer rate between the insulated and convective fin tips. The numerical solution to the formulated equations was obtained, and the outcomes were extensively discussed via graphical interpretations.
Methodology
In our proposed “Integrated Ternary Hybrid Nanofluid Porous Fin Model (ITHNPFM),” we have considered a permeable rectangular moving fin. The surface of the fin is assumed to be wetted with ternary hybrid nanofluid mixture GO-MoS2-Al2O3/C2H6O2-H2O. The proposed ITHNPFM is shown in . Darcy’s model was employed in the analysis due to the fin porosity. The fin is initially assumed to be at rest with the base temperature and ambient temperature
respectively. Subsequently, the horizontal movement of the fin with a steady velocity
results in a loss of heat due to radiation and natural convection. The steady velocity eliminates the transient effects. Furthermore, the analysis was carried out with the assumption to enable the simplification of partial differential equation to ordinary differential equation, the proposed model ITHNPFM is assumed to be time invariant. A well-defined boundary condition is established by assuming the temperature of the surrounding medium of the fin to be constant. To simplify the model, few parameters such as thermal conductance at the interface, contact area, contact pressure and surface roughness are eliminated by neglecting the thermal resistance at the interface between the base of the fin and the primary surface. To enhance the computational efficiency and the accuracy of the numerical simulation, the fin’s base temperature is assumed constant, as it facilitates a well-defined boundary condition that serves as a reference point for the temperature distribution along the fin. To reduce the variation in nanoparticle properties and maintain consistent thermal properties and heat transfer, GO-MoS2-Al2O3 nanoparticles and the liquid in the continuous phase are assumed to be at same temperature.
The governing thermal equilibrium equation of the ITHNPFM at an elementary cross-section dx is given by Gireesha et al. (Citation2020):
(1)
(1)
where
and
denotes the volumetric coefficient of thermal expansion, effective density, effective dynamic viscosity, thermal conductivity and specific heat with constant pressure of ternary hybrid nanofluid.
are constant velocity and temperature of the fin. The subscripts f, nf and
denotes fluid, nanofluid and hybrid nanofluid respectively. The axial distance is denoted by
whereas
are the permeability, uniform mass transfer Coefficient. The notation
are used to denote shape factor for radiation heat transfer, Stefan –Boltzmann constant,
for Acceleration due to gravity, Surface emissivity of fin and
for Heat transfer coefficient, Latent heat of water evaporation.
represent the humidity ratio of the saturated air,
porosity and
humidity ratio of the surrounding air. The change in the base fluid thermal conductivity after addition of each nanoparticles are given by Gireesha et al. (Citation2020):
(2)
(2)
(3)
(3)
(4)
(4)
(5)
(5)
(6)
(6)
(7)
(7)
(8)
(8)
Subscripts and
represent the solid nanoparticles 1. (GO), 2. (MoS2) and 3. (Al2O3) respectively.
represent the solid volume fractions of GO, MoS2 and Al2O3. In this investigation, we studied the performance of GO-MoS2-Al2O3/C2H6O2-H2O. The nanoparticle physical properties are listed in .
Table 1. Physical properties of the nanoparticles (Talbi et al. Citation2022; Pavithra et al. 2024).
The coefficient of heat transfer is defined as
(9)
(9)
where,
convective heat transport coefficient at temperature
The proposed model is subjected to following boundary conditions:
Case 1: The tip of the finite length fin is insulated that is, no transfer of heat from the fin tip.
Mathematically:
(10)
(10)
Case 2: The tip of the finite length fin is convective.
(11)
(11)
where is the length of the fin.
The differential equation (Gholinia et al., Citation2020) is non-dimensionalized using the following parameters
(12)
(12)
On substituting the EquationEquations (9)(9)
(9) and Equation(12)
(12)
(12) in (1), ODE is reduced to
(13)
(13)
Also, the boundary conditions in EquationEquations (10)(10)
(10) and Equation(11)
(11)
(11) are reduced to
(14)
(14)
where
denotes non-dimensional power index, wet porous parameter,
denotes non-dimensional convective, radiative parameters,
are non-dimensional Biot, Peclet numbers, and
denotes non-dimensional ambient temperature, respectively. The dimensionless temperature and axial distance are
and
whereas
are the constants.
Numerical procedure
The nonlinear ODE obtained in EquationEquation (13)(13)
(13) is integrated using 3-stage Lobatto – IIIa numerical technique. The exceptional stability and robust convergence characteristics of this technique makes it preferable and highly effective approach to solve boundary value problem. The effectiveness of this method was found in its ability to precisely depict the solution curvature. The BVP4C function incorporating 3-stage Lobatto – IIIa numerical technique of MATLAB simulation tool was employed to obtain the solution.
Results and discussion
The accuracy of the 3-stage Lobatto – IIIa numerical technique was validated by extracting from the existing model proposed by Talbi et al. (Citation2022). The obtained values are tabulated in and were found to be closely aligned with the expected values. displays a comparison between the proposed model and the existing model by Talbi et al. (Citation2022). The results show a substantial improvement in the heat absorption for various similarity parameter values.
Table 2. Validation of the 3-stage Lobatto – IIIa method at with the existing result of Talbi et al. (Citation2022) when
Table 3. Comparison of the proposed convective fin tip ITHNFPFM with the existing result of Talbi et al. (Citation2022) (Numerical values of ) at
when
(a) and (b) depict the repercussion of the Peclet number (P) on the temperature dispersion over the fin for both convective, insulated fin tips. As a general trend, an increment in the Peclet number results in rise in the fin’s temperature profile. This is attributed to the accelerated movement of the fin with higher
values, which consequently reduces the exposure time of the fin to the environment, resulting in an overall enhancement in the temperature. From the simulation result, It was observed that the fin temperature distribution profile enhanced by 3.48% with an increase in the P
value by 100% in the case of a convective tip. In addition, an average improvement of approximately 3.4% in the heat absorption was found in ITHNPFM compared to the model posited by Talbi et al. (Citation2022).
(a) and (b) illustrates the repercussion of the convective variable on the dimensionless fin temperature. The fin temperature dispersion along its length decreases with the elevation in the value of the convective variable. The convective parameter is the combination of Darcy’s and Rayleigh’s numbers. Scaling up its value alters Darcy’s number or Rayleigh’s number, thereby elevating the permeability or buoyancy effect, resulting in improvement in the heat transmission rate. The simulation result showed that an increase of 50% in the
value, reduced the temperature distribution profile by 1% in the proposed model with convective fin tip. In addition, the heat absorption improved by an average of approximately 1% compared to the model posited by Talbi et al. (Citation2022).
Figure 3. (a) Repercussion of on
for convective fin tip and (b) repercussion of
on
for insulated fin tip.
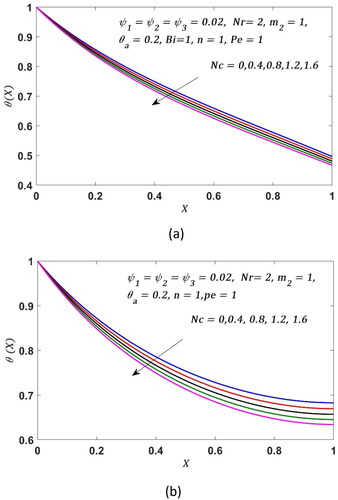
The radiative parameter plays a critical role in optimizing the heat transmission rate. The repercussion of this parameter on the dimensionless fin temperature are illustrated in . Strengthening the value of
indicates a strong radiation effect and correlates with a reduction in fin temperature along its axial length. The outcome is the improvement in the heat transfer mechanisms between the fin and the surrounding ternary hybrid nanofluid. A comprehensive graphical analysis showed that the convective tip fin temperature decreased by 2% with 50% increase in the value of
In addition, the heat absorption improved by average of approximately 18% compared to the model posited by Talbi et al. (Citation2022).
Figure 4. (a) Repercussion of on
for convective fin tip and (b) repercussion of
on
for an insulated fin tip.
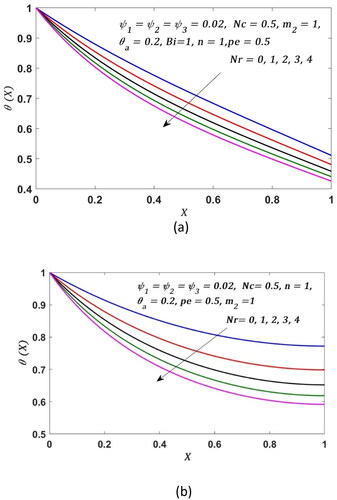
The influence of power index is illustrated in and . The variation indicates the various flow regimes of the temperature dispersion over the fin. The observation shows that the heat distribution is comparatively lower for a linear case (
) than for nonlinear cases (
as the fluid gains more resistance due to increase in non-linearity in its flow. For smaller values of “n” value, fluid flow is linear and the heat is efficiently dissipated from the fin due to lower resistance, keeping the fin cooler. This implies that the heat transmission rate falls for higher values of power index. The investigation results show that the heat absorption of ITHNPFM improved by an average of approximately 2.67% in comparison to the model posited by Talbi et al. (Citation2022).
Figure 5. (a) Repercussion of on
for a convective fin tip and (b) repercussion of
on
for an insulated fin tip.
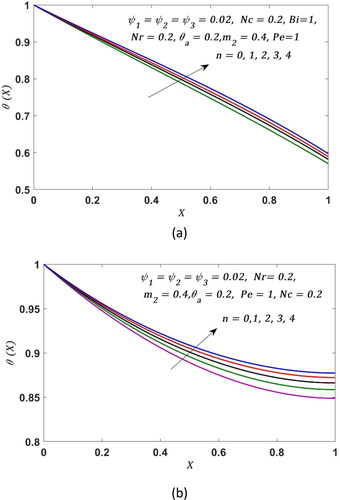
The repercussion of the wet porous parameter () on the dimensionless fin temperature is illustrated in . This trend clearly shows the decrease in temperature dispersion with an increment in the value of
As the value of m2 increases, the fluid flow through the porous medium will be more rapid compared to the free flow, resulting in enhancement of convection heat transfer. This in turn results in drop in fin temperature, enhancing the heat absorption by the surrounding fluid. The investigation results show that the heat absorption of ITHNPFM improved by an average of approximately 0.9% compared to the model posited by Talbi et al. (Citation2022).
Figure 6. (a) Repercussion of on
for a convective fin tip and (b) repercussion of
on
for an insulated fin tip.
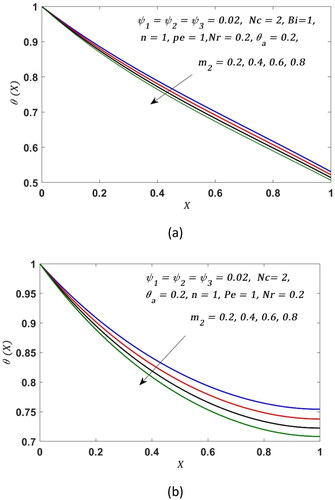
illustrates the repercussion of ambient temperature on the temperature dispersion over the fin. As the value of
increases, the surrounding fluid temperature increases, subsequently impeding the transfer of heat from the fin’s surface. This result in an enhancement in the temperature dispersion over the fin. The simulation outcome shows that the heat absorption of ITHNPFM improved by around 9% compared to the model posited by Talbi et al. (Citation2022).
Figure 7. (a) Repercussion of on
for a convective fin tip and (b) repercussion of
on
for an insulated fin tip.
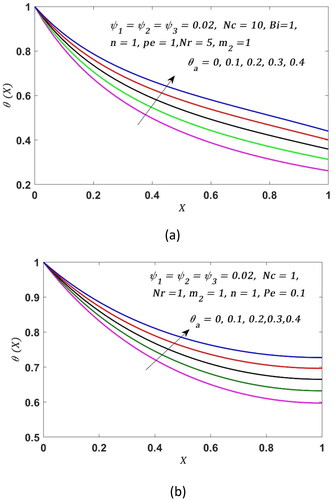
Another key parameter that influence the thermal performance of the proposed model is the Biot number. illustrates the repercussion of this parameter on the temperature dispersion over the fin. The outcome indicates that the heat distribution on the fin is lower for higher values of Biot number, resulting in an improvement in heat transport rate. This is due to the dominance of convection at the surface relative to conduction within the fin for larger values of Biot number. The heat absorption will be more, as the temperature gradient within the fin will be relatively low. For the convective fin tip, the simulation outcome shows that the heat absorption of ITHNPFM improved by an average of approximately 2.6% compared to the model posited by Gireesha et al. (Citation2020).
The overall thermal performance of the ITHNPFM is depicted in the in the form of variation in the heat transfer rate with respect to
and
values, for both convective and insulated tips. The variation clearly shows an enhancement in the rate of heat transfer with an increment in the values of
and
In case of convective fin tip, an enhancement in the heat transfer rate was observed compared to an insulated fin tip. Quantitatively, at
the heat transfer rate of convective fin tip was enhanced by 14.61%, 25% and 6.5% compared to an insulated fin tip.
The shape factor parameter refers to the geometric properties of the nanoparticles dispersed within the material. The repercussion of this parameter on thermal profile of the proposed model for various values are depicted in . From the simulation results obtained, it was observed that for a given value of
the dimensionless temperature of convective fin tip enhanced with the change in the shape of the nanoparticles from spherical to lamina, thus impacting the rate of heat absorption. The ternary hybrid nanofluid containing lamina-shaped nanoparticles demonstrated the most significant elevation in temperature profiles, with cylindrical-shaped nanoparticles exhibiting a moderately lower enhancement, followed by spherical shaped nanoparticles, which showed the least enhancement. Higher values of shape factor exhibits enhanced thermal conductivity along with larger surface area to interact, which can help in enhancing the transfer of convective thermal energy from the fin surface. The result from the analysis indicates that, as we change the shape of the nanoparticles from spherical to cylindrical for
=1, 7.36 % enhancement in the thermal distribution of the fin is observed at
This further enhances by 20.43 %, as we change the shape from cylindrical to lamina, thus making them an optimal choice for selection as they exhibit the highest temperature distribution compared to the other shapes. The effect of lamina shape nanoparticles in a ternary hybrid nanofluid on the temperature dispersion over the fin for various
values is depicted in .
Conclusions
The analysis investigates the heat transmission of the proposed model ITHNPFM with convective and insulated fin tip boundary conditions. Fins are efficient and simple structures used to enhance the heat flow from the surface to the fluid. The thermal performance of a moving fin in a ternary hybrid nanofluid is largely dependent on the flow characteristics of the ternary hybrid nanofluid, including its heat capacity, thermal conductivity, flow resistance and heat flow through convection. In this study, the dimensionless temperature profile of the fin and the heat transfer rate influenced by various similarity parameters and shape factors are comprehensively analysed in evaluating the thermal performance of the ITHNPFM.
Natural convection and radiation exert a profound impact on the heat absorption. An increase in convective, radiative and wet porous parameters results in an enhanced heat absorption by the ternary hybrid nanofluid.
Enhancement in the heat transfer rate is more in a fin with convective tip compared to an insulated tip. The heat flux enhances with the increase in the radiative, wet porous and convective parameters.
The temperature dispersion on the fin enhances with the increase in the value of power index and peclet number.
Adding ternary combination of nanoparticles to the base fluid improved the heat absorption compared to hybrid nanofluid.
The ternary hybrid nanofluid containing lamina-shaped nanoparticles demonstrated the most significant elevation in temperature profiles, relative to cylindrical and spherical shape nanoparticles.
Further research can be carried out:
To optimize the combination of nanoparticle types, sizes, and concentrations, as well as base fluid properties, to maximize heat transfer performance. This could involve experimental studies and computational simulations to identify the most effective hybrid nanofluid formulations.
To investigate the dynamic response of fins of different geometries immersed in hybrid nanofluids under varying operating conditions. This can provide insights into their performance in practical applications and enable the development of more robust heat transfer systems.
To experimentally verify the simulated data under realistic operating conditions, to bridge the gap between theoretical predictions and practical implementation. This will provide valuable insights into the feasibility and effectiveness of this technology in practical applications.
Author contributions
Conceptualization, Rekha G. Pai, Ammembal Gopalkrishna Pai; Methodology, Rekha G. Pai, Ammembal Gopalkrishna Pai; Software, Ammembal Gopalkrishna Pai, Rekha G. Pai; Validation, Rekha G. Pai; formal analysis, Ammembal Gopalkrishna Pai, Rekha G. Pai; Writing—Original draft preparation, Ammembal Gopalkrishna Pai, Rekha G. Pai; Writing—review and editing, Rekha G. Pai, Ammembal Gopalkrishna Pai; Supervision, Ammembal Gopalkrishna Pai, Rekha G. Pai.
Nomenclature | ||
= | Local fin Temperature(K) | |
= | Axial coordinate(m) | |
= | Constant velocity of the fin (m/s) | |
K | = | Permeability(N/A2) |
= | Specific heat at constant pressure (J/KgK) | |
= | Shape factor for radiation heat transfer | |
L | = | Length of the fin(m) |
= | Convective Parameter | |
= | Radiative Parameter | |
Pe | = | Peclet Number |
= | Ambient Temperature(K) | |
= | Base Temperature | |
= | Density (Kg/m3) | |
= | Dimensionless ambient temperature | |
= | Dynamic Viscosity (Kg/ms) | |
= | Humidity ratio of the saturated air | |
= | Humidity ratio of the surrounding air | |
= | Latent heat of water evaporation(J/Kg) | |
a | = | Ambient |
b | = | Base of fin |
f | = | Fluid |
nf | = | nano fluid |
hnf | = | Hybrid nanofluid |
thnf | = | Ternary nanofluid |
p1, p2 | = | Nanoparticles |
g | = | Acceleration due to gravity(m/s2) |
= | Heat transfer coefficient(W/m2K) | |
= | Heat transfer coefficient at temperature | |
= | Uniform mass transfer Coefficient | |
= | Thermal conductivity(W/mK) | |
n | = | Power index of Temperature dependenth |
t | = | Fin Thickness |
w | = | Width (m) |
= | Wet porous Parameter | |
X | = | Dimensionless axial Coordinate |
= | Constants | |
= | Non dimensional Temperature | |
= | Porosity | |
= | Solid Volume fraction of nanoparticles | |
= | Stefan –Boltzmann constant | |
= | Surface emissivity of fin | |
= | Volumetric coefficient thermal expansion (1/K) |
Disclosure statement
No potential conflict of interest was reported by the authors.
Data availability statement
The data that support the findings of this study are available from the corresponding author [R.G.P.], upon reasonable request.
Additional information
Funding
Notes on contributors
Ammembal Gopalkrishna Pai
Ammembal Gopalkrishna Pai obtained his B.Tech degree in 2000 from Mangalore University, Karnataka, India. He is currently Assistant Professor in the Department of Electronics and Communication, Manipal Institute of Technology, Manipal Academy of Higher Education, Manipal. He has published several articles in many International Journals and Conferences. His research area includes Nanofluids, Heat transfer, Nano Electronics and Integrated Circuits.
Rekha G. Pai
Rekha G. Pai obtained her M.Sc. degree in Mathematics in the year 2001 from Kuvempu University, Karnataka, India and PhD degree in Fluid Mechanics in the year 2015 from National Institute of Technology Karnataka, Surathkal, India. She is currently Associate Professor in the Department of Mathematics at Manipal Institute of Technology, Manipal Academy of Higher Education, Manipal. She has published several articles in many International Journals and Conferences in the field of Fluid Mechanics. Her research area includes Fluid Mechanics, Nanofluids, Heat transfer and Computational Fluid Dynamics.
References
- Hosseinzadeh, K., Mogharrebi, A. R., Asadi, A., Paikar, M., & Ganji, D. D. (2020). Effect of fin and hybrid nano-particles on solid process in hexagonal triplex latent heat thermal energy storage system. Journal of Molecular Liquids, 300, 112347. https://doi.org/10.1016/j.molliq.2019.112347
- Kundu, B., & Das, P. K. (1999). Performance analysis of eccentric annular fins with a variable base temperature. Numerical Heat Transfer: Part A: Applications, 36(7), 751–766. https://doi.org/10.1080/104077899274552
- Ahmad, A., Sulaiman, M., Alhindi, A., & Aljohani, A. J. (2020). Analysis of temperature profiles in longitudinal fin designs by a novel neuroevolutionary approach. IEEE Access, 8, 113285–113308. https://doi.org/10.1109/ACCESS.2020.3003253
- Ahmad, F., Abdal, S., Ayed, H., Hussain, S., Salim, S., & Othman Almatroud, A. (2021). The improved thermal efficiency of Maxwell hybrid nanofluid comprising of graphene oxide plus silver/kerosene oil over stretching sheet. Case Studies in Thermal Engineering, 27, 101257. https://doi.org/10.1016/j.csite.2021.101257
- Ahmad, S., Naveed Khan, M., & Nadeem, S. (2022). Unsteady three dimensional bioconvective flow of Maxwell nanofluid over an exponentially stretching sheet with variable thermal conductivity and chemical reaction. International Journal of Ambient Energy, 43(1), 6542–6552. https://doi.org/10.1080/01430750.2022.2029765
- Al-Hossainy, A. F., & Eid, M. R. (2021). Combined experimental thin films, TDDFT-DFT theoretical method, and spin effect on [PEG-H2O/ZrO2+ MgO] hybrid nanofluid flow with higher chemical rate. Surfaces and Interfaces, 23, 100971. https://doi.org/10.1016/j.surfin.2021.100971
- Ammembal Gopalkrishna Pai, Rekha G. Pai, Lavanya B, Vinay Madhusudanan, Sanjana T.D., Performance analysis of wet porous moving fin under the influence of spherical shaped TiO2-Ag hybrid nanoparticles in a water based fluid. CFD Letters, 7, 16(2024): 105–117. https://doi.org/10.37934/cfdl.16.7.105117
- Din, Z. U., Ali, A., Khan, Z. A., & Zaman, G. (2023). Investigation of moving trapezoidal and exponential fins with multiple nonlinearities. Ain Shams Engineering Journal, 14(5), 101959. https://doi.org/10.1016/j.asej.2022.101959
- Fallah Najafabadi, M., Talebi Rostami, H., Hosseinzadeh, K., & Domiri Ganji, D. (2021). Thermal analysis of a moving fin using the radial basis function approximation. Heat Transfer, 50(8), 7553–7567. https://doi.org/10.1002/htj.22242
- Gamaoun, F., Said, N. M., Makki, R., Varun Kumar, R. S., Sowmya, G., Prasannakumara, B. C., & Kumar, R. (2022). Energy transfer of a fin wetted with ZnO-SAE 50 nanolubricant: An application of α-parameterized differential transform method. Case Studies in Thermal Engineering, 40, 102501. https://doi.org/10.1016/j.csite.2022.102501
- Ghadikolaei, S. S., Yassari, M., Sadeghi, H., Hosseinzadeh, K., & Ganji, D. D. (2017). Investigation on thermophysical properties of Tio2–Cu/H2O hybrid nanofluid transport dependent on shape factor in MHD stagnation point flow. Powder Technology, 322, 428–438. https://doi.org/10.1016/j.powtec.2017.09.006
- Gholinia, M., Hosseinzadeh, K., & Ganji, D. D. (2020). Investigation of different base fluids suspend by CNTs hybrid nanoparticle over a vertical circular cylinder with sinusoidal radius. Case Studies in Thermal Engineering, 21, 100666. https://doi.org/10.1016/j.csite.2020.100666
- Gireesha, B. J., Sowmya, G., Ijaz Khan, M., & Öztop, H. F. (2020). Flow of hybrid nanofluid across a permeable longitudinal moving fin along with thermal radiation and natural convection. Computer Methods and Programs in Biomedicine, 185, 105166. https://doi.org/10.1016/j.cmpb.2019.105166
- Girish, R., Salma, A., Ananth Subray, P. V., Hanumagowda, B. N., Varma, S. V. K., Nagaraja, K. V., Singh Chohan, J., Khan, U., Hassan, A. M., & Gamaoun, F. (2023). Effect of temperature-dependent internal heat generation over exponential and dovetail convective-radiative porous fin wetted in hybrid nanofluid. Case Studies in Thermal Engineering, 49, 103214. https://doi.org/10.1016/j.csite.2023.103214
- Goud, J. S., Srilatha, P., Varun Kumar, R. S., Kumar, K. T., Khan, U., Raizah, Z., Gill, H. S., & Galal, A. M. (2022). Role of ternary hybrid nanofluid in the thermal distribution of a dovetail fin with the internal generation of heat. Case Studies in Thermal Engineering, 35, 102113. https://doi.org/10.1016/j.csite.2022.102113
- Hosseinzadeh, K., Asadi, A., Mogharrebi, A. R., Ermia Azari, M., & Ganji, D. D. (2021). Investigation of mixture fluid suspended by hybrid nanoparticles over vertical cylinder by considering shape factor effect. Journal of Thermal Analysis and Calorimetry, 143(2), 1081–1095. https://doi.org/10.1007/s10973-020-09347-x
- Hosseinzadeh, K., Salehi, S., Mardani, M. R., Mahmoudi, F. Y., Waqas, M., & Ganji, D. D. (2020). Investigation of nano-bioconvective fluid motile microorganism and nanoparticle flow by considering MHD and thermal radiation. Informatics in Medicine Unlocked, 21, 100462. https://doi.org/10.1016/j.imu.2020.100462
- Hussain, F., Hussain, A., & Nadeem, S. (2022). Unsteady shear-thinning behaviour of nanofluid flow over exponential stretching/shrinking cylinder. Journal of Molecular Liquids, 345, 117894. https://doi.org/10.1016/j.molliq.2021.117894
- Jing, D., Hu, S., Hatami, M., Xiao, Y., & Jia, J. (2020). Thermal analysis on a nanofluid-filled rectangular cavity with heated fins of different geometries under magnetic field effects. Journal of Thermal Analysis and Calorimetry, 139(6), 3577–3588. https://doi.org/10.1007/s10973-019-08758-9
- Keerthi, M. L., Gireesha, B. J., & Sowmya, G. (2022). Numerical investigation of efficiency of fully wet porous convective-radiative moving radial fin in the presence of shape-dependent hybrid nanofluid. International Communications in Heat and Mass Transfer, 138, 106341. https://doi.org/10.1016/j.icheatmasstransfer.2022.106341
- Kezzar, M., Tabet, I., & Eid, M. R. (2020). A new analytical solution of longitudinal fin with variable heat generation and thermal conductivity using DRA. The European Physical Journal Plus, 135(1), 1–15. https://doi.org/10.1140/epjp/s13360-020-00206-0
- Nayan, A., N. I. F. A. Fauzan, M. R. Ilias, S. F. Zakaria, and N. H. Z. Aznam. (2022). Aligned magnetohydrodynamics (MHD) flow of hybrid nanofluid over a vertical plate through porous medium. Journal of Advanced Research in Fluid Mechanics and Thermal Sciences, 92 1), 51–64. https://doi.org/10.37934/arfmts.92.1.5164
- Pavithra, C. G., & Gireesha, B. J. (2024). Heat transfer in a wet porous moving inclined longitudinal fin exposed to convection and radiation in the presence of shape-dependent hybrid nanofluid: Adomian decomposition Sumudu transformation approach. Journal of Molecular Liquids, 393, 123582. https://doi.org/10.1016/j.molliq.2023.123582
- Puneeth, V., Anandika, R., Manjunatha, S., Khan, M. I., Imran Khan, M., Althobaiti, A., & Galal, A. M. (2022). Implementation of modified Buongiorno’s model for the investigation of chemically reacting rGO-Fe3O4-TiO2-H2O ternary nanofluid jet flow in the presence of bio-active mixers. Chemical Physics Letters, 786, 139194. https://doi.org/10.1016/j.cplett.2021.139194
- Talbi, N., Kezzar, M., Malaver, M., Tabet, I., Sari, M. R., Metatla, A., & Eid, M. R. (2022). Increment of heat transfer by graphene-oxide and molybdenum-disulfide nanoparticles in ethylene glycol solution as working nanofluid in penetrable moveable longitudinal fin. Waves in Random and Complex Media, 1–23. https://doi.org/10.1080/17455030.2022.2026527
- Turkyilmazoglu, M. (2021). Thermal management of parabolic pin fin subjected to a uniform oncoming airflow: optimum fin dimensions. Journal of Thermal Analysis and Calorimetry, 143(5), 3731–3739. https://doi.org/10.1007/s10973-020-10382-x
- Venkateswarlu, B., & Satya Narayana, P. V. (2021). Cu‐Al2O3/H2O hybrid nanofluid flow past a porous stretching sheet due to temperatue‐dependent viscosity and viscous dissipation. Heat Transfer, 50(1), 432–449. https://doi.org/10.1002/htj.21884
- Wang, F., Varun Kumar, R. S., Sowmya, G., El-Zahar, E. R., Prasannakumara, B. C., Khan, M. I., Khan, S. U., Malik, M. Y., & Xia, W.-F. (2022). LSM and DTM-Pade approximation for the combined impacts of convective and radiative heat transfer on an inclined porous longitudinal fin. Case Studies in Thermal Engineering, 35, 101846. https://doi.org/10.1016/j.csite.2022.101846
- Weera, W., Varun Kumar, R. S., Sowmya, G., Khan, U., Prasannakumara, B. C., Mahmoud, E. E., & Yahia, I. S. (2023). Convective-radiative thermal investigation of a porous dovetail fin using spectral collocation method. Ain Shams Engineering Journal, 14(1), 101811. https://doi.org/10.1016/j.asej.2022.101811