Figures & data
Table 1. Simulation parameters of the aerosol at the outlet of the capillary.
Figure 3. Mass flow of the sheath gas (Argon) over aerosol mass flow in double logarithmic representation. Upright crosses: Parameter combinations with successful function (no wall contact), tilted crosses: No functioning operation is possible (wall contact of the aerosol). The dashed straight line gives the limit range of functioning operating points. Circle: Operating point chosen for further simulations.
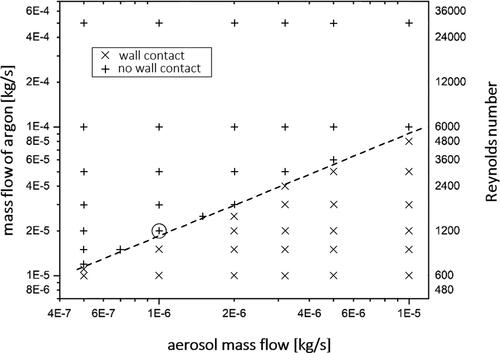
Figure 5. Left: Trajectories of the droplets in dependence of the nozzle angle. Red marked is the respective position of the focal point. Right: Variation of the Stokes number for two nozzle angles (10°, 15°).

Figure 7. (a) to (c) Velocity distributions in the antechamber outer rings and the mixing chamber inner disk for three different geometries of the antechamber. The dashed lines specify the direction of the respective profile. (d) Scaled velocity distribution in the mixing chamber only (design case ).
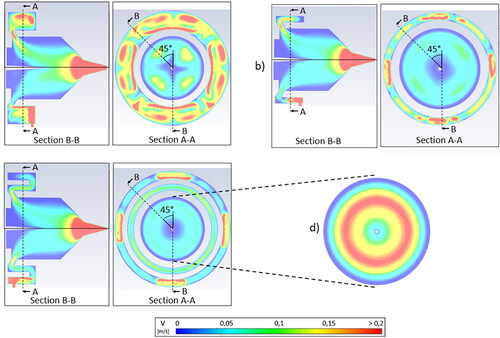