Figures & data
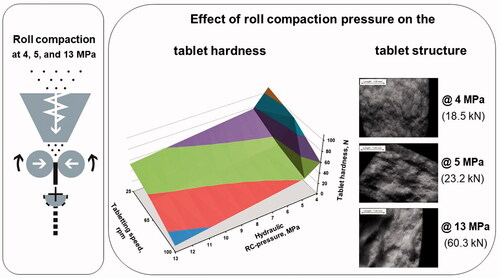
Table 1. The composition of granules and tablet core.
Figure 1. The schematic illustration of the roll compactor and the main functional parts: (1) vertical forced screw feeder; (2) compaction rolls; (3) rotor sieving mill.

Table 2. Summarized process conditions of granules manufacturing with industrial roll compactor.
Table 3. Parameters of the coating process.
Figure 3. Particle size distribution (A and C) and cumulative weight fractions (B and D) of piracetam substance before and after milling (A and B) and roll compacted granulates (C and D).
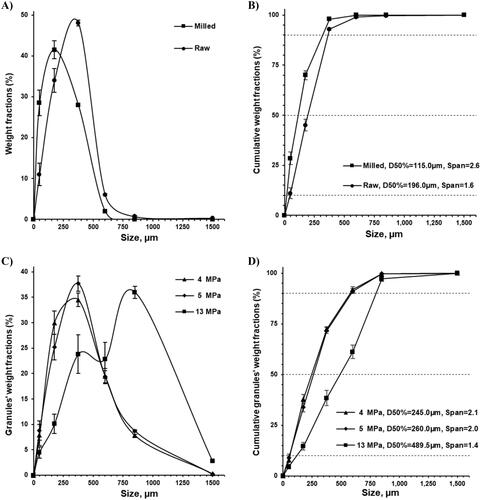
Table 4. Endotherm onset and peak temperatures for raw, milled and for roll compacted and then milled piracetam.
Figure 6. Light microscopy of roll compacted granules, cross-section (after determination of tablets hardness) and the surface of tablets and surface of coated tablets prepared at different roll compaction pressure and tableting at 25 kN.
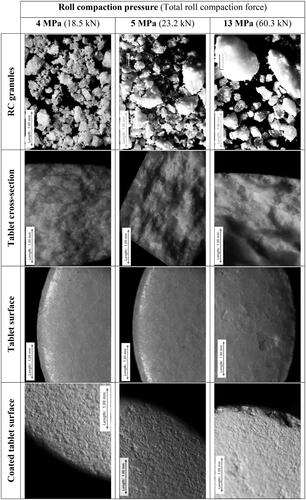
Figure 7. The effect of tapping on the density of roll compacted granules (RC granules) and the mixture which is intended for the tableting (tablet-mix).
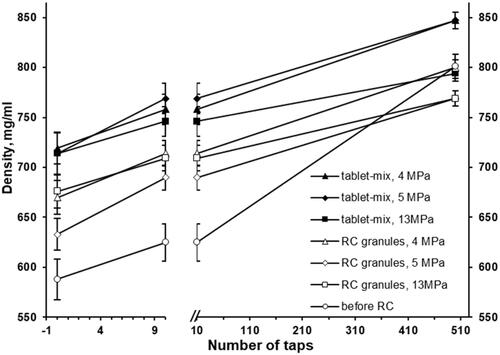
Figure 8. The effect of roll compaction pressure on the mass flow rate (FR) and Hausner ratio (HR) of roll compacted granules and the mixture which is intended for the tableting.
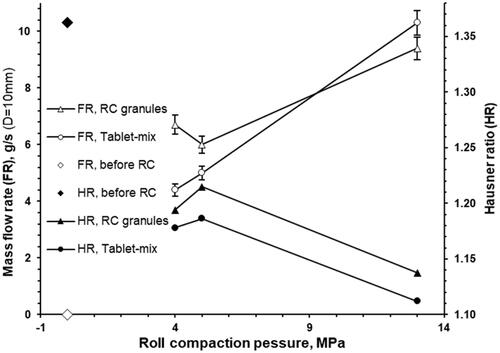