Figures & data
FIG. 1 Photograph of the practical situation for LFS nanocoating the roll-to-roll paperboard. The distance from burner face to paperboard is 15 cm.
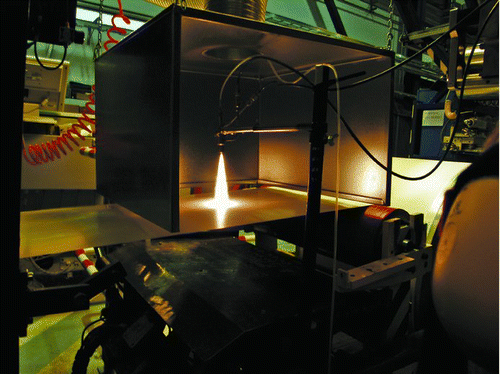
FIG. 2 Schematic of the LFS-coating process. The precursor liquid is fed by a syringe pump. The hydrogen (atomizing gas) and oxygen flows are controlled by mass flow controllers. Also the two heights used in the calculation, boundary layer height δ above the paperboard surface and the turbulent transport layer height h, are shown.
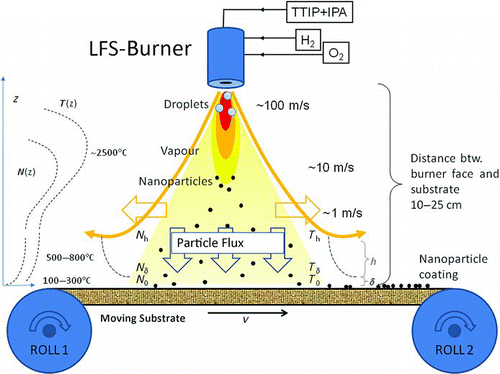
FIG. 3 Schematic of using only one coaxial burner for coating the moving paperboard, i.e., creating a narrow stripe for testing the method principles. The dashed rectangular area denotes the 1 cm × 15 cm sized area from where the chemical analysis was performed.
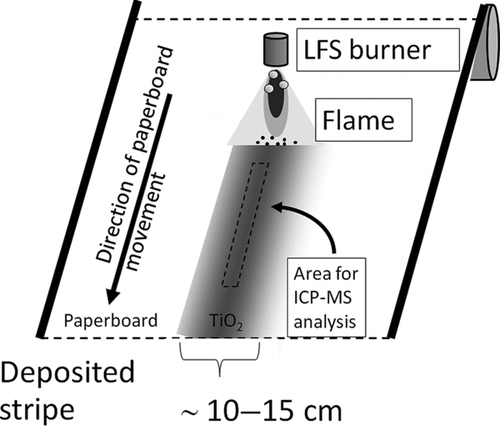
FIG. 4 Schematic of the main particle transport mechanisms in the liquid-flame-spray-driven nanoparticle coating of moving flexible roll-to-roll material. Only one half of the flame (shooting downward) is illustrated. Convective transport of particles occurs in the actual flame impinging toward the paperboard, turbulent transport moves the particles to the boundary layer, and finally, thermophoresis transports the particles through the boundary layer onto the paperboard. The particle losses are assumed to occur both by diffusion perpendicular to the downward flow (LOSS 1) and by horizontal convection above the paperboard (LOSS 2).
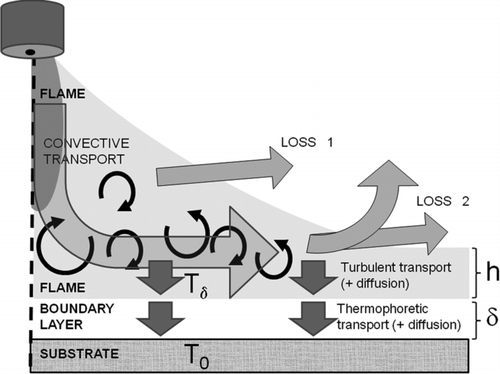
FIG. 5 Flame (gas) temperatures at various distances from the burner face. Measurements in this study using gas flows of H2 = 50 l/min and O2 = 15 l/min, and varying the IPA feed rate: (a) no IPA feeding, (b) feed rate of IPA = 8 ml/min, (c) feed rate of IPA = 15 ml/min, (d) feed rate of IPA = 30 ml/min.
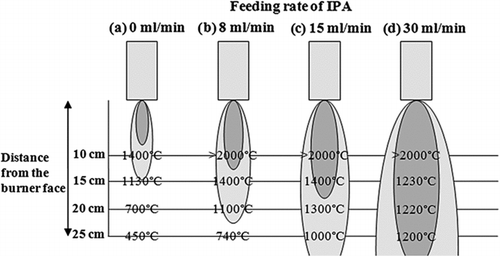
TABLE 1 Temperatures (°C) of the paperboard surface directly after the flame, measured from a spot 50 cm downstream of the flame using a pyrometer. The IPA feed rate of 23 ml/min corresponds to the “base case” used in this article
FIG. 6 A set of FEG-SEM graphs for four different line speeds: (a) 30 m/min, (b) 70 m/min, (c) 100 m/min, and (d) 150 m/min. Liquid feed rate, 23 ml/min; (atomic) Ti concentration in precursor, 50 mg/ml; distance from burner face to paperboard, 15 cm (base case).
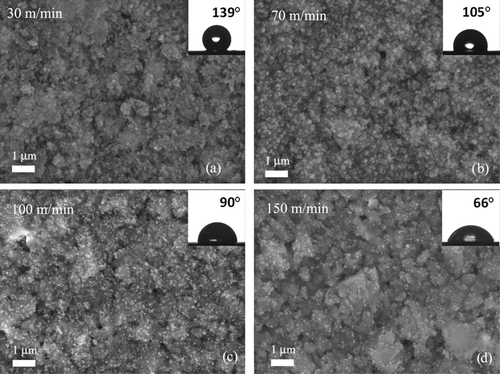
FIG. 7 (a) Particle size on the paperboard (bullets), estimated from FEG-SEM graphs, such as shown in Figure 8, given here as a function of the estimated residence time of substrate within the flame. The shortest residence time refers to a line speed of 150 m/min, and the highest time refers to a line speed of 30 m/min. (b) A TEM image of the particles collected from the flame with a TEM sampler. One fast sweep of collection through the flame was taken.
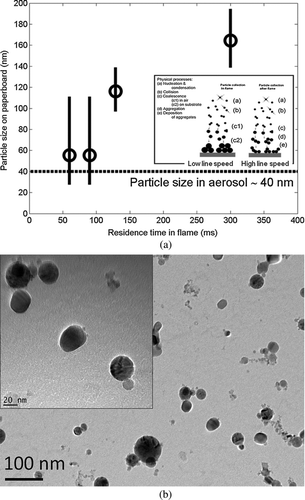
FIG. 8 A FEG-SEM graph of the paperboard coated with parameters: line speed, 150 m/min; liquid feed rate, 32 ml/min; Ti concentration, 50 mg/ml; distance from burner face to paperboard, 15 cm.
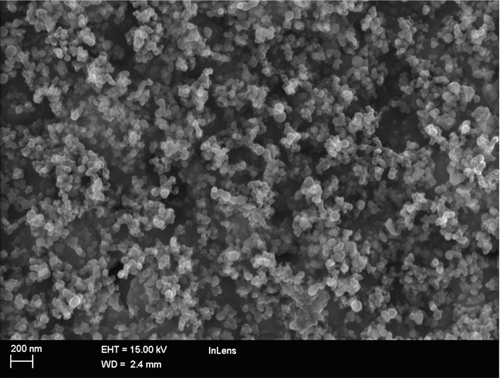
FIG. 9 Three 3D-AFM images of (a) the uncoated reference paperboard, (b) coated paperboard, and (c) the coated aluminum foil using identical parameters: line speed, 30 m/min; liquid feed rate, 32 ml/min; Ti concentration, 11.9 mg/ml. Comparison of (a) and (b) indicates the clear sintering of the titania nanoparticles on the paperboard. The aluminum foil is assumed to conduct some of the excess heat away from the surface to eventually weaken the particle sintering. Furthermore, coverage of around 100% is also suggested in this case.
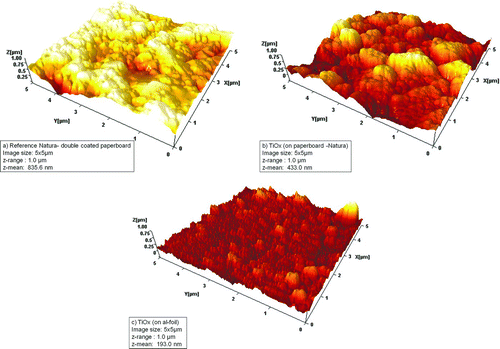