Figures & data
Figure 1. A schematic presentation of the combustion process shows, a) hotspot/coolspot initial T profile, b) centered ignition and regular propagation inside the hotspot/coolspot, c) off-centered primary ignition due to NTC and double ignition front propagation, and d) occurrence of primary ignition and subsequently, formation of the secondary ignition kernel due to NTC.
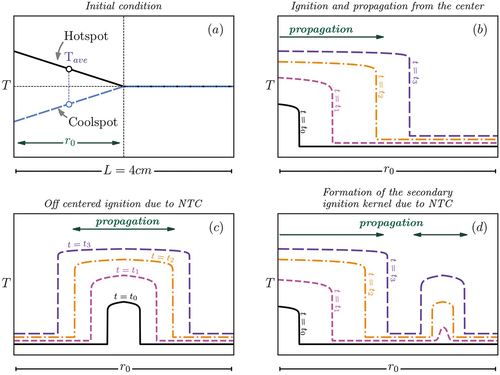
Figure 2. PRF and PRF-E ignition delay time versus temperature profiles at P = 20 and 50 bar, black circles are marking the locations of the studied cases.
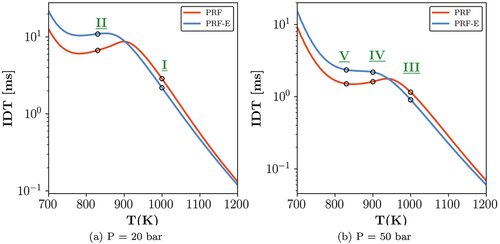
Table 1. Conditions for the five cases: pressure, average temperature, IDT, excitation time, IDT gradient versus temperature, acoustic speed, and constant volume pressure.
Table 2. Conditions for the five cases: pressure, average temperature, energy density, von-Neumann pressure, detonation equilibrium pressure, CJ velocity, and induction length ratio.
Figure 3. Ignition regime diagram of case I ( = 20 bar and
= 1000 K), red zone indicates the detonation peninsula of a) PRF and b) PRF-E mixtures, respectively. Colored circles display the hotspot pressure calculated for each 1D simulation. Letters P, B, and N indicate supersonic ignition, subusonic ignition and the nominal condition for knock initiation inside SI engines (Kalghatgi et al. Citation2009). c) IDT distribution at the initial time versus T of PRF and PRF-E mixtures.
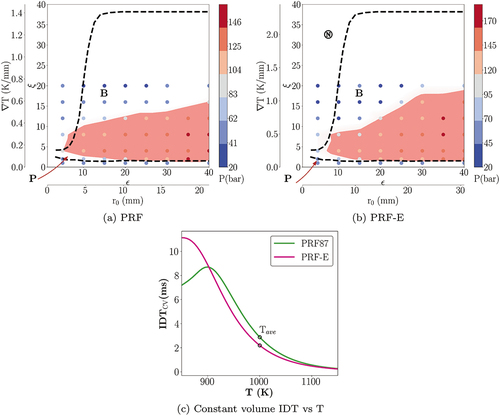
Figure 4. Ignition regime diagram of case II ( = 20 bar and
= 830 K), red zone indicates the detonation peninsula of a) PRF and b) PRF-E mixtures, respectively. Colored circles display the hotspot pressure calculated for each 1D simulation. Letters P, B, and N indicate supersonic ignition, subusonic ignition and the nominal condition for knock initiation inside SI engines (Kalghatgi et al. Citation2009). c) IDT distribution at the initial time versus T of PRF and PRF-E mixtures.
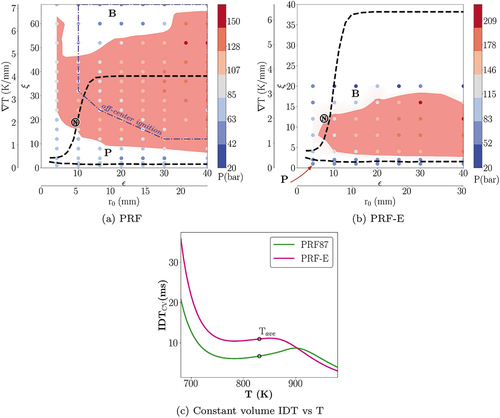
Figure 5. Ignition regime diagram of case III ( = 50 bar and
= 1000 K), red zone indicates the detonation peninsula of a) PRF and b) PRF-E mixtures, respectively. Colored circles display the hotspot pressure calculated for each 1D simulation. Letters P, B, and N indicate supersonic ignition, subusonic ignition and the nominal condition for knock initiation inside SI engines (Kalghatgi et al. Citation2009). c) IDT distribution at the initial time versus T of PRF and PRF-E mixtures.
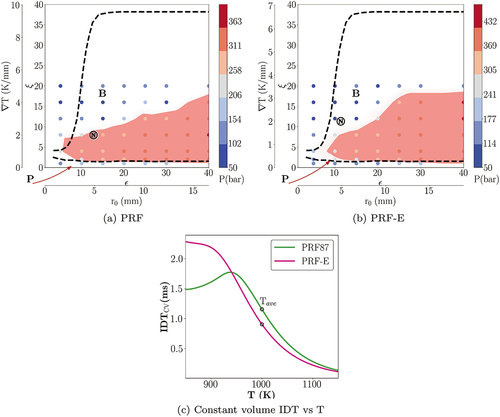
Figure 6. Ignition regime diagram of case I ( = 50 bar and
= 900 K), red zone indicates the detonation peninsula of a) PRF and b) PRF-E mixtures, respectively. Colored circles display the hotspot pressure calculated for each 1D simulation. Letters P, B, and N indicate supersonic ignition, subusonic ignition and the nominal condition for knock initiation inside SI engines (Kalghatgi et al. Citation2009). c) IDT distribution at the initial time versus T of PRF and PRF-E mixtures.
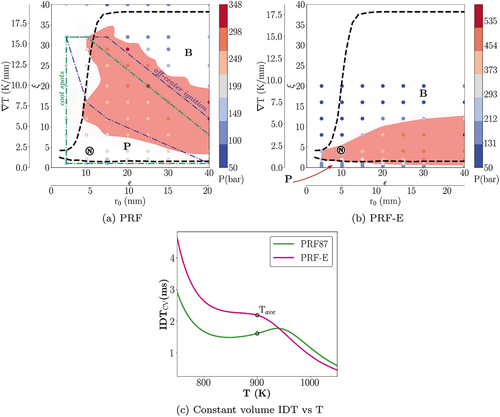
Figure 7. Ignition regime diagram of case V ( = 50 bar and
= 830 K), red zone indicates the detonation peninsula of a) PRF and b) PRF-E mixtures, respectively. Colored circles display the hotspot pressure calculated for each 1D simulation. Letters P, B, and N indicate supersonic ignition, subusonic ignition and the nominal condition for knock initiation inside SI engines (Kalghatgi et al. Citation2009). c) IDT distribution at the initial time versus T of PRF and PRF-E mixtures.
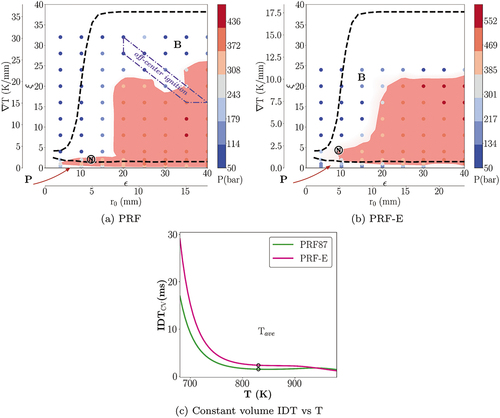
Figure 8. Predicted detonation peninsula of case I and II using the second method, i.e. The contours depict the maximum hotspot pressure normalized by the von Neumann pressure. Letters P, and B indicate supersonic ignition and subusonic ignition regimes.
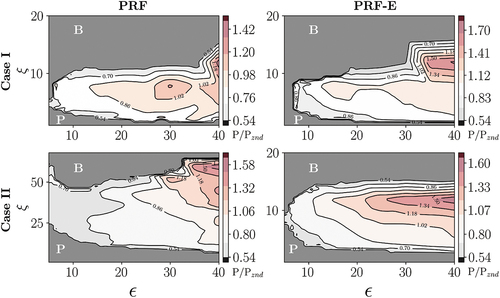
Figure 9. Predicted detonation peninsula of case III-V using the second method, i.E. The contours depict the maximum hotspot pressure normalized by the von Neumann pressure. Letters P, and B indicate supersonic ignition and subusonic ignition regimes.
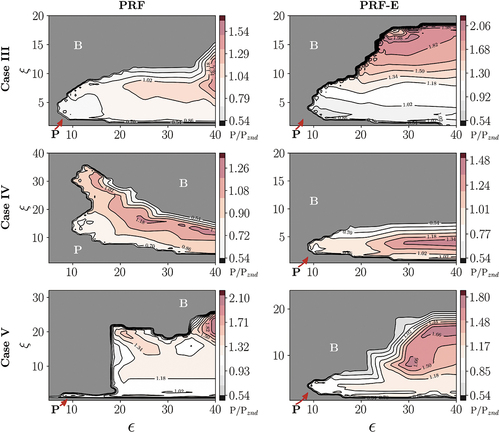
Table 3. Pressure intensity levels at the nominal point location and inside the detonation peninsula for case I-V. Additionally, the table shows the degree of the NTC behavior observed in 1D simulations for case I-V.
Figure 10. Locations of selected points on PRF mixture regime diagram for transient analysis at 50 bar and 900 K, case IV.
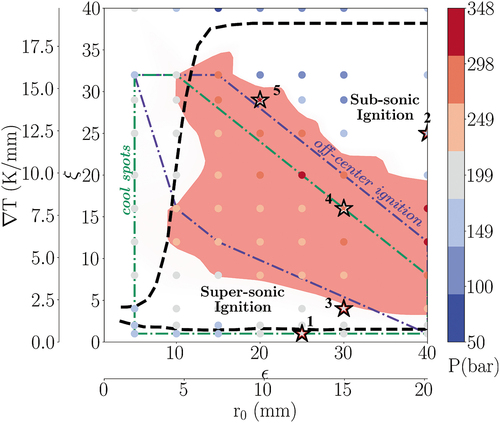
Figure 11. Transient profiles of temperature and normalized pressure at point 1 for PRF mixture at case IV (T = 900 K and P = 50 bar), demonstrating supersonic ignition propagation.
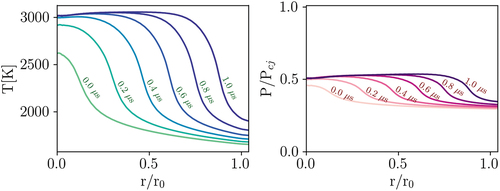
Figure 12. Transient profiles of temperature and normalized pressure at point 2 for PRF mixture at case IV (T = 900 K and P = 50 bar), demonstrating subsonic ignition propagation.
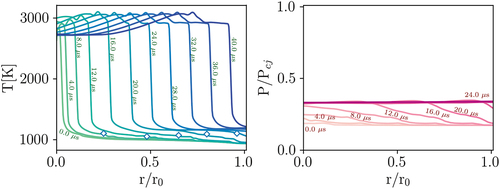
Figure 13. Transient profiles of temperature and normalized pressure at point 3 for PRF mixture at case IV (T = 900 K and P = 50 bar), demonstrating detonation development.
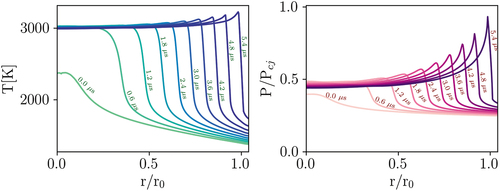
Figure 14. Transient profiles of temperature and normalized pressure at point 4 for PRF mixture at case IV (T = 900 K and P = 50 bar), demonstrating occurrence of off-centered ignition.
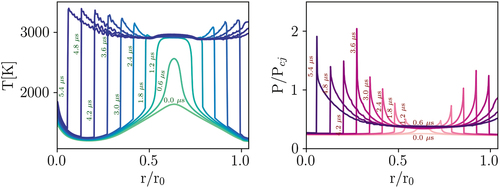
Figure 15. Transient profiles of temperature and normalized pressure at point 5 for PRF mixture at case IV (T = 900 K and P = 50 bar), demonstrating appearance of secondary ignition.
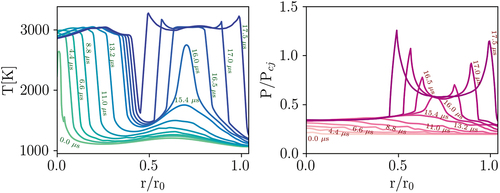
Table A1. Test case configuration.
Figure A1. Sod’s shocktube pressure, velocity, density and acoustic speed distribution versus analytical solution at 0.1644 s.
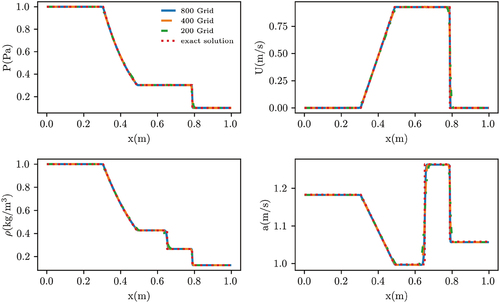
Table A2. Test case configuration.
Figure A2. Temperature profiles (dashed lines are from (Pan et al. Citation2019), solid lines are from the present work) and reaction, pressure fronts speeds for methane hotspot detonation, atm,
K,
K/mm,
mm. CJ speed is calculated at
using SDToolbox (Kao and Shepherd Citation2008).
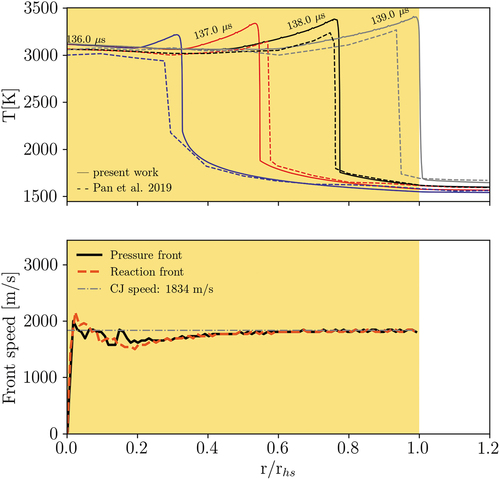
Table A3. Grid sensitivity case configuration.
Figure A3. Mesh sensitivity study for case.Black dashed-line result from grid size = , Blue solid line results from grid size = 0.75
, red dashed-line results from grid size = 0.5
.
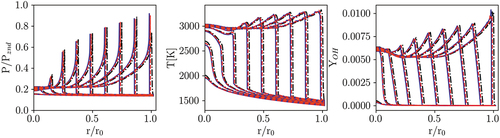
Figure B1. The ZND detonation structures of case I-V for PRF and PRF-E mixtures. The blue lines depict the heat release profiles, and the red-dashed lines depict the temperature profiles. L1 and L2 indicate the first and second induction lengths, respectively.
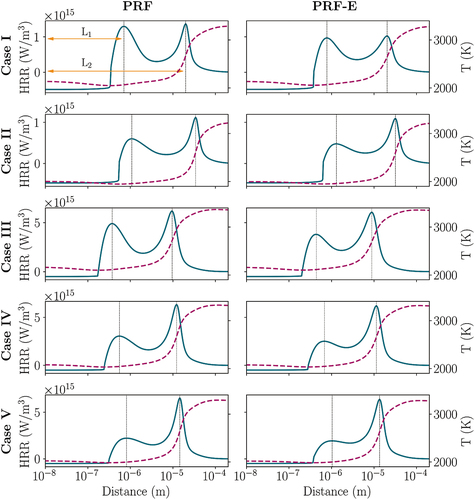
Figure C1. Transient temperature and pressure profiles as well as distribution of maximum pressure for a hotspot detonation scenario. Clusters are separated by colors. Yellow circles indicate the mean value calculated for each cluster.
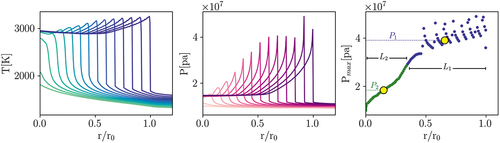