Figures & data
Table 1. Design parameters of the base cycle [Citation26].
Table 2. Geometrical parameters of the HTR and LTR [Citation26].
Figure 5. Compressor characteristics curves: (a) relative compression ratio; (b) relative efficiency.
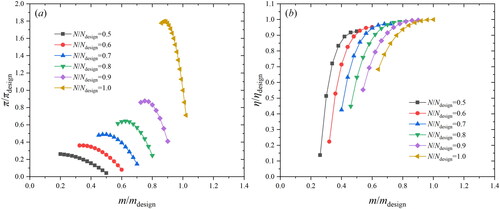
Table 3. Comparison of the calculation results and literature data of S-CO2 cycle [Citation26].
Table 4. Parameters in the cycle in different off-design conditions.
Figure 13. Outlet temperature transient variations of cold-side (a) and hot-side (b) fluids under mass flowrate stepwise varying conditions.
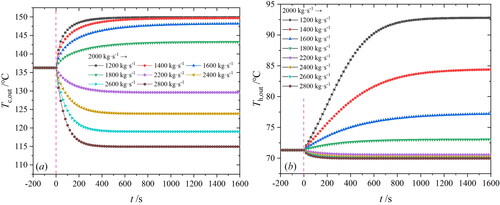
Figure 14. Pinch point location transient variations under mass flowrate stepwise-varying conditions.
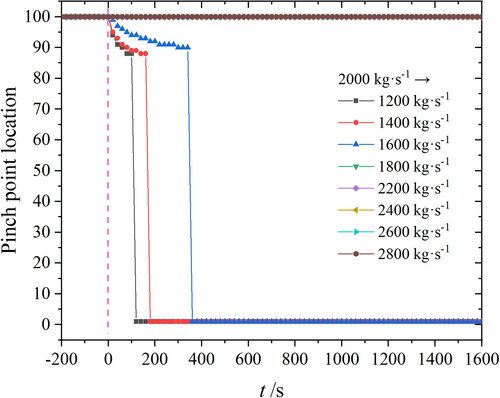
Figure 15. Pinch point temperature difference (a) and heat exchanger effectiveness (b) transient variations under mass flowrate stepwise-varying conditions.
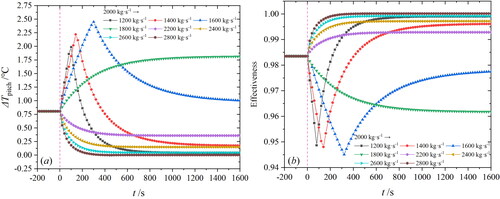
Figure 16. Outlet temperature variations of cold-side (a) and hot-side (b) fluids with time under pressure stepwise-varying conditions.
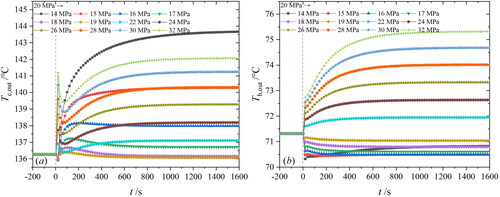
Figure 18. Pinch point temperature difference (a) and heat exchanger effectiveness (b) variations with time under pressure stepwise-varying conditions.
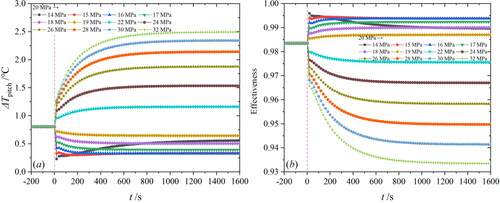
Figure 19. Outlet temperature variation of cold-side (a) and hot-side (b) fluids with time under temperature stepwise-varying conditions.
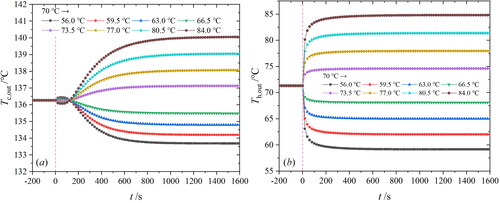
Figure 20. Pinch point location variations with time under temperature stepwise-decreasing (a) and stepwise-increasing (b) conditions.
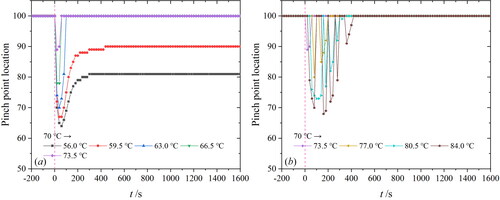
Figure 21. Pinch point temperature difference (a) and heat exchanger effectiveness (b) variations with time under temperature stepwise-varying conditions.
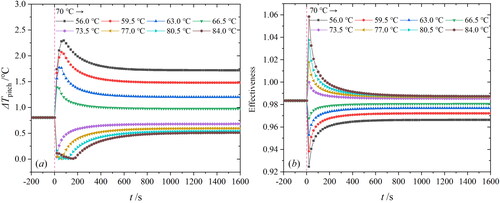
Figure 23. The variations of upper and lower CSRs with the temperature at the outlet of the precooler.
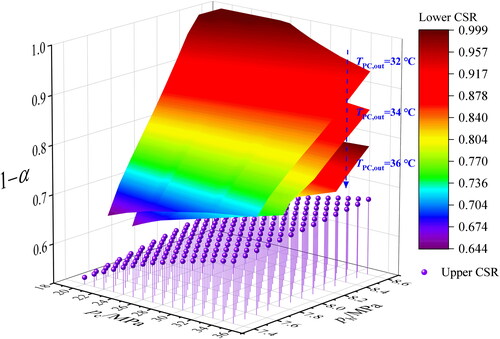
Figure 24. The upper and lower critical split ratio variation with isentropic efficiency of compressor.
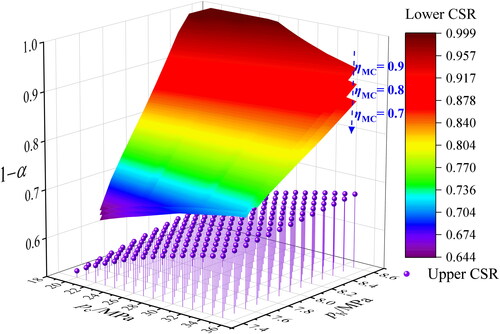