Figures & data
FIG. 1 Design concept of the BASE. The interstitial inlet is located toward the aft of the blunt body housing, below the line of sight of large droplets, and above the region where shatter particles are present. (Color figure available online.)
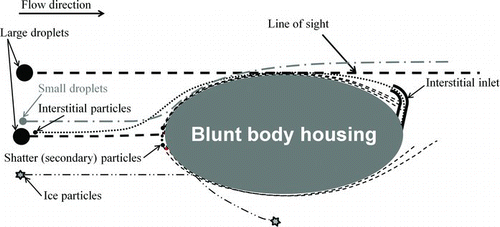
FIG. 2 Particle trajectories around double cone geometries of different aspect ratios. (a) and (b): Particle size separation increases with decreasing front cone chord length. (c) At very short cone chord lengths, flow separation results and size separation region decreases. All dimensions are in inches.
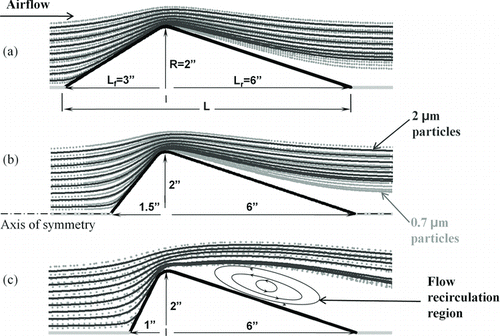
FIG. 3 The final shape of the BASE blunt body housing. Particle trajectories for 2 μm and 0.7 μm are shown on the top half of the geometry and flow streamlines are shown in the lower half. The location of the interstitial inlet is indicated with a line segment.
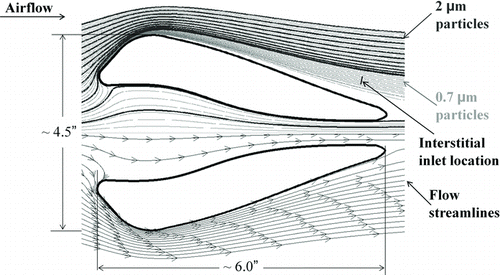
FIG. 5 Sampling efficiency of the inlet as function of aerodynamic diameter and Stokes number. The Stokes number is calculated based on freestream velocity and blunt body diameter.
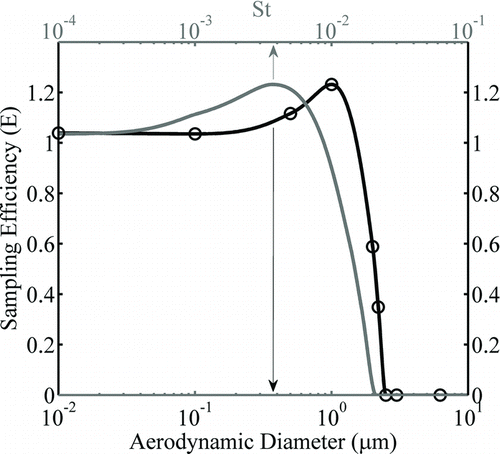
FIG. 6 The calculated sampling efficiencies of simulated shatter particles injected at the surface of the blunt body housing with 100 ms−1 normal velocity with respect to the surface of the body.
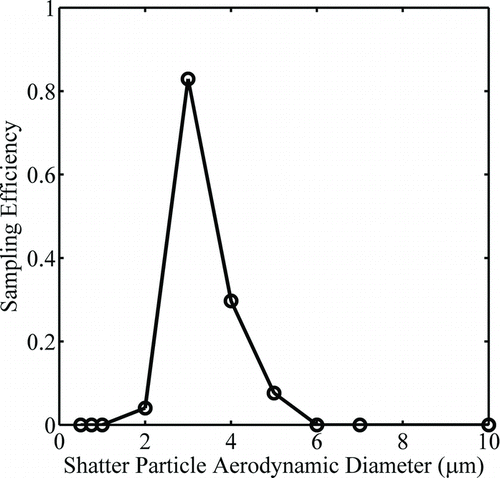
FIG. 7 The schematic diagram of the wind tunnel experimental setup used for initial validation of the BASE design concept.
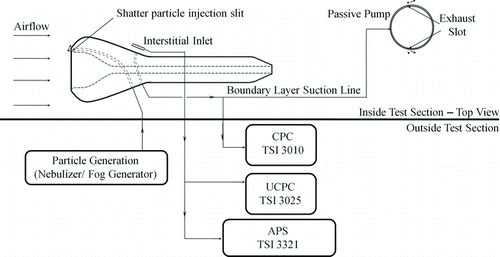
FIG. 8 Wind tunnel measurements of total number concentrations in the BASE boundary layer and interstitial inlet sample flow for cases of: no shatter particle injection (0–60 s) and nebulized shatter particle injection (60–120 s).
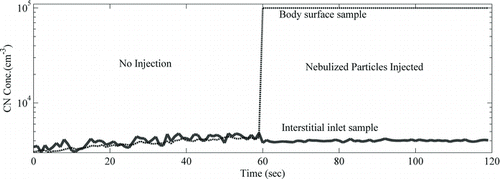
FIG. 9 Wind tunnel measurements of particle size distribution in the BASE boundary layer and interstitial inlet sample flow for cases of: no shatter particle injection and nebulized shatter particle injection.
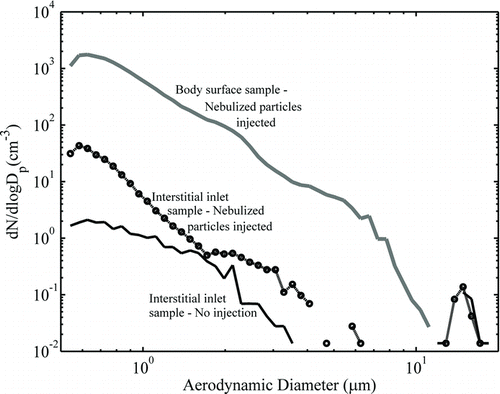
FIG. 10 Ratio of shatter particle concentration in the interstitial inlet to that in the body surface sample
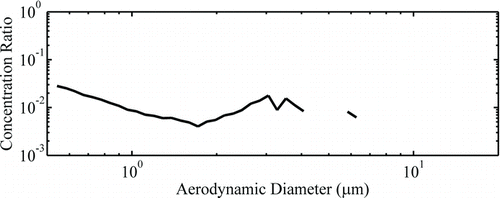
FIG. 11 Shatter particle size distribution in the interstitial inlet and the body surface sample and their ratio for the fog particle injection case.
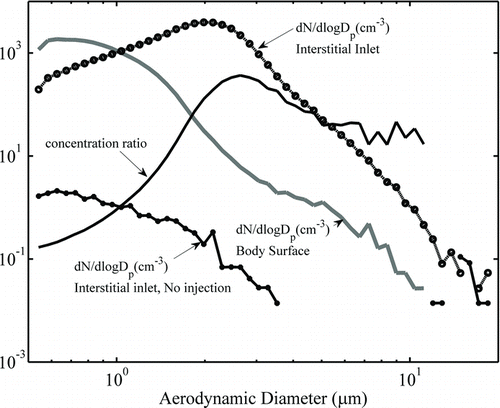